3. конструкционные материалы химического машиностроения
Вид материала | Документы |
- Титан губчатый гост 17746-79 ту 48-10-75-82, 32.3kb.
- Влияние факторов космического пространства и орбитального полета на состояние систем, 301.13kb.
- Вопросы по ткм, 45.01kb.
- Методические указания по выполнению контрольных работ по дисциплине «Автомобильные, 235.66kb.
- Ежеквартальныйотче т открытое акционерное общество "Уральский завод химического машиностроения", 2166.68kb.
- Россия, 193318,Санкт-Петербург Ул. Ворошилова д. 6 Тел. (921) 882-39-51, 346.6kb.
- Тематический план лекций по кафедре терапевтической стоматологии для курса пропедевтики, 48.29kb.
- 1 Направление «Эксплуатация машин и оборудований полиграфии, производство изделий, 104.11kb.
- О проведении IX всероссийской научно-практической конференции, 88.11kb.
- Конструкционные и функциональные материалы – основа нтп, 147.73kb.
3. КОНСТРУКЦИОННЫЕ МАТЕРИАЛЫ ХИМИЧЕСКОГО МАШИНОСТРОЕНИЯ.
Данный раздел традиционно обязателен для курсов «Специальное технологическое оборудование», читаемых инженерам-химикам. Причины очевидны. Поскольку оборудование изготавливают из определённых материалов, постольку свойства этих последних определяют возможности техники.
Наверное, едва ли найдётся иная область машиностроения, потребляющая такое разнообразие конструкционных материалов, и при этом предъявляющая к ним столь разнообразные, противоречивые и жёсткие требования, - как химическое машиностроение. Здесь: высокая прочность - и пластичность; высокая теплопроводность - и теплоизоляционные свойства; возможность применения различных методов (механических, термических, электрических, химических, диффузионых, иррадиационных) обработки и формования - и высокая устойчивость химической структуры материалов в процессах обработки. Наиболее жёсткие требования предъявляются к коррозионной стойкости материалов в плане не только обеспечения надёжности и долговечности самого оборудования, но и предупреждении негативного действия продуктов коррозии на качество продукции.
Химическое машиностроение использует очень многие виды конструкционных материалов.
1. Металлы группы железа и их сплавы между собой и с другими элементами.
2. Медь и её сплавы.
3. Алюминий и его сплавы.
4. Титан, тантал, ниобий, цирконий, вольфрам и их сплавы.
5. Стекло, фарфор, полиоксидные керамики.
6. Полимеризационные пластмассы, каучуки и резины, углепластики.
7. Композиционные, наполненные и тканые материалы
3.1. ЖЕЛЕЗО И ЕГО СПЛАВЫ
Железо – двадцать шестой элемент Периодической Системы; 4 период; IV ряд; VIII группа. Электронная формула атома 1s22s22p63s23p63d64s2. Является d-элементом с неполным заполнением подуровня.
Довольно твёрдый серебристо-белый металл. Плотность 7860 кг/м3. Существует в трёх аллотропных формах: α-
железо; γ-железо; δ-железо.
Форма Название Область устойчивости Кристаллическая Магнитные
ОС решётка свойства
α-железо феррит <910 ОЦК магнитен
γ-железо аустенит 910…1401 ГЦК немагнитен
δ-железо мартенсит > 1401 ОЦК магнитен
Железо и его сплавы – самый важный класс конструкционных материалов всей техники.
Чистое железо (равно как некоторые сорта отожжённых низкоуглеродистых сталей) как конструкционный материал используется только в электротехнических изделиях – и в соответствующих агрегатах химической техники.
В качестве конструкционных материалов для основных узлов – в том числе, контактирующих со средой, - применяются железоуглеродные сплавы: чугуны и углеродистые стали, а также стали с добавками иных металлов – легированные. Кроме того, определённое применение в не контактирующих со средой узлах находят железокремнийалюми-
нийуглеродные сплавы – ферросилиций; силаль, сихромаль.
3.1.1. ЧУГУНЫ.
Железоуглеродные сплавы с массовой долей углерода от 2,03 до 5,7 %. Получают в результате доменного процесса из железной руды. Чугуны, содержащие менее 4,25 % углерода, называют доэвтектическими; свыше 4,25 % углерода, называют заэвтектическими
Представляют собой многофазную гетерогенную систему, включающую твёрдый раствор β- и γ-карбидов железа (мартенсит и аустенит) в железе и коллоидный углерод.
