Лекция 14. Ручная электродуговая сварка
Вид материала | Лекция |
- Лабораторная работа 6 ручная электродуговая сварка металлическим электродом, 379.75kb.
- Тематический план и программа «Ручная электродуговая и газовая сварка» Профессия, 56.52kb.
- Программа вступительного экзамена в аспирантуру по специальности 05. 03. 06 «Сварка, 131.86kb.
- Ручная электро-дуговая сварка, 1686.86kb.
- Лекция 16. Способы сварки давлением. Контактная сварка. Стыковая, точечная, шовная, 82.74kb.
- Государственный стандарт союза сср ручная дуговая сварка. Гост, 1829.59kb.
- Лабораторная работа 1 Ручная дуговая сварка штучными электродами, 173.93kb.
- Тема: сварка алюминия и его сплавов, 56.75kb.
- Автоматизация турфирм. Простое решение сложной проблемы, 103.69kb.
- Зварачныя работы правiлы правядзення Издание официальное Министерство архитектуры, 2913.92kb.
Лекция 14. Ручная электродуговая сварка
Ручную дуговую сварку выполняют штучными электродами, которые сварщик подает к свариваемому изделию и перемещает в нужном направлении.
Используются электроды из сварочной проволоки диаметром 2–8 мм, на поверхность которых наносят различные покрытия–обмазки. Ручную сварку применяют для соединения металла толщиной от 1 мм и выше (до 30 мм) в любых пространственных положениях, любой протяженности и конфигурации, а также при наложении швов в труднодоступных местах. Сваривают стали, чугуны, алюминиевые и медные сплавы, некоторые титановые сплавы.
Существенным недостатком ручной дуговой сварки покрытыми электродами является невысокая производительность процесса и зависимость качества сварного шва от практических навыков сварщика, а также трудность сварки тонкого материала (менее 1–2 мм).
Ручную дуговую сварку можно осуществлять и неплавящимся угольным или вольфрамовым электродом.
Стальная сварочная проволока разделяется на низкоуглеродистую, легированную и высоколегированную. Всего выпускается 77 марок проволоки. Условное обозначение марок проволоки состоит: из индекса Св – сварочная и следующих за ним цифр, показывающих содержание углерода в сотых долях процента и буквенных обозначений элементов, входящих в состав проволоки. При содержании в проволоке менее 1% легирующих элементов ставят только букву этого элемента, если содержание легирующего элемента более 1%, то после буквы в целых единицах указывают содержание этого элемента. Буква А в конце условных обозначений марок низкоуглеродистой и легированной проволоки указывает на повышенную чистоту металла по содержанию серы и фосфора. Например, Св–08ГС, Св–06Х19Н10М5Т и др.
Сварочная проволока для сварки алюминия и его сплавов предусматривает 14 марок проволоки, химический состав которой идентичен свариваемому металлу (например, СвА97, СвА95, СвАМЦ, СвАМГ и др.).
Для сварки меди и ее сплавов применяют проволоку из меди и сплавов на медной основе.
Для сварки чугуна применяют стержни, отлитые из серого чугуна.
Для сварки титана используют сварочную проволоку из сплава ВТ1, ВТ5 и др.
Сварочная проволока используется и для изготовления присадочных прутков при сварке неплавящимся электродом.
Электроды классифицируют по следующим признакам:
-назначению
-типу и видам покрытия
-характеру жидкого шлака и др.
По назначению стальные электроды подразделяются на 4 класса:
-для сварки углеродистых и низколегированных сталей.
К этой группе относятся электроды типов Э34, Э42, Э42А,…,Э145. Цифры показывают прочность наплавленного металла в МПа, буква А – повышенную пластичность металла сварного шва. Например, Э34 – предел прочности 340 МПа или 34 кг/мм2. Для сварки сталей этого типа электроды выбирают с учетом равной прочности основного и электродного металла. Свойства наплавленного металла должны быть равны или несколько выше соответствующих свойств свариваемого металла.
-для сварки легированных теплоустойчивых сталей.
Электроды подразделяются на типы Э-М, Э-ХМ, Э-ХМФ, Э-Х5МФ, Э-ХМФБ и другие. Буквы Х, М, Ф,.Б означают легирование металла стержня соответственно хромом, молибденом, ванадием, ниобием, повышающими теплоустойчивость сварного шва. Электроды для сварки выбирают по признаку химического состава металла шва.
-для сварки высоколегированных сталей с особыми свойствами.
Наибольшее применение имеют хромистые и хромоникелевые стали. Главными легирующими элементами являются хром и никель, которые придают сталям высокую коррозионную стойкость.
а) сварка хромоникелевых сталей типа 12Х18Н9, 17Х18Н9, 12Х18Н10Т и др. Электроды выбирают по технологическим особенностям эксплуатации конструкции. То есть выбор зависит от того, в какой среде работает конструкция (слабой или сильной агрессивной) , при каких температурах (низких или высоких) и пр. Для этих целей установлено 34 различных типов электродов. Например, для слабой агрессивной среды ЭА-1а, для сильной агрессивной среды ЭА-1б. Буква А указывает на аустенитный класс сталей.
б) сварка хромистых сталей. Эти стали подразделяются на три основные группы: мартенситные с содержанием хрома до 12%; феррито-мартенситные – при содержании хрома 12-13%; ферритные стали, содержащие хрома 13% и выше.
Наибольшее распространение получили ферритные нержавеющие стали 12Х13, 20Х13, 30Х13, 15Х25Т, 15Х28. Сварку этих сталей производят по двум технологическим вариантам:
-применением сварочных материалов, электродов, обеспечивающих получение металла шва подобного основному металлу. В этом случае электроды выбирают по признаку химического состава и используют электроды типа ЭФ-Х13, ЭФ-Х17, ЭФ-Х25 и др. Цифра указывает содержание хрома в процентах в металле шва, буква Ф – класс свариваемой стали.
-использованием для сварки материалов, электродов аустенитного класса.
-для наплавки поверхностных слоев установлено 44 типа электродов. Обозначение электродов соответствует химическому составу наплавки и ее твердости по Роквеллу.
