Разработка экологически чистых технологий комплексного извлечения благородных и цветных металлов из электронного лома
Вид материала | Автореферат |
Содержание4. Физико-химические основы пирометаллургической технологии переработки электронного лома. |
- Доклад об осуществлении лицензионного контроля в сфере заготовки, переработки и реализации, 129.86kb.
- Московский Государственный Институт Стали и Сплавов (Технологический Университет) Кафедра, 461.38kb.
- Правительства Российской Федерации от 23 июля 2002 г. # 552 "Об утверждении Положения, 136.41kb.
- Пленарные доклады, 942.76kb.
- Коэффициенты, применяемые при расчете цен на лом и отходы никеля и никелевых сплавов, 50.78kb.
- Коэффициенты, применяемые при расчете цен на лом и отходы олова и оловянно-свинцовых, 43.04kb.
- Отчет по результатам исследования «Создание предприятий по заготовке, переработке, 4399.59kb.
- Выявление и раскрытие незаконного предпринимательства в сфере оборота лома и отходов, 375.22kb.
- «Создание экологически чистых и энергосберегающих горно-технологических автоматизированных, 142.89kb.
- «производство отливок из сплавов цветных металлов», 38.25kb.
4. Физико-химические основы пирометаллургической
технологии переработки электронного лома.
В данной главе изложены результаты исследований, направленных на разработку научных основ и технологии пирометаллургической переработки электронного лома. Изучены вопросы обжига и плавки электронного лома на медный коллектор. На основании результатов исследований выполнена разработка специализированного технологического оборудования для реализации этих процессов.
4.1. Обжиг электронного лома
На основании данных по изучению состава различных видов электронного лома было установлено, что в ломе содержатся органические материалы (полистирол, гетинакс, полиэтилен, полистирол, поливинилхлорид и др.) и их содержание составляет в зависимости от вида электронного лома от 5 до 27%. Учитывая высокую скорость горения органических материалов, значительный объём образующихся при этом газов и существенные трудности при их улавливании и очистке, является очевидным необходимость предварительного (до проведения плавки лома) удаления органических материалов из электронного лома.
В связи с изложенным электронный лом, содержащий драгоценные металлы, подвергают подготовительному металлургическому переделу – обжигу. Обжиг электронного лома, как уже отмечалось, осуществляют с целью удаления органических составляющих, отгонки при высокой температуре летучих металлов (мышьяка, свинца, цинка, олова и др.), перевода примесей в оксидную форму для селективного отделения их в процессе последующей переработки.
При выполнении данных исследований была изучена зависимость степени удаления органических материалов из электронного лома от температуры и продолжительности процесса обжига (рис.2), а также был определён состав образующихся при горении газов. Из рассмотрения экспериментальных данных (рис.2) следует, что степень удаления органических материалов из электронного лома возрастает с увеличением продолжительности и температуры процесса обжига. Полное сгорание органических материалов (степень удаления ~100%) достигается при обжиге электронного лома в течение 2 часов при температуре 700оС.
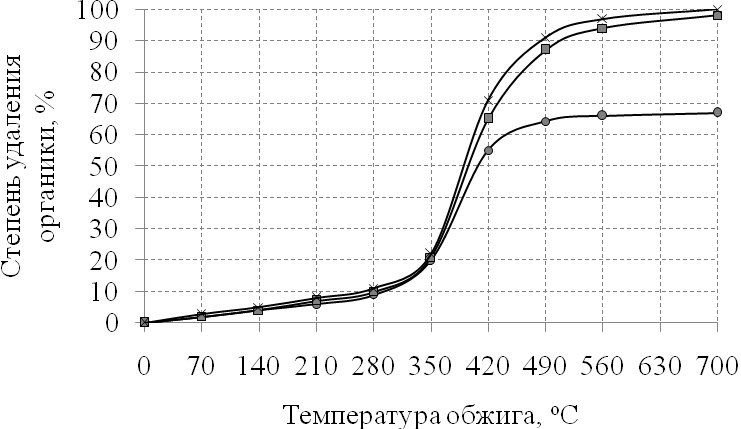
Рис. 2. Зависимость степени удаления органических материалов из электронного лома от температуры и продолжительности обжига.
Продолжительность обжига, час.: - 0,5 ; - 1,5 ; - 2.
Основными реакциями процесса обжига электронного лома являются реакции горения полиэтилена, полистирола, поливинилхлорида. При обжиге происходит окисление олова, свинца, цинка и углерода. Перечень наиболее токсичных веществ, образующихся в процессе обжига представлен в таблице 3. Концентрация свинца и олова в отходящих газов составляет 0,002 и 0,1000 мг/м3, соответственно. Согласно расчётам при температуре обжига 700°С концентрация олова в газах не должна превышать - 410-5 мг/м3. Повышенное содержание свинца и олова в отходящих газах, возможно связано с их частичным механическим захватом потоком продуктов сгорания органических материалов.
