Центробежно-роторные измельчители фуражного зерна
Вид материала | Автореферат |
- Агро-дайджест, 176.71kb.
- Администрация костромской области контрольное управление информационный обзор материалов, 567.02kb.
- В случае использования информации ссылка на сайт обязательна Справка о проведении производственных, 45.5kb.
- Применение центробежно-ударных мельниц «МЦ» при помоле цемента кушка, 76.77kb.
- Концепция государственной программы модернизации агропромышленного комплекса путем, 388.29kb.
- Рынок зерна в 1 полугодии 2006 года, 260.92kb.
- Концепция эффективного развития сельскохозяйственного производства и создания цивилизованного, 180.11kb.
- Перечислите основные операции послеуборочной обработки зерна на элеваторе, 879.69kb.
- Кабінету Міністрів України від 12 грудня 2002 року №1877 «Про затвердження Порядку, 111.26kb.
- Годовой отчет открытого акционерного общества «Ключевской элеватор» по итогам работы, 211.16kb.
На правах рукописи
СЕРГЕЕВ Николай Степанович
ЦЕНТРОБЕЖНО-РОТОРНЫЕ ИЗМЕЛЬЧИТЕЛИ
ФУРАЖНОГО ЗЕРНА
Специальность 05.20.01 – Технологии и средства
механизации сельского хозяйства
АВТОРЕФЕРАТ
диссертации на соискание ученой степени
доктора технических наук
Челябинск – 2008
Работа выполнена на кафедре «Технология и механизация животноводства» Федерального государственного образовательного учреждения высшего профессионального образования «Челябинский государственный агроинженерный университет».
Научный консультант - | доктор технических наук, профессор академик РАСХН Сыроватка Владимир Иванович |
Официальные оппоненты - | доктор технических наук, профессор Карташов Лев Петрович доктор технических наук, профессор Лапшин Петр Николаевич доктор технических наук, профессор Федоренко Иван Ярославович |
Ведущая организация | ФГОУ ВПО «Омский государственный аграрный университет» |
Защита состоится 19 июня 2008 г., в 10 часов на заседании диссертационного совета Д 220.069.01 при ФГОУ ВПО «Челябинский государственный агроинженерный университет» по адресу: 454080, г.Челябинск, пр. Ленина, 75.
С диссертацией можно ознакомиться в библиотеке Челябинского государственного агроинженерного университета
Автореферат разослан 12 мая 2008 г.
Ученый секретарь диссертационного совета
доктор технических наук, профессор Басарыгина Е.М.
ОБЩАЯ ХАРАКТЕРИСТИКА РАБОТЫ
Актуальность проблемы. Для достижения высоких экономических показателей в животноводческой отрасли кормовой рацион должен содержать определенный набор веществ, полностью удовлетворяющий потребности организма животного в питательных веществах. Это возможно путем приготовления полноценных комбикормов, доля которых в рационе кормления составляет: для птицы 95...100, свиней – 85...90, КРС – 24..30%. Поэтому производство комбикормов является важной отраслью сельского хозяйства.
Ответственной и энергоемкой технологической операцией в приготовлении комбикормов является измельчение зерна. За счет измельчения ингредиентов увеличивается площадь поверхности зернового материала, улучшается взаимодействие корма с пищеварительными ферментами, снижается энергоемкость продукции и повышается качество смешивания компонентов. Однако тонкое измельчение увеличивает энергетические затраты, а мучнистые компоненты вызывают заболевания животных, особенно свиней. Измельчение занимает 50% от общих энерго- и трудозатрат в приготовлении комбикормов.
На животноводческих фермах, комбикормовых заводах, перерабатывающих предприятиях широко используются молотковые и ударно-центробежные дробилки и измельчители, имеющие ряд существующих недостатков. При тонком измельчении содержание пылевидной фракции составляет до 30%, при грубом получается до 20% недоизмельченной фракции. Это приводит к повышению энергоемкости процесса измельчения и ухудшению качества готового продукта.
Теоретические исследования и традиционные конструктивные решения по данной проблеме не могут в полном объеме обеспечить коренное совершенствование технологического процесса. Поэтому исследования и разработка конструктивных решений, направленных на совершенствование рабочих органов с целью повышения качества готового продукта и снижения удельной энергоемкости в 1,5…2,0 раза, пылевидной фракции в 3…4 раза, являются актуальной проблемой и имеют важное народнохозяйственное значение.
Вытекающая из этого научно-техническая проблема заключается в создании научных основ разработки центробежно-роторных измельчителей фуражного зерна нового класса.
Научные исследования и разработки, выполненные в рамках решений данной проблемы, являются основой диссертационной работы, которая соответствует заданию раздела федеральной программы по научному обеспечению АПК РФ: шифр 01.02. «Разработать перспективную систему технологий и машин для производства продукции растениеводства и животноводства на период до 2015 г.» Межведомственной координационной программы фундаментальных и приоритетных прикладных исследований по научному обеспечению развития агропромышленного комплекса Российской Федерации на 2001-2005 гг., одобренной Президиумом Российской Академии сельскохозяйственных наук 18 октября 2001 г., а также межведомственным советом по формированию и реализации программы 31 октября 2001 г. и тематическим планам НИР ЧГАУ на 1993-2005 гг.
Цель исследований. Повышение эффективности процесса измельчения на основе изыскания рабочих органов и разработки методик расчета основных параметров измельчителей при их конструировании.
В соответствии с поставленной целью необходимо решить следующие задачи:
1. Разработать основные принципы и методы инженерных расчетов механико-технологических процессов измельчения семян рапса и фуражного зерна способом резания и скалывания в центробежно-роторных аппаратах.
2. Исследовать:
– закономерности динамического и кинематического взаимодействия зерновки с режущими элементами рабочих органов;
– зависимость длины канала рабочего органа центробежно-роторного аппарата от частоты вращения диска-ротора при рациональных скоростях резания и скалывания;
– зависимость усилия динамического резания целых зерен при различных углах заточки и защемления режущих элементов;
– зависимость модуля помола от количества режущих элементов измельчающих пар рабочих органов при рациональных скоростях динамического резания;
– зависимость модуля помола и удельной энергоемкости процесса измельчения от угловой скорости рабочих органов;
– износостойкость режущих элементов рабочих органов и дать рекомендации по их проектированию.
3. Установить зависимость модуля помола и удельной энергоемкости процесса измельчения от влажности зерна;
4. Создать центробежно-роторные измельчители разной производительности на основе оптимизации рабочих органов и технологии измельчения с учетом физико-механических свойств исходного материала.
5. Разработать опытные образцы измельчителей, провести производственные и государственные испытания, дать технико - экономическую оценку результатам исследований.
Объект исследований. Технологический процесс взаимодействия измельчающих элементов рабочих органов с перерабатываемым сырьем в измельчителе центробежно-роторного типа.
Предмет исследований. Закономерности, условия и режимы функционирования измельчителей, характеризующие процесс разрушения зерна способом среза и скалывания.
Методика исследований. Теоретические исследования выполнялись с использованием положений и законов классической механики, гидродинамики, математики и математического моделирования. Предложенные рабочие органы измельчителя испытывались в лабораторных и производственных условиях в соответствии с действующими ГОСТ, ОСТ и разработанными частными методиками. Результаты теоретических исследований подтверждены экспериментальной проверкой на физических моделях, лабораторных и опытно-производст-венных установках. Сходимость результатов теоретических и экспериментальных исследований составила не менее 90%, погрешность опытов - не более 5%. Обработка результатов экспериментальных исследований осуществлялась на ПЭВМ с использованием пакетов программ Statistica, MathCAD, Excel. Достоверность результатов работы подтверждается сходимостью результатов теоретических и экспериментальных исследований.
Научная новизна
1. Установлены закономерности динамического и кинематического взаимодействия семян и зерна с режущими элементами рабочих органов центробежно-роторного измельчителя, при этом срез (скалывание) происходит поперек зерна по минимальному сечению, что соответствует теории резания В.П. Горячкина.
2. Впервые получена система дифференциальных уравнений, описывающая поступательное и вращательное движение зерна в канале рабочего органа центробежно-роторного измельчителя.
3. Впервые в центробежно-роторных аппаратах применен способ резания и скалывания для измельчения семян рапса и фуражного зерна, обеспечивающий получение готового продукта высокого качества;
4. Разработаны модели и методика расчета рациональных параметров рабочих органов измельчителя.
5. Обоснованы конструктивные параметры измельчающих элементов рабочих органов центробежно-роторного измельчителя.
6. Получены следующие научные результаты:
– процесс измельчения зернового материала осуществляется с минимальным удельным расходом энергии;
– изыскана возможность измельчения семян масличных и высокобелковых культур (рапса, горчицы, расторопши, кориандра, амаранта, сои, гороха, и др.) с получением готового продукта без выделения жира и с хорошей сыпучестью;
7. Разработаны научные основы создания и проектирования центробежно-роторных измельчителей для переработки фуражного зерна и семян масличных культур.
8. Разработана методика инженерных расчетов рабочих органов и конструктивно-технологических параметров центробежно-роторных измельчителей нового класса.
Научная новизна и достоверность результатов работы подтверждены 18 авторскими свидетельствами и патентами на изобретения, результатами производственных и государственных испытаний, на базе которых созданы высокоэффективные центробежно-роторные измельчители фуражного зерна и семян масличных культур, позволяющие существенно снизить удельную энерго- и металлоемкость процесса измельчения.
Практическая ценность. Обобщена и развита теория и практика разрушения зерна способом резания и скалывания, разработаны механико-технологические основы создания и проектирования измельчителей центробежно-роторного типа, позволяющие обеспечить получение готового продукта зоотехнически требуемого качества с одновременным снижением пылевидной фракции в 3…4 раза, удельной энерго- и металлоемкости в 1,5…2,0 раза по сравнению с существующей технологией измельчения фуражного зерна. Впервые получена возможность измельчения семен масличных культур, в частности рапса, с жирностью до 50%, без выделения жира. Результаты исследований позволят ускорить разработку современного энергосберегающего оборудования для комбикормового производства.
Разработанные образцы измельчителей прошли производственную проверку и актами хозяйственных комиссий рекомендованы к внедрению, что является основой для создания новых машин и оборудования для измельчения фуражного зерна, семян масличных культур и других сыпучих материалов.
Реализация результатов исследований. Разработанная методика инженерных расчетов основных параметров центробежно-роторных измельчителей и техническая документация на их изготовление переданы на заводы Кировской области – ПО «Кировагропромремонт», г. Киров, АОЗТ «Нолинский ремонтно-механический завод», г. Нолинск; Челябинской области – АОЗТ «Агромаш», г. Челябинск, ФГУП «Приборостроительный завод», г. Трехгорный.
Опытные образцы измельчителей прошли производственную проверку и государственные испытания на Кировской МИС в г. Кирове, Поволжской МИС г. Кинеле и Центре сертификации электрооборудования АООТ «Электропривод» в г. Москве.
С 1990 года заводами Челябинской и Кировской областей выпущено более 5000 штук измельчителей четырех модификаций производительностью от 0,1 до 5,0 т/ч (ИЛС-0,1; ИЛС-0,15; ИЛС-0,5; ИЛС-5,0). В 1999 году измельчители включены в Систему технологии машин, в 2000 году – в каталоги «Машины и оборудование для АПК». Они нашли применение в сельском хозяйстве, пищевой, строительной, перерабатывающей и других отраслях народного хозяйства.
Результаты научной работы используются в учебном процессе агроинженерных факультетов вузов Минсельхоза России. Отдельные разделы диссертационной работыиспользуются преподавателями, аспирантами и студентами в качестве учебно-методического материала. Промышленные образцы центробежно-роторных измельчителей ИЛС изучаются студентами и слушателями факультетов повышения квалификации.
На защиту выносятся следующие основные положения:
– научные основы расчета и проектирования центробежно-роторных измельчителей для переработки фуражного зерна и семян масличных культур;
– методика инженерных расчетов рабочих органов и конструктивно-технологических параметров центробежно-роторных измельчителей нового типа;
– результаты экспериментальных исследований по оптимизации геометрических параметров рабочих органов и конструктивно-технологической схемы измельчителя;
– новые технологические и технические решения по созданию машин и оборудования для измельчения фуражного зерна, семян рапса, горчицы, расторопши, кориандра, амаранта и других культур;
– результаты энергетической и экономической оценки энергосберегающего процесса измельчения фуражного зерна и семян масличных культур.
Апробация. Основные положения работы и результаты исследований доложены и одобрены на научно-технических конференциях Челябинского ГАУ и Свердловской ГСХА (1989...2007 гг.), семинаре заведующих кафедрами МЖ в МИИСП (2002 г.), 9-й международной научно-практической конференции ВНИИМЖ (2006 г.), научно-технических советах: ПО «Кировагропромремонт», АООТ «Нолинский ремонтно-механический завод» Кировской области (1989, 1991гг.); «Приборостроительный завод» г.Трехгорный (1992, 1996, 1998 гг.), завод «Агромаш» Челябинской области (1992...1995 гг.). Опытные образцы центробежно-роторных измельчителей демонстрировались на ВДНХ СССР (1988, 1989 гг.), где были награждены тремя золотыми и одной серебряной медалями, на агропромышленной выставке в городе Львове (1992 г.), региональной выставке-ярмарке «Урал-конверсия, наука, бизнес-94» в городе Екатеринбурге (1994 г.), на VI Московском международном салоне инноваций и инвестиций ВВЦ (2006 г.), международной выставке-ярмарке «Лучшее оборудование и технологии для малого бизнеса» ВВЦ (2006 г.), 7-й специализированной выставке «Изделия и технологии двойного назначения. Диверсификация ОПК» ВВЦ (2006 г.), международной выставке «Агро-2006» в городе Челябинске, где были также награждены дипломами и медалями.
