Лекция 12 Тема: Состав и количество основного оборудования в непоточном производстве
Вид материала | Лекция |
СодержаниеПервый метод. Второй метод. Третий метод. Четвертый метод. Пятый метод. Шестой метод. |
- Лекция 11 Тема: Состав и количество основного оборудования в поточном производстве, 124.87kb.
- План лекций для студентов педиатрического факультета на весенний семестр 2011-2012, 50.89kb.
- Воробьева Ольга Владимировна Атмосфера и атмосферные явления. Тема урок, 55.05kb.
- Лекция Тема: система междуранодных отношений, 117.17kb.
- Программа по дисциплине сд. 3 " Технологическое оборудование в производстве, обработке, 220.17kb.
- Аннотация диплом, 1006.46kb.
- Лекция «Математика в жизни, производстве, науке, в твоей будущей профессии», 51.21kb.
- 1 11 Тема 2 12 тема 3 13 Тема 4 14 Тема 5 15 Тема 6 17 Тема 7 20 Тема 8 22 Тема, 284.17kb.
- Учебное пособие Москва 2007 Содержание Лекция № Актуальность борьбы с шумом на производстве,, 1016.54kb.
- План помещения Служебный состав завода Gibson Расположение оборудования, 201.2kb.
Лекция 12
Тема: Состав и количество основного оборудования в непоточном производстве
При выборе состава основного оборудования для непоточного производства следует в первую очередь ориентироваться на результаты расчета экономической эффективности, а так же учитывать возможность встраивания его в автоматический комплекс с учетом как автоматизации его загрузки и разгрузки, так и стыковки системы управления оборудования с цент реализованной ЭВМ. Расчет экономической эффективности должен основываться на учете следующих факторов: номенклатуры и объема выпуска изделий, характера выполняемых операций, числа переходов в них и степени параллелизации их выполнения, стоимости оборудования, необходимого количества обслуживающего персонала и др. Широта номенклатуры непоточного производства вынуждает использовать основное оборудование, которое может быстро переналаживаться при смене выпускаемой продукции. Этим требованиям отвечают станки с ЧПУ, которые позволяют осуществлять быструю кинематическую переналадку, а при оснащении их системами автоматической размерной настройки — точностную переналадку, т. е. оборудование более низкого класса и группы.
Таким образом, в состав участков непоточного производства следует включать оборудование, отвечающее заданным требованиям для конкретных условий изготовления продукции при использовании которого будет достигнута минимальная себестоимость изготовления.
Использование основного оборудования с системами ЧПУ в составе автоматизированных участков позволяет сократит потери времени на его переналадку, а также уменьшить затраты оборотных средств, связанных с незавершенным производством, так как в этом случае значительно сокращается цикл производства изготовления изделия и повышается оперативность управления всем цехом. Наибольший эффект, получаемый в результате использования систем ЧПУ в составе автоматизированных комплексов, достигается при изготовлении сложных деталей малыми партиями, так как в этом случае сокращается время на подготовку и смену управляющих программ за счет централизованного управления от ЭВМ.
Затраты на переналадку технологического оборудования, приходящиеся на одно изготовляемое изделие,
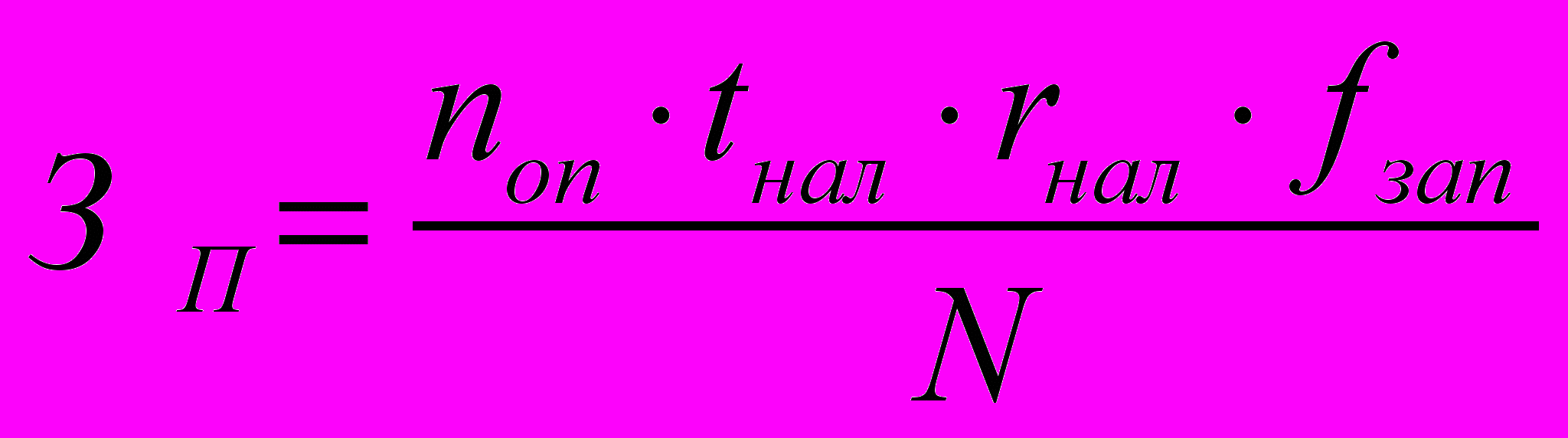
где поп — число операций, для которых по технологическому процессу необходима переналадка на изготовление изделий нового наименования; tнал — средняя продолжительность переналадки, ч; rнал — часовая ставка наладчика, учитывающая премию и накладные расходы на обслуживание производства, руб.; fзап — частота запуска партий изделий в течение года; N — годовой объем выпуска изделий, шт.
Следовательно, затраты на переналадку основного оборудования, приходящиеся на одну деталь, прямо пропорциональны сложности переналадки, частоте запуска партий изделий в течение года и обратно пропорциональны годовому объему выпуска изделий, т. е. они будут наиболее значительны в непоточном производстве.
Затраты в результате связывания оборотных средств в незавершенном производстве, приходящиеся на одно изделие,

где Си — полная себестоимость изделия, руб.; knот — коэффициент, учитывающий потери от связывания оборотных средств в незавершенном производстве, kпот = 0,1; Фд — число рабочих дней в году;
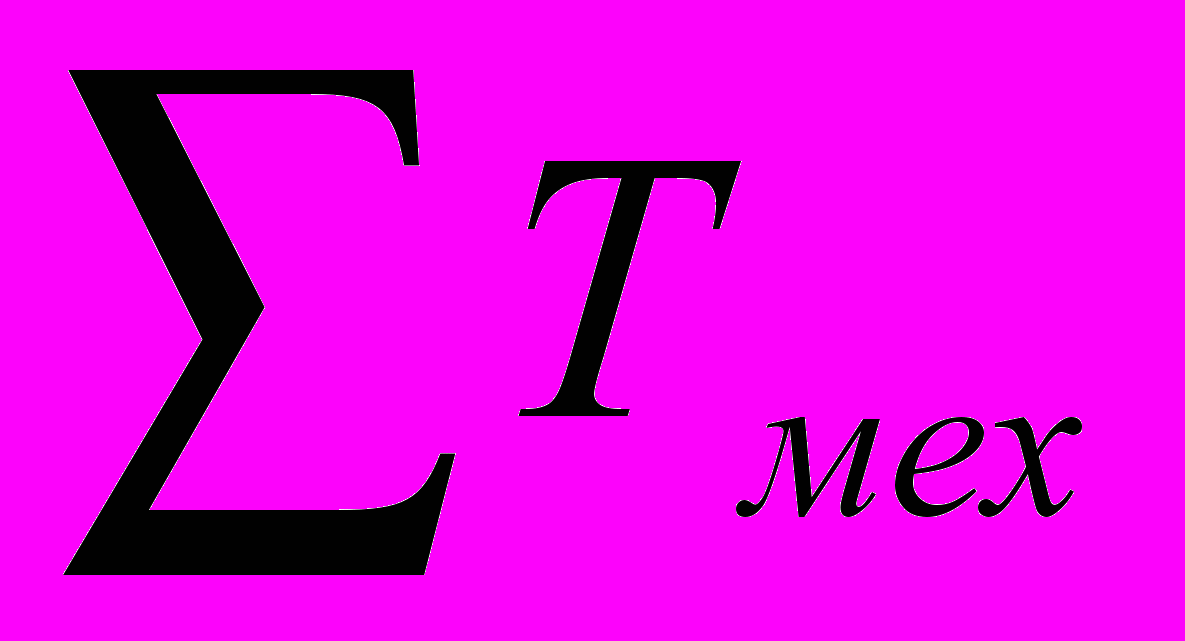
Из приведенной формулы вытекает, что с увеличением частоты запуска деталей в производство и уменьшением партии деталей пп = N/fзan затраты от связывания оборотных средств в незавершенном производстве будут снижаться.
Суммарные затраты, приходящиеся на одну деталь, от переналадки автономного оборудования с ЧПУ и связывания оборотных средств в незавершенном производств приведены на рис. 12.3. Из графика можно определить оптимальную част ту запуска, обеспечивающую минимум затрат.
