Разработка продукта и выбор технологического процесса в производственной сфере в этой главе
Вид материала | Документы |
- Кафедра технологии машиностроения и методики профессионального обучения курсовой проект, 88.72kb.
- Кафедра технологии машиностроения и методики профессионального обучения курсовой проект, 81.68kb.
- 3 5 Разработка маршрутного технологического процесса, 138.63kb.
- Кафедра технологии машиностроения и методики профессионального обучения курсовой проект, 89.23kb.
- Курсовой проект разработка технологического процесса механической обработки детали, 81.31kb.
- «Разработка технологического процесса изготовления детали «Корпус вибратора», 678.89kb.
- 1 Проектирование технологического процесса, 473.55kb.
- 1. 2 Патентные исследования, 27.99kb.
- Расчетно-пояснительная записка, 642.73kb.
- Барс русское Информационное Агентство, 83.79kb.
Компания Lexus:
постоянный процесс совершенствования продукта
Не так давно в дилерском центре Lexus Automobile, расположенном в Луизиане, произошел следующим случай, ярко характеризующий качество обслуживания клиентов этой компании.
Одна покупательница приобрела автомобиль этой марки, но. спустя неделю, вернулась в дилерский центр очень расстроенной. Дело в том. что она привыкла носить туфли только одной модели, и каблук ее правой туфли постоянно заклинивало педалью акселератора, в результате чего он сломался. Менеджер по обслуживанию клиентов зарегистрировал ее жалобу и предложил денежную компенсацию ущерба.
На этом удовлетворенная клиентка удалилась, решив, что ей вряд ли скоро придется встретиться с представителями компании. Однако неделю спустя на пороге ее дома появился инженер-конструктор японского завода Lexus и попросил показать испорченную туфлю. Он измерил ее. сделал зарисовку и удалился, не произнеся более ни слова.
Через месяц с этой женщиной опять связался дилер компании и попросил ее пригнать машину в дилерский центр. Инженер изменил конструкцию акселератора, в результате чего каблук больше не застревал между педалью и полом. Мастера центра заменили педаль в машине клиентки, и в последнее время эта модернизированная деталь стала стандартом для продукции Lexus.
Источник Tom Taorimina. Virtual Leadership and the ISO 9000 Imperative (Englewood Cliffs. NJ Prentice Hall. 1996). p 158
Развертывание функции качества
Один из методов включения в процесс проектирования конкретных требований будущего потребителя называют развертыванием функции качества (Quality Function Deployment — QFD)3. Этот метод заключается в том, что над разработкой нового продукта работают межфункциональные группы, включающие маркетологов, инженеров-проектировщиков и производственников. По словам официальных лиц из корпорации Toyota Motor Corporation, благодаря методу QFD компании удалось значительно сократить сроки проектирования и снизить стоимость производства своих автомобилей более чем на 60%.
Процесс QFD начинается с изучения мнений потребителей, в результате чего определяется, какими характеристиками должна обладать продукция наивысшего качества. В ходе исследования рынка определяются запросы и предпочтения потребителей, после чего они подразделяются на категории, получившие название требования потребителя. Для иллюстрации этого процесса приведем пример фирмы — производителя автомобилей, которая хотела бы усовершенствовать конструкцию автомобильной дверцы. Проведя интервью и составив обзоры, ей удалось выяснить, что потребители предъявляют к этой части машины два основных требования: "чтобы она оставалась открытой при наклоне автомобиля" и "чтобы она легко закрывалась снаружи". Далее эти требования "взвешиваются" с учетом степени их значимости для будущих автовладельцев, а затем потребителей просят дать оценку продукции компании по сравнению с ее основными конкурентами. Все это позволяет фирме выяснить, какие качества продукции имеют для потребителя наиболее важное значение, и сравнить свою продукцию с конкурирующей. Конечным результатом всей этой работы является правильная оценка и фокусирование усилий на разработке именно тех качеств продукции, которые, по мнению потребителей, нуждаются в улучшении.
Информация о требованиях потребителей заносится в матрицу (рис. 4.4), известную под названием "домик качества" (House of Quality).
Построив такую матрицу, межфункциональная группа QFD может полученные от потребителей сведения использовать в процессе принятия инженерных, маркетинговых и конструкторских решений. С ее помощью группа преобразует требования потребителей в конкретные технологические и инженерные задачи. В "домике качества" происходит взаимное согласование важнейших характеристик продукции с задачами их улучшения и уточнения. Данный процесс стимулирует совместную работу различных подразделений компании, в результате чего они лучше понимают задачи и цели друг друга. Однако самым значительным преимуществом использования этой матрицы является то, что она помогает группам сосредоточить усилия на создании продукции, которая полностью удовлетворяла бы запросам будущих потребителей.
