Конспект лекций «материаловедение»
Вид материала | Конспект |
- Конспект лекций по теме: «Материаловедение» для специальности 120100 "Технология, 104.18kb.
- Конспект лекций по теме: «Материаловедение» для специальности 120100 "Технология, 5022.76kb.
- Е. в конспект лекций «материаловедение» ч. 1 конспект, 33.7kb.
- Конспект лекций «материаловедение», 249.86kb.
- Конспект лекций «материаловедение», 137.13kb.
- Конспект лекций 2008 г. Батычко В. Т. Административное право. Конспект лекций. 2008, 1389.57kb.
- Конспект лекций 2010 г. Батычко Вл. Т. Муниципальное право. Конспект лекций. 2010, 2365.6kb.
- Конспект лекций «материаловедение», 123.26kb.
- Конспект лекций 2011 г. Батычко В. Т. Семейное право. Конспект лекций. 2011, 1718.16kb.
- Конспект лекций 2011 г. Батычко Вл. Т. Конституционное право зарубежных стран. Конспект, 2667.54kb.
© СЗТУ кафедра МТМиП, Шадричев Е.В конспект лекций «МАТЕРИАЛОВЕДЕНИЕ» ч.1
Глава 1. КРИСТАЛЛИЧЕСКОЕ СТРОЕНИЕ И
СВОЙСТВА МЕТАЛЛОВ
1.1. МЕТАЛЛИЧЕСКИИ ТИП СВЯЗИ И КРИСТАЛЛИЧЕСКОЕ СТРОЕНИЕ МЕТАЛЛОВ
Атомы в твердых телах удерживаются прочными межатомными связями. Характер этих связей, их сила определяются электронным строением отдельных атомов, причем главную роль играют электроны, находящиеся на внешних оболочках, - валентные электроны.
Для электронной структуры атомов металлических элементов характерно малое число валентных электронов (1, 2, реже 3). Сила связи электронов с ядром пропорциональна их количеству. Поэтому валентные электроны атомов металлических элементов значительно слабее «привязаны» к ядру, чем в атомах неметаллов, В этом случае объединение отдельных атомов в твердом теле - металле - приводит к обобществлению валентных электронов, образованию электронного газа. Этот газ практически свободно перемещается между ионами, образовавшимися из нейтральных атомов вследствие «потери» ими валентных электронов.1
В такой модели металлический тип связи можно представить, как электростатическое взаимодействие между положительно заряженными ионами и электронным газом, имеющим отрицательный заряд. Следовательно, электронный газ играет роль «цементирующей» прослойки, связывающей между собой одноименно заряженные ионы.
Эти представления позволяют понять характерные для металлов высокие значения электро- и теплопроводности. Действительно, большое количество свободных электронов (примерно 1022 1/см3) обеспечивают эффективный перенос заряда и теплоты в металлах.
Металлический тип связи объясняет и свойственную металлам высокую пластичность. Поскольку атомы (ионы) в этом случае скрепляются нелокализованными свободными электронами, такая связь не имеет определенного направления (в отличие, например, от ковалентной связи), она сферически симметрична. Поэтому пластическое деформирование металла, приводящее к сдвигу атомов (ионов) относительно друг друга, не разрушает связи, не изменяет ее характер. Это и означает высокую пластичность металлов, их способность легко деформироваться в процессе обработки давлением (ковки, штамповки и т. п.).
Особенности металлической связи обусловливают и характер размещения атомов в металле - его кристаллическую структуру.
Понятно, что в коллективе электронов и одноименно заряженных ионов, помимо сил притяжения, действуют и силы отталкивания. Зависимости этих сил от расстояния между ионами различны. На малых расстояниях резко возрастают силы отталкивания (этим объясняется малая сжимаемость твердых тел), с увеличением расстояния они быстро убывают, становятся меньше сил притяжения. Устойчивое положение ионов достигается при некотором расстоянии r=r0 , где эти силы уравновешиваются и результирующая сила F=0.
Это значит, что существуют определенные предпочтительные расстояния между ионами r0, которые отвечают минимуму энергии их взаимодействия Е, т. е. Е/r=Fr=r0 =0 (рис. 1.1).
Из термодинамики известно, что условием стабильности любой системы является минимум ее энергии.
