Материаловедение
Вид материала | Методические указания |
- Материаловедение 1, 26.57kb.
- Дисциплина «Материаловедение» Лекция, 167.85kb.
- Материаловедение. Особенности атомно-кристаллического строения металлов, 2225.68kb.
- Магистерской программы «Материаловедение металлических и неметаллических материалов, 24.46kb.
- Лекция 1 Материаловедение. Особенности атомно-кристаллического строения металлов, 2248.88kb.
- Программа курса электротехническое материаловедение для направлений подготовки бакалавров, 255.8kb.
- Примерная программа дисциплины стоматология модуль «материаловедение», 483.54kb.
- Vi международная научная школа-конференция «Фундаментальное и прикладное материаловедение», 99.7kb.
- Программа вступительного испытания в магистратуру по направлению 150100. 68 «Материаловедение, 430.47kb.
- Лекции по курсу «материаловедение» для студентов цдфо тула2003, 2252.78kb.
Министерство общего и профессионального образования РФ
Камский государственный политехнический институт
МАТЕРИАЛОВЕДЕНИЕ
Программа, методические указания и контрольные задания для студентов-заочников технических специальностей.
г. Набережные Челны, 2002г.
УДИ 669. 017. (075.8.).
Материаловедение. Программа, методические указания и контрольные задания для студентов – заочников технических специальностей. Составитель: В.И. Астащенко, Наб. Челны, КамГПИ, 2002г.
Методические указания по курсу «Материаловедение» составлены в соответствии с Государственным образовательным стандартом высшего профессионального образования по подготовке специалистов машиностроительного профиля, утверждённого государственным комитетом РФ по высшему образованию. Представлены основные разделы дисциплины для самостоятельного изучения студентами заочной формы обучения. Составлены и приведены варианты заданий для выполнения контрольной работы. В приложении представлены диаграммы двойных сплавов и диаграмма «Железо-карбид железа». После каждой темы программы приведены методические указания.
Работа выполнена на кафедре «Машины и технология литейного производства».
ИЛ.: 19
Рецензент: Главный специалист по термической обработке ОАО КамАЗ В.Г. Козлов.
Печатается в соответствии с решением научно-методического совета факультета автоматизации и прогрессивных технологий Камского государственного политехнического института
от_____ _______ 2002г.
Камский государственный
политехнический институт
2002г.
ВВЕДЕНИЕ
Материаловедение – наука, изучающая строение и свойства материалов в зависимости от их состава и условий обработки.
Курс материаловедение включает в себя два направления, а именно раздел по металловедению и термической обработке металлов и сплавов и раздел по неметаллическим материалам. Раздел металловедения изучает связь между состоянием, строением и свойствами металлов и сплавов и закономерности их изменения при воздействии различных факторов (тепловых, химических, механических, электромагнитных и т.д.). Раздел по неметаллическим материалам в основном посвящён изучению пластмасс.
При конструировании и изготовлении машин и приборов, организации их эксплуатации и ремонта инженер постоянно сталкивается с машиностроительными материалами и их использованием.
Для выпуска высококачественной продукции особое значение приобретают изучение свойств промышленных металлических материалов, разработка и внедрение в промышленность новых высокопрочных и технологичных сплавов, применение новейших методов их контроля и исследования.
Изучение курса «Материаловедение» должно дать будущим специалистам:
- Знание об основных закономерностях, определяющих строение, состав и свойства материалов;
- Представление об основных методах испытания материалов и принципом работы с приборами и машинами;
- Умение самостоятельного пользования технической и справочной литературой и дать достаточные знания для выбора основных промышленных, а также новых перспективных материалов и эффективных методов их обработки для обеспечения надёжности и долговечности, изготавливаемых из них изделий;
- Знание о перспективах развития и методах упрочнения рабочих поверхностей деталей.
Теоретической основой данного курса является соответствующие разделы дисциплины «Химия» (используются знания законов протекания химических реакций окисления и восстановления металлов, понятие о константах равновесия и т.д.), «Физика» (используются знания законов об агрегатном состоянии веществ и фазовых превращениях), «Технология конструкционных материалов» (используются знания атомно-кристаллического строения металлов и сплавов, кристаллизация, методы определения механических свойств материалов, понятие деформации и разрушения металла, маркировка черных и цветных металлов и сплавов и т.д.)
Вместе с другими дисциплинами студенты получают необходимую общеинженерную и технологическую подготовку необходимую как на производстве, так и при работе в научно-исследовательских и проектных институтах.
В таблице 1 приведены учебные планы для различных технических специальностей с указанием времени изучения дисциплины и выполнения контрольной работы, распределения общего объёма часов по видам занятий и формы итогового контроля с учётом базового образования студентов.
Учебный план технических специальностей
по дисциплине «Материаловедение».
Таблица 1.
№ | Специальность | Базовое образо-вание. | Распределение по семестрам | Объём в часах | примечание | ||||||
экз | зач | контр | всего | лек | лаб | пр. | сам | ||||
1 | 1201 | с/о | 3 | - | 3 | 119 | 6 | 4 | - | 109 | |
2 | 1201 | с/с | 2 | - | 2 | 119 | 6 | 4 | - | 109 | |
3 | 1204 | с/с | 2 | - | 2 | 119 | 6 | 4 | - | 109 | |
4 | 1502 | с/с | - | 5 | 5 | 60 | 2 | 2 | - | 56 | |
5 | 1502 | с/с | 2 | - | - | 60 | 2 | 2 | 2 | 54 | |
Примечание: с/о – среднее образование
с/с – среднее – специальное образование.
Согласно, учебного плана (см. табл.1) студент выполняет одну контрольную работу, состоящую из пяти заданий. Вариант контрольной работы должен строго соответствовать учебному шифру студента (см. группа №1-стр.34; группа №2-стр.52).
Выполненную контрольную работу студент обязан выслать в институт или представить на кафедру за месяц до начала установочно-экзаменационной сессии. Экзамен принимается после зачтения контрольной работы. На странице 70 приводится перечень рекомендуемой литературы. В основной литературе освещены все вопросы программы. Использование дополнительной литературы позволит более глубокому изучению отдельных вопросов. В каждом разделе приводится программа, методические указания и литература с указанием конкретных страниц.
Программа и методические указания к темам дисциплины.
Тема 1. Классификация материалов.
Структурная схема основных материалов применяемых в машиностроении. Основные свойства характеризующие металлы. Новые материалы для изделий машиностроительной промышленности.
Методические указания.
Материалы, используемые в народном хозяйстве можно условно разделить на две группы: металлы и металлические сплавы и неметаллы. Первую группу составляют чёрные и цветные металлы и сплавы. Железо и сплавы на его основе (чугун, сталь, ферросплавы) называют чёрными. На основе железа изготавливают около 95% всех конструкционных и инструментальных материалов. Это связано с большим содержанием его в земной коре, низкой стоимостью и высокими технологическими и механическими свойствами. Остальные металлы (медь, никель, алюминий, золото, серебро и т.д.) и сплавы на их основе относят к цветным. Это металлы со специальными свойствами: малая плотность, химическая инертность, низкая или высокая температура плавления и т.д.