По толщине покрытия в зависимости от отношения диаметра электрода D к диаметру стержня d электроды изготовляются:
- с тонким покрытием
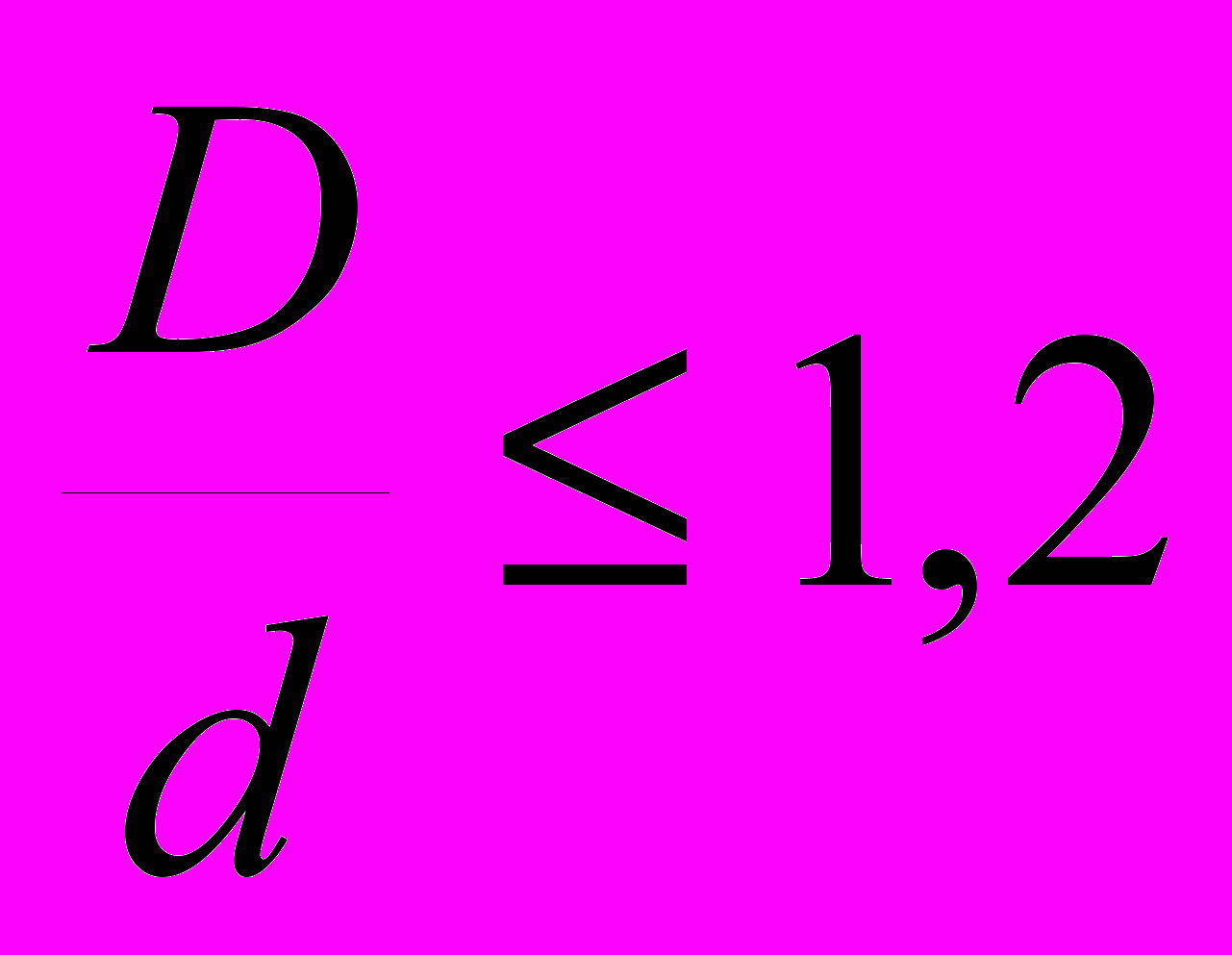
- со средним покрытием
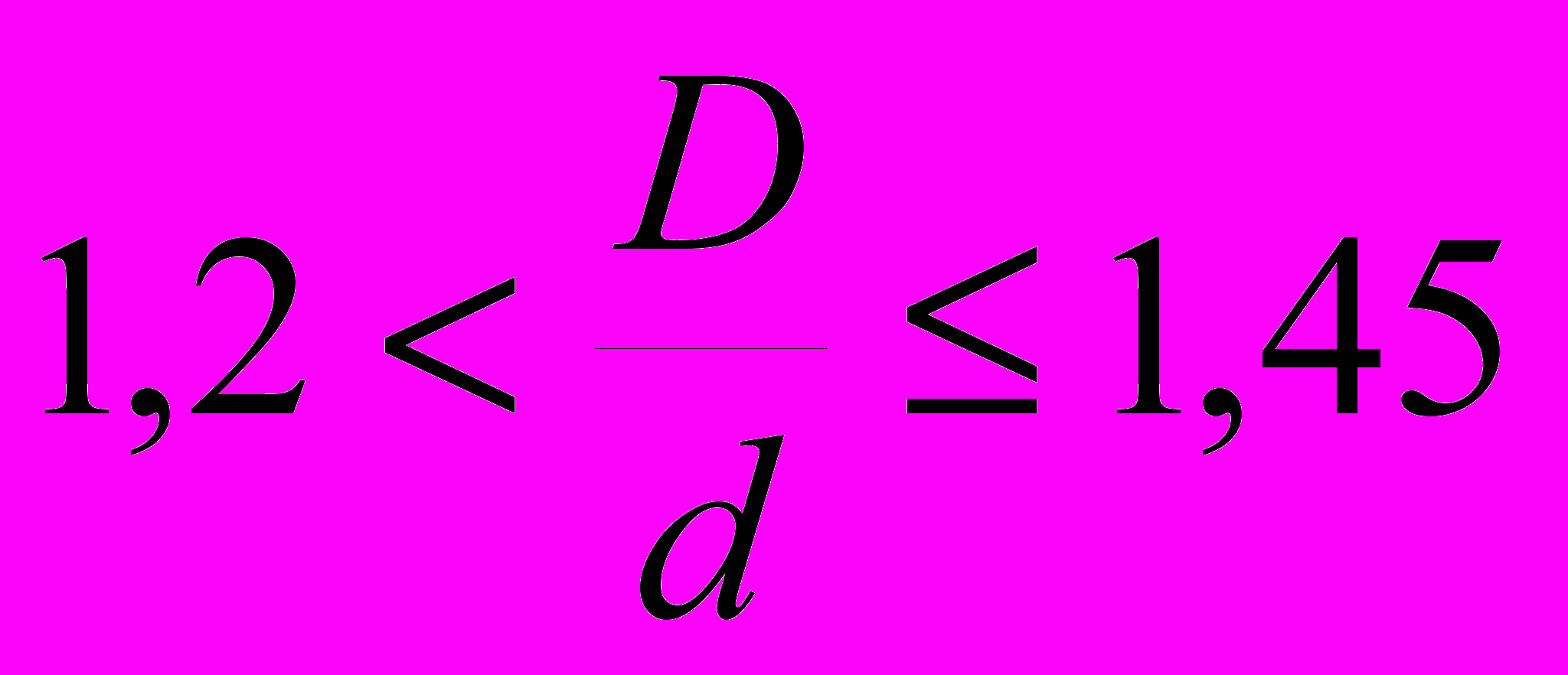
- с толстым покрытием
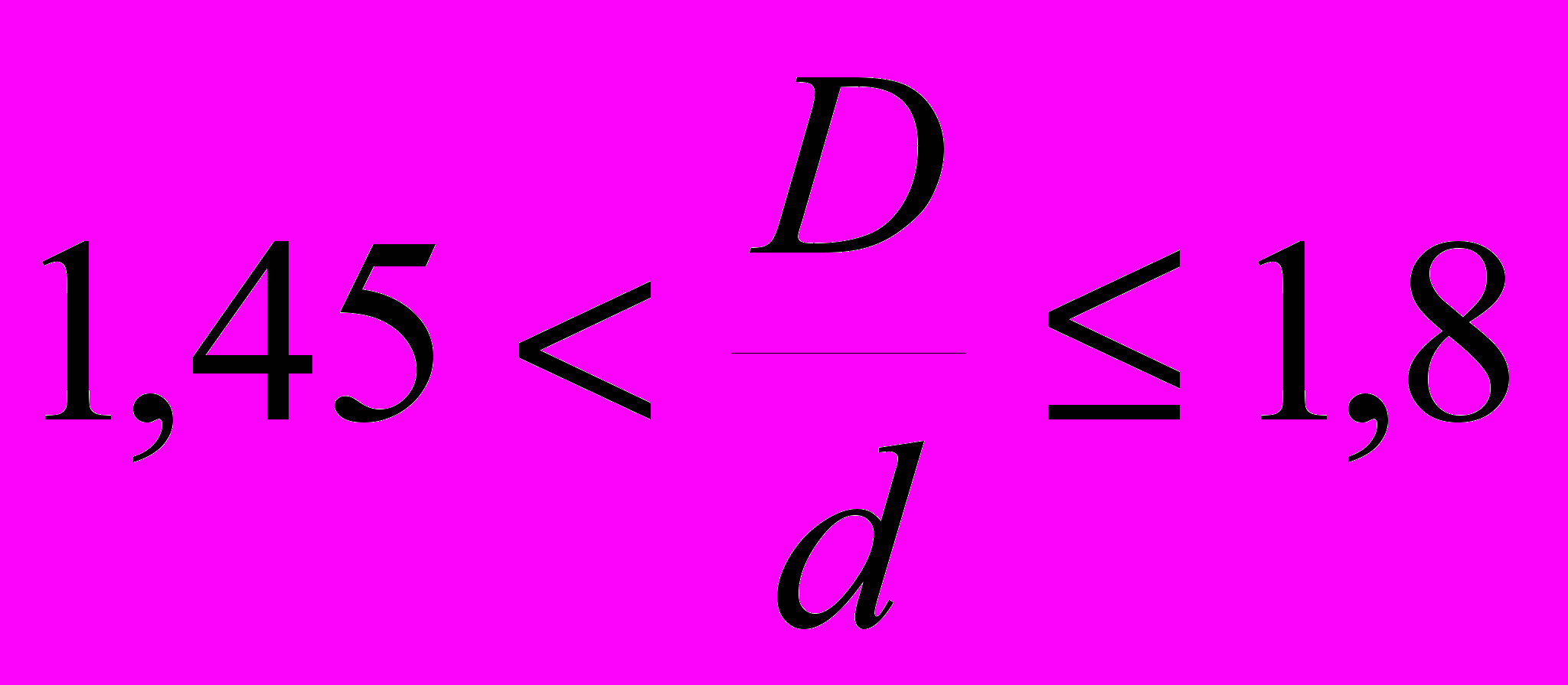
- с особо толстым покрытием
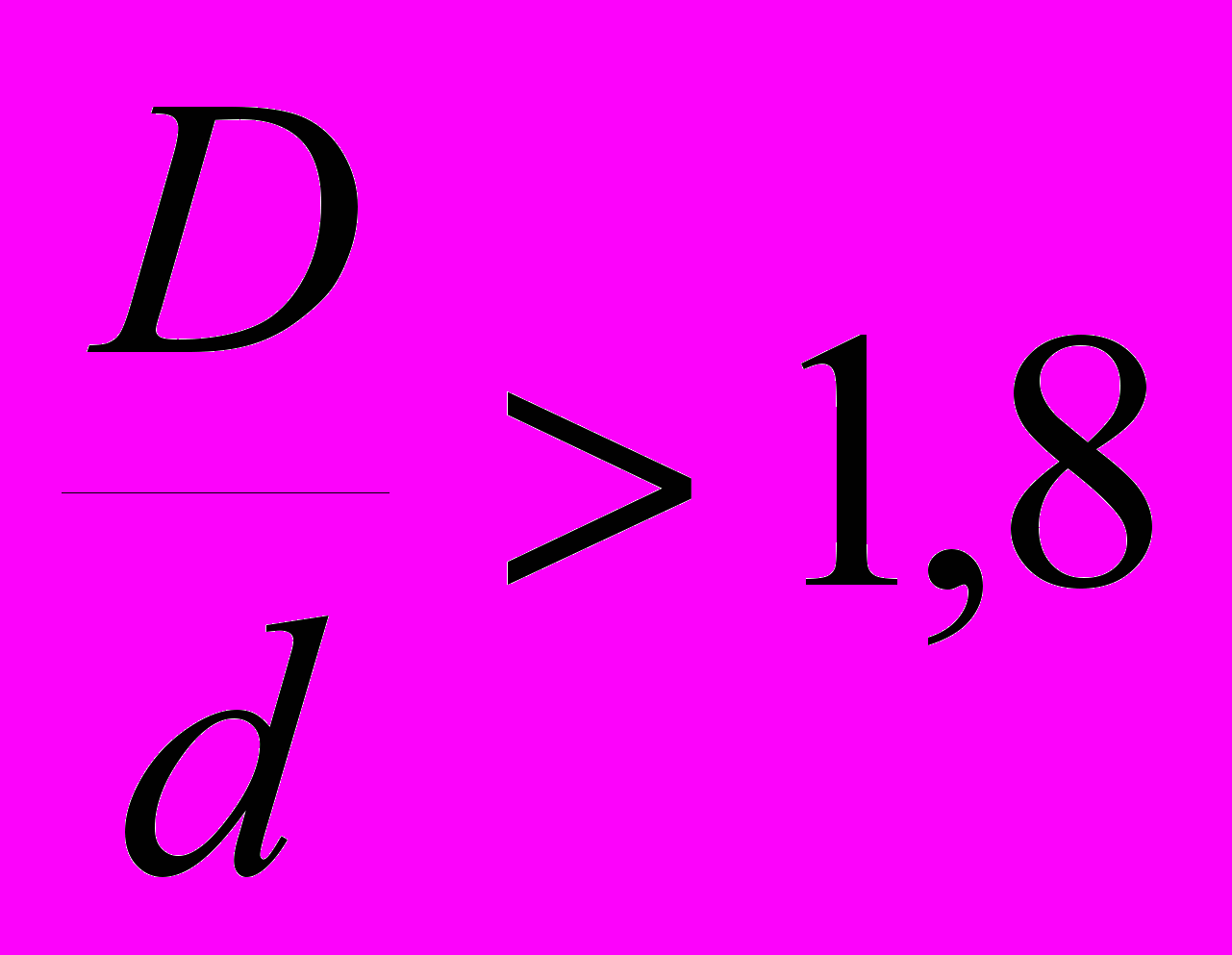
Покрытия выполняют следующие функции:
- газовая защита зоны сварки и расплавленного металла создается при сгорании газообразующих веществ и предохраняет расплавленный металл от воздействия кислорода, водорода и азота. Кислород, соединяясь с железом, образует закись железа
, которая хорошо растворима в расплавленном металле. При кристаллизации сварочной ванночки закись железа вытесняется к границам зерен металла, и, как следствие, металл шва приобретает низкие прочностные свойства.
Поглощение сварочной ванной азота и водорода приводит, в первом случае, к образованию нитридов (FeN) и повышенной хрупкости металла, а во втором случае, – к образованию кристаллизационных трещин.
Газообразующие вещества вводят в покрытие в виде органических соединений: древесной муки, декстрина, целлюлозы, крахмала, пищевой муки и т.д. Защитное действие этих веществ заключается в том, что при их сгорании в зоне дуги выделяется большое количество газов, которые оттесняют от сварочной ванны кислород и азот воздуха.
Защита расплавленного металла от водорода достигается путем связывания его в соединение прочное при высоких температурах и нерастворимое в жидком металле. Например, в HF, ОН. Это достигается использованием в электродных покрытиях соединения СаF2.
