Программа: 22. 09. 2009 г. Заезд участников конференции и регистрация в холле 1-го этажа 15
Вид материала | Программа |
- Программа работы Конгресса День Первый 30 сентября 2009 года. 30 час. 10. 30 час. Начало, 604.04kb.
- Программа конференции 00 10. 00 Регистрация участников конференции (холл 7 этажа)., 63.96kb.
- Программа всероссийской студенческой научно-практической конференции «Актуальные проблемы, 508.44kb.
- Программа международной научно-практической конференции молодых ученых «молодежь, 431.19kb.
- Краткая программа конференции 7 августа заезд и регистрация участников конференции., 42.29kb.
- Программа конференции 00-10. 00 регистрация участников холл 1 этажа здания мгппу пленарное, 55.61kb.
- Примерная программа III открытой межрегиональной конференции школьников: «Православие, 283.85kb.
- Научная студенческая конференция 17 апреля 2012 года, 309.52kb.
- А. Ю. Вафин Сопредседатели научного и организационного комитетов, 57.95kb.
- Примерная программа конференции: Заезд участников конференции 12 сентября 2011 г. Регистрация, 91.77kb.
Оптимизация температурных режимов для технологий ионно-плазменной обработки внутренней поверхности трубы
Москаленко А.А.1, Яцевский В.В.1, Хямялайнен Л.Т.2, Надтока В.Н.3
1-ИТТФ НАН Украина, г. Киев; 2-О ИВТ РАН,г.Москва; 3- ГП «КБ «Южное», г. Днепропетровск
Данная статья посвящена решению актуальной проблемы увеличения срока эксплуатации крупногабаритных трубных заготовок специального назначения, подвергающихся циклическим ударным воздействиям на внутреннюю поверхность сверхвысоких температур (2500-3500ºC), давлений (1406-5624 МПа) и механического трения [1]. Решающим фактором в потере работоспособности является эрозия – удаление частичек металла с его внутренней поверхности. Один из наиболее эффективных методов борьбы с эрозией - нанесение защитной плёнки металла повышенной твёрдости ( хром и др. ) между поверхностью и потоком газов. Нанесение ионно-плазменного защитного слоя хрома на внутреннюю поверхность заготовки спецтрубы должно проводиться при температуре поверхности металла трубной заготовки в пределах 300оС - 350оС. При этом будет сохранён необходимый уровень сопротивления металла малым пластическим деформациям циклических нагрузок, характеризующийся пределом упругости или коэффициентом пропорциональности.
Однако, в экспериментах, проведенных на трубных заготовках, зафиксирован значительный перегрев в зоне напыления. При перегреве металла – понижаются его прочностные свойства (твёрдость, прочность, упругость т.д.) приобретённые после предшествующей операции финишной термообработки, что негативно скажется на продолжительности его эксплуатации. Для обеспечения высокого качества адгезии защитного покрытия необходимо выполнять требование соблюдения оптимального температурного коридора: от 300 до 350оС [3].
При постановке задачи данной работы, авторами были учтены как результаты экспериментов на трубных заготовках, так и результаты предыдущих расчётов полей температур с помощью двух компьютерных программ: специализированной (BiLab) [4] и стандартной комплексной - Comsol multiphysiсs [5]. В программах использовались: адекватные реальному тепловому процессу математические модели, учитывающие как нестационарный характер теплообмена, так и существенную неравномерность распределения температур по длине спецтрубы. Выбор численного метода математического моделирования теплового состояния спецтрубы определялся геометрией трубы и нелинейными (непостоянными во времени и по поверхности) граничными условиями теплообмена. С учётом результатов экспериментов и этих расчетов были внесены изменения в первоначальную конструкцию блока «очиститель-испаритель». Дополнительной возможностью нормализации температурного поля в трубе могло быть увеличение длины модуля источников ионов и плазмы до 400 мм с сохранением неизменной их мощности. Результаты расчетов представлены в виде зависимостей температур от времени и от длины фрагмента трубы. Зависимости температуры стенок от длины трубы имеют характерную колоколообразную форму. Максимум температуры находится в районе центра зоны подогрева и перемещается вместе с ним вдоль оси трубы. Более высокие температуры стенки наблюдаются на этапе работы очистителя
Выполненные, применительно к условиям новых технологий защиты поверхности труб, работающих в тяжелых эксплутационных условиях, расчеты температурных режимов металла, позволяют с высокой достоверностью и надёжностью определить оптимальные условия теплообмена, при которых обеспечивается высокое качество нанесенного покрытия. Подытоживая результаты экспериментально-расчетного исследования, можно сделать следующие выводы:
1. Температура металла при выбранных параметрах сиcтемы нанесения защитного покрытия на 267-280оС превышает допустимую.
