Технологические аспекты, обеспечивающие создание корпусных материалов для водо-водяных реакторов повышенной безопасности и ресурса
Вид материала | Документы |
СодержаниеМеханические свойства при 350 С |
- Реферат по прикладной физике На тему: «Тренажеры водо-водяных реакторов», 159.71kb.
- Перспективные направления расчетных исследований динамики и прочности многокомпонентных, 237.01kb.
- Научно-практические аспекты разработки и применения упаковочных материалов с проектируемым, 662.23kb.
- Для режущего инструмента мигранов М. Ш., Постнов В. В., Шустер Л. Ш., Фукс-Рабинович, 46.16kb.
- Программа учебной дисциплины "Химия конструкционных материалов" для подготовки, 124.47kb.
- Безопасность технических устройств и конструкций, создаваемых человеком, как элемент, 416.12kb.
- Касьянов Константин Геннадьевич оценка несущей способности и ресурса конструкционных, 452kb.
- Семинар состоится, 42.28kb.
- Технологические правила проектирования, 2013.95kb.
- Кдокладам Научно-практической конференции Российской ассоциации электронных библиотек, 243.74kb.
ТЕХНОЛОГИЧЕСКИЕ АСПЕКТЫ, ОБЕСПЕЧИВАЮЩИЕ СОЗДАНИЕ КОРПУСНЫХ МАТЕРИАЛОВ ДЛЯ ВОДО-ВОДЯНЫХ РЕАКТОРОВ ПОВЫШЕННОЙ БЕЗОПАСНОСТИ И РЕСУРСА.
Г.Н. Филимонов, В.В. Цуканов, И.И. Грекова, И.И. Теплухина,
В.В. Дюков, Т.И. Титова, Н.А.Шульган, И.И. Храпов.
ФГУП ЦНИИ КМ «Прометей», Санкт-Петербург, Россия
ОАО «Ижорские заводы», Санкт-Петербург, Россия
В мировой энергетике и энергетике России наиболее широкое распространение получили водоохлаждаемые атомные энергетические установки с реакторами в корпусном исполнении с водой под давлением.
Задачи развития атомной энергетики в России в ближайшие годы будут решаться с помощью строительства энергоблоков с атомными реакторами большой мощности (до 1500 МВт и более) с ресурсом 60 лет и более. В соответствии с современной мировой тенденцией корпуса этих реакторов будут иметь больший диаметр (по сравнению с ВВЭР-1000) вследствие увеличения размеров активной зоны для повышения мощности и зазора между топливными элементами и стенкой корпуса для уменьшения интегрального флюенса на металл корпуса. Параметры водяного теплоносителя (температура и давление) при этом останутся примерно на том же уровне, что и у реакторов ВВЭР-1000. Для разрабатываемых конструкций корпусов требуются поковки обечаек с толщиной стенок до 650 мм.
Вместе с тем, совершенствование реакторных материалов остается по-прежнему актуальной задачей, т.к. реализация поставленной задачи только за счет конструктивных решений не всегда возможна и часто приводит к значительным, иногда неразрешимым технологическим затруднениям.
Совершенствование материалов включает как корректировку химического состава стали, так и оптимизацию технологического процесса их изготовления, включая, термо-механические режимы ковки и прокатки и, что особенно актуально, режимы предварительной и окончательной термической обработки.
Для корпусов ВВЭР, работающих при температурах 270-325°С широко используются Cr-Mo-V и Cr-Ni-Mo-V свариваемые стали марок 15Х2МФА (15Х2МФА-А), 15Х2НМФА (15Х2НМФА-А, 15Х2НМФА класс1).
Свариваемая теплостойкая сталь15Х2МФА была разработана около 50 лет назад и успешно применялась для изготовления российских атомных энергетических реакторов как корабельного типа, так и реакторов атомных электростанций средней мощности. Сталь марки 15Х2МФА-А повышенной чистоты обладает наиболее высоким сопротивлением радиационному и тепловому охрупчиванию среди отечественных и зарубежных сталей такого же назначения, что определяет высокий запас её эксплуатационной стабильности. Однако её применение для толстостенных корпусных деталей современных реакторов было ограничено недостаточным уровнем прочности (RP0,2 при 350°С ≥ 396 МПа) и прокаливаемости, определяющей максимальную толщину, в которой обеспечиваются необходимые свойства.
