Вестник Брянского государственного технического университета. 2006. №2 (10)
Вид материала | Документы |
СодержаниеСписок литературы |
- Вестник Брянского государственного технического университета. 2006. №1 (9), 88.23kb.
- Вестник Брянского государственного технического университета. 2006. №2 (10), 77.56kb.
- Вестник Брянского государственного технического университета. 2006. №3 (11) образование, 205.12kb.
- Вестник Брянского государственного технического университета. 2006. №1 (9), 161.23kb.
- Вестник Брянского государственного технического университета. 2006. №1 (9) Социально-философские, 117.78kb.
- Вестник Брянского государственного технического университета. 2011. №4(32), 114.16kb.
- Вестник Брянского государственного технического университета. 2006. №3 (11) Технология,, 94.65kb.
- Вестник Брянского государственного технического университета. 2010. №2(26), 83.85kb.
- Вестник Брянского государственного технического университета. 2008. №3(19), 168.61kb.
- Вестник Брянского государственного технического университета. 2008. №3(19), 138.83kb.
Вестник Брянского государственного технического университета. 2006. № 2 (10)
УДК 621.9
В. П. Фёдоров, В. В. Нагоркина, Е. В. Ковалёва
УПРАВЛЕНИЕ КАЧЕСТВОМ ОБРАБОТКИ ПОВЕРХНОСТЕЙ
ТРИБОЭЛЕМЕНТОВ В КОМБИНИРОВАННЫХ СИСТЕМАХ
ПОВЫШЕННОЙ ТЕХНОЛОГИЧЕСКОЙ ГИБКОСТИ
Рассматривается формирование качества и эксплуатационных свойств поверхностей трибоэлементов в комбинированных системах обработки, объединяющих процессы различной физической природы. Приводятся понятия технологической гибкости и технологической устойчивости процессов обработки. Анализируется их влияние на качество обработанной поверхности.
Одним из основных показателей конкурентоспособности продукции машиностроения в условиях рыночной экономики является её надёжность, важный компонент обеспечения которой – высокие эксплуатационные свойства соединений деталей, в частности их триботехнические характеристики. Показатели эксплуатационных свойств (ЭС), как и определяющие их параметры качества поверхностного слоя (КПС), формируются в основном на заключительной стадии технологического процесса – чистовых и финишных операциях [1]. Таким образом, технолог должен решать достаточно сложную задачу управления в процессе обработки группой геометрических и физико-механических параметров КПС, которая является одной из важнейших проблем инженерии поверхности [2].
В последнее время технологическое обеспечение триботехнических характеристик соединений осуществляется рядом эффективных методов обработки. Среди таких методов можно выделить комбинированные, основанные на чистовой размерной обработке лезвийным инструментом из поликристаллических сверхтвёрдых материалов (обеспечивается требуемая точность при высокой производительности), модификации поверхностей трибоэлементов твёрдыми износостойкими покрытиями или мягкими медесодержащими приработочными плёнками (создание физико-химических основ совместимости трущихся поверхностей) и финишной обработке поверхностным пластическим деформированием (ППД, формирование окончательной гаммы технологических параметров КПС и ЭС).
Эти системы обработки обладают повышенной технологической гибкостью, под которой понимается способность обеспечить заданные множества параметров КПС и ЭС в регламентированных интервалах с заданной надёжностью посредством направленного варьирования условий обработки и управления механизмом технологического наследования.
