Иван Васильевич Ефимов начальник центральной заводской лаборатории омк техническое состояние и опыт поставки труб с повышенными эксплуатационными характеристиками
Вид материала | Документы |
- М. А. Булгакова Вспомните, с какими произведениями Булгакова знакомы по книга, 41kb.
- Инженерные нанотехнологии в машиностроении, 13.77kb.
- Обеспечение сохранности защитного покрытия труб при транспортировке, 78.18kb.
- Реферат Иван Грозный как защитник православия, 832.5kb.
- Администрация костромской области контрольное управление информационный обзор материалов, 465.6kb.
- Николай Васильевич Гоголь Утро делового человека I кабинет; несколько шкафов с книга, 79.85kb.
- Техническое задание На изготовление стеклопластиковых насосно-компрессорных труб транспортируемый, 18.84kb.
- Конспект сдвоенного урока Тема: Подготовка к написанию сочинения описания внешности, 176.6kb.
- Компания Suzuki представляет совершенно новый автомобиль sx4 Sedan, отличающийся изысканной, 39.43kb.
- Кряжев Игорь Васильевич); планово-экономический отдел (начальник Спиридонова Наталья, 62.15kb.
Иван Васильевич Ефимов
начальник центральной заводской лаборатории ОМК
Техническое состояние и опыт поставки труб с повышенными эксплуатационными характеристиками
(Краткое описание технологии)
Участок подачи листа. На приемный рольганг осуществляется входной контроль исходного материала, заведение на каждый лист электронной карты контроля, присваивание листу заводского порядкового номера. Для повышения качества концов сварного соединения трубы к листу привариваются технологические планки, далее производится разделка продольных кромок под сварку;
Участок формовки труб. Подгибка продольных кромок листа осуществляется шаговым способом на шаговом прессе одновременно с двух сторон последовательно участками по всей длине, формовка основной части профиля трубной заготовки осуществляется на прессе шаговой формовки способом многопереходной гибки участков от подогнутых кромок к середине профиля одновременно по всей длине заготовки;
Участок сварки труб. Сварка труб производится в три этапа с удалением окалины; 1) однодуговая сварка технологического шва, 2) четырехдуговая сварка внутреннего шва 3) пятидуговая сварка наружного шва, автоматические режимы сварки дублируются визуальным контролем на мониторе,
Участок отделки труб. После зоны охлаждения сварного соединения труба поступает на участок автоматического ультразвукового контроля сварного соединения, на участке отделки трубы подвергаются ручному ультразвуковому контролю, производится механическая обработка торцов труб с образованием фасок;
Участок экспандирования и гидравлического испытания. На участке экспандирования и гидравлических испытании производится калибровка методом раздачи труб участками по всей длине механическим экспандером, далее на участке торцовки труб фрезеруется сварочная кромка без образования фаски, на гидропрессе проводится опрессовка трубы по всей длине;
Участок ремонта. Производится визуальный осмотр и ручной ультразвуковой контроль не подтвержденных в камерах рентген- телевизионного контроля дефектов, но отмеченных ультразвуковым контролем, по результатам контроля принимается решение о ремонте или отбраковке труб, затем производится обрезка кольцевых дефектных участков труб включая технологические планки с предварительной рашихтовкой отрезаемых колец;
Склад и отгрузка труб. Складирование проводится в штабели, каждая партия получает сертификат качества, отгрузка осуществляется на авто и железнодорожный транспорт.
Голеницкий Андрей Иванович
Заместитель начальника отдела сборно-разборных трубопроводов
ФГУП «25 ГосНИИ Минобороны России»
Использование сборно-разборных трубопроводов
для перекачки нефти в сложных природно-климатических условиях
В последние годы все более острой становится проблема транспортировки нефти из отдаленных регионов ее добычи – Крайнего Севера, Сибири и Дальнего Востока. С одной стороны, ареал добычи удаляется к северу от регионов с развитой инфраструктурой и транспортных коммуникаций, с другой – требуются значительные капиталовложения по созданию и обеспечению функционирования объектов транспорта во вновь осваиваемых районах добычи. В большинстве случаев точной оценке объемов запасов вновь открываемых месторождений нефти и их промышленному освоению в труднодоступных районах препятствует отсутствие возможностей по ее транспортировке. Очевидно, именно этим можно объяснить то, что в настоящее время не используется около 30% нефтяных скважин от общего количества состоящих на балансе.
Применение для вывоза нефти в таких условиях наливного автомобильного транспорта неэффективно увеличивается ее себестоимость, а в ряде случаев добыча становится нерентабельной. Строительство же стационарных трубопроводных систем на этапе опытного освоения месторождений, как правило, связано с экономическим риском, со значительными капиталовложениями и не всегда технически и экономически целесообразно. В этих условиях для транспортировки нефти представляет большой интерес использование сборно-разборных трубопроводов (СРТ).
Начиная с момента своего зарождения в Вооруженных Силах, сборно-разборные трубопроводы создавались для обеспечения горючим войск (флота) при ведении ими боевых действий. За долгий путь своего становления и развития они превратились в самые совершенные системы подобного рода не только у нас в стране, но и за рубежом. В них воплотились передовые научные идеи и технические решения. По своим техническим характеристикам, особенно по возможности механизированного монтажа и объемам перекачиваемого продукта, отечественные СРТ с раструбным соединением не имеют аналогов в мире. Соединение «Раструб» рассчитано на работу при давлении до 6 МПа; его сборка и разборка без специального инструмента невозможна.