Металлы и металлические сплавы – тела кристаллические, атомы расположены в металлах в строго определённом порядке. Они обладают рядом характерных свойств: высокая термопроводимость и электрическая проводимость; положительный коэффициент электрического сопротивления; хорошая отражательная способность; высокая способность к пластической деформации.
В современной технике широко применяют стали, которые обеспечивают высокую конструктивную прочность, а также сплавы, которые остаются прочными при высоких температурах, вязкими при температурах близких к абсолютному нулю, обладающие высокой коррозийной стойкостью в агрессивных средах или другими физико-химическими свойствами. Число новых сплавов постоянно растёт – это так называемые композиционные материалы, сплавы с памятью формы, обладающие эффектом сверх - пластичности и т.д.
Основу группы неметаллов составляют пластмасса, каучук, резина, стекло, керамика и т.д. Такие материалы при достаточной прочности обладают хорошей химической стойкостью, диэлектрическими свойствами и малой плотностью. Они технологичны и эффективны при использовании в различных отраслях машиностроения.
Литература: 1, 3-36; 3, 9-32
Вопросы для самопроверки.
- Каковы характерные свойства металлических материалов и неметаллов?
- Что такое сталь, чугун, латунь, бронза, силумины и дюралюмины?
- Какие материалы обладают свойствами анизотропии и изотропии?
- Охарактеризуйте основные параметры кристаллической решётки и их связь со свойствами материалов?
- Укажите причину изменения свойств материала под действием давления и температуры? Что такое полиморфные превращения?
Тема 2. Основы теории сплавов.
Изучите строение материалов и сплавов в твёрдом состоянии. Необходимо чётко представлять, что такое твёрдый раствор, химическое соединение и механическая смесь. Изучите принцип построения диаграммы состояния сплавов. Типы диаграмм состояния. Научитесь пользоваться правилом фаз и отрезков и устанавливать фазовый состав сплава. Отчётливо представляйте связь между составом сплава и его свойствами с помощью правила Курнакова.
Методические указания.
Сплав это вещество, полученное сплавлением двух или более элементов. (компонентов). Строение сплава зависит от типа взаимодействия компонентов образующих сплав. В металлических сплавах возможно получение механической смеси, химических соединений и твёрдых растворов.
Составляющие сплав вещества могут вступать в химическое взаимодействие, образуя химические соединения по правилу валентности, или взаимно растворяться друг в друге, образуя растворы внедрения или замещения. Строением сплава может быть механическая смесь, если в твёрдом состоянии отсутствует механическое взаимодействие. Диафрагмы состояния сплава строят экспериментальным путём, которые представляются в графической форме и показывают изменение состава в зависимости от содержания компонентов и температуры. Диаграммы состояния позволяют определить, какую структуру будут иметь медленно охлаждённые сплавы, а также решить вопрос о том, можно ли добиться изменения микроструктуры в результате теплового воздействия (термической обработки сплава).
Вид диаграммы определяется характером взаимодействия, которые возникают между компонентами в жидком и твёрдом состояниях.
Типичными диаграммами состояния металлических сплавов являются диаграммы:
а) с неограниченной растворимостью компонентов друг в друге;
б) с ограниченной растворимостью компонентов;
в) с образованием химических соединений;
г) с полиморфным превращением.
Концентрация компонентов и количество фаз у сплава определяется правилом отрезков. Это правило применимо только для двухфазных областей в двойных диаграммах состояния сплавов.
Общие закономерности сосуществования устойчивых фаз, отвечающих теоретическим условием равновесия, могут быть выражены правилом фаз.
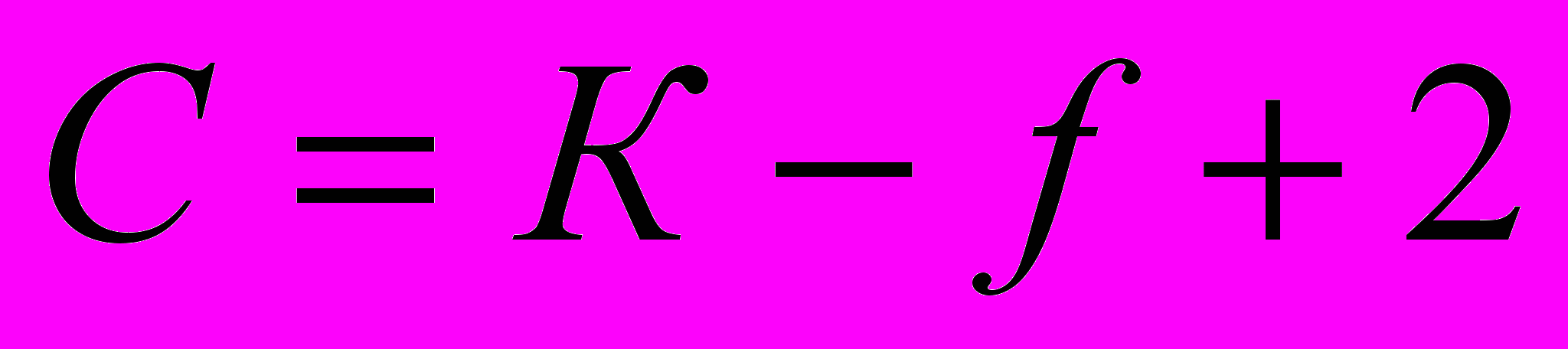
С – число степеней свободы,
К – количество компонентов составляющих сплав,
f – количество фаз,
2 – число переменных (давление и температура).
Если принять, что все превращения в сплавах протекают при постоянном давлении, то правило фаз примет следующий вид.
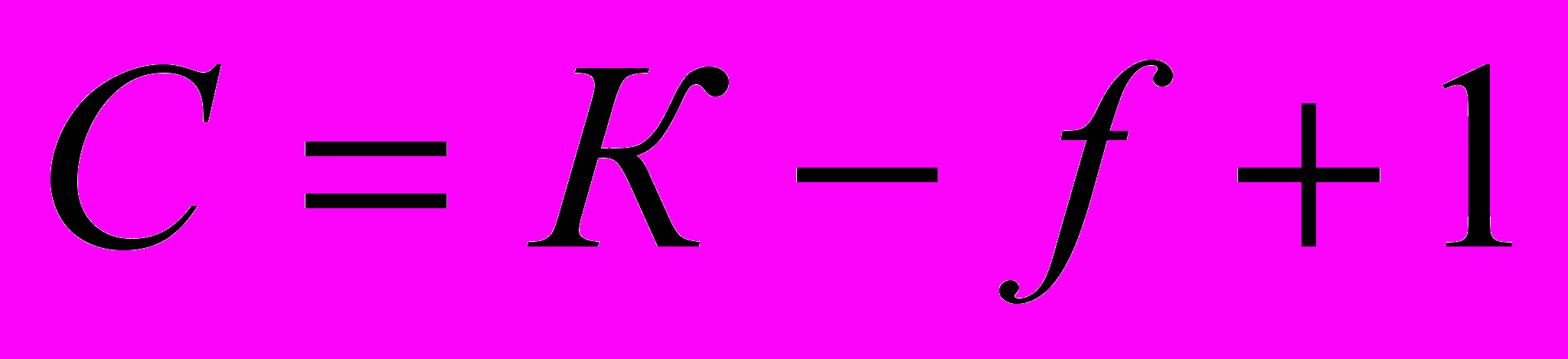
При числе степеней свободы равной «о» система находится в равновесии при строго определённой температуре (жидкая и твёрдая фазы).
