Основы технологии производства электротранспорта
Вид материала | Лекции |
Технико-экономические характеристики качества конструкции и их отклонения в производстве и эксплуатации Основные принципы конструирования |
- Примерные программы Специальные дисциплины примерная программа дисциплины основы сельскохозяйственного, 1349.6kb.
- 6М071300 Транспорт, транспортная техника и технологии По дисциплине – «Основы технологии, 110.86kb.
- Вопросы для подготовки к экзамену по дисциплине: «Основы технологии производства, 31.12kb.
- «Подъемно-транспортные, строительные, дорожные машины и оборудование», 14.82kb.
- Темы курсовых работ по курсу «Основы строительного производства» для студентов направления, 11.2kb.
- К рабочей программе учебной дисциплины, 23.79kb.
- Курс Код Факультет, наименование направления подготовки (специальности) Перечень, 130.47kb.
- Программа дополнительного образования при кафедре Технологии строительного производства, 173.05kb.
- М. В. Ломоносова Кафедра экономики и организации производства И. А. Назарова Основы, 599.04kb.
- Вопросы к курсовому экзамену по фармацевтической технологии заводского производства, 113.84kb.
1.3. Государственная система стандартизации как база конструирования
При разработке нового подвижного состава или других любых изделий конструктор должен пользоваться стандартами.
Стандартом называют нормативно-технический документ узаконивающий требование к объекту стандартизации.
Различают:
Государственный стандарт (ГОСТ) - обязательные к применению
всеми предприятиями, организациями и учреждениями РФ.
Отраслевые стандарты (ОСТ) - обязательные для всех предприятий и организаций отрасли.
Республиканские стандарты (РСТ) - учитывают требования ГОСТ и ОСТ и действуют в пределах республики.
Стандарты предприятия (СТП) - учитывают выше стоящие стандарты и действуют на данном предприятии.
Технические условия (ТУ) - нормативно-технические документы, устанавливающие комплекс требований к продукции конкретных типов и марок разрабатываемые на основе и в дополнение существующих стандартов.
Руководящие документы (РД) - нормативно-техническая документация, устанавливающая требования организационного и (или) методического характера, разрабатываемая на основе и в дополнение существующих стандартов.
Проектируемые узлы и детали при конструкторской проработке делят на 4 группы: стандартизированные (Нст), заимствованные (Нз), покупные (Нп) и оригинальные (Но). Рассмотрим их влияние на достигнутый уровень выпуска новой продукции.
Естественно общее количество деталей будет равно

где


где



Внешне заимствованные - детали применяемые ранее как оригинальные для одного изделия, а затем используемые в другом изделии.
Внутри заимствованные - детали используемые в разных сборочных единицах одного изделия.


Группа деталей
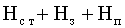

К примеру электровозы ВЛ60 и ВЛ80К имеют следующее количество деталей.
Таблица 1
Группа деталей | ВЛ60 | ВЛ80Т |
Стандартизованные | 450 | 644 |
Заимствованные | 1875 | 2545 |
Покупные | 225 | 745 |
Оригинальные | 4800 | 4200 |
Итого 7350 8134
Для электровоза ВЛ60
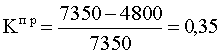
ВЛ80Т
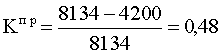
Уровень унификации совокупной продукции предприятия определяется отношением количества взаимно заимствованных деталей к общему:

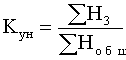
К примеру при выпуске электровозов ВЛ60, ВЛ80К и ВЛ80Т была осуществлена комплектация в виде рис.
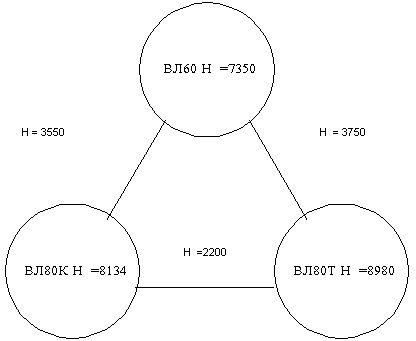
Тогда

Экономическую эффективность стандартизации можно оценить по коэффициенту экономической эффективности стандартизации как
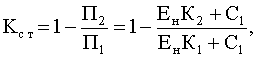
где




