Центробежно-роторные измельчители фуражного зерна
Вид материала | Автореферат |
СодержаниеГлава 4. Результаты и анализ экспериментальных исследований. |
- Агро-дайджест, 176.71kb.
- Администрация костромской области контрольное управление информационный обзор материалов, 567.02kb.
- В случае использования информации ссылка на сайт обязательна Справка о проведении производственных, 45.5kb.
- Применение центробежно-ударных мельниц «МЦ» при помоле цемента кушка, 76.77kb.
- Концепция государственной программы модернизации агропромышленного комплекса путем, 388.29kb.
- Рынок зерна в 1 полугодии 2006 года, 260.92kb.
- Концепция эффективного развития сельскохозяйственного производства и создания цивилизованного, 180.11kb.
- Перечислите основные операции послеуборочной обработки зерна на элеваторе, 879.69kb.
- Кабінету Міністрів України від 12 грудня 2002 року №1877 «Про затвердження Порядку, 111.26kb.
- Годовой отчет открытого акционерного общества «Ключевской элеватор» по итогам работы, 211.16kb.
1. Разработка частных методик экспериментальных исследований.
2. Изготовление лабораторно-экспериментальной установки и приборов для исследования процесса измельчения фуражного зерна и семян рапса.
3. Подготовка лабораторного оборудования и измерительной аппаратуры.
4. Проведение опытов, обработка и анализ результатов.
Для выполнения экспериментальных исследований разработаны:
– методика и прибор по исследованию физико-механических свойств зерна и влияния углов заточки и защемления режущих элементов при статическом нагружении;
– методика и специально разработанная лабораторная установка центробежно-роторного типа, оборудованная динамометрическим резцом и измерительной системой для регистрации силы резания при исследовании влияния скорости резания, углов заточки и защемления режущих элементов на усилие резания одиночных зерен злаковых культур и семян рапса;
– методика и экспериментальная установка для определения износостойкости высокопрочного чугуна с целью его использования при изготовлении рабочих органов измельчителей;
– методика по определению рациональных режимов рабочего процесса центробежно-роторного измельчителя в сельскохозяйственном производстве.
Исследования по определению эффективности измельчения фуражного зерна и семян рапса выполнялись на экспериментальных и опытных образцах центробежно-роторных установок. Критерием оценки выбраны качество готового продукта, удельная энергоемкость и производительность процесса измельчения.
Глава 4. Результаты и анализ экспериментальных исследований. На рисунке 9 представлены результаты экспериментальных исследований влияния конструктивных параметров режущих элементов на усилие резания одиночных зерен (семян) при статическом нагружении.
Из графических зависимостей усилия резания одиночных зерен влажностью 14-15% от угла заточки режущих элементов можно сделать вывод о том, что уменьшение угла заточки с 90 до 30° ведет к снижению усилия резания от 60 до 20 Н, но исходя из износостойкости режущего инструмента предпочтительнее иметь угол заточки 75…85°. Максимальное усилие резания зерна соответствует 42…52 Н, семян рапса 22…34 Н.
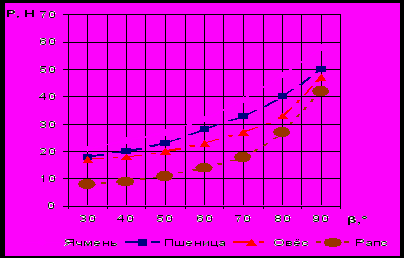
Рисунок 9 – Зависимость усилия резания одиночных зерен
влажностью 14-15 % от угла заточки режущего элемента
Значение геометрических параметров режущих элементов рабочих органов является немаловажным фактором при динамическом измельчении. С этой целью проведены исследования влияния скорости резания и углов заточки режущих элементов на усилие резания зерновки пшеницы, ячменя, овса и семян рапса.
Исследования выполнены на экспериментальной установке центробежно-роторного типа, оснащенной динамометрическими приборами (рисунок 10).

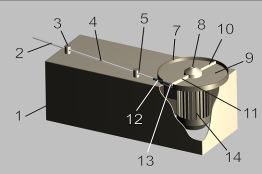
а) б)
Рисунок 10 – Экспериментальная установка динамического резания зерна: а) – внешний вид; б) – камера измельчения; 1 – корпус;
2 – динамометр; 3, 5 – кронштейн; 4 – стержень динамометра;
6 – канал для зерна; 7 – обечайка камеры измельчения; 8 – приемная
камера зерна; 9 – диск-ротор; 10 – противовес; 11 – планка-канал;
12 – резец; 13 – зерновка; 14 – электродвигатель
По результатам исследований построены графические зависимости усилия резания одиночных зёрен от скорости резания и геометрических параметров режущих элементов (рисунки 11-12).
