Основы технологии производства электротранспорта
Вид материала | Лекции |
- Примерные программы Специальные дисциплины примерная программа дисциплины основы сельскохозяйственного, 1349.6kb.
- 6М071300 Транспорт, транспортная техника и технологии По дисциплине – «Основы технологии, 110.86kb.
- Вопросы для подготовки к экзамену по дисциплине: «Основы технологии производства, 31.12kb.
- «Подъемно-транспортные, строительные, дорожные машины и оборудование», 14.82kb.
- Темы курсовых работ по курсу «Основы строительного производства» для студентов направления, 11.2kb.
- К рабочей программе учебной дисциплины, 23.79kb.
- Курс Код Факультет, наименование направления подготовки (специальности) Перечень, 130.47kb.
- Программа дополнительного образования при кафедре Технологии строительного производства, 173.05kb.
- М. В. Ломоносова Кафедра экономики и организации производства И. А. Назарова Основы, 599.04kb.
- Вопросы к курсовому экзамену по фармацевтической технологии заводского производства, 113.84kb.
Испытания на прочность проводят с целью опытной оценки уровня напряжений в элементах ЭТ в условиях действия эксплуатационных нагрузок. Экспериментальные испытания проводят на наиболее нагруженных элементах конструкций с помощью тензодатчиков, устанавливаемых в наиболее предполагаемых концентраций напряжений.
Уровень напряжений записывается на ленте осциллографа или магнитографа. Ходовые и динамические испытания всех составных частей ЭТ осуществляют при реализации силы тяги номинального режима и допустимой скорости движения. В обязательном порядке при этом измеряют перемещения в вертикальной и горизонтальной плоскости (на прямых участках и в кривых

При воздействии на ЭТ ударного усилия, эквивалентного продольной схимающей силе 2450 кН , приложенной к автосцепкам, определяют в горизонтальной (по оси пути) и вертикальной плоскоскостях ускорения электрооборудования, установленного внутри кузова, и отдельных несущих конструкций.
В процессе прочностных испытаний измеряют напряжения в составных частях ЭТ как от статических, так и динамических нагрузок по ГОСТ-23098-78. При статических нагрузках фиксируют напряжения в рамах тележек при опирании колес на рельс и сход их с рельсов от действия горизонтальной поперечной силы, в тормозной системе.
Затем определяют динамические добавки к напряжениям при реализации максимальных тяговых и тормозных усилий при

Напряжения и прочность кузова и механического оборудования на НЭВЗе определяют путем спуска подвижного состава с горки на жеские упоры. Моторные думпкары дополнительно испытывают на динамическую нагрузку от падения стального шара массой 3 т с высоты от 1 до 2,5 м. На дно думпкара предварительно из мягкой породы толщиной 250 мм.
Тягово-энергетические испытания преследуют цель: проверить соответствие опытного образца ЭТ техническому заданию и условиям эксплуатации; изучения тяговых и тормозных свойств подвижного состава и оценки стойкости его оборудования к воздействию тепловых нагрузок в условиях реальной эксплуатации в режимах, оговоренных ГОСТ 23098-78.
В процессе изучения тяговых свойств ЭТ производят снятие скоростных и тяговых характеристик. Скоростные характеристики V(I) получают экспериментально с помощью фиксации режимов работы ТД наименее нагруженных осей. При этом одновременно записывается уровень напряжения контактной сети, а затем осуществляется пересчет характеристик к номинальному питающему напряжению.
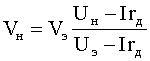
где



Типовую тяговую характеристику двигателя


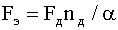
где





При этих испытаниях большой объем отводится на определение сцепных свойств локмотива, т.е. определение коэффициента сцепления и сопротивления движению в функции скорости локомотива. Коэффициент сцепления для определенной скорости определяют по силе тяги ТД в момент начала боксования тех осей, по которым произошел срыв из-за ограничения по сцеплению. По зафиксированным значениям токов и экспериментальным тяговым характеристикам определяют значения силы тяги