Публикации. Основные положения диссертационной работы изложены в 65 научных работах, в том числе 11, опубликованы в изданиях рекомендованных ВАК. Новизна технических решений защищена 18 авторскими свидетельствами и патентами на изобретения.
Структура и объем работы. Диссертация состоит из введения, пяти глав, общих выводов, списка литературы и приложений. Объем диссертации 315 стр., в том числе 258 стр. основного текста, 102 рисунка, 32 таблицы; список литературы включает в себя 250 наименований, в том числе 11 на иностранных языках.
СОДЕРЖАНИЕ РАБОТЫ
Введение. Дана общая характеристика рассматриваемой проблемы. Кратко изложена актуальность работы, сформулированы научная проблема, цель и объект исследования, научная новизна и основные положения, выносимые на защиту. Приведены сведения об апробации и внедрении результатов работы.
Глава 1. Состояние проблемы по измельчению фуражного зерна и задачи исследований. Рассмотрены требования, предъявляемые к техническим средствам по измельчению фуражного зерна и качеству получаемого продукта, кратко изложены способы механического измельчения, приведены классификация измельчающих машин, критический анализ результатов научных исследований физико-механических свойств фуражного зерна и конструктивных особенностей технических средств по его разрушению, а также намечены пути по совершенствованию рабочих органов измельчающих устройств с целью повышения качества готового продукта и снижения удельной энерго- и материалоемкости рабочего процесса. Сформулированы цель и задачи исследований.
Научными основами процессов приготовления кормов, теории резания, измельчения являются труды академика В.П. Горячкина. Исследованиями связи между затратами энергии и характеристиками измельчаемого продукта занимались П.Р. Риттингер, В.А. Кирпичев, Ф. Кик, Л.Б. Левенсон, П.А. Ребиндер, Г. Румпф, Е.М. Гутьяр, А.А. Гриффитс и другие. Совершенствованию отдельных технологических процессов и оборудования, связанных с механической обработкой компонентов комбикормов, посвящены исследования А.Я. Соколова, Г.И. Бремера, В.И. Сыроватки, Л.А. Глебова, С.В. Мельникова, В.А. Сысуева и других ученых.
Существенный вклад в теорию измельчения кормов внесли И.Ф. Василенко, Н.В. Сабликов, В.И. Сыроватка, А.А. Артюшин, В.А. Елисеев, А.А. Зеленов, А.П. Макаров, Я.Н. Куприц, С.Д. Хусид, С.В. Мельников, В.А. Сысуев, В.Г. Коба, В.И. Пахомов, П.И. Некрашевич, А.А. Омельченко, П.И. Леонтьев, П.А. Савиных, В.Р. Алешкин, Б.И. Вагин, А.И. Завражнов, В.И. Земсков, В.А. Зяблов, П.А. Кормщиков, Г.М. Кухта, Е.А. Маркарян, П.М. Рощин, Н.В. Сундеев, И.Я. Федоренко, В.Д. Денисов, С.В. Золотарев и другие ученые.
Большое количество исследований посвящено совершенствованию энергетической и экономической оценок технологических процессов в животноводстве. Из них существенное значение имеют работы Н.В.Брагинца, М.И. Искандаряна, Л.П. Карташова, В.А. Сысуева, П.А. Савиных, В.А. Коновалова, А.И. Купреенко, В.В. Лазовского, Н.М. Морозова, Д.Н. Мурусидзе, Ю.Ф. Новикова, Ю.В. Пануса, Е.М. Клычева, С.Г. Карташова.
Обзор и анализ исследований и разработок по механизации приготовления зерновых кормов и кормовых смесей показали следующее:
