Конференция «современные технологии водоподготовки и защиты оборудования от коррозии и накипеобразования»
Вид материала | Доклад |
- Комплексная программа по предотвращению процессов коррозии и накипеобразования в теплообменном, 1017.43kb.
- Конференция «современные технологии водоподготовки и защиты оборудования от коррозии, 1036.07kb.
- Удмуртским Государственным Университетом и нпк «Вектор». На чтениях прозвучал 41 доклад, 1249.61kb.
- Основные вопросы, которые планируется затронуть: Нормативно-правовое и нормативно-техническое, 49.05kb.
- Vi методы защиты от коррозии металлов и сплавов, 783.92kb.
- Ооо «интехэко» инновационные технологии и экология, 194.03kb.
- Защиты от коррозии и старения, 844.02kb.
- Защиты от коррозии и старения, 1104.68kb.
- Методическая разработка урока химии по теме: «понятие о коррозии металлов, способы, 159.91kb.
- Коррозии, виды коррозийных повреждений на газопроводах. Стресс-коррозия на газопроводах,, 549.97kb.
ЛИТЕРАТУРА:
- Правила технической эксплуатации электрических станций и сетей. М.: Энергоатоиздат, 1989.
- Методические указания по контролю состояния основного оборудования тепловых электростанций. РД 34.37.306–87. М.: СПООРГРЭС. 1988.
- Методические указания по эксплуатационной химической очистке котлов энергоблоков сверхкритического давления. РД 34.37.403–91. М.: СПО ОРГРЭС. 1991.
4. Химические очистки теплоэнергетического оборудования. Под ред.
Т.Х. Маргуловой. М.: Энергия. 1969.
- Шадрина Н.И., Соловьев С.Ф. Надежное ингибирование коррозии металлов – основа безопасности проведения химической очистки оборудования // Теплоэнергетика. 1999. №7. С. 20–24.
- Василенко Г.В., Мурзин М.А. Ингибиторы коррозии для химических очисток котлов // Электрические станции. 2000. №7. С. 25–26.
- Петров Л.Н., Сопрунюк Н.Г. Коррозионно–механическое разрушение металлов и сплавов. Киев: Наукова думка. 1991.
- Методические указания по предпусковой парокислородной очистке и пассивации пароводяного тракта теплоэнергетического оборудования.МУ 34–70–128–85. М.: СПО Союзтехэнерго. 1986.
9. Методические указания по послемонтажной пароводокислородной очистке и
пассивации внутренних поверхностей нагрева электрооборудования. РД 34.37.409–96.
М.: СПО ОРГРЭС. 1997.
10. Манькина П.П. и др. Стендовые исследования пароводокислородной очистки
и пассивации внутренней поверхности труб // Теплоэнергетика. 2000. №7. С. 23–27.
11. Стефанский И.Б. и др. Опыт применения парокислородной очистки и
консервации проточных частей паровых турбин // Электрические станции. 1997. №5.
С. 21–23.
- Методические указания по консервации теплоэнергетического оборудования с применением пленкообразующих аминов. Дополнение к РД 34.20.597–97. М.: 000 "Планти–ПРИНТ", 1998.
- Акользин П.А., Королев Н.А. Применение пленкообразующих аминов для защиты от коррозии теплосилового оборудования. Москва. БТИОРГРЭС, 1961.
14. Чемпик Э. Комлексное исследование влияния поверхностно–активного
вещества (пленкообразующего) октадециламина на энергетические и структурные
характеристики влажнопаровых потоков турбин и поведение основного оборудования
пароводяных контуров. М.: МЭИ. Автореферат канд. диссертации. 1980.
15. Филиппов Г.А. и др. К вопросу о консервации оборудования ТЭС И АЭС с использованием пленкообразующих аминов. Тэплоэнергетика. 1999. №4. С. 48–52.
16. Стырикович М.А. и др. Процессы генерации пара на электростанциях. М.:
Энергия, 1969.
17. Рыженков В.А., Куршаков А.В., Кулов В.Е., Петрова Т.И. Способ
химической очистки от отложений поверхностей теплоэнергетического
оборудования. Патент №2000117233, Российская Федерация, МПК 7 F28G9/00, В08
D3/08, С23 G3/04.
- Рыженков В.А., Куршаков А.В., Кулов В.Е. Опыт консервации блоков 200 Мвт Шатурской ГРЭС–5 с применением пленкообразующих аминов. // Водоподготовка, водный режим, химконтроль на ТЭС и АЭС и топливоиспользование. Тез. докладов научно–технической конференции МЭИ. М.: 000 "Планти–ПРИНТ", 2000, с. 23–24.
