Конструирование радиоэлектронной геофизической аппаратуры
Вид материала | Документы |
Содержание13.1. механические операции [3] 13.2. формирование токопроводящих элементов печатных плат [3, 4] |
- Конструирование радиоэлектронной геофизической аппаратуры, 376.83kb.
- Конструирование радиоэлектронной геофизической аппаратуры, 346.73kb.
- Конструирование радиоэлектронной геофизической аппаратуры, 299.74kb.
- Конструирование радиоэлектронной геофизической аппаратуры, 446.09kb.
- Конструирование радиоэлектронной геофизической аппаратуры, 385.32kb.
- Конструирование радиоэлектронной геофизической аппаратуры, 402.82kb.
- Конструирование радиоэлектронной геофизической аппаратуры, 487.83kb.
- Конструирование радиоэлектронной геофизической аппаратуры, 301.73kb.
- Конструирование радиоэлектронной геофизической аппаратуры, 330.88kb.
- Конструирование радиоэлектронной геофизической аппаратуры, 221.3kb.
КОНСТРУИРОВАНИЕ РАДИОЭЛЕКТРОННОЙ ГЕОФИЗИЧЕСКОЙ АППАРАТУРЫ
Development and creation of geophysical instruments. Technology of making of the printed boards
Тема 13: ТЕХНОЛОГИЧЕСКИЕ ОПЕРАЦИИ ИЗГОТОВЛЕНИЯ ПП
Боги прощают нам наши ошибки, люди – нет.
Наблюдение древних греков.
Хотел бы я посмотреть на греческих богов после их знакомства с современными творениями рук человеческих и методами ремонта аппаратуры в поле кулаком и матом. От их снисходительности и следа не останется.
Владимир Кузьмин. Новосибирский геофизик Уральской школы.
Содержание:
- Механические операции. Механическая обработка ПП. Подготовительные операции.
- Формирование токопроводящих элементов ПП. Технология металлизации. Активация поверхностей диэлектриков. Гальваническая металлизация. Формирование рисунка печатных плат. Травление меди с пробельных мест. Особенности изготовления МПП. Покрытия и маски для наружных слоев ПП. Контроль и испытания плат.
Основу модулей первого уровня РЭА составляет оригинальная деталь - коммутационная подложка, на которой устанавливаются компоненты и которая обеспечивает электрическое соединение между компонентами в соответствии с электрической схемой. В общем случае подложка представляет собой диэлектрическое основание и рисунок в виде металлических пленочных проводников, называемых печатными. Отсюда распространенное название таких плат - печатные платы (ПП). Различают следующие типы ПП: односторонние, двусторонние, многослойные и гибкие.
13.1. механические операции [3]
Механическая обработка ПП включает раскрой листового материала на полосы, получение из них заготовок, выполнение фиксирующих, технологических, переходных и монтажных отверстий, получение чистового контура ПП. Размеры заготовок определяются требованиями чертежа и наличием по всему периметру технологического поля, на котором выполняются фиксирующие отверстия для базирования деталей в процессе изготовления и тестовые элементы. При прессовании МПП на технологическом поле образуется зона некачественной пропрессовки пакета, которая удаляется при обработке контура. Ширина технологического поля не превышает 10 мм для ОПП и ДПП и 20-30 мм для МПП. Малогабаритные платы размером до 100 мм размещают на групповой заготовке площадью не менее 0,05 м2 с расстоянием 5-10 мм между ними.
Выбор метода получения заготовок определяется типом производства. В крупносерийном и массовом производстве раскрой листового материала осуществляют штамповкой на кривошипных или эксцентриковых прессах с одновременной пробивкой фиксирующих отверстий на технологическом поле. Для уменьшения вероятности образования трещин, сколов, расслоений и повышения точности обрабатываемый материал прижимают к плоскости матрицы фольгированной стороной. Вырубку в штампах производят как в холодном, так и в нагретом до 80-100 °С состоянии материала. Прогревают материал при получения сложного контура ПП и его толщине свыше 2 мм.