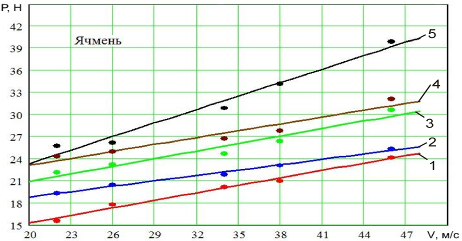
Рисунок 11 - Зависимость силы резания (Р) от скорости резания (V)
при у
°
глах защемления
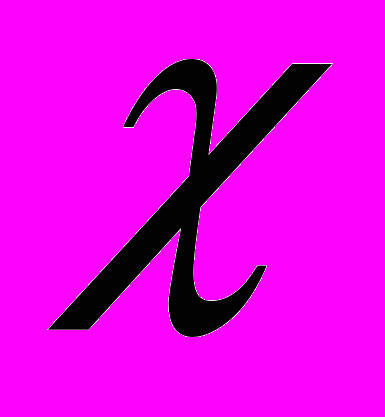
1– β=60˚; 2 – β=70˚; 3 – β=80˚; 4 – β=85˚
и углах защемления
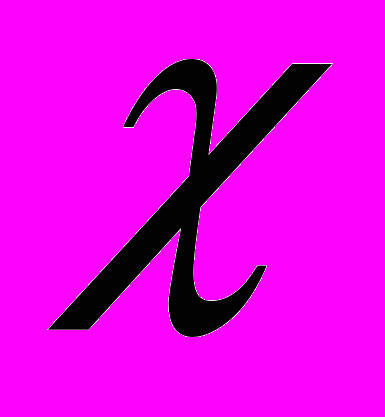
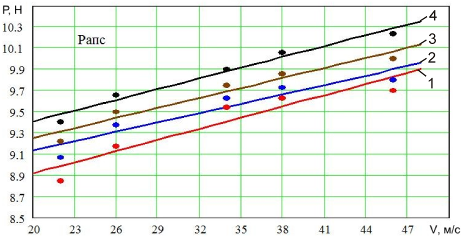
Рисунок 12 – Зависимость силы резания (Р) от скорости резания (V)
семян рапса при у
°
глах защемления
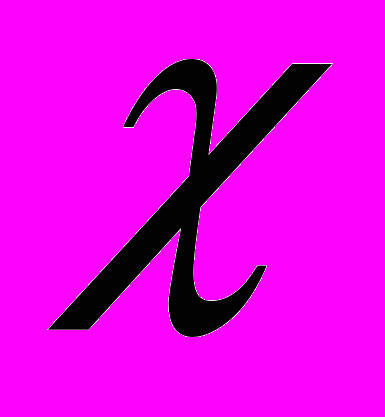
1 – β=60˚; 2 – β=70˚; 3 – β=80˚; 4 – β=85˚
Анализ полученных зависимостей позволяет сделать следующие выводы:
1. Усилие резания фуражного зерна режущими элементами с углами заточки β=60˚, β=70˚, β=80˚, β=85˚ и защемления
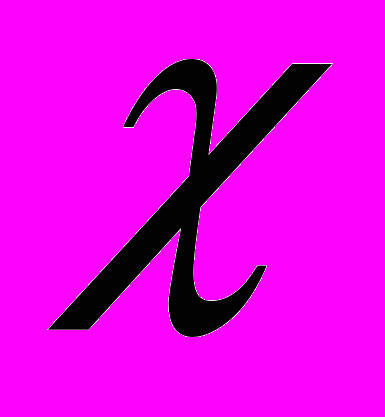
2. С уменьшением угла резания с 85º до 60º усилие резания снижается. Однако более острые углы режущих элементов изнашиваются и притупляются быстрее. По многочисленным опытам установлены рациональные углы резания для рассматриваемого случая: β=80-85º ;
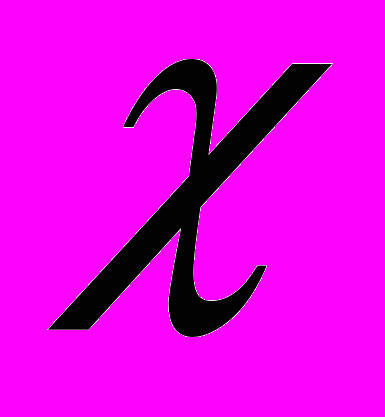
3. Усилие резания с углами заточки β=80˚ и β=85˚, при угле защемления
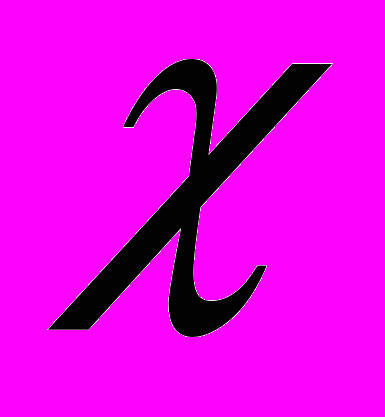
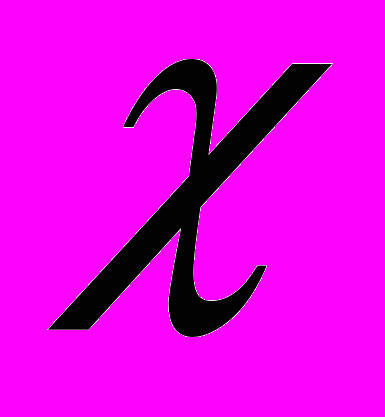
4. Предложенный метод проведения эксперимента по исследованию процесса динамического резания семян рапса и фуражного зерна позволяет фиксировать импульсный характер усилия резания на осциллограмме с высокой точностью. Результаты экспериментальных исследований подтверждают правильность выбора рабочих органов и теоретических расчетов по обоснованию их основных геометрических параметров и режимов работы.
