«Детали машин»
Вид материала | Реферат |
- Программа дисциплины по кафедре Детали машин детали машин и основы конструирования, 355.21kb.
- Программа дисциплины по кафедре Детали машин детали машин и механизмов, 575.22kb.
- Программа дисциплины по кафедре Детали машин теория механизмов и детали машин, 422.13kb.
- Методические указания к изучениюдисциплины «детали машин», 189.59kb.
- Программа вступительного экзамена в аспирантуру по специальной дисциплине 05. 02., 266.3kb.
- М. А. Копин Лабораторные и лабораторно-практические работы по дисциплине «Детали машин, 380.55kb.
- Чубенко Елена Филипповна Детали машин и основы конструирования конспект, 86.56kb.
- Программа дисциплины по кафедре Детали машин теория механизмов и машин, 480.47kb.
- Название курса: Детали машин, 59.22kb.
- Рабочей программы дисциплины Детали машин и основы конструирования по направлению подготовки, 37.93kb.

Содержание
Введение
1 Определение основных параметров элементов привода и выбор
электродвигателя
1.1 Определение нагрузочно-кинематических параметров рабочего органа
1.2 Определение нагрузочно-кинематических параметров электродвигателя
1.3 Определение серии и конструктивного исполнения электродвигателя
1.4 Выбор электродвигателя
1.5 Определение передаточного числа редуктора и его распределение
между ступенями
1.6 Выбор типа передач
2 Входные данные для расчета передач привода
3 Проектирование передач привода
3.1 Проектировочный расчет червячной передачи z1-z2
3.2 Проектировочный расчет цилиндрической косозубой передачи z3-z4
3.3 Проектировочный расчет цилиндрической прямозубой передачи z5-z6
4 Проектирование валов редуктора
4.1 Проектировочный расчет валов
4.2 Выбор подшипников
5 Проверочные расчеты
5.1 Проверочный расчет червячной передачи z1-z2
5.2 Проверочный расчет цилиндрической косозубой передачи z3-z4
5.3 Проверочный расчет цилиндрической прямозубой передачи z5-z6
5.4 Проверочный расчет валов редуктора
5.5 Расчет подшипников на долговечность
5.6 Расчет соединений, передающих крутящий момент
6 Выбор и расчет муфт
6.1 Выбор муфты входного вала
7 Конструирование и расчет элементов корпуса
7.1 Конструирование основных элементов
7.2 Конструирование вспомогательных элементов
8 Выбор смазки
Выводы
Перечень ссылок
Реферат
Пояснительная записка к курсовому проекту по дисциплине «Детали машин» содержит: 55 страниц, 12 таблиц, 11 рисунка, 6 источников.
Объект исследования: редуктор привода шнеков-смесителей для подачи флюса при непрерывной сварке в механосборочном цеху.
Цель работы: спроектировать трехступенчатый редуктор привода шнеков-смесителей.
В курсовом проекте проведен расчет входных данных для проектирования привода: передаточных чисел, частот вращения, мощности, вращающих моментов для всех валов редуктора.
Проведены проектировочные расчеты передач, валов, подшипников, шпоночных соединений. Кроме того, приведены проверочные расчеты передач редуктора и валов. Выбраны стандартизованные детали, тип смазки элементов привода. Описана схема сборки редуктора.
Разработаны: чертеж общего вида редуктора, сборочный чертеж редуктора в трех проекциях и рабочие чертежи четырех деталей
ШНЕК, ПРИВОД, ЭЛЕКТРОДВИГАТЕЛЬ, МУФТА, ВАЛ, ШЕСТЕРНЯ, КОЛЕСО ЗУБЧАТОЕ, МОДУЛЬ, СМАЗКА
Введение
В курсовом проекте выполнен расчет и проектирование механизма привода шнеков-смесителей. Для выполнения указанных в техническом задании условий по входным данным выбран электродвигатель, спроектирован редуктор. Разработаны чертежи: вида привода, сборочный чертеж редуктора, общего, рабочие чертежи деталей редуктора.
Выполнен выбор и проверка подшипников качения, в которых установлены валы редуктора. Рассчитаны конструктивные элементы корпуса. Разработаны спецификации на редуктор и привод.
1Определение основных параметров элементов привода и выбор электродвигателя
1.1Определение нагрузочно-кинематических параметров рабочего органа
К нагрузочно-кинематическим параметрам рабочего органа привода относятся:
- крутящий момент , [Н·м];
- мощность , [кВт];
- угловая скорость , [].
Кинематическая схема привода машины показана на рис.1.1.
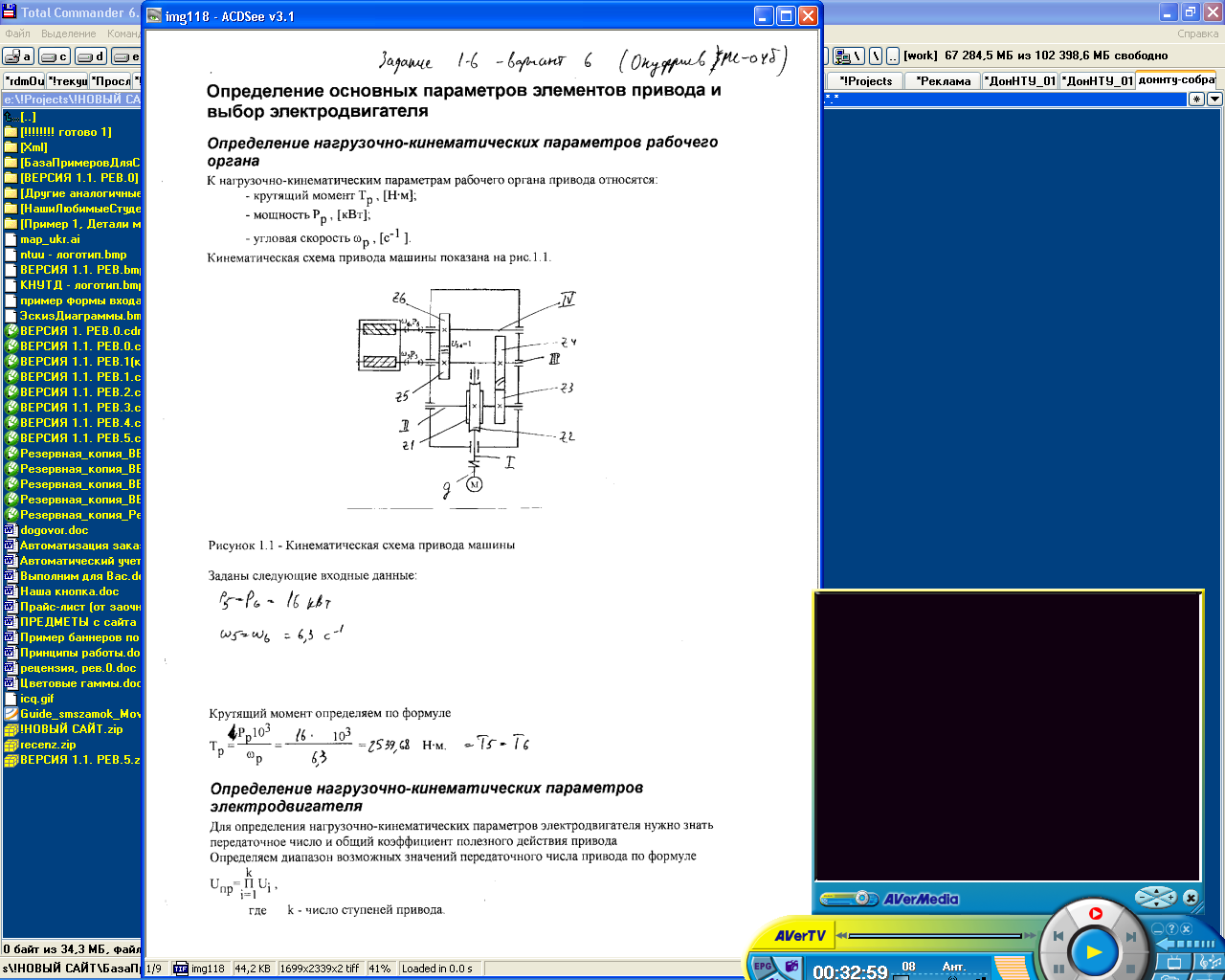
Рисунок 1.1 - Кинематическая схема привода машины
Заданы следующие входные данные:
Крутящий момент определяем по формуле
= Н·м.
1.2Определение нагрузочно-кинематических параметров электродвигателя
Для определения нагрузочно-кинематических параметров электродвигателя нужно знать передаточное число и общий коэффициент полезного действия привода
Определяем диапазон возможных значений передаточного числа привода по формуле
,
где k - число ступеней привода.
