Вестник Брянского государственного технического университета. 2006. №2 (10)
Вид материала | Документы |
- Вестник Брянского государственного технического университета. 2006. №1 (9), 88.23kb.
- Вестник Брянского государственного технического университета. 2006. №2 (10), 298.44kb.
- Вестник Брянского государственного технического университета. 2006. №3 (11) образование, 205.12kb.
- Вестник Брянского государственного технического университета. 2006. №1 (9), 161.23kb.
- Вестник Брянского государственного технического университета. 2006. №1 (9) Социально-философские, 117.78kb.
- Вестник Брянского государственного технического университета. 2011. №4(32), 114.16kb.
- Вестник Брянского государственного технического университета. 2006. №3 (11) Технология,, 94.65kb.
- Вестник Брянского государственного технического университета. 2010. №2(26), 83.85kb.
- Вестник Брянского государственного технического университета. 2008. №3(19), 168.61kb.
- Вестник Брянского государственного технического университета. 2008. №3(19), 138.83kb.
Вестник Брянского государственного технического университета. 2006. № 2 (10)
УДК 621.9
Д.И. Петрешин
ОБЕСПЕЧЕНИЕ ПАРАМЕТРОВ КАЧЕСТВА ПОВЕРХНОСТНОГО
СЛОЯ ДЕТАЛЕЙ ПРИ ТОЧЕНИИ САМООБУЧАЮЩЕЙСЯ
ТЕХНОЛОГИЧЕСКОЙ СИСТЕМОЙ
Рассматривается вопрос создания самообучающейся технологической системы для обеспечения параметров качества поверхностного слоя деталей при механической обработке.
Технологическое обеспечение параметров качества поверхностного слоя деталей машин при механической обработке сводится к выбору условий обработки рабочих поверхностей (методов и режимов обработки, характеристик оборудования и инструмента и т.п.), обеспечивающих получение заданных параметров с наименьшей технологической себестоимостью, и их корректировке в производственных условиях.
Практика показывает, что в большинстве случаев в реальном производстве режимы резания назначаются в соответствии с нормативами. Однако условия обработки в реальном производстве заметно отличаются от нормативных, в которых не учитываются состояние оборудования, колебания свойств обрабатываемого и инструментального материалов, колебания припуска и т.д. При этом задача обеспечения заданных параметров качества поверхностного слоя существенно усложняется еще и тем, что при обработке новых материалов или применении новых инструментальных материалов отсутствуют данные по условиям обработки или они не адекватны реальным условиям. Обычно реальные условия учитываются рабочим непосредственно на рабочем месте на основании его интуиции и опыта. Кроме того, рабочий главным образом преследует цель повышения производительности труда, часто игнорируя вопросы себестоимости и точного соблюдения требований чертежа по обеспечению заданных параметров качества поверхностного слоя. Поэтому актуальной является задача автоматизации процесса назначения и уточнения режимов резания непосредственно на рабочем месте для обеспечения заданных параметров качества поверхностного слоя. Решение этой задачи становится возможным в связи с развитием систем управления металлорежущих станков и созданием самообучающихся технологических систем [1].
Самообучающаяся технологическая система (САТС) - это система адаптивного управления металлорежущего станка с ЧПУ, работа которой заключается в получении математической модели, связывающей параметры качества поверхности с условиями обработки, и использовании полученной модели для управления технологической системой по любому из параметров качества. Исходя из этого, система должна иметь вычислительное устройство, двунаправленный канал связи с технологической системой, датчики для контроля выходных параметров процесса резания, а также программное и алгоритмическое обеспечение. Таким образом, структурная схема самообучающейся технологической системы будет иметь вид, представленный на рис. 1.
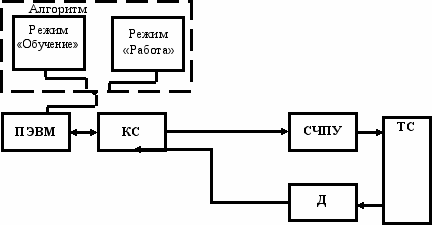
Рис. 1. Структурная схема самообучающейся технологической системы
Система разрабатывается на базе токарного станка модели 16Б16 Ф3 с УЧПУ NC200. В нее входят следующие элементы: технологическая система (ТС); датчик (Д), снимающий информацию о текущем значении параметра качества обработанной поверхности; контроллер сопряжения (КС) датчика с ПЭВМ и ПЭВМ с УЧПУ; система числового программного управления (СЧПУ) NC 200, обеспечивающая управление технологической системой; ПЭВМ, исполняющая роль управляющей системы.
