Методические указания к выполнению курсового проекта по дисциплине «Технология машиностроения» для студентов специальностей 120100, 060801 всех форм обучения
Вид материала | Методические указания |
- Методические указания по выполнению курсового проекта для студентов всех форм обучения, 363.24kb.
- Методические указания к выполнению курсового проекта по дисциплине «Микропроцессорные, 194.17kb.
- Методические указания к выполнению курсового проекта Красноярск 2002, 2057.27kb.
- Методические указания к выполнению курсового проекта по дисциплине «Металлические конструкции,, 208.08kb.
- Методические указания по выполнению контрольных работ по дисциплине «Страхование» для, 1588.5kb.
- Методические указания по выполнению курсового проекта по курсу Экономика предприятия, 338.42kb.
- Методические указания к выполнению курсового проекта по учебной дисциплине "Управленческого, 430.87kb.
- Пищевых продуктов проектирование торговых предприятий методические указания к выполнению, 253.91kb.
- Методические указания к выполнению лабораторной работы №6 для студентов всех форм обучения, 197.64kb.
- Методические указания по выполнению курсового проекта для студентов высших учебных, 343.67kb.
Министерство образования и науки Российской Федерации
Федеральное агентство по образованию
Саратовский государственный технический университет
Балаковский институт техники, технологии и управления
ПРОЕКТИРОВАНИЕ ТЕХНОЛОГИЧЕСКИХ ПРОЦЕССОВ МЕХАНИЧЕСКОЙ ОБРАБОТКИ ДЕТАЛЕЙ
Методические указания
к выполнению курсового проекта по дисциплине
«Технология машиностроения»
для студентов специальностей 120100, 060801
всех форм обучения
Одобрено
редакционно-издательским советом
Балаковского института техники,
технологии и управления
Балаково 2009
1. ВВЕДЕНИЕ
Методические указания содержат основные сведения о составе курсового проекта и указания по его разработке, знакомят с характером предъявляемых требований, последовательностью разработки его разделов, необходимой глубиной проработки каждого из них, объёмами выполняемых технологических расчетов.
2. ОСНОВНЫЕ ПОЛОЖЕНИЯ
Разработка технологических процессов изготовления деталей является самостоятельной творческой работой студента. Методические указания должны внести планомерность в работу, свести к минимуму непроизводительные затраты времени, исключить элементы шаблонности и формализма в работе, стимулировать творческий подход к выполнению задания. Вместе с тем, методические указания должны оказать помощь и руководителям курсового проекта в подготовке к занятиям со студентами, в оценке выполняемых ими работ и установить необходимое единообразие в руководстве и предъявляемых требованиях.
Курсовой проект в известной мере подытоживает знания, полученные студентами при изучении ряда дисциплин, и подготавливает их к предстоящей преддипломной практике и дипломному проектированию. Студент должен уметь использовать прогрессивные процессы, современные достижения науки и техники в области технологии машиностроения, обосновывать целесообразность их применения в данных конкретных условиях, грамотно выполнять необходимые расчеты, четко и логично формулировать свои мысли и предложения. В процессе работы над курсовым проектом студент вырабатывает необходимые навыки пользования учебной, специальной, технической и справочной литературой, нормативными документами и руководящими материалами (ГОСТ, ОСТ).
Основной целью курсового проекта является привитие студенту практического самостоятельного решения частных инженерных задач в области технологии машиностроения.
3. ОФОРМЛЕНИЕ РАСЧЁТНО-ПОЯСНИТЕЛЬНОЙ ЗАПИСКИ
Текстовые материалы состоят из пояснительной записки и карт технологического процесса. Записку необходимо писать одновременно с разработкой курсового проекта и окончательно оформлять после выполнения всех работ. В записке излагаются основные принципиальные решения, принятые в проекте по отдельным вопросам, даются необходимые пояснения, приводятся инженерные расчеты, иллюстрируемые схемами, эскизами, графиками. Записка пишется в сжатой форме и должна иметь минимум извлечений из различных литературных источников в виде цитат и максимум ссылок на литературу, собственных выводов, предложений, пояснений, расчетов.
Комплектование материалов пояснительной записки курсового проекта производится в следующей последовательности:
1. Титульный лист.
2. Задание на курсовой проект.
3. Реферат.
4. Введение.
5. Определение типа производства.
6. Анализ исходных данных.
6.1. Служебное назначение детали и условия ее работы в сборочной единице.
6.2. Конструкторский контроль чертежа детали.
6.3. Анализ технических требований на изготовление детали.
6.4. Анализ технологичности конструкции детали.
7. Технико-экономическое обоснование выбора метода получения заготовки и ее проектирование.
8. Анализ базового технологического процесса изготовления детали.
9. Разработка и обоснование проектируемого технологического процесса изготовления детали.
9.1. Выбор баз.
9.2. Разработка маршрутного технологического процесса.
9.3. Расчет припусков и промежуточных размеров.
9.4. Построение операций и выбор оборудования.
9.5. Определение рациональных режимов резания.
9.6. Нормирование технологических операций.
10. Разработка расчетно-технологической карты и управляющей прог-раммы обработки заготовки на станке с ЧПУ.
11. Заключение.
12. Список использованных источников.
13. Приложения.
Титульный лист является первым листом пояснительной записки. На нем указывается тема проекта, фамилия и инициалы студента и руководителя проекта. Подписи указанных лиц на титульном листе обязательны. Задание на курсовой проект является вторым листом пояснительной записки.
На третьем листе пояснительной записки помещается реферат. Реферат содержит: заглавное слово «Реферат»; сведения об объеме проекта; перечень ключевых слов; текст реферата. Сведения об объеме проекта включают данные о количестве страниц пояснительной записки и содержащихся в ней рисунков и таблиц, количество источников и приложений. Ключевые слова отражают основное содержание проекта и используются в информационно-поисковой системе научно-технической информации. Перечень включает от 5 до 15 слов (словосочетаний), написанных в строку прописными буквами через запятые в именительном падеже. В тексте реферата отражают основные результаты, полученные в проекте. Объем текста реферата не более 400…600 знаков.
«Содержание» включает наименование всех разделов, подразделов и пунктов с указанием номера страницы (листа), на которых размещается начало материала раздела (подраздела, пункта). «Введение» и «Заключение» являются самостоятельными составляющими записки. Каждый раздел необходимо начинать с нового листа. Разделы должны иметь порядковую нумерацию и обозначаться арабскими цифрами с точкой, «Введение» и «Заключение» не нумеруются.
Текст пояснительной записки начинается «Введением» и заканчивается «Заключением», являющимися обязательными структурными составляю-щими работы. Во введении дается обоснование важности и актуальности курсовой работы. В «Заключении» должны содержаться краткие выводы по всем разделам и оценка полученных результатов в сопоставлении с базовыми показателями. Текст записки пишется аккуратно и разборчиво.
Кроме текста в записке помещаются иллюстрации – таблицы, рисунки, схемы, фотографии, графики и др. Иллюстрации (кроме таблицы) обозначаются словом «рис.» и нумеруются последовательно арабскими цифрами в пределах каждого раздела. Номер рисунка и таблицы должен состоять из номера раздела и порядкового номера иллюстрации в данном разделе, разделенных точкой.
Например, «Рис. 1.3» (третий рисунок первого раздела), «Таблица 3.1» (первая таблица третьего раздела).
Каждая иллюстрация должна иметь наименование, при необходимости их сопровождают поясняющими данными. После номера рисунка следует его название, затем ниже – поясняющие данные. Надпись «Таблица» с указанием номера таблицы помещают над наименованием таблицы в правом верхнем углу.
Формулы нумеруются арабскими цифрами в пределах каждого раздела, аналогично нумерации иллюстраций. Номер формулы помещают с правой стороны листа на уровне формулы в круглых скобках, например, (3.1) – первая формула третьего раздела.
Ссылки в тексте на иллюстрации даются с помощью их порядкового номера, например … изображено на рис.2.4. При ссылке на таблицу слово «таблица» пишут сокращенно и указывают ее номер, например… дано в табл. 2.3.
В ссылке на использованный источник указывают его порядковый номер по списку, выделенный квадратными скобками, например, по данным [4] материал обладает хорошей обрабатываемостью-резанием. В список использованных источников включают учебную, научную, нормативную, патентную, справочную и другую литературу и документы по мере их упоминания в тексте записки.
Образцы выполнения курсовых работ представлены на стендах в кабинете курсового проектирования кафедры «Технология и автоматизация машиностроения» (ТАМ).
4. ОФОРМЛЕНИЕ ГРАФИЧЕСКОЙ ЧАСТИ
Графическая часть проекта включает в себя рабочий чертёж детали, который студент берёт на производственной практике, оформленный на формате А1 и выполненный в соответствии с требованиями ЕСКД.
Комплектование материалов графической части курсового проекта включает в себя:
1. Чертеж детали (А1).
2. Размерный анализ детали (А1).
3. Операционные эскизы механической обработки (А1).
4. РТК (А1).
