Научное обоснование и разработка комплекса средств механизации для обеспечения качества углепродукции
Вид материала | Автореферат |
- Проблеми вищої школи, 123.83kb.
- Отчет о научно-исследовательской работе «Разработка Концепции обеспечения качества, 1446.28kb.
- Учебно-методический комплекс дисциплины разработка и стандартизация программных средств, 362.73kb.
- Обоснование и разработка эффективных методов лекарственного обеспечения на уровне высокоспециализированной, 3030.03kb.
- Целевая программа «Развитие научного потенциала высшей школы (2006-2008 годы)» Мероприятие, 311.58kb.
- Программа вступительного экзамена в аспирантуру по специальной дисциплине 05. 20., 94.72kb.
- Обоснование параметров и режимов работы комбинированной бороны для предпосевной обработки, 257.81kb.
- Научное обоснование и практическое применение новых подходов к обеспечению качества, 787.48kb.
- Рабочая программа по дисциплине опд. Ф. 11 «Подъемно-транспортные установки», 249.7kb.
- На правах рукописи, 644.37kb.
2. Преобразование процессов перевозки
и хранения угля
В настоящее время при транспортировке угля, перевалке с одного вида транспорта на другой и при его хранении происходят значительные потери. Хранение угля навалом на открытых складах повышает зольность, обуславливает его выдувание, вымывание, самовозгорание. Все это приводит к ежегодным потерям до 7 % добываемого угля, а также к сильному загрязнению прилегающей территории и воздушного бассейна. В работе выполнен анализ процессов, приводящих к потерям, и даны их качественные оценки.
Пожарная безопасность скоплений углей может быть обеспечена условиями стационарности потока тепла путем снижения объемов. Это может быть эффективно достигнуто перевозкой и временным хранением угля в контейнерах.
Значительного внимания потребовала проблема смерзания угля в зимнее время. В основе процессов, происходящих при примерзании угля к кузову, лежит теплообмен между кузовом и обтекающим его холодным воздухом. Из-за намерзания угля в полувагоне не удается полностью выгрузить его на вагоноопрокидывателе. Замеры невыгруженного угля (рис. 6) показывают, что максимальная масса достигает 7,5 т, а среднее значение за отопительный сезон с октября 2002 г. по март 2003 г. составляет 1,64 т на один вагон.
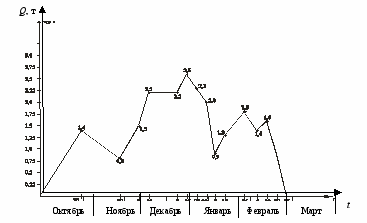
Рис. 6. Средняя масса примерзшего угля, перевозимого в полувагонах
на Назаровскую ГРЭС в отопительном сезоне 2002–2003 гг.
Разгрузка примерзшего угля из полувагона через нижние люки трудоемка и выдвигает другую проблему – это поломки полувагона. Вследствие механического воздействия разгрузочные люки и их торсионные устройства выходят из строя (рис. 7), что вынуждает работников угольных складов закрывать их ломами. На закрытие каждого люка (170 кг) задействуется 3 человека. Неисправные полувагоны являются одной из основных причин потерь угля при перевозках.
Исследованы потери угля при его перевозке различными видами автомобильного транспорта. Для оценки потерь были проведены наблюдения за перевозками угля автомобильным транспортом. Установлено, что потери распределяются по длине маршрута неравномерно, большие отмечаются в начале транспортирования, когда происходит «утряска» угля в кузове и ссыпание кусков угля и мелочи, находящихся на бортах кузова и оказавшихся там при погрузке.
Рис. 7. Структура неисправностей полувагонов, перевозивших уголь: 1 – щели разгрузочных люков; 2 – зазоры в торцевой части вагона; 3 – пробоины кузова; 4 – трещины, зазоры в кузове; 5 – порыв, смятие верхней обвязки кузова | ![]() |
Наблюдения за перевозками позволили выявить основные факторы, от которых зависят потери угля (табл. 1), и оценить степень их влияния.
Таблица 1
Основные факторы, влияющие на потери угля при перевозках
автомобильным транспортом
Факторы | Характеристика | Степень влияния* |
Дорожные условия | Тип дорожного покрытия: | |
асфальто- и цементобетонное | – | |
сборное железобетонное | + | |
щебеночное, гравийное, шлаковое и грунтощебеночное | + | |
укатанное грунтовое | + | |
Состояние дорожного покрытия (ухабы, рытвины, ж/д переезды) | + | |
План трассы (повороты, виражи) | + | |
Профиль трассы (подъемы, спуски) | + | |
Подвижной состав | Тип подвижного состава: | |
бортовой автомобиль | 0 | |
прицеп | 0 | |
полуприцеп | 0 | |
самосвал (без заднего борта) | + | |
Техническое состояние подвижного состава: | | |
основных бортов и днища | + | |
надставных бортов | + | |
подвески | + | |
Форма кузова | – | |
Периметр кузова | 0 |
Продолжение табл. 1
Факторы | Характеристика | Степень влияния* |
Темперамент водителя | Сангвиник | + |
Флегматик | – | |
Холерик | + | |
Меланхолик | 0 | |
Груз и условия погрузки | Марка угля | – |
Гранулометрический состав | + | |
Загрузка кузова: | | |
с «шапкой» | + | |
без «шапки» | – | |
Погодные условия | Температура воздуха | – |
Ветер | + | |
Осадки (дождь, снег) | 0 | |
Влажность | 0 |
* Знак «–» соответствует слабому влиянию, «0» – среднему, «+» – сильному.