= =
где - диапазон оптимальных передаточных чисел для передачи 1-2, для конической/цилиндрической/червячной передачи =( ... );
- диапазон оптимальных передаточных чисел для передачи 3-4, для конической/цилиндрической/червячной передачи =( ... );
- диапазон оптимальных передаточных чисел для передачи 5-6, для конической/цилиндрической/червячной передачи =( ... );
- диапазон оптимальных передаточных чисел для передачи 7-8, для конической/цилиндрической/червячной передачи =( ... ).
Соответственно, диапазон возможных значений угловых скоростей ротора электродвигателя имеет значение
= =
Соответственный диапазон частоты вращения ротора электродвигателя:
= = об/мин.
Коэффициент полезного действия привода определяем по формуле:
,
где m - количество элементов привода, в которых имеют место потери механической энергии.
= ,
где - кпд компенсирующей муфты, =0,98;
- кпд уполтнения, =0,99;
- кпд подшипников качения, =0,99;
- кпд передачи 1-2, для конической/цилиндрической/червячной =0,98;
- кпд передачи 3-4, для конической/цилиндрической/червячной =0,98;
- кпд передачи 5-6, для конической/цилиндрической/червячной =0,98;
- кпд передачи 7-8, для конической/цилиндрической/червячной =0,98;
=
Соответствующее значение максимальной мощности на валу электродвигателя составляет
= кВт.
1.3Определение серии и конструктивного исполнения электродвигателя
В качестве электродвигателя для привода машины применим промышленный трехфазный асинхронный электродвигатель с короткозамкнутым ротором. Такие двигатели имеют наиболее простую конструкцию, наименьшую стоимость и минимальные требования к обслуживанию по сравнению с другими электродвигателями.
Принимаем серию 4А общего применения с чугунным корпусом (ГОСТ 19523-81) для климатических условий типа У (нормальные - сухое, чистое, отапливаемое помещение) категории 3.
Конструктивное исполнение электродвигателя принимаем следующее: с креплением на лапах/с фланцевым креплением.
1.4Выбор электродвигателя
Т.к. нагрузка на привод во время эксплуатации изменяется, выполнять выбор электродвигателя по максимальной мощности не целесообразно. Поэтому, на основе нагрузочной диаграммы (см. рис.1.2) определяем среднеквадратичную мощность на валу электродвигателя, т.е. такую условную статическую мощность, при которой нагрев электродвигателя будет таким же, как и в случае работы с переменной нагрузкой:
= ,
где - коэффициент приведения эксплуатационного нагружения к эквивалентной тепловой мощности двигателя.
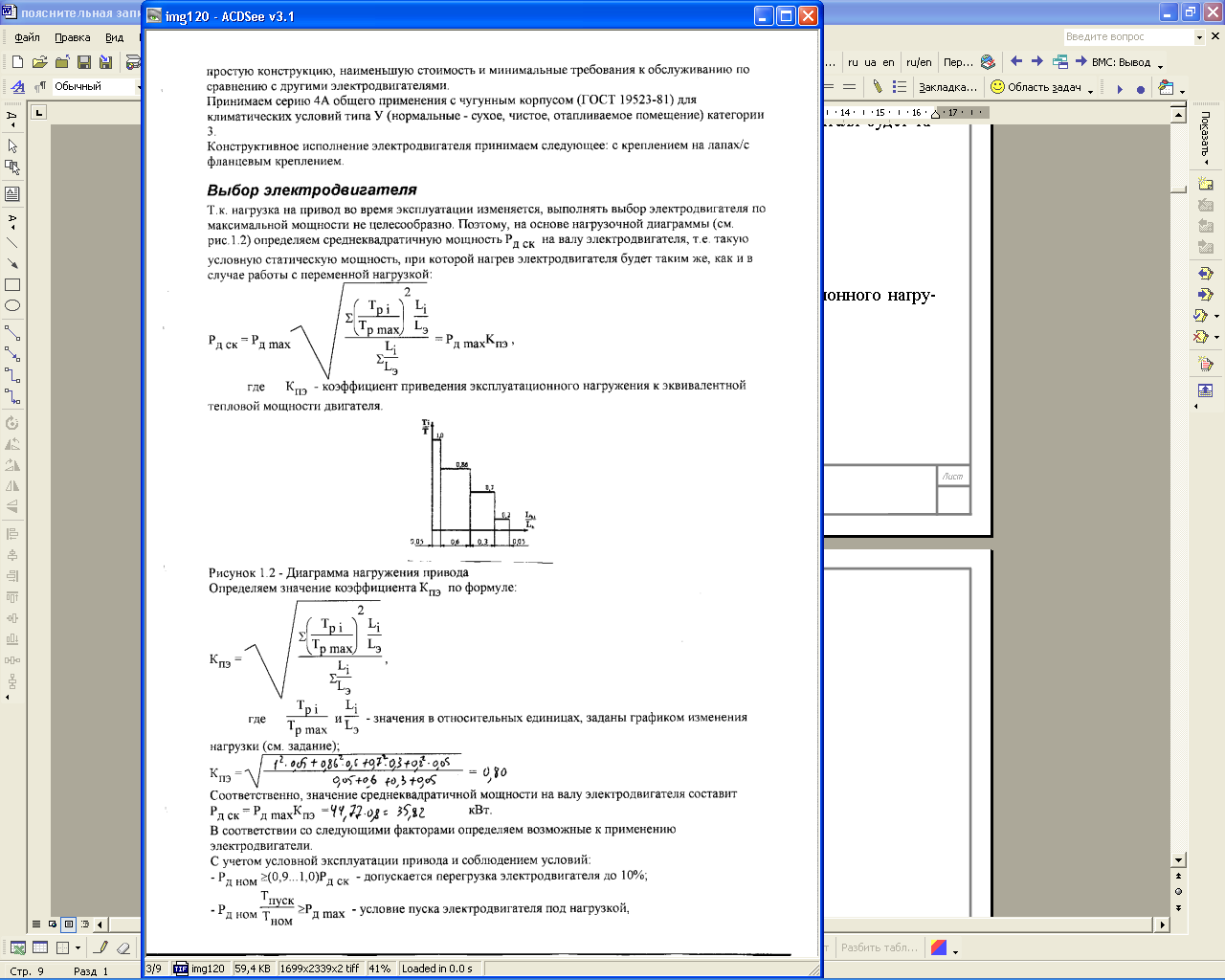
Рисунок 1.2 - Диаграмма нагружения привода
Определяем значение коэффициента по формуле:
,
где и - значения в относительных единицах, заданы графиком изменения нагрузки (см. задание);
=
Соответственно, значение среднеквадратичной мощности на валу электродвигателя составит
= кВт.
В соответствии со следующими факторами определяем возможные к применению электродвигатели.
С учетом условной эксплуатации привода и соблюдением условий:
- ³(0,9...1,0) - допускается перегрузка электродвигателя до 10%;
- ³ - условие пуска электродвигателя под нагрузкой,
где - соотношение пускового и номинального моментов электродвигателя;
- номинальная частота электродвигателя должна попадать в диапазон .
Таблица 1.1 - Параметры возможных к применению электродвигателей
Принимаем электродвигатель с минимальной массой (относительной себестоимостью) .
1.5Определение передаточного числа редуктора и его распределение между ступенями
Угловая скорость вращения вала ротора электродвигателя
= = .
Передаточное число привода
= = .
Передаточное число редуктора
Для
Тогда = =
=
= ·100% = % < =4%, следовательно, расчет выполнен удовлетворительно.
1.6Выбор типа передач редуктора
Ступень 1 –
…………..
2Входные данные для расчета передач привода
Определяем время эксплуатации привода по формуле:
, [час]
где = 41 - средняя длительность рабочей недели (часов);
z - количество смен за сутки, z= ;
=50 - среднее количество недель за год;
- коэффициент использования привода в течении смены, = ;
L - длительность эксплуатации, L= лет;
= часов.
Режим работы привода принимается нереверсивным.
Определяем нагрузочно-кинематические параметры на соответствующих валах
Вал д (вал электродвигателя)
3проектирование передач привода
3.1Проектировочный расчет червячной
передачи z1-z2
Входные данные:
- частота вращения шестерни =2945 об/мин;
- номинальный вращающий момент на шестерне =139500 Н·мм;
- частота вращения колеса =105,18 об/мин;
- номинальный вращающий момент на колесе =3123410 Н·мм;
- передаточное число =28;
- число заходов червяка =2;
- число зубьев червячного колеса =56.
Выбор материалов для изготовления червячного колеса и червяка
Ориентировочное значение скорости скольжения между зубьями червячного колеса и витками червяка
= = 15,08 м/с.
Так как предварительный расчет показал значительное отличие ориентировочного значения скорости скольжения от фактического принимаем = 18,87 м/с.