Весьма эффективной для обработки опорных шеек валов (сталь HRC 40…45) под подшипники скольжения является комбинированная технологическая система антифрикционной обработки (КАФО), включающая чистовое точение композитом 10, нанесение мягких медесодержащих приработочных плёнок и последующее алмазное выглаживание [3].
Чистовое точение композитом 10 марки 2106-0331 осуществлялось стандартными резцовыми вставками (ТУ 2–0237–194–77) на станке 16К20 при следующих режимах: = 60о, Vт = 65…200 м/мин; Sт = 0,05…0,15 мм/об; t = 0,1…0,25 мм; жёсткость технологической системы j = 2,6…16,2 кН/мм.
Нанесение мягкой приработочной плёнки осуществлялось методом фрикционного латунирования (ЛФ) или химического меднения (МХ) по специальной технологии.
Из двух альтернативных методов ППД – вращающимся стальным индентором (ролик или шарик) и неподвижным алмазным индентором (стандартный выглаживатель из синтетического алмаза АСПК) – выбрано алмазное выглаживание (АВ) как метод, обладающий большей технологической гибкостью и более высокой энергетической устойчивостью. На основе справочных данных и пробных экспериментов выбраны следующие режимы АВ: радиус индентора r = 3,5 мм; сила АВ Qав = 100…300 Н; скорость Vав = 65…100 м/мин; S = 0,075…0,15 мм/об. АВ проводилось при наличии смазки И-20.
Триботехнические характеристики исследовались по результатам испытаний на специальном программируемом стенде моделей подшипников трения скольжения, работающих со смазкой при динамических нагрузках.
Вкладыши изготовлялись из бронзы Бр ОЦС 5-5-5 и антифрикционного чугуна АСЧ-1. Их рабочие поверхности обрабатывались чистовым точением.
В качестве факторов, формирующих единую триботехнологическую систему, рассматривались условия приработки: указанные материалы вкладыша; скорость относительного скольжения поверхностей Vпр = 10…50 м/мин; средняя погонная нагрузка на соединение Рпр = 30…50 Н/мм; относительное изменение средней нагрузки в динамическом режиме приработки р = (15…25) %. Приработка осуществлялась с подачей смазки И-30 на специальном стенде, оснащённом виртуальной измерительной системой.
Исследовались следующие триботехнические характеристики соединения в условиях трения скольжения: коэффициент трения в начале (f1) и в конце (f0) приработки; величины начального износа (h01, h02), пути приработки (L01, L02) и интенсивности износа (I1, I2) для валов и вкладышей соответственно.
Анализ формирования коэффициента трения показал, что его установившееся значение уменьшается с ростом скорости скольжения V при приработке, причём разность между начальным (L = 0) и конечным (L = L0) значениями f с ростом V возрастает (рис. 1а).
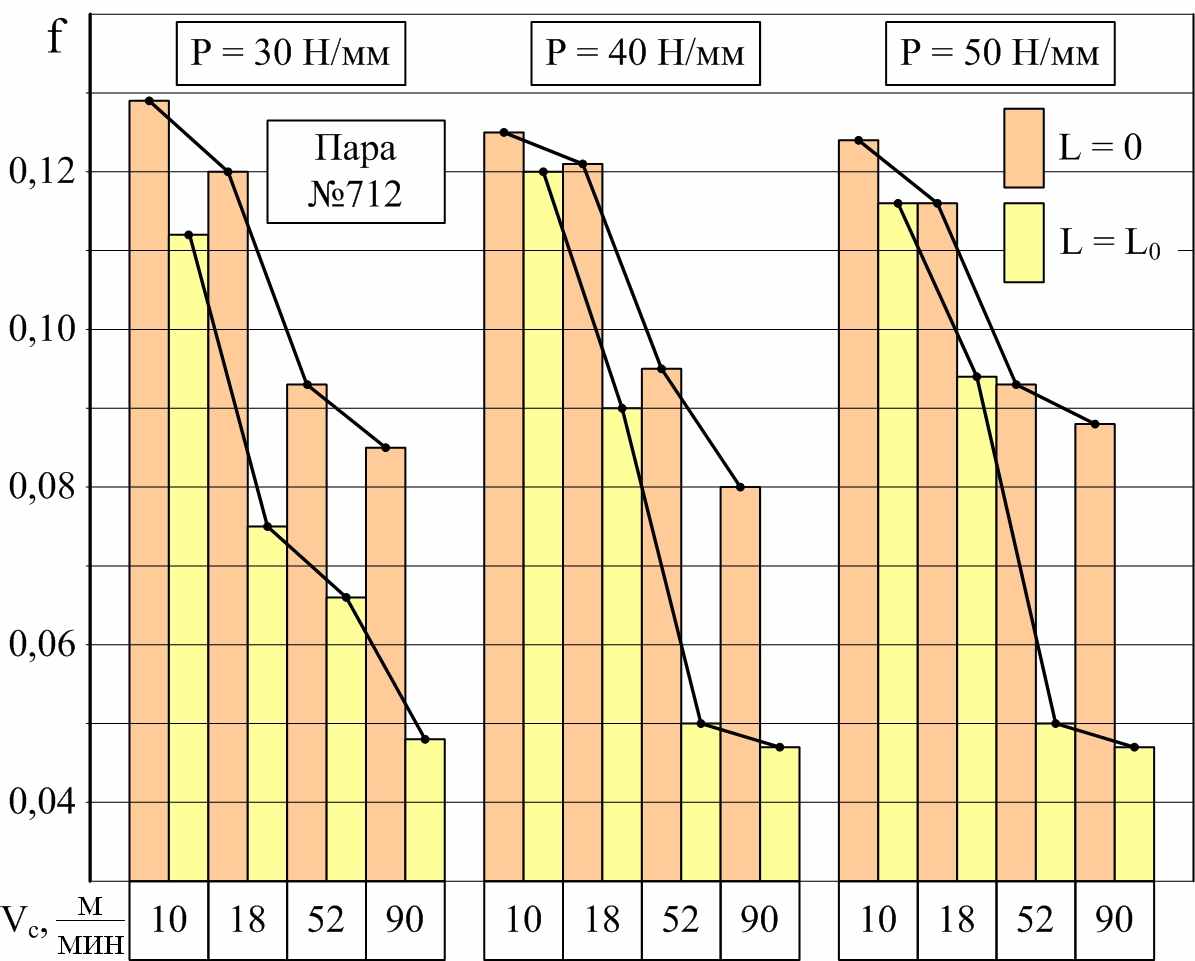
0
Vc,
м/мин
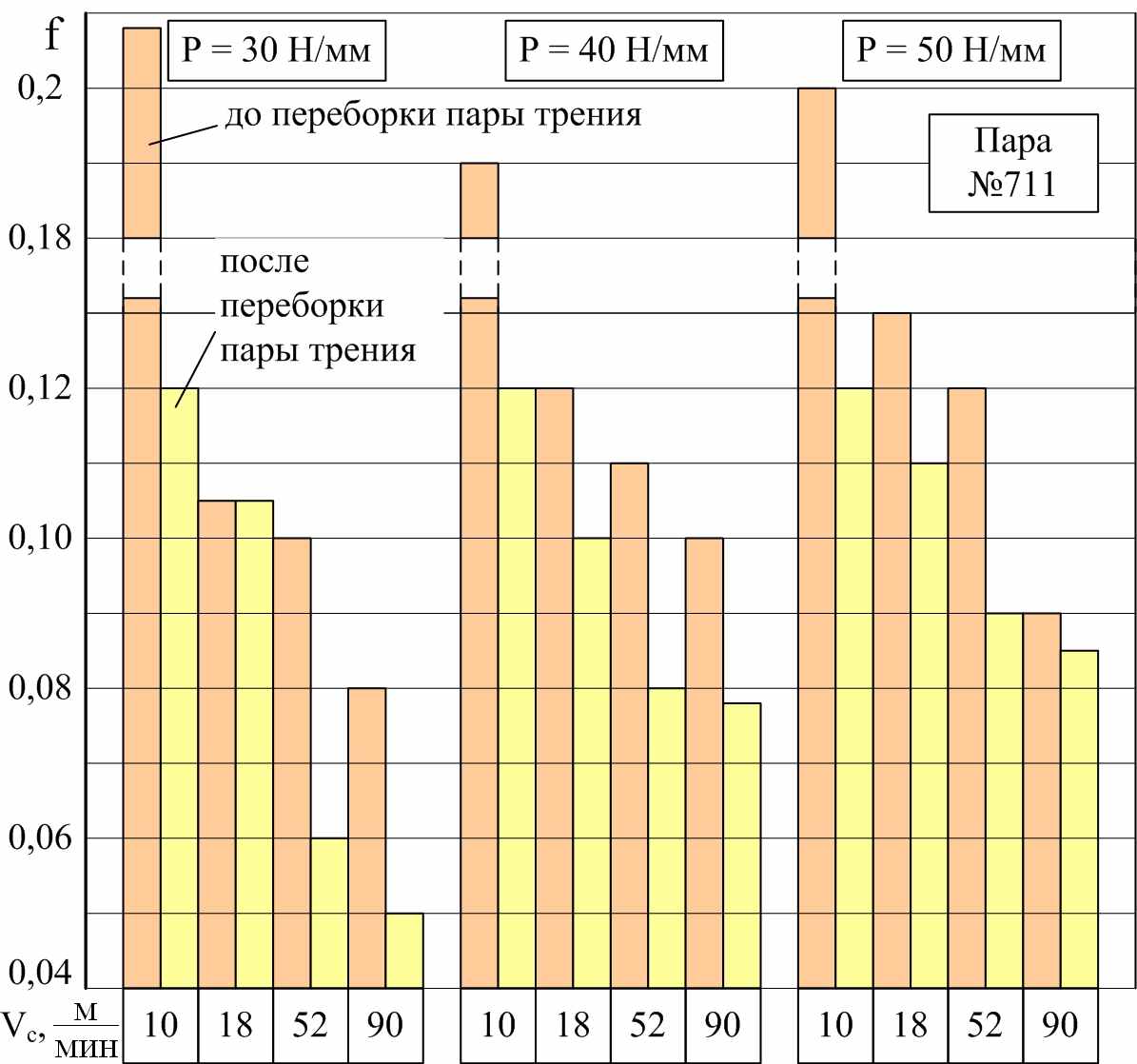
а) б)
Р
Vc,
м/мин
ис. 1. Формирование коэффициента трения в процессе приработки: а – влияние скорости
относительного скольжения; б – влияние процесса переборки пары
0
Положительно сказывается на процессе приработки в части формирования коэффициента трения f переборка пары трения (рис. 1б). Это естественно, так как при этом удаляются образовавшиеся частицы износа, играющие в процессе приработки отрицательную роль. Указанные особенности характерны для всех рассмотренных случаев и нагрузок на сопряжение P от 30 до 50 Н/мм.
