3. конструкционные материалы химического машиностроения
Вид материала | Документы |
- Титан губчатый гост 17746-79 ту 48-10-75-82, 32.3kb.
- Влияние факторов космического пространства и орбитального полета на состояние систем, 301.13kb.
- Вопросы по ткм, 45.01kb.
- Методические указания по выполнению контрольных работ по дисциплине «Автомобильные, 235.66kb.
- Ежеквартальныйотче т открытое акционерное общество "Уральский завод химического машиностроения", 2166.68kb.
- Россия, 193318,Санкт-Петербург Ул. Ворошилова д. 6 Тел. (921) 882-39-51, 346.6kb.
- Тематический план лекций по кафедре терапевтической стоматологии для курса пропедевтики, 48.29kb.
- 1 Направление «Эксплуатация машин и оборудований полиграфии, производство изделий, 104.11kb.
- О проведении IX всероссийской научно-практической конференции, 88.11kb.
- Конструкционные и функциональные материалы – основа нтп, 147.73kb.
Каучуки – продукты полимеризации 2-R-1,3-бутадиенов [R= H (бутадиен); Cl (хлоропрен); Me(изорпрен)] или сополимеризации их с замещёнными этиленами (изобутен; акрилонитрил, стирол).
Принципиальная структурная особенность каучуков – сохранение в макромолекуле этиленовых фрагментов; кроме того, эта особенность даёт возможность синтеза стереорегулярных структур: все-транс (типа натурального
каучука) или все-цис (типа гуттаперчи)
(-СН2-СН=СR-СН2- )N - монополимеры
(-СН2-СН=СR-СН2- СН2- СR'- )N - сополимеры
Эластомеры – продукты вулканизации каучуков - реакции с серой и оксидами металлов при температурах (150…200) ОС.
Таблица 4 – Типы вулканизованных материалов
Класс продукта | Тип продукта | Массовая доля серы, % |
Эластомеры | Мягкая резина | 2…4 |
Полужёсткая резина | 12…20 | |
Эбонит | Жёсткая резина | 30…50 |
Специфичность структуры сообщает каучукам и эластомерам уникальную эластичность и упругость. Каучуки и резины обладают хорошей адгезией к металлам. Стойки к действию большинства неорганических реагентов, в т.ч., к окислителям – кроме галогенов и галогенангидридов. Также стойки к спиртам, карбоновым кислотам; нестойки к углеводородам, алкил- и арилгалогенидам. Диапазон рабочих температур от (-30) до (100…150) ОС.
Особое место в этом классе материалов занимают т.н. силиконовые каучуки - полидиалкилсилоксаны общей формулы [O-SiR2-O-]N. Кремнийорганические полимеры отличаются не только высокой прочностью и упругостью, но и уникальной, сопоставимой с фторопластами – химической стойкостью к действию почти всех агентов. Диапазон рабочих температур: от (-60) до (200…300) ОС.
Каучуки и резины в основном применяют для изготовления уплотнительных деталей оборудования, шлангов, труб, а также в качестве клеев и герметиков.
Важнейший аспект – использование в качестве защитных покрытий стальной аппаратуры: реакторов, сосудов, фильтров, центрифуг, труб. Защита резиновыми покрытиями называется гуммированием. Гуммируемые детали обкладываеют листами сырой резины и вулканизуют в среде острого пара или воздуха при температуре порядка 150 ОС. Гуммированное оборудование работоспособно при температурах до 100 ОС в неабразивных средах.
УГЛЕРОДНЫЕ (ГРАФИТОВЫЕ) МАТЕРИАЛЫ – УГЛЕПЛАСТЫ.
Из четырёх известных в настоящее время аллотропных форм углерода – сажи, фуллерена, графита и алмаза лишь графит нашёл широкое применение в химическом машиностроении.