На рисунках 13 и 14 графически представлены зависимости модуля помола фуражного зерна от количества режущих элементов на первой и второй измельчающих парах рабочих органов.
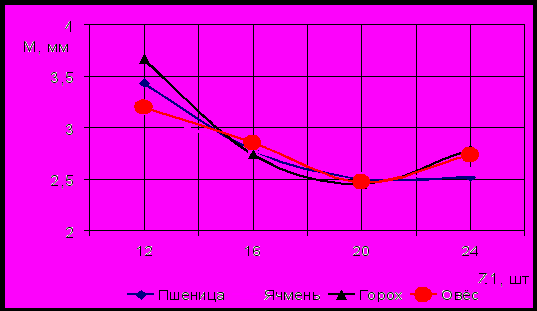
Рисунок 13 – Зависимость модуля помола (М) пшеницы, ячменя,
гороха и овса от количества режущих элементов (z) на первой
измельчающей паре рабочих органов при скорости резания υ1=26 м/с
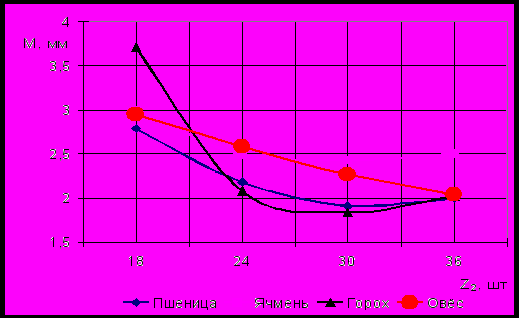
Рисунок 14 – Зависимость модуля помола (М) пшеницы, ячменя,
овса и гороха и овса от количества режущих элементов (z) на второй измельчающей паре рабочих органов при скорости резания υ2=36 м/с
Оптимальное количество режущих элементов на первой измельчающей паре рабочих органов составляет 20, на второй – 30. Результаты опытов подтверждают справедливость формулы (5).
Зависимости основных показателей процесса измельчения от угловой скорости рабочих органов, построенные по результатам экспериментальных исследований, показаны на рисунке 20.