Заготовки ПП в единичном и мелкосерийном производстве получают разрезкой на одно- и многоножевых роликовых или гильотинных ножницах. Применяемые ножи должны быть установлены параллельно друг другу с минимальным зазором 0,01-0,03 мм по всей длине реза.
Фиксирующие отверстия диаметром 4-6 мм выполняют штамповкой или сверлением с высокой точностью (0,01-0,05 мм). Для сверления используют универсальные станки, в которых точность достигается применением кондукторов, или специальное полуавтоматическое оборудование, которое в одном цикле с обработкой пакета заготовок предусматривает пневматическую установку штифтов, фиксирующих пакет. Сверление ведут спиральными сверлами из быстрорежущей стали или твердых сплавов при скорости 30-50 м/мин и подаче 0,03-0,07 мм/об. Биение сверла при обработке не должно превышать 0,03 мм. Повышение точности сверления фиксирующих отверстий достигается их развертыванием при скорости 10-30 м/мин и ручной подаче инструмента.
Аналогичными методами выполняют и технологические отверстия, которые используют для предотвращения смещения заготовок слоев МПП в процессе прессования, но к точности их обработки не предъявляются такие жесткие требования, как к точности обработки фиксирующих отверстий, по которым идет совмещение заготовок с фотошаблонами и отдельных слоев в пакете.
Монтажные и переходные отверстия получают также штамповкой и сверлением. Пробивку отверстий на универсальных или специальных штампах применяют в тех случаях, когда отверстие в дальнейшем не подвергается металлизации и его диаметр не менее 1 мм. При пробивке отверстий в односторонних фольгированных диэлектриках применяют штампы с увеличенным зазором между пуансоном и матрицей, обеспечивающим затягивание фольги в отверстие, чем достигается его частичная металлизация. Максимальная глубина затягивания фольги в отверстия диаметром 1-1,3 мм достигается при технологическом зазоре 0,4+0,2 мм. Если плата имеет высокую плотность монтажа, большое количество отверстий и малый шаг координатной сетки, то применяют последовательную пробивку на нескольких штампах. Применение универсальных штампов, в которых необходимое количество отдельных пуансонов набирается в специальном трафарете, делает процесс штамповки экономичным в условиях мелкосерийного производства.
Металлизированные монтажные и переходные отверстия обрабатывают с высокой точностью на специализированных одно- и многошпиндельных сверлильных станках с ЧПУ. Эти станки имеют координатный стол с автоматической системой позиционирования, сверлильные шпиндели с бесступенчатым регулированием скорости и систему ЧПУ позиционного типа. В зависимости от размеров обрабатываемых плат и требуемой производительности станки можно оснастить различным числом шпиндельных головок. Каждый шпиндель имеет независимый привод скоростей, в связи с чем за одну установку и по одной общей программе могут обрабатываться отверстия разных диаметров.
Для обработки металлизированных отверстий используются специальные спиральные сверла из металлокерамических твердых сплавов. Их стойкость при обработке фольгированных стеклотекстолитов составляет 3000-7000 тыс. отверстий, при наличии лакового покрытия на ПП стойкость инструмента уменьшается в 2—3 раза. Номинальное значение диаметра сверла следует выбирать исходя из зависимости
dсв = d + 0.7(1+2),
где d - номинальный диаметр отверстия, мм; 1 - допуск на этот диаметр, мм; 2 - допустимое уменьшение диаметра обрабатываемого отверстия после охлаждения слоистых пластиков, мм.
Повышение температуры в зоне обработки при сверлении слоистых пластиков приводит к наволакиванию размягченной смолы на кромки контактных площадок, препятствующему последующей металлизации отверстий. Для устранения этого недостатка предлагается ряд усовершенствований: применение охлаждающих агентов, не содержащих смазок (вода, водяной туман, очищенный сжатый воздух и т. п.); двойное сверление; наложение на поверхность платы алюминиевых листов; разработка сверл с дополнительными режущими кромками, направленными в сторону, противоположную основным, и т. п. Однако все перечисленные способы оказываются малоэффективными в условиях массового производства. Предлагаемый фирмой IBM (США) процесс лазерного фрезерования хотя и устраняет наволакивание смолы на торцы контактных площадок, но не исключает ее стеклование на поверхности стенок отверстия. Наиболее эффективным средством устранения наволакивания признана последующая гидроабразивная очистка.
