«Производство труб для новых проектов сухопутных и морских газопроводов и нефтепроводов»
Вид материала | Решение |
- Система нормативных документов в строительстве, 2095.91kb.
- Для исследования процесса, 27.84kb.
- Анализ постановки на производство на ОАО чмз профильных труб из сплавов циркония для, 76.85kb.
- Руководящий документ правила технической эксплуатации магистральных нефтепроводов, 2701.99kb.
- «анализ состояния конкуренции на рынке труб», 534.01kb.
- А. Б. Дитмар от птолемея до колумба москва · мысль · 1989, 3316.08kb.
- Справочник работ и профессий рабочих Выпуск 48 Разделы: "Общие профессии производств, 10592.39kb.
- Типовая технологическая карта (ттк) производство работ по монтажу систем внутренней, 479.71kb.
- Перечень важнейших инвестиционных проектов, предусмотренных к реализации в 2010 году, 1424.03kb.
- Общая экономико-географическая характеристика США, 48.74kb.
Решение Проблемного научно-технического совета Российского союза нефтегазостроителей по теме «Производство труб для новых проектов сухопутных и морских газопроводов и нефтепроводов».
20 октября 2010г. г.Москва
Системы магистральных трубопроводов нефти, газа и продуктов их переработки играют большую роль в обеспечении энергетической безопасности страны, в решении экономических, социальных и политических проблем в мире. И не случайно в годы мирового кризиса трубопроводы продолжали строиться по полной программе. Так в 2008 году нефтегазовые компании мира построили 24,5 тыс. км магистральных трубопроводов, израсходовав на это 61,5 млрд. долларов. В России в годы кризиса была построена нефтяная магистраль ВСТО, Сахалинские и другие трубопроводы.
В настоящее время началось сооружение гигантской Ямальской газотранспортной системы протяженностью 2400 км, по ней будет подаваться в центр страны и на экспорт 250 млрд. м3 газа. Строится первенец этой системы - 2-х ниточный газопровод Бованенково-Ухта длиной тысячу километров, диаметром 1420 мм, с высоким внутренним давлением - 11,8 МПа.
Началось строительство двухниточного газопровода в Балтийском море Выброг-Грайфсвальд (Германия) длиной 1224 км диаметром 1200 мм с рабочим давлением 220 атм. Его стоимость 7,4 млрд. евро.
Для подачи газа в Северный поток будет построен сухопутный газопровод Грязовец-Выборг длиной 917 км диаметром 1420 мм, внутреннее давление 100 атм.
На очереди газопроводы Сахалин–Хабаровск-Владивосток, Мурманск-Волхов, нефтепроводы системы ВСТО-2, БТС-2, Южный поток через Чёрное море в Болгарию на глубине до 2км протяжённостью 900 км. Начать строительство намечено в 2015г., Производительность системы 63 млрд. м3, стоимость 8,6 млрд. евро.
И сухопутные трубопроводные системы стоят очень дорого. В США в 2009г. стоимость прокладки 1 км сухопутных трубопроводов составляла 2,3 млн. долларов, 1 км морских трубопроводов – 5,37 млн. долларов. В стоимости трубопроводных проектов добрую половину составляет затраты на основной конструкционный материал – трубы.
В бытность Миннефтегазстроя на нефтегазовых стройках перерабатывалось до 5,5 млн. тонн труб, из них до 3 млн. тонн закупались за рубежом. Трубы были вечным дефицитом. Теперь конъюнктура на трубном рынке коренным образом поменялась. В последние десятилетия трубная промышленность России сделала технический, технологический рывок, ввела новые мощности по прокату трубных сталей, в том числе и нового класса прочности, новые трубные станы для изготовления труб большого диаметра на Выксе, в Волгограде, Челябинске и Ижевске, обеспечив импортозамещение.
В мировом производстве труб Россия занимает устойчивое третье место (рис.1).
Рисунок 1. Ведущие Мировые производители трубной продукции в мире
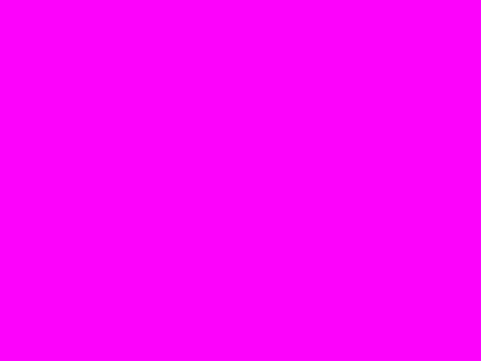
Среди ведущих мировых производителей стальных труб наши трубные компании занимают достойное место (рис.2).
Опираясь на утверждённую Правительством РФ Стратегию развития нефтегазового комплекса до 2020г. российские трубные компании разработали и успешно реализуют комплексные программы обновления производственных мощностей.
За период 2002 – 2010 гг. затраты на обновление основных фондов уже составили около 10 млрд. долларов США собственных и заемных средств.
Удельные инвестиции в трубной отрасли являются одними из самых высоких в реальном секторе экономики и составляют 200 долларов на одну тонну готовой продукции. На рис.3 показано увеличение добавленной стоимости в ходе повышения глубины переработки продукции.
Рисунок 2. Ведущие мировые производители стальных труб в 2007г., млн. тонн (отгрузка)
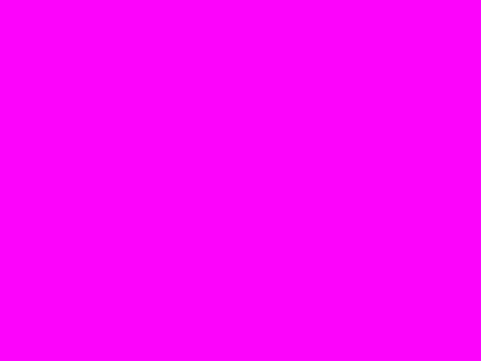
Суммарные мощности российских трубных заводов по производству труб большого диаметра (ТБД) в 2010 году составят 5 млн. тонн, в том числе одношовных ТБД – 2,7 млн. тонн в год.
Рисунок 3. Увеличение добавленной стоимости в ходе повышения глубины переработки продукции
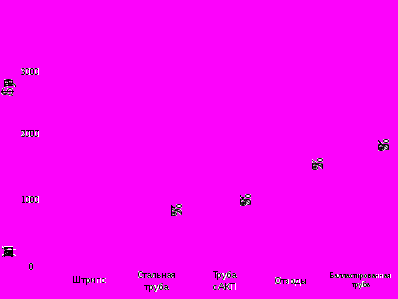
Основная техническая политика в области труб для магистральных трубопроводов – создание мощностей по выпуску штрипсов нужной характеристики, в том числе из сталей высокой прочности, изготовление стальных труб, отвечающих международным стандартам, по новейшим технологиям с антикоррозионным и внутренним гладкостным покрытием, изготовление комплектующих трубных деталей и налаживание производства балластированных труб. Конечно, перечисленное – это только фрагмент большой технической программы, осуществляемой на металлургических и трубных предприятиях.