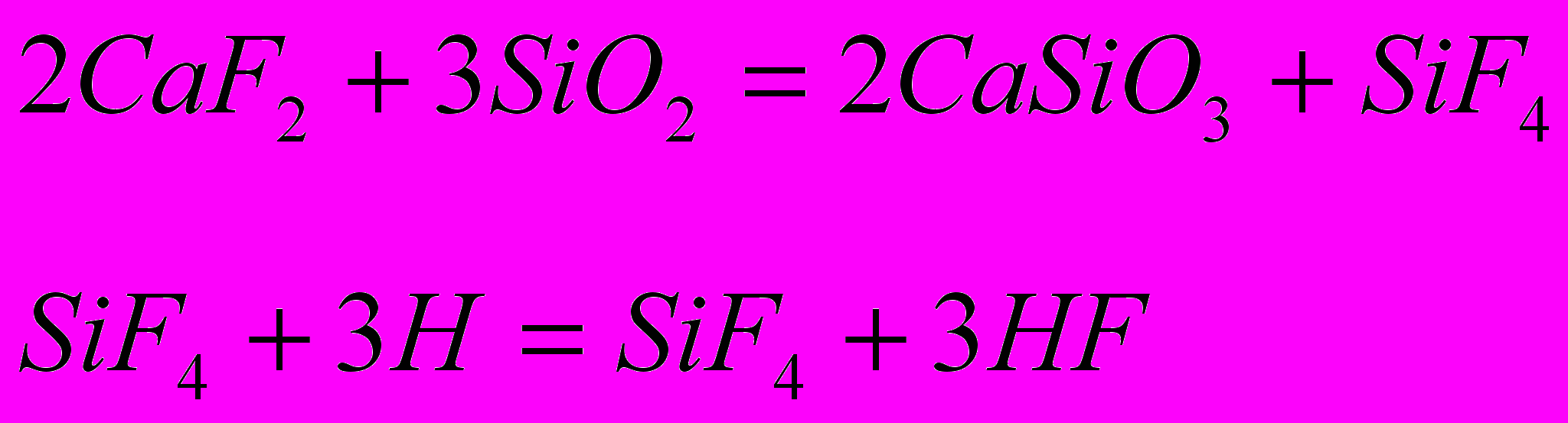
- раскисление металла сварочной ванны элементами, обладающими большим сродством с кислородом, чем железо применяют для удаления из сварочной ванны имеющегося в ней кислорода. Для этого в состав покрытия вводят марганец, кремний, алюминий, молибден, хром. Эти элементы, находясь в расплавленном металле сварного шва, легче вступают в химические соединения с кислородом и, будучи сами нерастворимыми в стали или имея ограниченную растворимость, в виде окислов всплывают на поверхность сварочной ванны.
- шлаковая защита служит для защиты расплавленного металла от воздействия кислорода и азота воздуха путем образования шлакового покрытия на поверхности расплавленного металла шва. Шлаковое покрытие уменьшает скорость охлаждения и затвердевания металла шва, способствуя выходу из него газовых и неметаллических включений. Шлакообразующими компонентами являются титановый концентрат, каолин, мрамор, мел, кварцевый песок, доломит, полевой шпат и др.
- легирование металла шва для придания специальных свойств наплавленному металлу. Легирование осуществляют хромом, никелем, молибденом, марганцем и др.
- стабилизация горения дуги посредством соединений калия, натрия, кальция , бария.
В качестве связующего компонента применяют жидкое стекло. Оно связывает компоненты покрытия между собой и со стержнем электрода.
Компоненты покрытий просушивают, тонко измельчают в требуемых весовых соотношениях и после добавки жидкого стекла наносят на электродные стержни. Наносят обмазку двумя способами:
1)погружением в полужидкий замес
2)методом прессования.
После нанесения покрытия сырые электроды просушивают в течение 12-24 часов при комнатной температуре, а затем прокаливают при температуре 200–250оС в течение 1–2 часов.
По химическому составу жидких шлаков покрытия подразделяют на кислые и основные.
В шлаках кислых покрытий преобладает окись кремния SiO2.Кислые шлаки обладают хорошими раскисляющими свойствами, но через них нельзя в широких пределах легировать наплавленный металл в связи с интенсивным выгоранием легирующих примесей. В состав кислых шлаков входят марганцевая руда, полевой шпат, рутил и т.п. Электроды с кислыми покрытиями (руднокислым, рутиловым и органическим) применяют для сварки углеродистых и низколегированных сталей.
В шлаках основных покрытий преобладает окись кальция CaO. Основные шлаки обеспечивают достаточно хорошее раскисление и позволяют вводить в металл шва значительные количества легирующих элементов. В состав основных покрытий входят мрамор, плавиковый шпат CaF2 и ферросплавы. Электроды с основным покрытием (фтористокальциевым) используются для сварки легированных и высоколегированных сталей.
Важной характеристикой электрода является его марка – она определяет состав покрытия, технологические свойства электрода: род и полярность тока, возможность сварки в различных пространственных положениях и др (УОНИ–13/45, ЦЛ–18, ЦЛ–10, ОММ–5, ОМА–2 и др.).
Один конец электрода на 30–40 мм очищают от покрытия для закрепления его в электродержателе.
Электроды характеризуются коэффициентами расплавления, наплавки и потерь.
Коэффициент расплавления – количество расплавленного электродного металла в граммах в течение часа, приходящееся на один ампер сварочного тока
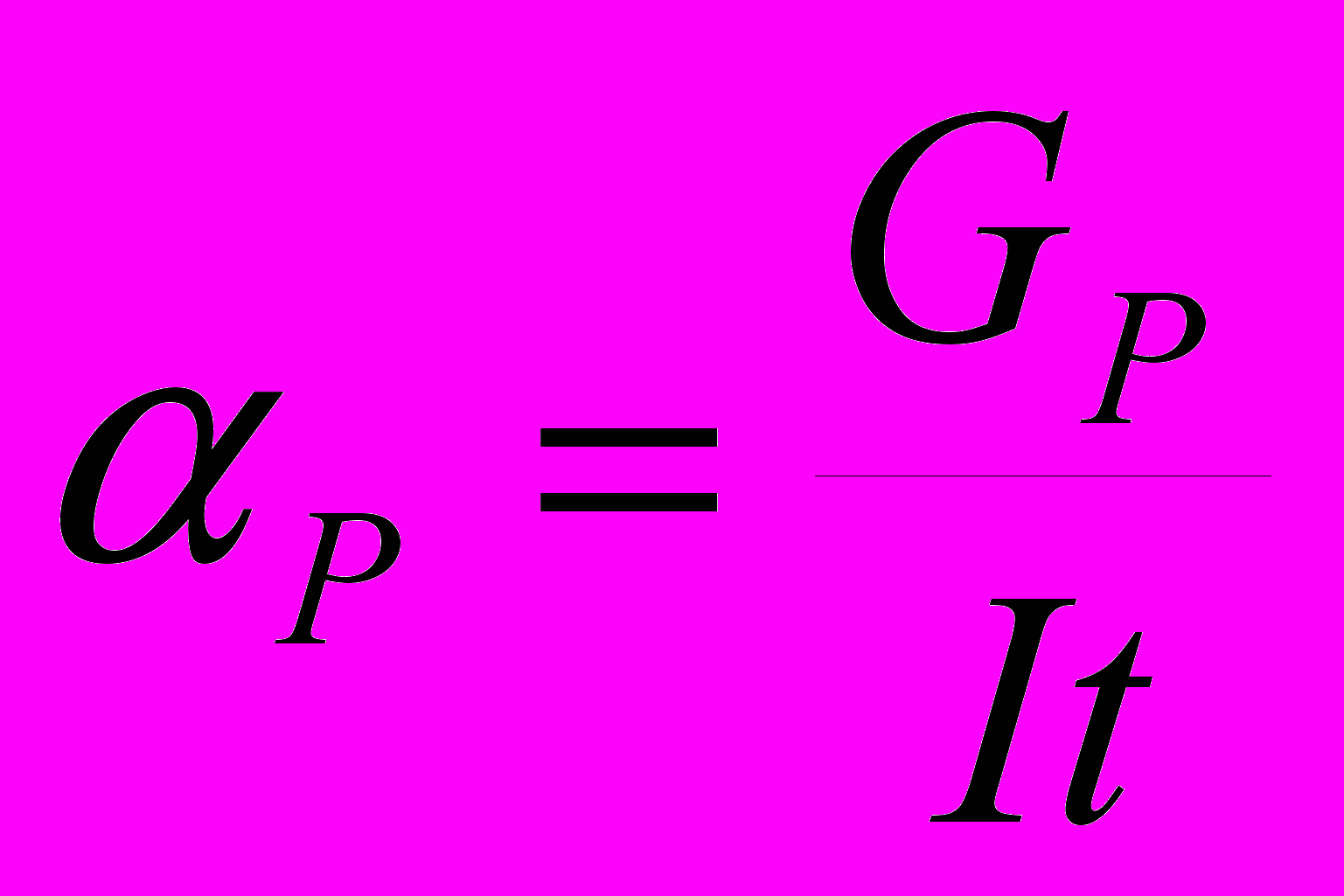
где:
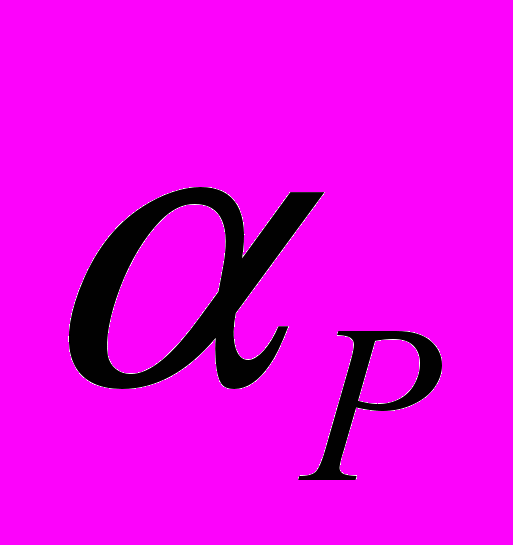
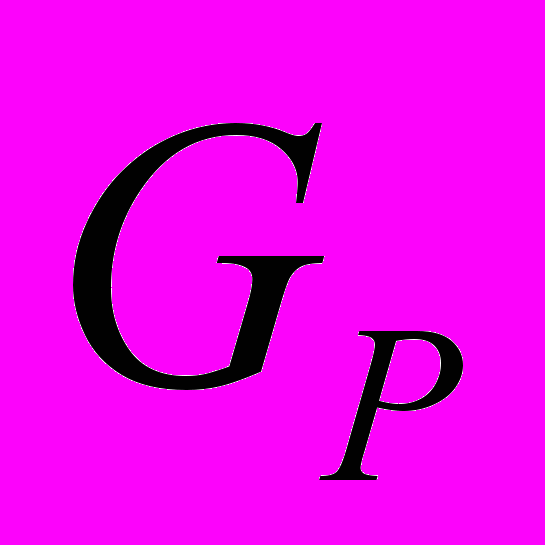
I–сварочный ток, А;
t–время горения дуги, равное 1 час.