2. Соблюдение технологических требований по рабочей температуре металла (Т=300-350оС) при выбранных параметрах не возможно без принудительного отвода тепла с внешней поверхности трубы. Увеличение длины модуля до 400 мм не решает полностью проблему нормализации температуры металла.
3. Проведенные на основании обновленной математической модели технологического процесса расчеты позволяют подобрать для различных диаметров трубы и мощностей источников оптимальные режимы работы системы охлаждения, которые обеспечивают соблюдение требуемого для данного технологического процесса температурного режима.
Использованная литература
1. Ahmad I., “The problem of gun barrel erosion: an overview” in “Gun propulsion technology”, Vol. 109, Progress in Astronautics and Aeronautics, edited by M Summerfield, AIAA, 1988, pages 311- 356.
2. Василина В.Г., Надтока В.Н., ЗайцевВ.И. Экспериментальная установка для нанесения ионно-плазменных покрытий на внутреннюю поверхность труб. Вакуумная техника и технология. – 2—6, т. 16, №1, с. 83-85.
3. Мовчан В.А., Малашенко И.С. Жаростойкие покрытия, осажденные в вакууме. Киев, Наукова думка, 1983, 232 с.
4. Москаленко А.А., Зотов Е.Н., Добривечер В.В., Надтока В.Н., Хямялайнен Л.Т. Експериментально-расчетное определение поля температур полого цилиндра при локальном внутреннем обогреве. Сборник докладов конференции «Результаты фундаментальных исследований в области енергетики и их практическое значение», Москва, 24-26 марта 2007г., М., ОИВТ РАН, «Шанс», 2008.-с.99-105.
5. Бирюлин Г.В. Теплофизические расчеты в конечно-элементном пакете COMSOL / FEMLAB. Методическое пособие . ,С-Петерб. ГУ ИТМО., 2006 г, 86с.
Исследование охлаждающих характеристик новых закалочных сред на основе минеральных масел
МоскаленкоА.А. 1, ЛогвиненкоП.Н.,2 Проценко Л.Н.1, Синило В.Н.3 ,
1 - ИТТФ НАН Украины, г.Киев; 2 - ООО «Баркор», г.Киев;
3 - ОАО «СКФ Украина», г.Луцк
Минеральные масла различного химического состава широко используются наряду с другими жидкостями (вода, растворы солей и полимеров) в металлообработке, машиностроении, металлургии, технологиях термического упрочнения металлоизделий и др. До настоящего времени трудно найти равноценную замену этим охлаждающим средам, обладающим оптимальными способностями повышать твердость и прочность металла, сохраняя другие важные эксплуатационные его показатели - пластичность и др., исключая такой вид производственного брака, как деформация и трещинообразование.
Для обеспечения стабильности качества металлоизделий важны контрольные измерения химического состава, вязкости, наличия механических включений, примесей воды и других показателей закалочных сред, в начале эксплуатации и, периодически, в процессе её использования. Испытанием, которое объединяет результаты анализов и определяет итоговое заключение о соответствии данного масла требованиям технологии по динамике охлаждения металла для получения нужных структур и свойств, является тестирование масла по охлаждающей способности в соответствии с утверждённым Международным стандартом ISO 9950 [1].В ИТТФ НАН Украины на базе ранее разработанной автоматизированной системы регистрации и обработки термоакустических экспериментальных данных процессов нестационарного теплообмена [2], была создана установка для тестирования охлаждающих свойств жидкостей. Установка состоит из печи с блоком управления нагревом до 850+3оС, стального образца (термозонда) D=12,5мм, Н=60мм. В центре образца размещена хромель-аллюмелевая термопара. После нагрева до нужной температуры термозонд опускается в тестируемую жидкость. В процессе охлаждения сигнал от термопары подаётся на блок аналого-цифрового преобразователя. Цифровая информация передаётся в базу данных переносного компьютера, в котором с помощью специально разработанной программы производится рассчетная и графическая обработка опытных данных.