Чистовой контур ПП получают штамповкой, отрезкой на гильотинных ножницах или на специальных станках с прецизионными алмазными пилами, фрезерованием. Повышение производительности фрезерных работ достигается групповой обработкой пакета ПП толщиной 10-30 мм. Для исключения повреждения их поверхностей между отдельными заготовками прокладывают картон, а пакет помещают между прокладками из листового гетинакса.
В последнее время для чистовой обработки все большее распространение получают контурно-фрезерные многошпиндельные станки с ЧПУ, которые обеспечивают хорошее качество кромок ПП и точность размеров в пределах ±0,025 мм, позволяют обрабатывать внешние и внутренние контуры за одно крепление, характеризуются высокой производительностью (1500-2000 плат/ч) и надежностью. Они снабжены устройствами для автоматической смены фрез, защитными скафандрами для ограждения оператора от шума, пыли и стружки при обработке, бесступенчатым регулированием частоты вращения инструмента в диапазоне 15-60 тыс/мин.
Подготовительные операции предназначены для обеспечения качества при выполнении основных процессов формирования элементов печатного монтажа. Они включают очистку исходных материалов и монтажных отверстий от окислов, жировых пятен, смазки, пленок и других загрязнений, активирование поверхностей проводящего рисунка, специальную обработку диэлектриков, а также контроль качества подготовки. В зависимости от характера и степени загрязнений очистку (активирование) проводят механическими, химическими, электрохимическими, плазменными методами и их сочетанием.
Механическая подготовка в условиях мелкосерийного производства осуществляется вручную смесью венской извести и шлиф-порошка под струей воды. Экономически оправдано применение механизированных и автоматических конвейерных линий в условиях крупносерийного и массового производства. Инструментом на этих линиях служат абразивные круги, капроновые или нейлоновые щетки, на которые подается абразивная суспензия. В некоторых зарубежных установках для зачистки используются круги из нетканого нейлона, насыщенные мелкодисперсным порошком карборунда или алунда, которые для устранения перегрева обильно смачивают водой. Для очистки монтажных отверстий от наволакивания смолы и других загрязнений широко применяются установки гидроабразивной обработки, в которых платы со скоростью 0,2-0,4 м/мин проходят рабочую, промывную и сушильную камеры установки. В рабочей камере через инжекторные форсунки, качающиеся вокруг оси с частотой 35-100 циклов в минуту, под давлением 0,5-0,7 МПа подается пульпа, состоящая из абразивного порошка и воды. Подача воды под давлением 1-1,2 МПа обеспечивает тщательную промывку отверстий в следующей камере. Сушка заготовок осуществляется сжатым воздухом.
Химическая и электрохимическая подготовка поверхности проводится в ваннах с различными растворами при покачивании плат и последующей их промывкой, а механизированная - на автооператорных линиях модульного типа по заданной программе.
Высокое качество и производительность обеспечивает плазменная очистка ПП, которая устраняет использование токсичных кислот, щелочей и их вредное воздействие на обслуживающий персонал, материалы обработки и окружающую среду. Установки плазмохимической обработки состоят из реактора, мощного ВЧ-генератора, устройства управления и регулирования процессов, вакуумного насоса. Плазмообразующий газ, состоящий из кислорода (70%) и тетрафторметана (30%), подается в камеру со скоростью 600-900 см3/мин. Мощность ВЧ-генератора регулируется в диапазоне 0-4000 Вт, а частота составляет 13,56 МГц. На установке одновременно обрабатывается до 15 плат размером 45х60 см, каждая из которых имеет до 3000 отверстий. Длительность операции очистки пакета— 10... 16 мин.
