Ббк. 34. 642 С 36 удк 621. 791. 94
Вид материала | Справочник |
- Удк 621. 316: 621. 311. 1 Экономика и организация производства, 95.87kb.
- Учебное пособие Санкт-Петербург 2005 удк 662. 61. 9: 621. 892: 663. 63 Ббк г214(я7), 546.15kb.
- Развитие тезауруса классификационных рубрик по физике полупроводников, 199.49kb.
- Удк 621. 311, 94.08kb.
- Удк 621. 787. 4, 81.3kb.
- Удк 621. 313 Молчанова светлана юрьевна, 209.19kb.
- Методические указания Волгоград 2010 удк 621. 91 Рецензент, 669.19kb.
- Удк 621. 045/. 07: 669., 80.54kb.
- Удк 656 08; 629 072 ббк 52. 5: 88., 1958.04kb.
- Удк 338. 45: 621 Новиков Александр Николаевич, 260.62kb.
Назначение рациональных режимов обработки при зубодолблении заключается в выборе величины круговой подачи и скорости резания, которые зависят от параметров обрабатываемого зубчатого колеса, характеристики используемого оборудования и требуемого качества нарезаемого колеса.
Рекомендуемые величины круговых подач для станков с различной мощностью главного привода приведены в табл. 53, рекомендуемые скорости резания — в табл. 54, а поправочные коэффициенты на режимы резания для измененных условий работы — в табл. 55.
Величины подач в таблицах указаны при обработке за один рабочий ход. При черновой обработке в два рабочих хода табличные значения подач следует увеличить на 20% (умножить на коэффициент 1,2). Величины радиальных подач (при врезании) определяются по формуле spall = 0,1 . . . 0,3 sKp-

Большие значения подач следует применять при обработке зубчатых колес с числом зубьев свыше 25, меньшие — с числом зубьев до 25.
где I — длина хода штосселя, мм; п — частота движения штосселя, дв. ход/мин.
Эксцентриситет кривошипного вала (КМ) обеспечивает длину хода штосселя на величину до 120 мм.
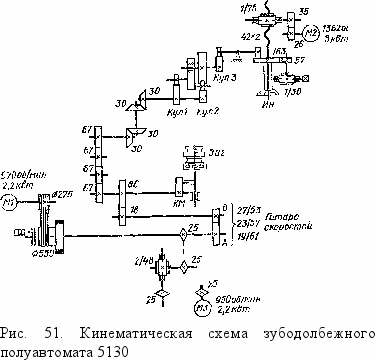
Кинематическая цепь подачи связывает поступательное движение заготовки (Заг) с радиальным перемещением резцов в резцовой головке (Ин). Подача и отвод резцов производятся двумя конусами, между которыми расположены хвостовики резцов. В цепи подачи имеются три кулачка, которые производят следующие действия. Кулачок 1 (Кул1) за каждый двойной ход заготовки совершает один оборот и через систему рычагов воздействует на конусы
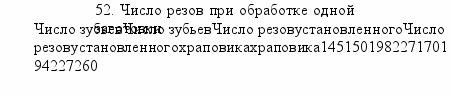
резцовой головки, опуская и поднимая их на 1,7 им, что в свою очередь сдвигает и раздвигает резцы на величину 0,85 ,мм. При раздвинутых резцах заготовка совершает холостой ход вниз. Кулачок 2 (Кул2) .воздействует на собачку храпового механизма, связанного с кулачком 3 (КулЗ), профиль которого имеет плавный подъем кривой на большей части окружности и «рутой спуск на меньшей ее части. Величина подъема профиля кулачка 3 должна быть равна двойной высоте зуба нарезаемого колеса; следовательно, на каждый нарезаемый модуль требуется свой кулачок подачи. Для получения различной величины единичной подачи устанавливают храповик с другим числом зубьев, при этом одна заготовка полностью может быть обработана с различным числом резов, приведенных в табл. 52.
55. Поправочные коэффициенты на режимы резання для измененных условий работы [7]
В зависимости от механической характеристики стали
Коэффициенты
Марка стали
Твердость НВ
на подачу
на скорость
на мощность Kajj\{
35
156 .. . 187 170 .. . 207
1.0
I.I
1,0
45
До 241
170 .. . 229
0,9
0,8 0,9 1.0
35Х, 40Х
156 .
