Содержание общие вопросы метрологического обеспечения измерительных систем 9 Брюханов В. А. 9
Вид материала | Доклад |
СодержаниеО некоторых особенностях нормированияи контроля метрологических характеристикИС учета количества нефтепродуктов М обе части (3)): (4) Здесь k Крысин Ю.М. |
- Вопросы по дисциплине «Метрология, стандартизация и сертификация» для подготовки, 69.28kb.
- Организационной основой метрологического обеспечения ОАО «Теплоприбор» является Центр, 31.48kb.
- Совершенствование метрологического обеспечения инклинометрии нефтегазовых скважин 25., 254.4kb.
- Решение IX семинара по вопросам метрологического обеспечения топографо-геодезического, 201.85kb.
- Эталонный комплекс для метрологического обеспечения акустических измерений в твердом, 58.45kb.
- Экзаменационные вопросы по дисциплине «Измерительная техника», 40.7kb.
- Методика приемки из наладки в эксплуатацию измерительных каналов информационно-измерительных, 235.63kb.
- Отдел метрологического обеспечения измерений физико-химических величин, 18.17kb.
- Рабочая программа дисциплины мерительные устройства систем управления, 448.87kb.
- Анализ и синтез измерительных преобразователей с частотным выходным сигналом для информационно-измерительных, 675kb.
О некоторых особенностях нормирования
и контроля метрологических характеристик
ИС учета количества нефтепродуктов
Терминальные комплексы на базе резервуаров можно рассматривать как многоканальные крупнотоннажные дозаторы. Сложный канал такой ИС образован градуированным резервуаром с системами измерения уровня и плотности продукта. Система измерения плотности может быть как полностью автоматизированной, так и с “ручным” вводом значений плотности, измеряемой в отбираемых пробах. В любом случае многоканальная система измерения температуры, входящая в каждый сложный канал, играет вспомогательную роль. Наибольшее распространение в последнее время получают радарные уровнемеры и системы измерения средней плотности типа “уровень + гидростатический подпор” с прецизионным дифманометром.
Первое, на что мы обратили внимание при поверке: ИС не имеют паспорта, он не предусмотрен описанием типа в разделе “Комплектность”. Казалось, можно было бы поверять каждый сложный канал и ограничиться свидетельствами о поверке каналов измерений уровня, температуры, плотности и свидетельством на канал. Однако в реестре у нас ИС, а не отдельный канал, да и задача учета решается системой в целом, а не одним каналом. Даже в мелководном Архангельском нефтяном порту, куда приходят танкеры дедвейтом до 10000 т, загрузку одного танкера иногда приходится производить из нескольких резервуаров, тем более что значительная часть резервуарного парка – это емкости в 5000 м3. Работу пришлось начинать с составления паспортов на ИС и утверждения их руководством организации – владельца. Терминальные комплексы крупных нефтяных компаний находятся в стадии интенсивного оснащения резервуарного парка измерительными компонентами, так что состав ИС будет меняться – число каналов будет увеличиваться. Это обстоятельство следует учесть, допустив периодическое обновление паспорта от поверки к поверке по мере “распухания” ИС.
В эксплуатационных документах рассматриваемых ИС обычно нормированы характеристики погрешности измерительных компонентов-уровнемеров, дифманометров, каналов измерения температуры. В то же время методики поверки предусматривают поканальный принцип: поверять рекомендовано канал измерений уровня, канал измерений средней температуры, канал измерений средней плотности.
У каждого из этих каналов имеются не только характеристики погрешности, но и установленные диапазоны измерений. В условиях поверочной лаборатории можно было бы провести полномасштабную поверку указанных средств измерений – измерительных компонентов сложного канала – в установленных точках диапазонов измерений. Правда, один из важнейших измерительных компонентов – резервуар- все равно поверяется (градуируется) на месте эксплуатации.
Нефтяной терминальный комплекс – технический объект с непрерывным производственным циклом. Одни резервуары принимают продукт, другие отпускают, и только третьи некоторое время находятся в “состоянии покоя”. Поверка измерительных каналов сложного канала возможна только в последних, поскольку требуется определенное время (это время зависит от вида продукта, в основном, от его вязкости, так что существенное влияние оказывает температура продукта) для достижения равновесных состояний, в которых поверка имеет смысл. Нереально позволить себе ждать, когда в одном резервуаре будет воспроизведено несколько различных состояний – уровней, температур, плотностей. Поэтому поверка проводится в “точке технологического состояния резервуара” на момент поверки. Сравниваются усредненные значения измеряемых величин, полученные с применением эталонных СИ, и показания, снимаемые с дисплея в операторском зале системы. Если канал системы снабжен дисплеем на месте установки (на крыше резервуара), то показания этого дисплея принимались за измеренные значения. Отдельно проверялось соответствие показаний на промежуточном и оконечном дисплеях.
Заметим, что рассматриваемые системы не являются диковинным исключением. Можно указать ещё на системы учета (практически это тоже системы отпуска количества товара) количества теплоты на крупных ТЭЦ с трубопроводами диаметром порядка метра и более. Установленные на таких трубопроводах расходомеры (с ультразвуковыми, электромагнитными преобразователями средней скорости потока воды) могут подвергаться контролю метрологических характеристик на месте установки в реальных режимах работы. По крайней мере, зимние и летние расходы, различающиеся в разы, дают возможность проводить контроль (технологию его еще нужно продумать, прежде чем можно будет называть эту операцию поверкой) в двух точках диапазона измерений.
Схема принятия решений по результатам поверки проста и естественна: сложный канал ИС годен, если признаны годными все его “простые” каналы. Система в составе годных каналов в целом признается годной.
На каждый простой, каждый сложный канал и на систему в целом составляется протокол поверки и оформляется свидетельство о поверке. Так, на ИС, принадлежащую ООО “Роснефть-Туапсенефте-продукт” и включавшую на момент поверки 15 сложных каналов, было оформлено 61 свидетельство1.
Обратимся к характеристике погрешности сложного канала – канала измерений количества продукта в резервуаре. Нас, строго говоря, не интересует предел допускаемой погрешности, поскольку мы не поверяем сложный канал комплексно и нам не нужно использовать это “браковочное число”. Для нас важно оценить предельную погрешность определения массы продукта при заданной доверительной вероятности – практически то, что имеется в виду при оценке составляющей типа “В” неопределенности результата [1]. Рассмотрим случай полностью автоматического канала, когда автоматически измеряются и уровень, и средняя плотность. Запишем для массы М продукта в резервуаре:
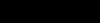
Здесь h – значение уровня, – средняя плотность, S(h) – среднее значение сечения при уровне h.
Поскольку