К положительным качествам СРТ, обусловливающим возможность их эффективного использования для перекачки нефти, можно отнести высокие темпы сооружения при относительно малых капиталовложениях. Так, одна бригада в составе 12-15 человек в течение рабочего дня прокладывает 3 км СРТ диаметром 150 мм. Следует назвать и такие преимущества, как возможность прокладки и эксплуатации в любых природно-климатических условиях, на местности с рельефом различной степени сложности при минимальном объеме проектно-изыскательских и земляных работ; высокая техническая надежность; модульность и простота конструкции; низкая себестоимость транспортной работы, быстрая самоокупаемость и другие. К тому же комплекты СРТ представляют собой готовые к применению инженерно-технические комплексы, включающие трубы, трубопроводное и вспомогательное оборудование, запорную и регулирующую арматуру, монтажный инструмент, компрессорные станции и передвижные средства перекачки.
Ранее все сооружаемые трубопроводы по конструкции были сборно-разборными, лишь в 1926 г. они становятся сварными. Однако с того времени СРТ претерпели большие изменения, и сейчас они опять находят себе широкое применение.
Впервые в наше время сборно-разборный трубопровод начал использоваться для перекачки нефти в Республике Саха (Якутия) в 1996 г.
Обладая рядом крупных месторождений нефти и не имея возможности вывезти ее из труднодоступных районов, республика вынуждена была ежегодно ввозить для энергообеспечения и теплоснабжения до 160 тыс. т дизельного топлива. В то же время местные ресурсы использовались минимально. Так, нефть, добываемую на расположенном в тайге Талаканском газонефтяном месторождении, можно было вывозить только в период с ноября по март в автоцистернах по зимнику. За сезон с этого месторождения вывозилось автотранспортом не более 9 тыс. т нефти.
Правительство Якутии приняло нетрадиционное решение – приобрести у Министерства обороны и использовать для транспортировки нефти с Талаканского месторождения до поселка Витим, на берегу реки Лены, сборно-разборный трубопровод ПМТП-150.
Учитывая сложные природно-климатические условия, было принято решение вести перекачку нефти по трубопроводу только при положительной температуре окружающей среды, с мая по октябрь.
В течение сезонов эксплуатации 1996-2005 гг. по сборно-разборному трубопроводу длиной 110 км было подано порядка 1,7 млн. т нефти. Объем перекачки нефти в 2005 г. составил 254 тыс. т. Срок окупаемости капитальных вложений составил менее одного года, а себестоимость транспортировки нефти по трубопроводу не превышала 60 руб./т (для автомобильной перевозки – около 200 руб./т).
За весь период эксплуатации нефтепровод сохранил полную герметичность, аварийных ситуаций и неисправностей трубопроводной техники и оборудования с проливами нефти не отмечено.
Опыт длительного применения сборно-разборного трубопровода для перекачки нефти, полученный в крайне неблагоприятных условиях сибирской тайги, оказался востребованным. Сооруженные в последствие нефтепроводы рассчитаны на круглогодичную эксплуатацию.
В 2000 г. аналогичный трубопровод сооружен на направлении Мусюршор-Сандивей (Ненецкий автономный округ).
Строительство нефтепровода протяженностью 50,5 км велось в июне-июле 2000 г., подача по нему составила 250-300 т/сут.
В 2002 г. временный нефтепровод протяженностью 112 км из комплекта ПМТП-150 был сооружен в весенне-летний период на направлении Яракта - Верхнемарково (Иркутская область). Трубопровод прокладывался в глухой тайге по просеке рядом с грунтовой дорогой, доступной только для транспорта высокой проходимости.
В 2003 г. сооружен временный нефтепровод Дулисьма – Яракта протяженностью 78 км (Иркутская обл.).
В настоящее время разрабатывается проект «Система трубопроводного транспорта нефти «Верхнечонское НГКМ – Усть-Кут» протяженностью 571 км.
Технологическая схема СРТ, использующегося для перекачки нефти, разрабатывается индивидуально с учетом специфических особенностей трубопровода и базируется на типовых технологических схемах его основных элементов.
Используемые для перекачки передвижные насосные установки позволяют при различном их сочетании в составе насосной станции добиться широкого диапазона подач по трубопроводу – от 50 до 500 м3/ч.
Таким образом, опыт сооружения и эксплуатации нефтепроводов показал высокую эффективность трубопроводной техники и оборудования из состава комплектов сборно-разборных трубопроводов при перекачке нефти в сложных природно-климатических условиях страны.
В настоящее время проектированием и сооружением СРТ для перекачки нефти занимаются совместно ФГУП «25 ГосНИИ Минобороны России» и ООО «НЕФТЕГАЗ ИНЖИНИРИНГ».
Арно Жерболе,
технический специалист, Arkema
Разработка адгезива
Для защитного покрытия трубопроводов и нанесение 3-слойных ПЭ-покрытий
ОПИСАНИЕ ПРОЦЕССА
Процесс нанесения 3-хслойных полиолефиновых покрытий аналогичен процессу нанесения покрытий «экструзионным методом»
Линия нанесения «трехслойного покрытия» с одной станцией подогрева
- - привод, вращающий трубу
- - индукционный нагрев
- - станция нанесения эпоксидного праймера
- - экструзия адгезива
- - экструзия ПЭ
- - прижимной ролик
- - охлаждение разбрызгиванием воды
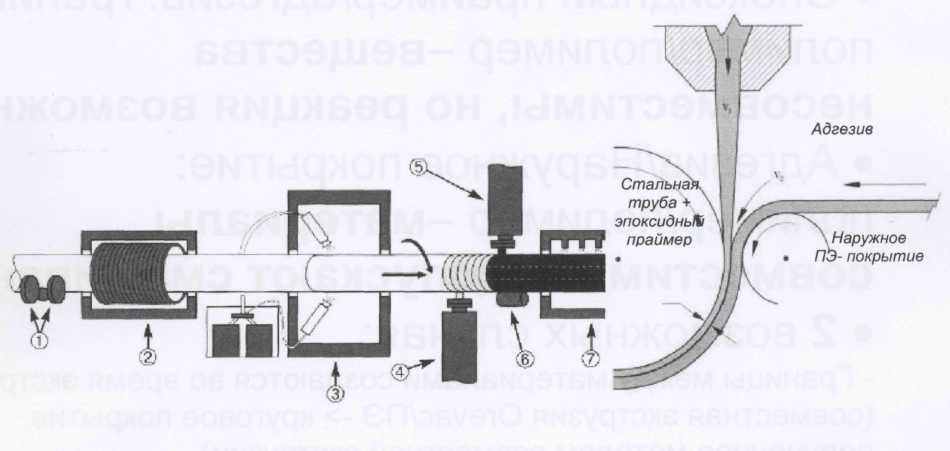
ОПИСАНИЕ ПРОЦЕССА
Возможные типы границ между двумя материалами
- Сталь/эпоксидный праймер: граница
между металлом/полимером: реакция
возможна
- Эпоксидный праймер/адгезив: граница
полимер/полимер -вещества
несовместимы, но реакция возможна
- Адгезив/Наружное покрытие:
полимер/полимер -материалы
совместимы и допускают смешивание
- 2 возможных случая:
- Границы между материалами создаются во время экструзии
(совместная экструзия Orevac/ПЭ -> круговое покрытие,
полученное методом совместной экструзии)
- Граница между материалами формируется при нанесении:
нанесение покрытия экструзией
• Для обоих случаев:
- Адгезив представляет собой экструдируемый
термопластичный материла (реология, обработка,
термостабильность,...)
- Молекулярная подвижность и способность вступать в
реакцию характерны только для расплавленного состояния
ПРИНЦИПЫ РАЗРАБОТКИ АДГЕЗИВА
•