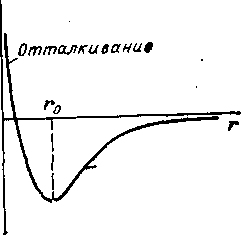
Рис. 1.1. Зависимость энергии взаимодействия E атомов (ионов) в кристалле от расстояния r между ними
В связи с этим атомы в металлах расположены строго упорядоченным образом, на определенных расстояниях друг от друга по различным направлениям. Центры атомов, соединенные системой параллельных линий в трех различных направлениях (х, у, z), образуют пространственную периодическую решетку (рис. 1.2). Видно, что закономерный порядок в расположении атомов в различных направлениях сохраняется на расстояниях, во много раз превышающих расстояния между соседними атомами. Такой порядок называется дальним, а тела, им обладающие, кристаллическими. Большинство материалов в твердом состоянии (металлы, диэлектрики, полупроводники) имеют кристаллическое строение. В отличие от них некристаллическим, аморфным телам присущ лишь ближний порядок, т. е. повторяемость взаимного расположения атомов только в пределах ближайшего окружения данного атома. Примерами некристаллических тел являются жидкости, расплавы, а в твердом состоянии -органические и неорганические стекла и получаемые в особых условиях (см. главу 2) аморфные металлы (металлические стекла).
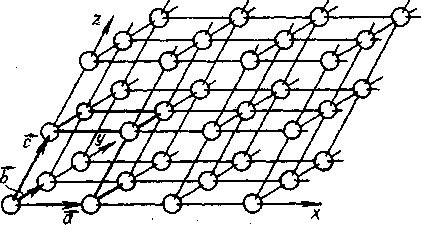
Рис. 1.2. Пространственная периодическая (кристаллическая) решетка
Основное свойство кристаллических решеток - пространственная периодичность. Это означает, что всегда можно выбрать некий элементарный объем в решетке, многократное повторение которого в трех измерениях позволит воспроизвести решетку в целом. Такой минимальный объем, сохраняющий характерные признаки данной решетки, называется элементарной ячейкой и представляет собой в общем случае параллелепипед, построенный на трех векторах а,b,с (рис. 1.2).
Тип кристаллической решетки определяется формой элементарной ячейки и характером расположения в ней атомов.
Количественно кристаллические решетки описываются следующими основными характеристиками:
1. Период (или параметр) решетки - длина векторов, на которых построена элементарная ячейка, или, другими словами, расстояние между центрами соседних атомов, помещенных в узлах элементарной ячейки. Т. е. в общем случае (рис. 1.2) решетка характеризуется тремя параметрами (периодами) - скалярными величинами а, b, с.
Период (и тип) решетки определяется рентгеноструктурным анализом. Величина периода решетки металлических элементов составляет примерно 0,2...0,6 нм (1 нм =10-9 м =10-7 см =10 А).
В
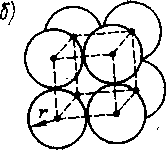
Рис. 1.4. Определение координационного числа и относительной плотности упаковки в простой кубической решетке
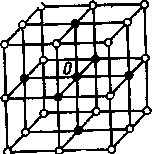
Рис. 1.3. Элементарная ячейка простой кубической решетки (а) и схема упаковки атомов в ней (б)
Для оценки компактности решеток используют две следующие характеристики.
2. Координационное число К - число ближайших атомов, окружающих данный и находящихся от него на одинаковом расстоянии.
3. Относительная плотность упаковки q - отношение объема, занимаемого атомами в элементарной ячейке, к объему самой ячейки.
Для примера определим указанные характеристики в простой кубической решетке (такую решетку имеют, например, кристаллы каменной соли, NаСl). Реальная упаковка атомов радиуса r показана на рис. 1.3. Период такой решётки - это ребро куба а=2r.
Для того чтобы определить значения K и q, т. е. оценить компактность решетки, нужно представить элементарную ячейку как один из кубиков пространственной периодической решетки (рис. 1.4). Легко видеть, что координационное число K в этом случае равно 6 (поэтому простая кубическая решетка в кристаллографии обозначается как K6).
