Удк 621. 045/. 07: 669. 1
Вид материала | Документы |
- Удк 621. 316: 621. 311. 1 Экономика и организация производства, 95.87kb.
- Удк 669. 2/ 002. 68: 006. 354 , 1544.94kb.
- Гост 26824-86 , 244.75kb.
- Учебное пособие санкт-петербург 2 004 удк 669. 2/8; 669. 4 (075. 80) Ббк 34., 990.55kb.
- Удк 621. 787. 4, 81.3kb.
- Удк 621. 311, 94.08kb.
- Ббк. 34. 642 С 36 удк 621. 791., 3973.42kb.
- Удк 669. 168 Применение математического моделирования для решения задач сложного теплообмена, 185.45kb.
- Удк 621. 313 Молчанова светлана юрьевна, 209.19kb.
- Методические указания Волгоград 2010 удк 621. 91 Рецензент, 669.19kb.
УДК 621.045/.07:669.1/.8
Технология и оборудование для организации производства точных отливок из железоуглеродистых и цветных сплавов по газифицируемым моделям
О. И. Шинский, доктор техн. наук (ФТИМС НАН Украины)
В статье представлены новые направления развития литья по газифицируемым моделям, включая получение отливок под высоким регулируемым давлением в вакуумируемых, магнитных формах, контейнерные и роторные технологии, а так же оборудование и системы экологической защиты для их реализации. Указано, что применение перспективных технологий и оборудования литья по газифицируемым моделям позволяет по сравнению с литьем в песчаные формы снизить расход шихтовых, формовочных материалов и электроэнергии на 25-30%, 85-95% и 25-30% соответственно. При этом коэффициент использования металла, выход годного и потребительские свойства отливок возрастают до 0,97, 85-90% и в 1,2-1,7 раза соответственно. Созданные технологии и оборудование позволяют организовать предприятия, цеха и участки изготовления точных отливок из железоуглеродистых и цветных сплавов с объемом производства 100-10000 тонн/год.
Современное машиностроение значительно повысило требования к качеству литых заготовок, что заставило литейную промышленность начать реконструкцию своих производств на основе новых технологических процессов и оборудования. Для удовлетворения этих потребностей в литейной практике стали широко использовать разновидности литья по газифицируемым моделям (ЛГМ-процесс). Так, по данным фирмы “Vulcan” (США) в 1997 г. в мире произведено на основе ЛГМ-процесса 460 тыс. тонн. В реализации широкомасштабного освоения методов литья по газифицируемым моделям принимает участие Физико-технологический институт металлов и сплавов НАН Украины (ФТИМС), который уже на протяжении 25 лет на основе изучения особенностей газогидродинамики, тепломассопереноса и затвердевания различных сплавов при литье по газифицируемым моделям создает и осваивает в промышленности новые технологии ЛГМ-процесса и оборудование для их реализации. Во ФТИМСе созданы технологии литья в магнитные, песчаные и вакуумированные формы с заполнением их гравитационной заливкой нижним и верхним подводом металла, а так же под высоким регулируемым давлением [1-3].
Для реализации в практике созданных технологий литья по газифицируемым моделям разработаны методы выбора формовочных материалов, противопригарных покрытий, пенопластов и оптимизации их физико-механических свойств, расчета и оптимизации технологических параметров ЛГМ- и ГОМОДАР-процессов, которые существенно отличаются от известных аналогичных методик используемых в литейной практике литья в полые формы. Новые методики включают определение параметров предварительного вспенивания полистирола и изготовление из него моделей автоклавным способом и методом теплового удара, скорости подъема металла в форме и времени ее заполнения, а так же температуры заливаемого сплава, расчета геометрических параметров элементов литниково-питающих систем различных сплавов гравитационной заливкой с нижним и верхним подводом металла и под регулируемым давлением в магнитные, песчаные и вакуумированные формы. Используя созданные методы оптимизации параметров, а так же математические модели ЛГМ- и ГАМОДАР-процессов [4-6], во ФТИМСе разработали компьютерные программы для экспертных оценок выбранных основных технологических факторов и материалов, применение которых позволяет прогнозировать качество получаемых отливок по выходным данным, к которым относится скорость подъема металла в форме W1, противодавление Рф, зазор “металл-модель” δ и температура Т1 (рис. 1). Полученные значения позволяют откорректировать расчетные технологические параметры и физико-механические характеристики применяемых материалов в соответствии с комплексной методикой, блок-схема которой представлена на рис. 2.