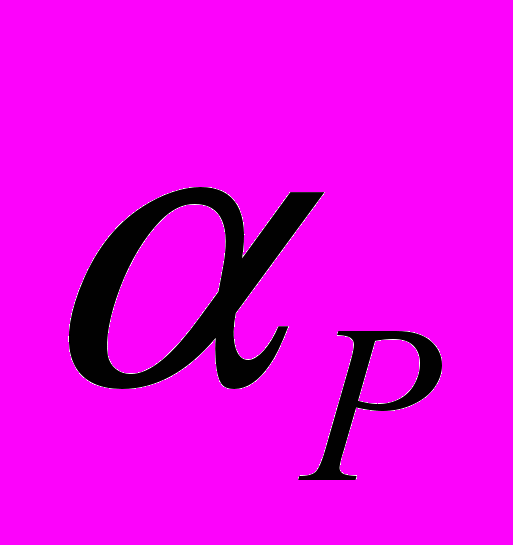
Коэффициент наплавки – количество наплавленного электродного металла в граммах в течение часа, приходящееся на один ампер сварочного тока
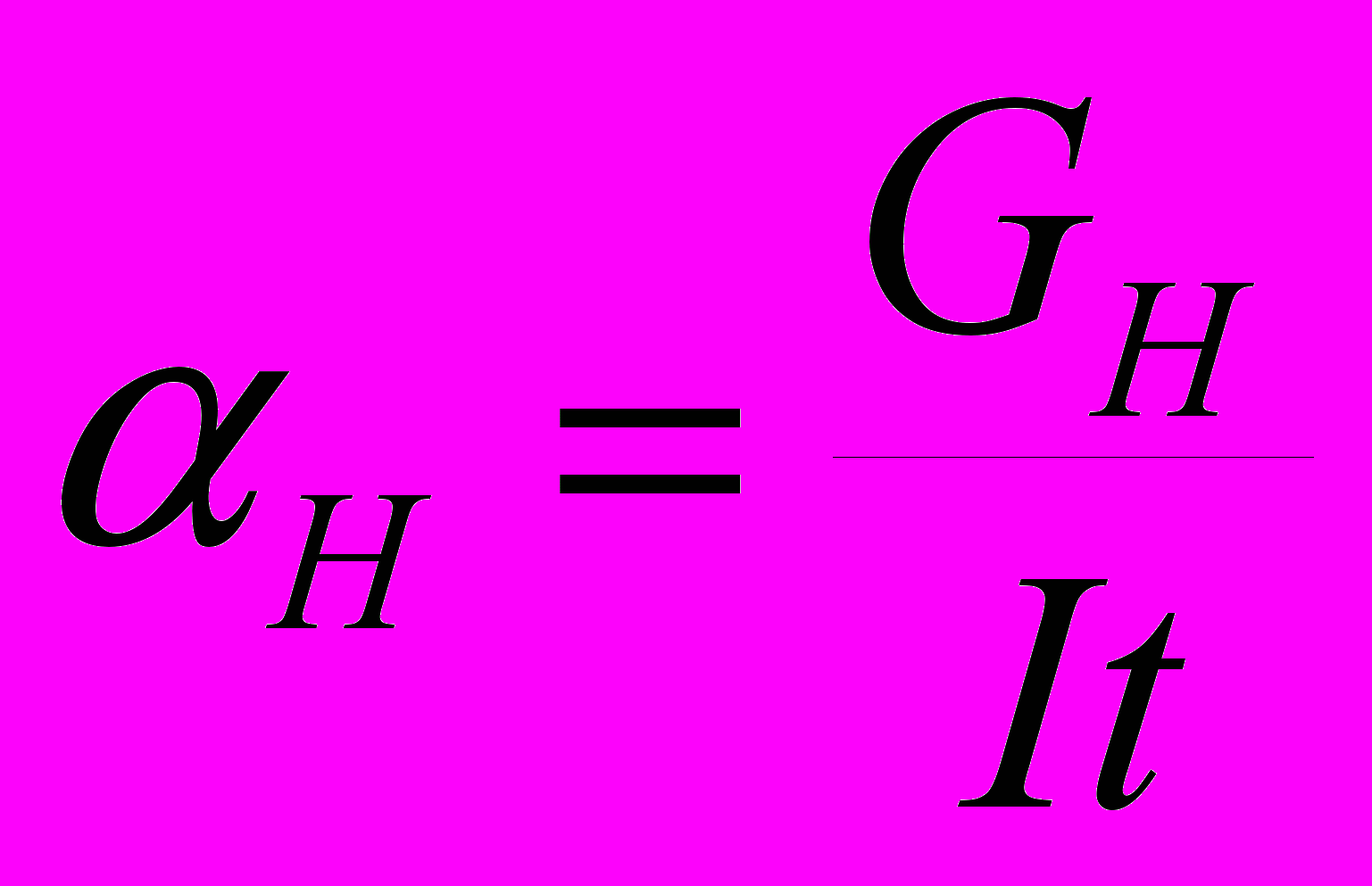
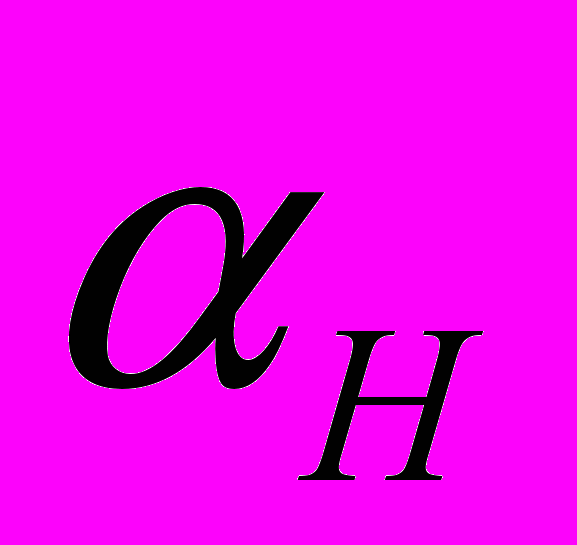
Коэффициент потерь представляет собой
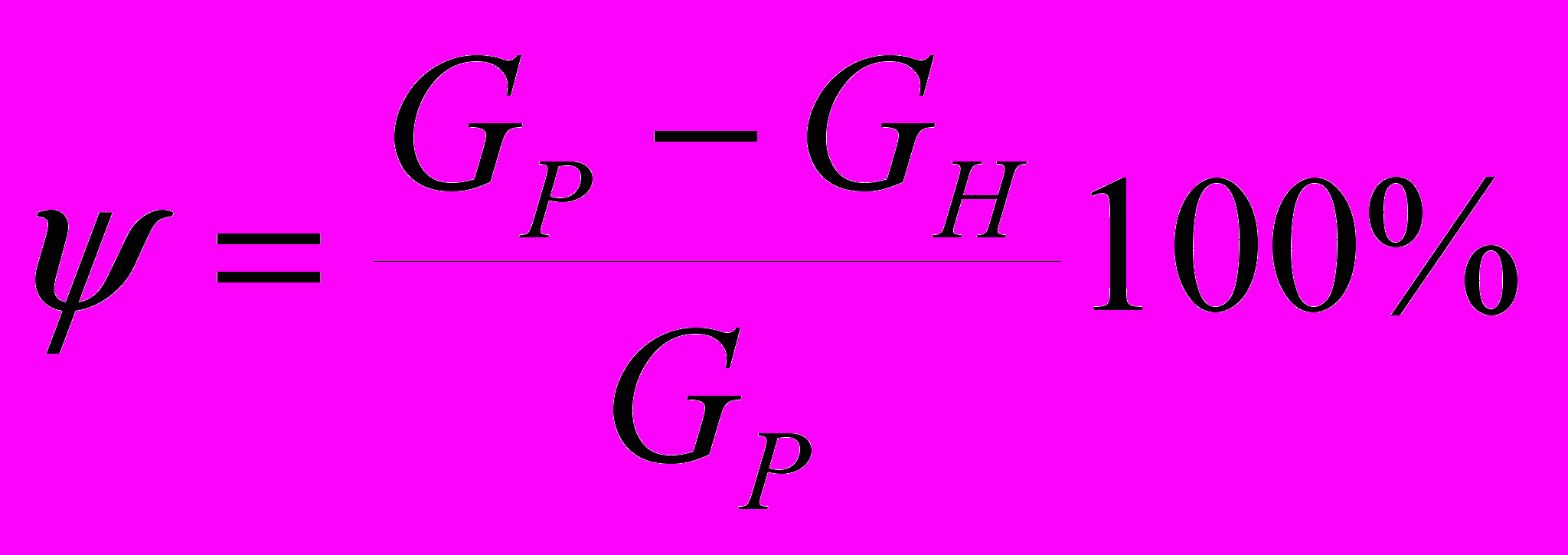
и составляет при сварке тонкопокрытыми электродами 10-20%, толстопокрытыми 5–10%, в защитных газах 3–10% под флюсом 1–3%.
Режимы ручной сварки