Этот же рисунок поможёт определить и относительную плотность упаковки. По определению (см. выше)
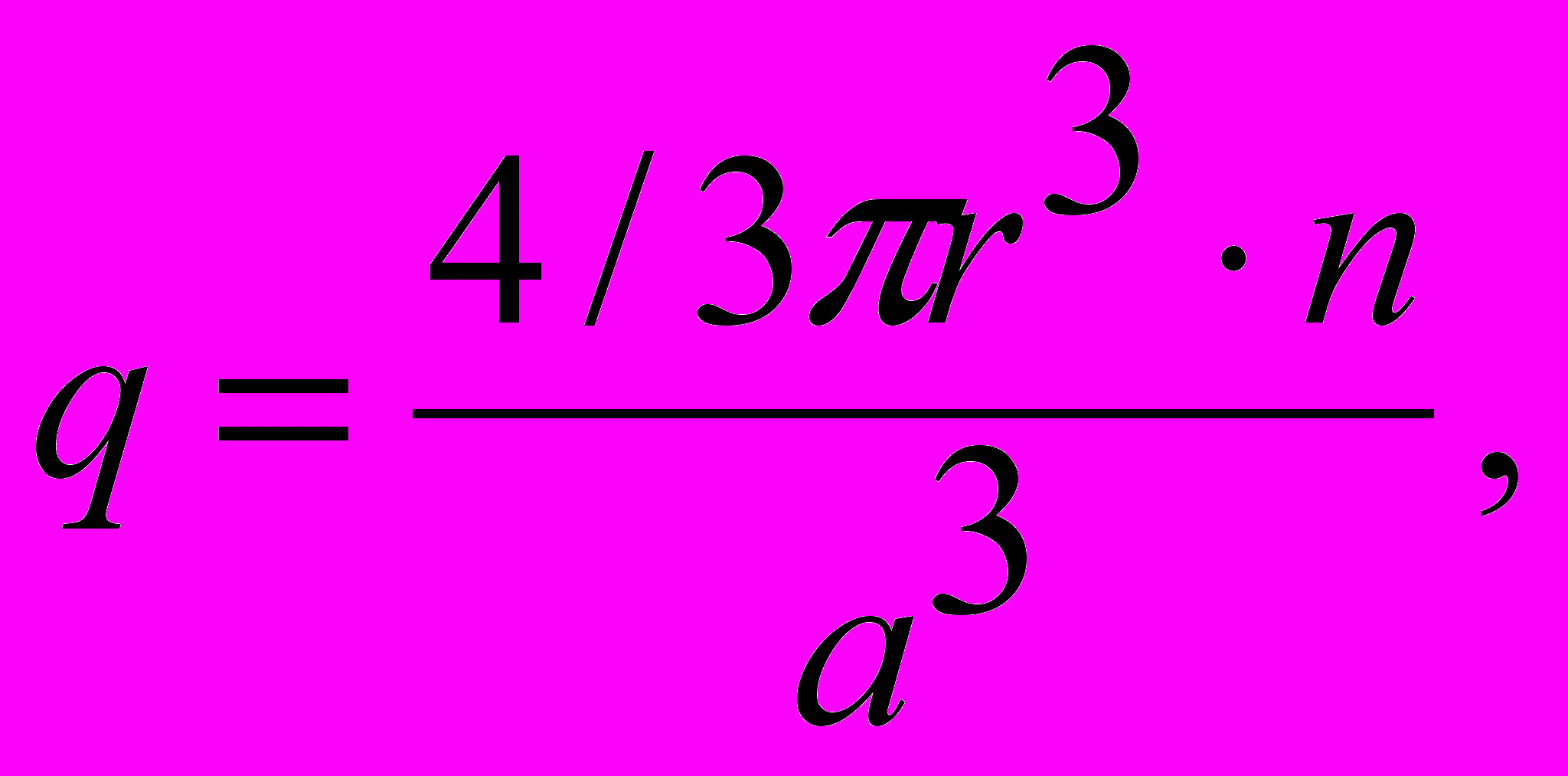
где п - число целых атомов, приходящихся на одну ячейку.
Очевидно, что каждый из 8 атомов, находящихся в вершинах ячейки, принадлежит ей лишь 1/8 своей частью. Поэтому п=1/88=1. Тогда, учитывая, что а=2r, найдем величину q=0,52. Это значит, что простая кубическая решетка «заполнена веществом» примерно наполовину; 48 % ее объема приходится на межатомные пустоты. Такая решетка является «рыхлой».
Металлическим элементам свойственны плотноупакованные решетки с высокой степенью компактности, т. е. с большими значениями К и q. Это является следствием металлического типа связи.
Выше отмечалось, что такая связь, осуществляемая посредством газа свободных (валентных) электронов, является ненаправленной, сферически симметричной. Кроме того, поскольку валентные оболочки атомов в металлах не заполнены, металлическая связь характеризуется ненасыщенностью. В случае ковалентной связи п валентных электронов, обобществляемых соседними атомами, полностью (до 8) застраивают их внешние электронные оболочки. В этой ситуации каждый атом может быть окружен строго ограниченным числом соседей (К) в соответствии с правилом валентности К= 8-п.
