З м І с т стор. Вступ. Лекція
Вид материала | Лекція |
- План. Вступ. Стор. 1 Волюнтаризм як напрямок філософської думки. Стор. 2 А. Шопенгауер., 301.41kb.
- Укра ї нська мова, 20.84kb.
- Аналітична записка, 438.14kb.
- Зміст Стор. Вступ 4, 438.28kb.
- Методичні рекомендації з питань правової освіти „ Корекційна робота з агресивними дітьми, 1401.54kb.
- Народна демонологія: розкриття образу нечистої сили, 225.3kb.
- План святкування вечірки Словникова робота Маршрут екскурсій по Харкову Література, 16.38kb.
- И. Л. Кривопуск Вивчити § 36 (правила). Впр. 254, стор. 115; § 37 виписати стор. 116, 63.13kb.
- Питання на екзамен з курсу “атомна фізика”, 41.66kb.
- Загальноосвітній навчально-виховний комплекс гуманітарно-естетичного профілю (гімназія-інтернат, 2327.17kb.
ЛЕКЦІЯ 8
Специфічні процеси лиття
Для певних модифікацій СП розглянуті вище процеси лиття не завжди придатні. Тут використовуються специфічні процеси ливарного виробництва. По-перше, це штамповка рідкого металу. Даний процес поєднує в собі елементи лиття під тиском і об’ємної штамповки. За цим методом, на залитий у бак розплав діє зусилля пуансона, що створює умови для об’ємно-стиснутого стану металу і його спрямованої кристалізації. Як пуансон використується металічний стрижень з циліндричною порожниною, в якому розміщено суцільний кооксиальний циліндр меншого діаметра. Рідкий метал витісняється у простір між циліндрами, в результаті чого з’являється заготовка для деталі СП з покращеними експлуатаційними характеристиками. У такий спосіб виготовляють корпуси шахтних СП і світильників для підводних човнів (тобто в першу чергу там, де є необхідною міцність конструкції).
Іншим різновидом лиття під тиском є продування розплаву через щілину заданої конфігурації - фільєру. Даний метод буде наведений нижче при описанні процесів виготовлення елементів СП з полімерних матеріалів. У даному випадку треба тільки відзначити високий темп виробництва (50 м заготовки за хвилину) і його незалежність від складності виробу. Вказаним методом зружно виготовляти металічні корпуси для люмінісцентних СП.
Виробництво деталей СП з полімерних матеріалів
Починаючи розгляд процесів вироблення елементів СП з полімерних матеріалів, тобто пластмас, звернемо увагу на загальні особливості останніх. У порівнянні з металічними матеріалами, у пласмас є низка суттєвих переваг:
1.Деталі з пласмас мають тверду і гладку поверхню, не потребують додаткової механічної обробки.
2.Пласмаси не потребують фарбування, оскільки їх колір одержується додаванням у вихідний матеріал фарбувальних речовин пігментів.
3.Деталі з полімерних матеріалів не піддаються корозії.
4.Вага пласмасових деталей незначна.
5.Для пластмас є високою енергоекономічність роботи.
Залежно від поведінки при нагріванні пластмаси розділяють на два класи – реактопласти і термопласти. Реактопласти набувають пластичності при нагріванні, а після охолодження втрачають її назавжди, тобто їх подальша переробка неможлива. Термопласти при нагріванні завжди набувають пластичності. Відходи деталей з термопластів широко використовуються як вторинні матеріали.
