Комплексное извлечение попутных элементов из сырья металлургических предприятий урала
Вид материала | Автореферат диссертации |
- Темы: Коррозия металлов. Современные методы защиты металлов от коррозии. Основные виды, 135.67kb.
- Разработка методики расчета и рекомендаций по повышению остаточных напряжений в сетях, 645.83kb.
- Экономический рост и проблемы экологии в Республике, 387.29kb.
- Физико-химические и технологические основы повышения эффективности комплексной переработки, 851.1kb.
- Организация переработки мяса в сельскохозяйственных потребительских кооперативах характеристика, 1223.51kb.
- Рекомендовано Минобразованием России для направления подготовки диплом, 100.07kb.
- Дипломного проекта, 326.25kb.
- Общественное питание классификация предприятий извлечение гост р 50762-95 Дата введения, 214.07kb.
- Науки, Академика, Героя Социалистического Труда, дважды лауреата Государственной премии, 67.96kb.
- Во пылей, которые необходимо улавливать и утилизировать с целью извлечения содержащихся, 59.29kb.
промышленного ≥ 110 Zn; ≤ 0,003 Cu;
антисептика ≤ 0,01 As; рН 4-4,2;
< 0,0001 Tartrat; < 0,0001 ЦПБ
Рис.3 Технологическая схема переработки тонких и грубых
металлургических пылей медеплавильного производства
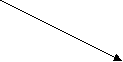
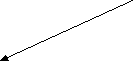
(

0,01 In; 0,7 As; 0,015 In; 0,9 As;
26,6 Pb; 21,6 Zn; 0,6 Сu 32,5 Pb; 25,1 Zn; 0,9 Сu






Двухстадийное выщелачивание
(25-30 г/дм3 [H2SO4]равн.; 338-343 К; 2 час)

Фильтрация пульпы





П




Промвода Кек (2 класс опасности),%:






Селективная сорбция индия
(333-343 К; Vр-ра/час =Vсмолы )






(3% ГМФ)
Гидролитическая очистка от As Десорбция индия
(343-353 К; рН 4-4,5; 8 час) (333-343 К; 0,5Vр-ра/час =Vсмолы)






