Управления технологическими процессами 10
Вид материала | Документы |
- Вавилова в процессе проведения экзамена и приема зачетов по 2-м модулям дисциплины, 130.51kb.
- Гост 27883-88. Средства измерения и управления технологическими процессами. Надежность., 11.02kb.
- Автоматизированная система управления технологическими объектами хранения и реализации, 212.74kb.
- Справочник базовых цен на разработку технической документации на автоматизированные, 599.84kb.
- Справочник базовых цен на разработку технической документации на автоматизированные, 684.81kb.
- Основы построения автоматизированных систем иерархически-взаимосвязанного управления, 455.86kb.
- Методические указания к курсовому проектированию по дисциплине "проектирование автоматизированных, 973.54kb.
- Основы построения автоматизированных систем иерархически-взаимосвязанного управления, 455.78kb.
- Техническое задание для разработки системы автоматизированного управления технологическими, 501.34kb.
- 107. Бунке А. С., Мовчан А. П. Использование искусственного интеллекта для оптимизации, 1425.26kb.
ООО НПФ “C.Т.А. ТЕХНИКА” ПЗ-96402, л.
СОДЕРЖАНИЕ
КИП И АВТОМАТИКА 3
АВТОМАТИЧЕСКАЯ СИСТЕМА УПРАВЛЕНИЯ ТЕХНОЛОГИЧЕСКИМИ ПРОЦЕССАМИ 10
Структурное описание системы 18
Уровень 1 18
Датчики и устройства сбора данных 18
Устройства распределённого ввода/вывода 18
Программируемые контроллеры 19
Сетевое коммуникационное оборудование 20
Уровень 2 21
Операторские станции 21
Инжиниринговая станция 22
Программаторы 23
Сервер баз данных 23
Принтеры 24
Сетевое коммуникационное оборудование 24
Программное обеспечение 25
Системное программное обеспечение Уровня 1 25
Прикладное программное обеспечение Уровня 1 26
Системное программное обеспечение Уровня 2 26
Прикладное программное обеспечение Уровня 2 28
Функциональное описание системы 29
Подсистема контроля и регулирования параметров работы сульфатного отделения 29
Подсистема контроля и регулирования параметров работы бензольного отделения 30
Подсистема контроля и регулирования параметров работы машинного зала и насосной конденсации 31
Подсистема централизованного диспетчерского контроля работы объектов цеха улавливания 32
СИСТЕМЫ СВЯЗИ, АВТОМАТИЧЕСКИЕ УСТАНОВКИ ПОЖАРНОЙ СИГНАЛИЗАЦИИ, АВТОМАТИЧЕСКАЯ ОХРАННАЯ СИГНАЛИЗАЦИЯ. 34
Системы связи 34
Автоматические установки пожарной сигнализации. 35
Автоматическая охранная сигнализация. 36
КИП И АВТОМАТИКА
Целью данной разработки является оснащение КИП и А следующих объектов:
- машинного зала;
- трубчатых газовых холодильников;
- механизированных осветлителей;
- насосной конденсации с наружным оборудованием и аммиачного отделения;
- сульфатной установки;
- склада реактивов;
- бензольно-скруберного отделения.
Проект автоматизации технологического процесса во всех отделениях охватывает не только вновь проектируемое оборудование, но и предусматривает замену устаревших приборов на существующем оборудовании не подлежащем замене.
Для измерения давления и перепадов давления применяются современные датчики «Метран» с выходом 4-20мА. Измерение расходов конденсата коксового газа и смолы осуществляется массовыми расходомерами основанными на кориолисовом методе измерения имеющие высокую точность измерения и позволяющие измерять расходы независимо от электропроводности, вязкости и плотности продукта.
Для измерения уровней агрессивных и высоковязких сред в проекте применяются радиоволновые уровнемеры Барс 341И Приборостроительного предприятие «Контакт-1», г. Рязань; ультразвуковые датчики и сигнализаторы уровня ОАО «Теплоприбор», измерение уровня раздела фаз "вода-смола" в механизированном осветлителе надсмольной воды осуществляется посредством ультразвуковых датчиков.
Вся информация от датчиков передается на контроллер, на котором реализуются задачи регулирования, формируются необходимые сигналы для блокировок, технологической и аварийной сигнализации. Информация о состоянии параметров технологического процесса отображается на рабочих станциях оператора.
Система автоматизации машинного зала предусматривает измерение и регулирование разрежения перед газодувными машинами, контроль температуры коксового газа до и после газодувных машин, измерение давления коксового газа после газодувных машин. Контролируется также температура подшипников газодувных машин.
Автоматизация технологического процесса в трубчатых газовых холодильниках позволяет контролировать следующие параметры:
- температура коксового газа до ПГХ №№1-6,
- разрежение коксового газа до и после ПГХ №№1-6,
- температура коксового газа после каждого холодильника,
- разрежение коксового газа после каждого холодильника,
- температура охлажденной оборотной технической воды на ПГХ,
- охлажденной оборотной технической воды на ПГХ,
- расход охлажденной оборотной технической воды на ПГХ,
- температура охлажденной оборотной технической воды перед каждым холодильником,
- давление охлажденной оборотной технической воды перед каждым холодильником,
- температура нагретой оборотной технической воды после ПГХ,
- давление нагретой оборотной технической воды после ПГХ,
- температура и давление нагретой оборотной технической воды после каждого холодильника,
- температура конденсата коксового газа и водосмоляной смеси в сборниках Y10-1.3 и Y10-1.4,
- уровень конденсата коксового газа и водосмоляной смеси в сборнике Y10-1.4,
- давление в линии нагнетания насосов для смеси конденсата коксового газа и смолы,
- расход с откачиваемого конденсата коксового газа и смолы в мехосветлитель,
- давление в линии нагнетания насосов для откачки ливневых вод,
- температура подшипников насосов для смеси конденсата коксового газа и смолы и насосов для откачки ливневых вод,
- расход откачиваемых ливневых вод,
- давление пара на установку,
- температура пара на установку,
- давление азота на установку,
- температура азота на установку.
Осуществляется также измерение и расчет таких хозрасчетных величин, как расход пара на установку и расход азота на установку.
Регулируется расход смеси конденсата коксового газа и смолы на промывку ПГХ и уровень конденсата коксового газа и водосмоляной смеси в сборнике в сборнике Y10-1.3.
Проектом предусматривается сигнализация минимального и максимального уровня в сборниках Y10-1.3 и Y10-1.4, а также блокировки при отсутствии давления на трубопроводе нагнетания насосов и повышения температуры подшипников насосов.
Автоматизация технологического процесса механизированных осветлителей позволяет контролировать следующие параметры:
- температура в мехосветлителе надсмольной воды,
- температура в мехосветлителе конденсата коксового газа,
- уровень в мехосветлителе надсмольной воды,
- уровень раздела фаз в мехосветлителе надсмольной воды,
- уровень в мехосветлителе конденсата коксового газа,
- уровень раздела фаз в мехосветлителе конденсата коксового газа,
- уровень в сборнике Y10-2.3,
- давление в линии нагнетания насосов,
- температура подшипников насосов,
- расход пара к мехосветлителю конденсата коксового газа,
- давление пара к мехосветлителю конденсата коксового газа,
- температура пара к мехосветлителю конденсата коксового газа,
- давление паров в стабилизаторе давления,
- расход азота в коллекторную систему,
- давление паров в коллекторной системе.