207
1,0
1,0
12ХН4А, 20ХНМ, 18ХГТ, I2XH3, 20Х
156 ... 229
0,9
0,9
ЗОХГТ
156 ... 207
0,9
0,8
0,9
38ХМЮА
156 .. . 229
0,7
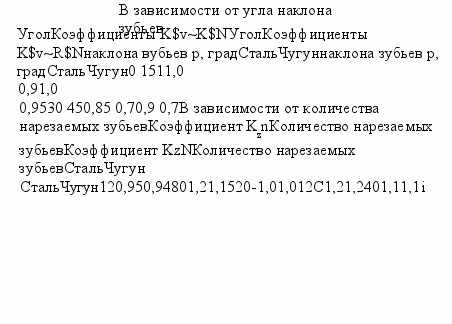
Частота движения долбяка определяется по формуле
1ООО•v , , п = ——— (дв. ход/мин),
где L — длина хода долбяка, состоящая из ширины нарезаемого зубчатого венца (Ь) и величины перебега (U) в обе стороны от венца, определяемого по табл. 56.

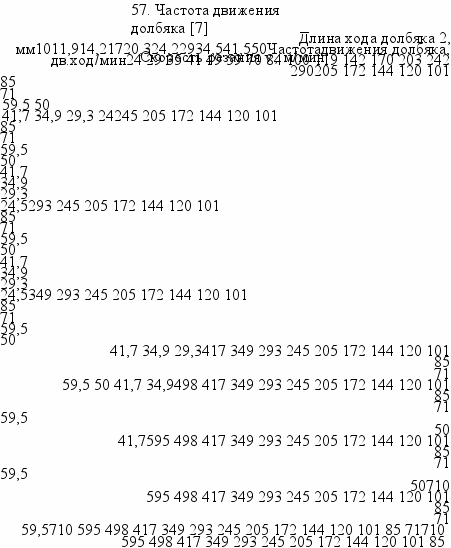
В табл. 57 приведена частота движения долбяка, определенная для ряда длин и скоростей. На станке устанавливается ближайшее от табличного значение.
Пример определения режимов резания при зубодолблении
Деталь — цилиндрическое зубчатое колесо, модуль т = 3 мм, число зубьев z = 35, ширина венца Ь = 25 мм, угол наклона зубьев 6 = 20°, материал сталь 40Х, твердость НВ 156 .. . 207.
Операция — чистовая обработка по сплошному металлу.
Оборудование — универсальный зубодолбежный полуавтомат 5122, мощность главного привода 2,1/3 кВт, наибольший обрабатываемый модуль 5 мм.
Выбор подачи. По табл. 53 круговая подача при чистовом нарезании по сплошному металлу для стали выбирается s кр = 0,30 мм/дв. ход. По табл. 55 поправочный коэффициент на подачу К Ms — 1,0.
Согласно паспорту станка круговая подача принимается sKp= 0,315 мм/дв. ход.
Величина радиальной подачи подсчитывается s рад= sKp -0,2 = 0,30-0,2== =0,06 мм/дв. ход и принимается согласно паспорту станка 5рад=0,067 мм/дв. ход.
Определение скорости резания. По табл. 54 для нарезаемого модуля до 4 мм и при круговой подаче 0,32 мм/дв. ход скорость резания составляет v = = 18,2 м/мин.
По табл. 55 поправочные коэффициенты на скорость резания: а) в зависимости от механической характеристики стали Д'лг» = 1,0; б) в зависимости от угла наклона зуба К = 0,9. Нормативная скорость резания с учетом коэффициентов v = 18,2 1,0-0,9 = 16,4 м/мин.
Частота движения долбяка. По табл. 56 величина перебега долбяка для ширины венца свыше 19 и до 51 мм составляет h = 8 мм.
Длина хода долбяка L = b + U = 25 + 8 = 33 мм. По табл. 57 для длины хода долбяка 35 мм и скорости резания 17 м/мин частота движения долбяка составляет я = 245 дв. ход/мин.