Установлено, что в ходе приработки, особенно на стадии её завершения, при определённых условиях происходит самоорганизация коэффициента трения, то есть в зоне контакта трущихся поверхностей при наличии смазки протекают синергетические процессы.
При дозированной подаче смазки в зону трения (точки 6, 7, 8, 9, рис. 2а) наблюдается нелогичное, с первого взгляда, кратковременное возрастание коэффициента трения, который через некоторое время уменьшается, его значение становится меньше исходного, и при изменении нагрузки с постоянной на пульсирующую (t = 16…17 мин) картина не меняется. Установлено возникновение бифуркаций на стадии завершения приработки и без внешнего вмешательства в работу трибосистемы: разрывные недифференцируемые скачки коэффициента трения (участок а – b, рис. 2б) и резкое его повышение с дальнейшим спадом и стабилизацией (b – c – d – e, рис. 2б). Участок а – e по времени длился около 2 мин, а путь трения для вкладыша составил 180 м.
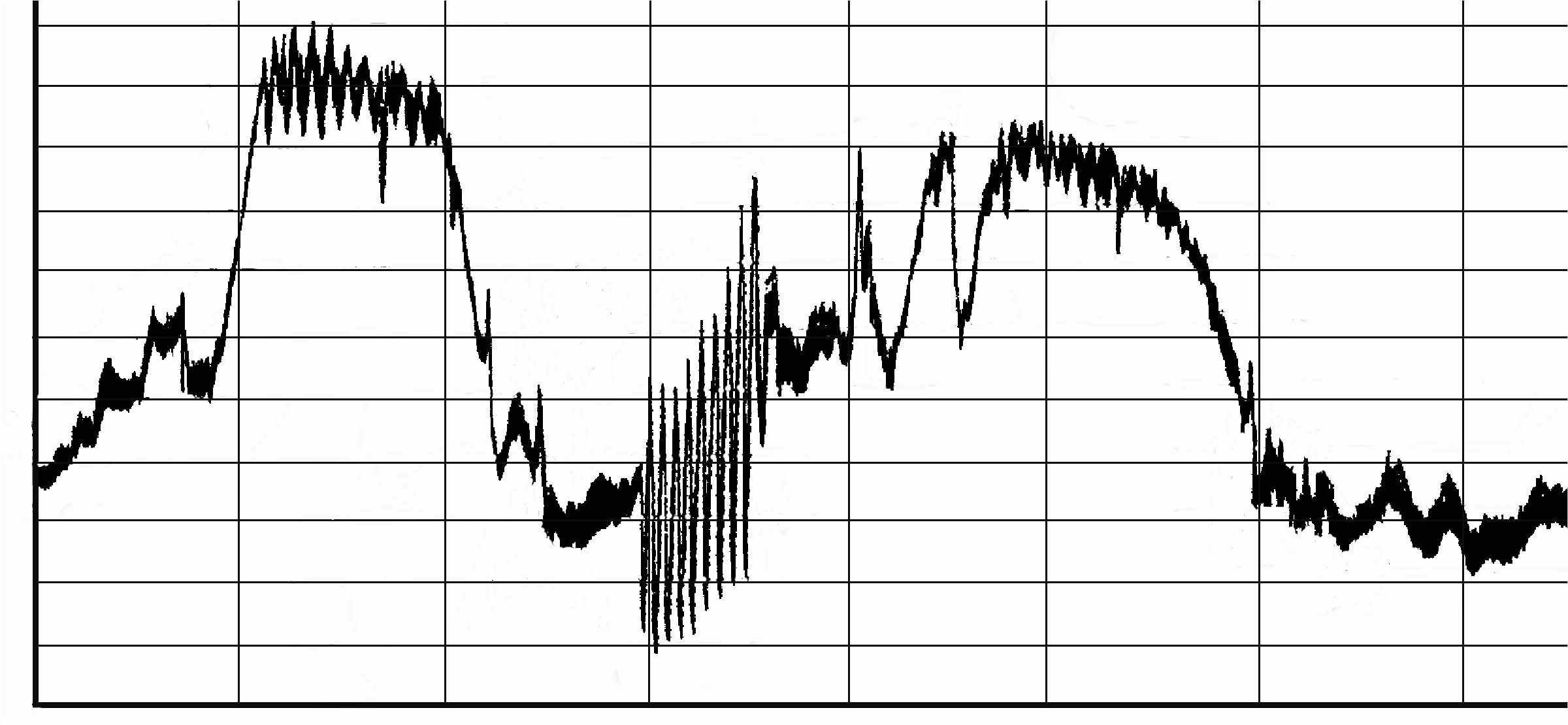
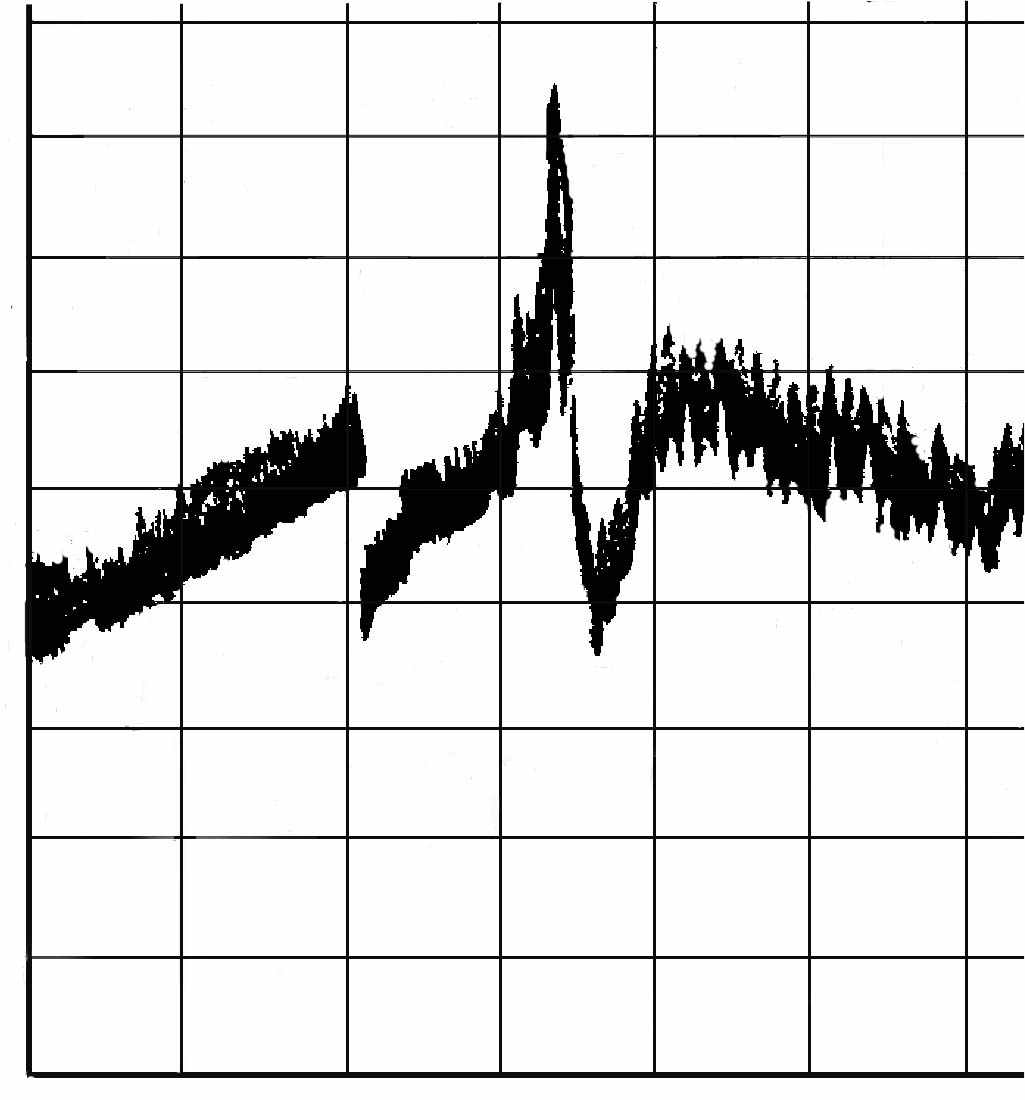
fтр
0,16
0,14
0,12
0,10
0,08
121 122 123 124 125 t, мин
f
0,12
0,10
0,08
0,06
0
Р
t = 103С
P = 50 Н/мм
VС = 90 мм/мин
10 12 14 16 18 20 22 t, мин
10
9
8
7
6
5
4
3

c

a

b0
b

d

e
fтр0

fтр0

а) б)
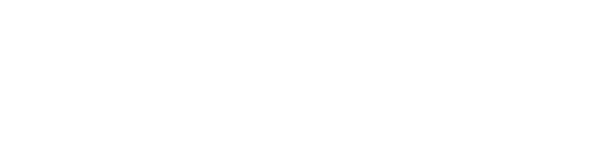
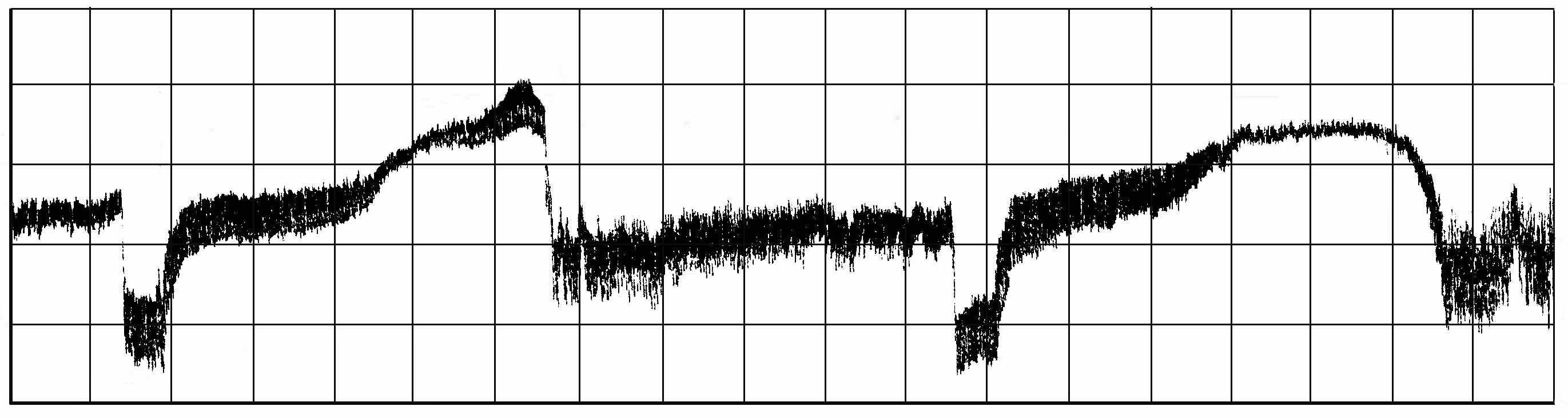
f
0,16
0,12
0,08
0,04
0 10 20 30 40 50 60 70 80 t, сек



a
d
e
Дозированная подача смазки


b

c

P = 30 Н / мм VС = 50 м / мин
в)
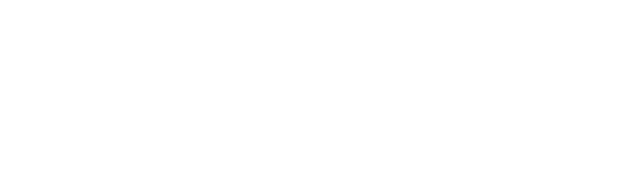
Рис. 2. Динамика самоорганизации коэффициента трения f: а, в - при дозированной подаче
смазки в зону контакта, б - без вмешательства в процесс приработки
Микропрофиль и микротопография неровностей поверхностей исследовались с использованием компьютеризированных измерительно-информационных систем ИИС-1 и ВИСМА [4].
Применение КАФО позволяет с помощью режимов чистового точения и алмазного выглаживания управлять параметрами эксплуатационного микрорельефа (ЭМР) (рис. 3а), создавая на поверхности своеобразные карманы в виде относительно глубоких регулярных впадин, которые способствуют удалению продуктов изнашивания из зоны контакта, сохранению материала приработочной плёнки и повышению маслоёмкости поверхности.
Анализ текстуры и цветовой гаммы поверхности после АВ показал (рис. 3б), что АВ не уничтожает ранее нанесенную приработочную плёнку, это свидетельствует о высокой адгезии материала плёнки с поверхностью. Гистограмма яркости смещена влево, в сторону тёмных тонов цвета плёнки. Приработочная плёнка сохраняется и по завершении процесса приработки, трансформируясь в более тонкую и упорядоченную поверхностную структуру (рис. 3в). Гистограмма яркости более равномерна в области светлых тонов. Присутствие в ней тёмных тонов, имеющих соответствующую цветовую гамму, свидетельствует о наличии во впадинах микропрофиля материала для восстановления плёнки на поверхности.
Для рассматриваемой триботехнической системы удалось построить адекватные физико-статистические имитационные модели:

где Yi – i-я триботехническая характеристика; К1, К2 – коэффициенты, учитывающие вид приработочной плёнки (ЛФ или МХ) и материал вкладыша соответственно; bk – коэффициенты модели Кобба-Дугласа.