Особенность определения количества основного оборудования в непоточном производстве, характеризующегося широкой и в ряде случаев нестабильной номенклатурой выпускаемых изделий, заключается в том, что в большинстве случаев невозможно разработать технологические процессы на каждое наименование изделия. В то же время для расчета количества основного оборудования необходимо знать суммарную станкоемкость обработки или машиноемкость в условиях автоматизированной сборки по операциям
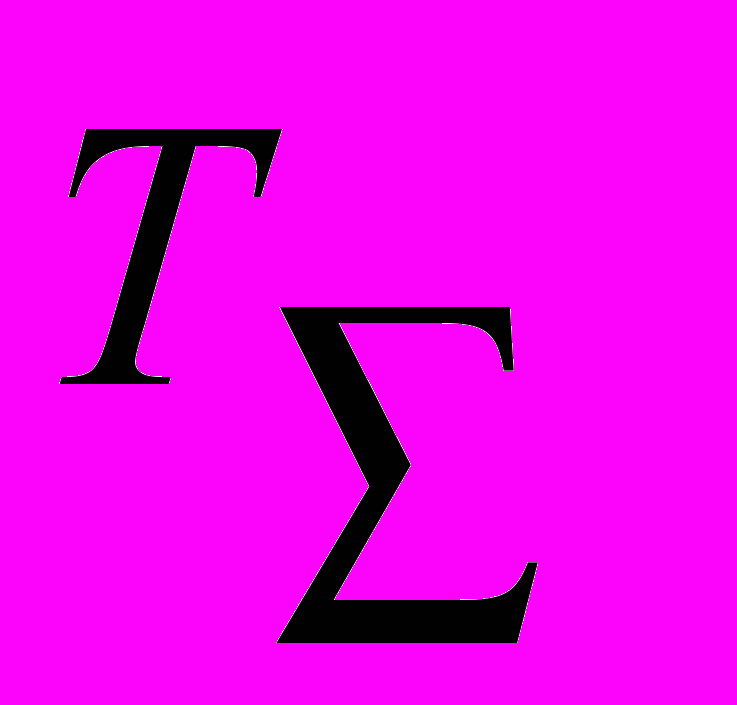
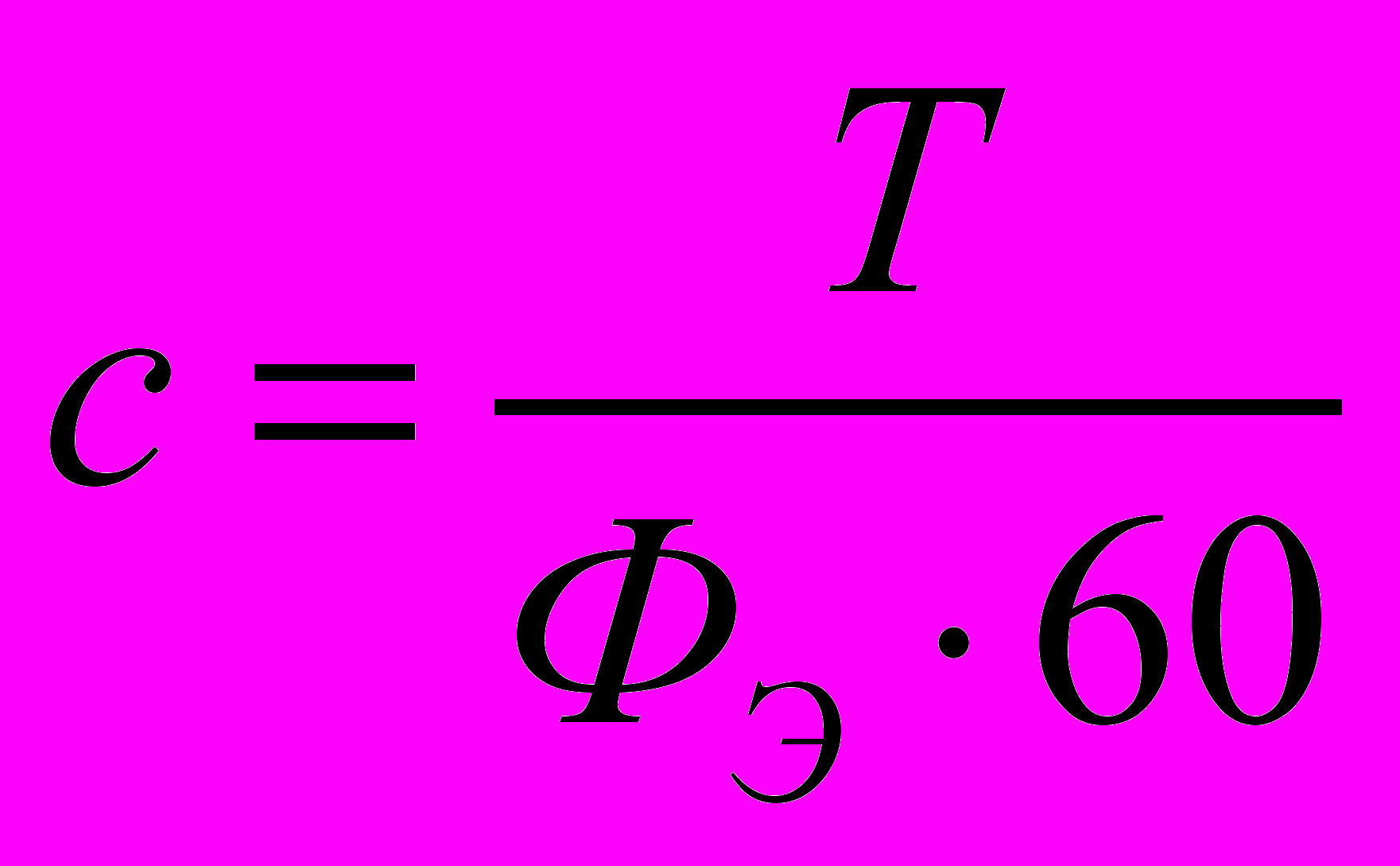
Для расчета количества оборудования в непоточном производстве используют различные методы приведения про граммы выпуска изделий, сущность которых заключаете в том, что суммарную станкоемкость или машиноемкость определяют для выбранных изделий-представителей в каждой группе изделий, на которые разрабатываются технологические процессы изготовления. В этом случае сокращается длительность и трудоемкость проектных работ.
На первом этапе осуществляют разбивку всех деталей сборочных единиц на группы по конструктивному и технологическому подобию. Для разбивки на группы необходимо классифицировать изделия с целью статистического описания совокупности изделий и их основных характеристик, для чего разработаны соответствующие классификационные признаки. Состав классификационных признаков обеспечивает возможность разбиения изделий на технологические группы в основе которых заложена не только общность технологических маршрутов изготовления, но и возможности используемого основного оборудования. Поэтому наиболее целесообразна классификация деталей, в основу которой положены технологические возможности металлорежущих станков. В этом случае любая деталь из всего множества номенклатуры, входящей в определенную группу, может быть описана набором классификационных признаков.
Кроме габаритных параметров, должны учитываться вид заготовки, определяющий особенности основного оборудования и технологический процесс изготовления, материал изготовляемой детали, определяющий условия стружкоудаления, и т. д.
Классификация сборочных единиц также осуществляется по конструктивно-технологическим признакам на базе общности применяемого сборочного оборудования и технологической оснастки. В качестве конструктивно-технологических признаков учитывают габаритные размеры, массу и геометрическую форму объектов сборки, их материал, геометрическую форму и размеры сопрягаемых поверхностей и баз, способность объектов сборки к загрузке в оборудование, точность относительной ориентации объектов на позиции сборки, вид сборочной операции и др.
В условиях автоматизированного проектирования классификация деталей может быть проведена по методике Оргстанкинпрома. Кодирование сложности детали проводится с использованием классификатора деталей, в котором детали различаются по следующим признакам: служебному назначению, основной форме (класс), габаритным размерам, материалу, массе, виду термической обработки, видам элементарных поверхностей и их размерам, точности и шероховатости. На каждую деталь заполняют кодировочную таблицу по данным чертежа детали и классификаторов классов деталей и элементарных поверхностей. Таким образом, создаются массивы данных по группам, классам и подгруппам материалов деталей. Затем проводится выявление и анализ характеристик совокупности деталей с целью определения основных требований к станкам и выбора деталей-представителей для проектирования технологических процессов.
Путем машинной обработки данных о деталях выявляют их распределения, характеризующие всю совокупность деталей определенного класса, в частности трехмерные распределения; размеры — сложность деталей, размеры — масса деталей, размеры — точность деталей; тип элементарной поверхности — положение относительно основной базы, тип элементарной поверхности — точность, тип элементарной поверхности — размер и др.
В распределениях, имеющих размерный параметр детали, можно выделить ряд деталей по размерным характеристика станков и иметь для этих интервалов описание совокупности деталей, которые по существу являются характеристикой комплексной детали.
Следует иметь в виду, что точность расчетов с использованием методов приведения программы выпуска в значительно степени зависит от формирования групп и выбора изделий-представителей.
Исходя из данных о распределении основных параметров изделий, определяют изделия-представители для класса изделий в выбранных размерных группах, отражающие характерный технологический маршрут изготовления изделий данной группы.