Свойства любого сплава зависят от того, какие соединения или какие фазы образовали компоненты сплава.
В качестве примера по изучению фазового и структурного состояния сплавов рассмотрим диаграмму системы «олово-цинк» (Sn - Zn) (смотри приложение (рис. 1))
Согласно этой диаграммы линия АВС – линия ликвидус, а линия ДВЕ – солидус. Кроме того, линия ДВЕ соответствует температуре, при которой в процессе охлаждения сплавов в них протекает эвтектическая реакция с образованием эвтектики.
Сплавы системы «олово-свинец» в основном применяются в качестве мягких припоев.
При содержании 8% Zn и 92% Sn образуется эвтектический сплав. Температура его образования при кристаллизации соответствует 1990С.
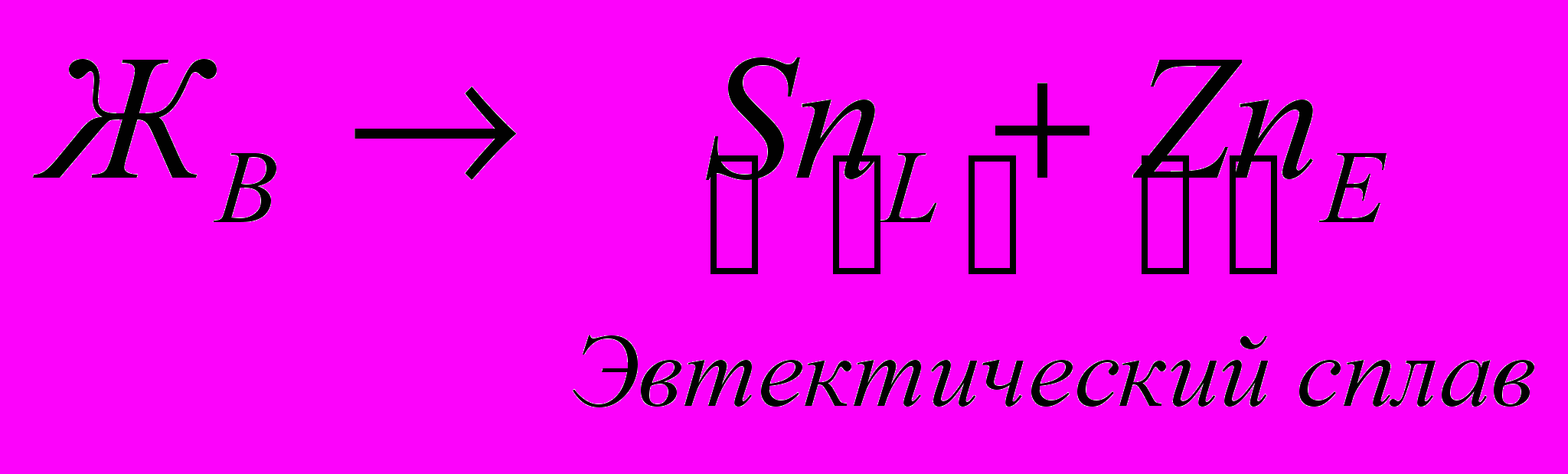
В качестве припоев применяют сплавы с содержанием олова 90,70,60 и 40% марок ПОЦ – 90, ПОЦ – 70, ПОЦ – 60 и ПОЦ – 40.
Наилучшим из этой серии является сплав ПОЦ -90, так как он имеет самую низкую температуру кристаллизации 2020С. Эти сплавы имеют более высокую прочность, нежели оловянно свинцовистые сплавы.
При образовании смесей олово-цинк свойства сплава изменяются по линейному закону, следовательно, значения свойств сплава находятся в интервале между свойствами чистых компонентов.
Литература: 1, 37-65; 3, 88-123; 3, 139 – 141.
Вопросы для самостоятельной проверки.
- Охарактеризуйте, что такое компонент, сплав, фаза и система?
- Как проводят построения диаграмм состояния сплавов? Что такое линия солидус и ликвидус?
- В чём различие между эвтектической, эвтектоидной и перитектической реакциями? Запишите их и проведите фазовый и структурный анализ?
- В чём сущность и назначение правила Курнакова?
- Что такое твердые растворы внедрения и замещения?
- Изобразите основные виды диаграммы состояния сплавов? Проведите структурный и фазовый состав сплавов по этим диаграммам.
Тема 3. Железо и его сплавы.
Диаграмма состояния «Железо-цементит». Построения кривых охлаждения (нагрева) для железоуглеродистых сплавов с применением правила фаз. Классификация углеродистых сталей по структуре, качеству и степени раскисления. Маркировка и назначение углеродистых сталей. Классификация и маркировка чугунов. Свойства, назначение и способы получения белых, серых ковких и высокопрочных чугунов. Влияние легирующих элементов на полиморфизм железа и на превращение в сталях. Получение сталей ферритного, мартенситного, ледебуритного и аустенитного класса. Маркировка, свойства и назначения легированных сталей.
Методические указания.
Наибольшее применение в промышленности имеют сплавы железа с углеродом – стали и чугуны. Поэтому изучение диаграммы состояния «железо-углерод» является основной задачей в подготовке специалистов машиностроительных предприятий. Указанная диаграмма (см. приложение рис. 2) показывает фазовый состав и структуру сплавов с концентрацией от чистого железа до цементита Fe3С (6,67% углерода). На диаграмме Fe – Fe3C показаны характерные точки и линии. Линия АВСД (линия ликвидус) показывает температуру начала кристаллизации из жидкого сплава кристаллов твердой фазы. Линия АНJЕF (линия солидус) является температурной границей, ниже которой сплавы находятся только в твёрдом состоянии. Характерными линиями являются также линия НJB, ECF и PSK. При температуре (14990С) (линия HJB) в сплавах протекает перитектическая реакция с образованием аустенита, состав которого по углероду соответствует точке «J».
