Лекция 15. Дуговая сварка в среде защитных газов
Вид материала | Лекция |
- Ручная электро-дуговая сварка, 1686.86kb.
- Программа вступительного экзамена в аспирантуру по специальности 05. 03. 06 «Сварка, 131.86kb.
- Лабораторная работа 1 Ручная дуговая сварка штучными электродами, 173.93kb.
- Государственный стандарт союза сср сварка, пайка и термическая резка металлов гост, 487.3kb.
- Выпрямители сварочные вс-300Б, 26.33kb.
- Лекция 16. Способы сварки давлением. Контактная сварка. Стыковая, точечная, шовная, 82.74kb.
- Государственный стандарт союза сср ручная дуговая сварка. Гост, 1829.59kb.
- Тема: сварка алюминия и его сплавов, 56.75kb.
- Зварачныя работы правiлы правядзення Издание официальное Министерство архитектуры, 2913.92kb.
- Нуукская декларация об окружающей среде и развитии в Арктике, 219.44kb.
Лекция 15. Дуговая сварка в среде защитных газов.
Для защиты металла сварочной ванны применяют инертные газы (наиболее широкое применение в промышленности получил газ аргон) и активные газы (углекислый газ, азот и др.).
Аргонодуговая сварка
Этот способ сварки применяется при изготовлении тонколистовых конструкций из легированных сталей, меди, алюминия и их сплавов, а также химически активных и тугоплавких металлов.
Сварка обеспечивает надежную защиту расплавленного металла сварочной ванны и околошовной зоны от кислорода и азота воздуха.
Сварка выполняется:
I. Неплавящимся электродом. В качестве электрода применяется стержень диаметром 0,5–3 мм из вольфрама. Сварочная дуга горит между электродом и изделием. В процессе сварки вольфрамовый электрод не плавится. Для образования сварного шва используется металл отбортовки или присадочная электродная проволока, которая вводится в зону дуги извне. Подача электродной проволоки может осуществляться вручную (ручная сварка) или с помощью автомата (автоматическая или полуавтоматическая сварка). Для защиты расплавленного металла сварочной ванны от окисления из горелки подается защитный газ, который своим давлением оттесняет от сварочной ванны кислород и азот воздуха.
Д
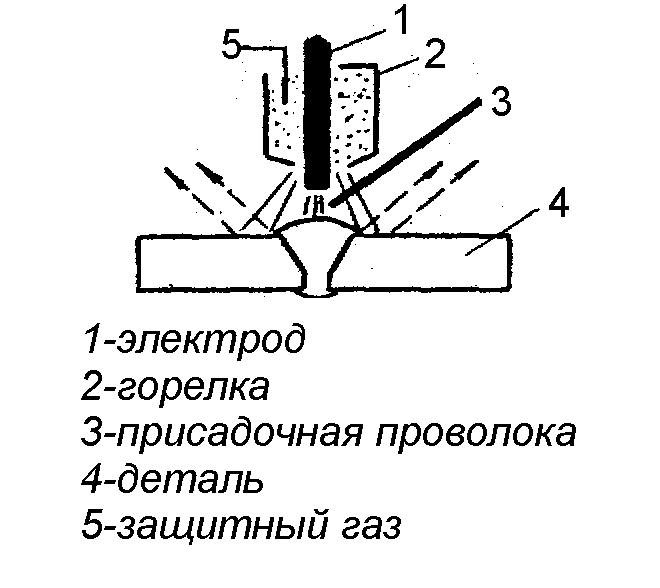
Сварка неплавящимся электродом осуществляется на постоянном и переменном токах. Постоянным током (обычно прямой полярности) сваривают нержавеющие и жаропрочные стали, никель и его сплавы, титан, цирконий, молибден и другие металлы толщиной 0,1–6 мм. Применяется источник тока с падающей внешней характеристикой.
Переменным током сваривают алюминий, магний и их сплавы. Причем в те полупериоды, когда катодом является изделие, его поверхность бомбардируется тяжелыми положительными ионами аргона, и происходит так называемое катодное распыление тугоплавких оксидных пленок алюминия или магния. Поэтому нет необходимости применять флюсы для их удаления.
Сварку можно вести и без присадочного материала за счет расплавления кромок металла свариваемого изделия.
II. Плавящимся электродом. В этом случае в качестве электрода применяется электродная проволока диаметром 0,5–3 мм. Химический состав электрода должен быть близок к составу металла изделия. Сварку производят на постоянном токе обратной полярности. Применяют источник тока с жесткой или возрастающей внешней характеристикой. Плавящимся электродом сваривают алюминий, магний, их сплавы, а также нержавеющие стали.