В проекте предусматривается измерение уровня раздела фаз "вода-смола" в механизированном осветлителе надсмольной воды посредством ультразвуковых датчиков которые посылают акустические импульсы с узким конусом. Измерительный преобразователь определяет время между отправкой импульса и приемом отражения и вычисляет расстояние от сенсора до уровня смолы в осветлителях и передает информацию в контроллер. При превышении уровня смолы в механизированном осветлителе выше заданного контроллер формирует и выдает команду на включение звуковой и световой сигнализации на операторский пункт.
Уровень в сборнике Y10-2.3 поддерживается за счет регулирования количества откачиваемой из сборника смолы. Работа насосов сблокирована с уровнем в сборнике, также предусматривается защита насосов от работы "всухую".
Автоматизация технологического процесса насосной конденсации и аммиачного отделения позволяет контролировать следующие параметры:
- расход пара в насосную и к наружному оборудованию,
- расход воды на каждую аммиачную колонну,
- расход пара на каждую аммиачную колонну,
- давление технической воды,
- давление паров в аммиачных колоннах,
- температура в аммиачных колоннах,
- температура технической воды,
- уровень в промсборниках,
- уровень в аммиачном хранилище №№ 1-2,
- уровень смолы в хранилище №№ 1-2,
- температура щелочи в сборнике подготовки щелочи,
- температура после подогревателя смолы,
- разрежение в коллекторе объединения воздушек,
- давление азота в трубопроводе,
- уровень воды в миксте,
- расход щелочи на насосы подачи воды на аммиачные колонны,
- температура азота после подогревателя,
- расход смолы в смолоперегонный цех,
- температура подшипников насосов,
В проекте предусматривается регулирование температуры в отстойнике, резервуарах избыточной надсмольной воды, уровня надсмольной воды в промежуточном резервуаре.
Сигнализация уровней в промсборниках надсмольной воды, в аммиачном хранилище, смолы в хранилище №№ 1-2, давления надсмольной воды на нагнетании насоса , а также блокировки при отсутствии давления на трубопроводе нагнетания насосов и повышения температуры подшипников насосов предусматриваются.
Автоматизация технологического процесса сульфатного отделения позволяет контролировать следующие параметры:
- сопротивление сатураторов,
- температура в ванне сатуратора,
- температура газа после газоподогревателей,
- температура воды на промывку сульфата,
- давление коксового газа до сатураторов,
- расход пара низкого давления на сульфатное отделение,
- давление технической воды после фильтра,
- расход азота на перемешивание сатураторов,
- температура коксового газа перед каждым сатуратором,
- температура воздуха в сушке сульфата №1 и №2,
- давление воздуха под кипящим слоем сушки №1 и №2,
- кислотность маточного раствора в кристаллоприемниках, рН,
- кислотность в ванне сатураторов.
Кроме того, проектом предусматривается регулирование кислотности в ванне сатураторов, температура газа после газоподогревателей, заданной разницы между температурой в ванне сатураторов и температурой газа после газоподогревателей, температуры воды на промывку сульфата, температура воздуха в сушке сульфата.
Автоматизированная система управления технологическим процессом бензольно-скрубберного отделения позволяет:
- давление коксового газа до КГХ №1 и №2,
- давление коксового газа после КГХ №1 и №2,
- давление коксового газа после скруббера №1,
- давление коксового газа после скруббера №2,
- температура коксового газа до и после КГХ №1 и №2,
- расход «грязной» воды на КГХ №1 и №2,
- расход чистой воды на теплообменники,
- расход «грязной» воды (общий),
- температура «чистой» и «грязной» воды на теплообменники,
- температура масла в нафталинопромывателе,
- расход поглотительного масла на скрубберы.
- уровень воды в промсборнике,
- уровень масла в сборнике чистого масла,
- уровень масла в сборнике « грязного» масла,
- уровень в сборнике конденсата газа,
- давление пара низкого давления,
- расход пара низкого давления на бензольное отделение,
- температура пара низкого давления на бензольное отделение,
- уровень в скруббере,
- температура в верхней и нижней части отпарной колонны,
- давление в верхней и нижней части отпарной колонны,
- температура в верхней и нижней части разделительной колонны,
- давление в верхней и нижней части разделительной колонны,
- расход масла на отпарную колонну,
- расход сырого бензола на разделительную колонну.
Кроме того, проектом предусматривается регулирование расхода пара на отпарную колонну, расхода пара на нафталиновую колонну, расхода пара на решифер для нагрева масла бензине, расхода пара на нагреватель разделительной колонны, расход и давление газа на трубчатую печь.
Автоматизация склада реактивов позволяет контролировать следующие параметры:
- температура щелочи в резервуаре,
- температура серной кислоты после насосов,
- температура щелочи после насосов,
- температура на коллекторе пара,
- уровень в резервуаре для серной кислоты,
- уровень в резервуаре для щелочи,
- уровень в сборнике для опорожнения кислотных коммуникаций,
- давление после насосов серной кислоты,
- давление после насосов щелочи,
- давление на коллекторе пара,
- расход пара на склад.
Кроме того, проектом предусматривается регулирование температуры щелочи в резервуаре подачей пара в подогреватели. Работа насосов сблокирована с уровнями в соответствующих резервуарах.
АВТОМАТИЧЕСКАЯ СИСТЕМА УПРАВЛЕНИЯ ТЕХНОЛОГИЧЕСКИМИ ПРОЦЕССАМИ
Предлагаемая система автоматизации цеха улавливания №1 представляет собой распределённую систему, являющуюся совокупностью универсальных и специализированных вычислительных средств и узлов распределённой обработки данных, объединённых структурированной коммуникационной системой для решения задач контроля и управления непрерывными технологическими процессами цеха улавливания №1 ОАО «Северсталь» в реальном масштабе времени.
Основная цель создания настоящей системы заключается в обеспечении оперативной информационно-технологической и аналитической поддержки процедур принятия решений эксплуатационным персоналом цеха улавливания №1 и накоплении статистических материалов с целью обеспечения полной автоматизации управления и регулирования технологического процесса улавливания химических продуктов.
Основными целями предлагаемой системы автоматизации цеха улавливания №1 являются:
- увеличение производительности объектов цеха улавливания и срока их службы;
- обеспечение непрерывности и правильности управления технологическим процессом;
- повышение надежности управления;
- снижение энергопотребления;
- контроль состояния производства;
- уменьшение стоимости производства и обслуживания технологического процесса путем использования однородных аппаратно-программных компонентов;
- облегчение задач управления путем использования дружественного к пользователю человеко-машинного интерфейса;
- улучшение состояния окружающей среды и безопасности производства;
- обеспечение оперативной информационно-технологической и аналитической поддержки процедур принятия решений эксплуатационным персоналом.