Расчетный коэффициент сцепления определяют на основании обобщения многочисленных опытов с последующей их статической обработкой.
При этих испытаниях также снимают внешние характеристики преобразователей, эффективность регулирования напряжения, определяют коэффициенты мощности и полезного действия ЭТ, фиксируют параметры работы защиты силовых и вспомогательных цепей, цепей управления и сигнализации.
Большой объем в программе тягово-энергетических испытаний занимают исследования тормозных свойств ЭТ. Здесь определяют удельный возврат электроэнергии при рекуперативном торможении, нагрев стабилизирующих резисторов и эффективность примененной системы автоматического управления. Для реостатного торможения определяют дополнительный расход электроэнергии для питания обмоток возбуждения ТД также контролируют нагрев тормозных резисторов.
Для обоих видов электрического торможения определяют токовые нагрузки по цепи возбуждения и якорям ТД, расчетный коэффициент сцепления, время перехода из тягового в тормозной режим и обратно. Проверяется система блокирования электрического тормоза и пневматических тормозов.
Тормозные характеристики строят аналогично тяговым характеристикам, при этом тормозную силу определяют по формуле
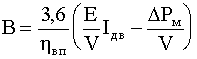
где

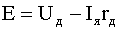









Испытпния проводятся с использованием специальных вагон-лабораторий тяги, динамометрических вагонов и специальной аппаратуры (магнитографов, осциллографов, измерительных комплексов и контрольных приборов). Особо тщательно проводится тарировка измерительных систем ( тензостанций, контрольных приборов, включенных на измерительные шунты и трансформаторы тока, особенно постоянного тока, т.к. точность измерений зависит от загрузки вторичной обмотки трансформатора тока). Нагрев обмоток тягового двигателя одна из нерешенных проблем для испытаний, ибо метод амперметра-вольтметра требует остановки поезда при испытаниях, что вносит дополнительные искажения при замерах.
По результатам испытаний делаются выводы соответствия опытного образца ЭТ ТЗ техническим условиям и условиям эксплуатации.
Приемо-сдаточные испытания.
Для всех типов ЭТ на стадии ОКР и промышленного производства проводятся приемо-сдаточные испытания.
После завершения монтажно-сборочных работ и очистки ЭТ от посторонних предметов, монтажных и технических материалов проверяют комплектность и полноту установки составных частей, качество сборки ЭТ, внешний вид, а также соответствие всего оборудования, правильность маркировки составных частей и его оборудования.
Проверяют правильность заправки системы охлаждения силового трансформатора с взятием пробы масла.
Убеждаются в заправке и соответствие времени года смазки моторно-осевых подшипников, кожухов зубчатых передач ТД и маслом компрессоров. Осматривают надежность защитных заземлений, снятие закорачивающих перемычек, наличие пломб на защитной и другой аппаратуре, а также наличие необходимых зазоров между токоведущими и заземленными частями.
Проверяются все электрические цепи на соответствие принципиальной электрической схеме.
Проверяют соответствие положений органов управления и тяговых электрических машин, аппаратов, связи, сигнализации, освещения и других устройств, надежность срабатывания аппаратов защиты, блокировок и устройств электробезопасности обслуживающего персонала.
Настраивают аппаратуру АЛСН и радиостанцию, проверяют схему их велючения и работу.
В процессе приемо-сдаточных испытаний контролируют сопротивления, емкость и индуктивность элементов цепей. Отклонение активных сопроивлений резисторов от номинальных значений при t=








Проверяется емкость конденсаторов, при этом возможно применение метода амперметра-вольтметра. Для чего на f=50 Гц от автотрансформатора измеряют I и U и емкость в МкФ определяют как С = 3185 I/U.
Проверку индуктивности нагрузочных, коммутирующих дросселей, дросселей фильтров и прочих катушек, а также регулировку электрических аппаратов проводят, пользуясь методами, описанными в ГОСТ 9219-75.
Проверяют уставки всех аппаратов защиты и управления. Все аппараты до установки на ЭТ должны быть подвергнуты испытаниям после их изготовления.
Проверяются с помощью электронно-лучевых осциллографов настройки аппаратуры управления тиристорными преобразователями.
Измеряют сопротивление изоляции электрических цепей, аккумуляторной батареи; проверяют электрическую прочность изоляции высоким напряжением. Сопротивление изоляции проверяют мегометрами напряжением 2500, 1000 или 500 В в зависимости от рабочего напряжения цепи.
Измерение сопротивления изоляции аккумуляторной батареи проивзодят без включения нагрузки с помощью вольтметра, сопротивление которого должно быть точно известно. Тогда сопротивление изоляции батареи относительно земли