- результаты исследований отечественных и зарубежных ученых в области кормления сельскохозяйственных животных, проведенных в последние годы, указывают на возможность повышения эффективности скармливания кормов за счет улучшения фракционного состава измельченного зерна для каждого вида и возраста животных. За счет оптимизации технологических параметров измельчителей;
- применяемые схемы технологии измельчения и конструкции зернодробилок не в полной мере обеспечивают получение готового продукта, удовлетворяющего зоотехническим требованиям и нормам по содержанию пылевидной фракции, гранулометрическому составу, и имеют большую удельную энергоемкость и материалоемкость;
- роторные и ударно-центробежные дробилки, дезинтеграторы и дисмембраторы представляют собой новый тип измельчающего оборудования, обладают высокими показателями при измельчении хрупких сыпучих материалов, однако процесс измельчения зерна в них изучен недостаточно, отсутствуют методики расчета конструктивно-технологических параметров и режимов их работы.
Анализ состояния научно-технической проблемы позволил сформулировать цель и задачи для её решения.
Глава 2. Теоретический анализ способов измельчения и обоснование высокоэффективных измельчающих устройств. На процесс измельчения существенное влияние оказывают влажность, температура, физико-механические свойства зерна и др. Немаловажное значение имеют состояние, вид и конструктивные параметры рабочих органов измельчающих машин, способ подвода исходного материала в зону измельчения и отвода готового продукта и т.п. В связи с этим разработана классификационная схема основных факторов, влияющих на эффективность работы центробежно-роторного измельчителя фуражного зерна (рисунок 1). В центробежных, роторных и центробежно-роторных измельчающих устройствах на эффективность измельчения большое влияние оказывают удельные нагрузки и окружные скорости рабочих органов.
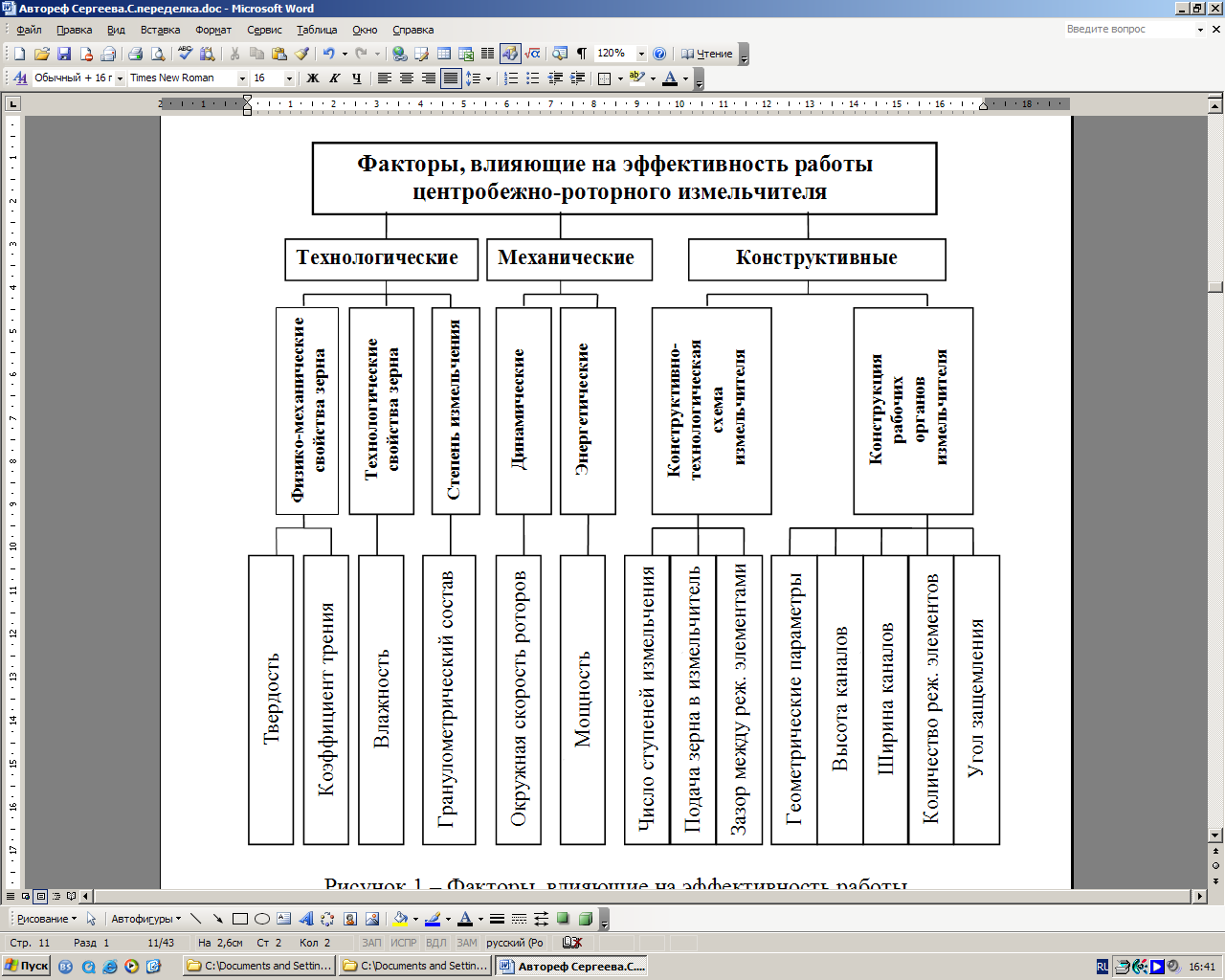
Рисунок 1 – Факторы, влияющие на эффективность работы
центробежно-роторного измельчителя
Значительное количество переменных факторов, влияющих на процесс измельчения, настолько осложняет всю проблему в целом, что решить ее можно простейшими частными случаями и то при определенных допущениях. На эффективность работы центробежно-роторных измельчителей фуражного зерна существенное влияние оказывает ориентация зерна в канале рабочего органа по отношению к кромкам режущих элементов. Для этого было исследовано движение частицы, а затем эллипсоида вращения по поверхности плоскости с вертикальной осью вращения. На зерно при движении по диску-ротору вдоль стенки канала (лопатки) действуют: сила тяжести
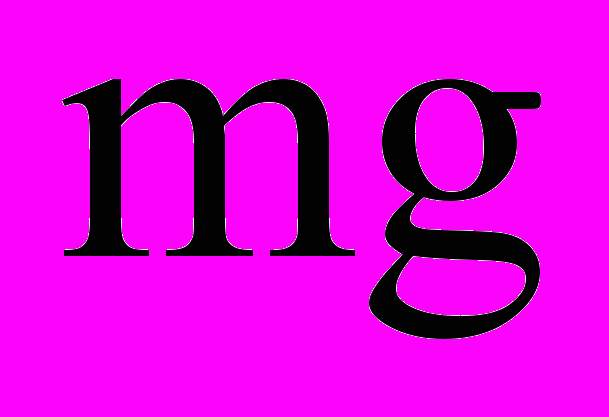

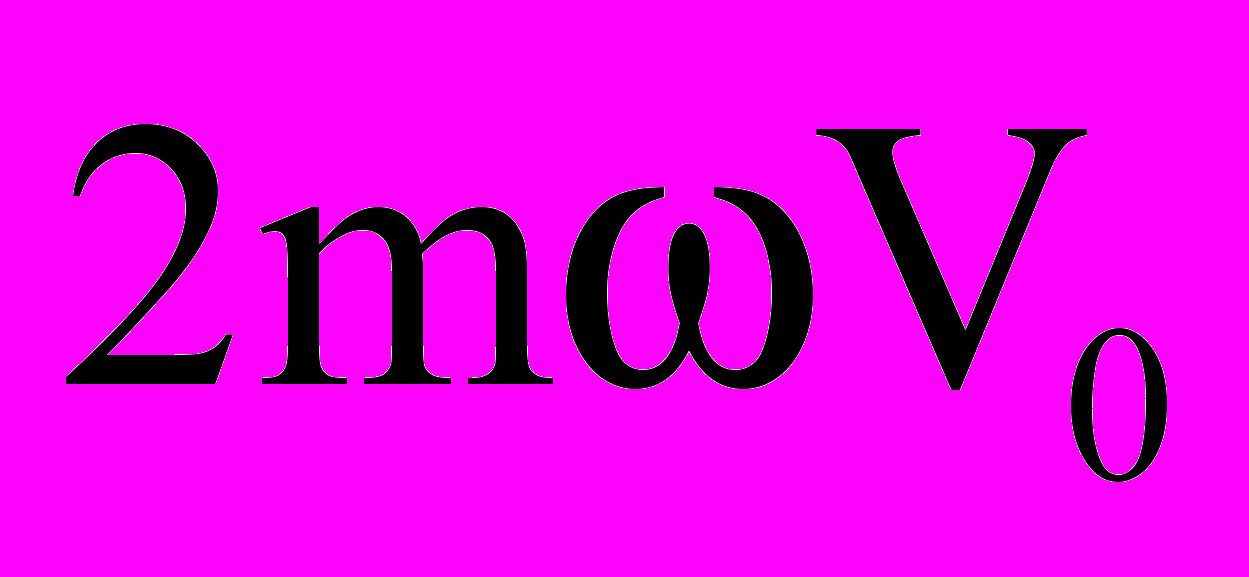
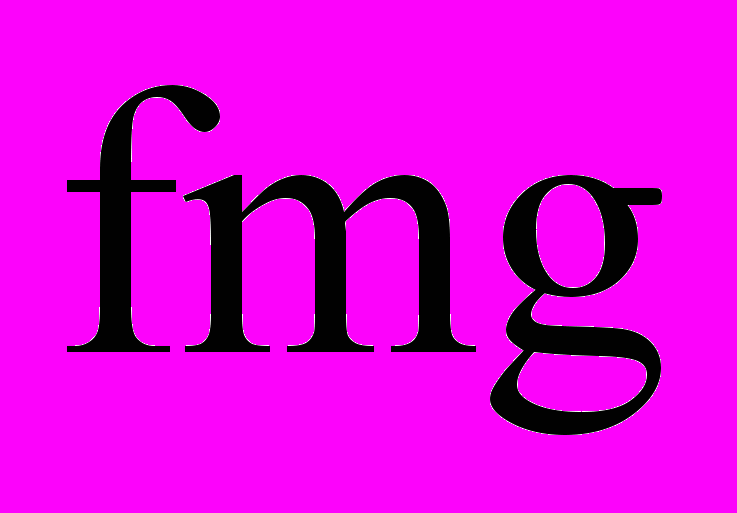
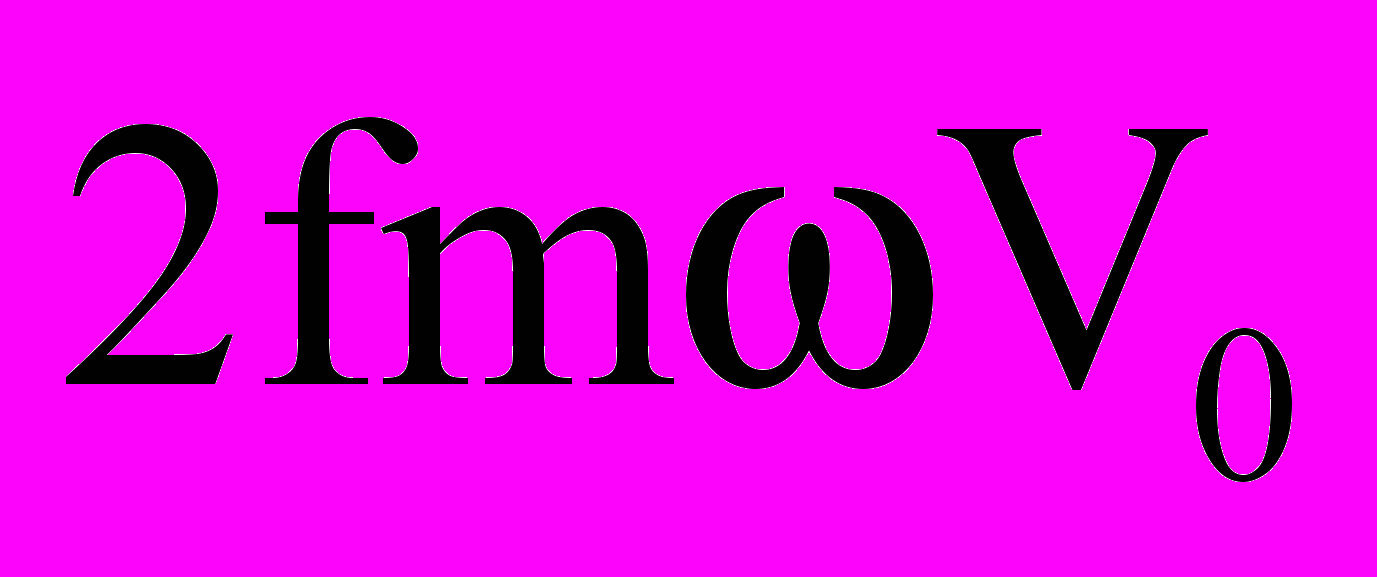
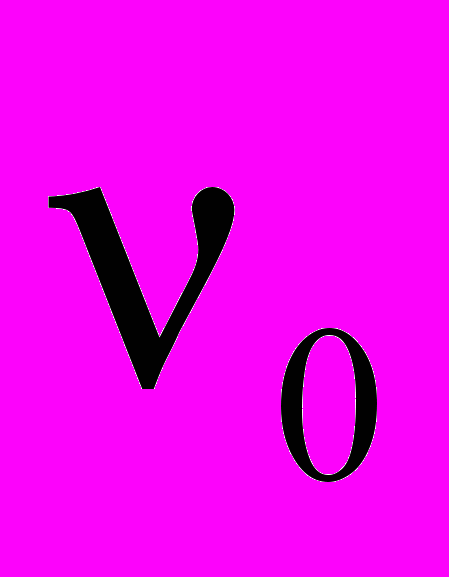
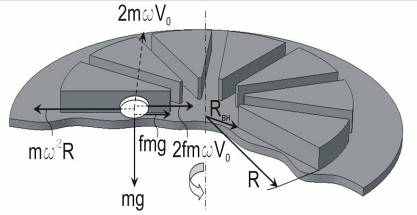
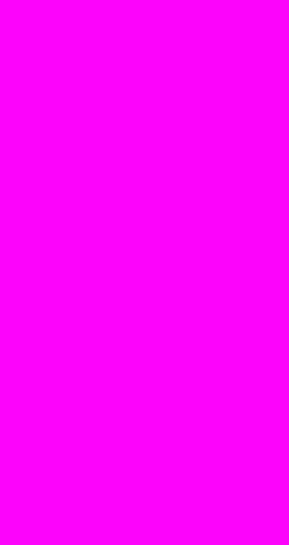
Рисунок 2 – Схема движения зерна вдоль
стенки канала диска ротора
Для обоснования конструктивно-технологической схемы центробежно-роторного измельчителя выполнено следующее.
1. Предложена система дифференциальных уравнений по расчету оптимальной длины канала рабочего органа (1)-(3). В качестве модели зерна рассматривается трехосный эллипсоид (рисунок 3).
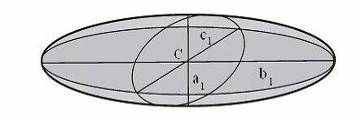
