Конференция «современные технологии водоподготовки и защиты оборудования от коррозии и накипеобразования»
Вид материала | Доклад |
СодержаниеОпыт применения иомс Реагент «акварезалт» Предупреждение закисления оборотной воды в Новая технология удаления отложений и |
- Комплексная программа по предотвращению процессов коррозии и накипеобразования в теплообменном, 1017.43kb.
- Конференция «современные технологии водоподготовки и защиты оборудования от коррозии, 1036.07kb.
- Удмуртским Государственным Университетом и нпк «Вектор». На чтениях прозвучал 41 доклад, 1249.61kb.
- Основные вопросы, которые планируется затронуть: Нормативно-правовое и нормативно-техническое, 49.05kb.
- Vi методы защиты от коррозии металлов и сплавов, 783.92kb.
- Ооо «интехэко» инновационные технологии и экология, 194.03kb.
- Защиты от коррозии и старения, 844.02kb.
- Защиты от коррозии и старения, 1104.68kb.
- Методическая разработка урока химии по теме: «понятие о коррозии металлов, способы, 159.91kb.
- Коррозии, виды коррозийных повреждений на газопроводах. Стресс-коррозия на газопроводах,, 549.97kb.
ОПЫТ ПРИМЕНЕНИЯ ИОМС–1 ДЛЯ ПОДГОТОВКИ
ПОДПИТОЧНОЙ И СЕТЕВОЙ ВОДЫ
Белоконова Н.А., к.х.н., Корюкова Л.В., инж., ОАО «Свердловэнерго», г. Екатеринбург
В структуру ОАО “Свердловэнерго” включено ряд предприятий Свердловской области.
Несмотря на отработанную систему химконтроля и корректировки ВХР, сложную и достаточно затратную технологию водоприготовления не всегда удавалось решить проблему образования отложений на поверхностях нагрева теплообменного оборудования.
В течение отопительного сезона подогреватели на некоторых теплоисточниках подвергались механической чистке, которая была малоэффективной т.к. отложения имели плотную структуру и состояли, в основном из ионов – накипеобразователей.
С 1993 года в ОАО “Свердловэнерго” начато внедрение новой технологии обработки подпиточной воды с помощью ингибитора осаждения минеральных солей (ИОМС–1).
Внедрению новой технологии предшествовало проведение комплекса научно–исследовательских работ и испытаний:
! выбор эффективного ингибитора, решение проблем его качества,
! стендовые и промышленные испытания,
! отработка и аттестация методики химического контроля.
На основании вышеперечисленных исследований для каждой станции был выбран регламент ингибирования с формированием схем по приему и дозированию ингибитора.
В настоящее время нашими специалистами технология внедрена на 10 теплоисточниках ОАО “Свердловэнерго” и ряде других предприятий.
Внедрение новой технологии дало следующие результаты:
! отмечено снижение удельной загрязненности поверхностей нагрева сетевых подогревателей,
! изменилась структура отложений – они стали рыхлые и легко отмываются при водных отмывках,
упрощены технологические схемы водоподготовки, в ОАО “Свердловэнерго” ежегодно экономится:
! 1000 т серной кислоты,
! 3000 т поваренной соли,
! 100 т катионита,
а солевой сток в водоемы сократился на 900 тыс. м3/год.
Несмотря на простоту реализации технологии, на практике требуется углубленный подход к анализу результатов как химического, так и теплотехнического контроля и для обеспечения эффективности указанной технологии особенно важно:
! выбрать оптимальную дозу ингибитора, скорректировать методику и погрешность определения реагента. При расчете расхода ингибитора и его фактического содержания необходимо учитывать расход пара или греющей среды на деаэрацию.
! совместно с внедрением новой технологии решать проблемы, связанные с коррозией оборудования, эффективностью предочистки и деаэрации. В последнее время на ряде предприятий производится замена ингибитора ИОМС–1 на СК–110.
В 1998 г с целью снижения затрат на реагент (в основном за счет транспортных расходов), нами была исследована возможность замены для предприятий ОАО “Свердловэнерго”.
Но, на основании результатов экспериментальных работ, был сделан следующий вывод: в соответствии с реальными условиями работы схем теплоснабжения на электростанциях нашей энергосистемы, замена ИОМС–1 на СК–110 нецелесообразна, т.к. термическая стабильность СК–110 ниже, чем ИОМС–1, поэтому в случае применения СК–110 температура сетевой воды должна быть не выше 130.