Параметры моделей (1) и расчётные значения критерия Фишера Fрасч для триботехнических характеристик и некоторых параметров эксплуатационного микропрофиля даны в таблице. Сравнение Fрасч с табличным значением при уровне значимости = 0,05 (Fтабл = 6,59) свидетельствует об адекватности моделей.
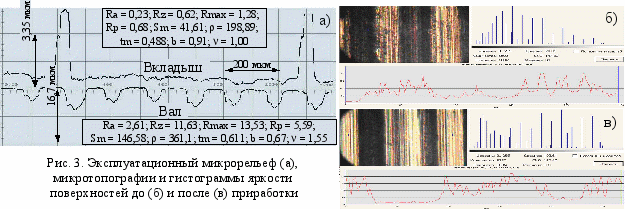
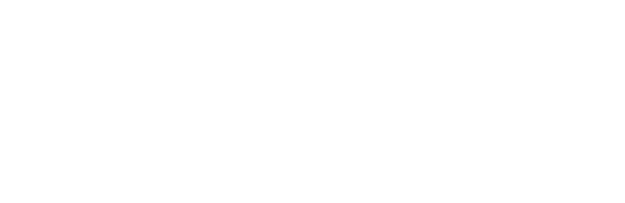
Таблица
Параметры имитационных моделей
Ко | b0 | К1 | К2 | b1 | b2 | b3 | b4 | b6 | b7 | b8 | b10 | b11 | b12 | Fр | ||
ЛФ | МХ | Бр | АСЧ | |||||||||||||
f1 | 2,0 | 1,31 | 1,10 | 1,11 | 1,05 | -0,06 | 0,04 | -0,05 | 0,02 | -0,07 | 0,47 | -0,05 | -0,32 | -0,09 | – | 1,3 |
f0 | 2,82 | 1,64 | 1,20 | 0,92 | 0,96 | 0,03 | 0,20 | 0,19 | 0,11 | -0,14 | 0,28 | -0,03 | -0,35 | 0,03 | 0,62 | 0,5 |
h01 | 3,74 | 1,20 | 1,07 | 1,23 | 1,09 | 0,31 | 0,15 | 0,02 | 0,04 | -0,38 | 0,32 | 0,68 | 0,05 | -0,74 | -0,19 | 5,6 |
h02 | 8,08 | 1,10 | 1,04 | 1,28 | 1,11 | 0,07 | 0,27 | 0,09 | -0,07 | -0,16 | -0,04 | 0,05 | 0,04 | 0,10 | -0,40 | 4,7 |
I110-12 | 316 | 1,77 | 1,23 | 0,87 | 0,94 | 0,08 | 0,22 | 0,21 | 0,13 | -0,17 | 0,43 | -0,05 | -0,43 | -0,10 | 0,76 | 2,8 |
I210-11 | 147 | 1,80 | 1,24 | 0,94 | 0,97 | 0,08 | 0,22 | 0,14 | 0,14 | -0,13 | 0,25 | -0,06 | -0,4 | 0,02 | 0,64 | 2,1 |
Raэ | 450 | 1,26 | 1,10 | 1,54 | 1,20 | 0,06 | 0,58 | 0,66 | -0,60 | 0,07 | 0,13 | 0,25 | -0,30 | -0,12 | 1,60 | 1,2 |
Rmaxэ | 170 | 1,53 | 1,17 | 1,57 | 1,21 | 0,15 | 0,54 | 0,35 | -0,34 | 0,27 | 0,02 | 0,02 | -0,20 | -0,20 | 1,1 | 3,3 |
Smэ | 960 | 1,57 | 1,18 | 1,65 | 1,24 | 0,20 | 0,33 | 0,36 | -0,18 | 0,04 | – | 0,18 | -0,10 | -0,50 | 0,66 | 2,7 |
Результаты эксперимента (рис. 4а) выявили, что исследуемыми триботехническими характеристиками путем варьирования факторов триботехнологической системы можно управлять в достаточно широких пределах и с весьма высокой надёжностью (рис. 4б), которая определялась методом обработки результатов машинных экспериментов над моделями вида (1), выполненных по схеме Монте-Карло.
У
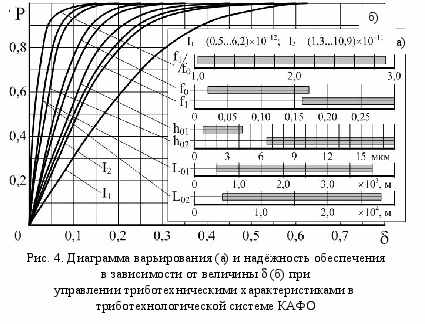
Высокая степень влияния фактора р, а также результаты, приведенные на рис. 1, указывают на желательность проведения приработки на форсированных режимах, то есть под воздействием управляемых динамических нагрузок при высоких скоростях относительного скольжения и с профилактической переборкой трибосопряжения.
Рассмотренная комбинированная система антифрикционной обработки обладает высокой технологической гибкостью, так как на заключительных этапах технологического процесса в формировании параметров КПС и ЭС обрабатываемой поверхности участвует большое число управляемых воздействий на поверхностный слой детали, имеющих различную физическую природу. Параметры КПС при этом изотропны, что гарантирует изотропность параметров ЭС при условии постоянства внешних возмущений (величины и спектры нагрузок и скоростей, изменения температуры окружающей среды, действие внешних вибраций и др.), действующих на соединение, в частности на соединение, работающее в условиях трения скольжения со смазкой, поверхность одного из трибоэлементов которого обработана методом КАФО.
Постоянство внешних возмущений свойственно стационарным режимам эксплуатации технических объектов, к которым, в частности, относятся и пары трения скольжения, работающие как в присутствии смазки, так и без неё.
Практически в большинстве случаев существуют нестационарные условия эксплуатации, характеризующиеся неравномерным распределением нагрузок, скоростей относительного скольжения и других возмущающих воздействий по контактирующим поверхностям трибоэлементов. В таких случаях при изотропности параметров КПС будет наблюдаться анизотропность эксплуатационных свойств поверхности, проявляющаяся, например, в различных величинах износа и контактной жёсткости её отдельных локальных участков, потере ими требуемой герметичности и т. д. Это будет отрицательно сказываться на качестве эксплуатационных свойств характеристик изделия в целом, то есть на определяющем этапе его жизненного цикла, связанного с потребителем. Наиболее характерными поверхностями, эксплуатируемыми в нестационарных условиях, изменяющихся для различных локальных участков, являются плоские и цилиндрические поверхности направляющих технологического оборудования, поверхности сложного профиля цилиндрических и плоских кулачков силовых механизмов и др.
Избежать нежелательной анизотропии показателей ЭС поверхностей при эксплуатации в нестационарных условиях можно при условии обеспечения соответствующей анизотропности гаммы лимитирующих параметров КПС обработкой в системе с повышенной технологической гибкостью в пределах перехода, так как именно на его протяжении обрабатывается одна, в данном случае функциональная, поверхность детали.
Итак, возможны два рода технологической гибкости систем (ТГС) обработки:
1) технологическая гибкость 1-го рода (ТГС 1) – возможность выбора гаммы методов обработки поверхностей (в общем случае различной физической природы) для заключительных операций технологического процесса и группы управляемых факторов каждого из них, постоянных по величине в пределах соответствующего перехода и обеспечивающих изотропность поверхности по регламентируемым значениям параметров КПС или ЭС в заданных пределах с требуемой надёжностью;
2) технологическая гибкость 2-го рода (ТГС 2) – возможность выбора гаммы методов обработки поверхностей (в общем случае различной физической природы) для заключительных операций технологического процесса и группы управляемых факторов каждого из них, одним или несколькими из которых можно программно управлять в пределах перехода по закону, обеспечивающему в итоге заданную анизотропность распределения параметров КПС или ЭС по обрабатываемой поверхности с требуемой надёжностью.
Все системы обработки поверхностей, в которых отсутствуют элементы программного управления типа CNC, обладают технологической гибкостью первого рода. К ним можно отнести следующие методы формирования поверхностей деталей машин на чистовых и финишных стадиях технологического процесса обработки:
1) резание (чистовое и тонкое точение, фрезерование, шлифование, алмазно-абразивная обработка и др.);
2) резание + нанесение покрытий (гальванические, ФАБО, твёрдые нитридсодержащие, лазерное легирование, ионная имплантация и др.);
3) резание + ППД (накатывание шариками, роликами, дорнование, алмазное выглаживание, вибронакатывание, вибровыглаживание и др.);
4) резание + ППД + покрытия;
5) резание + покрытия + ППД;
6) электрофизические и электрохимические методы обработки.
Технологическая гибкость 2-го рода присуща системам ЧПУ, где имеется возможность изменять условия обработки (факторы) программным способом в пределах перехода, то есть локальные участки одной и той же поверхности обрабатываются с различными режимами и получают в итоге различные значения показателей КПС и ЭС.
Очевидно, что важным показателем процесса обработки является степень его технологической гибкости, которой целесообразно придавать какое-то численное значение. На первый взгляд может показаться, что для этого достаточно ограничиться количеством управляемых факторов, но это далеко не так.
