Методические указания для выполнения домашних заданий и курсовых работ для студентов очной и заочной форм обучения. Направление 190500 Эксплуатация транспортных средств. Специальности 190603, 150405
Вид материала | Методические указания |
- Темы (задания) курсовых работ и методические указания по их выполнению для студентов, 578.18kb.
- Методические указания по выполнению контрольных работ и домашних заданий (рефератов), 314.07kb.
- Методические указания по выполнению контрольных работ и домашних заданий (рефератов), 137.22kb.
- Методические указания для выполнения лабораторной работы для студентов очной и заочной, 106.59kb.
- Гражданское право, 165.36kb.
- Методические указания по выполнению курсовых работ для студентов заочной форм обучения, 117.01kb.
- Методические указания по выполнению и оформлению дипломной работы для студентов специальности, 458.23kb.
- Методические указания по выполнению курсовых работ для студентов дневной и заочной, 75.21kb.
- Методические указания для выполнения курсовых работ по дисциплине «Финансы» для студентов, 348.35kb.
- Методические указания по написанию курсовой работы для студентов очной, заочной и очно-заочной, 318.34kb.
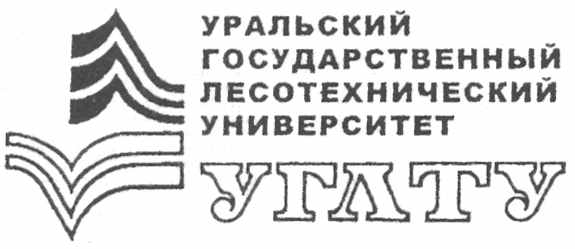
В.В. Илюшин
Б.А. Потехин
ТЕХНОЛОГИЯ
МАШИНОСТРОЕНИЯ
Екатеринбург
2011
Министерство образования и науки Российской Федерации
Уральский государственный лесотехнический университет
Кафедра технологии металлов
В.В. Илюшин
Б.А. Потехин
ТЕХНОЛОГИЯ
МАШИНОСТРОЕНИЯ
Методические указания для выполнения домашних заданий и курсовых работ для студентов очной и заочной форм обучения.
Направление 190500 – Эксплуатация транспортных средств.
Специальности 190603, 150405
Екатеринбург
2011
Печатается по рекомендации методической комиссии
лесомеханического факультета
Протокол № 6 от 27.05.2011
Рецензент – В.П. Лесников, докт. техн. наук, директор ООО «Турбомет»
Редактор
Компьютерная верстка
Подписано в печать Формат 60х84 1/16 Поз. №
Плоская печать Печ.л. Тираж экз.
Заказ № Цена
Редакционно-издательский отдел УГЛТУ
Отдел оперативной полиграфии УГЛТУ
ОГЛАВЛЕНИЕ
Содержание, порядок оформления и представления работы
студентом ..…………………………………………………………….… 5
1. Выбор заготовки ……………………………………………………… 5
2. Обоснование маршрута изготовления детали ……………….……... 5
3. Выбор оборудования, инструментов и приспособлений ………….. 6
4. Выбор режимов резания ……………………………………….…….. 7
5. Проверка оборудования по крутящему моменту ………………....... 9
6. Определение трудоемкости изготовления детали ……...………… 10
7. Определение коэффициента использования металла …………….. 12
Рекомендуемая литература ……………………………………..….….. 12
Приложение 1 Задания к работе ………………………..…………..… 13
Приложение 2 Пример выполнения работы ………………………..... 17
Содержание, порядок выполнения и
представления работы студентом
Расчетно-пояснительная записка должна быть представлена строго в следующем порядке:
1. Титульный лист;
2. Маршрутная технологическая карта;
3. Описание выбора заготовки;
4. Обоснование технологического процесса изготовления детали;
5. Выбор оборудования, инструментов и приспособлений;
6. Выбор режимов резания;
7. Проверка оборудования по мощности;
8. Расчет трудоемкости изготовления детали;
9. Расчет коэффициента использования металла;
10. Список используемой литературы.
1. ВЫБОР ЗАГОТОВКИ
Заготовка выбирается так, чтобы она по геометрии минимально отличалась от готовой детали при этом коэффициент использования металла Ким (см. п. 7) должен быть максимально возможным. Требуемое количество металла, например, длина заготовки сортового металла, рассчитывается на всю партию изделий с учетом припусков на изготовление, например, на разрезку проката и торцевание заготовки (детали). Типовой сортамент выбирается по специальной литературе, например [1, 2], и должен соответствовать требованиям ГОСТ.
2. ОБОСНОВАНИЕ МАРШРУТА ИЗГОТОВЛЕНИЯ ДЕТАЛИ
Технологический процесс (последовательность операций) нельзя составлять фрагментами, то есть его следует разработать полностью, чтобы увидеть целиком и, например, если требуется, обсудить с преподавателем.
Следует стремиться к использованию наименьшего количества оборудования, инструментов, приспособлений, операций, переходов; необходима бдительность при выборе места термической обработки в технологическом процессе.