Вопросы технической политики и производства трубной продукции подробно осветил на заседании НТС директор НК «ФРТП» А.Д.Дейнеко в докладе «Трубная промышленность России – пример успешной модернизации отрасли». Приводим отдельные выдержки из доклада:
Некоммерческая организация «Фонд Развития Трубной Промышленности» является объединением основных производителей труб на территории Российской Федерации. Эти компании организовали фонд в 1999г. Участниками Некоммерческой организации «Фонд Развития Трубной Промышленности» являются: ОАО «Трубная Металлургическая Компания» (ОАО «Волжский трубный завод», ОАО «Северский трубный завод», «Синарский трубный завод», ОАО «Тагмет»), ЗАО «Группа ЧТПЗ» (ОАО «Первоуральский новотрубный завод», ОАО «Челябинский трубопрокатный завод»), ЗАО «Объединённая Металлургическая Компания» (ОАО «Альметьевский трубный завод», «Выксунский металлургический завод») и ОАО «Ижорский трубный завод».
Доля трубных компаний – участников НО «ФРТП» на российском внутреннем рынке традиционно составляет 65-70 процентов. Что касается наших крупнейших компаний, после консолидации активов ОАО «ТМК» занимает устойчивое 2-е место в мире.
В рамках программы по перевооружению основных производственных фондов за период 2005 – 2009 гг. было организовано производство одношовных труб большого диаметра:
- Волжский трубный завод. В 2008 году завершена работа по расширению производства ТБД и выпуску до 650 тыс. тонн в год одношовных газопроводных труб диаметром 508-1420 мм с толщиной стенки до 42 мм, из штрипса прочностью до X100, с наружным и внутренним покрытием. Промышленное производство одношовных ТБД начато в декабре 2008 года.
- Выксунский металлургический завод. В апреле 2005 г. запущена новая линия по производству более 450 тыс. тонн в год труб большого диаметра с характеристиками, превышающими импортные аналоги. В 2008 году мощности по производству одношовных труб (диаметром до 1420 мм, толщиной стенки до 48 мм длиной трубы до 12 м, рассчитанных на давление до 250 атм., с использованием штрипса категории прочности до X100) расширены до 950 тыс. тонн в год.
- Ижорский трубный завод. Пуск стана осуществлен в 2006 году. Мощность цеха до 600 тыс. тонн одношовных труб диаметром до 1420мм для нужд нефтяной и газовой промышленности.
На этих заводах также организованы участки нанесения наружного антикоррозионного трехслойного полимерного и внутреннего гладкостного покрытий.
23 июля 2010 года осуществлён пуск нового трубоэлектросварочного цеха «Высота 239» по производству труб большого диаметра на ОАО «ЧТПЗ» мощностью 600 тыс. тонн. Это уникальное производство, равного которому нет нигде в мире. Оно уникально по технологии, оснащённости и гибкости, по условиям труда.
В этом же году ожидается пуск электросталеплавильного комплекса на ОАО «ПНТЗ» мощностью до 900 тыс. тонн трубной заготовки. Мартены уходят в прошлое, что обеспечивает экономию электроэнергии, улучшает экологию, условия труда и повышает качество. Кроме того, на «Трубодеталь» вводится новый цех по производству тройников. Ожидается ввод новой линии отделки обсадных труб на ОАО «ВМЗ» суммарной мощностью до 900 тыс. тонн. Таким образом, мощности по прокату, по сварке и по отделке теперь будут сопряжены.
Кризис отразился на инвестировании, поэтому будут вводится новые мощности и в 2011, 2012 и 2013 году.
-2011г. – планируется пуск стана 5000 на ОАО «ВМЗ» мощностью 1,2 млн. тонн широколистового горячекатаного проката;
-2012г. – пуск новых станов непрерывной горячей прокатки труб на ОАО «СТЗ» и ОАО «ЧТПЗ», пуск электросталеплавильного комплекса на ОАО «Тагмет» мощностью до 900 тыс. тонн трубной заготовки.
-2013г. – пуск комплекса финишной обработки промысловых труб на ОАО «СТЗ».
По мнению НО «ФРТП», намеченная программа обеспечит перспективные потребности в трубах до 2020г. для традиционных регионов добычи нефти и газа, нефтегазотранспортных магистралей, даже с учётом новых проектов, подобных Северному и Южному потоку, Штокману, трубопроводу Сахалин-Хабаровск-Владивосток.
Сегодня есть четыре площадки, которые производят трубы большого диаметра с разными технологиями формовки: спиральная, валковая, шаговая (рис.4). Для потребителя это очень важно: разные технологии и производители, принадлежащие разным акционерам, предоставляют широкий выбор. Это четыре группы компаний, которые конкурируют между собой на российском рынке, что выгодно для ОАО «Транснефть», ОАО «Газпром» и другим компаниям, которые закупают трубы большого диаметра.
Рисунок 4. Производственный потенциал российских производителей сварных ТБД
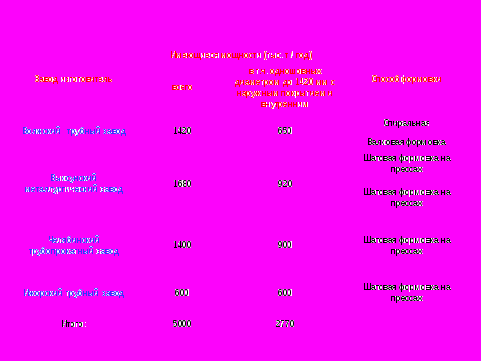
Все трубы большого диаметра российских производителей соответствуют международным стандартам (рис.5). Вся продукция ОАО «ВТЗ», ОАО «ВМЗ» и ОАО «ИТЗ» проходит аттестацию.
Рисунок 5. Международные стандарты, по которым аттестованы ТБД российских трубных заводов
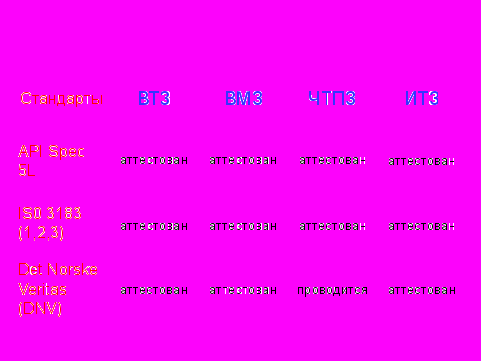
Примеры поставки российских труб большого диаметра для сооружения подводных трубопроводов:
- Укладка подводной части Nord Stream. Использована труба Выксунского металлургического завода диаметром 1220 мм с толщиной стенки более 30 мм, обетонированная на Московском трубозаготовительным комбинатом. Устройство для подачи труб – норвежское, баржа – отечественная.
- Подводный переход через Байдарацкую губу магистрального газопровода «Бованенково-Ухта» диаметром 1220 мм, толщина стенки 27мм. Укладка осуществляется начиная с лета 2006г. Проблем с трубами не возникало.