Повышение единичной мощности блоков АЭС привело к увеличению размеров и толщины стенок корпусов ВВЭР. С целью повышения прокаливаемости в крупных сечениях были разработаны стали Cr-Ni-Mo-V композиции марок 15Х2НМФА (15Х2НМФА-А), содержащие никель до 1,5 %. Они обладают более высокой прокаливаемостью и более высоким уровнем прочности (при 350°С RP0,2 ≥441 МПа) по сравнению с безникелевой композицией. Однако, многочисленными исследованиями было показано преимущество Cr-Mo-V композиции в отношении сопротивления тепловому и радиационному охрупчиванию перед отечественными сталями, дополнительно легированными никелем, а также перед зарубежными реакторными сталями /1/. Сталь 15Х2НМФА(А) даже при низком содержании вредных примесей имеет менее высокую радиационную стойкость и более чувствительна к тепловому охрупчиванию, чем сталь марки 15Х2МФА-А, хотя и не уступает по этим характеристикам зарубежным корпусным сталям Mn-Ni-Mo композиции (А-533, А-508 кл.3). Никель, как известно, повышает чувствительность стали к радиационному и тепловому охрупчиванию (рис. 1). При содержании Ni более 1,3% дозовая зависимость изменения критической температуры хрупкости становится достаточно крутой, что свидетельствует об увеличении интенсивности процесса охрупчивания и о возможном изменении самого механизма радиационного повреждения стали. В связи с этим в стали марки 15Х2НМФА-А, для деталей корпусов АЭС, подвергаемых интенсивному облучению, максимальное содержание никеля было снижено с 1,5% до 1,3% (сталь марки 15Х2НМФА кл.1).
С учётом накопленного опыта эксплуатации материалов корпусов реакторов, а также результатов исследований зависимости теплового и радиационного охрупчивания от содержания никеля, выполненных в РНЦ КИ и ЦНИИ КМ «Прометей», и показавших слабое влияние никеля до концентраций менее 0,8%, была разработана новая марка стали с содержанием никеля в пределах 0,6-0,8% /2/.
Уменьшение прокаливаемости вследствие снижения содержания никеля на 0,5% по сравнению со сталью марки 15Х2НМФА кл.1 компенсируется повышением содержания хрома до 3,0% и повышением минимально допустимого содержания углерода. Увеличение содержания ванадия способствует, повышению эксплуатационной стабильности за счет образования более температурно-устойчивых карбидов.
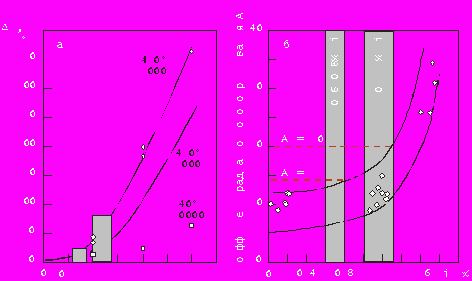
Рис.1. Влияние никеля на тепловое (а) и радиационное (б) охрупчивание стали типа15Х2НМФА
Учитывая, что медь и фосфор играют важнейшую роль в процессе радиационного охрупчивания корпусных сталей, допускаемое содержание этих вредных примесей было понижено до 0,07% и 0,007%. Предельный уровень содержания серы, оказывающей отрицательное влияние на уровень вязкости в исходном состоянии, был также снижен до 0,007%. Получение крупных полуфабрикатов корпусных реакторных сталей с таким низким содержанием вредных примесных элементов стало возможным только благодаря научным и техническим достижениям металлургии, металлургического машиностроения, а также развитию методов и приборного оснащения экспресс-анализа химического состава.
Важнейшими проблемами при изготовлении массивных поковок из слитков более 150 тонн являются получение возможно большей степени гомогенности состава и изотропности свойств, а также мелкозернистой бейнитно-мартенситной структуры по всему объёму заготовок.
С этой целью был разработан и применяется ряд технологических мероприятий, включающих:
- на стадии выплавки:
- использование контролируемой по примесным элементам шихты,
- использование специально подобранных модификаторов, а также технологии их введения для глобулизации неметаллических включений с применением обработки в установке внепечного рафинирования и вакуумирования,
- применение особых методов выплавки и рафинирования металла для снижения степени зональной и осевой ликваций,
- применение вакуумной разливки;
- на стадии горячей пластической обработки:
- выбор оптимального режима ковки, позволяющего избежать перегрева и неконтролируемого роста зерна;
- на стадии термической обработки:
- - применение режимов предварительной и основной термической обработки, обеспечивающих отсутствие флокенов и мелкозернистую мартенситно-бейнитную структуру;
- выбор оптимального сочетания режимов основного и дополнительных отпусков для получения требуемого соотношения прочностных и пластических свойств.
Настоящее сообщение посвящено вопросу выбора оптимальных режимов термической обработки.
Увеличение безопасного срока службы корпуса реактора можно обеспечить за счет повышения запаса хрупкой прочности материала корпуса реактора, т.е. путем применения стали, обладающей высоким уровнем вязкости в исходном состоянии (состоянии поставки) и низким темпом деградации вязких свойств в условиях эксплуатации.
Одним из резервов для достижения этой цели является измельчение зерна при термической обработке. Как известно /1,3/, при измельчении зерна в стали существенно снижается критическая температура хрупкости в исходном состоянии и повышаются эксплуатационные характеристики материала. Повышение эксплуатационной стабильности стали в этом случае достигается благодаря ослаблению охрупчивающего действия фосфора вследствие снижения концентрации фосфора на межзёренных границах. Кроме того, энергоёмкость разрушения мелкозернистой структуры даже при межзёренном характере разрушения значительно выше, чем при крупном зерне, поскольку траектория распространения трещины по границам зёрен связана с большим числом резких изменений направления, поглощающих энергию /3/. Поэтому разработка режимов термической обработки, обеспечивающих получение мелкого зерна в крупных поковках, является актуальной задачей.