Назначаем материал червяка и червячного колеса исходя из ориентировочного значения скорости скольжения между зубьями червячного колеса и витками червяка:
для червяка
материал - сталь 45;
термообработка - закалка ТВЧ;
твердость - HRC48...53.
для червячного колеса
материал - Бр010Ф1;
способ отливки - в песок;
(механические свойства материала червячного колеса, соответствующие твердости червяка и характеристикам передачи:)
предел прочности =180 МПа; [2, c.28, табл.4.4]
предел текучести =100 МПа; [2, c.28, табл.4.4]
условное допустимое контактное напряжение =160 МПа; [2, c.26, табл.4.2]
условное допустимое изгибное напряжение для нереверсивных передач =50 МПа; [2, c.28, табл.4.4]
условное допустимое изгибное напряжение для реверсивных передач =36 МПа; [2, c.28, табл.4.4]
предельное допустимое напряжение при кратковременных перегрузках =100 МПа. [2, c.28, табл.4.5]
Определение допустимых напряжений материала червячного колеса
Допустимые напряжения при расчете на контактную прочность
где - условное допустимое напряжение при расчете на контактную прочность =160 МПа;
- коэффициент долговечности.
Коэффициент эквивалентного нагружения
,
где - относительное время действия момента за расчетный термин службы ;
- число часов работы передачи при крутящем моменте .
==0,45;
=60·2945·24395·0,45=6,93· циклов;
=0,79.
Принимаем =0,79.
= 126,4 МПа.
Допустимые напряжения при расчете на изгибную прочность
где , - условные допустимые напряжения при расчете на изгибную прочность (при базовом числе циклов ) для нереверсивных и реверсивных передач соответственно =50 МПа, =36 МПа;
- коэффициент долговечности.
Коэффициент эквивалентного нагружения
,
==0,217;
=60·105,18·24395·0,217=33,41· циклов;
=0,68.
Принимаем =0,68.
= 34 МПа.
Определение расчетной нагрузки
Расчетная нагрузка определяется умножением номинальной нагрузки на коэффициент нагрузки К:
…………….
3.2Проектировочный расчет цилиндрической косозубой передачи z3-z4
Входные данные:
- частота вращения шестерни =105,18 об/мин;
- номинальный вращающий момент на шестерне =3093550 Н·мм;
- частота вращения колеса =58,44 об/мин;
- номинальный вращающий момент на колесе =5454610 Н·мм;
- передаточное число =1,8.
Назначение уровня твердости и вида термической обработки зубчатых колес
Предъявляемые требования к габаритам передачи для привода шнеков-смесителей при типе производства - единичное: не жесткие.
В соответствии с предъявляемыми требованиями принимаем: вид термической обработки - нормализация; твердость поверхности зуба HB160...200; предел изгибной прочности =280...360 МПа.
Приближенное определение модуля передачи
Значение модуля определяем из условия обеспечения изгибной прочности зубьев при усредненных параметрах передачи:
,
где - предварительные допускаемые напряжения при расчете зубьев на изгибную прочность,
, для нереверсивных передач.
Принимаем =320 МПа.
= 320/2 = 160 МПа.
= 7,52 мм.
Принимаем =8 мм.
Выбор материала зубчатых колес, определение допустимых напряжений
Для выбор марки стали необходимо иметь следующую дополнительную информацию.
Предварительно определяем диаметры окружностей вершин зубьев шестерни и колеса:
=20;
=8(20+2)=176 мм;
=20·1,8=36;
=8(36+2)=304 мм;
Принимаем способ получения заготовки:
для шестерни - поковка;
для колеса - поковка.
Предварительно определяем ширину шестерни и колеса:
=(12...15)8=96...120 мм.
Принимаем =110 мм.
Определяем конструктивное исполнение шестерни
,
где T - вращающий момент на валу шестерни, Т=3093550 Н·мм;
- допускаемые напряжения при кручении, предварительно принимаем =20 МПа;
= 91,79 мм.
Принимаем =95 мм.
При =176/95=1,85<2, шестерня изготовляется монолитно с валом (вал-шестерня).
= 176/2=88 мм;
= 8·8=64 мм;
Назначаем марку стали и вид термической обработки с учетом принятых значений предельных напряжений , а также механические свойства материала с учетом толщины размера сечения S проектируемых зубчатых колес:
для шестерни
материал - сталь 50Л;
термообработка - нормализация;
твердость - HB160...210;
(механические свойства материала:)
предел прочности =600 МПа;
предел текучести =400 МПа;
предел контактной выносливости =440 МПа;
предел изгибной выносливости =330 МПа.
для колеса
материал - сталь 50Л;
термообработка - нормализация;
твердость - HB160...210;
(механические свойства материала:)
=600 МПа; =400 МПа; =440 МПа; =330 МПа.
Определяем допустимые напряжения при расчете на изгибную прочность
Для шестерни:
,
где - предел изгибной выносливости материала зубчатого колеса, =330 МПа;
- допустимый коэффициент запаса прочности по изгибным напряжениям, для вида ТО - нормализация =1,7;
- коэффициент, который учитывает характер изменения напряжений изгиба в реверсивных и нереверсивных передачах. В нашем случае =1,
- коэффициент долговечности, который учитывает повышение предельных напряжений при числе циклов нагружения меньших базового,
³1,
где q=6 (нормализация приводит к однородной структуре материала);
=4 - базовое число циклов нагружений;
- эквивалентное число циклов нагружений;
,
где n - частота вращения зубчатого колеса;
- срок службы передачи;
- коэффициент эквивалентности нагрузки;
,
где - относительное время действия момента за расчетный термин службы ;
- число часов работы передачи при крутящем моменте .
==0,328;
=60·105,18·24395·0,328=50,5· циклов;
=0,66.
Принимаем =1.
= 194,12 МПа.
Для колеса:
=330 МПа; =1; q=6 (нормализация приводит к однородной структуре материала); =4.
==0,328;
=60·58,44·24395·0,328=28,06· циклов;
=0,72.
Принимаем =1.
= 194,12 МПа.
Определяем допустимые напряжения при расчете на контактную прочность
Для шестерни:
,
где - предел контактной выносливости материала зубчатого колеса, =440 МПа;
- допустимый коэффициент запаса прочности по контактным напряжениям, для вида ТО - нормализация =1,1;
- коэффициент долговечности, который учитывает повышение предельных напряжений при числе циклов нагружения меньших базового,
³1,
- базовое число циклов нагружений, при твердости материала HB185 =10 циклов;
- эквивалентное число циклов нагружений;
,
где n - частота вращения зубчатого колеса;
- срок службы передачи;
- коэффициент эквивалентности нагрузки;
,
где - относительное время действия момента за расчетный термин службы ;
- число часов работы передачи при крутящем моменте .
==0,535;
=60·105,18·24395·0,535=82,36· циклов;
=0,7.
Принимаем =1.
= 400 МПа.
Для колеса:
=440 МПа; =1,1 (для вида ТО - нормализация); =10 циклов (при твердости материала HB185);
==0,535;
=60·58,44·24395·0,535=45,76· циклов;
=0,78.
Принимаем =1.
= 400 МПа.
Проектировочный расчет передачи на контактную прочность зубьев
Межосевое расстояние
,
где C=270 (для косозубых колес);
K - коэффициент нагрузки, предварительно принимаем K=1,7 с последующим уточнением;
- коэффициент ширины колеса, принимаем =0,315.
=449,59 мм.
Округляем межосевое расстояние до ближайшего числа из ряда Ra40 ГОСТ 6636-69 [2, c.17, табл.2.5] =450 мм.
Определяем ширину колеса
=0,315·450=141,75 мм.
Округляем ширину колеса до ближайшего числа из ряда Ra40 ГОСТ 6636-69 [2, c.17, табл.2.5] =150 мм.
Определяем ширину шестерни
= + 5 мм = 150+5=155 мм.
Округляем ширину шестерни до ближайшего числа из ряда Ra40 ГОСТ 6636-69 [2, c.17, табл.2.5] =160 мм.
Модуль передачи определяем конструктивно
=(4,5...9) мм.
Округляем модуль согласно ГОСТ 9563-60 [2, с.16, табл.2.4] =6 мм.
Определяем числа зубьев
суммарное число зубьев
принимаем b=13°
= = 146,16, принимаем =146
число зубьев шестерни
= 52,1, принимаем =52
число зубьев колеса
= - = 146-52=94.
Уточняем передаточное число
= =1,81.