Специальная обработка диэлектрического материала при изготовлении МПП или ПП аддитивными методами заключается в его подтравливании и придании шероховатости для увеличения прочности сцепления с металлизацией. Подтравливание диэлектрика проводится последовательной обработкой сначала в серной кислоте, а затем в плавиковой или в их смеси (5:1) при температуре 50-60°С. Серная кислота образует с эпоксидной смолой сложный, растворимый в воде, сульфированный полимер, а обнажившееся стекловолокно вступает в реакцию с плавиковой кислотой. Скорость травления составляет 40-80 мкм/мин. После обработки платы нейтрализуют в растворе щелочей и тщательно промывают.
Увеличение шероховатости диэлектрических поверхностей и клеевых композиций достигается механической (гидроабразивной) или химической обработкой.
Контроль качества подготовки металлических поверхностей заготовок ПП оценивают по полноте смачивания их водой. Состояние диэлектрических поверхностей проверяют микроскопическими исследованиями, измерением высоты микронеровностей, проведением пробной металлизации и оценкой ее прочности сцепления с основанием. Объективным показателем качества является также проверка сопротивления изоляции после пребывания в камере влажности.
К подготовительным операциям относится упаковка ПП, которая производится на автоматическом оборудовании. Заготовки со скоростью 120-240 шт./ч помещаются между слоями полиэтиленовой пленки, которая при помощи тепловой обработки заваривается с четырех сторон и образует герметичную упаковку.
13.2. формирование токопроводящих элементов печатных плат [3, 4]
Технология металлизации. Формирование токопроводящих элементов ПП осуществляется двумя основными методами: химическим (бестоковым) и электрохимическим. Химическая металлизация используется в качестве основного слоя при изготовлении плат аддитивным методом, при этом после соответствующей активации на них осаждают химическим способом проводящий слой толщиной до 3 мкм, а затем его усиливают гальваническим способом до необходимой толщины, так как гальваническое осаждение значительно дешевле. В основном этот метод применяют для осаждения меди и никеля в межслойных переходах ПП