На первом этапе построения "домика качества" составляется перечень требований, предъявляемых потребителем к продукции. Эти требования располагаются в перечне в порядке убывания значимости. Затем проводится еще один опрос потребителей, в ходе которого их просят сравнить продукцию компании с продукцией ее конкурентов. Далее разрабатывается перечень технических характеристик, которые должны соответствовать требованиям потребителя. Затем проводится оценка этих характеристик, и компания либо принимает, либо опровергает высказанное потребителем мнение относительно качеств исследуемой продукции. Полученные в результате данные используются для оценки "плюсов" и "минусов" продукции с точки зрения ее технических характеристик.
Функционально-стоимостный анализ
Для обеспечения наименьшей стоимости при проектировании продукции применяют функционально-стоимостный анализ (Value Analysis/Value Engineering — VA/VE), состоящий из стоимостного и конструкторского анализа. Цель этого анализа заключается в упрощении продукции и технологического процесса, а основная задача—в достижении эквивалентных или даже более высоких показателей совершенства продукции с меньшими затратами при обеспечении всех основных функциональных требований, определенных потребителем. Анализ VA/VE решает эту задачу, отыскивая необязательные затраты и отказываясь от них. Теоретически, анализ стоимости (VA) проводится для продукции, уже находящейся в производстве, и используется для оценки выполнения технических условий продукции и требований, указанных в производственной документации. Обычно такой анализ осуществляется отделами по закупкам материалов в качестве одного из способов сокращения издержек. Что касается анализа стоимости в процессе разработки продукта, то он выполняется перед стадией производства и рассматривается как метод, позволяющий избежать избыточной стоимости. На практике, однако, между двумя этими видами анализа, применяемыми к конкретной продукции, существует тесная связь. Это происходит потому, что новые материалы, технологические процессы и тому подобное, применение которых следует из анализа стоимости VA, требуют проведения нового конструкторского анализа VE, выполняемого в рамках проектирования. Анализ VA/VE выполняется, чтобы получить ответ на следующие важные вопросы.
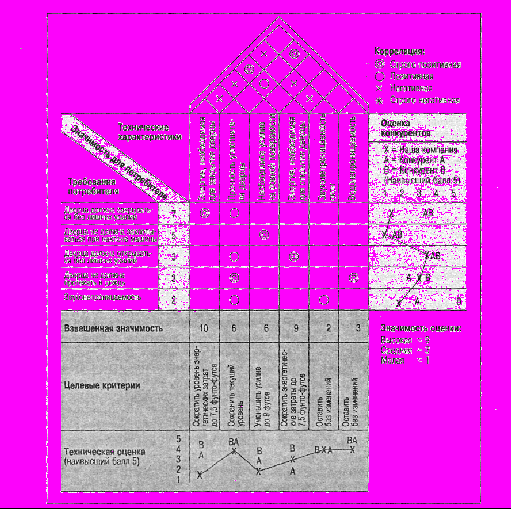
Рис. 4.4. Заполненная матрица «домика качества» для дверцы автомобиля
Источник. По материалам статьи John R. Mauser and Don Clausing, "The House of Quality", Harvard Business Review, May-June 1988, p. 62-73.
- Не обладает ли данная продукция качествами, которые не являются для нее необходимыми?
- Нельзя ли объединить две или несколько деталей в одну?
- Каким образом можно уменьшить массу изделия?
- Какие нестандартные детали можно удалить из конструкции?
В следующем разделе описан формальный подход, который часто применяется для управления процессом проектирования и улучшения конструкции продукта.
Конструкторский анализ процесса сборки
Английское слово design имеет множество разных значений. Иногда оно означает эстетическое оформление (дизайн) изделия, например форму автомобиля, текстуру материала, форму и отделку консервного ножа. В другом случае это слово означает процесс определения базовых параметров какой-либо системы. Так, например, прежде чем приступить к рассмотрению деталей, дизайн энергоагрегата может означать процесс определения характеристик его отдельных элементов: генератора, насосов, бойлеров, соединительной системы и т.д.