При разработке технологического процесса следует хорошо понимать следующие термины:
- технологический процесс - это часть производственного процесса, содержащая целенаправленные действия по изменению состояния предмета труда (ГОСТ 3.1109 – 82);
- технологическая операция - законченная часть технологического процесса, выполняемая на одном рабочем месте;
- технологический переход - законченная часть технологической операции, выполняемая одними и теми же средствами технологического оснащения при постоянных технологических режимах и установке заготовки;
- установ – часть технологической операции, выполняемая при неизменном закреплении обрабатываемой заготовки;
- проход (рабочий ход i = 1…n) – часть перехода, осуществляемая при одном рабочем перемещении инструмента в направлении подачи. За один проход снимают один слой металла.
3. ВЫБОР ОБОРУДОВАНИЯ, ИНСТРУМЕНТОВ и
ПРИСПОСОБЛЕНИЙ
Выбор оборудования следует выполнять из условия обеспечения высокой производительности процесса, минимальных энергозатрат производства и требуемого класса точности готовой продукции.
При выборе станков следует руководствоваться габаритами устанавливаемой заготовки. Для токарного станка максимальный диаметр заготовки ограничивается расстоянием от оси вращения шпинделя до направляющих суппорта. Максимальный размер (диаметр) длинномерной заготовки – проката, ограничивается диаметром отверстия в шпинделе. Для фрезерного и сверлильного станков максимальный размер устанавливаемой заготовки следует ограничить габаритами стола для закрепления. При этом максимальная величина обрабатываемого размера, например, длина, ограничивается положением конечных выключателей, которые определяют возможное перемещение стола.
Инструменты следует выбирать многофункциональные, чтобы одним резцом, например, можно было: торцевать заготовку, точить поверхность, снимать фаски и др.
При выборе оборудования, инструмента и приспособлений рекомендуется опираться на литературу [3, 4].
В настоящем разделе записки обязательно следует привести характеристики выбранных станков, характеристики и эскизы основных резцов, фрез. Для типового инструмента - сверл, метчиков, плашек, зенкеров, разверток можно лишь указать их характеристики, без эскизов.
В технологической карте для каждой операции, каждого перехода необходимо указывать применяемые инструменты и приспособления (тисы, оправки, патроны, люнеты, хомуты, слесарный инструмент и др.).
4. Выбор режимов резания
Режимы резания следует выбирать по таблицам 1 и 2 из условия обеспечения рациональной производительности процесса резания, требуемой шероховатости и точности изготовления детали.
Допустимую скорость резания [Vрез] при достаточной стойкости инструмента Т = 40 мин в первом приближении можно определить по таблице 1. При этом целесообразно скорость резания при точении принимать равной Vрез = 0,5…0,75[Vрез], а при фрезеровании и сверлении – Vрез = 0,25…0,5[Vрез].
Таблица 1 - Значение допустимой скорости резания [Vрез], м/мин для марки режущей части инструмента при твердости заготовки НВ
Твердость заготовки НВ, кгс/мм2 | Марка режущей части инструмента | |
Т15К6 | Р6М5 | |
200 | 300 | 60 |
300 | 200 | 40 |
400 | 100 | 20 |
500 | 50 | - |
После выбора скорости резания, определяются обороты шпинделя:
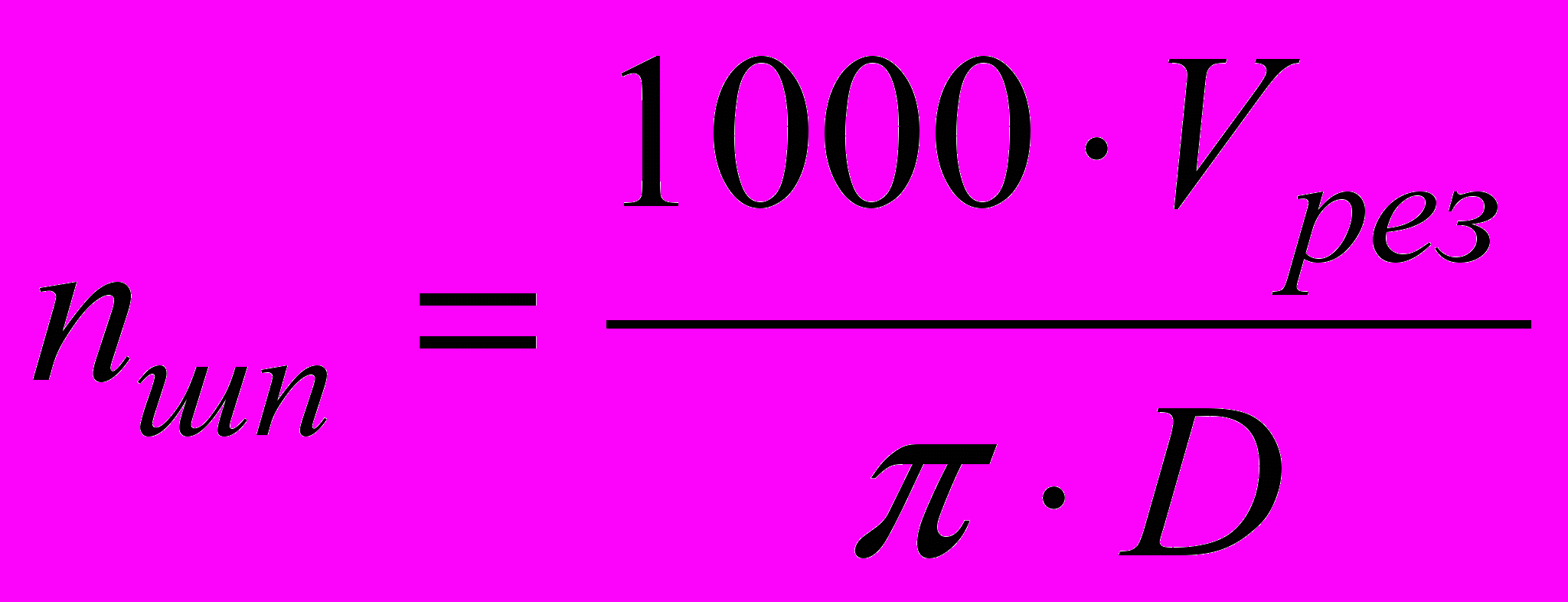
где D – диаметр заготовки при токарной обработке, диаметр фрезы или сверла соответственно при фрезеровании или сверлении, мм.