Азотнодуговая сварка
В качестве защитного газа используется активный газ азот. Применяется для сварки меди и ее сплавов, так как азот с медью не образует химического соединения.
Обычно сварка меди производится угольным или вольфрамовым электродом. Для раскисления сварочной ванны при сварке меди используют специальные флюсы или специальная электродная проволока, содержащая раскислители.
Сварка в среде углекислого газа
Самый дешевый способ сварки. Применяется при сварке углеродистых и низколегированных сталей. Сварка может производиться как плавящимся электродом так и неплавящимся угольным электродом на постоянном токе обратной полярности. Применяют источник тока с жесткой или возрастающей внешней характеристикой.
Углекислый газ, попадая в высокотемпературную часть дуги, диссоциирует на кислород и окись углерода

Для компенсации окислительного действия углекислого газа повышают содержание в электродной проволоке раскисляющих элементов (Mn, Si),которые раскисляют железо, и соединяясь с кислородом, всплывают в виде шлаков.(Например берут проволоку Св–08Г2С).
Для получения плотного, беспористого шва и уменьшения разбрызгивания металла необходимо поддерживать короткую длину дуги (1,5–4 мм).
Расход углекислого газа составляет 15–25 л/мин при давлении 0,5 атм.
Режим сварки: при сварке деталей толщиной до 2 мм U=22 В, I=60–150 А, расстояние от сопла горелки до металла 7–14 мм. При сварке средних толщин U=26–34 В, I=250–500 А, расстояние от сопла горелки до металла 15–25 мм.
Электрошлаковая сварка
Электрошлаковая сварка – это термический способ сварки, при котором источником нагрева служит шлаковая ванна с высокой температурой.
Шлаковая ванна образуется путем расплавления флюса при прохождении через него преимущественно переменного тока. Используется сварочный трансформатор с жесткой характеристикой. При этом шлак нагревается до температуры, превышающей температуру плавления основного металла и электродной проволоки. Следует помнить, что основное назначение сварочного флюса при электрошлаковой сварке – это преобразование электрической энергии в тепловую, а получение сварных швов определенного химического состава осуществляется выбором соответствующей электродной проволоки.
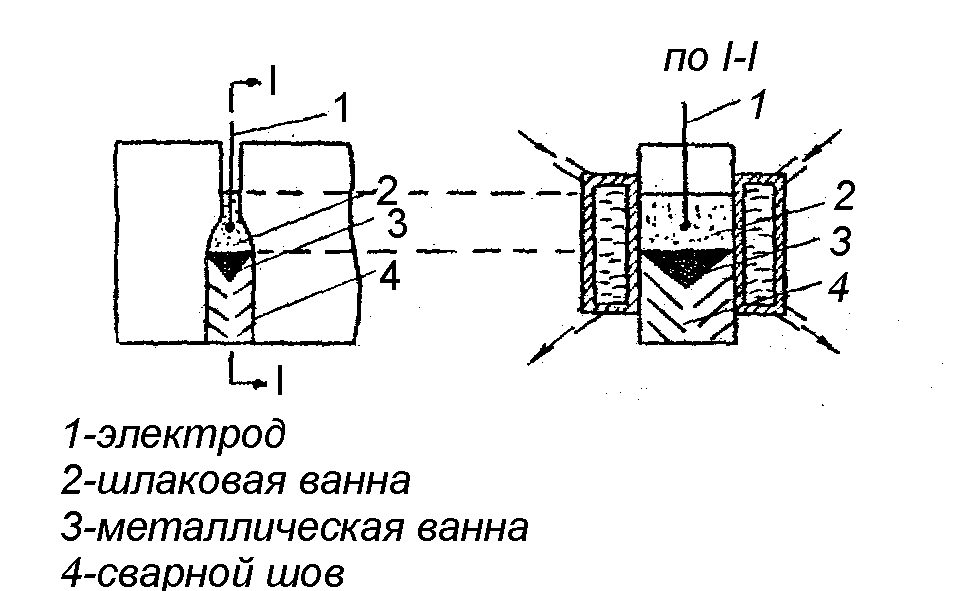
В пространство между кромками вертикально установленных деталей, приставной стальной или медной планкой и шлакоудерживающими медными ползунами подается флюс и одна или несколько сварочных проволок диаметром 2–3 мм. Сварка начинается с зажигания дуги под слоем флюса между электродными проволоками и приставной планкой. Планка имеет такую же толщину, как и свариваемые листы, она приваривается к нижней части стыка. Электроды подаются от сварочного агрегата. Флюс насыпается из специального бункера. Медные ползуны ставятся для предотвращения вытекания жидкого металла и шлака и ускорения затвердевания сварного шва, так как они охлаждаются водой.