При рассмотрении фактора дорожных условий было установлено, что потери зависят не только от типа дорожного покрытия, но и очень сильно от его состояния. Выявленные закономерности потерь угля от дорожных факторов на условном маршруте можно представить в виде графика интенсивности потерь (рис. 8).
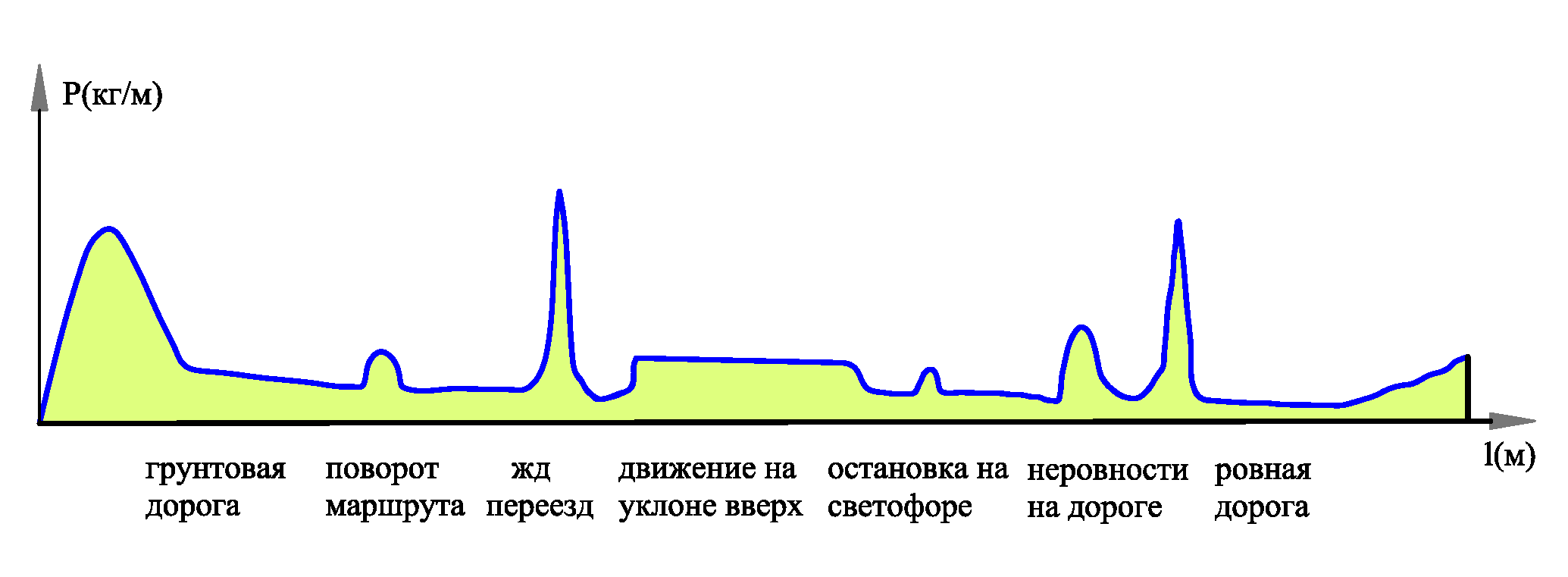
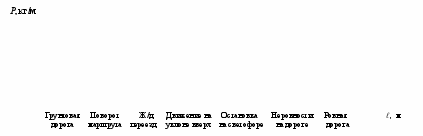
Рис. 8. График интенсивности потерь угля на условном маршруте перевозки
автомобильным транспортом
Потери угля на маршруте зависят также от подвижного состава. Ввиду небольшой объемной массы угля его обычно грузят с «шапкой». При движении от тряски и вибрации угол естественного откоса уменьшается, и уголь, находящийся в кузове, сдвигается к бортам, откуда и происходит его падение. Особенно большие потери наблюдаются при отсутствии заднего борта у автомобиля-самосвала.
