Научно-исследовательская работа студентов
Вид материала | Научно-исследовательская работа |
- Научно-исследовательская работа студентов и пути её совершенствования Оглавление: Введение, 219.43kb.
- Научно-исследовательская работа преподавателей и студентов как условие эффективного, 91.08kb.
- Научно-исследовательская работа студентов Научно-исследовательская работа студентов, 20.56kb.
- Научно-исследовательская работа студентов (нирс) является обязательной, неотъемлемой, 111.22kb.
- Научно-исследовательская работа студентов (нирс) 10. 1 Информационно-аналитический, 648.54kb.
- Научно-исследовательская работа студентов (нирс) 10. 1 Информационно-аналитический, 662.36kb.
- Научно-исследовательская работа студентов, 216.82kb.
- Научно-исследовательская работа студентов на кафедре мировой экономики в 2009 2010, 48.05kb.
- Положение об организации научно-исследовательской работы студентов, 130.25kb.
- Научно-исследовательская работа студентов лингвистического университета как способ, 161.47kb.
Секция технологии металлов
и ремонта
Оптимизация числа постов
по ремонту агрегатов машин
Кутырев Е. В. — студ. 5 курса
Научный руководитель — докт. техн. н., проф. Шиловский В. Н.
В условиях рыночной экономики автотракторная техника стала эксплуатироваться на предприятиях и в фирмах различных форм собственности и типоразмеров, в которых производство ремонтных работ не стало подвергаться былой плановой регламентации. При случайной, а не плановой загрузке пунктов технического сервиса (ПТС) в потоке заявок имеют место сгущения и разряжения. Сгущения приводят либо к отказу в обслуживании, либо к образованию очереди. Разряжения приводят к непроизводительному (убыточному) простою