Рекомендуются следующие соотношения массы Мпр и годового объема выпуска Nnp изделия-представителя с соответствующими показателями в группе:


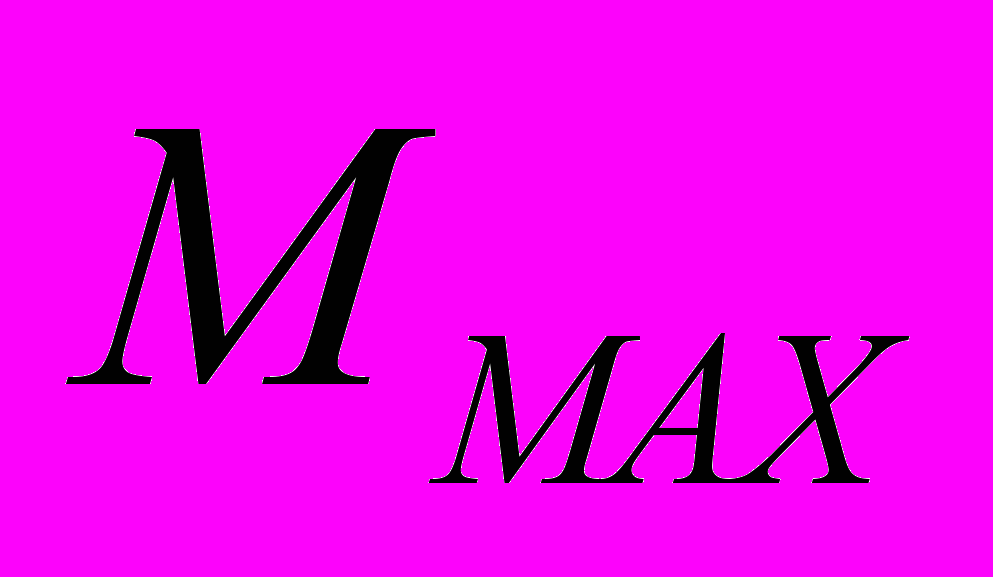
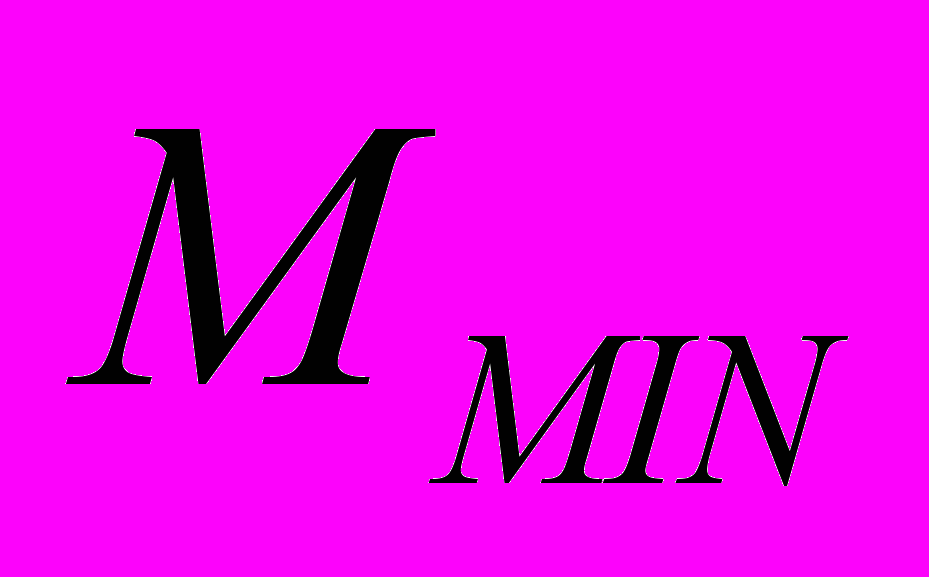
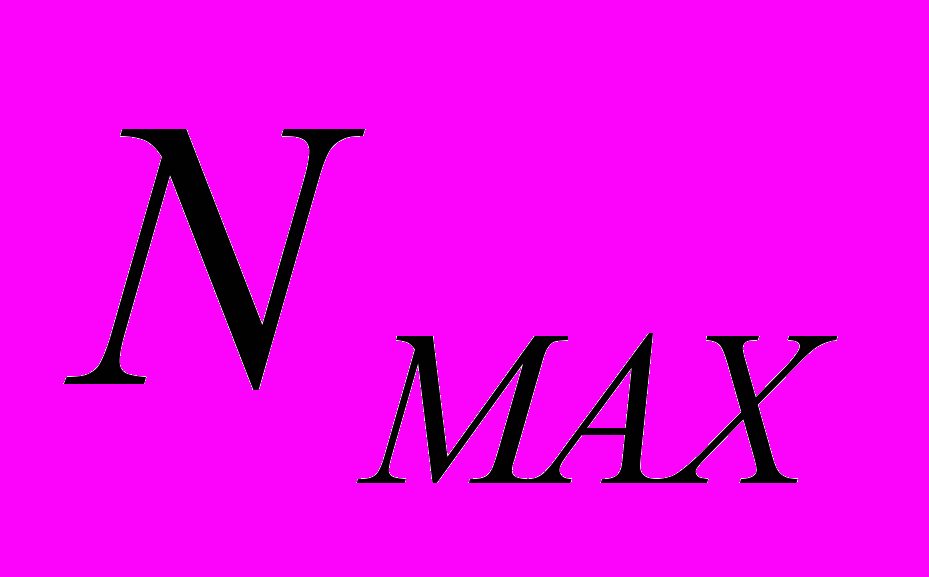
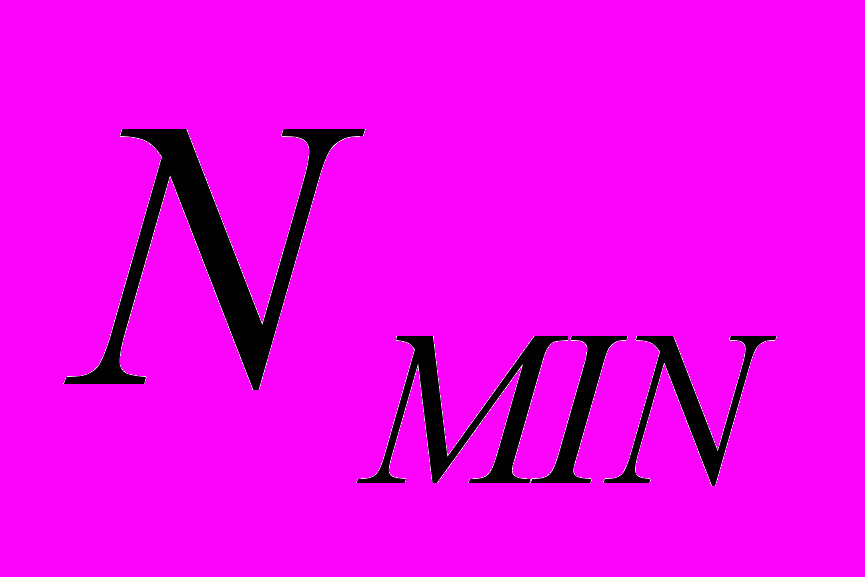
Разрабатывают технологические процессы и определяют станкоемкости изготовления изделий-представителей по операциям, имеющим наибольшую, среднюю и наименьшую сложность в группе.
Расчет количества каждого типа основного оборудования производится с использованием одного из следующих методов приведения программы выпуска.
Первый метод.
Поскольку известно значение машиноемкости в крайних интервалах (размах) и закон распределения (логарифмически нормальный), можно определить математическое ожидание машиноемкости по каждой операции и, умножив ее на число изделий, изготовляемых на данной операции, определить машиноемкость на годовую программу выпуска. Затем по формуле (12.3) рассчитывают количество основного оборудования, требуемое для каждой операции. Данный метод эффективен при автоматизированном проектировании машиностроительного производства.
Второй метод.