Для уменьшения потерь, повышения коэффициента использования грузоподъемности и оперативного реагирования на изменение объемного веса перевозимого груза была разработана конструкция кузова автосамосвала, которая позволяет менять высоту надставных бортов. Задний борт открывается автоматически при разгрузке с образованием увеличенного проходного сечения между днищем кузова и задним бортом, предотвращая тем самым возможные поломки заднего борта (рис. 9).
Рис. 9. Конструкция кузова автосамосвала с изменяемой высотой надставных бортов и автоматическим открыванием заднего борта (а.с. СССР № 1637159; а.с. СССР № 1719254): 1 – боковой борт кузова; 2 – надставной борт; 3 – ось вращения надставного борта; 4 – задний борт; 5 – днище кузова; 6 – трос; 7 – регулировочное устройства троса; 8 – ось вращения кузова | ![]() |
Предложенная конструкция решает локальную задачу, однако в целом проблема, связанная с потерями и снижением качества топлива при перевозке угля навалом, остается нерешенной.
Более сильное влияние на потери оказывает герметичность кузова и состояние подвески автомобиля.
Для выявления количественных потерь угля при перевозке его автотранспортом были проведены экспериментальные исследования на грунтовой дороге, ведущей от угольного склада ст. Бугач до асфальтированной ул. Калинина г. Красноярска. Этот отрезок пути протяженностью около 500 м со сравнительно ровной для грунтовой дороги поверхностью имеет в двух местах явно выраженные неровности (ухабы). На ней было проведено более 300 наблюдений за перевозками угля автомобилями с замерами угольных потерь. Большая часть этих наблюдений носила вспомогательный характер. С их помощью было установлено следующее:
– сравнительно простому измерению поддаются потери кусков угля размером не менее 1 см, т.к. улавливание угольной мелочи и пыли требует более дорогих и трудно выполнимых приемов;
– основная часть кусковых потерь угля приходится на два упомянутых выше участка с неровностями, на которых в отдельных случаях потери доходили до 6 кг;
– главными факторами, влияющими на потери угля на неровностях дороги, являются наличие заднего борта, наращенных бортов и манера вождения (темперамент) водителя.
С целью уточнения влияния упомянутых факторов на потери кускового угля на неровностях дороги был проведен полный четырехфакторный двухуровневый эксперимент 24, где х1 – наличие (отсутствие) заднего борта, х2 – наличие (отсутствие) наращенных бортов, х3 – темперамент водителя, х4 – номер неровности. Функцией отклика являлись угольные потери, г. Для х1, х2 и х3 наличию фактора соответствовала (+1), отсутствию – (–1), для х4 (–1) соответствовала первой неровности, а (+1) – второй неровности, если их считать от угольного склада. Последний фактор был управляемым, а первые три фактора – условно управляемые, т.к. приходилось дожидаться автомобиля с нужными значениями этих факторов.
При этом удалось обеспечить равномерное трехкратное дублирование опытов, т.е. в обработке участвовало 48 специально отобранных наблюдений за автомобилями. Рандомизация опытов по редким сочетаниям факторов носила естественный характер, по остальным – проводилась специально.
Обработка результатов эксперимента велась по стандартным формулам для полного факторного эксперимента 24.
Интерес представляла не столько точность определения угольных потерь на конкретной дороге по найденной функции регрессии, сколько вывод о влиянии входных факторов на эти потери, поэтому при построении модели было решено ограничиться линейной частью и парными эффектами.
Проверка найденных коэффициентов на значимость по t-критерию Стьюдента подтвердила значимость всех коэффициентов линейной части и половины коэффициентов парных эффектов. Модель потерь угля у, г, в которой оставлены только значимые коэффициенты, имеет вид
у = 2 643 – 924х1 + 345х2 + 1 472х3 + 260х4 + 111х1х2 + 172х2х4 – 84х3х4. (4)
Данная модель признана адекватной по F-критерию Фишера.
Анализ модели показывает, что потери кусков угля на неровностях дороги зависят, во-первых, от темперамента водителя и, во-вторых, от отсутствия заднего борта. Наличие наращенных бортов влияет на потери заметно меньше. Порядковый номер неровности на дороге почти не влияет на потери, что вполне понятно, т.к. расстояние между ухабами невелико. При этом на втором ухабе потери несколько выше, что объясняется постепенным расползанием угольной «шапки» на начальном этапе транспортирования. Анализ парных эффектов требует большей осторожности из-за меньшей величины самих коэффициентов. Самый крупный из них в24 (перед х2х4) показывает, что машины с наращенными бортами имеют большие потери на втором ухабе, т.е. эти борта сдерживают расползание «шапки». Отрицательный коэффициент в34 свидетельствует о том, что темпераментный водитель больше теряет на первой неровности, т.е. весь процесс потерь у него происходит быстрее. Положительный коэффициент в12 обозначает, что отсутствие заднего борта, которое само по себе увеличивает потери, не позволяет насыпать при погрузке высокую «шапку», это уменьшает потери через наращенные борта.