- эффективное предоставление управляющему персонала завода информации, необходимой для управления предприятием.
Система решает следующие задачи:
- оперативный сбор, обработка, документирование и отображение информации о протекании технологических процессов, их регулирование по заданным законам;
- регулирование хода технологического процесса по заданным законам;
- обеспечение ритмичности протекания технологических процессов;
- улучшение условий труда оператора и обслуживающего персонала, за счёт сокращения затрат ручного труда в управлении и контроле технологическими процессами;
- улучшение технико-экономических показателей работы цеха улавливания;
- предупреждение или сведение к минимуму неблагоприятных воздействий на окружающую среду.
Функционально система построена по модульному принципу и включает в себя следующие подсистемы:
- контроль и регулирование параметров работы сульфатного отделения;
- контроль и регулирование параметров работы бензольного отделения;
- контроль и регулирование параметров работы машинного зала и насосной конденсации;
- централизованный диспетчерский контроль работы объектов цеха улавливания;
Все подсистемы, решая возложенные на них задачи и являясь функционально законченными, связаны между собой, работают на едином аппаратно-программном обеспечении и используют в своей работе данные, полученные из других подсистем.
Общая функциональная схема системы приведена на прилагаемом чертеже «Схема функциональная».
Структурно система построена по иерархическому принципу и является двухуровневой.
На Уровне 1 осуществляется сбор информации по технологическим параметрам от измерительных приборов и логический контроль, а также управление технологическими процессами и механизмами. Технические средства этого уровня представлены:
- датчиками и полевыми устройствами;
- устройствами распределённого ввода/вывода;
- программируемыми логическими контроллерами;
- сетевым коммуникационным оборудованием;
На Уровне 2 реализуется централизованный мониторинг и управление технологическими процессами, используя системы человеко-машинного интерфейса на рабочих станциях. Этот уровень представлен:
- операторскими станциями;
- инжиниринговой станцией;
- сервером баз данных;
- вспомогательными периферийными устройствами (принтерами);
- сетевым коммуникационным оборудованием.
Общая структурная схема системы приведена на прилагаемом чертеже «Схема структурная».
Технически система построена с использованием комплекса PCS7 производства SIEMENS AG. Аппаратные и программные продукты и решения от SIEMENS AG покрывают все уровни и реализуют все необходимые функции системы, начиная от сбора данных от технологических объектов и заканчивая связью автономных объектов производства информационной сетью. Наличие на всех уровнях продуктов от одного поставщика существенно упрощает и удешевляет процесс монтажа, наладки, программирования, обслуживания и поддержки системы, гарантирует соответствие всех компонентов системы предъявляемым требованиям по надёжности, расширяемости, возможности модернизации и замены, удобству работы и обслуживания. Система PCS7 предоставляет полный набор средств для создания современных распределенных систем управления, обеспечивая все стадии сбора, контроля, обработки и хранения данных, проектирования, диагностики, визуализации, связи с заводским уровнем управления. В качестве дополнительного системного программного обеспечения (серверы Web, серверы баз данных) также используются продукты производства Microsoft Corporation, тесным образом интегрированные с операционными системами этой же фирмы, что повышает надёжность и производительность этих средств. Программное обеспечение SIEMENS AG рассчитано на работу в операционных средах Microsoft и оптимизировано именно для этих систем.
Топологически система представляет собой совокупность автономных объектов производства, управляемых из диспетчерских и операторских пунктов. Пункты, между которыми необходим обмен информацией, соединяются между собой сетью Industrial Ethernet, с использованием оптоволоконных линий связи. Таким образом, каждый объект, управляясь локально из соответствующего диспетчерского пункта, включен в информационную сеть производства, предоставляя доступ к собственным данным и получая необходимые данные от других объектов. Внутри каждого объекта элементы системы автоматизации связаны между собой сетями разного типа. На Уровне 1 используются сети PROFIBUS-DP/MPI (для подключения распределённой периферии к контроллерам.
На Уровне 2 для связи между рабочими станциями и серверами используется электрическая сеть Ethernet и стандартный протокол передачи данных TCP/IP. Для связи между Уровнем 1 и 2 используются электрические и оптические сети Industrial Ethernet и ISO-совместимый протокол. Такая коммуникационная структура позволяет обеспечить гибкость, надёжность, возможность расширения и подключения новых объектов и устройств на любом уровне, гарантирует передачу разных типов информационных данных по разным сетям, что уменьшает загрузку и увеличивает производительность сетевого обмена.
Коммуникационные соединения внутри системы автоматизации цеха улавливания №1 приведены на прилагаемом чертеже «Схема структурная».
Организационно система предполагает наличие персонала, обученного и обладающего достаточной квалификацией для работы с системой и её обслуживания. Предусмотрен доступ к системе следующих типов и групп пользователей, в каждую из которых может входить произвольное количество членов:
- в группу «Гости» входят пользователи с самыми низкими полномочиями на работу с системой. Члены этой группы не имеют права доступа к аппаратной конфигурации и осуществлению процессов управления, но могут просматривать текущую и архивную системную информацию в виде мнемосхем, трендов, отчётов, таблиц, журнала нарушений.
- в группу «Операторы» входят пользователи, осуществляющие непосредственное управление объектами производства. Члены этой группы могут делать все те же действия, что и члены группы «Гости», однако в дополнение к этому могут выполнять необходимые операции по ручному и автоматическому регулированию, подтверждать системные сообщения, снимать аварийные и блокировочные сигналы, изменять уставки и режим работы объектов управления в соответствии с текущей информацией.
- в группу «Инженеры» входят пользователи, осуществляющие контроль и сопровождение работы, как системы, так и объектов управления. Обладая всеми правами членов группы «Операторы», члены группы «Инженеры» могут дополнительно выполнять запуск/остановку работы компонентов системы, замену неисправных аппаратных модулей, добавление/удаление технологических параметров, коммутацию сетевого оборудования, проведение профилактических и, при необходимости, восстановительных работ, модификацию и переконфигурирование экранных форм, отчётных документов, алгоритмов управления и технологических программ. Члены этой группы осуществляют полное сопровождение системы в течение всего её жизненного цикла, и ответственны за поддержание всех её элементов в рабочем состоянии.
- в группу «Администраторы» входят пользователи, в обязанности которых входит управление группами и пользователями системы, в частности, добавление, удаление и перевод пользователей в другие группы, а также назначение им соответствующих прав доступа. Администратор ведёт полный список пользователей системы и является ответственным за обеспечение реализации возможности доступа и работы с системой всех пользователей.
Каждый пользователь идентифицируется в системе уникальным именем и аутентифицируется паролем, вводимым с клавиатуры операторской или инжиниринговой станции при входе в систему. В системе ведётся учёт и аудит событий входов/выходов различных пользователей для возможности последующего анализа соответствующими службами.
Подробное структурное и функциональное описание элементов системы приведено ниже.