Трудоемкости изготовления изделий-представителей TMi по типам используемого оборудования в технологическом процессе изготовления делят на массу Mj соответствующих изделий-представителей, определяют машиноемкость изготовления одного килограмма изделия, которую и принимают как среднюю для всей рассматриваемой группы, из которой взяты изделия-представители. Умножив массу всей группы изделий Мj на среднюю станкоемкость 1 кг этой группы по типам оборудования и просуммировав полученные произведения, определяют общую машиноемкость, необходимую для изготовления изделий заданной программы выпуска по формуле:
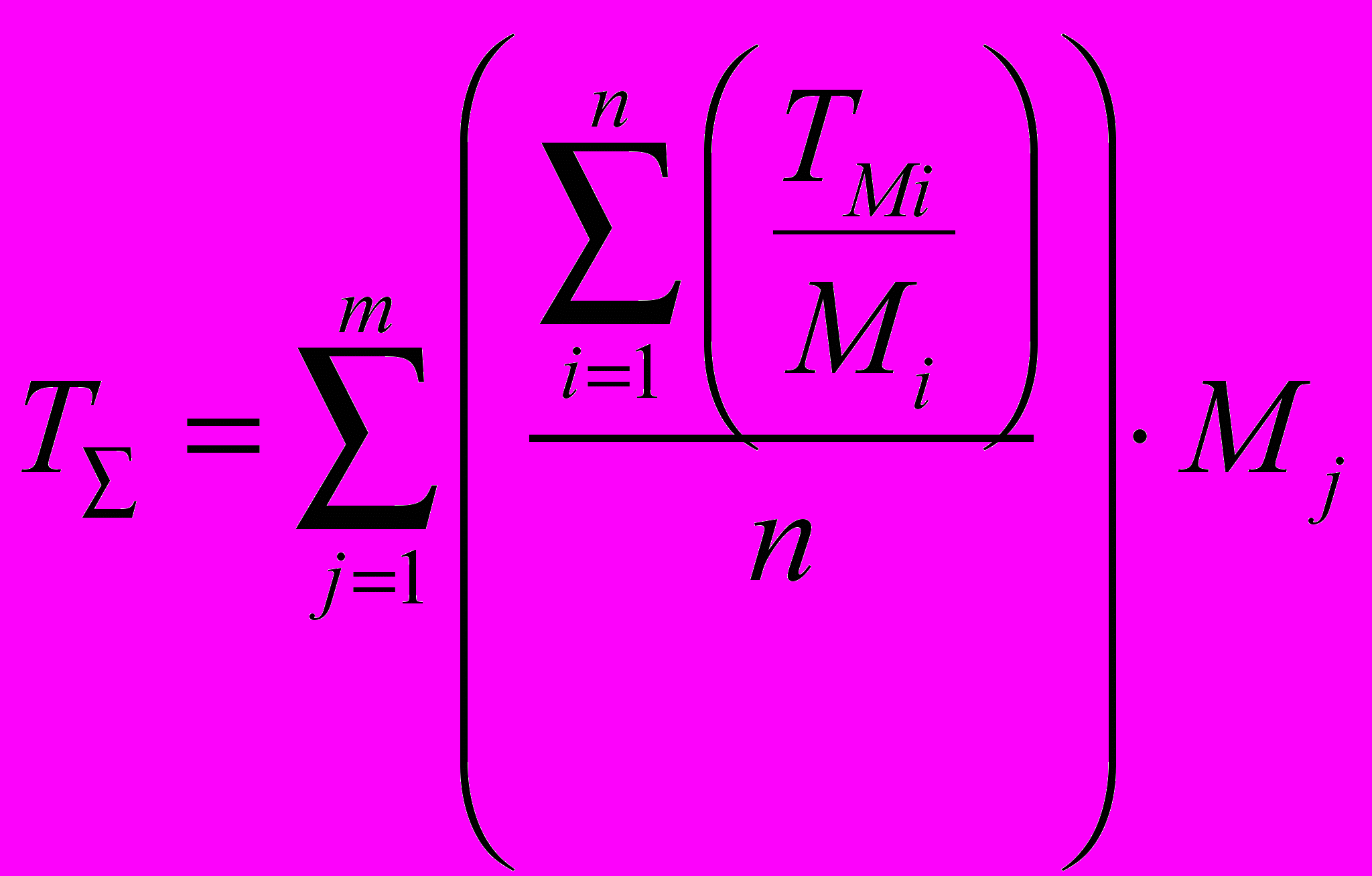
где n — число изделий-представителей; m — число групп.
Третий метод.
Определяют общий коэффициент приведения kпр, характеризующий отношение станкоемкости (машиноемкости) изготовления приводимого изделия к станкоемкости (машиноемкости) изделия-представителя. Он может быть определен через коэффициенты массы kM, серийности kсер, точности kT и оригинальности k0, по формуле:

Коэффициент kM, учитывающий различие в массе собираемого приводимого изделия Мпр и изделия-представителя Мпс, определяют по следующей эмпирической формуле:
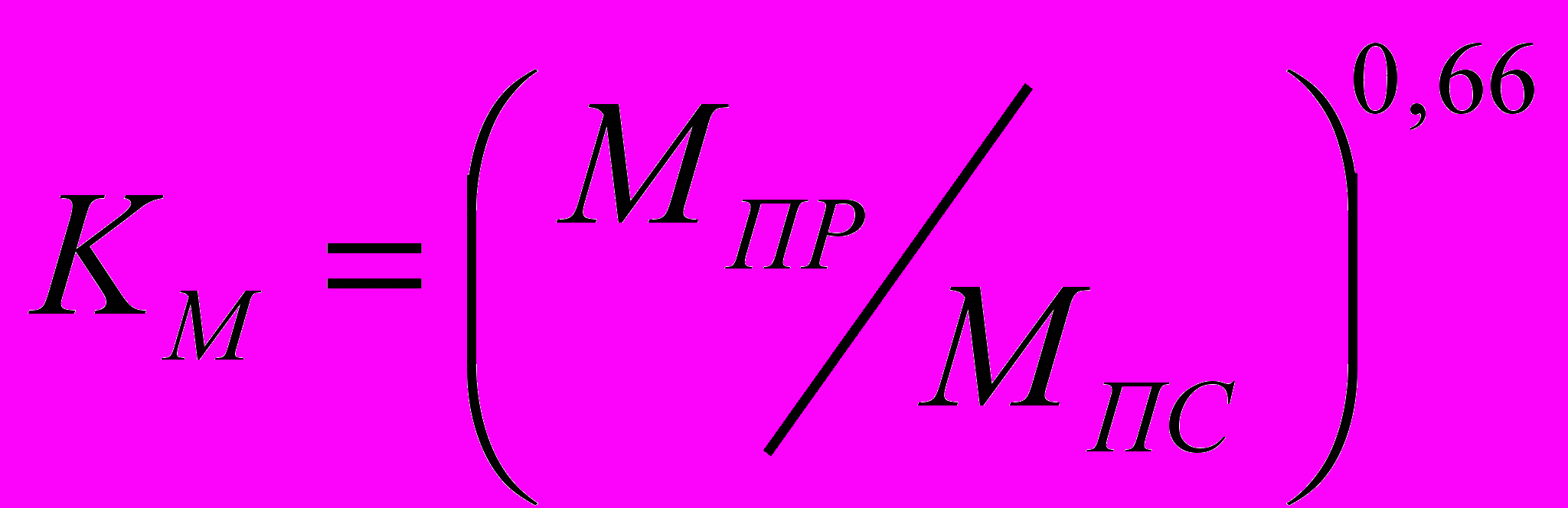
При механической обработке расчет выполняют по это же формуле, используя отношение площадей обрабатываемых поверхностей приводимого изделия и изделия-представителя.