Построенная модель, хотя и носит локальный характер и не включает многие факторы угольных потерь, однако дает возможность оценить влияние на потери задействованных в ней факторов и представить в динамике процесс потерь на начальном этапе транспортирования.
Выявлены особенности потерь угля при перевозке его речным транспортом, где разгрузка в портах осуществляется на береговую линию плавучими кранами. Затем бульдозерами и погрузчиками уголь перемещают от реки вглубь берега, формируя угольный бурт. При этом большое количество топлива измельчается, увлажняется при осадках и теряется, попадая в воду. «угольный след» образуется по длине перемещения угля от береговой линии и собственно в месте нахождения самого бурта. В то же время под воздействием ножа бульдозера часть грунта попадает в угольный бурт, разубоживая уголь и снижая его качество. С береговых угольных складов уголь грузится погрузчиками в автотранспорт и доставляется до места потребления со значительными потерями.
Особое место занимают потери угля от пыления при перевозках. Универсального метода расчета таких потерь нет, хотя этому вопросу посвящено много работ. Основываясь на экспериментально полученной В.Н. Мосинцом формуле удельной сдуваемости пыли в зависимости от скорости ветра V, критической скорости сдуваемости пыли Vкр и ряда констант, характеризующих свойства пыли, была получена формула интенсивности пыления g, мг/с, угольного объема с площадью основания So:

или

В формуле учтено также экспоненциальное затухание пыления от времени, соответствующее нормам естественной убыли угля. При транспортировании величину V в формуле (5) следует вычислять по формуле
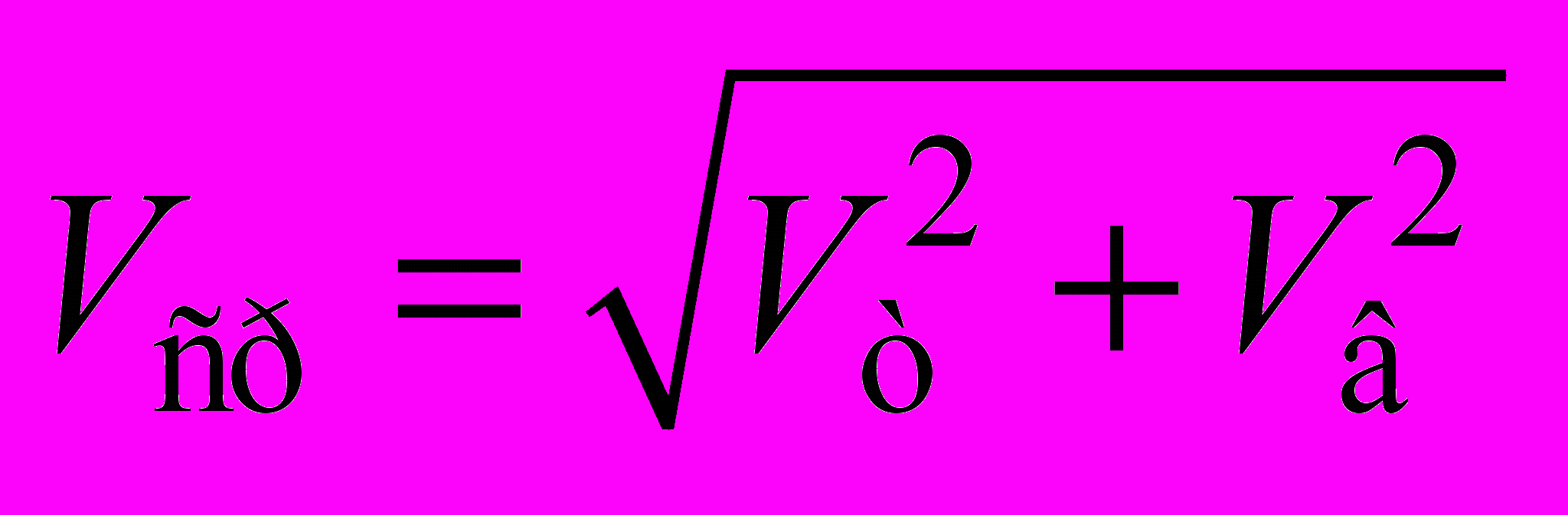
где Vт – скорость транспортирования; Vв – скорость ветра.
Потери угольной пыли при перевозке угля от разреза Бородинский до г. Красноярска (расстояние 180 км) по железной дороге в полувагонах размером 12,068 на 2,878 м и грузоподъемностью 69 т со средней скоростью на перегонах 14 м/с, скоростью ветра 5,4 м/с и при правильной погрузке составляют согласно формулам (5), (6) около 276 кг на полувагон, или 0,4 % от перевозимой массы, и соответствуют норме (до 0,6 %) угольных потерь для таких расстояний. Это подтверждает работоспособность приведенных формул.