Расчетное значение оборотов шпинделя согласуют с рядом стандартных значений оборотов шпинделя конкретного станка, выбранного в пункте 3, округляя в меньшую сторону. Данные о частоте вращения шпинделя приведены в технической характеристике станка (паспорте), либо на панели управления станка.
Подачу S при черновой обработке принимают исходя из требований максимальной производительности, минимального количества проходов и возможностей оборудования. При назначении подачи для черновой обработки можно воспользоваться уравнением (8) приведенным в п.5. Значение подачи не рекомендуется назначать более 0,5 мм/об при точении, сверлении и 200 мм/мин при фрезеровании.
Допустимые подачи [ S] при точении и сверлении или [SZ] при фрезеровании для обеспечения требуемой по чертежу шероховатости поверхности Ra, выбирают в зависимости от радиуса r вершины резца (таблица 2).
Таблица 2 - Значение допустимой подачи [S], мм/об (при точении, сверлении) или [SZ], мм/зуб при фрезеровании для получения требуемой шероховатость Ra в зависимости от радиуса r вершины резца
Шероховатость Ra, мкм | Радиус вершине резца r, мм | ||
0,2 | 0,5 | 1,0 | |
0,125 | 0,03 | 0,05 | 0,08 |
0,63 | 0,07 | 0,10 | 0,12 |
1,25 | 0,10 | 0,15 | 0,18 |
2,50 | 0,15 | 0,20 | 0,25 |
4,00 | 0,25 | 0,30 | 0,38 |
6,30 | 0,35 | 0,45 | 0,50 |
12,50 | 0,50 | 0,65 | 0,70 |
В общем случае при фрезерной обработке оперируют минутной подачей Sм которая связана с подачей на зуб фрезы SZ следующими соотношениями:
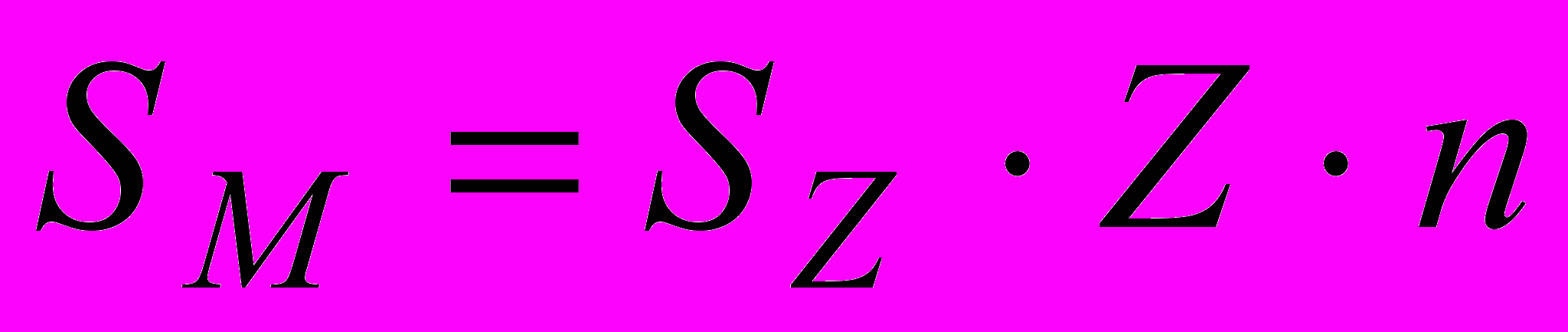
где SM – минутная подача, величина перемещение заготовки в направлении подачи за одну минуту, мм/мин;
SZ – подача на один зуб фрезы, величина перемещения заготовки за время поворота фрезы на один зуб, мм/зуб;
Выбранную подачу S, об/мин при точении и сверлении, либо рассчитанную SМ, мм/мин при фрезеровании, согласуют с рядом стандартных значений подач конкретного станка, выбранного в пункте 3, округляя в меньшую сторону.
Глубина резания t для черновой обработки выбирается максимальная (желательно снять черновой припуск за один проход) исходя из возможности оборудования по крутящему моменту на шпинделе станка.
5. Проверка оборудования по
крутящему моменту
Проверять возможности станка следует по одной, самой напряженной операции, связанной с наружным точением (обтачиванием, торцеванием). Самой напряженной, является операция, для которой произведение t∙S∙НВ – максимально. Как правило, такому условию соответствуют операции черновой обработки с максимальными значениями глубины резания t и подачи S.