При изготовлении крупных поковок интенсивный рост зерна наблюдается в условиях, когда деформация при ковке имеет критическую степень, и ковка завершается при высокой температуре. Кроме того, т.к. процесс ковки крупных полуфабрикатов осуществляется за большое число выносов, некоторые части поковки могут подвергаться высокотемпературному нагреву, без последующей пластической обработки, что также приводит к значительному увеличению размера зерен. Крупные поковки, как правило, имеют ярко выраженную разнозернистость. Кроме перечисленных причин, это вызывается различными степенями укова в разных частях поковки. Согласно данным ОАО «Ижорские заводы» размер зерна в крупногабаритной обечайке из стали марки 15Х2НМФА кл.1 после предварительной термической обработки колебался от 5-го до –3-го балла
Наиболее опасны эти явления для сталей, склонных к структурной наследственности /4,5/. При нагреве под закалку сталей, имеющих кристаллографически упорядоченную структуру (мартенсит, бейнит), при определённых условиях образование аустенита может не сопровождаться измельчением зерна, а приводить к восстановлению формы и размеров исходных крупных аустенитных зёрен и сохранению первоначальной кристаллографической ориентировки после α → γ → α превращений. Во время фазовой перекристаллизации в процессе α → γ превращения при этом не происходит измельчение кристаллической структуры, что значительно затрудняет задачу получения мелкого зерна в крупной поковке.
Таким образом, всякий раз, когда возникает кристаллографически упорядоченная мартенситная или бейнитная – крупнозернистая структура, появляется определённая опасность того, что при последующем нагреве выше критических точек не произойдёт привычного исправления крупнозернистой структуры. Важно, что отсутствие перекристаллизации при нагреве наблюдается как при быстром, так и сравнительно медленном нагреве.
Как показывает опыт, применяемые в настоящее время режимы термической обработки (как предварительной, так и окончательной), не всегда полностью устраняют разнозернистость и крупнозернистость, возникшие при горячей пластической обработке, вследствие чего не обеспечивается низкий уровень критической температуры хрупкости и однородность свойств по толщине поковки.
В соответствии с литературными данными /6,7/, при нагреве отпущенной стали металлографически выявляются два механизма образования аустенита, степень реализации которых зависит от легирования стали, исходной структуры и условий нагрева, особенно в межкритическом интервале температур. Один из этих механизмов приводит к образованию аустенита, ориентационно и морфологически связанного с исходной мартенситной (бейнитной) структурой и, следовательно, с аустенитом, из которого она получена. В предельном случае этот механизм приводит к полному восстановлению по величине и по кристаллографической ориентировке исходных зёрен аустенита – исправление структуры полностью отсутствует. Другой механизм ведёт к возникновению новых, сравнительно мелких и равноосных зёрен аустенита. При полном развитии этого процесса достигается привычный эффект исправления крупнозернистой структуры. Нередко реализуется промежуточный вариант, когда возникает сложная структура, представляющая собой зёрна восстановленного аустенита и расположенные по их границам и в их объеме новые зёрна. Соотношение этих составляющих зависит от степени перенагрева над точкой начала образования аустенита. При малом перенагреве, т.е. в условиях более близких к равновесным, превалирует фон восстановленного аустенита, при большем перенагреве преобладают новые зёрна /7/.
Параметры факторов, от которых зависит чувствительность стали к структурной наследственности взаимосвязаны и в значительной степени зависят от ее легирования и структурного состояния, и поэтому должны изучаться применительно к конкретным составам и условиям термической обработки
В работах ФГУП ЦНИИ КМ «Прометей» и ОАО «Ижорские заводы» была исследована склонность разработанной модификации стали 15Х2МФА-А с 0,6-0,8% Ni к проявлению структурной наследственности и росту зерна. Исследования проводились на металле опытно-промышленной выплавки. Критические точки при нагреве для данной стали Ас1 и Ас3 составляли 790 и 8350С соответственно. Заготовки из исследуемой стали были подвергнуты высокотемпературному нагреву (12000С, 2 часа), имитирующему нагрев под ковку, с целью получения крупного зерна. Учитывая, что предварительная термическая обработка поковок корпусных реакторных сталей всегда заканчивается операцией отпуска и что отпуск может оказывать значительное влияние на проявление структурной наследственности, часть заготовок была отпущена при температуре 6700С, а часть не подвергалась отпуску. Затем все заготовки проходили повторную закалку от различных температур и отпуск при 6700С, после чего исследовалась микроструктура. Скорость нагрева под закалку составляла ~ 50 град/мин.