Таблица 3 - Состав газов, образующихся при обжиге электронного лома
Наименование вещества | Содержание от общего количества вредных выбросов, мг/м3 | ПДК рабочей зоны, мг/м3 | Класс опасности |
1,4 Диоксан | 0,080 | 0,100 | 1 |
Ацетонитрил | 7,000 | 10,000 | 2 |
Этилбензол | 0,400 | 1,000 | − |
Стирол | 0,500 | 5,000 | − |
Хлор | 0,030 | 0,100 | 2 |
Фосген | 0,008 | <0,010 | 1 |
Пыль неорганическая, содержащая SiO2 | 0,450 | 0,500 | 3 |
Оксид углерода | 4,700 | 5,000 | 4 |
Свинец | 0,002 | 0,003 | 1 |
Олово | 0,100 | 0,050 | 5 |
– Временно допустимая концентрация |
4.2. Разработка обжиговой печи и оптимизация условий обжига
На основе результатов выполненных исследований была спроектирована промышленная вращающаяся электропечь непрерывного действия для обжига электронного лома. Технические характеристики печи представлены в таблице 4.
Таблица 4 - Основные технические характеристики печи для обжига электронного лома
Наименование характеристики | Значение |
Скорость вращения барабана, об/мин. | 0,09-2,15 |
Угол наклона барабана печи к горизонту, ° | 1-3 |
Установленная мощность, кВт | 328 |
Потребляемая мощность, кВт | 269 |
Напряжение питания, В | 380 |
Число тепловых зон | 2 |
Температура по зонам печи, °С | 0-900 |
Длина барабана, мм | 5400 |
Диаметр, мм | 890 |
Масса печи, т | 17,92 |
Габаритные размеры, мм | 9400x2310x3040 |
Данная печь была изготовлена и были проведены промышленные испытания печи с целью определения оптимальных условий ведения процесса обжига с учетом состава перерабатываемого на заводе сырья. Было изучено влияние температуры и продолжительности обжига на убыль массы электронного лома. На рис.3 приведены данные по убыли массы электронного лома в зависимости от вида сырья и температуры процесса обжига. Было установлено, что резкая убыль массы обжигаемого материала наблюдается в интервале температур 460-5000С и обусловлена тем, при этих температурах происходит воспламенение полимеров, входящих в состав органической фазы электронного лома и затем – активное горение всего органического материала. Наиболее полное сгорание органических материалов происходит уже при температуре 7000С в течение двух часов, что хорошо согласуется с результатами лабораторных исследований. Дальнейшее повышение температуры процесса обжига или увеличение его продолжительности процесса нецелесообразно, так как практически не влияет на степень удаления органических материалов, но приводит к существенному увеличению расхода электроэнергии.
Был проведён расчет теплового баланса обжиговой печи, который показал, что для нагрева 1 кг перерабатываемого материала до температуры 700°С требуется (с учётом потерь) 87358,68 кДж, а при обжиге 1 кг смешанного электронного лома с учетом тепла окислительных реакций выделяется 129382,53 кДж тепла. Благодаря этому обстоятельству вывод печи на полую мощность необходим только в начальный период обжига.