- К вопросу об эффективности удаления отложений, санации и защиты от коррозии поверхностей пароводяных трактов оборудования ТЭС. / Доброхотов В.И., Рыженков В.А., Куршаков А.В., Кулов В.Е., Шамко В.Н., Гвоздев В.М. // Теплоэнергетика. – 2002. – N1. – с. 44–49
ИНГИБИРОВАНИЕ КОРРОЗИИ МЕТАЛЛОВ
В ВОДНЫХ РАСТВОРАХ ФОСФОНАТАМИ.
Кузнецов Ю.И., Исаев В.А., Зинченко Г.В., Институт физической химии РАН, г. Москва
Тезисы доклада
Несмотря на то, что композиции на основе фосфоновых кислот как средства для защиты от накипеобразования и коррозии систем промышленного водопользования известны с 60–х годов прошлого столетия, исследование механизма их действия по прежнему привлекают многочисленных исследователей во всем мире.
В работах, начатых в нашем Институте еще в 70–х годах были впервые предложены и развиты представления о формировании на металлах пленок, предотвращающих их коррозию.
Согласно этому механизму, при взаимодействии стали с комплексонатом, в условиях подщелачивания приэлетродного слоя вследствии катодной реакции восстановления кислорода, на поверхности металла формируется труднорастворимая пленка, обладающая эффектом последействия и состоящая из гидроксида катиона-комплексообразователя и полиядерных комплексов фосфоновой кислоты с катионами железа. Установлено, что эффективность этих ингибиторов в водных средах, не содержащих солей жесткости, зависит от произведения растворимости катиона–комплексообразователя и константы устойчивости самого комплекса.
Эти закономерности сохраняются при замене лиганда комлексоната, изменении состношения металл: лиганд, а также при повышении температуры воды.
Обсуждаются вопросы, связанные с ролью катионов железа и рН воды при ингибировании коррозии стали комплексонатами.
Исходя из полученных закономерностей предложены пути повышения эффективности этих ингибиторов при реагентной обработке систем промышленного водопользования.
АНАЛИЗ ПРИЧИН И ПУТЕЙ БОРЬБЫ С БАКТЕРИАЛЬНОЙ
КОРРОЗИЕЙ ТРУБОПРОВОДОВ ТЕПЛОВЫХ СЕТЕЙ
Г. ОДЕССА.
А.В. Талалай, Б.Н. Шукайло, П.В. Коломиец, НПФ «МИОР», Северодонецк
Впервые с проблемой бактериальной коррозии трубопроводов теплосетей НПФ «МИОР» столкнулась в 1999 г при отмывке поверхности теплообмена котлов КВ–ГМ 50 от отложений. Отложения представляли собой плотный слой оксидов железа, в основном магнетита с высокой электропроводностью. Анализ добавочной воды показал ее соответствие с требованиями по показателям жесткость (<50 мкг–экв/л), железо. Содержание кислорода колебалось на уровне 50÷100 мкг/л.
В обратной воде содержание солей жесткости не увеличивалось (присос отсутствовал), а содержание общего железа доходило до 500 мкг/л.
Скорость коррозии, измеренная по образцам, составляла 0,2÷0,6 мм/год, а уровень отложений достигал 2÷6 кг/м2.
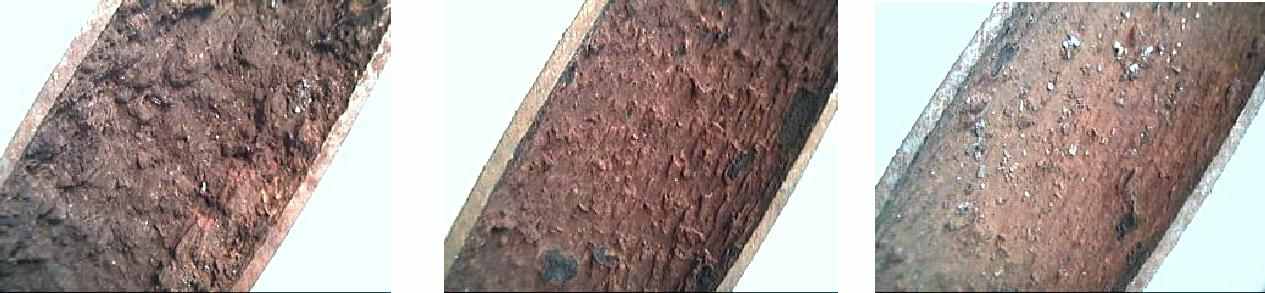
Рис. 1 Трубы правого бокового экрана котла №6 котельной «Чубаевка» на разных
степенях отмывки. (а) – до начала отмывки; б) – промежуточный этап
отмывки; в) – после отмывки отложений композицией «МИОР»)
В целом характер отложений, уровень коррозии не соответствовали уровню подготовки воды. Анализ сетевой и добавочной воды показал, что содержание нитратов в добавочной воде составляло 8÷12 мг/л, а в сетевой падало до 0,5÷2 мг/л. Учитывая тот факт, что нитраты в нейтральных средах не восстанавливаются железом, было сделано предположение о бактериальном «катализе» окисления железа нитрат–ионом и «переносе» образовавшегося двухвалентного железа на теплообменные поверхности. Порыв трубопровода обратной воды и дальнейший анализ характера повреждений показал состоятельность такого предположения. Внешне бактериальная коррозия на внутренних поверхностях трубопровода проявлялась как образование пористых наростов размером от 5 до 50 мм в поперечнике и до 30 мм высотой. Под наростом на поверхности металла обнаруживалась каверна соответствующего диаметра и глубиной вплоть до толщины исходного материала.