Фильтрация Осаждение и флотация (фильтрация) сублат-соли индия




Ш

<

0,4 Pb; 4,9 Zn; 0,1 Сu

Н

промышленного индия
антисептика
Товарный раствор ZnSO4, г/дм3:
≥ 110 Zn; ≤ 0,001 Cu; ≤ 0,01
As; < 0,001 In; < 0,001 ГМФ;
< 0,0001 ЦПБ; рН 4-4,2
Рис.4 Технологическая схема переработки конверторных пылей и
возгонов медеплавильного производства
Разработана технологическая схема переработки металлургических пылей и возгонов медеплавильного производства (рис.3), предусматривающая:
двухстадийное выщелачивание серной кислотой; селективное осаждение из фильтратов выщелачивания тартратных комплексов германия галогенидами четвертичных аммониевых или пиридиниевых оснований, например, цетилпиридиний бромидом (ЦПБ) при молярном отношении Ge:винная кислота:ЦПБ = = 1:2:3, с последующей флотацией или фильтрацией осадка; гидролитическая очистка раствора от меди и мышьяка. Регулятором флотации служил бутиловый ксантогенат, рекуперированный при утилизации кубовых остатков производства ксантогенатов. Продуктами предложенной технологии являются: медьсодержащий кек выщелачивания, утилизируемый в производстве черновой меди, первичный германийсодержащий концентрат – сырье для получения металла высокой чистоты, раствор сульфата цинка – флотореагент, используемый при обогащении медно-цинковых концентратов, мышьяксодержащий шлам гидролитической очистки растворов, поступающий на получение соединений арсенатов – главного компонента промышленного антисептика «Элемсепт» ТУ 2157-107-00194429-2007.
Основные технологические операции при переработке конверторных пылей и возгонов: двухстадийное выщелачивание серной кислотой; селективная сорбция индия из фильтратов выщелачивания на ионитах КФП-12 или КФ-7 с последующим элюированием индия 3 %-ным раствором гексаметафосфата натрия (ГМФ); осаждение индия из элюата 8,5 %-ным раствором ЦПБ при молярном отношении In : ГМФ : ЦПБ = 1:1:3; выделение осадка из раствора флотацией или фильтрацией; гидролитическая очистка растворов от As (рис.4).
Оценка величины предотвращенного экологического ущерба (ПУпро) от
сокращения площадей промышленных отвалов, вовлекаемых в переработку, проведена по формуле:
ПУпро = УудроКфгпΣk=1к(mпkросКоkр), руб/год, (5)
где Уудро = НсSКэп/Мр - показатель удельного ущерба окружающей природной
среде от размещения 1 т отходов производства 5 класса опасности (1 условной тонны для всех отходов), руб./усл.т; Нс - средняя по региону кадастровая стоимость сельскохозяйственной земли, руб/га; S – площадь мест организованного
размещения отходов производства всех классов опасности, га; Кэп – коэффици-
ент экологической ситуации и значимости состояния почв; Мр - суммарная масса отходов, накопленных в данном регионе на конец года, усл. т; Кфгп - фоновый коэффициент экологической ситуации и экологической значимости состояния почвы в r-ом муниципальном образовании, где расположена свалка отходов (Кфгп =2,5 для УрФО, уровень загрязнения почвы Zc ≥ 32); mпkрос - масса санкционированного размещения на предприятии отходов производства k-ого класса опасности, т; Коkр - коэффициент, учитывающий относительную опасность k-ого класса отходов (табл.11).
При значениях: Нс =21400 руб/га, S = 9332,6 га, Кэп =1,7, Мр = 568937000 усл.т, определены величины Уудро = 0,6 руб/усл.т и ПУпро = 0,82 млн.руб/год,
что подтверждено расчетами Института экономики УрО РАН.
Таблица 11 - Исходные данные для расчета величины предотвращенного экологического ущерба ПУпро
Перерабатываемые отходы | Масса отхода (mпkрос), т/год | Класс опасности | Коkр | Приведенная масса отходов (Мотх),усл.т/год |
Шламы очистки сточных вод | 470 | 3 | 33 | 15510 |
Металлургические пыли | 5250 | 2 | 50 | 262500 |
Конверторные пыли | 5000 | 2 | 50 | 250000 |
Гипсогидратные кеки | 1000 | 2 | 50 | 50000 |
Золы-уносы от сжигания углей | 500 | 4 | 17 | 8500 |
Всего | 12220 | | | 586510 |
Итого с ![]() | | 1366275 |
В четвертой главе приведены результаты исследований по созданию гидрометаллургической технологии комплексной переработки анодных остатков электролитического рафинирования чернового алюминия с рекуперацией меди, алюминия, железа, галлия. Дано термодинамическое обоснование принципа подбора поверхностно-активных веществ для процесса ионной флотации коллигендов. Экспериментально определены исходные данные для расчета величины адсорбционно-сольватного фактора устойчивости дисперсных систем.