где R - сопротивление вольтметра, кОм; U - напряжение на зажимах батареи без нагрузки, В;


Сопротивление изоляции заряженной батареи относительно земли (кожуха) ЭТ должно быть не менее 25 кОм. Затем проверяют работу РЩ, а также пределы стабилизации питающих напряжений.
Проверяется правильность регулировки и работы пневматических цепей ( работу компрессоров, тормозов, выходов штоков и т.д.).
Проверяют работу токоприемников с контролем всех параметров (время подъема, опускания при давлении 0,49 МПа).
Проверяют работу токоприемников при давлении 0,35 МПа, пневматических блокировок, песочниц и вспомогательного компрессора.
При проверке системы вентиляции измеряют частоту вращения вентиляторов и распределение и подачу воздуха по всем потребителям, а также избыточное давление в кузове.
Испытание кузова на каплезащищенность проводят дождеванием.
Затем проводится проверка работы ЭТ на обкатном кольце - пробег не менее 30 км.
Измерение массы ( взвешивание) производят после всех работ по сборке и проведения испытания.
Запас песка должен быть 2/3 от полного объема, одновременно проверяют развеску ЭТ по осям и колесам.
Периодические и типовые испытания.
Проводят для отдельного подвижного состава, так для промышленного ЭТ периодические испытания проводят через 5 лет, для ЭПС такие испытания проводят после выполения ТР-3 , они аналогичны приемо-сдаточным испытаниям.
Их необходимость выявления работоспособности всех узлов подвижного состава.
В этот вид испытаний включают вентиляционные испытания, проверку работоспособности аккумуляторной батареи; при изменении конструкции - испытание на прочность; проверяют рапределение токов и обратных напряжений преобразователей под нагрузкой, проверяется вписывание в кривую с измерением зазоров между элементами экипажной части; проводятся санитарно-гигаенические исследования в части контроля соответствия защитных приспособлений, системы пожаротушения и освещенности, температуры, уровня шума и вибраций.
Типовые испытания проводят при изменении основных параметров ЭТ. Объем и последовательность выполнения этого вида испытаний определяются программой и методикой разработанной предприятием-разработчиком.
Специальные испытания. Сюда относят: эксплуатационные, на ремонтопригодность, санитарно-гигиенические и на радиопомехи.
Эксплуатационные испытания проводят с целью оценки безотносительности ЭТ при продолжительной работе в реальных условиях эксплуатации. Пробег за время проведения испытаний должен быть не менее 5000 км.
Проводит их предприятие-разработчик совместно с заказчиком, иногда привлекают сторонние организации.
Проверяется работоспособность ЭТ в различное время года; удобство управления и обслуживания; оптимальность системы ТО, предусмотренной инструкцией по эксплуатации; приспособленность ЭТ к экипировке; уровень запыленности помещений и оборудования, эффективность тормозных средств, рациональный режим вождения поезда с установлением нормы по массе поезда; параметры безотказной работы; износ быстроизнашиваемых деталей; достаточность жесткости конструкции элементов экипажной части.
Испытание на ремонтопригодность проводят с целью определения приспособленности ЭТ к обнаружению причин возникновения его отказов и устранению их последствий. На основе анализа статистических данных об отказах и повреждениях локомотивов, а также проведения опытных ремонтов и ТО при испытаниях на ремонтопригодность определяют трудоемкость монтажа, демонтажа составных частей и оптимальность комплекта запасных частей, инструктажа и принадлежностей.