Если взять режимы обработки для точения ( V, S, t) и для ППД ( Q, S, V), то управляемых факторов в каждом случае по три, но технологическая гибкость процесса ППД значительно выше: в этом случае всеми параметрами КПС (макро- и микрогеометрия, физико-механические свойства и др.) можно управлять в гораздо более широких пределах и более надёжно, чем при точении.
Кроме того, анализ приведенных систем обработки 1 - 6 показывает, что применение той или иной системы способствует формированию совершенно новых, не свойственных основному материалу детали свойств (2; 4 - 6).
Целесообразно, чтобы численная оценка технологической гибкости 1-го или 2-го рода включала наряду с числом управляемых факторов обработки номенклатуру, количество и достижимый диапазон варьирования показателей формируемого КПС, то есть являлась комплексной. В этом направлении необходимо провести ряд исследований для окончательного решения вопроса о методике оценки технологической гибкости систем обработки и её унификации.
Изложенное позволяет заключить, что рассмотренная высокоэффективная система КАФО обладает технологической гибкостью 1-го рода, степень которой, безусловно, высока.
К эффективным системам обработки, обладающим технологической гибкостью 2-го рода, относится обработка поверхностным пластическим деформированием программным способом (ППДПС), которая синтезирована на основе реализации известных методов ППД на станках с компьютерными системами ЧПУ [5]. В этом случае программное управление такими факторами, как сила Q, скорость обработки V, подача S, плотность обработки и рисунок микрорельефа в пределах перехода, обеспечивает системе ППДПС технологическую гибкость 2-го рода.
Гибридизация ТС обработки с ЧПУ (в простейшем случае типа NC) позволяет значительно расширять её технологические возможности, осуществлять операции различного технологического назначения: размерная обработка ППД программным способом, нанесение покрытий – и всё это при максимальной технологической гибкости, так как имеется и реализуется возможность программного управления режимами обработки в пределах перехода. С учётом возможностей ПК его гибридизация даже с простой системой ЧПУ типа NC порождает систему PCNC – систему с совершенно иными, расширенными функциональными возможностями [6].
Созданная на базе станка мод. 6Р13Ф3 с системой ЧПУ «Координата 2ПТ71» система «Контур ПК-NC-01» в качестве управляющего модуля включает персональный компьютер. Управляющая программа от компьютера передаётся на устройство ЧПУ через блок гальванической развязки, который необходим для согласования уровней напряжения соответствующих сигналов (рис. 5). Метод ППДПС применим для обработки как плоских, так и цилиндрических, торцевых, конических и других поверхностей, образующие которых имеют аналитическое описание.
Блок-схема функционирования системы позволяет в комплексе решать ряд задач: расчёт режимов и моделирование результатов обработки в форме диалога; при получении положительного результата – разработка управляющей программы; реализация обработки по управляющей программе с визуализацией процесса в режиме реального времени. ПК, входящий в систему PCNC, можно связать с ЭВМ верхнего уровня, обеспечивающей выход в компьютерные сети с целью получения или передачи информации. Таким образом, подобные системы могут работать в составе виртуальных предприятий, так как они допускают разделение функций моделирования управления и обработки в пространстве, а при наличии банков данных – и во времени.
Важным фактором повышения триботехнических характеристик поверхностей типа направляющих, герметичности фланцевых соединений, качества отделочных работ в плане дизайна и др. является создание микрорельефов на поверхности, отвечающих тем или иным требованиям. Эта задача просто и надёжно решается обработкой ППДПС в ТС с ЧПУ типа PCNC, например «Контур ПК-НЦ-01». Результаты моделирования микрорельефов для разных поверхностей при различных исходных данных (рис. 6) убедительно свидетельствуют о высокой степени технологической гибкости обработки ППДПС поверхности.
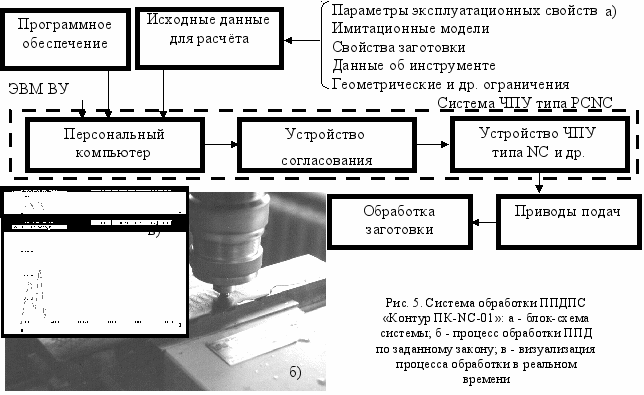
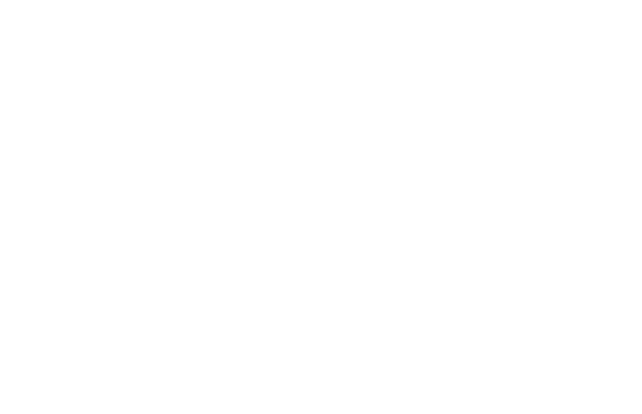
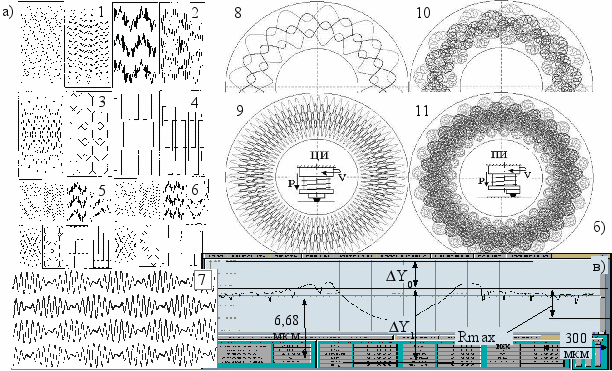
Рис. 6. Результаты моделирования микрорельефов, реализуемых в системе ППДПС: а – плоские
поверхности типа направляющих скольжения; б – плоские фланцевые поверхности;
в – типовая форма поперечного сечения остаточного следа индентора на обработанной поверхности
Модели 1 - 9 соответствуют обработке ППДПС с центрально расположенным индентором (ЦИ), а модели 10, 11 – с периферийным расположением индентора (ПИ). При моделировании в случаях 8 - 11 (рис. 6б) предусмотрено изменение силы воздействия индентора на поверхность в процессе обработки программным способом. Тёмные линии рельефа соответствуют её увеличению. Таким образом, тёмные участки моделей указывают на изменения параметров КПС и ЭС соответствующих участков обработанных реальных поверхностей, то есть осуществляется программное управление эксплуатационными свойствами поверхностей в функции их координат, что характеризует обработку ППДПС как систему с технологической гибкостью 2-го рода.
Следует отметить, что регулярные микрорельефы 3 - 6 и квазирегулярный 7 нельзя реализовать традиционными способами образования регулярных микрорельефов. Что касается математического уравнения основной несущей составляющей микрорельефа (траектория движения центра индентора), то его выбор основывается на физическом представлении процессов, протекающих в сопряжении, и должен способствовать решению задач, которые ставит инженерия поверхности, исходя из конкретных условий эксплуатации. К основным задачам такого рода следует отнести:
1. Повышение маслоёмкости поверхности, которое достигается путем технологического управления плотностью микрорельефа и параметрами поперечного сечения остаточного следа индентора на обработанной поверхности (рис. 6в), исследованными в работе [3].
2. Создание благоприятных условий для удержания в зазорах и формирования требуемых физических параметров (число Рейнольдса и др.) потоков смазочных материалов, диктуемых гидро- и газодинамикой в высокоскоростных соединениях с гидродинамической и газовой смазкой.
3. Формирование поверхностей с заданными параметрами эксплуатационных свойств (контактная жёсткость и др.) путем управления плотностью обработки, параметрами поперечного сечения остаточного следа индентора и величиной наклёпа поверхности.
4. Технологическое обеспечение требуемой герметичности соединений как при наличии третьего, более упругого тела, так и без него (путем создания уплотнений типа «лабиринт»).
5. Решение задач промышленной эстетики при проведении отделочных работ.
При получении положительного результата даётся команда генерации соответствующей управляющей программы, по завершении которой она передаётся на устройство согласования и обрабатывается поверхность в соответствии с полученной моделью по блок-схеме (рис. 5а).
Разработанный способ ППДПС позволяет реализовать и принципиально новые типы микрорельефов: А-стохастический (со случайной амплитудой); Т-стохастический (со случайным периодом); АТ-стохастический (со случайными амплитудой и периодом). Эксплуатационные свойства ряда из них к настоящему времени не исследованы, и эту задачу ещё предстоит решать.