После образования шлаковой ванны достаточной глубины, дуга гаснет и процесс сварки переходит из дугового в электрошлаковый. Подача проволоки и подача тока продолжаются и при прохождении тока через шлаковую ванну образуется достаточная теплота для расплавления проволоки и кромок основного металла. По мере расплавления металла и образования сварочного шва медные ползуны вместе с механизмом подачи проволоки перемещаются вверх. Заканчивают сварку на 20–30 мм выше верхней кромки свариваемых листов на специальной выводной планке. Сварка осуществляется всегда автоматически.
Минимальная толщина металла, свариваемого электрошлаковой сваркой, составляет 45–50 мм. Сварка металла меньшей толщины экономически невыгодна. Сварка выполняется без разделки кромок и за один проход.
При сварке основной металл подвержен сильному термическому воздействию, происходит рост зерен металла и ухудшение структуры. Поэтому изделия, полученные этим способом сварки, обязательно подвергают отжигу или нормализации.
Способы электрошлаковой сварки:
1. Сварка электродной проволокой. Этот способ применяют для сварки металла толщиной не более 500 мм, при любой длине шва. Электродная проволоки марки Св-Г2 выбирается диаметром 2–3 мм, сварочный ток в пределах 100–600 А.
Одним электродом без колебаний его в зазоре можно сваривать металл толщиной 60 мм. Общее количество электродов, необходимых для сварки, определяют:
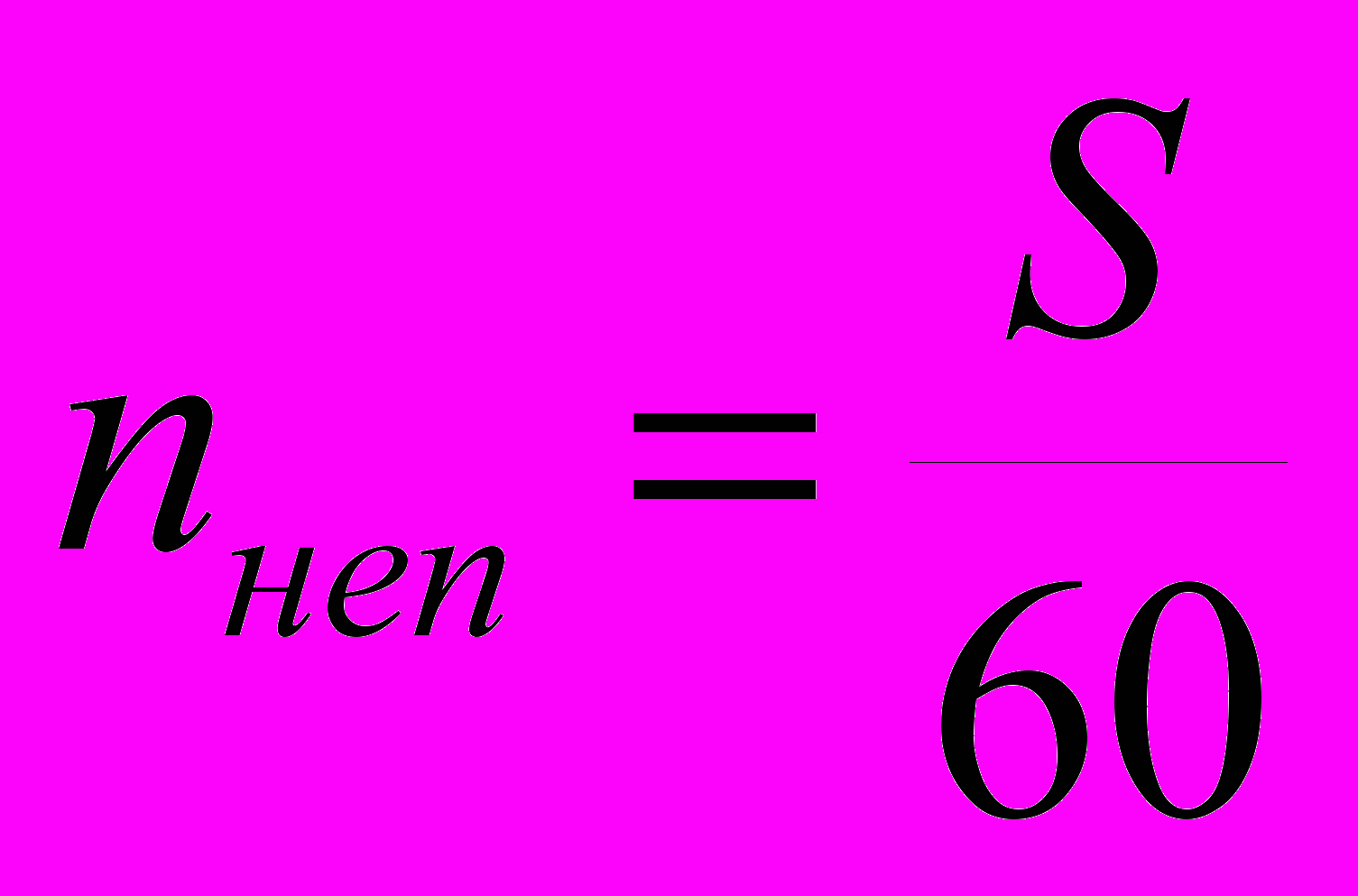
Для улучшения провара металла и равномерности его плавления делаются поперечные колебания электрода в зазоре, при этом общее количество электродов, необходимых для сварки, определяется:
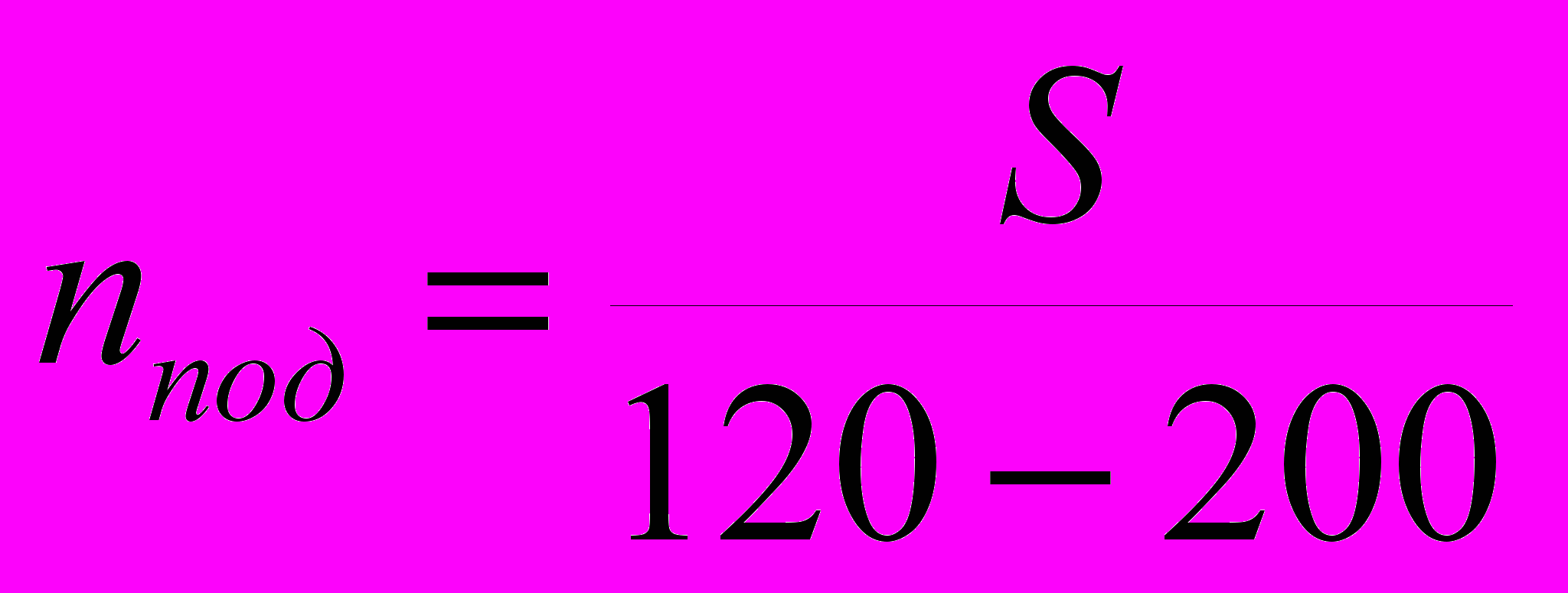
Следует иметь в виду, что общее количество электродов для сварки не должно превышать трех. При большем количестве электродов усложняется конструкция сварочного агрегата и технология сварки.