Анодные остатки, соcтава, %: 19-27 Al; 0,15-0,22 Ga; 15-21 Cu; 5-12 Fe, содержат оксидную и металлизированную фракции в соотношении (4-5):1, которые предложено выщелачивать в кислотных (H2SO4=0,04-0,23 моль/дм3) и
смешанных кислотно-солевых растворителях (H2SO4/CuSO4=0,02-0,4/0,04-0,23 моль/дм3) при Ж:Т = (3-10):1. В условиях, исключающих внешнедиффузионное сопротивление (mо(Al) = 3,73 г; mo(Ga) = 0,03 г; S = 0,83 дм2; V = 1 дм3), исследовано влияние концентрации кислоты и температуры пульпы на величину удельной скорости (ω, дм/об0,5·с0,5), коэффициент диффузии (D, дм2/с) и энергию активации растворения металлизированной фракции. Установлено, что выщелачивание кислотным растворителем протекает в кинетической области: значения коэффициента (b = Δln(Cо-Cτ)/Δτ, с-1) удельной скорости растворения возрастают в интервале (0,91-1,3).10-4 с-1; Еакт = 31-35 кДж/моль (табл.12).
Определены основные параметры технологии и аппаратов для цементационного выщелачивания металлизированной фракции анодных остатков (масса/объем фракции mф/vф = 2,5т /0,93 м3; ρ =2,7 г/см3; ΣAl,Ga = 0,82 т; d = 0,3 дм; Т:Ж=1:10; H2SO4 / CuSO4 = 0,21/ 0,23 моль/дм3; ω =3,2.10-4 дм/об0,5.с0,5: продолжительность выщелачивания τв = [lnCo- ln(Co-Cτ)]V/ωSn0,5 = 8,3 час; объем пульпы vп = vф+vр-ра= 26 м3; объем реактора 32,5 м3, при коэффициенте заполнения 0,8 (Н/d = 2,5; dр = 2,55 м; Нр = 6,38 м).
Исследовано влияние концентрации кислоты и температуры пульпы на процесс растворения оксидной фракции при условиях: mо(Al) = 14,9 г; mo(Ga )= 0,1 г; V =1 дм3; S = 4,1 дм2; n = 9 с-1; Т = 323-363 К (табл.13).
Таблица 12 – Параметры процесса растворения металлизированной фракции
[H2SO4], моль/дм3 | [CuSO4], моль/дм3 | H2SO4 /CuSO4/ (Al+Ga ) | b.104, с-1 | ω.106, дм/об0,5·с0,5 | Еакт, кДж/М |
0,046 | 0 | 0,33/0/1 | 0,91 | 0,84 | 35 |
0,092 | 0,66/0/1 | 1 | 0,92 | 34,3 | |
0,14 | 0,99/0/1 | 1,12 | 1,03 | 33,2 | |
0,18 | 1,31/0/1 | 1,21 | 1,11 | 32,1 | |
0,23 | 1,64/0/1 | 1,3 | 1,2 | 31 | |
| D.105, дм2/с | | |||
0,02 | 0,23 | 0,15/1,65/1 | 5,52 | 1,32 | 13,3 |
0,04 | 0,3/1,65/1 | 8,69 | 1,78 | 11,9 | |
0,07 | 0,53/1,65/1 | 14,28 | 2,48 | 10,7 | |
0,11 | 0,75/1,65/1 | 20,71 | 3,18 | 8,5 | |
0,21 | 1,5/1,65/1 | 20,93 | 3,2 | ||
0,25 | 0,19 | 1,78/1,38/1 | 17,03 | 2,79 | 12,3 |
0,29 | 0,15 | 2,05/1,1/1 | 13,3 | 2,37 | 16,7 |
0,33 | 0,12 | 2,33/0,83/1 | 9,79 | 1,93 | 20,6 |
0,36 | 0,08 | 2,6/0,55/1 | 6,82 | 1,52 | 24,1 |
0,4 | 0,04 | 2,88/0,28/1 | 4,07 | 1,08 | 27,9 |
Таблица 13 – Параметры процесса растворения оксидной фракции
[H2SO4], моль/дм3 | [H2SO4]/ [(Al+Ga)] | b.104, с-1 | ω.106, дм/об0,5·с0,5 | Еакт, кДж/моль |
0,18 | 0,33 | 7,55 | 1,39 | 14,3 |
0,37 | 0,66 | 13,55 | 2,5 | 18,1 |
0,55 | 0,99 | 19,17 | 3,53 | 22,3 |
0,74 | 1,32 | 23,3 | 4,29 | 26 |
0,92 | 1,65 | 24,71 | 4,55 | 29,7 |
1,29 | 2,31 | 19,93 | 3,67 | 31,1 |
1,84 | 3,31 | 15,25 | 2,81 | 33,2 |
В слабокислых растворах (H2SO4 ≤ 0,18 моль/дм3) процесс протекает в
диффузионной области (Еакт. < 14 кДж/моль или < 5,7 kТ). В интервале концентраций серной кислоты (0,18-0,92) моль/дм3 выщелачивание протекает в переходной области: при возрастании концентрации кислоты скорость растворения оксидной фракции увеличивается и лимитируется лишь диффузией растворителя, Еакт = 14,3-29,7 кДж/моль (5,8-12 kТ). В области концентрированных растворов (H2SO4 > 1 моль/дм3) скорость выщелачивания оксидной фракции снижается из-за уменьшения растворимости сульфата алюминия и лимитируется диффузией продуктов реакции, Еакт.= 31,1-33,2 кДж/моль (12,6-13,4 kТ).
Определены основные технологии и размеры аппаратов для выщелачивания оксидной фракции анодных остатков (масса / объем фракции
mф / vф = 7,5 т/1,92 м3; ρ = 3,9 г/см3; Σ(Al,Ga)2О3 = 3,04 т; dчас = 0,015 дм;
Т:Ж = 1:6; H2SO4 = 0,9 моль/дм3; ω = 4,55.10-4 дм/об0,5.с0,5): продолжительность выщелачивания τв = [lnCo- ln(Co-Cτ)]V/ωSn0,5 = 0,4 час; общий объем пульпы
47 м3; объем реактора 30 м3, при коэффициенте заполнения 0,8 и двух циклах выщелачивания (Н/d = 2,5; dр = 2,5 м; Нр = 6,25 м).
Раздельное выщелачивание при оптимальных условиях металлизированной и оксидной фракций позволило минимизировать продолжительность процесса переработки анодных остатков.
Селективная сорбция галлия из растворов, получаемых при выщелачивании анодных остатков на хелатообразующих аминокарбоксильных и фосфорнокислых смолах (КБ-2; АНКБ-(2-50); r = 0,05 см; v = 9 с-1) лимитируется химической кинетикой - на показатели процесса влияют природа, степень ионизации и место расположения в матрице ионногенных групп смолы, а также степень гидратации и способность к комплексообразованию сорбирующихся