Крутящий момент на шпинделе Мшп станка зависит от мощности приводного электродвигателя Nдв и числа оборотов шпинделя nшп:
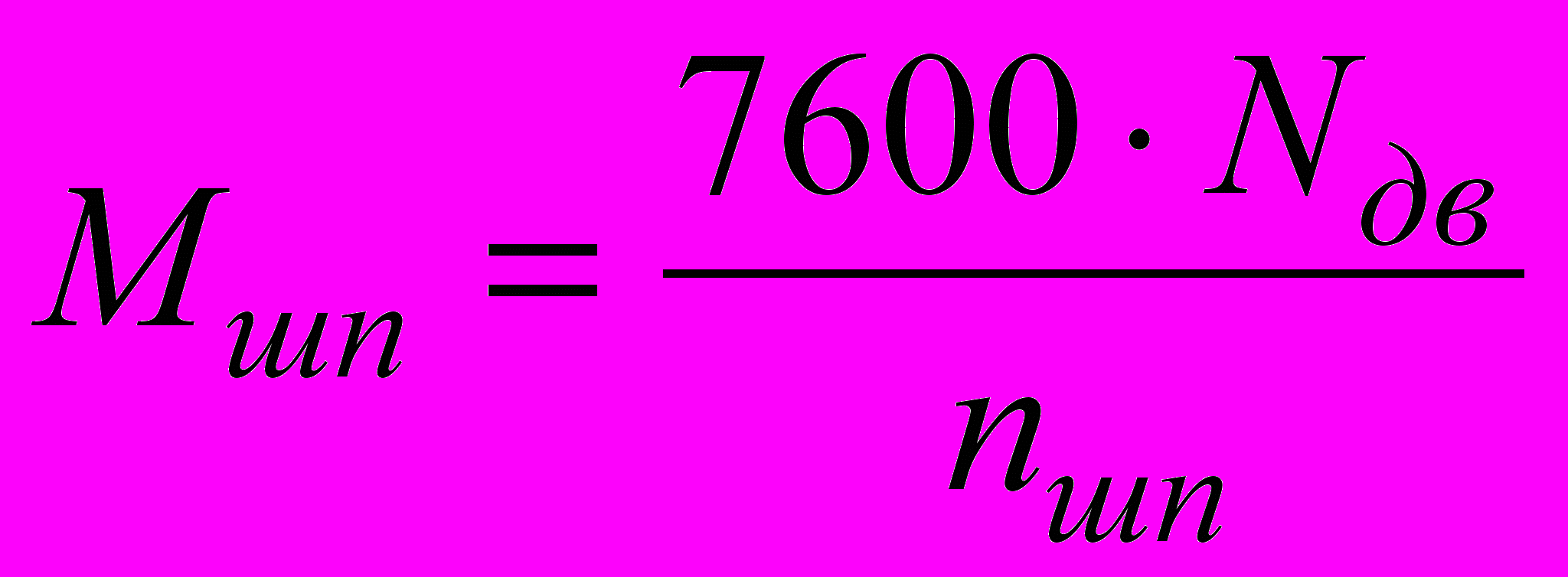
где Мшп – крутящий момент на шпинделе, Н∙м;
Nдв – мощность электродвигателя станка, кВт;
nшп – число оборотов шпинделя, об/мин.
В процессе резания на заготовке силы резания создают момент резания противоположного знака, который направлен навстречу крутящему моменту на шпинделе. Величина момента резания пропорциональна глубине резания, подаче, прочности на срез ср и радиусу обрабатываемой детали или радиусу инструмента R:

где Мпез – момент резания на заготовке, Н∙м;
ср – прочность материала заготовки на срез, МПа;
t – глубина резания, мм;
S – подача, мм/об;
R – радиус обрабатываемой детали, м.
Учитывая, что ср ≈ 2,5НВ имеем:

Условием резания является:
Мшп > Мрез (6)
или после преобразований:
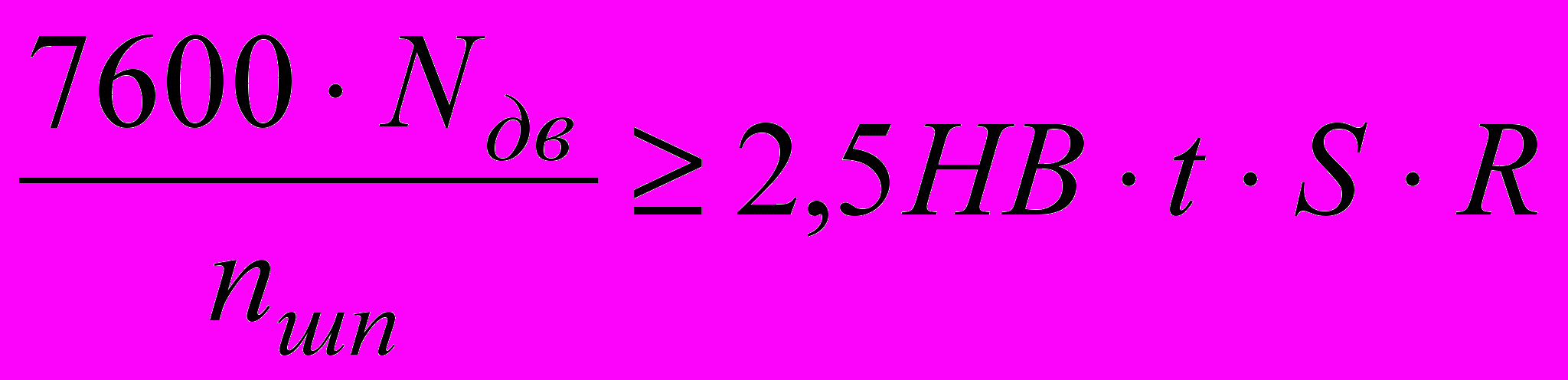
Это уравнение можно представить в виде:

Если момент на шпинделе Мшп не обеспечивает обработку на выбранных в пункте 4 режимах резания Vрез, S и t, то следует их соответствующим образом откорректировать. Например, уменьшить nшп в 2 раза, при этом Мшп повысится в 2 раза (3), либо, если необходимо, выбрать станок требуемой мощности.