П
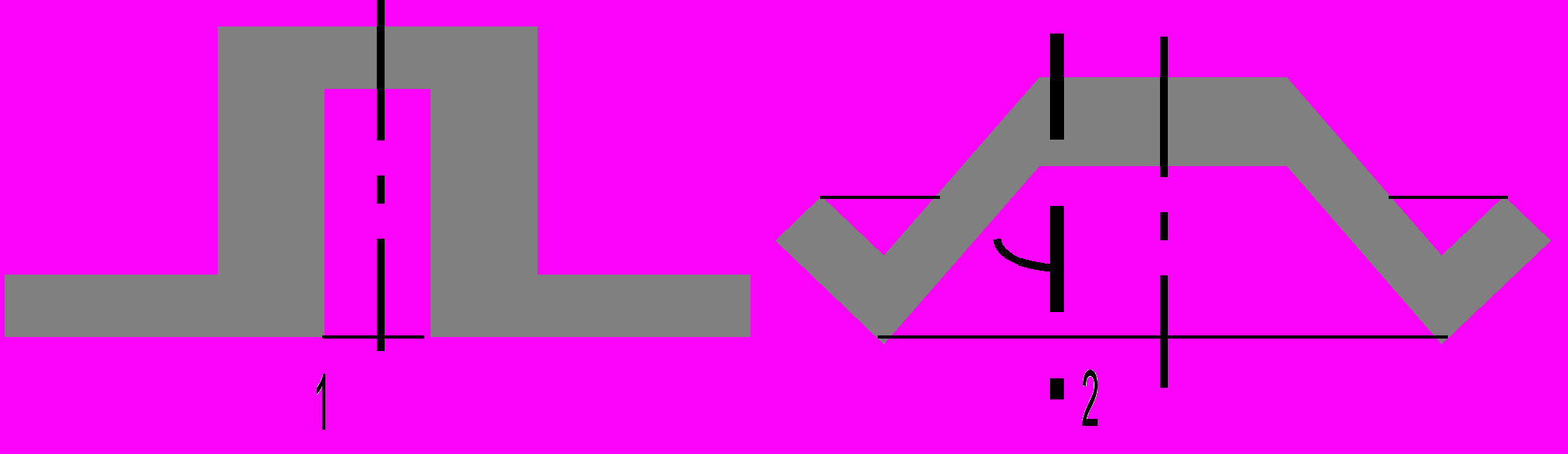
ри виготовленні деталей з пластмас треба враховувати їх усадку і технологічні уклони. Під усадкою розуміють різницю між розмірами прес-форми і деталі при температурі 20 С через 24 години після закінчення формування. Технологічні уклони (див. рис. 19.2) зменшують зусилля по вилученню готової деталі з прес-форми і сприяють полегшенню проникання пластичної маси у форму.
Рис.19 - 1- відсутність технологічного уклону (нераціонально),
2 – наявність технологічного уклону (раціонально)
Дослідним шляхом встановлено оптимальні значення технологічних уклонів для виробів з пласмас різної висоти. Узагальнена інформація про таку кореляцію наведена в табл. 4.
Таблиця 4 - Мінімальні значення технологічних уклонів
Висота деталі, мм | Зовнішня поверхня | Внутрішня поверхня |
до 10 | 1:100 | 1,5:100 |
10-50 | 0,8:100 | 1,2:100 |
50-100 | 0,6:100 | 1:100 |
100-200 | 0,5:100 | 0,8:100 |
200 | 0,3:100 | 0,6:100 |
Товщина стінок пресованих деталей з пластмас звичайно складає 1,5 - 4 мм, а формованих методом виливання під тиском 0,6 - 3 мм. Вибір оптимальної товщини деталі є важливим промисловим завданням. При недостатній товщині програє міцність деталі в цілому, при надмірній – збільшується час технологічного процесу, оскільки деталі остигають надто повільно. Для термопластів використують емпіричну формулу, яка дозволяє визначити мінімальну товщину Smin деталі заданої висоти:

Суттєвим є також вибір радіуса r закруглення при сполученні поверхонь. Наявність цих радіусів покращує зовнішній вигляд деталей і знижує їх вибракування. Вважається оптимальним таке закруглення: r 2 h.
Важливою складовою технологічного процесу переробки пластмас є підготовка прес-матеріалу – таблетування і попередній підігрів таблеток. Таблетування є процесом перетворення прес-матеріалу в таблетки заданої форми і маси. Використання таблеток є зручним, так як при цьому спрощується дозування матеріалу, зкорочення часу на його нагрів і формування, підвищується якість матеріалу і заготовки. Як вихідний при таблетуванні використовують порошкоподібний полімерний матеріал і домішки, які ретельно перемішують багаторазовим пропусканням суміші через систему двох валків.
Зваження порцій прес-матеріалу виконують високотехнологічним способом об’ємного дозування (див. рис. 20). Як можно бачити з рисунка, бункер 2 може відкривати чи закривати отвір для подання пластичної маси 3. Пуансон 1 є нерухомим і відіграє роль упора. Пресування матеріалу виконують пуансоном 4. Якщо бункер відвести ліворуч, пуансон 4 звільниться і готову таблетку можна виштовхнути пуансоном 1. Прес-матеріал слід подавати в бункер нагрітим. Знаходячись у формі декілька секунд він не встигає втратити свої властивості, а лише пом’ягшується. Вплив попереднього нагрівання на тривалість обробки прес-матеріала показано у табл. 5.
Таблиця 5 - Тривалість обробки пластмас при різних режимах нагріву
Температура нагріву, С | Тривалість нагріву, хв. | Скорочення тривалості витримки матеріалу у прес-формі, % |
80 | 15-16 | 10-30 |
100 | 13-15 | 20-40 |
120 | 8-10 | 25-50 |
160 | 6-9 | 30-60 |
1 ![]() 80 | 5-8 | 40-80 |
Рис. 20 - Таблетування пласмас
Контрольні запитання
1. Специфічні процеси лиття.
2. Характеристики пластмас і виробів з них.
3. Особливості раціонального виготовлення виробів з пластмас.
4. Процес таблетування.