Рисунок 3 - Модель зерна: a1 – длина малой полуоси, мм;
c1– длина средней полуоси, мм; b1 – длина большой полуоси, мм;
с – центр тяжести
Для упрощения решения поставленной задачи приняты следующие допущения: зерно касается поверхности диска-ротора в точке, где его малая полуось касается плоскости диска и остается перпендикулярной к этой плоскости; зерно не вращается относительно своей продольной оси Х1 (рисунок 4).
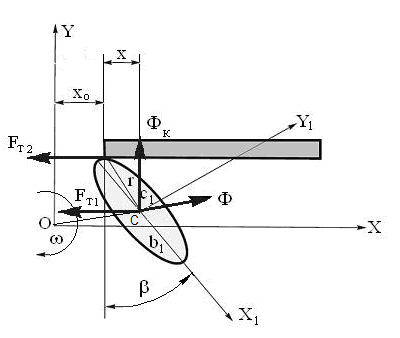
Рисунок 4 - Модель движения зерна вдоль стенки канала
рабочего органа:
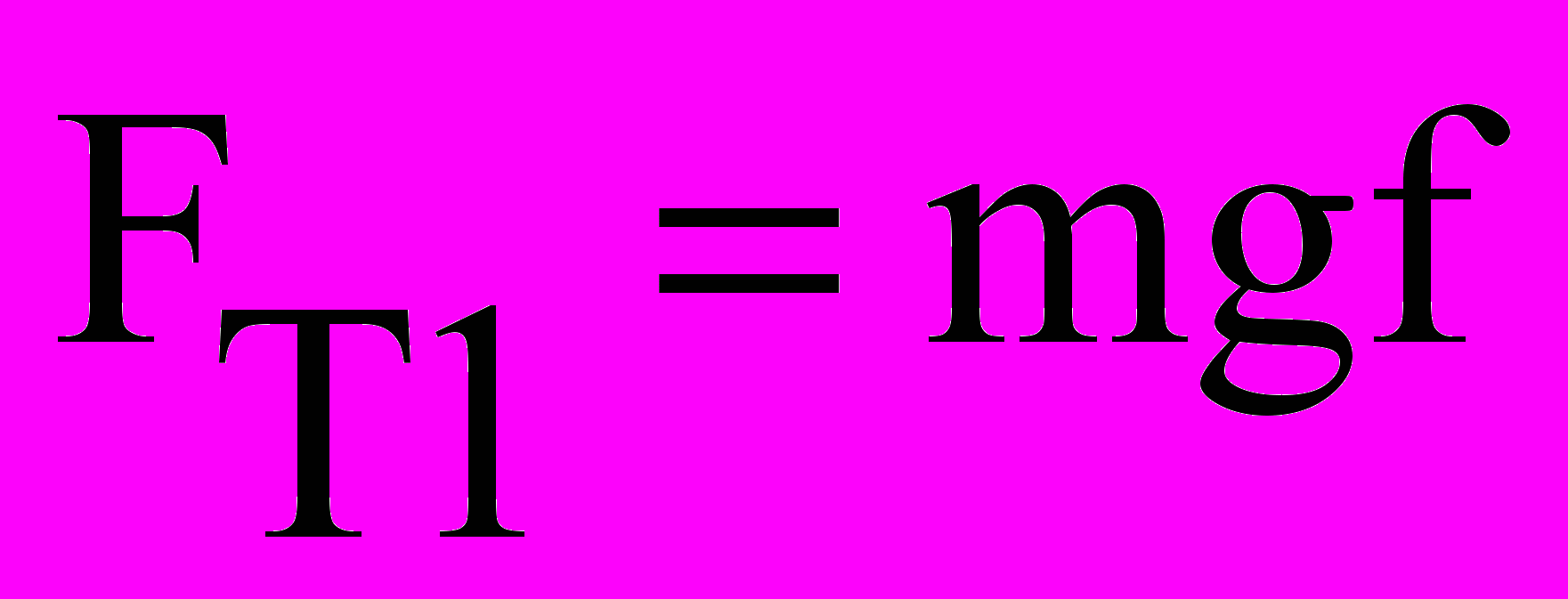
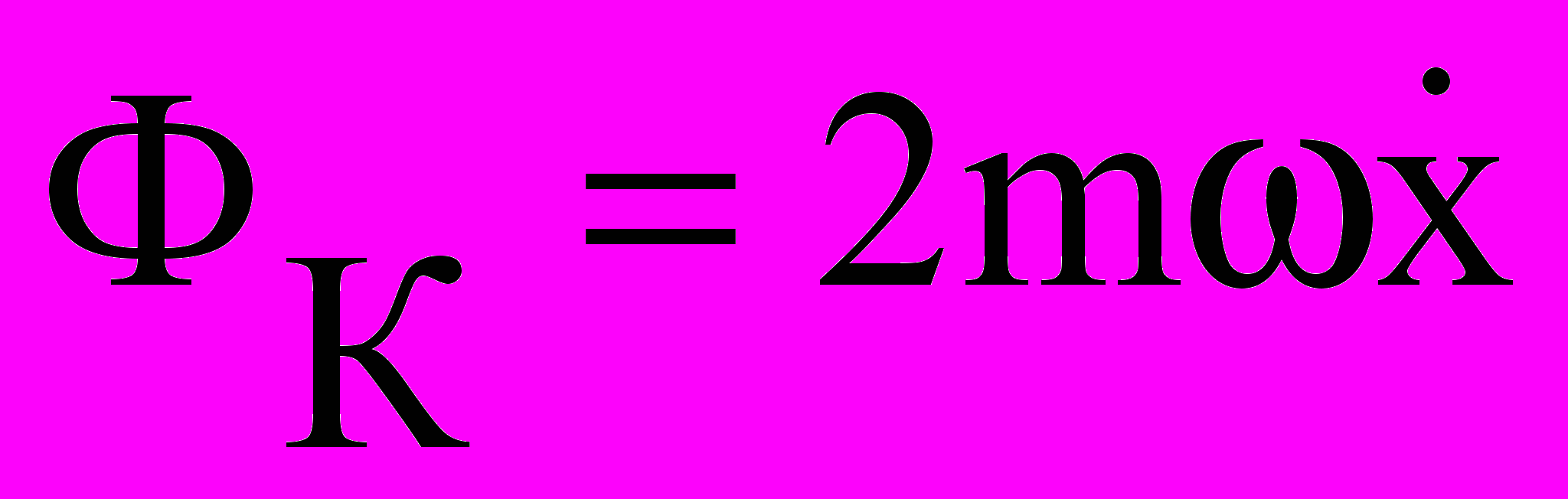
Кориолисова сила инерции;
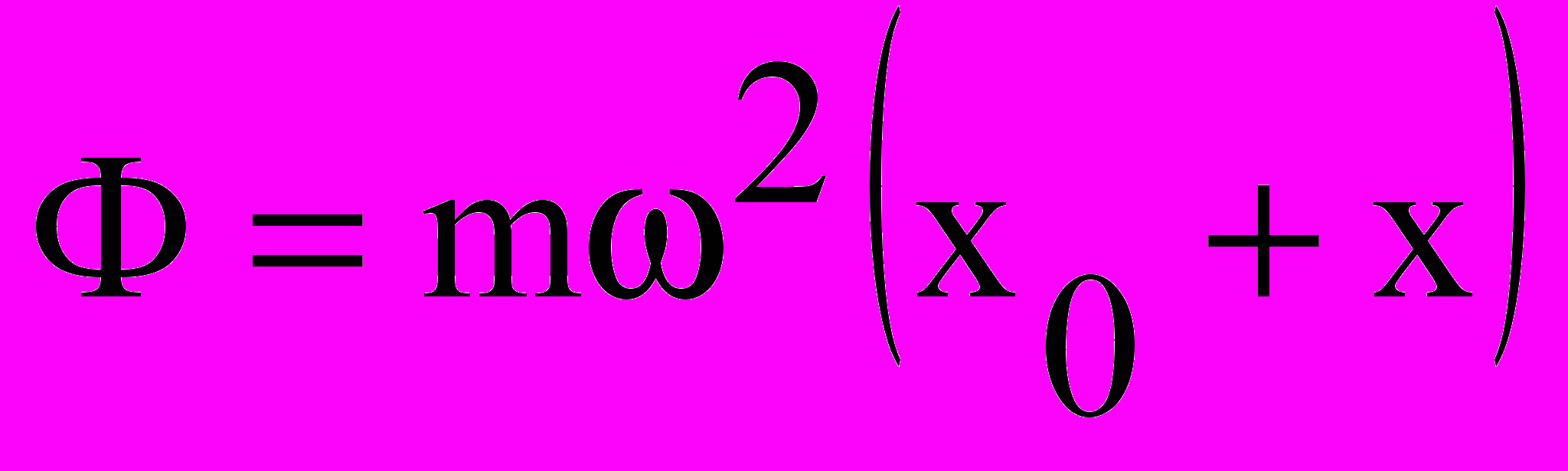
инерции;
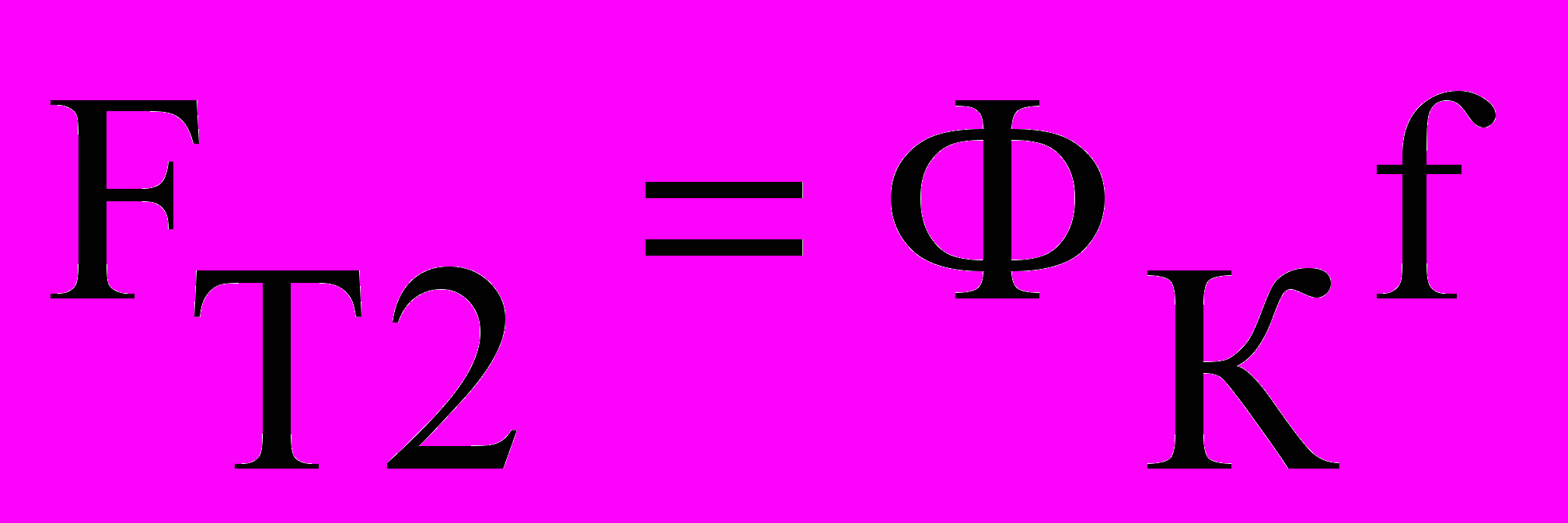
Система дифференциальных уравнений, описывающих положение зерна в канале рабочего органа центробежно-роторного измельчителя (рисунок 4), имеет следующий вид:
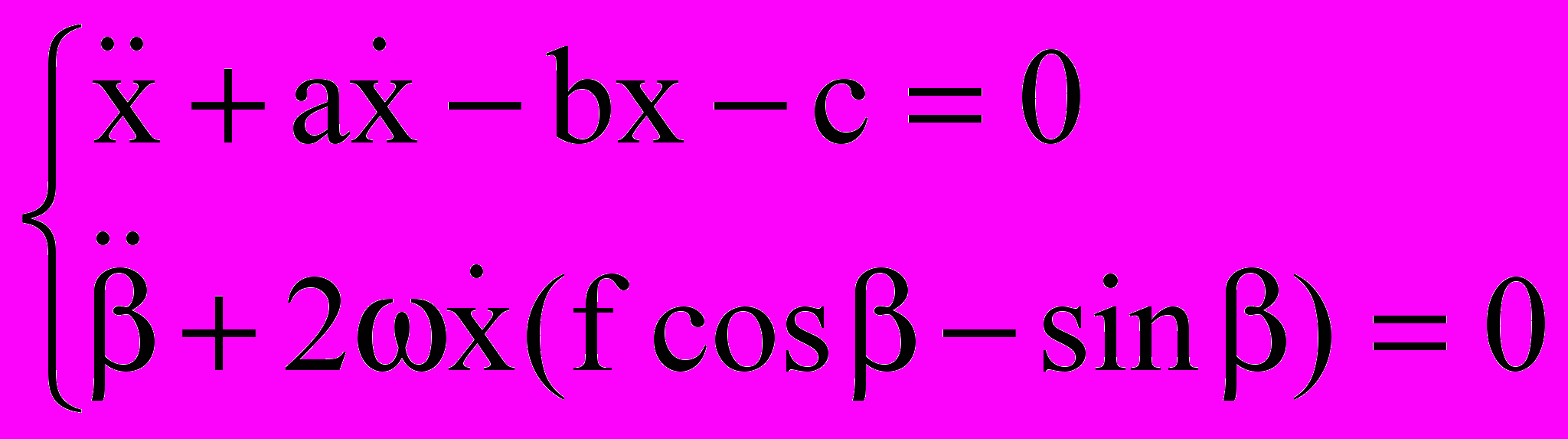
где a, b, c, d - постоянные коэффициенты связи дифференциального уравнения;

где n – частота вращения диска-ротора, мин-1;
f – коэффициент трения зерна по поверхности диска-ротора;
ω – угловая скорость вращения диска-ротора;
хо – начальное положение зерна на диске-роторе (минимальный радиус до начала канала);
g – ускорение силы тяжести;
β – угол поворота оси X1 зерна относительно оси Y;
Связь эллипсоида с поверхностью стенки канала выражается зависимостью
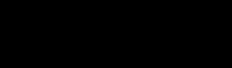
где
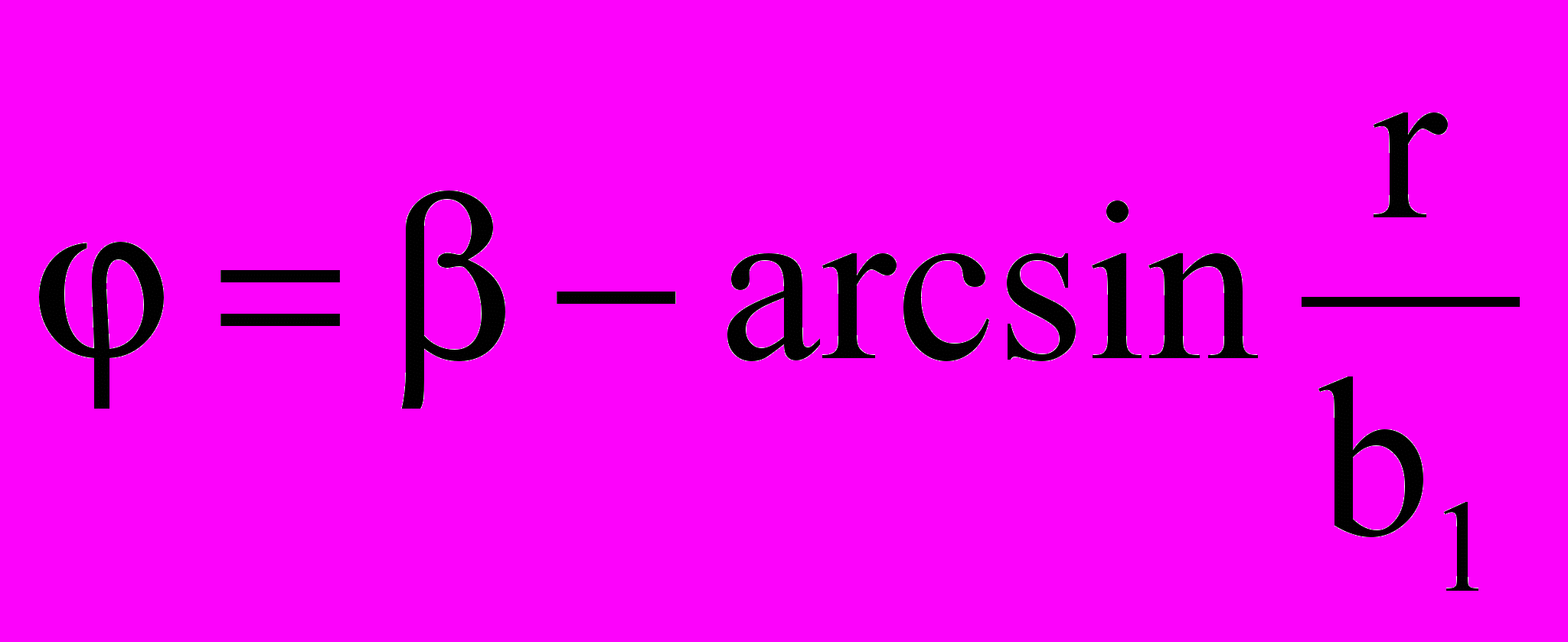
При r = с1 углы φ=90º; β=90º; ось Х1 занимает положение параллельно оси Х.
Уравнения движения зерна в канале рабочего органа центробежно-роторного измельчителя позволяют определить длину канала, необходимую для подачи зерна длинной осью к плоскости резания.
Решение дифференциальных уравнений выполнено численным методом. Теоретические исследования проводились для различных зерновых материалов (ячмень, пшеница, овёс, рапс) с учётом кинематических и конструктивных параметров канала диска-ротора рабочих органов измельчителя. По полученным результатам построены графические зависимости (рисунки 5, 6).
По результатам графических зависимостей длины канала от частоты вращения диска-ротора при скорости резания от 20 до 35 м/с с максимальными геометрическими размерами зерна и расстояния от оси вращения диска-ротора до начала канала рабочих органов (R1=20 мм; R2=70 мм; R3=120 мм), на первой режущей паре оптимальная длина каналов должна составлять: L1=8 мм; L2=12 мм; L3=16 мм.
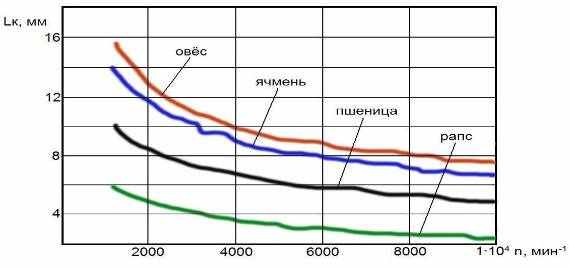
Рисунок 5 – Зависимость длины канала рабочего органа
от частоты вращения диска-ротора при скорости резания 20 м/с
с максимальными размерами зерна
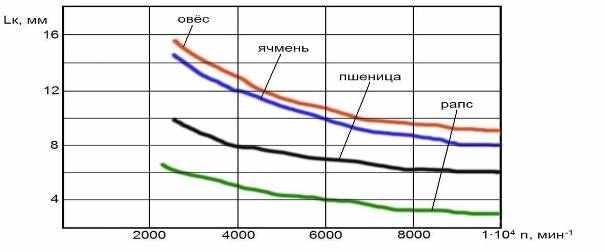
Рисунок 6 – Зависимость длины канала рабочего органа
от частоты вращения диска-ротора при скорости резания 35 м/с
с максимальными размерами зерна
Зерно при движении в канале первой режущей пары рабочего органа центробежно-роторного измельчителя поворачивается, ориентируясь длинной осью вдоль стенки канала. Такое положение позволяет
осуществлять процесс среза и скалывания по минимальному сечению зерна, после чего отрезанная часть вновь поворачивается длинной осью в направлении движения, и процесс повторяется на следующих режущих парах.