Проводят предприятия-разработчики и заказчики с привлечением при необхоидмости научно-исследовательских организаций.
Пример.
Участие кафедры ЭПС ДВГАПС в освоении ВЛ80Р и ВЛ85, а теперь ВЛ65.
Санитарно-гигиенические испытания выполняют с целью проверки соответствия ЭТ требованиям ьезопасности и охраны труда. Участвуют в испытаниях те же организации, что и выше, та же и программа.
Испытания на радиопомехи проводят для определения соответствия ЭТ допустимым нормам индустриальных помех.
Контрольные вопросы:
1. Каким видам испытаний подвергается подвижной состав?
2. Как проверить нагревание тягового двигателя?
3. Как определить напряжение в металлах механического оборудования?
4. Какие датчики перемещений известны Вам?
5. Какие датчики поворота вала используются на подвижном составе?
6. Как проверить герметичность кузова подвижного состава?
7. Методы и средства проверки уровня изоляции электрических цепей.
8. В каких случаях проверяется интенсивность охлаждения тяговых двигателей?
9. Как определить расход охлаждающего воздуха?
3.1. Выбор конструкционных материалов и методов заготовительной технологии
Технологические основы конструирования - это принцип конструктивной реализации технологических пребований производства к продукции машиностроения, касающиеся влияния на конструирование выбора материалов и технологических требований обработки и сборки.
При разработке новой конструкции выбор материала является важным этапом создания нового изделия. Отмечается, что стоимость материалов в серийном и особенно в массовом производстве составляет до 30-60 % от общей стоимости машин. Поэтому уменьшение затрат на материалы является одним из главных направлений снижения себестоимости.
В настоящее время наряду с традиционными материалами сплавами черных и цветных металлов и дерева при изготовлении ЭТ широко используют такие принципиально новые материалы, как пластмассы, металло-керамические композиции, техническая резина, монолитная изоляция и т.д. Применение их в новых конструкциях позволяет значительно изменить технологию изготовления, снизить стоимость материалов, уменьшить эксплуатационные расходы.
Так применение пластмассы позволяет уменьшить вес изделия, получить хорошие диэлектрические свойства, повысить химостойкость, а в отдельных случаях и хладостойкость, улучшить внешний вид, упростить технологию изготовления деталей.
В последние 10-15 лет пластмассы как конструктивный материал применят в конструкции кузовов механического и электрического оборудования ЭТ.
Выбор материалов осуществляют на основе технико-экономического анализа с учетом требований:
1. Конструктивных - материал должен удовлетворять требованиям конструкции по своим прочностным и физическим характристикам.
2. Технологических - материал должен удовлетворять требованиям манимальной трудоемкости на всех стадиях изготовления деталей с возможностью внедрения прогрессивных технологий изготовления заготовок и их обработки.
3. Экономических - материал должен быть дешевым, допускать экономичные методы изготовления и обработки, обеспечивать большой срок службы при минимальных затратах эксплуатационных расходов.
4. Эстетико-художественных - иметь хорошие декоратинвные свойства и обесппечивать получение нужных конструктивно-художественных и гигиенических форм.
Вбор материала по двум вариантам может быть оценен по стоимостному показателю

