Автореферат диссертации на соискание учёной степени
Вид материала | Автореферат диссертации |
- Автореферат диссертации на соискание ученой степени, 378.33kb.
- Автореферат диссертации на соискание учёной степени, 846.35kb.
- Автореферат диссертации на соискание ученой степени, 267.76kb.
- Акинфиев Сергей Николаевич автореферат диссертации, 1335.17kb.
- L. в экосистемах баренцева моря >03. 02. 04 зоология 03. 02. 08 экология Автореферат, 302.63kb.
- Автореферат диссертации на соискание ученой степени, 645.65kb.
- Автореферат диссертации на соискание ученой степени, 678.39kb.
- Автореферат диссертации на соискание ученой степени, 331.91kb.
- Автореферат диссертации на соискание ученой степени, 298.92kb.
- Автореферат диссертации на соискание ученой степени, 500.38kb.
Результаты исследований апробировались на 50 Всесоюзных, Всероссийских, Республиканских и Международных конференциях, конгрессах, симпозиумах, и совещаниях. Основные результаты работы были представлены: на Межотраслевой научно-технической конференции (ВИАМ, Москва, 1984); ХХII-й Всесоюзной сессии «Защитные покрытия в машиностроении» (Киев, 1987); XIV Менделеевском съезде по общей и прикладной химии, (Москва, 1989); Всесоюзной конференции «Перспективные направления развития науки и технологии силикатов и тугоплавких неметаллических материалов» (Днепропетровск, 1991); на Конгрессе «Защита – 92» (Москва, 1992); International Simposium on Sol-gel Science and Technology (Los Angeles, Biltmore, 1994); 9-th International Workshop «Glasses, Ceramics, Hybrids and Nanocomposites from Gels» (Sheffield, 1996); на VII Международной конференции «Высокотемпературная химия силикатов и оксидов» (Санкт-Петербург, 1998); на II Съезде Российского керамического общества «Проблемы ультрадисперсного состояния» (Санкт-Петербург, 1999); 11th International Workshop «Glasses, Ceramics, Hybrids And Nanocomposites From Gels» (Padova, Italy, 2001); на III Межународной конференции «Электрическая изоляция – 2002» Санкт – Петербург, 2002); на Международном симпозиуме по теоретической и прикладной плазмохимии (Иваново-Плес, 2002); на VIII Всероссийском совещании «Высокотемпературная химия силикатов и оксидов» (Санкт-Петербург, 2002); Topical Meeting of the European Ceramic Society «Nanoparticles, Nanostructures & Nanocomposites» (Saint Petersburg, Russia 2004); Topical Meeting of the European Ceramic Society. Structural Chemistry of Partially Ordered Systems, Nanoparticalls and Nanocomposites, 2006, Saint-Petersburg. Russia.
Публикации.
Материалы диссертации опубликованы в одной монографии, 76 статьях и 45 тезисах докладов.
Объём и структура диссертации.
Диссертация состоит из введения, 8 глав, выводов, библиографии и приложений. Работа изложена на 351 странице машинописного текста, содержит 108 рисунков и 43 таблицы. Список литературы включает 400 наименований.
Краткое содержание диссертации.
Во Введении обоснована актуальность диссертационной работы, выбор темы, определены цели и задачи исследования. Представлены основные положения, выносимые на защиту.
В Главе 1 «Жаропрочные материалы и средства защиты от высокотемпературной газовой коррозии», состоящей из трёх основных разделов, представлен обзор литературных источников и исследований, посвящённых данной проблематике.
В первом разделе приводится краткий анализ состояния разработок в области создания жаропрочных материалов для силовых установок.
Во втором разделе рассматриваются характерные особенности газовой коррозии тугоплавких металлов в условиях высоких температур. Показано, что к наиболее перспективным конструкционным материалам с высокими механическими характеристиками в температурном интервале, который превышает 1200 С, относятся ниобиевые сплавы.
Третий раздел посвящён сравнительному анализу состояния разработок в области создания средств защиты тугоплавких конструкционных сплавов от высокотемпературной газовой коррозии. Приведённые данные свидетельствуют об эффективности покрытий как средства предотвращения окисления подложки. Сравнение различных методов формирования защитных покрытий показывает, что особый интерес, в силу универсальности и высокой технологичности, представляет метод синтеза бескислородных покрытий в режиме экзотермического взаимодействия из дисперсных композиций на основе компонентов (Mo, Cr, Ta, Nb, Si, B и др.), образующих жаростойкие соединения с температурой плавления значительно превышающей температуру активации процесса синтеза.
Прямой синтез бескислородных покрытий из дисперсных композиций на основе элементарных Mo, Cr, Ta, Nb, Si, B и др. впервые в отечественной и, по–видимому, в зарубежной практике был осуществлён группой сотрудников Института химии силикатов РАН (АН СССР) под руководством д. т. н., профессора А. И. Борисенко. Авторы показали, что образующаяся в системе Mo—Cr—Si (рис. 1) в условиях эвтектического плавления хрома и кремния (1355 °С) жидкая фаза инициирует процессы взаимодействия компонентов дисперсных композиций, которые завершаются формированием тугоплавких и жаростойких соединений с температурой плавления на 500600 °С, превышающей температуру активации экзотермической реакции.
На этапе разработки технологии синтеза бескислородных жаростойких покрытий неординарность проблемы, отсутствие опыта и научно обоснованных методов явились причиной преобладания эмпирического подхода при решении поставленной задачи. Практические результаты, базирующиеся на общих представлениях о характере физико-химических процессов, далеко опередили понимание механизма явлений, необходимое для создания промышленной технологии формирования покрытий (рис. 2).
В
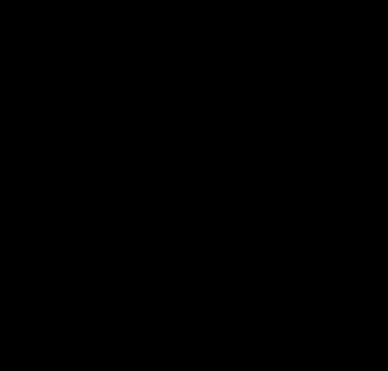
Исследования, которым посвящена диссертационная работа, акцентировались на последовательном изучении характера формирования бескислородных покрытий, в системе Cr—Mo—Nb—Si—B, рекомендованной для практического применения, при защите подложки из ниобиевого сплава 5ВМЦ. Выбор объекта определялся возможностью использования данных, полученных автором диссертации, на этапах отработки технологии в лабораторных и производственных условиях, включающих результаты стендовых испытаний.