Уточняем угол наклона зубьев
= arccos 0,9733=13,27°=13°16'0''
Определяем основные геометрические размеры зубчатых колес
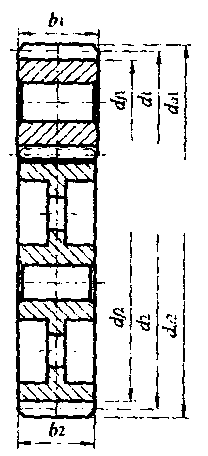
Диаметры основных и делительных окружностей
= = 320,559 мм;
= = 579,472 мм;
Диаметры окружностей впадин
= 320,559-2,5·6=305,559 мм;
= 579,472-2,5·6=564,472 мм;
Диаметры окружностей выступов
= 320,559+2·6=332,559 мм;
= 579,472+2·6=591,472 мм.
3.3Проектировочный расчет цилиндрической прямозубой передачи z5-z6
Входные данные:
- частота вращения шестерни =58,44 об/мин;
- номинальный вращающий момент на шестерне =2730670 Н·мм;
- частота вращения колеса =58,44 об/мин;
- номинальный вращающий момент на колесе =2676750 Н·мм;
- передаточное число =1.
Назначение уровня твердости и вида термической обработки зубчатых колес
Предъявляемые требования к габаритам передачи для привода шнеков-смесителей при типе производства - единичное: не жесткие.
В соответствии с предъявляемыми требованиями принимаем: вид термической обработки - улучшение; твердость поверхности зуба HB200...320; предел изгибной прочности =360...570 МПа.
Приближенное определение модуля передачи
Значение модуля определяем из условия обеспечения изгибной прочности зубьев при усредненных параметрах передачи:
,
где - предварительные допускаемые напряжения при расчете зубьев на изгибную прочность,
, для нереверсивных передач.
Принимаем =465 МПа.
= 465/2 = 232,5 МПа.
= 7,96 мм.
Принимаем =8 мм.
Выбор материала зубчатых колес, определение допустимых напряжений
Для выбор марки стали необходимо иметь следующую дополнительную информацию.
Предварительно определяем диаметры окружностей вершин зубьев шестерни и колеса:
=20;
=8(20+2)=176 мм;
=20·1=20;
=8(20+2)=176 мм;
Принимаем способ получения заготовки:
для шестерни - поковка;
для колеса - поковка.
Предварительно определяем ширину шестерни и колеса:
=(8...12)8=64...96 мм.
Принимаем =80 мм.
Определяем конструктивное исполнение шестерни
,
где T - вращающий момент на валу шестерни, Т=2730670 Н·мм;
- допускаемые напряжения при кручении, предварительно принимаем =20 МПа;
= 88,05 мм.
Принимаем =90 мм.
При =176/90=1,96<2, шестерня изготовляется монолитно с валом (вал-шестерня).
= 176/2=88 мм;
= 8·8=64 мм;
Назначаем марку стали и вид термической обработки с учетом принятых значений предельных напряжений , а также механические свойства материала с учетом толщины размера сечения S проектируемых зубчатых колес:
для шестерни
материал - сталь 40Х;
термообработка - улучшение;
твердость - HB250...280;
(механические свойства материала:)
предел прочности =900 МПа;
предел текучести =750 МПа;
предел контактной выносливости =600 МПа;
предел изгибной выносливости =480 МПа.
для колеса
материал - сталь 40Х;
термообработка - улучшение;
твердость - HB250...280;
(механические свойства материала:)
=900 МПа; =750 МПа; =600 МПа; =480 МПа.
Определяем допустимые напряжения при расчете на изгибную прочность
Для шестерни:
,
где - предел изгибной выносливости материала зубчатого колеса, =480 МПа;
- допустимый коэффициент запаса прочности по изгибным напряжениям, для вида ТО - улучшение =1,7;
- коэффициент, который учитывает характер изменения напряжений изгиба в реверсивных и нереверсивных передачах. В нашем случае =1,
- коэффициент долговечности, который учитывает повышение предельных напряжений при числе циклов нагружения меньших базового,
³1,
где q=6 (улучшение приводит к однородной структуре материала);
=4 - базовое число циклов нагружений;
- эквивалентное число циклов нагружений;
,
где n - частота вращения зубчатого колеса;
- срок службы передачи;
- коэффициент эквивалентности нагрузки;
,
где - относительное время действия момента за расчетный термин службы ;
- число часов работы передачи при крутящем моменте .
==0,328;
=60·58,44·24395·0,328=28,06· циклов;
=0,72.
Принимаем =1.
= 282,35 МПа.
Для колеса:
=480 МПа; =1; q=6 (улучшение приводит к однородной структуре материала); =4.
==0,328;
=60·58,44·24395·0,328=28,06· циклов;
=0,72.
Принимаем =1.
= 282,35 МПа.
Определяем допустимые напряжения при расчете на контактную прочность
Для шестерни:
,
где - предел контактной выносливости материала зубчатого колеса, =600 МПа;
- допустимый коэффициент запаса прочности по контактным напряжениям, для вида ТО - улучшение =1,1;
- коэффициент долговечности, который учитывает повышение предельных напряжений при числе циклов нагружения меньших базового,
³1,
- базовое число циклов нагружений, при твердости материала HB265 =23 циклов;
- эквивалентное число циклов нагружений;
,
где n - частота вращения зубчатого колеса;
- срок службы передачи;
- коэффициент эквивалентности нагрузки;
,
где - относительное время действия момента за расчетный термин службы ;
- число часов работы передачи при крутящем моменте .
==0,535;
=60·58,44·24395·0,535=45,76· циклов;
=0,89.
Принимаем =1.
= 545,45 МПа.
Для колеса:
=600 МПа; =1,1 (для вида ТО - улучшение); =23 циклов (при твердости материала HB265);
==0,535;
=60·58,44·24395·0,535=45,76· циклов;
=0,89.
Принимаем =1.
= 545,45 МПа.
Проектировочный расчет передачи на контактную прочность зубьев
Межосевое расстояние
,
где C=310 (для прямозубых колес);
K - коэффициент нагрузки, предварительно принимаем K=1,6 с последующим уточнением;
- коэффициент ширины колеса, принимаем =0,25.
=353,75 мм.
Округляем межосевое расстояние до ближайшего числа из ряда Ra40 ГОСТ 6636-69 [2, c.17, табл.2.5] =360 мм.
Определяем ширину колеса
=0,25·360=90 мм.
Округляем ширину колеса до ближайшего числа из ряда Ra40 ГОСТ 6636-69 [2, c.17, табл.2.5] =90 мм.
Определяем ширину шестерни
= + 5 мм = 90+5=95 мм.
Округляем ширину шестерни до ближайшего числа из ряда Ra40 ГОСТ 6636-69 [2, c.17, табл.2.5] =95 мм.
Модуль передачи определяем конструктивно
=(3,6...7,2) мм.
Округляем модуль согласно ГОСТ 9563-60 [2, с.16, табл.2.4] m=6 мм.
Определяем числа зубьев
суммарное число зубьев
= = 120 - целое число, число зубьев шестерни
= 60, принимаем =60
число зубьев колеса
= - = 120-60=60.
Уточняем передаточное число
= =1.
Определяем основные геометрические размеры зубчатых колес
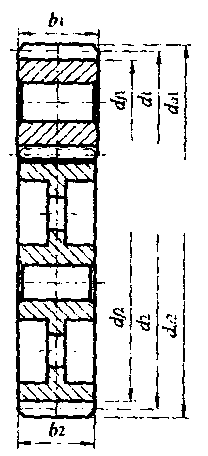
Диаметры основных и делительных окружностей
= 6·60 = 360 мм;
= 6·60 = 360 мм;
Диаметры окружностей впадин
= 360-2,5·6=345 мм;
= 360-2,5·6=345 мм;
Диаметры окружностей выступов
= 360+2·6=372 мм;
= 360+2·6=372 мм.
4ПРОЕКТИРОВАНИЕ ВАЛОВ РЕДКТОРА
4.1Проектировочный расчет валов
входной вал
d³ =32,7 мм;
Принимаем диаметр под подшипник dп=65 мм (с учетом размещения на валу муфты);
промежуточной вал
d³ =91,8 мм;
Принимаем диаметр под подшипник dп=95 мм;
выходной вал 0
d³ =110,1 мм;
Принимаем диаметр под подшипник dп=110 мм (с учетом размещения на валу муфты);
выходной вал 1
d³ =86,9 мм;
Принимаем диаметр под подшипник dп=90 мм (с учетом размещения на валу муфты).