отдельных постов, стендов или зоны ремонта в целом. Предприятие технического сервиса машин становится типичной системой массового обслуживания (СМО) открытого или закрытого типа. При оптимальном числе постов (Ni) экономические потери (возможные убытки) как от непроизводительного простоя постов, так и вследствие отказов от исполнения поступивших заявок W(Ni*), будут иметь минимальные значения. Таким образом, условие выбора оптимального числа постов имеет вид: W(Ni*)=minW(Ni). Функция оптимизации отражает количественное значение суммарных экономических потерь:
W(Ni) = C1∙λi
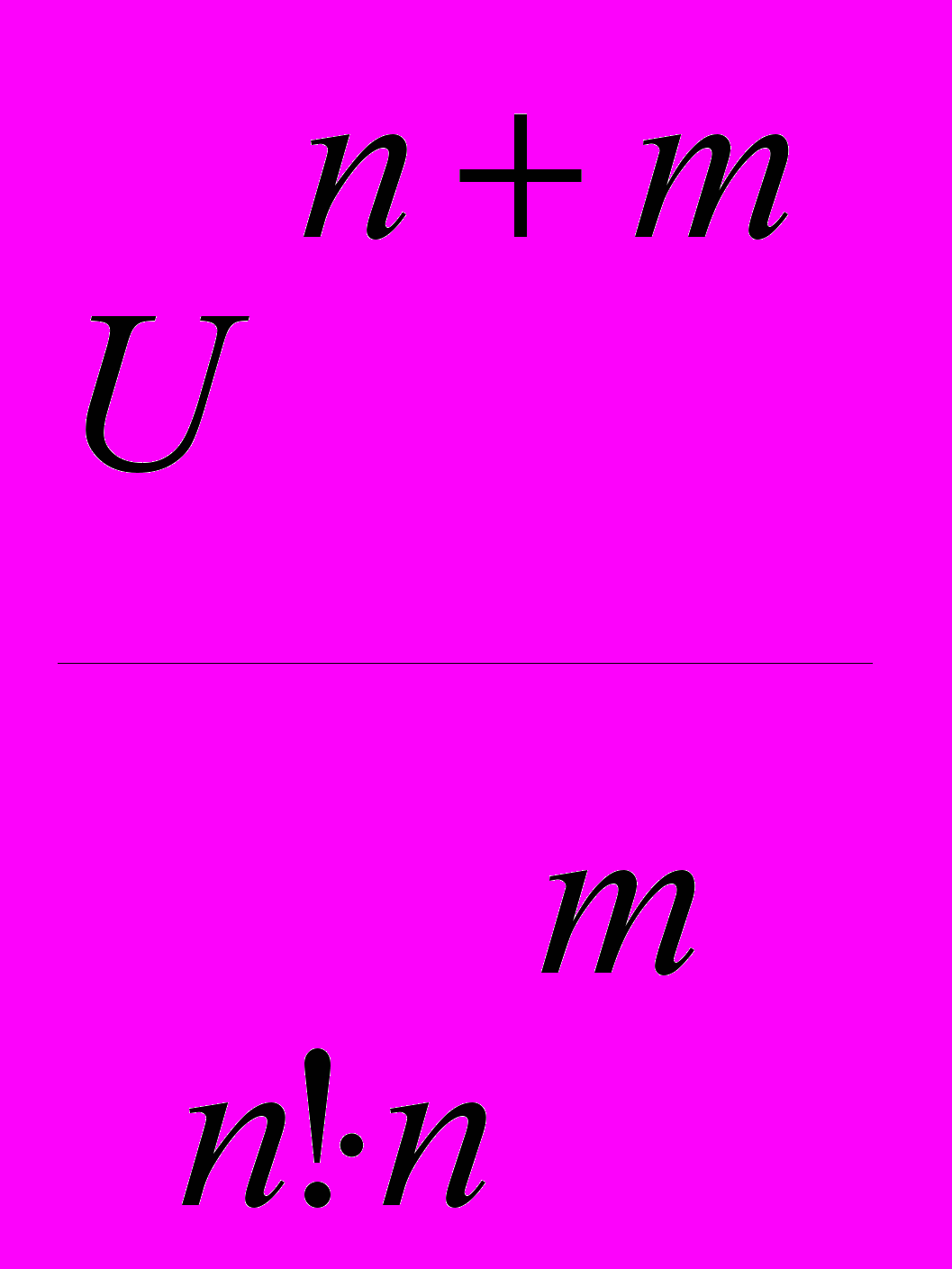
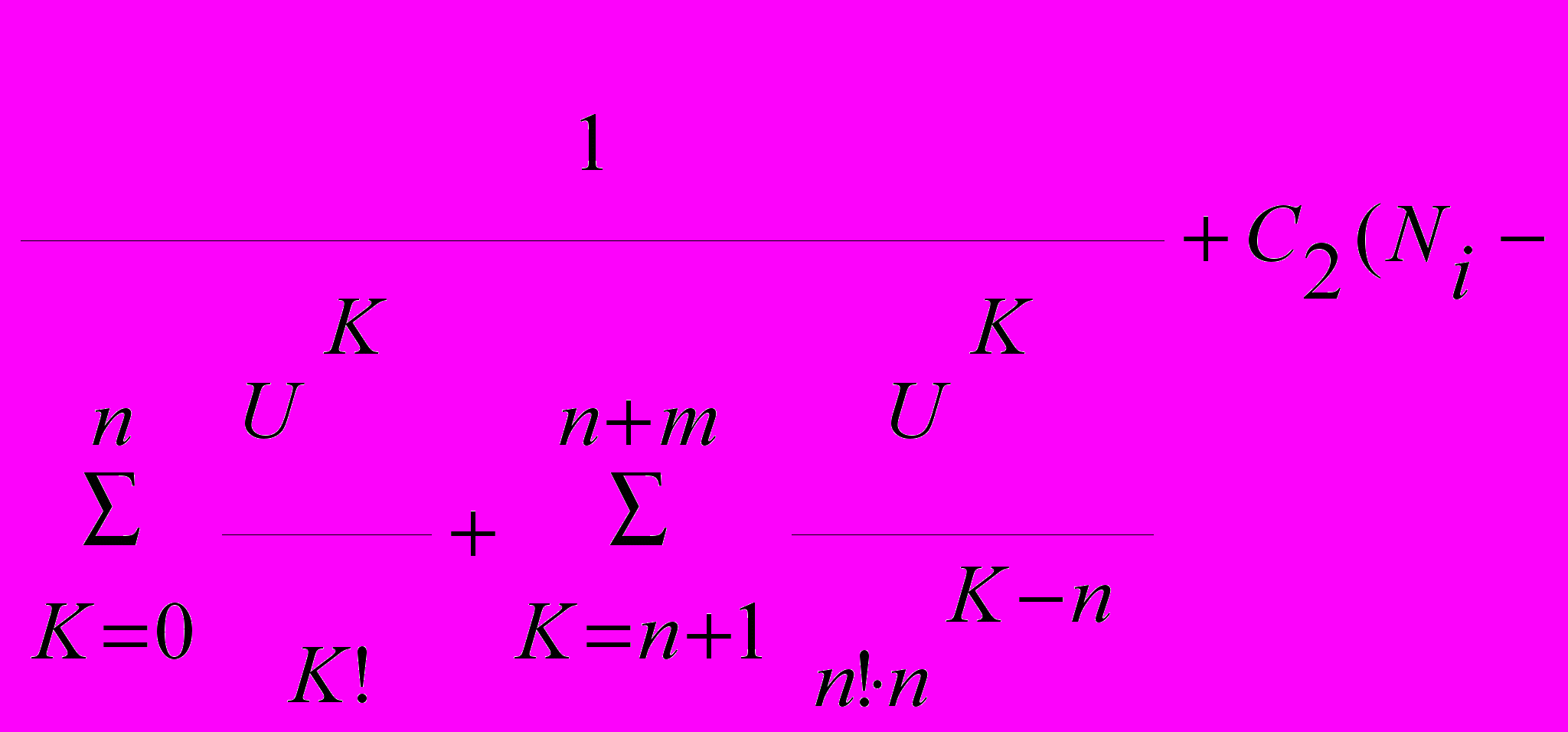
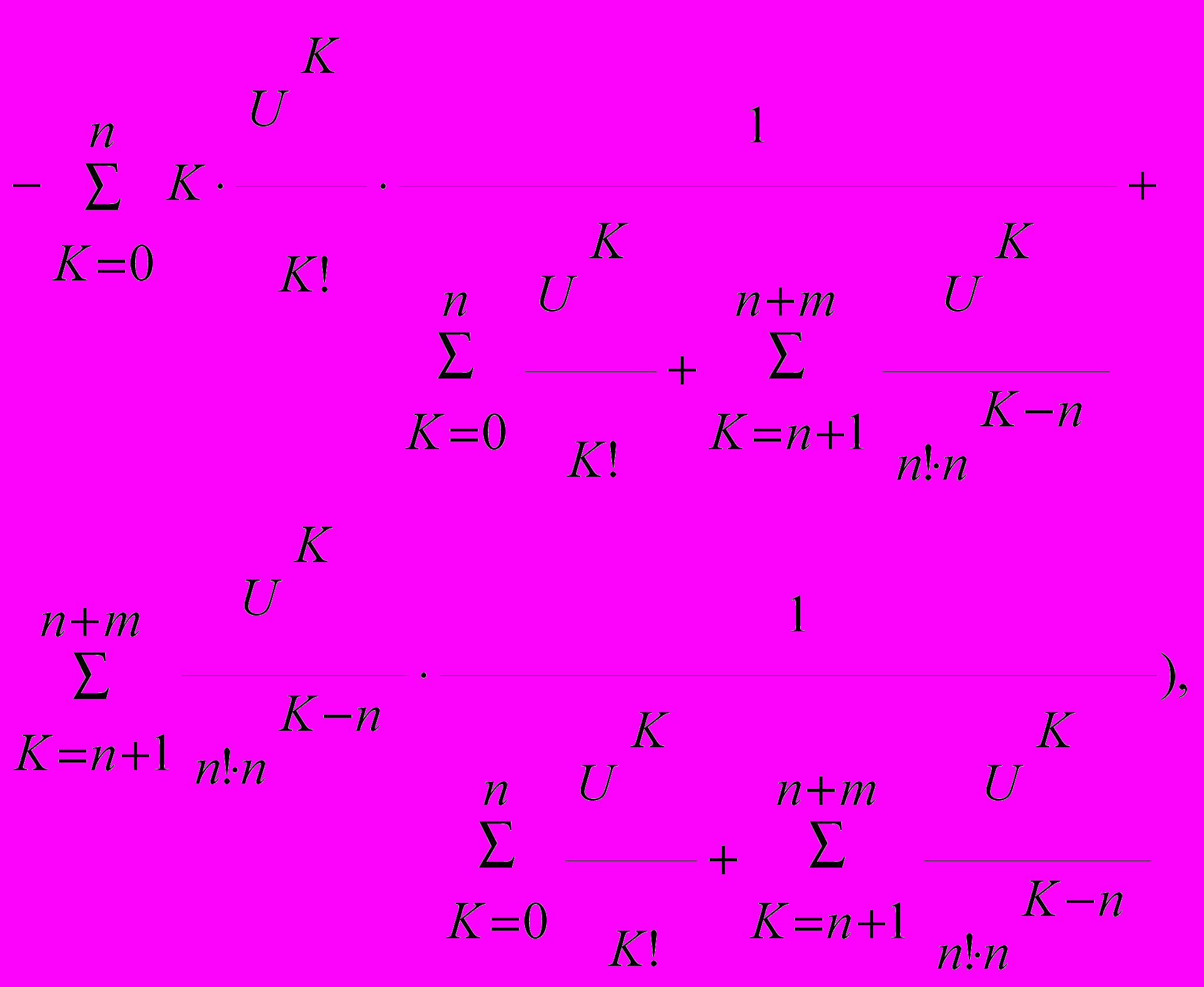
где U = λ∙T; остальные параметры приведены ниже в исходных данных примера.
