Итоги тысячелетия, столетия, года александр Прохоров
Вид материала | Статья |
СодержаниеТяни vs Толкай, или “куда ни крути, а главное — кто будет отвечать” JIT и Kanban JIT и Kanban Рис. 5. “Виртуальный бизнес” |
- Объединенная компания «Российский Алюминий», 2149.38kb.
- Итоги Второй мировой войны для Великобритании, 536.44kb.
- Конец двадцатого столетия и первые годы нашего нового тысячелетия в ретроспективе составляют, 116.51kb.
- Методичні рекомендації по розділу "Поліклініка", 2465.5kb.
- Итоги 2011 года дмитрий Медведев и Владимир Путин подвели в правительстве итоги года, 428.81kb.
- Декларация тысячелетия Организации Объединенных Наций, 150.18kb.
- Итоги ivстолетия. Культура XII-XIII в в. III четверть: V ст.(1262-1362). Образование, 402.83kb.
- В. М. Розин (Институт философии ран), 3988.06kb.
- Б. Б. Прохоров Экология человека: понятийно-терминологический, 2497.75kb.
- Унас в гостях блистательный писатель Александр Мелехов, 29.83kb.
Тяни vs Толкай, или “куда ни крути, а главное — кто будет отвечать”
Не претендуя на абсолютную точность могу предположить, что идея управления логистическими цепочками зародилась в недрах методов производственного управления известных как JIT (Just in Time — “точно вовремя” заказать и установить ) и Kanban (точно во-время привезти). По сути дела это модификации одного и того же метода, первая ориентирована на push, вторая — на pull технологию. В какой-то момент эти технологии казались “панацеей” от всех производственных болезней, но их недостатки не позволили сделать их “универсальными”. Возможно что на пути их распространения стала как раз их существенная трудоемкость реализации,
Идея данных методологий состоит в том, что затраты на производство можно существенно сократить, если кардинально уменьшить складские запасы, а следовательно и издержки на них. Комплектующие при этом идут “в работу” “с колес”, не скапливаясь на складах временного хранения, где они имеют тенденцию портиться и теряться (типичный пример подобной ситуации — площадки вокруг строящихся домов, забитые “про запас” привезенными блоками, а после окончания стройки — их обломками). Естественно подобный стиль работы требует повышенной ответственности всех работников и весьма качественной системы управления поставками в целом. По-видимому, это и привело к анализу всей системы поставок и, впоследствии, к созданию концепции управления логистическими цепочками.
Интересно, что распространение JIT и Kanban оказалось значительно меньше, чем первоначальный интерес к ним. И этому есть несколько весьма важных причин. Избежать ошибок в ассортименте и срывов сроков поставок очень трудно даже в условиях Японии и США, а каждый такой “сбой” приводит, в условиях “точных” технологий, к остановке производства. Поэтому приходится держать “горячий запас” в размере по меньшей мере разовой загрузки оборудования, что, в условиях крупных производств, может оказаться довольно накладно. Поэтому не удается избежать кардинальной статьи затрат — капитальные вложения в складские помещения и оборудование, а ее то больше всего и хотелось “редуцировать”. Однако, в некоторых секторах производства, например малосерийная сборка и строительство, данная технология весьма распространена, в частности, в большинстве высокотехнологичных компаний: Nortel, Xerox, HP, Honda, Toyota, Sony. Для тех отраслей, где она применяется, характерна малая мощность обрабатывающих центров, как правило многоцелевых, стабильные сборочные спецификации и технологические карты.
Еще один важнейший момент в понятии “логистическая цепочка” — уже упомянутое и мало пока привычное понятие push/pull технологии. Сущность данного понятия — различные точки инициирования операций по всей “цепочке”. Например, вариант “выталкивания” продукции. Предприятие произвело продукт, далее продает — “с глаз долой, из сердца вон”. Или технология “выдергивания” — “надо — вот возьмите”. Естественно это упрощенный подход. К тому же концепция push/pull не вполне очевидна — она показывает довольно тонкое различие между методологиями управления системой закупок или продаж, к тому же практически применяемые системы продаж часто являются некоторой смесью двух базовых техник. Опять же очень упрощенно можно сказать, что система продаж по заказам — это технология выдергивания, а производство на склад — технология выталкивания.
Что интересно, так это то, что создание и развитие этих технологий не связано непосредственно с информационными технологиями, в отличие от системы MRP—ERP. Обе технологии вполне реализуемы и ручными методами, более того реализация их в автоматизированных системах оказалась достаточно сложной, так как кроме количественных показателей в них необходимо регистрировать и такой неочевидно формализуемый показатель, как “ответственность за принятие решения”.
Различие между методами JIT и Kanban принципиально, что станет ясно если включить в рассмотрение не только общую схему товародвижения, но и схему ответственности за процесс. В случае “выдергивания” ответственность фокусируется на “конечном” исполнителе. В случае “выталкивания” она распределяется по уровням логистической цепочки, в результате чего повышается устойчивость системы управления в целом и снижается риск принятия неверных решений (естественно, при ответственном отношении каждого менеджера и исполнителя, что также не всегда имеет место). Однако при этом ответственность становится менее гибкой — снижается “обратная связь” с последних стадий производства, что в принципе может создать проблемы с исправлением выявленных недостатков в качестве продукции и увеличивает проблемы в случае возникновения непредвиденных ситуаций. Например, изменение строительной спецификации при “выталкивании” приводит к существенно большим проблемам, чем при “выдергивании”. Действительно, спецификация доведена до всех уровней, включена в производственные планы. Определить на какой стадии и где нужно вмешаться, достаточно сложно. При схеме “выдергивания” процесс разбит на маленькие звенья, связанные в цепь, и “спускаясь” по цепочке значительно легче обнаружить “активное” звено и произвести изменения.