где



Как видим , при сравнении выбираемых материалов учитываются все затраты , в том числе на заготовительные технологии.
Основными методами получения заготовок деталей являются методы литья, обработки давлением, листовой штамповки и сварки. Каждый из них имеет много разновидностей.
Литье - в разовые песчаные формы, металлические формы - кокили (кокильное литье ) , в оболочковые тонкостенные формы ( корковое литье, ( по выплавляемым моделям, под давлением.
Обработка металлов под давлением - свободная ковка, горячая штамповка, горячая и холодная высадка, штамповка жидкого металла.
Листовая штамповка - методом гибки, вытяжки, вырубки.
Сварка - открытой дугой, под флюсом, в струе газа и пр.
Выбор способа изготовления заготовок вновь зависит от многих факторов, которые также можно учесть по стоимостным показателям с учетом требований к конструкции, допусков на обработку и др.
Контрольные вопросы:
1. Чем необходимо руководствоваться при выборе материалов для тягового подвижного состава?
2. Какие методы изготовления заготовок известны Вам?
3. Что является определяющим при выборе материала?
3.2. Технологические требования конструирования литых заготовок
Методами литейного производства для ЭТ изготовляют элементы механического борудования (буксы, детали автосцепок, рамы тележек и др.) , электрических машин (корпуса ТД и вспомогательных машин и др.) , элементы электрических аппаратов и ТД, существуют различные методы литейного производства, о чем мы уже говорили. Широкое использование литейного производства объясняется двумя обстоятельствами.
Во-первых, при литейной технологии изготовления самый короткий цикл переработки и поэтому минимальная стоимость литейных материалов.
Во-вторых, литейные технологии позволяют создать достаточно жеские монтажные конструкции, такие как рамы тележек без сварных, заклепочных, болтовых и прочих соединений, создающих различные концентраторы напряжений, моноблочные конструкции требуют арматурой в виде пространственной решетки 1 (рис. 3.1., а ) или отдельных вставок - вкладышей 2 (рис.3.1., б).
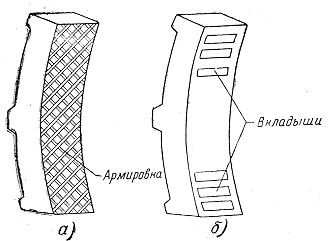
Рис 3.1. Варианты исполнения композиционных тормозных колодок методом литья.
Точность изготовления и чмстота поверхности деталей зависит от выбранногометода литья.
Точность литья в печатные формы не превышает 7-9-го класса точности и 1-5 -го классов шероховатости.
Литье в металлические формы - точность отливок лежит в пределах 6-9-го классов при широховатости 3-5-го классов. Оболочковое литье дает 5-8 класс точности и 3-5 - широховатости. Выплавляемые модели 4-7 точности и 4-6 класса широховатости. Литье под давлением позволяет получить 3-5 класс точности и 5-7 класс широховатости, а это уже уровень черновой и даже чистовой механической обработки.
При проектировании литых заготовок необходимо:
1. Упрощение формы деталей, всякие выступы - ребра, фланцы, бобышки и т.п. не должны затруднять выемку модели из формы и усложнять модели, а сами модели по возможности не иметь разъемных частей, не желательно применение стержней. Литейные уклоны должны быть: 1/5 - для деталей до 25 мм и 1/50 - для деталей 500 мм и выше. Нежелательно применение О-образных сечений. Предпочтение отдается формам открытое корыто, U и П-образное сечение.
Например, литые подшипниковые стойки (рис.3.2).
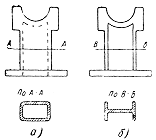
Рис.3.2. Нетехнологичная и технологичная
литые подшипниковые стойки
2. Толщина стенок и неравномерность сечений ухудшают условия заполнения форм жидким металлом. Выбор толщины обусловлен методом литья и габаритами детали. Так, при литье в землю толщина стенок должна быть больше, чем при литье под давлением. Важным в этом плане выбор оптимальной толщины стенок, ибо это вес и прочность литья.
В этом плане толщина стенок А и прочность литой заготовки

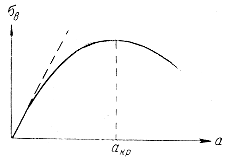
Рис.3.3. Зависимость

заготовки от толщины стенки А
Как видим имеет место


Оптимальной толщину стенок и сечений стальных отливок при размере детали до 500 мм составляет 6-8 мм; 500-1000 мм



Чтобы обеспечить равномерность охлаждения внутренние стенки делают на 20% тоньше, чем наружные. Толщину наружных ребер жескости с учетом фактора концентрации температурных напряжений принимают не более 0,8 , а внутренних, как более медленно остывающих, - не более 0,6 толщины стенок.
3. Важным при проектировании литых конструкций является выбор сопряжений литых стенок, применение технологических отверстий, переходных конусов и др. (см.рис.3.4).
Так, в соединениях стенок различного сечения быстрее сотывают меньшего сечения, что создает жесткую оболочку, внутри которой находится еще жидкий металл. При усадке металла в этом узле образуются пустоты и рыхлости, поэтому необходимо предусматривать дополнительные питатели.
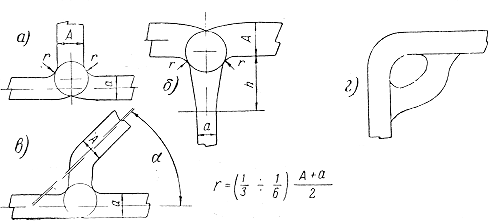
Рис.3.4. Схемы сопряжения стенок литых деталей
Для исключения тепловых узлов в местах соединений необходимо: стыковку стенок производить в шахматном порядке (исключать крестообразные соединения); соединения производить под прямым углом, радиусы закруглений r следует принимать