4.2Выбор подшипников
входной вал
Принимаем роликоподшипники радиально-упорные конические однорядные № 7313 ГОСТ 333-79
d=65 мм; D=140 мм; B=33 мм; C=134000 Н; =111000 Н;
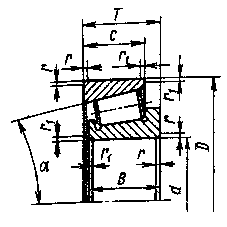
промежуточной вал
Принимаем роликоподшипники радиально-упорные конические однорядные № 7219 ГОСТ 333-79
d=95 мм; D=170 мм; B=32 мм; C=145000 Н; =131000 Н;
выходной вал 1
Принимаем роликоподшипники радиально-упорные конические однорядные № 7522 ГОСТ 333-79
d=110 мм; D=200 мм; B=53 мм; C=291000 Н; =296000 Н;
выходной вал 2
Принимаем шарикоподшипники радиальные однорядные № 218 ГОСТ 8338-75
d=90 мм; D=160 мм; B=30 мм; C=75300 Н; =61700 Н;
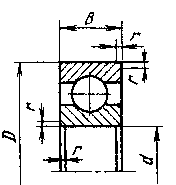
5ПРОВЕРОЧНЫЕ РАСЧЕТЫ
5.1Проверочный расчет червячной передачи z1-z2
Уточнение скорости скольжения
Значение скорости скольжения
= 19,66 м/с.
Проверочный расчет зубьев червячного колеса на контактную прочность
Расчет заключается в определении фактических контактных напряжений и сравнении их с допустимыми
£
= 122,46 МПа.
= 122,46 < = 126,4, контактная прочность зубьев червячного колеса обеспечена.
Проверочный расчет зубьев червячного колеса на изгибную прочность
Условие изгибной прочности
£ ,
где - тангенциальная сила,
= 8924,03 Н,
= 1,06·1,2 = 1,27;
…………………
5.2Проверочный расчет цилиндрической косозубой передачи z3-z4
Так как после проектировочного расчета уточненные параметры передачи, как правило, отличаются от предварительно принятых, выполняем проверочный расчет как на контактную прочность, так и на прочность при изгибе.
Назначаем степень точности изготовления зубчатой передачи в зависимости от окружной скорости и других эксплуатационных и технических требований
= = 1,77 м/с.
По данным [2, с.22, табл.3.1] принимаем степень точности передачи по норме плавности 9, шероховатость рабочих поверхностей зубьев Rz20...10.
Уточняем расчетную нагрузку
,
где - полезная или номинальная нагрузка, в предположении, что она распределяется по длине зубьев и между зубьями равномерно и прикладывается статично;
К - коэффициент нагрузки, учитывающий дополнительные нагрузки на зубчатые колеса (принято K==);
где - коэффициент неравномерности распределения нагрузки по длине зуба;
…………..
5.3Проверочный расчет цилиндрической прямозубой передачи z5-z6
Так как после проектировочного расчета уточненные параметры передачи, как правило, отличаются от предварительно принятых, выполняем проверочный расчет как на контактную прочность, так и на прочность при изгибе.
Назначаем степень точности изготовления зубчатой передачи в зависимости от окружной скорости и других эксплуатационных и технических требований
= = 1,1 м/с.
По данным [2, с.22, табл.3.1] принимаем степень точности передачи по норме плавности 9, шероховатость рабочих поверхностей зубьев Rz20...10.
Уточняем расчетную нагрузку
,
где - полезная или номинальная нагрузка, в предположении, что она распределяется по длине зубьев и между зубьями равномерно и прикладывается статично;
К - коэффициент нагрузки, учитывающий дополнительные нагрузки на зубчатые колеса (принято K==);
где - коэффициент неравномерности распределения нагрузки по длине зуба;
………………..
5.4Проверочный расчет валов редуктора
Основные критерии работоспособности валов - прочность и жесткость. Прочность валов определяют размером и характером напряжений, возникающих под влиянием сил, действующих со стороны установленных на них деталей машин. В общем случае в валах возникает напряжение изгиба (от поперечных сил), нормальные напряжения растяжения-сжатия (от осевых сил) и касательные напряжения кручения (от вращающего момента), т.е. вал находится в условиях сложного напряженно состояния. Нормальные напряжения, а иногда и касательные, изменяются циклически, поэтому основной причиной разрушения валов является усталость материалов.
Для валов различают усталостную прочность при номинальных нагрузках (выносливость) и статическую прочность при пиковых нагрузках. Из-за опасности усталостного разрушения валы рассчитывают на усталостную прочность. Валы, работающие с перегрузками, рассчитывают не только на сопротивление усталости, но и на статическую прочность.
Для расчета валов составляем расчетную схему (см. рис. ). При этом принимаем, что детали передают валу силы и моменты посередине своей ширины. Собственную массу вала и массу установленных на нем деталей, а также силы трения, возникающие в опорах, не учитываем.
входной вал
1 Назначаем материал вала
К материалам машинных валов предъявляются требования достаточной прочности, жесткости, ударной вязкости при минимальной чувствительности к концентрации напряжения. Этим требованиям отвечают малоуглеродистые стали марок Ст. 5, Ст. 6 (ГОСТ 380-88), среднеуглеродистые стали - Сталь 35, Сталь 45 (ГОСТ 1050-88), легированные стали - 40Х, 40ХН, 20Х, 12ХНЗА, 18ХГТ, 30ХГТ (ГОСТ 4543-88).
Для изготовления вала назначаем материал Сталь 45 ГОСТ 1050-88:
- предел прочности по нормальным напряжениям =600 МПа;
- предел текучести по нормальным напряжениям =340 МПа;
- предел текучести по касательным напряжениям =220 МПа;
- предел выносливости по нормальным напряжениям
при симметричном цикле для образца =250 МПа;
- предел выносливости по касательным напряжениям
при симметричном цикле для образца =150 МПа.
2 Определяем силы, действующие на вал
К этим силам относятся силы, возникающие в деталях передач и от веса этих деталей, внешние силы на валу от действия шкивов, звездочек, муфт
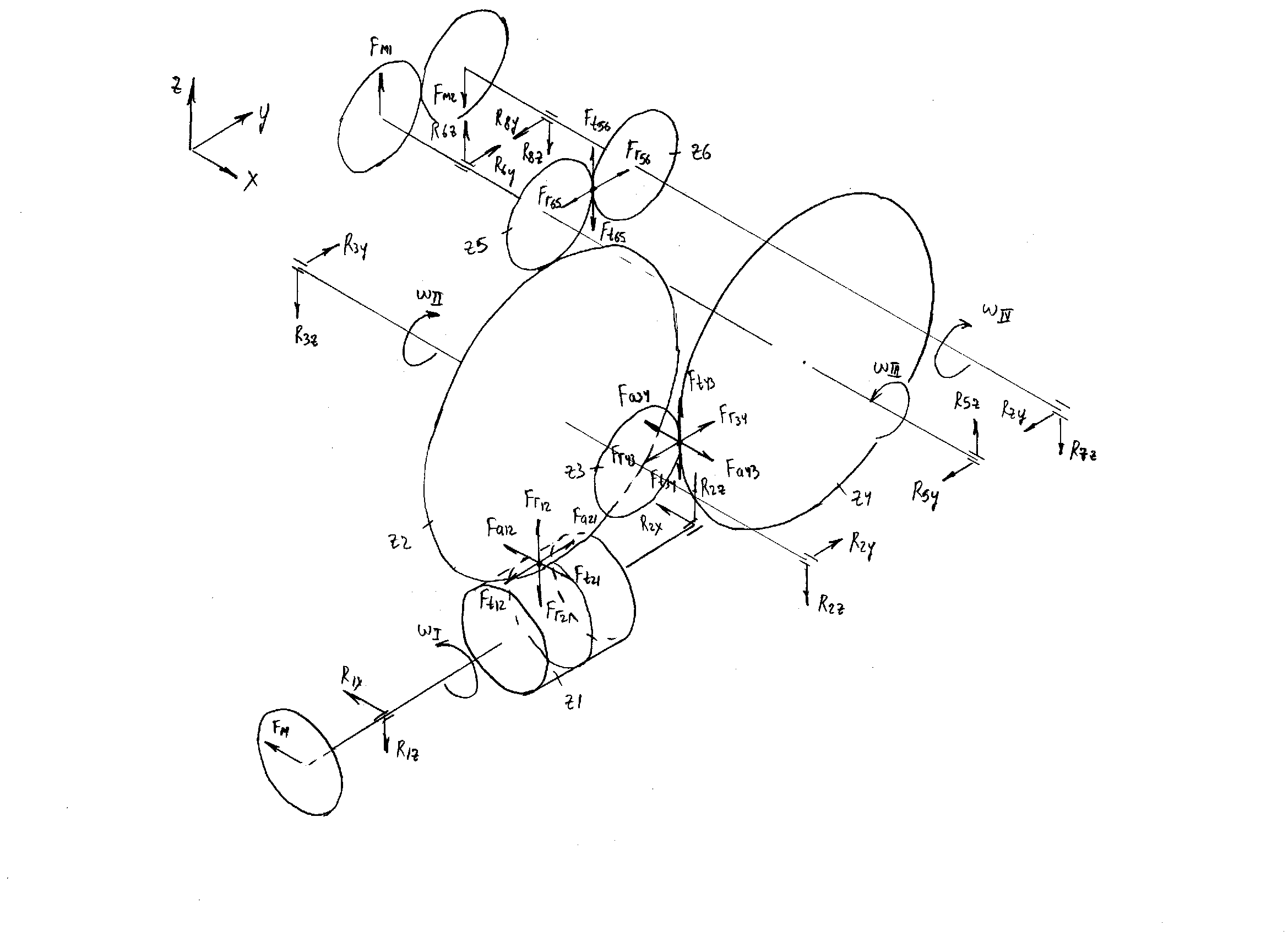
Рисунок - Расчетная схема
2.1 Рассчитываем силы в зацеплении червячной передачи
- окружная сила Ft21= = = 2232 Н;
- радиальная сила Fr21= Ft21tg a= 2232·0,364= 812,38 Н;
- осевая сила Fa21= = = 8924,03 Н;
где a - профильный угол в осевом сечении червяка, a=20°.