5. ПОСЛЕДОВАТЕЛЬНОСТЬ РАБОТЫ НАД ПРОЕКТОМ
5.1. Определение типа производства
Тип производства зависит от заданной программы и трудоемкости изготовления изделия
Коэффициент серийности рассчитывается по формуле
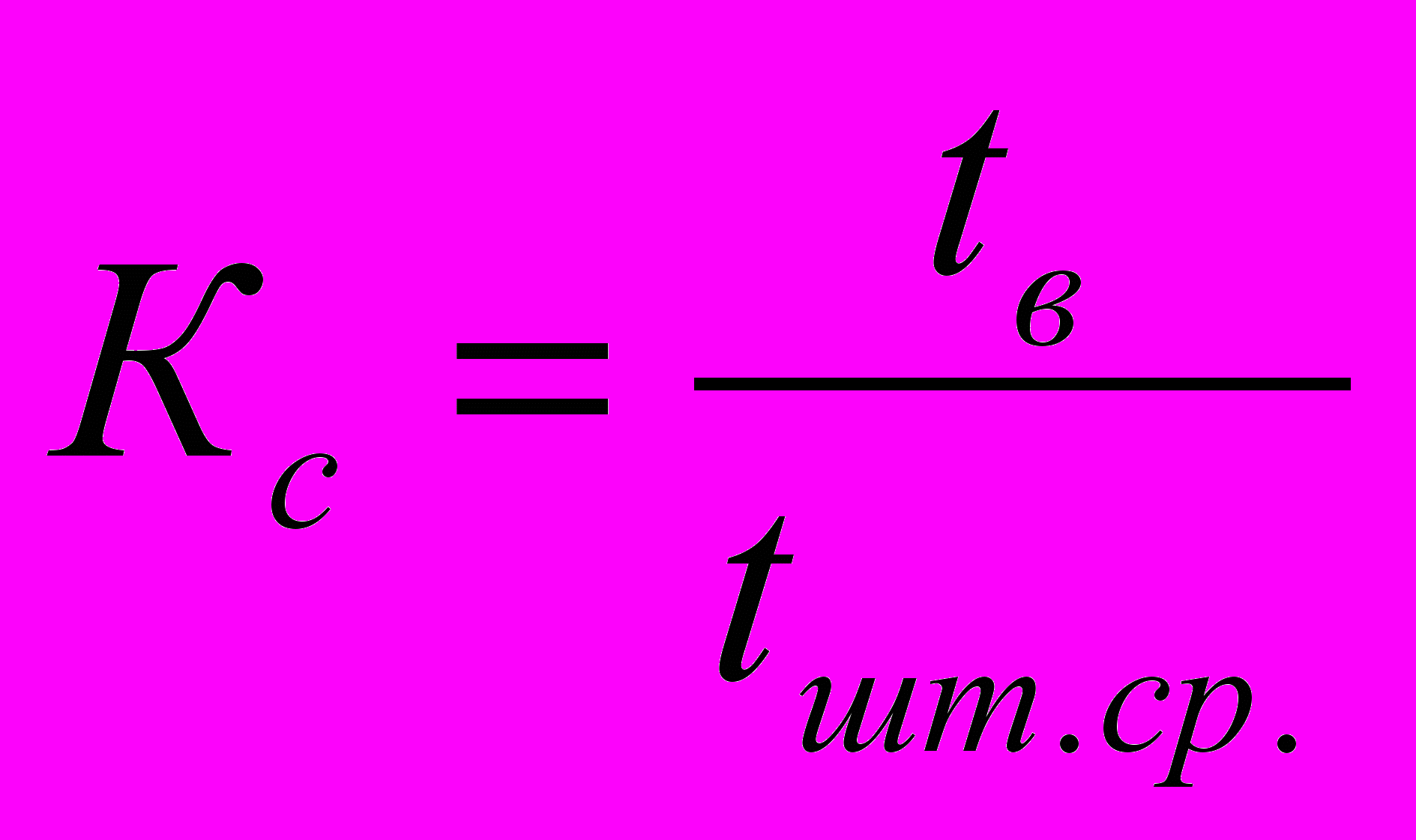
где
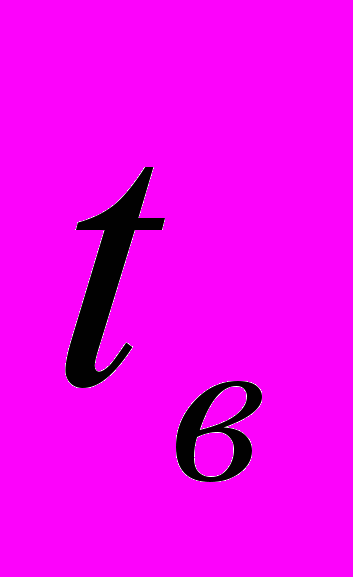
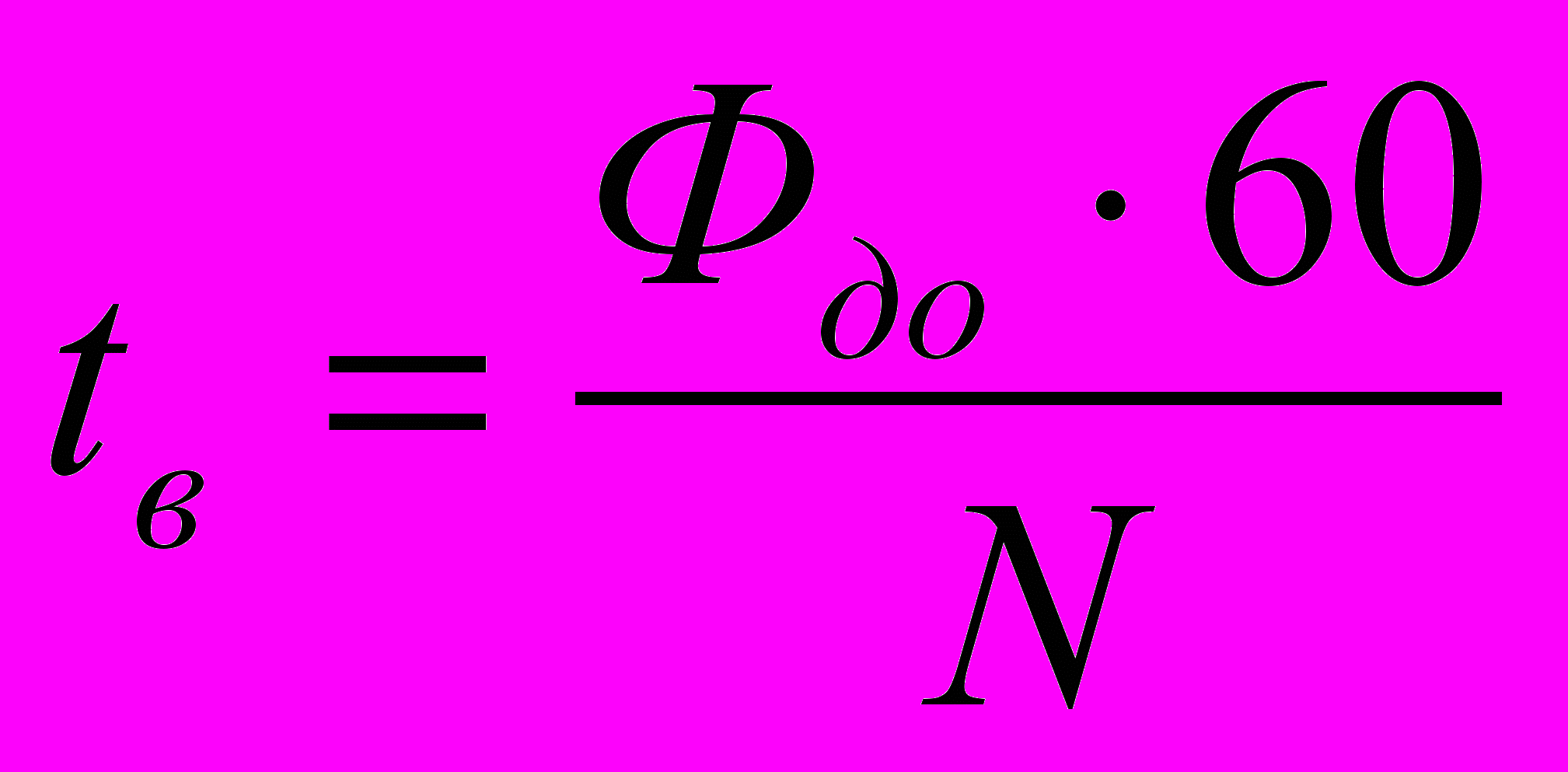
где
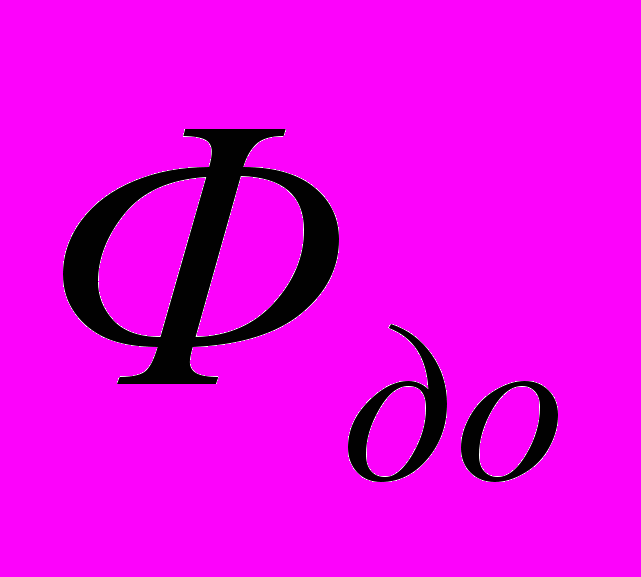
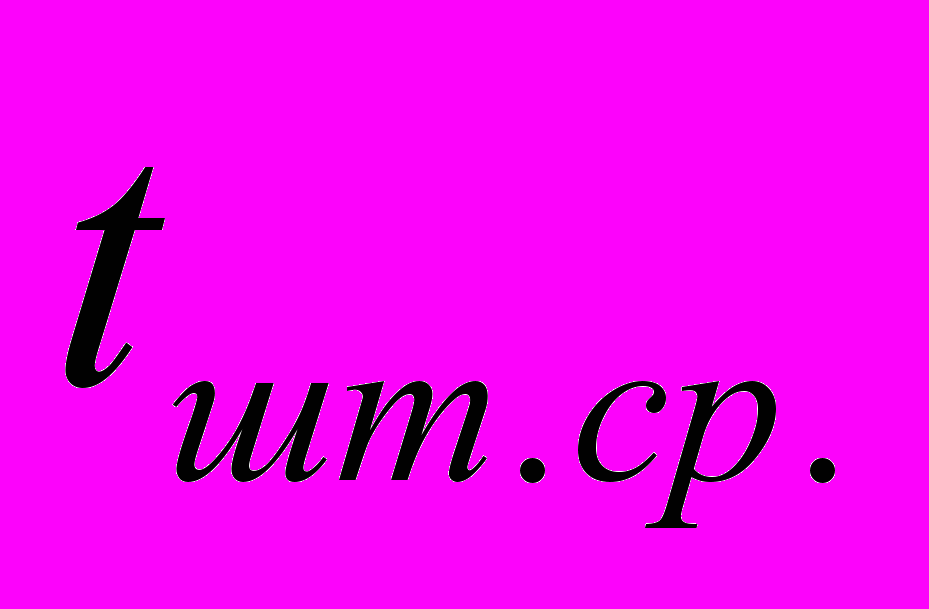
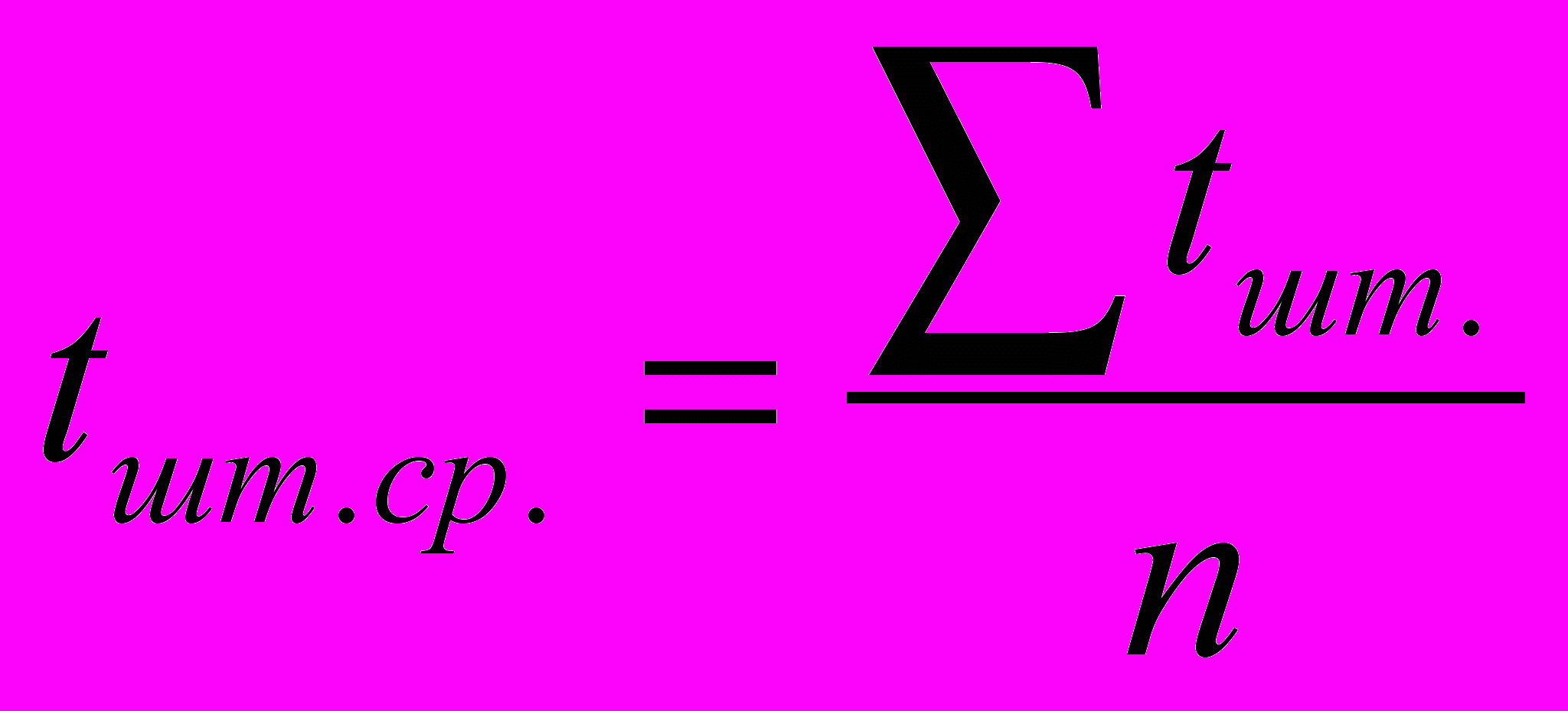
Согласно ГОСТ [6], при
Кз.о ≤ 1 – массовое производство;
1 < Кз.о ≤ 10 – крупносерийное производство;
10 < Кз.о ≤ 20 – серийное производство;
20 < Кз.о ≤ 40 – мелкосерийное производство;
Кз.о для единичного производства не регламентируется.
Определение действительного годового фонда времени работы оборудования
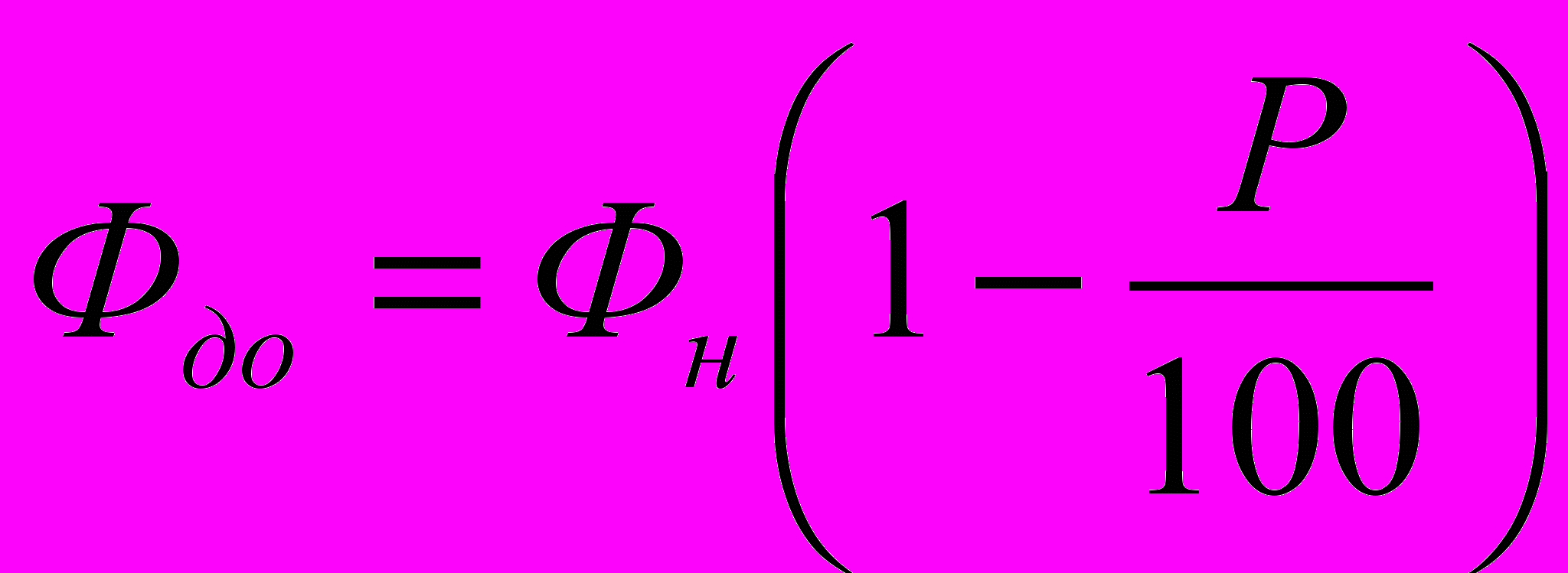
где
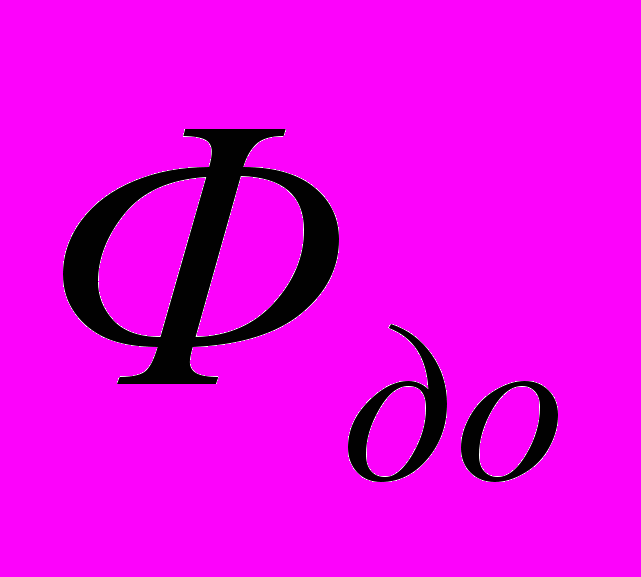
Номинальный фонд времени в год:
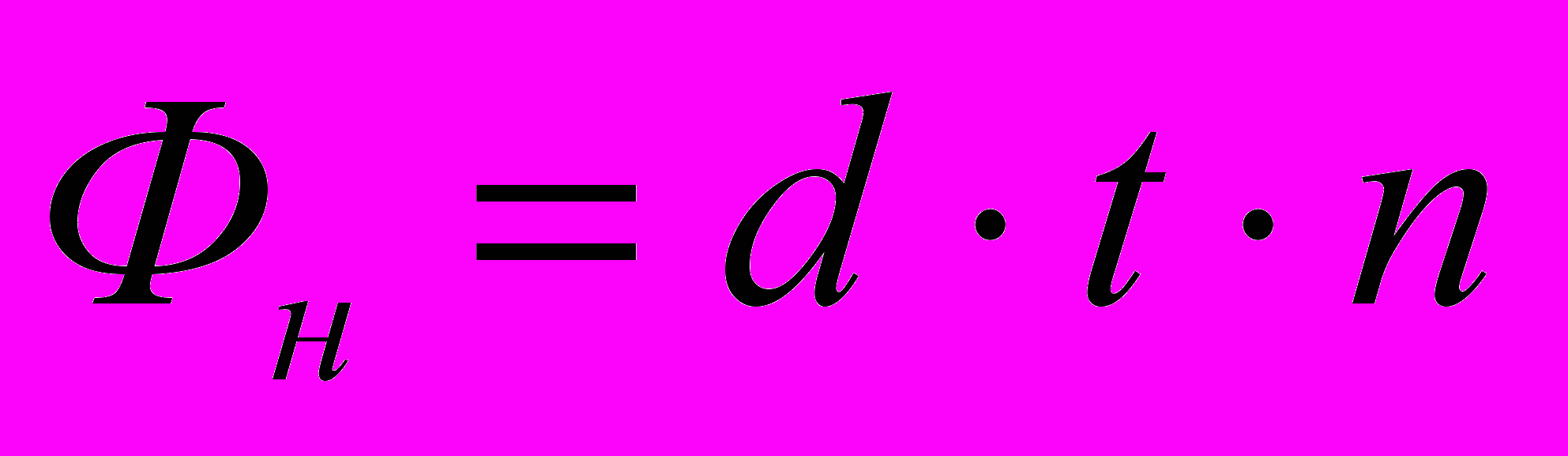
где d - число рабочих дней в году, исходя из пятидневной рабочей недели; каждая восьмая-шестидневная; t - нормальная продолжительность смены в часах (8 часов); n - число смен в сутки.
5.2. Анализ исходных данных
5.2.1 Служебное назначение детали и условия ее работы
в сборочной единице
Описание служебного назначения детали и условий ее работы в сборочной единице производится после изучения сборочного чертежа узла, содержащего деталь и описания работы этого узла. В этом разделе необходимо дать краткую характеристику изделия, привести его эксплуатационные параметры и виды контактного взаимодействия изучаемой детали с сопрягаемыми деталями, динамические и статические нагрузки, воспринимаемые данной деталью (изгиб, кручение, сжатие и т.д.), их величину и цикличность, направление, темпера-турный режим, агрессивность среды, планируемый ресурс работы, указываются наиболее нагруженные элементы изделия и др.
Если в описании функционального назначения узла отсутствует опии-сание служебных функций отдельных поверхностей рассматриваемой детали, то после анализа по выше приведенной методике это несложно сделать и самостоятельно [1].
После этого необходимо определить основные и вспомогательные базы детали. В этом же разделе приводятся сведения о материале детали – химический состав и механические свойства.
5.2.2 Конструкторский контроль чертежа детали