Контроллер сопряжения предназначен для организации обмена информацией датчика с ПЭВМ и ПЭВМ с системой ЧПУ. В состав контроллера входят элементы, преобразующие аналоговый сигнал, поступающий с датчика, в цифровой и передающие его в ПЭВМ. Вычисленная величина поправки (подачи или скорости резания) передается от ПЭВМ контроллеру и далее в систему ЧПУ.
Связь ПЭВМ с контроллером осуществляется через стандартный интерфейс RS-232, а связь контроллера с системой ЧПУ NC 200 - через выходные модули постоянного тока и модуль дискретных входов-выходов, встроенный в систему ЧПУ. Программируемая логика станка позволяет настроить систему ЧПУ на изменение условий обработки путем внешнего программного управления корректорами подач и частоты вращения шпинделя. Функциональная схема модуля сопряжения представлена на рис. 2.
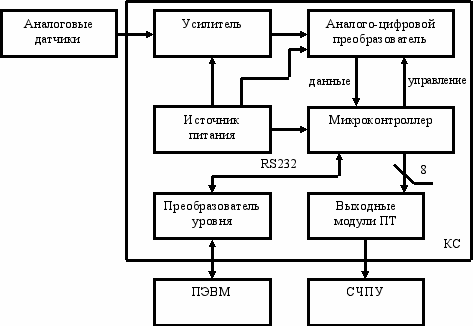
Рис. 2. Функциональная схема модуля сопряжения
В настоящее время при создании автоматизированных систем управления технологическим оборудованием важнейшая роль отводится не только аппаратным средствам, но и алгоритмическому и программному обеспечению. Поэтому алгоритм работы следует рассматривать как неотъемлемую часть самообучающейся системы.
Алгоритмическое обеспечение САТС можно условно разделить на две взаимозависимые части. Первая часть относится к алгоритмическому обеспечению аппаратной части САТС и описывает процедуру связи между технологической системой, ПЭВМ и УЧПУ. Вторая часть относится к алгоритму самообучения и адаптивному управлению технологической системой по параметрам качества поверхностного слоя.
Алгоритм самообучения и адаптивного управления технологической системой представлен на рис. 3. Он описывает следующие основные режимы работы системы: 1) ввод и анализ исходных данных; 2) база знаний; 3) обучение; 4) работа.
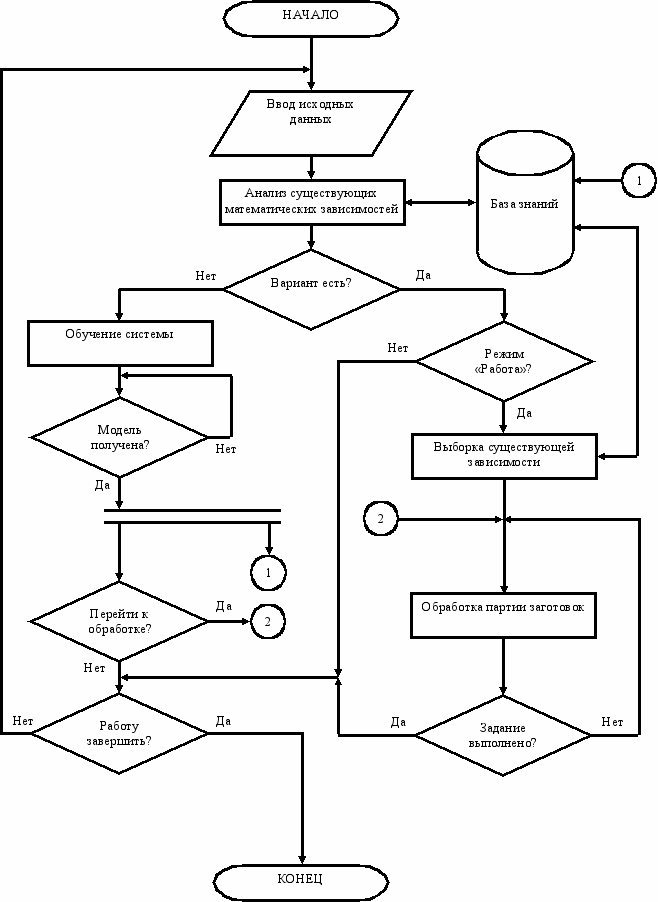
Рис. 3. Алгоритм самообучения и адаптивного управления ТС
Режим «Ввод и анализ исходных данных» предназначен для ввода и анализа исходных данных перед началом обработки. К исходным данным относятся: материал обрабатываемых деталей, геометрия инструмента, режимы резания, жесткость технологической системы, параметр качества обработанной поверхности, который необходимо обеспечить, и его требуемое значение. По введенным данным система устанавливает, имеется ли в базе знаний соответствующая им математическая модель.
