Научное обоснование и разработка комплекса средств механизации для обеспечения качества углепродукции
Вид материала | Автореферат |
- Проблеми вищої школи, 123.83kb.
- Отчет о научно-исследовательской работе «Разработка Концепции обеспечения качества, 1446.28kb.
- Учебно-методический комплекс дисциплины разработка и стандартизация программных средств, 362.73kb.
- Обоснование и разработка эффективных методов лекарственного обеспечения на уровне высокоспециализированной, 3030.03kb.
- Целевая программа «Развитие научного потенциала высшей школы (2006-2008 годы)» Мероприятие, 311.58kb.
- Программа вступительного экзамена в аспирантуру по специальной дисциплине 05. 20., 94.72kb.
- Обоснование параметров и режимов работы комбинированной бороны для предпосевной обработки, 257.81kb.
- Научное обоснование и практическое применение новых подходов к обеспечению качества, 787.48kb.
- Рабочая программа по дисциплине опд. Ф. 11 «Подъемно-транспортные установки», 249.7kb.
- На правах рукописи, 644.37kb.
На правах рукописи
ДЕМЧЕНКО ИГОРЬ ИВАНОВИЧ
НАУЧНОЕ ОБОСНОВАНИЕ И РАЗРАБОТКА
КОМПЛЕКСА СРЕДСТВ МЕХАНИЗАЦИИ
ДЛЯ ОБЕСПЕЧЕНИЯ КАЧЕСТВА
УГЛЕПРОДУКЦИИ
Специальность 05.05.06 – «Горные машины»
25.00.22 – «Геотехнология
(подземная, открытая и строительная)»
А в т о р е ф е р а т
диссертации на соискание ученой степени
доктора технических наук
Иркутск – 2009
Работа выполнена в Федеральном государственном образовательном
учреждении высшего профессионального образования
«Сибирский федеральный университет»
Научный консультант Заслуженный деятель науки РФ
доктор технических наук, профессор
Буткин Владимир Дмитриевич
Официальные оппоненты Доктор технических наук, профессор
Викулов Михаил Александрович
Заслуженный деятель науки РФ
доктор технических наук
Маттис Альфред Робертович
Доктор технических наук, профессор
Щадов Иван Михайлович
Ведущая организация: Институт систем энергетики им. Л.А. Мелентьева
СО РАН
Защита диссертации состоится 14 октября 2009 г. в 1000 ч на заседании диссертационного совета Д 212.073.04 при Государственном образовательном учреждении высшего профессионального образования «Иркутский государственный технический университет» по адресу: 664074, г. Иркутск, ул. Лермонтова, 83, корпус К, конференцзал
Автореферат разослан 20 августа 2009 г.
Ученый секретарь диссертационного совета доктор технических наук, профессор | ![]() | Н.Н. Страбыкин |
ОБЩАЯ ХАРАКТЕРИСТИКА РАБОТЫ
Актуальность работы. Экономическое положение России в значительной степени определяется состоянием топливно-энергетического комплекса страны. Одним из основных факторов повышения конкурентоспособности угля, по сравнению с другими энергоносителями, является улучшение качества и сертификация угольной продукции, соответствующей Международной системе обеспечения качества ИСО-9000.
Большое разнообразие угля и преобладание валовой выемки приводит к тому, что потребителю поставляется рядовой уголь, имеющий разные качественные характеристики, определяющие энергетическую, экологическую и экономическую эффективность его использования.
Качество угля и его изменение зависят от способа добычи, транспортирования, перегрузки и временного хранения. Открытая перевозка и хранение угля приводят к прямым потерям твердого топлива. При перевозке железнодорожным транспортом потери углей мелких классов от выдувания воздушным потоком при их транспортировании на 500 км составляют 0,5–0,6 т в расчете на один вагон. Это эквивалентно 1 % транспортируемых углей. В целом по стране на железнодорожных перевозках теряется 3–5 млн т угля в год.
При перевозках угля автомобильным транспортом, осуществляемых на котельные в коммунально-бытовом секторе и индивидуальным потребителям, потери еще больше и составляют 5 % перевозимых углей. Открытый способ перевозки и хранения угля способствует измельчению, увеличению влаги, что часто приводит к смерзанию и осложнениям при разгрузке, а также к окислению и возможному самовозгоранию, от чего теряется до 7 % добываемого топлива. Перевозка и хранение угля навалом уменьшают теплоту сгорания на 5–80 ккал/кг в месяц, при этом снижение содержания мелочи на 1 % обеспечивает экономию топлива в размере 0,54 %.
Применяемая технология перевозки угля загрязняет окружающую среду, превращая прилегающую к транспортным коммуникациям и угольным складам территорию в малопривлекательную и вредную для проживания.
Потеря качества угля при открытом способе перевозки и хранения, характеризующееся уменьшением теплоты сгорания, измельчением, увеличением зольности и влаги, приводит к несоответствию поставляемого топлива проектному. Особенно такое несоответствие наблюдается при поставках топлива в котельные малой и средней мощности в коммунально-бытовом секторе, которые составляют большинство в топливно-энергетическом комплексе страны (только в Красноярском крае их насчитывается более 2000).
Применение ресурсосберегающей и экологичной технологии получения и доставки углепродукции повышенного качества, особенно в котельные со слоевым сжиганием топлива, сдерживается отсутствием соответствующих машин и оборудования, создание которых недостаточно обеспечено научно обоснованными методами проектирования.
Таким образом, важнейшее хозяйственное значение для развития угольной промышленности имеет решение научной проблемы разработки теоретических основ совершенствования и создания новых эффективных средств механизации технологических процессов получения на разрезе углепродуктов повышенного качества и их транспортирования потребителям, исключающих изменение качественных и количественных характеристик угля и загрязнение окружающей среды.
Работа охватывает обширный комплекс горных машин и оборудования: экскаваторы, углеперерабатывающие агрегаты, транспортные системы, усреднительные установки, средства механизации на складах.
Диссертационная работа основана на результатах исследований, начатых автором в 1994 г. в институте КАТЭКНИИуголь по государственной программе 0-46 «Разработать ресурсосберегающие технологии и создать оборудование по получению конкурентоспособных продуктов из угля и средств углепроводного транспорта» и продолженных на кафедре «Горные машины и комплексы» ФГОУ ВПО «СФУ» по теме «Повешение эффективности работы выемочно-погрузочного и сортировочного оборудования» и грантам Красноярского краевого фонда науки.
Целью диссертационной работы является научное обоснование и разработка машин и оборудования, комплексно обеспечивающих высокое качество топлива, при ресурсосбережении и экологичности процессов производства, транспортирования, хранения полученных углепродуктов и усреднения у потребителя.
Основная идея работы заключается в разработке и применении специализированных контейнеров на всех стадиях от получения углепродукции повышенного качества в забое до использования у потребителя, которые в комплексе с другими средствами обеспечивают высокие потребительские свойства топлива.
Основные положения диссертации, выносимые на защиту:
1. Полученная математическая зависимость суммарных транспортных затрат от расположения углеперерабатывающих установок обусловливает целесообразность размещения их в блочно-модульном исполнении непосредственно на добывающем оборудовании или на сопряженном с ним мобильном шасси, причем в качестве добывающего оборудования следует использовать экскаваторы фрезерного типа, имеющие лучшее соотношение производительности и массы машины и позволяющие отрабатывать пласты любой мощности.
2. Установленные закономерности изменения потерь угля при перевозках и их влияния на загрязнение окружающей среды позволяют утверждать, что основным средством сохранения качественных и количественных характеристик сортового угля и брикетов и экологической безопасности является тарное перемещение их от момента переработки до использования.
3. Разработанная математическая модель формирования транспортных потоков углепродукции требуемого качества позволяет учесть особенности различных групп потребителей с помощью предложенных специализированных контейнеров.
4. Выявленные зависимости площадей буртового и контейнерного угольных складов от их объема, формы, высоты, грузоподъемности специализированных контейнеров и числа ярусов их установки определяют целесообразность размещения различных марок углей в одном многоярусном контейнерном штабеле, что обеспечивает неизменное качество углепродукции, полную механизацию складских операций с соблюдением экологической безопасности.
5. Установленные зависимости и факторы, влияющие на процесс бункерного усреднения углей с разными характеристиками, а также разработанные установки новых конструкций являются основой окончательного формирования требуемого качества топлива для конкретного потребителя.
Обоснованность и достоверность научных положений, выводов и рекомендаций подтверждается сочетанием теоретических и лабораторных исследований с результатами анализа производственных и опытных данных; сходимостью результатов теоретических исследований и экспериментальных данных; эффективностью промышленного применения найденных технических решений.
Научная новизна результатов исследований состоит в:
– установлении зависимости, позволившей определить целесообразность максимального приближения углеперерабатывающего оборудования к добычному забою и возможность размещения перерабатывающего оборудования на экскаваторах фрезерного типа;
– выявлении (на экспериментальной установке с гравитационным способом перемешивания) зависимости и основных факторов, влияющих на процесс бункерного усреднения сортовых углей с получением у смеси свойств, эффективных для конкретного котельно-топочного оборудования;
– разработке математической модели формирования транспортных потоков углепродукции требуемого качества, предназначенных для перевозки углепродуктов конкретным потребителям;
– определении зависимости времени вынужденного простоя специализированных контейнеров при перегрузке с одного вида транспорта на другой от грузоподъемности и времени оборота транспортных единиц;
– установлении зависимости площадей буртового и контейнерного угольных складов от их объема, формы, высоты, грузоподъемности специализированных контейнеров и числа ярусов их установки;
– определении основных закономерностей изменения потерь угля при традиционной технологии его перевозки железнодорожным и автомобильным транспортом;
– уточнении степени влияния угольных потерь от выдувания на загрязнение территории и воздушного бассейна при существующей технологии транспортирования и хранения.