- Варандейский нефтеналивной терминал – труба 820 мм, толщина стенки – 20,5 мм.
Что касается поставки труб для строительства трубопровода Nord Stream, то на первую нитку российские заводы поставят 280 тыс. тонн из 1,2 млн. тонн, то есть 25%. Единственным поставщиком, который соответствовал требованиям Nord Stream – Выксунский металлургический завод.
Доля ОАО «Газпром» в проекте Nord Streamсоставляет 51%. Отечественные мощности вполне позволяют поставить вообще весь объём на проект. К сожалению, Nord Stream AG пригласил японских производителей для поставки на проект 100 тыс. тонн труб. Российские трубники такое решение считают неверным. Если крупные международные проекты реализуются с российским участием, то доля поставщиков (это не только труб касается, но и других поставщиков оборудования и комплектующих) должна быть пропорциональна доле в акционерном капитале.
Этот принципиальный подход поддержало Правительство РФ. Вышла директива для ОАО «Газпром», которую он принял: в следующем проекте доля будет пропорциональна участию. Доля акционерного участия ОАО «Газпром» в Штокмне - 51%, следовательно, на 51% поставки труб может претендовать Россия. За него будут бороться четыре независимых производителя труб большого диаметра, и никакого сговора монополистов быть не может.
Трубы нефтегазового сортамента производятся на многих заводах. Традиционные производители: Волжский, Северский, Синарский, Таганрогский, Первоуральский и Челябинский. Новые предприятия – Шекснинский, Волгореченский – работают несколько лет, Выксунский, Уралтрубопром – расширили и обновили мощности (рис.6). Суммарная мощность - 5 850 тыс. тонн более чем достаточна для российских потребителей. Есть трубы с термообработкой – 2 700 тыс. тонн, трубы всех повышенных групп прочности, всех премиум классов, всю нарезку, с приварными замками.
Рисунок 6. Производители труб нефтегазового сортамента в России
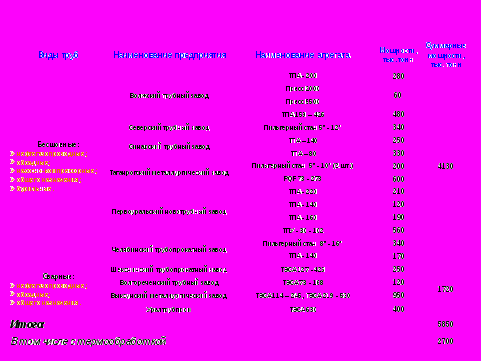
На заседании Проблемного научно-технического совета был заслушан доклад начальника научно-технического управления ООО «ЧТПЗ-Инжиниринг» к.т.н. С.В.Перевезенцева «Техническая политика в трубном производстве ОАО «ЧТПЗ».
В настоящее время ОАО «ЧТПЗ» – это вертикально интегрированная компания (рис.7), которая объединяет предприятия трубного производства, представленные Челябинским трубопрокатным и Первоуральским новотрубным заводами, и нефтесервисное направление – представленное компанией «Римера».
В целях обеспечения системного подхода при формировании и реализации стратегических и операционных программ модернизации производств ОАО «ЧТПЗ» в 2010 году создана Инжиниринговая компания «ЧТПЗ-инжиниринг».
Рисунок 7. Структура ОАО «ЧТПЗ»
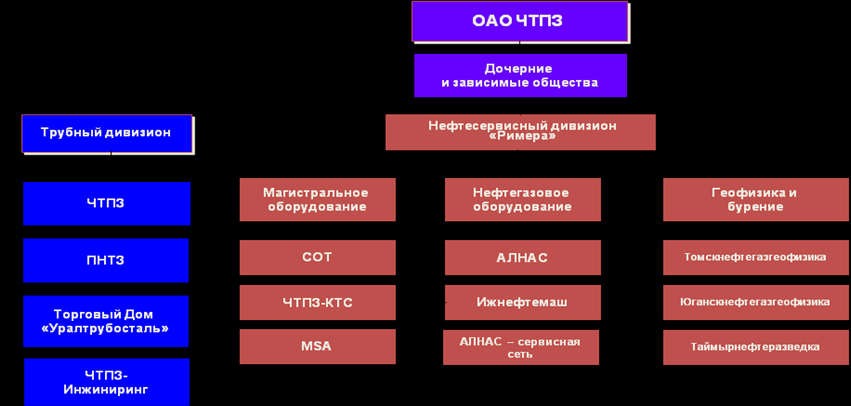
Важнейшими стратегическими задачами Инжинирингового центра являются (рис.8): повышение эффективности и сокращения сроков реализации программ модернизации и инновационного развития производственных предприятий ОАО «ЧТПЗ», разработка требований к трубам, основанных на изучении запросов потребителей, реально достигнутого уровня технологии производства труб и направлений развития трубопроводного транспорта.
Основным вектором, определяющим стратегию научно-технического направления деятельности Инжинирингового Центра, является работа, связанная с повышением работоспособности и долговечности производимой ОАО «ЧТПЗ» продукции при различных, в том числе экстремальных, условиях ее эксплуатации. Поэтому большое внимание в ближайшие годы будет уделяться вопросам повышения механических свойств металла и эксплуатационных характеристик труб, в том числе в рамках научно-технического сотрудничества с основными Заказчиками – ОАО «Газпром» и ОАО «АК «Транснефть», при одновременном снижении металлоемкости продукции. Особое место занимает работа над системой гарантированного обеспечения долговечности и работоспособности труб при заданных условиях эксплуатации.
Рисунок 8. «ЧТПЗ-Инжиниринг» – системообразующий технический центр подготовки и реализации решений по повышению эффективности использования и развития производственных активов предприятий ОАО «ЧТПЗ»
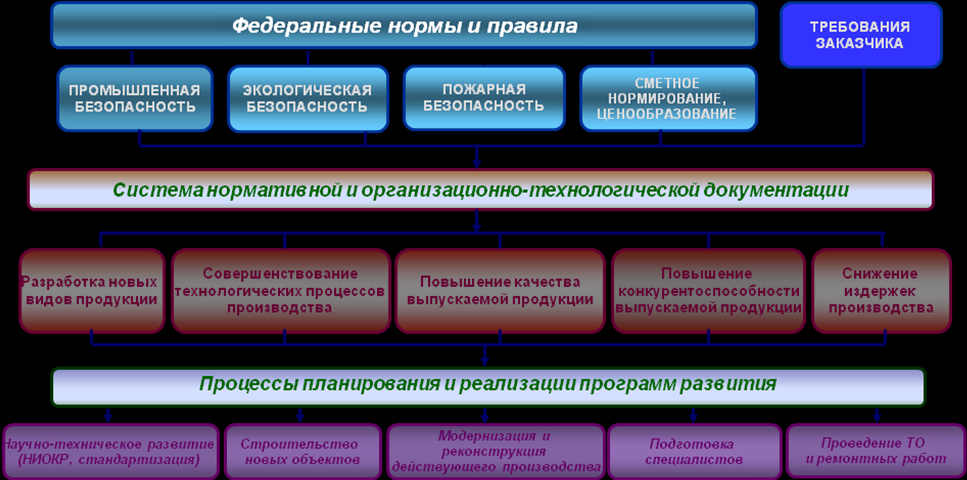
В соответствии с Программой модернизации производства сварных труб большого диаметра для строительства магистральных нефтегазопроводов с июля 2010 г. ОАО «ЧТПЗ» приступил к изготовлению продукции в новом трубоэлектросварочном цехе «Высота 239» по производству одношовных труб большого диаметра. Общий объем капитальных вложений в строительство нового цеха составил более 21 млрд. рублей, производственная мощность – 600 тыс. тонн в год.