Согласно паспорту станка принимаем ближайшее большее значение, так как нормативная взята по меньшим параметрам скорости резания: п = 280 дв. ход/мин. При этом фактическая скорость резания будет
2-n-L 2-280-33
v= = = 18,5 м/мин.
1000 1000
Проверка режимов по мощности, затрачиваемой на резание, производится по табл. 54.
Для модуля до 4 мм и круговой подачи «кр = 0,32 мм/дв. ход мощность на резание составляет N = 1,2 кВт.
По табл. 55 поправочные коэффициенты на мощность: в зависимости от механической характеристики стали К mist = 1,0; в зависимости от угла наклона зуба Kpiv — 0,9; в зависимости от числа зубьев Kzjy = 1,1.
Нормативная мощность, затрачиваемая на резание с учетом коэффициентов: N = 1,2-1,0-0,9-1,1 = 1Д8 кВт.
Мощность на шпинделе станка N3 с учетом к.п.д. г]=0,8 составляет; N3 = 2,1-0,8 = 1,68 кВт, что больше мощности, потребляемой на резание; следовательно, режимы резания выбраны правильно.
§ 25. Причины брака при зубодолблении и способы его устранения
При зубодолблении цилиндрических колес на них могут возникать погрешности, превышающие величины, допускаемые соответствующими стандартами для требуемой точности колеса, и приводящие к браку.
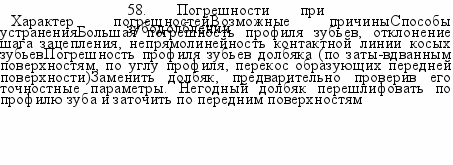
В табл. 58 приведены наиболее характерные из этих погрешностей, указаны причины их возникновения я даны способы их устранения.
Характер погрешностей
Возможные причины
Способы устранения
Местное отклонение у ножки зуба. Отклонение контактной линии косых зубьев, неравномерность шагов зубьев
Циклические погрешности делительных передач станка, большие осевые люфты в делительных передачах
Затупление уголков зубьев долбяка
Нестабильность фиксации механизма отвода долбяка на рабочем ходу
Местные погрешности шагов зубьев долбяка
Подтянуть гайки на валу червяка, довести зазоры в червячной делительной передаче до величины не более 0,005 мм
Заточить долбяк
Проверить надежность фиксации механизма отвода долбяка
Перешлифовать долбяк по профилю зубьев
Большая накопленная погрешность окружных шагов зубьев, радиальное биение зубчатого венца, колебание длины общей нормали
Погрешность направления зубьев, симметричная по обоим профилям (конусообразность зубьев
Погрешность направления в одну сторону по обоим профилям
Большая шероховатость поверхности зубьев
Большая накопленная погрешность шага зубьев долбяка
Радиальное биение долбя-ка на станке, перекос передней поверхности долбяка!
Неполный оборот колеса на рабочем ходе
Значительное изменение температуры в процессе нарезания одного колеса
Непараллельность направления движения штосселя с долбяком относительно оси вращения колеса в его радиальной плоскости
При нарезании прямозубых колес: непарал-яельность направления движения штосселя относительно оси вращения колеса в плоскости, касательной колесу
При нарезании косозу-бых колес неточность винтовых направляющих станка
Затупление режущих кромок долбяка
Нежесткое крепление долбяка или заготовки
Загрязнение и неправильный выбор смазочно-охлаждающей жидкости (СОЖ)
Заменить долбяк
Установить заново долбяк с минимальным радиальным биением и без перекоса передней поверхности
Заменить долбяк на имеющий более благоприятное отношение чисел зубьев долбяка и нарезаемого колеса
Обильно охлаждать заготовку, измелить режимы резания
Довести точность станка по направлению движения штосселя до нормативной величины
Довести точность станка по направлению движения штосселя до нормативной величины
Сменить и а станке винтовые направляющие
Заточить долбяк
Увеличить жесткость крепления заготовки, приблизив опорный торец приспособления к нарезаемому венцу
Сменить СОЖ
ГЛАВА V. ШЕВИНГОВАНИЕ И ХОНИНГОВАНИЕ ЗУБЬЕВ ЦИЛИНДРИЧЕСКИХ КОЛЕС
§ 28. Технические данные зубошевинговальных и зубохонинговальных станков
На зубошевинговальных и зубохонинговальных станках, основные технические данные которых приведены в табл. 59, производят отделку профиля зубьев цилиндрических колес до состояния, обеспечивающего работу зубчатого колеса в определенных условиях эксплуатации.