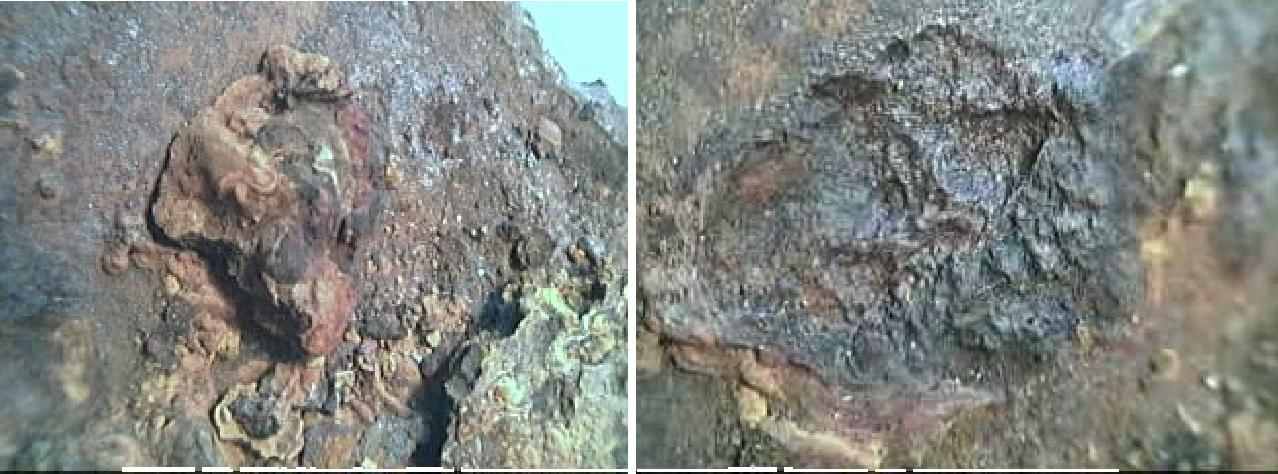
Рис. 2. Трубопровод обратной сетевой воды к. «Северная». Колония бактерий и каверна, обнаруженная под колонией.
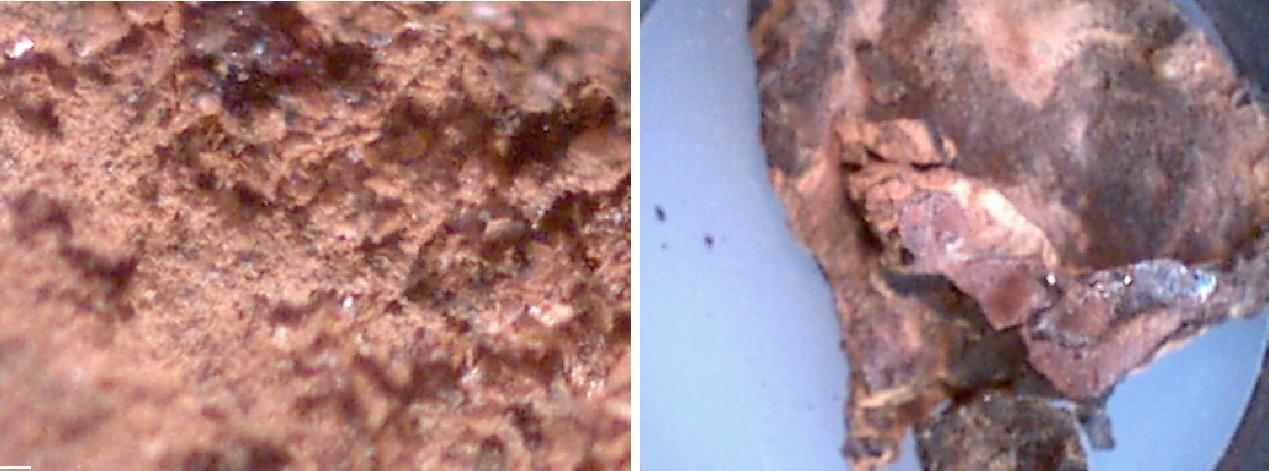
а) б)
Рис. 3. Фотографии образцов отложений с поверхности трубопровода обратной сетевой воды к. «Северная». (а) – увеличение в 200 раз; б) – увеличение в 10 раз)
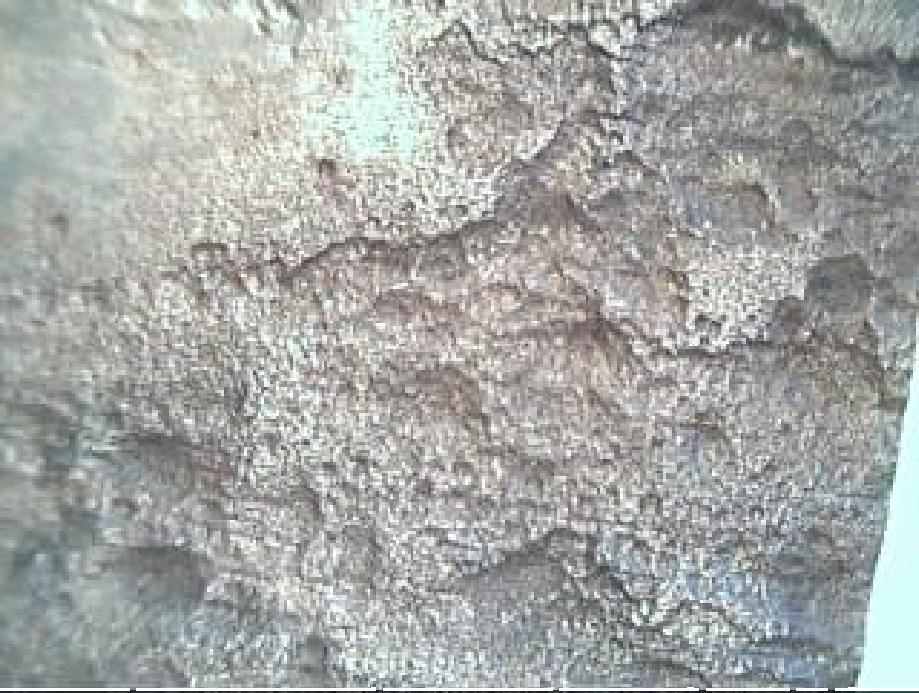
Рис. 4. Поверхность трубопровода обратной сетевой воды к. «Северная» после удаления отложений и продуктов коррозии.
В старых трубопроводах бактериальная коррозия представляет собой сплошной слой пористых отложений до 50 мм высотой.
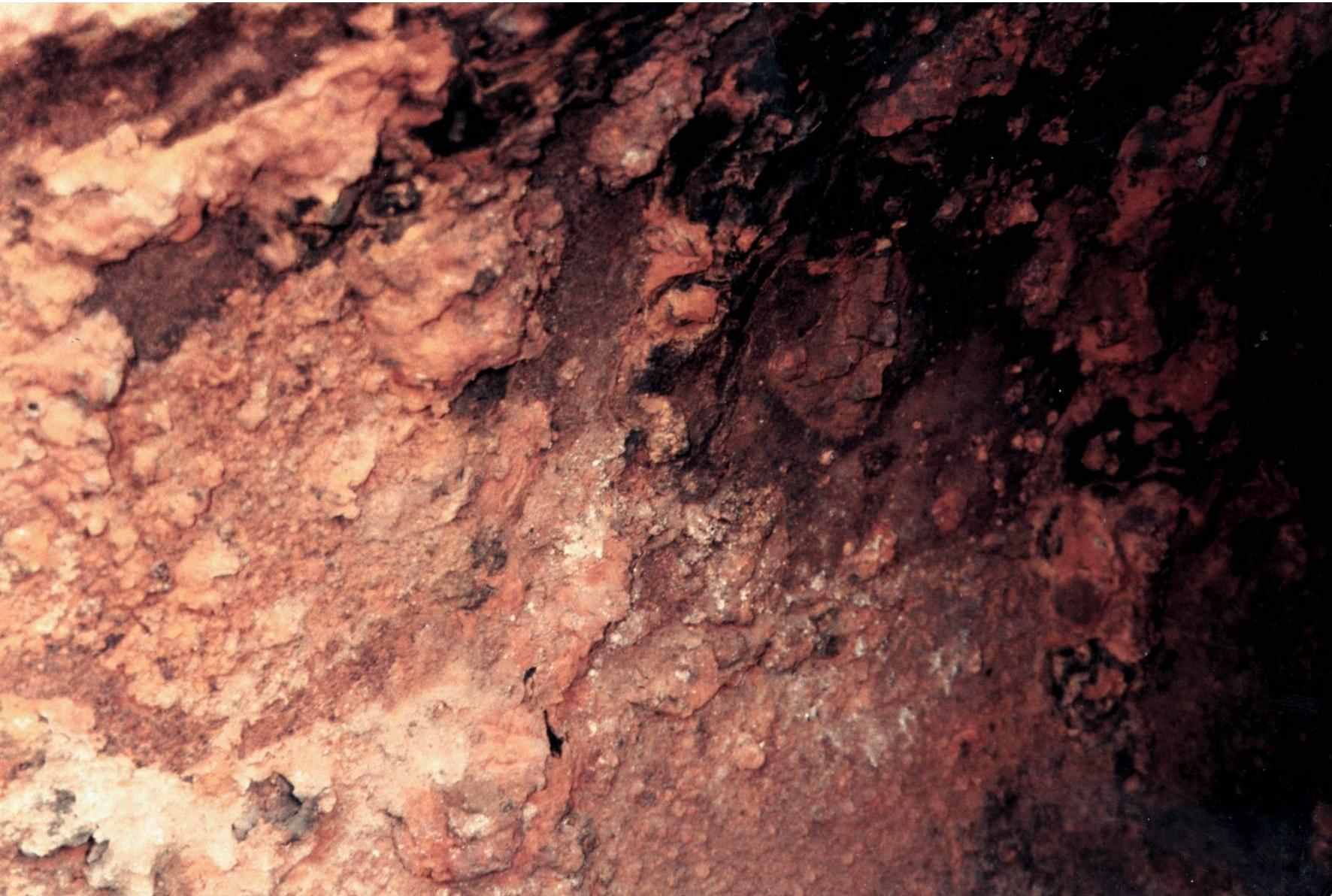
Рис 5. Трубопровод обратной сетевой воды. Эксплуатация ≈30 лет.
Наросты и отложения образованы колониями бактерий и продуктами коррозии стали – сульфидом железа, магнетитом, гидроксидом трехвалентного железа с различной степенью гидратации. Колонии бактерий, по данным Одесского университета, образованы железобактериями, тионовыми, сульфатредуцирующими и нитрифицирующими бактериями.
Для роста бактериальных колоний, представленных на рисунках 2 и 3, необходимы следующие составляющие:
! источник органического или неорганического углерода
! окисляемый субстрат – соединения двухвалентного железа, газообразный водород, аммиак, восстановленные соединения серы, органические вещества