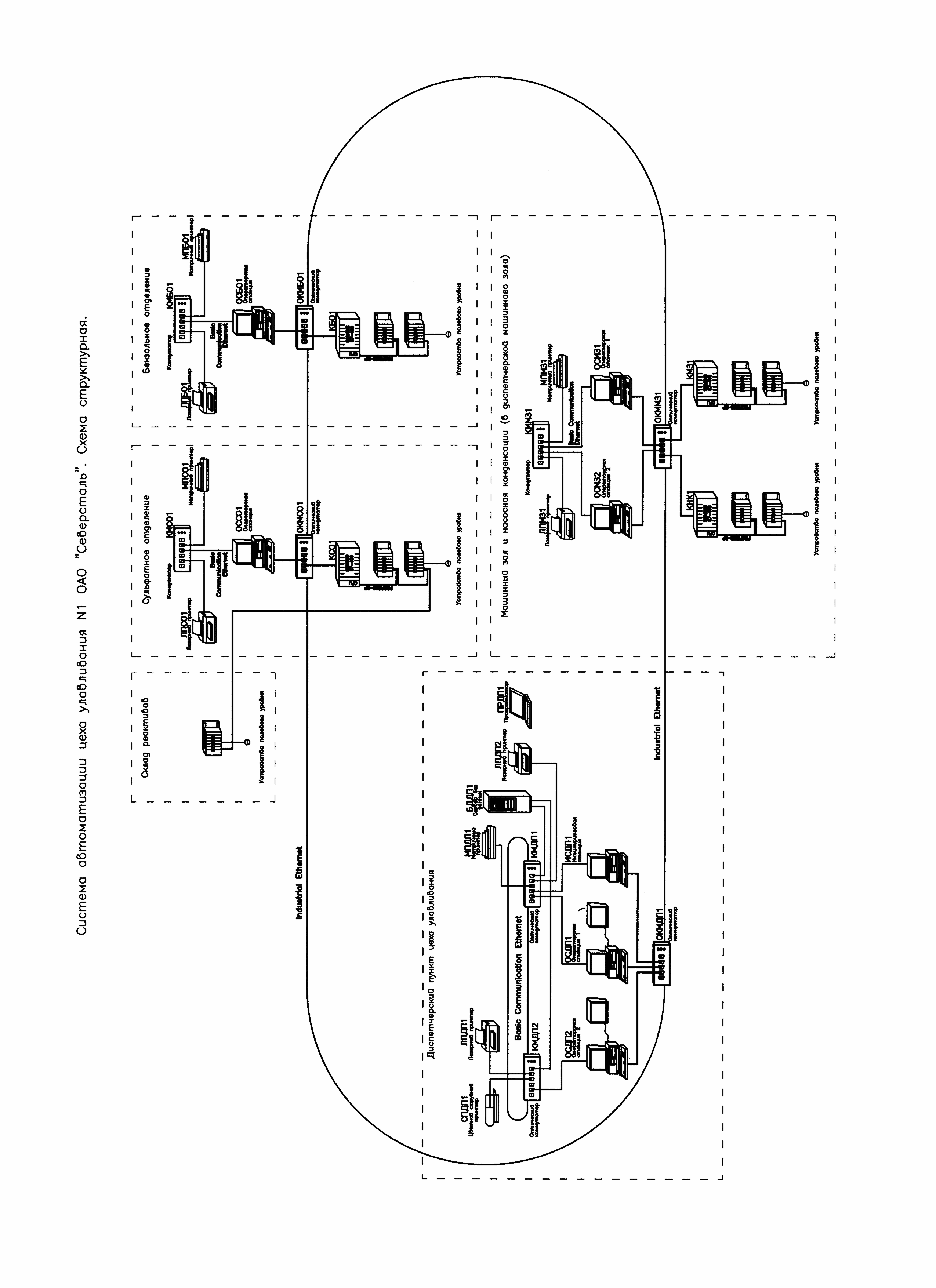
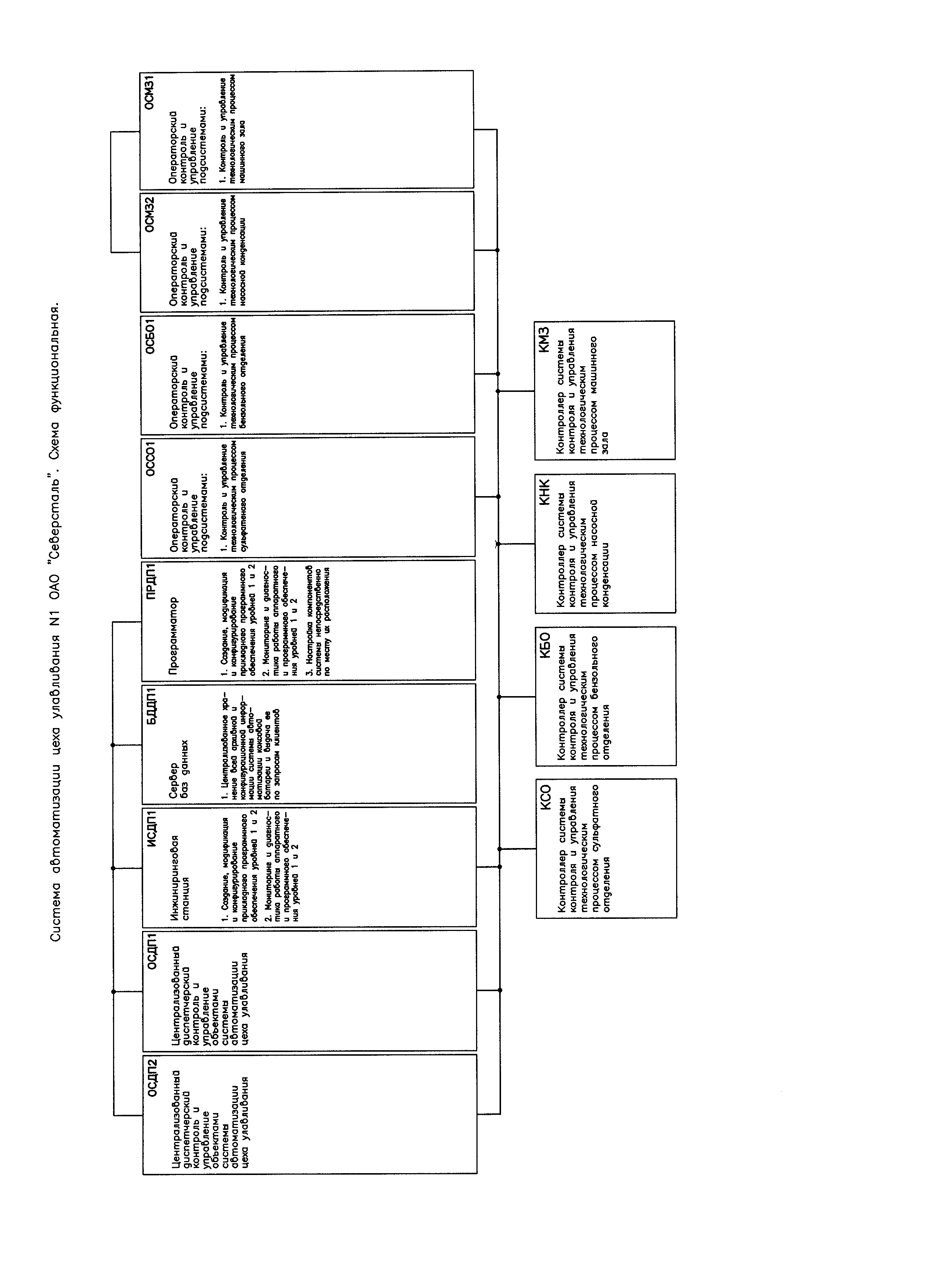
Структурное описание системы
Уровень 1
Датчики и устройства сбора данных
Измерительные приборы (датчики) Уровня 0 подключаются к устройствам Уровня 1 с помощью импульсных линий и служат для преобразования характеризующих технологический процесс физических величин в электрические сигналы стандартного формата. В системе используются следующие типы сигналов:
Входные:
- Аналоговые сигналы в диапазоне 4…20 мА;
- Дискретные сигналы.