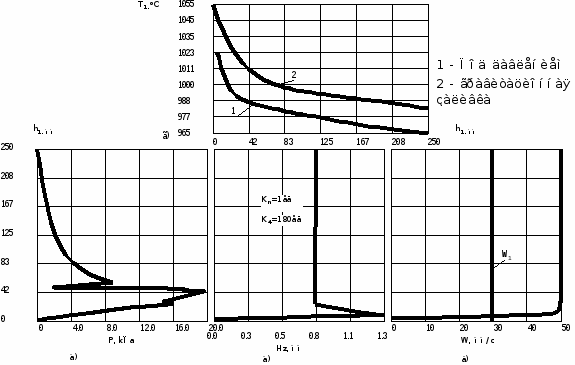
Рис. 1. Компьютерные данные кинетики изменения противодавления Рг, зазора “металл-модель” Hz, скорости подъема металла в форме W1 и температуры металла Т1 при литье бронзы по газифицируемым моделям в вакуумированные формы с начальным давлением 1,0 МПа
С целью расширения возможностей литья по газифицируемым моделям и для получения особосложных отливок переменного сечения, которые гравитационным методом литья получить затруднительно или невозможно [7-8], создан метод литья под регулируемым давлением, который имеет фирменное название ГОМОДАР – процесс [9-10]. Применение этого метода изменяет условия тепломассообмена в системе “форма-металл-модель” и газогидродинамику процесса, что позволяет в сравнении с ЛГМ-процессом увеличить скорость заполнения формы в 2-4 раза, а плотность модели до 50 кг/м2. Это дает возможность получать тонкостенные, сложные отливки, обеспечить повышение размерной точности и снижение шероховатости поверхности отливок, исключить образования пригара и даже отказаться от

применения противопригарных покрытий. К тому же позволило создать условия для повышения физико-механических свойств материала отливок и снижения их массы на 10-30%, увеличения выхода годного и коэффициента использования металла до 85-95% и 0,95-0,98 соответственно.
В целях повышения уровня экологической защиты биологических объектов и окружающей среды разработана принципиально новая контейнерная технология литья по газифицируемым моделям [11], суть которой заключается в следующем. Формовка блоков моделей (поз. 1., рис. 3) происходит путем совмещения контейнера 1 с ГМ 2 и блоком литниковых систем 3 со вспомогательным бункером 6, формовочным материалом (ФМ) 5 и последующим пересыпанием ФМ в контейнер 1, который подвергается вибрации. После виброуплотнения ФМ контейнер 1 и бункер 6 расстыковываются и на контейнер 1 устанавливается механизм вибропрессования 7 (поз. 2., рис. 3). После поворота контейнера 1 на 180° происходит заливка металла и выдавливание его с помощью механизма 7 (поз. 3, рис. 3). После заполнения формы металлом и его затвердевания происходит удаление механизма 7 (поз. 4., рис. 3) и стыковка вспомогательного бункера 6 частично заполненного ФМ с контейнером 1 (поз.5., рис. 3). После кантовки системы “контейнер-вспомагательный бункер” на 180° ФМ перемещается с помощью устройства 8. При последующем повороте контейнера 1 происходит удаление отливок 9 и цикл вновь возобновляется.
Для организации массового производства отливок с использованием высокого регулируемого давления впервые в литейной практике разработана роторная технология, а для ее реализации – первая роторно-конвейерная линия, производительность которой составляет Ж250/500 форм/час и позволяет получать отливки массой до 50 кг с габаритами 200х600 мм [12]. Эта линия превосходит по производительности существующие автоматические линии литья по газифицируемым моделям в 1,7-3 раза и даже высокопроизводительные комплексы типа “DISAMATIN+GF” в 1,5 раза.