Графит – основная форма существования углерода. Характеризуется sp2-гибридизованными связями. Структура – слоистая. Плотность 2265 кг/м3. Является одним из стандартных, базовых веществ химической термодинамики: HO=GO0. Теплоёмкость Ср=8,54 Дж/моль.К. Отличается уникальной тугоплавкостью: ТСУБЛ 3700 ОС. Как металлы, графит электропроводен; отличается также высокой (электронной) теплопроводностью: . 90 Вт/м.К. Уникальна также химическая стойкость графита – по существу. он разрушается только концентрированной серной кислотой и фтором. Недостаток графита – хрупкость. Поэтому в основном используют графитопласты – композиции графита с фенопластами (в основном – фаолитом и бакелитом)
Из графитопластов изготавливают корпуса и лопатки химических насосов; трубы; уплотнительные детали, детали пар скольжения; электроды и корпуса электролизёров; теплообменники для работы в среде паров галогенов и гидрогалогенидов.
КОРРОЗИЯ И АНТИКОРРОЗИОННАЯ ЗАЩИТА ХИМИЧЕСКОГО ОБОРУДОВАНИЯ
КОРРОЗИЯ
Коррозия – явление структурного разрушения конструкционных материалов и элементов технических систем под воздействием комплекса химических, биохимических, физических (электрических, деформационных, термичес-ких, вибрационных, радиационных) факторов окружающей среды – природной или техногенной.
(Очевидно, что явления преднамеренного разрушения к коррозии не относятся).
Коррозия – едва ли не единственное явление, которое в технике считается совершенноым злом, поскольку практически невозможно использовать его в созидательных целях.
Коррозия – явление многообразное и чрезвычайно сложное. Непременным и первостепенным фактором, вызывающим коррозию, являются многообразные химические процессы. Видов и механизмов коррозии чрезвычайно много; в данном курсе будут рассмотрены (увы, крайне поверхностно) только наиболее характерные для химической
аппаратуры.
Типичные виды коррозии
Следует отметить, что коррозия проявляется принципиально в двух формах.
1. Нарушение макроструктуры материала, приводящее к потере прочности.
Сюда можно отнести такие явления как набухание полимеров во многих органических средах; межкристаллитное растрескивание сплавов (в первую очередь, сталей), бетонов и иных микрокристаллических материалов; растрескивание слоистых материалов (пластиков, древесины); водородная хрупкость сталей, вызываемая насыщением сплава гидридами металлов.
Это вид коррозии весьма опасен, поскольку зачастую видимые эффекты разрушения отсутствуют, даже когда прочность материала критически уменьшена.
2. Явное разрушение материала с исчезновением вещества. Этот эффект традиционно определяет как коррозию.
Основные механизмы коррозии.
Наиболее распространены следующие механизмы коррозии.
1. Химическая.
В строгом смысле слова это те виды коррозии, где отсутствуют другие сопутствующие факторы: электрическое
поле, механические напряжения материала и т.д. Многообразные процессы, протекающие в агрессивных средах.
В МЕТАЛЛАХ И ИХ СПЛАВАХ – это в первую очередь окислительные реакции. Особо здесь можно отметить уже упомянутую выше водородную коррозию, крайне опасную для сталей и чугунов. Действие водорода, особенно при температурах свыше 300 ОС и давлениях порядка 20 МПа выражается в двух процессах:
- дезкарбонизация (обезуглероживание) вследствие образования метана
ССПЛАВ + 2Н2 СН4
этот эффект приводит к восстановлению карбидов FeXCY до чистого железа, прочность которого много ниже.
- образование гидридов (наводороживание)
М + Н2 М-… Н2+
ещё более опасный эффект, делающий материал хрупким.
В СИЛИКАТНЫХ МАТЕРИАЛАХ – наиболее характерны реакции замещения при действии: фтора и его
соединений; концентрированных щелочей; концентрированной ортофосфорной кислоты.
В ПОЛИМЕРНЫХ МАТЕРИАЛАХ (пластмассах, каучуках, резинах)– также наиболее характерны реакции
замещения при действии галогенов, азотной кислоты, органических галогенангидридов, кислорода, серы.