Естественно, что возможность применения СК–110 должна оцениваться комплексно для конкретных условий с учетом специфики проблем на производстве в целом, но для объективного обоснования необходимости замены одного реагента на другой целесообразно осуществить комплексный анализ практических результатов работы.
В противном случае “замена” лишь видоизменит проблемы, а не решит их по существу.
РЕАГЕНТ «АКВАРЕЗАЛТ»
Кинд В.Б., НПП «Биотехпрогресс», г. Кириши
В охладительных водооборотных системах любого промышленного предприятия возникают проблемы, связанные с коррозией, отложением минеральных солей, биологическим обрастание на поверхности контакта воды с элементами охлаждающей системы. Это влечет за собой нарушение технологических режимов и эффективности производственного процесса, быстрый износ технологического оборудования, увеличивает производственные затраты.
НПП «Биотехпрогресс», используя специальные, лицензированные программы по расчету ингибирования систем охладительных циклов и теплоснабжения, на основании собственного опыта и имея доступ к информационной базе ведущих организаций в области водоочистки, предлагает Вашему вниманию, разработанный нашей компанией, уникальный реагент «АКВАРЕЗАЛТ 1010» для коррекционной обработки воды охладительных циклов.
Назначение: «АКВАРЕЗАЛТ 1010» предназначен для ингибирования коррозии металлов и солеотложения в водооборотных системах охлаждения промышленных предприятий (химических, нефтехимических, металлургических и др.) и тепловых электростанций, в замкнутых системах теплоснабжения, а так же в качестве реагента для отмывки солеотложений на различных промышленных объектах.
Состав: В состав реагента «АКВАРЕЗАЛТ 1010» входят фосфонокарбоксильные кислоты и водорастворимые полимеры–дисперсанты, а так же добавляются бактерицидные средства при необходимости.
Технические характеристики: «АКВАРЕЗАЛТ 1010» имеет следующие физико–
химические показатели:
№ | Наименование показателя | Значение | Метод испытания |
1. | Внешний вид | Прозрачная жидкость от бесцветного до желтого цвета | ГОСТ 28084–89 разд. 4.1. |
2. | Величина pH продукта, не более | 8 | ГОСТ 28084–89 разд.4.8. |
3. | Эффективность ингибирования солеотложения, %, не менее | 90 | ТУ 6–09–20–152–88 разд. 4.6. |
4. | Коррозийная агрессивность рабочих жидкостей. | выдерживает | ГОСТ 6243–75 разд. 2. |
Дозировка: Уровень дозы реагента зависит от качества (состава) обрабатываемой воды (в частности от индекса стабильности Ланжелье) и составляет от 4 до 50 мг/л. Дозируется реагент в любую точку охладительного водооборотного цикла, контроль степени ингибирования солеотложений осуществляется по жесткости циркуляционной воды.
Сертификация и безопасность: «АКВАРЕЗАЛТ 1010» – не горючий, пожаровзрывобезопасный продукт, по степени воздействия на организм человека по ГОСТ 12.1.007–76 относится к веществам малоопасным – IV класса опасности, раздражающим и мутогенным действием не обладает. Предельно–допустимая концентрация продукта в воздухе рабочей зоны – 10 мг/м3, класс опасности 4 по ГОСТ 12.1.005–88. ПДК продукта в воде водоемов хозяйственно–питьевого и культурно–бытового назначения – 4 мг/дм3, в воде рыбохозяйственных водоемов – 10 мг/дм3. На продукт «АКВАРЕЗАЛТ 1010» имеется санитарно–эпидемиологическое заключение. При работе с продуктом необходимо соблюдать общие требования безопасности по ГОСТ 12.3.009–76. При попадании продукта на кожу или в глаза необходимо промыть их водой.
Упаковка и транспортирование: Продукт «АКВАРЕЗАЛТ 1010» разливают в полиэтиленовые бочки по ОСТ 6–19–500–78 типа I, II, III вместимостью 50, 60, 80, 100, 120, 160, 200 дм3. Допускаются другие виды упаковки, утвержденные в установленном порядке по согласованию с потребителем. Транспортируют продукт в закрытом виде любыми видами крытых транспортных средств, хранят в закрытых и сухих помещениях, срок хранения продукта составляет два года.