Выходные:
- Аналоговые сигналы в диапазоне 4…20 мА;
- Дискретные сигналы.
Устройства распределённого ввода/вывода
Все датчики и устройства сбора данных подключаются к контроллерам Уровня 1 через станции распределённой периферии ET 200M производства SIEMENS AG. Станция распределённой периферии ET 200M представляет собой конструкцию формата серии SIMATIC S7-300, состоящую из профильной шины с возможностью «горячей замены» любого модуля, интерфейсного модуля IM 153-2, набора модулей аналогового и дискретного ввода/вывода S7-300 и батареи питания PS 307. Интерфейсные модули IM 153-2 осуществляют подключение станции ET 200M к процессорам системы PLC S7-400, используя шину PROFIBUS-DP на скорости до 12 Mbps. Для объектов с большим количеством входов/выходов несколько станций ET 200M соединяются последовательно шиной PROFIBUS-DP. Встроенные средства диагностики модулей и станций
ET 200M обеспечивают возможность мониторинга состояния каждого модуля и всей стойки в целом на операторских и инжиниринговых станциях верхнего уровня.
В системе используются следующие модули ввода-вывода производства SIEMENS AG:
- модуль аналогового ввода SM 331 (8 оптоизолированных аналоговых входов, 12-битный АЦП, встроенная диагностика, возможность горячей замены, ввод токового сигнала 4…20 мА или сигнала с термопреобразователей сопротивления);
- модуль дискретного ввода SM 321 (32 оптоизолированных дискретных входа 24V DC, встроенная диагностика, возможность горячей замены);
- модуль аналогового вывода SM 332 (4 оптоизолированных аналоговых выхода, 12-битный ЦАП, встроенная диагностика, возможность горячей замены, вывод токового сигнала 4…20 мА);
- модуль дискретного вывода SM 322 (16 оптоизолированных дискретных вывода 24V DC/0.5A, встроенная диагностика, возможность горячей замены).
Параметрирование и программирование станций распределённого ввода/вывода и сети PROFIBUS-DP осуществляется с помощью стандартного программного обеспечения STEP7 от SIEMENS AG, входящего в комплект инжинирингового программного обеспечения PCS7 на инжиниринговых станциях и программаторах.
Программируемые контроллеры
Используемые в системе программируемые логические контроллеры КСО1, КБО1, КНК1, КМЗ1 представляют собой устройства серии SIMATIC S7-400 производства SIEMENS AG. Каждый контроллер устанавливается на 9-ти местную монтажную стойку UR2 и состоит из центрального процессора CPU 416-2DP со встроенным DP-интерфейсом, коммуникационного процессора CP 443-1 для связи с другими устройствами по сети Industrial Ethernet и батареи питания PS 407. Дополнительные места стойки UR2 могут быть использованы для возможного расширения системы в будущем и установки дополнительных модулей. Центральный процессор CPU 416-2DP обеспечивает высокую производительность и возможность выполнения технологических программ большой сложности. Встроенный в процессор интерфейс PROFIBUS-DP позволяет подключать периферийные устройства напрямую к центральному процессору, используя сеть PROFIBUS. Коммуникационный процессор CP 443-1 обеспечивает включение контроллера в общую сеть Industrial Ethernet как равноправного абонента на скорости до 100 Mbps. Встроенные средства диагностики процессоров обеспечивают возможность мониторинга и анализа состояния каждого CPU на операторских и инжиниринговых станциях верхнего уровня.
Параметрирование и программирование центральных процессоров, коммуникационных процессоров и сетей PROFIBUS и Industrial Ethernet осуществляется с помощью стандартного программного обеспечения STEP7 от SIEMENS AG, входящего в комплект программного обеспечения PCS7 на инжиниринговых станциях и программаторах. Загрузка программы в общем случае возможна без остановки CPU и производится с помощью программного обеспечения STEP7 с программатора или инжиниринговой станции.
Сетевое коммуникационное оборудование
Сетевое оборудование Уровня 1 обеспечивает:
- подключение станций распределённой периферии ET 200M к контролерам S7-400 по сети PROFIBUS-DP;
- подключение контроллеров S7-400 в сеть Industrial Ethernet;
Сеть PROFIBUS относится к типу сетей с детерминированным временем отклика типа «ведущий-ведомый», осуществляющих арбитраж шины путем циклической передачи специального разрешающего маркера между абонентами сети. Физическое соединение абонентов осуществляется электрическим кабелем типа «витая пара» с максимальной скоростью передачи данных до 12 Mbps.
Станции распределённой периферии ET200M подключаются к процессорам контроллера S7-400, через интерфейс PROFIBUS-DP со скоростью обмена данными 12 Mbps, используя топологию «общая шина». Центральные процессоры CPU 416-2DP играют в этом случае роль мастера («ведущего») сети PROFIBUS-DP, станции ET 200M – роль слейвов («ведомых»).
Сеть Industrial Ethernet относится к типу сетей с недетерминированным временем отклика, осуществляющих арбитраж шины путём обнаружения множественного доступа и разрешением коллизий, согласно стандарту IEEE 802.3. Физическое соединение абонентов сети Industrial Ethernet на Уровне 1 осуществляется с помощью электрического кабеля типа «экранированная индустриальная витая пара» на скорости до 100 Mbps.
Контроллеры S7-400 подключаются к коммутаторам Уровня 2 общей сети Industrial Ethernet, используя топологию «звезда», с помощью установленных в корзине UR2Н каждого контроллера коммуникационного процессора CP 443-1. Ethernet-адресом контроллера в такой сети является адрес, назначенный коммуникационному процессору CP 443-1.
Для соединения устройств Уровней 1 и 2 сети Industrial Ethernet применяются 8-ми портовые оптоэлектрические коммутаторы типа OSM ITP53 от SIEMENS AG. Каждый коммутатор OSM ITP53 имеет 5 электрических портов и 3 оптических порта подключения терминальных устройств (контроллеров S7-400, Уровень 1, операторских и инжиниринговых станций, Уровень 2). Передача информации между абонентами сети осуществляется по ISO совместимому протоколу.