Таким образом, были определены условия обжига электронного лома различных видов, разработана технология этого процесса, спроектирована и изготовлена вращающаяся электрическая печь мощностью ~330 кВт для обжига электронного лома. Печь для обжига электронного лома прошла программу необходимых испытаний и введена в эксплуатацию в ОАО «Щелковский завод ВДМ».
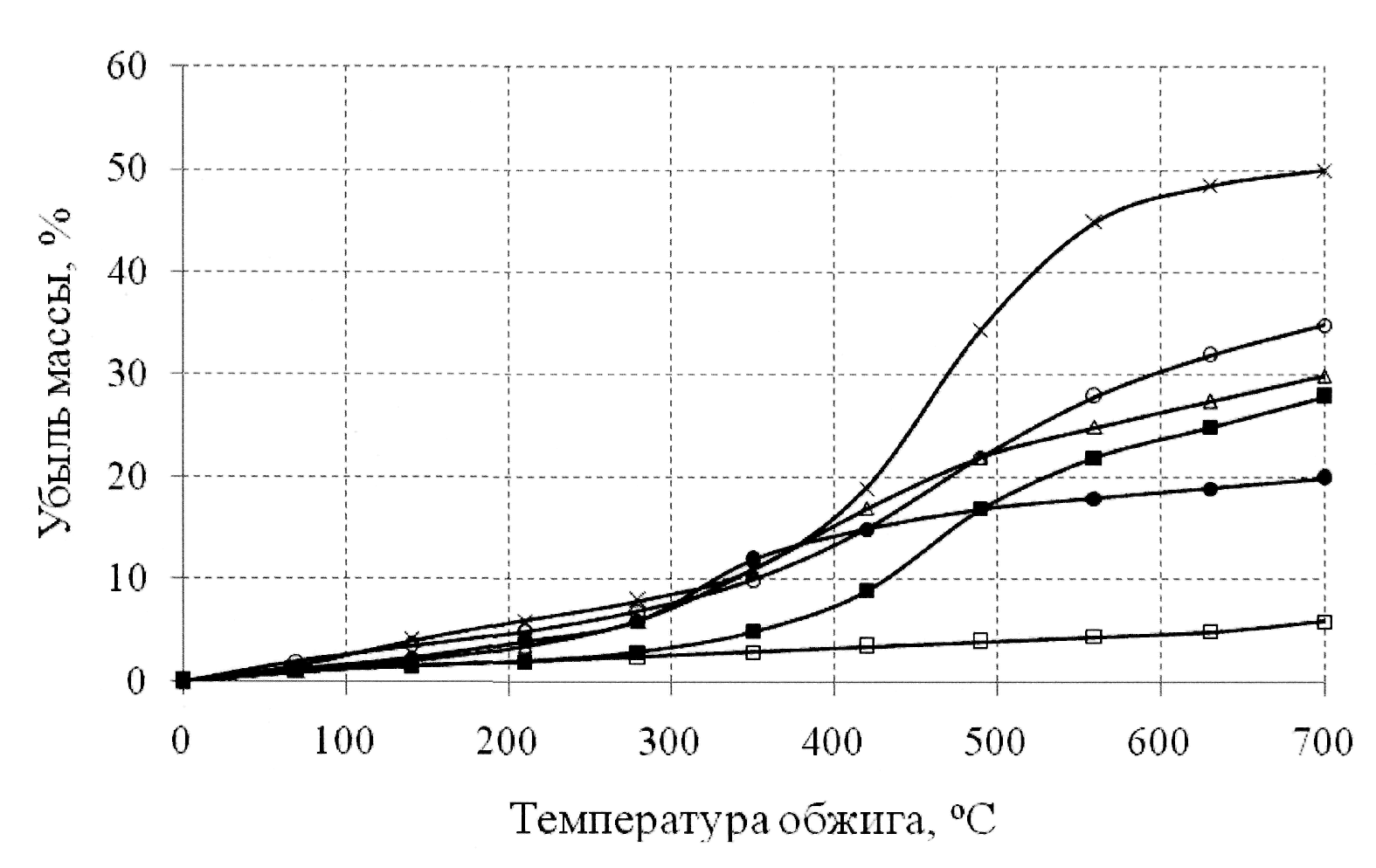
Рис. 3. Зависимость убыли массы различных видов электронного лома от температуры процесса обжига; продолжительности обжига – 2 часа.
Виды электронного лома:
- ЭВМ (состав №4); - смешанный лом электронных приборов (состав №3); - лом приборов самолётов (состав №1); - платы электронные (состав №2); - стеклянные изоляторы (состав №6); - элементы с функциями переключения (состав №5)
4.3. Плавка электронного лома с использованием медного коллектора
4.3.1. Состав и свойства шлаков
Плавка с медным коллектором электронного лома после его обжига позволяет консолидировать в сплав все металлы, и, прежде всего, драгоценные и цветные. Технологичность и эффективность плавки с медным коллектором в значительной степени зависит от состава и физико-химических свойств шлаков, в частности, от вязкости шлаков.
На основании предварительных экспериментов и оценки состава основных фазовых составляющих шлаков, образующихся в реальных условиях при плавке электронного лома, было установлено, что состав шлаков в значительной степени предопределен составом применяемых для плавки флюсов и содержит преимущественно оксидные соединения, входящие в состав последних - SiO2, CaO, Na2O, B2O3, FeO. Для получения корректных данных о вязкости шлаков и влияния на вязкость состава шлаков и температуры были выполнены исследования, в которых объектом изучения являлась система на основе SiO2-FeO-Na2O-CaO- B2O3, составленная из индивидуальных (100%-ных) материалов и моделирующая состав и свойства шлаков, образующихся в условиях реальной плавки электронного лома. Такие шлаки, полученные при переплавке практически чистых флюсов, т.е. в отсутствии сырья, в так называемых «холостых» плавках, в тексте указаны как Х-шлаки. Измерение вязкости Х-шлаков проводили на ротационном вязкозиметре при максимальной температуре 1350°С и через каждые 25 градусов, снижая температуру до тех пор, пока из расплава не выпадали кристаллы тугоплавких компонентов, о чем свидетельствовало резкое повышение вязкости. В рассматриваемых экспериментах кристаллизация фаз на основе тугоплавких компонентов происходила в интервале 1100-1150°С.
Таблица 5 - Состав Х-шлаков
Шлак, № | %, масс. | ||||
FeO | SiO2 | Na2O | В2О3 | CaO | |
1 | 29,8 | 33,6 | 6,4 | 14,6 | 15,6 |
2 | 30,5 | 31,2 | 7,6 | 17,4 | 13,3 |
3 | 32,3 | 28,7 | 9,3 | 21,1 | 8,6 |
4 | 10,1 | 40,4 | 31,5 | - | 18,0 |
5 | 15,0 | 38,2 | 29,7 | - | 17,1 |
6 | 19,9 | 36,5 | 27,4 | - | 16,2 |
7 | 25,2 | 33,7 | 26,0 | - | 15,1 |
Результаты экспериментальных исследований вязкости Х-шлаков в зависимости от состава и температуры приведены в таблице 6.