В Главе 2 «Низкотемпературная стадия формирования бескислородных покрытий», которая состоит из двух основных разделов, рассмотрен низкотемпературный этап формирования покрытий в системе Cr—Si—Mo—Nb—B, связанный с получением суспензий, диспергированием и гомогенизацией поликомпонентных бескислородных композиций, процессом нанесения слоя покрытия на поверхность подложки.
Данные исследований указывают на то, что низкотемпературная стадия формирования бескислородных покрытий сопровождается рядом явлений, которые играют важную роль в предыстории синтеза защитного слоя.
Установлено, что процессы диспергирования и гомогенизации в системе Cr—Mo—Nb—Si—B характеризуются механохимическим и химическим взаимодействием компонентов дисперсной составляющей, дисперсной фазы и дисперсионной составляющей, что может оказывать как позитивное, так и негативное влияние на формирование фазового состава покрытий. В результате механохимического взаимодействия компонентов на стадии усреднения состава дисперсной составляющей возможно образование соединений, присутствие к
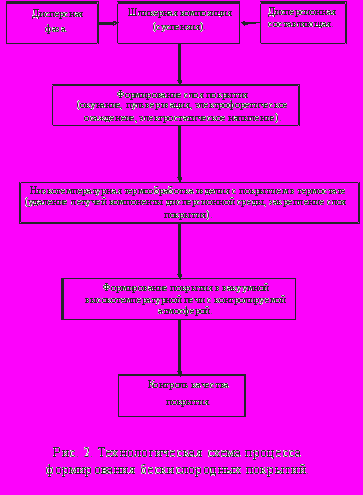
Формирование шликерных композиций (суспензий), состоящих из дисперсной фазы и дисперсионной среды (раствор анионного ПАВ - алкил бензолсульфоната натрия) сопровождается окислением дисперсной компоненты и образованием водорастворимых соединений, в частности гидроксидов молибдена переменного состава, которые играют значительную роль в процессе высокотемпературной стадии формирования покрытий.
Технологические аспекты нанесения и закрепления бескислородных композиций на поверхности подложки рассматриваются в разделе 2.2. второй главы. Опыт промышленного использования суспензионно-обжиговой технологии синтеза бескислородных защитных покрытий показал универсальность и технологичность суспензионного метода нанесения покрытий. Однако используемая технология низкотемпературной стадии формирования покрытий из суспензий методами погружения и пульверизации имеет ряд недостатков, одна из первопричин которых кроется в недостаточной седиментационной устойчивостью суспензии, обусловленной большим интервалом плотности компонентов дисперсной фазы (Сг, Мо, Nb, Si) и широким разбросом гранулометрических характеристик. Это приводит к образованию структурных дефектов и фазовых неоднородностей в защитном слое, снижая жаростойкость и эксплуатационные характеристики покрытий. Поэтому была рассмотрена возможность альтернативной замены компонентов композиции на бескислородные неогранические соединения, которые обладают более низкой плотностью, высокой дисперсностью и удельной поверхностью.
Экспериментальная и технологическая проработка показала, что в наибольшей степени этим качествам отвечают сульфиды, селениды, силициды и гидриды металлов V – VI -а гр. Результаты исследования характера влияния замены дисперсного молибдена, в композиции (Cr—Mo—Nb—Si—B), на MoS2, MoSe2 и MoSi2, на свойства синтезированных покрытий, подтвердили обоснованность сделанных предположений. Было установлено, что введение данных соединений, за исключением дисилицида молибдена, инициирует процессы формирования покрытий с улучшенной структурой и фазовым составом, в котором преобладают соединения, определяющие высокую жаростойкость защитного слоя.
Перспективность использования халькогенидных соединений в качестве составной части поликомпонентных бескислородных композиций была подтверждена исследованиями в области возможного использования метода электрофоретического осаждения для формирования бескислородных покрытий из поликомпонентных композиций, которые показали, что в условиях совместного электрофоретического осаждения компонентов дисперсной композиции в системе Si - MoS2 на выходе можно получать гомогенизированный осадок необходимой толщины в пределах допустимых отклонений от заданного состава.
В Главе 3 «Высокотемпературный синтез бескислородных покрытий», состоящей из пяти разделов, представлены данные, характеризующие составы и свойства бескислородных покрытий, синтезированных в условиях прямого синтеза, физико-химические особенности формирования бескислородных высокоэнтальпийных соединений и покрытий при пониженном остаточном давлении в области высоких температур, аппаратурное оформление условий высокотемпературного синтеза.
Анализ термограмм высокотемпературного синтеза бескислородной композиции в системе Cr—Mo—Nb—Si—B и визуальные наблюдения показали, что температура активации процесса находится в интервале 13001500 °С. Процесс характеризуется наличием значительного экзотермического эффекта, который фиксируется прямыми термопарными измерениями, охватывает температурный интервал ~13001700 °С и достигает своего максимума на пятой секунде с момента начала взаимодействия компонентов системы.
Пример синтеза диборида циркония ZrB2 (-DH°298 = -76,7 ккал/моль) при тепловом воспламенении в условиях внешнего неизотермического разогрева, показывает, что процессы в аналогичных системах могут протекать в твёрдой фазе и характеризуются чрезвычайно высокой активностью. Термопарные измерения, выполненные в процессе горения образца из механической дисперсной смеси циркония и бора (соотношение 1:2, ат. %) показали, что в момент горения, скорость изменения температуры, на участке монотонного роста, составила (~20×103 °С/с), а скорость распространении волны горения 35 мм/с. Процесс взаимодействия компонентов в объёме ~ 25 см3 завершается образованием практически чистого диборида циркония в течение 1¸1,5 с.
Таким образом, при исследовании характера тепловых процессов, сопровождающих стадию высокотемпературного синтеза бескислородных покрытий было установлено, что формирование силицидов и боридов может протекать с высокими скоростями и сопровождаться значительными тепловыми эффектами.
Синтез покрытий на основе бескислородных композиций осуществляется, как правило, в вакууме (Ратм. ост.=110-1Па). Температурный диапазон, определённый в экспериментальных условиях, составляет 14501600 С. Временной интервал термообработки находится в пределах нескольких десятков секунд, определяется массой изделия и параметрами высокотемпературной установки.