Процесс химической металлизации основан на окислительно-восстановительной реакции ионов металла из его соли в определенной среде, при которой необходимые для восстановления катионов металла электроны получают в результате окисления специальных веществ, называемых восстановителями.
Для создания межслойных переходов в ПП и для изготовления проводящего рисунка плат используют, как правило, восстановительную ванну для меднения в одном из растворов, приведенных в таблице.
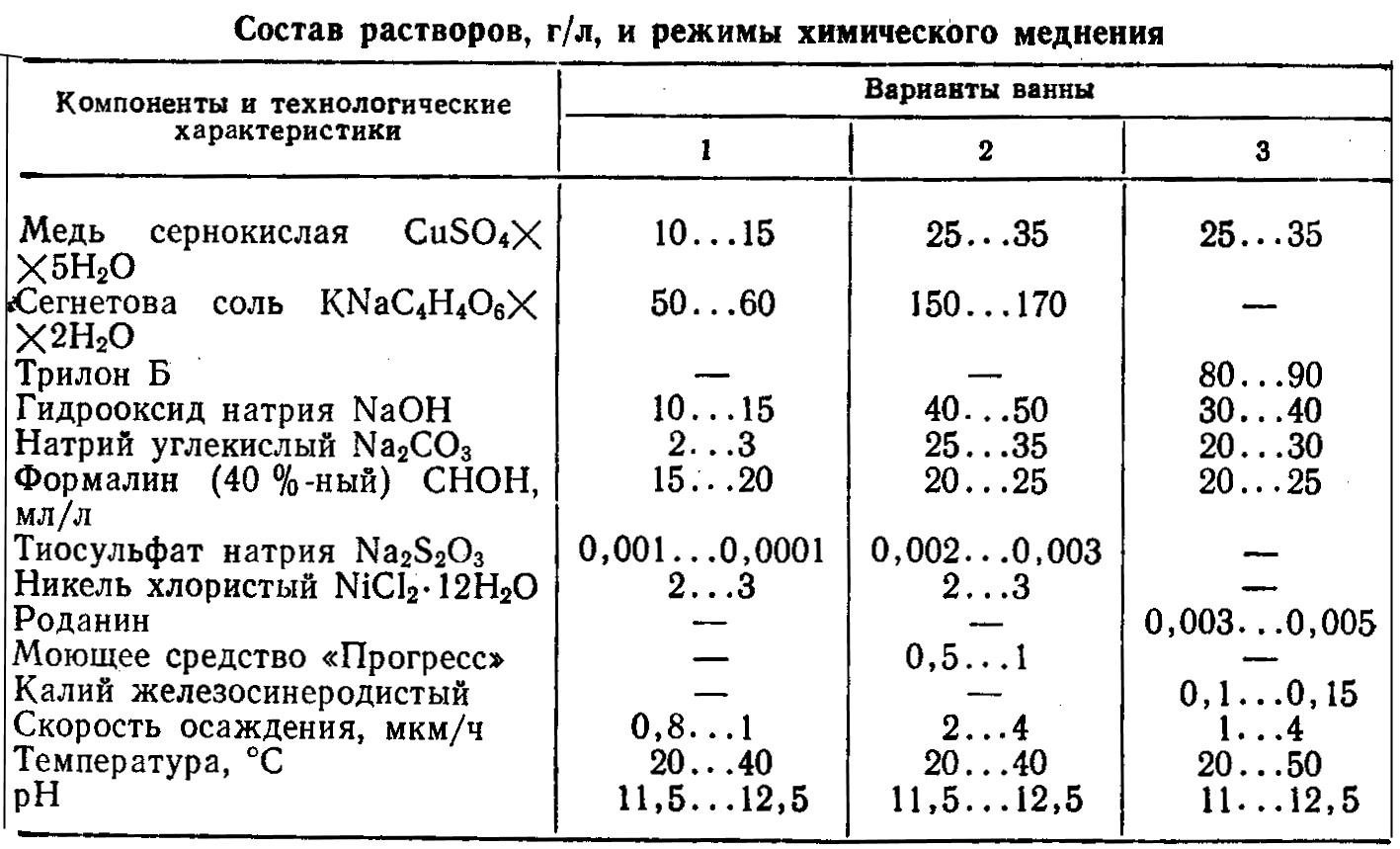
Разбавленные растворы (1) характеризуются более высокой стабильностью, чем концентрированные (2 и 3), но в них выделение меди происходит с низкой скоростью. При температуре ванны в 35-40 °С получают за 30 мин слой меди толщиной 0,5 мкм. Высокопроизводительные восстановительные ванны для меднения позволяют при температуре примерно 50 °С осадить слой в 25 мкм в течение 4 ч. Для облегчения удаления водорода, выделяющегося в процессе меднения, в растворы вводят поверхностно-активные вещества (моющее средство), а процесс ведется с плавным покачиванием плат (8-10 колеб./мин при амплитуде 50-100 мм).
В последнее время рекомендуют применять для получения металлического проводящего слоя также ванны для химического никелирования, которые являются более стабильными и простыми в управлении. В ванны добавляют стабилизаторы, способствующие тому, что реакции происходят только на нужной поверхности, а не в растворе. При температуре 52-54 °С, рН=5÷6 и соотношении площади поверхности и объема ванны 1 дм2/л за 7-10 мин образуется слой никеля толщиной в 1 мкм.
Активация поверхностей диэлектриков. На диэлектриках реакция восстановления протекает при наличии на их поверхности каталитически активного слоя. Для придания диэлектрику способности к металлизации производят двухступенчатую операцию сенсибилизации и активирования.