При транспортировании угля водным транспортом на барже РВ-1800 с площадкой, имеющей So = 1 050 м2, грузоподъемностью 1 800 т (около 1 000 т угля), со скоростью Vт = 6,9 м/с (около 25 км/ч) при скорости ветра Vв = 8 м/с и критической скорости сдувания пыли Vкр = 3 м/с (учитывая влажность) потери от пыления согласно тем же формулам составляют:
за первые сутки – 936,8 кг (≈ 0,094 %),
за двое суток – 1 040 кг (≈ 0,104 %),
за трое суток – 1 051,2 кг (≈ 0,105 %),
за любое число суток – не превосходят 1 052,6 кг.
Котельным в черте города уголь доставляется с угольного склада автомобилями, при движении которых потери угля от пыления невелики из-за малого времени в пути и сравнительно невысоких скоростей. Однако угольная пыль наносит экологический вред.
Прямолинейный участок трассы, который автомобиль проходит со скоростью Vт, можно рассматривать как линейный импульсный источник пыли мощностью g/Vт, мг/м. Пыль сносится ветром и рассеивается в результате турбулентной диффузии. Рассеивание происходит в плоскости ХОУ, перпендикулярной линии источника, где ОХ – горизонтальная ось, а ОУ – вертикальная полуось. На основе формулы рассеивания пыли от точечного источника, приведенной В.С. Никитиным, была получена формула применительно к рассматриваемому случаю:
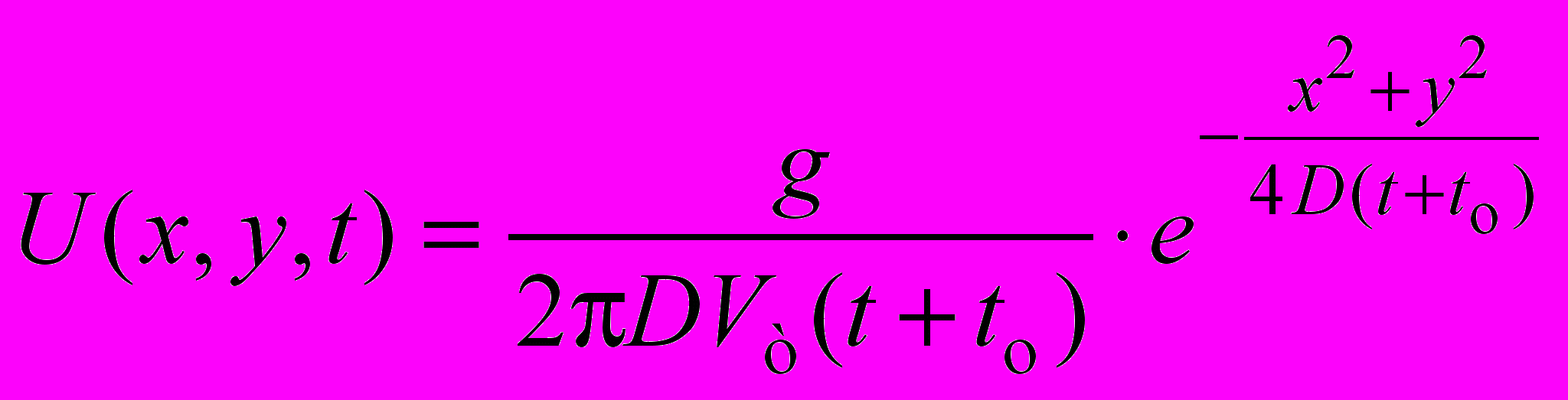
где
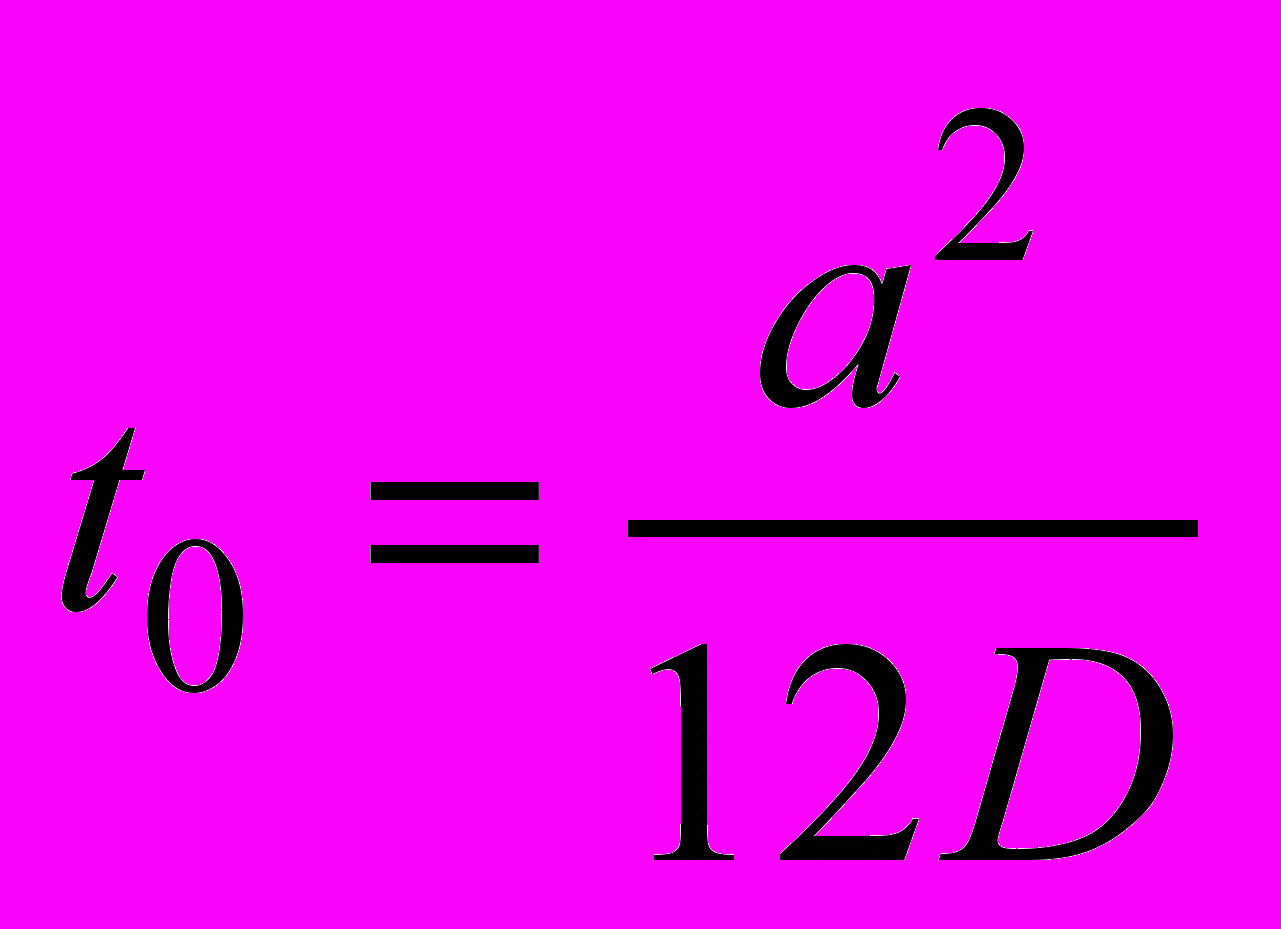
Формула (7) позволяет рассчитать рассеивание пыли за автомобилем, где началу пыления соответствует время t = 0. Пылевое облако сносится ветром, поэтому его центр движется со скоростью ветра. В любой момент времени наибольшая концентрация пыли достигается в центре пылевого облака и вычисляется по формуле
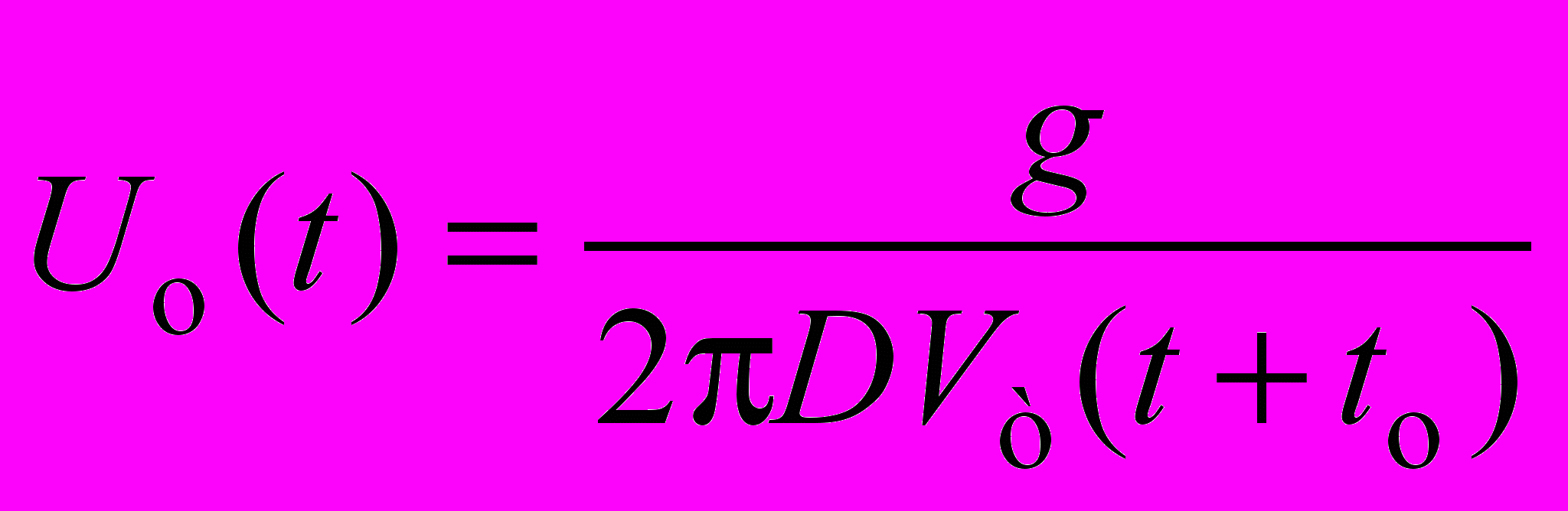
В начальный момент времени она равна своему максимальному значению:
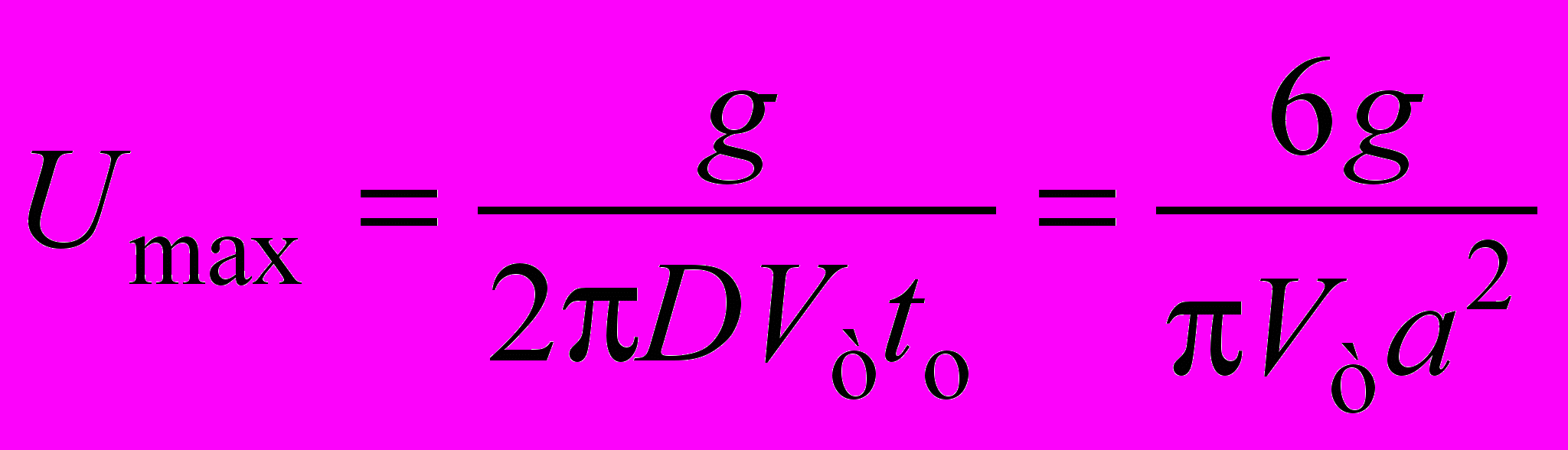
которое уменьшается в соответствии с формулой (8).
Перевозящий уголь автомобиль (например, КамАЗ-5511) высо- той 3,5 м до верха угольной «шапки», шириной 2,310 м и длиной 4,525 м, двигающийся со скоростью 8 м/с (29 км/ч) при скорости ветра 6 м/с, оставляет за собой шлейф пыли с концентрацией 22,1 мг/м3 в середине шлейфа. Это превышает предельно допустимую концентрацию (ПДК) угольной пыли 4 мг/м3 в 5,5 раза. Концентрация пыли в центре шлейфа падает ниже предельно допустимых концентраций через 73 с. Это подтверждает наличие экологического вреда от существующего способа перевозок.
Математическая модель расчета угольных потерь при перевозках железнодорожным, водным и автомобильным транспортом дает возможность оценить потери на этапах транспортирования, сходимость которых подтверждается нормами естественной убыли, и определить экологический ущерб, наносимый такими потерями.
Все рассмотренные виды потерь угля и связанный с ними экологический ущерб устраняются или уменьшаются при перевозках угля в контейнерах. При этом способе достигаются преимущества, которые позволяют:
Во-первых, контейнерный способ доставки даст возможность перевозить на одном транспортном средстве и хранить на одном складе угли различных марок.
Во-вторых, требования пожарной безопасности при перевозках угля в контейнерах сводятся к контролю температуры нагрева контейнера при погрузке. Ввиду относительно небольшого периода времени нахождения контейнера с углем на транспортном средстве, без попадания влаги и вентиляции, маловероятно, что окислительные процессы могут привести к нагреванию контейнера. Нагретые контейнеры к погрузке не допускаются, после их охлаждения подверженный окислению уголь реализуется на местном рынке.