Характер формирования бескислородных покрытий в условиях высокотемпературного синтеза при пониженном остаточном давлении связан с количественными изменениями соотношения компонентов по сравнению с исходным составом композиции. Это обусловлено испарением ряда компонентов композиции и продуктов термодеструкции, образующихся соединений, взаймодействием компонентов композиции и системы подложка - покрытие в целом.
Один из разделов третьей главы посвящён изучению особенностей характера формирования бескислородных покрытий в экспериментальных условиях. Опыт показал, что переход от исследований к условиям производства может сопровождаться ухудшением жаростойкости покрытий. Анализ физико-химических процессов, сопровождающих высокотемпературную стадию экспериментального «экспресс» синтеза покрытий на основе боросилицидных композиций, в установке с вакуумируемым объёмом 2 л и вольфрамовым нагревательным элементом позволил выявить основную причину этого явления, которая обусловлена характером формирования боросилицидных покрытий в условиях ограниченного пространства.
Н
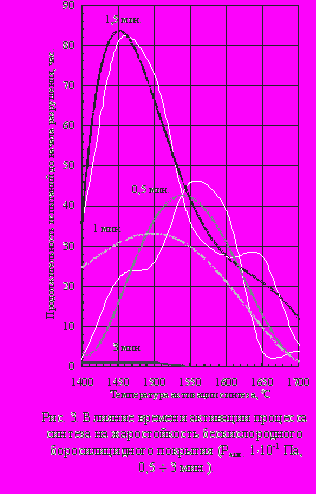
В Главе 4 «Физико-химические процессы, сопровождающие высокотемпературный синтез бескислородных покрытий, система Cr—Mo—Nb—Si—B, в условиях оптимизации технологического процесса», состоящей из четырёх разделов, рассмотрены результаты исследования физико-химических явлений, сопровождающих высокотемпературный синтез бескислородных покрытий в условиях оптимизации технологического процесса.
В качестве критерия, на основании которого определялся оптимальный режим высокотемпературного синтеза бескислородных покрытий, были использованы данные испытаний на жаростойкость образцов с трёхслойным покрытием, время активации синтеза которого составляло 30 с, 1 мин, 1,5 и 3 мин (диапазон температур 14001800 С через 50 С). Данные эксперимента подтвердили эмпирически установленный факт существования определённых временных и температурных интервалов формирования покрытий, обладающих максимальной жаростойкостью. Для исследуемых образцов оптимальный режим высокотемпературного синтеза находился в пределах 1,5 мин и 1450 °С соответственно (рис. 3).
Исследование процессов фазообразования в бескислородной боросилицидной композиции проводилось на образцах с одно-, двух- и трёхслойными покрытиями, которые формировались в оптимальном временном промежутке 1,5 мин. и температурном диапазоне 1400¸1800 °С. Результаты исследований, выполненных с привлечением метода рентгеновского фазового анализа, микрорентгеноспектрального анализа и растровой электронной микроскопии, позволили установить, что характер формирования фазового состава в условиях активации высокотемпературного синтеза покрытий, в бескислородной системе определяется взаимодействием компонентов композиции и процессами фазообразования на границе раздела подложка – покрытие. По мере удаления от поверхности подложки, при послойном синтезе, происходит упорядочение кристаллической структуры покрытия, а основными фазообразующими составляющими становятся компоненты композиции.
Активность процессов фазообразования в покрытии начинает проявляться при температуре активации синтеза 1450 °С. Оптимальные температуры активации, в бескислородной системе Cr—Mo—Nb—Si—B—подложка, находятся в температурном интервале 14501550 С. Данная температурная область характеризуется формированием высших силицидов, образованием в зоне подложка - покрытие силицидных образований с преимущественным содержанием ниобия и хрома, граничного слоя, фазовый состав которого идентифицирован как диборид ниобия NbB2 (табл. 1).
В области температур 1500¸1700 °C образуются устойчивые кристаллические фазы. Высокотемпературный интервал активации синтеза 1750 ¸ 1800 °C характеризуется
Таблица. 1. Фазовый состав бескислородного боросилицидного покрытия, система Cr – Mo – Nb – Si – B, синтезированного в оптимальном временном (1,5 мин.) и температурном (14501500 °С) интервалах.
Слой покрытия | Доминирующие фазы |
Первый, область подложки | MoSi2, NbSi2, Nb5Si3, NbCr2 (следы), (Nb,Cr)xBy, NbВ2, Si (следы) |
Второй, промежуточный | MoSi2, NbSi2, (Mo,Nb) Si2, (Mo,Nb)5Si3, NbCr2 (следы), (Nb,Cr)x By, NbВ2 |
Третий, поверхность покрытия | MoSi2, NbSi2, Nb5Si3, (Nb,Cr)xBy, NbВ2 |
формированием низших силицидов и менее упорядоченных кристаллических образований, происходит усиление интенсивности взаимодействия ниобиевой подложки с компонентами покрытия, эрозия подложки, разрушение зоны обогащённой хромом и боридного слоя, наблюдается появление структурных неоднородностей.
Анализ результатов интегрирования изотермических зависимостей относительной ренетгеновской интенсивности компонентов (МРСА) по толщине покрытия в температурном интервале синтеза 1400¸1800 °С свидетельствуют о существенном влиянии на фазообразование процессов массопереноса, обусловленных характером (экзо- эндо-) взаимодействия в системе, испарением (сублимацией) компонентов композиции и продуктов термодеструкции соединений, образующихся при более низких температурах.
Детальное исследование характера количественных изменений, сопровождающих высокотемпературный синтез покрытий, проведённое с использованием метода весового анализа в широком температурном интервале показало, что рост доли потерь в диапазоне температур 14001600 °С обусловлен испарением адсорбированной влаги и продуктов разложения кристаллогидратов МоО25(ОН)510, термодеструкцией остатков ПАВ - алкилбензолсульфоната СnH2n+1 C6H4SO3Na (n = 10 – 18), Na2SO4 и Na2SO3, а также испарением (сублимацией) продуктов взаимодействия, образующихся на стадии формирования суспензии и компонентов композиции (хрома, кремния и бора). Увеличение потерь при переходе от первого слоя покрытия к последующим, является следствием ослабления влияния подложки на процессы взаимодействия с компонентами композиции.
Изменение характера процесса в температурном интервале 16001800 °С вызвано перестройкой процессов фазообразования, разложением высших силицидов и образованием твёрдых растворов низших силицидов (Nb,Mo)5Si3, (Mo,Nb)5Si3, замещением кремния бором в низших силицидах молибдена Mo5(В,Si)3, формированием боросилицидов (Nb,Mo)5(В,Si)3.