2. Произведены выбор и обоснование конструктивных параметров рабочих органов измельчителя, обеспечивающих технологический процесс измельчения зерна посредством среза и скалывания.
Анализ значений геометрических параметров режущей пары для процесса измельчения показывает, что эти параметры удобно разделить на две группы: параметры в плоскости резания и параметры в плоскости, перпендикулярной к плоскости резания (рисунок 7).
а) ![]() | б) ![]() |
Рисунок 7 – Схемы режущей пары: а) – в плоскости резания; б) – в плоскости, перпендикулярной к плоскости резания |
К конструктивным параметрам режущей пары рабочих органов центробежно-роторного измельчителя относятся:
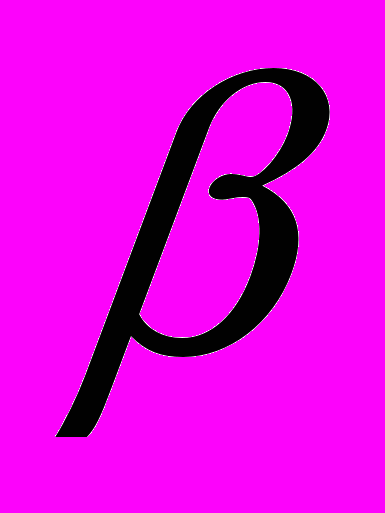
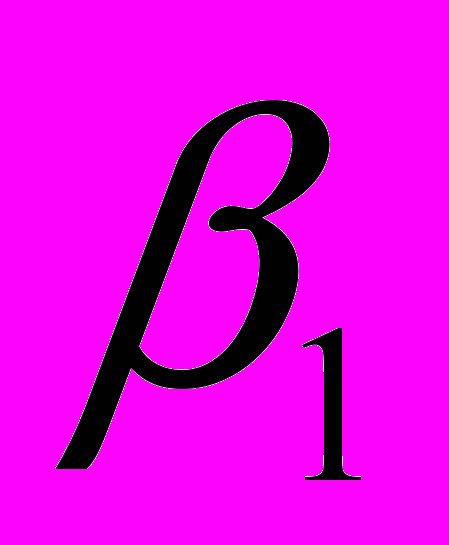
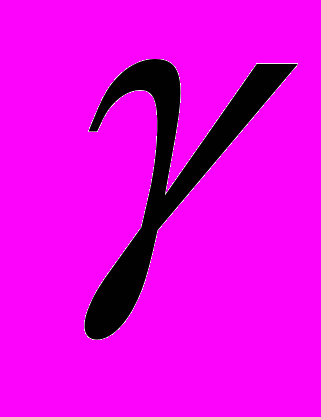



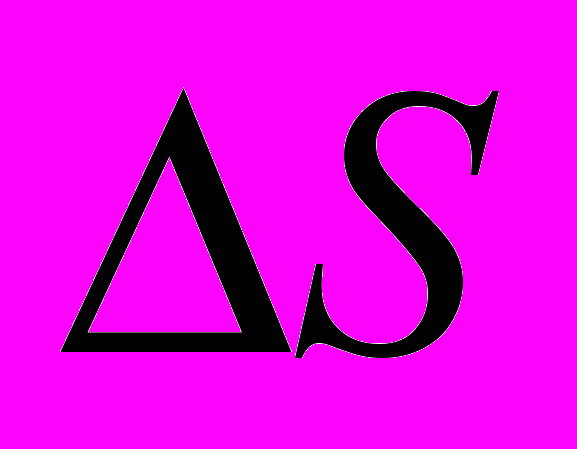
На рисунке 8 представлена принципиальная схема рабочих органов центробежно-роторного измельчителя.
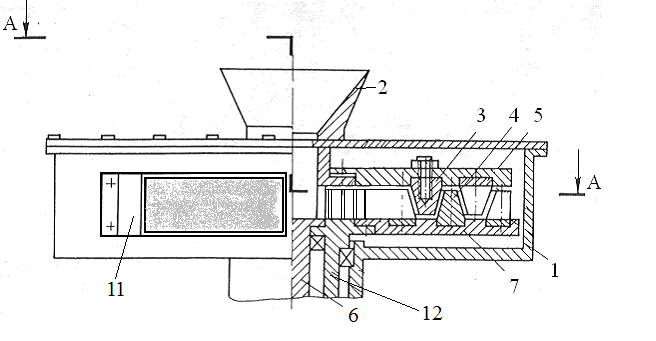
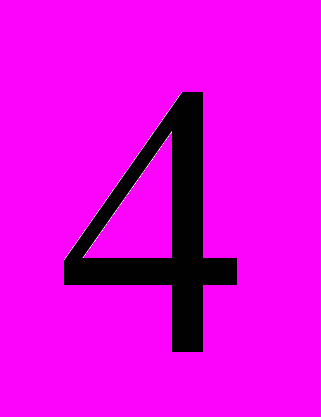
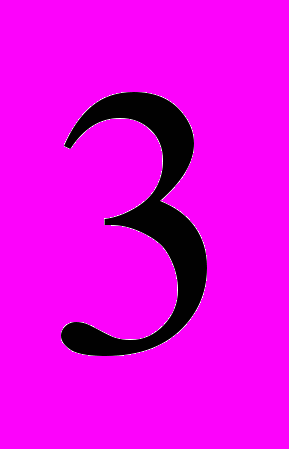

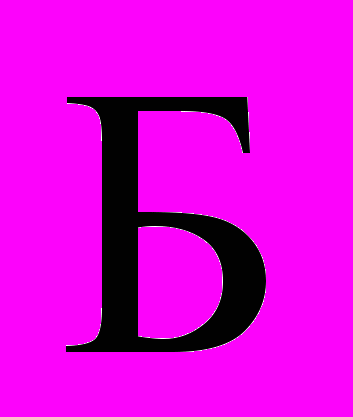
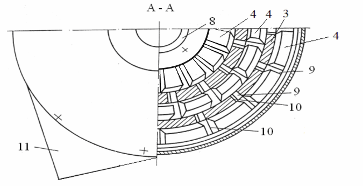
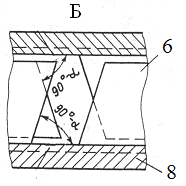
Рисунок 8 – Схема рабочих органов центробежно-роторного
измельчителя: 1 – корпус; 2 – патрубок загрузочный; 3, 4 – режущие
элементы; 5 – диск-ротор верхний; 6 – вал внутренний; 7 – диск-ротор нижний; 8 – окна радиальные; 9 – каналы (пазы); 10 – стенка канала;
11 – патрубок выгрузной; 12 – вал полый.
По теории резания В.П. Горячкина, для технологического процесса основными параметрами являются давление ножа (режущего элемента) на материал и боковое его движение. Количественное соотношение между двумя этими параметрами характеризуется значениями коэффициента скольжения и коэффициента трения лезвия ножа (кромки режущего элемента) о разрезаемый материал. При этом следует отметить важную роль угла защемления
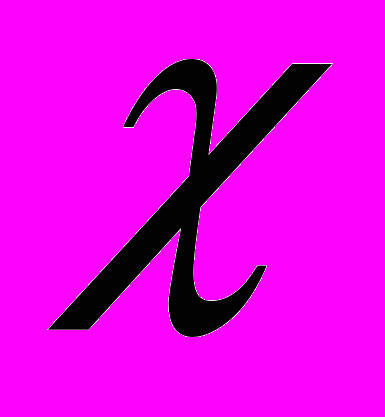
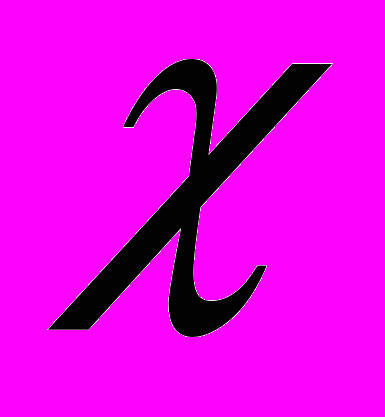
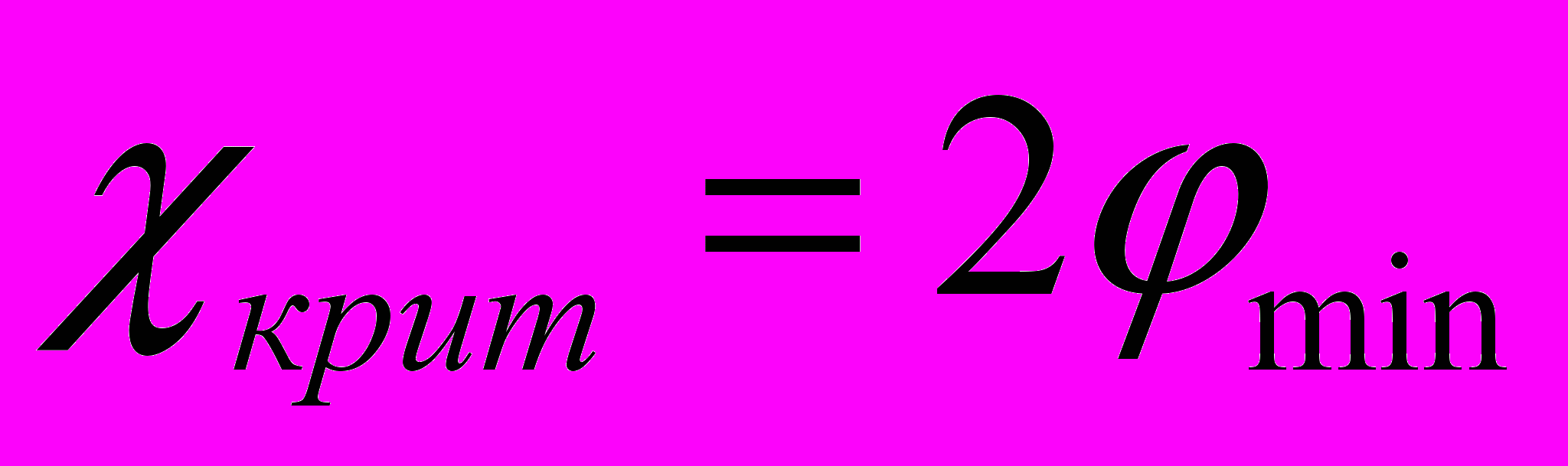
где
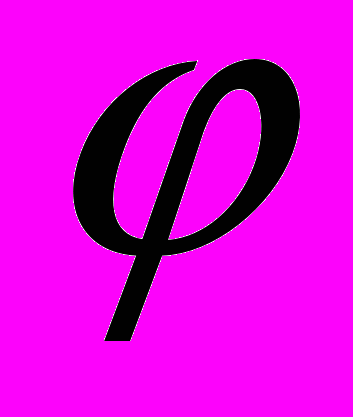
Допустимую величину угла защемления определяют опытным путем при различных условиях (тип режущего инструмента, его острота, физико-механические свойства измельчаемого материала и т.п.).