К преимуществам нашего предложения относим то, что специалисты нашего предприятия готовы довести композицию и дозировки реагента индивидуально под «Вашу воду» и технологические особенности производства. Реагент «АКВАРЕЗАЛТ 1010» готовится из высокочистых веществ, что минимизирует его дозировки и, соответственно, материальные затраты.
В случае Вашей заинтересованности, будет предоставлена более подробная информация.
Также нами разработана серия «Акварезалт 1010–М» – ингибиторов солеотложений в установках обратного осмоса.
ПРЕДУПРЕЖДЕНИЕ ЗАКИСЛЕНИЯ ОБОРОТНОЙ ВОДЫ В
РЕЗУЛЬТАТЕ БИОЛОГИЧЕСКОЙ НИТРИФИКАЦИИ
А.В. Талалай, Б.Н. Шукайло, П.В. Коломиец, НПФ «МИОР», г. Северодонецк
Низкая скорость коррозии теплообменного оборудования является непременным условием безаварийной работы всех производств, использующих оборотную охлаждающую воду. Как правило, коррозионные процессы протекают под действием нескольких факторов, один из которых – снижение величины рН оборотной воды. Довольно часто закисление оборотной воды происходит в результате биологической нитрификации – окисления аммиака в азотную и азотистую кислоты под действием микроорганизмов – нитрификаторов. Аммиак может попадать в воду с технологическим конденсатом, при подпитке оборотного цикла биохимочищенной водой, улавливаться при контакте оборотной воды с воздухом в градирне и т.д. Кроме самого аммиака, в оборотную воду могут попадать его соединения и вещества, гидролизующиеся с образованием аммиака – соли аммония, карбамид и др. Описанные явления характерны для нефтеперерабатывающих предприятий и предприятий азотной промышленности.
В оборотный цикл установки каталитического крекинга ОАО «ТНК–ЛиНОС» аммиак попадал с технологическим конденсатом водородной установки и с биохимочищенной водой. Результатом этого было массовое развитие нитрифицирующей микрофлоры, окислявшей аммиак в азотную кислоту, что приводило к снижению величины рН оборотной воды до 6 ед. рН (рис. №1). Скорость коррозии оборудования из углеродистой стали в этих условиях достигала критических величин – 0.3–0.8 мм в год.
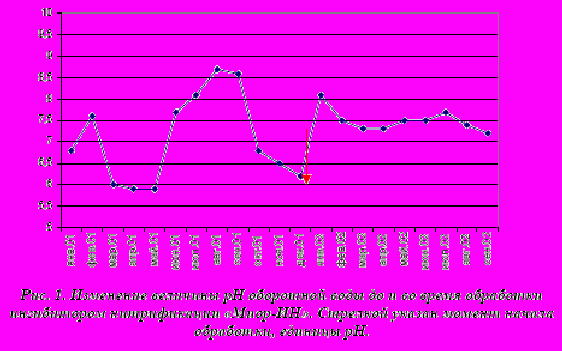
Поскольку первопричиной коррозии являлись микробиологические процессы, то, на первый взгляд, представлялось целесообразным сосредоточить усилия именно на подавлении микробной деятельности, иначе говоря, на биоцидной обработке воды. Однако традиционная биоцидная обработка воды гипохлоритом натрия в данной ситуации неэффективна из–за того, что активный хлор, в первую очередь, расходуется на взаимодействие с непредельными углеводородами и аммиаком. При содержании олефинов и аммиака в концентрациях, превышающих 100 мг/л, необходимая доза гипохлорита увеличивается до неприемлемо больших значений: около 1 кг/м3 физического объёма оборотного цикла.
Применительно к водооборотному циклу установки каталитического крекинга это означало одномоментное внесение приблизительно 20 тонн товарного гипохлорита натрия с периодичностью около 5 суток. Однако содержание хлоридов в оборотной воде при этом достигало бы таких величин, что общая скорость коррозии не снизилась бы, а увеличилась.
Популярная в последнее время биоцидная обработка четвертичными аммониевыми основаниями – катамином и подобными продуктами эффективна также при весьма высоких их концентрациях – не менее 50 мг/л, что весьма дорого.