Ввод в эксплуатацию ТЭСЦ «Высота 239» позволил увеличить мощности ОАО «ЧТПЗ» по выпуску труб большого диаметра различного конструктивного исполнения до 1,34 млн. тонн в год.
В новом цехе имеется возможность выпускать трубы в хладостойком исполнении и трубы с повышенными эксплуатационными характеристиками из высокопрочных сталей для строительства магистральных трубопроводов в любых климатических зонах, включая Крайний Север и акваторию морей.
Принятая технология производства предусматривает возможность изготовления труб с наружным и внутренним гладкостным покрытием.
Основные характеристики труб, выпускаемых в ТЭСЦ «Высота 239»:
диаметр труб, мм 508-1420;
толщина стенки, мм 6,4-48,0;
длина труб, м 12 и 18;
группа прочности, max К80 (Х100).
Рисунок 9.Сортамент выпускаемой продукции
Диаметр 508-1420 мм | Толщина стенки 6-45 мм | Длина готовой трубы от 10,6-18,2 м |

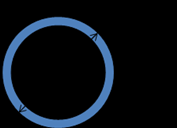
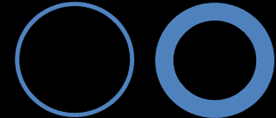



Класс прочности К52-К80 (Х60-Х100) |
Выпускаемые трубы по своим характеристикам соответствуют требованиям ОАО «Газпром», ОАО «АК «Транснефть», АРI, DNV, ГОСТ.
Изготовление и поставку основного современного технологического оборудования трубосварочного отделения осуществляла комплектно фирма SMS MEER (Германия).
В ТЭСЦ «Высота 239» приняты следующие новые современные
технические и технологические решения, направленные на повышение качества производимой продукции:
а) предусмотрены 2 линии формовки труб, на длину трубы 12 и 18 метров;
б) обеспечена повышенная точность по геометрическим параметрам труб относительно требований потребителей за счет:
– новой конструкции пресса подгибки кромок (повышение точности сборки под сварку);
– контроля геометрических параметров на каждом этапе производства (автоматические установки лазерного измерения);
– математического моделирования процессов формоизменения и геометрии инструмента для обеспечения повышенной точности труб по диаметру;
– дробеметной очистки поверхности листа (исключение образования дефектов в процессе формовки штрипса);
– экспандирования по всему телу трубы.
в) повышены технические характеристики сварного соединения относительно требований потребителей за счет:
– применения новых сварочных материалов и работы на оптимальных режимах сварки, предварительно отработанных на специализированном сварочном стане;
– специальной подготовки поверхности под сварку (гарантированная чистота поверхности при сварке);
– обеспечения собственного производства новых марок керамического флюса европейского уровня.
г) применен повышенный уровень автоматизированного контроля с целью исключения производства и отгрузки труб с дефектами потребителям (с протоколированием результатов контроля):
– 100%-ный ультразвуковой контроль листа перед задачей в производственную линию (исключение задачи штрипса с дефектами);
– ультразвуковой контроль трубы по всей поверхности, перед окончательной приемкой (исключение поставки труб с дефектами потребителям);
– применение рентгеновского контроля концов сварного шва, а также дополнительного рентгеновского контроля шва по всей длине в случае необходимости.
д) минимизировано влияние человеческого фактора вследствие:
– высокого уровня автоматизации производственного процесса, в том числе формовки и сварки труб;
– применения робототехники при выполнении сварочных операций;
– автоматизации контрольных операций;
– формирования электронного паспорта трубы содержащего всю информацию о параметрах производства.
Применение всех указанных решений сформировало идеологию «белой металлургии» на ОАО «ЧТПЗ»: в новом цехе присутствуют только операторы производственных процессов, в действительности находящиеся на своем рабочем месте в белых халатах.
Трубы, изготовленные в ТЭСЦ «Высота 239», характеризуются стабильно высокими прочностными и вязкопластическими свойствами основного металла и сварного соединения; улучшенной геометрией, достигаемой на комплексе современных прессов формовки труб; увеличенной до 18 метров длиной трубы; наличием внутреннего гладкостного покрытия. Сочетание данных параметров для электросварных труб большого диаметра является уникальным не только для российских, но и для зарубежных производителей.
ОАО «ЧТПЗ» участвует в разработке технических регламентов и работ по национальной стандартизации в области магистрального трубопроводного транспорта, является членом Технических комитетов по стандартизации (ТК 357 «Стальные и чугунные трубы и баллоны», ТК 23 «Техника и технология добычи и переработки нефти и газа»).
По заказу ОАО «ЧТПЗ» ведущими научными организациями в области трубопроводного транспорта: ОАО НПО «ЦНИИТМАШ», ИМАШ РАН, ФГУП НПО «ЦНИИчермет», ИМЕТ РАН, ЗАО НПО «Спецнефтегаз» подготовлены проекты двух национальных стандартов:
1.ГОСТ Р «Магистральные трубопроводы. Нормы проектирования».
2.ГОСТ Р «Трубопроводы магистральные. Общие технические требования на трубы».
В подготовленных национальных стандартах помимо ужесточения известных ранее действующих количественных показателей введены и новые показатели, регламентирующие качество изготавливаемых труб. Выполненные при разработке стандартов экспериментальные исследования и теоретические расчеты позволили обосновать соответствующие коэффициенты запаса (коэффициент надёжности по материалу), что позволяет при сохранении показателей по безопасности и надежности сократить металлоемкость объектов.
Необходимость разработки двух гармонизированных между собой национальных стандартов позволит обеспечить организационно-техническую совместимость всех этапов создания и технического перевооружения нефтегазопроводов: проектирование, изготовление труб, строительство и эксплуатация.
Очевидно, что создание системы технических требований к продукции, методов проведения испытаний, подтверждения соответствия и расчетных обоснований в форме национальных стандартов является инструментом планомерного воздействия и стимулирования развития промышленности и создания антидискриминационной среды в области принятия решений по выбору поставщиков.