ионов (табл.14).
Таблица 14 – Показатели сорбции галлия при химической кинетике
Ионит | [Ga], г-ат/дм3 | [H2SO4], М | *)В·104,с-1 | *)t0,5·10-4,c | Еакт.,кДж/М |
КБ-2 | 0,033 | рН = 3,0-3,3 | 0,084 | 3,521 | 32,7 |
АНКБ-35 | 0,033 | 0,067 | 4,414 | 38,7 | |
АНКБ-10 | 0,033 | 0,089 | 3,323 | 33,3 | |
АНКБ-50 | 0,056 | 5,282 | 42,6 | ||
АНКБ-2 | 0,8-1 | 0,049 | 6,039 | 49,8 | |
КФП-12 | 0,2-0,25 | 0,073 | 4,052 | 36,8 | |
АНКБ-35 | 0,04 | рН = 3,0-3,3 | 0,069 | 4,286 | - |
0,035 | 0,051 | 5,80 | |||
0,03 | 0,038 | 7,784 | |||
0,025 | 0,026 | 11,38 | |||
0,033 | 0,1-0,15 | 0,055 | 5,376 | 34 |
*) температура раствора 293 К
При сорбции на карбоксильном катионите КБ-2 катионы галлия, наряду с ионной связью, способны образовывать и ковалентную связь – значения В = 8,4.10-6 с-1, Еакт = 32,7 кДж/моль (13,2 kТ).
Аминокарбоксильные амфолиты АНКБ содержат аминоуксусные и ами-
нодиуксусные группировки, вследствие чего, доля ковалентной связи, по срав-
нению с КБ-2, ещё более возрастает и становится определяющей, что характе-
ризуется снижением константы скорости (В, с-1) и увеличением энергии акти-
вации. процесса (для АНКБ-35: В = 6,7.10-6 с-1, Еакт. = 38,7 кДж/моль (15,6 kT).
При возрастании доли аминодиуксусных группировок с 0,33 до 1 и степени комплексообразования функциональных групп ионитов с ионами металлов в ряду от АНКБ-10 к АНКБ-50 константа скорости В снижается: с 8,9.10-6 до 5,6.10-6 с-1, а Еакт. увеличивается с 33,3 до 42,6 кДж/моль (13,5-17,2 kT).
У смолы АНКБ-2, в отличие от других исследованных аминокарбоксильных амфолитов, аминная группа входит в состав бензольного кольца, что значительно усиливает её свойства как акцептора протонов и способность к образованию координационных связей с сорбируемыми ионами металлов - значение В снижается до 4,9·10-6 с-1, Еакт. возрастает до 49,8 кДж/моль (20,1 kT).
При увеличении степени ионизации фосфорнокислых групп до рКн = 2,15 (КФП-12) по сравнению с рКн = 4 для карбоксильных групп (КБ-2, АНКБ-
(10-50), расширяется рабочий кислотный диапазон смол до 20-25 г/дм3 H2SO4.
При сорбции на хелатообразующих ионитах с увеличением исходной концентрации галлия значения B возрастают, порядок реакции равняется n = 2, выявлено наличие линейной зависимости в координатах «lg(dF/dt)–lgCo».
Набухаемость (ρ) амфолита АНКБ-35 в кислых растворах (H2SO4 >
0,05 моль/дм3) снижается с 1,3 до 1,05 см3/г, усиливается влияние гелевой кинетики и сорбция протекает в переходной области: величина Еакт. уменьшается до 34 кДж/моль (13,7 kT).
Технологическая схема переработки анодных остатков электролитического рафинирования чернового алюминия (рис.5), предусматривает следующие основные операции: дробление и грохочение - для разделения металлизированной (+2 мм) и оксидной (-2 мм) фракций; цементационное растворение металлизированной фракции в кислотно-солевом растворителе; кислотное выщелачивание оксидной фракции; селективную сорбцию галлия из объединённых растворов выщелачивания на амфолите АНКБ-35 с последующим элюированием галлия раствором 1,3 моль/дм3 H2SO4 и осаждением гидроксидов галлия и железа.
Продуктами предложенной технологии являются: медьсодержащий кек и шлам нейтрализации растворов выщелачивания, утилизируемые в медеплавильном производстве; первичный галлийсодержащий концентрат; смешанный железо-алюминийсодержащий коагулянт, используемый при очистке промышленных сточных вод, а также в производстве защитных покровных материалов на основе отходов обогащения минеральных волокон хризотил-асбеста.
При термодинамическом обосновании подбора ПАВ (собирателей) для ионной флотации компонентов раствора (коллигендов) рассмотрены два варианта протекания процесса:
- пенная сепарация (фракционирование), когда извлекаемые ионы не образуют с собирателями малорастворимого соединения (сублата) и адсорбируются на подвижной границе «жидкость-газ», активированной поверхностно-активными ионами (ПАИ) собирателя;
- пеночная (плёночная) флотация, когда ПАИ входит в состав сублата, являясь одновременно осадителем и собирателем извлекаемых ионов.
Второй вариант характеризуется высокими значениями скорости флотации и коэффициента концентрирования коллигенда (γ = [Ме]пен/[Ме]р-р).
Величина произведения растворимости (ПР) образующегося сублата связана с изменением свободной энергии Гиббса (∆Gобр) реакции:
∆Gобр. = - R∙T∙lnПР (6)