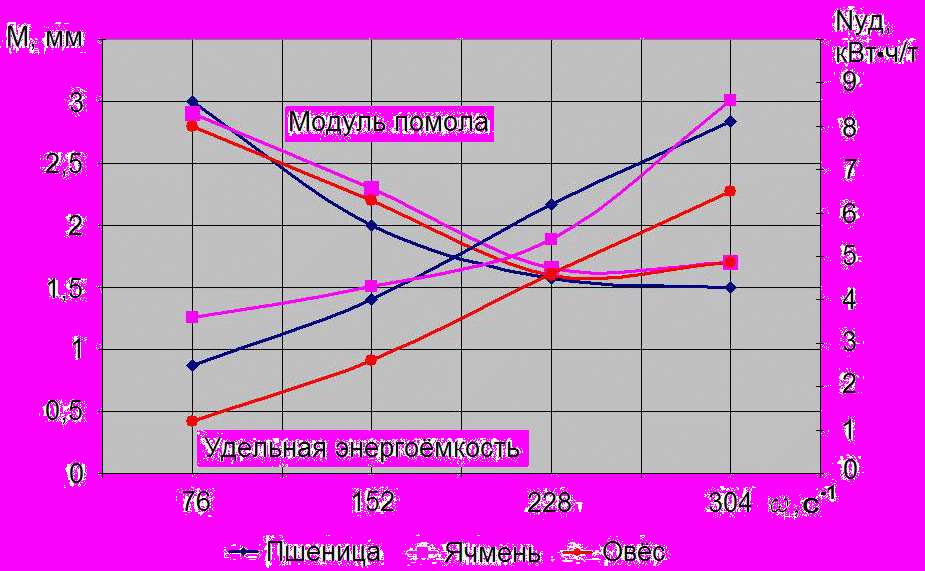
процесса измельчения от угловой скорости рабочих органов
Результаты экспериментальных исследований свидетельствуют о том, что при рациональном режиме измельчения (угловая скорость роторов
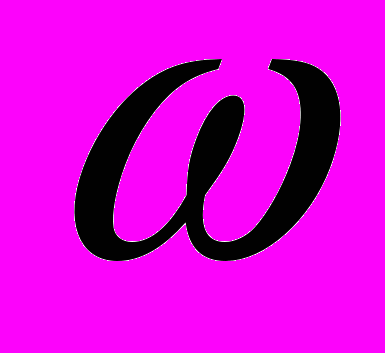
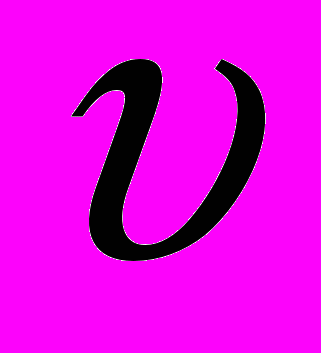
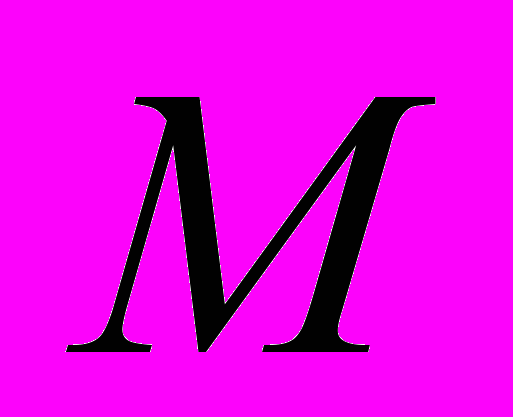
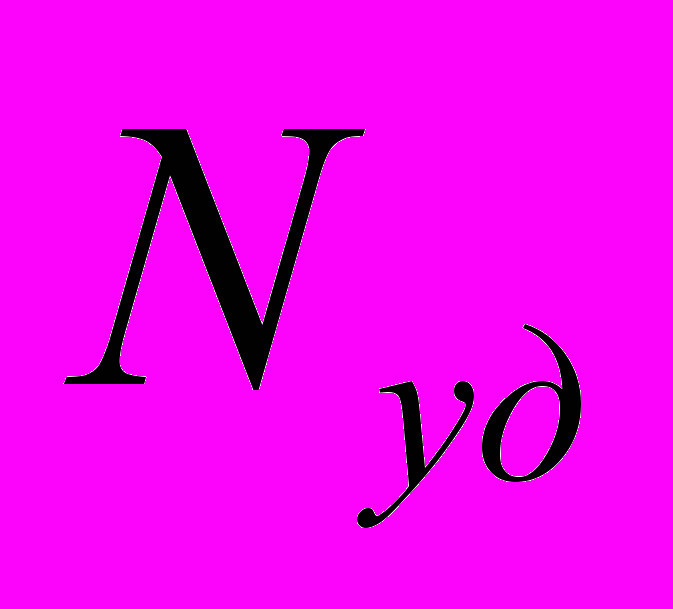
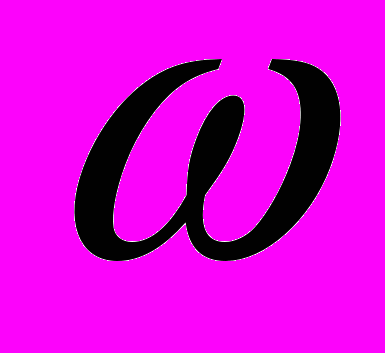
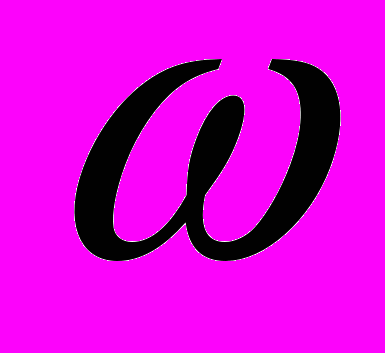
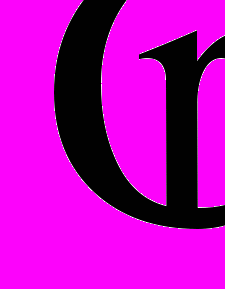
Получение готового продукта заданного гранулометрического состава, в зависимости от выбранного режима работы центробежно-роторного измельчителя, возможно. Это соответствует цели исследований. По данным частотного распределения по фракциям при кинематическом режиме измельчения с параметрами
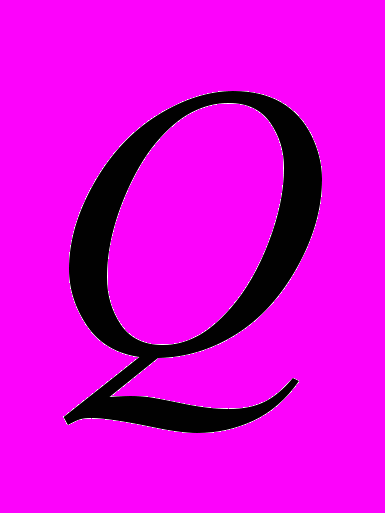
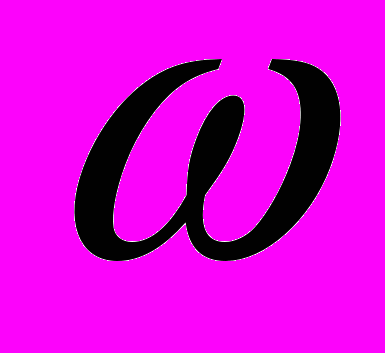
В молотковых дробилках и других измельчающих устройствах, в которых разрушение материала осуществляется за счет энергии удара, влажность и жирность измельчаемого зерна существенно влияют на энергетические и качественные характеристики. В исследуемых же измельчителях картина несколько иная.
Таким образом, можно констатировать следующее:
– центробежно-роторные измельчители способны перерабатывать фуражное зерно и семена рапса с влажностью до 22% и жирностью до 50%;
– при повышении влажности на 1% относительно зоотехнических норм (14-15%) удельная энергоемкость процесса измельчения фуражного зерна и его смесей увеличивается на 0,7 кВт∙ч/т, в то время как на молотковых дробилках – на 2 кВт∙ч/т;
– при измельчении семян рапса с повышением влажности удельная энергоемкость имеет тенденцию к уменьшению, при этом производительность увеличивается и качество готового продукта практически не изменяется, что является немаловажным фактором в кормоприготовлении.
В процессе многолетней эксплуатации измельчителей выявлена необходимость повышения износостойкости рабочих органов.
Исследование износа поверхности режущих элементов рабочих органов муаровым методом дает достаточную информацию об изменении величины износа при эксплуатации (рисунки 16-18).
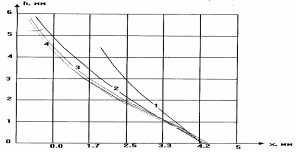
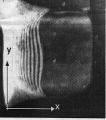
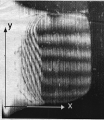
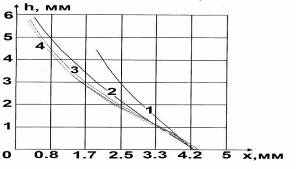
а) б) в)
Рисунок 16 – Картины муаровых полос и график износа
режущего элемента в различных сечениях (вид сверху)
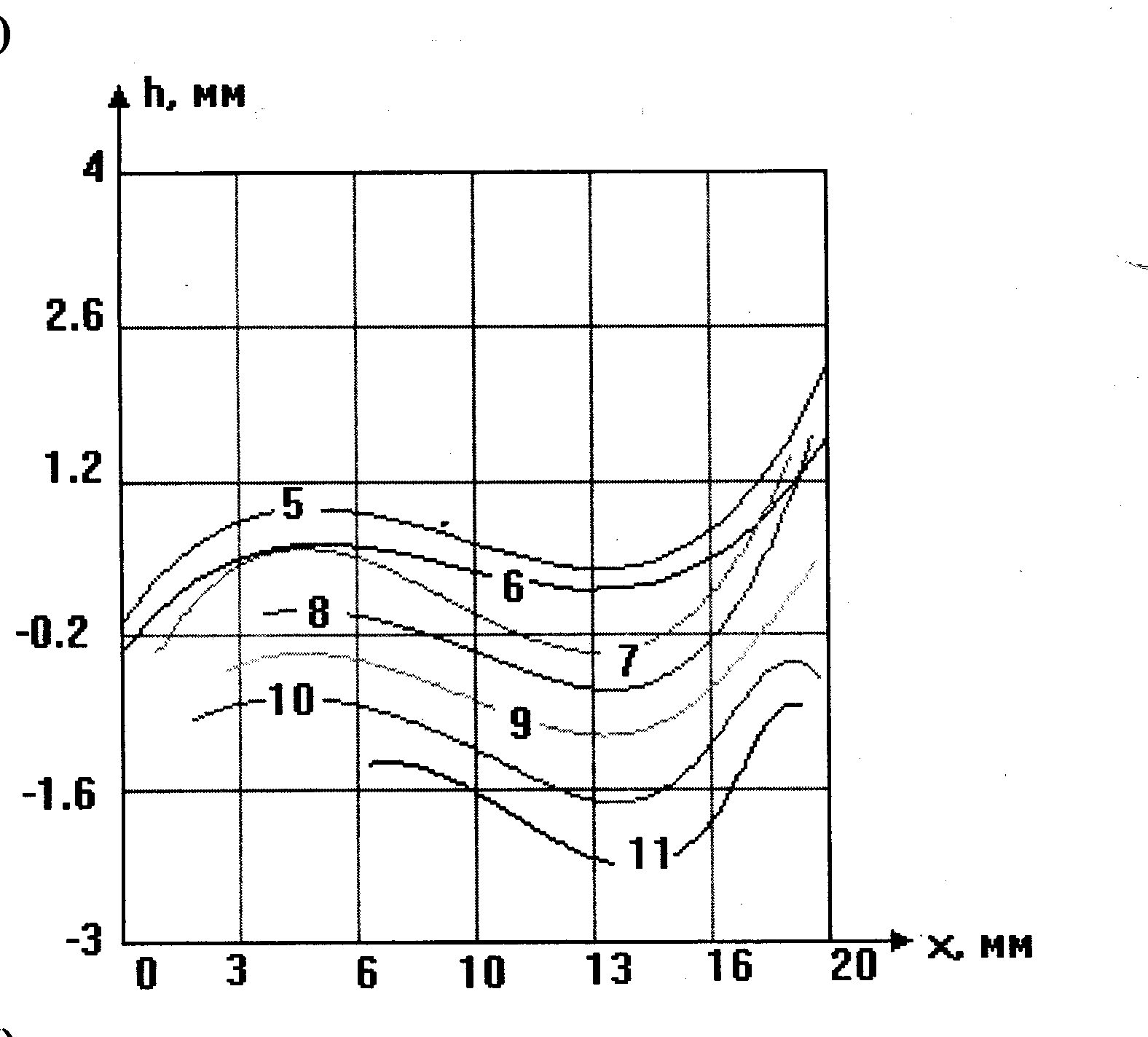
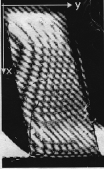
а) б)