Практическое значение результатов работы заключается в разработке:
– схем размещения и структуры комплексов карьерного горного оборудования в забое (пат. РФ № 2078928), обеспечивающих получение качественного углепродукта непосредственно в забойных условиях разреза или максимально приближенных к нему;
– стрелового фрезерного экскаватора (пат. РФ № 2315866), обеспечивающего эффективный гранулометрический состав добываемого угля;
– основных требований к специализированным контейнерам, предназначенным для перевозки высококачественных углепродуктов разным потребителям и обеспечивающим сохранность и качество поставляемого топлива на этапах перевозки, перегрузки и хранения;
– типоразмерного ряда специализированных контейнеров (пат. РФ № 2153452, № 2178379, № 2243140, № 2271974, № 2254278), предназначенных для перевозки углепродуктов в разных условиях эксплуатации и обеспечивающих, в зависимости от необходимости, возможность их порционной или единовременной разгрузки;
– грузоподъемной траверсы (пат. РФ № 2248930) для захвата и опрокидывания контейнеров с сортовым углем при необходимости его единовременной разгрузки у потребителя;
– установок по усреднению углей с гравитационным (пат. РФ № 2268219) и принудительным (пат. РФ № 2271975) способами перемешивания углей и получением проектного топлива у потребителя;
– специализированных автотранспортных средств (а.с. СССР № 1637159, № 1719254), обеспечивающих повышение коэффициента использования грузоподъемности при перевозке грузов с различным объемным весом и удобство разгрузки (пат. РФ № 2273568);
– новой технологии хранения угля на складах с заменой существующего экологически вредного и затратного оборудования в виде бульдозеров и погрузчиков на экологически чистое грузоподъемное оборудование с электроприводом.
Реализация результатов работы. В промышленности:
– в создании карьерного мобильного сортировочного агрегата на базе прицепа тяжеловоза ЧМЗАП-5208 для Балахтинского разреза;
– в разработке конструкции кузовов карьерных автосамосвалов для перевозки угля на Черногорском разрезе;
– при проектировании оборудования в НПО «КРАСБРИК» для получения и доставки потребителю углепродукции повышенного качества.
В научно-исследовательских и опытно-конструкторских работах:
– «Разработать техническое задание на технологию сортировки угля на базе грохотов с канатным движущимся полем» НИР 2991067300 и «Отработка маломощных пластов оборудованием, обеспечивающим получение высококачественного твердого топлива, экологически чистое его транспортирование и хранение» НИР 2901069001, входящих в государственную программу 0-46 «Разработать ресурсосберегающие технологии и создать оборудование по получению конкурентоспособных продуктов из угля и средств углепроводного транспорта», 1994–1995 гг.;
– НИР 29104606903 с научно-технической горной ассоциацией «Разработать техническое задание на сортировочное оборудование горного комплекса для извлечения угля из пластов-спутников и создание контейнеров для доставки и временного хранения угля потребителю» (проект «Разработка ресурсосберегающих технологий и оборудования по подготовке сортового топлива и извлечения угля из разубоженной горной массы на угольных разрезах России»), 1996 г.;
– грант Красноярского краевого фонда науки «Разработка ресурсосберегающих и экологически чистых технологий и создание оборудования для получения конкурентоспособных продуктов из угля», 1998 г.;
– программа «Повышение эффективности работы горно-металлур-гического оборудования» в госбюджетной НИОКР «Повышение эффективности работы выемочно-погрузочного и сортировочного оборудования» на 2006–2010 гг.
В учебном процессе:
– основные результаты диссертационной работы изложены в трех учебных пособиях и двух монографиях, использующихся в учебном процессе в ФГОУ ВПО «СФУ»;
– стенды по усреднению углей с гравитационным и принудительным способом перемешивания применяются в научно-исследовательских работах студентов и аспирантов ФГОУ ВПО «СФУ».
Апробация работы. Основные положения и результаты диссертации представлялись, докладывались и обсуждались: на IV Международном форуме «Минерально-сырьевые ресурсы стран СНГ», симпозиуме «Горное оборудование, переработка минерального сырья, новые технологии, экология» (г. Санкт-Петербург, 1996 г.); Proceedings of the 6 TH international energy conference (Beijing, China, 1996 г.); Proceedings Fourth International Symposium on Mine Mechanization and Automation (Brisbane, Queensland, 1997 г.); международной конференции «Забайкалье на пути к устойчивому развитию: экология, ресурсы, управление» (г. Чита, 1997 г.); научно-практической конференции «Достижения науки и техники – развитию г. Красноярска» (г. Красноярск, 1997 г.); II международной научно-практической конференции на секции «Уголь и углепродукты» (г. Кемерово, 1997 г.); научном симпозиуме «Неделя Горняка» (г. Москва, 1997 и 2009 гг.); I научно-практической конференции по реализации Федеральной целевой программы освоения Нижнего Приангарья в Красноярском крае (г. Красноярск, 1997 г.); Всероссийской научно-практической конференции с международным участием «Достижения науки и техники – развитию сибирских регионов» (г. Красноярск, 1999 г.); научно-практической конференции «Минеральные ресурсы рудного и нерудного сырья Сибири в XXI веке» (г. Новосибирск, 1999 г.); во Всероссийском выставочном центре «Инновационный и научный потенциал Красноярского края» (г. Москва, 1999 г.); на конференции АО «Красноярскуголь» по маркетинговому исследованию и организации рынка КАУ (г. Красноярск, 1999 г.); научно-практической конференции «Проблемы экологии и развития городов» (г. Красноярск, 2000 г.); международной научно-практической конференции «Инвестиционный потенциал минерально-сырьевого комплекса Красноярского края» (г. Красноярск, 2000 г.); II Всероссийской научно-практической конференции «Транспортные средства Сибири» (г. Красноярск, 2004 г.); VIII Международной научно-практической конференции «Кузбасский международный угольный форум – 2006» (Кемерово, 2006 г.).
Личный вклад автора состоит: в постановке цели и задач диссертационной работы; разработке технологических схем размещения и взаимодействия добычного и перерабатывающего оборудования; создании ряда конструкций специализированных контейнеров и автотранспортных средств для перевозки твердого топлива, грузоподъемного оборудования (защищенных патентами) и их систематизации; научном обосновании необходимого количества контейнеров, обслуживающих грузопоток; разработке установок по усреднению углей и определении основных факторов, влияющих на процесс смешивания; анализе влияния различных факторов на потери угля при перевозке железнодорожным и автомобильным транспортом; в проведении теоретических и производственных исследований, позволяющих создать методики расчета угольных потерь и площадей контейнерных складов с углем.
Все результаты диссертационной работы, перечисленные в ее заключении, получены лично автором.
Автор выражает глубокую благодарность заслуженному деятелю науки Российской Федерации, доктору технических наук, профессору В.Д. Буткину за научные консультации и неоценимую методологическую помощь при работе над диссертацией. Особая признательность С.Б. Васильеву, В.И. Зудину, А.В. Гилеву и всем сотрудникам кафедры «Горные машины и комплексы» за поддержку и содействие при выполнении работы.
Публикации. По теме диссертации опубликованы 62 печатные работы, в том числе 2 монографии, 3 учебных пособия, представлено 11 докладов на международных научно-практических конференциях, получено 2 авторских свидетельства и 14 патентов на изобретения. В изданиях, рекомендованных ВАК, опубликовано 12 работ.
Объем и структура диссертации. Диссертация состоит из введения, восьми глав, заключения и приложений. Содержит 350 страниц машинописного текста, включая 122 рисунка, 52 таблицы и библиографический список литературы из 155 наименований.
ОСНОВНОЕ СОДЕРЖАНИЕ РАБОТЫ
В первой главе рассмотрены перспективы развития угольной промышленности, и в частности угольных разрезов Красноярского края, дана оценка проблемы, определены задачи и методы исследований.
Во второй главе приведено обоснование схем размещения и структуры комплексов карьерного горного оборудования в забое. Даны подходы к получению углепродуктов повышенного качества (сорта).
В третьей главе рассмотрены свойства угля и факторы, влияющие на потерю его качества при доставке потребителю. Предложены конструкции специализированных контейнеров для различных групп потребителей. Приведена математическая модель оборота контейнеров, обслуживающих конкретный угольный поток.
В четвертой главе исследованы факторы, влияющие на потери качества угля при его перевозке в полувагонах железнодорожным транспортом и разгрузке, а также при хранении на временных складах. Представлена методика расчета, которая позволяет оценить площади складов при хранении угля в буртах или в контейнерах с разными высотами буртов, ярусами установки и типами контейнеров.
В пятой главе определены факторы, влияющие на потери угля при его перевозке автомобильным транспортом. Разработаны технические решения, позволяющие адаптировать кузов автосамосвала к перевозке сыпучих грузов с различным объемным весом. Представлены конструкции специализированных автотранспортных средств-контейнеровозов.
В шестой главе рассмотрены особенности речного транспорта. Показаны преимущества использования новой технологии с точки зрения оперативности и безопасности перевозок. Предложена математическая модель оценки степени загрязнений, происходящих при перевозке угля навалом и открытом способе хранения.
В седьмой главе определены основные факторы, влияющие на процесс усреднения углей на установке гравитационного типа. Предложены варианты устройств по усреднению углей. Изложены рекомендации по механизации работ на складах.
В восьмой главе отражена экономическая эффективность проекта на всех этапах предлагаемой технологии.
Заключение содержит основные выводы и рекомендации по результатам выполненной работы.
В приложении приведены материалы о реализации основных методологических и технических решений, предложенных в диссертации.
1. Значение и теоретические предпосылки
создания комплексов оборудования для получения
высококачественной углепродукции
Перспективные ресурсосберегающие технологии, направленные на улучшение качества угля и повышение стабильности его характеристик, целесообразно основывать на следующих принципах: малооперационность технологического процесса получения ценных и энергонасыщенных углепродуктов, сохранное (без потерь качества и количества), экономичное и экологичное перемещение полученного на разрезе углепродукта в места потребления высокомеханизированными системами транспортирования и временного хранения. Этим принципам может соответствовать использование специализированных контейнеров во всех звеньях механизации технологического комплекса разреза.