С учетом этих соображений была разработана технология повышения рН оборотной воды именно за счет подавления биологической нитрификации. Технология заключалась в периодической обработке оборотной воды ингибитором нитрификации «Миор–ИН» по ТУ У 24.2–30421760–002–2002. С учетом низкой скорости роста нитрифицирующей микрофлоры, было признано целесообразным проводить обработку один раз в четыре недели. Последующая опытно–промышленная проверка подтвердила эффективность такого графика. В результате натурного эксперимента было установлено, что по критерию «стоимость–эффективность» оптимальная доза внесения ингибитора нитрификации «Миор–ИН» составляет 25 г на 1 м3 физического объема оборотного цикла при условии поддержания этой концентрации в течение 12–24 часов.
Процесс применения ингибитора нитрификации «Миор–ИН» отслеживался по показателям оборотной воды «нитриты», «нитраты», «аммиак» и «значение рН». Динамика изменения этих показателей приведена на рисунках №1, 2.
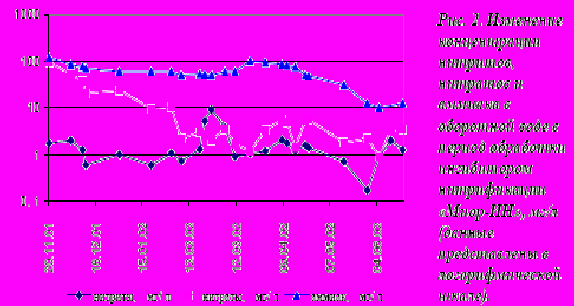
Начало обработки водооборотного цикла установки каталитического крекинга ингибитором нитрификации «Миор–ИН» пришлось на февраль 2002 г. В феврале 2002 г, как видно из рисунка №1, наблюдалось снижение концентрации нитритов и нитратов в оборотной воде до величин, соответствующих их концентрациям в подпиточной воде с учетом коэффициента упаривания. Значение рН оборотной воды, как видно из рисунков №1 и 2, коррелирует с концентрациями окислённых форм азота: периоды низких концентраций нитритов и нитратов в оборотной воде совпадают с периодами повышения значения рН. Это подтверждает зависимость значения рН оборотной воды от протекания процесса нитрификации.
Применение ингибитора нитрификации «Миор–ИН» на водооборотном цикле установки каталитического крекинга позволило стабилизировать величину рН оборотной воды в интервале 7.2–8.0 ед. рН, что привело к снижению скорости коррозии до величин 0.07–0.17 мм в год, что близко к допустимым величинам. Стоимость оборотной воды увеличилась при этом на 1.2%.
Следует отметить, что снижение скорости коррозии оборудования с 0.34–0.7 мм в год до 0.07–0.17 мм в год (рис. №3) было обусловлено не только стабилизацией величины рН оборотной воды, но и применением композиции «Миор» по ТУ У 24.6–30421760.001–2000, содержащей фосфонаты и полифосфаты. Оборотная вода установки каталитического крекинга имеет крайне низкое качество по ряду важнейших показателей: содержание сульфатов, хлоридов, сероводорода, высокие БПК, окисляемость, солесодержание, микробное число превышают требования СНиП для оборотной воды. В этих условиях скорость коррозии на уровне 0.07–0.17 мм в год, по–видимому, близка к минимально возможной при экономически оправданной обработке воды.
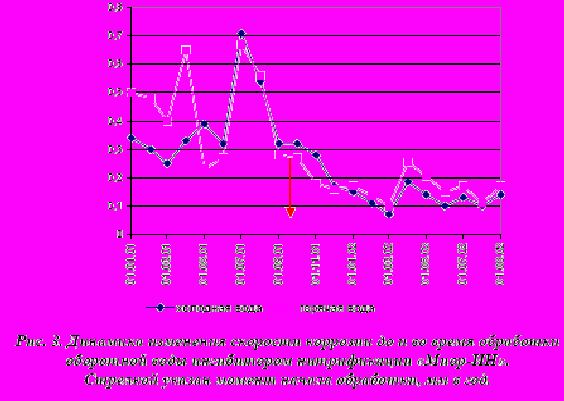
Опыт применения ингибитора нитрификации «Миор–ИН» и композиции «Миор» показал их высокую эффективность, в результате чего оба реагента были внесены в расходные нормы, а их применение – в регламент работы оборотного цикла. Полученный опыт может быть распространен на водооборотные циклы, имеющие схожие проблемы. На оба реагента имеются ТУ и весь комплекс необходимых санитарно–гигиенических документов Украины и России.