Существующие методы оценки уровня стандартизации и унификации основаны, как правило, на учете количественных соотношений и поэтому недостаточно результативны. Имеются исследования, направленные на решение этой задачи методами качественного анализа. Рассмотрим основные положения такого подхода к анализу качества продукции.
1.4. Технико-экономические характеристики качества конструкции и их отклонения в производстве и эксплуатации
Совокупность свойств, определяющих способность той или другой конструкции удовлетворять своему назначению, называют качеством продукции, а количественные характеристики тех или других свойств - показатели качества. Это вновь таки стандартизированные понятия и подчиняются ГОСТ 15467-70 " Качество продукции'. Термины".
Существуют и другие нормативные акты в этой области, к примеру "Методика оценки качества промышленной продукции", "Методика технико-экономической оценки эффективности новой техники" и др. материалы.
Качество ЭТ можно определить следующими группами показателей.
Технико-экономических, характеризующих технические параметры и показатели его использования в эксплуатации:
- показатель назначения ( локомотив грузовой, пассажирский, маневровый, промышленный и пр.);
- осевая формула, масса, сцепной вес, нагрузка на ось;
- энергетические мощность, сила тяги, скорость, напряжение на токоприемнике;
- удельные расход материала на кВт мощности, удельная сила тяги на кВт мощности, удельный расход электрической энергии на ткм перевозочной работы пр.
Надежности - способность ЭТ выполнять заданную функцию, сохраняя эксплуатационные свойства в установленных пределах в течение требуемой наработки в заданных условиях эксплуатации. Здесь основной показатель это безотказность и долговечность ( срок службы) ЭТ. Применительно к подвижному составу это количество отказов на

Технологичности, характеризующих конструкторско-технологические решения в отношении обеспечения высокой производительности труда при производстве локомотива и удобства его эксплуатации. Сюда относят - трудоемкость изготовления в нормо-часах, процент внедрения прогрессивных технологических процессов, коэффициент оснащенности и др.
Уровня стандартизации и унификации конструкции, отражающих степень использования стандартизованных изделий, возможность использования типового оборудования, унифицированных конструктивных элементов и типовых технологических процессов. Критерии оценки назывались выше - это коэффициент применяемости, унификации и пр.
Эргономических, характеризующих систему человек – изделие – среда по комплексу свойств, обеспечивающих безопасность, удобство работы и оптимальные условия труда обслуживающего персонала. Здесь оценки - в баллах удобство управления и обслуживания, уровень шума и вибрации, температура в кабине и др.
Художественно-конструкторских, характеризующих целесообразность и эстетичность художественно-конструкторского решения: выразительность, гармоничность, цельность, соответствие среде и стилю. Основными здесь являются показатели архитектоники (в баллах), товарного вида и отделки (в баллах).
Пример. Окраски электровоза поставляемой в Финляндию и ее качества.
Патентно-правовой защиты, оценивающих степень патентной защиты изделия в РФ и за рубежом и его так называемую патентную чистоту. Здесь количество и доля в общей стоимости реализуемых в изделии новых отечественных изобретений и показатель патентной чистоты - возможность беспрепятственной реализации изделия за рубежом.
Примеры: 1. Строительство Суданской плотины.
2. Уплотнение гробов США при войне во Вьетнаме.
Существуют следующие методы определения показателей качества промышленной продукции - экспериментальный - основан на прямом или косвенном измерении показателя качества с использованием технических средств или подсчете событий или объектов;
- расчетный, здесь нужно иметь теоретические или экспериментальные зависимости показателей качества от определяющих их параметров;
- органолептический, основанный на анализе зрительных, слуховых или других ощущений.
Пример: Езда на Моквиче-408 и Суббару.
- социологический - использование анкет опроса (эксплуатационников, пассажиров) и пр.
- экспертный - основанный на обработке мнений группы специально подобранных специалистов-экспертов.
Уровень качества продукции определяют относительно базового изделия отечественного или зарубежного.
Существует единичный показатель уровня качества

сопоставляя для заданных условий эксплуатации соответствующие показатели качества




Комплексный показатель уровня качества

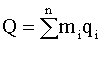
где


Сумма весовых коэффициентов при этом всегда должна быть равна 1.
Пример.
При оценке качества продукции локомотивов за базовый принимают локомотив размерного ряда и типажа перспективных магистральных локомотивов по руководящему документу (РТМ) электровозостроения
Порядок расчетов:
1. Определяют отношение