Выступавший с заключением в конце заседания Заместитель председателя Проблемного совета д.т.н. проф. О.М.Иванцов отметил:
Безопасность трубопроводного транспорта во многом зависит от качества реализации проектных решений, нормативных условий при выполнении работ в процессе строительства трубопроводов. Технические требования к трубам, как совокупность обобщённых характеристик металла труб, заводских сварных соединений, а также геометрических параметров изделия, должны гарантировать требуемую по условиям эксплуатации несущую способность трубопровода после проведения всех технологических сварочно-монтажных операций, перевозки труб и плетей, холодной и горячей гибки, других деформаций в процессе строительства.
В последнее время влияние строительной науки на формирование трубной продукции практически полностью отсутствует.
Нефтегазостроители в прежние годы вместе с металлургами, заказчиками участвовали в формировании технической трубной политики, подписывали технические условия на поставку труб, участвовали в изучении трубной продукции и формировании требований к трубам. Во ВНИИСТе работали исследовательские лаборатории и единственная в России бронекамера для испытания труб и трубных секций с доведением до разрушения при заданных температурных режимах. ВНИИгаз продолжает подобные исследования на своём полигоне по испытанию плетей труб разных заводов класса прочности Х70 и Х80 для газопровода Бованенково-Ухта.
А в нефтегазостроительной отрасли наука о трубах, к глубокому сожалению, угасает. А строителей интересует, конечно, не только свариваемость, углеродный эквивалент, выбор сварочных технологий и геометрические, весовые параметры труб. При выполнении строительно-монтажных работ трубы проходят даже более жёсткие испытания, чем при эксплуатации. Внутреннее статическое давление при испытаниях перед сдачей в эксплуатацию, существенно выше рабочего давления трубопровода. Трубы при строительстве проходят жёсткие испытания на деформационную прочность начиная с погрузки, разгрузки и перевозки трубных секций, при укладке плетей в траншеи на суше, укладке протаскиванием или свободным погружением на водных переходах, протаскиванием в скважины при наклонно-направленном бурении, при прокладке морских трубопроводов со стингеров или методом j, а также при холодном и горячем гнутье, в процессе изготовления трубных деталей. Строителей интересует трещиностойкость и коррозионная стойкость труб, реакция на термообработку стыков. Строителей интересует всё, что определяет качество и безопасность трубной продукции. Поэтому мы и проводим настоящее заседание совета.
Статистика по магистральным газопроводам показывает, что из обнаруженных в 2008 году 2250 дефектов 20% связано со строительством, 13% - с заводскими дефектами труб. Всё конечно перекрывают эксплуатационные дефекты, 36% - только со стресс-коррозией. Ещё многие-многие задачи нужно решить владельцам трубопроводов, строителям и трубникам для обеспечения безопасности и надёжности трубопроводного транспорта.
В заключение следует отметить, что научно-технический Совет нефтегазостроителей получил развёрнутую, интересную информацию о возможностях современной трубной промышленности России для выполнения сложных трубопроводных проектов.
Необходимо активное участие нефтегазостроителей в формировании технической трубной политики, в разработке нормативной базы и возобновлении прикладной науки о трубах в строительной отрасли».
Заслушав и обсудив представленные на сессию Проблемного научно-технического совета доклад директора Некоммерческой организации «Фонд Развития Трубной Промышленности» А.Д.Дейнеко «Трубная промышленность России – пример успешной модернизации отрасли», доклад начальника научно-технического управления ООО «ЧТПЗ-Инжиниринг» к.т.н. С.В.Перевезенцева «Техническая политика в трубном производстве ОАО «ЧТПЗ», выступления Президента «НГБ-Энергодиагностика» В.А.Надеина, Генерального директора СРО «Нефтегазстрой» д.т.н., проф. В.П.Курамина, Зам. председателя Проблемного научно-технического совета РОССНГС д.т.н, проф. О.М.Иванцова, Проблемный научно-технический совет РОССНГС принял решение:
1.Отметить, что после застоя в развитии трубопроводного транспорта 90-х годов наступил новый этап сооружения сухопутных и морских трубопроводных систем, реализации уникальных трубопроводных проектов: нефтепроводные системы ВСТО-1, ВСТО-2, БТС-2 и др., газопроводные системы Ямал-Европа, Сахалин-Хабаровск-Владивосток, Грязовец-Выборг, Мурманск-Волхов, Выборг-Грайфсвальд по Балтийскому морю, Южный поток и другие.
Стратегия развития нефтегазового комплекса на период до 2020г. предусматривает огромную программу строительства магистральных трубопроводов для транспортировки нефти, газа и продуктов их переработки.
На рисунках 10 и 11 показаны доли, объёмы, конечные потребители нефти и газа, доля экспорта. Это официально утверждённая стратегия. Схемы, изображённые на рисунках, предоставлены Минпромторгом.
2.Отметить, что российские трубные компании, опираясь на Стратегию развития нефтегазового комплекса успешно реализуют свои комплексные программы обновления производственных мощностей, рассчитанных на период 2002-2012 гг.
За этот период затраты на обновление основных фондов уже составили около $10 млрд. собственных и заёмных средств. Удельные инвестиции в трубной отрасли являются одними из самых высоких в реальном секторе экономики и составляют $200 за одну тонну готовой продукции.