Исследования показали, что при данной скорости нагрева, в случае, когда сталь не подвергалась отпуску после закалки с 12000С, образуется сложная структура, представляющая собой зёрна восстановленого исходного аустенитного зерна с сеткой мелких зёрен по их границам. Эта структура наблюдается до температуры нагрева под повторную закалку ~ 950 0С, после чего при дальнейшем повышении температуры аустенизации происходит измельчение зерна вследствие рекристаллизации, протекающей под влиянием фазового наклепа (рис.2). Причиной «зернограничного эффекта» (неупорядоченное превращение, локализованное по границам зерен) в данном случае являются, по видимому, процессы отпуска, успевающие протекать при нагреве под повторную закалку в области субкритических температур. При этом выделение карбидов первоначально происходит по границам аустенитных зёрен, в результате чего приграничные области аустенита претерпевают распад на феррито-карбидную смесь в наиболее полной степени. Кроме того, причиной «зернограничного эффекта» могут быть имеющиеся в приграничных зонах искажения кристаллической решетки. Однако эти искажения не исключают возможности упорядоченного превращения при более высоких скоростях нагрева.
Кардинальным образом картина менялась при проведении отпуска при 6700С после закалки с 12000С. Как показал эксперимент, при исследуемой скорости нагрева проведение предварительного отпуска устраняет склонность стали к структурной наследственности, и при повторной закалке уже от температуры
~ 900 0 С происходит перекристаллизация и измельчение зерна. При повторной закалке от температур выше 10000С имеют место процессы собирательной рекристаллизации, приводящие к росту зерна (рис.3).
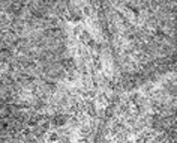
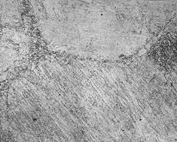
а б
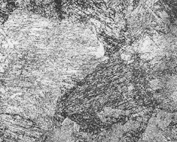
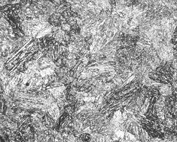
в г
Рис.2. Микроструктура модификации стали 15Х2МФА-А с 0,6-0,8% Ni после закалки от 12000С и последующего нагрева со скоростью ~50 град/мин до температур:
а – 8300С; б – 9000С; в – 9500С; г – 11000С (х 100)
В соответствии с классическими работами о структурной наследственности, при медленном (≤ 1,5 град/мин) нагреве, когда аустенит образуется в условиях, близких к равновесным, также происходит упорядоченное превращение α → γ и восстановление исходного зерна /6,7/. В этих условиях ускорение нагрева, напротив, мешает восстановлению первоначального зерна аустенита и способствует образованию глобулярного аустенита, слабо или совсем не связанного ориентационно с исходной структурой. Ускорение нагрева в данном случае благоприятствует фазовой перекристаллизации. При этом если исходная структура представляет собой двухфазную феррито-карбидную смесь и нагрев производится со скоростью, при которой возможны необходимые диффузионные процессы, образующийся восстановленный аустенит, как и при быстром нагреве неотпущенного мартенсита, структурно нестабилен и претерпевает рекристаллизацию при дальнейшем повышении температуры.
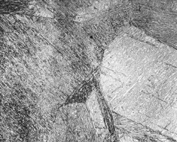
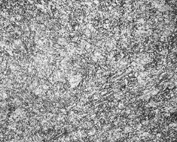
а б
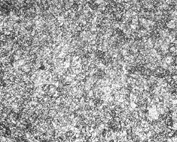
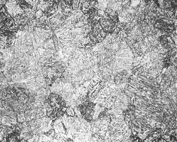
в г
Рис.3. Микроструктура модификации стали 15Х2МФА-А с 0,6-0,8% Ni после закалки от 12000С и отпуска при 670 0 С (а, исходное состояние) и последующего нагрева со скоростью
~50 г/мин до температур:
б – 9000С; в – 9500С; г – 11000С (х 100)
Изучение проявления структурной наследственности при медленном нагреве представляет большой практический интерес, поскольку скорость нагрева менее 1÷1,5 град/мин, при которой для многих сталей реализуется эффект восстановления зерна, примерно соответствует практическим условиям нагрева крупногабаритных изделий.
В связи с этим на высокотемпературном микроскопе НМ-4 проводилось изучение кинетики роста аустенитного зерна в интервале температур от 9000С до 10500С при скорости нагрева 1,5 град/мин после закалки с 12000С и отпуска при 6700С. Этот эксперимент показал, что при заданных условиях (медленный нагрев и предварительный отпуск) не происходит полное восстановление сверхкрупного аустенитного зерна в результате упорядоченного превращения. В процессе α → γ превращения образовывались мелкие слаборазориентированные аустенитные зерна, видимо не имеющие на своих границах защитных дефектных слоев. При дальнейшем нагреве происходил рост отдельных аустенитных зерен посредством объединения нескольких мелких, в результате чего уже в начальный период изотермической выдержки при температурах аустенизации (900–960)0С формировалась структура с ярко выраженной разнозернистостью. При дальнейшем увеличении выдержки изменения были не столь значительны и протекали более медленно. Увеличение выдержки более 30-40 мин. до 2 час. не вызвало заметного изменения зеренной структуры. Повышение температуры аустенизации до (930, 960, 1000 и 1050) 0С не привело к заметным изменениям в кинетике образования и роста зерен. Таким образом основные изменения структуры происходили в процессе нагрева до заданной температуры. При этом к началу изотермической выдержки при температурах 9300С и 9600С образовывалась структура с высокой степенью разнозернистости, к началу изотермических выдержек при 10000С и 10500С зерно было более крупным, но степень разнозернистости меньше. Размер зерна соответствовал 2-4 баллу. Следует отметить, что в процессе выдержки при 9300С и 9600С наблюдался избирательный рост отдельных зерен. Видимо при медленной скорости нагрева и наличии предварительного отпуска реализуется смешанный характер превращения, когда наряду с частичным восстановлением аустенитных зерен мы наблюдаем образование новых равновесных аустенитных зерен.