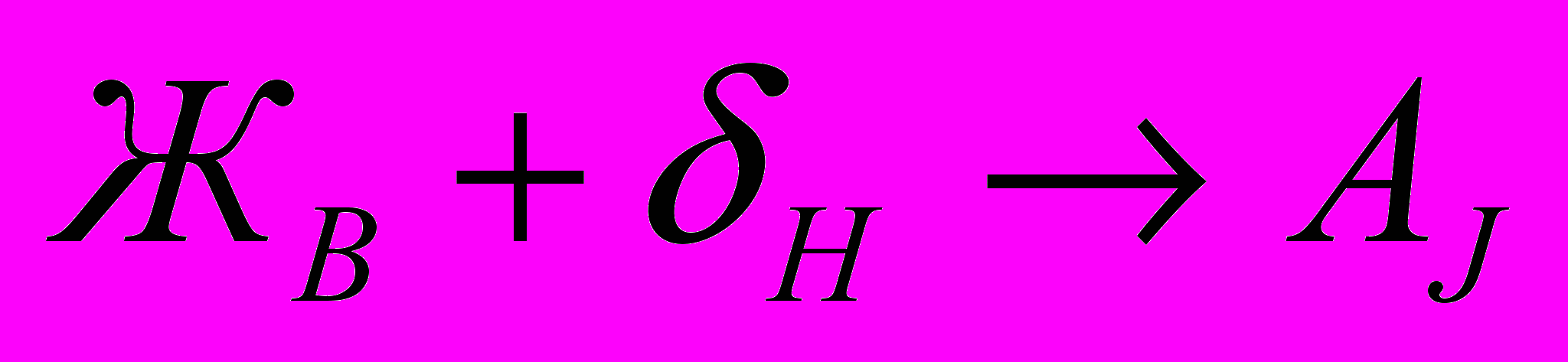
При температуре 11470С (линия ЕСF) в процессе охлаждения в сплавах протекает эвтектическая реакция с образованием ледебурита (Л) - смеси состоящей из аустенита (А) и цементита (Ц).

Линия РSК – линия эвтектоидного превращения, которая при охлаждении соответствует распаду аустенита с образованием эвтектоида – феррито - цементитной структуры, получившей название перлит.

Используя диаграмму «железо-углерод» рассмотрим изменения фазового состава сплава с содержанием 0,45% углерода. В приложении на рисунке 3. приведена кривая охлаждения для такого сплава. Точки на кривой охлаждения соответствуют точкам указанным на диаграмме Fe – Fe3C (см. приложение рис.2)
При температуре 14990С во время охлаждения сплава протекает перитектическая реакция, сущность которой состоит в следующем:

Образующийся аустенит имеет состав соответствующий точке «J». По содержанию углерода это 0,16%.
При дальнейшем охлаждении сплава вплоть до температуры соответствующей точки 3 система состоит из аустенита и жидкости. Окончательный переход жидкости в аустенит завершается при этой температуре, между температурами точек 3 и 4 сплав имеет аустенитную структуру.
При температуре 7270С (точка 5) во время охлаждения сплава в нем протекает эвтектоидное превращение.
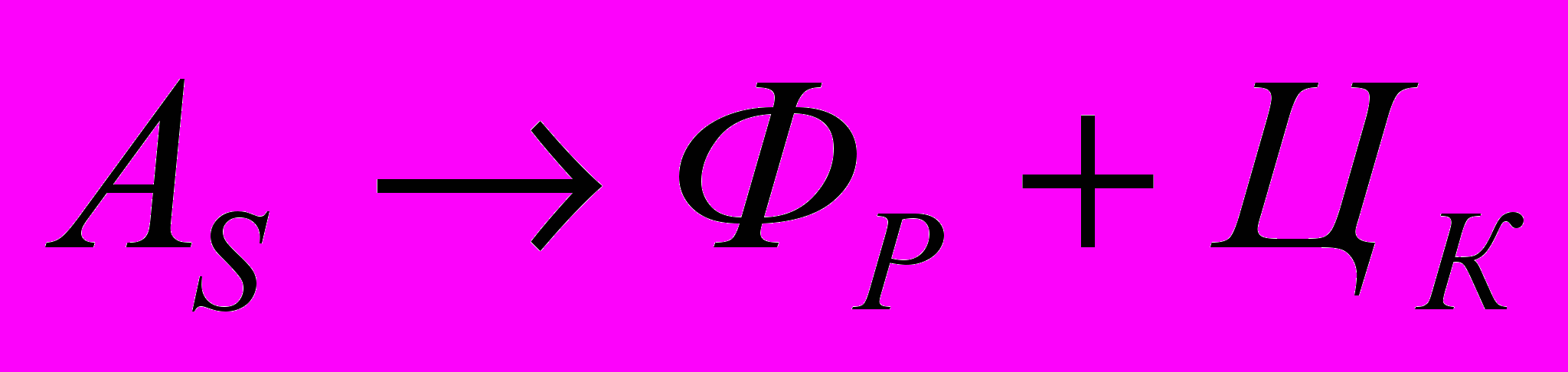
В результате этого превращения образуется механическая смесь, состоящая из феррита и цементита, то есть перлит. Содержание углерода в этой смеси – 0,8%. Последующее охлаждение до комнатной температуры не вызывает дополнительных превращений и структура сплава состоит из перлита и феррита.
В настоящее время в промышленности используется более 1500 марок сталей. По химическому составу стали, подразделяются на углеродистые и легированные. А любой стали, присутствуют постоянные (Si, Mn, S, P) и скрытые (О2, N2, Н2) примеси. По содержанию углерода стали, бывают доэвтектоидные (С0,8%) структура «перлит + феррит», эвтектоидные (С0,8%) структура «перлит », и заэвтектоидные (0,8 С 2,14%) структура «перлит + цемент». В зависимости от степени раскисления расплава Si, Mn и Аl стали, имеют различную степень загрязнения и называются спокойными (С.П.), полуспокойными (П.С.) и кипящими (К.П.). Наличие в стали серы и фосфора является основным критерием оценки её качества. В таблице 2 приведены предельно – допустимые содержания вредных примесей в стали различного качества.
Таблица 2.
№ | Качество стали | Содержание вредных примесей, в % | Интервал колебания по содержанию углерода | Условное обозначение | |
сера | фосфор | ||||
1 | 2 | 3 | 4 | 5 | 6 |
1 | Сталь обык-новенного качества | 0,06 | 0,07 | 0,09 | Ст.0 Ст.1 ![]() Ст.6 |
2 | Сталь качественная | 0,04 | 0,035 | 0,08 | Ст.45 40Х |
3 | Сталь высо-кокачествен-ная | 0,025 | 0,025 | 0,07 | Буква «А» в конце маркировки |
4 | Сталь особо-высокока-чественная | 0,015 | 0,015 | 0,07 | Буква «Ш» в конце маркировки |
Легированные стали – сплавы, в состав которых введены химические элементы для придания специальных свойств. Поэтому в маркировке стали в обязательном порядке указывают наличие такого элемента. Каждый легирующий элемент обозначают строго определённой буквой, а его количество указывают цифрой после буквенного обозначения. Отсутствие цифры означает, что такого легирующего элемента составляет 11,5% и менее. Условное обозначение, Х – хром; Н – никель; Т – титан; С – кремний; М – молибден; Ю – алюминий; Ф – ванадий; В – вольфрам; Д – медь; Г – марганец; К – кобальт; Б – ниобий; А – азот; Р – бор.