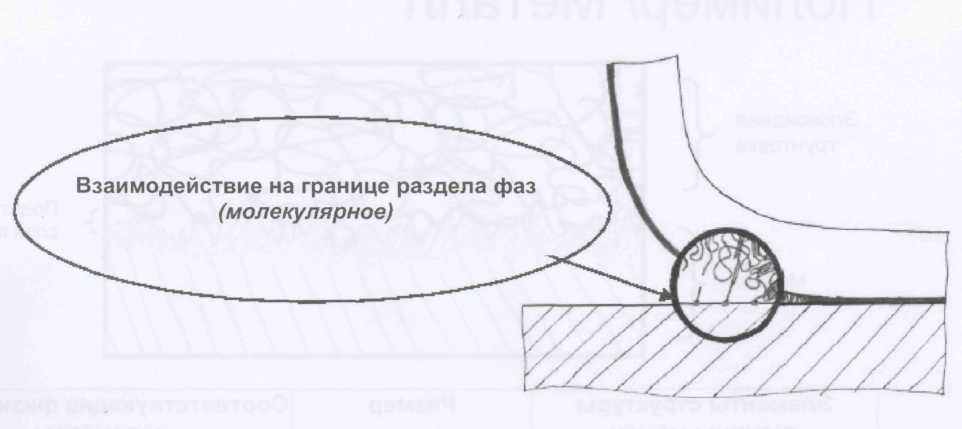
ПРИНЦИПЫ РАЗРАБОТКИ АДГЕЗИВА
О


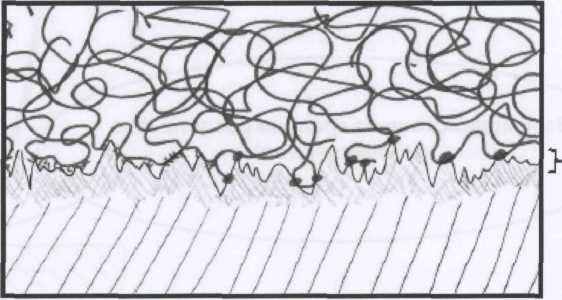
Эпоксидная грунтовка
Металл
Подготовленный слой поверхности
Элементы структуры границы между материалами | Размер | Соответствующие физические параметры |
- Взаимодействия на границе раздела фаз - Эффект увлажнения и капиллярный эффект | 1 нм | - Сила взаимодействий или связей - Способность к смачиванию |
- Адсорбированные молекулы - Механические зависимости | От 10 нм до 100 нм | - Плотность поверхности адсорбированных цепочек - Прочность границы между материалами |
- Связи, объединяющие макромолекулу/массу | От 100 до 1000 нм | - Переплетения или кристаллическое состояние |
ПРИНЦИПЫ РАЗРАБОТКИ АДГЕЗИВА
О

Полимер/Полимер

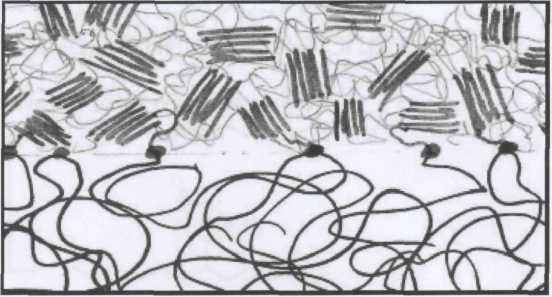
Полимер А
частично кристаллический
Полимер В
аморфный
Элементы структуры границы между материалами | Размер | Соответствующие физические параметры |
- Взаимодействия на границе раздела фаз (от VdW к ионно-ковалентной) | 1 нм | - Сила взаимодействий или связей |
- В месте нахождения сополимеров | 10 нм | - Плотность поверхности |
- Связи, объединяющие макромолекулу/массу | От 100 до 1000 нм | - Переплетения или кристаллическое состояние |
- граница между эпоксидной смолой и адгезивом
- граница между адгезивом - наружным покрытием
(два частично кристаллических полимера)
ПРИНЦИПЫ РАЗРАБОТКИ АДГЕЗИВА
С

• Сцепление на границе зависит от:
• Химической реакции между эпоксидной смолой и малеиновым ангидридом:
Упрощенная реакция между эпоксидной смолой и ангидридными группами
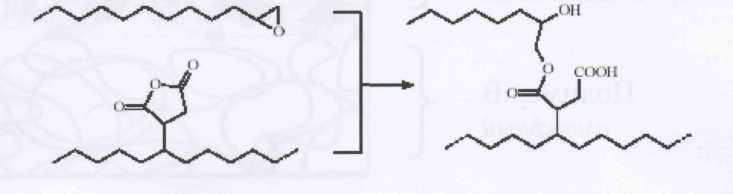
• Сцепление обеспечивается: • Состоянием эпоксидной смолы при нанесении слоя адгезива; мобильностью связей эпоксидной смолы и возможностью подавления реактивной функции эпоксидной смолы; температурой стальной трубы, химической активностью способностью к смачиванию эпоксидной смолы; временем гелеобразования.
ПРИНЦИПЫ РАЗРАБОТКИ АДГЕЗИВА
О