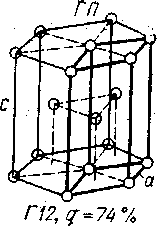
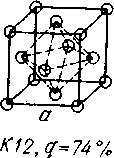
Ненаправленность и ненасыщенность металлической связи приводят к тому, что атомы в металлах стремятся окружить себя максимально возможным числом соседей. Именно поэтому подавляющее большинство металлов кристаллизуется в трех типах решеток, которые характеризуются максимальными координационными числами и наиболее плотными упаковками. Это - объемноцентрированная (ОЦК), гранецентрированная (ГЦК) и гексагональная плотноупакованная (ГП) решетки. Их элементарные ячейки2 и характеристики (они определяются подобно тому, как это делалось выше для простой кубической решетки) приведены на рис. 1.5. Отметим, что значения К=12 и q=74 % являются максимальными для упаковки частиц, представляющих собой упругие шары.
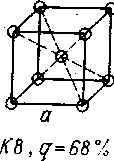
Рис. 1.5. Основные типы кристаллических решеток металлов.
ОЦК - объемноцентрированная кубическая;
ГЦК - гранецентрированная кубическая;
ГП - гексагональная плотноупакованная
1.2. ДЕФЕКТЫ КРИСТАЛЛИЧЕСКОЯ РЕШЕТКИ
(НЕСОВЕРШЕНСТВА КРИСТАЛЛИЧЕСКОГО СТРОЕНИЯ
РЕАЛЬНЫХ МЕТАЛЛОВ)
В реальных металлах всегда существуют отклонения от идеального от порядка в расположении атомов в кристаллической решетке. Эти нарушения называются несовершенствами или дефектами решетки. По геометрическому фактору дефекты решетки можно подразделить на точечные, линейные и
поверхностные. Из дальнейшего будет ясно, что любые дефекты решетки в той или иной мере влияют практически на все свойства кристаллических тел, поэтому имеет смысл рассмотреть их более подробно.
1.2.1. Точечные дефекты
Известно, что атомы в твердом теле находятся в непрерывном колебательном движении, причем амплитуда колебаний возрастает с повышением температуры. В результате неравномерного распределения энергии между атомами отдельные, наиболее «энергичные» атомы могут покинуть узлы решетки. Оставшийся пустым узел решетки является ее дефектом - вакансией.
Если вакансия образуется внутри кристалла, то одновременно с ней появляется другой точечный дефект - дислоцированный атом (атом в междоузлии). Перечисленные дефекты есть в любой решетке, так как обычная причина их появления - тепловое движение атомов. С повышением температуры число этих дефектов растет по экспоненциальному закону. К резкому увеличению этих дефектов может привести также пластическая деформация металла и облучение его частицами высоких энергий (нейтронов).
Далее следует сказать, что металлы, даже специально очищаемые от примесей, никогда не бывают свободными от чужеродных атомов. Эти атомы, размещаемые либо в узлах решетки (в вакансиях), либо (при небольших размерах) в междоузельных пустотах, также являются точечными дефектами решетки.
Перечисленные типы дефектов схематически показаны на рис. 1.6.
Вокруг любого такого дефекта возникает локальное искажение решетки радиусом 1-2 межатомных расстояния. В этом смысле рис. 1.6. неточен, более правильно изобразить, например, вакансию следует так, как показано на рис. 1.7,а. При наличии дислоцированных атомов и атомов примесей решетка деформируется в обратном направлении (рис. 1.7,б).
Хотя размеры нарушений вокруг точечных дефектов, невелики, при достаточно большом количестве точечных дефектов они оказывают заметное влияние на свойства металлов. Это проявляется, в частности, в сильном уменьшении электропроводности меди при наличии некоторых примесей.
1.2.2. Линейные дефекты
Линейные дефекты называются дислокациями. Появление дислокаций вызвано наличием в отдельных частях кристалла «лишних» атомных полуплоскостей, называемых также экстраплоскостями. Экстраплоскости образуются в процессе роста кристаллов из расплава или в результате пластической деформации, как это показано на рис. 1.8. Видно, что под действием приложенного усилия Р произошел частичный сдвиг верхней части кристалла относительно нижней - образовалась экстраплоскость. Край (обрыв) экстраплоскости называется краевой дислокацией, она обозначается символом .
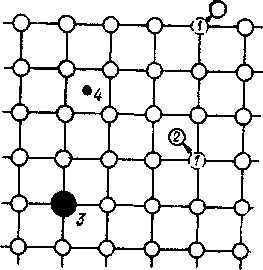
Рис. 1.6. Различные типы точечных дефектов кристаллической решетки.