В результате изучения и анализа рабочего чертежа детали необходимо указать соответствие выполнения чертежа требованиям действующих стандартов ЕСКД. При этом в расчетно-пояснительной записке делается запись о достаточности проекций, разрезов, сечений и видов для полного понимания конфигурации детали, все ли необходимые размеры проставлены, для всех ли поверхностей проставлена шероховатость, соответствует ли требованиям стандартов запись технических требований и т.п. Кроме этого рабочий чертеж должен содержать сведения о марке материала детали, массу детали, масштаб, её название, заводской номер и др. В случае, если в процессе анализа рабочего чертежа детали были выявлены отступления от требований ЕСКД, в подразделе пояснительной записки оформляется таблица следующего вида.
Таблица 1
Изображено на чертеже | Должно быть по ЕСКД |
![]() ![]() | |
При выполнении этого подраздела расчетно-пояснительной записки проекта рекомендуется использовать следующую литературу [17-23].
5.2.3 Анализ технических требований на изготовление детали
Анализ технических требований (ТТ) выполняется на основании определения служебного назначения изделия. Состав ТТ, их количественные и качественные показатели зависят от служебного назначения детали и условий её работы в сборочной единице. В качестве ТТ практически всех рабочих чертежей деталей выступают точность размеров (их квалитеты), точность формы и расположения поверхностей детали, шероховатость поверхности. Кроме этого во многих рабочих чертежах представлены требования по твердости, термообработке, гальваническим и лакокрасочным защитным и декоративным покрытиям, методам неразрушающего контроля и многое другое. Целью анализа ТТ является, во-первых, полное понимание технологических задач по изготовлению детали в соответствии с требованиями рабочего чертежа и, во-вторых, проверка правильности их назначения.
При анализе ТТ необходимо тщательно разобраться в сути каждого пункта текстовых записей ТТ, которые приводятся с правой стороны над штампом рабочего чертежа. Следует досконально разобраться в приведенных ТТ – что представляет собой каждое требование, что оно означает, для чего оно указано в чертеже и что произойдет, если оно не будет выполнено. Определяют правомерность назначения конструктором заданных величин отклонений размеров, формы поверхностей или их расположения. Во многих случаях допустимые отклонения регламентируются соответствующими стан-дартами, например, ГОСТ 1643-81 регламентирует допустимые отклонения на межосевые расстояния и на параллельность осей зубчатых передач и их точность, ГОСТ 520-89 регламентирует осевое биение дорожки качения шариковых упорных подшипников, радиальное биение дорожки качения роликовых конических подшипников и т.д.