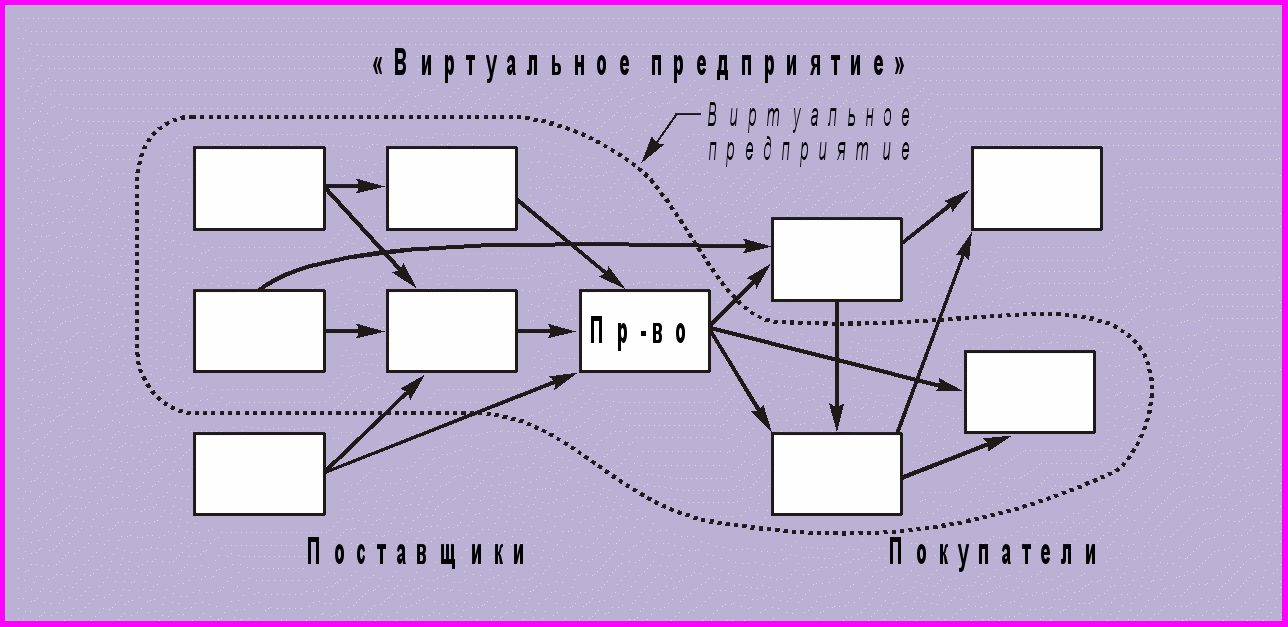
Рис. 5. “Виртуальный бизнес”
Баланс
Однако, вернемся к логистическим цепочкам. Уже сама по себе, логистическая цепочка представляет собой весьма интересный инструмент управления бизнесом. Но кроме того, с использованием соответствующих финансовых инструментов возможно создание “виртуального бизнеса” (рис. 5) из распределенной системы нескольких компаний, охватывающего полный “жизненный цикл” товара, или, наоборот, разделение одной компании на несколько “виртуальных бизнесов”. При этом для каждого “виртуального бизнеса” возможна поддержка полного спектра “виртуальных систем управления”, характерных для единой компании. Однако такая система работает корректно только в случае “прозрачности” всей “виртуальной” сети, входящей в компанию. При наличии “черной растаможки”, что характерно для наших условий, да и “серой”, применяемой повсеместно, корректность определения полной стоимости товара и операционных издержек весьма условна, что сводит на нет все усилия по финансовому управлению виртуальным предприятием с помощью “простых рецептов” логистических цепочек. Для этих случаев применяются методы управления финансовыми холдингами, о которых следует говорить отдельно.
В заключение хотелось бы обратить внимание на один аспект, который пока ускользнул от внимания аналитиков. Методологии Supply Chain и CSRP взаимно дополняют друг друга. Первая фокусируется на “глобальной” логистике и связанных с ней, “внешних”, по отношению к производству, процессах, вторая — на “внутренних”, в частности, на тонком управлении заказами и расширенном управлении издержками, благодаря трактовке бизнес-цикла товара, как “расширенного” производственного цикла, и, что важно, не “товара вообще”, как MRP, а “товара в конкретном заказе”, что точно соответствует идеологии Supply Chain.
Учитывая, что “ядром” логистических цепочек является производитель (в глобальном толковании — производитель добавочной стоимости), можно сказать, что методология CSRP — это методология производственного ядра Supply Chain. Объединение этих двух методологий в единой системе позволило бы выйти на новый качественный уровень систем и методологий управления ресурсами бизнеса. Автоматизированные системы, поддерживающие “тонкое” управление заказами и логистическими цепочками, могут дать очень значительные конкурентные преимущества. Исходя из общих тенденций развития делового программного обеспечения можно предположить, что такого рода предложения должны появиться уже к концу текущего года.