! окислитель – растворенный кислород, нитриты, нитраты
! оптимальные значения температуры и pH
! Для сетевой воды г. Одесса характерно наличие следующих составляющих для интенсивной бактериальной корозии:
! содержание неорганического углерода – 40÷60 мг/л, органического – 2÷3 мг/л
! содержание окисляемого субстрата – органические вещества до 5 мг/л, железо – неограниченно
! содержание окислителя – нитратов до 12 мг/л, кислорода до 50 мкг/л, сульфатов до 100 мг/л
Исходя из данных аналитического и бактериального контроля можно предположить следующий постадийный механизм коррозионного повреждения стали:
! «пусковая» водородная или сероводородная коррозия в бескислородной среде
! вовлечение водорода в цикл биохимического восстановления сульфатов до сероводорода
! образование сульфида железа
! окисление сульфида железа нитрат–ионами под действием бактерий p. Thiobacillus denitrificans с образованием гидроксида железа и серной кислоты
! кислотная коррозия железа за счет снижения pH внутри колонии с продукцией водорода и замыканием цикла коррозии.
! температура до 850С, pH – 8,0÷8,4
Учитывая исходное содержание нитратов в добавочной воде можно оценить ежегодные потери стали на бактериальную коррозию и оценить скорость роста отложений в котлах.