2. Для сварки металла толщиной свыше 500 мм и при длине шва не более 1 м применяется электрошлаковая сварка пластинами. Пластины выбираются шириной 200–300 мм, толщиной 1/3 зазора между листами, длина пластин выбирается равной 3,5 длины шва. Плотность тока составляет 0,6–2 А/мм2.
3. Для сварки деталей длиной более одного метра, толщиной более 500 мм, а также деталей переменного поперечного сечения применяется сварка плавящимся мундштуком. Мундштук представляет собой пластину, форма которой повторяет форму поперечного сечения свариваемых деталей.
При сварке благодаря литейной усадке шва установленный зазор между листами уменьшается, и это приводит к искажению размеров конструкции и появлению остаточных сварочных напряжений.. Поэтому в верхней части соединения зазор устанавливают больший, чем в нижней части, на 3–5 мм на каждый метр шва.
Плазменная сварка
Плазменная сварка –это способ обработки металлов плазменной струей.
Плазма – сильно ионизированный газ, состоящий из нейтральных атомов и молекул, ионов и электронов. Плазменная струя выделяется из столба дуги при помощи специальных устройств – дуговых плазменных горелок, работающих на постоянном токе. Температура плазменной струи 10000–30000оС.
Плазменной дугой сваривают углеродистые и нержавеющие стали, тугоплавкие и цветные металлы, а также неметаллические материалы толщиной от нескольких десятков микрометров и больше.
1