2.4 Рассчитываем силу, действующую со стороны упругой втулочно-пальцевой муфты
Fм = = 0,15·1210,33 = 181,55 Н,
где - окружное усилие на диаметре расположения пальцев муфты,
= 1210,33 Н.
3 Расчет опорных реакций и изгибающих моментов
Расчетная схема вала приведена на рисунке.
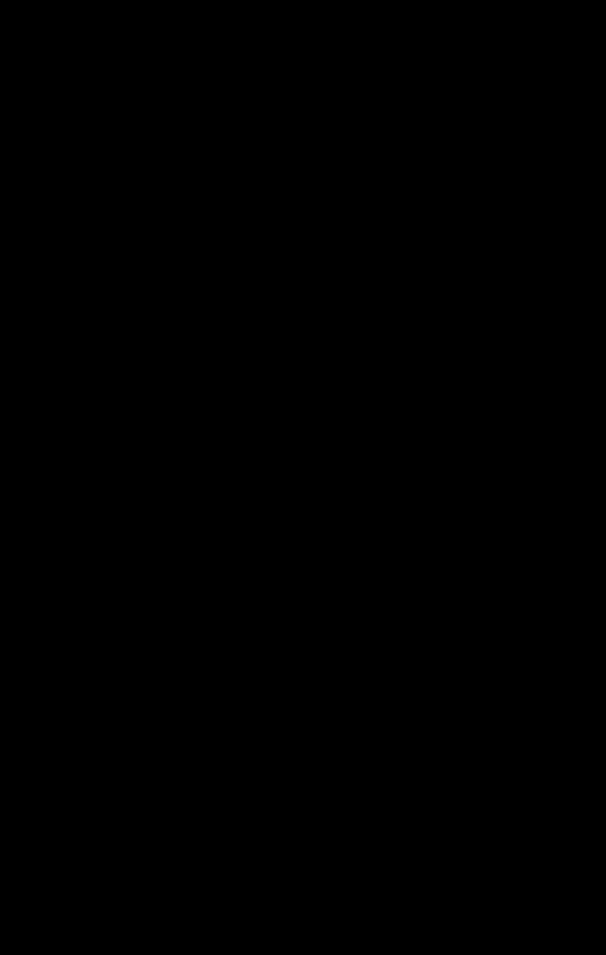
3.1 Вертикальная плоскость
составляем ур-е равновесия относительно опоры 1:
=+Fr21·344+Fa21·62,5-R2z·600=0
откуда
R2z=(+Fr21·344+Fa21·62,5)/600;
R2z=(+812,38·344+8924,03·62,5)/600=1395,35 Н;
составляем ур-е равновесия относительно опоры 2:
=-Fr21·256+Fa21·62,5-R1z·600=0
откуда
R1z=(-Fr21·256+Fa21·62,5)/600;
R1z=(-812,38·256+8924,03·62,5)/600=582,97 Н;
проверка: SZ=-Fr21-R1z+R2z=-812,38-582,97+1395,35=0,
следовательно расчет выполнен правильно.
рассчитываем изгибающие моменты в сечениях:
=0 Н·м;
=0 Н·м;
=-R1z·0,344=-582,97·0,344=-200,54 Н·м;
'=+Fa21·0,0625-R1z·0,344=+8924,03·0,0625-582,97·0,344=357,21 Н·м;
=-Fr21·0,256+Fa21·0,0625-R1z·0,6=
=-812,38·0,256+8924,03·0,0625-582,97·0,6=0 Н·м;
3.2 Горизонтальная плоскость
составляем ур-е равновесия относительно опоры 1:
=-Ft21·344+R2x·600-Fм·155=0
откуда
R2x=(+Ft21·344+Fм·155)/600;
R2x=(+2232·344+181,55·155)/600=1326,58 Н;
составляем ур-е равновесия относительно опоры 2:
=+Ft21·256-R1x·600-Fм·755=0
откуда
R1x=(+Ft21·256-Fм·755)/600;
R1x=(+2232·256-181,55·755)/600=723,87 Н;
проверка: SX=+Ft21-R1x-R2x-Fм=+2232-723,87-1326,58-181,55=0,
следовательно расчет выполнен правильно.
рассчитываем изгибающие моменты в сечениях:
=0 Н·м;
=-Fм·0,155=-181,55·0,155=-28,14 Н·м;
=-R1x·0,344-Fм·0,499=-723,87·0,344-181,55·0,499=-339,6 Н·м;
=+Ft21·0,256-R1x·0,6-Fм·0,755=+2232·0,256-723,87·0,6-181,55·0,755=0 Н·м;
4 Определяем опасные сечения
сечение (б-б)
………………
5.5Расчет подшипников на долговечность
Расчетное условие:
где - долговечность, которую может выработать подшипник;
- долговечность, заданная в техническом задании.
Расчет подшипников входного вала
Тип подшипников, на которых установлен вал:
опора 1: 7313 - роликоподшипники радиально-упорные конические однорядные ГОСТ 333-79 C=134000 Н; C0=111000 Н;
опора 2: 313 - шарикоподшипники радиальные однорядные ГОСТ 8338-75 C=72700 Н; C0=56700 Н;
Рассчитываем нагрузки, действующие в опорах
= = = 929,43 Н;
= = = 1925,31 Н;
Опора 2 является более нагруженной, по ней и ведем дальнейший расчет.
Рассчитываем долговечность подшипника в млн.об.
= 1925,31·1·1,5·1=2887,96 Н;
где - суммарная нагрузка на подшипник;
=1, так как вращается внутреннее кольцо подшипника;
- коэффициент, учитывающий рабочую температуру нагрева подшипника, =1 (до 100°С);
- коэффициент безопасности, =1,5.
= =11964,4 млн.об
где - динамическая грузоподъемность подшипника;
- коэффициент, учитывающий вероятность отказов, для степени надежности S=0,9, =1;
=0,75 - для шарикоподшипников;
=3 - для шарикоподшипников;
Рассчитываем долговечность подшипника в часах с повышенной гарантией рабочего ресурса
= =67710,24 ч
где - частота вращения вала;
= 24395 ч
- подшипник годен.
………………..
5.6Расчет соединений, передающих крутящий момент
Выполним расчет основных соединений, передающих крутящий момент между валом и посаженной на нем деталью
Соединения на входном валу
- расчет шпоночного соединения (в1 - м)
Исходные данные: T=145,24 Н·м; d=60 мм; Lст=150 мм.
Назначаем материал шпонки: Сталь 6, =330 МПа.
По ГОСТ 23360-78 устанавливаем размеры призматической шпонки: b´h=18´11; L=140 мм.
Рассчитываем смятие на рабочей грани шпонки
= =9,02 МПа,
где K=0,4h=0,4·11=4,4 мм;
Lр=L-b=140-18=122 мм;
Рассчитываем допускаемое напряжение смятия
= = 165 МПа,
где [S] - принятый коэффициент запаса прочности, [S]=2;
- предел текучести для материала шпонки, =330 МПа.
< = 165 МПа, следовательно, шпоночное соединение работоспособно.
…………….
6ВЫБОР И РАСЧЕТ МУФТ
6.1Выбор муфты входного вала
Муфта упругая втулочно-пальцевая (МУВП)
Муфтами называют устройства, с помощью которых соединяют между собой валы или валы с находящимися на них деталями для передачи вращающего момента. В таких соединениях муфты, как правило, должны обеспечить не только передачу крутящего момента, но и иметь возможность компенсировать различного рода смещения геометрических осей соединяемых валов. Осевые и радиальные смещения валов, а также их угловой перекос возникают в результате упругих деформаций деталей под нагрузкой и в результате неточностей изготовления и сборки узлов. В реальных соединениях валов все эти виды смещений наблюдаются одновременно.