В результате изучения состояния проблемы, обобщения теории и практики по теме диссертации не удалось выявить исследований по применению контейнерного способа доставки углепродукции, обеспечивающего неизменность ее качественных и количественных показателей при доставке потребителю.
Существенный вклад в разработку теоретических основ комплексного использования и обеспечения качества добываемого полезного ископаемого внесли А.А. Абрамов, С.П. Артюшин, З.Ш. Беринберг, И.С. Благов, В.Д. Буткин, В.Ф. Бызов, С.И. Гройсман, Н.Х. Загиров, Л.И. Кантович, А.П. Красавин, Г.Г. Ломоносов, Д.Е. Махно, Н.В. Мельников, И.В. Пономарев, В.В. Ржевский, Н.Н. Страбыкин, К.Н. Трубецкой, П.И. Томаков, Т.Г. Фоменко, С.Э. Фридман, О.К. Щербаков.
Потери полезного ископаемого при его транспортировании и хранении изучались С.П. Амельчуговым, В.С. Веселовским, Е.И. Глузбергом, В.В. Жучковым, В.М. Ивановым, Я.С. Киселевым, С.И. Протасовым, И.В. Радовицким, В.И. Саранчуком, Ж.К. Текеновым, Л.П. Хитриным, А.И. Хрисанфовой, А.В. Швыдкиным.
Стабилизацией качества добытого угля занимались А.В. Баскин, Н.Г. Бедрань, Н.М. Белик, Ф.Г. Грачев, В.В. Демкин, В.А. Земляков, А.И. Карякин, И.П. Крапчин, М.Ф. Кундым, А.Р. Молявко, В.П. Немчинов, Н.А. Самылин, С.А. Саракисянц, Н.В. Федоров, Р.Р. Шаль, Л.П. Шупов.