Полимер/Полимер

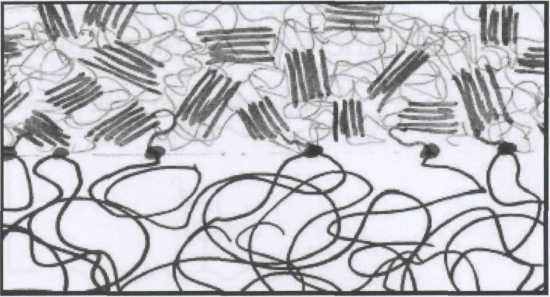
Полимер А
частично кристаллический
Полимер В
аморфный
Элементы структуры границы между материалами | Размер | Соответствующие физические параметры |
- Взаимодействия на границе раздела фаз (от VdW к ионно-ковалентной) | 1 нм | - Сила взаимодействий или связей |
- В месте нахождения сополимеров | 10 нм | - Плотность поверхности |
- Связи, объединяющие макромолекулу/массу | От 100 до 1000 нм | - Переплетения или кристаллическое состояние |
- граница между эпоксидной смолой и адгезивом
- граница между адгезивом - наружным покрытием
(два частично кристаллических полимера)
ПРИНЦИПЫ РАЗРАБОТКИ АДГЕЗИВА
О

Покрытие, наносимое экструзией
• Важные факторы:
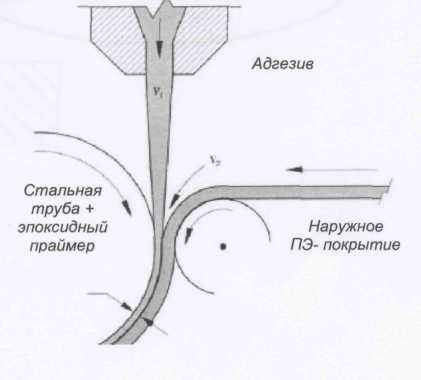
- Температуры
- Молекулярная кинематика вступающих в реакцию
макромолекул в расплавленном состоянии (с момента
непосредственного соприкосновения до момента
кристаллизации)
- Химическая активность в расплавленном состоянии
- Свойства твердой поверхности (химическая
активность, загрязненность и т.д.)
- Принудительное
увлажнение эпоксидной
смолы или адгезива на
шероховатых поверхностях
или в порах (давление)
- Шкала времени
кристаллизации при
разработке адгезива после
контакта
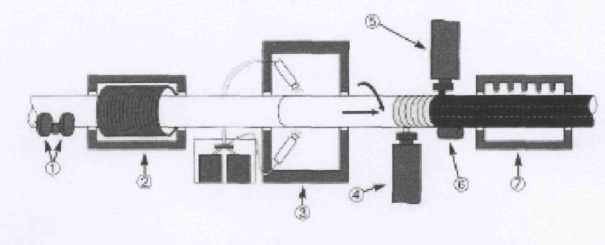
Линия нанесения «трехслойного покрытия» с одной станцией подогрева
- - привод, вращающий трубу
- - индукционный нагрев
- - станция нанесения
эпоксидного праймера
- - экструзия адгезива
- - экструзия ПЭ
- - прижимной ролик
- - охлаждение
разбрызгиванием воды
ПРИНЦИПЫ РАЗРАБОТКИ АДГЕЗИВА
•

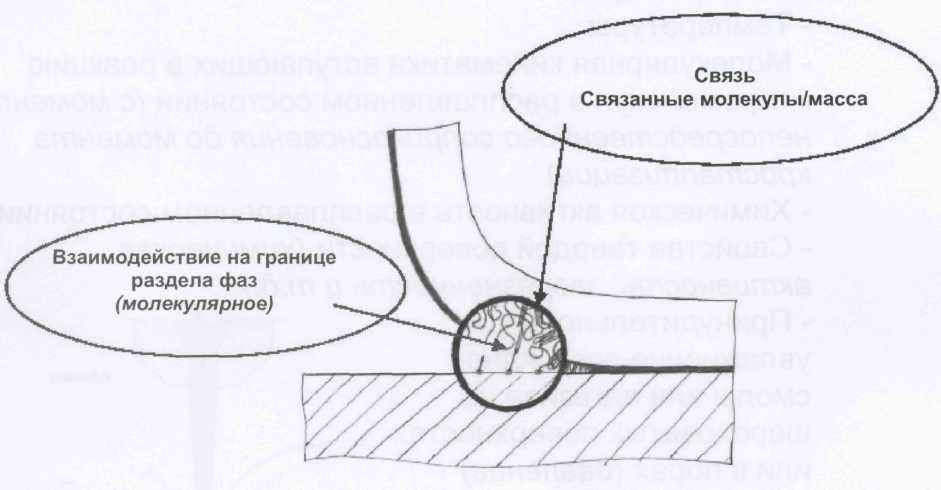
ПРИНЦИПЫ РАЗРАБОТКИ АДГЕЗИВА
С

- Взаимодействие между связанной
молекулой на границе раздела и массой
должно быть эффективным
- => большое значение имеет структура
адгезива
- Структура цепочек, полученных в результате
привитой сополимеризации
- Цепочка должна быть оптимизирована
- скорость кристаллизации
- молекулярный вес
- распределение длины
- наличие низкомолекулярной массы
- скорость МАН
ПРИНЦИПЫ РАЗРАБОТКИ АДГЕЗИВА
М

- Сцепление существует ТОЛЬКО в том
случае, если во время отделения различных
слоев будет рассеиваться энергия.
- => большую роль играет поведение адгезива
вблизи границы раздела фаз.
Для хорошего сцепления необходимы
- - ХОРОШАЯ ХИМИЧЕСКАЯ РЕАКЦИЯ И СВЯЗЬ МЕЖДУ ЭПОКСИДНОЙ
СМОЛОЙ И АДГЕЗИВОМ
- - ХОРОШАЯ МЕХАНИЧЕСКАЯ ХАРАКТЕРИСТИКА СОЕДИНЯЮЩЕГО
СЛОЯ
- - Диссипативные свойства адгезива, изменяющиеся в зависимости от
качества границы раздела фаз.
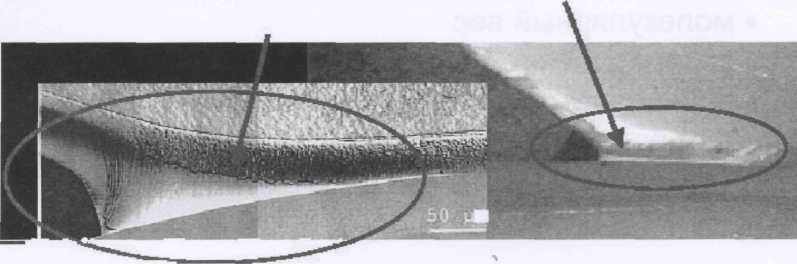
ПРИНЦИПЫ РАЗРАБОТКИ АДГЕЗИВА
Ч