По плотности и теплоёмкости теплоёмкости чугуны почти не отличаются от сталей. Как правило, имеют большую теплопроводность – (45…93) Вт/м.К. Высокоферромагнитны.
Химическая стойкость чугунов в водных средах, особенно кислых, невысока: соответствует уровню: «ограниченно стойкий-нестойкий».
Достоинство чугунов как конструкционных материалов в том, что они хорошо льются, а также поддаются обработке резанием и шлифованием – каковые методы доминируют в изготовлении изделий из чугуна. Благодаря этому, на чугунном оборудовании формируют гладкие поверхности с хорошим сопряжением профилей. Данное качество позволяет наносить на чугунные аппараты разнообразные устойчивые защитные покрытия; в первую очередь – эмалевые.
Наличие значительного количества свободного коллоидного углерода предопределяет основные недостатки чугунов – хрупкость и несвариваемость.
Из чугуна изготавливают корпуса трубопроводной арматуры; сосудов и реакторов-котлов вместимостью от 0,01 до 2,0 м3, а также разнообразные детали и узлы механических агрегатов (стойки, станины, рамы, узлы редукторов и т.д).
Чугунные аппараты используют в качестве сульфураторов и котлов для щелочного плавления и тиирования/осернения.
Наиболее широко в производствах БАВ применяются эмалированные чугунные аппараты и сосуды. Нужно отметить, что (вследствие применения литьевой технологии изготовления) эмалевые покрытия на чугуне держатся лучше, чем на стали.
Хрупкость чугуна предопределяет то, что стенки сосудов приходится делать толстыми (не менее 18 мм). Поэтому чугунная аппаратура всегда значительно тяжелее стальной или титановой; при этом она характеризуется большой тепловой инерционностью и низкими коэффициентами теплопередачи. Несвариваемость чугуна обусловливает к тому же то, что рубашки чугунных аппаратов – съёмные, крепятся к дополнительному фланцу на корпусе; следовательно, поверхность теплообмена в чугунных аппаратах существенно меньше, нежели в иных аппаратах той же вместимости. Чугунные аппараты малопригодны для ведения высокоэнергетичных процессов. В настоящее время использование чугуна в химическом машиностроении неуклонно сокращается.
3.1.2. УГЛЕРОДИСТЫЕ СТАЛИ.
Железоуглеродные сплавы с массовой долей углерода не более 2,03 %. Получают в результате конвертерных процессов из чугуна или непосредственно из железной руды.
Представляют собой многофазную гетерогенную систему, включающую твёрдый раствор α-, β-, γ- и δ-карбидов железа (феррит, цементит, мартенсит и аустенит) в железе. Свободный коллоидный углерод в сталях практически отсутствует. Как и чугуны – ферромагнитны.
Маркировка углеродистых сталей включает: аббревиатуру «Ст»; цифровое указание массовой доли углерода в десятых или сотых долях %; буквенное обозначение технологии удаления кислорода/раскисления (Сп –спокойная; Кип - кипящая).
Пример маркировки:
Ст10 Сп
| | |
| | |_____________________________ Спокойная (<0,005% О2)
| |__________________________________углерод– 0,10 %
|__________________________________ Сталь
В сталях жёстко ограничивают содержание серы, вызывающей хладноломкость (<0,02 %) и фосфора, вызывающего красноломкость (<0,03 %).
Особенности состава и физико-химической структуры предопределяют высокие пластические и прочностные и технологические характеристики сталей. К ним хорошо применимы все методы механической, термической и оптической обработки, в т.ч., методы порошковой металлургии.
Химическая стойкость углеродистых сталей в водных и водно-органических средах, особенно кислых, также невысока: соответствует уровню: «ограниченно стойкий - нестойкий». Стали довольно устойчивы к щелочным и аммонийным средам; концентрированная серная кислота также пассивирует их. Органические кислоты, особенно муравьиная и уксусная, также корродируют углеродистые стали.
Углеродистые стали используют для изготовления всех видов и типов химического оборудования. Детали, предназначенные для контакта с агрессивными средами, подлежат антикоррозийной защите. В настоящее время использование углеродистых сталей в химическом машиностроении сокращается.