2. Множат отношение показателей на весовой коэффициент.
Для всех выше приведенных показателей качества продукции, а затем вновь с учетом весовых коэффициентов определяют уже комплексный показатель всего изделия.
Согласно РТМ электровозостроения существует три категории качества:
- высшая, при

- первая, при

- вторая, при

1.5. Принципы анализа характеристик качества
Математическая зависимость характеристик качества элементов конструкции от условий производства и эксплуатации в общем виде выражается уравнением

где

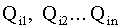


определяющий закон связи между

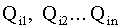
Вся трудность анализа качества продукции по выше приведенной зависимости не в расчетах, а в определении функциональной связи между условиями производства и эксплуатации характеристиками качества, т.е.

Практически о качестве продукции судят по отклонениям параметров изделия от номинальных ( расчетных ) величин.
Так, при составлении дефектных ведомостей состояние деталей и узлов оценивают величиной и отклонениями их количественных и качественных характеристик от установленных технической документацией ( ПТЭ, Правила ремонта ТУ, паспорт локомотива и т.д.)
Под состоянием детали понимают группу определенных его рабочих параметров (размеры, определяющие напряжения в деталях, диэлектрические прочности, действующие нагрузки, уровень изоляции,
уставки по току, напряжению, зазоры и натяги в сопряжениях, шероховатость поверхности). Иными словами, рассматривают:
- физико-механические характеристики;
- параметры рабочих режимов;
- регулировочные характеристики;
- характеристики размеров и формы.
Номинальной называют величину рабочего параметра в результате расчетов. Затем устанавливаются допуски на размер
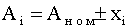

Конструктивным значением называют



Уменьшение допуска приводит к росту стабильности характеристик, точности и надежности конструкции, но возрастает стоимость производства. Поэтому необходимы технико-экономические расчеты.
Производственным (заводским) значением параметра называют его фактическую величину при выпуске детали или узла с завода-изготовителя (


Это точность и надежность завода-изготовителя
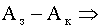
Эксплуатационным допуском


Эксплуатационное значение


Ремонтные размеры и допуски устанавливают правилами ремонта для соответствующих видов ТО и ТР. Чем больше объем ремонтных работ, тем меньше разброс допусков.
Предельной

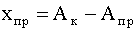
Заметим, что выход характеристик качества за пределы эксплуатационного допуска может быть по причине износа и нарушения регулировки, а также совместного действия нескольких причин.
Так, дисбаланс ротора электрической машины приводит к ускоренному износу подшипников, а они в свою очередь увеличивают вибрации ротора и в конечном случае разрушение подшипников.
Величину предельных износов деталей и сопряжения устанавливает конструктор в зависимости от назначения деталей и ответственности работы в механизмах, размеров, формы, материала и других факторов, а затем их уточняют в эксплуатации. Для особо ответственных деталей ЭТ предельные износы и дефекты, с которыми нельзя его выпускать на линию оговариваются правилами технической эксплуатации и нормами допусков на ремонт.
В практике отклонения характеристик качества от расчетных величин имеют значительный разброс, что получило название "рассеивание характеристик качества изделий".
Иными словами характеристика качества изделия


В хорошо отлаженных производственных процессах математическое ожидание М(А) совпадает с


Разность х=А-М(А) является случайным отклонением.
Исчерпывающей характеристикой случайной величины является ее закон распределения. Чаще это нормальный закон распределения с плотностью вероятности

где А - независимая переменная; M = M(А) - ее математическое ожидание;

Из анализа эмпирических распределений можно сделать ряд важнейших количественных и качественных оценок технологического процесса изготовления изделия.
Так, определение поля рассеивания дает представление о выполнении конструктивных допусков.
Чем меньше

При изготовлении любого изделия существуют определенные погрешности в размерах и формах деталей. Все погрешности изготовление изделий можно свести к следующим:
1. погрешность размеров,
2. погрешность геометрической формы,
3. погрешность взаимного расположения поверхностей,
4. погрешность, связанная с чистотой обработки (шероховатостью).
Все названные 4 вида погрешностей возникают под действием ряда причин; причин, которых следует отметить:
- неточность изготовления оборудования (станок, пресс и т.д.) - С;
- неточность изготовления приспособления для обработки, их износ - П;
- упругие деформации режущих инструментов, их износ, неточность изготовления инструмента, температурные влияния - И;
- неоднородность материала, упругие деформации, температурные влияния и другие погрешности детали - Д.
Это система технологических погрешностей