5.2.4 Анализ технологичности конструкции детали
Основная задача обеспечения ТКИ заключается в достижении оптимальных трудовых, материальных и топливно-энергетических затрат на проектирование, подготовку производства, изготовление, монтаж вне предприятия-изготовителя, технологическое и техническое обслуживание, ремонт при обеспечении прочих заданных показателей качества изделия в принятых условиях проведения работ.
Главными факторами, определяющими требования к ТКИ, являются:
- вид изделия, степень его надежности и сложности, условия изготов-ления, ремонта и технического обслуживания, показатели качества;
- тип производства;
- условия производства, в том числе наличие опыта и прогрессивных методов изготовления аналогичных изделий, оборудования, оснастки и т.д.
Вид изделия определяет главные конструкторско-технологические признаки, обусловливающие характерные требования к технологичности конструкции. Улучшением технологичности конструкции можно увеличить выпуск продукции при тех же средствах производства. Трудоемкость машин нередко удается сократить на 15-25% и более, а себестоимость их изготов-ления уменьшить на 5-10%.
На начальном этапе отработки изделия на технологичность целесо-образно выполнение следующих действий:
- На основании изучения конструкции детали, её служебного назначения, технических требований на её изготовление, определения типа производства сделать анализ возможности упрощения конструкции детали или её отдельных элементов.
- Для деталей, подвергающихся термической обработке, рассмотреть возможность введения новых конструктивных элементов, уменьшающих её коробление в результате температурного воздействия.
- С целью оптимизации выбора рационального метода получения заготовки исследовать возможность замены марки материала детали и т.д.
- Нормализовать и унифицировать элементы детали для унификации режущего и измерительного инструмента.
Оценка технологичности конструкции изделия может быть двух видов – качественной и количественной.
При качественном анализе ТКИ необходимо определить:
- Обеспечивается ли нормализация и унификация деталей и сборочных единиц, а также элементов конструкции детали (резьб, шлицев, шпонок, модулей зубьев и т.п.), позволяющих уменьшить число операций, переходов, оснастки, оборудования.
- Достаточно ли ограничена номенклатура применяемых материалов (для сборочных единиц).
- Обеспечено ли членение изделия на сборочные единицы с возмож-ностью применения производственных процессов сборки, контроля испытания.