В данном случае применяется муфта упругая втулочно-пальцевая. Муфты упругие втулочно-пальцевые получили весьма широкое распространение в современном машиностроении.
Достоинства муфт: сравнительная простота конструкции и дешевизна изготовления, хорошая демпфирующая способность; обладают также электроизолирующей способностью.
Недостатки: из-за низкой прочности резины по сравнению с металлами эти муфты обычно применяются для передачи малых и средних крутящих моментов; обладают низкими компенсационными свойствами, допускаемые ими радиальные смещения валов зависят от их диаметра.
На работу муфты существенно влияют толчки, удары и колебания, обусловленные характером работы приводимой в движение машины. Поэтому выбор муфты производят не по номинальному моменту на валу машины, а по расчетному:
=Т=1,16·145,24=168,48 Н·м,
где Т - номинальный вращающий момент на валу машины,
- коэффициент режима работы, зависящий от = 1,16 (см.предыдущие расчеты).
Кроме того, при выборе муфты учитываются диаметры концов сопрягаемых валов.
Принимаем муфту ……………
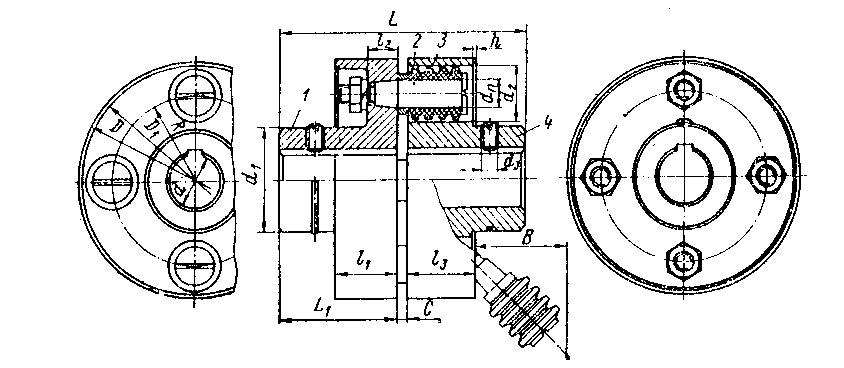
Рисунок 1 - Муфта упругая втулочно-пальцевая (МУВП)
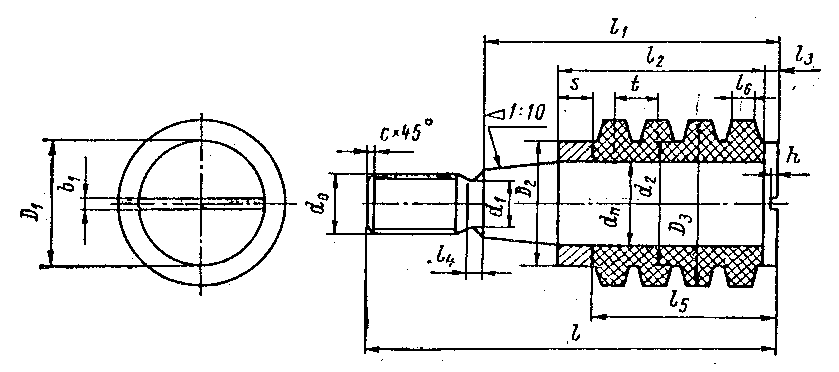
Рисунок 2 - Пальцы со втулками муфты МУВП
Конструкция муфты (см. рис. 1): во фланце полумуфты 1 коническими хвостовиками укрепляются пальцы 2 (см. рис. 2), на которые надеваются упругие резиновые втулки 3. Упругие втулки входят в отверстия, расположенные во фланце полумуфты 4. Отверстия растачиваются коническими или цилиндрическими.
………………….
7Конструирование и расчет элементов корпуса
7.1Конструирование основных элементов корпуса
Толщина стенки основания корпуса
= = 9,6 мм ,
где - максимальный вращающий момент на тихоходном валу.
Принимаем s=10 мм.
Толщина стенки крышки корпуса
= 0,9·10=9 мм.
Принимаем =9 мм.
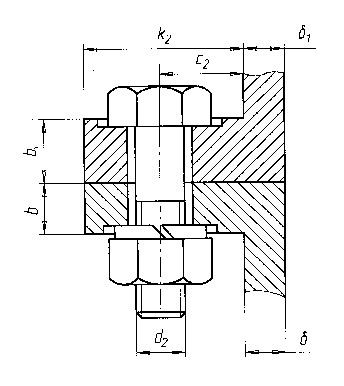
Рисунок - Размеры верхнего пояса фланца основания корпуса и фланца крышки корпуса
……………..
7.2Конструирование вспомогательных элементов корпуса
Размеры проушин
- толщина проушины
S = 2s = 2·10 = 20 мм.
………………
8ВЫБОР СМАЗКИ
Для уменьшения потерь мощности на трение и снижения интенсивности изнашивания трущихся поверхностей, а также для предохранения их от заедания, задиров, коррозии и для лучшего отвода теплоты трущиеся поверхности деталей должны иметь надежное смазывание.
Смазка подшипников качения
Выбор смазки осуществляется в зависимости от окружной скорости подвижного кольца. При скоростях v<2 м/с рационально использовать консистентную смазки. При v<5 м/с можно использовать как консистентную, так и жидкую смазку.
Определим окружные скорости:
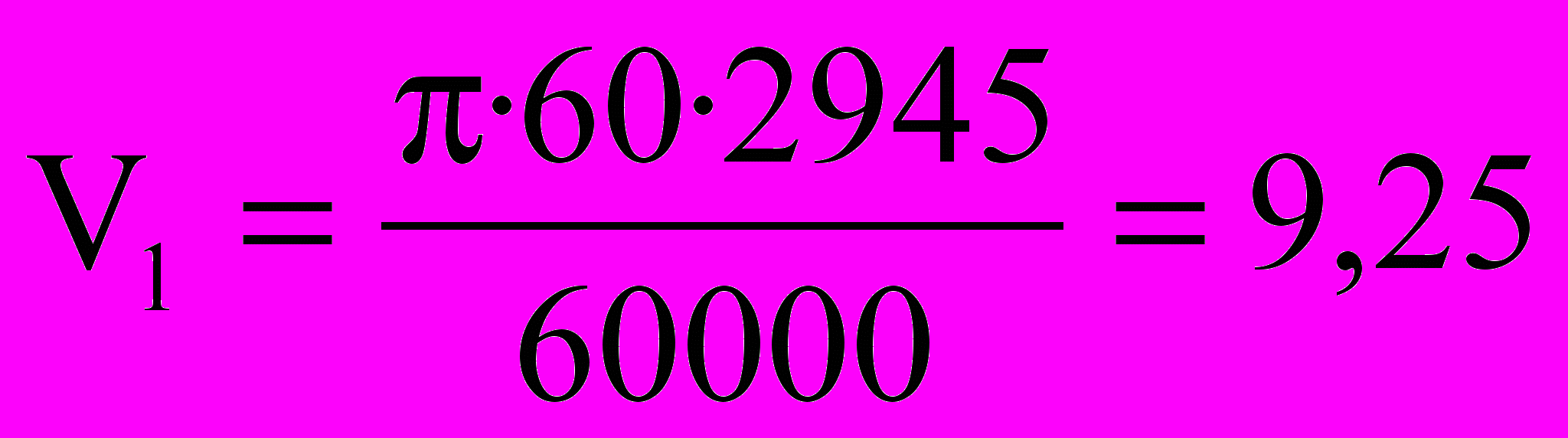
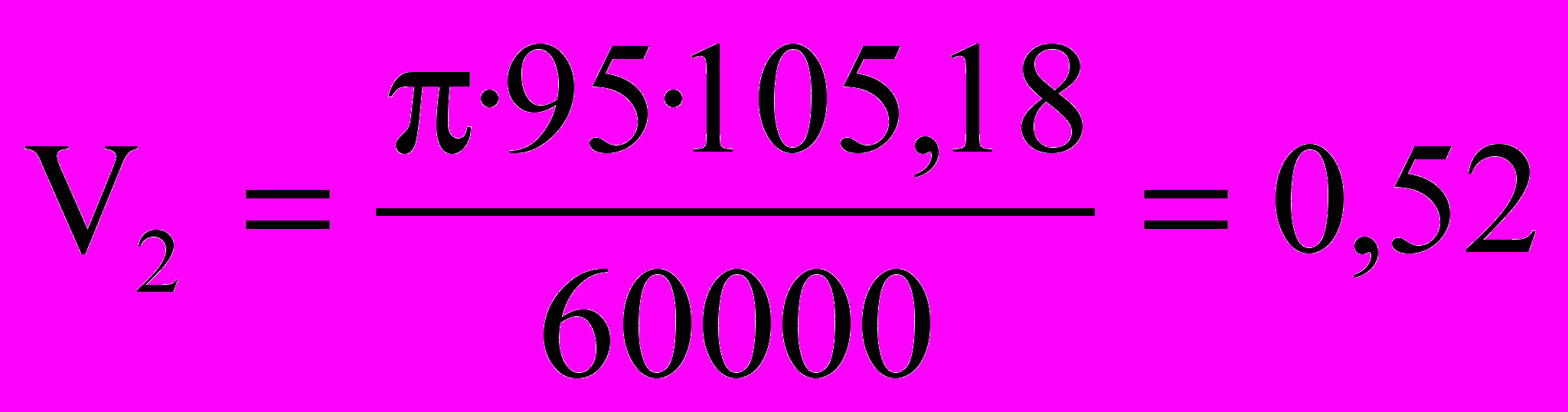
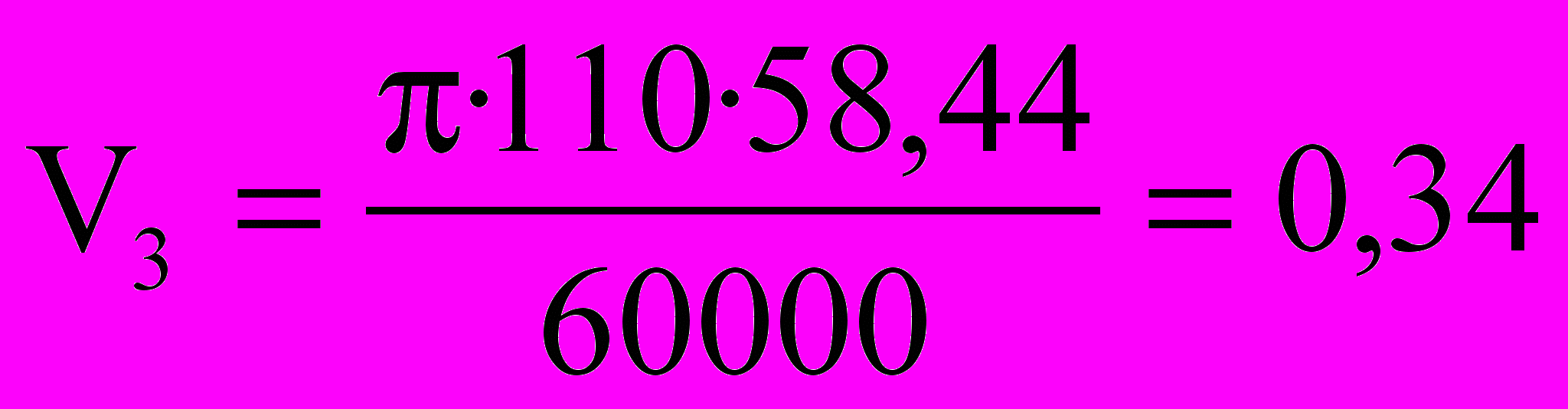

Для входного вала можно применить как консистентную, так и жидкую смазку подшипникового узла.
Для выходного и промежуточных валов исползуем консистентную смазку.
Учитывая условия работы (сухое отапливаемое помещение) принимаем в качестве смазки „Жировое масло I-13” [3, с.71, табл.9.2]
Для защиты подшипников от загрязнения, а также предотвращения вытекания смазки используют уплотнительные устройства.
Определяющим факотором при выборе уплотнения является линейная скорость вала под уплотнением.
Выберем манжетные резиновые уплатнения типа I ГОСТ 8752-79 [3, с.72, табл.9.3]
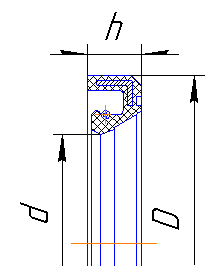
Рисунок 8.1 – Манжетное уплотенение резиновое, ГОСТ 8752-79
Параметрны уплотнений:
-на выходном валу
d=65мм; D=85мм; h=12мм;
- на выхдоном валу
d=110мм; D=135мм; h=12мм;
d=90мм; D=120мм; h=12мм;
Смазывание передач