Так для котельной «Чубаевка» при уровне потребления добавочной воды 70 м3/час и времени работы 4000 часов в год годовое количество восстановленных нитратов составит 3 т., что эквивалентно 6,5 т. ушедшей на коррозионное повреждение стали при 9÷9,5 т. отложений в год. При суммарной внутренней поверхности котлов в котельной на уровне 6000 м2 годовой прирост отложений может составить 1,5÷1,7 кг/м2. Это вполне отображает реальное состояние теплообменных поверхностей с учетом накопления оксидов железа в трубопроводах с одной стороны и вклада кислородной коррозии при ежегодном заполнении тепловой сети с другой стороны.
Анализ средств борьбы с бактериальной коррозией показывает, что могут быть применены следующие методы, позволяющие создать неблагоприятные условия для роста бактерий:
Для удаления органического и неорганического углерода – методы известкования, ионного обмена, обратного осмоса.
Для удаления окисляемого субстрата – защитные покрытия, сорбция.
Для удаления окислителя – обескислораживание, денитрификация, ионный обмен.
Поддержание высокой температуры (>850С) и значения pH (>10).
Дезинфекция.
Учитывая новую редакцию «Правил приема сточных вод предприятий в коммунальные и ведомственные системы канализации населенных пунктов Украины», фактически запрещающие применение ионного обмена за счет сброса регенерационных растворов, экономически целесообразными можно считать известкование (едконатровое умягчение), обратный осмос и денитрификацию.