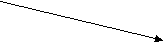
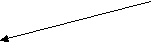



К




К



Промывка (рН = 5-7) Нейтрализация

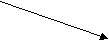

Т=318-323 К τ = 5 час


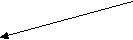








(30 кг/м3)
Селективная сорбция галлия

















Получение металлического галлия
Сухой остаток, %:


Рис.5 Технологическая схема переработки анодных остатков
электролитического рафинирования чернового алюминия
Согласно принципу аддитивности вкладов, ∆Gобр. сублата складывается из изменения свободной энергии, имеющего место в результате перехода в состав сублата углеводородного радикала собирателя (∆GR), ПАИ собирателя (∆GP) и иона коллигенда (∆GK):
∆Gобр. = zP(∆GR ±∆GP) ± zK(∆GK), (7)
ПР = ехр[zP(∆GR±∆GP) ± zK(∆GK)]/RT, (8)
где zP и zK – стехиометрические количества ионов собирателя и коллигенда, необходимые для образования сублата.
Для гомологического ряда собирателей вклад ∆GR:
∆GR = ∆GСН2∙nCH2, (9)
где ∆GСН2 ≈ 2,5 кДж/моль соответствует работе, необходимой для раздвижения диполей воды на объем СН2-группы при ее переходе из сублата в раствор; nCH2 – количество метиленовых групп в углеводородном радикале.
Суммарный вклад полярной группы собирателя и коллигенда (∆GPK):
ехр ∆GPK/RT = ПР – (ехр zP∆GR/RT) (10)
Выявлены эмпирические зависимости ∆GPK от энтропии гидратации коллигендов (∆S, э.е.) и ∆GP от константы ионизации (рКн) ПАИ (рис.6):
∆GPK = zP∆GP + F∙∆S, (11)
где F – температурный коэффициент пропорциональности (0,43 К).
∆GP = С + D∙рКН, (12)
где D ≈ 7,11 кДж/рКН - угловой коэффициент.
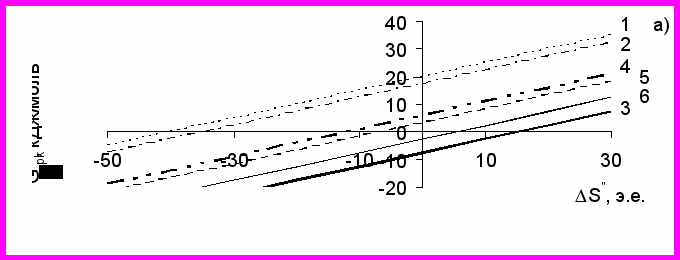
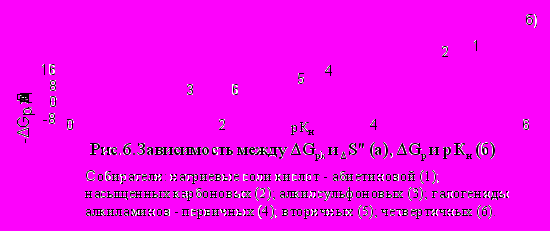
Образование малорастворимого сублата и его флотация в плёночном режиме возможна при отрицательных значениях ∆GPK < 0. Сродство коллигендов к ПАИ собирателей возрастает с увеличением отрицательной гидратации ионов (∆S>0) и уменьшением константы ионизации рКН полярной группы ПАИ.
Для простых гидратированных катионов цветных и редких металлов характерны высокие значения изменения энтропии растворителя в области положительной гидратации (∆S < 0): от -44,5 э.е. (Zn) до -104,2 э.е. (Ga), вследствие чего они не образуют сублатов с анионными собирателями.
Для получения сублатов предложено переводить редкие и рассеянные
металлы в состав растворимых комплексных анионов с высокими значениями
изменения энтропии в области отрицательной гидратации (∆S > 0), например, германий с оксикислотами (щавелевая, винная), индий и галлий с метафосфатами (тетра-, гекса-), которые осаждают из раствора длинноцепочечными (С10-С18) катионоактивными алкиламинами [R-N+(C5H5)], с последующим выделением из объема раствора флотацией или фильтрацией.
Расход собирателей для флотационного выделения коллигендов определяется экспериментально путем построения диаграмм состояния водных рас-творов собирателей и коллигендов, отражающих их различные формы: участок
1кривой отделяет истинный раствор ПАВ и коллигенда от мицеллярного раствора ПАВ; участок 2 кривой - мицеллярный раствор ПАВ от суспензии сублата; участок 3 кривой – истинный раствор собирателя и коллигенда от суспензии сублата (рис.7).
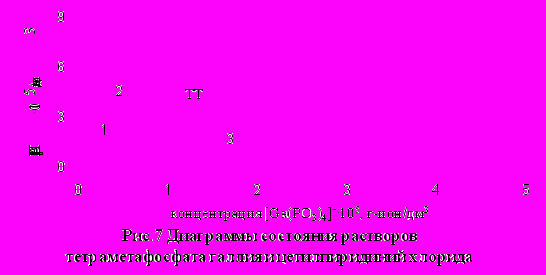
В точке пересечения участков 1-3 кривых–тройной точке (ТТ) диаграмм, сосуществуют истинные и коллоидные растворы ПАВ с суспензией сублата. Соотношение концентраций собирателя и коллигенда в тройной точке диаграмм состояния соответствуют стехиометрическому составу образующегося сублата. Минимально необходимое количество ПАВ для осаждения из раствора коллигенда равно концентрации собирателя в тройной точке.
Флотация катионов галлия Ga(Н2О)х3+ и анионных комплексов Nax[Ga(PO3)6]-(3-x) с исходной концентрацией Со = 10-4-10-3 г-ион/дм3 осуществлена с использованием солей алкилсульфатов (R-OSO3Na) и алкилпиридиния (R-NC5H5Cl) в диапазоне концентраций С = 10-3-10-2 моль/дм3.
Определены (табл. 15): коэффициент (Е = mпен / mр-р) и степень (ε, %)
извлечения коллигенда в пенный продукт; константа равновесия (K); концентрация собирателя в пенной фракции (Ci, моль/дм3); коэффициент концентрирования коллигенда γm = Спен/Ср-р.
Таблица 15 – Показатели процесса пенной сепарации ионов галлия
Ci .102, моль/дм3 | 0,45 | 1,35 | 2,25 | 3,15 | 4,05 | 4,5 |
ε, % | 7,8 | 21,8 | 33,7 | 43,7 | 52,5 | 55,9 |
ln(Ei+1) .102 | 8,2 | 24,6 | 41 | 57,4 | 73,8 | 82 |
Ki, дм3/моль | 18,2 |
При флотации катионов галлия алкилсульфатами степень извлечения коллигенда ε пропорциональна концентрации собирателя в пенной фракции Ci. Величины адсорбции собирателя на поверхности пузырьков воздуха и константы скорости пенной сепарации, соответственно, составили Гm=2,4·10-6 моль/м2 и Km=5,4·10-4 с-1; коэффициент γm= 30-35.
Для дисперсной фазы сублата – цетилпиридиний гексаметафосфат галлия (С16Н33NC5H5)3[Ga(PO3)6] с исходным содержанием Со = 0,1-1 моль/дм3 значения константы скорости и коэффициента концентрирования, соответственно, равны: Кs = (143 – 241)·10-4, с-1; γs ≥ 350.
Увеличение кинетических показателей процесса при флотации сублата происходит, благодаря многослойному покрытию поверхности пузырьков воздуха частицами дисперсной фазы, в отличие от монослойного распределения ионов коллигенда на поверхности пузырьков воздуха при пенной сепарации (Гs >> Гm).
Для реализации в технологических схемах рекомендовано флотировать коллигенд в составе малорастворимого сублата. В качестве регулятора флотации дисперсной фазы сублатов использован эмульгатор - бутилксантогенат калия (~0,01 моль/дм3), рекуперированный из кубовых остатков производства флотореагента на СУМЗе (г.Ревда).
Проведен анализ процессов взаимодействия частиц сублата между собой и с пузырьками воздуха при пленочной флотации. Для расчёта потенциальных кривых в координатах ΣU(kT)―h(м) предварительно определены значения сложной константы Гамакера (А*=0,682∙10-20, Дж), обратный радиус Дебая (θ=(4,6-458)∙10 6, м-1), радиус (rч=(1-10).10-7 м, rп=(0,5-5).10-4 м) и величина заряда (φч≤15 мВ, φп=10--60 мВ), соответственно, частиц (rч, φч) и пузырьков (rп, φп) воздуха.
В слабокислых растворах (рН = 2-6) при концентрации собирателя ЦПХ, равной (0,43-0,85)∙10-6 моль/дм3, частицы сублата ‒ цетилпиридиний гексаметафосфата галлия (Со = 27 мг/дм3) обладают небольшим положительным зарядом (φч ≤ 12 мВ). При этом энергетический барьер отталкивания отсутствует (ΣU < 1,5 kT), что позволяет частицам дисперсной фазы необратимо коагулировать в ближнем минимуме в режиме «быстрой» коагуляции (рис.8а).
Рассчетная величина константы скорости «быстрой» коагуляции равняется Кб = 1,073.10-17 м3/с.