Примеры обозначения углеродистых и легированных марок сталей:
Ст. 0; Ст. 1Ст. 6- углеродистые стали обыкновенного качества. Цифра указывает на порядковый номер.
Сталь 10, Сталь 15 и т.д. – Стали углеродистые качественные. Цифра указывает на содержание углерода в сотых долях процента, а именно 0,10%; 0,15% и т.д.
Сталь 40Х – сталь качественная легированная, содержащая углерода 0,4%; хрома 1%, серы 0,035% и фосфора 0,035%.
Сталь 20Х2Н4ВА – сталь высококачественная легированная, содержащая: Углерод – 0,2%
Хром – 2%
Никель – 4%
Вольфрам 1%
Сера 0,025%
Фосфор 0,025%
При низком содержании углерода и большом количестве легирующего элемента (C , Мo, W, V, Si, Al и т.д.), образуется сталь, относящаяся к ферритному классу. Структура таких сталей при всех температурах состоит из легированного феррита. При высоком содержании в стали никеля и марганца при комнатной температуре можно получить чисто аустенитную структуру. Это класс сталей называют аустенитным. Кроме того, исходя из структуры полученной после охлаждения на воздухе, стали также бывают перлитного, мартенситного и карбидного классов.
На диаграмме Fe – Fe3C сплавы с содержанием углерода более 2,14% относятся к чугунам. В зависимости от содержания углерода, белые чугуны подразделяются на доэвтектичекие (2,14 С 4,3%), эвтектические (С4,3%) и заэвтектические (4,3 С 6,67%). Белые чугуны обладают высокой твёрдостью и износостойкостью. Углерод в таких сплавах находится в связанном состоянии в виде цемента (Fe3С). Это достигается за счёт высокой скорости кристаллизации расплава, и последующего ускоренного охлаждения изделий до температуры ниже точки А1.
При очень маленькой скорости охлаждения, то есть когда степень переохлаждения расплава невелика в сплаве образуется графит. Выделение графита в основном происходит из жидкой фазы и, кроме того, количество его увеличивается за счет распада аустенита.
В зависимости от формы графита и условий его образования различают следующие группы чугунов: серые, ковкие и высокопрочные. Чугуны маркируются следующим образом:
Ковкие – КЧ 30; КЧ 36 и тд.
Серые – СЧ 15; СЧ 40 и тд.
Высокопрочные – ВЧ 50; ВЧ 55 и тд.
Цифры указывают на минимальное значение предела прочности при растяжении.
Формы графита в чугунах:
Серых – пластичная; ковких – хлопьевидная; высокопрочных – шаровидная. Серые чугуны получают за счет медленного охлаждения расплава и изделия в форме, ковкие – путём высокотемпературного длительного отжига, высокопрочные – модифицированием расплава магнием или церием. Чугуны применяют в автостроении, двигателестроении и других отраслях народного хозяйства, как конструкционные материалы.
Литература: 1, 118 – 156; 3, 159 - 222
Вопросы для самопроверки.
- Что такое перлит, феррит, аустенит, цементит и ледебурит?
- В чём различие метастабильной и стабильной диаграммы Fe –Fe3C (Fe - C)?
- Как проводится маркировка углеродистых и легированных марок сталей и чугунов?
- Дайте объяснение и укажите способы получения белых и графитовых чугунов?
- Что такое критические точки А1, А2, А3, А4, и Ам?
- Вычертите диаграмму Fe – Fe3C, укажите структурное состояние во всех областях диаграммы и опишите превращение протекающие в сплавах при охлаждении при температурах 14990С, 11470С и 7270С?
- Разберитесь в построении кривых охлаждения (нагрева) сплавов с различным содержанием углерода.
Тема 4. Термическая обработка сталей и чугунов.
Основные превращения в сталях при нагреве и охлаждении. Критические точки в стали. Диаграммы изотермического превращения аустенита. Основные виды термической обработки: отжиг, нормализация, закалка и отпуск. Цель и назначение каждого вида термообработки. Закалка стали, её режимы и методы. Закалочные среды, понятие закаливаемости и прокаливаемости стали. Обработка стали холодом. Технология и виды отпуска. Отпускная хрупкость стали. Термомеханическая обработка. Виды брака при термообработке и методы его исправления и предупреждения.
Методические указания.
Термическая обработка – это процесс температурно-временного воздействия на металлы и сплавы с целью придания им необходимых свойств.
При многих видах термической обработки сталь нагревают до температур соответствующих существованию аустенита. Образование аустенита при нагреве является диффузионным процессом. При температуре 7270С перлит превращается в аустенит.
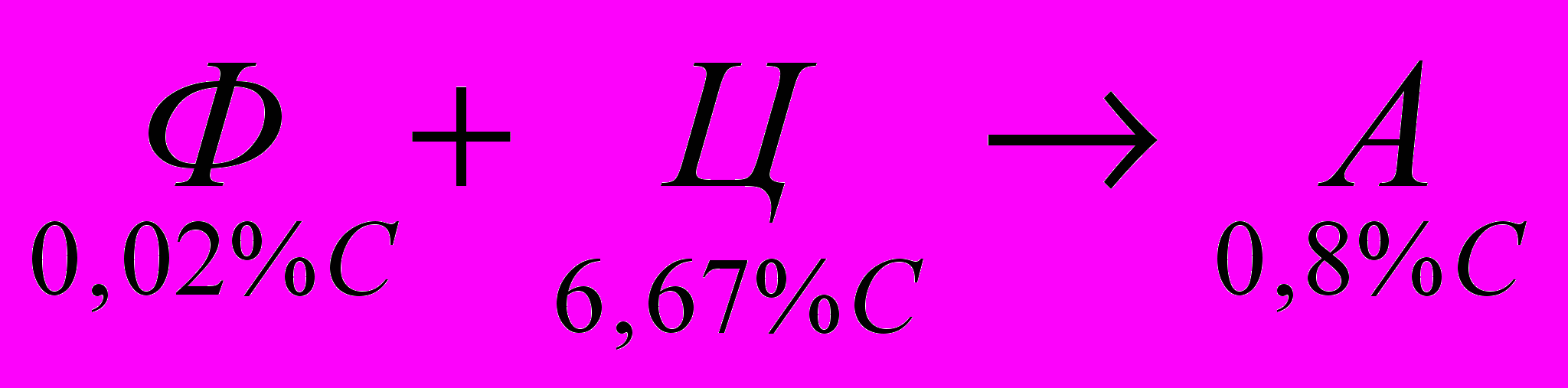
При невысоких температурах нагрева зерна аустенита мелкие. В результате повышения температуры зерно аустенита растёт. Однако склонность к росту зерна неодинакова у сталей, поэтому различают стали наследственно мелкозернистые и крупнозернистые. Продолжительный нагрев стали при температурах, значительно превышающих точки Ас3 или Асм приводит к образованию крупного зерна. Такое состояние называют, перегревом стали. Нагрев еще при более высоких температурах в окислительной среде вызывает пережог стали, который сопровождается образованием окислов железа по границам зерен. Пережог – неисправимый дефект стали. Величина зерна влияет на ударную вязкость и порог хладноломкости. Определение размера зерна проводится в соответствии с ГОСТ 5639-65.