НОВАЯ ТЕХНОЛОГИЯ УДАЛЕНИЯ ОТЛОЖЕНИЙ И
ЗАЩИТЫ ОТ КОРРОЗИИ ТЕПЛОЭНЕРГЕТИЧЕСКОГО
ОБОРУДОВАНИЯ
Рыженков В.А., д.т.н, проф., Куршаков А.В. к.т.н., вед. научн. сотр.,
Кулов В.Е. к.т.н., доц.,
ГОУВПО Московский энергетический инстиут ТУ, г. Москва
Проведение эксплуатационных очисток внутренних поверхностей пароводяных трактов теплоэнергетического оборудования диктуется необходимостью поддержания уровня отложений, не превышающих допустимого, и регламентируется соответствующими нормативными документами [1, 2]. Практика проведения химических очисток на тепловых электростанциях в последнее время существенно изменилась в связи с тем, что большое количество энергоблоков, котлов и турбин находится длительное время в простое, а также по причине нехватки материальных средств и наличия значительного количества устаревшего оборудования. Часто очистки на электростанциях проводятся без привлечения специализированных организаций. К сожалению, имеют место случаи, когда отложения с трубных поверхностей экранных систем барабанных котлов удаляют посредствам использования неингибированной соляной кислотой и даже без последующей пассивации поверхностей, что безусловно входит в противоречие с современными требованиями к уровню эксплуатации энергетического оборудования, обуславливающего тщательное соблюдение технологических регламентов очисток теплообменного оборудования. В том случае, если оборудование выводится в резерв или ремонт на срок более 5 суток, в технологическом режиме очистки необходимо предусматривать пассивацию (консервацию) очищенных поверхностей для защиты металла от «стояночной» коррозии, а также по возможности проводить их санацию (удаление коррозионно-активных элементов и соединений – хлоридов, сульфатов и др.) [З].
Из всего многообразия известных способов периодической очистки теплообменных поверхностей (химические, гидравлические, механические, электродинамические и др.) применительно к оборудованию современных ТЭС с учетом сложности его конструкций и схем можно выделить восемь основных принципов с различными механизмами взаимодействия применяемых для очистки оборудования реагентов с элементами, входящими в состав отложений. Шесть из них базируется на химическом взаимодействии [4].
К реагентам, широко применяемым при химических очистках, относятся щелочи, минеральные и органические кислоты, комплексоны. Достаточно широкий спектр составляющих моющих водных растворов (соляной, серной, сульфаминовой, плавиковой кислот, композиции трилона Б или двухзамещенной аммонийной соли ЭДТК с лимонной, серной, фталевой, аскорбиновой кислотами, смеси серной кислоты с бифторидом аммония; едкого натра, кальцинированной соды, фосфатов натрия, аммиака и др.), а также технологические режимы химической очистки предполагают достижение высокой ее эффективности и результативности. Однако подавляющее большинство применяемых реагентов характеризуется значительной агрессивностью по отношению с конструкционным сталям. По этой причине при осуществлении химических очисток стремление максимально удалить отложения вступает в явное противоречие с обеспечением сохранности поверхности, неизменности структуры и механических характеристик поверхностных слоев металла оборудования (недопущение утонения стенок, локального обезуглероживания, наводораживания, восстановления оксидов металла до металла с последующим образованием карбонилов металла в присутствии монооксида углерода, т.е. перехода в некристаллическое состояние и разрыхление металла, концентрирования в микропорах хлоридов при использовании соляной кислоты и др.).
