Автофоретическое формирование полимерных покрытий на поверхности алюминиевых и медных сплавов
Вид материала | Автореферат диссертации |
Содержание4.1.Разработка состава Ок для алюминия и его сплавов 4.2.Разработка состава Ок для меди и её сплавов |
- Тема: сварка алюминия и его сплавов, 56.75kb.
- Флюсы и рециклинг алюминия, 130.43kb.
- Новые технологии и оборудование для формирования покрытий из полимерных экструдатов, 25.72kb.
- Протасов В. Н. Ргу нефти и газа им., 101.76kb.
- Реферат по научно-исследовательской работе г 08 Нано- и микроструктурная модификация, 64.1kb.
- Влияние импульсного электронного облучения на формирование ультрамелкозернистой структуры, 35.51kb.
- Развивающаяся область модификации поверхности это нанокомпозиты на основе сверхтонких, 41.9kb.
- Физические свойства вакуумно-плазменных покрытий для режущего инструмента, 338.06kb.
- Онно-твердеющих сплавов в основе своей связано с разработкой и исследованием высокопрочных, 98.83kb.
- Технологические и металлургические особенности лазерной сварки современных авиационных, 212.71kb.
4.1.Разработка состава Ок для алюминия и его сплавов
При создании Ок необходимо учитывать, что решающим фактором для образования на алюминии гелеобразной пленки является наличие на поверхности металла протонов. Поэтому изучили влияние различных способов подготовки поверхности на процесс автоосаждения.
Исследования состояния поверхности алюминия показало, что нанесение подслоя путем анодирования и хроматирования алюминия не дало положительных результатов. На образцах с оксидной пленкой, погруженных в Ок, покрытия формируются в узкой области рН и не обладают стойкостью к агрессивным растворам.
Установлено, что доброкачественные покрытия образуются на поверхностях, фосфатированных в растворе, содержащем фосфорную и хромовую кислоты и фторид натрия. Фосфатная пленка имеет пористую структуру, что способствует увеличению адсорбции (рис.10) и лучшему закреплению Оп на металле.
![]() |
Рис.10. Изотерма адсорбции олигомера КЧ-0125, осажденного на фосфатированную (1) и нефосфатированную (2) поверхность алюминия, при рН = 7,3. |
Величина адсорбции олигомера КЧ-0125 значительно выше при осаждении на фосфатированную поверхность по сравнению с нефосфатированной. Фосфатная пленка не подвергается термоотверждению и автоосаждение осуществляется на сырой фосфатный слой, что приводит к гетерогенности поверхности металла. Об этом свидетельствует тот факт, что потенциал алюминия становится более отрицательным (рис.11) и возрастает скорость генерации протонов. Толщина автофорезного олигомерного покрытия при этом увеличивается.
![]() |
Рис.11. Зависимость стационарного потенциала от времени процесса для образцов с различной подготовкой поверхности (СКЧ-0125 = 18%, рН = 7,0); 1 – без фосфатирования; 2 – с фосфатированием |
На процесс образования качественного Оп оказывают влияние различные факторы: концентрация исходных компонентов, сухого остатка, рН среды, время процесса.
Изучение зависимости коррозионной стойкости Оп от концентрации ИПС и олигомера КЧ-0125, времени процесса (рис.12) позволило определить область доброкачественных покрытий.
![]() а) | ![]() б) |
Р
а)
а)
а)
а)
а)
а)
ис.12. Диаграммы время автоосаждения покрытий – концентрация ИПС (а) и – концентрация олигомера (б). Заштрихованная область – область получения доброкачественных покрытий.
Снижение концентрации олигомера менее 15% (по с.о.) приводит к получению «шагрени» на Оп, увеличение концентрации олигомера более 25% приводит к толстым с наплывами покрытиям. При увеличении продолжительности процесса автоосаждения более 5 минут, в результате выравнивания концентрации ионов Н+ в близи поверхности изделий и объеме раствора, наблюдается обратный процесс подрастворения образовавшегося Оп. При уменьшении времени процесса менее 2 минут получаются тонкие Оп.
Границы интервала рН композиции определялись с одной стороны, неустойчивостью Ок, приводящей к осаждению олигомера в объеме Ок и получению неравномерных Оп, а с другой – подрастворением образующегося Оп, приводящее к получению, как и в случае уменьшения времени процесса, тонких пленок с пониженной коррозионной стойкостью (рис.13).
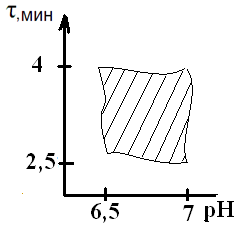
Рис.13. Диаграмма продолжительность автоосаждения покрытий – рН композиции. Заштрихованная область – область получения доброкачественных покрытий. Область качественных Оп лежит в интервале рН = 6,5 – 7.
Таким образом, в результате исследований определен состав Ок (г/л):
Олигомер КЧ-0125 150 – 250
NH4OH (25%) 11 – 16 мл/л
ИПС–вода (1:1) до 1 литра
4.2.Разработка состава Ок для меди и её сплавов
Так как состояние поверхности оказывает влияние на генерацию ионов Н+ исследовали различные способы подготовки поверхности медно-цинковых сплавов. Лучшие результаты по коррозионной стойкости автоосажденных Оп получены после пассивации в растворе, содержащем хромовый ангидрид и серную кислоту.
На рис.14 показано влияние концентрации олигомера КЧ-0125 на изменение потенциала латуни при выбранной подготовке поверхности.
![]() |
Рис.14. Зависимость потенциала поверхности сплава Л-63 от времени выдержки в водно-спиртовом растворе при рН = 6,5 –7,0 с разной концентрацией олигомера КЧ-0125: 1 – 1,9%; 2 – 4,5%; 3 – 14,6%; 4 – 20,5%. |
С увеличением концентрации олигомера потенциал смещается в сторону положительных значений, что свидетельствует о лучшей адсорбируемости олигомера на подложке.
На основании полученных данных установлено оптимальное количество олигомера (15 – 20)% с.о. Пп при этом с.о имеют высокую устойчивость к воздействию 3% раствора NaCl, однако они недостаточно монолитны, видны включения крупных частиц олигомера.
С целью улучшения растекаемости Оп исследовалось автоосаждение при введении в состав Ок добавок различных органических веществ. Лучшие результаты получены при введении в Ок незначительных количеств бутанола. (рис.15).
![]() |
Рис.15. Влияние концентрации бутанола на качество автофорезных покрытий. Заштрихованная область – область получения доброкачественных покрытий. |
При введении бутанола в пределах (0,2 – 0,3) мл/л Оп становятся более блестящими, и на них отсутствуют разводы. При уменьшении концентрации бутанола на поверхности пленок появляются разводы, а при увеличении – снижается время пробоя пленок агрессивным раствором Существенное влияние на получение доброкачественных покрытий оказывает рН среды (рис.16). При рН ≤ 6 покрытие отсутствует, олигомер выпадает в осадок. При рН > 7 получается неравномерное Оп с большими наплывами и натеками. Область равномерных покрытий находится в пределах рН =6,5 – 7.
![]() |
Рис.16. Влияние рН на качество получаемых покрытий |
Таким образом, полученные данные позволили создать автофорезную композицию:
Олигомер КЧ-0125 150-200 г/л
Аммиак (25%) 11-13 мл/л
Бутанол 0,2-0,3 мл/л
ИПС: Н2О (1:1) до 1 л.
По результатам исследований разработали технологический процесс нанесения Оп методом автофореза на алюминиевые и медные сплавы