Уровень 2
Операторские станции
Операторские станции представляют человеко-машинный интерфейс между оператором и технологическим процессом, реализующий полные возможности мониторинга текущего состояния процесса, управления отдельными участками и механизмами, просмотра архивных данных по истории процесса, сообщений о состоянии объекта, генерации технологических отчётов. Они осуществляют также сбор информации о ходе технологического процесса от контроллеров Уровня 1, их первичную обработку и сохранение в системных базах данных.
Экспорт и импорт данных и конфигурации с операторских станций на сервер баз данных системы реализуется с помощью специализированных модулей прикладного программного обеспечения, создаваемых в рамках настоящего проекта.
Операторские станции, используемые в системе автоматизации цеха улавливания №1, представляют собой рабочие станции PCS7 ES/OS IL 40 производства SIEMENS AG, на которые установлено программное обеспечение PCS7 OS Software Single Station от SIEMENS AG. С каждой операторской станции возможен мониторинг и управление любым технологическим участком или группой участков, входящих в проект системы автоматизации цеха улавливания №1.
С использованием программного обеспечения WinCC Redundance V6.0 от SIEMENS AG реализуется взаимное резервирование двух операторских станций (ОСМЗ1-ОСМЗ2 для операторского пункта машинного зала, ОСДП1-ОСДП2 для диспетчерского пункта цеха улавливания) непосредственно подключенных к устройствам Уровня 1 сетью Industrial Ethernet. В любой момент времени одна из станций работает в режиме «основной», вторая – в режиме «резервный». При сбое или отказе одной из станций данные процесса обрабатываются второй станцией. После ввода второй станции в работу происходит автоматическое выравнивание текущей и архивной конфигурации станций. Такая конфигурация обеспечивает высокую степень надёжности и устойчивости системы.
Инжиниринговая станция
Инжиниринговая станция ИСДП1, расположенная в помещении компьютеров Уровня 2 диспетчерского пункта цеха улавливания №1, используется для создания, модификации и конфигурирования прикладного программного обеспечения Уровней 1 и 2, а также мониторинга и диагностики работы аппаратного и программного обеспечения Уровней 1 и 2. Изменения в программных проектах, сделанные на инжиниринговой станции, могут быть внесены в контроллеры и операторские станции в общем случае без перезапуска этих устройств. Инжиниринговая станция представляет собой станцию PCS7 ES/OS IL 40 производства SIEMENS AG, на которую установлено необходимое системное и прикладное программное обеспечение PCS7 Engineering Software с дополнительными программными пакетами, перечисленными ниже в пункте 3.1.
Программаторы
Под программатором ПРДП1 понимается переносной компьютер (ноутбук), использующийся для создания, модификации и конфигурирования прикладного программного обеспечения Уровней 1 и 2, а также мониторинга работы аппаратного и программного обеспечения Уровней 1 и 2, и настройки компонентов системы непосредственно по месту их расположения. Изменения в программных проектах, сделанные на программаторе, могут быть внесены в контроллеры и операторские станции без перезапуска этих устройств. Программатор является полнофункциональным переносным компьютером PowerPG, на который установлено необходимое системное и прикладное программное обеспечение PCS7 Engineering Software с дополнительными программными пакетами, перечисленными ниже в пункте 3.1.
Сервер баз данных
Сервер баз данных БДДП1 представляет собой компьютер под управлением операционной системы Microsoft® Windows 2000 Server с лицензией на 20 клиентских подключений. Он осуществляет централизованное хранение всей архивной и конфигурационной информации системы автоматизации цеха улавливания №1 в базах данных, работающих под управлением СУБД Microsoft® SQL Server, и выдачу её по запросам клиентов. Для генерации и просмотра статистических и отчётных данных по работе системы в виде отчётов используется установленный на сервере баз данных Microsoft® Internet Information Server, реализующий Web-интерфейс доступа клиентов и генерирующий HTML-документы на основании данных, хранящихся в системных базах данных и представляющий их пользователям.
Экспорт и импорт данных и конфигурации с сервера баз данных системы на операторские и инжиниринговые станции реализуется с помощью специализированных модулей прикладного программного обеспечения, создаваемых в рамках настоящего проекта.
Принтеры
Принтеры подключаются к внутренней сети Ethernet TCP/IP системы автоматизации цеха улавливания №1 как автономные устройства через внешние принт-серверы. Таким образом, каждый принтер является полноправным абонентом сети Ethernet TCP/IP, доступным с любой операторской, инжиниринговой станции или сервера баз данных. Используются следующие принтеры:
Помещения операторских пунктов объектов системы автоматизации цеха улавливания №1:
- чёрно-белый лазерный принтер формата А3. Он предназначен для вывода отчётных документов, таблиц, графиков с любой из операторских станций;
- черно-белый матричный принтер формата А3. Он предназначен для печати в режиме терминала протокола системных отклонений, аварий и возникающих в ходе технологического процесса нарушений с любой из операторских станций.
Помещение компьютеров Уровня 2 диспетчерского пункта цеха улавливания №1:
- чёрно-белый лазерный принтер формата А3. Он предназначен для вывода любых документов, таблиц, графиков, необходимых при обслуживании и наладке системы автоматизации цеха улавливания №1.
Используются принтеры, производимые фирмой Hewlett-Packard.
Сетевое коммуникационное оборудование
Сетевое оборудование Уровня 2 обеспечивает:
- связь операторских и инжиниринговых станций с устройствами Уровня 1 по сети Industrial Ethernet;
- подключение операторских станций, инжиниринговой станции и сервера баз данных в сеть Ethernet TCP/IP.
Операторские и инжиниринговые станции подключаются к коммутаторам OSM ITP53 Уровня 1 системы автоматизации цеха улавливания №1, используя платы коммуникационного процессора CP 1613 производства SIEMENS AG, устанавливаемые в PCI-разъёмы. Данная плата использует электрический интерфейс Ethernet типа «индустриальная витая пара» и позволяет подключаться к сетевому оборудованию на скорости до 100 Mbps.
Все рабочие станции и принтеры цеха локальных объектов улавливания №1 соединены внутренней сетью Ethernet TCP/IP на скорости 100 Mbps, для чего используются 6-ти портовые оптические коммутаторы типа OSM TP62 от SIEMENS AG. В каждой рабочей станции предусмотрена сетевая плата Intel EtherExpress 100, использующая электрический интерфейс Ethernet типа «витая пара» и позволяющая подключаться к коммутаторам OSM TP62 на скорости до 100 Mbps. В диспетчерском пункте коммутаторы OSM TP62 соединены между собой в резервированное кольцо со скоростью до 100 Mbps, используя оптические линии связи.
Программное обеспечение
Системное программное обеспечение Уровня 1
Под системным программным обеспечением Уровня 1 понимается специализированное программное обеспечение системы PCS7, поставляемое SIEMENS AG, а также других производителей, используемое для настройки, программирования и конфигурирования устройств и сетей Уровня 1. Это программное обеспечение устанавливается на инжиниринговых станциях и программаторах. В его состав входят следующие компоненты и приложения:
- PCS7 Engineering Software – базовое инжиниринговое программное обеспечение системы PCS7. Обеспечивает поддержку всех этапов разработки проекта, как-то: конфигурирование и настройка аппаратуры, определение коммуникационных связей, программирование, тестирование, отладку, запуск и обслуживание системы, документирование и архивацию данных, диагностику системы, экспорт/импорт переменных и блоков между различными компонентами системы. Поддерживает одновременную работу нескольких разработчиков одного проекта.