Ингибирование моющих растворов позволяет существенно снизить скорость коррозии основного металла. К наиболее часто употребляемым ингибиторам следует отнести ОП–7 (ОП–10), каптакс, катапин КИ–1, тиомочевиу, уротропин, ПБ–5, В–1 (В–2). Практика применения того или иного ингибитора или их комбинаций показала неоднозначную эффективность действия. Так, например, в работах [5, 6] указывается, что наиболее перспективным и лучшим по защитным свойствам является катапин КИ–1 (состав: катапин – 25%, солянокислый уротропин – 25%, вода – 50%). В то же время высокая эффективность ингибиторов кислотной коррозии металлов не всегда является достаточным аргументом для их использования. Как показывают исследования [7], некоторые ингибиторы наводораживают металл (например, уротропин). Проводимая по регламенту водная отмывка с нейтрализацией и пассивацией (например, раствором аммиака, тринатрийфосфата, нитрита натрия, гидразина и их комбинаций, водокислородной обработкой, продувкой высокотемпературным паром) не всегда способна полностью ликвидировать отрицательные последствия после полной химической очистки. В основе окислительной очистки, включающей парокислородную (ПКО) и пароводокислородную (ПВКО) очистки [8, 9] лежит способ, основанный на одновременном воздействии на поверхность с отложениями перегретого пара, пароводяной смеси или воды с окислителем – кислородом или перекисью водорода, что обеспечивает окисление продуктов коррозии, уменьшение сцепления оксидов железа с поверхностью металла и их выносу из трактов (седьмой принцип). Интенсивность выноса загрязнений зависит от скорости среды и концентрации окислителя. Согласно [8] продолжительность очистки при ПКО в среднем составляет 0,5–2,0 ч. Однако как показали дополнительные исследования [10], очистка поверхностей как при ПКО, так и при ПВКО протекает наиболее эффективно при длительности обработки до 10 ч. При этом рекомендуется изменять фазовое состояние среды (переходить с перегретого пара на воду или с воды на насыщенный пар) при одновременном изменении температуры на 80–100°С, что, конечно, приведет к удорожанию и без того достаточно энергоемкой технологии и главное – к снижению надежности оборудования из–за резких изменений тепловых нагрузок.
При всех известных преимуществах ПКО и ПВКО могут послужить причиной негативных явлений, особенно если не в полной мере соблюдены технологические регламенты (не выдержаны необходимые значения массовой скорости среды, уровни температур и др.). Так, например, известны случаи интенсивного абразивного износа лопаточного аппарата цилиндров высокого и среднего давления мощных паровых турбин в результате выноса из пароперегревательной части котлов образовавшейся после такой обработки окалины. В случае достаточно высокой загрязненности теплообменных поверхностей эффективность ПКО и ПВКО может оказаться недостаточной. Так, в частности, проведение ПКО турбины Р–6–35/10 Первоуральской ТЭЦ от солевых отложений (занос натриевыми солями до 12%) не привело к желаемым результатам [11].
Как самостоятельный необходимо выделить способ удаления водонерастворимых отложений, который не связан с какими–либо химическими реакциями, а основывается на взаимодействии адсорбирующихся на поверхности молекул поверхностно–активных веществ с отложениями, в процессе которого происходит их разрыхление и ослабление сцепления с поверхностью, что в конечном итоге при воздействии потока рабочего тела (пар, вода) приводит к полному или частичному удалению последних с поверхностей (восьмой принцип). Известно, что поддержание качественного состояния внутренних поверхностей пароводяных трактов оборудования ТЭС может, быть обеспечено с помощью технологий с применением поверхностно–активных веществ из класса высших пленкообразующих алифатических аминов, в частности, октадециламина (ОДА), например, для защиты от стояночной коррозии [12]. Защитные свойства адсорбированного на поверхности металла ОДА в виде гидрофобной пленки, являющейся преградой для проникновения кислорода и углекислоты (эффект диффузионного барьера), связан еще и с тем, что электродный потенциал поверхности металла в этом случае смещается в положительную сторону и уменьшается скорость анодной реакции ионизации, т.е. металл «облагораживается» (эффект деполяризационной пассивации)[13].
Наряду с ингибирующими свойствами ОДА выявлена еще одна весьма положительная его особенность. В процессе сорбции молекул ОДА из рабочего тела (вода, влажный и перегретый пар) на поверхности пароводяных трактов разрыхляют и отслаивают отложения и продукты коррозии), способствуя очистке оборудования [14, 15]. В связи с тем, что присутствие ОДА в воде приводит к значительному снижению ее поверхностного натяжения (приблизительно в три раза) и соответствующему повышению смачиваемости поверхности, молекулы амина проникают в поверхностные трещины и каверны, из которых затем вытесняют накопившиеся отложения, в том числе и коррозионно–активные, что при использовании других способов осуществить не представляется возможным.