Таблица 6 - Вязкость Х-шлаков на основе системы SiO2-FeO-Na2O-CaO в зависимости от состава и температуры
Шлак, № | Температура, 0С | ||||||
1150 | 1175 | 1200 | 1225 | 1250 | 1275 | 1300 | |
Вязкость, Пас | |||||||
1 | - | 4,725 | 3,185 | 1,912 | 1,317 | 1,123 | 1,027 |
2 | 3,611 | 2,000 | 1,373 | 1,143 | 0,917 | 0,853 | 0,687 |
3 | 2,592 | 1,709 | 0,961 | 0,753 | 0,610 | 0,520 | 0,513 |
4 | 0,842 | 0,712 | 0,515 | 0,393 | 0,308 | 0,226 | 0,184 |
5 | 0,866 | 0,642 | 0,463 | 0,375 | 0,308 | 0,248 | 0,221 |
6 | 0,675 | 0,552 | 0,471 | 0,348 | 0,282 | 0,226 | 0,184 |
7 | 0,667 | 0,510 | 0,387 | 0,304 | 0,226 | 0,147 | 0,123 |
Из рассмотрения представленных данных следует, что температурная зависимость вязкости Х-шлаков подчиняется экспоненциальному закону. До температуры 1250-1275°С происходит резкое снижение вязкости Х-шлака, далее, с увеличением температуры снижение вязкости незначительное. Для Х-шлака с содержанием оксида железа 19,9 % вязкость при температуре 1150 °С составляет 0,675 Пас, а при температуре 1250°С вязкость равна 0,282 Пас. Повышение температуры до 1300°С снижает вязкость этого шлака до 0,184 Паc. Для Х-шлаков с содержанием 25 % тетраборнокислого натрия (Na2B4O7 10H2O) вязкость при температуре 1150°С составляет 3,611 Пас и снижается до 0,917 Пас при температуре 1250°С. Увеличение содержания Na2B4O7 10H2O до 30% снижает вязкость шлака до 0,513 Пас при температуре 1300°С. Полученные результаты позволяют заключить, что для получения более жидкотекучих шлаков с вязкостью до 0,1-0,2 Пас следует увеличивать содержание Na2B4O7 10H2O, однако, из-за резкого увеличения при этом агрессивности шлака, концентрацию Na2B4O7 10H2O следует ограничивать 30-35%.
Содержание оксида железа в шлаках оказывает слабое влияние на изменение их вязкости. С увеличением содержания оксида железа в шлаках от 10 до 25 % его вязкость при температуре 1300°C снижается с 0,184 до 0,123 Пас. Heзначительное снижение вязкости при увеличении содержания оксида железа объясняется сохранением химической связи компонентов в расплаве шлака из-за отсутствия легкоплавких соединений железа в расплаве. На основании проведённых исследований для плавки электронного лома, содержащего драгоценные металлы, предпочтительно использовать натриевосиликатные шлаки, так как они обладают меньшей вязкостью и менее агрессивны. И в этом отношении оптимальным является состав шлака №7 (табл.5), так как он обладает наиболее низкой вязкостью и при этом содержит до 25 % оксидов железа.
В работе были проведены исследования по изучению феррит-кальциевых шлаков. Установлено, что введение в шлак до 25% CaO резко снижает температуру плавления шлака. Поэтому феррит-кальциевые шлаки предпочтительнее по сравнению с обычными железосиликатными шлаками. Эти шлаки в определенной области составов обладают более низкой температурой плавления и вязкостью, отличаются избирательным растворением различных цветных металлов. Показано, что в процессе извлечения из электронного лома меди допустимо изменение состава шлака в следующих пределах: 30-40% SiO2; 25-30% - Na2O; 10-30% CaO.
С учетом полученных данных о составе и свойствах шлаков в работе было изучено влияние количества коллектора при проведении плавки электронного лома на процесс извлечения из него золота. Было установлено, что с повышением количества коллектора с 1 до 25 % происходит увеличение извлечения золота с 55 % до 98,5 %. Коэффициент распределения золота в меди одинаков, но если масса коллектора значительна, то большее количество золота успевает в нем раствориться. При этом не следует увеличивать количество меди, так она начинает теряться со шлаком, что приводит к потере золота. Поэтому оптимальным соотношением лом-коллектор следует считать 100 : 14-20. При малом количестве коллектора можно повысить извлечения золота, но для этого необходимо увеличить продолжительность плавки и отстоя после плавки до 1,5-2 часов. При этом следует учитывать, что коллектор может использоваться многократно – до достижения определённой концентрации золота в нём.