Основными видами термической обработки являются отжиг, нормализация, закалка и отпуск.
Отжиг заключается в нагреве стали выше критической точки, выдержке и последующим медленным охлаждением. В результате отжига получают структуру перлит с ферритом или цементитом, и сталь приобретает высокую пластичность и низкую твёрдость. Различают следующие виды отжига: неполный, полный, изотермический, диффузионный и рекристализационный.
Нормализация стали это процесс нагрева выше критической точки Ас3 (Асm) с последующим охлаждением на воздухе. Получаемая структура – мелкопластинчатая перлитного класса (перлит, сорбит, троостит).
Закалкой называют нагрев стали выше точка Ас3 или Ас1 и последующее быстрое охлаждение (со скоростью выше критической). При охлаждении сталь приобретает структуру мартенсит и обладает высокой твёрдостью, прочностью и износостойкостью. На рисунке 18 (см. приложение) изображена зона оптимальных температур нагрева сталей под закалку в зависимости от содержания углерода. Закалка не является окончательным видом термической обработки. В зависимости от температуры нагрева закалка бывает полной и неполной. По условию охлаждения закалку подразделяют на непрерывную, прерывистую, ступенчатую и изотермическую. Чтобы уменьшить напряжения, вызванные закалкой, и получить нужные механические свойства, сталь после закалки обязательно подвергают отпуску.
Под отпуском понимают нагрев закалённой на мартенсит стали до температуры ниже точки Ас1 (7270С) с последующим охлаждением. В зависимости от температуры нагрева отпуск подразделяется на низкий (150 – 250оС), средний (300-450оС) и высокий (500-700оС). С увеличением температуры отпуска повышаются пластические свойства и снижается прочность стали.
Для грамотного назначения параметров термической обработки (температура и скорость нагрева, время выдержки и скорость охлаждения) с целью получения требуемых свойств стали необходимо пользоваться диаграммами изотермического и термокинетического распада аустенита.
В результате закалки сталей с содержанием углерода более 0.6 % углерода в структуре наряду с мартенситом сохраняется и остаточный аустенит, наличие которого снижает твердость и прочность изделия. Для превращения остаточного аустенита в мартенсит сталь необходимо переохладить до более низких температур. Эту задачу выполняет процесс обработки стали холодом.
Для упрочнения длинномерных изделий в промышленности применяют термомеханическую обработку, заключающуюся в сочетании горячей пластической деформации и термической обработки.
Отливки из чугуна подвергают отжигу, нормализации, закалке с отпуском в зависимости от требований предъявляемых к ним по структуре и твердости.
Рассмотрим выбор стали для изготовления пружин. Укажем состав и обоснуем режим термической обработки и опишем получаемую структуру и свойства стали.
(Для указанных деталей рекомендуем сталь 70С3А)
Сталь 70С3А. имеет следующий химический состав:
Углерод ~ 0,7% Сера 0,025%
Кремний ~ 3% Фосфор 0.025%
Марганец 0,8% Железо – остальное
Основные свойства рессорнопружинных сталей – придание изделиям высоких усталостных характеристик с целью надежной работы деталей в условиях знакопеременных нагрузок.
Для формирования таких свойств необходимо получить структуру троостит или троосто-мартенсит с твердостью 42-48НRС на деталях после термообработки. Такие свойства достигаются после нижеуказанной термической обработки:
- Нагрев в защитной атмосфере до температуры 820-860оС, выдержки до завершения всех фазовых превращений и закалка в масло с рабочей температурой 40-60оС. После закалки сталь приобретает структуру мартенсит + небольшое количество остаточного аустенита. Твердость 55 НRС.
- Отпуск при температуре 420-460оС в течении 2-3 часов.
После отпуска – структура троостит.
Свойства стали после такой обработки:
- Твердость 44-46 НRС.
- Предел прочности – более 1800Мпа.
- Предел текучести – более 1600 Мпа.
- Относительное удлинение (сужение) – более 6 (25)%.
Наличие кремния в стали, повышает ее прокаливаемость и значительно упрочняет феррит, задерживает распад мартенсита при отпуске и, как следствие, повышает предел текучести и упругость стали. Эти стали склонны к обезуглероживанию, поэтому их нагрев под закалку необходимо вести в защитной или контролируемой по углероду атмосфере.
Литература: 1,стр.156-220; 3 стр. 223-311.
Вопросы для самопроверки.
- В чем различия между перлитом, сорбитом и трооститом?
- Укажите сущность различных видов отжига и их назначение.
- Рассмотрите диаграммы изотермического и термокинетического превращения сталей. Объясните связь скорости охлаждения с превращениями в стали.
- В чем различие закаливаемости и прокаливаемости стали. Факторы влияющие на эти параметры и методы определения этих характеристик.
- Изучите традиционные закалочные среды и их применение для закалки изделий из различных марок сталей.
- Дайте понятие критической скорости охлаждения и изобразите ее на диаграмме изотермического превращения аустенита.
- Что такое обратимая и необратимая отпускная хрупкость.
- Какие преимущества имеет термомеханическая обработка перед закалкой с низким отпуском и почему?
Тема 5. Поверхностные методы упрочнения.
Основные методы поверхностного упрочнения – закалка с нагрева токами высокой частоты (Т.В.Ч.) и химико-термическая обработка (Х.Т.О.). Требования к химическому составу сталей для этих методов упрочнения. Механизм насыщения и формирования структуры в поверхностном слое при цементации, нитроцементации, азотировании и борировании. Примеры марок сталей, подвергаемых различным методам упрочнения. Термическая обработка цементованных и нитроцементованных деталей. Способы дополнительной поверхностной обработки деталей с учетом условий эксплуатации. Поверхностное упрочнение наклепом, лучем лазера и электронным лучом.
Методические указания.
Для получения большой твердости в поверхностном слое детали с сохранением вязкой сердцевины, что обеспечивает износоустойчивость и одновременно высокую динамическую прочность детали, применяют поверхностные методы упрочнения – закалку с нагрева Т.В.Ч. или Х.Т.О. Сущность закалки с нагрева Т.В.Ч. заключается в том, что поверхностные слои детали быстро нагреваются выше критических точек и создается резкий градиент температур по сечению. Если нагрев прервать и провести быстрое охлаждение, то слой металла, нагретый выше критической температуры получит закалку, а не нагретая сердцевина сохранит свое исходное структурное состояние. Для такого способа упрочнения применяют стали с содержанием углерода 0.4% и выше.
Химико-термическая обработка – процесс диффузионного насыщения поверхностного слоя неметаллами (С, N, Si,B и др.) или металлами (Cr, Al и др.) в процессе выдержки при определенной температуре в активной жидкой или газовой среде.