При стыковке, когда А>1,25а применяют плавные конусные переходы на длине h как на рис.3.4.б при этом уклон конуса должен быть не более 1/4; стенки , расположенные под углом

Если не удается избежать тепловых узлов - ставят над ними прибыли (выпоры), которые усложняют литейные формы и дополнительной обработки литья.
Иными словами как видим, для литыхконструкций приходится учитывать множество факторов конструктивного и технологического порядка.
Пример.
Литые рамы тележек ВЛ8 первых выпусков имели много трещин в боковинах над буксами.
Контрольные вопросы:
1. Какие детали подвижного состава изготовляют методами литейного производства?
2. Каковы требования к литым конструкциям ЭТ?
3. Какие особенности конструкции литых рам ЭТ?
3.3.Технологические требования к изготовлению
сварных конструкций ЭТ
Формирование неразборных конструкций методом сварки при изготовлении и ремонте ЭТ имеет очень широкое применение. К примеру кузовов, рамных конструкций изтолстолистового и профильного проката, отдельных деталей аппаратов и электрических машин, восстановление наплавкой изношенных деталей и устранение параков литых деталей и штамповок.
Это вызвано преимуществом сварки перед клепаными , а в ряде случаев и литыми конструкциями. Основные из них:
1. Экономия металла, снижение веса на 10-20% по сравнению с клепаными и на 20-40% - с литыми. Особенно сварные конструкции предпочтительны перед литыми для сравнительно простых по форме сборочных единиц. Сложные же - литые. Большая перспектива у штампо-сварных конструкций (рам тележек).
2. Снижение трудоемкости по сравнению с клепаными конструкциями (не требуются отверстия, установка заклепок, их изготовление) улучшаются условиятруда(шум).
3. Снижение стоимости оборудования и увеличение съема продукции по сравнению с клепаными и литыми конструкциями.
При разработке технологии сварочных процессов необходимо руководствоваться ГОСТ, ТУ по применении сварки, инструктивных указаний к примеру ЦТтеп/251.
При проектировани сварных конструкций необходимо:
1. Выбор вида сварки производить на основе технико-экономических соображений учитывая производительность, качество сварных швов, наличие оборудования и т.д. Выбор вида сварки зависит от толщины свариваемых конструкций и длины свариваемых швов. Для толстолистового и профильного проката - электродуговая сварка: ручная, автоматическая или полуавтоматическая. Короткие швы варят вручную или, полуавтоматической. Тонколистовой прокат (обшивка кузова и др.) варят шовной или точечной контактной электросваркой, автоматической или полуавтоматической под слоем флюса, что ограничивает прожог. Иногда применяют специальные виды, так для тонких листов применяют сварку электрозаклепками (тонкий лист к толстому прокату); бездуговую электрошлаковую сварку (при варке обечаек толщиной 40 мм и более. Обечайка - барабан без днища); контактную стыковую сварку сопротивлением (например, при сварке головок с тягами тормозной рычажной передачи) и др.
2. Отдавать предпочтение сварным конструкциям с автоматической сваркой - длинные прямые или круговые швы, что легко автоматизировать с помощью самоходных сварочных головок, сварочных порталов и самоходных сварочных тракторов с работов по направляющим и без них.
3. Выбирать конструкционные материалы, имеющие наиболее хорошую свариваемость при принятом способе сварки и большую производительность.
4. Стремится создавать уравновешенные конструкции с симметричным расположением швов, уменьшающих коробление при сварке, использовать штампованные отбортовки и ЗИГИ для создания жесткости.
5. Отдавать предпочтение сварным конструкциям с использованием стеллажей, сборочно-сварочных кондукторов, кантователей, манипуляторов и стапелей.