1. Диаметр электрода выбирают в зависимости от толщины металла и типа сварного соединения. При этом можно руководствоваться ориентировочно следующими данными
Толщина металла, мм | 0,5 | 1–2 | 2–5 | 5–10 | Свыше 10 |
Диаметр электрода, мм | 1,5 | 2–2,5 | 2,5–4,0 | 4–6 | 4–8 |
2. Величина сварочного тока зависит от диаметра электрода. Ориентировочно можно определить по формуле
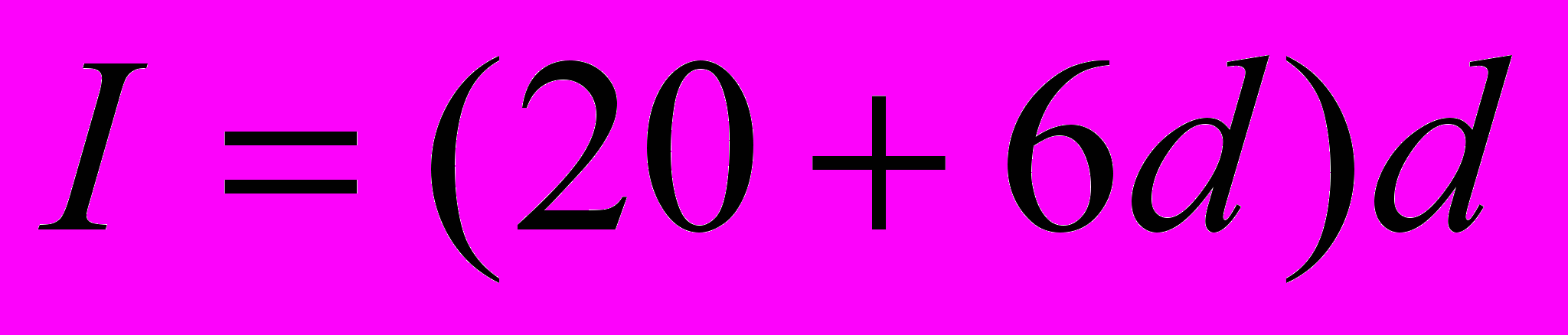
где d–диаметр электрода, мм.
3. Длина дуги определяется по формуле
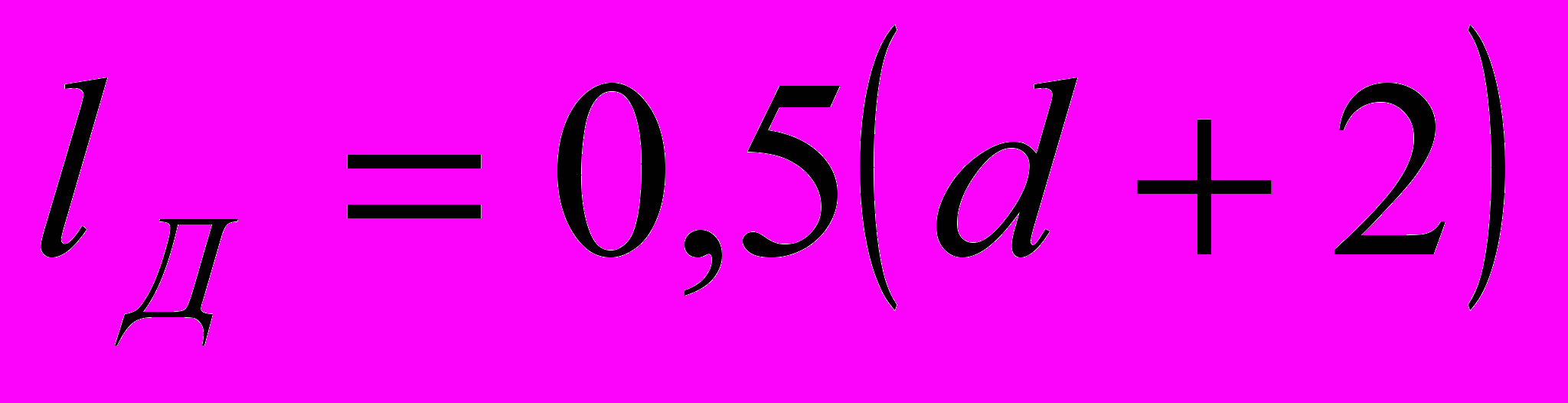
Чем короче дуга, тем выше качество наплавленного металла.