Показатель прочности при расслоении эквивалентен силе, необходимой для отделения слоев. Этот показатель определяется 3 различными механизмами:
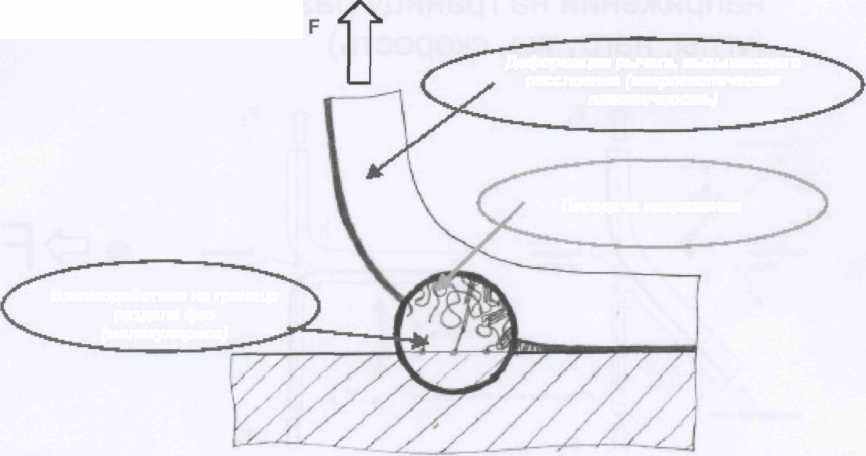
Усилие расслоения
Деформация рычага, вызывающего
расслоение (макроскопическая
пластичность)
Передача напряжения
Взаимодействие на границе
раздела фаз (молекулярное)
ПРИНЦИПЫ РАЗРАБОТКИ АДГЕЗИВА
Ч

расслоения
• Последствия: измеренное усилие
зависит
- => От параметров технологического процесса
- => От структуры (свойства различных слоев
адгезива и ПЭ, которые необходимо проверять:
термомеханические, термические)
- => От характеристик способов передачи
напряжений на границу раздела фаз при расслоении
(углы, нагрузка, скорость)
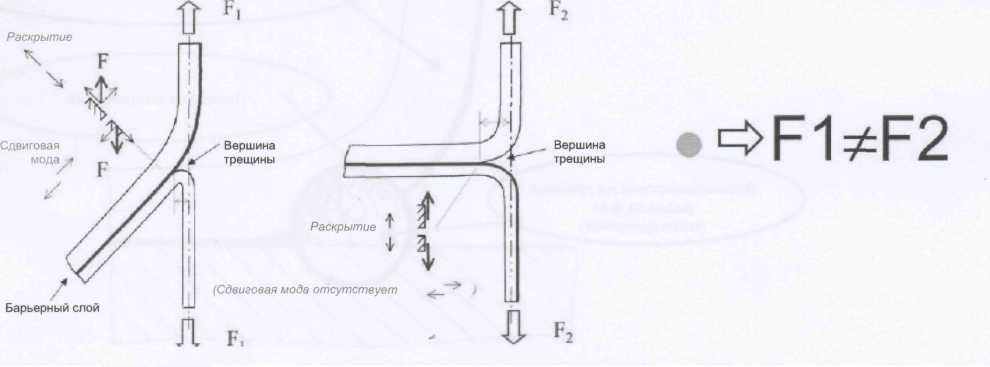
Нанесение адгезива для 3-хслойных ПЭ покрытий
•

Нанесение адгезива для 3-хслойных ПЭ покрытий
А

• Испытания DMA: динамомеханический анализ
• от-100°С до 150°С, Е' (модуль упругости), Е" (модуль пластичности), логарифмическая шкала
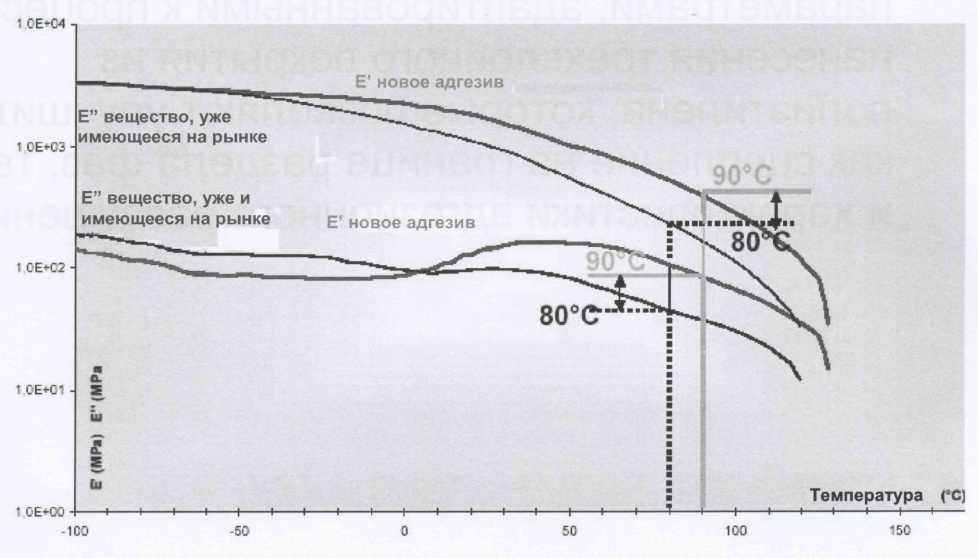
• Механические модули (упругости и пластичности) нового адгезива выше, чем у других веществ, имеющихся на рынке.
• При испытаниях на отслаивание было обнаружено, что для развития трещины требуется более высокая энергия.
Нанесение адгезива для 3-хслойных ПЭ покрытий
•