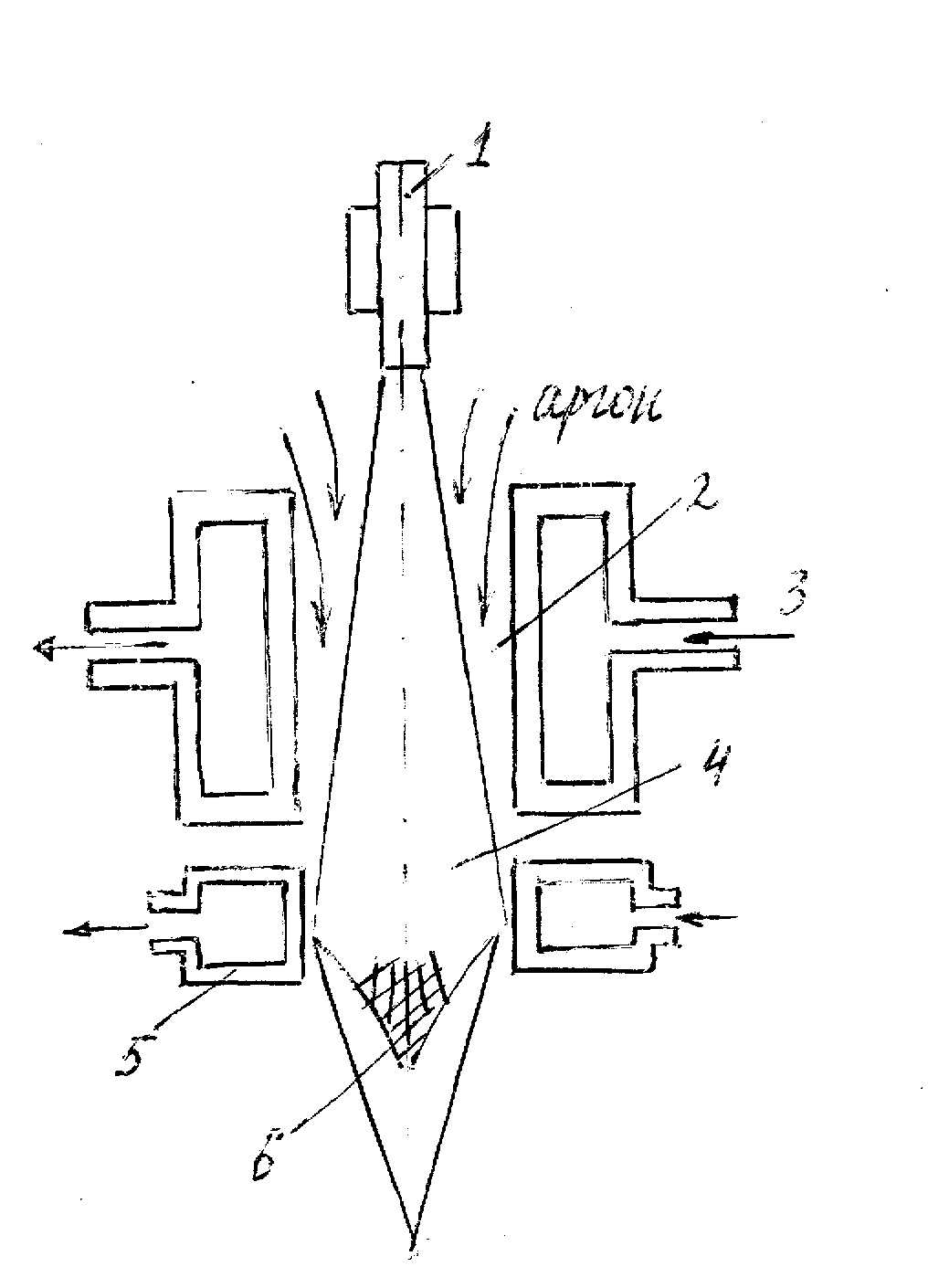
2–канал
3–каналы охлаждения
4-дуговой разряд
5–сопло
6–плазма
Дуговой разряд 4 возбуждается между электродом 1 и соплом 5. Вдоль дуги по каналу 2 пропускается газ –аргон, гелий, азот, водород и др. При увеличении тока столб дуги расширяться не может, так как пространство ограничено стенками горелки и к тому же дополнительно сжимается газовым потоком, поэтому температура столба дуги и степень ионизации газа резко возрастают. Практически весь газ, проходящий сквозь столб сжатой дуги, ионизируется и превращается в плазму. Головки охлаждаются водой через каналы.
Различают плазменную дугу прямого и косвенного действия. Дуга 4 прямого действия горит между вольфрамовым электродом 1 (катодом) и изделием (анодом). Дуга косвенного действия горит между вольфрамовым электродом 1 и медным соплом 5 горелки.
Сварка электронным лучом в вакууме
Сущность процесса сварки состоит в использовании кинетической энергии быстродвижущихся электронов в глубоком вакууме. Электроны, бомбардируя свариваемый металл, внедряются в него и затормаживаются в нем, теряя свою энергию. При этом их кинетическая энергия переходит в тепловую, вызывая нагрев металла. Температура в месте соударения может достигать 5000-6000оС.
1
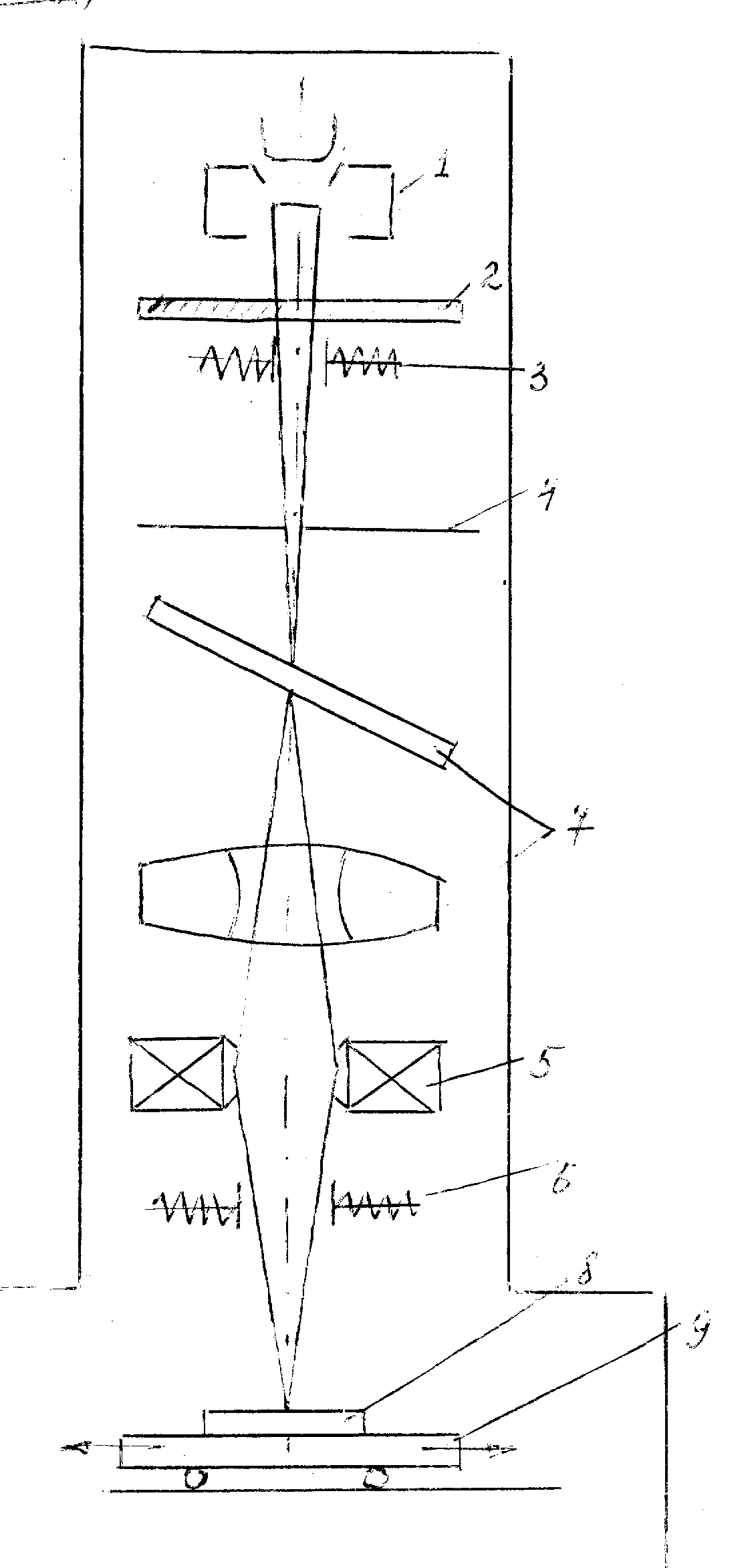
2–дисковый анод
3–юстированные катушки
4–диафрагма
5–магнитная линза
6–отклоняющие катушки
7–оптическая система