Одним из продуктов переработки рядового угля и самым простым по технологическому процессу получения является сортовой уголь, который рассматривается как начальный уровень ресурсосберегающей технологии. При этом большое значение имеет оптимальное расположение перерабатывающего оборудования, которое может быть установлено в местах добычи, пунктах пересечения транспортных коммуникаций и у потребителя.
Пусть при сортировке угля производится К его сортов, которые поставляются n потребителям. Обозначим mi j – массу угля iго сорта, поставляемого jму потребителю за определенный отрезок времени Т (mi j ≥ 0). Тогда
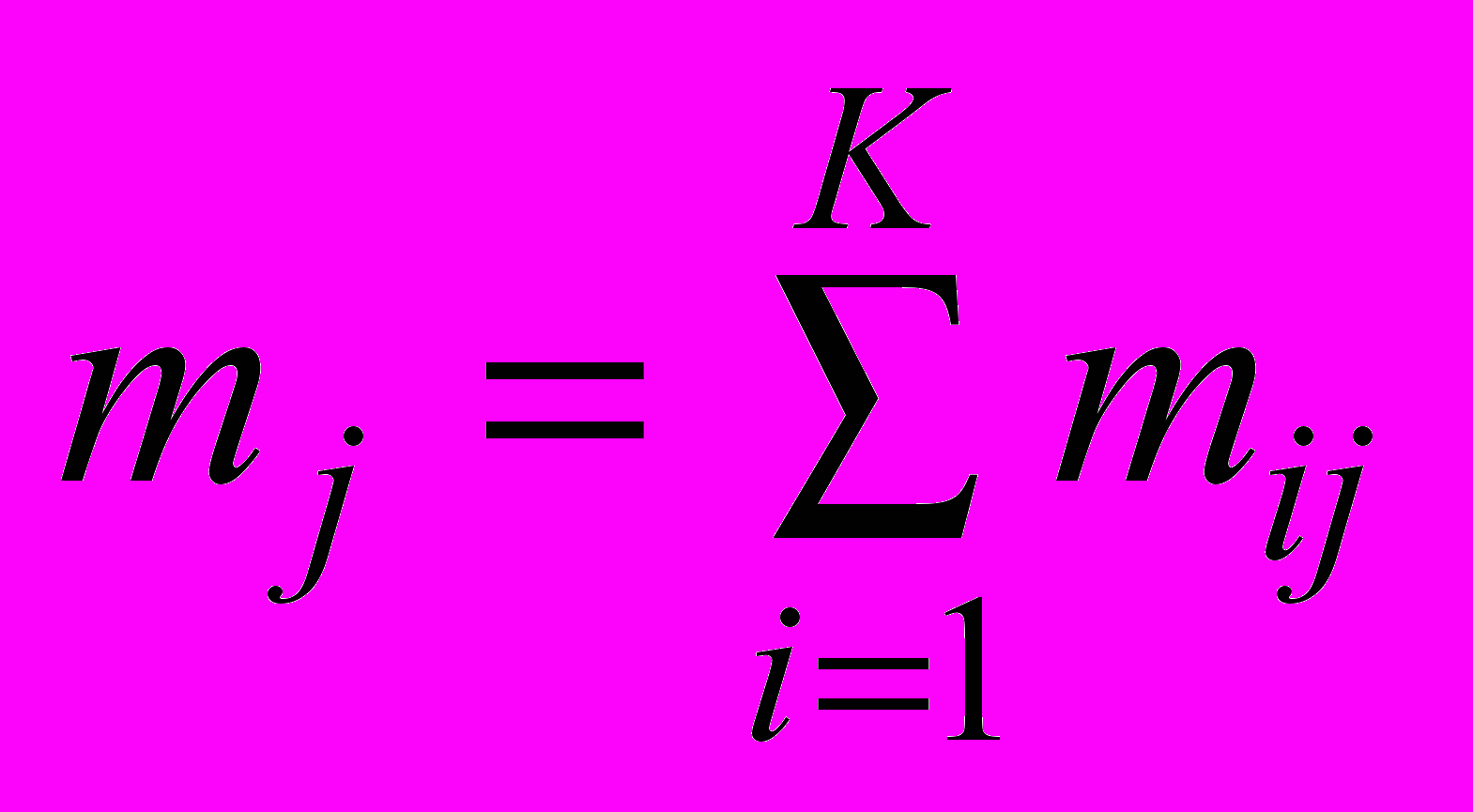
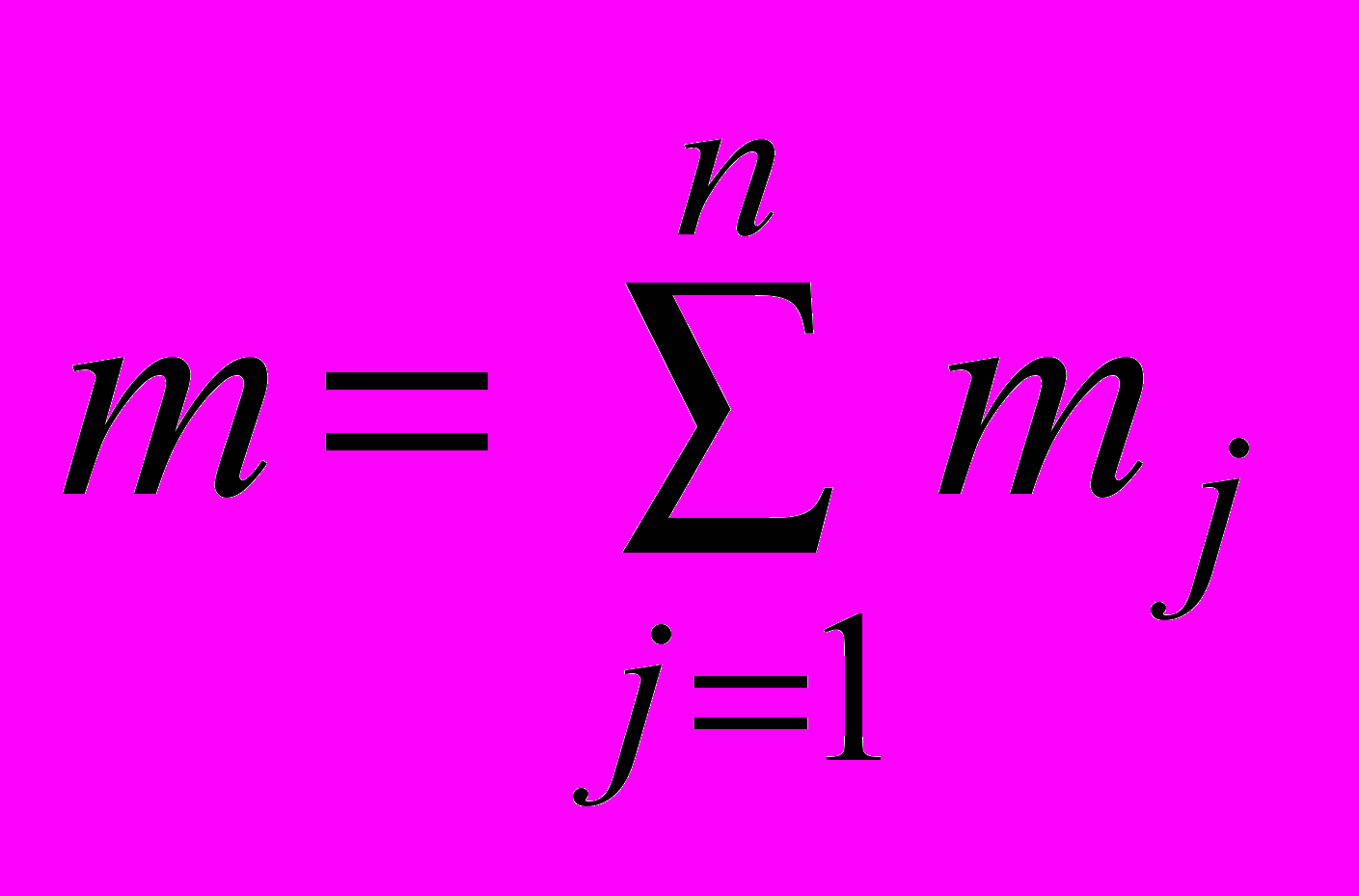
Пусть Sj – стоимость перевозки единицы массы угля (далее просто стоимость перевозки) от пункта сортировки до jго потребителя, j = 1, 2, …, n, S0 – стоимость перевозки от разреза, поставляющего рядовой уголь, до пункта сортировки. Тогда затраты на перевозку сортового угля от пункта сортировки до jго потребителя равны mj · Sj, а затраты на перевозку всего сортового угля от пункта сортировки равны
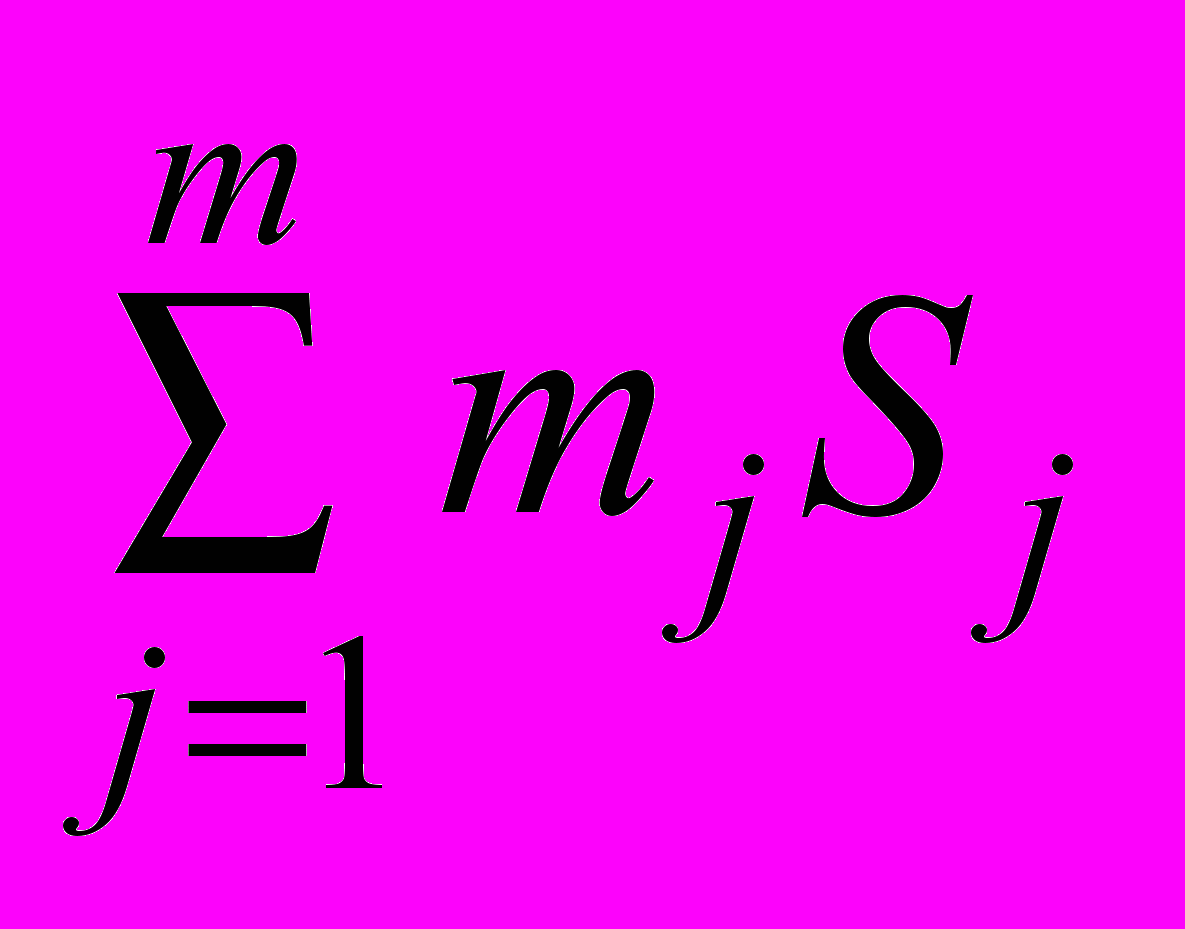

которую необходимо минимизировать для определения оптимального места расположения пункта сортировки угля.
Все способы перевозки угля из пункта А в пункт В обозначим GАВ. Стоимость S перевозки зависит от способа перевозки, поэтому стоимость перевозки по конкретному способу
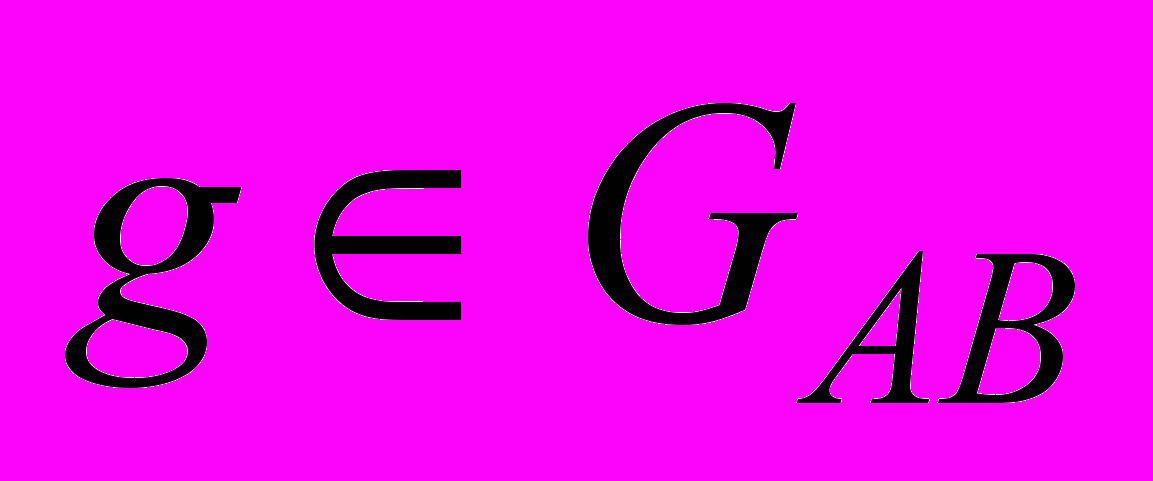
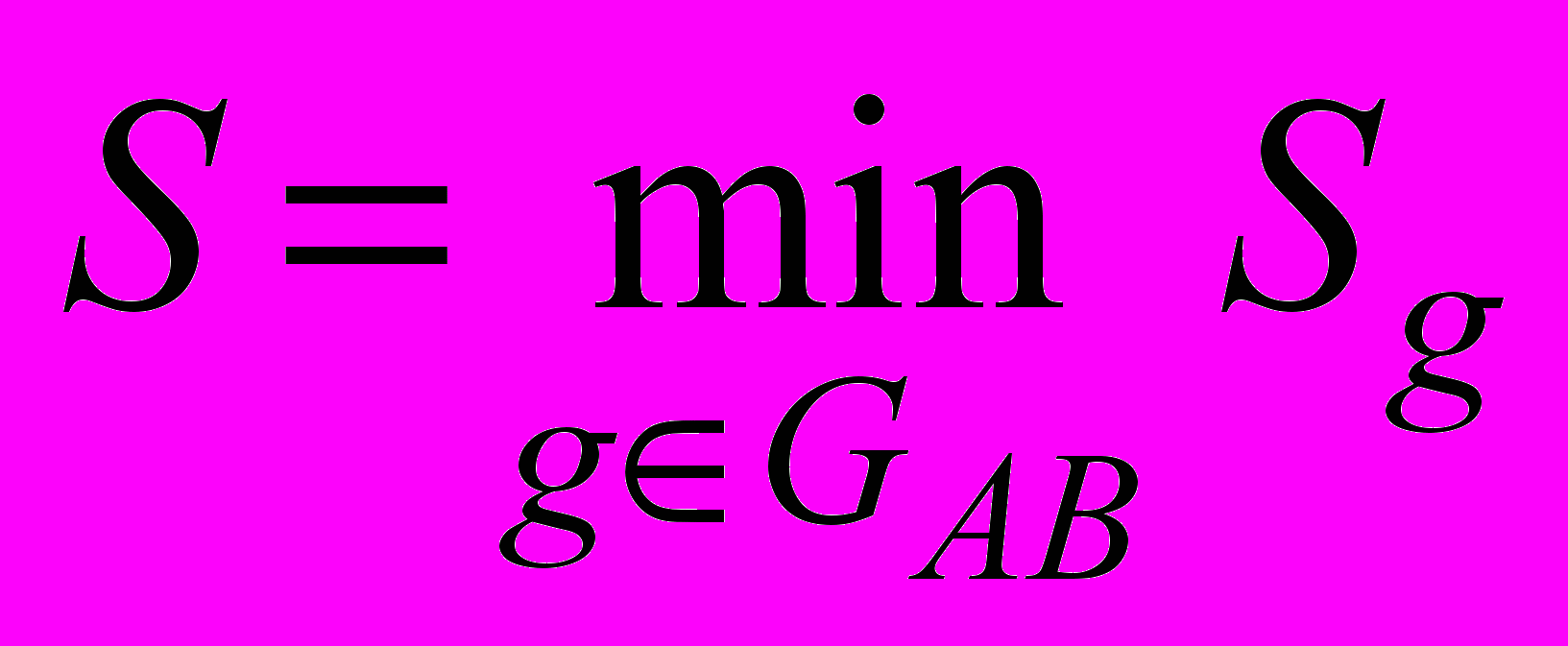
Упомянутые выше стоимости перевозок S0, S1, …, Sn определяются именно так. Способ перевозки, которому соответствует наименьшая стоимость, считается оптимальным.