Таким образом проведенное исследование показало, что предварительный отпуск препятствуя полному восстановлению крупного зерна, полученного на стадии горячей пластической обработки, не обеспечивает получения мелкозернистой однородной структуры.
Наиболее надёжным и эффективным средством устранения последствий высокотемпературных нагревов в структуре стали является отжиг с распадом аустенита на феррито-перлитной ступени /6/. В результате эвтектоидного превращения уже в процессе охлаждения от температуры аустенитизации зёрна аустенита разбиваются на феррито-перлитные колонии, каждую из которых можно рассматривать как самостоятельное зерно; таким образом, кристаллическая структура стали рафинируется уже самим процессом распада аустенита. Исследование, проведенное для стали с 0,6-0,8 % никеля (при моделировании условий термической обработки в производственных условиях) показало значительную эффективность применения «перлитизации» для измельчения зерна.
Режимы термической обработки, предписанные нормативными документами, не всегда в полной мере обеспечивают достижение указанных целей. Поэтому были предложены усовершенствованные режимы, обладающие целым рядом преимуществ по сравнению с традиционными.
В отличие от применяемых режимов, в предложенный цикл предварительной термообработки (рис.4) включена изотермическая выдержка при температуре минимальной устойчивости аустенита с целью обеспечения распада аустенита с образованием феррито-перлитной структуры при охлаждении после нагрева выше АС3 для устранения склонности стали к проявлению структурной наследственности при повторном нагреве. При этом аустенитные зёрна претерпевают фазовую перекристаллизацию с измельчением зерна при переходе А → Ф+П. Кроме того, температуру аустенитизации было предложено повысить до температуры рекристаллизации аустенита с целью дополнительного измельчения зерна при нагреве выше АС3 . Копёж предложено проводить при температуре
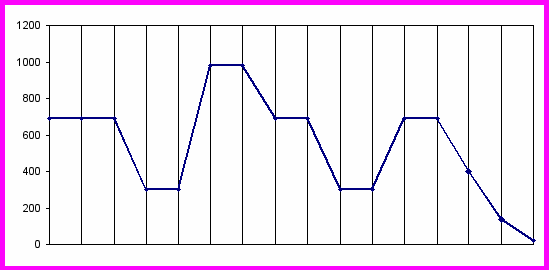
АС1
АС3
АС3 + 130÷160°С (Трекр)
4000С
с печью со
скоростью ≤40°С/ч
охл. с печью со скоростью≤30°С/ч


с печью со
скоростью ≤20°С/ч

Время



1500С
воздух



на выдвинутой
подине

высокий
отпуск
копёж
изотермическая
выдержка

Рис.4. Усовершенствованный режим предварительной термической обработки крупногабаритных поковок.
минимальной устойчивости аустенита для обеспечения гарантированного протекания превращения А → Ф+П уже на этой стадии. Все указанные мероприятия на стадии предварительной термической обработки обеспечивают удаление водорода из крупной поковки и равномерное распределение оставшегося водорода по сечению поковки, что надёжно предохраняет заготовку от возникновения флокенов. Кроме того, проведение усовершенствованных режимов предварительной термической обработки поковок способствует измельчению и выравниванию зерна в поковке ещё на стадии предварительной термической обработки.
Усовершенствованный режим окончательной термической обработки включает также ступень изотермической выдержки при температуре минимальной устойчивости аустенита для обеспечения протекания распада аустенита на феррито-перлитную смесь с целью дополнительного измельчения зерна после первой аустенитизации (рис.5).
АС3 + 130÷160°С (Трекр)
АС3 + 110÷140°С (Тзак)
вода

Время

АС3
АС1

высокий
отпуск
воздух

первая
аустенитизация
вторая
аустенитизация


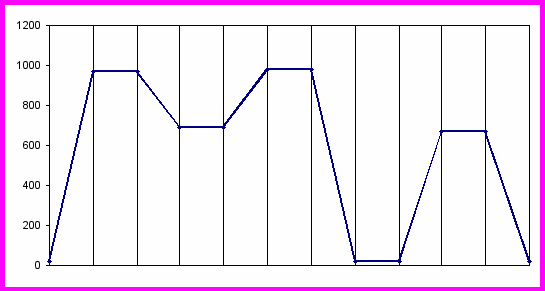
Рис.5. Усовершенствованный режим окончательной термической обработки крупногабаритных поковок.