В программу исследований, согласованную с представителями ОАО «СКФ Украина и ООО «БАРКОР» - разработчика новых видов масел, были включены отечественные и импортные марки масел. В качестве базового для тестирования выбрано индустриальное масло И-12, а для сравнения закалочное масло Isorapid 277HM, (производитель «Petrofer chemie”, ФРГ), хорошо зарекомендовавшее себя как среда с высокой скоростью охлаждения в зоне неустойчивого аустенита. Для поиска более экономичных закалочных сред, исследованы многокомпонентные составовы на базе масла И-12 и пакета присадок ML-EP87 (производитель фирма «ML Lubrication»). Группу сред «Гартол» в широком спектре специальных присадок предоставил для тестирования ООО «БАРКОР». Также было протестировано масло марки «Термол», производитель - фирма «Кальви», г. Львов.
Для всех масел при тестировании устанавливалась Тм=: 50_+2 оС
Получен ряд зависимостей температуры термозонда и скорости его охлаждения от времени. На кривых охлаждения T= f(τ) наблюдаются три характерных участка, соответствующих трём режимам теплоотдачи от поверхности к жидкости: двухфазного (плёночного и пузырькового кипения) и конвективного теплообмена. Зоны быстрого охлаждения на графике T(τ) соответствуют участкам со значительной крутизной снижения температуры, что важно в диапазоне температур 650-400оС и благоприятно влияет на формирование мартенситной микроструктуры металла. Предпочтительно выглядят две из исследованных сред : «Isorapid 277 HM», а также «Гартол-S». для этих сред зона пленочного кипения слабо выражена, кратковременна, поэтому практически не сказывается на замедлении охлаждения металла в вышеуказанном диапазоне температур. Максимумы скоростей охлаждения для них смещены в зону более высоких температур 610-620оС и по абсолютной величине превышают другие масла на 10-35 град/с.Принятое по требованиям ISO 9950 представление процесса для различных сред шестью характерными показателями динамики охлаждения зонда, приведенными в табличной форме, подтверждает позитивную оценку данных марок масел в качестве закалочных жидкостей.
Выводы:
- Исследование закалочных масел в соответствии с требованиями ISO 9950, позволило получить зависимости динамики охлаждения стандартного термозонда для 14 типов масел.
- Анализ полученных результатов даёт основания рекомендовать для использования в процессах термоупрочнения, марки масел «Isorapid 277HM» и «Гартол–S» (дополнительным преимуществом последнего является сравнительно низкая стоимость).
Литература
1. International Standart ISO9950. Indastrial quenching oil – Determination of cooling characteristics – Nickel-alloy probe test method, 1995, p.9.
2. Москаленко А.А., Симаченко А.В., Добривечер В.И., Дейнеко Л.Н., Кимстач Т.В., Проценко Л.Н. Разработка апаратно-программного комплекса для оапределения охлаждающих свойств закалочных сред. «Строительство, материаловедение, машиностроение», Сб. научн. трудов .Вып.48 ч.3.Дн-вск., ПГАСА,2009. – С.99-105.
Влияние пульсации потока на работу небольшой
тепловой электростанции
Юрий Тонконогий (контактное лицо), jurij@mail.lei.lt, тел.: +(370 37) 401 862, Антанас Пядишюс, эл. почта: testlab@mail.lei.lt, Арунас Станкявичюс, эл. почта: aras@mail.lei.lt, Андрюс Тонконоговас, эл. почта: andriust@mail.lei.lt, Литовский энергетический институт.