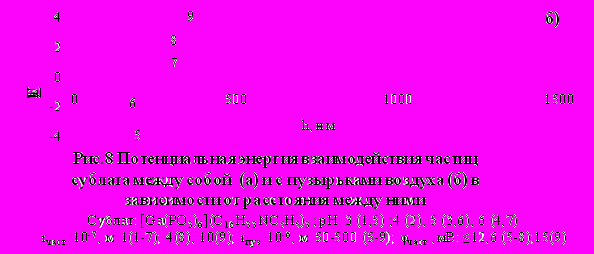
При взаимодействии относительно небольших по размеру(rч ≤ 4.10-7 м) и заряду (φч ≤ 12 мВ) частиц сублата; с пузырьками воздуха (rп = (0,5-5).10-4 м; φп ≤ 60 мВ) энергетический барьер отталкивания отсутствует (ΣU < 1,5 kT) и частицы дисперсной фазы свободно переходят на поверхность пузырьков воздуха и выносятся в пенный продукт. По мере увеличения размера (rч >4.10-7 м) и заряда поверхности частиц (φч >12 мВ) сублата, появляется энергетический барьер отталкивания (ΣU > 1,5 kT), который затрудняет переход частиц дисперсной фазы на поверхность раздела фаз «жидкость-газ» (рис.8б). В этом случае, частицы агрегируют в дальнем минимуме и переходят в пенный продукт вместе с межпузырьковой жидкостью, что увеличивает продолжительность процесса и снижает коэффициент концентрирования.
Необходимо точно подбирать концентрацию катионного собирателя, чтобы не допустить перезарядки частиц дисперсной фазы.
Исследована кинетика коагуляции частиц сублата (27 мг/дм3 цетилпиридиний гексаметафосфата галлия), стабилизированного неионогенным ПАВ (ОП-7), в дисперсных системах без электростатического барьера отталкивания (Ui < 1,5 kT). Замедление процесса коагуляции и снижение значений констант «медленной» коагуляции, по сравнению с константой «быстрой» коагуляции в 20-40 раз (Км < Кб = 1,073.10-17 м3/с), обусловлено адсорбционно-сольватным барьером отталкивания (Ustr = 3,12-3,7 kT), реализуемого за счет адсорбции на поверхности частиц дисперсной фазы молекул растворителя и неионогенного ПАВ (табл.16).
Таблица 16 - Параметры процесса коагуляции сублат-соли галлия
Количество ОП-7 | Км∙1017, м3/с | τ0,5,с | Ustr, kT | |
10-5 моль/кг | 10-10 моль/м2 | |||
0 | 0 | 0,0474 | 311 | 3,12 |
0,2 | 0,633 | 0,0433 | 340 | 3,21 |
0,4 | 1,266 | 0,0369 | 399 | 3,37 |
0,6 | 1,899 | 0,0327 | 451 | 3,49 |
0,8 | 2,532 | 0,0293 | 503 | 3,6 |
1 | 3,165 | 0,0265 | 556 | 3,7 |
Оценка величины предотвращенного экологического ущерба (ПУпро) от
сокращения площадей промышленных отвалов, за счет вовлечения в перера-
ботку анодных остатков электролитического рафинирования чернового алю-миния 3 класса опасности проведена по формуле (5): ПУпро = Уудро.Мотх = 0,25 млн.руб/год, при значениях mпkрос = 5000 т/год; Коkр = 33; Кфгп = 2,5; Мотх = 412500 усл.т/год, что подтверждено расчетами Института экономики УрО РАН.
В пятой главе на основе выявленных закономерностей массопереноса, кинетики и построенных математических моделей исследованных гидрометаллургических процессов произведен расчет основных размеров и характеристик головных образцов агрегатов с оптимальным расходом конструкционных материалов для разработанных ресурсо- и энергосберегающих процессов по комплексной переработке жидкого и твердого техногенного сырья.
Для сорбционного доизвлечения примесей тяжелых цветных и черных металлов (ΣСMe = 5·10-4 г-ион/дм3) из сточных вод (V=1000 м3/сут) на КУ-2-8 (СОЕ = 7,5·10-4 г-ион/г (47,6 мг/г); В = 0,527.10-3 с-1) в количестве mMe=ΣСMe.V=500 г-ион/сут необходимое количество (объем) ионита составляет mc = mMe/СОЕ=0,67 т (vc=0,867 м3) КУ-2-8 при продолжительности сорбции τс=СОЕ/В=25,1 час. Для поддержания заданной производительности очистки стоков от металлов-примесей (mMe=500 г-ион/сут) окончательное количество (объем) смолы на стадии сорбции/десорбции составило mc.кон. = mc.τс/24=0,7 т (vc.кон=0,906 м3). Суммарное количество смолы в процессе сорбции Σmc.кон=mc.кон.2=1,4 т. Объем сорбционной колонны 1,13 м3, при заполнении 0,8 (Н/d = 6; Нк = 3,73 м; dк = 0,62 м).
Для доизвлечения металлов-примесей (ΣСо = 5·10-4 г-ион/дм3) из сточных вод (V=1000 м3/сут) флотацией (Qвоз=2,4.10-2 м/с; [ДСН]равн=1 моль/м3; ε=0,95; R=1.10-4 м; Km.экс=1,8.10-4 с-1) продолжительность процесса составляет τф=ε/Km=5278 с; количество циклов флотации в сутки nц = 24/tф=16,4; объем растворов в цикле Vц=V/nц = 61м3; объем флотационной колонны 7,64 м3, при заполнении 0,8 (Н:d = 5; Нк = 6,25 м; dк = 1,25 м) потребуется 10 флотоколонн.
Определены основные размеры сгустителей-отстойников для оптимального режима свободного осаждения гидроксидов металлов из сточных вод
(V=1000 м3/сут; qтв.исх= (0,15-0,5) кг/м3=(150-500) кг/сут; Сфл ≤ 0,9·10-3 кг/м3,
qфл ≤ 6 мг/гтв ): dс = 4-4,2 м; Нс = 2,5–3,1 м; Fос = 12,6 -14 м2 (табл.6).
При выщелачивании германийсодержащих металлургических пылей (масса/объем пыли mп/vп = 2,5т/1м3; ρ = 2,5 г/см3; d = 150 мкм; S = 4.106 дм2; Ge=0,015 %; mGe=5,17 г-ион; Т=293 К; Т:Ж=1:3; vуд=0,27.10-9 г-ион/дм2.с) продолжительность растворения германия составляет τв= mGe/vуд.S=1,33 час; объем пульпы v = vп+ vр-ра = 8,5м3; объем реактора выщелачивания 10,63 м3, при заполнении 0,8 (Н/d = 2,5; dр= 1,76 м; Нр= 4,39 м).