Сенсибилизация — это процесс создания на поверхности диэлектрика пленки ионов двухвалентного олова, которые впоследствии обеспечат восстановление ионов активатора металлизации. ПП хорошо очищают в специальных растворах, особое внимание обращают на обезжиривание. Если печатные платы имеют отверстия особо малых диаметров, то их необходимо очищать в ультразвуковых ваннах. Затем платы опускают на 3-5 мин в солянокислый раствор дихлорида олова (SnCl2 – 5-10 г/л, HCl – 20-40 г/л). Чтобы предотвратить разрушение раствора в результате гидролиза, необходимо поддерживать высокую концентрацию кислоты. Постепенное разбавление сенсибилизирующей ванны водой, остающейся на платах после промывки, предотвращают, предварительно погружая заготовку в 10%-ную HCl. Время работы сенсибилизирующей ванны можно существенно повысить, добавляя в нее гранулы олова. После сенсибилизации платы промывают в холодной воде. При этом на их поверхности образуется нерастворимая и несмываемая гидроокись олова:
SnCl2 + 2 H2O Sn(OH)2 + 2 HCl.
Активирование заключается в том, что на поверхности, сенсибилизированной двухвалентным оловом, происходит реакция восстановления ионов каталитического металла. Обработку проводят в растворах благородных металлов, преимущественно палладия (PdCl2 – 0,5-2 г/л, НС1 – 10-20 мл/л) в течение 3-5 мин. Адсорбированные на поверхности плат ионы олова восстанавливают ионы палладия:
Sn2+ + Pd2+ Pd + Sn4+.
Атомы палладия являются высокоактивным катализатором для химической металлизации на поверхности диэлектрика. После активации необходимо хорошо промыть заготовки, чтобы не загрязнять ванны химической металлизации. Управление ванной (концентрацией реактивов, величиной рН), чистота ванны (содержание и виды примесей) и степень предварительной очистки плат определяют качество покрытия поверхности палладием, а вместе, с тем качество последующей химической металлизации.
Применяется также одноступенчатая активация в коллоидном растворе, который содержит НСl, катионы Sn2+, Sn4+ и Pd в коллоидной форме (0,1 - 1 г/л). Одноступенчатую активацию проводят при комнатной температуре. Ванну не подвергают регенерации, а эксплуатируют до полной выработки, после чего составляют заново. Для покрытия 100 м2 поверхности необходимо примерно 2 г палладия. При одноступенчатой активации в ванне происходят те же процессы, что и при двухступенчатой активации. При погружении ПП в ванну зародыши палладия, как и катионы Sn2+ и Sn4+, адсорбируются одновременно. При последующей промывке ПП в результате реакции воды с ионами Sn получаются гидроксил-хлориды и четырехвалентные соединения олова, при этом продукты гидролиза удаляются, а палладий остается адсорбированным.
Основными проблемами химической металлизации являются низкая производительность, сложность процесса, использование дорогостоящих материалов. Для устранения указанных недостатков разрабатываются методы беспалладиевой металлизации, например термохимический. Процесс проводится в растворе (г/л): кальций фосфорноватисто-кислый 130-170, медь сернокислая пятиводная 200-250, гипофосфат аммония 6-10, аммиак (25%) 200-300 мл/л. После обработки платы выдерживаются в термошкафу при 100-150°С в течение 8-10 мин. В результате термического разложения комплексной соли гипофосфита меди на поверхности ПП и в монтажных отверстиях образуется электропроводящее покрытие, которое служит основой для электрохимического наращивания металла.
Конечным продуктом химической металлизации является готовая печатная плата или промежуточная заготовка, которая затем подвергается гальваническому наращиванию. В этом случае безукоризненная химическая металлизация является основой для хорошего качества гальванического покрытия. Во время гальванического процесса наращиваются не только гладкие поверхности химически осажденного слоя металла, но и все выступы, неровности и прочие дефекты. Каждая неровность, вызванная сверлением или травлением, покрывается без малейшего эффекта выравнивания. Так как гальванический слой растет преимущественно вертикально, возникают причудливые образования, которые могут затруднить установку элементов на печатные платы и пайку. Причиной появления пор при химической металлизации могут быть остатки химических растворов очистки и травления в микротрещинах диэлектрика, пористые образования на стенках отверстий. Они являются продуктами распада материала основы, образующимися при очистке и травлении, или следствием грубой механической обработки.