Решение задачи оптимизации числа постов с помощью специально созданной программы и ПЭВМ можно проиллюстрировать на примере следующих исходных данных: число постов СТОА (N) — 10, число мест в очереди (n) — 0, параметр потока заявок (1) — 1, среднее время ремонта (T) — 3,5 дня, время работы станции — 1 день, средняя прибыль от выполнения заявки — 150 тыс. руб., потери от простоя одного поста i-го наименования — 30 тыс. руб. Результаты расчетов сведены в таблицу 1.
^ Таблица 1
Результаты расчетов оптимального числа постов
N | 1 | 2 | 3 | 4 | 5 | 6 | 7 | 8 | 9 | 10 |
W | 123,3 | 102,0 | 87,5 | 81,4 | 84,3 | 96,0 | 115,1 | 139,3 | 166,7 | 195,6 |
Вывод: минимум потерь будет при наличии четырех постов.
^
ПОСТАНОВКА ЗАДАЧИ ОПРЕДЕЛЕНИЯ
РАЦИОНАЛЬНОЙ ПЕРИОДИЧНОСТИ
ДИАГНОСТИРОВАНИЯ МАШИН И ОБОРУДОВАНИЯ
Мармылев М. А. — студ. 5 курса
Научный руководитель — докт. техн. н., проф. Шиловский В. Н.