2. Электрохимическая.
Специфический вид коррозии, характерный для электропроводящих материалов – в первую очередь, металлов. Выделяют две разновидности ЭХК.
1. Контактная.
Всегда может возникать в парах металлов с различными стандартными редокс-потенциалами при взаимодействии таких пар с проводящей средой, особенно водной. Явление крайне опасно для металлических защитных покрытий (оцинковки, лужения, никелирования, хромирования) при их механическом повреждении.
2. Коррозия под напряжением.
Возникает при наложении внешнего электрического поля – как постоянного, так и переменного. Проявляется в наибольшей мере в электрохимической аппаратуре; в “обычных” (неэлектрохимических) процессах вызывается
блуждающими токами и разрядами статического электричества.
3. Фреттинг-коррозия (коррозия в механически нагруженных материалах).
Механические напряжения, такие как давление, вакуум, а наибольшей мере – колебания – способны существенно ускорять коррозию. Все виды механических нагрузок заметно повышают потенциальную энергию напряжённого материала и одновременно снижают целостность поверхностных слоёв (т.к. в них напряжения максимальны).
Это явление характерно, например, для автоклавов; аппаратов с акустической активацией процессов.
Специфический вид такой коррозии – абразивное действие твёрдых дисперсных материалов (например, катализаторов Ренея) на рабочие поверхности аппаратуры.
4. Фото- и радиационнохимическая коррозия.
Процессы деструкции материалов под действием видимого света, УФ-, ренгеновского и -излучения. Излучения
особо опасны для органических материалов, поскольку возбуждаемые ими фотореакции быстро разрушают полимер.
5. Абляция
Наиболее сложный вид коррозии, вызываемый совместным действием (синергизмом) мноих факторов – агрессивной среды, высокой температуры, механических нагрузок, внешних полей.
Проявляется в реакторах, предназначенных для высоскотемпературных процессов пиролиза.
.
ФОРМЫ ПРОЯВЛЕНИЯ КОРРОЗИИ
Здесь имеются в виду “зримые” явления коррозионного разрушения материала.
1. Равномерная коррозия
Рисунок. Картина развития равномерной коррозии
- Агрессивная среда
- Слой корродированного материала
- Слой некорродированного материала
Характерна для химической коррозии однородных по свойствам материалов. Проявляеся как образование и
разрастание слоя продуктов коррозии на поверхности материала.
2. Питтинговая коррозия (изъязвление поверхности материала)
Рисунок. Картина развития питтинговой коррозии
- Агрессивная среда
- Питтинги (очаги корродированного материала)
- Слой некорродированного материала
Характерна для химической коррозии неоднородных по свойствам материалов. Проявляеся как образование на многих участках поверхности очаговых зон коррозии - язвочек (от английского слова pitting -язва). Если свойства материала сильно неоднородны по его объёму, то далее питтинги постепенно углубляются. превращаясь в глубокие очаги – вплоть до образование сквозных отверстий в материале ("проедания"). В случае относительно однородных материалов питтинги со временем сливаются в сплошной слой, и процесс в дальнейшем неотличим от равномерной
коррозии.
3. Коррозионное растрескивание
Данный вид коррозии характерен для гетерогенныех материалов – чугунов, сталей, биметаллов, слоистых пластиков, текстолитов, бетонов – и им подобных. Эти материалы состоят из компонентов-фаз с существенно различными свойствами. Поверхности контакта фаз всегда являются областями повышенного потенциала; в силу этого зачастую коррозия интенсивно протекает именно вдоль поверхности раздела фаз. В результате материал растрескивается и затем крошится.
4. Щелевая коррозия
Обобщённый термин, относящийся к разным по механизму видам коррозии, развивающейся в стыках, соединениях деталей и узлов аппаратуры и строительных конструкций.
В местах стыков, как правило, существуют неплотности и щели между отдельными элементами конструкций. В процессе эксплуатации выделяющиеся в воздух рабочей зоны или в атмосферу агрессивные вещества способны накапливаться в таких щелях; причём удалить их оттуда весьма нелегко. В результате стыки подвергаются усиленному и длительному коррозионному воздействию среды.