Таким образом, один из важных факторов, определяющих характер формирования бескислородных покрытий в условиях высокотемпературного синтеза, при пониженном остаточном давлении связан с количественными изменениями, которые оказывают значительное влияние на изменение заданного состава.
В Главе 5 «Формирование и эксплуатация бескислородных покрытий в условиях нестационарного теплообмена», которая состоит из трёх основных разделов, приводятся данные исследования физико-химических явлений, характерных для процессов формирования и эксплуатации бескислородных покрытий в условиях нестационарного теплообмена.
Из обзора литературных источников следует, что современные энергетические установки отличает интенсивность тепловых процессов, обусловленных высокими температурами, скоростями и давлением продуктов сгорания. Так, например, на отдельных участках камеры сгорания жидкостного ракетного двигателя ЖРД, удельные тепловые потоки могут достигать нескольких десятков млн. ккал/м2×час. С момента начала химической реакции, по мере продвижения вдоль тракта ЖРД, температура рабочего тела повышается до 3000 °С и более, а высокие скорости газового потока, неравномерность смешения компонентов топлива способствуют эрозии – размыванию стенки камеры сгорания.
Одно из основных требований технологии формирования бескислородных покрытий на деталях энергетических установок сопряжено с возможностью оптимизации условий процесса высокотемпературной активации синтеза в зоне теплонапряжённых участков, т. е. создания на этих участках защитного слоя, структура и фазовый состав которого должны обеспечивать высокие эксплуатационные характеристики.
Преобладающее большинство объектов, используемых в теплоэнергетических установках, имеет сложную конфигурацию. Масса подложки, ее теплопроводность, наличие внутренних полостей, утолщений корпуса, ряд других физических, геометрических и размерных факторов, характеризующих конкретное изделие, затрудняет определение оптимальных температурно-временных параметров процесса высокотемпературной активации синтеза в потенциально теплонапряжённых зонах.
З
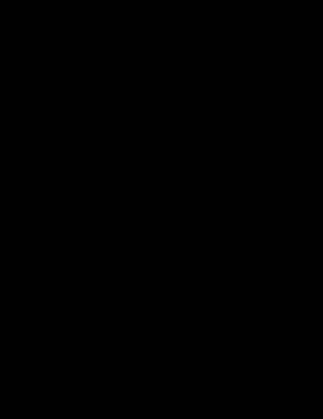
Мониторинг системы позволил фиксировать изменение основных параметров процесса (температура, давление) в реальном масштабе времени и определять, таким образом, значение временного интервала формирования защитного слоя с оптимальным фазовым составом на наиболее ответственных участках детали.
Другое важное обстоятельство, которое необходимо учитывать, связано с тем, что покрытия, формируемые на различных участках детали в условиях нестационарного теплообмена, при пониженном атмосферном давлении, отличаясь по фазовому составу, характеризуются определённой структурой. В частности, высокотемпературная активация синтеза покрытия при температуре 1500 °С сопровождается образованием, в зоне подложка – покрытие, слоя обогащенного бором, фазовый состав которого идентифицирован, как диборид ниобия NbB2 (рис. 5). Синтезированные покрытия обладают хорошей жаростойкостью, а температурный интервал активации синтеза является оптимальным. Таким образом, высокие эксплуатационные характеристики защитного слоя обусловлены не только свойствами фазового состава, но и структурой покрытия. Это явилось основанием для проведения исследований характера формирования бескислородных покрытий в условиях температурного градиента.
При исследовании взаимодействия компонентов композиции Cr—Mo—Nb—Si—B в системе покрытие—подложка—покрытие, было получено подтверждение того, что при формировании фазового состава и структуры бескислородных покрытий определённое влияние на характер процесса оказывает массоперенос вещества, который может инициироваться газообразными продуктами, образующимися в результате испарения (сублимации) ряда компонентов покрытия (хром, кремний), продуктов взаимодействия некоторых компонентов композиции с остаточными газами (оксиды, сульфиды и др.), диссоциации остаточной и гидратированной влаги на водород и кислород, при 1500 °С и выше.
Л
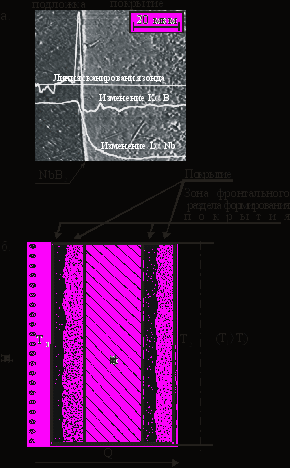
Исследования физико-химических явлений, характеризующих процессы эксплуатации бескислородных покрытий в условиях нестационарного теплообмена, который является характерным для работы камеры сгорания ЖРД в импульсном режиме, показали, что фазовый состав и структура защитного слоя, синтезированного в оптимальном температурном интервале, наиболее адекватно отвечают предъявляемым требованиям.
Процесс эксплуатации защитного слоя в условиях воздействия высокотемпературного сверхзвукового потока продуктов горения несимметричного диметилгидразина N2H2(CH3)2 и окислителя, азотная кислота HNO3 (78%) + тетраоксид азота N2O4 (22%), при максимально допустимой температуре 1550 50 С, сопровождается образованием боридов, сложных боридов и боросилицидов (табл. 2).
Таблица 2. Фазовый состав покрытия Cr – Mo – Nb – Si – B, синтезированного в оптимальном режиме (1450¸1500 °С), после огневых испытаний в течение 300 с. Среднеинтегральная температура поверхности камеры сгорания 1550 ± 50°С.
Объект исследования | Доминирующие фазы |
поверхность синтезированного покрытия | MoSi2, NbSi2, (Nb,Cr)xBy |
наружная поверхность стенки камеры сгорания | Cr3 Nb2 Si6, Nb Cr2, Nb B2, Mo5 Si3, Cr3 Nb Si2,66 |
внутренняя поверхность стенки камеры сгорания | Nb5Si3, Nb B2, Cr3 Nb2 Si6, (Mo, Nb)5 Si3 |
Низкая Жаростойкость покрытий, синтезированных в температурном интервале, превышающем оптимальный режим активации, обусловлена взаимодействием кристаллических новообразований и разрыхлением кристаллической решётки, что приводит, в конечном счёте, к разрушению покрытия.