Режим «База знаний» служит для сохранения и накопления информации об обработанных материалах, условиях обработки и соответствующих им полученных математических моделях. Так, для каждого обрабатываемого материала и каждого из условий обработки в базе знаний имеется своя математическая модель. Если соответствующей математической модели нет, то система автоматически переходит в режим «Обучение».
Задачей режима «Обучение» является постановка эксперимента и получение математической модели. Для этого на станке обрабатывается пробная деталь – образец. Причем инструмент, его геометрия, материал образца и глубина резания должны быть такие же, как и при обработке последующей партии деталей. Образец разбивается на участки, затем каждый из них автоматически обрабатывается с заданными режимами резания. В процессе обработки системой автоматически контролируются параметры качества обработанной поверхности.
Данные о входных и выходных параметрах процесса резания заносятся автоматически в ЭВМ, осуществляется их статистическая обработка, и получается математическая модель, например вида
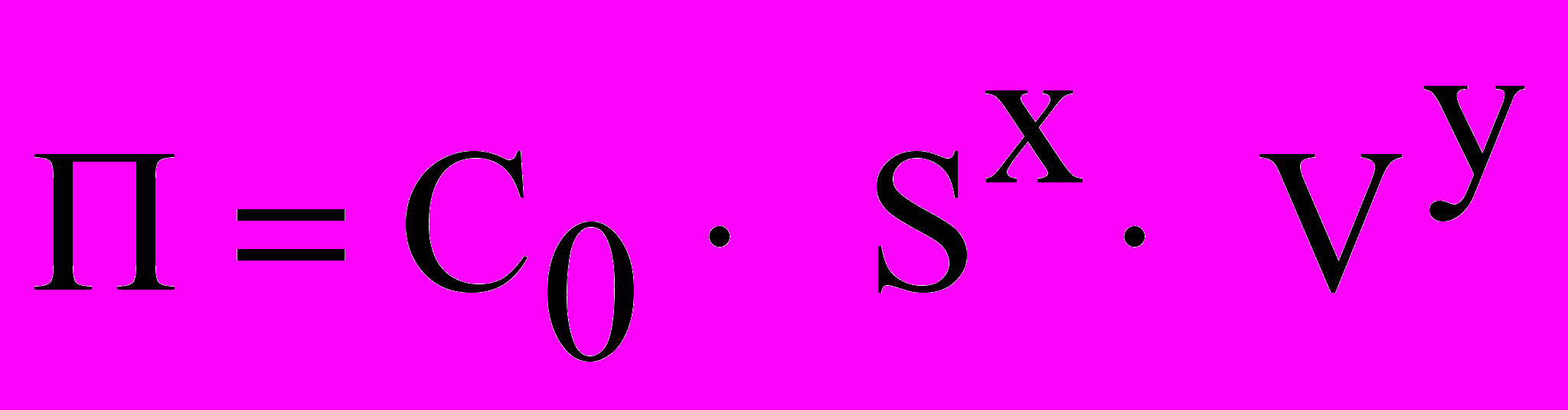
где П – управляемый параметр качества обработанной поверхности; S – величина продольной подачи, мм/об; V – скорость резания, м/мин; C0, x, y – коэффициенты модели.
Двухфакторная модель используется для управления геометрическими параметрами качества обработанной поверхности, т.к. остальные входные факторы (материал заготовки, глубина резания, инструмент и т.д.) не оказывают существенного влияния на их формирование и остаются неизменными [2].