59. Технические данные зубошевинговальных и зубохонинговальных станков
Модель станка
Наибольшие размеры обрабатываемых зубчатых колес, ни
Он
я « и s: га ч
а I «Я га
к г. 3 и
о
га "
Частота вращения ведущего звена, об/мин
инструмента
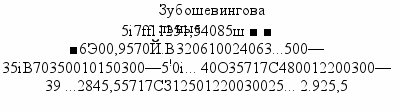

Зубошевингование повышает точность зубчатых колес по нормам плавности и контакта, а также уменьшает радиальное биение зубчатого венца.
Зубохонингованяе устраняет заусенцы и другие повреждения поверхности зубьев после термической обработки колеса, а также уменьшает шероховатость поверхности зубьев.
§ 27. Инструмент для шевингования и хонингования зубьев
Шевингование цилиндрических зубчатых колес производится цилиндрическим шевером. Шевер (рис. 52) представляет собой закаленное прямозубое или косозубое колесо с канавками на профиле зубьев, расположенными перпендикулярно оси шевера или направлению его зубьев. Косозубые шеверы изготовляют с правым или левым направлением зубьев и углами их наклона 5, 10 и 15Р. В большинстве случаев шеверы имеют простое число зубьев, чтобы при шевинговании числа зубьев шевера и колеса по возможности ие имели общих множителей. Шеверы изготовляют как стандартизованными (ГОСТ 8570—57), так и по отраслевым нормалям (МН 1801—61 и МН 18021—61.). В табл. 60 приведены размеры стандартизованных шеверов средних модулей.
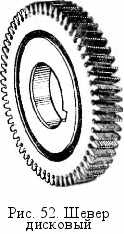
Стандартные шеверы изготовляют трех классов точности: А, В и С. При шевинговании зубчатых колес шевером класса А достигается 6-я степень, шеве-ром класса В — 7-я степень, а шевером класса С — 8-я степень точности по ГОСТ 1643—72.
Пример условного обозначения дискового шевера модуля 3 мм с числом зубьев z0 = 73, углом наклона (5а=15°, класса точности В: шевер т ЗХ73Х XI5° В ГОСТ 8570—57.
X о и и н г о в а н и е цилиндрических зубчатых колес производится дисковыми хонами. Хон представляет собой зубчатое колесо, выполненное из пластмассы, содержащей абразив. Применяют шесть типов хонов, отличающихся между собой по конструкции « составляющим элементам. Размеры дисковых хонов приведены в тэбл. 61.
Основным является хан типа I, состоящий из двух элементов — стальной ступицы <я пластмассово-абраэивной смеси на зубчатом венце.
Хоном типа II с резиновой прокладкой можно хонинговать зубчатые колеса «в распор» без амортизирующих устройств. Хон типа III используется при обработке зубчатых колес больших модулей. Хои типа IV с рессорами обладает повышенной упругостью в окружном направлении.