Рисунок 10
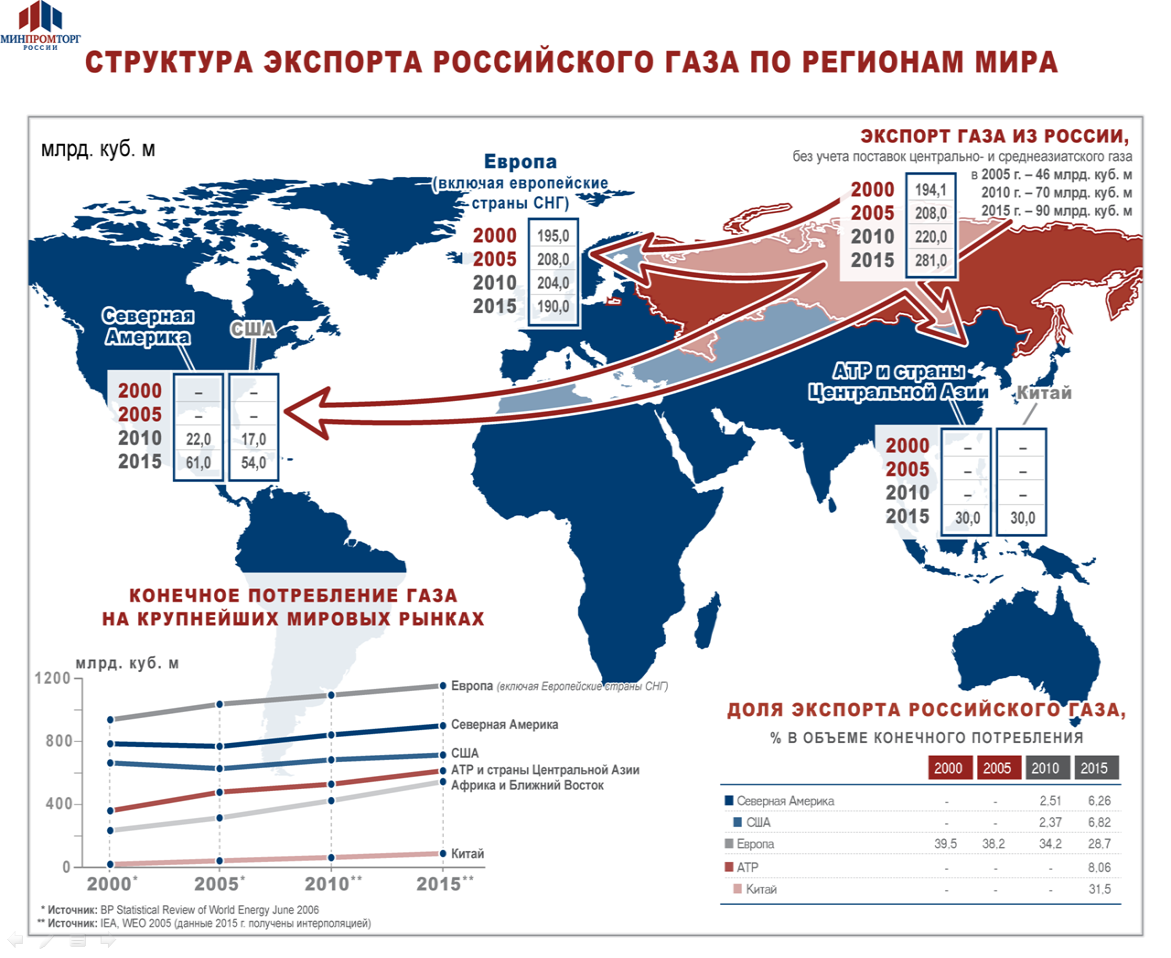
Рисунок 11
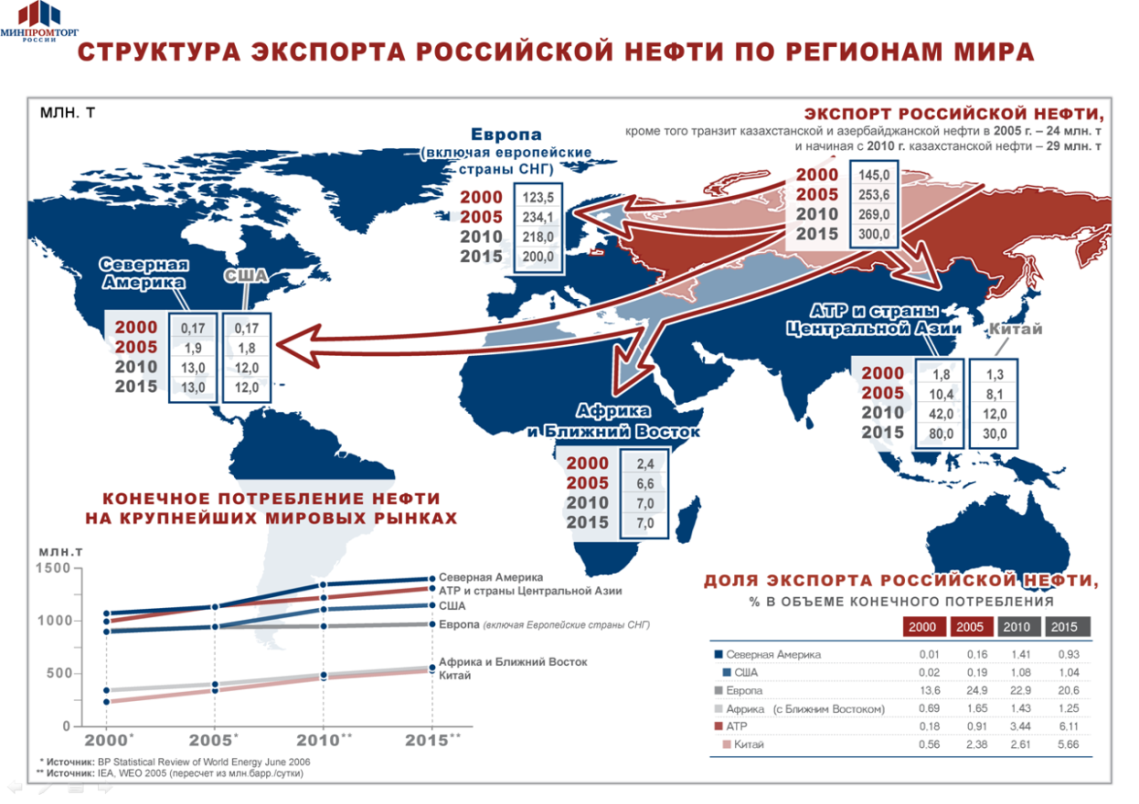
На рисунке 12 показан рост мощности выпуска труб, в том числе сварных и бесшовных. Производство труб большого диаметра планируется довести даже выше указанного до 5,7-6,00 млн. тонн, в том числе 3млн. тонн одношовных для подводных частей будущих трубопроводов.
Рисунок 12. Расширение мощностей трубного производства ведущих производителей в период 2004-2012гг.
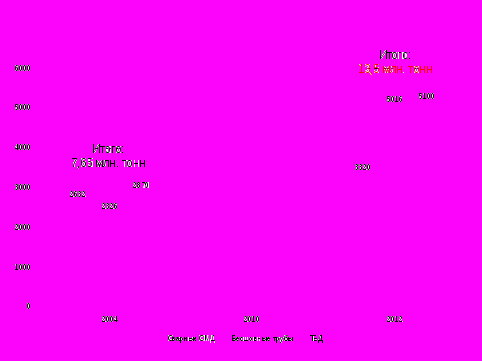
Суммарные мощности российских трубных предприятий по производству ТБД в 2010 году составят 5 млн. тонн, в том числе одношовных ТБД – 2,7 млн. тонн в год. В мировом производстве труб Россия занимает устойчивое третье место.
3.Трубная промышленность России – пример успешной модернизации отрасли (рис.13).