5. Погрешность измерения, включающая погрешность измерительных средств.
6. Погрешность, зависящая от выбранной технологической системы и режимов обработки.
7. Колебания припуска на механическую обработку и т.д.
Конструктор при разработке рабочих чертежей предусматривает предельные размеры, о чем мы уже говорили и отклонения от них, а также принимает поле допусков.
Обычно на чертежах конструктор указывает на один, и два предельно допустимых размера, больший из которых называется наибольшим предельным размером и обозначается




Разность
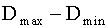

Допуск на обработку на чертежах показывают в виде двух отклонений от номинального размера. Одно отклонение - верхнее, а другое - нижнее.
Верхнее обозначают ES (es), а нижнее EI (ei).


где D- номинальный размер отверстия; d - номинальный размер вала.
Величина допуска в этом случае определяется как разность между верхним и нижним отклонением TD=ES-EI и Td=es-ei.
Пример.
Необходимо изготовить вал d=30 мм. Конструктор указал


30,030 - брак
30,020
30,010 годные
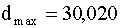
30,000 детали
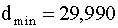
29,990 Td = 0,030
29,980 - брак
Иными словами, при изготовлении необходимо выдерживать условие
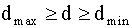

На чертежах допуски могут иметь шесть обозначений


Знание допусков и реальных размеров деталей важно для сборочных процессов при изготовлении любых изделий. Это необходимо для выбора того или другого метода сборки.
Величина допуска не совсем полно характеризует точность обработки. Например, у вала
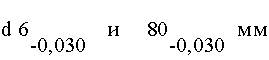
Величина допуска одинакова 0,030 мм , но обработать вал диаметром 80 мм значительно труднее, чем вал, диаметром 6 мм с тем же допуском.
В качестве единицы точности, с помощью которой можно установить зависимость изменения допуска при изменении диаметра, принимается единица допуска. Практикой установлено, что трудность обработки в основном возрастает с увеличением размеров деталей по закону кубической параболы в виде