При сорбционном выделении германия из растворов выщелачивания
(V=7,5 м3/цикл; СGe=6,89·10-2 г-ион/дм3; mGe = 516,6 г-ион/цикл; Т=353 К) на ионите АН-31Г (СОЕGe =40 мг/г (5,51·10-4 г-ион/г); В=4.10-3 с-1; r=5.10-2 см; ρ=1,3 см3/г) количество cорбента для одного цикла равно mc(vc) = mGe /СОЕGe = 0,94 т (1,22 м3); продолжительность сорбции τс = СОЕGe/В = 2,78 час , число циклов сорбции nц = 24/τс = 8 цикл/сут; с учетом загрузки десорбционной колонны суммарная масса ионита в процессе Σmc=mc.2=2т; объем сорбционной колонны 1,53м3, при заполнении 0,8 (Н/d = 6, dк= 0,69 м; Нк= 4,14 м).
При расчете флотомашин использована универсальная модель процесса ионной флотации:
dC/dt = (Cоq – Cq - kГkτkdkпCQ)/V, моль/м3.с (13)
где t – продолжительность флотации, с; Cо,С – концентрации извлекаемого компонента, соответственно, в исходном растворе и во флотационной камере, моль/м3;q – объемный расход поступающей на флотацию (или отработанной) жидкости, м3/с; kГ = Г*St/C – фактор распределения для всплывающих пузырьков газа, м; Г*St – адсорбция (адгезия) извлекаемого компонента на пузырьках газа при стационарном (равновесном) состоянии, моль/м2; kτ = Г*τ/Г*St – степень приближения Г*τ к Г*St («кинетика» адсорбции); Г*τ - адсорбция (адгезия) извлекаемого компонента на пузырьках газа за время всплывания τ; kd – удельная (на единицу объема газа) поверхность пузырьков, м2/м3; kп = 1 – [(dМп - dМАП)/dMВ] – степень отделения металла, вынесенного пузырьками газа к верхней границе жидкости; dМп – количество извлекаемого компонента адсорбируемого (десорбируемого) в объем водной фазы с ее поверхности за время dt; dМАП - количество извлекаемого компонента на пузырьках газа, находящихся у верхней границы жидкости (от момента начала торможения до окончания перехода через указанную границу) за время dt; dMВ - количество извлекаемого компонента, выносимого пузырьками газа к верхней границы жидкости за время dt; Q – объемный расход газа, м3/с, V – объем жидкости во флотационной камере, м3.
Частным случаем уравнения (13) является уравнение стационарного режима (dC/dt =0; C = CSt = const) непрерывного процесса:
CSt/Co = 1/(1 + kГkτkdkпQ/q) (14)
С учетом уравнения (14):
ε = 1 – [1/(1+ kГkτkdkпQ/q)], (15)
где ε ≈ (1 – С/Со) – извлечение при флотации.
Значения кинетического коэффициента (k) процесса непрерывной флотации рассчитаны по результатам эксперимента на примере цетилпиридиний тартрата германия по уравнению:
k = q/(1 - ε)Q (16)
Для дискретного флотационного процесса извлечение и продолжительность флотации (tф) определяли по уравнениям:
ε = 1 – ехр(-kQt/V) (17)
tф = V/q (18)
Величина k может рассчитана по данным дискретной флотации:
k ≈ (Δε/Δt)[V/Q(1 – ε*)], (19)
где ε* – среднее для интервала Δt значение ε.
С учетом (19), исходя из кинетических кривых кривых ε = f(t), рассчитывали зависимость величины кинетического коэффициента от концентрации извлекаемого компонента k = φ1(C). Полученные данные использованы для построения зависимостей эффективности непрерывного процесса флотации от его физических параметров, а также для определения необходимого числа камер промышленной флотомашины.
Концентрация извлекаемого компонента в отработанном растворе в стационарном режиме связана с расходом жидкости уравнением:
СSt = Со/[(1 + (kQ/q)] (20)
Для построения зависимости СSt от q в экспериментах по дискретной флотации при заданных значениях Со, Q, dпуз.и Н снимали кинетическую кривую ε = f(t) с учетом выражения (19), после чего рассчитывали зависимость k = φ1(C). По уравнению (20) определяли зависимости СSt = φ2(k), соответствующие различным значениям q при постоянных Со и Q.
Из уравнения (20) получено выражение для n-камерной флотомашины при k = const:
СSt = Со[1/(1 + kQ/q)]n (21)
В общем случае:
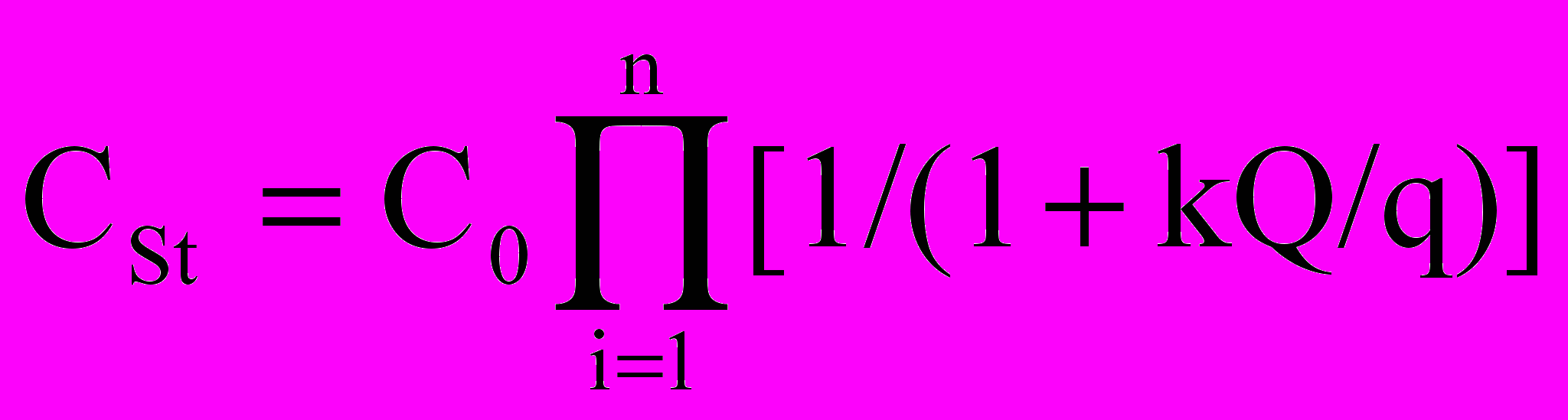
Для определения (n) по результатам порционных экспериментов, проведенных при заданных для проектируемой машины значениях Со, Н, dпуз. И интенсивности аэрации (Q/V), строили зависимость k = φ1(С) (рис.9, кривая 1).
Затем по уравнению (20) рассчитали зависимость СSt-i = φ2(k) для заданного Q/q (рис.9, кривая 21). Абсцисса точки их пересечения (I) определяет СSt-1 для первой камеры, равную исходной концентрации компонента Со2 для второй камеры. Для значения Со2 вновь рассчитали зависимость СSt-i = φ2(k) при том же Q/q (рис.9, кривая 22), определили абсциссу точки ее пересечения (II) с кривой 1 и т.д., до тех пор, пока не было достигнуто необходимое значение СSt.