Рисунок 13
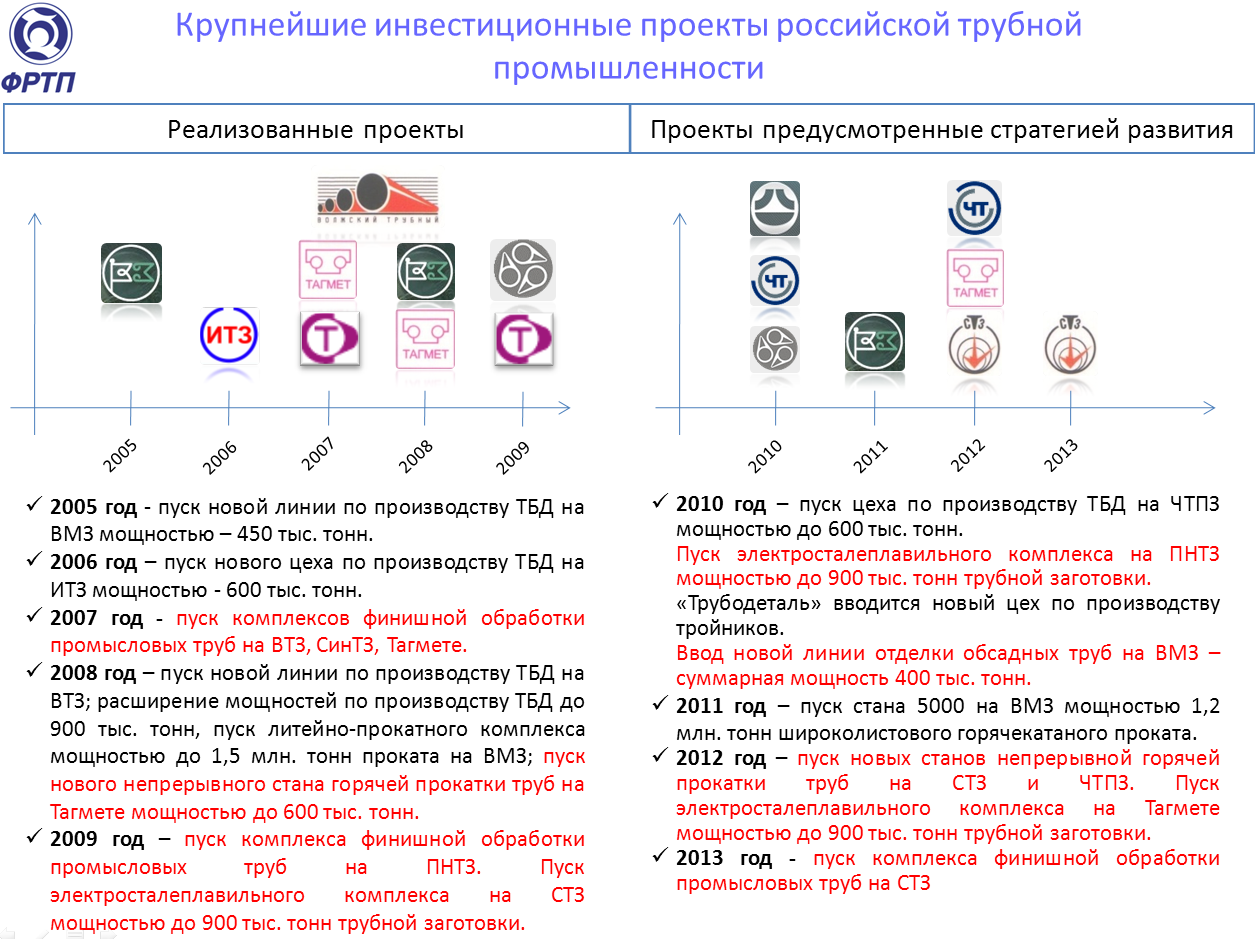
В соответствии с программой модернизации производства труб большого диаметра с июля 2010 года ОАО «ЧТПЗ» ввёл в производство новый трубосварочный цех «Высота 239» по производству одношовных труб большого диаметра. Ввод нового стана позволил увеличить производство труб большого диаметра различного конструктивного исполнения до 1,34 млн. тонн в год. Трубы выпускаются с повышенными эксплуатационными характеристиками из высокопрочных сталей для строительства на Крайнем Севере и акваториях морей:
диаметр труб, мм 508-1420;
толщина стенки, мм 6,4-48,0;
длина труб, м 12 и 18;
группа прочности, max К80 (Х100).
В ТСЦ «Высота 239» приняты все самые совершенные современные технологии, сформирована идеология «белой металлургии». В цехе фигурируют только операторы, одетые на своём рабочем месте в белые халаты.
4.Трубы большого диаметра, производимые на российских заводах, не уступают своим зарубежным аналогам, а зачастую и превосходят их (рис.14).
Рисунок 14
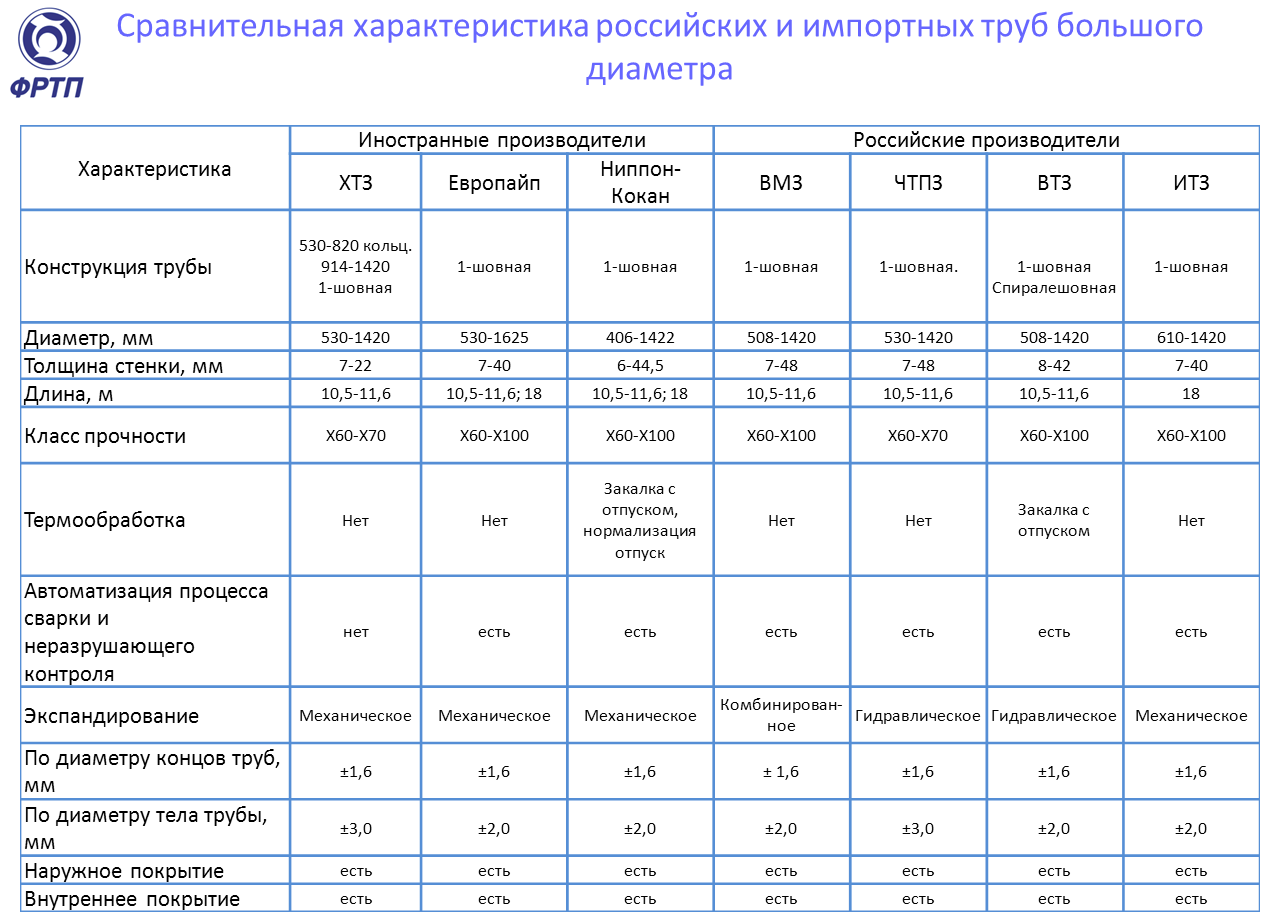
Одношовные трубы большого диаметра, производимые на ВМЗ, ИТЗ, ВТЗ аттестованы на соответствие всем ведущим мировым стандартам, в том числе стандарту DNV. На Челябинском трубопрокатном заводе уже ведется работа по аттестации производства одношовных ТБД в новом цехе «Высота 239».