Коэффициент серийности Кcep учитывает изменение машиноемкости (станкоемкости) изготовления при изменении объема выпуска изделий. Он отражает влияние объема выпуска изделий на время переналадок основного оборудования и определяется по формуле:
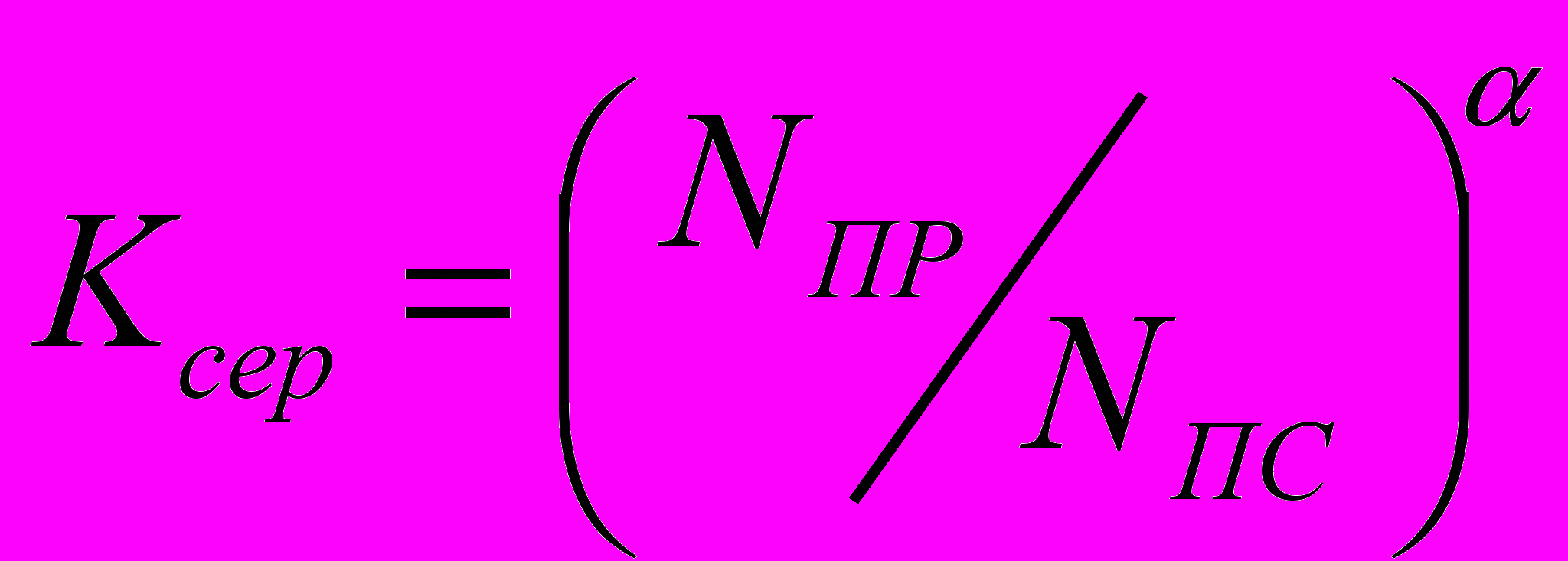
где
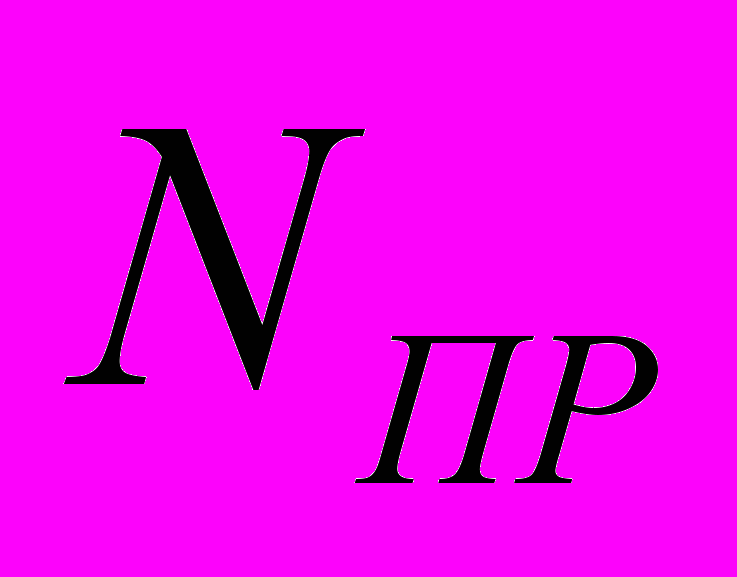
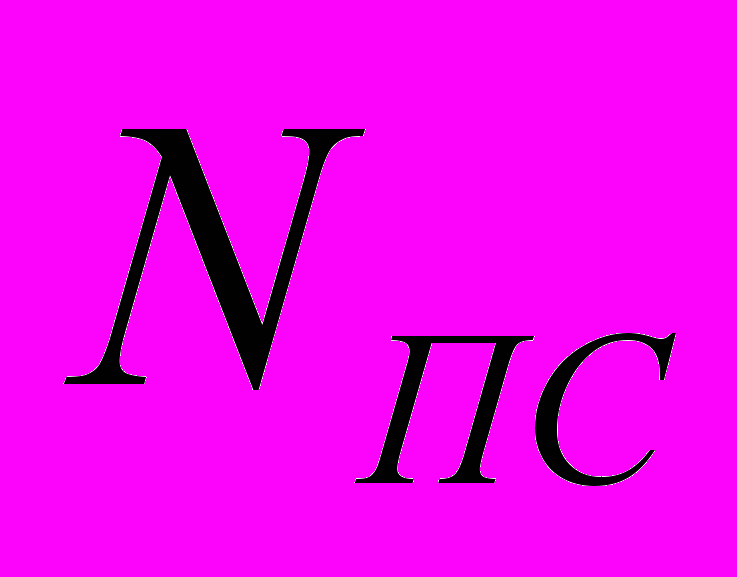
Коэффициент приведения по точности КT учитывает влияние точности изготовления изделий на станкоемкость (машиноемкость) операций. Например, ужесточение требования к точности или шероховатости обрабатываемых поверхностей приводит к росту станкоемкости обработки деталей за счет увеличения числа переходов или снижения режимов резания. В общем случае при сборке изделий нормальной точности Кт = 1,0; изделий повышенной точности Кт = 1,1 и изделий высокой точности Кт= 1,2. При механической обработке коэффициент Кт учитывает средний квалитет и среднее значение параметра шероховатости поверхностей детали Ra. Среднее значение квалитета приводимого изделия и изделия-представителя:
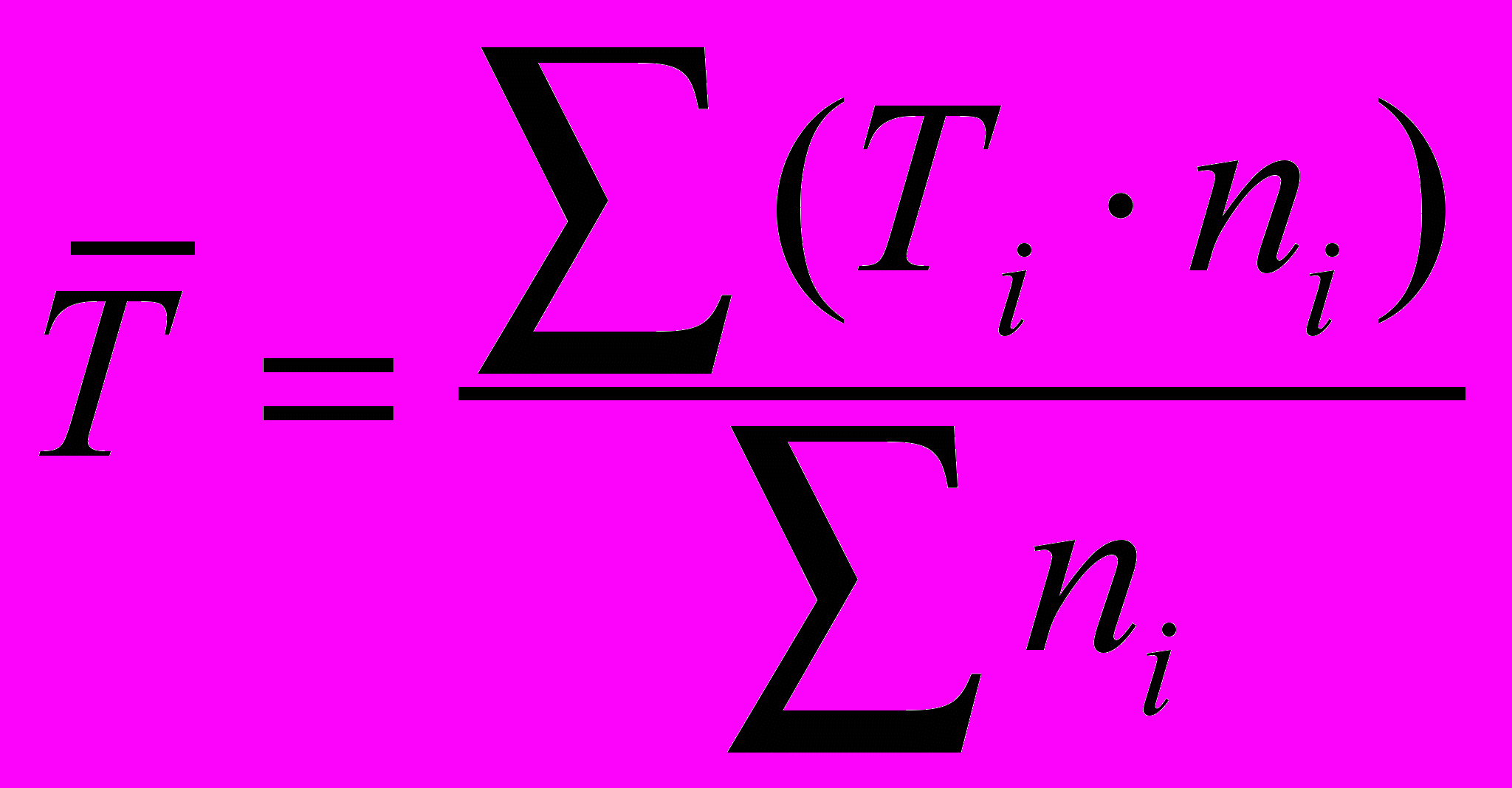
где Ti — i-й квалитет; ni — число размеров i-го квалитета.