В Главе 6 «Высокотемпературный синтез бескислородных покрытий в контролируемой атмосфере», которая состоит из двух разделов, рассматриваются технологические и прикладные аспекты высокотемпературного синтеза бескислородных покрытий в контролируемой атмосфере.
Создание контролируемой атмосферы в условиях высокотемпературного синтеза бескислородных покрытий диктуется, главным образом, необходимостью предохранения от окисления компонентов покрытия и подложки. Синтез бескислородных покрытий осуществляется в вакууме или среде инертного газа.
Данные сравнительного исследования процессов фазообразования и жаростойкости бескислородных покрытий на основе композиции Cr—Mo—Nb—Si—B, синтезированных в условиях контролируемой атмосферы (аргон, азот, воздух) указывают на то, что газовая среда является активным агентом, который оказывает значительное влияние на процессы фазообразования в высоко-энтальпийных системах.
Фазовый состав покрытий, синтезированных в среде аргона и азота, представлен жаростойкими соединениями, которые являются типичными для бескислородных покрытий, сформированных в оптимальных условиях термической активации, при пониженном остаточном давлении воздушной атмосферы.
В покрытии, сформированном в оптимальном интервале остаточного давления, присутствуют силициды молибдена, хрома и ниобия, силициды, легированные бором, диборид ниобия и, в случае синтеза защитного слоя в атмосфере азота, нитриды ниобия. Максимальную жаростойкость имеют покрытия, синтезированные при остаточном давлении 2,75×10 Па. (2×10ˉ4 ат.), в последовательности: аргон – 78 ч; азот - 36 ч и воздуха - 20 ч.
Увеличение или понижение давления приводит к ухудшению жаростойкости защитного слоя (табл. 3). Синтез бескислородных покрытий в области пониженного давления атмосферы воздуха приводит к резкому падению жаростойкости защитного слоя. Отмечена непосредственная связь характера формирования структуры покрытий, с составом и давленим газовой среды.
Ухудшение жаростойкости покрытий, в ряду аргон—азот—воздух связано с дефектностью защитного слоя. Общим для покрытий, сформированных в атмосфере азота и воздуха, является присутствие структурных неоднородностей идентичных по строению.
Данные изменения интегральной концентрации компонентов композиции в зоне подложки от состава и давления, указывают на то, что в покрытиях с максимальной жаростойкостью преобладают соединения, которые преимущественно содержат кремний и бор.
Понижение жаростойкости в ряду аргон—азот—воздух сопровождается изменением соотношения концентрации металлической и неметаллической составляющей композиции (Nb, Cr, Mo)/(Si, B): ~0,33 (аргон), 0,5 (азот), 1,5 (воздух).
Характер изменения интегральной концентрации компонентов бескислородных покрытий, синтезированных в атмосфере воздуха, указывает на высокое содержание ниобия, которое превышает исходное более чем на 40 ат. %.
Таблица 3. Жаростойкость бескислородного боросилицидного покрытия на основе композиции Cr – Si – Mo – Nb – B, синтезированного в контролируемой атмосфере.
Состав атмосферы. | Остаточное давление Р, Па., (ат.). | Жаростойкость покрытия в статической атмосфере воздуха, при температуре 1400 С, ч. |
АРГОН. | 5,0104 Па. (0,5 ат.) | 36 |
2,7510 Па. (210ˉ4 ат.). | 78 | |
1,2310¹ Па. (1,210ˉ4 ат.) | 59-78 | |
5,51 Па. (5,410ˉ5 ат.) | 36-54 | |
АЗОТ. | 5,0104 Па. (0,5 ат.) | 10 |
2,7510 Па. (210ˉ4 ат.). | 36 | |
1,2310¹ Па. (1,210ˉ4 ат.) | 29-36 | |
5,51 Па. (5,410ˉ5 ат.) | 10 | |
ВОЗДУХ. | 5,0104 Па. (0,5 ат.) | |
2,7510 Па. (210ˉ4 ат.). | 20 | |
1,2310¹ Па. (1,210ˉ4 ат.) | 1 ч. | |
5,51 Па. (5,410ˉ5 ат.) | 1 ч. |
В Главе 7 «Жаростойкие бескислородные покрытия: свойства, вопросы совершенствования химии и технологии формирования, прикладные аспекты» рассматриваются свойства бескислородных покрытий (табл. 4) и некоторые направления модификации технологии синтеза.
Представлены результаты исследований, связанных с возможностью использования приёмов синтеза наноразмерных частиц (НРЧ) в условиях термического разложения химических соединений и формирования жаростойких покрытий в системе Cr—Mo—Nb—Si—B из композиций, содержащих бескислородные соединения. Приводятся данные, характеризующие состояние разработок в области создания бескислородных покрытий для технологической защиты конструкционных тугоплавких сплавов при изготовлении деталей методами горячей пластической деформации.
Эксплуатационные характеристики жаростойких бескислородных покрытий говорят о том, что химическая технология средств защиты тугоплавких металлов от высокотемпературной газовой коррозии на основе бескислородных композиций позволяет синтезировать покрытия, отвечающие основным требованиям надёжности, которые предъявляются к теплонапряжённым элементам конструкции высокоэнергетических установок.
Особо необходимо отметить, что температура эксплуатации такого защитного слоя существенно превышает температуры синтеза и порога начала разупрочнения подложки. Это явилось достаточным основанием для использования бескислородных жаростойких покрытий в качестве эффективной защиты деталей из тугоплавких конструкционных сплавов, в условиях высокой температуры и агрессивного влияния продуктов горения компонентов ракетных топлив, таких как несимметричный диметилгидразин и азотная кислота.
Таблица 4. Основные свойства жаростойких бескислородных покрытий (композиция Cr – Si – Mo – Nb – B, состав БС-975).