4. Напряжение горения дуги зависит от длины дуги и определяется по формуле:
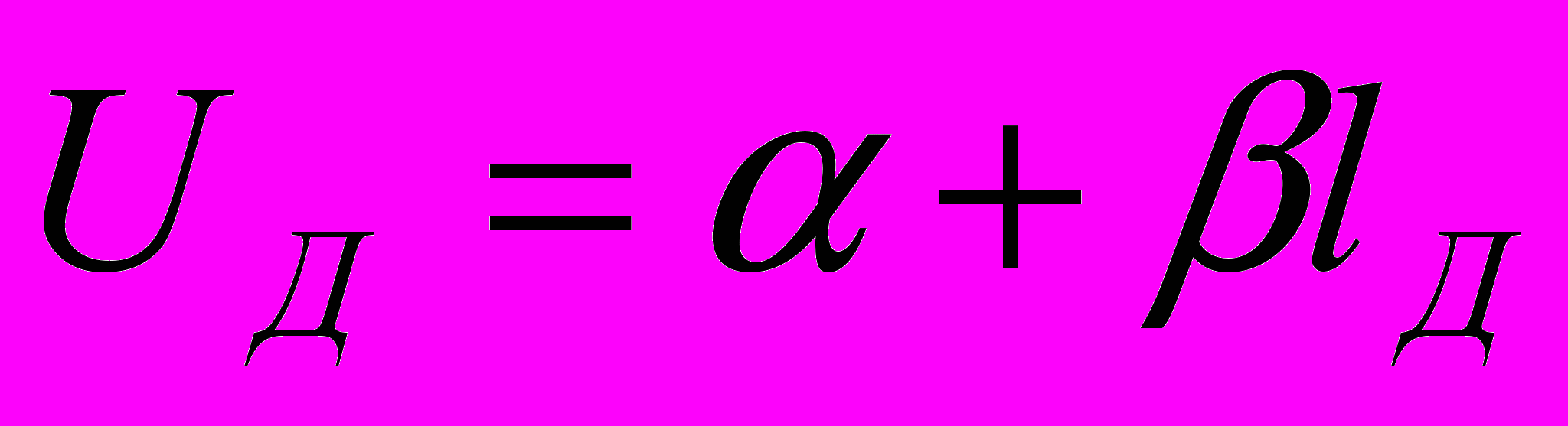
Автоматическая сварка под слоем флюса
Основным современным видом сварки при изготовлении ответственных конструкций является дуговая сварка под слоем флюса. Характерные особенности этого вида сварки заключаются в следующем:
- сварка ведется непокрытой электродной проволокой
- защита дуги и сварочной ванны осуществляется флюсом
- перемещение электрода в вертикальном направлении и вдоль сварного шва механизированы.
Автоматическую сварку под флюсом целесообразно применять для выполнения кольцевых, прямолинейных, стыковых и угловых швов протяженностью 0,8 м и более на металле толщиной 3 − 100 мм со свободным входом и выходом сварочной головки для начала и конца шва.
Преимущества сварки:
1. Хорошая и сравнительно дешевая защита расплавленного металла от воздействия атмосферного воздуха.
2. Производительность при автоматической сварке под флюсом по сравнению с ручной дуговой увеличивается в 5–25 раз за счет увеличения скорости сварки с 2 м/час до 30 м/час; увеличения силы сварочного тока в результате отсутствия опасения разбрызгивания металла.
3. Более низкий расход электродного металла вследствие уменьшения доли электродного металла в образовании шва (с70 до 30%), снижения потерь на угар, разбрызгивание и огарки.
4. Отпадает необходимость защиты глаз от светового излучения и не требуется квалифицированная рабочая сила.
Недостатки автоматической сварки под флюсом:
1. Возможность сварки только в нижнем положении;
2. Необходимость более тщательной (по сравнению с ручной сваркой) подготовки кромок и более точной сборки деталей под сварку;
3. Невозможность сварки стыковых швов на весу, то есть без подкладки или предварительной подварки корня шва.
1
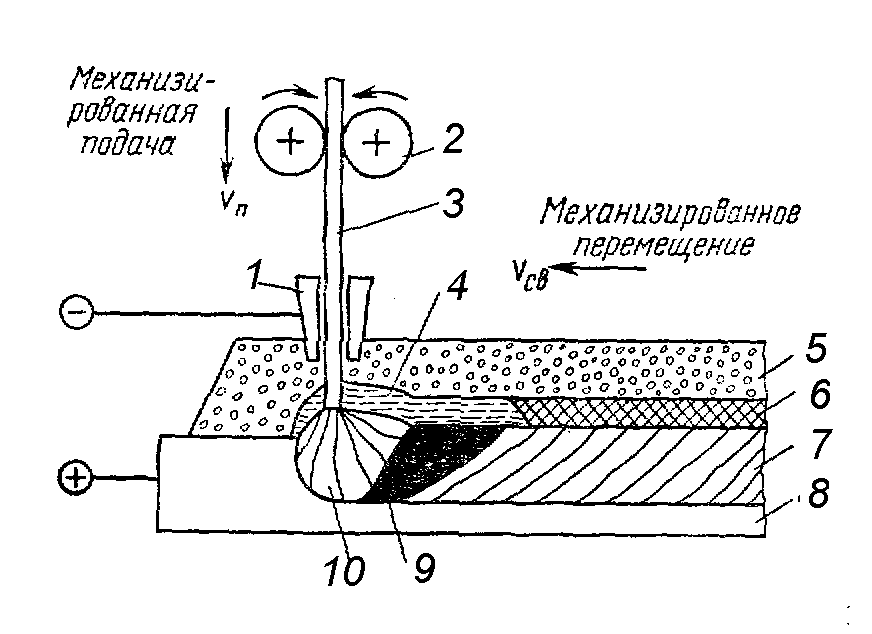
2–ролики
3–электродная проволока
4–ванна жидкого шлака
5–гранулированный флюс
6–шлаковая корка
7–сварочный шов
8–основной металл
9–ванна жидкого металла
10–дуга
Дуга горит между электродной проволокой и основным металлом. Столб дуги и сварочная ванна закрыты слоем флюса толщиной 30–50 мм. Часть флюса расплавляется, образуя ванну жидкого шлака. При поступательном движении электрода постепенно происходит затвердевание сварочной и шлаковой ванн, образование сварного шва, покрытого твердой шлаковой коркой, которая впоследствии легко отделяется от наплавленного металла.
Нерасплавленный в процессе сварки флюс пневматическим устройством отсасывается со шва и используется в дальнейшем при сварке.
При сварке под флюсом к электродной проволоке предъявляются строгие требования по химическому составу, чистоте поверхности и калибровке ее сечения. Отклонения размеров проволоки по диаметру нарушают работу роликов автоматической головки и ухудшают качество шва.
Сварку под флюсом можно осуществлять переменным и постоянным током. Предпочтение должно быть отдано сварке на постоянном токе, обеспечивающем, как правило, высокое качество сварных швов. Высоколегированные коррозионно-стойкие стали сваривают на постоянном токе обратной полярности.
Оборудованием для сварки являются сварочные автоматы. Они имеют:
- механизм подачи электродной проволоки в зону дуги (автоматическая головка)
- механизм перемещения головки или механизм перемещения изделий.
Сварочный автомат, у которого головка закреплена на самоходной тележке, имеющей самостоятельный привод, называют сварочным трактором.
Сварочные флюсы
Флюс представляет собой зернообразный продукт с размером зерен 1–3 мм.
По способу изготовления флюсы подразделяются на плавленые и керамические.