Единицу допуска определяют по формуле

Здесь i- единица допуска для номинальных размеров до 500 мм.
Например, для размера 3 мм i=0,55, а для размера 500 мм i=3,89.
Точность изготовления деталей характеризуют квалитетом (степень точности).
Квалитет - это совокупность допусков рассматриваемых как соответствующие одному уровню точности для всех номинальных размеров. Квалитет обозначается порядковым номером, возрастающим с увеличением допуска. Всего предусмотрено 20 квалитетов: 0,1; 0; 1; 3; 4; 5; 6; 7; 8; 9; 10; 11; 12; 13; 14; 15; 16; 17; 18. Cокращенно допуск обозначается латинскими буквами IT - "стандартный допуск".
Например IT7 обозначает допуск по 7-му квалитету.
Допуски для каждого квалитета рассчитываются по формулам в зависимости от диаметра, хотя их можно определить и по таблицам ГОСТ 25346-89 для деталей до 500 мм (см. таблицу).
Знание допусков для различных соединений деталей крайне необходимо, ибо по ним определяются зазоры или натяги между последними.
В этом плане к примеру известны для вида посадок в системе вал - отверстие, а именно "посадка в системе отверстия" и " посадка в системе вал".
Посадка в системе отверстия - это посадки, в которых различные зазоры или натяги получают соединением различных валов (например, q, m, p и др.) с основным отверстием Н.
Посадка в системе вала - это посадки, в которых различные зазоры или натяги получают соединением различных отверстий ( например, F, R, N и др.) с основным валом h.
Предпочтение при выборе вида посадки отдается системе "посадка в системе отверстия" так как это сокращает количество режущего инструмента ( сверл, зенкеров, протяжек), калибров - пробок и оправок для приспособлений.
Действительно, обработка валов с различными размерами проще: например, на одном токарном или шлифовальном станке можно получить разные значения размеров вала.
Таблица 2
Значения допусков для размеров до 500 мм (по ГОСТ 25346-89)
Интервал | | | | | | | | | | ква | лит | еты | | | | | | | | | |||||||||||||||||||
размеров, | 01 | 0 | 1 | 2 | 3 | 4 | 5 | 6 | 7 | 8 | 9 | 10 | 11 | 12 | 13 | 14 | 15 | 16 | 17 | 18 | |||||||||||||||||||
мм | | | | | | | | | до | пуск | IT, | мкм | | | | | | | | | |||||||||||||||||||
До 3 | 0,3 | 0,5 | 0,8 | 1,2 | 2 | 3 | 4 | 6 | 10 | 14 | 25 | 40 | 60 | 100 | 140 | 250 | 400 | 600 | 1000 | 1400 | |||||||||||||||||||
Св. 3 до 6 | 0,4 | 0,6 | 1 | 1,5 | 2,5 | 4 | 5 | 8 | 12 | 18 | 30 | 48 | 75 | 120 | 180 | 300 | 480 | 750 | 1200 | 1800 | |||||||||||||||||||
св. 6 до 10 | 0,4 | 0,6 | 1 | 1,5 | 2,5 | 4 | 6 | 9 | 15 | 22 | 36 | 58 | 90 | 150 | 220 | 360 | 580 | 900 | 1500 | 2200 | |||||||||||||||||||
св. 10 до 18 | 0,5 | 0,8 | 1,2 | 2 | 3 | 5 | 8 | 11 | 18 | 27 | 43 | 70 | 110 | 180 | 270 | 430 | 700 | 1100 | 1800 | 2700 | |||||||||||||||||||
св. 10 до 30 | 0,6 | 1 | 1,5 | 2,5 | 4 | 6 | 9 | 13 | 21 | 33 | 52 | 84 | 130 | 210 | 330 | 520 | 840 | 1300 | 2100 | 3300 | |||||||||||||||||||
св. 30 до 50 | 0,6 | 1 | 1,5 | 2,5 | 4 | 7 | 11 | 16 | 25 | 39 | 62 | 100 | 160 | 250 | 390 | 620 | 1000 | 1600 | 2500 | 3900 | |||||||||||||||||||
св. 50 до 80 | 0,8 | 1,2 | 2 | 3 | 5 | 8 | 13 | 19 | 30 | 46 | 74 | 120 | 190 | 300 | 460 | 740 | 1200 | 1900 | 3000 | 4600 | |||||||||||||||||||
св. 80 до 120 | 1 | 1,5 | 2,5 | 4 | 6 | 10 | 15 | 22 | 35 | 54 | 87 | 140 | 220 | 350 | 540 | 870 | 1400 | 2200 | 3500 | 5400 | |||||||||||||||||||
св.120 до 180 | 1,2 | 2 | 3,5 | 5 | 8 | 12 | 18 | 25 | 40 | 63 | 100 | 160 | 250 | 400 | 630 | 1000 | 1600 | 2500 | 4000 | 6300 | |||||||||||||||||||
св.180 до 250 | 2 | 3 | 4,5 | 7 | 10 | 14 | 20 | 29 | 46 | 72 | 115 | 185 | 290 | 460 | 720 | 1150 | 1850 | 2900 | 4600 | 7200 | |||||||||||||||||||
св.250 до 315 | 2,5 | 4 | 6 | 8 | 12 | 16 | 23 | 32 | 52 | 81 | 130 | 210 | 320 | 520 | 810 | 1300 | 2100 | 3200 | 5200 | 8100 | |||||||||||||||||||
св.315 до 400 | 3 | 5 | 7 | 9 | 13 | 18 | 25 | 36 | 57 | 89 | 140 | 230 | 360 | 570 | 890 | 1400 | 2300 | 3600 | 5700 | 8900 | |||||||||||||||||||
св.400 до 500 | 4 | 6 | 8 | 10 | 15 | 20 | 27 | 40 | 63 | 97 | 155 | 250 | 400 | 630 | 970 | 1550 | 2500 | 4000 | 6300 | 9700 |
Примечание. Для размеров до 1 мм квалитеты от 14 до 18 не применяются.
Хотя, если вал изготовляют без обточки, к примеру, из цельнотянутого прута или проволоки, то экономически выгоднее принимать различные допуски по отверстию сборочной конструкции.
Напомню, что поле допусков в системе ОСТ и классы точности имеют следующие обозначения в технической документации.
Поле допусков обозначают прописными (заглавными) русскими буквами: основное отверстие - А, а основной вал - В. Подвижные посадки обозначают буквами С - скольжение; Д - движение; Х - ходовая; Л - легкоходовая; Ш - широховатая; ТХ - теплоходовая. Пореходные посадки: Г - глухая; Т - тугая; Н - напряженная; П - плотная. Посадки с натягом: Гр - горячепрессовая; Пр - прессовая; Пл - легкопрессовая;