Широко применяются в машиностроении цементация (насыщение поверхности углеродом), нитроцементация (насыщение углеродом и азотом), азотирования (насыщение азотом) и борирование (насыщение бором). Цементации и нитроцементации подвергают, стали с содержанием углерода до 0,3%. Цементацию проводят при температуре 930-950оС, нитроцементацию – при 840-880оС. После насыщения изделия закаливают в масло, а затем подвергают отпуску при температуре 180-220оС. Эти виды Х.Т.О. обеспечивают получение твердости поверхности выше 55 НRС, а сердцевины менее 40НRC.
Для увеличения твердости, износостойкости, предела выносливости и коррозионной стойкости стальных изделий их подвергают азотированию, которое проводится при температуре 500-600оС в среде диссоциированного аммиака. Для азотирования применяют среднеуглеродистые легированные марки стали, предварительно прошедшие термическое улучшение. Упрочнение проводят на глубину 0,2-0,4 мм и получают поверхностную твердость в пределах 650-1200НV. Преимуществом этого метода является сохранение высокой твердости поверхности при нагреве деталей до 450-470оС и практически отсутствие деформации и коробления изделий.
Максимальная степень поверхностного упрочнения стальных деталей (НV1700 и выше) может быть получена путем борирования при температуре 910-950оС. После борирования стойкость деталей возрастает в 5-10 раз.
Для закрепления изученного материала, к примеру, проведен выбор обработки шестерен из стали 20Х. Рассмотрим микроструктуру и свойства поверхности и сердцевины детали после упрочнения. В соответствии с ГОСТ 4343-71 сталь 20Х имеет следующий химический состав:
Углерод – 0,17 – 0,23%;
Хром = 0,7 – 1,0%;
Кремний – 0.17 – 0.37%;
Марганец – 0,5 – 0,8%;
Сера, фосфор 0,035%;
Остальное – железо.
Свойства шестерен с учетом их условий эксплуатации должны быть следующими: для поверхности зуба – высокая твердость и износостойкость; для сердцевины – высокая пластичность.
Учитывая низкое содержание углерода в стали для упрочнения деталей рекомендуется: химико-термическая обработка – цементация или нитроцементация.
Оба вида упрочнения могут быть использованы, и выбор конкретного способа упрочнения зависит от требований предъявляемых к деталям по глубине упрочненного слоя и деформации и короблению деталей.
При глубине упрочненного слоя более 1,0 мм необходимо использовать цементацию, то есть провести насыщение поверхности детали углеродом. Цементация проводится при температуре 930-950оС, скорость насыщения углеродом 0,1 мм/час. После цементации детали подвергают термической обработке. Далее рассмотрим один из таких способов.
- Нагрев до 860-880оС, выдержка и охлаждение. Этот нагрев назначается с целью исправления крупнозернистой структуры сердцевины, полученной при нахождении стали длительное время при температуре цементации;
- Нагрев до 770-780оС, выдержка и закалка в масло;
После закалки получают твердость в пределах 58-62НRС на поверхности, и 30-35НRС в сердцевине.
- Отпуск при температуре 180-200оС для снятия напряженного состояния полученного в результате закалки.
Свойства шестерен после химико-термической обработки:
- Твердость поверхности – 58-62НRС;
- Микроструктура поверхности – мартенсит + остаточный аустенит;
- Твердость сердцевины – 30-35НRС;
- Микроструктура сердцевины – малоуглеродистый мартенсит + феррит.
Литература: 1, стр. 220-252; 3 стр. 312-340.
Вопросы для самопроверки
- Какие процессы протекают при химико-термической обработке?
- В чем сущность поверхностей закалки деталей с нагрева ТВЧ. Какие марки стали, подвергают этому способу упрочнения.
- Назовите преимущества и недостатки поверхностной закалки с нагрева ТВЧ в сравнении с Х.Т.О.
- Рассмотрите технологию цементации в твердом карбюризаторе и газовой атмосфере.
- Укажите преимущества нитроцементации деталей перед цементацией.
- Для каких целей используют поверхностную дробеструйную обработку стальных изделий?
- Изучите технологические процессы азотирования и борирования. Какие основные требования предъявляются к предварительной обработке упрочняемых деталей?
Тема 6. Конструкционные и инструментальные стали.
Классификация и назначение конструкционных сталей. Углеродистые качественные и обыкновенного качества стали. Легированные конструкционные стали. Цементуемые и улучшаемые стали, их свойства и применение. Рессорно-пружинные и шарико - подшипниковые стали. Стали повышенной обрабатываемости резанием. Стали для зубчатых колес, валов, деталей ходовой части и тормозной системы. Высоколегированные коррозионностойкие, жаропрочные и окалиностойкие стали.
Классификация и маркировка инструментальных сталей. Стали для режущего, штампового, медицинского и измерительного инструмента. Твердые сплавы, их свойства и назначение. Термическая обработка инструмента. Выбор марок сталей для инструмента с учетом условий эксплуатации.
Методические указания.
Конструкционные стали – это сплавы предназначенные для изготовления деталей машин и изделий строительной индустрии. Кроме того, к этой группе относятся и стали со специальными свойствами – износостойкие, коррозионно-стойкие, жаропрочные, пружинные и т.д.
Углеродистые стали обыкновенного качества изготавливают марок Ст.0, Ст.1, Ст.6. в соответствии с ГОСТ 380-71. Такие стали, в основном, применяют в строительстве, так как они обладают хорошей свариваемостью и достаточной прочностью.
Качественные углеродистые (ГОСТ 1050-74) и легированные (ГОСТ 4543-71) стали, применяют в машиностроении и других видах промышленности. Стали этого класса подвергают термической и химико-термической обработке для придания изделиям требуемых физико-механических свойств. Наличие легирующих элементов (до10%) в стали, обеспечивает высокие показатели прочности и пластичности и дает возможность их применения для высоконагруженных деталей машин. Высоколегированные стали (содержание легирующих элементов более 10%) имеют специальное назначение – коррозионно-стойкие, окалиностойкие, немагнитные и т.д.
Для улучшения обрабатываемости резанием в сталь дополнительно вводят серу, селен, свинец и кальций. Содержание серы и свинца до 0,3%, селена и кальция до 0,05% позволяет повысить стойкость режущего инструмента в 2 раза, но их наличие снижают свойства стали. Поэтому применение таких сталей не рекомендуется для деталей работающих в сложно - напряженном состоянии.
Повышение устойчивости стали против коррозии, достигается за счет введения в нее хрома, который образует плотную окисную пленку на поверхности типа Cr2O3. К этой группе относятся стали с содержанием хрома более 12%.
Инструментальные стали имеют высокую твердость, износостойкость и прочность. Они используются для режущего инструмента, штампов холодного и горячего деформирования, измерительных инструментов различных размеров и форм. Стали для режущего и штампового инструмента должны обладать теплостойкостью, то есть сохранять высокую твердость и прочность при нагреве до высоких температур. В связи с этим различают нетеплостойкие, полутеплостойкие и теплостойкие стали. Для инструмента подвергаемого нагреву до 200оС в эксплуатации применяют углеродистые, и низколегированные марки стали – У8, У10, У13, 9ХС, 11Х и т.д.