Метод известкования позволяет решить вопрос как создания защитного покрытия на поверхности нагрева и в трубопроводах в виде карбоната кальция, так и повышения значения pH в сетевой воде. Недостаток метода, заключающийся в «заносе» котла карбонатом кальция легко устраняется введением ингибиторов отложений.
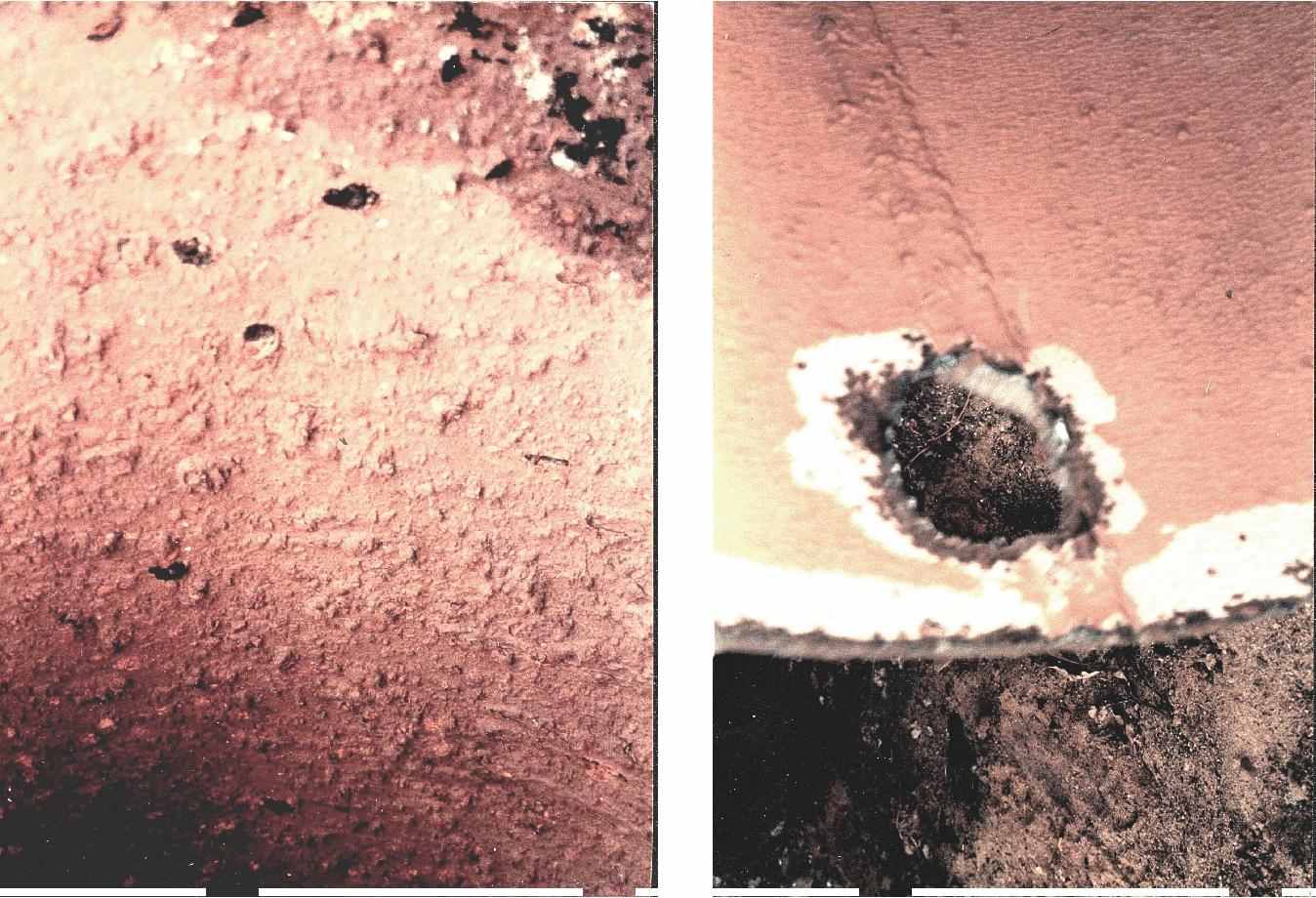
Рис. 6. Трубопровод прямой сетевой
воды Одесской ТЭЦ. Срок службы
≈30 лет.
Метод обратного осмоса позволяет радикально решить вопрос с солями жесткости и сульфатами, но селективность по нитратам недостаточна, кроме того, высок уровень сброса сточных вод.
Метод биологической денитрификации позволяет решить вопрос удаления кислорода, нитратов и подкисления добавочной воды для снижения уровня накипеобразования без образования сточных вод.