Температура первой аустенитизации при этом соответствует температуре рекристаллизации аустенита, что обеспечивает дополнительное измельчение зерна на стадии нагрева выше АС3 .Температура последующей закалки должна обеспечить максимальное растворение карбидной фазы для достижения необходимой степени легирования аустенита и, как следствие, прокаливаемости заготовки по толщине, а также отпускоустойчивости при проведении последующих отпусков. Определение оптимальных параметров последней аустенитизации представляется наиболее важной задачей, так как в результате проведения изотермической выдержки при температуре минимальной устойчивости аустенита образующаяся карбидная фаза является более стабильной и крупной и для её растворения требуются определённые температурно-временные условия. Проведенное исследование показало, что при неоптимальных температурно-временных параметрах аустенитизации происходит неполное растворение карбидной фазы и С-образные кривые на термокинетических диаграммах превращения аустенита сдвигаются влево, что является признаком ухудшения прокаливаемости (рис.6).
Рис.1. Влияние никеля на тепловое (а) и радиационное (б) охрупчивание стали типа15Х2НМФА
вторая
аустенитизация

50
3
1
0,3
0,15
0,1
0,04
Скорость
охлаждения,0/сек
Рис.1. Влияние никеля на тепловое (а) и радиационное (б) охрупчивание стали типа15Х2НМФА