8–заготовка
9–стол
Электроны излучаются при нагреве катода 1, формируются в пучок анодом 2, имеющем отверстие, и под действием электрического поля, создаваемого высокой разностью потенциалов между катодом и анодом, ускоряются в вертикальном направлении. Это направление обеспечивается юстированными катушками 3, которые питаются постоянным регулируемым током.
Оптическая система 7 соединена с микроскопом и служит для наблюдения за процессом сварки при многократном увеличении. Заготовка может перемещаться на столе 9 и помещена в вакуумную камеру. Отклоняющая магнитная линза 5 направляет луч на обрабатываемое изделие.
Отсутствие окисления, характеризующее этот способ сварки, позволяет сваривать химически активные и тугоплавкие металлы: тантал, цирконий, вольфрам, титан, никель, медь, алюминий, магний и высоколегированные стали.
Важным достоинством электронно-лучевой сварки является возможность получения узкой и глубокой зоны проплавления с минимальной величиной зоны термического влияния. Это позволяет изготавливать конструкции с минимальным короблением и снижает возможность укрупнения зерна в зоне термического влияния.
Сварка лазерным лучом
Под сваркой лазерным лучом понимают светолучевую сварку мощным сконцентрированным световым потоком, получаемым в специальных установках, называемых лазерами. По концентрации нагрева металла этот способ сварки превосходит все известные способы.