Рисунок 17 – Вид режущего элемента с наружной стороны
и график поперечных перемещений
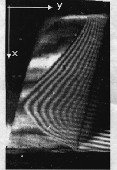
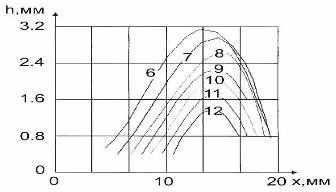
а) б)
Рисунок 18 – Вид режущего элемента с внутренней стороны
и график поперечных перемещений
Анализируя «муаровые картины», можно заключить, что наружный профиль режущего элемента имеет сложную криволинейную поверхность. Результаты, полученные при расшифровке «муаровых картин», дали достаточную информацию об изменении величины износа по всей поверхности режущего элемента (зуба) рабочих органов центробежно-роторного измельчителя. Таким образом, муаровый метод является перспективным направлением в исследовании износа поверхностей рабочих органов сельскохозяйственных машин.
Подтверждена целесообразность применения модифицированного высокопрочного чугуна ВЧ 501 с содержанием перлита 85% для изготовления рабочих органов.
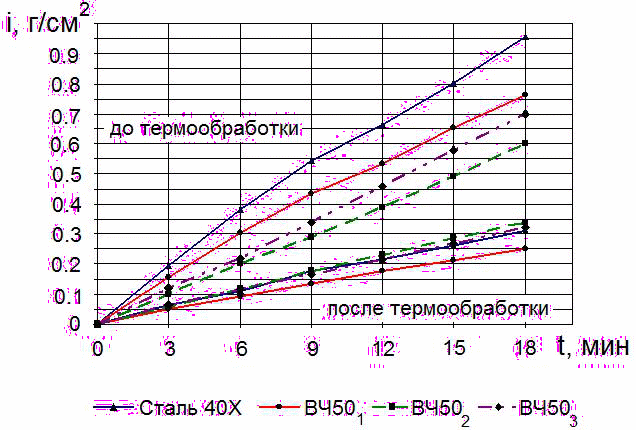
Рисунок 19 - График удельной истираемости
стального и чугунных образцов до и после термообработки
Сравнение кривых удельной истираемости термообработанных стального и чугунных образцов показывает, что высокопрочный чугун ВЧ 501 практически не уступает стальному сталь 40Х, а даже превосходит на 18-20% (рисунок 19).