Свойства покрытия. | Показатели, характеризующие свойства покрытия. | Примечания |
Цвет и внешний вид покрытия. | Светло-серое, матовое, ровное. | |
Коэффициент черноты. | 0,900,92 | ОС 92-099-69 |
Толщина покрытия, мкм. | 6070 мкм | |
Масса покрытия на ед. поверхности. | 115 гм-2 | |
Температурный коэффициент линейного расширения в интервале температур (201000 С), С-1. | (7074)10-7 С-1 | ГОСТ 15173 |
Термостойкость – количество теплосмен в атм. воздуха (20 ![]() | 200 циклов | |
Коррозионная стойкость, растворение в меланже (смесь 100% HNO3 + 96% H2SO4, соотношение 9/1). | 1 мкм/год | Температура испытаний 2530 С |
Микротвёрдость, кгсмм-2. | 12001300 кгсмм-2 | ГОСТ 9450-60 |
Прочность при ударе, кгссм не менее. | 80 кгссм | ГОСТ 4765-73 |
Прочность при изгибе, мм. | 20 мм | ГОСТ 6806-73 |
Предел прочности при отрыве, кгссм-2. | 300 кгссм-2 | ГОСТ 14760-69 |
Пористость (общая), %. | 00,02 % | ГОСТ 2409-67 |
Вибростойкость. Электродинамический вибростенд, частота 500 Гц, виброускорение до 5 g. | Признаки разрушения отсутствуют. | |
Назначение и рекомендуемая область применения покрытия. | Применяется для длительной защиты ниобиевых сплавов от газовой коррозии в интервале 1300 С. | |
Возможность массового производства компонентов, входящих в состав покрытия. | Исходные компоненты имеют ГОСТы и выпускаются отечественной промышленностью. | |
Кем разработан состав и технология синтеза покрытия. | Институт химии силикатов РАН. |
Важное обстоятельство технологии синтеза бескислородных покрытий связано с возможностью широкой корректировки свойств защитного слоя путём изменения составов, формирования композиционных многослойных покрытий, создания промежуточных и барьерных слоёв (карбидные, боридные и др.) без существенного изменения технологических параметров.
В тоже время результаты исследования характера физико-химических процессов, сопровождающих основные этапы синтеза, указывают на существование резервов, использование которых даёт возможность существенно улучшить качество покрытий. Один из таких резервов кроется в использовании композиций, содержащих бескислородные соединения.
Данные исследования характера формирования бескислородных покрытий в системах Cr—Si—MoS2—Nb—B и Cr—Si—MoSe2—Nb—B подтверждают высокую эффективность модификации бескислородных композиций халькогенидными соединениями молибдена на процессы, сопровождающие основные этапы низкотемпературной и высокотемпературной стадии технологии синтеза жаростойких бескислородных покрытий.
Обзор литературных источников по этой проблематике указывает на то, что синтез жаростойких бескислородных покрытий в системе Cr—Si—Mo—Nb—B из композиций, содержащих халькогениды молибдена MoS2 и MoSe2, имеет много общего с процессами, которые сопровождают синтез НРЧ в условиях термического разложения химических соединений при получении металлов в индивидуальном состоянии или в виде составных частей нанокомпозитов. Следствием образования, в результате диссоциации халькогенидов, высокоактивной формы элементарного молибдена, является формирование фазового состава с преобладанием соединений, определяющих высокую жаростойкость защитного слоя (табл. 5).
Таблица 5. Данные сравнительных исследований фазового состава и жаростойкости бескислородных покрытий, синтезированных из композиций на основе Cr – Mo – Nb – Si – B, содержащих халькогениды молибдена (MoS2, MoSe2). Синтез осуществлён в контролируемой атмосфере воздуха, при остаточном давлении 2,7510 Па. (210ˉ4 ат.).
Состав композиции | Объект исследования | Доминирующие фазы | Жаростойкость, ч (воздух, 1400/1600 С) |
Исходная композиция Cr – Si – Mo – Nb – B | поверхность покрытия | MoSi2, Mo5(B, Si)3, NbSi2, (Nb, Cr)xBy | 45/3 |
промежуточная область | MoSi2, Cr3NbSi2,66, NbSi2, CrSi | ||
зона подложка - покрытие | MoSi2, Cr3NbSi2,66, NbSi2, NbB2 | ||
Cr – Si – MoS2 – Nb – B | поверхность покрытия | MoSi2, NbSi2, Mo5(B, Si)3, (Nb, Cr)xBy | 170/6 |
промежуточная область | MoSi2, Cr3NbSi2,66, NbSi2 | ||
зона подложка - покрытие | MoSi2, Cr3NbSi2,66, Nb5Si3 | ||
Cr – Si – MoSe2 – Nb – B | поверхность покрытия | MoSi2, NbSi2, CrB | 560/6 |
промежуточная область | Mo, MoSi2, NbSi2, Cr3NbSi2,66 | ||
зона подложка - покрытие | Mo, MoSi2, NbSi2, |
Отщепляемые халькогенидные составляющие (S, Se) инициируют окислительно-восстановительные процессы, протекающие как в формируемом слое, так и на границе раздела с окружающей средой, вследствие чего образуются газообразные соединения, которые легко удаляются из зоны реакции в условиях пониженного давления.
Полученные результаты свидетельствуют о том, что использование, в качестве прекурсоров, халькогенидов или других бескислородных соединений металлов IV–VI а групп и аналогичных соединений некоторых металлов расширяет область применения элементов технологии синтеза высокодисперсных материалов.
В ряду положительных свойств бескислородных жаростойких покрытий следует отметить их пластичность в горячем состоянии и высокую адгезионную прочность сцепления с поверхностью. Эти качества позволяют использовать бескислородные покрытия для технологической защиты конструкционных, тугоплавких сплавов в условиях пластической деформации при выполнении операций, связанных с различными видами механической обработки заготовок - ковки, штамповки и др. Переделы такого рода на заготовках с бескислородными технологическими покрытиями могут осуществляться в условиях воздушной среды и оптимальном температурном интервале пластичности конструкционных сплавов на основе ниобия и молибдена (1200÷1300 ºС).
Данные исследований, модификация и корректировка составов, отработка режимов формирования защитного слоя, позволили перейти к производственному технологическому процессу использования бескислородных покрытий для технологической защиты конструкционных, тугоплавких сплавов при изготовлении деталей методом горячей обьемной штамповки (табл. 6).
Пластическая деформация деталей осуществлялась на горизонтально-ковочной машине ГКМ-4, кривошипном прессе КГШП-4000т и паровоздушном молоте с массой падающих частей 16 т за 1-3 перехода без промежуточных подогревов. Во всех случаях покрытие на поверхности отштампованных деталей сохраняется в виде тонкого, но сплошного слоя, без дефектов трещин и сколов.
Таблица. 6. Механические свойства сплава ВН2АЭ с бескислородным технологическим покрытием после горячей деформации.