Нанесение адгезива для 3-хслойных ПЭ покрытий
С

• Повышение адгезии по мере роста температуры из-за более высоких значений термических характеристик нового адгезива
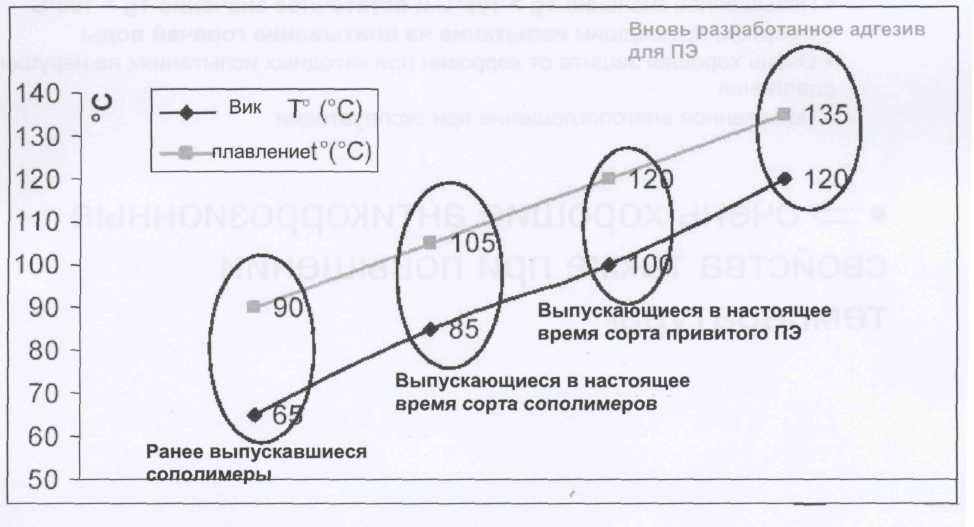
Нанесение адгезива для 3-хслойных ПЭ покрытий
А

• Лучшая антикоррозионная защита
эпоксидной смолы:
- Требуется состав эпоксидной смолы с низким содержанием
абсорбционной воды
- Новые эпоксидные смолы :
- Повышенное значение Тд > 105°С и остаточное значение Тд > 100°С
- с сортом, прошедшим испытание на впитывание горячей воды
- Очень хорошая защита от коррозии при катодных испытаниях на нарушение
сцепления
- Пониженное влагопоглощение при эксплуатации.
• => очень хорошие антикоррозионные
свойства также при повышении
температуры
Нанесение адгезива для 3-хслойных ПЭ покрытий
•

• Повышенную адгезию при температуре окружающей среды (23°С), а также при повышенной температуре.
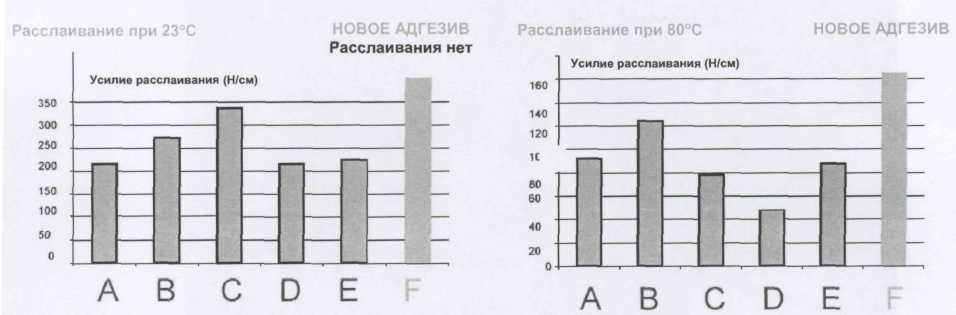
• При температуре 90°С при использовании нового адгезива: F > 100 Н/см
- Испытания проводились с использованием покрытых труб 0 8
дюймов (20,3 см), в характерных производственных условиях, а
также в тяжелых условиях эксплуатации.
- Эпоксидный праймер 90 мкм/адгезив (250 мкм)/ полиэтилен
повышенной плотности (2,5 мм)
Нанесение адгезива для 3-хслойных ПЭ покрытий
•