- SIMATIC Standard PID Control с библиотекой функциональных блоков, для реализации сложных алгоритмов PID-регулирования для контроллеров S7-400.
- SIMATIC PLCSIM для эмуляции работы контроллеров с целью отладки технологических программ.
Прикладное программное обеспечение Уровня 1
Под прикладным программным обеспечением Уровня 1 понимается программное обеспечение, разработанное в рамках настоящего проекта для решения задач управления Уровня 1 системы автоматизации цеха улавливания №1. Сюда входят технологические программы, алгоритмы регулирования и обмена данными для контроллеров. Подробная спецификация прикладного программного обеспечения Уровня 1 будет приведена позже.
Системное программное обеспечение Уровня 2
Под системным программным обеспечением Уровня 2 понимается специализированное программное обеспечение, поставляемое SIEMENS AG и другими производителями, используемое для создания, настройки, программирования и конфигурирования объектов, устройств и сетей Уровня 2. Это программное обеспечение устанавливается на операторских станциях, инжиниринговых станциях, программаторах и сервере баз данных. В его состав входят следующие компоненты и приложения:
Microsoft Corporation:
- Поставляемые в составе всех станций PCS7 операционные системы Microsoft® Windows 2000 Professional на клиентских станциях, инжиниринговой станции;
- Броузер Microsoft Internet Explorer, устанавливаемый на всех операторских и инжиниринговых станциях, сервере баз данных и программаторах, входящих в автоматизированную систему цеха улавливания №1;
- Web-сервер Microsoft Internet Information Server, устанавливаемый на сервере баз данных;
- Пакет Microsoft® Small Business Server, устанавливаемый на сервере баз данных и включающий в себя:
- операционную систему Microsoft® Windows 2000 Server;
- сервер системы управления базами данных Microsoft® SQL Server;
- сервер обмена сообщениями и групповой работы Microsoft® Exchange Server;
- сервер совместного доступа и фильтрации данных Microsoft® Internet Security and Acceleration Server 2000;
- дополнительное программное обеспечение настройки, управления и диагностики сервера баз данных;
- лицензию на 20 клиентских подключений;
- операционную систему Microsoft® Windows 2000 Server;
- Пакет офисных приложений Microsoft® Office, устанавливаемый на инжиниринговой станции и сервере баз данных;
- Среда разработки Windows-приложений Microsoft® Visual Studio, устанавливаемая на инжиниринговой станции и программаторах;
- Справочная система Microsoft MSDN Library, устанавливаемая на инжиниринговой станции и программаторах.
SIEMENS AG:
- SIMATIC NET S7-1613 – базовое программное обеспечение (драйверы и службы), обеспечивающее связь операторских станций и инжиниринговой станции цеха улавливания №1 с устройствами Уровня 1 по сети Industrial Ethernet, используя коммуникационные процессоры CP 1613 и оптические коммутаторы OSM ITP53.
- PCS7 OS Software Single Station – программный пакет, устанавливаемый на операторские станции в помещении ЦПУ. Включает в себя средства визуализации и человеко-машинного интерфейса. Обеспечивает связь с программируемыми контроллерами Уровня 1, предварительную обработку и архивацию данных в реальном времени;
- WinCC Redundancy – программный пакет, устанавливаемый на операторские станции ОСМЗ1-ОСМЗ2, ОСДП1-ОСДП2 и обеспечивающий горячее резервирование операторских станций с выравниванием текущей и архивной информации на них.
- SIMATIC WinCC ODK – дополнительный пакет для программирования в среде WinCC, используя открытые интерфейсы WinCC API. Устанавливается на инжиниринговую станцию и программаторы;
Прикладное программное обеспечение Уровня 2
Под прикладным программным обеспечением Уровня 2 понимается любое программное обеспечение, разработанное в рамках настоящего проекта для решения задач контроля и управления Уровня 2 системы автоматизации цеха улавливания №1. Сюда входят:
- модули сбора и обработки данных процесса и операторского интерфейса на операторских станциях;
- специализированное программное обеспечение импорта/экспорта архивных и конфигурационных данных между объектами Уровня 2 для операторских станций, сервера баз данных и инжиниринговой станции;
- архивные и конфигурационные базы данных системы автоматизации, находящиеся на сервере баз данных;
- алгоритмы контроля и управления всех объектов Уровня 2.
Функциональное описание системы
Подсистема контроля и регулирования параметров работы сульфатного отделения
Система контроля и управления технологическим процессом сульфатного отделения включает следующие объекты:
- собственно сульфатное отделение;
- склад реактивов;
Объекты сульфатного отделения управляются следующими контроллерами:
- КСО1 – сульфатное отделение плюс данные со склада реактивов;
Сбор от контроллера КСО1, обработка и архивация всех данных, относящихся к подсистеме контроля работы объектов сульфатного отделения производится операторской станцией ОССО1.
Непосредственное регулирование параметров объектов сульфатного отделения и выдача управляющих воздействий на исполнительные механизмы производится контроллером КСО1. Каждый из реализованных регуляторов может работать в следующих режимах:
- автоматический. В этом режиме регулирование осуществляется программным алгоритмом ПИД-регулирования, реализованным в технологической программе регулятора. Установка задания и параметров регулятора производится оператором с операторской станции ОССО1, через технологическую программу контроллера КСО1. Этот режим является основным режимом работы регуляторов;
- ручной. В этом режиме регулятор выполняет только непосредственные команды оператора, подаваемые на исполнительные механизмы. Подача команд производится оператором с операторской станции ОССО1.
Визуальное отображение состояния текущих параметров возможно производить с операторской станции ОССО1, расположенной в локальном операторском пункте сульфатного отделения.
Помимо локального диспетчерского пункта сульфатного отделения, данные технологического процесса можно просматривать на операторских станциях ОСДП1…ОСДП2, находящихся в диспетчерском пункте цеха улавливания №1.
Подсистема контроля и регулирования параметров работы бензольного отделения
Настоящая подсистема предназначена для контроля и управления технологическим процессом бензольного отделения. Объекты бензольного отделения управляются следующими контроллерами:
- КБО1 – контроллер объектов бензольного отделения;
Сбор от контроллера КБО1, обработка и архивация всех данных, относящихся к подсистеме контроля работы объектов бензольного отделения производится операторской станцией ОСБО1, расположенной в локальном операторском пункте бензольного отделения.
Непосредственное регулирование параметров объектов бензольного отделения и выдача управляющих воздействий на исполнительные механизмы производится контроллером КБО1. Каждый из реализованных регуляторов может работать в следующих режимах:
- автоматический. В этом режиме регулирование осуществляется программным алгоритмом ПИД-регулирования, реализованным в технологической программе регулятора. Установка задания и параметров регулятора производится оператором с операторской станции ОСБО1, через технологическую программу контроллера КБО1. Этот режим является основным режимом работы регуляторов;
- ручной. В этом режиме регулятор выполняет только непосредственные команды оператора, подаваемые на исполнительные механизмы. Подача команд производится оператором с операторской станции ОСБО1.