Эффект очистки с помощью ОДА проявляется практически по отношению ко всем входящим в состав отложений составляющим: оксидов металлов (железа, меди, цинка и др.), различных солей кремнекислоты и многочисленных силикатов, органических веществ и т.д., однако зависит как от плотности и структурных характеристик этих компонентов, так и от времени воздействия. В отличие от любых химических очисток процесс разрыхления отложений с помощью ОДА существенно более медленный и плавный. Наиболее легко и в первую очередь удаляются пористые и рыхлые составляющие – гематит, карбонаты и др.
Что же касается защитной пленки магнетита, то ее устойчивость в существенной степени зависит от способа формирования, т.е. сплошности упаковки кристаллов, сцепления ее с основным металлом, а также от толщины. Многолетняя практика применения ОДА–технологии на разнообразном оборудовании ТЭС показала, что магнетитовая пленка при этом не нарушается. Более того, образовавшиеся в ней во время эксплуатации микротрещины и сколы, в обычной ситуации являющиеся очагами коррозии, при обработке ОДА как бы «залечиваются» под действием эффектов диффузионного барьера и деполяризационной пассивации.
Как известно [16], присутствие в рабочем теле хлоридов уменьшает пассивность стали в связи с их способностью проникать через пассивирующую оксидную пленку и накапливаться в отдельных местах, особенно в местах с деформированной кристаллической решеткой, приводя к локальному разрушению пленки и как следствие к язвенной или другим видам коррозии (для аустенитных сталей меж- или транскристаллитному растрескиванию). Ситуация усугубляется еще и тем, что:
– качество питательной воды, а также конденсата пара (в том числе по электропроводности, содержанию железа, рН) в режиме останова и особенно при пуске оборудования резко ухудшается;
– в паровых конденсационных турбинах в так называемой «зоне Вильсона» происходит резкое повышение концентраций различных примесей (в том числе ионов хлора);
– хлориды обладают способностью концентрироваться в труднодоступных местах (например, в замковых соединениях турбинных лопаток и дисков).
Наряду с этим по данным института изотопных и радиационных исследований (Германия) обнаружена способность ОДА связывать ионы хлора, что является крайне важным в замедлении коррозионных процессов.
Надо заметить, что «моющий» эффект ОДА проявляется в той или иной степени в каждом случае, когда проводится консервация и расконсервация теплоэнергетического оборудования с использованием этого реагента, и казалось бы, что вопрос очистки поверхностей от отложений не должен возникать. Однако действительные уровни удельной загрязненности поверхностей оборудования в ряде случаев исчисляются сотнями грамм на 1 м2.
Для того чтобы полностью очистить такие поверхности, требуется длительный процесс обработки с повышенными концентрациями реагента (ОДА), что становится нерентабельным, а иногда и невозможным (по условиям временного регламента, устанавливаемого для проведения ремонтных работ или по другим причинам).
Именно в таких ситуациях становится актуальным применение технологии «щадящих» химических промывок (при этом применяются известные моющие композиции на основе органических или минеральных кислот, комплексоны с коррекцией по рН или щелочи, позволяющие достаточно быстро перевести в раствор большую часть отложений с последующей доочисткой, санацией, пассивацией и консервацией поверхностей с помощью пленкообразующих аминов (ОДА). Этот способ, разработанный в МЭИ (ТУ), запатентован [17] и прошел промышленную апробацию [18, 19]. В частности, в 1999 году на энергоблоке 200 МВт Шатурской ГРЭС–5 ОАО «Мосэнерго» был проведен комплекс работ, включающий на первом этапе композиционную отмывку экранных систем двух корпусов барабанного котла ТП–108 в «щадящем» режиме и на втором – дополнительную очистку санацию пассивацию и консервацию пароводяных трактов энергоблока в целом (котел, турбина, ППП, конденсатор, конденсатно–питательный тракт, ПНД, деаэратор, ПВД, насосы, арматура).