Щелевая коррозия особо опасна для строительных конструкций и открытых стационарных сооружений.
МЕТОДЫ ИСПЫТАНИЙ И ХАРАКТЕРИСТИКИ
КОРРОЗИОННОЙ СТОЙКОСТИ МАТЕРИАЛОВ
Очевидно, что для обеспечения возможности корректно использовать конструкционные материалы (а равным образом – и оборудование из них) необходимо испытывать, измерять и характеризовать их коррозионную стойкость.
Методы испытаний
Методы испытаний коррозионной стойкости всегда основаны на помещении испытуемого образца в реальную или модельную агрессивную среду при заданной температуре и иных факторах (давление. вибрации. наложение электрического поля, интенсивные излучения и т.д.) на определённое время. В ходе испытаний измеряют потери массы материала, контролируют или характеризуют качественно изменения его физических свойств (например, факт набухания полимера или растрескивания композита можно обнаружить визуально).
В результате можно получить сведения о скорости разрушения (растворения) материала; о механизме коррозии; о времени устойчивости материала в данной среде; о составе среды или температуре, при которых материалы являются стойкими.
Наиболее распространён простейший тест, схема которого приведена на рисунке …
Рисунок. Схема опыта измерения скорости коррозии
- Сосуд
- Агрессивная среда
- Испытуемый образец