1 - вакансии;
2 - дислоцированный атом (атом в междоузлии);
3 и 4 - атомы примесей в узле и междоузлии решетки соответственно
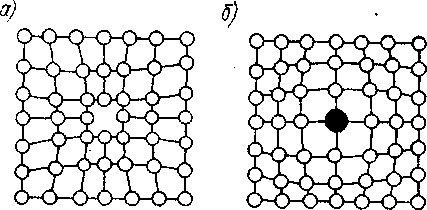
Рис. 1.7. Локальное искажение кристаллической решетки вокруг вакансии (а) и примесного атома в узле решетки (б)
Вокруг линии дислокации dd возникает упругое искажение решетки. Радиус этого искажения невелик - лишь несколько постоянных решетки, протяженность же равна длине линии дислокации, т. е. может составлять сотни тысяч таких расстояний и в пределе достигать размера кристалла. Именно такая геометрия этих искажений решетки позволяет называть дислокации линейными дефектами.
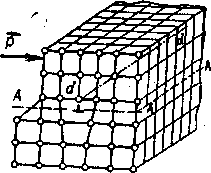
Рис. 1.8. Образование краевой дислокации () в результате частичного сдвига верхней части кристалла под действием усилияР; АА - плоскость скольжения; dd - линия дислокации
Важнейшие механические характеристики металлов - прочность и пластичность - определяются наличием дислокаций, их поведением при нагружении тела. В связи с этим необходимо остановиться на двух особенностях механизма перемещения дислокаций.
1. Если в кристалле (какой-то его части) помимо дислокации отсутствуют другие нарушения в решетке, дислокация может легко передвигаться вдоль плоскости скольжения под действием весьма небольших усилий (рис. 1.9). Такое движение представляет собой последовательность элементарных актов и носит эстафетный характер. В каждом акте экстраплоскость смещает соседний (по ходу движения) слой атомов (расположенных на рис. 1.9 выше плоскости скольжения АА) на одно межатомное расстояние, и сама занимает его место. В результате «старая» экстраплоскость исчезает и появляется смещенная относительно нее новая, т. е. происходит передача «эстафетной палочки» - дислокации на одно межатомное расстояние. Если приложенное усилие достаточно3, этот процесс будет развиваться до тех пор, пока дислокация не выйдет на поверхность кристалла и самоликвидируется. Выход дислокации на поверхность кристалла означает необратимое смещение одной части кристалла относительно другой на одно межатомное расстояние - пластическую деформацию. Поскольку в каждом элементарном акте такого смещения участвуют только атомы слоев, соседних с экстраплоскостью, движение дислокации не требует значительных усилий.
2. В любых, даже самых совершенных металлических кристаллах всегда имеется достаточно большое количество различных дефектов решетки. Вспомним, например, тепловую природу вакансий. В технических металлах уже в процессе их кристаллизации возникает до 106...108 дислокаций в сечении, равном 1 см2.4
Дислокации взаимодействуют друг с другом и другими дефектами решетки, что приводит к ограничению их подвижности.
Если в кристалле много дислокаций, то их скольжение происходит обычно по нескольким системам плоскостей. При пересечении этих плоскостей пересекаются дислокационные линии различных систем скольжения. При этом дислокации блокируют, тормозят друг друга.
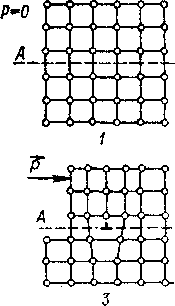

Рис. 1.9. Схема эстафетного перемещения дислокации () вдоль плоскости скольжения (АА) под действием сдвигающего усилия Р
Протяженные пустоты в решетке в месте обрыва экстра плоскости являются удобным местом для стока точечных дефектов. Поэтому вокруг линии дислокации скапливаются атомы примесей. В такой «шубе» примесных атомов дислокация становится малоподвижной.
ПРОПУЩЕНА СТР. 16
тропными (это проявляется, например, в различии механиче-ских свойств вдоль и поперек проката).
На границах зерен периодичность решетки нарушена, так как кристаллографические плоскости повернуты относительно друг друга на угол (рис. 1.10), величина которого колеблется от долей до нескольких десятков градусов. Граница между зернами представляет собой переходный слой шириной до 10 межатомных расстояний, обычно с неупорядоченным расположением атомов. Это место скопления дислокаций, вакансий и примесных атомов.