Показатели | Требования инструкции ИМ 33-75 | Фрагменты деталей, использованные для проведения испытаний. | ||
Стакан. | Втулка. | Уголок. | ||
Прочность на растяжение в, кгмм-2. | 40 | 60,8 | 57 | 63 |
Предел текучести т, кгмм-2. | 30 | 48,3 | 45,1 | 54 |
Относительное удлинение , %. | 18 | 24,3 | 24 | 19 |
Относительное сужение , %. | 45 | 56 | 60,7 | 55 |
Ударная вязкость аH, кГмсм-2. | 8,0 | 12,1 | 10,3 | 11 |
Применение бескислородных технологических покрытий позволило исключить дополнительную механическую обработку или уменьшить припуск до 0,51,0 мм на сторону. Высокое качество поверхности деталей после штамповки, технологичность процесса и его рентабельность, позволили рекомендовать бескислородные модифицированные композиции к широкому использованию в качестве защитных покрытий при производстве точных рациональных заготовок из конструкционных тугоплавких сплавов методами пластической деформации. Промышленное использование технологического процесса подтверждено отраслевым стандартом ОСТ 92-4437-84 «Поковки кованые и штампованные из ниобиевых сплавов», регламентирующем технические требования, правила приёмки и методы испытаний.
В Главе 8 «Синтез стеклокерамических материалов с использованием приёмов золь - гель технологии», которая состоит из трёх разделов, предметом исследования являются золь-гель методы получения композиционных стеклокерамических материалов и покрытий.
История исследований в области химии композиционных стеклокерамических материалов во многом связана с работами группы сотрудников Института химии силикатов РАН, возглавляемой профессором А. И. Борисенко, который положил начало получению неорганических покрытий золь-гель методом из дисперсных коллоидных систем - золей и суспензий на основе алкоксидных, щелочесиликатных и фосфатных прекурсоров с оксидными наполнителями.
Использование принципиально новых растворных композиций для получения жаростойких стеклокерамических электроизоляционных покрытий, в которых дисперсионной компонентой является коллоидный раствор - золь, а дисперсной фазой высокодисперсные оксидные компоненты, позволило создать новый вид стеклокерамических материалов, существенно отличающихся от аналогов, получаемых с использованием методов традиционного эмалирования.
В тоже время исследования позволили выявить некоторые особенности присущие физико-химическим процессам, которые протекают в условиях синтеза стеклокерамических материалов с использованием элементов золь-гель технологии:
• Во-первых, в случае получения стекловидной матрицы непосредственно из золей существуют определенные ограничения, лимитирующие количество образующейся стеклосвязки, обусловленные, прежде всего, растворимостью исходных соединений, условиями протекания гидролиза и поликонденсации прекурсоров в тонком слое золя во время формирования стекловидного слоя.
• Во-вторых, при получении материалов из суспензий, в состав которых, наряду с золями входит дисперсная неорганическая составляющая, на высокотемпературной стадии синтеза значительная часть образующейся стеклофазы, в большинстве случаев, расходуется на взаимодействие с наполнителем. В конечном счете, это негативно отражается на прочности, пористости и других свойствах стеклокерамики.
Один из путей решения проблемы находится в плоскости использования, в процессе получения материалов и покрытий, промежуточных продуктов в виде – дисперсных стеклокерамических композиций, которые формируются из гомогенизированных суспензий, в состав которых входит дисперсная компонента и дисперсионная составляющая, как правило, золи водно-спиртовых растворов частично гидролизованного и полимеризованного тетраэтилового эфира ортокремнёвой кислоты (ТЭС), нитратов металлов, эмульгаторов и соответствующего катализатора. Основа дисперсионной составляющей стеклообразующих растворов может быть представлена рядом других алкоксидных соединений, а также щелочесиликатными и фосфатными прекурсорами (рис. 6).
М
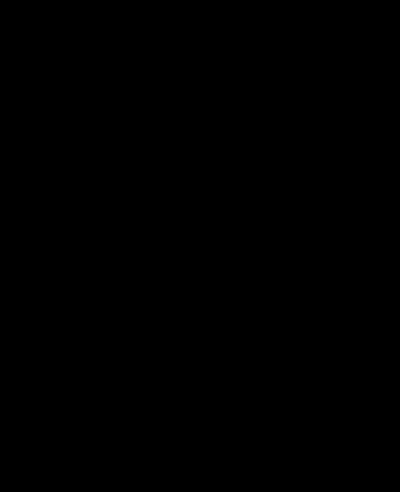
В контексте данной проблематики представлены основные результаты исследований, полученные при разработке технологии синтеза дисперсного «модифицированного» оксида алюминия Al2O3 с использованием элементов золь-гель синтеза из прекурсоров на основе g- , a- формы Al2O3 и кордиеритоподобной золь–гель композиции 2CoO×2Al2O3×5SiO2.
Выбор композиции, используемой для модифицирования поверхности дисперсной составляющей путём создания стекловидной оболочки, обусловлен физико-химическими свойствами стекла, которое формируется в той или иной системе. В данном случае это система 2CoO×2Al2O3×5SiO2 идентичная по составу кордиериту 2MgO×2Al2O3×5SiO2, в котором магний замещен кобальтом. Стекло имеет низкий коэффициент теплового расширения и не кристаллизуется при длительном отжиге, что позволяет использовать «модифицированную» дисперсную композицию в качестве исходного материала для формирования теплозащитных покрытий методами электродугового плазменного напыления.
Основной элемент предлагаемой технологии связан с оптимизацией процессов структурирования, гелеобразования и коагуляции в золях и суспензиях, что позволяет получать устойчивые «наполненные» гели с дисперсной составляющей, равномерно распределенной по всему объему, без признаков расслоения и седиментации. Такие гели являются исходным продуктом для формирования, после соответствующей термообработки, дисперсных «модифицированных» стеклокерамических материалов, которые представляют собой частицы неорганических веществ, заключенных в стекловидную оболочку практически любого состава.
В качестве дисперсной составляющей «наполненных» гелей, использовался g- Al2O3 с размером зерна 50¸90 мкм. Повышение седиментационной устойчивости дисперсии осуществлялось путём введения поливинилового спирта (ПВС) в количестве 1¸10 мас.%. При исследовании влияния процессов гелеобразования на свойства формируемого материала, соотношение количества дисперсионной среды и дисперсной составляющей варьировалось в пределах 20¸80 мас.%. В оптимальном варианте соотношение компонентов в наполненном ксерогеле составило - ксерогель+ПВС / g-Al2O3 = 50 / 50. Гомогенизация дисперсии проводилась путём ультразвукового воздействия. Этап формирования «наполненных» гелей после определённого промежутка времени вызревания завершался термостатированием при 100 °С и образованием дисперсного продукта в виде оксидных частиц заключённых в оболочку из ксерогеля.