Среднее значение параметра шероховатости поверхностей приводимого изделия и изделия-представителя:
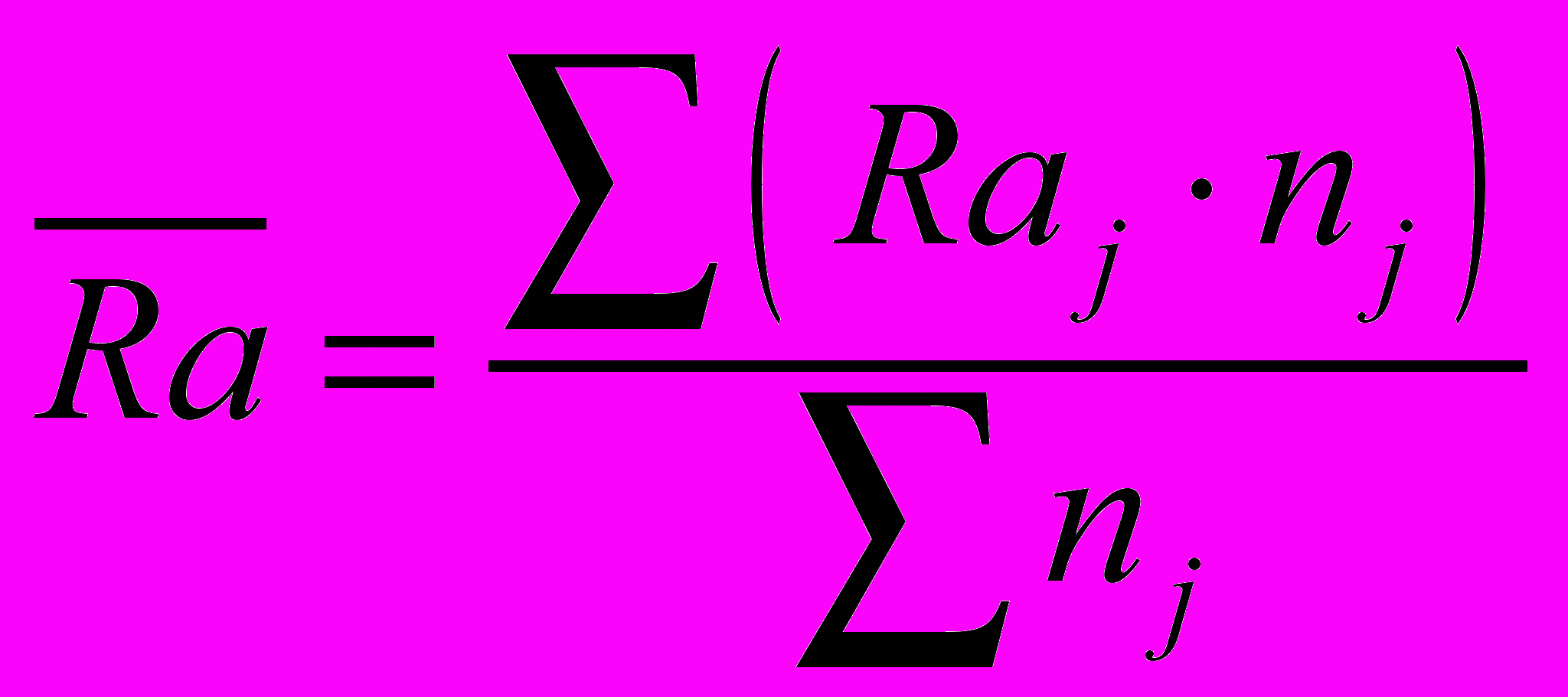
где Raj — j-e значение Ra; nj — число поверхностей, имеющих значение Ra = j.
Для определения коэффициента КT, характеризующего квалитет точности изделия, рекомендуется использовать следующие зависимости:
Средний квалитет Т | 6 | 7 | 8 | 11 | 12 | 13 |
КТ | 1,3 | 1,2 | 1,1 | 1,0 | 0,9 | 0,8 |
Величина Кш зависит от среднего параметра шероховатости поверхностей детали:
Среднее значение параметра шероховатости поверхности Ra | 20 | 10 | 5 | 2,5 | 1,25 | 0,63 |
КШ | 0,95 | 0,97 | 1,0 | 1,1 | 1,2 | 1,4 |
При механической обработке:
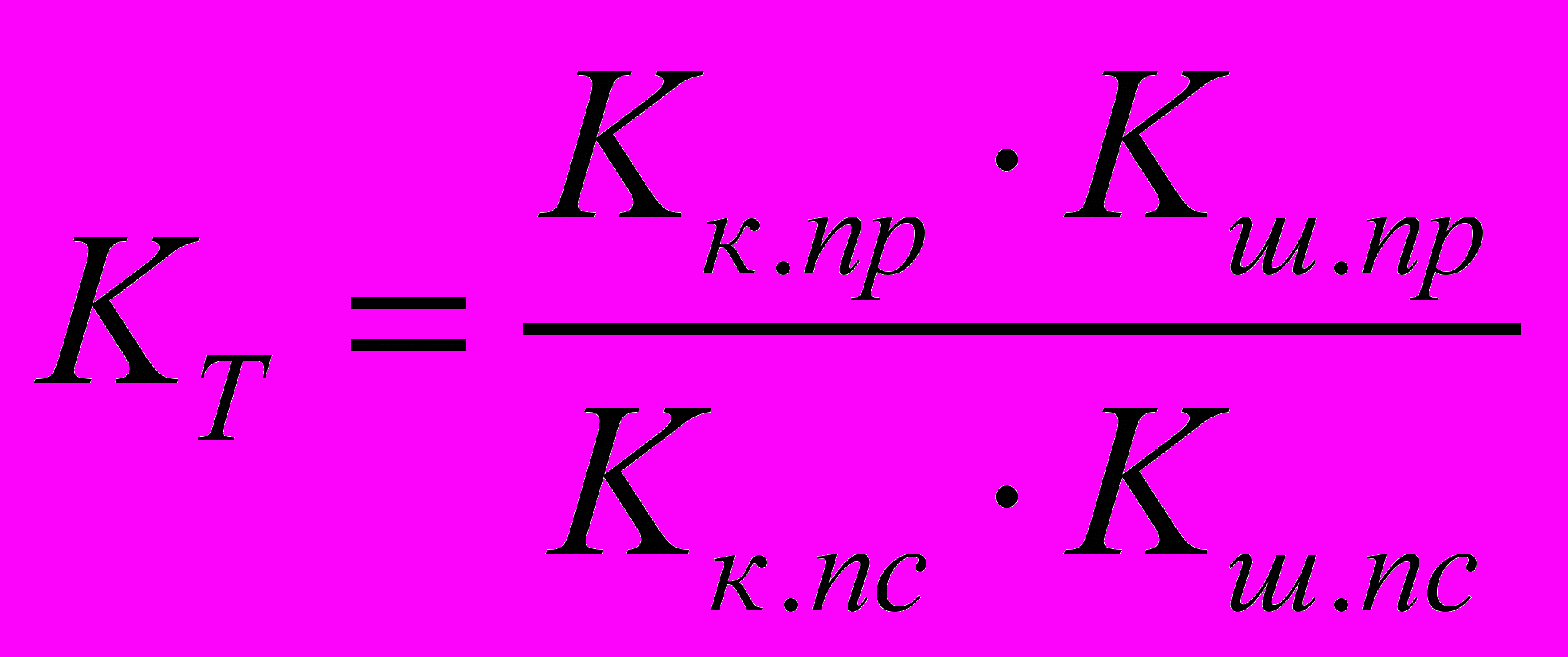
В сборочном производстве определяют коэффициент Ко, учитывающий число оригинальных деталей в сборочных единицах, из зависимости
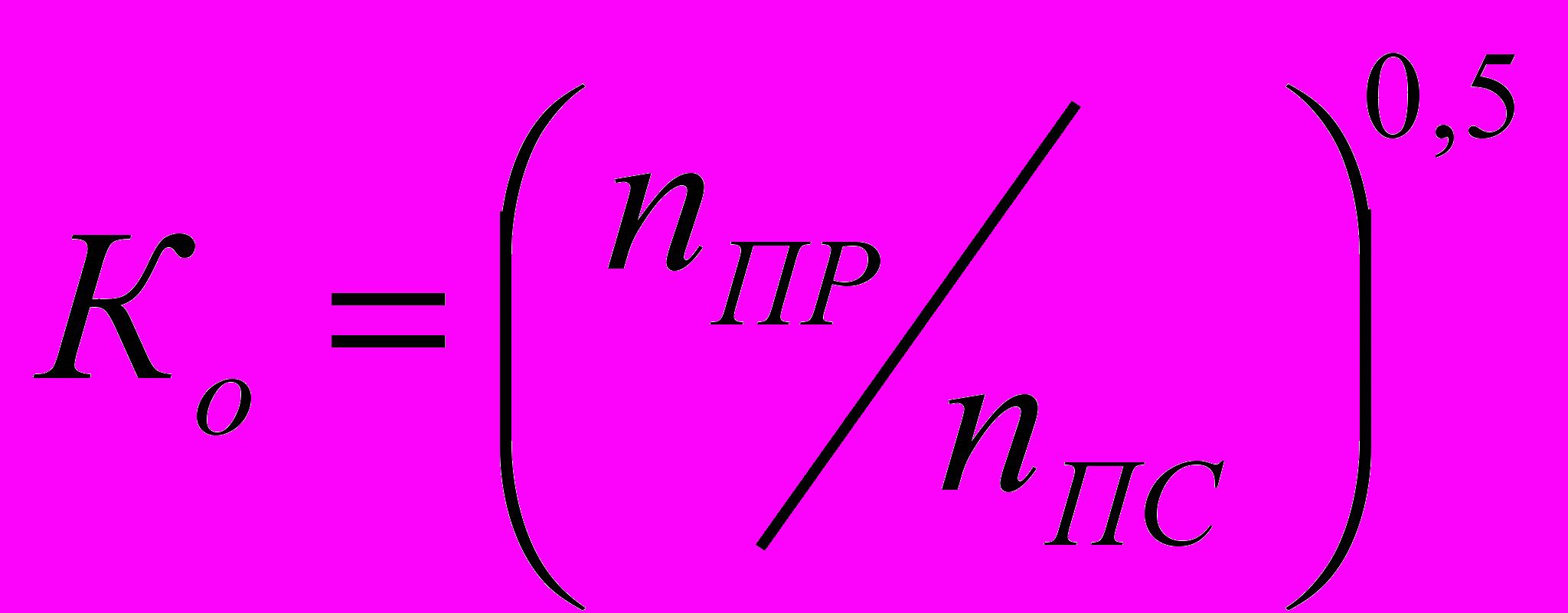
Произведение всех коэффициентов приведения даст общий коэффициент приведения KПР, который позволит определить станкоемкость изготовления детали или машиноемкость сборки узла в автоматизированном производстве, не разрабатывая при этом технологический процесс изготовления рассматриваемого изделия. Для этого умножают коэффициент приведения KПР на станкоемкость (машиноемкость) изделия-представителя:
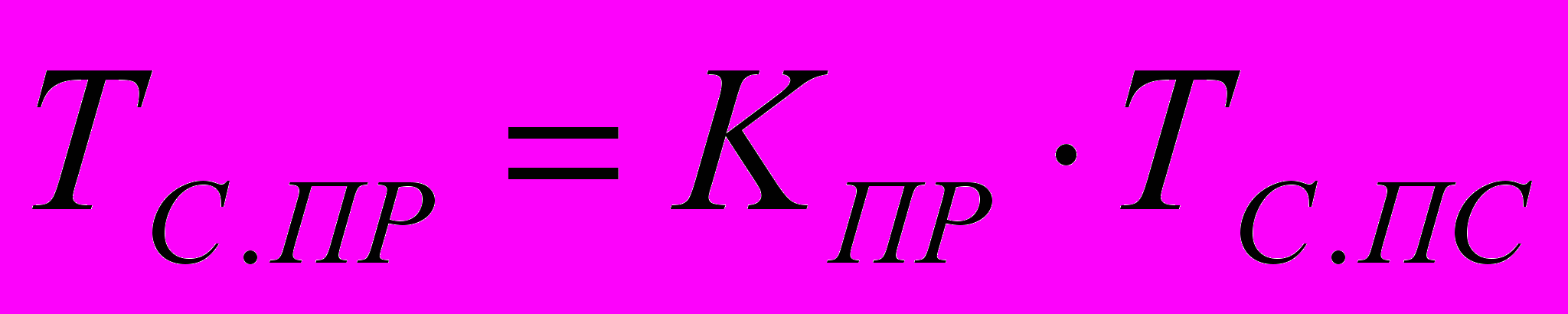
Определив коэффициент приведения для каждого изделия в группе, можно найти суммарную станкоемкость (машиноемкость) изготовления изделий всей группы.