6. Определение трудоемкости изготовления
детали
Трудоемкость изготовления детали определяется затратами рабочего времени. Штучное время представляет собой затрату рабочего времени, приходящуюся на изготовление одной детали Тшт, мин [5]:
Тшт = Тосн + Твсп + Тдоп, (9)
где Тосн – основное время, затрачиваемое на снятие стружки;
Твсп – вспомогательное время, затрачивается на установку детали, операторскую работу станочника, измерения детали и др.
Тдоп – дополнительное время (перерывы в работе, отдых и др.).
Основное время Тосн для точения и сверления легко рассчитать по известным расчетной длине обработки lр (мм), подаче S (мм/об), числу оборотов шпинделя n (об/мин) и числу проходов (i):
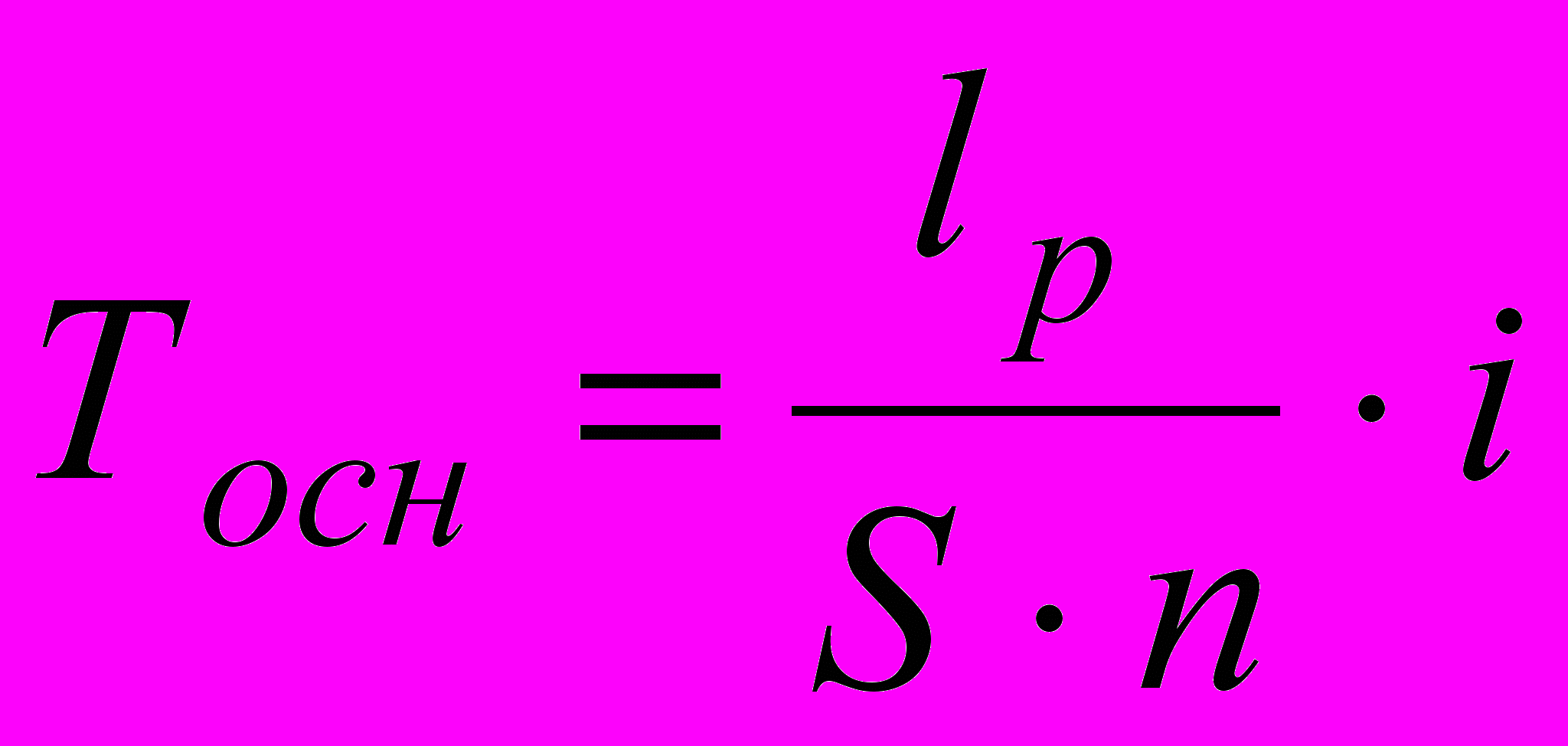
Например, длина точения цилиндра l = 100 мм прибавим путь врезания lвр и путь схода (выхода) lсх по 2 мм [4], получим:
lр = l + lвр + lсх = 104 мм
при S = 0,05 мм /об, n = 500 об/мин, точение в один проход i = 1 получаем:
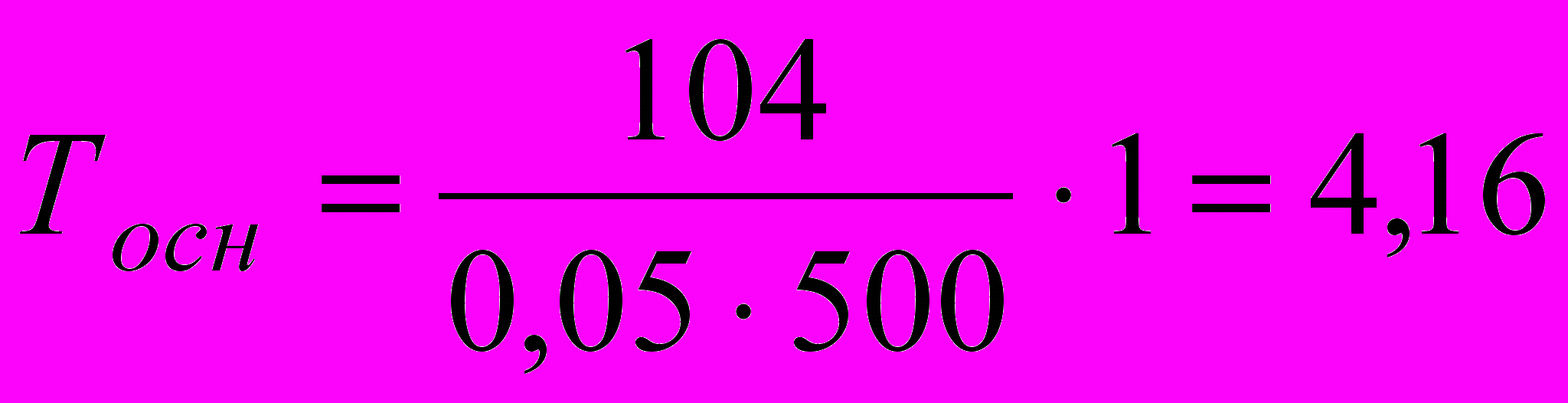
Основное время Тосн для фрезерной обработки рассчитывается по формуле:
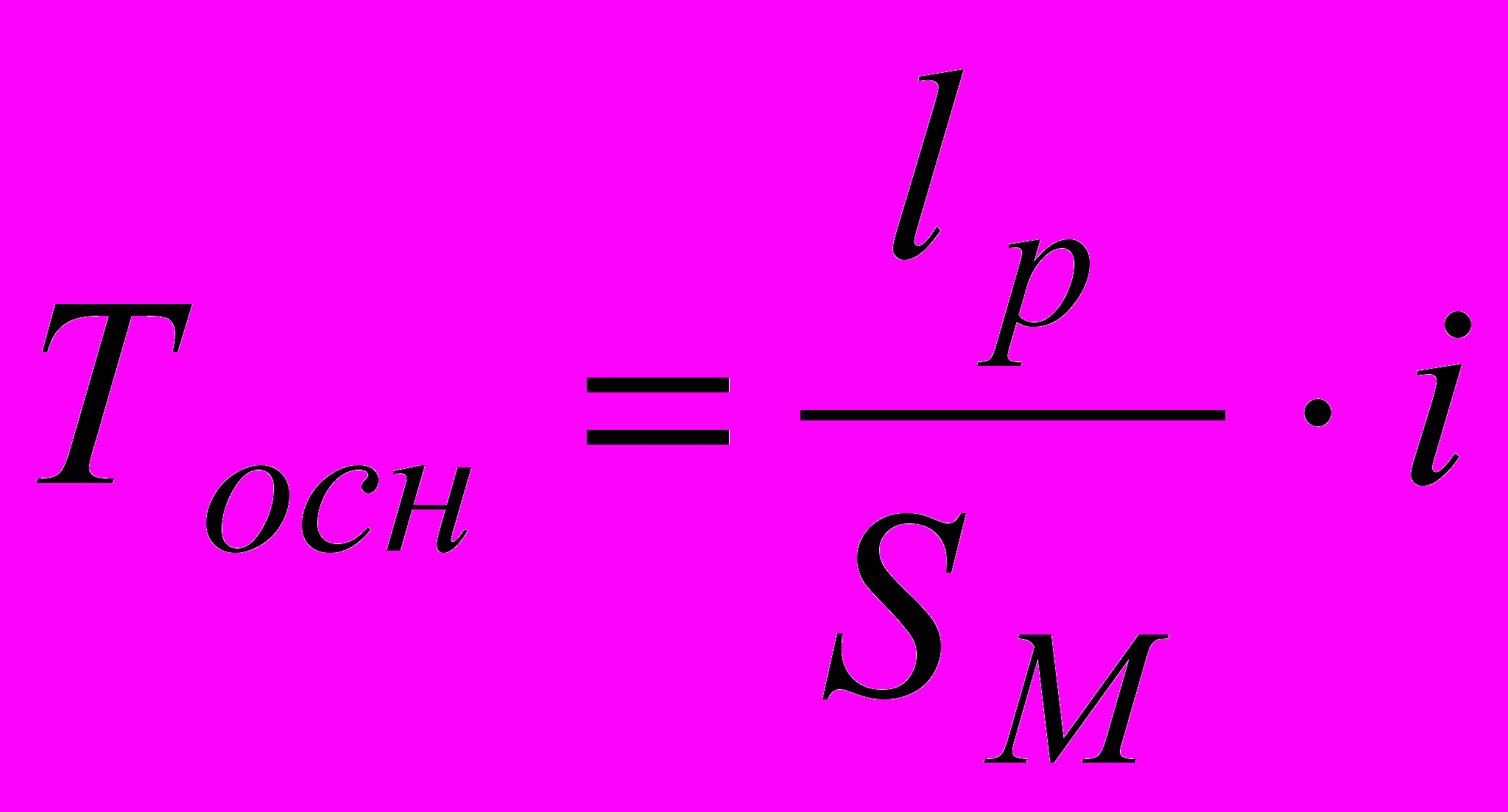
Значение основного времени должно лежать в разумных пределах, например время обработки поверхности длиной lр = 100 мм не может быть 0,01 мин, то есть 0,6 с. При необходимости следует откорректировать режимы резания.