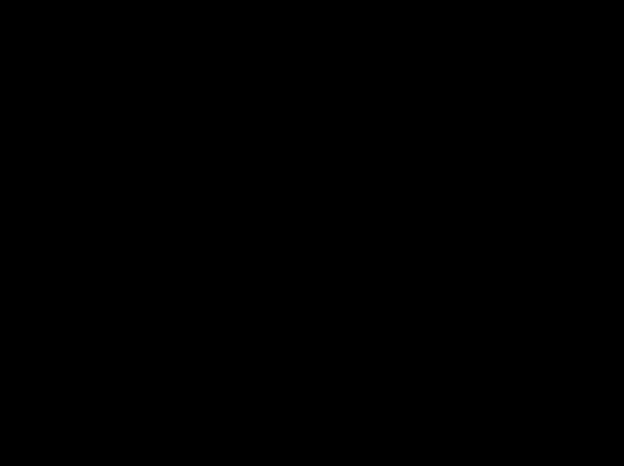
Оценка характера взаимодействия золя с поверхностью оксида алюминия производилась на основании атомной силовой микроскопии (АСМ) поверхности полированного корунда «Polycor 5» с плёнкой из золя 2CoO×2Al2O3×5SiO2, нанесённой методом центрифугирования, которая позволяет (рис. 7) констатировать факт присутствия на поверхности подложки бездефектной, достаточно однородной плёнки.
Заключительная стадия технологического процесса формирования модифицированной композиции осуществляется путём высокотемпературной термообработки промежуточного дисперсного продукта в температурном интервале 1000¸1300 °С и завершается образованием стекловидной оболочки на поверхности оксидной частицы. В процессе термообработки создаются условия, при которых формируется продукт, обладающий необходимым комплексом физико-химических свойств.
Результаты физико-химических исследований характера изменений, которые происходят при термообработке гелей и модифицированных композиций, полученных из суспензий с различной концентрацией дисперсной составляющей, дают основание полагать, что при разложении геля в температурном интервале, превышающем 500 °С, происходит образование смеси аморфных оксидов, инертных по отношению к наполнителю. Повышение температуры до 1000 °С сопровождается началом взаимодействием компонентов в объёме ксерогеля с образованием алюмокобальтовой шпинели CoAl2O4 и оксидов алюминия различных переходных кристаллических модификаций (κ- , d- , χ- Al2O3).
Область температур ≤ 1300 °С характеризуется продолжением образования в ксерогеле алюмокобальтовой шпинели CoAl2O4 и появлением β- кристобаллита, при этом исходный дисперсный g- Al2O3 переходит в a- Al2O3. Следует отметить определённую зависимость, связанную с резким уменьшением интенсивности аморфной фазы при введении в состав композиции поливинилового спирта (ПВС), что, по-видимому, обусловлено характером агрегатирования компонентов растворной композиции в присутствии поверхностно-активного вещества, которым является ПВС.
Одно из примечательных явлений связано с появлением в составе композиций, полученных без введения ПВС, после термообработки при 1300 °С низкотемпературной переходной фазы оксида алюминия (κ- Al2O3). Это, вероятно, вызвано определённым стабилизирующим влиянием, которое может оказывать силикатная оболочка, сформированная на поверхности дисперсного оксида алюминия.
Таким образом, оптимальный температурный интервал термообработки композиции находится в области температуры 1000 °С. Следствием дальнейшего повышения температуры является взаимодействие компонентов оболочки и образование соединений с дисперсной частицей. В результате этих процессов из модифицирующей составляющей выводятся компоненты, в данном случае оксиды, необходимые для последующего формирования фазы, обеспечивающей контактное взаимодействие в условиях синтеза покрытий или компактного материала.
В ряде случаев в технологии получения тугоплавких материалов и тонкодисперсных порошков используется низкотемпературная плазма. Плазмохимический синтез в электродуговой плазме сочетает высокие температуры и большие скорости охлаждения.
Перспективы, которые открывает использование электродуговой плазмы на высокотемпературной стадии синтеза «модифицированных» композиций из дисперсных оксидов, представляют несомненный интерес. Наряду с возможностью создания высоких температур в ионизированной газовой среде заданного состава, это связано с большими скоростями гетерогенных реакций.
Высокая скорость взаимодействия обусловлена атомными и молекулярными столкновениями в перемешивающихся потоках с относительно большими концентрациями реакционноспособных частиц, что приводит к образованию дефектов на поверхности твёрдой фазы, ускоряющих диффузию исходных веществ из объёма к поверхности.
С
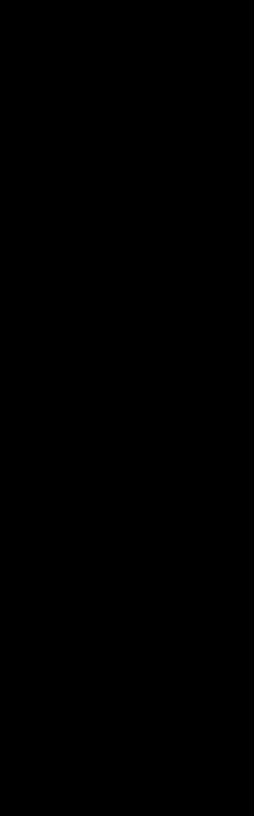
В целом, можно констатировать следующее:
- созданы основы технологии получения стеклокерамических материалов с использованием элементов золь-гель синтеза устойчивых дисперсий с дисперсными оксидами из золей на основе тетраэтоксисилана (ТЭС), допантов и стабилизирующих добавок;
- синтезирован композиционный керамический порошковый материал на основе дисперсного Al2O3 (g-, a- формы), капсулированного в стекловидную оболочку из кордиеритоподобной золь–гель композиции 2CoO×2Al2O3×5SiO2;
- установлен факт стабилизации промежуточных метастабильных фаз оксида алюминия: d- и χ- фаз Аl2О3 при 1000 °С, κ- фазы при 1300° С;
- выявлен ряд особенностей, связанных с процессами аморфизации стекловидной оболочки и стабилизации промежуточных метастабильных фаз оксида алюминия: κ- и χ- Al2O3 в условиях воздействия воздушной электродуговой плазмы;
- материалы разработки защищены двумя патентами РФ.