Отдельные зерна в свою очередь состоят из блоков - субзерен. Субструктура, т. е. структура отдельных зерен, отличается от поликристаллической структуры значительно меньшими величинами размеров субзерен (10-4...10-6 см) и углов их разориентировки (от нескольких секунд до нескольких минут). На границах блоков так же, как и на границах зерен, повышенная концентрация дислокаций и примесных атомов.
Таким образом, границы зерен и границы блоков внутри зерна в трехмерном пространстве являются поверхностными дефектами решетки. Напомним, что, как отмечалось выше, они являются трудно преодолимыми препятствиями для перемещения дислокаций.
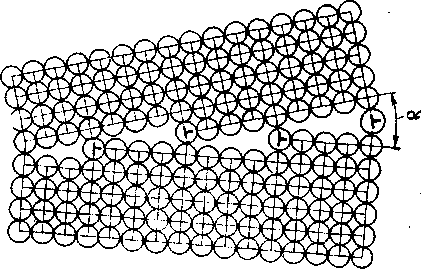
Рис. 1.10. Схема строения границ зерен в поликристаллическом материале
1.3. ВЛИЯНИЕ ДЕФЕКТОВ РЕШЕТКИ НА ПРОЧНОСТЪ МЁТАЛЛОВ. МЕХАНИЗМЫ УПРОЧНЕНИЯ МЕТАЛЛОВ
Прочность - способность материала сопротивляться разрушению или деформации под действием внешней нагрузки - является одной из важнейших механических характеристик материала. С величиной прочности связана работоспособность и материалоемкость изделия.5 Обычно, когда говорят о прочности, имеют в виду прочность на разрыв. Это обусловлено, в частности, наибольшей опасностью растягивающих механических напряжений.
Характеристики прочности в этом случае определяются по результатам механических испытаний образцов при одноосном статическом растяжении. На рис. 1.11 приведена диаграмма напряжений при растяжении стержня с первоначальной длиной l0 и поперечным сечением s0 под действием растягивающей силы Р. Вызываемая напряжением =Р/S0 деформация характеризуется относительным удлинением образца =l/lо (l/lо=l-/lо - абсолютное удлинение).
На начальном участке кривой OА наблюдается прямая пропорциональная зависимость между напряжением и деформацией (закон Гука)
=E. (1.1)
Соответствующая этому участку деформация является упругой, исчезающей при снятии нагрузки. Тангенс угла наклона ОA к оси абсцисс пропорционален модулю упругости (модуль Юнга). Величина Е определяется силами межатомной связи и характеризует жесткость материала - сопротивляемость упругой деформации.
В точке А закон Гука начинает нарушаться; соответствующее напряжение называется пределом пропорциональности пц.
Р
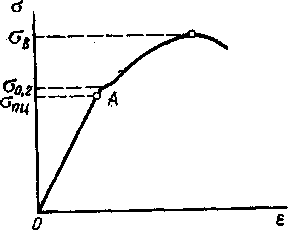
Рис. 1.11. Диаграмма напряжений при одноосном растяжении
Выше точки А деформация не исчезает полностью при снятии нагрузки, такая деформация называется пластической или остаточной. Напряжение, при котором она становится заметной, в технике определяют как условный предел текучести 0,2, так как относительное остаточное удлинение образца составляет при этом 0,2 %.
Максимальное напряжение, которое выдерживает образец до разрыва (точка В на кривой =f()) называется временным сопротивлением или пределом прочности в.
Таким образом, основными критериями прочности при статических нагрузках являются предел текучёсти 0,2 и предел прочности в.6 Предел текучести характеризует сопротивление материала сдвигу, поскольку пластическая деформация осуществляется скольжением атомных слоев решетки относительно друг друга. Предел прочности, строго говоря, - это сопротивление материала отрыву, однако надо иметь в виду, что в пластичных материалах - металлах - отрыву атомных слоев друг от друга всегда предшествует сдвиг, т. е. пластическая деформация.
Суммируя сказанное, можно заключить, что прочность кристаллических тел - это их сопротивление приложенной механической нагрузке, стремящейся сдвинуть (или, в пределе, оторвать) одну часть кристалла относительно другой. Понятно, что эффективность этого сопротивления (т. е. прочность) должна быть пропорциональна величине межатомных сил связи и числу атомов, «сцепление» которых при сдвиге (или отрыве) нужно преодолеть.
Исходя из этого можно рассчитать теоретическую прочность идеального (бездефектного) кристалла (теор) как произведение величины межатомных сил на число атомов, приходящихся на единицу сечения, вдоль которого происходит сдвиг (или отрыв).