Периодичность проверки или диагностики машин и оборудования зависит от технического состояния их элементов и закона его изменения во времени. Проверка технического состояния сопряжена с тем, что проверяемая система или какая-то ее часть должны быть выведены из состояния готовности или работы на некоторое время для осуществления самой процедуры проверки. Это обстоятельство обозначает, что более частые проверки приводят к уменьшению полезного времени работы, а с другой стороны, более редкие проверки создают меньшую уверенность в предупреждении возникновения аварийных отказов или состояния объекта, при котором его эксплуатация становится убыточной. Заслуживает внимания планирование проверок на основе баланса их стоимости и потерь от обнаружения неисправности системы (машины, оборудования). При этом каждая проверка имеет фиксированную стоимость С1, а пребывание системы в неисправном состоянии в течение одного часа обходится в С2 руб./час. Неисправности, которые несут эксплуатационные потери, могут возникнуть в любой момент времени между К-й и (К+1)-й по счету проверкой. Для определения оптимального значения моментов проверок tk можно воспользоваться следующим реккурентным соотношением:
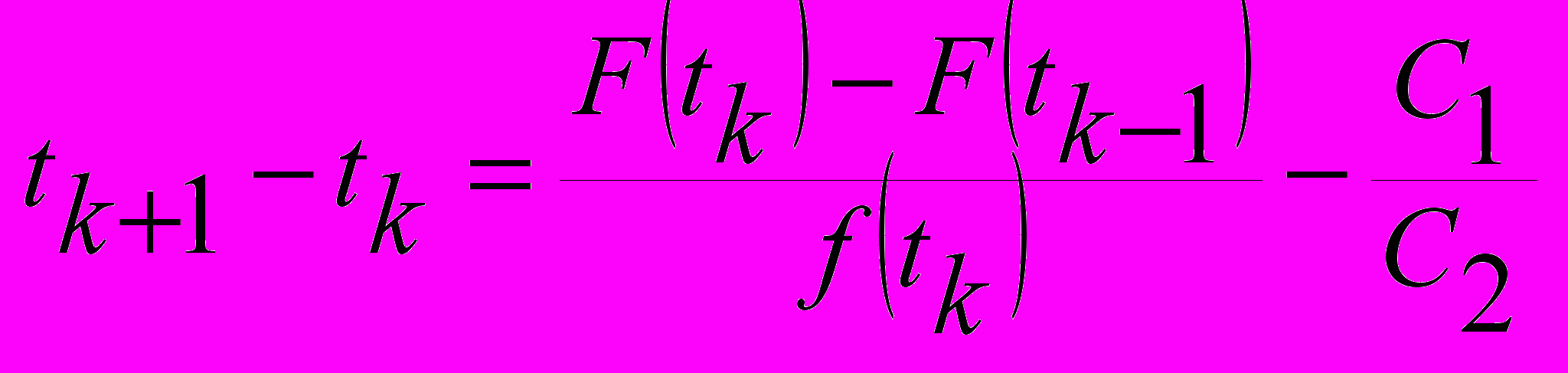
где
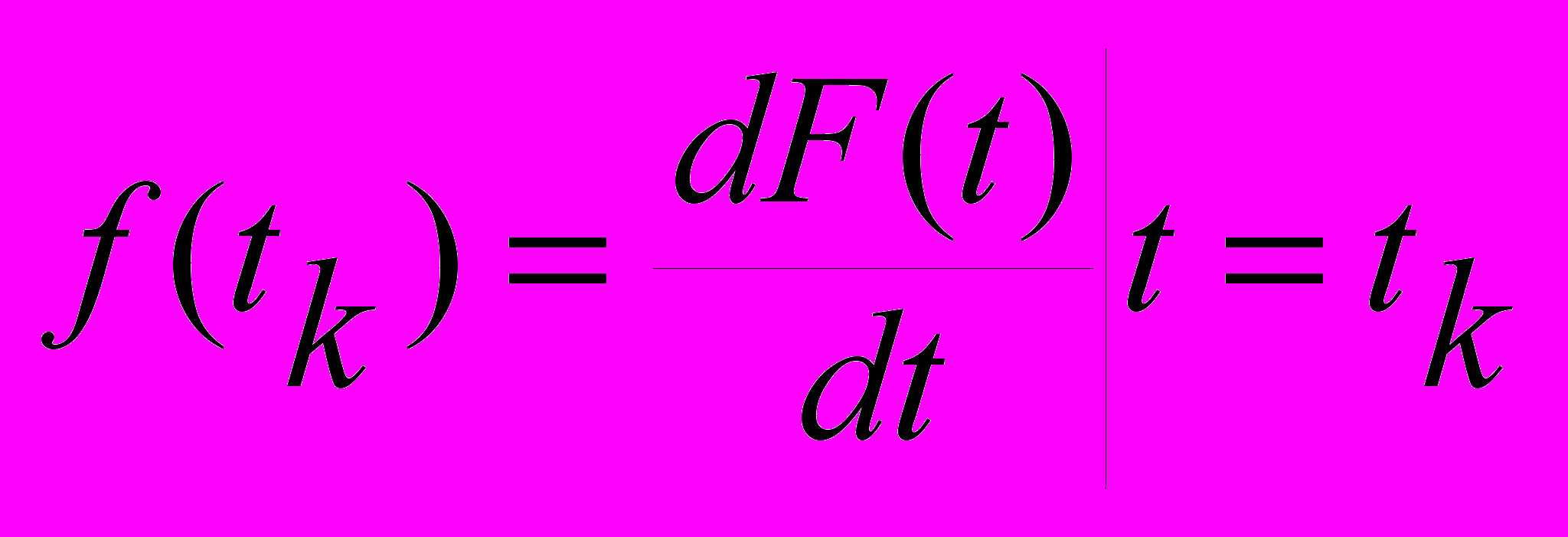
F(t) — распределение времени до первой неисправности системы. Для некоторого вида распределения F(t), имеющего возрастающую функцию опасности λ(t), процедура выбора момента проверки устанавливается следующим положением. Выбрав в качестве момента первой проверки некоторое положительное число t1 и определив с помощью его последующие моменты проверок по вышеприведенной формуле, устанавливаем, что если значение t1 выбрано так, что t1> t*1, то для некоторых положительных целых значений n имеет место соотношение: Δn=tn+1-tn>Δn-1= tn- tn-1, а когда t1< t*1, то для некоторых положительных значений n Δn<0. Это положение обосновывает итеративную процедуру отыскания оптимальной последовательности проверок для весьма широкого класса распределений F(t).