Полученная математическая модель и ее данные, т.е. условия обработки, при которых она была получена, и коэффициенты модели, запоминаются в базе знаний и используются в дальнейшем. При изменении инструмента, его геометрии, материала деталей, глубины резания и т.п. необходимо будет опять провести обучение системы. Затем приступают к обработке деталей, используя режим «Работа».
Режим «Работа» осуществляет адаптивное управление технологической системой по заданному параметру качества обработанной поверхности. В этом режиме выполняются прием измерительной информации от контроллера сопряжения и анализ полученной информации, на основе которого принимается решение об управлении технологической системой.
Для управления технологической системой по одному из параметров качества поверхности необходимо из математической модели (1) получить закон управления, например вида
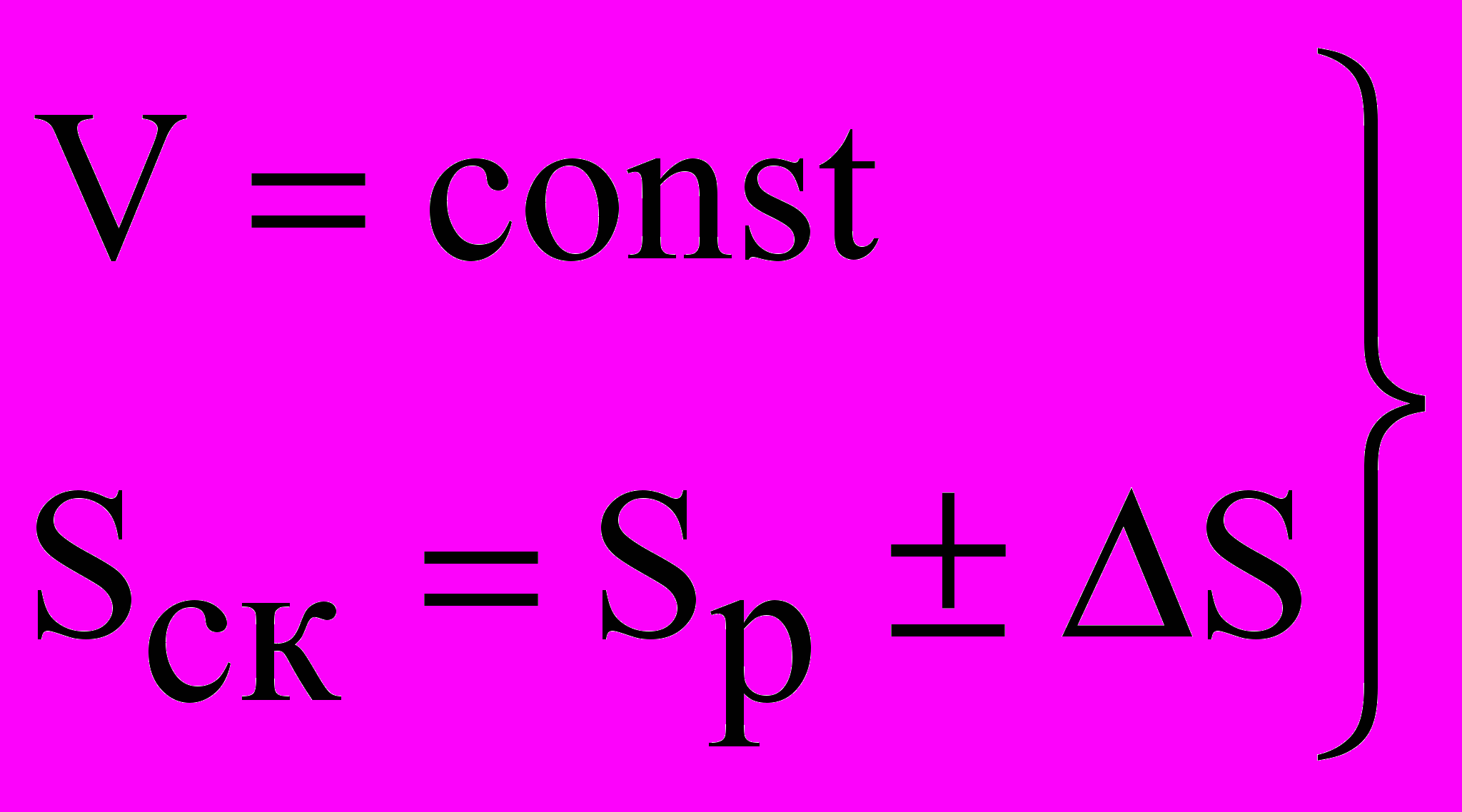
где V – скорость резания, м/мин; Sск – скорректированное значение подачи, мм/об; Sр – начальное значение подачи, мм/об; S – поправка на величину подачи, которую необходимо внести в процесс обработки, чтобы параметр качества поверхности достиг требуемого значения или находился в пределах допуска на это значение. S рассчитывается по зависимости
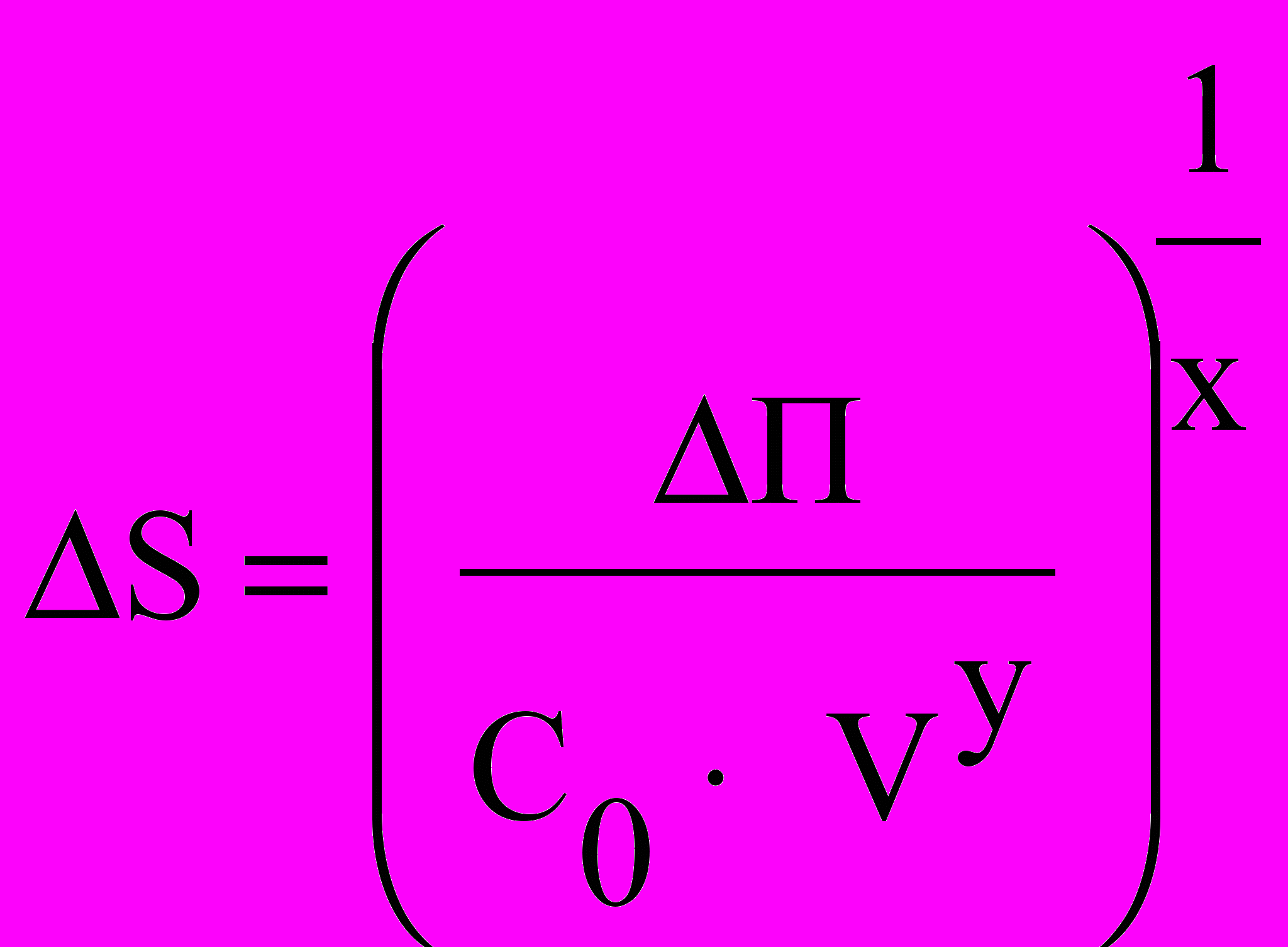
где П – отклонение параметра качества обработанной поверхности от требуемого значения.