Существует и еще одна интерпретация английского слова design, согласно которой оно означает процесс детализации сведений о материалах, формах и допустимых отклонениях всех отдельных деталей продукта, т.е. его проектирование. Именно этой теме посвящен данный раздел. Проектирование — это деятельность, которая начинается с создания чертежей компонентов и сборочных узлов и осуществляется в системе автоматизированного проектирования (Computer-Aided Design — CAD). Процесс автоматизированного проектирования подробно описан в дополнении к этой главе. При этом создаются подробные чертежи отдельных деталей и все сборочные чертежи. Затем готовые чертежи передаются инженерам разработке процесса сборки и инженерам-технологам, дача которых заключается в создании и оптимизации производственного процесса, на основе которого будет производиться продукция после окончания проектированная. Зачастую именно на этой стадии обнаруживаются проблемы, связанные с производством и сборкой, и делаются заявки о необходимости изменения конструкции. Довольно часто эти изменения бывают настолько существенны, что приводят к значительным дополнительным расходам и в конечном итоге могут стать причиной задержки срока выпуска новой продукции.
Традиционное отношение проектировщиков к производственному процессу можно описать следующим образом: "Мы это спроектировали, а вы производите". Сегодня для такого подхода даже введен новый термин — "работа через стену". Это означает, что проектировщики как бы сидят с одной стороны стены и "перебрасывают" через нее готовый проект инженерам-технологам, отгораживаясь от дальнейшей деятельности. В результате последним приходится разбираться со всеми проблемами, возникающими из-за того, что их мнение в ходе проектирования продукции не учитывалось. Один из способов избежать такой ситуации предполагает постоянные консультации проектировщиков с инженерами-технологами, т.е. групповой подход. Создаваемые с этой целью группы совместной инженерной разработки нуждаются в специальных инструментах для анализа, помогающих изучать предложенные проекты и оценивать их с точки зрения сложности и стоимости производства.
Сущность конструкторского анализа
Рассмотрим пример конструкторского анализа с точки зрения процесса сборки изделия (Design for Assembly Analysis — DFA)4. На рис. 4.5 изображен узел электропривода с датчиком положения, перемещающийся по двум стальным направляющим полозкам.
Такой привод применяется для автоматического управления открытием и закрытием окна, как, например, в торговых точках McDonald's, обслуживающих водителей прямо в автомобилях. По техническим нормам устройство должно быть помещено в цельный корпус со съемной крышкой для доступа к механизму настройки позиционного датчика. Основное требование к устройству заключается в том, что оно должно иметь жесткое основание, спроектированное таким образом, чтобы узел мог скользить вверх и вниз по направляющим, служащим опорой для привода, и чтобы датчик размещался в определенном положении. Мотор и датчик должны быть соединены проводами с источником тока и блоком управления.
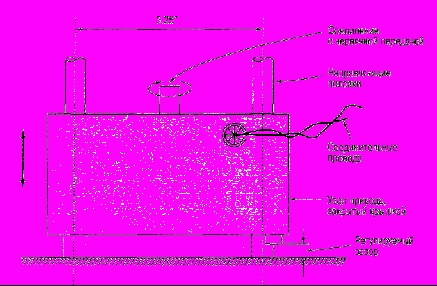
Рис. 4.5. Узел электропривода
Первоначально предложенное конструкторами решение представлено на рис. 4.6.
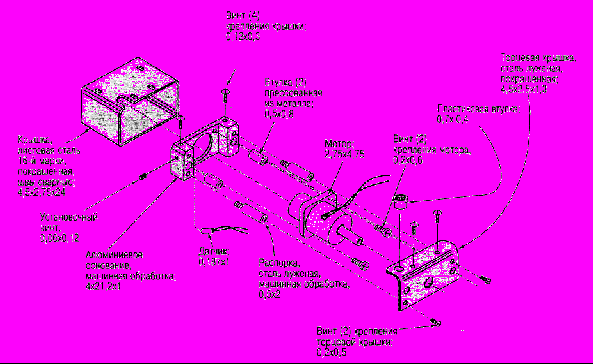
Рис. 4.6. Предложенная конструкция электропривода
В основании есть две втулки с вкладышами, которые предохраняют отверстия от быстрого износа. Мотор крепится к основанию двумя винтами, а в отверстие вставляется цилиндрический датчик, прикрепляющийся с помощью установочного винта. Чтобы корпус соответствовал техническим требованиям, торцевая крышка для создания зазора крепится к двум распоркам, которые в свою очередь привинчиваются к основанию. Во избежание закорачивания проводов при соприкосновении с металлической крышкой, на торцевой крышке устанавливается пластиковая втулка, через которую и пропускается электропроводка. И наконец, крышка в форме коробки закрывает снизу весь узел и привинчивается четырьмя винтами: два — крепят ее к основанию, а другие два — к торцевой крышке.