50
3
1
0,3
0,1
Рис.1. Влияние никеля на тепловое (а) и радиационное (б) охрупчивание стали типа15Х2НМФА
А→Ф
А→Ф
А→Б
А→Б
10
10
102
102
103
103
104
104
Время, с
Время, с
250
500
750
950
0,15

0,04

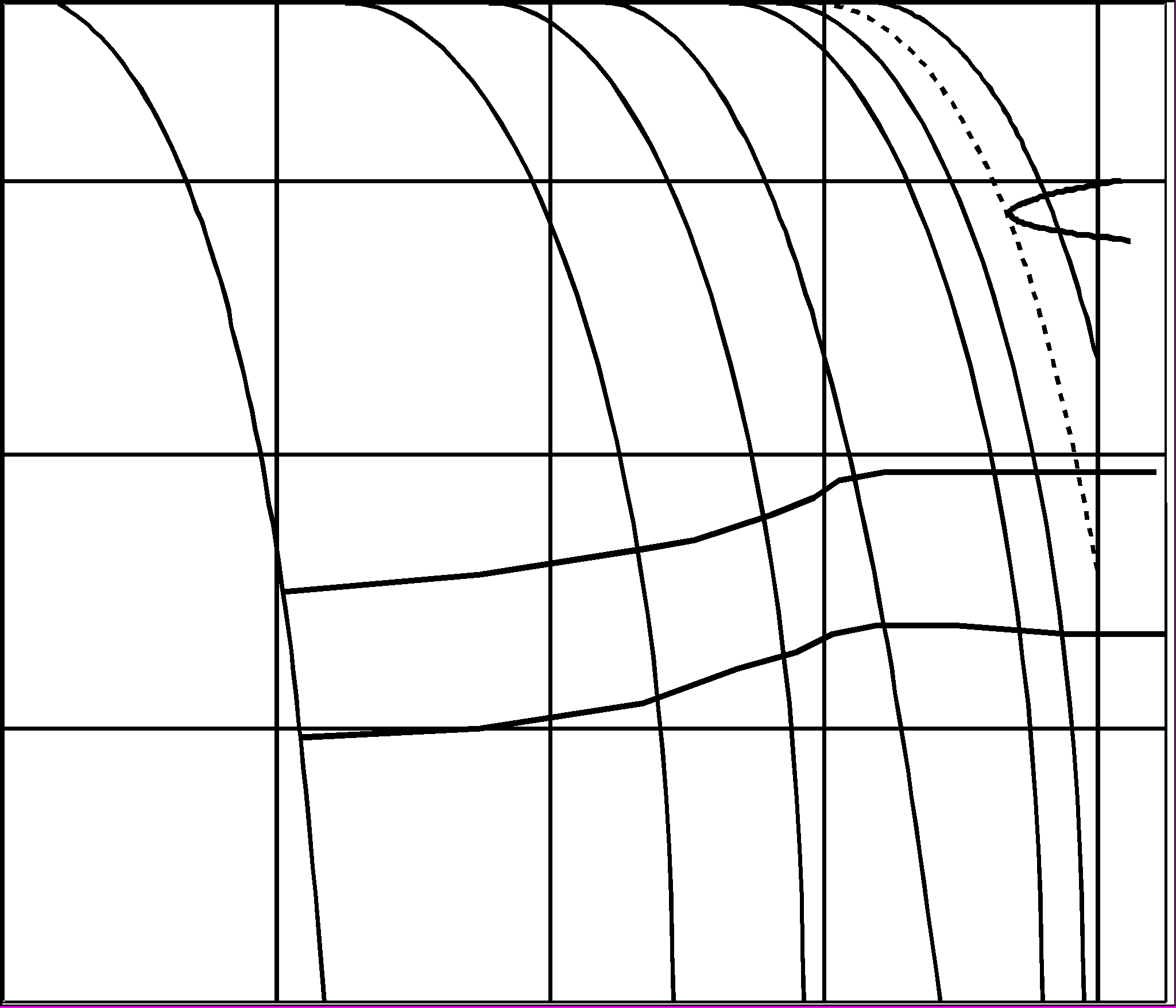
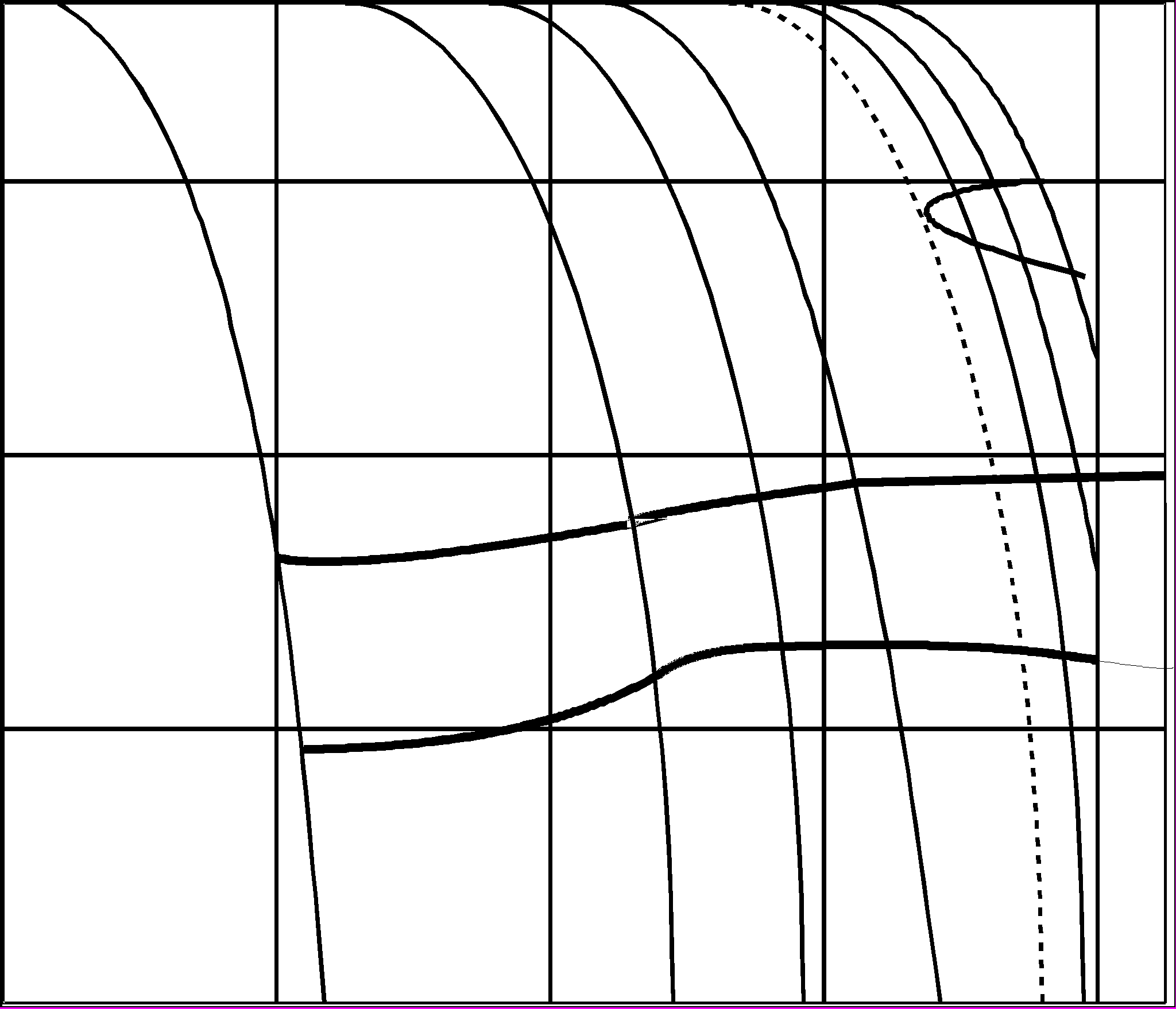
Температура аустенитизации – 9500С, время выдержки – 20 минут
Рис.6. Влияние структурного состояния на термокинетические диаграммы распада аустенита в модификации стали 15Х2МФА-А с содержанием никеля 0,6-0,8%
а – после термической обработки без «перлитизации»;
б – после предварительной термической обработки, включающей «перлитизацию»
Термическая обработка крупногабаритных опытно-промышленных обечаек переменного сечения толщиной 420-525 мм и 320-420 мм из модификации стали 15Х2МФА-А с 0,6-0,8% Ni по предложенной технологии, включающей «перлитизацию» на стадии предварительной и основной термической обработки, обеспечила получение в толщине этих заготовок мелкозернистой бейнитно-мартенситной структуры (рис.7) и высоких значений прочности и вязкости (табл.1). Уровень механических свойств, полученный на металле этих обечаек после основной термической обработки, состоящей из двойной закалки и высокого отпуска, был более низким,особенно в больших сечениях, а размер зерна крупнее.