Метод применяется для измерения скорости равномерной коррозии. Образец – как правило, прямоугольную пластинку формата АхВ известной толщины S и массы М0 помещают в среду. Через определённые промежутки времени пластинку извлекают, промывают. высушивают и взвешивают. Таким образом получают зависимость массы М от времени .
По измереным значениям вычисляют скорость коррозии.
Массовая скорость
Wm [кг/(м2.с)] =
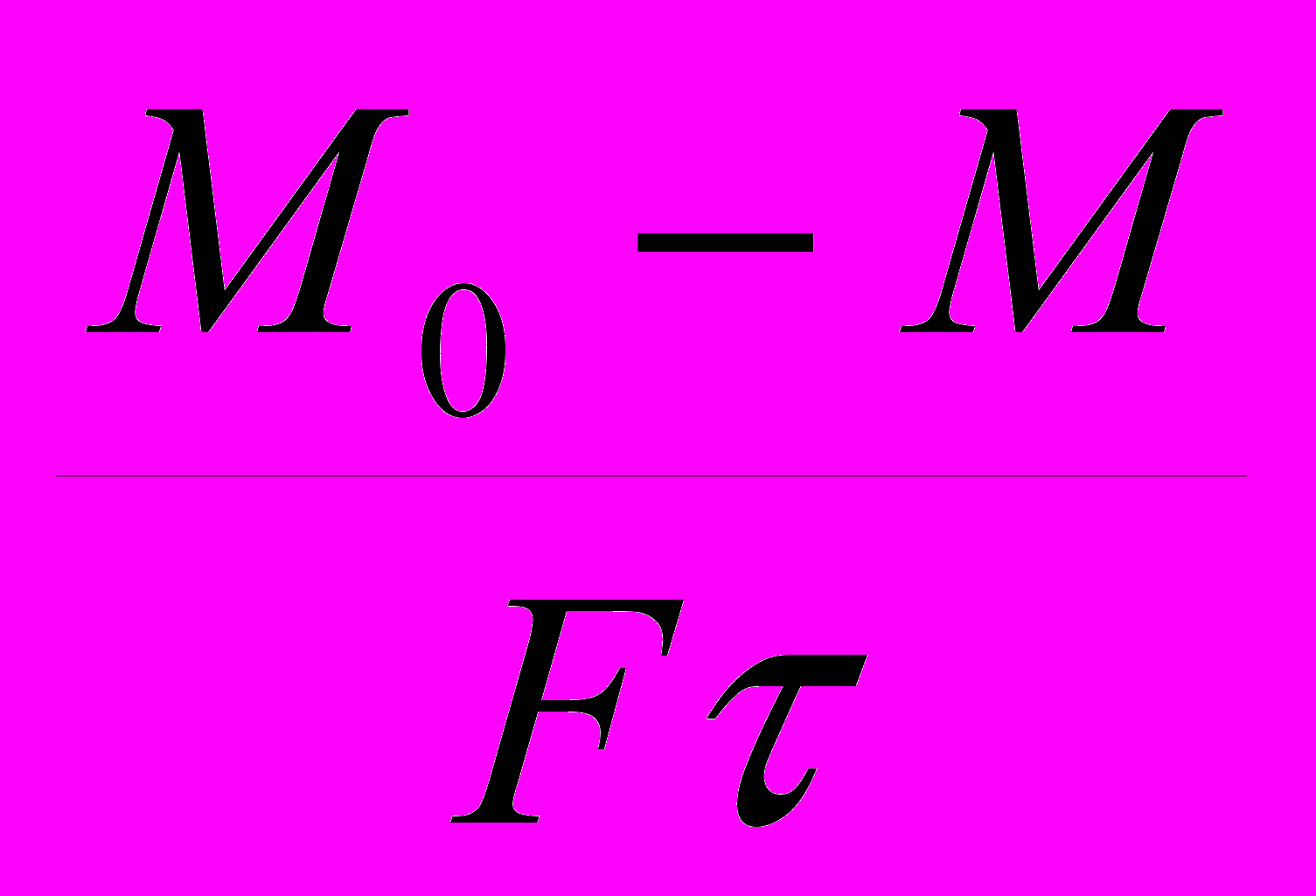
Линейная скорость
WL [м./с)] =
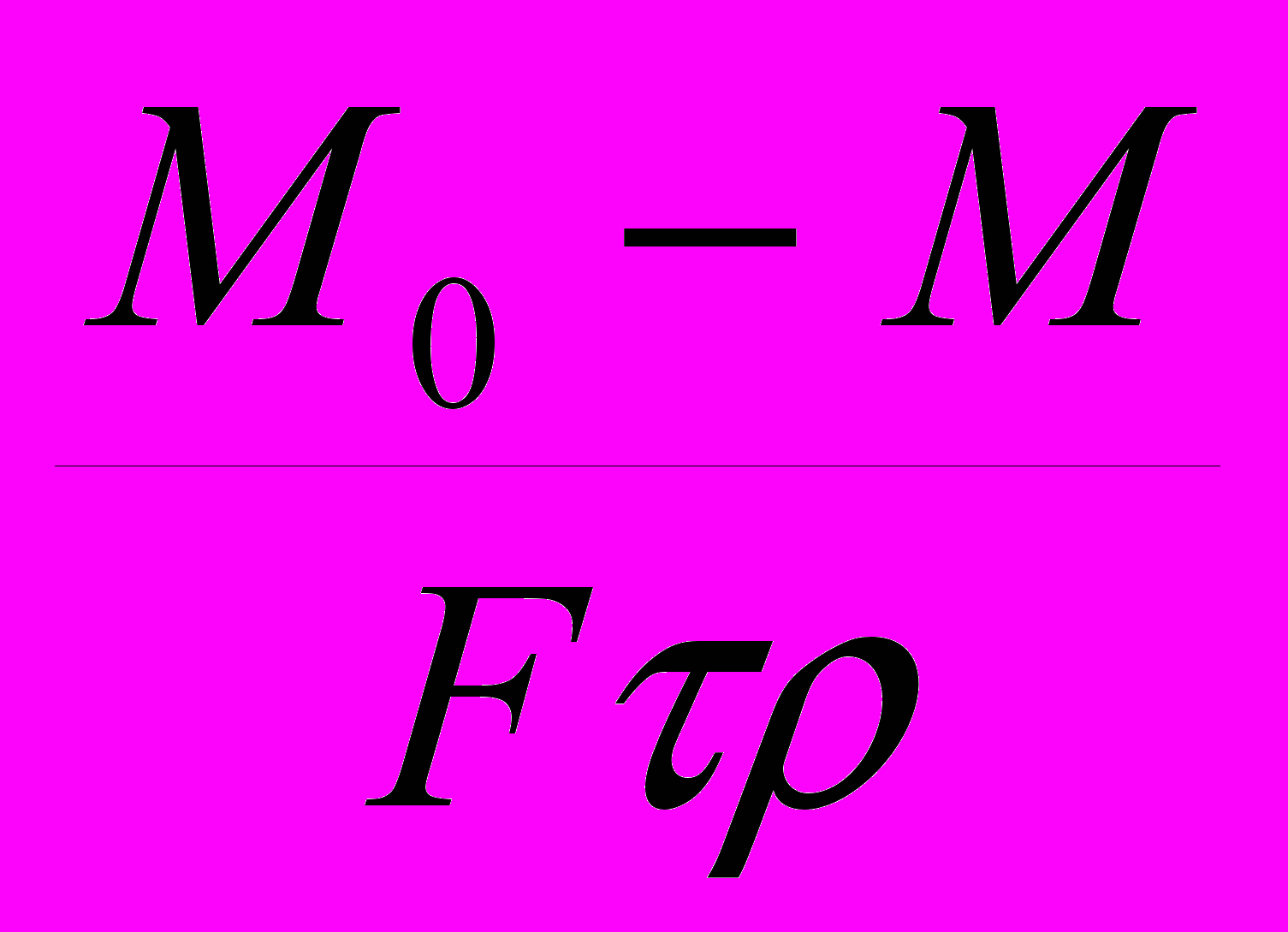
- плотность материала, кг/м3.
Классификация коррозионной стойкости материалов
Значения линейной скорости коррозии лежат в основе классификации коррозионной стойкости.
Таблица 3.1 - Классы коррозионной стойкости материалов
Класс | Группа | Линейная скорость коррозии, мм/год |
Совершенно стойкие | I | менее 0,001 |
Вполне стойкие | II | 0,001…0,005 |
III | 0,005…0,01 | |
Умеренно стойкие | IV | 0,01…0,05 |
V | 0,05…0,1 | |
Ограниченно стойкие | VI | 0,1…0,5 |
VI | 0,5…1 | |
Малостойкие | VII | 1…5 |
IX | 5…10 | |
Нестойкие | X | свыше 10 |
Следует сказать, что нормы и правила фармацевтических производств, нормы и методы контроля качества АФС (Фармакопея) предъявляют весьма жёсткие требования к коррозионной стойкости рабочих (контактирующих с продуктом) узлов оборудования.