Вспомогательное время Твсп определяется по таблицам, справочникам, хронометражем, или принимается ориентировочно:
Твсп = 0,5∙Тосн; 1∙Тосн или 1,5∙Тосн (12)
При этом значение Твсп на каждом переходе операции механической обработки принимать не менее 15 секунд (например, установка и снятие детали, подвод и отвод инструмента измерение детали и т.п.).
Для термических операций Твсп рекомендуется принимать: для закалки – не менее 3 мин (например, загрузка и вынимание заготовок, перенос до закалочной ванны и т.д.); для отпуска – не менее 2 мин.
Для химико-термической операции – цементации вспомогательное время Твсп принять равным 15 мин.
Дополнительное время Тдоп для операций механической обработки принимается как 10% от оперативного времени (Тосн + Твсп), то есть:
Тдоп = 0,1∙(Тосн + Твсп) (13)
Дополнительное время для термической и химико-термической операции принять Тдоп=0.
7. определение Коэффициент использования металла
Коэффициент использования металла Ким, % определяется как:
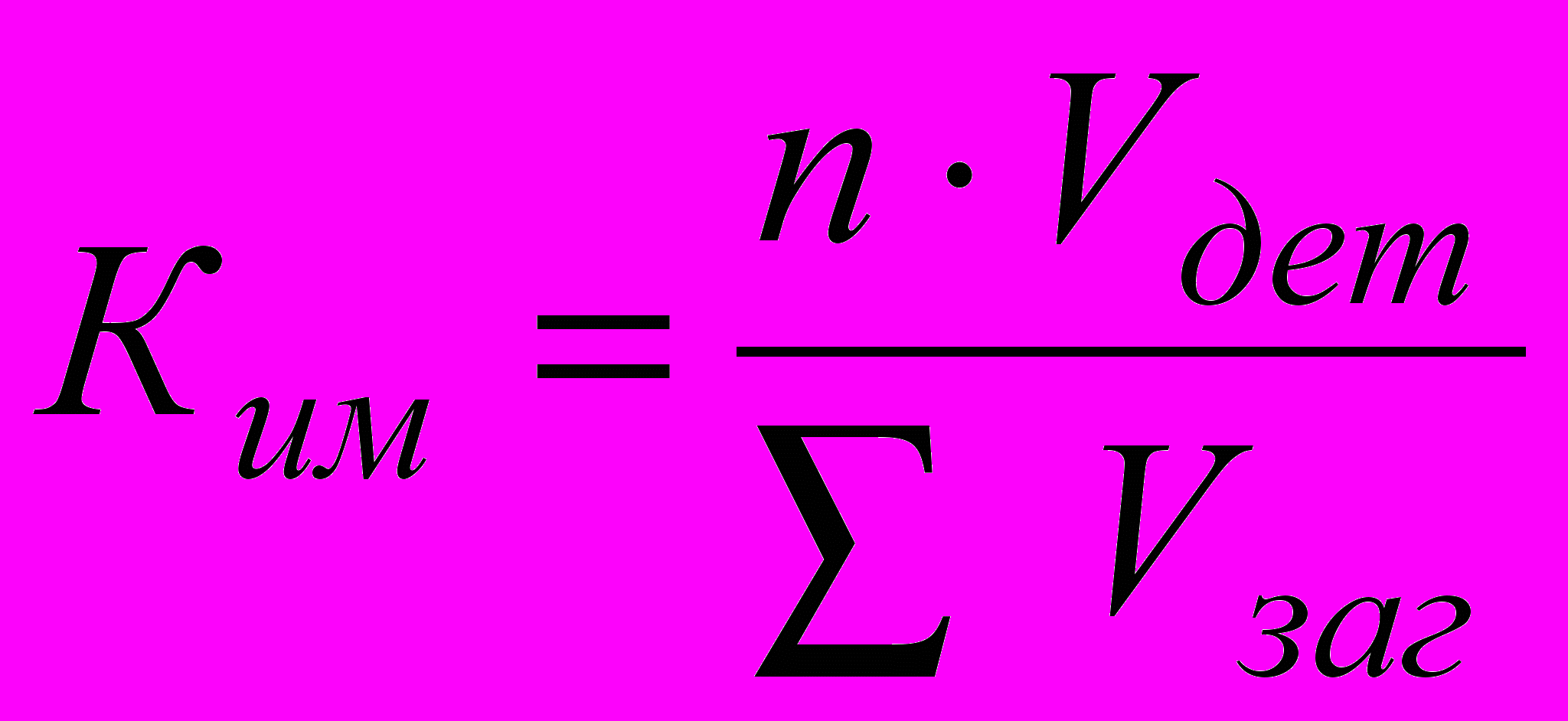
где