- Возможно ли использование методов получения заготовок, обеспечи-вающих получение ряда поверхностей, не требующих дальнейшей обработки или требующих обработки с малыми припусками.
- Могут ли основные конструкторские базы использоваться как измерительные и технологические, что снижает погрешность базирования и трудоёмкость механической обработки.
- Позволяет ли простановка размеров на чертежах деталей производить обработку по принципу автоматического получения размеров на настроенных станках, автоматах и полуавтоматах.
- Позволяет ли конструкция детали применять наиболее совершенные и производительные методы механической обработки на многорезцовых, агрегатных и многопозиционных станках фасонным и многолезвийным инструментом и т.д.
- Обеспечены ли обработка на проход, условия для врезания и выхода режущего инструмента, доступ ко всем элементам изделия для обработки и измерения, есть ли возможность замены глухих отверстий сквозными и пр.
Анализ технологичности конструкции по качественным показателям сводится в таблицу 2.
Таблица 2
Оценка качественных показателей технологичности конструкции изделия
№№ п/п | Наименование показателей | Степень соответствия данному показателю |
| | |
Для количественного анализа ТКИ рекомендуется все поверхности детали пронумеровать. Нумерацию производить по часовой стрелке араб-скими цифрами в окружностях на выносных линиях. Это позволит упростить и ускорить процесс проведения анализа, а также идентифицировать обозна-чение обрабатываемых поверхностей в технологической документации.
Количественную оценку технологичности конструкции изделия рекомендуется производить по следующим показателям.
- По коэффициенту унификации конструктивных элементов:
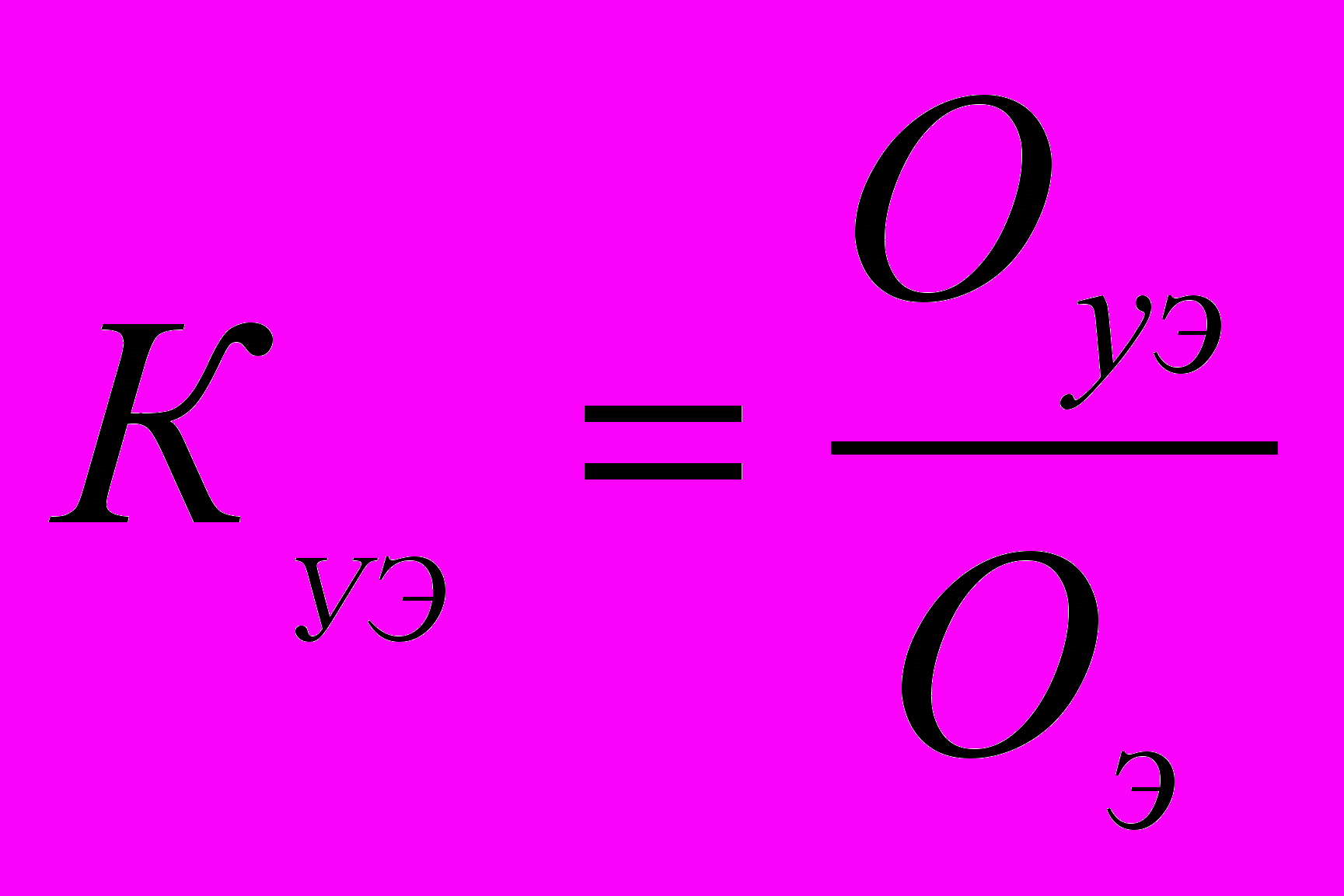
где
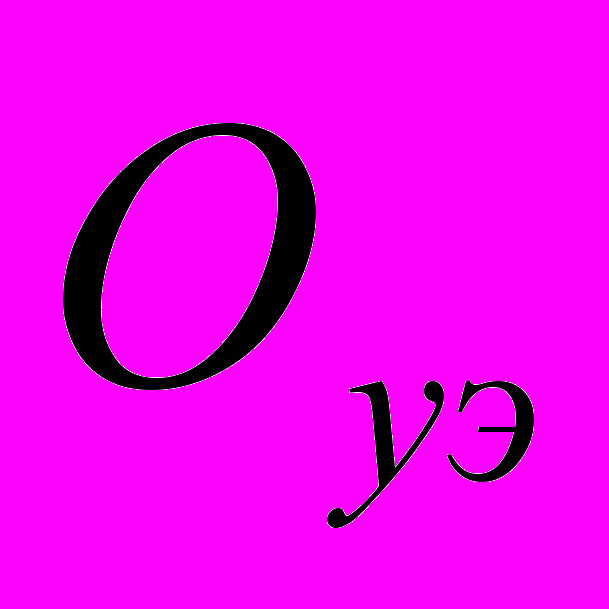
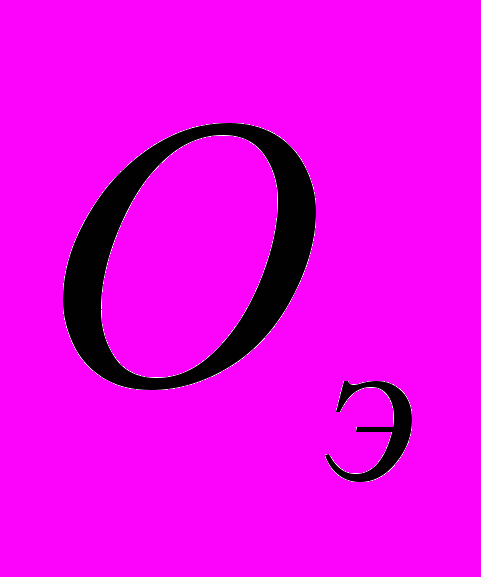
По ЕСТПП для технологичных изделий
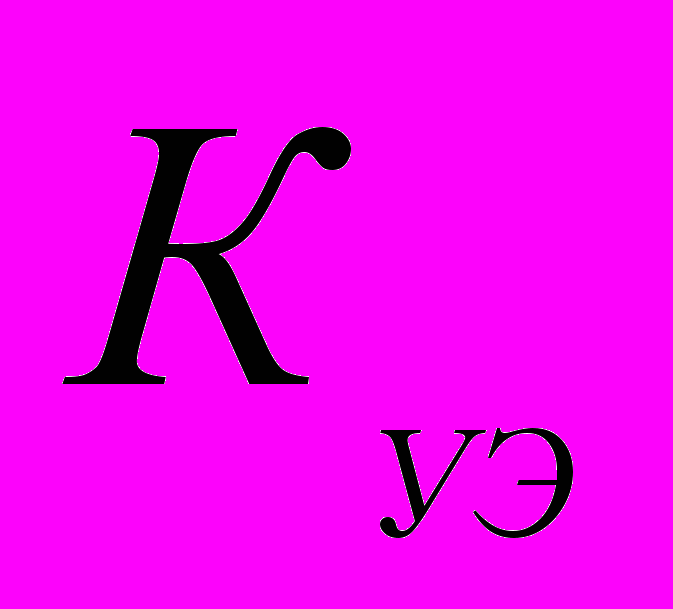
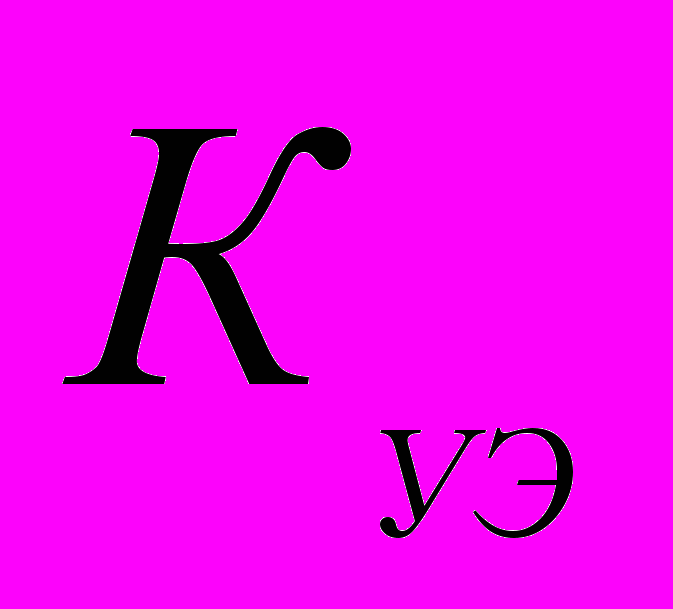
2. По коэффициенту точности обработки:
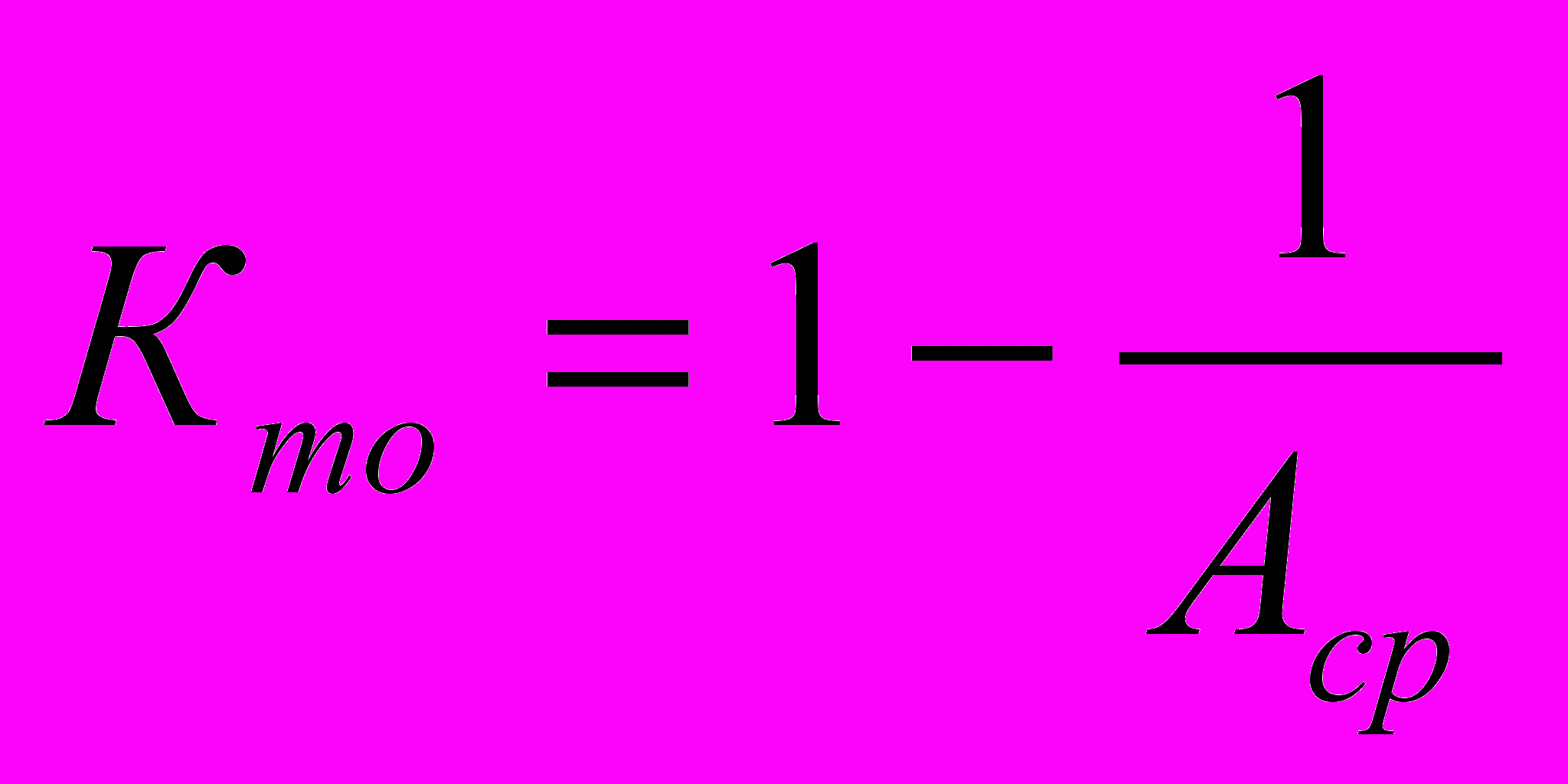

где
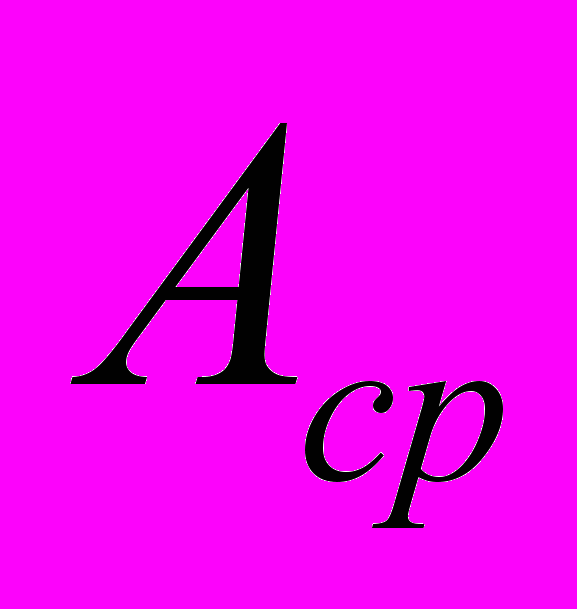
Чем больше
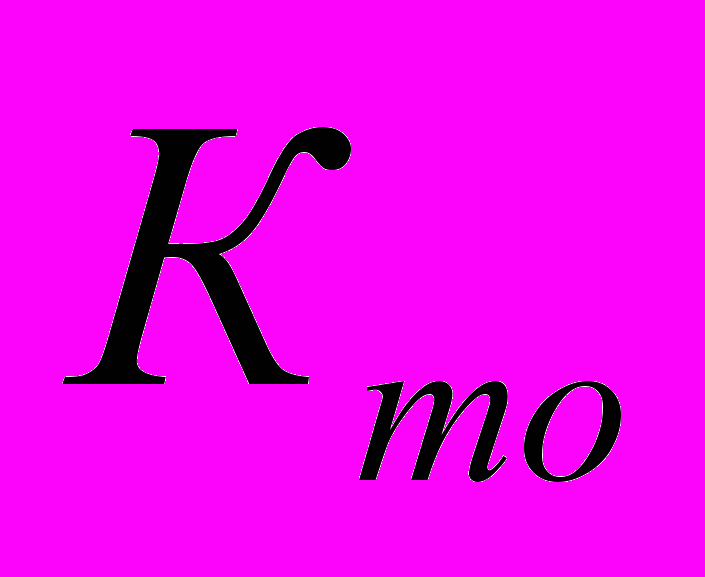
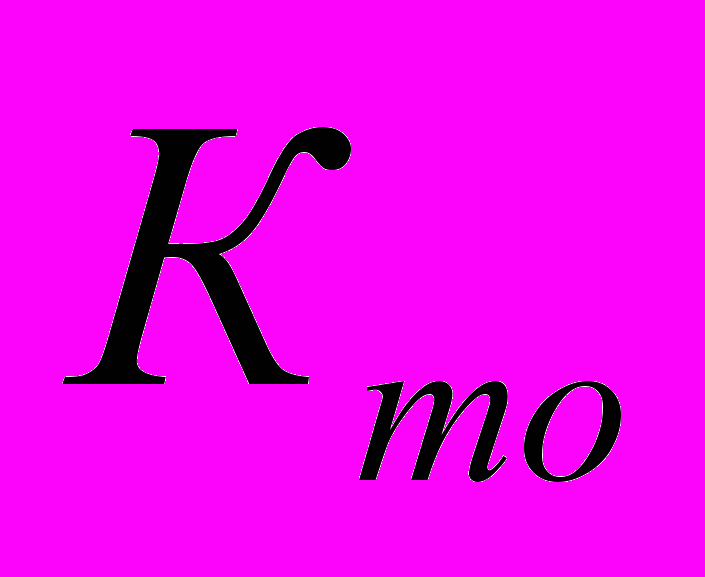
- По коэффициенту шероховатости:
,
где

Чем больше коэффициент шероховатости
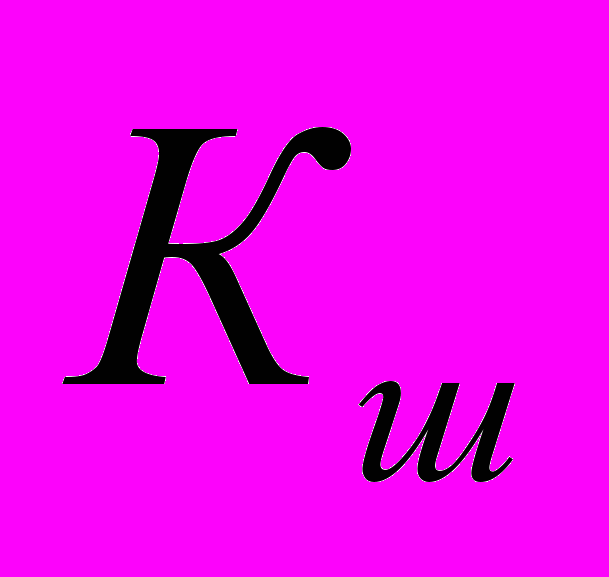
- По коэффициенту использования материала:
,
где
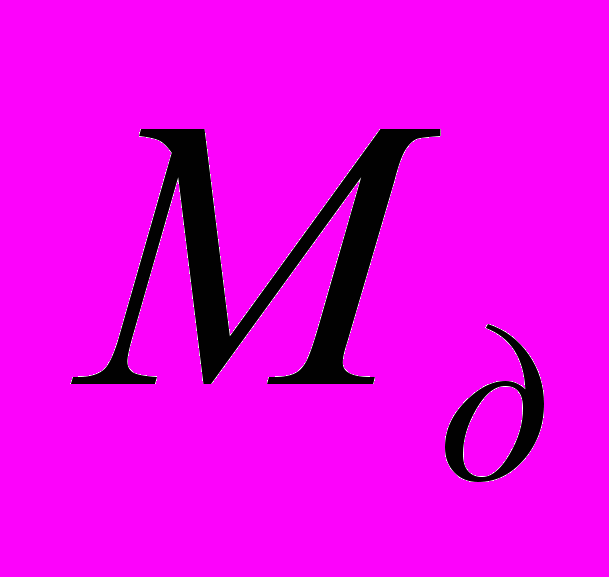
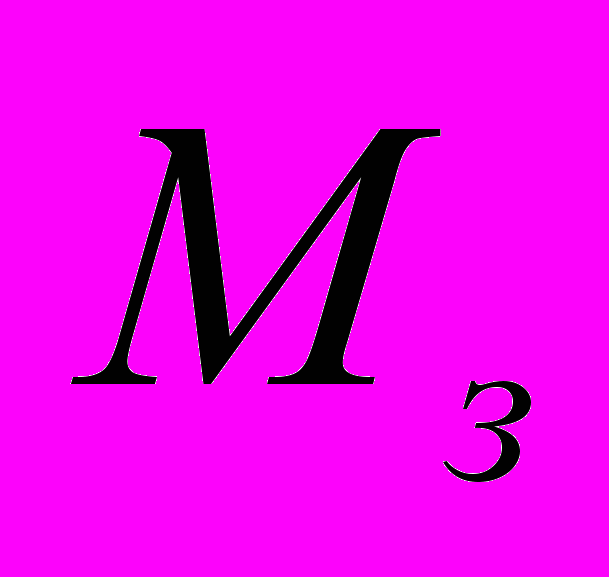
Коэффициент использования материала должен быть
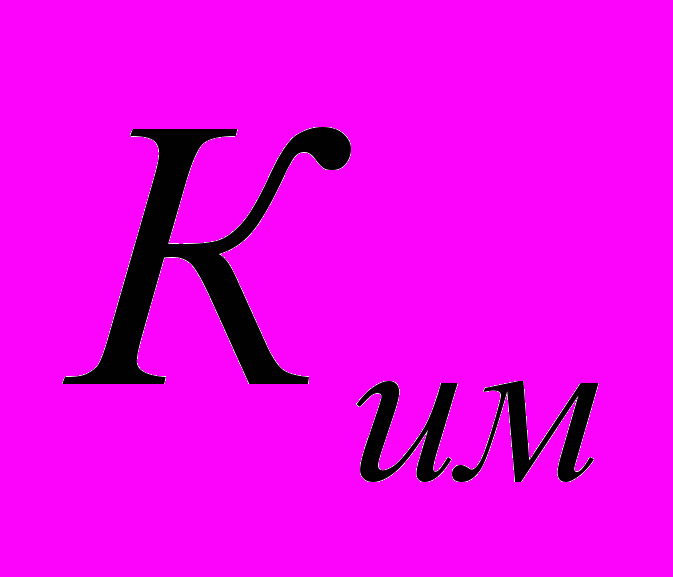
5.3. Технико-экономическое обоснование выбора метода
получения заготовки и ее проектирование