Содержание золота в электронном ломе достаточно низкое и составляет 100г/тонну и за одну плавку с медным коллектором концентрация золота в меди может составить 0,08%. Сплав с таким содержанием золота экономически нецелесообразно перерабатывать с целью извлечения золота. Как уже отмечалось, является эффективным многократное использование медного коллектора. В результате достигается повышение содержания золота в меди до нескольких процентов. При четырёхкратном обороте медного коллектора концентрация золота возрастает до 1,3 %, серебра - до 7,1 %, платины - до 0,9 %, палладия - до 0,3 %. Извлечение золота за четыре операции составило 96 %, серебра - 92 %, платины и палладия - 93 %.
Достоинства технологии с многократным использованием коллектора при плавке очевидны и, прежде всего, при переработке электронного лома, в котором содержится платина и палладий. Эти металлы не извлекаются при гидрометаллургической переработке и, как правило, теряются с хвостами. При плавке с медным коллектором в коллектор переходят все драгоценные металлы.
При исследовании условий проведения плавки с медным коллектором различных видов электронного лома было установлено, что на характер проведения плавки заметное влияние оказывает наличие в шихте углерода. Показано, что концентрация углерода, с одной стороны, не должна быть высокой, поскольку для окисления железа, содержащегося в электронном ломе, необходима окислительная среда, с другой стороны, содержание углерода не должно быть слишком низким, чтобы исключить нежелательное окисление меди. В связи с изложенным вначале плавки поддерживается окислительная атмосфера и лишь в конце процесса плавки переходят на слабо восстановительную атмосферу. С учётом того, что при температуре 12000С растворимость железа в меди достаточно высокая – до 5% масс., следует избегать возможности восстановления оксида (гематита и магнетита) до металлического железа, часть которого может образовать раствор с медью и привести к снижению извлечения золота в коллектор.
Процесс восстановления гематита до вюстита в процессе плавки можно регулировать только расходом восстановителя. Установлено, что при увеличении количества углерода от соотношения восстановитель : электронный лом в шихте при плавке - 1:30 до соотношения 1:10 извлечение золота увеличивается с 75 % до 97 %. Дальнейшее увеличение количества восстановителя до 1:5, приводит к уменьшению извлечения золота до 88 %. Это объясняется тем, что при увеличении соотношения восстановитель (уголь) : электронный лом более 1:10 начинается восстановление гематита и магнетита до металлического железа и часть железа начинает растворяться в меди.
Результаты исследования состава сплава и шлака, образующихся при окислительной плавке на коллектор электронного лома в зависимости от соотношения компонентов в шлаке приведены в таблицах 7 и 8. Из представленных в таблицах 7 и 8 данных можно заключить, что оптимальные, с точки зрения состава получаемого сплава, условия плавки на коллектор электронного лома реализуются при следующем соотношении основных компонентов в исходном шлаке: CaO:SiO2:FeO:Na2O = 15,1:33,7:25,2:26,0. При этом достигается максимальное извлечение меди и драгоценных металлов, минимальное содержание железа в сплаве и минимальные потери меди со шлаками.
Таблица 7 - Состав сплавов, полученных при плавке на медный коллектор электронного лома при различных соотношениях компонентов в шлаке
Тпл., 0С | Время, мин. | Соотношение CaO:SiO2:FeO:Na2O | Массовая доля компонента в меди, % | ||||||
Сu | Ni | Fe | Sn | Pb | Al | Аu | |||
1320 | 60 | 17,1:38,2:15,0:29,7 | 88,420 | 8,860 | 0,223 | 0,210 | 0,3120 | 0,180 | 1,780 |
1320 | 60 | 16,2:36,5:19,0:27,4 | 86,120 | 11,120 | 0,370 | 0,200 | 0,350 | 0,190 | 1,540 |
1320 | 60 | 15,1:33,7:25,2:26,0 | 90,190 | 7,080 | 0,140 | 0,140 | 0,120 | 0,170 | 2,150 |
Таблица 8 - Содержание цветных металлов в шлаках, образующихся при плавке на медный коллектор электронного лома при различных соотношениях компонентов в шлаке
Т пл, °C | Время, мин. | Соотношение CaO:Si02:FeO: Na2O | Массовая доля компонента, % | ||||
Си | Ni | Fe | Sn | Pb | |||
1320 | 60 | 17,1:38,2:15,0:29,7 | 5,69 | 4,69 | 11,7 | 0,17 | 0,06 |
1320 | 60 | 16,2:36,5:19,0:27,4 | 6,18 | 2,98 | 14,8 | 0,20 | 0,04 |
1320 | 60 | 15,1:33,7:25,2:26,0 | 4,29 | 5,12 | 19,8 | 0,18 | 0,08 |
4.3.2. Применение воздушного (кислородного) дутья.
Для более полного удаления примесей из сплава на основе меди, получаемого плавкой на коллектор электронного лома, и повышения чистоты меди было изучено влияние продувки расплава воздухом в процессе плавки. Плавка проводилась при температуре 1320-13500С. Продолжительность подачи воздуха составляла 15,30,45 и 60 минут. Было установлено, что увеличение продолжительности продувки расплава воздухом с 15 минут до 60 минут при постоянном его расходе приводит к увеличению содержания меди и золота в сплаве до 78-80% и ~ 2,0%, соответственно. Дальнейшее увеличение продолжительности продувки сверх 60 минут практически не влияет на содержание меди в сплаве, но приводит к увеличению общих потерь меди со шлаком.