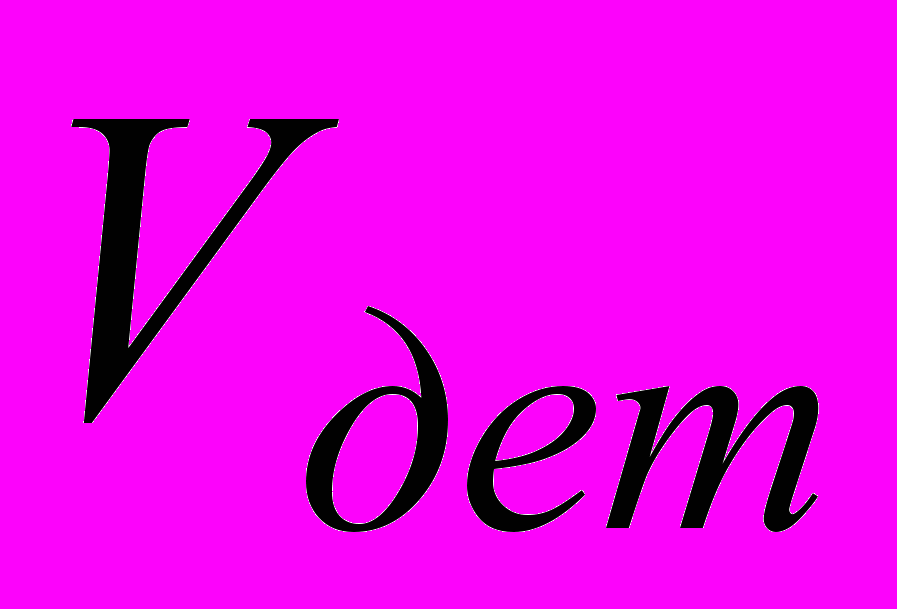
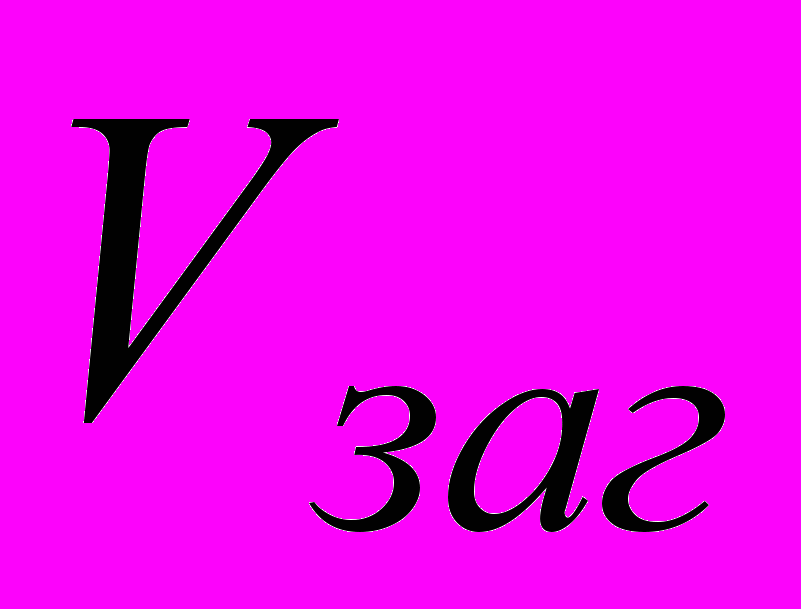
n – число деталей в партии (указано в задании).
Рекомендуемая Литература
1. Анурьев В.И. Справочник конструктора машиностроителя [Текст]: в 3-х т. / Под ред. И. Н. Жестковой. 8-е изд., перераб. и доп. – М.: Машиностроение, 2001. – 1 т. ; – 920 с.: ил.
2. Стали и сплавы. Марочник [Текст]: Справочное издание / В.Г. Сорокин и др. ред. В.Г. Сорокин, М.А. Гервасьев - М.: «Интермет Инжиринг», 2001. – 608 с. : ил.
3. Справочник технолога-машиностроителя [Текст]: в 2-х т. / Под ред. А.Г. Косиловой и Р.К. Мещеряковой. 4-е изд., перераб. и доп. – М.: Машиностроение, 1986. – 496 с., ил.
4. Ягуткин В.А. Технология машиностроения [Текст]: Учебное пособие / В.А. Ягуткин, Б.А. Потехин – Екатеринбург.: УГЛТУ, 2005. - 192 с., ил.
5. Ягуткин В.А. Технология машиностроения [Текст]: Учебно-методическое пособие для студентов спец. 17.04.00; 23.01.00; 55.21.00; 15.02.00, 26.02.00 / В.А. Ягуткин, Б.А. Потехин, Н.К. Джемилев - Екатеринбург, УГЛТУ, 2001. - 60 с., ил.