С
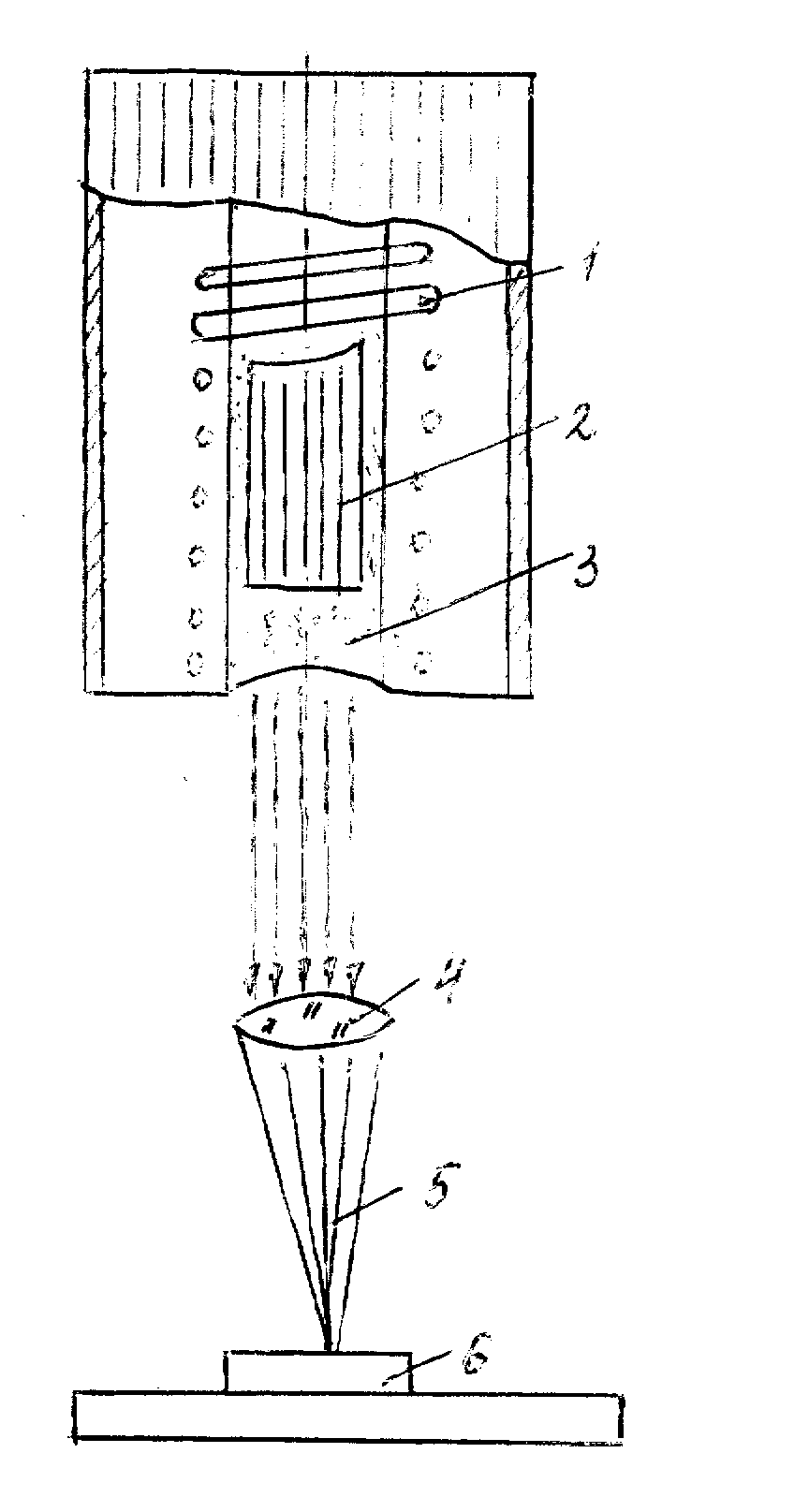
1– ксеноновая лампа (нагнетатель энергии)
2–рубиновый кристалл
3–охлаждающая система
4–линза
5–луч
6–свариваемые детали
Основной энергетический элемент ОКГ – кристалл рубина (кристалл окиси алюминия, содержащий 0,05% хрома). Ему придается форма стержня, длина и диаметр которого определяют мощность излучения. Торцы стержня полируют и подвергают серебрению для получения строго параллельных отражающих поверхностей. Выходную поверхность торца стержня делают полупрозрачной.
Возбуждение активного элемента (рубина) производится вспышкой ксеноновой лампы, которая питается от высоковольтного импульсного источника. При освещении лампой рубина значительная часть атомов хрома переходит в возбужденное состояние. Возвращаясь в исходное состояние, каждый атом хрома испускает фотон. При этом фотоны, направленный под углом к оси стержня, мгновенно покидают его пределы, а фотоны, направленные вдоль оси стержня, взаимодействуя с возбужденными атомами, способствуют образованию фотонов того же направления. Этот процесс протекает лавинообразно. Интенсивность пучка фотонов растет вследствие многократного отражения от торцов кристалла. В результате этого наступает момент появления эффекта квантового усиления, и тогда с полупрозрачного торца стержня за тысячные доли секунды выбрасывается интенсивный узконаправленный поток фотонов (луч света). Луч света фокусируется линзой и направляется на обрабатываемое изделие.
С помощью лазера сваривают однородные и разнородные металлы: алюминий с никелем, золото с германием, медь, алюминий, вправляют тонкую проволоку в стекло, сваривают тугоплавкие металлы (детали из титана, ниобия, бериллия, вольфрама), керамику. Используют в медицине – для соединения живых тканей.
ОКГ могут работать на твердых, жидких и газообразных телах.