3. Предложена формула для определения оптимального количества режущих элементов (
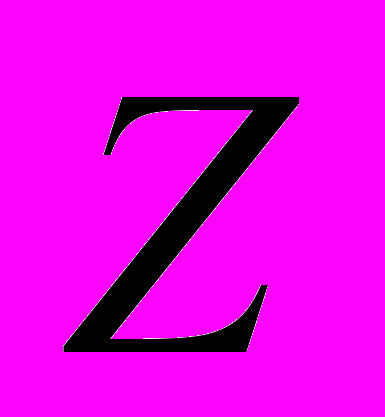
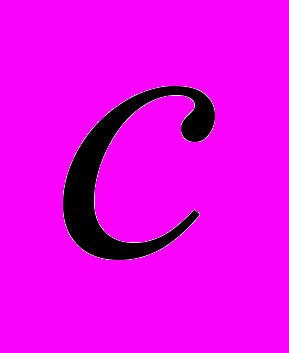

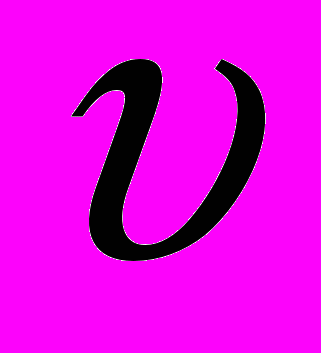

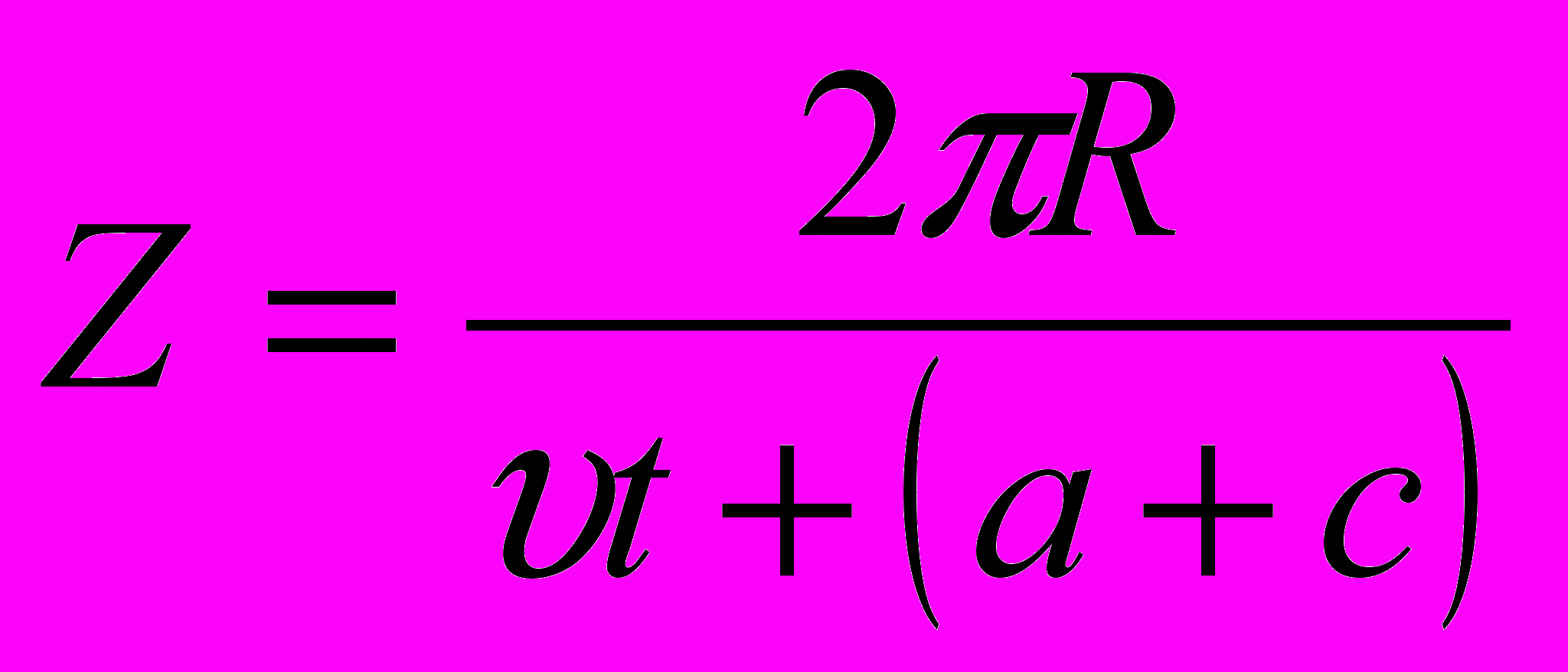
4. Разработана методика по определению производительности измельчителя. Производительность центробежно-роторного измельчителя зависит от того, какое количество зерна может пройти через радиальные сквозные каналы (пазы) первого кольцевого ряда, размещенного на диске-роторе рабочих органов, в единицу времени. Для определения времени движения (
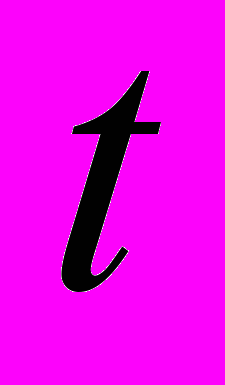
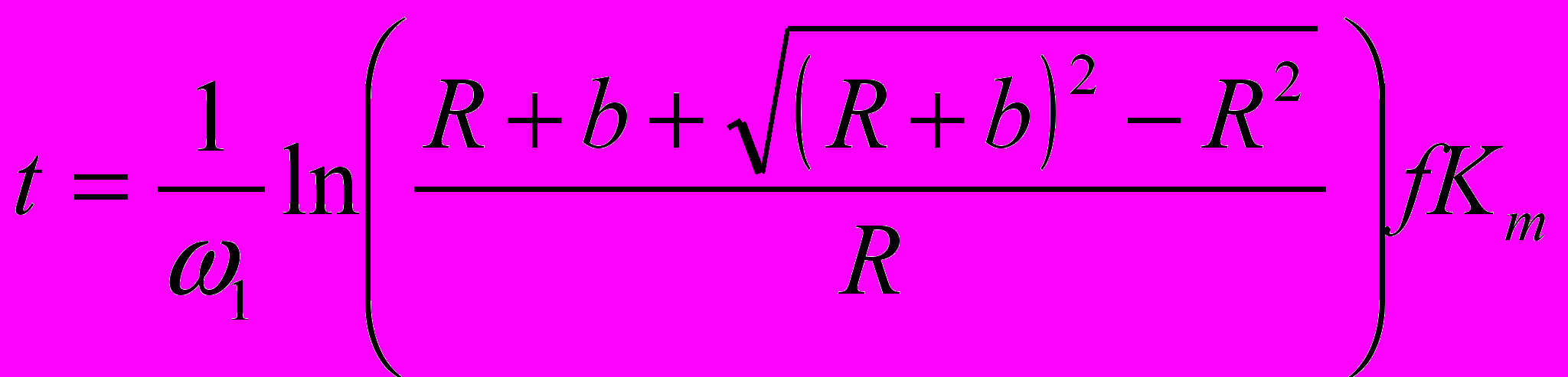
где
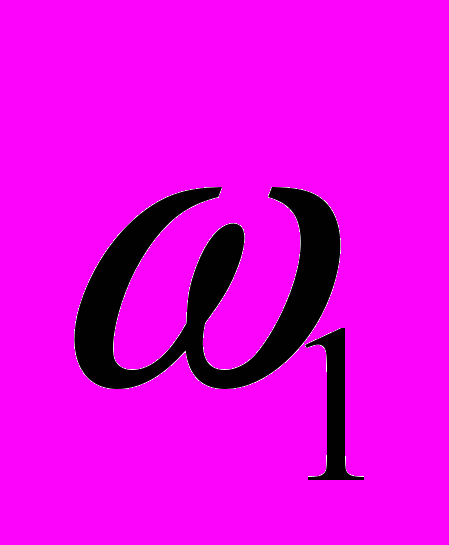
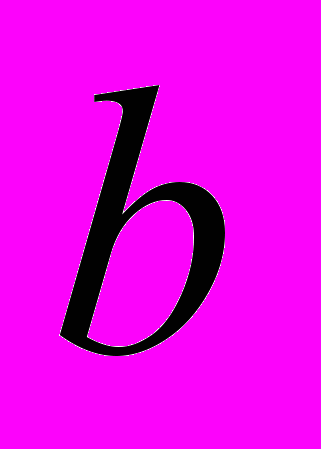
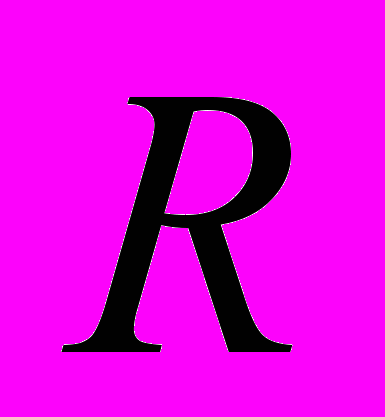
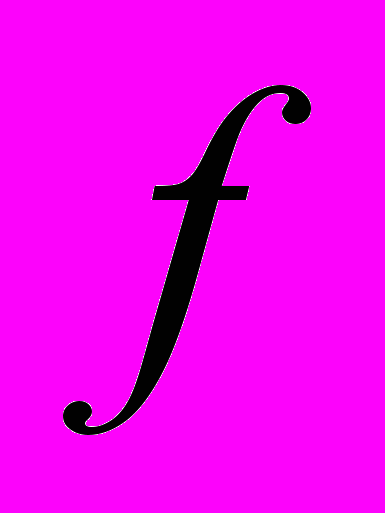
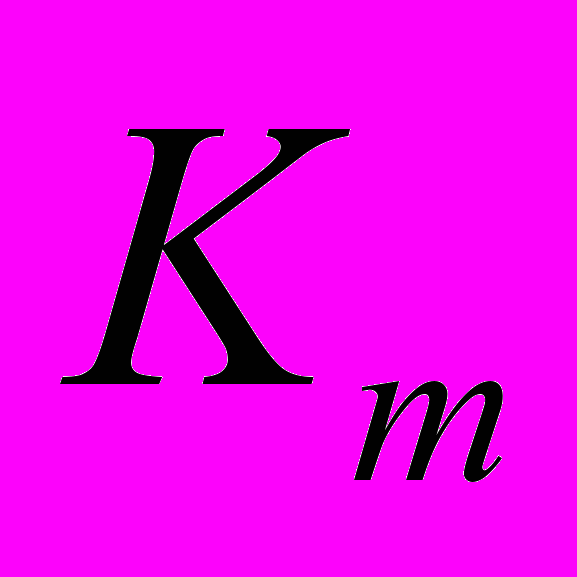
Количество радиальных каналов на первом кольцевом ряде
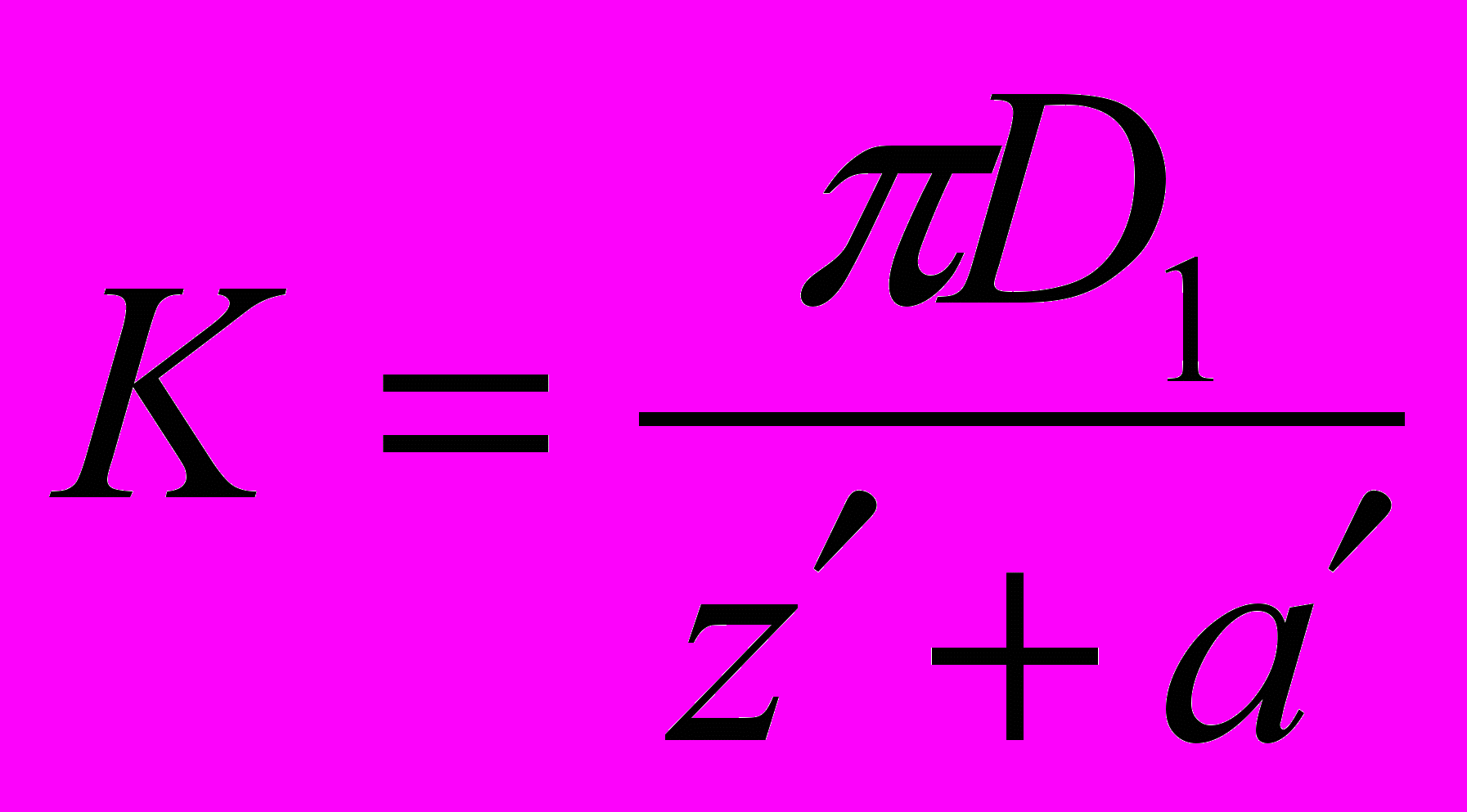
где
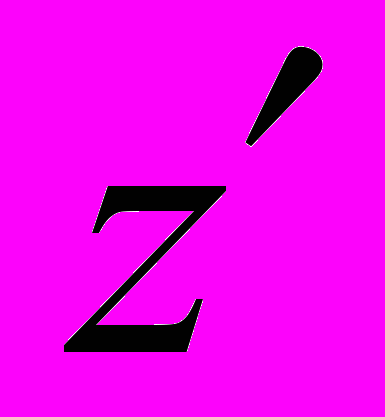
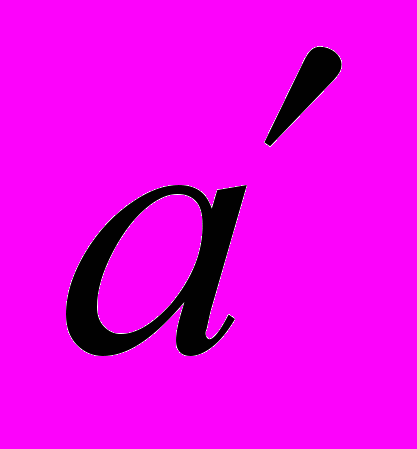
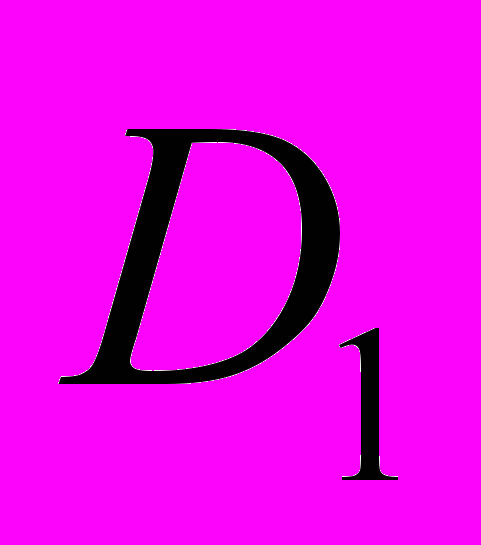