Обозначение на чертежах:


при этом цифры обозначают класс точности по ОСТ , которые соответствуют классам точности ( квалитетам) в Международной системе допусков и посадок - ИСО ( по названию международной организации по стандартизации) согласно таблицы
Таблица 3
Соответствие классам точности ОСТ и квалитетам ИСО
Классы точности ОСТ | 1 | | 2 | | 2 | а | 3 | 3а | 4 | 5 | 7 | 8 | 9 | 10 |
Квалитеты | вал | отв | вал | отв | вал | отв | | | | | | | | |
ИСО | 5 | 6 | 6 | 7 | 7 | 8 | 8-9 | 10 | 11 | 12-13 | 14 | 15 | 16 | 17 |
Кстати в первом приближении точность обработки согласно классификации ИСО можно получить из таблицы 4.
Cледует оговориться, что данные таблицы 4 примерные, и вообще при обработке на одном и том же оборудовании диапазоны применения рядов точности гораздо шире и результаты точности обработки могут зависеть как от состояния оборудования, так и от исполнителя.
Таблица 4
Точность различных методов обработки
Метод обработки | Квалитет | Метод обработки | Квалитет |
1 | 2 | 3 | 4 |
Точение: черновое чистовое тонкое Фрезерование: черновое чистовое Строгание: черновое чистовое тонкое Сверление Зенкерование | 11 10 8-9 11 8 12-11 10 8 11-12 10 | Развертывание: предварительное окончательное Протягивание: чистовое отделочное Шлифование: грубое чистовое тонкое Притирка и доводка: предварительная окончательная | 9 8 8 7 10-9 6-7 5-6 6 5 |
Пример. Притирка и доводка детали исполнителями различной квалификации и стажа работы.
В заключении отмечу, что в системе ОСТ 2-й класс точности наиболее распространен в машиностроении, он считается основным, и в обозначениях на чертежах цифра 2 опускается, всего же классов точности по ОСТ 11, что отражено в табл.3.
И еще одно замечание – квалитеты класса точности по ИСО 01; 1; 2; 3 и 4 применяются при особо точных работах.
В заключении отметим, что при выборе сочетания полей допусков валов и отверстий для номинальных размеров 1-500 мм рекомендуется использовать предпочтительные посадки согласно табл. 5.
Как видим для предпочтительного применения выделены 17 посадок в системе отверстия и 10 посадок в системе вала.
Напомню основные виды посадок:
- В скользящих посадках
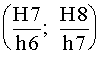
- Посадки типа

- Посадка

- Посадка
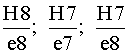
- Посадка

- Посадка

- Посадки

1.6. Взаимозаменяемость и методы обеспечения взаимозаменяемости в производстве и эксплуатации ЭТ.
Знание допусков на обработку отдельных деталей ЭТ позволяет решить задачи сборки узлов и агрегатов. При этом большое значение при создании нового ЭТ и организации его технического обслуживания и ремонта имеет взаимозаменяемость конструкций и их отдельных элементов.
Под взаимозаменяемость в широком смысле понимают идентичность характеристик качества однотипных конструкций или их элементов, обеспечивающую возможность замены одних из них другими без дополнительных операций обработки (пригонки) так, что эта замена не отражается ( в пределах предусмотренных допусков) на работе изделия или системы, в которую они входят.
Пример.
1. Замена локомотива под поездом в пределах серии.
2. Замена токоприемника.
3. Замена компрессора и др.
Если замена возможна без дополнительного подбора говорят о полной взаимозаменяемости, если же при замене необходимо выдержать определенный допуск к примеру отклонение характеристики колесно-моторного блока к примеру