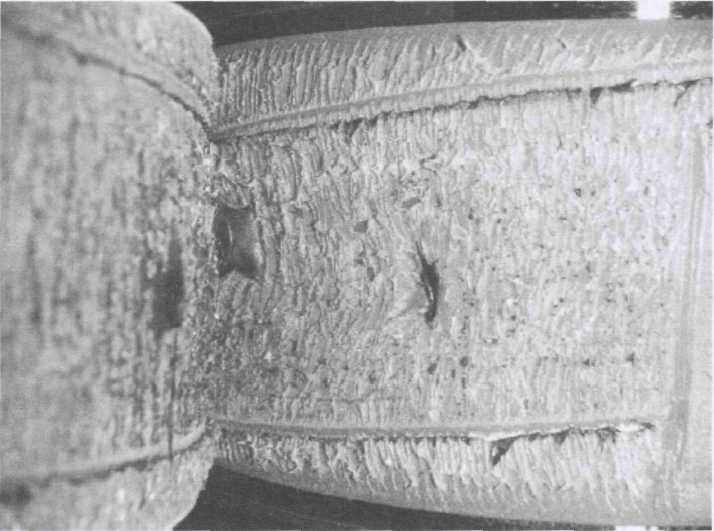
Нанесение адгезива для 3-хслойных ПЭ покрытий
| | | | |
Характеристики | Единицы измерения | Стандарты | Средние значения | |
Сопротивление отслаиванию 23° С 80°С 90°С | Н/5см | NFA49710 | > 1500 >600 >350 | |
Катодное нарушение сцепления 23°С/28 дней 40°С/7дней 95°С/28 дней | мм | NFA49710 | 2-4 3-5 8 | |
Электрическое сопротивление изоляции | Вт/м' | NFA49710 | > 10л10 | |
Ударная вязкость | Дж/мм | NFA49710 | 10-15 | |
Сопротивление вдавливанию 23°С 80°С 90°С | мм | NFA49710 | <0,06 <0,2 <0,3 | |
Твердость по Шору D (1 сек/15 сек) | | ASTMD2240 | 65 | |
Относительное удлинение при разрыве | % | NFA49710 | >500 | |
Стойкость к растрескиванию под действием напряжения окружающей среды (условие В) | час | ASTMD1693 | F20>1000 | |
УФ-старение | % | DIN 30670 NFA49 710 | ∆MFI<+/-35% Л% относит, удлинения <+/- 35% | |
Тепловое старение | | 1000 час- 100°С | ∆% относит, удлинения <+/- 25% | |
1000 час-110°С | ∆% относит, удлинения <+/- 25% | |
Нанесение адгезива для 3-хслойных ПЭ покрытий
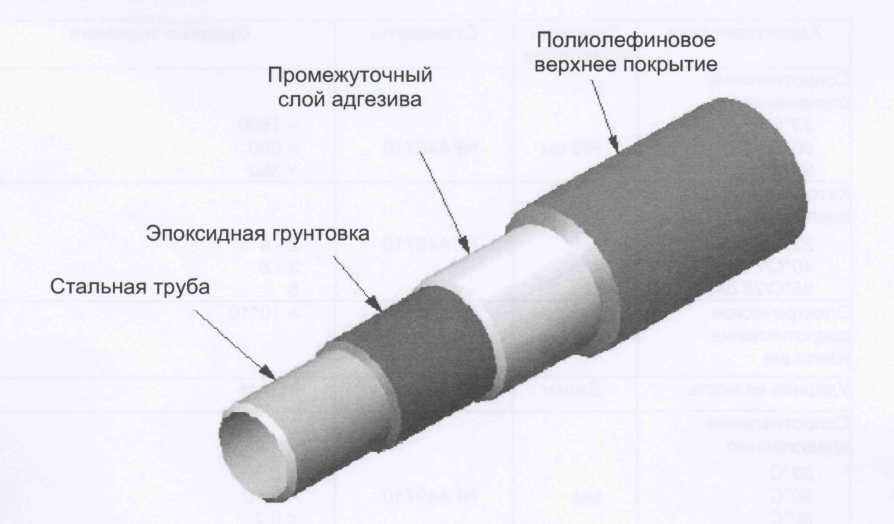
Свечкопалов Анатолий Петрович Генеральный директор ОАО МТЗК
НОВЫЙ СПОСОБ ПРОИЗВОДСТВА БАЛЛАСТНЫХ (ОБЕТОНИРОВАННЫХ) ТРУБ В ПОЛИЭТИЛЕНОВОЙ ОБОЛОЧКЕ ДЛЯ ИСПОЛЬЗОВАНИЯ ИХ ПРИ СТРОИТЕЛЬСТВЕ, РЕКОНСТРУКЦИИ И РЕМОНТЕ МАГИСТРАЛЬНЫХ ГАЗОНЕФТЕПРОВОДОВ НА ПОДВОДНЫХ И БОЛОТИСТЫХ УЧАСТКАХ
В настоящее время Россия, обладающая богатейшими залежами углеводородного сырья на шельфе, практически только начинает развивать свою морскую нефтегазодобывающую промышленность, в то время как удельный вес добычи морской нефти и газа в мире достигает 40%.
В последнее десятилетие пристальное внимание ряда стран привлечено к Северному Ледовитому океану и Каспийскому морю. Это связано с открытием в этом секторе мирового океана крупнейших залежей углеводородов, превышающих структуры Персидского залива.
Близость шельфа Западной Арктики и Каспия к индустриально развитым районам России и странам Западной Европы даёт возможность использовать добываемую продукцию как для внутреннего потребления, так и для реализации на экспорт через систему трубопроводов.
Кроме танкерных перевозок нефти и газового конденсата от перевалочных и береговых терминалов, наиболее перспективный вид транспорта углеводородов - использование подводных морских трубопроводов.
Использование подводных трубопроводов невозможно без балластировки. В мировой практике самым надёжным способом балластировки является обетонирование, т.е. на предварительно изолированную трубу наносится бетонное балластное покрытие. Разработанный на Московском трубозаготовительном комбинате (ОАО МТЗК) метод балластировки трубопроводов позволяет проводить обетонирование труб. На данную технологию обетонирования был выдан патент РФ. Главное отличие от «классического» способа балластировки (набрызг бетонного раствора на трубу, установки утяжелителей и т.д.) в том, что предварительно изолированная труба помещается в полиэтиленовую оболочку и пространство между ними заполняется бетонным раствором. Данный вид бетонной балластировки (бетон + полиэтиленовая оболочка) можно рассматривать и как дополнительное защитное покрытие, повышающее надёжность как морских подводных трубопроводов, так и укладываемых в водонасыщенных грунтах.
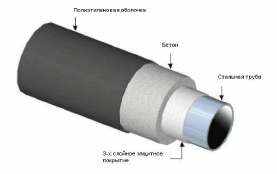
Конструкция трубы с балластным покрытием
Для противокоррозионной защиты наружной поверхности труб в базовых условиях применяют различные системы покрытий, в частности двухслойную систему покрытия (экструдированный адгезив-расплав -экструдированный полиэтилен или полипропилен) и трёхслойную систему покрытия (эпоксидная смола -экструдированный адгезив-расплав - экструдированный полиэтилен или полипропилен), а также однослойную эпоксидную систему покрытия.
Перед нанесением любого покрытия наружная поверхность труб сушится и очищается дребемётным способом, а также обеспыливается.
Далее трубы подвергаются хроматной обработке и нагреваются до определённой температуры.
Затем на трубы наносятся последовательно слои эпоксидного праймера, адгезионной композиции, полиэтилена или полипропилена. Полученное покрытие охлаждается.
После нанесения и охлаждения покрытия концы труб зачищаются под сварку.
После нанесения основного защитного покрытия на трубы устанавливаются и жестко крепятся опорные центрирующие кольца. Затем труба с опорными центрирующими кольцами вводится в полиэтиленовую оболочку с расчетной толщиной стенки 8-15,6 мм. Таким образом, мы получаем конструкцию «труба в трубе». После этого пространство между оболочкой и трубой заполняется бетоном.
Следует отметить, что при поперечных подвижках трубопровода новый вид балластного покрытия имеет достаточный запас прочности конструкции и обтекаемую гладкую поверхность (за счет полиэтиленовой оболочки), перемещается практически без изменения своего пространственного положения относительно трубы, сохраняя балластирующую способность и препятствуя всплытию трубопровода.
Данный способ балластировки труб может применяется не только для морских трубопроводов , но и для трубопроводов, предназначенных для прокладки в водонасыщенных грунтах (болотах, поймах рек и т.д.).