Таким образом, в соответствии с предложенным проектом устройство состоит из 19 комплектующих, собрав которые, вы получите требуемый электропривод: два сборочных узла (мотор и датчик), еще восемь основных деталей (крышка, основание, две втулки, две распорки, пластиковая втулка и торцевая крышка) и восемь винтов.
Основные усовершенствования на стадии проектирования продукции для облегчения сборки и производства достигаются упрощением изделия, т.е. сокращением количества отдельных входящих в нее деталей. В помощь проектировщику, занятому решением этой задачи, предлагается три критерия, по которым специалист оценивает каждую комплектующую, входящую в изделие.
- Будет ли данная деталь перемещаться относительно остальных в процессе эксплуатации изделия?
- Обязательно ли изготавливать данную деталь из материала, отличного от материала других деталей? Необходимо ли ее выделить в отдельную деталь?
- Должна ли деталь легко отделяться ото всех остальных с тем, чтобы впоследствии можно было разобрать изделие для наладки или технического обслуживания?
Применив эти критерии к рассматриваемому нами примеру, получим следующие результаты.
- Основание. Поскольку с этой детали начинается сборка и нет деталей, которые можно с ней объединить, теоретически она является необходимой.
- Две втулки. Эти детали не удовлетворяют второму критерию. Теоретически основание и втулку можно изготовить из одного и того же материала.
- Мотор. Мотор является отдельным сборочным узлом и закупается у поставщика. Все критерии неприменимы.
- Два винта крепления мотора. В большинстве случаев отдельные крепежные элементы не столь уж необходимы, поскольку можно предусмотреть крепление непосредственно на какой-либо другой детали (например, защелкивать деталь в нужном месте).
- Датчик. Еще один стандартный компонент. Критерии неприменимы.
- Крепежный винт. То же самое, что и в п. 4, необязателен.
- Две распорки. Не удовлетворяют второму критерию, поскольку распорки можно сделать в основании.
- Торцевая крышка. Она должна быть съемной и обеспечивать возможность разбирать узел (следует применить все три критерия).
- Два винта крепления торцевой крышки. Необязательны.
- Пластиковая втулка. Можно изготовить из того же материала, что торцевую крышку и, следовательно, можно объединить с ней.
- Крышка. Можно объединить с торцевой крышкой.
- Четыре винта для крышки. Необязательны.
Исходя из результатов такого анализа, делаем вывод, что если спроектировать устройство таким образом, чтобы отдельные сборочные узлы (мотор и датчик) крепились к основанию без винтов, и сконструировать пластиковую крышку, крепящуюся по такому же принципу, то вместо 19 отдельных компонентов понадобится всего 4. Эти четыре комплектующие представляют собой теоретически минимальное число деталей, необходимых с учетом всех ограничений, для выполнения основной функции изделия.
На данном этапе задача проектной группы заключается в том, чтобы оправдать включение в проект деталей, не входящих в теоретический минимум. Их доводы основываются на аргументах практического, технического либо экономического характера. В данном примере, например, можно указать, что два винта необходимы для закрепления мотора, и один установочный винт — для крепежа датчика, поскольку любые другие варианты крепежа нецелесообразны для продукции, выпускаемой малыми партиями (таковым является рассматриваемый нами электропривод). Однако место установки этих винтов можно изменить так, чтобы ускорить процесс сборки.
На рис. 4.7 изображен чертеж перепроектированного электропривода, состоящего теперь всего из семи отдельных деталей.
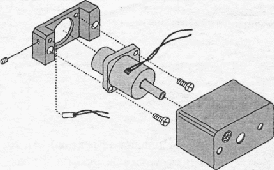
Рис. 4.7. Устройство электропривода, перепроектированного по результатам конструкторского анализа процесса сборки (Design for Assembly Analysis — DFA)
Обратите внимание на то, какие комплектующие были удалены. Новая пластиковая крышка спроектирована таким образом, что крепится к основанию без винтов. Поскольку новая модель состоит из меньшего количества деталей, сборка ее будет проще, и, соответственно, значительно сократятся издержки ее производства.
Реальный пример конструкторского анализа, проводимого на ранней стадии проектирования, приведен во врезке "Новый дешевый двигатель фирмы Toyota".