Для смазывания передач применяем картерную систему. В корпус заливают масло так, чтобы венцы колес были в него погружены. Колеса при вращении увлекают масло, разбрызгивая его внутри корпуса. Масло попадает на внутренние стенки корпуса, откуда стекает в нижнюю его часть. Внутри корпуса образуется взвесь частиц масла в воздухе, которая покрывает поверхность расположенных внутри корпуса деталей.
Назначение марки масла. Принцип назначения марки масла следующий: чем выше контактные давления в зубьях, тем большей вязкостью должно обладать масло, чем выше окружная скорость колеса, тем меньше должна быть вязкость масла. Поэтому требуемую вязкость масла определяют в зависимости от контактного напряжения и окружной скорости колес.
Определяем параметры для назначения марки масла
= = 2,08 м/с;
= =232,46
Этому значению соответствует требуемая вязкость масла =40 [10, с.135, табл. 8.4]
В соответствии с этим принимаем для смазки зубчатой передачи жидкую нефтяную смазку - индустриальное масло И-40A ГОСТ 20799-75, для которого = 35…45 . [10, с.135, табл. 8.1]
Расчет потребного количества масла
=2(0,35…0,7)Рпотр=2·0,35·4,62 = 3,2 л
Рассчитываем предельно допустимые уровни погружения колес в масляную ванну
=1,5m=1,5·2 =3 мм;
=R=86,5 = 29 мм;
Принимаем h=20 мм.
В соответствии с конструкцией заливается =6,5 л, чтобы обеспечить необходимое погружение колеса в масло.
Уровень масла, находящегося в корпусе редуктора, контролируют жезловым маслоуказателем.
При длительной работе в связи с нагревом масли и воздуха повышается давление внутри корпуса. Это приводит к просачиванию масла через уплотнения и стыки, чтобы избежать этого внутренняя полость корпуса сообщается с внешней средой за счет установки пробки-отдушины.
Выводы
В курсовом проекте проведены расчеты и проектирование механизма привода шнеков-смесителей. Для исполнения указанных условий по входным данным выбран электродвигатель, спроектирован редуктор. Проведен проверочный расчет передач привода и валов редуктора. Разработаны чертежи: вида привода, сборочный чертеж редуктора, общего, рабочие чертежи деталей редуктора.
Выполнен выбор и проверка подшипников качения. Подобраны смазочные материалы. Расчитаны конструктивные элементы корпуса. Разработаны спецификации на редуктор и привод.
В процессе выполнения работы представлен
В процессе выполнения работы представлен полный порядок разработки конструкции привода шнеков-смеситетелй и связанной с ним документации.
Перечень ссылок
1 Методичні вказівки до виконання курсового проекту з деталей машин. ”Вибір електродвигуна та визначення вихідних даних для розрахунку приводу” (для студентів напрямку „Інженерна механіка”). Автори: Оніщенко В.П., Ісадченко В.С., Недосекін В.Б., - Донецьк: ДонНТУ, 2005. – 36 с.
2 Методичні вказівки до виконання курсового проекту з деталей машин. Розділ 2 „Проектування зубчастих і черв’ячних передач” (для студентів напрямку „Інженерна механіка”)./ Автори: В.П. Блескун, С.Л. Сулєйманов. – Донецьк.: ДонНТУ, 2005. – 48 с.
3 Методичні вказівки до виконання курсового проекту з деталей машин. Розділ 3. проектування валів та їх опор на підшипниках кочення (для студентів напрямку „Інженерна механіка”)/ Автори: О.В. Деркач, О.В. Лукінов, В.Б. Недосекін, Проскуряков С.В – Донецьк: ДонНТУ, 2005. 106 с.
4 Методичні вказівки до виконання курсового проекту з деталей машин. Конструювання муфт і корпусів (для студентів напрямку „Інженерна механіка”)/ Сост.: В.С.Ісадченко, П.М. Матеко, В.О. Голдобін. – Донецьк: ДонНТУ, 2005. – 40 с.
5 Перель Л.Я. Подшипники качения: Расчёт, проэктирование и обслуживание опор: Справочник. – М.: Машиностроение, 1983. – 543 с., ил.
6 Разработка и оформление технической документации. Учебное пособие. / Сост.: А.Н. Михайлов, А.В. Лукичёв, И.А. Горобец, А.П. Гуня, А.В. Деркач, И.В. Клименко, Н.В. Голубов, В.Б. Недосекин, В.А. Голдобін. – Донецк: ДонНТУ, 2005. – 56 с.
5>2>