Образец ВЧ 501 с твердостью 46-48 НRС обладает наименьшим удельным износом по сравнению с другими образцами, из чего можно сделать вывод, что сопротивление истирающим нагрузкам у высокопрочного чугуна тем больше, чем выше его твердость. При этом можно заметить, что чугунный образец твердостью 46-48 НRС изнашивается меньше, чем стальной с твердостью 54-56 (рисунок 20). Это подтверждает гипотезу о том, что для высокопрочного чугуна высокая твердость в меньшей мере влияет на характеристики износа, чем у стали. Исследования позволяют сделать вывод о возможности применения высокопрочного чугуна ВЧ 501 для изготовления рабочих органов центробежно-роторных измельчителей. При этом затраты на изготовление одного комплекта рабочих органов снижаются на 20 – 25% по сравнению с затратами на изготовления из стали 40Х.
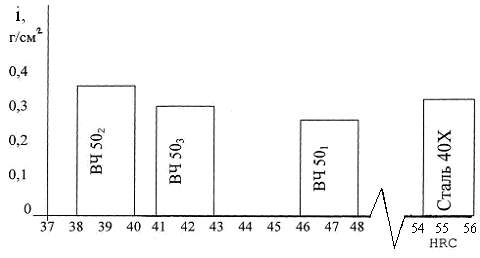
Рисунок 20 – График зависимости удельной истираемости
от твердости материала
Экономический эффект от применения высокопрочного чугуна для изготовления рабочих органов достигается за счет снижения затрат на их изготовление и снижения стоимости материала.
Глава 5. Производственная проверка и экономическая эффективность использования центробежно-роторных измельчителей фуражного зерна в сельскохозяйственном производстве. В 1988 году центробежно-роторный измельчитель фуражного зерна ИЛС-5 прошел ведомственные и государственные испытания.
1. По результатам ведомственных испытаний на комбикормовом заводе МХП «Радуга» Троицкого района Челябинской области выявлено, что удельная энерго- и металлоемкость в сравнении с серийно выпускаемыми молотковыми дробилками ДДМ-5 и ДБ-5 ниже в 1,4- 2,0 и 2,5- 4,0 раза.
2. Государственные приемочные испытания опытного образца измельчителя ИЛС-5 (ДЛС-394) проводились на Поволжской МИС. В период испытаний измельчитель был использован для производства комбикормов на Алексеевском комбикормовом заводе производственного управления хлебопродуктов Куйбышевской области. Согласно протоколу МИС № 19-137-88 (4320510) выявлено: зоотехнические показатели корма, измельченного на ИЛС-5, выше, чем у корма, приготовленного на сравниваемой дробилке ДБ-5; измельчитель надежно выполняет технологический процесс и пригоден для измельчения фуражного зерна, а также семян рапса. В готовом продукте содержание пылевидной фракции не превышает 5%; результаты экономического расчета показывают, что измельчитель позволяет снизить затраты труда по сравнению с базовой дробилкой ДБ-5 на 6,6 % вследствие более высокой эксплуатационной производительности; технический уровень выше, а удельная энергоемкость процесса измельчения в 1,45 раза меньше. Результаты представлены в таблице 1.
Центробежно-роторный измельчитель ИЛС-5 обеспечивает заданное качество измельчения семян рапса без выжима масла и равномерный помол фуражного зерна. Удельный расход энергии на измельчение семян рапса составляет 4 кВт·ч/т, фуражного зерна 5 кВт·ч/т против 10 кВт·ч/т на серийной дробилке ДБ-5.
3. После государственных испытаний измельчитель ИЛС-5 производительностью 3-5 т/ч был рекомендован для серийного производства заводу «Агромаш» Челябинской области (1989 г.) и Нолинскому ремонтно-механическому заводу ПО «Кировагропромремонт» Кировской области (1990 г.). С 1990 года начато серийное производство измельчителей производительностью от 0,1 до 0,5 т/ч на Приборостроительном заводе в г. Трехгорном Челябинской области. За период 1989 - 2006 гг. год выпущено более 5000 штук измельчителей 4-х модификаций производительностью от 0,1 до 5,0 т/ч (ИЛС-0,15; ИЛС-0,5; ИЛС-5). В 1998 году измельчители включены в Систему технологии машин, в 2000 году в каталоги «Машины и оборудование для АПК».