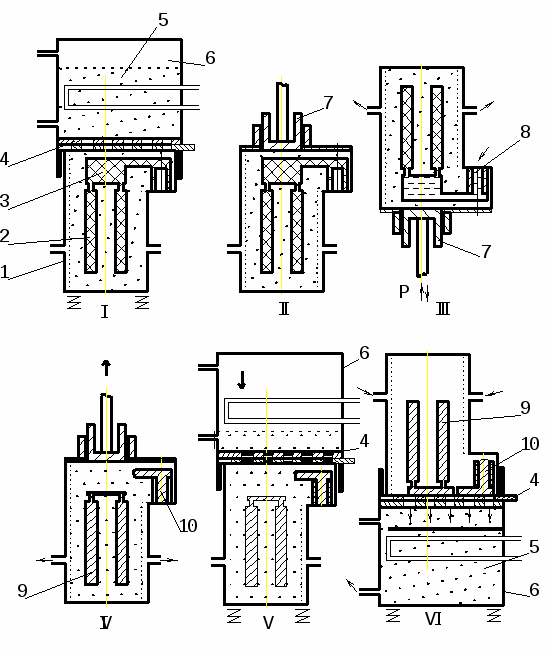
Рис. 3. Технологическая схема контейнерной технологии литья по газифицируемым моделям. 1 – контейнер; 2 – пенополистироловая модель; 3 – блок литниковой системы; 4 – жалюзи; 5 – формовочный материал; 6 – вспомогательный бункер; 7 – механизм выжимания; 8 – жидкий металл; 9 – отливка; 10 – литниковая система.
Кроме того для создания экологически чистых технологий литья по газифицированным моделям исследованы условия термодеструкции пенополистироловых моделей на всех стадиях технологического передела в температурном интервале 750-1650°С [13]. Это позволило определить количественный и качественный состав вредных выбросов и на этой основе разработать эффективные методы обезвреживания этих газов и регенерации формовочного материала. Созданные на этой основе системы термокаталитического обезвреживания газов и регенерации песка обеспечивают степень их очистки равную 0,98. Причем в атмосферу после обезвреживания выбрасываются пары воды и углекислого газа, концентрация которого в 8-10 ниже норм предельно-допустимых выбросов (ПДВ).
Для оценки преимуществ созданных методов литья определялись и технико-экономические показатели созданных цехов и участков производящих отливки по газифицируемым моделям из различных сплавов и широкой номенклатуры. Анализ этих показателей [14] при оценке экономической эффективности использования ЛГМ- и ГОМОДАР-процесса для получения отливок из серого и высокопрочного чугуна, углеродистой и легированной сталей, медных и алюминиевых сплавов в цехах и заводах производительностью 100-5000 тонн/год показал, что снижается расход формовочных и стержневых материалов на 85-95%, шихтовых материалов на 25-30%, электроэнергии на 25-30%, уменьшаются трудоемкость формовочных и финишных операций в 2-4 раза и на 70-80%, соответственно. К тому же применение этих технологий при реконструкции и строительстве новых производств позволяет сократить капитальные затраты и производственные площади в 2-4 раза. Особо следует отметить, что снижается и объем вредных выбросов в 8-10 раз в сравнении с производством литья в песчаные формы. Одновременно обеспечивается снижение массы литых заготовок на 15-30%, повышение их потребительских свойств в 1,2-1,7 раза, увеличение КИМ до 0,97, выхода годного на 10-15% при гравитационной заливке и на 20-30% при литье под давлением, что в целом ведет к снижению себестоимости литых заготовок на 10-30% по сравнению с литьем в песчаные формы в 1,5-2,0 раза в сравнении с литьем по выплавляемым моделям.
Таким образом, на основании многолетних исследований закономерностей получения отливок с применением различных методов литья по газифицируемым моделям разработаны перспективные технологические процессы получения отливок из железоуглеродистых и цветных сплавов массой от 0,1 до 10000 кг различной номенклатуры и серийности, а также оборудование для их реализации и системы экологической безопасности, которые позволяют создать эффективные производства точных отливок мощностью от 100 до 10000 тонн в год и обеспечить при этом качество литых заготовок соответствующих требованиям современного машиностроения
ЛИТЕРАТУРА
- Шуляк В.С., Шинский О.И., Анненко Л.П. Литье в магнитные формы.-К: Общество “Знание” Украинской ССР.-1979.-С.27.