Тоже можно сказать о взаимозаменяемости отдельных деталей в агрегатах, если деталь при сборке требует пригонки - говорят о неполной взаимозаменяемости.
Для получения той или другой ( полной или неполной)взаимозаменяемости должна быть обеспечена соответствующая точность обработки.
В конечном счете выбор полноты взаимозаменяемости решается экономической целесообразностью, ибо как уже говорилось раньше, точность обработки с одной стороны повышает стоимость изготовления, а с другой - сокращает затраты при сборке и эксплуатации ЭТ.
Иными словами необходимо отыскание минимума затрат
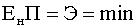
где

Для получения полной взаимозаменяемости необходимо, чтобы заводской допуск



Если принять, что повторяемость производственных допусков подчиняется закону нормального распределения, о чем говорили раньше, можно задаваясь

С ростом допуска

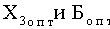
Рис 1.6. Зависимость стоимости обработки и стоимости исправления
брака от допускаемого процента брака
Естественно эти оптимумы будут завесить ль количества выпускаемой продукции. При поточной форме производства (значительная партия) идут на сжатие поля заводского допуска, так как начинают преобладать затраты на сборочных процессах и наоборот.
С целью сокращения затрат на сборке идут на подбор деталей для чего в ремонте к примеру устанавливают градационные ряды.
Сборка по методу подбора является вариантом селективной сборки (штучный метод подбора) - на месте сборки измеряют одну деталь, а к ней подбирают вторую деталь с допуском.
Пример.
Сборка колесной пары, когда непосредственно в цехе подбирают по натягам бандажи к колесным центрам, а колесные центры - к оси колесной пары.
Есть еще один метод сборки при неполной взаимозаменяемости. Сборка методом регулировки, когда в конструкцию вводится специальная деталь - компенсатор (регулировочная шайба и др.).
Такой способ сборки получил название компенсаторов: самоуправляющиеся, регулируемые и нерегулируемые.
Самоустанавливающийся компенсатор обеспечивает автоматическую компенсацию погрешностей размерной цепи без регулирования и подбора.
Пример.
1. Карданы - компенсируют угловые отклонения.
2. Зубчатые, шлицевые и шарнирно-рычажные муфты - компенсация угловых и линейных смещений.
3. Пружинные компенсаторы и др.
Регулируемые компенсаторы обеспечивают поглощение погрешностей размерных цепей регулирования.
Пример.
1. Резьбовые муфты, набор прокладок и др.
2. Много дырочные головки и резьбовые муфты в тормозных тягах.
Эти компенсаторы значительно облегчают ремонт устройств при износе.
Нерегулируемые компенсаторы предусматривают применение одной или нескольких ( небольшого количества) деталей многозвенной размерной цепи. Такие компенсаторы требуют дополнительной обработки (пригонки) с целью получения заданной точности сборки.
Пример.
Сборка групповых переключателей с проверкой развертки кулачковых шайб.
Существует метод плазово-шаблонной (кондукторной) сборки в производстве плоских и объемных конструкций кузовов и рам тележек методом сварки. В кондукторе или стапеле без промеров и разметки из заготовок собирают конструкции.
При этом важно обеспечить точность сборки тех размеров узла, которые определяют точность его сопряжения с другими узлами конструкции , для этого на кондукторе имеются соответствующие упоры, направляющие и т.д.
Этот же метод используют для сборки проводов силовых цепей и цепей управления ЭТ в пучки (кондуиты).
И наконец существует метод сборки по принципу пригонки. В этом случае одна или обе детали, входящие в сопряжение, изготовляют с небольшой точность.
Производят предварительную сборку или по результатам обмера определяют величину припуска на пригонку, который затем вынимают вручную (опиловкой, шабрением, шкуркой и т.д.) или дополнительной механической обработкой сопряженных поверхностей ( хонингованием, шевингованием, шлифованием и др.). Затем вновь собирают и производят проверку. Часто припуск снимают в несколько приемов. Такой способ сборки обусловлен недостатками конструкции или недостаточной точностью изготовления.
Пример.
1. Сборка колесно-моторного блока, когда точность сборки зубчатой
передачи обеспечивается подбором толщины вкладышей моторно-осевых подшипников. Применение опорно-рамной подвески исключит необходимость такой сборки КМБ.
2. Притирка клапанов электропневматических вентилей.
2. ОСНОВНЫЕ ПРИНЦИПЫ КОНСТРУИРОВАНИЯ
2.1. Научные основы конструирования
Сущствует два принципа конструирования:
- функциональный;
- норсмализованный.