В-третьих, контейнеры с углем перегружаются с применением грузоподъемного оборудования с электроприводом. Это даст возможность значительно сократить время перегрузки, исключить из работы бульдозеры, избежать потерь угля и, как следствие, загрязнения окружающей среды.
Таким образом, проведенные теоретические и экспериментальные исследования позволяют обосновать второе положение:
Установленные закономерности изменения потерь угля при перевозках и их влияния на загрязнение окружающей среды позволяют утверждать, что основным средством сохранения качественных и количественных характеристик сортового угля и брикетов и экологической безопасности является тарное перемещение их от момента переработки до использования.
3. Обоснование конструкций специализированных
контейнеров и математическое моделирование их оборота
Известные конструкции универсальных и специализированных контейнеров в силу разных причин не пригодны для их использования в перевозках сортового угля и брикетов. Поэтому для перевозки углепродукции повышенного качества в диссертации обоснованы необходимые требования и разработаны новые конструкции специализированных контейнеров, систематизированных (табл. 2) с учетом особенностей различных групп потребителей.
Таблица 2
Варианты конструкций специализированных контейнеров
для перевозки углепродукции повышенного качества
Класс, брутто | Назначение | Конструктивная особенность | Особенности разгрузки | Иллюстрация |
Малотоннажные, до 3 т | Индивидуальные потребители, котельные малой мощности | Разгрузочный люк | Порционная, с при-нудительным наклоном днища | Рис. 10 |
С автоматическим наклоном днища в сторону разгрузки | Рис. 11 | |||
Среднетоннажные, от 3 до 10 т | Котельные малой и средней мощности | Крышка из двух половин, закрывающаяся крюком | Единовременная, опрокидыванием | Рис. 12 |
Крупнотоннажные, свыше 10 т | Котельные средней мощности | Сдвижная крышка из двух половин | То же | Рис. 13 |
Средне- и крупнотоннажные | Для перевозки угле-продукции, cклон-ной к смерзанию | Мягкий контейнер в жестком каркасе | –«– | Рис. 14 |
Для определения необходимого количества специализированных контейнеров в конкретном грузопотоке выполнено математическое моделирование по технико-экономическим критериям.
![]() | ![]() | |||
а | б | |||
Рис. 10. Контейнер для перевозки, хранения и порционной разгрузки сортового угля или брикетов с принудительным наклоном днища в сторону разгрузки (пат. РФ № 2153452): а – транспортное положение; б – положение днища при разгрузке; 1 – крышка; 2 – ось; 3, 4 – пластины днища (3 – горизонтальная, 4 – вертикальная); 5 – шарнир; 6 – передняя стенка; 7 – дверца; 8 – шарнир; 9, 10 – фиксаторы открытого и закрытого положения; 11 – ролики; 12 – задняя стенка; 13 – гайка; 14 – шарнир гайки; 15 – тяга; 16 – подшипник; 17 – квадратные или шлицевые грани; 18 – желоб; 19 – опоры | ||||
![]() | ![]() | ![]() | ||
а | б | в | ||
Рис. 11. Контейнер с автоматическим наклоном днища в сторону разгрузки при уменьшении в нем топлива (пат. РФ № 2178379): а – транспортное положение; б – положение днища при разгрузке с пружиной кручения; в – то же с плоской ленточной пружиной; 1 – крышка; 2 – ось крышки; 3, 4 – пластины днища (3 – горизонтальная, 4 – вертикальная); 5 – шарнир пластин; 6 – шарнир днища; 7 – передняя стенка; 8 – дверца; 9 – шарнир дверцы; 10, 11 – фиксаторы открытого и закрытого положения дверцы; 12 – ролики; 13 – зад- няя стенка; 14 – пружина; 15 – пружина кручения; 16 – ленточная пружина | ||||
![]() | Рис. 12. Среднетоннажный контейнер с массой брутто 5–10 т для перевозки углепродукции (пат. РФ № 2243140): 1 – боковая стенка; 2 – крышка; 3 – шарнир; 4 – пружина; 5 – пластина; 6 – палец; 7 – рычаг; 8 – ось рычага; 9 – крюк; 10 – фиксатор |
![]() | Рис. 13. Крупнотоннажный кон- тейнер для перевозки углепро- дукции со сдвижными створками крыши (пат. РФ № 2271974): 1 – боковая стенка; 2 – торцевая стенка; 3 – сдвижная крыша, выполненная из шарнирно зак- репленных пластин; 4 – верхний трос; 5 – зубчатая рейка; 6 – нижний трос; 7 – блоки; 8 – нап-равляющие; 9 – шестерня; 10 – упор; 11 – шток пневмоцилиндра; 12 – пневмоцилиндр |
![]() | ![]() | ![]() |
а | б | в |