3.1.3. КОРРОЗИОННОСТОЙКИЕ СТАЛИ.
Низкая коррозионная стойкость углеродистых сталей привела к необходимости создания материалов с улучшенными свойствами. Основной способ улучшения свойств – введение в состав сплава т.н. легирующих добавок - компонентов, обеспечивающих повышение отдельных или сразу многих качеств сплава. Стали, содержащие такие добавки, называют легированными .
Для химического машиностроения наиболее важно улучшить антикоррозионные свойства. Соответственно, коррозионностойкие стали представляют важнейший класс легированных.
Наиболее сильным пассивирующим действием на стали обладают хром, никель, титан, ниобий и марганец. Как известно, стандартный потенциал реакции Fe0 → Fe2+ Uo = -0,44 В. Пассивирующее действие добавок начинает слабо проявляться при их содержании свыше 2 %. При содержании Cr (10…12) % происходит резкий скачок потенциала до 0,56 В (рисунок 2).
Помимо пассивации железа, легирующие элементы связывают свободный углерод в карбиды (например Cr7C3). Поэтому легированные стали как правило, являются гомогенными кристаллическими веществами. Основной тип кристаллической решётки – кубическая гранецентрированная - КГЦ.
| Потенциал реакции
| Fe0 → Fe2+ UO, В
1 -|
|
| * *
0,5-| *
|
| *
0 -| *
|
| *
-0.5 -|* * * * * * *
|________________________________________________________________
| | | | | | | | | | | | | | массовая доля хрома, %
0 1 2 3 4 5 6 7 8 9 10 11 12 13
Рисунок 2 Пассивирующее действие добавок хрома на окисление железа в стали
В соответствии с этим коррозионностойкие стали делят на три класса: низколегированные (НЛС), среднелегиро-
ванные (СЛС), высоколегированные (ВЛС) (таблица 1).
Таблица 1 – Классификация коррозионностойких сталей
Наименование | Массовая доля легирующих добавок, % |
Низколегированные | менее 2 |
Среднелегированные | свыше 2 до 10 |
Высоколегированные | свыше 10 до 60 |
Обозначение легирующих элементов: Х –хром; Н – никель; Т – титан; М – молибден; Г – марганец; Ю – алюминий; Ф - вольфрам; С – кремний; Д – медь; Б – ниобий; А – азот.
Маркировка легированных сталей включает буквенное обозначение элемента и цифровое указание его массовой доли в %. Массовая доля углерода в таких сталях не превышает 0,12 %; углерод буквой не обозначают.
Пример маркировки:
10Х18Н10Т
| | | |__________________________ титан - < 2%
| | |_____________________________ никель – 10 %
| |_________________________________ хром - 18 %
|__________________________________ углерод – 0,10 %
НЛС ферромагнитны; коррозионностойкие ВЛС, как правило, парамагнитны или диамагнитны. Плотность и теплоёмкость их несколько выше, чем у чугунов и углеродистых сталей – (7900…7980) кг/м3; теплопроводность значительно ниже – (8…20) Вт/(м.К). Легированные стали, как правило, отличаются большей прочностью, твёрдостью и вязкостью, чем углеродистые (кроме броневых) – 6-8 баллов по шкале Мооса. Поэтому они сложнее поддаются термической и механической обработке и хуже поддаются литью (за исключением некоторых марок). Сварка (ЛС свариваются друг с другом, углеродистыми сталями, другими железосодержащими сплавами) требует специальных условий – лазерная или аргонно-дуговая, - в противном случае в сварных швах разрушается структура сплава и теряется коррозионная стойкость.
Для химического машиностроения наиболее важны аустенитные ВЛС: хромоникельтитановые - типа 10Х18Н10Т; хромоникельмолибденовые - типа 10Х17Н14ТМ2; хромоникельмарганцевые - типа 20Х13Н4Г9. На них приходится порядка 70 % всего потребления коррозионностойких сталей. Стали этого класса отличаются высокой устойчивостью к различным твёрдым, жидким и газообразным неорганическим и органическим реагентам (в том числе к их комбинированному действию) при температурах от (- 100) до (300…500) ОС [в некоторых случаях – до 1200 ОС]. Стойкость их соответствует классам “совершенно стойкий – высокостойкий”. Наиболее опасны для нержавеющих сталей молекулярные галогены (F2; Cl2; Br2; J2 - особенно в присутствии воды); в органических средах, особенно апротонных, опасен лишь фтор.