Полутеплостойкие стали, преимущественно используют для штампов горячего деформирования, рабочая кромка которого нагревается до 400-500ОС. Это стали легированные хромом, молибденом, вольфрамом и ванадием типа 4Х5МФС, 3Х3ВМФ, 5ХНМ, 5ХНВ и т.д.
При нагреве инструмента в процессе работы до 600-800оС для его изготовления рекомендуются быстрорежущие стали типа Р9, Р18, Р6М5К5 и др. Главный легирующий элемент таких сталей – вольфрам, который образует стойкий карбид.
Свойства инструментальных сталей достигаются за счет термической обработки закалки и отпуска.
Литература: 1, 252-313; 3, 364-508; 6, 73-135; 6, 143-174.
Вопросы для самопроверки.
- Можно ли кипящую сталь применять для изделий работающих при температурах ниже –40оС?
- Чем объяснить хорошую обрабатываемость резанием стали легированной S, Pb,Ca?
- Каким требованиям должна обладать сталь для холодной штамповки?
- Какую термическую обработку проходят стали 40ХН, 40Х, 38ХМЮА, 42ХМФА?
- Какие стали, применяют для работы в окислительных и других агрессивных средах?
- Назовите марки сталей для пружин, рессор и подшипников? Каким видам термической обработки они подвергаются?
- Какие достоинства и недостатки имеют углеродистые стали для режущего инструмента?
- Укажите, стали для штампов холодного и горячего деформирования. Рассмотрите термическую обработку и получаемые свойства этими сталями.
- Какие требования предъявляются к сталям для измерительного инструмента и укажите пути достижения стабильности структуры и свойств при эксплуатации?
Тема 7. Цветные металлы и сплавы.
Классификация медных, алюминиевых и магниевых сплавов. Латуни и бронзы, их маркировка, свойства и назначение. Алюминиевые сплавы, их маркировка, термическая обработка, свойства и области применения. Припои и антифрикционные материалы. Припои на оловянистой и свинцовой основе. Выбор сплавов для изделий машиностроения.
Методические указания.
В машиностроении широко используют сплавы на основе меди, алюминия, магния и титана. Основное преимущество медных сплавов - латуней и бронз, - низкий коэффициент трения, высокая пластичность и хорошая стойкость против коррозии в ряде агрессивных сред. Латунь – это сплав меди с цинком. Для придания специальных свойств латуням в их состав вводят дополнительные химические элементы, о чем указывают в маркировке. Пример обозначения латуни ЛС 59-1 ( медь – 59%, свинец –1%, цинк – остальное до 100%).
Бронза – сплав меди с одним или несколькими химическими элементами, среди которых в качестве второго и последующего элемента может быть и цинк.
Пример обозначения бронз:
Бр. АЖН 10-4-4 ( алюминий – 10%, железо – 4%, никель – 4; медь – остальное).
Алюминиевые сплавы – дюралюмины и силумины – обладают малой плотностью при достаточно высоких механических свойствах. Эти сплавы получают методом литья и спеканием и могут подвергаться пластической деформации. Примеры обозначения сплавов: Д16 (дюралюмин), АЛ 9 (силумины).
Магниевые сплавы (например МА2) обладают небольшой плотностью, небольшим модулем упругости и высоким уровнем демпфирования.
Титановые сплавы имеют высокую коррозионную стойкость, высокую прочность при низких температурах и хорошую жаропрочность.
Пример: Для изготовления некоторых деталей самолёта используется сплав AMr. Приведите характеристики механических свойств сплава и его состав.
Сплав Al с Mg относятся к сплавам не упрочняемых термической обработкой. Упрочнение такого сплава происходит за счёт образования - твёрдого раствора (раствор Mg в Al).
Из приведенного рисунка 19 (см. приложение) видно, что сплавы Al с Mg обладают наивысшими прочностными и пластическими свойствами при содержании в них магния до 15%. Поэтому в промышленности применяют сплавы с небольшим содержанием магния – типа AMг 2, AMг 3, AMг 5, AMг 6.
Химический состав и механические свойства сплавов приведены в таблице 3
Таблица 3
Сплав | Содержание элементов, % | Механические свойства | |||
Mn | Mg | B, MПa | 0,2MПa | ,% | |
AMг 2 | 0,2-0,6 | 1,8-2,8 | 200(250) | 100(200) | 23(10) |
AMг 3 | 0,3-0,6 | 3,2-3,8 | 220 | 110 | 23 |
AMг 5 | 0,3-0,6 | 4,8-5,8 | 300 | 150 | 20 |
AMг 6 | 0,5-0,8 | 5,8-6,8 | 340(400) | 170(300) | 18(10) |
Указанные сплавы применяются в отожженном состоянии. Отжиг проводится при температуре 270-2800С (AMг 3) и 350 – 4100С (AMг 2).
Повысить прочность этих сплавов можно за счёт нагартовки (наклёпа). В таблице 3 показаны свойства сплавов после того упрочнения.
Сплавы Al c Mg хорошо обрабатываются резанием, хорошо свариваются и обладают высокой коррозийностью.
Литература: 1,378-432; 564-628; 6, 395-582.
Вопросы для самопроверки.
- Расшифруйте цветные металлы и сплавы: М1; ЛО 60-2; Бр. Б2; Бр. АЖ 9-4; А99; АЛ21; Д16; МА 2-1; МЛ15; ОТ 4-1; ВТ22.
- Для каких целей используют оловянные, алюминиевые и бериллиевые бронзы?
- Укажите преимущества и недостатки титановых сплавов в сравнении с медными сплавами.
- За счет чего увеличивается прочность магниевых сплавов?
- Изучите способы термической обработки алюминиевых сплавов и уясните их причину упрочнения.
- Приведите примеры применения цветных сплавов в машиностроении.
Тема 8. Неметаллические материалы.
Классификация полимерных материалов. Пластмассы и эластичные материалы. Термопласты и пластики с твердым наполнителем. Органические стекла. Техническая керамика. Технология производства пластмассы и резины. Композиционные материалы. Области применения и преимущества применения таких материалов.
Методические указания.
Неметаллические материалы являются в ряде случаев заменителями металлических материалов, но и применяются, как и самостоятельные. Их применение обеспечивает значительную экономию при достаточно высокой механической прочности, легкости, термической и химической стойкости и технологичности. Наибольшее применение имеют пластмассы, композиты, резина, стекло, ситаллы и керамика. В зависимости от рабочей температуры пластмассы подразделяются на термопластичные и термореактивные.
Композиционные материалы – это искусственные материалы, получаемые сочетанием химически разнородных компонентов. Это перспективные материалы для различных отраслей машиностроения. Основное применение нашли карбоволокниты, бороволокниты, органоволокниты и материалы с металлической матрицей.