Анализ поперечного микропрофиля поверхности с остаточными следами индентора после ППД показал, что в зависимости от шага Sк между следами, силы ППД Q и максимальной величины исходного микропрофиля Rmax его параметры меняются не только количественно, но и качественно. Это представляет практический интерес при восстановлении размера изношенных деталей методом выдавливания участков поверхности при ППД. Рассматривая общий случай (рис. 7), следует отметить типовые геометрические характеристики профиля поверхности после размерного восстановления методом ППД: Y0– максимальная величина выдавливания поверхности относительно линии выступов 0 – 0, мкм; Y0п– высота выдавливания участков исходной поверхности с деформированным исходным профилем П относительно средней линии, мкм; Y1 – максимальная глубина канавок относительно линии 0 – 0, мкм; Lab – длина восстанавливаемой поверхности, мкм; l1, …, li ,…, lk – величины, необходимые для определения относительной опорной длины профиля уровня 0 – 0, мкм. Помимо указанных величин, рассматривались следующие дополнительные характеристики: коэффициент выдавливания Kв; коэффициент выдавливания поверхности Kвп; коэффициент вдавливания поверхности K2; относительная опорная длина восстановленной поверхности на линии 0 – 0. Зависимости для определения этих величин имеют следующий вид:
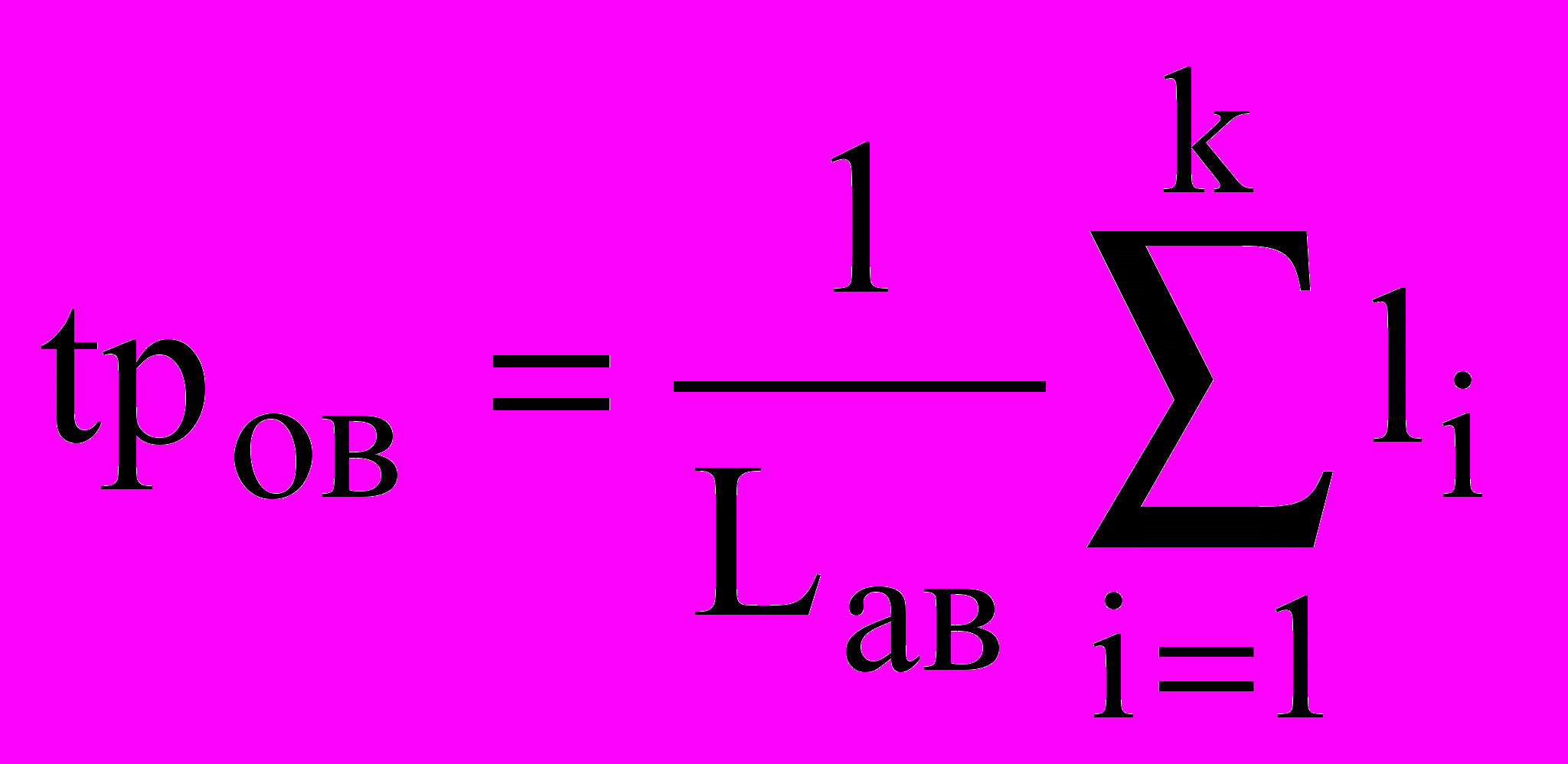
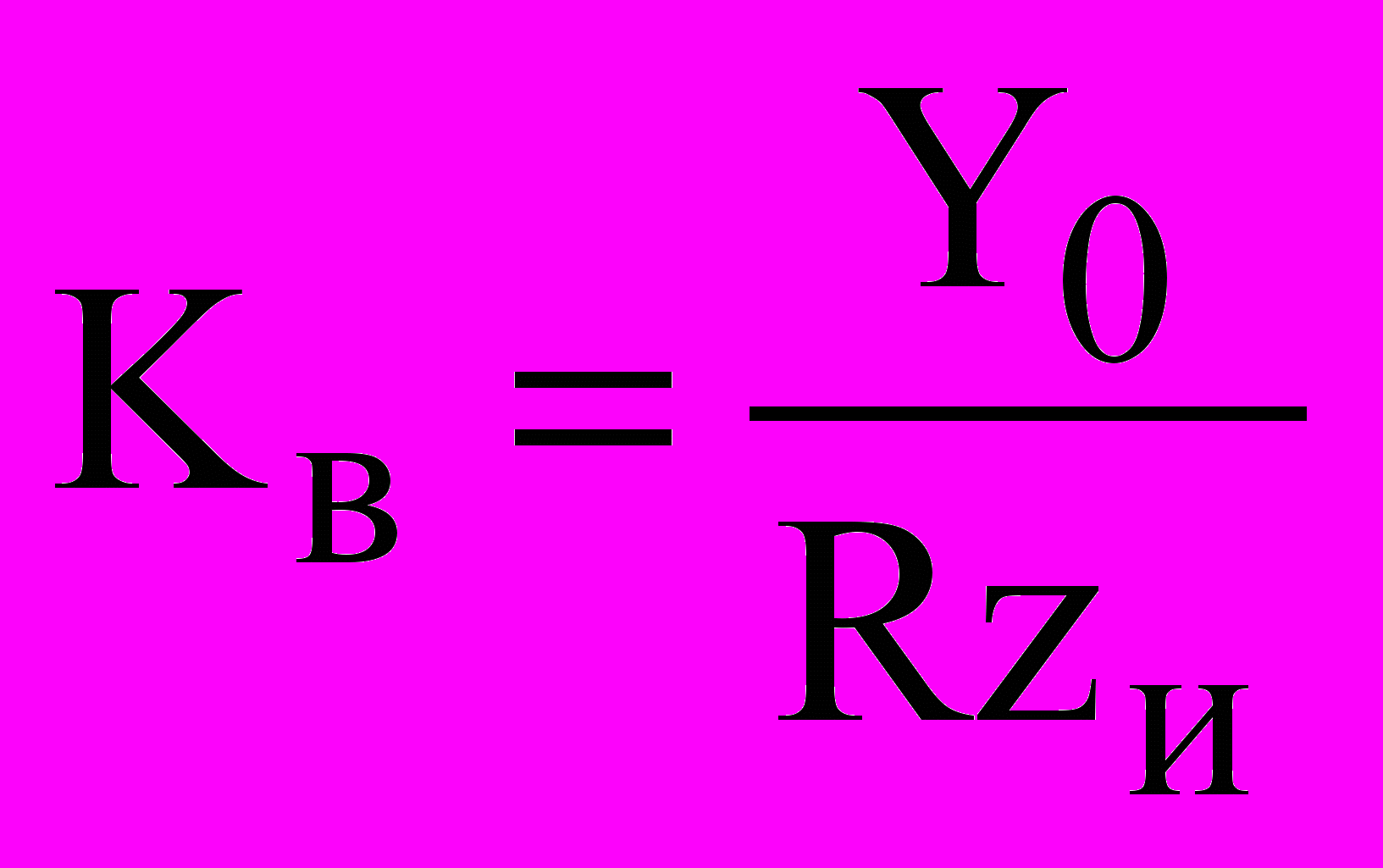
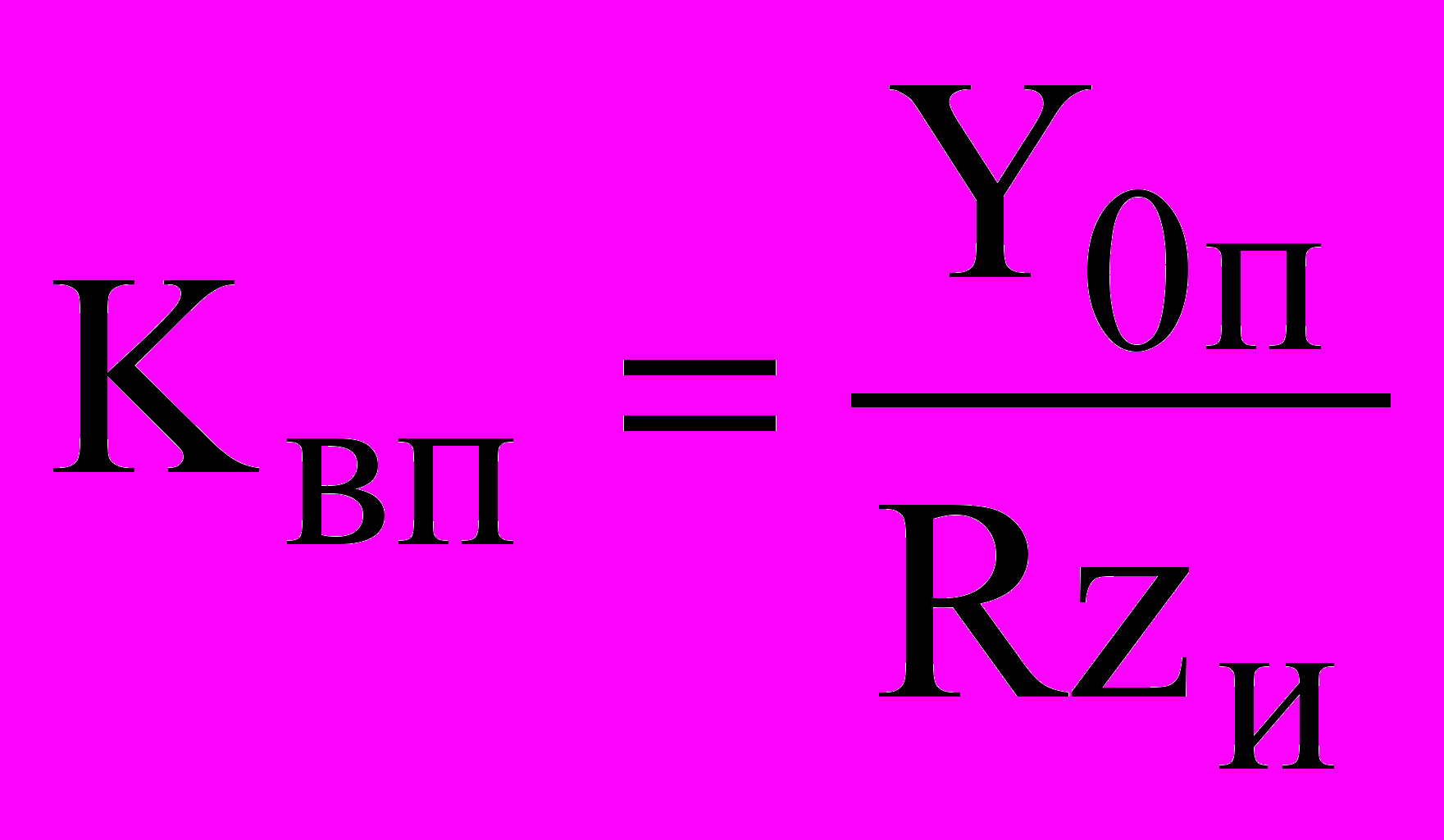