Можно априори сказать, что рабочие узлы оборудования, особенно на стадиях получения очищенных ("фармакопейных") АФС должны быть изготовлены только из совершенно стойких или вполне стойких материалов. Более того, зачастую требования ещё жёстче; причём коррозионная активность большинства реакционных сред производств БАВ не охарактеризована в литературе по антикоррозионной защите. В этих случаях материалы и оборудование подлежат обязательному испытанию в реальных производственных (или близких к ним) условиях.
ЗАЩИТА ОТ КОРРОЗИИ
Антикоррозионная защита оборудования – важная задача для любой сферы техники, а для химических отраслей промышленности – особенно.
Все методы антикоррозионной защиты можно свести в несколько классов.
1. Использование коррозионностойких материалов.
Самый очевидный, самый эффективный (отнюдь не всегда – самый дешёвый) – самый важный метод.
В настоящее время в развитых странах химическую аппаратуру практически полностью изготовляют из коррозионностойких материалов. Несмотря на удорожание такого оборудования в среднем на (30…100) %, снижение потерь от коррозии позволяет существенно повысить надёжность техники и, следовательно, безопасность производства. При этом исключаются необходимость окраски и других подобных мер защиты; затраты на эксплуатацию снижаются в (2..5) раз. Практически исключается или радикально снижается количество выбросов продуктов коррозии в окружающую среду.