Увеличение расхода воздуха на 25-50% позволяет получать сплав с содержанием Cu до 90-91% и Au до ~2,15%. Дальнейшее увеличение расхода воздуха практически не влияет на увеличение содержания меди и золота в сплаве, но оно приводит в образованию тугоплавких соединений железа и снижению характеристик исходного шлака.
Рассмотрим поведение компонентов в расплаве в условиях подачи в него воздуха.
Наименьшее сродство к кислороду по сравнению с другими металлами (кроме драгоценных), присутствующими в расплаве, имеет медь. Однако вследствие неравномерного распределения потоков воздуха в ванне расплава медь начинает окисляться до Cu2O уже с самого начала продувки. Оксид меди хорошо растворяется в металлической меди и благодаря этому обеспечивает перенос кислорода, необходимого для окисления примесей Zn, Pb, Sn, Ni и других металлов и перевода их в шлак.
Таблица 9 - Влияние условий плавки на медный коллектор электронного лома на содержание примесей в сплаве на основе меди.
Тпл, °С | Продолжительность подачи воздуха, мин. | Расход воздуха, л/ч | Массовая доля металла, % | |||
Fe | Sn | Zn | РЬ | |||
1320 | - | - | 31,09 | 1,90 | 0,80 | 1,17 |
1320 | 30 | 3,00 | 0,73 | 0,63 | 0,11 | 0,77 |
1320 | 45 | 3,00 | 0,32 | 042 | 0,08 | 0,70 |
1320 | 60 | 3,00 | 0,22 | 0,31 | 0,05 | 0,51 |
1320 | 30 | 3,75 | 0,61 | 0,51 | 0,08 | 0,65 |
1320 | 45 | 3,75 | 0,23 | 0,38 | 0,04 | 0,51 |
1320 | 60 | 3,75 | 0,16 | 0,22 | 0,01 | 0,30 |
1320 | 30 | 4,50 | 0,51 | 0,32 | 0,03 | 0,50 |
1320 | 45 | 4,50 | 0,18 | 0,15 | 0,02 | 0,43 |
1320 | 60 | 4,50 | 0,14 | 0,10 | 0,01 | 0,12 |
1320 | 45 | 6,00 | 0,19 | 0,14 | 0,01 | 0,44 |
1320 | 60 | 6,00 | 0,13 | 0,10 | 0,01 | 0,12 |
При продувке ванны расплава воздухом цинк частично окисляется и отшлаковывается. Основная же масса металла переходит в газовую фазу, где пары цинка окисляются до ZnO. Остаточное содержание цинка в черновой меди не превышает 0,01 % и практически не зависит от концентрации этого металла в перерабатываемых материалах.
Свинец отгоняется в газовую фазу уже в начале продувки расплава воздухом, благодаря высокой летучести РЬО (температура кипения 1470 °С), однако наиболее интенсивное удаление свинца из черновой меди происходит после отгонки и ошлаковывания основной массы цинка. В газовую фазу удаляется 25-30 % свинца; 55-60 % свинца переходит в шлак и ~10% - в черновую медь. Остаточное содержание РЬ в сплаве на основе меди ~0,12%.
Металлическое олово в виде паров не отгоняется (температура кипения 2260 °С), а окисляется до SnO2 или SnO и переводится в шлак. Однако, часть олова - до 30-35 % от содержания в электронном ломе может переходить в газовую фазу через испарение SnO, что связано с повышенной летучестью SnO (температура кипения 1425 °С).
Наиболее трудно удаляется из черновой меди никель. Достаточно интенсивное окисление и удаление никеля происходит только в конце продувки. Никель, окисляясь до NiO, частично переходит в шлак. В значительных количествах никель остается в меди в виде медно-никелевого твёрдого раствора. Остаточное содержание никеля в сплаве на основе меди ~7%.
4.4. Разработка плавильной печи и её характеристики
В настоящее время в стране отсутствует выпуск металлургического оборудования, которое можно было бы эффективно использовать для плавки электронного лома. Наиболее распространённые электродуговые печи с контролируемой атмосферой, но, как правило, это печи малой производительности и периодического действия с разливкой металла и шлака в изложницы. Конструкция этих печей не позволяет добиться хорошего разделения металла и шлака и приводит к снижению извлечения золота и меди в металл и их повышенному содержанию в шлаке.