Четвертый метод.
Проектирование экспериментальных сборочных и механических производств выполняют по условной программе, так как для них характерна нестабильность номенклатуры выпускаемых изделий. В этом случае выбирают условные изделия, на которые имеются чертежи, в таком количестве, чтобы их масса была равна массе изделий, планируемых к выпуску в данном производстве. На все детали этого изделия разрабатывают технологические процессы и определяют суммарную станкоемкость по типам необходимого оборудования (по операциям) на годовой выпуск деталей по заданной программе.
Пятый метод.
При реконструкции или техническом перевооружении действующих цехов используют способ расчета количества основного оборудования, основывающийся на наличии заводских данных о станкоемкости изготовления изделий и планируемого снижения станкоемкости за счет внедрения прогрессивной технологии и повышения уровня автоматизации проектируемого производства.
Наибольший эффект достигается в результате внедрения нового оборудования на лимитирующих операциях технологического процесса, поэтому при изучении действующего процесса необходимо их выявить и выяснить их фактическую трудоемкость, уровень технологического оснащения. Повышение производительности на лимитирующих операциях позволит резко повысить производительность всего производственного процесса.
Сущность расчета количества основного оборудования заключается в следующем. Собирают данные о фактической станкоемкости выполнения каждой операции технологического процесса изготовления трех-четырех изделий-представителей в каждой группе. На основании анализа полученных данных определяют лимитирующие операции, на которых следует использовать более прогрессивное оборудование. Имеющиеся станкоемкости по каждому виду работ корректируют с учетом изменения объема выпуска изделий и снижения станкоемкости изготовления благодаря использованию более производительного оборудования. Коррекция осуществляется путем введения коэффициента коррекции станкоемкости Kкp, определяемого по формуле:
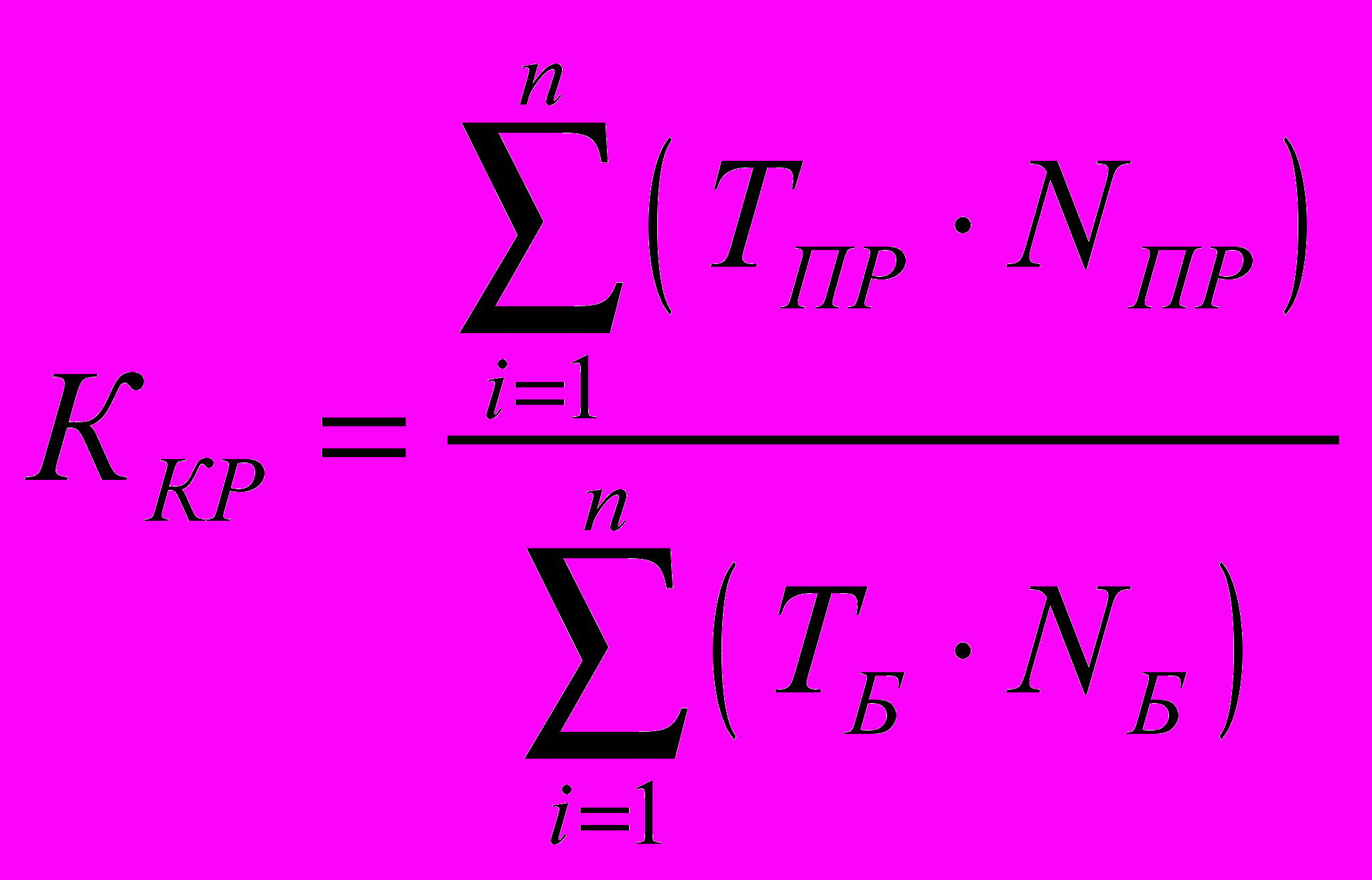
где Тб и Тпр — соответственно базовая и проектная станкоемкость выполнения операции; Nб и Nпр — соответственно базовый и проектный объем выпуска изделий-представителей; n — число изделий-представителей в выбранной группе.
Для определения проектной станкоемкости Тпр разрабатывают новый прогрессивный технологический процесс для реконструируемого производства. Коэффициент коррекции станкоемкости зависит от сложности изготовляемых изделий, технического уровня действующего производства и партии запуска. Чем сложнее изготовляемое изделие, ниже технический уровень действующего производства и меньше партия запуска, тем меньше коэффициент коррекции станкоемкости, и наоборот.