Выше отмечалось, что модуль Юнга Е характеризует величину межатомных сил связи, поэтому не удивительно, что теоретическая прочность может быть выражена как теор=kE (1.2)
Расчеты показывают, что почти для всех кристаллических тел величина k0,1, т. е. их идеальная, теоретическая прочность
теор0,1E. (1.3)
По сути это означает (сравним (1.3) с (1.1)), что разрушение происходит при напряжениях, которые вызывают смещение атомов из положения равновесия (узла решетки) на 0,1 величины периода решетки.
Величина модуля Юнга для многих металлов колеблется в пределах (1...2)105 МПа, поэтому их теоретическая прочность должна составлять приблизительно (1...2)104 МПа. Известно, однако, что реальная прочность технических металлов значительно ниже, например, прочность железа всего 200...300 МПа. В чем же причина такого сильного расхождения между значениями теоретической и реальной прочности металлов?
В предыдущем разделе отмечалось, что в любом реальном металле уже в процессе его кристаллизации образуется много дислокаций, их плотность достигает 106...108 1/см2.
В кристалле, содержащем дислокации, под действием нагрузки деформация происходит не путем одновременного сдвига всех атомов вдоль плоскости скольжения,7 а посредством последовательного, эстафетного перемещения дислокаций (см. рис. 1.9). В разделе 1.1.2 обсуждалось, что такой процесс сдвига требует весьма небольших усилий, что и обусловливает снижение сопротивляемости материала пластической деформации, т. е. снижение его прочности.
Из сказанного следует естественный вывод - повышение прочности может быть достигнуто удалением дислокаций из металла. Действительно, опыты, проведенные на бездислокационных образцах, подтвердили высокую, близкую к теоретической, прочность таких материалов. Однако такой путь упрочнения не технологичен, поскольку бездислокационные металлы удается получать лишь в виде тонких нитей (так называемых «усов») диаметром в несколько микрон и длиной до 10 мм.
Поэтому применяемые на практике способы упрочнения основаны на торможении, блокировании подвижных дислокаций. Ранее (раздел 1.2.2) отмечалось, что любые дефекты решетки и, в первую очередь, линейные (дислокации) и поверхностные (границы зерен) оказывают такое тормозящее действие, затрудняют скольжение дислокаций при пластическом деформировании металла. Преодоление создаваемых ими внутренних упругих напряжений требует увеличения прилагаемых усилий деформирования, что и означает повышение прочности.
Подобным упрочняющим действием обладают микрообласти упругих искажений решетки различной природы, а также дисперсные частицы твердых дополнительных фаз, как бы заклинивающих плоскости скольжения, блокирующих дислокации.
Традиционными практическими методами упрочнения металлов являются: обработка давлением, термическая обработка, химико-термическая обработка, создание сплавов, легирование. Эти процессы и их влияние на прочность будут рассмотрены в последующих разделах. Здесь же в качестве иллюстрации влияния различных методов упрочнения приведен рис. 1.12, на котором показано, как путем регулирования плотности дислокаций р можно существенно изменять прочность металла в. На этом же рисунке для примера указана прочность железа (и стали — сплава на основе железа) в различных отмеченных на зависимости в=f(р) состояниях. Видно, что применяемые в настоящее время способы упрочнения далеко не реализуют природную прочность железа.
В заключение этого раздела можно сказать, что представления о дислокационном механизме сдвига достаточно хорошо объясняют поведение пластичных металлов при механическом нагружении. Однако этих представлений оказывается недостаточно для понимания часто наблюдаемой пониженной прочности изделий, в которых использован металл с невысокой пластичностью. Пониженная прочность таких изделий объясняется наличием в них поверхностных или внутренних дефектов типа микротрещин. Помимо деформационных и термических трещин, роль таких дефектов могут играть частицы неметаллических включений, поры или «конструктивные дефекты» типа надрезов: выточки, галтели, отверстия.
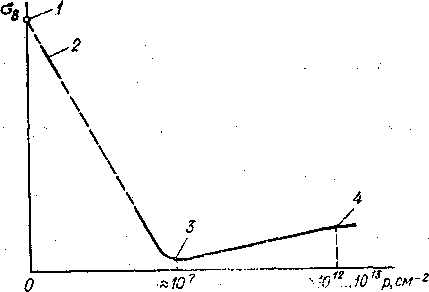
1 - идеальный, бездефектный металл - расчет (20000); 2 - бездислокационный, «усы» (13000);
3 - технический, не упрочненный (300); 4 - упрочненный методами, основанными на торможении дислокаций (3000); термически упрочненная сталь - сплав на основе железа)
Приложение растягивающего усилия Р к такому изделию приводит к концентрации внутренних напряжений ( = Р/S) около вершины микротрещины (рис. 1.13.). Величина этих напряжений к зависит от глубины трещины l и радиуса кривизны в ее вершине r:
к = 2l/r (1.4)
Видно, что при наличии протяженной или острой микротрещины напряжение в ее вершине к может значительно превышать среднее, номинальное напряжение по сечению образца =Р/S.