5.Сформирована основная стратегия в производстве труб большого диаметра: от штрипсов к обетонированной трубе, защищённой от коррозии, плюс отводы, т.е. вверх по цепочке добавленной стоимости. Сегодня стальная труба, особенно труба большого диаметра - 100% покрывается в заводских условиях трёхслойным антикоррозионным, гладкостным внутренним покрытием. У всех трубных компаний появились активы по изготовлению отводов, тройников, переходников и т.д. Кроме того, появилась и российское производство балластированной трубы. Её изготавливает Московский трубозаготовительный комбинат. Трубы превращаются в строительную конструкцию.
6.Изучение динамики ёмкости российского трубного рынка показывает большую неравномерность спроса по годам. Об этом в частности свидетельствуют диаграммы по трубам большого диаметра (рис.15 и рис.16).
Рисунок 15. Прогноз ёмкости российского рынка труб большого диаметра
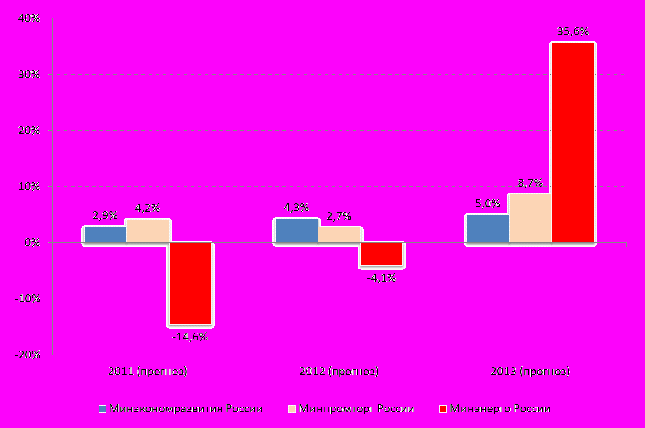
Р
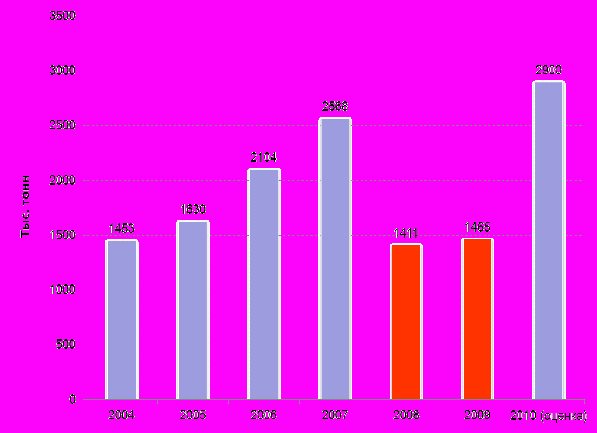
исунок 16. Динамика российского рынка труб большого диаметра
Три разных министерства дают три разных прогноза в потребности труб. Планирование на один год не позволяет избежать возможности таких скачков в потребности объёмов труб. Это ведёт к простоям, консервации производства, что стоит дороже производства. Затем незапланированная срочная потребность ведёт к форсированному производству и росту цен на продукцию.
Необходимо делать хотя бы инвестиционную трёхлетку, тем более, что в нефтегазовом комплексе много компаний с государственным участием (длительное инвестиционное проектирование). В мире существуют даже 5-летние финансовые планы, основанные на опыте СССР.
Просить федеральные органы исполнительной власти о переходе на среднесрочное планирование инновационных бюджетов нефтегазовых компаний, на среднесрочное (3-5 лет) планирование инвестиционных бюджетов нефтегазовых компаний с государственным участием (длительное инвестиционное проектирование) с целью предсказуемости объёмов потребления труб большого диаметра и других материально-технических ресурсов для сооружения магистральных трубопроводов.
7. Просить Технический комитет по стандартизации №23 «Техника и технология добычи и переработки нефти и газа» (В.В.Русакову) при разработке или рассмотрении национальных стандартов, включающих разделы по требованиям к трубной продукции, привлекать специалистов в области строительства нефтегазовых объектов.
8.Просить дирекцию ВНИИСТа организовать (восстановить) исследования в области работоспособности новой трубной продукции при выполнении комплекса строительно-монтажных работ на объектах нефтяной и газовой промышленности. Такие исследования необходимы для регламентации параметрических показателей, характеризующих ресурс и безопасность трубопроводов.
Отсутствие результатов таких исследований не позволяет создать методологию оценки технического состояния трубопроводов и выполнить расчёты технико-экономических, экологических и социальных рисков, определяющих конкурентоспособность отечественных производителей на мировых рынках.
9.Рекомендовать СРО «Нефтегазстрой» (В.П.Курамину) при разработке национального стандарта «Магистральные трубопроводы для транспортировки нефти, природного газа и продуктов их переработки. Организация и технология производства строительно-монтажных работ» использовать при формировании требований к трубной продукции современные возможности отечественной трубной промышленности, нашедшие отражение в настоящем постановлении Совета.
Президент, Председатель Проблемного научно-технического Совета РОССНГС д.т.н. проф. В.Г.Чирсков
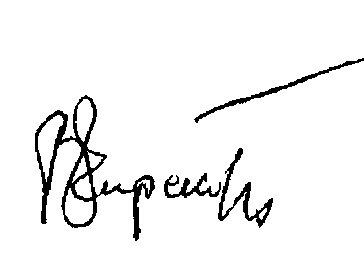
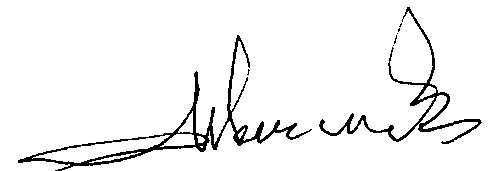