Одним из важнейших этапов проектирования технологии изготовления детали является выбор исходной заготовки. В машиностроении основными видами получения заготовок являются – литье стальное, чугунное и из цветных и жаропрочных сплавов, поковки и штамповки стальные, из титановых и легких сплавов, всевозможные профили проката. На выбор формы, размеров и метода получения заготовки большое влияние оказывают материал, конструкция, размеры, функциональное назначение детали, тип производства и другие факторы.
Цель этого этапа курсового проектирования – выбор оптимального метода получения исходной заготовки, позволяющего в данных производ-ственных условиях свести к минимуму технические и экономические затраты, позволяющие снизить себестоимость изготовления детали и, соответственно, повысить её конкурентоспособность.
Рационально подобранный метод получения заготовки в значительной мере предопределяет технологический процесс изготовления детали, сводя к минимуму число обрабатываемых поверхностей детали, величину снимаемых припусков, количество переходов и операций механической обработки и т.д.
Выбор заготовки и метода её получения необходимо производить в следующей последовательности.
- Определение вида заготовки.
- Выбор метода получения заготовки.
- Назначение припусков на все обрабатываемые поверхности.
- Разработка эскиза заготовки и её массы.
- Технико-экономическая оценка конкурирующих вариантов получения заготовки.
Подбирают наиболее прогрессивный метод получения заготовки, кон-курирующий с базовым, учитывая требования и условия производства, при этом предпочтение отдается методу, позволяющему обеспечить точность и качество получаемой заготовки (таблица 3).
Таблица 3
Качество поверхностей заготовок
Вид заготовки | Точность, квалитет | Шероховатость, Rа, мкм |
Литье в землю (песчано-глинистые формы) | - | 80 |
Литье в кокиль | 12…14 | 5…80 |
Литье в оболочковые формы | 12…14 | 5…20 |
Литье под давлением | 9…12 | 2,5…10 |
Литье по выплавляемым моделям | 9…12 | 5…10 |
Штамповка | 15…17 | 40…75 |
Прокат горячекатаный | 14…16 | 40…75 |
Прокат калиброванный гладкотянутый | 7…12 | 10…20 |
Выбор вида заготовок и сортамента материала можно производить по справочникам [4].
5.4. Анализ базового технологического процесса
изготовления детали