Плавленые флюсы получают сплавлением исходных компонентов в пламенных или электрических печах с последующей грануляцией. Исходными компонентами являются только шлакообразующие компоненты: марганцевая руда MnO, кремнезем SiO2, полевой и плавиковый шпат, доломит, известняк СаО. Компоненты замешиваются на жидком стекле. Эти флюсы пассивны в металлургическом отношении и служат только для образования шлаков.
Плавленые флюсы применяются при сварке углеродистых сталей.
Керамические флюсы кроме шлакообразующих компонентов содержат также раскислители и различные легирующие элементы. Их технология изготовления подобна технологии изготовления покрытий качественных электродов. Компоненты тщательно размалывают и в установленной пропорции перемешивают с жтдким стеклом. Приготовленную однородную смесь протирают через сито и получают флюс в виде влажных крупинок размером 1–3 мм. После просушивания и последующего прокаливания при 600–700оС крупинки упрочняются и флюс становится пригодным для использования.
Керамические флюсы применяются для сварки легированных сталей, включая коррозионностойкие, цветных металлов и сплавов.
По химическому составу флюсы классифицируют по содержанию кремния и марганца:
-низкокремнистые флюсы, содержат менее 35% SiO2
-высококремнистые флюсы, содержат более 35% SiO2
-марганцевый, содержит более 1% MnO
-безмарганцевый, содержит менее 1% MnO
-бескислородные флюсы, состоят в основном из фторидных и хлоридных солей металлов. Их применяют при сварке химически активных металлов. Например, флюс АН-А1 для сварки алюминия и его сплавов состоит из 50 %KCl; 20 % NaCl; 30 % Na3AlF6.
Кроме автоматической сварки под слоем флюса есть полуавтоматическая сварка. Она отличается от автоматической тем, что перемещение электродной проволоки вдоль шва производится вручную. Применяется для коротких и прерывистых швов, а также криволинейных, которые нельзя сварить автоматической сваркой.
Так как объем сварочной ванны достаточно велик (10–20 см3, а при ручной дуговой 1–2 см3), то во избежание стекания жидкого металла и флюса сварка этими способами осуществляется только в нижнем положении, т.е. когда шов располагается в горизонтальной плоскости или при очень небольших наклонах свариваемых листов, как правило, не более 7о.
Особенностью сварки под флюсом является возможность глубокого проплавления основного металла. Поэтому при сварке под флюсом металл большой толщины можно сваривать без разделки кромок, но с применением обязательного зазора между листами.
Важное значение имеет качество сборки деталей под сварку. Необходимо обеспечить:
- постоянную величину зазора по всей длине шва;
- защиту обратной стороны шва от вытекания металла из зазора.
Сборка и сварка конструкций производится на специальных стеллажах или приспособлениях. Необходимый зазор и взаимное расположение листов фиксируется прихватками. Чтобы не возникли продольные трещины при переваривании сборочных прихваток в швах, прихватки должны быть длиной 50 мм и отстоять друг от друга на расстоянии 500 мм. При сварке соединений с разделкой кромок прихватки ставят с обратной стороны шва.
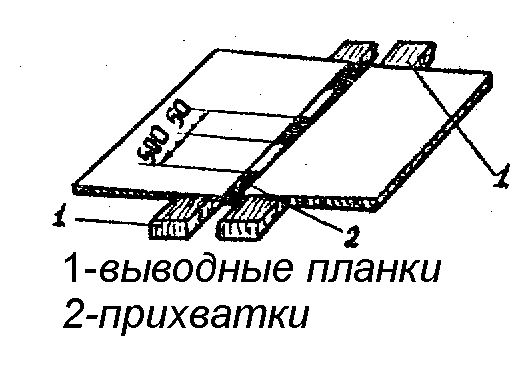
Для удержания жидкого металла в зоне сварки применяют специальные технологические приемы.
1. Флюсовая подушка.
К
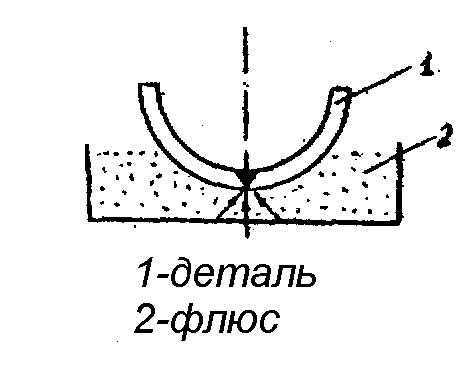
П
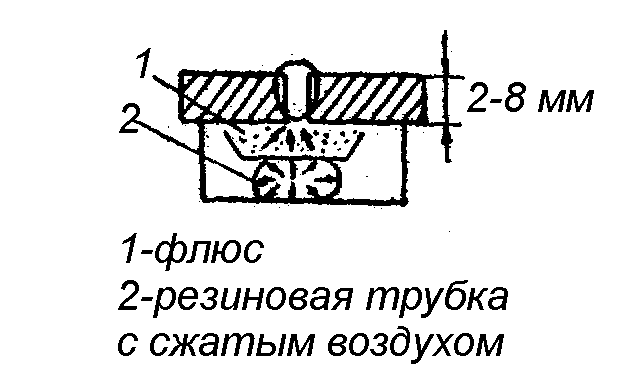
С
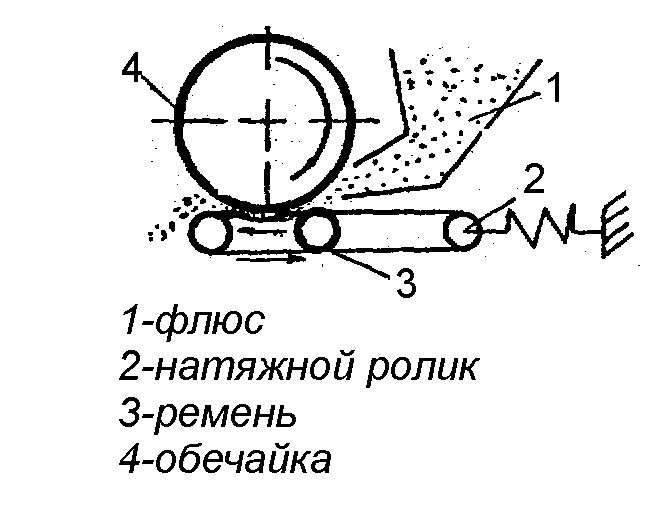
2. Сварка на медной и флюсомедной подкладке.
К
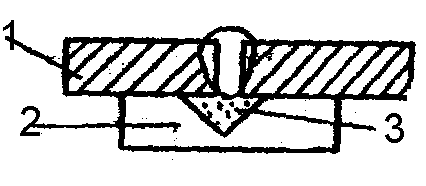
3. Сварка по ручной подварке.
В
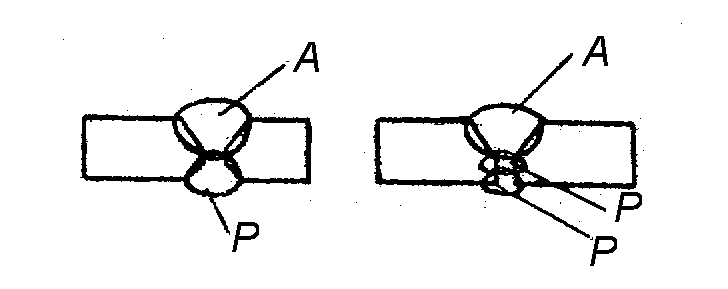
А–автоматический шов
Р–ручная подварка
4. Сварка угловых соединений.
Ч
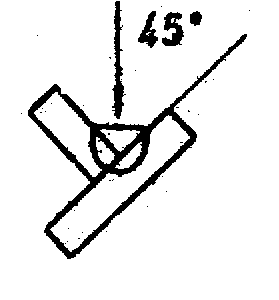