На основании результатов выполненных исследований и полученных экспериментальных данных был разработан технологический регламент на проектирование электродуговой печи непрерывного действия с контролируемой атмосферой. Конструкция печи должна обеспечить сбор медного коллектора в донной части печи и по мере достижения им определённого объёма и насыщения драгоценными металлами разливать расплав в изложницы и получать аноды для последующего электролиза. На основе технологического регламента была спроектирована (проектирование выполнялось Истринским филиалом ВНИИЭТО) и изготовлена промышленная дуговая печь для плавки электронного лома
В процессе испытаний и опытно-промышленной эксплуатации печи были изучены и отработаны условия проведения плавки и влияния на неё следующих факторов: продолжительности плавки, объёма, загрузки, производительности, продолжительности продувки соотношения масс флюс – сырьё, количества коллектора.
По результатам выполненных работ было установлено, что оптимальная продолжительность плавки составляет 2 часа и температура плавки 12500С. Соотношение сырья и флюсов не должно выходить за пределы соотношений от 1:1 до 1:4.
В условиях опытно-промышленной эксплуатации печи была изучена зависимость извлечения золота из различных видов электронного лома от соотношения масс коллектора и сырья. В рамках опытно-промышленной эксплуатации плавильной печи были выполнены работы по изучению степени извлечения золота в зависимости от количества коллектора, которые в целом подтвердили данные лабораторных исследований. При недостатке коллектора золото из-за его малой концентрации не успевает объединиться в коллектор и для его более полного извлечения необходимо увеличение продолжительности плавки и отстоя расплава, как было установлено, до 4-6 часов. При этом производительность печи снижается в 2-3 раза, что существенно влияет на экономические показатели печи и производства в целом. Было установлено, что общее количество коллектора (масса меди в исходном сырье и плюс медь, добавляемая в шихту) должно составлять 25% от количества сырья.
Было установлено, что при высоком содержании в электронном ломе алюминия и железа также необходимо существенно увеличивать количество меди в коллекторе до значений соотношения масса коллектора: масса сырья от 0,5:1 до 1:1. В этом случае зависимость извлечения золота во времени отличается более пологим характером.
Была изучена зависимость извлечения золота от соотношения масса флюса : масса электронного лома (рис.4) и установлено, что при увеличении указанного соотношения от 1:20 до 1:1 извлечение золота возрастает от 81,5 до 99,8%. Данные результаты свидетельствуют о том, что при малом количестве флюса в него переходят железо и алюминий, повышая, в частности, концентрацию железа выше 25%, что, в свою очередь, приводит к росту вязкости шлака и снижению скорости перехода золота в коллектор. Изложенное подтверждается результатами, полученными при плавке различных видов электронного лома при фиксированном соотношении масс флюсов и лома 1:10., согласно которым при повышении содержания железа от 7,15% до 35,26% извлечение золота уменьшилось с 90,1% до 73,6%. При увеличении соотношения масс флюсов и электронного лома до 1:5 извлечение золота увеличилось до 84,2% (рис.5). При этом концентрация оксида железа в шлаке составила 41,5%.
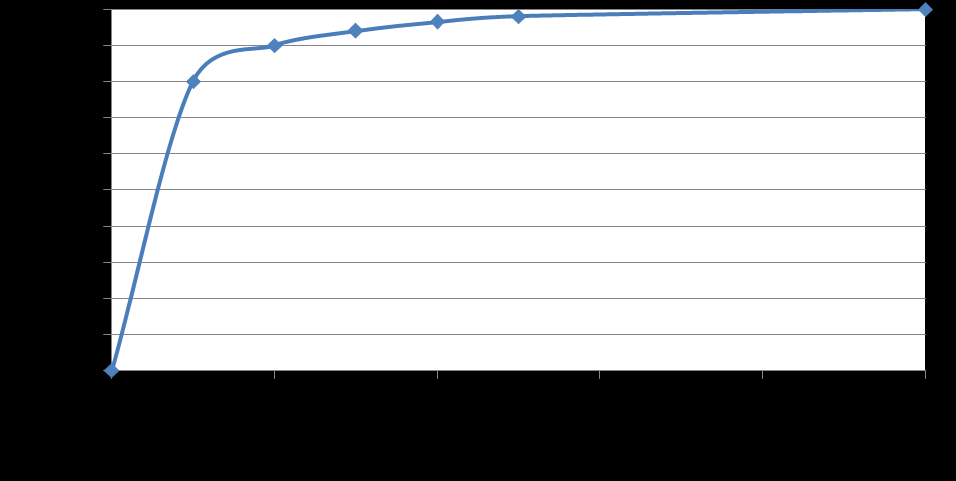
Рис.4 Зависимость извлечения золота от соотношения масс флюс: электронный лом
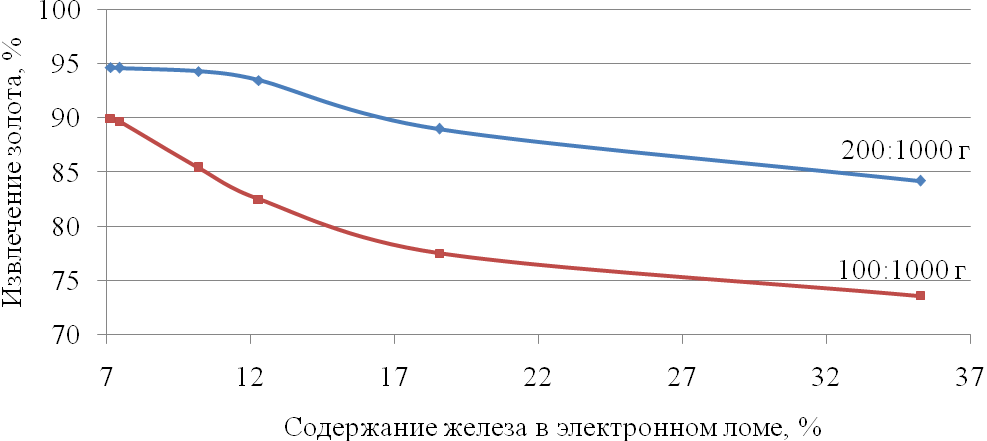
Рис. 5. Зависимость извлечения золота от содержания железа в исходном электронном
ломе. Соотношение масс сода: электронный лом .