![]() |
Рис. 2. Возникновение резонанса. Частота пульсаций и резонансная частота до (1, 3) и после (2, 4) установки диафрагмы; 5 – расчетная резонансная частота |
![]() а |
![]() б |
Рис. 1. Зависимость частоты (а) и амплитуды (б) пульсации давления от нагрузки до (1) и после (2) установки диафрагмы; 3 - частота вращения компрессора |
![]() |
Рис. 3. Зависимость погрешности ТСГ от нагрузки |
Характер зависимости погрешности ТСГ (рис. 3) и амплитуды пульсации давления от нагрузки очень похожи, т.к. именно повышенная пульсация являются причиной повышенной погрешности. При уменьшении нагрузки ниже 18 МВт резко возрастает до величины + 62 %. При нагрузках выше 18 МВт значения погрешности не превышают величины +5 %.. Установка диафрагмы несколько уменьшает пульсацию и вибрацию, но не решают проблему до конца.
Динамическая погрешность турбинного счетчика газа при сложных законах пульсации
Юрий Тонконогий (контактное лицо), jurij@mail.lei.lt, тел.: +(370 37) 401 862, Антанас Пядишюс, эл. почта: testlab@mail.lei.lt, Андрюс Тонконоговас, эл. почта: andriust@mail.lei.lt, Литовский энергетический институт; Павел Круковский, Институт технической теплофизики нану, эл. почта: kruk@i.kiev.ua
![]() |
Рис. 1. Отклик ТСГ на пульсацию при С=0. 1 - расход газа; 2, 3, 4, 5, 6 – отклик при f*T = 0,00083; 0,17; 0,41; 0,83; 83 соответственно |
![]() |
Рис. 2. Влияние частоты и параметра С на динамическую погрешность ТСГ. 1 – С<0,25; C>0,5; 2, 3, 4, 5, 6, 7 – С = 0,3; 0,34; 0,35; 0,355; 0,36; 0,38 соответственно |
Нами изучены отклик и динамическая погрешность ТСГ в вышеуказанных условиях в зависимости от частоты f и амплитуды пульсаций Q. Для этого применен ранее разработанный метод численного моделирования, в соответствии с которым на каждом шаге времени t для вычислений применяется уравнение отклика ТСГ на резкое (ступенчатое) изменение расхода. При этом в качестве основного параметра процесса используется экспериментально определяемая постоянная времени Т счетчика. Большое преимущество метода - его пригодность для любых, в том числе и знакопеременных, законов пульсации потока. Для обобщения результатов введены безразмерные переменные: погрешность пр, частота пульсаций f*T, время f*t и параметр
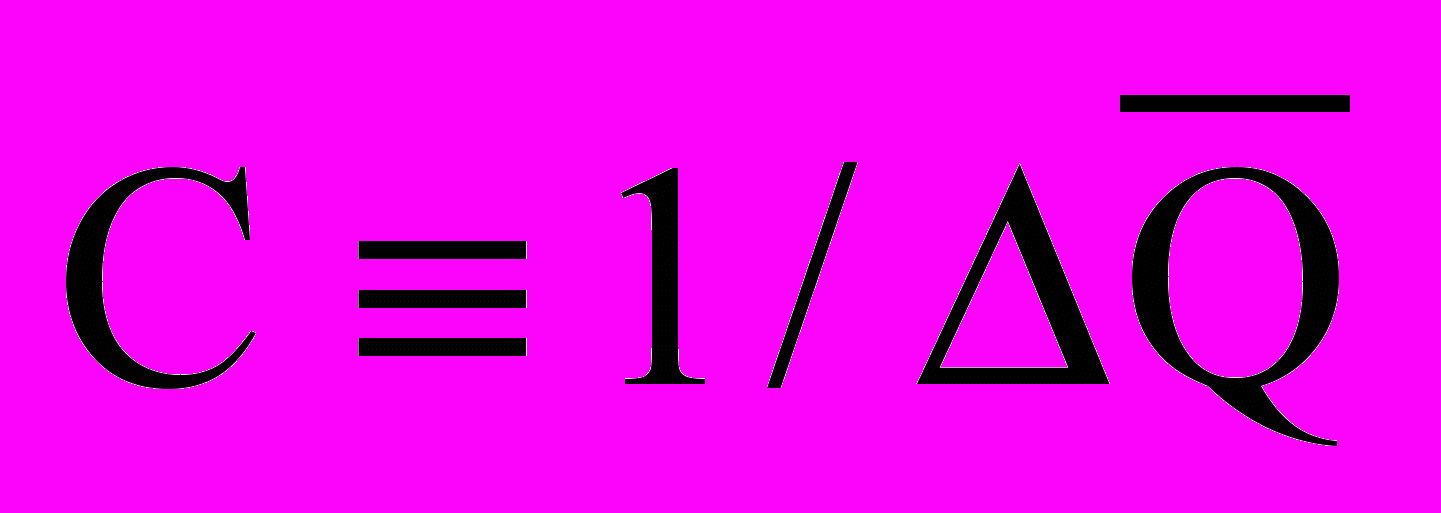
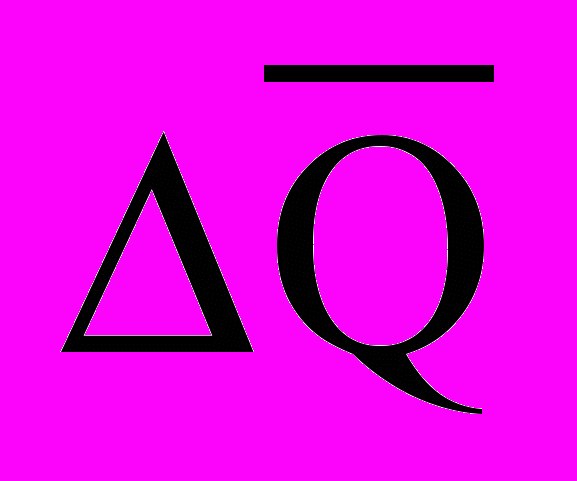
![]() |
Рис. 3. Зависимость предельной динамической погрешности от параметра С |