Сортовой уголь суммарной массой mj, поставляемый jму потребителю, перевозится сначала от места добычи А до пункта сортировки в составе рядового угля и затем от пункта сортировки до потребителя Вj некоторым способом
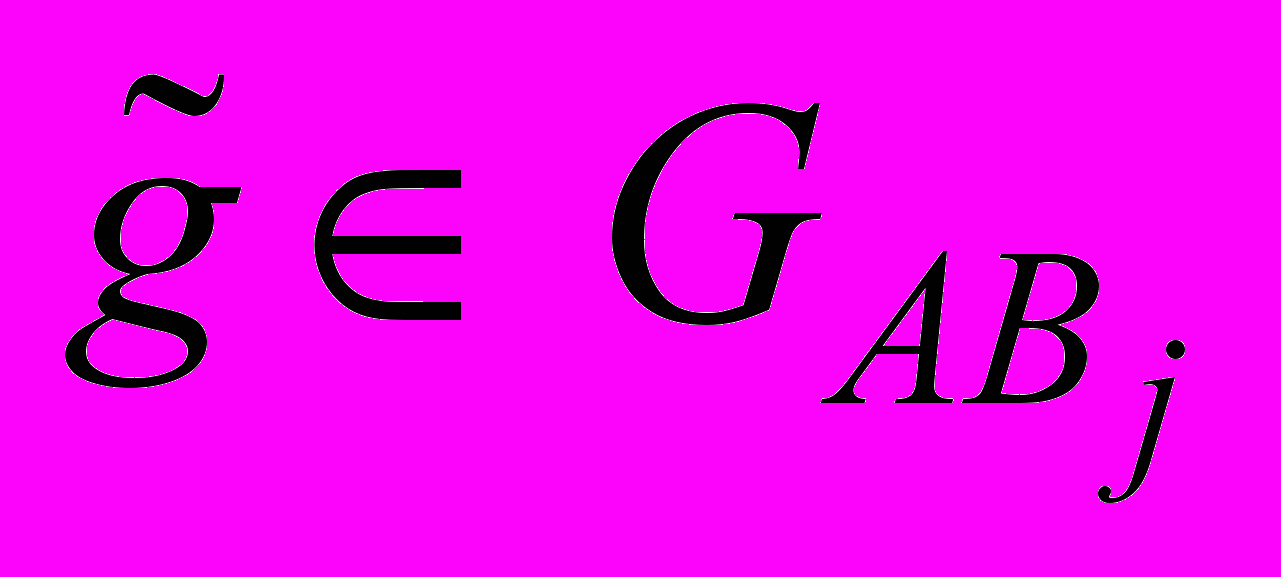
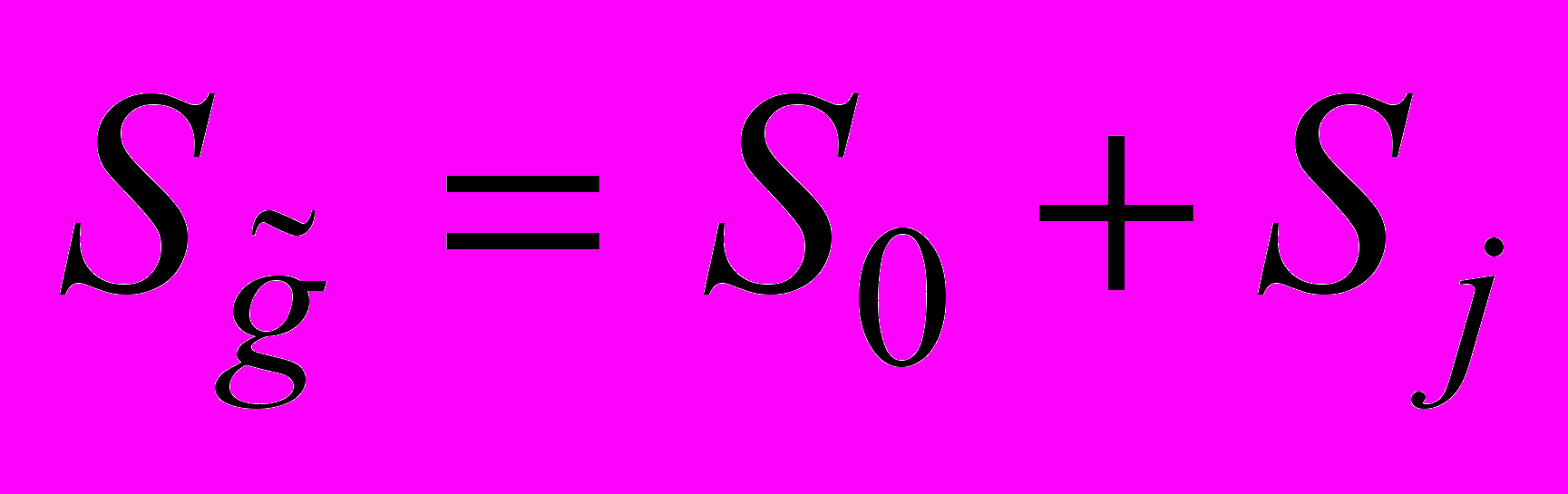
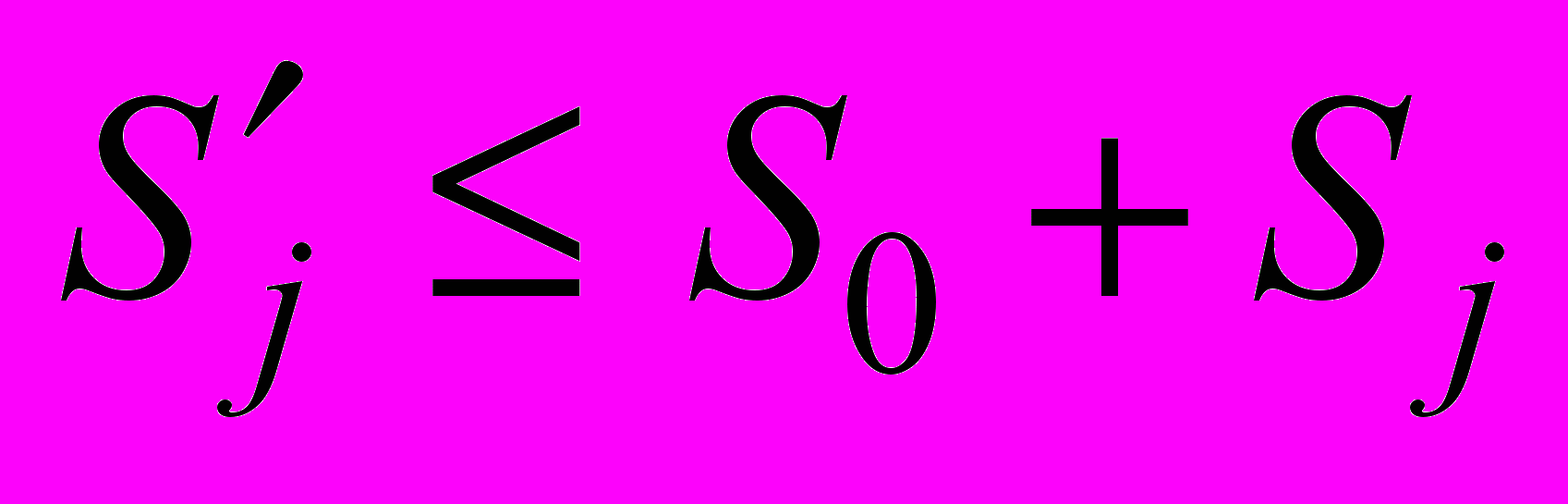
где наименьшая стоимость
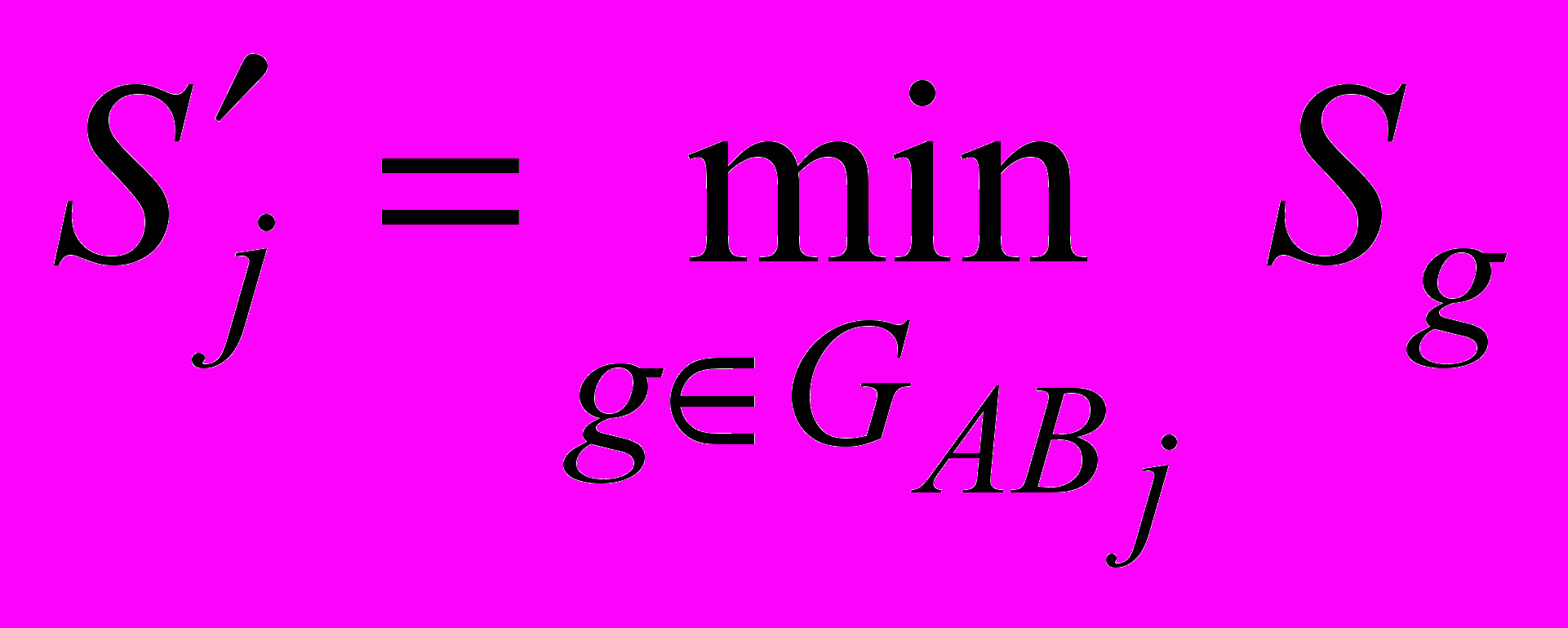
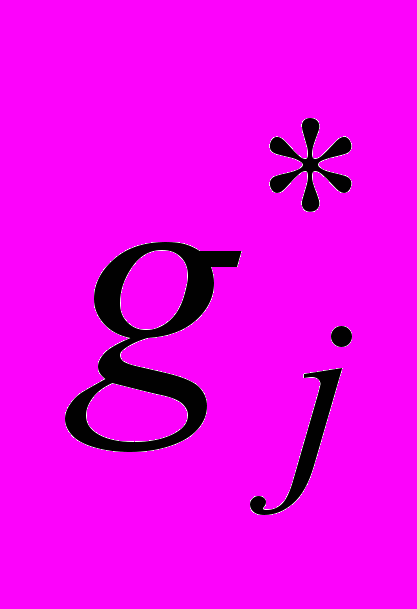
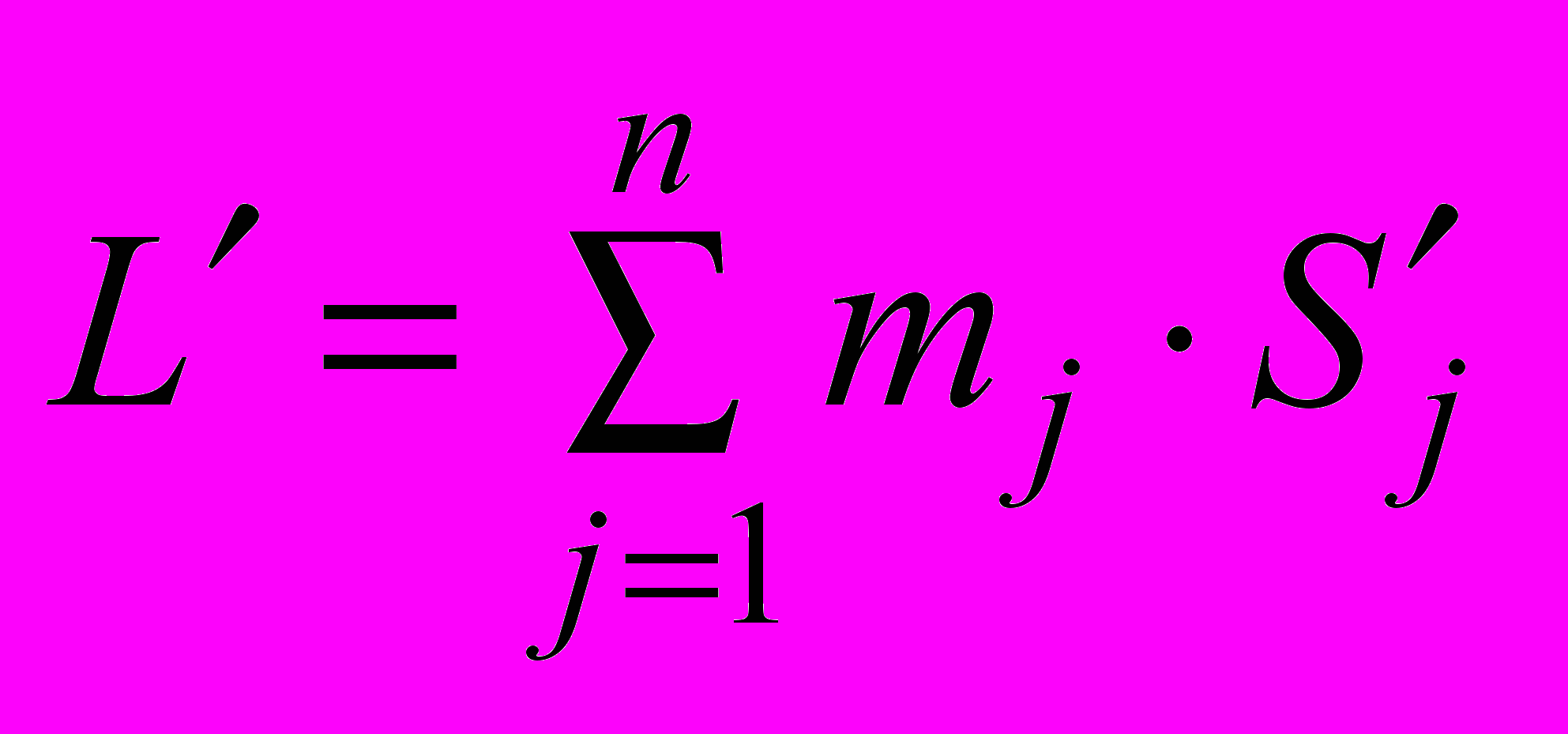
Из формул (1)–(3) следует неравенство
L' ≤ L,
которое доказывает, что минимум целевой функции (минимум затрат на перевозку угля потребителям) отмечается при расположении пункта сортировки в месте добычи (на разрезе). При этом расположение его непосредственно на добывающем оборудовании или на мобильном шасси в технологической цепочке с добывающим оборудованием выгоднее устройства отдельного сортировочного пункта. Это объясняется тем, что дополнительные затраты на перемещение сортировочного оборудования вместе с добывающим значительно меньше затрат на перегрузку, т.к. произведение массы сортировочного оборудования на его перемещение меньше произведения массы добытого угля на его перемещение только при выгрузке. Учет затрат на другие операции, связанные с выгрузкой, погрузкой и хранением угля в отдельном пункте сортировки, завершает доказательство.
Указанные решения могут быть реализованы при работе любого выемочно-погрузочного оборудования.