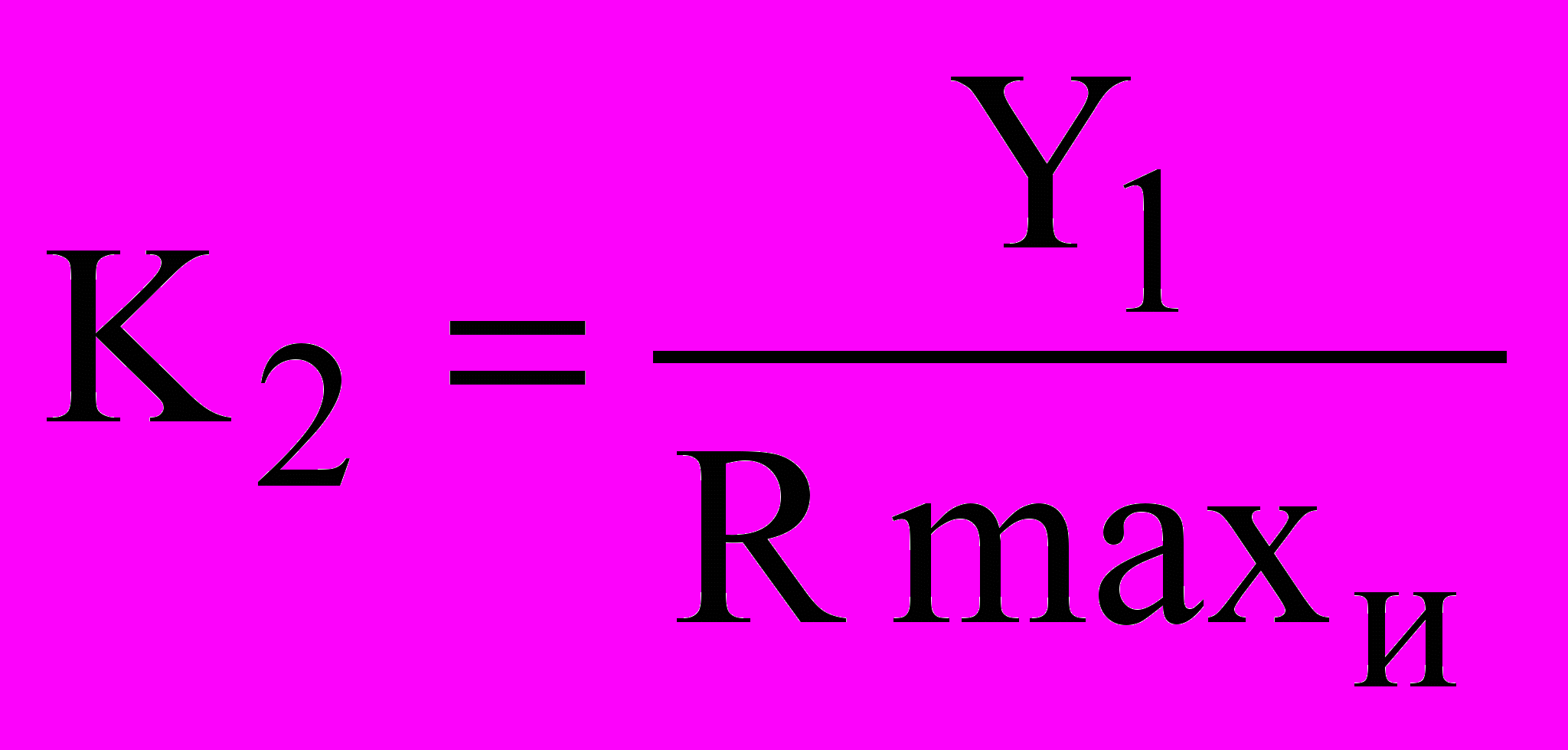
Экспериментально установлено, что алмазное выглаживание при значениях факторов обработки Rmaxисх = 11,5…36 мкм; Q = 590…790 Н; /r = 0,5…0,63 (r – радиус индентора при ППД) позволяет управлять всеми рассмотренными величинами, а величинами Y0 и Y0п - в пределах 14…48 и 9…39 мкм соответственно.
Таким образом, восстановление диаметрального размера D = 2Y0 или D = 2Y0п возможно в пределах от 28 до 96 мкм в первом случае и от 18 до 78 мкм во втором случае.
Ориентация на величину Y0п (второй случай) более предпочтительна, так как острые пики выдавленной поверхности, определяющие величину Y0, подвергнутся быстрому интенсивному изнашиванию в начальный период работы восстановленной поверхности детали.
![]() | |
Рис. 7. Типовой профиль поверхности с остаточными следами воздействия индентора при ППДПС:
0-0 – линия выступов исходной поверхности; , мм – шаг между соседними траекториями
движения индентора; П – исходная поверхность с параметрами шероховатости Rmaxисх и Rzисх
В итоге необходимо отметить, что гибридизация метода ППД с системой ЧПУ даёт возможность реализации размерного восстановления программным способом, преимущество которого заключается в том, что благодаря технологической гибкости 2-го рода при восстановлении изношенной поверхности, получившей макроотклонения из-за нестационарности условий эксплуатации, восстановленная поверхность не будет иметь макроотклонений (вогнутость, выпуклость, бочкообразность и др.).