Пропускная способность первого кольцевого ряда, имеющего радиальные сквозные каналы (пазы), определяется по формуле
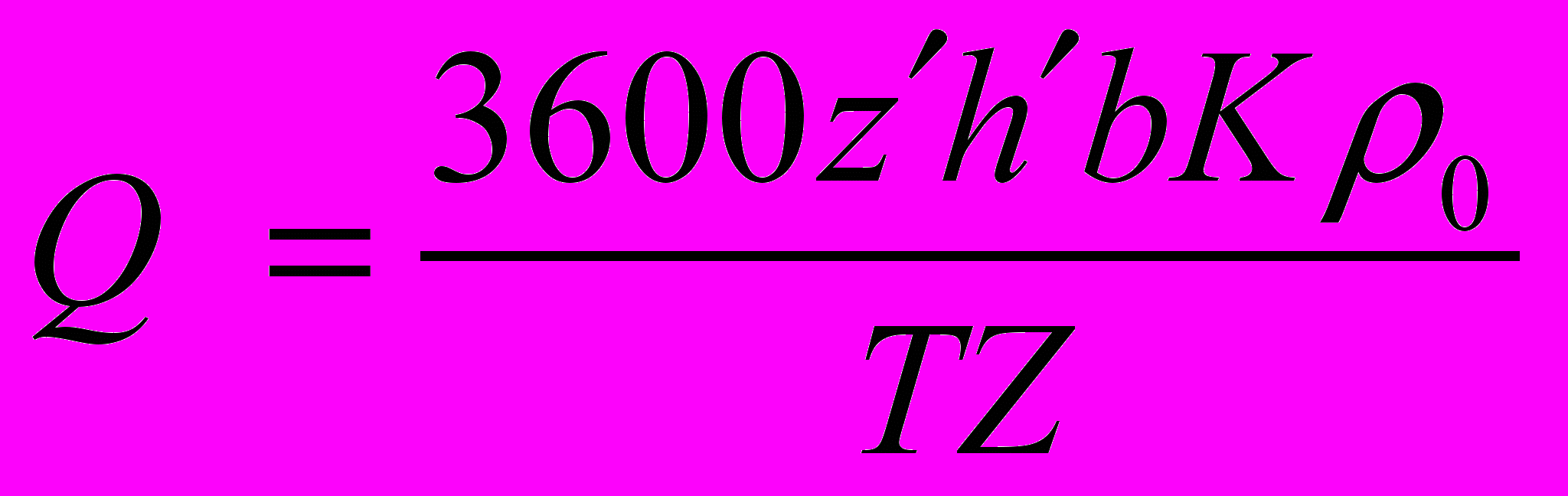
где
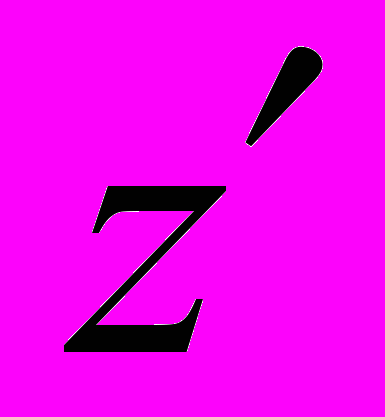
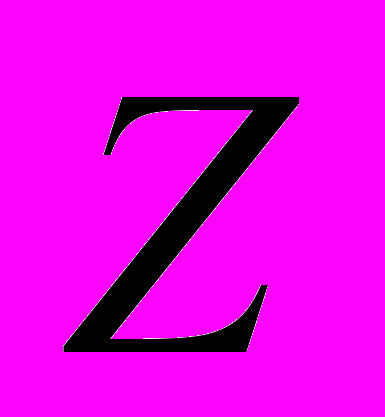
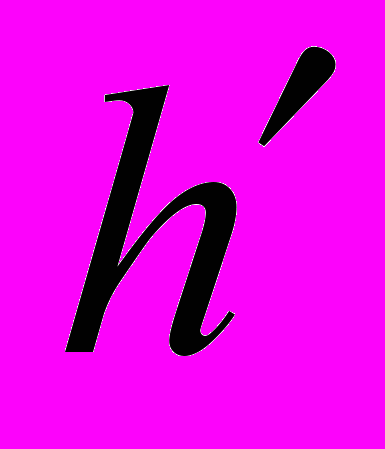
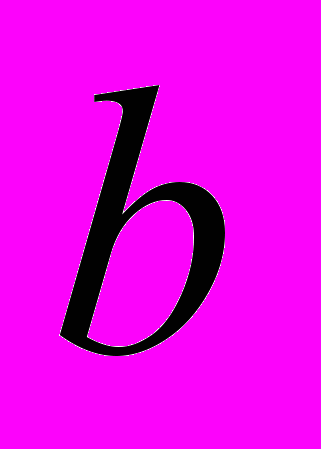

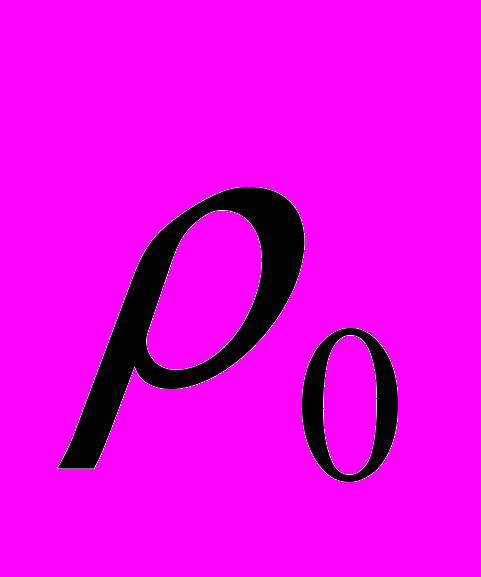
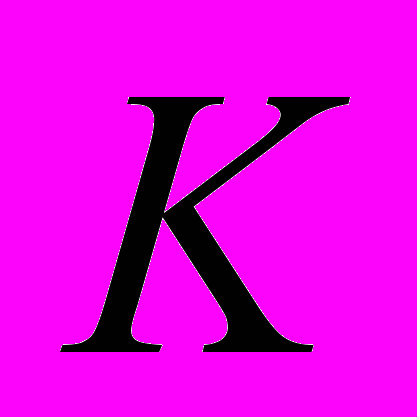
Пропускная способность последующих кольцевых рядов, имеющих радиальные сквозные каналы, можно определять аналогичным способом. Пропускная способность каждого последующего кольцевого ряда рабочих органов должна быть не меньше предыдущего, т.е.
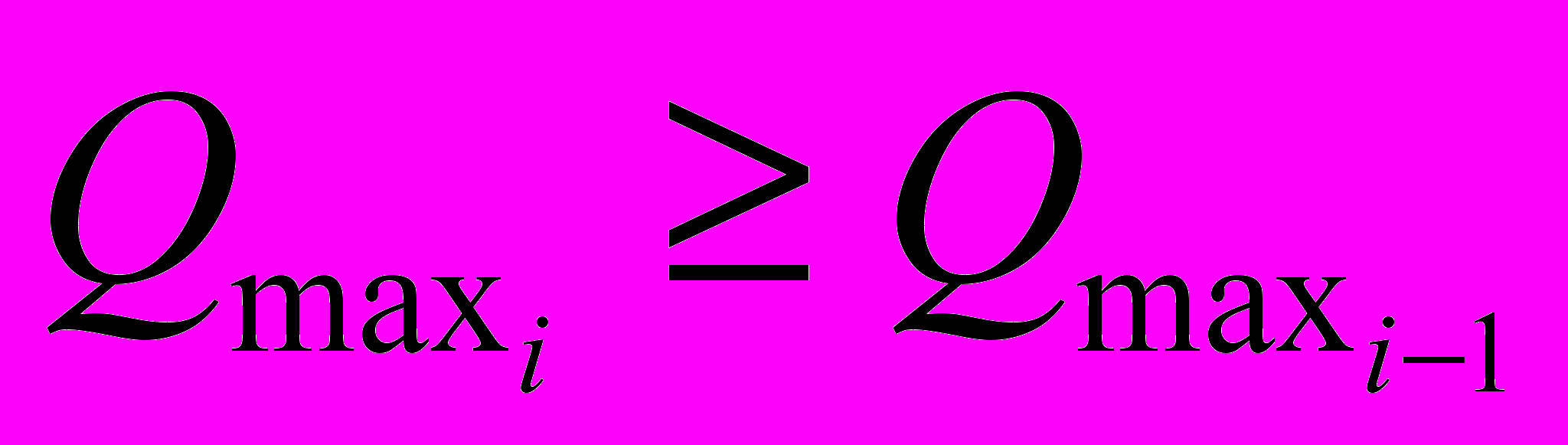
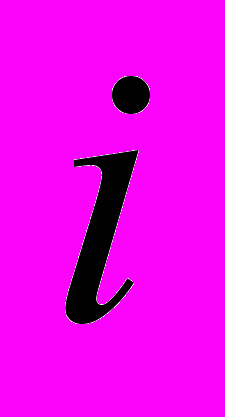
5. Предложена формула (9) по определению мощности, расходуемой на процесс измельчения с учетом особенностей конструкции рабочих органов измельчителя. Зерновой материал под действием центробежной силы движется по радиальным каналам рабочих органов. Во время совмещения каналов смежных кольцевых рядов встречно вращающихся дисков-роторов зерно