Рассмотрим машины непрерывного действия. Учитывая особенности карьерного фонда, изобилующего разрезами малой и средней мощности, а также то, что на разрезах с большой производственной мощностью имеются маломощные или тонкие пласты, которые ввиду несовершенства технологии зачастую отрабатываются в отвал, весьма перспективным становится более широкое применение экскаваторов фрезерного типа, в том числе и стреловых (пат. РФ № 2315866). Опыт эксплуатации экскаватора КСМ-2000РМ на разрезе Талдинский показал, что эти машины обеспечивают полноту выемки полезного ископаемого. Поэтому предлагается использовать экскаватор типа КСМ вместе с другими горными машинами в составе горного карьерного комплекса (ГКК) по добыче и переработке угля. Важной особенностью экскаваторов фрезерного типа является также выход «нужного» гранулометрического состава, наиболее пригодного для переработки.
На рис. 1 изображен экскаватор типа СМ, работающий в технологической цепочке с перерабатывающим оборудованием. Исходя из специфики конкретных разрезов и требований рынка, возможно дополнительное включение или замена одного мобильного перерабатывающего оборудования на другое.
Показанная на рис. 1 технологическая цепочка лишь схема. Конечно, не на каждом разрезе горно-геологические условия дают возможность разместить вслед за экскаватором шлейф перерабатывающего оборудования. Однако, во-первых, перерабатывающее оборудование на мобильном шасси можно устанавливать вблизи добычного участка, связывая его с экскаватором, например межуступным перегружателем, и перемещать это мобильное оборудование по мере продвижения фронта работ.
Во-вторых, компактность и относительно малая материалоемкость (рис. 2) экскаваторов фрезерного типа могут послужить основой для создания ГКК по добыче и переработке угля на одном шасси.