^
Определение качества щепы на рубительной
машине марки МРН-150 в древесно-
подготовительном цехе ОАО «Кондопога»
Овечкин С. А. — студ. 5 курса
Научный руководитель — к. техн. н., доц. Кондратьев Ю. Н.
Качество бумаги во многом зависит от нормативных параметров щепы. В производстве бумаги примерно 70% чисто окоренного баланса поступает в древесно-массный завод для получения древесной массы и 30% поступает на рубительные машины для получения технологической щепы, а щепа затем идет на целлюлозный завод для получения целлюлозы.
Технологический процесс производства газетной бумаги начинается с древесно-подготовительного цеха. Подготовка древесины для древесно-массного производства ограничивается ее распиловкой и окоркой; для целлюлозного производства подготовка аналогична, но дополнительно производится рубка древесины на щепу и сортирование ее по фракциям.
В производстве целлюлозы необходима щепа нормальной фракции, так как при химическом разложении древесины из нее получается равномерный по качеству полуфабрикат бумажного производства. Щепа мелкой фракции быстрее проваривается, чем нормальная, как следствие, при продолжительной варке переваренная мелкая щепа будет причиной волокнистых потерь. Крупная щепа замедляет процесс получения качественной целлюлозы. Исходя из вышесказанного, условием полного использования древесины при получении целлюлозы является равномерность щепы по размерам и качеству. Поэтому рубительное отделение занимает важное место в производстве целлюлозы.
Цель исследований заключалась в определении размеров щепы на старой машине МРН-150.