- О.И. Шинский. Технология и оборудование для литья железоуглеродистых и цветных сплавов по газифицированным моделям под высоким регулируемым давлением. // Металл и литье Украины.-1997-№1.-С.25-28.
- Найдек В.Л., Шинский О.И. Новые литые материалы, специальные способы их получения и обработки. Доклады III Всесоюзного научно-технического съезда литейщиков. –М.;ВНИИ ТЭМП.;-1989.С.51-61.
- Особенности формирования и расчета противодавления в форме с газифицируемой моделью.//Процессы литья.-1993..№2.-С.117-123.
- О.И. Шинский, В.А. Залубко, М. Брынзеа. Особенности управления процессом заполнения формы металлом при литье по газифицированным моделям коленчатых валов легковых автомобилей // Процессы литья-1991.-С. 146-156.
- О.И. Шинский, В.А. Залубко. Газовый режим и особенности заполнения формы с газифицируемой моделью под низким и высоким давлением // Литье с применением давления.-К.:ИПЛАНУкраины.-1991.-С.146-156.
- О.И. Шинский, Н.И. Бех, В.А. Залубко и др. Особенности заполнения форм переменного сечения и ее газовые режимы при литье по газифицированным моделям. // Процессы литья, - 1995 - №1.-С 16-19.
- О.И. Шинский, Н.И. Бех, И.О. Шинский. Технологический процесс получения литых заготовок коленвалов автомобилей КАМАЗ по газифицированным моделям с кристаллизацией под давлением//Металлы и литье Украины, - 1994 - № 11-12,-С16-19.
- Патент РФ 2020040. Способ получения отливок по газифицированным моделям с кристаллизацией под давлением./О.И. Шинский, В.А. Ефимов, А.И. Валигура и др./Опубликовано Б.И-1993№18.
- Патент Украины № 1183. Спосіб виготовлення виливкі по моделям, що газифікуються з кристалізацією під тиском./О.Й. Шинський, В.О. Ефімов, А.І. Валігура та ін./Зареєстровано 30.06.1993р.
- Патент України № 1402. Установка для виготовлення та вибивки форм із сипучого матеріалу при литті по моделям, що газифікуються./О.Й. Шинський, В.О. Ефімов, О.Ю. Синчугов та ін./ Зареєстровано 16.08.1993р.
- Oleg I. Shinsky, Igor O.Shynsky “Theory and practice of Lost Foam Process (LFP)” из сборника докладов 62го Международного Конгресса литейщиков (МКТАЛ), США, Филадельфия, 19-23 апреля 1996г.-С.47-52.
- Ю.И. Хвастухин. Экологические аспекты литья по газифицированным моделям//Литейное производство.-1993,-№7.-С 17-19.
- В.С. Шуляк, О.И. Шинский, А.И. Валигура. Технологические и технико-экономические аспекты литья по газифицируемым моделям – К: РВЭНТП ЧССР, 1991-18С.
SUMMARY
O. I. Shinsky
Technology and equipment for organization of precise castings production from iron-ore and non-ferrous alloys on gasifiable models
The article gives new direction of casting development on gasifiable models including getting of castings under high controller pressure in vacuumed, magnetic forms, containered andd rotor technologies, as well as equipment anndd systems of ecological protection for their realization. It is shown that use of perspective technologies and equipment of cast on gasifiable models permits as compared with cast in sand molds to decrease expendiittures of charge, forming materials and electric energy on 25 – 30%, 85 – 95% and 25 – 30%. Also coefficient of use of metals, output of ready-made and consumption properties of castings increase till 0.97, 85 – 90% and in 1..2 – 1.7 times. Created technologies and equipment permit to organize the enterprises, shops and sections of manufacturing of precise castings from iron-ore and non-ferrous alloys with volum of production 100 – 1000 tonnes/year.