НОВАЦИЯ
Новый дешевый двигатель фирмы Toyota
"Если говорить о фирме Toyota, особенно о ее нововведениях с целью повышения эффективности и снижения издержек производства, следует отметить, что она всегда была и остается примером для подражания, — отметил аналитик по вопросам автомобилестроения Дэйв Андреа (Rodney & Co., Детройт). Ее успехи в этой области просто непостижимы".
Японский производитель автомобилей номер 1, фирма объявила, что в следующем месяце в Японии поступит в продажу новая модель, оснащенная "простым и мощным" двигателем, разработанным специалистами этой компании. Производство этого двигателя обойдется фирме в три разе дешевле, чем двигатель старой конструкции, поскольку в него входит в три раза меньше деталей.
Хотя компания не раскрывает всех подробностей, эксперты автомобилестроения предсказывают, что при таких условиях двигатель, производство которого обычно обходилось в 600 долларов, теперь будет стоить фирме не больше 400 долларов. В отрасли промышленности, в которой компании экономят буквально на всем, чтобы хоть немного снизить производственные расходы, такая экономия означает неоценимое конкурентное преимущество.
Экономия путем изменения проекта
Финансовый директор фирмы Риюджи Араки подтвердил, что Toyota действительно стремится сократить издержки производства, улучшив проект продукции. По его словам, кроме двигателей, компания напряженно работает над такими важнейшими комплектующими автомобиля, как коробка передач, карданный вал, мост, платформа и шасси. Все это смещает основное внимание фирмы в области снижения издержек производства и переносит его из заводских цехов (где компания на протяжении многих лет была лидером в своей отрасли промышленности) на чертежную доску.
По заявлению официальных лиц фирмы Toyota, за полгода, с апреля по сентябрь 1996 года, компания сэкономила 500 миллионов долларов, причем преимущественно благодаря усовершенствованию процесса проектирования на ранней фазе разработки базовой концепции. Такие заявления чрезвычайно нервно воспринимаются другим крупнейшим производителем автомобилей, компанией Detroit, которая в прошлом году выигрывала у своих японских конкурентов благодаря ценовому преимуществу.
Слухи о новом всплеске эффективности фирмы Toyota весьма серьезно воспринимаются всеми, кто одобряет общую культуру этой компании. Toyota поощряет своих инженеров и поставщиков искать возможности значительной экономии, а не сокращения издержек производства на пару йен на каждую деталь. Основываясь на экономии, достигнутой благодаря высокому качеству проектных работ, фирма также постоянно стимулирует своих поставщиков. По мнению аналитика по промышленным вопросам Кристофера Седергрена (Сайта-Ана, штат Калифорния): "Это просто-напросто очередное доказательство того, что Toyota — настоящий лидер в сфере снижения издержек производства".
Стремление фирмы Toyota к постоянному снижению издержек производства подкрепляется также ее значительным бюджетом, выделенным на научно-исследовательские работы. Только с апреля по сентябрь 1996 года затраты фирмы на эту деятельность увеличились по сравнению с первоначальными финансовыми планами на 52,5 миллиардов йен (468,6 миллионов долларов), а до конца финансового года (он истекает 31 марта) компания планировала инвестировать в исследования 300 миллиардов йен.
Источник. "Toyota to Unveil Low-Cost Engine Next Month", The Wall Street Journal, November 11, 1996. Перепечатано с разрешения The Wall Street Journal © Dow Jones & Company, Inc. Все права защищены.
Выбор технологического процесса
Отличие выбора процесса от его планирования
Инженерное проектирование технологического процесса (как мы видим, оно включено в число основных фаз создания новой продукции, изображенной на рис. 4.1) — это область деятельности, непосредственно связанная с планированием операций, т.е. с регулярным принятием тактических решений в производственном процессе. Выбор процесса, наоборот, относится к стратегическим решениям, которые определяют, какие технологии следует использовать на заводе. Вспомним пример с электроприводом. В этом случае, поскольку данная продукция выпускается малыми объемами, можно просто поставить одного рабочего, который будет изготавливать небольшие партии устройств. Но если объемы производства очень велики, целесообразно заняться созданием сборочной линии.
Типы технологических процессов
В самом общем виде производственные процессы можно разделить на следующие категории.
Процессы переработки (Conversion Processes). В качестве примера можно привести переработку железной руды в стальной прокат либо объединение всех ингредиентов, перечисленных на коробке с зубной пастой, в пасту.
Процессы изготовления (Fabrication Process). Примером такого процесса может служить преобразование сырья в какую-либо специфическую форму (например, штамповка листовой стали, в результате чего получаются крылья для автомобилей, или формовка золота в зубную коронку).