На погрешность ТСГ (рис. 2) влияют те же факторы, что и на отклик. Помимо инерции ротора существенен тот факт, что современные ТСГ не реагируют на перемену знака потока и независимо от него посылают все импульсы от вращения в один сумматор. Степень влияния этих двух факторов различна при различных значениях С и f*Т. Поэтому влияние на погрешность безразмерной частоты f*Т немонотонно, что особенно сильно проявляется в области С = (0,25 – 0,5). Незначительное изменение значения С от 0,35 до 0,36 вызывает резкое изменение характера зависимости пр как от С, так и от f*Т. При больших значениях частоты пр = 1, что соответствует определению пр. На рис. 3 представлена зависимость предельного значения погрешности пр от С. Особенно сильно, как по абсолютной величине, так и по знаку, эта погрешность меняется в области знакопеременных пульсаций, при 0 ≤ С < 1. Аналогичные результаты получены для других законов пульсаций, в частности, для ряда сложных косинусоидальных законов. Полученные результаты находятся в полном согласии с известными результатами там, где сравнение возможно.
Вариант энергоэкономичной дегидратации биоэтанола
Бремерс Гунарс1, Бирзиетис Гинтс1, Шкеле Арнолдс1, Блия Анита1, Данилевич Алексей2, Лебедева Кристина3, Шипковс Петерис3
1Институт силовых машин Латвийского Сельскохозяйственного Университета
Ул. Лиела 2, Елгава, LV-3001; тел.:+371 630-80685;
е-почта: gints.birzietis@llu.lv
2Институт Микробиологии и биотехнологии Латвийского Университета
Бульвар Кронвальда 4, Рига, LV-1586; тел.:+371 67034886;
е-почта: danil@lanet.lv
3 Физико - энергетический институт
Ул. Айзкрауклес 21, Рига, LV-1006; тел./факс:+371 67553537;
е-почта: kristina.lebedeva@edi.lv
Для переписки: Г.Бремерс - тел.: +371 630-24782; е-почта: gunars.bremers@gmail.com
Дегидратация является наиболее энергозатратной стадией получения биоэтанола.
Цель работы
Показать и обосновать возможность снижения расхода тепла на конечных стадиях ректификации и сушки.
Результаты
Предлагается дегидратацию биоэтанола проводить в совмещенном процессе ректификации и адсорбции путем введения в ректифицируемую среду адсорбирующего молекулы воды вещества.
Выводы
Совмещение ректификации с адсорбцией дает возможность уменьшить количество тарелок в ректификационной колонне, а расход энергии на обезвоживание сократить, примерно, на 70%.