2. Методы флегматизации среды.
Коррозия – очень сложный процесс, зависящий от многих факторов. В ряде случаев даже незначительные изменения состава среды – особенно концентраций электролитов и окислителей – существенно изменяют редокс-потенциал системы, вплоть до перехода в область пассивации.
Так, например введение в среду незначительных количеств бихроматов или KMnO4 резко – в (5…200) раз – повышает стойкость титана к хлороводороду и соляной кислоте. Аналогично, добавки бихроматов повышают стойкость ряда сталей к азотной кислоте.
Специфический метод применяют для защиты контактных пар от электрохимической коррозии. К элементам пары подключают источник напряжения, равного по значению и противоположного по знаку потенциалу пары – в итоге суммарная Э.Д.С. системы становится нулевой, что подавляет коррозию.
3. Методы пассивации поверхности.
3.1. Химические методы.
Эти методы применяют преимущественно для металлических материалов. Они сводятся к образованию на поверхности металла слоя защитной плёнки (оксидной, сульфидной, фосфидной, фторидной), значительно более стойкой, нежели сам металл.
Химическая пассивация называется травлением. Широко применяются методы электрохимической – как анодной. так и катодной пассивации (для алюминия - анодирование).
3.2. Механико-технологические методы.
Сюда относятся приёмы уплотнения (накатки, наклёпки, ковки), а также тщательной шлифовки и полировки рабочих поверхностей.
Реальные материалы всегда имеют (как это известно из курсов физики, механики и ПАХТ) шероховатую поверхность.
Рисунок 4. Схема шероховатой поверхности.
r1 и r2 – главные радиусы кривизны шероховатостей.
_____________________________
Если в простейшем приближении считать, что все шероховатости – полусфера радиуса r, - то избыточная площадь реальной шероховатой поверхности – по сравнению с идеальной плоскостью составит
Fе = 2 Nшr2 – 1 (3.3)
Nш – число шероховатостей на единице поверхности материала;
r – радиус кривизны, м.
Кроме того, за счёт поверхностного натяжения повышается потенциальная энергия искривлённой поверхности
Ее = 2/r
Где - поверхностное натяжение.
Любое уплотнение снижает поверхностное натяжение и уменьшает избыточную поверхность; как следствие.
возрастает степень однородности и стойкость материала.
4. ПРИМЕНЕНИЕ ЗАЩИТНЫХ ПОКРЫТИЙ.
МЕТАЛЛИЧЕСКИЕ ПОКРЫТИЯ
Металлические покрытия применяют, в основном, для защиты оборудования из стали.
В качестве защищающих металлов наиболее часто используют никель и хром. Покрытия наносят электрохимически или термодиффузионными методами.
Специфический – и очень распространённый – вариант способа: изготовление биметаллов. Биметаллы – двухслойные листовые материалы, получаемые методом горячей прокатки. Несущий толстый слой – подложка – из малостойкого материала; верхний – защитный, т.н., плакирующий - из высокостойкого материала.
_________________________
\\\\\\\\\\\\\\\\\\\\\\\\\\\\\\\\\\\\\\\\\\\\\\\\ - Плакирующий слой
/ / / / / / / / / / - Подложка
/ / / / / / / / / /
Основная масса биметаллов – стальные: подложка – стали Ст10 или Ст20; плакировка – стали типа Х18Н10Т.
Аналогично медь плакируют томпаком (сорт латуни); дюраль – алюминием.
Применение биметаллов позволяет создавать защищённую аппаратуру при существенной экономии высокостойких материалов; однако термические напряжения на ПРФ ограничивают (сужают) диапазон рабочих температур такого оборудования.
ПОКРЫТИЕ НИТРИДАМИ
В качестве защитного покрытия для узлов, работающих при повышенной температуре и со значительными механическими нагрузками всё большее применение находит нитрид титана.