Высоколегированные коррозионностойкие стали – самый важный класс конструкционных материалов для химического машиностроения. Их них изготавливают все детали и узлы химического, нефтяного и пищевого оборудования, контактирующие со средой - разнообразные сосуды; корпуса, мешалки, теплообменные и статические внутренние устройства реакторов-котлов; колонные аппараты; теплообменники всех конструкций; фильтры; корпуса и роторы центрифуг и жидкостных сепараторов; рабочие органы насосов, газодувок и компрессоров; трубы и трубные детали; рабочие части трубопроводной арматуры; защитные узлы для устройств КИПСА.
Высокая прочность ЛС позволяет существенно уменьшать массу оборудования при равных технических характеристиках.
3.2. НИКЕЛЬ, КОБАЛЬТ И ИХ СПЛАВЫ
Никель и кобальт – элементы подгруппы железа. По свойствам они сходны с железом, однако имеют и ряд существенных отличий. Плотность их (около 8900 кг/м3) существенно выше плотности железа, чугунов и сталей [(7700…7900) кг/м3]. Оба металла также прочнее и твёрже, чем железо. Оба отличаются меньшей химической активностью и большей коррозионной стойкостью; особо ценное их качество – довольно высокая стойкость к газовой коррозии. Кроме того, оба элемента и их соединения высокотоксичны. Оба металла также значительно дороже железа и его сплавов.
Основное их использование – антикоррозионные наружные покрытия на изделия из железа и углеродистых сталей, наносимые электрохимически. Кроме того, из никеля и кобальта изготовляют детали и узлы пар скольжения и уплотнений. Особое значение имеют сплавы никеля и кобальта с железом – инвар, коинвар, маллой, пермаллой, супермаллой. Эти сплавы имеют высокие магнитные свойства и применяются для изготовления магнитопроводов электромагнитных устройств.
3.3. МЕДЬ И ЕЁ СПЛАВЫ
Медь – двадцать девятый элемент Периодической Системы. Один из двух окрашенных металлов. Мягкий металл. Плотность 8910 кг/м3. Отличается высокой тепло- и электропроводностью; диамагнитна. Хорошо поддаётся термомеханической обработке, литью, пайке и сварке.
Стандартный потенциал основной реакции окисления меди U0 (Cu0
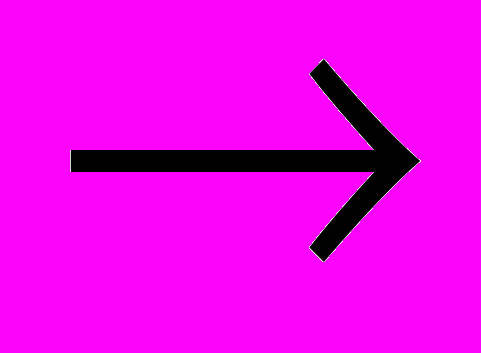
Медь как чистый металл в химическом машиностроении применяется для изготовления электроведущих деталей (провода, шины, электроды электрохимических реакторов); деталей и узлов пар скольжения и деталей уплотнений (вкладышей, гильз, колец, шайб) в аппаратуре высоких давлений и глубокого вакуума.
Большое значение имеют сплавы меди: латуни и бронзы.
Латуни. Сплавы меди, содержащие цинк (до 45 %). Кроме цинка, латуни легируют добавками Al, Mg, Si, Mn, Ni, Cr.
Бронзы. Любые сплавы меди, не содержащие цинка. Бронзы легируют добавками Sn, Al, Mg, Si, Mn, Ni, Cr, Ве.
Маркировка
Латуни. ЛАЖ 60-1-1 Бронзы. БрАЖН 10-4-4
| | | | | |____ (1…2) % Fe | | | | | | |____ (3,5…5,5) % Ni
| | | | |______(1…2) % Al | | | | | |______(3,5…5,5) % Fe
| | | |_________(59…61) % Cu | | | | |_________(9…11) % Al
| | |____________ железо | | | |____________ никель
| |_____________ алюминий | | |_____________ железо
|_______________ латунь | |_______________ алюминий
|__________________ бронза
Латуни и бронзы по коррозионной стойкости не уступают или превосходят медь (особенно по отношению к атмосферной коррозии). По механическим свойствам, как правило, превосходят медь. Наибольшей стойкостью отличаются алюминиево-бериллиевые бронзы. Применяются для изготовления труб, корпусов и внутренних деталей трубопроводной арматуры, уплотнительных деталей аппаратуры, теплообменных аппаратов, деталей КИПСА.