Отмывка экранных систем котла производилась скорректированной по рекомендации МЭИ (ТУ) на основании учета состава отложений моющей композицией на основе ингибированной соляной кислоты с добавлением комплексонов и биоразлагаемых поверхностно–активных веществ с низким пенообразованием. Такая моющая композиция позволяет эффективно переводить в раствор оксиды железа, окалину, карбонаты и другие отложения с одновременным снижением газовыделения, количества шлама, диспергирезацией частиц взвесей. Количество моющей композиции, время обработки, выбор концентрации и режимных параметров отмывки определялись расчетным путем, а затем проверялись экспериментально в лабораторных условиях исходя из принципа частичной отмывки (не более 80–90%). В результате на стадии химической очистки из экранных систем котла были удалены железоокисные отложения общим количеством около 1300 кг (в пересчете на окись трехвалентного железа). Образовавшийся в процессе отмывки шлам представлял собой мелкодисперсную взвесь с модальным размером 60–70 мкм и общей массой около 150 кг. Дренирование моющего раствора после завершения отмывки реализовано беспрепятственно без забивания дренажей. После химической отмывки в режиме работы блока на пониженных параметрах проводилась обработка с помощью ОДА (корпуса А котла, турбины, промежуточного пароперегревателя, конденсатора, конденсатно–питательного тракта с системой регенерации, корпуса Б котла, промперегрева, конденсатора и далее как в первом контуре) производилась доочистка, санация и пассивация экранных систем котла, а также консервация всех пароводяных трактов энергоблока ОДА, который дозировался в виде водной эмульсии на всас питательного электронасоса.
Наряду с этим в процессе консервации по результатам химических анализов в различных точках контура («питательная вода», «котловая вода», «насыщенный пар», «перегретый пар», «конденсат») зафиксирован значительный «моющий» эффект. Особо следует отметить ярко выраженный эффект выведения с поверхности хлоридов. Максимальные значения концентраций ионов хлора превысили 140 мкг/кг и в конце процесса консервации снизились до 2,5 мкг/кг (за счет удаления «грязного» рабочего тела из контура консервации). По окончании консервации после останова блока на плановый профилактический ремонтный период был проведен контрольный осмотр внутренних поверхностей барабанов котла, проточной части турбины, вскрыты коллекторы панелей экранов, сделаны вырезки контрольных образцов труб котла.
Осмотр барабанов показал наличие сплошной гидрофобной защитной пленки ОДА в водяной и паровой частях. В турбине практически на всех элементах (рабочие лопатки, диафрагмы, корпуса цилиндров) зафиксирована защитная пленка консерванта, а также частичная отмывка от отложений. Все коллекторы экранов оказались чистыми, сухими, без шлама, покрытыми защитной пленкой ОДА. Удельная сорбция ОДА на внутренних поверхностях контрольных образцов труб варьировалась от 83 мкг/см2 (водяной экономайзер) до 3–4 мкг/см2 (боковые экраны), что свидетельствует о гарантированной их защите от стояночной коррозии.
МЭИ (ТУ) получил положительный опыт по применению технологии удаления отложений, санации и защиты от коррозии в едином технологическом цикле: Шатурская ГРЭС, Рязанская ГРЭС, Черепетская ГРЭС, Приморская ГРЭС, Камчатская ТЭЦ–1. Авторы разработанной технология отмечены дипломом и золотой медалью ВВЦ (2002 г), дипломом с отличием и золотой медалью 51–го Всемирного салона инноваций, научных исследований и новых технологий "Брюссель–Эврика–2002".
Таким образом, в соответствии с вышеизложенным можно сделать следующие выводы.
1. Применяемые в настоящее время методы очистки теплоэнергетического
оборудования, включая чисто химические, а также парокислородные и
пароводокислородные, не всегда гарантируют эффективную очистку при
одновременном обеспечении надежной дальнейшей его эксплуатации (травмирование
основного металла оборудования, провоцирование коррозионных процессов,
абразивный износ лопаточного аппарата турбин и др.)
2. Известный метод консервации оборудования с применением
пленкообразующих аминов позволяет очищать поверхности от отложений, в том
числе от коррозионно–опасных (в частности, хлоридов) и при этом не травмировать
основной металл и сохранять защитные пленки. Однако этот процесс очистки требует значительно большего времени и нецелесообразен при наличии отложений, значительно превышающих нормативные значения.
3. Разработан и апробирован в промышленных условиях новый способ «щадящей» очистки теплообменного оборудования с использованием высокоэффективных моющих композиций с последующей санацией, пассивацией и защитой поверхностей от коррозии на основе применения пленкооразующих аминов, который может быть рекомендован для очистки теплообменного оборудования трубопроводов в системах теплоснабжения.