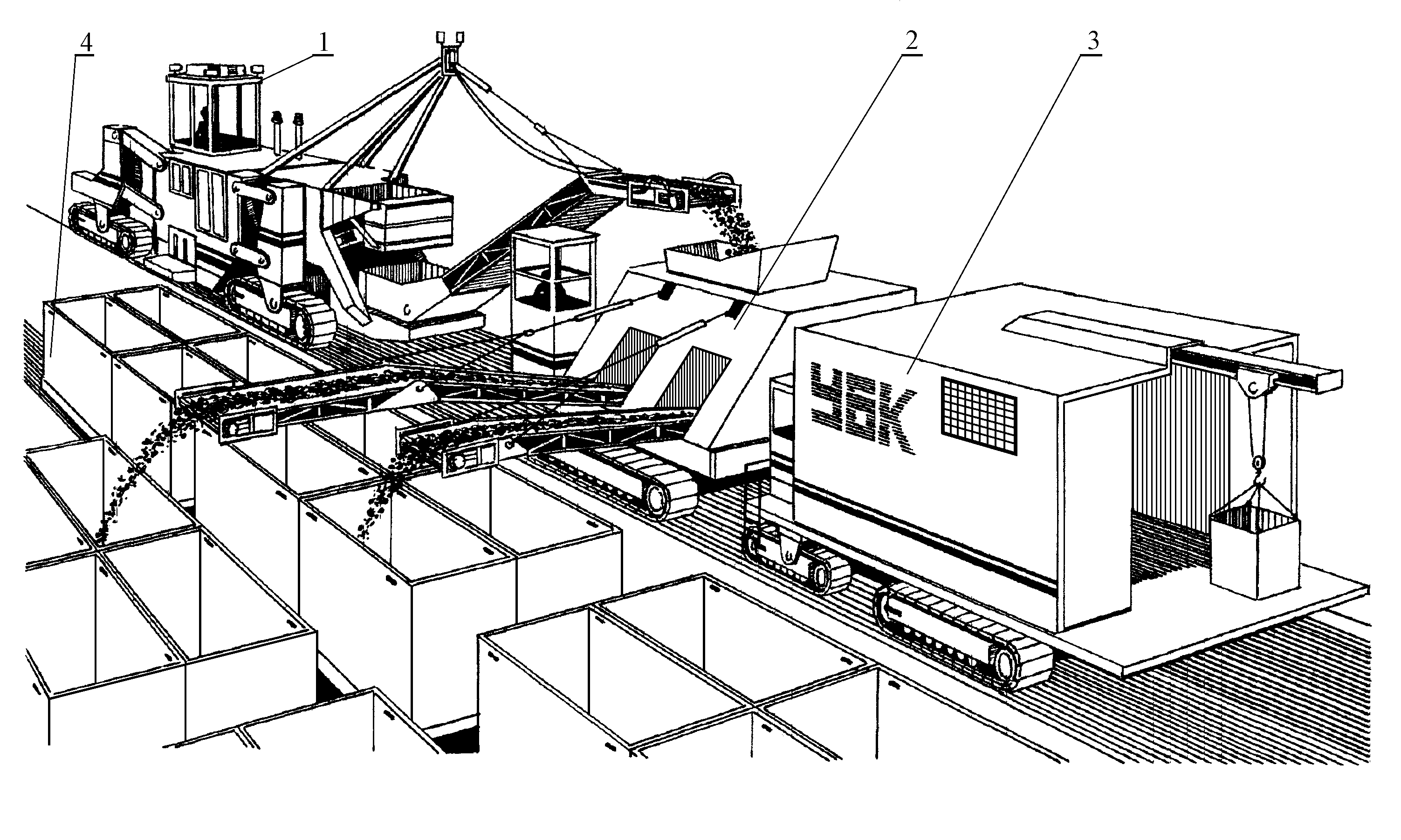
Рис. 1. Комплекс карьерного горного оборудования в забое (пат. РФ № 2078928): 1 – экскаватор; 2 – сепарационно-сортировочный агрегат; 3 – упаковочно-
брикетный участок; 4 – контейнеры
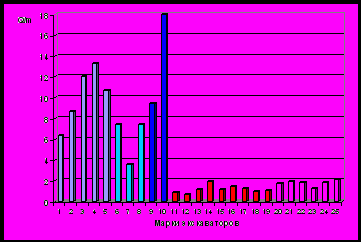
Q/m
Рис. 2. График отношения производительности Q, м3/ч, к массе m, т, некоторых экскаваторов непрерывного действия: 1 – СМ 1900; 2 – СМ 2600; 3 – СМ 3000; 4 – СМ 3600; 5 – СМ 4200; 6 – КСМ 2000; 7 – КСМ 2000РМ; 8 – КСМ 4000; 9 – EASI-1224 «HURON»; 10 – 5Е «VOEST ALPINE»; 11 – ЭРГВ-630.9/05(Ц); 12 – ЭР-630.10,5/1(Г); 13 – ЭРП-1250.16/1(Г); 14 – ЭРП-1250.16/1(Г); 15 – ЭР-1250.17/1ОЦ; 16 – ЭРП-2500.21.4/1; 17 – ЭРШРД-5250.22/2; 18 – ЭРШРД-5000.50/3; 19 – ЭРШР-5000.40/7; 20 – SRS(K)-470; 21 – SRS(K)-2000; 22 – SRS-2400; 23 – KU-300;
24 – KU-800; 25 – SchRS-1500
На рис. 3 представлен вариант ГКК по добыче и переработке угля. Грузоподъемное оборудование обеспечивает перегрузку с ГКК на транспортные средства груженых и в обратном направлении порожних контейнеров, а также необходимых для работы ГКК расходных материалов, например связующего для брикетного участка. На ГКК предусмотрена также отгрузка рядового угля без переработки.
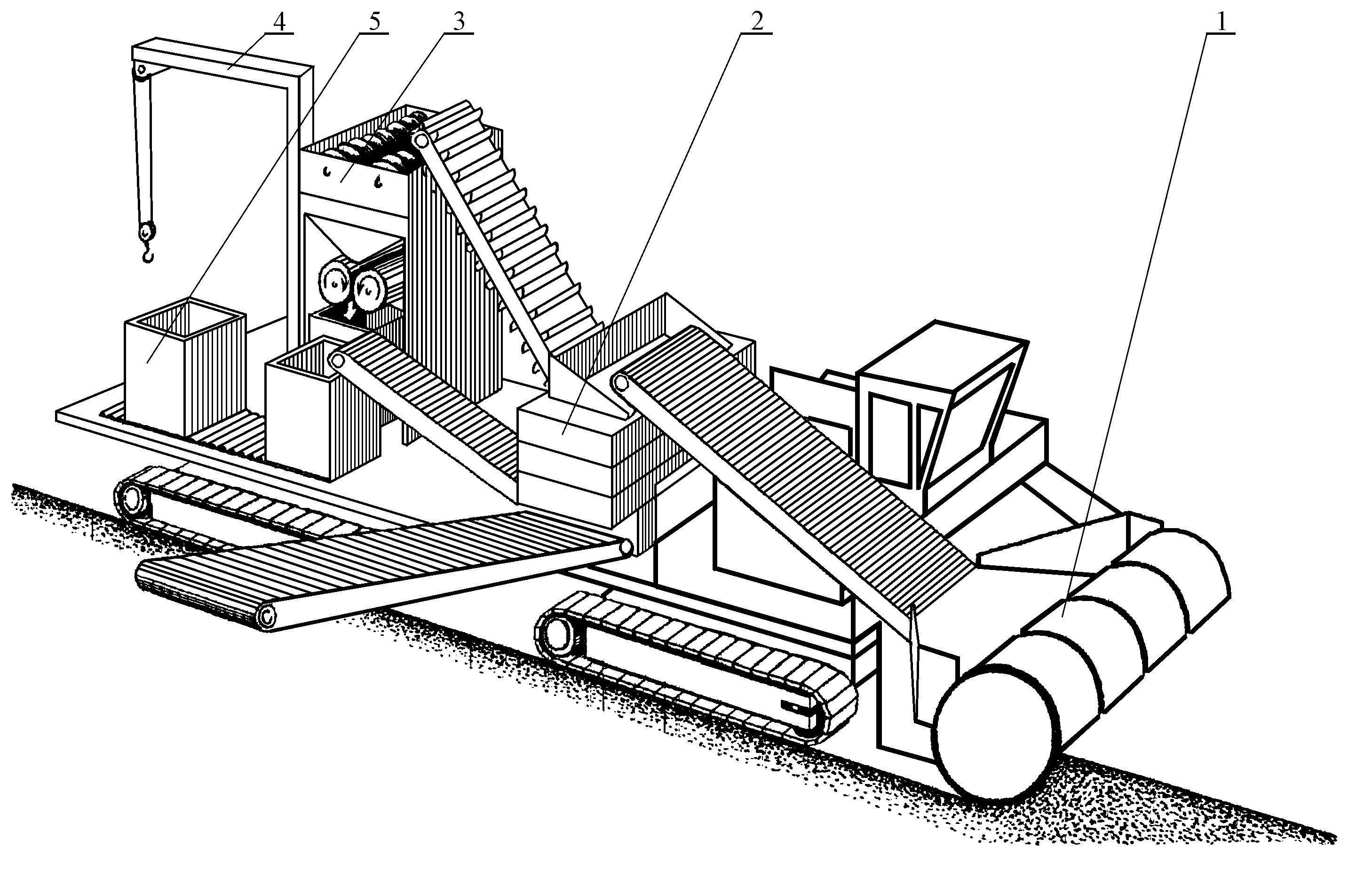
Рис. 3. Горный карьерный комплекс для экскавации угля с получением высококачественных углепродуктов (пат. РФ № 2083839): 1 – экскавационное оборудование; 2 – сортировочный блок; 3 – блок брикетирования; 4 – грузоподъемное оборудование; 5 – контейнеры
Принципиальной основой создания ГКК является блочно-модуль- ный способ его построения с возможностью установки дополнительных перерабатывающих блоков или замены отдельных модульных блоков на другие для оперативного реагирования на изменение конъюнктуры рынка, исходя из индивидуальных потребностей заказчика.
Приведенная схема размещения перерабатывающего оборудования вблизи добычного участка применима и для его взаимодействия с экскаватором цикличного действия.
Для исключения потери качества сортового угля при его перевалке с одного вида транспорта на другой предлагается отгружать уголь в специализированные контейнеры. Возможно как минимум два варианта размещения контейнеров в момент погрузки. Первый вариант – контейнеры находятся на самом карьерном мобильном сортировочном агрегате, куда подаются с помощью его грузоподъемного оборудования либо другого мобильного грузоподъемного оборудования, например погрузчика. Второй вариант – контейнеры расположены на транспортном средстве.