Визуальное отображение состояния текущих параметров возможно производить с операторской станции ОСБО1.
Помимо локального диспетчерского пункта бензольного отделения, данные технологического процесса можно просматривать на операторских станциях ОСДП1…ОСДП2, находящихся в диспетчерском пункте цеха улавливания №1.
Подсистема контроля и регулирования параметров работы машинного зала и насосной конденсации
В цехе улавливания №1 данной подсистемой охватываются следующие объекты:
- трубчатые газовые холодильники;
- электрофильтры прямого коксового газа;
- машинный зал;
- механизированные осветлители;
Объекты машинного зала управляются следующими контроллерами:
- КМЗ1 – контроллер объектов машинного зала;
- КНК1 – контроллер объектов насосной конденсации;
Сбор от контроллеров КМЗ1 и КНК1, обработка и архивация всех данных, относящихся к подсистеме контроля работы объектов производственного водоснабжения производится операторскими станциями ОСМЗ1…ОСМЗ2.
Непосредственное регулирование параметров объектов машинного зала и выдача управляющих воздействий на исполнительные механизмы производится контроллерами КМЗ1 и КНК1. Каждый из реализованных регуляторов может работать в следующих режимах:
- автоматический. В этом режиме регулирование осуществляется программным алгоритмом ПИД-регулирования, реализованным в технологической программе регулятора. Установка задания и параметров регулятора производится оператором с любой из операторских станций ОСМЗ1…ОСМЗ2, через технологическую программу контроллеров КМЗ1 и КНК1. Этот режим является основным режимом работы регуляторов;
- ручной. В этом режиме регулятор выполняет только непосредственные команды оператора, подаваемые на исполнительные механизмы. Подача команд производится оператором с любой операторской станции ОСМЗ1…ОСМЗ2.
Визуальное отображение состояния текущих параметров возможно производить с любой из операторских станций ОСМЗ1…ОСМЗ2, расположенными в локальном операторском пункте машинного зала.
Кроме того, в диспетчерском пункте цеха улавливания №1 находятся операторские станции ОСДП1 и ОСДП2, с которых можно производить контроль работы машинного зала и насосной конденсации.
Подсистема централизованного диспетчерского контроля работы объектов цеха улавливания
Подсистема диспетчерского контроля работы объектов цеха улавливания №1 предназначена для централизованного диспетчерского контроля работы следующих объектов:
- сульфатного отделения;
- бензольного отделения;
- машинного зала с насосной конденсации;
Подсистема диспетчерского контроля работы объектов цеха улавливания №1 предназначена для выполнения следующих функций:
- автоматический контроль технологических параметров с представлением информации на дисплее в виде мнемосхем, графиков и таблиц;
- предупредительная аварийная сигнализация отклонения технологических параметров от нормальных значений;
- выдача инструкции оператору о действиях при отклонении параметра от нормы;
- ведение архивов состояния и хода технологического процесса;
- автоматическое формирование и выдача выходных документов.
Сбор от контроллеров локальных объектов автоматизации цеха улавливания №1, обработка и архивация на сервере баз данных БДДП1 всех данных, относящихся к объектам системы автоматизации цеха улавливания №1 производится операторскими станциями ОСДП1…ОСДП2.
Визуальное отображение состояния текущих параметров возможно производить с любой из операторских станций ОСДП1…ОСДП2.
СИСТЕМЫ СВЯЗИ, АВТОМАТИЧЕСКИЕ УСТАНОВКИ ПОЖАРНОЙ СИГНАЛИЗАЦИИ, АВТОМАТИЧЕСКАЯ ОХРАННАЯ СИГНАЛИЗАЦИЯ.
Системы связи
В соответствии со структурой управления коксохимпроизводством предусматриваются следующие виды связи:
- производственная автоматическая телефонная связь;
- оперативно-диспетчерская телефонная связь (ОДТС);
- распорядительно-поисковая связь (РПС);
- производственная громкоговорящая связь (ПГС);
- радиосвязь;
- электрочасофикация.
Производственная автоматическая телефонная связь предназначена для организации связи участков и отдельных работников между собой, а также включения определенной группы абонентов в городскую телефонную сеть. Телефонные аппараты по комплексной телефонной сети включаются в автоматическую телефонную станцию ОАО «Северсталь».
Ввиду сложившейся на коксохимпроизводстве структуры построения ОДТС на базе станции оперативной телефонной связи «Регион-120ХТ» устанавливается пульт «Регион-Ц» у диспетчера ЦУ №1 и телефонные аппараты ЦБ у абонентов. Указанное оборудование ОДТС обеспечивает двухстороннюю связь с абонентами, связь по соединительным линиям с другими пультами и коммутаторными установками.
Предусматривается прокладка новых телефонных сетей связи от главной конторы КХП до объектов цеха улавливания химических продуктов №1.
Распорядительно-поисковая связь предназначена для передачи информации, распоряжений и поиска нужных лиц. В существующую сеть РПС цеха улавливания химических продуктов №1 включаются громкоговорители различной мощности.
Предусматривается прокладка новых сетей РПС от главной конторы КХП до объектов цеха улавливания химических продуктов №1.Сети распорядительно-поисковой связи выполняются отдельными кабелями и проводами.
Производственная громкоговорящая связь (ПГС) предназначена для обеспечения двухсторонней технологической связи между рабочими местами. Приборы ПГС устанавливаются на рабочих местах, связанных между собой единой технологией.
Для организации диспетчерских сетей связи предусмотрено применение стационарной диспетчерской и носимых абонентских радиостанций Motorola. Радиостанции обеспечивают бесподстроечную и беспоисковую симплексную радиосвязь указанных абонентов между собой.
В помещениях с обслуживающим персоналом предусматриваются установка автономных кварцевых электрических часов.
Автоматические установки пожарной сигнализации.
Автоматическими установками пожарной сигнализации (АУПС) будут защищены здания, сооружения и помещения согласно НПБ 110-03.
Автоматическая пожарная сигнализация предназначена для передачи сигналов тревоги на пульт центрального наблюдения, установленный в здании аварийной газоспасательной службы., от автоматических извещателей, извещателей ручного действия и других устройств, устанавливаемых на охраняемых объектах. В диспетчерском помещении цеха улавливания химических продуктов №1 предусматривается установка промежуточного приемно-контрольного пожарного прибора СI1145-4 фирмы Cerberus.
Автоматическая охранная сигнализация.
Автоматической охранной сигнализацией (АОС) оборудуются помещения в соответствии с «Перечнем объектов черной металлургии, подлежащих оборудованию автоматической охранной сигнализацией».
АОС предназначена для передачи сигналов тревоги на пульт центрального наблюдения службы безопасности 2.
АОС предусматривается на объектах без постоянного присутствия обслуживающего персонала – в электропунктах и в трансформаторных подстанциях. В электропомещениях устанавливаются выносные контрольные панели NX-4 и пульты управления NX-148.
2004г