Применительно к подготовке добавочной воды, применение этого метода полностью проработано, и НПФ «МИОР» готова внедрить его в опытно–промышленном масштабе в тепловых сетях в сезон 2003–2004 года.
ПРИМЕНЕНИЕ РЕАГЕНТА ДИФАЛОН В МЕТАЛЛУРГИИ.
Н.Н. Верхошенцева, Е.А. Серкова, О.Ю. Серкова, Н.И.Крутикова, Магнитогорский металлургический комбинат, НПП «Поликом», г. Москва
Тезисы доклада
В процессах получения стали в конверторах в аппаратах мокрой газоочистки на стенках газоочистного оборудования и в шламопроводах появляются твердые и рыхлые отложения, вследствие наличия в конвертерных газах гидроокиси кальция и двуокиси углерода.
Рыхлые отложения убираются водяной и пневмоводяной промывками. Однако для удаления твердых отложений одной водной промывки недостаточно, необходима химическая промывка шламопроводов.
Так как характерной особенностью состава воды оборотного цикла газоочисток является высокая гидратная щелочность, источником образования которой в воде является вынос в газоочистной тракт мелких фракций шлакообразующих, подаваемых в конвертеры (до газоочисток 10–11,6 мг–экв/л, после газоочисток до 14,6 мг–экв/л), то для растворения отложений и предотвращения образования новых было предложено использовать дифалон (рН=1).
Входящие в состав дифалона комплексоны образуют с отложениями растворимые комплексонаты Са, Fe, обладающие высокой прочностью и не склонные к повторному осаждению в области рабочих значений (рН до 4).
Опыт применения реагента дифалон показал, что действие препарата на отложения объясняется следующим образом: органофосфонаты в совокупности с другими добавками «вытягивают» кальций из отложений, происходит разрыхление отложений. А рыхлые отложения легко смываются водой. Ввод дифалона преследует еще одну цель – поддержания значения рН, предотвращающее образование гидратной щелочности.
ПОВЫШЕНИЕ ЭФФЕКТИВНОСТИ ЭКСПЛУАТАЦИИ ТЕПЛОВЫХ СИСТЕМ
Н.И.Кидова, Ш.Ш. Халилуллов, Группа компаний «Инженерный сервис», г. Москва
Группа компаний «Инженерный сервис» успешно работает более 7 лет на рынке в сфере оказания услуг по очистке систем канализации, отопления, водоснабжения и вентиляции.
Хорошо известно, насколько большой проблемой являются плохо работающие загрязнённые системы отопления, горячего и холодного водоснабжения в жилых и общественных зданиях, производственных помещениях и учреждениях. Тепло, вырабатываемое на теплогенерирующих установках, доходит до конечного потребителя с большими потерями, уровень которых достигает 70%. Увеличивается расход топлива, особенно в отопительный сезон, нарушаются проектные обогревательные режимы жилых и производственных помещений.
Проблема надежности и долговечности гидросистем находится в прямой зависимости от чистоты внутренней поверхности этих систем. В процессе эксплуатации гидросистем наблюдается образование отложений на поверхности труб водяного тракта. Состав отложений может изменяться в значительных пределах в зависимости от водного режима, температурных условий поверхностей нагрева и конструктивных особенностей системы. Отложения могут образовываться в виде:
! первичной накипи, которая образуется на наиболее нагретых и теплонапряженных участках
! поверхности нагрева,
! вторичной накипи – прикипевших к поверхности металла частиц шлама (как правило, отложения этого вида образуются при низких скоростях движения воды и низких теплонапряжениях),
! продуктов коррозии металлов в виде железо–оксидных или медных соединений.
В результате образования отложений хорошо известны негативные последствия:
! уменьшается срок службы системы;
! увеличивается расход топлива (при толщине отложений в 1 мм на 12%);
! снижается температура в помещениях;
! снижается температура горячей воды;
! увеличивается расход сетевой воды;
! возрастает число внеплановых ремонтов;
! увеличиваются затраты электроэнергии на транспортировку воды;
! создается большое термическое сопротивление тепловому потоку и гидродинамическое сопротивление потоку воды.
В частности, почти все трубопроводы систем отопления здания со сроком эксплуатации более 10 лет забиты отложениями на 50% и более. Это значит, что уменьшается теплоотдача и пропускная способность труб.
Загрязнение бойлеров систем отопления отложениями толщиной более 2 мм приводит к снижению эффективности теплообмена до 30% и падению температуры теплоносителя на 20...25°С, что также ведёт к перерасходу топлива и электроэнергии. Теплопроводность любой накипи более чем в 40 раз ниже теплопроводности металла.