60. Шеверы дисковые для цилиндрических зубчатых колес (ГОСТ 8570—57)
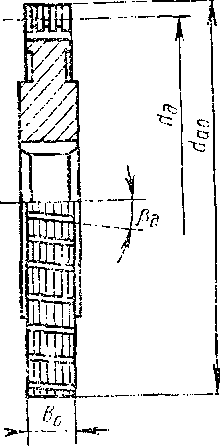
Модуль нормальный т , мм | SS си О, 4Z <Х S »s« й >н IS g О | Число зубьев шевера | Ширина шевера Ь0, мм | Модуль нормальный тп, мм | Номинальный делительный диаметр | й О, О СО Qi а м CJ л о (» о о | о *5 й О-0> и и а се X Эй |
I | 85 | 86 | 16 | 2 | 180 240 | 83 115 | 20 25 |
1,25 | 85 | 76 | |||||
2,25 | 180 240 | 73 103 | 20 25 | ||||
1,25 | 85 180 | 67 115 | |||||
20 | 2'5 | 180 240 | 67 91 | 20 25 | |||
1,375 | 85 180 | 62 115 | 16 20 | ||||
2,75 | 180 240 | 61 83 | 20 25 | ||||
1,5 | 85 180 | 58 115 | 16 20 | ||||
3 | 180 240 | 53 73 | 20 25 | ||||
1,75 | 180 | 100 | 20 | ||||
| | | |
Модуль нормальный m„ мм | Номинальный делительный диаметр дном* мм | Число зубьев шевера хо | Ширина шевера Ьь, | Модуль нормальный гп, мм | Номинальный делительный диаметр еном.мм | Число зубьев ше»ера z9 | Ширина шевера b0l мм |
3,25 | 180 240 | 53 67 | 20 25 | 5 1 | 180 240 | 31 43 | 20 25 |
3,5 | 180 240 | 47 61 | 20 25 | 5,5 | 180 240 | 29 41 | 20 25 |
3,75 | 180 240 | 43 61 | 20 25 | 6 | 180 240 | 27 37 | 20 |
4 | 180 240 | 41 53 | 20 25 | 6,5 | 240 | 35 | 25 |
4,25 | 180 240 | 37 53 | 20 25 | 7 | 240 | 31 | |
4,5 | 180 240 | 37 51 | 20 25 | 8 | 240 | 27 | 25 |
Хон типа V имеет абразивный веисц с внутренними зубьями. Xo;i типа VI состоит из тонкой металлической втулки, пластмассовой ступицы н пластмассо-во-абразивного венца.
Хон типа VII состоит из стального корпуса, безалмззного слоя и алмазоносных зубьев. Для обработки колес малых модулей такие зубья состоят из металлической связки с равномерно распределенными алмазами. Для обработки колес средних модулей алмазы распределены только в рабочем слое зубьев хо-на, а для обработки круономодульных колес на зубьях хопа прикреплены алмазоносные пластинки.
При выборе параметров хона необходимо учитывать следующее: для повышения производительности обработки применять хоны, обеспечивающие угол скрещивания осей 15... 20°. Для достижения высокого класса шероховатости поверхности зубьев следует применять хоны, обеспечивающие угол скрещивегния 10 ... 1-2°.
61. Основные характеристики и размеры дисковых хонов [10]
Размеры хона, мм
Тип хона
Эскиз
Боставляющие элементы
наружный диаметр
а' мм диаметр отверстия й, мм
К Ч V § <у £
а » к
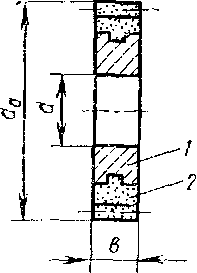
/ —сгаль 2 — пласт-маесово-абразивная смесь
I80...245 196; 190
63,5; 100
40 40 30
II
777/
£22
/ — сгаль
- —резина
- — абразивная смесь
245
90
40
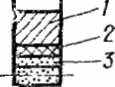
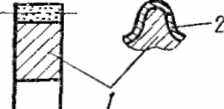
III
/ — сталь 2 — абразивная омесь
245
90; 100
40
1
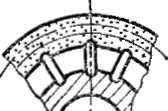
IV
2zZ
- ■— сгаль
- — рессора
- — абразивная смесь
245
90; 100
40
Размеры хона, мм
Тип хена
Эскиз
Составляющие элементы
наружный диаметр d , мм диаметр отверстия d, мм
V
- —сталь
- — абразивная смесь
220
40
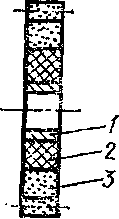
VI
- — стальная втулка
- — пластмасса
- — абразивная смесь
230
57
20
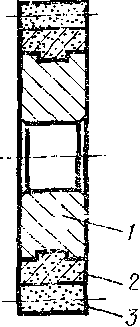
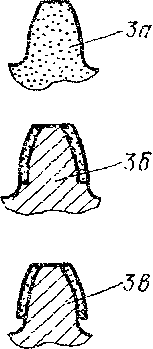
VII
/ —сгаль
- — безалмазный слой
- — алмазный слой За — алмазные зубья
3 6 — алмазный слой
3 в — алмазные пластины
221...235
100
20