Знак коррекции, т.е. увеличение или уменьшение продольной подачи, система определяет сама автоматически на основе результата сравнения заданного и измеренного значений параметра качества обработанной поверхности.
Другими немаловажными параметрами качества поверхностного слоя, от которых также зависят эксплуатационные свойства деталей машин, являются остаточные напряжения и степень упрочнения поверхностного слоя детали. Как известно, этими параметрами можно управлять через температурно-силовое воздействие на обрабатываемую поверхность посредством режимов резания, скорости резания, продольной подачи и глубины резания при условии, что остальные входные факторы остаются неизменными.
Для обучения такой системы также необходимо обработать пробную деталь и получить информацию о температуре и силе резания. На основе полученной информации определяются математические зависимости вида
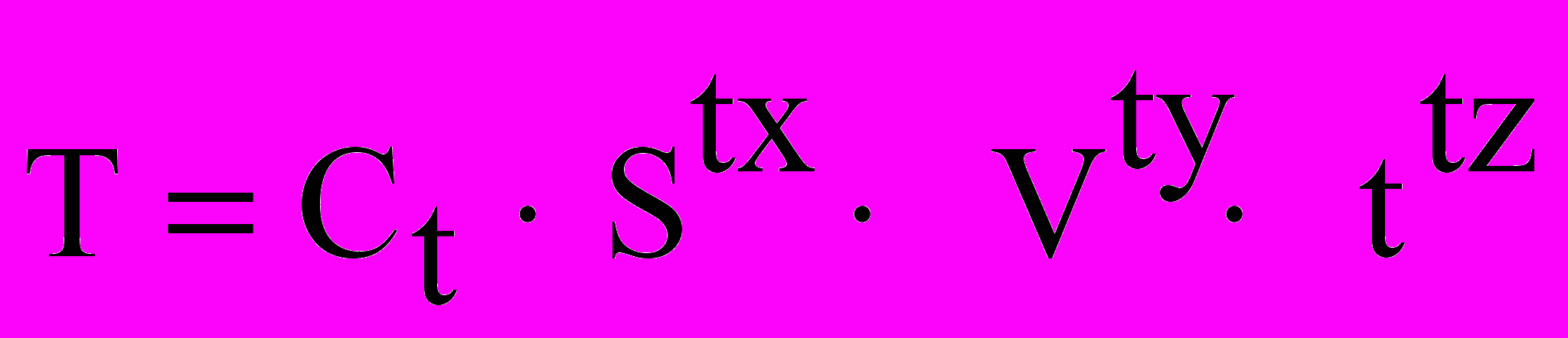

где T – температура в зоне резания; t - глубина резания; tx, ty, tz, Ct – коэффициенты для модели; Pz,y,x – составляющие силы резания; Сp, px, py, pz - коэффициенты для составляющих сил резания модели.
Кроме полученных зависимостей, необходимо иметь закон управления, который бы связывал остаточные напряжения или степень упрочнения с режимами обработки через температуру и силу резания. Для определения закона управления необходимо знать степень влияния скорости резания, продольной подачи и глубины резания на выходные параметры процесса. Дальнейшие действия аналогичны описанным. Параметр управления, который оказывает наибольшее влияние на выходные показатели процесса, изменяется первым с учетом всех ограничений, а затем управление передается другому параметру.
В режиме «Работа» измеряются сила резания и температура в зоне обработки, рассчитываются по полученным данным выходные параметры процесса, степень упрочнения или остаточные напряжения, сравниваются расчетные и требуемые параметры и принимается решение.
СПИСОК ЛИТЕРАТУРЫ
- Суслов, А.Г. Технологическое обеспечение качества обработанных поверхностей деталей машин с использованием самообучающихся технологических систем / А.Г. Суслов, Д.И. Петрешин, Д.И. Финатов // Инженерный журнал: справочник. - 2004 №1, с. 14 - 17.
- Суслов, А.Г. Научные основы технологии машиностроения / А.Г. Суслов, А.М. Дальский - М.: Машиностроение, 2002. - 684 с.
Материал поступил в редколлегию 20.02.06.