Методика исследований предусматривала следующее. Исследования проводились в феврале 2004 года. Объект исследований — 10 замеров различных фракций щепы в граммах, выбранных из типичной партии щепы. Фракции щепы сортировались при помощи сит с различными размерами ячеек. Испытания проводились следующим образом. Из потока щепы набирается навеска массой два килограмма. Оценка качества производится по виду щепы. Отобранная проба щепы сортируется по величине на лабораторном ситовом механическом анализаторе марки АЛГ-М. В лаборатории на подвижном основании анализатора устанавливают набор контрольных сит с отверстиями диаметром 30, 20, 10, 5 мм и поддон. Навеску после отбора из нее коры и гнили высыпают на верхнее сито. Набор сит затягивают стяжками, включают анализатор
и сортируют навеску в течение одной минуты. После полной остановки анализатора остатки на ситах взвешивают на весах с погрешностью не более 1 грамма. При сортировании пробы щепы устанавливается весовое и процентное количество частиц щепы крупной фракции, нормальной фракции, мелкой фракции и опилок. Полученные данные сравнивались с нормативными значениями.
Нормативные значения в процентном выражении фракций щепы составляют: опилок не более 1,5%, мелких фракций не более 9,2%, нормальных фракции не менее 85% и крупных фракций не более 4,3%. Получены следующие значения: опилок 2,7%, мелких фракций 9,83%, нормальных фракций 84,05% и крупных фракций 3,95%.
Результаты исследований показывают, что при нормативных значениях 1,5% фракции опилок фактически составляют 2,06%, что на 0,56% больше нормативных. Мелких фракций больше на 0,63%. Нормальных фракций на 0,95% меньше нормативных значений. Крупные фракции соответствуют нормативным требованиям.
Выводы по результатам исследований. Необходимо заменить старую рубительную машину по причине ее физического и морального износа, не позволяющую повысить качество и производительность выработки технологической щепы, на новую.
^
Пути решения проблемы исследования
и оценки ремонтопригодности машин
Печерин В. В. — студ. 4 курса
Научный руководитель — докт. техн. н., проф. Шиловский В. Н.
Ремонтопригодность — свойство машин, заключающееся в приспособленности их конструкции к техническому обслуживанию и ремонту, осуществляемым с целью поддержания и восстановления работоспособного состояния и ресурса.
Требуемые свойства машин, в том числе и ремонтопригодность, закладываются при разработке их конструкций, обеспечиваются при изготовлении и поддерживаются в заданных границах в процессе эксплуатации. Проблема исследования ремонтопригодности машин заключается в том, что определение показателей ремонтопригодности требует значительных затрат времени и материальных средств.
Целью работы является разработка методики теоретических экспериментов по оценке и выявлению основных показателей ремонтопригодности машин. Для этого необходимо определить и установить критерии продолжительности и трудоемкости снятия и установки типовых деталей, узлов, агрегатов.
Была разработана технологическая карта снятия коробки передач
с автомобилей КамАЗ и ЗИЛ и дана сравнительная оценка ремонтопригодности по двум показателям: времени снятия и трудоемкости операций. Исходными данными послужили рабочие чертежи автомобилей, каталоги запасных частей и руководства по техническому обслуживанию и ремонту рассматриваемых автомобилей. Были получены следующие результаты:
1. Количество операций по снятию коробки передач с автомобиля ЗИЛ на 16 операций меньше, чем для автомобиля КамАЗ.
2. Трудоемкость снятия данного узла составила 102 чел.*мин. для автомобиля ЗИЛ и 193 чел.*мин. для автомобиля КамАЗ.
3. Время снятия данного узла двумя рабочими 60 мин. для автомобиля ЗИЛ и 100 мин. для автомобиля КамАЗ.
Можно сказать, что количественные показатели ремонтопригодности автомобиля ЗИЛ почти в два раза превышают показатели автомобиля КамАЗ.
Ремонтопригодность является не единственным свойством машины. Решение комплекса вопросов, связанных с заданием и обеспечением ремонтопригодности, должно осуществляться с учетом обеспечения
и других свойств машины.
В будущем необходима программа создания базы данных, обработки данных, составления технологических карт разборки-сборки и оценка ремонтопригодности машин с использованием ПЭВМ.