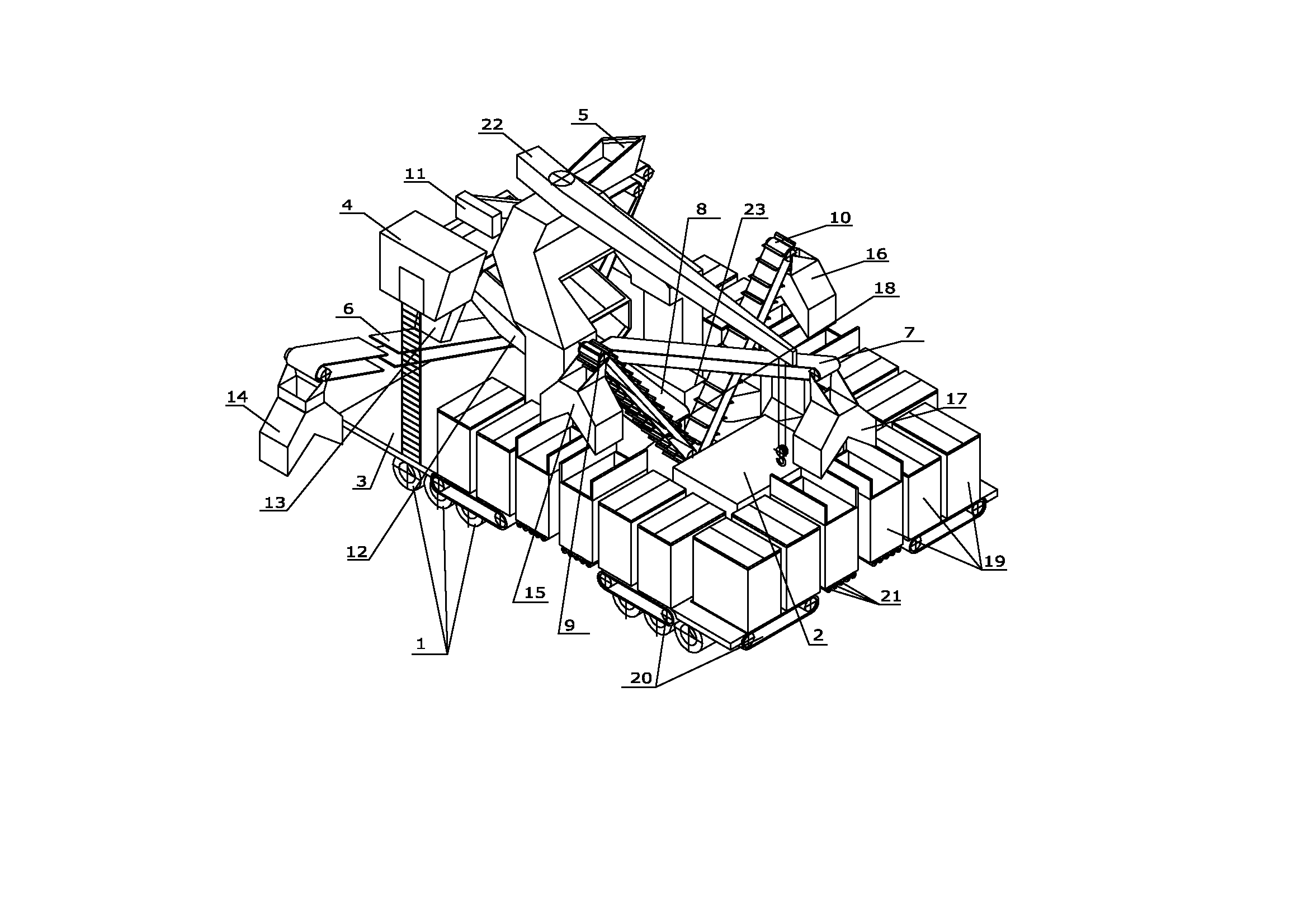
Рис. 4. Карьерный мобильный сортировочный агрегат (пат. РФ № 2119015): 1 – ходовое оборудование; 2 – привод; 3 – поворотная платформа; 4 – кабина; 5 – приемный бункер; 6–10 – конвейеры; 11 – плуг-отделитель; 12 – грохот; 13 – лоток; 14–17 – бункеры-распределители; 18 – реверсивный конвейер; 19 – контейнеры; 20 – питатель; 21 – весы; 22 – кран;
23 – компрессор
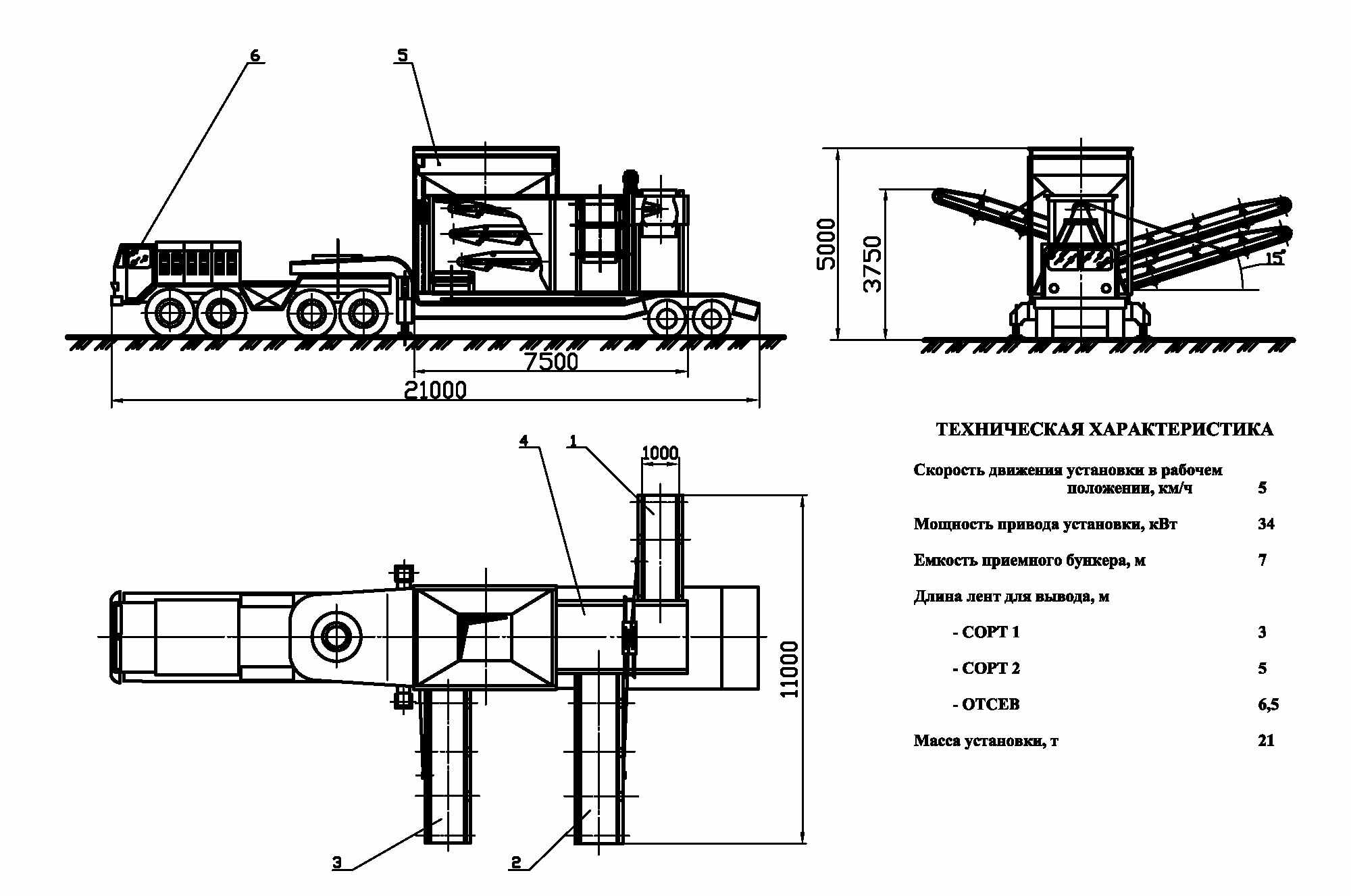
Рис. 5. Сортировочный модульный блок на низкорамном полуприцепе-тяжеловозе ЧМЗАП-9399: 1 – конвейер погрузки сортового угля одного класса крупности; 2 – конвейер подрешетного материала; 3 – конвейер погрузки сортового угля другого класса крупности; 4 – конвейер сброса нега-
баритов; 5 – сортировочный модульный блок; 6 – автомобиль-тягач
По первому варианту предлагаемый карьерный мобильный сортировочный агрегат (КМСА), принципиальная схема которого представлена на рис. 4, работает в технологической цепочке с добычным экскаватором, передвигаясь вместе с ним по уступу. Блочно-модульное сортировочное оборудование можно установить на автомобиль, полуприцеп (рис. 5) или прицеп, тогда контейнеры не располагаются на КМСА. По варианту два контейнеры находятся на других транспортных средствах.
В процессе сортировки выделяется уголь двух классов крупности и отсев. Для удаления негабаритных кусков (не более 5 % добычи) с поля сортировочной установки используется ленточный конвейер 4 (рис. 5), расположенный в задней части сортировочной установки. С конвейера уголь сбрасывается на поверхность рабочей площадки, зачищается бульдозером и повторно экскавируется.
Концепция создания КМСА была реализована со шнековым грохотом ГШ-1000 на базе прицепа-тяжеловоза ЧМЗАП-5208 грузоподъемностью 40 т на Балахтинском разрезе.
Использование рассмотренных схем размещения сортировочного оборудования в забойных условиях разрезов или максимально приближенных к ним по технологии работ позволяет выгодно получать сортовой уголь даже на малых разрезах.
Таким образом, обосновано первое положение:
Полученная математическая зависимость суммарных транспортных затрат от расположения углеперерабатывающих установок обусловливает целесообразность размещения их в блочно-модульном исполнении непосредственно на добывающем оборудовании или на сопряженном с ним мобильном шасси, причем в качестве добывающего оборудования следует использовать экскаваторы фрезерного типа, имеющие лучшее соотношение производительности и массы машины и позволяющие отрабатывать пласты любой мощности.