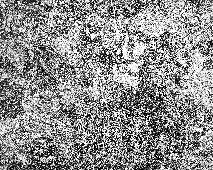
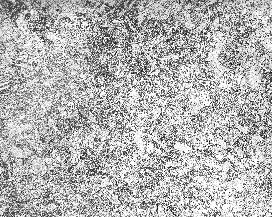
а б
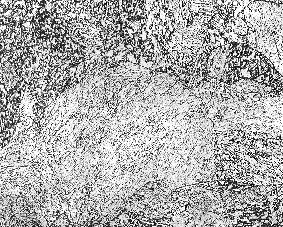
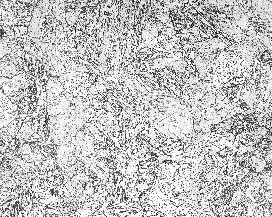
в г
Рис.7. Микроструктура опытно-промышленных обечаек переменного сечения толщиной 420-525 мм и 320-420 мм из модификации стали 15Х2МФА-А с 0,6-0,8% Ni после различных термических обработок.
а,в – Микроструктура обечайки толщиной 420-525 мм (в толщине 420 мм) после двойной закалки и высокого отпуска
б,г – Микроструктура обечайки толщиной 320-420 мм(в толщине 420 мм) после аустенизации с «перлитизацией» и высокого отпуска
Таблица 1
Механические свойства проб основного металла опытно-промышленных обечаек переменного сечения толщиной 420-525 мм и 320-420 мм из модификации стали 15Х2МФА-А с 0,6-0,8% Ni
| Толщина, мм | Вид термической обработки | Механические свойства при 350 0 С | | |||
в, МПа | 0,2, , МПа | ,% | ,% | Т ко , 0 С | |||
Опытно-промышленная обечайка толщиной 420-525 мм | 420 | Двойная закалка + высокий отпуск | 560 | 490 | 17,0 | 76,0 | -15 |
525 | 550 | 475 | 17,0 | 76,0 | -35 | ||
420 | Аустенизация с «перлитизацией» + высокий отпуск | 610 | 540 | 15,5 | 76,0 | - 55 | |
525 | 620 | 550 | 15,0 | 74,0 | - 55 | ||
Опытно-промышленная обечайка толщиной 320-420 мм | 320 | Двойная закалка + высокий отпуск | 580 | 500 | 17,5 | 76,0 | -45 ÷ -65 |
420 | 560 | 485 | 17,0 | 80,0 | -35 ÷ - 45 | ||
320 | Аустенизация с «перлитизацией» + высокий отпуск | 590 | 510 | 18,0 | 77,0 | - 55 | |
420 | 620 | 550 | 17,0 | 77,0 | - 55 |
Таким образом, предлагаемые усовершенствованные режимы предварительной и окончательной термической обработки крупногабаритных поковок обеспечивают предотвращение дефектов (флокенов, трещин), получение однородной по сечению мелкозернистой структуры обрабатываемых поковок, снижение исходного уровня критической температуры хрупкости (ТКО) и должны благоприятно влиять на уменьшение сдвига критической температуры хрупкости в результате облучения (∆ТF).
Необходимо отметить, что каждый технологический приём дает свой вклад в формирование высокого металлургического качества, гомогенности состава, технологических и эксплуатационных свойств металла. Как показала практика, только их совместное использование является успешным.
Учитывая последнее, ЦНИИ КМ «Прометей» и ОАО «ИЗ» разработали технологию производства поковок и заготовок стали усовершенствованного состава для корпусов реакторов современных проектов. Данная технология включает в себя множество мероприятий по снижению содержания вредных примесей, получению однородной и мелкозернистой структуры и гомогенности по химическому составу.
Список литературы:
1.И.В. Горынин, В.В. Рыбин, Г.П. Карзов, Г.Н. Филимонов и др. Создание и совершенствование сталей для корпусов реакторов атомных энергетических установок с водой под давлением.// Вопросы материаловедения, №3(20), 1999, стр. 63-85.
2.Патент на изобретение № 2139952 от 20.10.1999. сталь для корпусных конструкций атомных энергоустановок повышенной безопасности и надёжности. Авторы: Горынин И.В., Карзов Г.П., Филимонов Г.Н. и др.
3. А.Д. Амаев., А.М. Крюков, И.М. Неклюдов и др./ под ред. А.М. Паршина и П.А. Платонова, «Радиационная повреждаемость и работоспособность конструкционных материалов» -СПб.: Политехника, 1977.- 312 с.: ил.
4. Склюев П.В. «Водород и флокены в крупных поковках».-М.: Машгиз, 1963.- 187 с.
5. Башнин Ю.А., Паисов И.В. и др. «Термическая обработка крупных поковок».- М.: Металлургия, 1973.- 173с.
6. В.Д. Садовский. «Структурная наследственность в стали».-М.: Металлургия, 1973.- 205 с.
7. «Металловедение и термическая обработка стали». Справочник под редакцией М.Л. Бернштейна и А.Г. Рахштадта, том 2. – М.:Металлургия, 1983.- 366 с.