6. Учитывать требования удобства сборки конструкций для сварки, сварки их, осмотра и контроля сварных швов. Отдавать предпочтение нижнему расположению швов (расположение электрода над швом), т.к. формирование потолочного и вертикального шва затруднительно.
Необходимо добиваться равнопрочности металла сварного шва и основного, что нетрудно получить при сварке низкоуглеродистых и низколегированных сталей. При сварке же легированных сталей прочность шва обычно уступает прочности основного металла, почему необходима разработка специальных электродов.
Пример.
Работы кафедры "Технология металлов" ДВГАПС по применению в составе обмоток минерального сырья ДВ.
Часто после сварки, а иногда до сварки применяется термическая обработка или нагрев свариваемых деталей, чем снимаются температурные напряжения или обеспечивается достаточная однородность основной и наплавляемой структуры металла.
Большое значение с точки зрения прочности шва имеет способ разделки кромок (см.рис. 3.5).
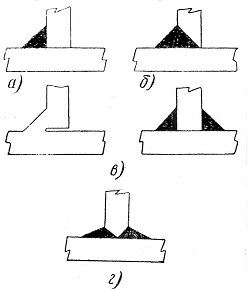
Рис. 3.5. Основные виды сварных швов
Односторонний шов без разделки кромок рис.3.5.а имеет наименьшу прочность по
концентрации напряжений равноценен надрезу. Односторонний шов с разделкой (рис.3.5.б)
создает значительно меньшую концентрацию напряжений, а значит - большую прочность.
Двухсторонний шов без разделки (рис.3.5.в) как и односторонний является концентратором
напряжений и даже уступает предыдущему по прочности. Наибольшую прочность имеет
четвертый вид сварного соединения (рис.3.5.г), когда выполняется двухсторонняя разделка
кромок. На прочность сварных соединений, кроме этого влияет расположение сварных швов
относительно направления напряжений в материале конструкции от рабочих нагрузок.
Рис.3.5. К примеру шов 2 (см.рис.3.6.а) не желателен, т.к. для Основные боковины является
доплнительным концентратором виды сарных напряжений, кроме этого он перекрещивается
с швов горизонтальным швом 3, что также не желательно. Для снижения напряжений шов 2 для этого необходимо обрывать плавным окончанием перед швом 3. Горизонтальный лист поперечной балки выполняют округленным (исключают часть изображенную пунктиром), что также уменьшает напряжения в боковине рамы.
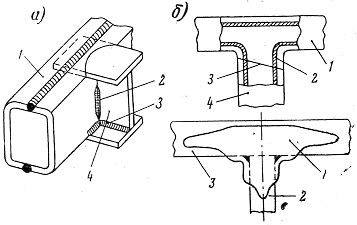
Рис.3.6. Примеры соедиения балок сваркой.
Удачной конструкцией соединения поперечины слеудет считать по рис.3.6.б. Здесь полность удалось избежать поперечных швов, что значительно повышает прочность соединения. Внутренние стенки 2 боковины рамы выполнены выгибом, что в корне изменило процесс сварки узла.
Выполнение горизонтальной накладки 1 (см.рис.3.6.в ) также удачный вариант снижения напряжений в элементах 2 и 3, ибо сварные швы имеют максимальную длину в направлении продольной оси рамы.
Технология сварки должна исключать коробление деталей за счет температурных напряжений в сварном шве.
Здесь следует придерживаться следующих правил:
1. Симметрично располагать сварные щвы 1-4 как показано на рис.3.7.а;
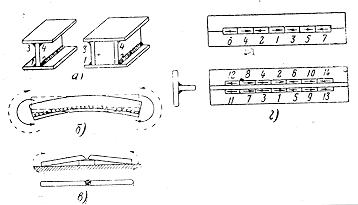
Рис.3.7. Приемы предупреждения коробления конструкции при сварке
2. Осуществлять жесткое закрепление элементов перед сваркой (различными приемами);
3. Осуществлять предварительный изгиб как на рис.3.7.б и в;
4. Применять метод обратно-ступенчатой сварки при выполнении швов большой длины. Участки длиной не более 350-400 мм направлять навстречу друг другу как на рис.3.7.г (цифры указываюит порядок наложения швов);
5. Применять скоростную сварку за счет увеличения плотности сварочного тока, что дает меньшие остаточные деформации сварных конструкций;
6. Применять меры интенсивного охлаждения швов, например водой. Закалку шва удалять затем отжигом.
Контрольные вопросы:
1. Каковы преимущества сварных конструкций перед клепаными?
2. Каким нормативным актом необходимо пользоваться при разработке технологического процесса ремонтных работ с применением сварки?
3. Как избежать коробления деталей при сварке?
4. Как обеспечить прочность сварных швов?
5. Какие особенности изготовления сварных рам ЭТ?
3.4. Технологические требования к деталям из пластмассы
Полимерные материалы находят в последнее время широкое применение в конструкциях ЭТ как при выпуске нового, так и в ремонте. Их применяют в качестве отделочных и облицовочных мотериалов (техстовинит и др.), для звуко- и теплоизоляции (пено- и газопластмассы), для изготовления высоконагруженных армированных и неармированных шайб и стержней тяговой аппаратуры ( пресс-материал АГ-4, изодин, волокнит, карболит), для дугогасительных камер (асбоцемент, асбопласт), для декоративного покрытия (напыление) державок, поручней и других деталей кузова, ходовых частей и электрического оборудования.
При литьевом прессовании можно получить очень мелкие детали - толщина стенок может быть 0,3-0,4 мм, при этом как правило не требуется механической обработки, кроме удаления литников и облоя.
Освоение пластмассовых технологий производства требуетдовольно дорогого оборудования ( прессов, обогреваемых пресс-формы), однако сокращение в 10-15 раз механической обработки для таких деталей обеспечивает технико-экономическую эффективность внедрения.
При серийном производстве изделия из цветных металлов, дерева, кожи и т.д. и превосходят последние по своим качественным показателям. Фенопласт, например, прочен, как , сталь, но имеет в 2 раза меньший вес, чем алюминий; волокнит не уступает чугуну в стойкости на излом и износ, но примерно в 4 раза легче чугуна; подшипники и втулки из пластмасс отличаются в 8-10 раз больщей износостойкостью по сравнениб с металлическими; шестерни из текстолита бесшумны и отличаются большой прочностью и коррозионной стойкостью.
Испоьзуются три вида пластмасс: термореактивные, которые при нагревании текут, а затем необратимо затвердевают; термопластичные, которые способны многократно размягчаться, а при обычной температуре находиться в твердом состоянии (капрон), и пресс-материалы холодного прессования, которые после прессовки сушат на воздухе и подвергают термообработке ( проваркой) в горячей воде.
Технологический процесс изготовления деталей из пластмасс должен исключать механическую обработку, т.к. при этом нарушается структура детали, сами детали не должны иметь острых кромок - концентраторов напряжений, толщина стенок не большая, до 10 мм, тогда напряжения распределяются равномерно.
Оптимальной толщиной стенок считают для деталей на основе фенальных смол - 0,7-6,5 мм; из алюминиевых порошков 0,7-3,5 мм; при литье из термопалстичных материалов - 2-3 мм.
Для повышения жесткости применяют ребра жесткости.
Формовку сквозных и глухих отверстий следует осуществлять выступами пресс-формы без использования знаков. Примеры таких форм на рис.3.8.
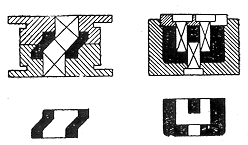
Рис.3.8. Примеры пресс-форм для изготовления деталей
Часто в детали из пластмасс вводят металлические элементы ( для резьб и т.д.), в этом случае толщина стенок пластмассы вокруг арматуры должна быть не менее 1/6 ее диаметра. Это вызвано различным линейным расширением материалов при нагревании. У некоторых пластмасс коэффициент линейного расширения в 10 раз и более превышает коэффициент линейного теплового расширения металлов. По этой же причине необходимо иметь буртики и опоры на металле (см.рис.3.9).
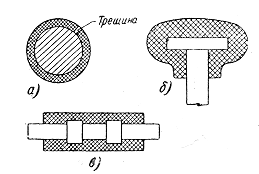
Рис.3.9. Примеры деталей опрессованных пласстмассой
Рассмотрим основные виды пресс-материалов, применяемых в конструкциях ЭТ.