продвигается на определенную величину и срезается кромками режущих элементов. Зная геометрическую форму поперечного сечения канала и количество в нем зерен, подлежащих одновременному срезу, можно определить потребную мощность:

где
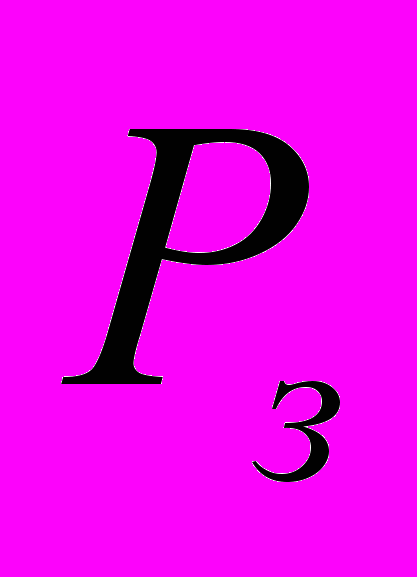
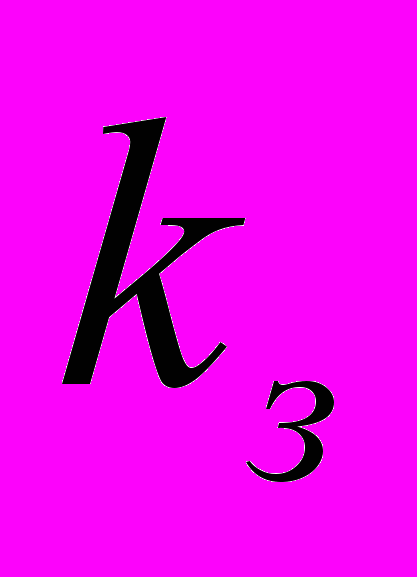
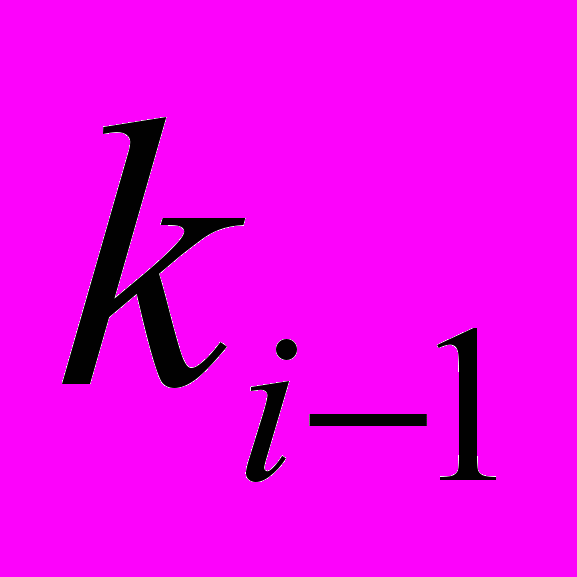
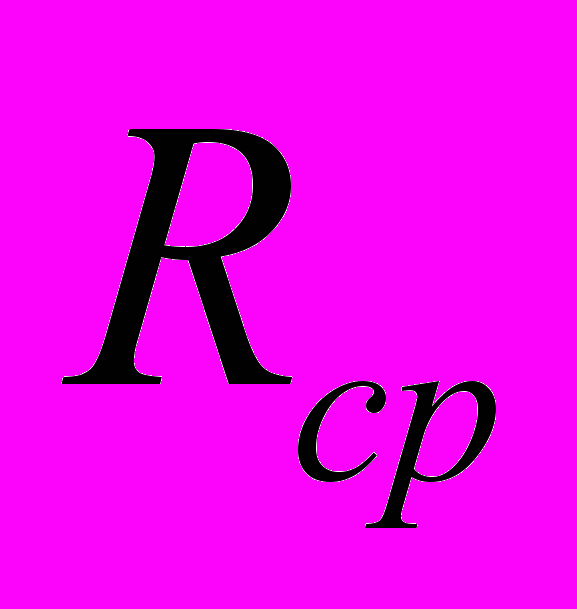
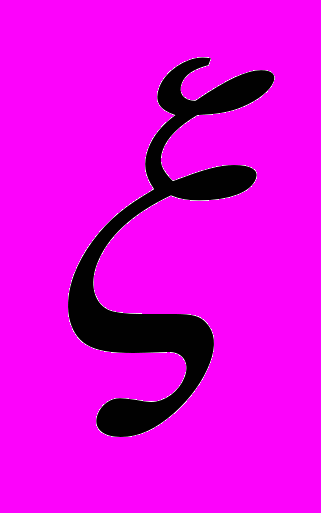
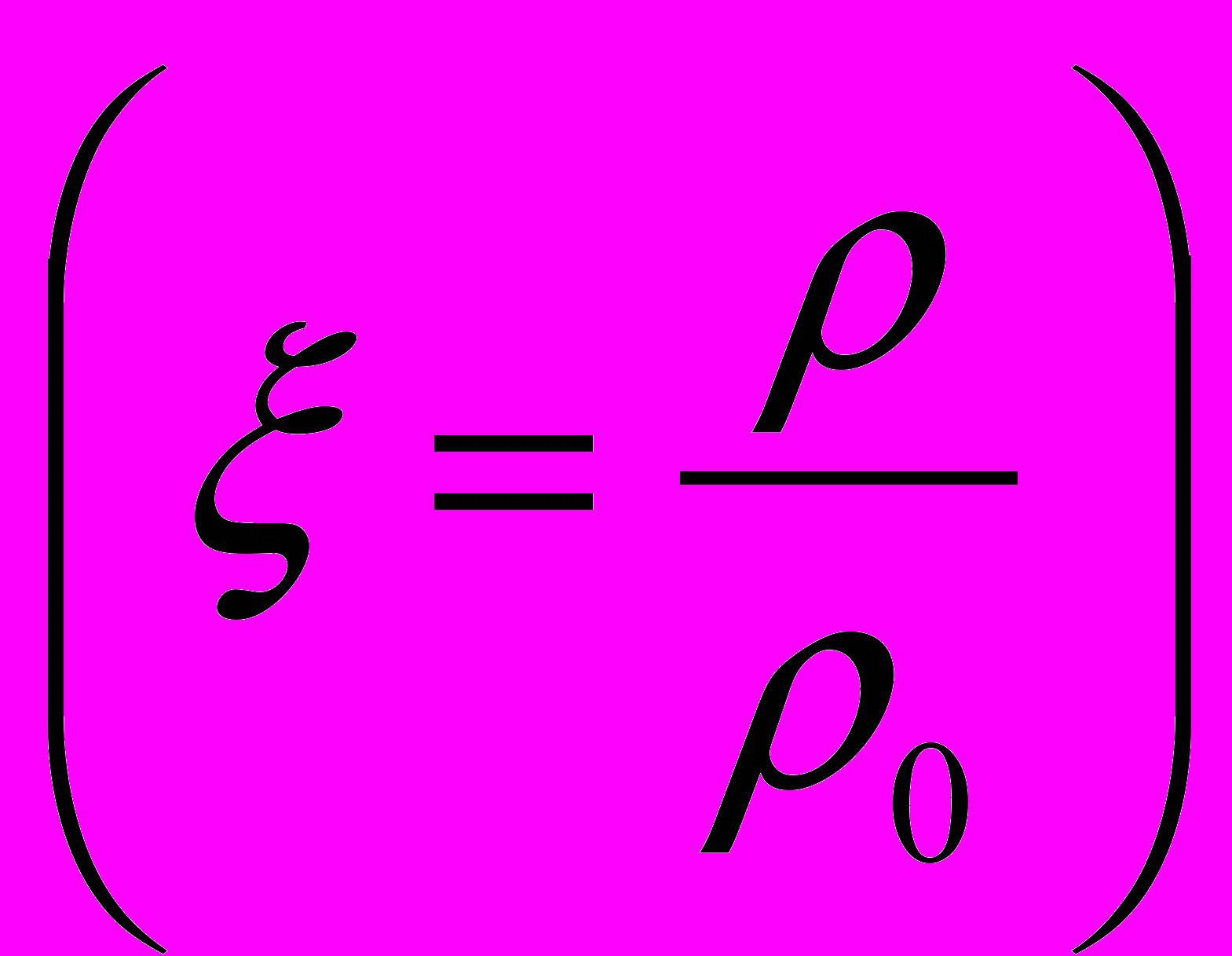
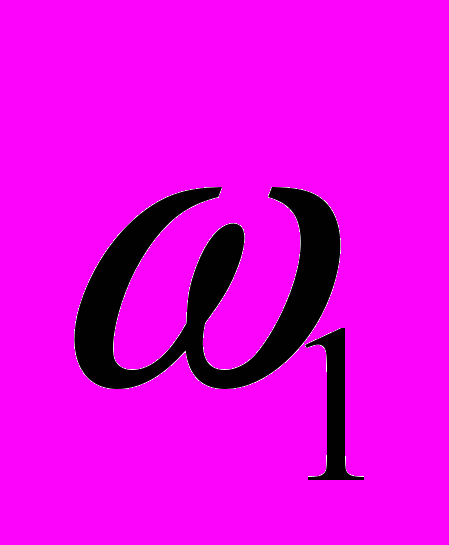
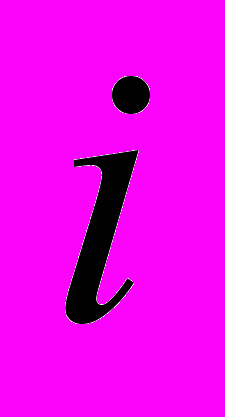
Потребная мощность, расходуемая на обеспечение подачи зерна к рабочим органам:
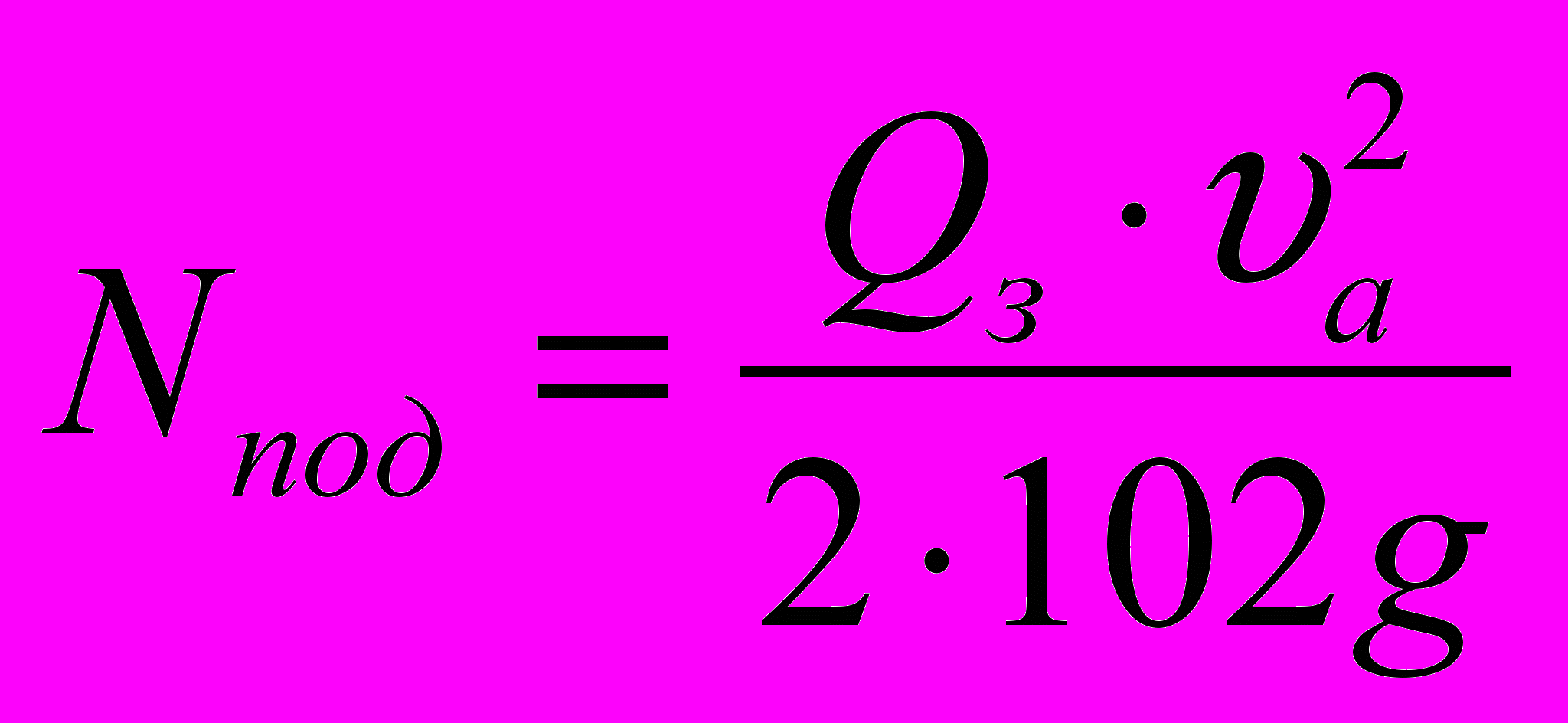
где
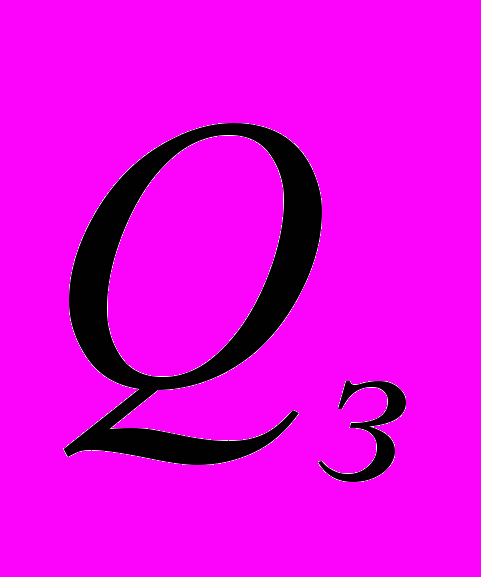
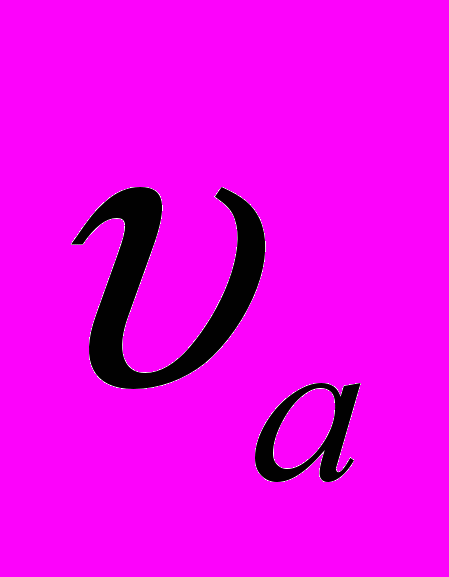
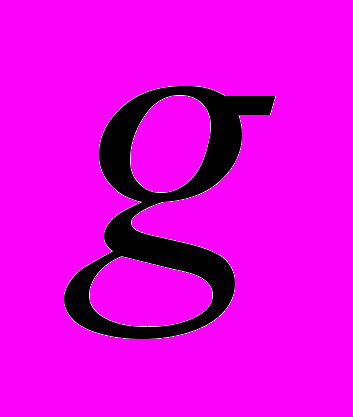
Таким образом, рассчитав потребную полезную мощность по формулам (9) и (10), просуммировав результаты в соответствии с балансом мощности получим потребную мощность на процесс измельчения. Расходы энергии на другие потери отнесены к холостому ходу. Общая мощность привода измельчителя