На качество поверхности, обрабатываемой методами ППД (ППДПС) устройствами упругого действия, сильное влияние оказывает динамика процесса. Анализ качества поверхности, имевшей предварительную волнистость с высотой Wmax и шагом по средней линии Smw и обработанной ППД, показал, что в зависимости от соотношения конструктивных (m – масса ползуна, кг; c – жёсткость пружины, Н/м), режимных (V – скорость обработки, м/мин) и технологических (Wmax, Smw, мкм) факторов наблюдаются участки с равномерной и неравномерной обработкой (подскоки с пролётом индентора над поверхностью, его удары о поверхность с оставлением на ней вмятин). Анализ устойчивости с позиций теории автоматического управления показал, что система обработки ППД во всех этих случаях является динамически устойчивой, так как отмеченные возмущения затухают с течением времени. Однако их последствия в виде оставшихся необработанными участков исходной поверхности, участков со следами ударов и др. остались. Так как наличие таких участков не соответствует требованиям по качеству, результат обработки нельзя считать удовлетворительным. Таким образом, для обеспечения заданных параметров качества динамической устойчивости процесса оказывается недостаточно. Нужно, чтобы процесс обладал технологической устойчивостью, которой можно дать следующую формулировку:
- технологическая устойчивость процесса обработки ППД устройствами упругого действия – это его способность непрерывно по всей обрабатываемой поверхности обеспечивать требуемый вектор
параметров качества поверхностного слоя (включая эксплуатационные) в регламентированных границах (
) с заданной надёжностью Р(Ri (
).
Область определения технологической устойчивости может рассматриваться в пространстве факторов КПС (Ra, H, 0 и др.) или факторов ЭС, или на их пересечении. Математические условия технологической устойчивости имеют вид

где Ri – i-й вектор параметров качества; P – минимально допустимая надёжность его обеспечения.
Из изложенного следует, что условием технологической устойчивости обработки ППД устройствами упругого действия является поддержание силы обработки в установленных допустимых пределах Q0 < Q < Q0, где < 1, > 1 – коэффициенты, а Q0 = cY0 – номинальная сила при ППД (Y0 – величина предварительного натяга пружины устройства).
Исходя из этого требования, в результате решения дифференциального уравнения динамики процесса ППД получены критерии технологической устойчивости в виде ограничений максимальной скорости обработки:
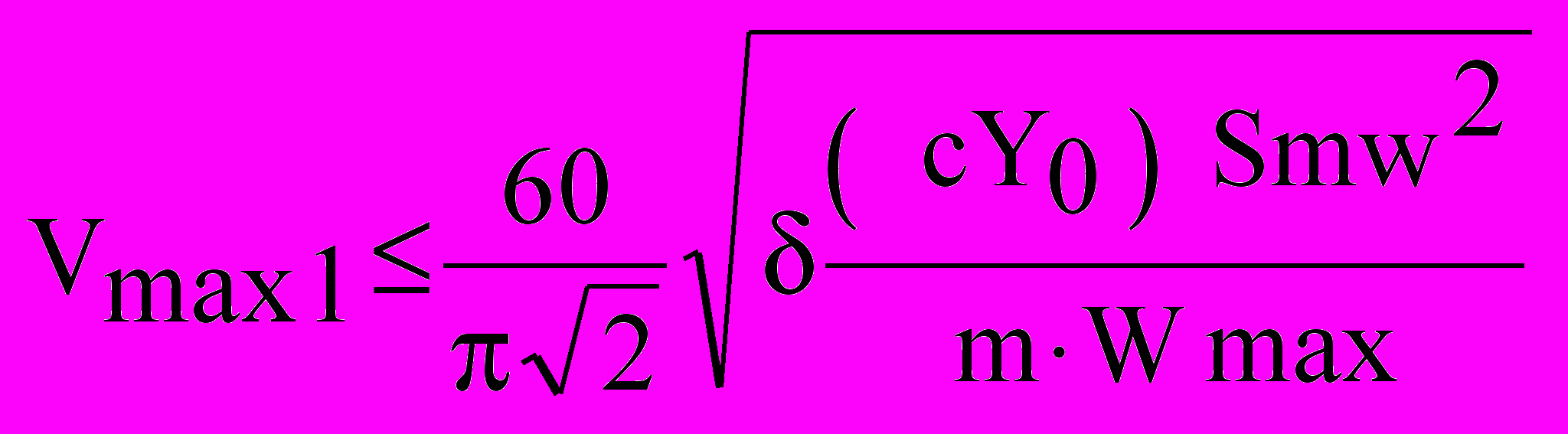
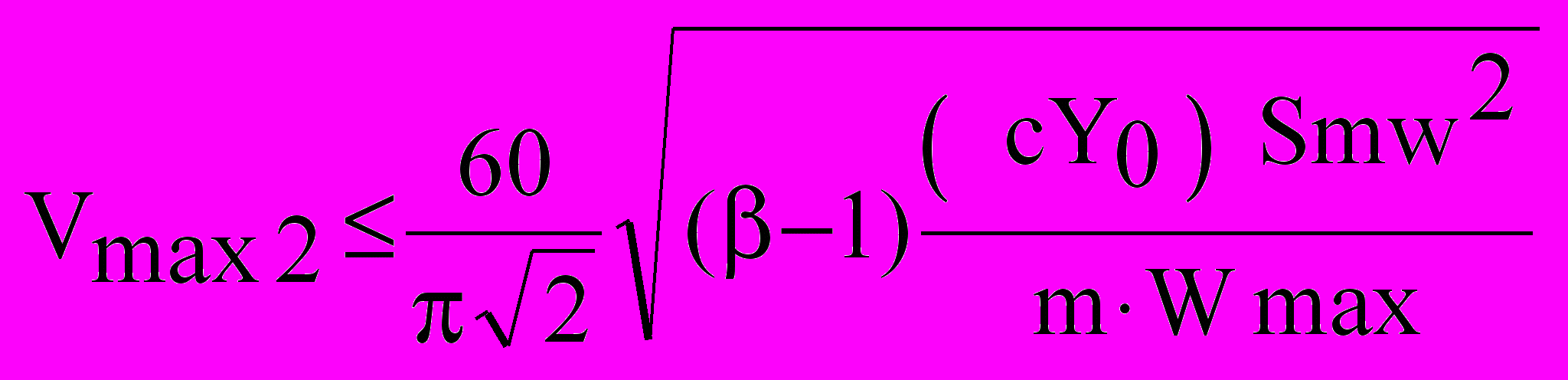
Фактическая максимальная скорость выбирается из условия: Vmax факт min (Vmax1; Vmax2).
Полученные критерии включают параметры КПС после исходной обработки (Wmax, Smw), конструктивные особенности устройства ППД (с, m) и технологические факторы (Q0 = cּY0, , ).
Изложенное позволяет отметить, что для обеспечения высоких эксплуатационных свойств поверхностей трибоэлементов, работающих в условиях трения скольжения со смазкой, необходимо создание и применение технологически гибких процессов обработки. Следует различать технологическую гибкость 1-го и 2-го рода: технологические гибкие системы 1-го рода (ТГС-1) обеспечивают эффективную, но жёсткую обработку в пределах перехода, а 2-го рода (ТГС-2) – эффективную и управляемую программным способом обработку в пределах перехода, обеспечивая адаптацию поверхности к нестационарным условиям эксплуатации.
Среди ТГС-1 наибольшей эффективностью обладают системы, сочетающие обработку поверхностей методами различной физической природы (обработка резанием, нанесение покрытий, ППД и др.). Гибридизация методов обработки с системами ЧПУ образует класс систем ТГС-2, обладающих наиболее высокой гибкостью. В этом плане перспективно практическое применение ППД программным способом (ППДПС).
Наряду с технологической гибкостью одним из основных условий обеспечения высокого качества обрабатываемых поверхностей деталей машин является технологическая устойчивость процесса обработки, которая отличается от динамической устойчивости и достигается при соблюдении определённых критериев, включающих конструктивные и технологические факторы.
СПИСОК ЛИТЕРАТУРЫ
- Суслов, А. Г. Качество поверхностного слоя деталей машин/А.Г. Суслов. – М.: Машиностроение, 2000. – 320 с.
- Суслов, А. Г. Инженерия поверхности деталей – резерв в повышении конкурентоспособности машин/ А.Г. Суслов // Инженерный журнал: справочник: прил № 4. – 2000. - С. 3 – 9.
- Тотай, А. В. Формирование геометрических параметров качества поверхности деталей машин обработкой сверхтвёрдыми синтетическими материалами/А.В. Тотай, В. П. Фёдоров, В. В. Нагоркина // Вестник Брянского государственного технического университета. – 2004. - № 3. – С. 13 – 21.
- Аверченков, В. И. Новые подходы к автоматизации технологических исследований на основе виртуальных измерительных комплексов/ В.И. Аверченков, В. П. Фёдоров, М. Н. Нагоркин // Вестник Брянского государственного технического университета. – 2005. - № 1. – С. 13 - 21.
- Аверченков, В.I. Iнженерiя I компютерний монiторинг поверхонь деталей машин при обробцi на верстатах iз ЧПУ/В.I. Аверченков, О.В. Ковальова, М.М. Нагоркiн, В.П. Федоров // Вiсник Житомирського iнженерно-технологiчного iнституту. Технiчнi науки. - 2001. – С. 7 – 14.
- Сосонкин, В. Л. Принцип построения открытых систем ЧПУ типа PCNC/В.Л. Сосонкин // Конструкторско-технологическая информатика – 2000: труды конгресса. В 2-т. Т. 2. / IV междунар. конгресс. – М.: Изд-во «Станкин», 2000. – С. 170 - 173.
Материал поступил в редколлегию 20.02.06.