Полученный расчетным путем средний коэффициент коррекции станкоемкости относят ко всем изделиям в группе и, пользуясь им, определяют проектную, новую станкоемкость изготовления всех изделий в группе, не разрабатывая при этом технологического процесса их изготовления. Проектную станкоемкость определяют по формуле
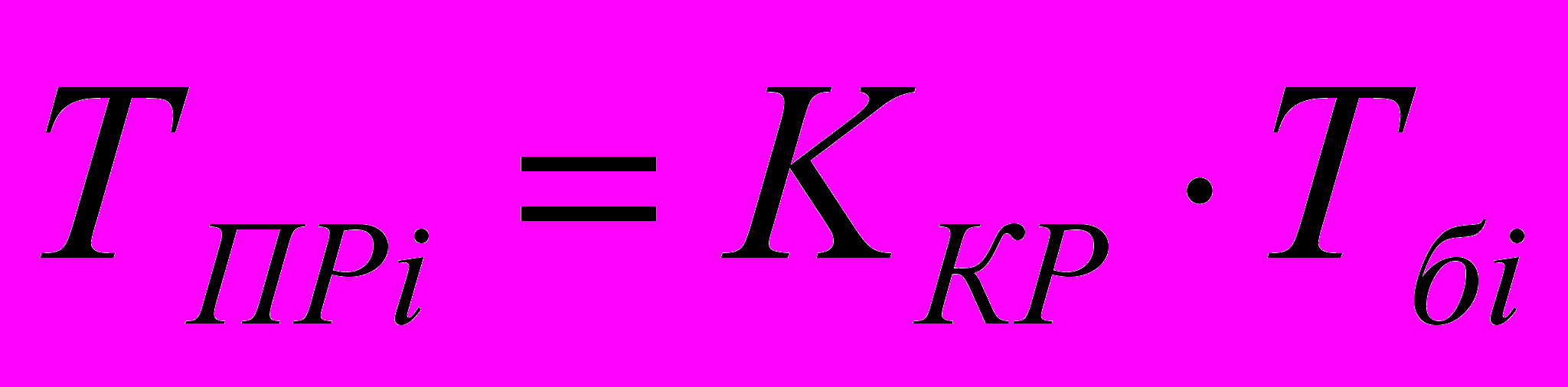
Аналогичные расчеты проводят для каждой группы изделий и, суммируя эти значения для каждой операции, определяют количество основного оборудования.
Шестой метод.
На стадии предпроектного периода используют укрупненный способ определения количества основного оборудования, основанный на использовании технико-экономических показателей. При этом способе в качестве исходных данных должны быть известны показатели продукции по массе, габаритным размерам, сложности, точности и соответствующие нормативные технико-экономические показатели. Последние устанавливают на основании анализа изготовления аналогичных изделий на передовых заводах страны и за рубежом, проведенного специальными отраслевыми технологическими институтами.
При этом способе технологический процесс изготовления изделий не разрабатывают, а в качестве основы для расчетов принимают следующие обобщающие технико-экономические показатели:
- станкоемкость механической обработки или трудоемкость (машиноемкость) сборочных работ 1 т массы изделий;
- годовой выпуск продукции, осуществляемый единицей основного оборудования для принятого режима работы в натуральном выражении (т, шт.);
- годовой выпуск изделий, осуществляемый единицей основного оборудования в денежном выражении (вследствие непостоянства показателя он используется редко).
Точность расчетов, выполненных этим способом, в основном зависит от точности принятых в основу технико-экономических показателей.
Расчет по показателю машиноемкости осуществляют в следующей последовательности. Выбрав из аналогичных производств подобное изделие, которое будет изготовляться в проектируемом цехе, и зная машиноемкость изготовления 1 т его массы, берут этот показатель в качестве исходного. Суммарная машиноемкость изготовления всех изделий

где Тн — нормативная машиноемкость изготовления 1 т изделий, маш-ч; Ми — масса изделия, т; N — годовой объем выпуска данного изделия, шт.;
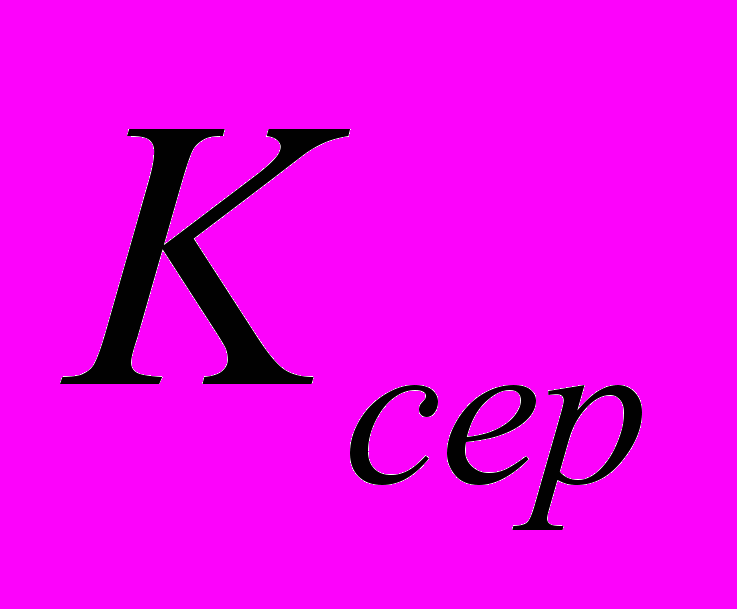
Коэффициент серийности
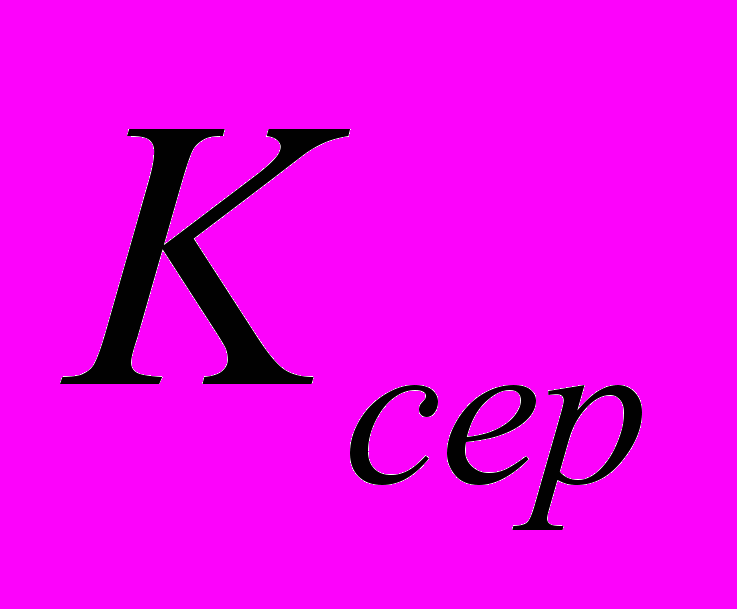
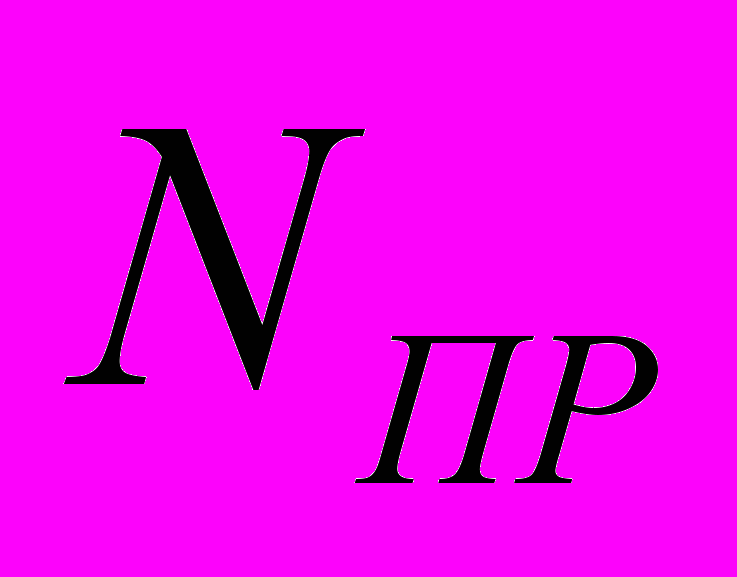
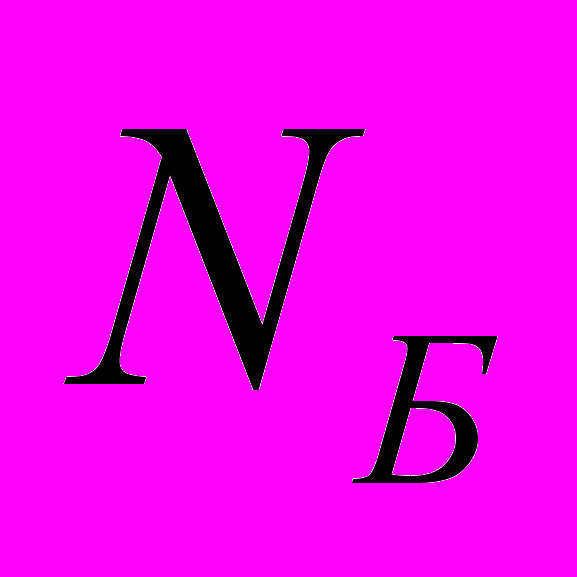
![]() | 0,10 | 0,20 | 0,30 | 0,40 | 0,50 | 0,65 | 0,90 |
![]() | 0,73 | 0,78 | 0,83 | 0,87 | 0,90 | 0,94 | 0,99 |
Зная суммарную станкоемкость изготовления изделий, с помощью формулы (12.3) можно рассчитать количество основного оборудования для проектируемого машиностроительного производства.