Будем исходить из того, что ускорение свободного падения в месте установки резервуаров известно с достаточной точностью и не вносит вклада в неопределенность.
Стандартная неопределенность по типу “В” с учетом корелляционной независимости составляющих запишется:
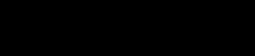
или, в относительных величинах (делим на М обе части (3)):
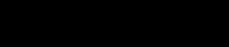
Здесь k() – коэффициент охвата для доверительной вероятности , р – предел допускаемой приведенной погрешности дифманометра,

И короткое замечание о неопределенности измеренных значений отпущенной/принятой массы продукта:

Обратим внимание на то, что оба значения массы в (5) измерены “одним и тем же прибором”, так что коэффициент корреляции погрешностей положителен и наверняка заметно больше нуля. Учитывая вид формулы (5), запишем:

Здесь – коэффициент корреляции.
Для нас существенно то, что корреляция погрешностей измерений масс до отпуска продукта и после окончания отпуска в целом снижает значение оцененной неопределенности.
Такие расчеты были проделаны для одного из резервуаров терминала ООО “Роснефть-Туапсенефтепродукт”.
При полной емкости 10000 м3 для бензина плотностью 753 кг/м3 начальный уровень был 11200 мм, конечный 3500 мм. Без учета корреляции оцененная неопределенность отпуска составила 8050 кг или 0,18%, с учетом корреляции 6500 кг или 0,15%. Основной составляющей при оценке коэффициента корреляции считались полностью коррелированные погрешности дифманометра, тогда как погрешности градуировки резервуара полагались некоррелированными.
Литература
1. Руководство по выражению неопределенности измерений / Пер. ФГУП “ВНИИМ им. Д.И. Менделеева”. – Санкт-Петербург, 1999.
Авторы
Евдокимов Александр Степанович – заместитель генерального директора ФГУ “Ростест-Москва”.
Тел. (095) 332-98-56 E-mail: metrology@rostest.ru
Медведев Валерий Афанасьевич – начальник лаборатории ФГУ “Ростест-Москва”, к.т.н.
Тел. (095) 332-18-72. E-mail: valeryam@rostest.ru
Мурин Петр Николаевич, начальник сектора ФГУ “Ростест-Москва”
Тел. (095) 332-97-01
Россия, 117418, Москва, Нахимовский пр. 31. www.rostest.ru