Рассматривая заводской технологический процесс изготовления детали, следует указать его достоинства и недостатки. Для этого необходимо проанализировать все операции с точки зрения соблюдения принципов проектирования технологических процессов, применяемое оборудование с позиций правомерности его выбора по назначению (габариты, точность, мощность, универсальность), его прогрессивности, технологическую оснас-тку (установочно-зажимные и контрольно-измерительные приспособления), инструмент (режущий и измерительный), режимы резания, нормы времени. Рассматривается соответствие базового технологического процесса требо-ваниям ЕСТП, ЕСКД и ЕСТПП с позиций оформления – используемая технологическая документация (ТЛ, МК, ОК, КЭ, ОКТК и др.), правильность её заполнения. Особое внимание следует обратить на уровень автоматизации и механизации всех производственных процессов изготовления детали. В результате выполнения анализа следует отметить те операции базового технологического процесса, которые целесообразно использовать в разраба-тываемом техпроцессе.
5.5. Разработка и обоснование проектируемого
технологического процесса изготовления детали
В курсовом проекте чаще всего разрабатываются единичные техноло-гические процессы. При проектировании технологических процессов необхо-димо стремиться полностью использовать все технические возможности станка, инструмента, приспособлений при оптимальных режимах резания и в итоге обеспечить заданные технические условия на обработку с наибольшей производительностью и наименьшей себестоимостью. Технологический про-цесс для условий мелкосерийного производства следует разрабатывать по принципу группового метода обработки деталей, дающего возможность эффективно применять на универсальном оборудовании специализированную высокопроизводительную технологическую оснастку, использовать станки с ЧПУ и обрабатывающие центры, позволяющие повысить производительность труда, сократить сроки подготовки производства, использовать рабочих более низкой квалификации и т.д. Для условий серийного производства следует проектировать технологический процесс, ориентируясь на использование переменно-поточных линий, когда параллельно изготавливаются партии деталей разных наименований. В условиях массового производства следует стремиться разрабатывать технологический процесс для непрерывной поточной линии с использованием высокопроизводительных станков, специальной технологической оснастки и максимальной автоматизации и механизации производства.
В основу разработки технологических процессов положены два прин-ципа – технический и экономический. В соответствии с техническим принципом проектируемый технологический процесс должен полностью обеспечить выполнение всех требований рабочего чертежа и технических требований на изготовление заданной детали. В соответствии с эконо-мическим принципом, изготовление должно вестись с минимальными затратами труда и издержками производства.