4. Измельчители нашли практическое применение в пищевой и медицинской отраслях – при измельчении семян кориандра, горчицы, высушенных корней цикория и хрена, арахиса, семян расторопши; в строительной – при измельчении мраморной крошки, змеевика и других минералов для строительно-отделочных работ и т.п. Например, с 2001 года в С.-Петербурге на фармакологическом объединении ОАО им. Пастера производится переработка семян расторопши на центробежно-роторных измельчителях ИЛС-0,5 и ИЛС-5. С 1998 года в Челябинской городской больнице №10 в макробиологическом центре используются измельчители ИЛС-0,1 и ИЛС-0,5 для переработки зерна арахиса для лечения больных и т.д.
Таблица 1 - Показатели экономической эффективности центробежно-роторного измельчителя фуражного зерна ИЛС-5
Основные показатели | ДБ-5 Базовый вариант | ИЛС-5 Новый вариант | ||||||||
ячмень | пшеница | рапс | ячмень | пшеница | рапс | |||||
Эксплуатационные | ||||||||||
Годовая выработка, т | 1760 | 1760 | 1760 | 1760 | 1760 | 1760 | ||||
Установленная мощность, кВт | 32 | 32 | 32 | 22 | 22 | 22 | ||||
Производительность, т/ч | 3,12 | 4,88 | - | 4,21 | 4,89 | 5,5 | ||||
Удельный расход электроэнергии, кВтч/т | 10,2 | 6,6 | - | 5,2 | 4,5 | 4,0 | ||||
Масса, кг | 1000 | 1000 | 1000 | 500 | 500 | 500 | ||||
Количество обслуживающего персонала | 1 | 1 | 1 | 1 | 1 | 1 | ||||
Технологические | ||||||||||
Коэффициент использования сменного времени, ч | 0,8 | 0,8 | - | 0,8 | 0,8 | 0,8 | ||||
Коэффициент использования эксплуатационного времени, ч | 0,74 | 0,74 | - | 0,8 | 0,8 | 0,8 | ||||
Качество технологического процесса | ||||||||||
Модуль помола, мм | 1,3-2,0 | 1,3-2,0 | - | 1,5-1,9 | 1,5-1,9 | 0,8-1,2 | ||||
Количество пылевидной фракции, % | 8,5-11,2 | 10,8-16,8 | | 2,5-3,8 | 3,6-4,4 | 1,0-1,3 | ||||
Себестоимость едини- цы продукции, руб./т | 45,1 | 39.8 | - | 28,8 | 21,7 | | ||||
Годовой экономический эффект, руб. | | | | 96502,6 | 124551,6 | | ||||
Срок окупаемости, год | | | - | 0,75 |
5. В 2003 году на Челябинском абразивном заводе проведены производственно-экспериментальные исследования по измельчению нормального и белого электрокорунда для решения задачи получения максимального количества зерна требуемых фракций. Измельчение электрокорунда было произведено на центробежно-роторном измельчителе ИЛС-5. Для сравнения были взяты пробы измельченного электрокорунда после стержневой мельницы. Зерновой состав материала, полученный измельчением на ИЛС-5, предсказуем и выгоден. Наличие пыльной фракции сведено к минимуму, а это значит, что предполагается снижение производственных потерь более чем в два раза и получение дополнительной прибыли в размере 100 – 300 руб. (по ценам 2003 года) на одну тонну электрокорунда. Наиболее ходовая фракция по зернистости увеличилась в 1,5 – 2,0 раза.
6. Технико-экономические расчёты показали, что экономия прямых энергозатрат при измельчении фуражного зерна на измельчителе ИЛС-5 по сравнению с дробилкой ДБ-5, в среднем уменьшилась на 90,7 МДж/т, а коэффициент эффективности составил 1,7. Себестоимость готовой продукции также ниже на 29,8%, потребление электроэнергии – на 40%. Годовой экономический эффект составляет 110527,2 руб. в год. Срок окупаемости – 0,7 года. Для измельчителей ИЛС-0,5, в сравнении с молотковой дробилкой КДМ-1, годовой экономический эффект составляет 23172,5 руб. в год на один измельчитель. Срок окупаемости – 2,4 года. Для измельчителей ИЛС-0,15, в сравнении с молотковой дробилкой ДЗ-Т-1, годовой экономический эффект составляет 7021,8 руб. Срок окупаемости – 2,2 года. Общий среднегодовой экономический эффект от внедрения в сельскохозяйственное производство и другие отрасли народного хозяйства, выпущенных заводами Южного Урала и Нечернозёмной зоны России измельчителей ИЛС, составляет 18,812 млн руб./год (в ценах 2006 года).