3.4. СВИНЕЦ
Восемьдесят второй элемент Периодической Системы. Мягкий белый металл. Плотность 11344 кг/м3. Свинец и все его соединения высокотоксичны. Стандартный потенциал основной реакции окисления свинца U0 (Pb0
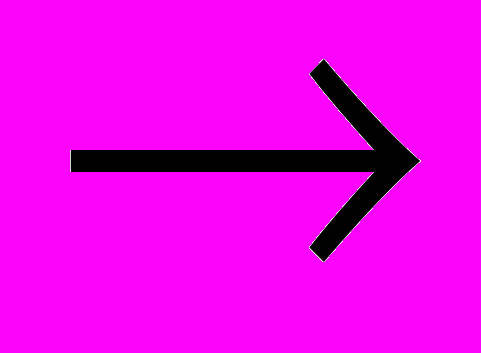
3.5. АЛЮМИНИЙ И ЕГО СПЛАВЫ
Тринадцатый элемент Периодической Системы. Самый распространённый из металлов – 7,4 % в земной коре; присутствует в виде оксидов, смешанных фосфатов и силикатов. [ Кристаллический оксид - Al2O3 – корунд – второй по твёрдости минерал после алмаза (9 баллов по шкале Мооса)]. Тип кристаллической решётки – ОГЦ. Мягкий белый пластичный лёгкий металл. Плотность ρ20=2702 кг/м3. Температура плавления ТПЛ = 660 0С. Отличается высокой теплопроводностью (λ =188 Вт/м.К) и электропроводностью [σ= (1,6…2,6).107 Сн/м). Получают электротермическими и электрохимическими методами, достигая высокой степени чистоты (до 99,999999 %). Алюминий и его соединения малотоксичны. Стандартный потенциал основной реакции окисления алюминия U0 (Al0
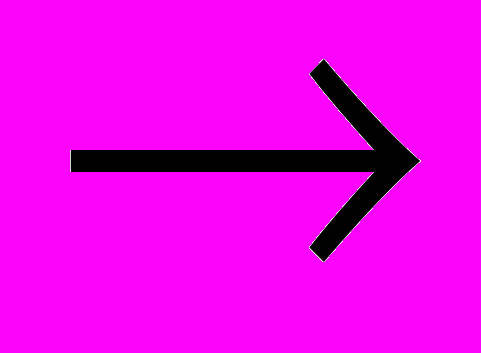
Достоинство алюминия – лёгкость; существенный недостаток – низкая прочность. В технике, в т.ч. – химическом машиностроении большое значение имеют сплавы с кремнием, медью, магнием, марганцем, хромом, железом –
силумины, дюралимины, магналины. Дюралюмины имеют высокие прочностные свойства, но низкую стойкость; изделия из них защищают плакированием чистым алюминием. Силумины отличаются хорошей стойкостью к окислительным нейтральным и кислым средам, а также к газовой коррозии. Магналины имеют наилучшие из сплавов алюминия свойства. Особенность всех сплавов алюминия – нестойкость к контактной электрохимической коррозии –
особенно в парах со сплавами меди и железа.
Таблица 2 – Сплавы на основе алюминия
Наименование | Марки | Массовые доли легирующих добавок, % | |||||
Si | Cu | Mn | Mg | Cr, Ti | Fe | ||
Алюминий | АВ, АД | <1,5 - в сумме | |||||
Дюралюмины | Д1-Д6 | - | 2…7 | 0,4…1,8 | 0,3…0,9 | - | - |
Силумины | АЛ1-АЛ7 | 0,8…13,0 | 0,2…4,5 | - | 0,5…13,0 | - | - |
Магналины | АМгМц, Амгб | - | - | <1 | 4,0…12,0 | 0,1 | <0,25 |
Алюминий и его сплавы применяют для изготовления реакторов, кристаллизаторов, сосудов, фильтров, теплооб
менников, дистилляционных и ректификационных аппаратов и труб, работающих под давлением до 0,6 МПа.
910>