Помимо самого балластного покрытия на МТЗК были разработаны варианты изоляции сварных стыков трубопровода путем установки муфт с последующей заливкой межтрубного пространства цементно-песчаным раствором или асфальтом, а также вариант заполнения межтрубного пространства после сварки и изоляции стыка бетонными полукольцами с закреплением их сваркой и установкой сверху термоусаживающейся муфты.
Способ обетонирования труб, разработанный на МТЗК, позволяет также проводить балластировку теплоизолированных труб с установкой системы подогрева трубы на основе СКИН-СИСТЕМЫ другим нашим партнером - ООО «Специальные Системы и Технологии» (ССТ), что невозможно при «классическом» методе балластировки. Подобные трубы могут найти широкое применение при прокладке нефтепроводов в прибрежной (шельфовой) зоне северных районов России.
На ОАО МТЗК подготовлены к производству трубы для подводной прокладки и прокладки в водонасыщенных грунтах с любым видом современного заводского антикоррозионного покрытия (2-х и 3-хслойным полиэтиленовым или полипропиленовым, однослойным эпоксидным, тепловым пенополиуретановым) с балластным цементно-песчаным покрытием в прочной полиэтиленовой оболочке.
Необходимо заметить, что трубы с наружным эпоксидным, тепловым пенополиуретановым и балластным покрытиями с установленной системой подогрева труб на основе СКИН-СИСТЕМЫ (производства ССТ) специально разработаны специалистами ЗАО «Мосфлоулайн» совместно с ОАО МТЗК для условий арктического шельфа, при этом температура носителя может достигать +110°С и выше.
В настоящее время совместно с ООО «Институт «Шельф» (г. Симферополь) и проектными институтами России уже проведены обсчеты 11-ти диаметров стальной трубы с балластным покрытием (0820, 0530 и др.) (см. таблицу 1); подготовлены и согласовываются технические условия.
Фирмы «Det Norske Veritas» (DNV) и «Germanischer Lloyd» (GL) согласилась принять участие в подготовке международной сертификации по соответствию нового типа балластного покрытия стандартам «Offshore Standart DNV-OS-F101 Sabmarine Pipeline Systems» и «GL Rules Subsea Pipeliness and Risers», провести технический аудит и сертификацию выпускаемой изолированной балластной стальной трубы.
По результатам аудита «Germanischer Lloyd» в ноябре 2005 года выдал ОАО МТЗК Сертификат Квалификации Производителя (МСС) и, тем самым, подтвердил способность ОАО МТЗК к производству труб с балластным покрытием для подводной прокладки магистральных нефтегазопроводов в соответствии с требованиями применяемых технических условий и с положениями Правил «Germanischer Lloyd» для подводных трубопроводов и стояков «GL Ruies for Sub-sea Pipelines and Risers». Ведутся переговоры с российскими организациями, занимающимися разработкой морских шельфов, проектными и научными организациями, трубными заводами и строительными организациями о внедрении нового типа балластного покрытия в области строительства подводных трубопроводов в морских акваториях и болотистых районах Севера России и Каспийского моря.
С июня 2005 года на ОАО МТЗК проводится балластировка стальных труб 0 820 х 20,5 мм для строящегося нефтепровода длиной 45 км Варандейского терминала в Баренцевом море. Контроль над выполнением заказа ведет «Germanischer Lloyd».
На комбинате для выполнения этого заказа было создано 2 участка (летний и зимний) по балластировке стальных труб, где отработана технология балластировки и начато промышленное производство балластных труб.
В настоящее время ведется работа по повышению производительности оборудования с учетом перспективы получения новых заказов и их выполнения.
Проводится также большая работа по изучению свойств трубы с балластным покрытием, в частности испытания образцов труб с балластным покрытием на сжатие и сдвиг балластного покрытия относительно тела трубы, сдвиг оболочки относительно бетона, а также разрабатываются и патентуется несколько вариантов заделки стыков труб с балластным покрытием.
Итак, новый способ обетонирования стальных труб позволяет решить следующие задачи:
равномерно распределить по длине трубы нагрузку утяжеления, что затруднительно при использовании различного типа навесных утяжелителей;
снизить толщину стенки стальной трубы;
значительно повысить срок жизни и экологическую безопасность эксплуатируемых газовых и нефтяных трубопроводов за счет дополнительной защиты полиэтиленовой оболочкой и бетоном, который одновременно является балластом;
отказаться от импорта балластных труб в Россию;
в случае необходимости обеспечить подогрев трубы с балластным покрытием;
проводить балластировку фасонных частей трубопроводов (гнутых отводов, переходов и т.д.).
Продолжается работа по требованию заказчиков по увеличению удельного веса балластной смеси, проводятся испытания стальной трубы с балластным покрытием на сдавливание и на сдвиг стальной трубы по отношению к балласту и полиэтиленовой оболочке. Получаемые результаты подчеркивают надежность разработанной конструкции и ее перспективу.
Таблица 1
Примеры прорабатываемых ОАО МТЗК заказов на балластное покрытие стальных труб
№№ | Диаметр, мм | Толщина стенки, мм | Толщина балласта, мм | Назначение |
1 | 219,1 | 12,7 | 42,35 | Каспийское море |
2 | 273,1 | 14,3 | 57,15 | Каспийское море |
3 | 323,8 | 14,3 | 56,1 | Каспийское море |
4 | 323,9 | 12,7 | 46,2 | Каспийское море |
5 | 355,6 | 15,9 | 40,2 | Каспийское море |
6 | 426 | 8 | 58,2 | Каспийское море |