В связи с высокой критичностью влияния содержания железа на извлечение золота и для реализации оптимальных условий плавки в процессе опытно-промышленного освоения печи содержание железа в шлаках регулировали, используя комбинации различных видов электронного лома или увеличивая количества флюсов, тем самым обеспечивая максимальное извлечение золота.
В условиях опытно-промышленного освоения печи для плавки электронного лома дополнительно исследовано и уточнено содержание компонентов в шлаке. Так, при плавке электронного лома (составы 1 и 4 – табл.1) при постоянном содержании SiO2 и СаО было изучено влияние Na2O (соды) на извлечение золота. Показано, что повышение содержания Na2O до соотношения масс сода : электронный лом до 1:10 и 1:5 и, тем самым, снижение вязкости шлака приводит к росту извлечения золота до 90% и 97% (рис.6), соответственно. Дальнейшее увеличение количества соды в шлаке практически не влияет на извлечение золота.
Таким образом, в данной главе рассмотрены результаты исследований, направленные на создание физико-химических основ технологии обжига и плавки ЭЛ. Показана необходимость предварительного обжига ЭЛ с целью удаления и утилизации газов, образующихся при сжигании органических материалов. Обжиг обеспечивает сокращение объёма переплавляемого материала до 30 %, и позволяет существенно увеличить производительность плавильного агрегата. Установлено, что тепло, выделяемое от сжигания органических материалов позволяет сократить расход электроэнергии на обжиг со 115 кВтхч/кг до 33,5 кВтхч/кг. На основании результатов исследований была разработана, изготовлена и внедрена в производство печь для обжига электронного лома. Благодаря предварительному обжигу ЭЛ были устранены технические проблемы, связанные со вспениванием материала при проведении плавки, уменьшен вынос металлов с газами и т.д.
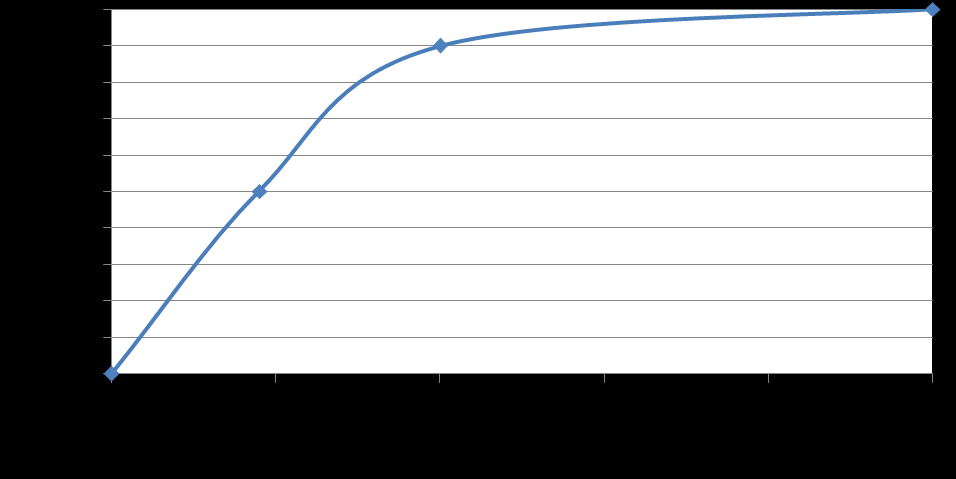
Рис.6. Зависимость извлечения золота от соотношения масс -
сода в шлаке : электронный лом.
Разработаны физико-химические основы и технология плавки ЭЛ на медный коллектор с использованием меди, находящейся в электронном ломе. Выбор оптимального состава шлака позволил повысить извлечение драгоценных металлов до 89-99 %, уменьшить потери меди со шлаками до 0,4% и исключить потери платиновых металлов, сконцентрировав платиноиды в медном коллекторе. Разработана, спроектирована, изготовлена и внедрена электродуговая печь ЭПЗ-1,5 с мощностью 1,5 мВт для плавки на медный коллектор электронного лома.