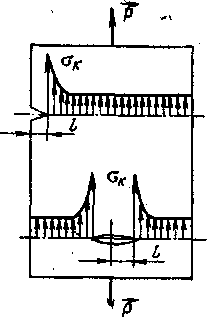
Рис. 1.13. Концентрация напряжений в образце с дефектами типа трещин
В пластичных металлах пластическая деформация, возникающая в вершине трещины, сопровождается увеличением радиуса ее кривизны r, что приводит к уменьшению концентрации напряжений, согласно формуле (1.4). В таких материалах указанные дефекты обычно не представляют большой опасности.
В хрупких материалах радиус вершины трещины может быть очень мал (в пределе соизмерим с атомным радиусом). В этом случае к в формуле (1.4) может возрасти до очень больших значений, превышающих предел прочности материала в. В результате произойдет локальное разрушение материала в вершине трещины, т. е. увеличение l и, следовательно, дальнейшее возрастание к. Этот процесс приводит к катастрофическому разрушению, скорость которого близка к скорости распространения упругих волн в твердом теле (скорость звука).
Такое поведение хрупких материалов существенно осложняет проблему создания и применения высокопрочных сплавов. Легкость скольжения дислокаций в чистых металлах обусловливает их низкую прочность, но и высокую пластичность, так как пластическая деформация осуществляется путем скольжения дислокаций. Поэтому упрочнение металлов, основанное на торможении дислокаций, приводит к снижению пластичности. В результате уменьшается надежность упрочненного материала, так как он становится чувствительным к различного рода дефектам типа микротрещин. В связи с этим материал в зависимости от назначения и условий эксплуатации конкретного изделия должен обладать оптимальным сочетанием прочности и пластичности.
Таким образом, представления о дислокациях, рассмотренные в этом разделе, объясняют особенности поведения металлов при нагружении, их механические свойства — прочность и пластичность. На этих представлениях основаны практические методы упрочнения металлов, которые будут обсуждены ниже.
1 Реально в металле происходит обобществление валентных электронов, а не потеря (или приобретение) их атомами, как в веществах с ионным типом связи. Поэтому более правильно здесь говорить не об ионах, а атомных остатках - атомах за вычетом валентных электронов. Тем не менее при качественном рассмотрении межатомной связи в металлах для наглядности пользуются представлением об ионах. Такое упрощение оправдано тем, что атомные остатки, как и ионы, имеют положительный заряд.
2 Элементарные ячейки решеток могут выбираться различными способами. В частности, элементарной ячейкой ГП решетки по сути является параллелепипед, в основании которого ромб с углом 120° (на рис. 1.5 показан сплошными линиями). Однако обычно принято изображать ячейки так, чтобы они наилучшим образом отражали симметрию данного типа решетки. Этот принцип использован и на рис. 1.5.
3 Из курса сопротивления материалов известно, что пластическая деформация реализуется, если при приложении нагрузки Р в сечении S возникает напряжение = P/S, превышающее предел текучести (см. ниже разд. 1.3).
4 Плотность дислокаций р определяется длиной их линий, приходящейся на единицу объема [см/см3], или числом линий дислокаций, пересекающих площадку в 1 см2
5 Работоспособность материала в конкретном изделии (конструкции) в реальных условиях эксплуатации оценивается комплексной характеристикой, называемой конструкционной прочностью. Обсуждаемые в данном разделе критерии прочности являются важнейшими среди параметров, характеризующих конструкционную прочность.
6 На практике широко применяются измерения твердости материалов. Твердость — способность материала сопротивляться деформации (при внедрении в него более твердого тела) - является, по сути, также характеристикой прочности. Поэтому для пластичных материалов между величинами прочности в и твердости НВ (твердость по Бринеллю) существует линейная связь в=kНВ, где коэффициент k для различных материалов изменяется обычно в пределах 0,2...0,4.
7 В идеальном - бездислокационном кристалле, единственно возможный механизм деформации - это одновременный сдвиг всех атомов одной плоскости относительно другой. Эта модель и используется в расчете теоретической прочности.