Зависимость k = φ1(C) при Со = 10-3 моль/дм3, q = 360 см3/мин; Q = 100 см3/мин; Н = 50 см; V = 0,5 дм3 (рис.9, кривая 1), соответствует уравнению:
k = – 0,107Cst2 + 2,215Cst + 0,31
Зависимости СSt-i = φ2(k) (рис.9, кривые 21-4) соответствуют уравнениям:
k2-1 = 0,185Cst2 – 3,542Cst + 17,04;
k2-2 = 3,687Cst2 – 20,59Cst + 29,28;
k2-3 = 15,32Cst2 – 43,26Cst + 29,75;
k2-4 = 24,68Cst2 – 43,79Cst + 19,48
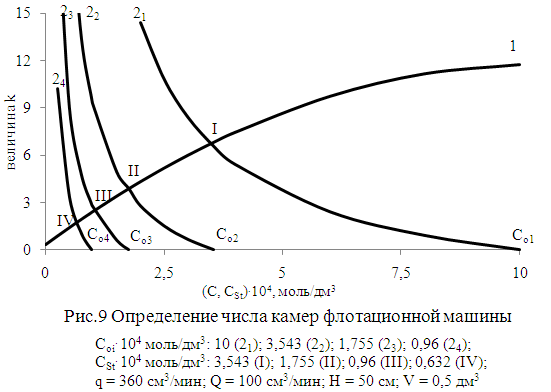
Таким образом, для осуществления ионной флотации в стационарном режиме (1м3/час), например, цетилпиридиний тартрата германия, из раствора выщелачивания металлургических пылей с исходной концентрацией извлекаемого компонента Со=10-3 моль/дм3 при заданных параметрах процесса: СSt=0,63.10-4 моль/дм3; q = 277,8.10-6 м3/с; V = 23,15.10-3 м3, q/V = 0,012 с-1; Q = 77,18.10-6 м3/с; Q/V = 3,334.10-3 с-1; Н = 0,5 м; dпуз.=1,5.10-3 м, необходима 4-х камерная флотомашина (n=4) с рабочими размерами каждой камеры: высота – 0,55 м; диаметр – 0,243 м: площадь поперечного сечения – 0,0463 м2.
В шестой главе методами многомерного регрессионного анализа и
компьютерного моделирования с использованием стандартных программных пакетов («Excel», «Mathcad», «Maple», «Statistica») выведены регрессионные уравнения (23-27) зависимости основных показателей (Yi) от величины параметров (Xj) исследованных пиро- и гидрометаллургических процессов, использованные при разработке систем для эффективного управления и автоматизации разработанных технологий:
– очистка шахтных и сточных вод
Y = 540,79 + 1,39Х1 – 9,12Х2 – 3,10Х3 – 0,14Х1Х2 + 0,02Х1Х3 +
+0,03Х2Х3 –0,006Х12+0,62Х22+0,009Х32; R2 = 0,99; (23)
где Y – cкорость осаждения дисперсной фазы, Vос=(1,9-8).10-4, м/с; Х1 – содержание дисперсной фазы в пульпе, qтв.исх=75-600, г/м3; Х2 – диаметр частиц, d=27-45, мкм; Х3 – температура пульпы, Т=277-363, К;
– пирометаллургическая возгонка германия:
Y= – 311,16+0,58X1-1,15X2 +42,36X3+127,38X4+0,09X1X2-0,25X1X3- 0,59X1X4+
+0,04X2X3-0,51X2X4-8,68X3X4-0,03X12–0,004X22-0,04X32-0,28X42; R2=0,99; (24) где Y – степень возгонки германия, γ = 55-98%; Х1 – основность шихты, (CaO+MgO)/SiO2) = 0,3-0,8; Х2 – содержание шлакообразующих компонентов,
∑(CaO,MgO,SiO2) = 10-70%; Х3 – содержание углерода, С = 2,5-32,5%; Х4 – со-
держание серы, S = 4-11%;
– цементационное выщелачивание анодного остатка
Y = – 88,68+ 4,49X1 + 3,56X2 - 22,53X3 + 3,55X4 + 0,06X1X2 –
– 0,67X1X3 + 0,14X1X4 + 0,27X2X3 - 0,11X2X4 + 0,29X3X4 +
+0,002X12 - 0,001X22 - 0,38X32 + 0,02X42; R2 = 0,994; (25)
где Y – удельная приведенная скорость растворения анодного остатка, ωп= (2,9-10,95)·10-6, дм3/см2·с; Х1 – отношение концентраций серной кислоты и медного купороса в составе кислотно-солевого растворителя,
[H2SO4]/[CuSO4] = (4,43-64,2); Х2 – суммарная концентрация алюминия и галлия в пульпе, (Al+Ga) = (0,63-1,02), г-ат/дм3; Х3 – интенсивность перемешивания пульпы, n = (1,66-9),с-1; Х4 – температура пульпы, t = 50-90, оС;
– выход медьсодержащей массы при шахтной плавке
Y = – 3349,88 + 33,88Х1 + 33,64Х2 + 33,97Х3 + 33,91Х4 +
+ 33,91Х5 + 33,78Х6 + 33,5Х7 + 34,07Х8; R2 = 0,533; (26)
где Y - выход медьсодержащей массы (31,85-35,59),%; Х1- медный лом (9,1-14,16),%; Х2 - смесь РДК (5,99-14,57),%; Х3 - анодный и силикатный шлаки, штейн (0,01-7,85),%; Х4 - сульфидные материалы (30,38-38,45),%; Х5 - золотосодержащие концентраты (0,01-4,52),%; Х6 – оборотные материалы (15,67-28,2),%; Х7 – клинкер (6,47-10,94),%; Х8 – флюсы (8,22-11,18),%;
– содержание примесей в медьсодержащей массе при шахтной плавке
Y = – 9,53 + 0,107Х1 + 0,133Х2 + 0,096Х3 + 0,102Х4 +
+ 0,095Х5 + 0,102Х6 + 0,095Х7 + 0,113Х8; R2 = 0,564; (27)
где Y – отношение медь/примеси в медьсодержащей массы (1,06-1,09),%; Х1- медный лом (8,22-15,96),%; Х2 - смесь РДК (5,31-8,56),%; Х3 - анодный и силикатный шлаки, штейн (0,01-9,0),%; Х4 - сульфидные материалы (27,52-39,72),%; Х5 - золотосодержащие концентраты (0,01-4,76),%; Х6 – оборотные материалы (18,7-31,15),%; Х7 – клинкер (6,98-10,14),%; Х8 – флюсы (6,48-10,84),%.
Полученные аналитические зависимости использованы для анализа и оптимизации пиро- и гидрометаллургических переделов исследованных видов жидкого и твердого техногенного сырья, что позволило минимизировать удельные расходы реагентов, увеличить выход товарной продукции, уменьшить образование вторичных отходов производства.