Решение проблемы лежит в широкомасштабном и интенсивном использовании прогрессивной экологически чистой комплексной технологии промывки и прочистки гидросистем. Комплексная технология объединяет в единое целое несколько самостоятельно существующих технологий на базе уникального специального оборудования и экологически чистых суперочистителей, предназначенных для проведения профилактических и аварийных работ по очистке гидросистем. До настоящего времени для удаления накипно–коррозионных отложений используют, в основном, следующие методы очистки:
! механическая очистка;
! очистка с использованием пневмо–, гидро – и электроимпульсных устройств;
! гидродинамическая очистка;
! химическая очистка.
Механическая очистка – трудоемкий и малопродуктивный способ, который часто приводит к разрушению труб.
Способы очистки второй группы эффективны для более широкого круга объектов. Однако их применение ограничено конструктивными особенностями очищаемого оборудования, необходимостью использования дорогостоящего специального оборудования, а также высокими требованиями к квалификации персонала.
Гидродинамические методы промывки основаны на динамическом воздействии потока жидкости на твердые частицы загрязнений, которые способствуют отрыву частиц от поверхности и выносу их из гидросистемы. Данный метод обеспечивает максимальный эффект очистки при небольших затратах, высокую производительность и полную экологическую безопасность.
Химический метод очистки наиболее универсальный для всех видов отложений и конструкций очищаемого оборудования. Этот метод позволяет полностью перевести накипно-коррозионные отложения в растворенное состояние и, в сочетании с гидродинамической промывкой, удалить все отложения из системы.
Наша компания использует комплексный гидропнемохимический метод промывки тепловых сетей, включающий в себя широкий спектр химических реагентов. Моющие химические реагенты сочетают в себе эффективность действия с высокой коррозионной и экологической безопасностью при проведении работ.
Их основные преимущества:
! высокая моющая способность;
! селективность воздействия (удаляют исключительно накипно–коррозионные отложения, не разрушая базовый конструкционный материал);
! экологическая безопасность (все используемые нами моющие средства биологически
! разлагаемые, применение их соответствует государственным санитарно-эпидемиологическим правилам и нормативам).
Комплекный гидропневмохимический метод позволяет наилучшим образом осуществить очистку. Очень часто он является единственно приемлемым. Затраты на химическую очистку компенсируются в течение довольно короткого времени, благодаря снижению энергозатрат.
Технология комплексной гидропневмохимической очистки состоит в следующем.
Очистка гидросистем производится с использованием специальной уникальной установки. Установка спроектирована специалистами группы компаний «Инженерный сервис». Новизна её защищена патентом РФ №22758 от 13.11.2001 г. Всё оборудование установки выполнено из нержавеющей стали, что полностью исключает попадание ржавчины и грязи извне. В зависимости от объёма тепловой системы используется определённый класс установки. Сегодня их три, но мы ведём постоянный процесс по усовершенствованию, модернизации и изготовлению новых установок.
В настоящее время изготовленные установки обеспечивают применение комплекса технологических операций, а именно:
! приготовление промывочных растворов;
! прокачка воды/промывочных растворов через тракт тепловой системы со скоростью не менее 1 м/сек.;
! изменение направления движения потоков воды/промывочных растворов (реверсирование);
! барботаж воздухом для улучшения разрыхления и удаления отложений;
! выборочная промывка приборов отопления, путём создания кинетической импульсной волны «КIW».
Для каждого конкретного объекта специалистами фирмы разрабатывается индивидуальная технология комплексной промывки. Технология учитывает особенности, присущие данному объекту, такие как:
! срок эксплуатации;
! изношенность оборудования;
! качественный состав отложений;
! степень загрязнения системы и ряд других факторов.
Индивидуальный подход к каждому объекту позволяет достигать максимальной эффективности проводимых работ.
Применение комплексной очистки системы отопления позволяет удалить до 70% отложений и грязи. При регулярной (ежегодной) промывке объем отложений и грязи сводится к минимуму, а при повторных промывках стоимость работ может быть снижена до 50% от первоначальной. Теплоотдача системы повышается от 25 до 50%. Экономия теплоносителя более 30%. Повышение температуры в помещениях на 5... 10°С. Продление срока эксплуатации систем на 10... 15 лет. Стоимость капитального ремонта (замены системы), существенно, не менее чем в 3...5 раз превышает затраты на комплексную промывку. Срок окупаемости комплексной промывки – не более 3.. .4 месяцев (один отопительный сезон).
Группой компаний «Инженерный сервис» за 7 лет работ по повышению эффективности эксплуатации гидросистем накоплен большой положительный опыт по комплексной промывке инженерных систем отопления, горячего и холодного водоснабжения в жилых и общественных зданиях, производственных помещениях и учреждениях. Ежегодно проводится комплексное обслуживание около 100 объектов и систем различных объемов и назначений, включая системы отопления, горячего и холодного водоснабжения, бойлера, градирни, а также теплообменники.
Успешная работа нашей фирмы в этой сфере подтверждена положительными отзывами организаций о качественном выполнении работ, а также сертификатом доверия МГТС.
50>