Кроме того, разработанный технологический процесс должен соответ-ствовать требованиям техники безопасности и промышленной санитарии, изложенным в системе стандартов безопасности труда (ССБТ), инструкциях и других нормативных документах.
Разработка технологических процессов состоит из взаимосвязанных этапов, для которых определены конкретные задачи, а также основные документы и системы, обеспечивающие решение этих задач. В общем виде можно представить укрупненную схему последовательности выполнения этапов проектирования технологии механообработки заготовки, представлен-ную на рис.1.
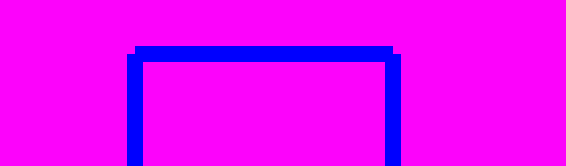
Из этой схемы видна взаимосвязь этапов проектирования техноло-гических процессов. Задачи, связанные с выполнением некоторых этапов были рассмотрены выше.
5.5.1 Выбор баз
Выбор баз необходимо делать обоснованно, показать их связь с точностью выполнения размеров, с конструкцией приспособлений и произво-дительностью обработки. При выборе технологических баз необходимо соблюдать ряд принципов.
- Выбирать такую схему базирования, которая обеспечит наименьшую погрешность установки.
- Соблюдать принцип совмещения баз – совмещать конструкторскую, технологическую и измерительную базы.
- Стремиться к соблюдению принципа постоянства баз – на различных операциях механообработки использовать одни и те же базы (поверхности) обрабатываемой детали.
Кроме этого необходимо помнить, что нельзя использовать дважды (и более) в качестве баз «черные» (необработанные) поверхности заготовки. При этом в случае использования в качестве баз «черных» поверхностей, приоритет отдается тем поверхностям, которые после изготовления детали остаются не обработанными. Поэтому на первой операции всегда идет подготовка технологических баз под последующую обработку.
При выборе баз рекомендуется использовать литературу [1, 2, 3].
5.5.2 Разработка маршрутного технологического процесса
обработки детали
Вначале полезно ознакомиться с типовыми технологическими процесс-сами механической обработки, а также с основными принципами проектирования таких процессов [1, 5].
Следует помнить, что каждый процесс (точение, хонингование и т.д.) обеспечивает соответствующую ему точность и шероховатость поверхности лишь в том случае, если проведена необходимая предварительная подготовка обрабатываемой поверхности. Например, развертывание отверстия ∅>12 мм позволяет получить 7-й квалитет точности и 7-8-й классы шероховатости лишь при условии, что отверстие предварительно обработано зенкером и черновой разверткой.
При обработке отверстий диаметром до 15 мм включительно в чугуне растачивание зенкером не применяется. В случае применения одной развертки на неё распространяется суммарный припуск черновой и чистовой разверток. Начиная с ∅75 мм, рекомендуется вместо сверления спиральными сверлами применять кольцевое сверление. При наличии больших литейных припусков первое черновое растачивание производить в два или больше проходов. В случае применения одной развертки на нее распространяется суммарный припуск черновой и чистовой разверток. Таким образом, выбрав процесс финишной обработки, необходимо выбрать процессы предвари-тельной обработки поверхностей деталей.
При установлении последовательности операций следует руковод-ствоваться следующими общими соображениями:
- в первую очередь надо обработать поверхности деталей, которые являются основными базами для дальнейшей обработки;
- затем следует обрабатывать поверхности, с которых снимается наиболее толстый слой металла, так как при этом легче обнаруживаются дефекты заготовки (раковины, включения, трещины и т. п.);
- операции, при выполнении которых существует вероятность брака из-за дефектов в материале или сложности механической обработки, должны выполняться в начале процесса;
- далее последовательность операций устанавливается в зависимости от требуемой точности поверхности: чем точнее должна быть поверхность, тем позднее она должна обрабатываться, так как обработка каждой последующей поверхности может вызвать искажение ранее обработанной поверхности. Это происходит из-за того, что снятие каждого слоя металла с поверхности детали вызывает перераспределение остаточных напряжений, что приводит к деформации детали;
- поверхности, которые должны быть наиболее чистыми, также обраба-тываются последними. Этим исключается или уменьшается возможность повреждения окончательно обработанных поверхностей.
Если такие поверхности были обработаны ранее и потом выполнялись другие операции, то их обрабатывают повторно для окончательной отделки.
В плане обработки, который составляется перед оформлением маршрут-ного технологического процесса, указывается последовательность выпол-нения технологических операций, начиная от черновой обработки заготовки и кончая контролем готовой детали. По каждой операции устанавливаются: метод обработки, используемое оборудование, приспособление и режущий инструмент.
Любая деталь может быть получена различными методами механической обработки: могут быть применены различные виды оборудования, различные приспособления (универсальные или специальные), различные виды инстру-ментов (универсальные, специальные), могут использоваться различные виды заготовок (прутки, поковки, штамповки, разной точности отливки).
Студент предлагает несколько вариантов процесса и дает общую словесную оценку каждого (достоинства и недостатки). Затем по согласованию с руководителем выбираются два варианта процесса, которые подробно разрабатываются и сравниваются по технологической себес-тоимости. В плане обработки указывается только вид заготовки, наимено-вание операций, оборудование, приспособления и инструменты.
5.5.3 Расчет припусков и промежуточных размеров
При проектировании технологического процесса механической обработки необходимо установить оптимальные припуски, которые бы обеспечивали заданную точность и качество обрабатываемых поверхностей.
Припуски могут быть операционными и промежуточными.
Операционный припуск – это припуск, удаляемый при выполнении одной технологической операции.
Припуск, удаляемый при выполнении одного технологического пере-хода, называют промежуточным.
Установление оптимальных припусков играет важную роль при разработке технологических процессов изготовления деталей. Увеличение припусков приводит к повышенному расходу материала и энергии, введению дополнительных технологических переходов, а иногда и операций. Все это увеличивает трудоёмкость и повышает себестоимость изготовления деталей, а значит и уменьшает конкурентоспособность всего изделия в целом.
Необоснованно уменьшенные припуски не дают возможность удалить дефектные слои материала и достичь заданной точности и шероховатости обрабатываемых поверхностей, что может привести к появлению брака.
Имеются два основных метода определения припусков на механическую обработку поверхности: опытно-статистический и расчетно-аналитический.
В опытно-статистическом методе припуск устанавливают по стандартам и таблицам, которые составлены на основе обобщения и систематизации производственных данных целого ряда производственных предприятий. Припуски на механическую обработку поковок, изготовленных различными методами, и отливок из металлов и сплавов приведены в ГОСТ 7505-89, ГОСТ 7062-90, ГОСТ 7829-70, ГОСТ 26645-85.
При расчетно-аналитическом методе, разработанным проф. М.В. Кова-ном, рассчитывают минимальный припуск на основе анализа факторов, влияющих на формирование припуска, с использованием нормативных документов. При этом припуски на обработку определяют таким образом, чтобы на выполняемом технологическом переходе были устранены погреш-ности изготовления детали, которые остались от предшествующего перехода.
В курсовом или дипломном проекте при разработке технологического процесса изготовления детали припуски на механическую обработку на одну из наиболее точных поверхностей определяют расчетно-аналитическим методом [4]. На все остальные поверхности припуск определяется опытно-статистическим методом [4].
Имея расчетные формулы и заданные чертежом предельные размеры рассматриваемой поверхности, можно определить предельные размеры по всем технологическим переходам при обработке этой поверхности, включая размеры исходной заготовки.
Операционные размеры и допуски определяют для всех операций и переходов. Они необходимы для оформления операционных карт, операции-онных эскизов и настроечных схем обработки.
Результаты расчетов припусков и межоперационных размеров обычно представляют в виде таблицы.
5.5.4 Построение операций и выбор оборудования
Основные задачи, которые решаются на этом этапе – это определение рациональной структуры операции, что позволяет разработать или уточнить содержание и последовательность переходов в операции, возможность их совмещения во времени; разработать операционные эскизы и схемы наладок, рассчитать настроечные размеры; выбрать средства технологического оснащения, средства механизации и автоматизации выполнения операции, выбрать или уточнить оборудование.
Степень концентрации и дифференциации операций является важней-шим принципом построения операции технологического процесса механической обработки заготовок.
Концентрацией операции называется объединение нескольких простых технологических переходов в одну операцию. Дифференциацией операции называется разделение операции на несколько более простых.
При концентрации операции сокращают число установов заготовок на станок, широко применяют многоинструментальную обработку одной или нескольких поверхностей, а также многоместную обработку. При этом повышается точность взаимного расположения обрабатываемых поверх-ностей, производительность обработки за счет снижения основного и вспомогательного времени, сокращается длительность производственного цикла и т.д. Но, при этом, возрастают требования к точности станка, его технологическим возможностям, непрофильное использование рабочих высокой квалификации (выполнение как окончательной, так и предвари-тельной обработки) и др.
При дифференциации операций происходит разделение обработки на предварительную и окончательную с соответствующим использованием оборудования и трудовых ресурсов.
В зависимости от конкретных производственных условий используется тот или иной принцип.
Для технологических процессов единичного и мелкосерийного произ-водства характерно построение операций по принципу концентрации. В среднесерийном производстве часто используют оба принципа. В массовом и крупносерийном производстве в основном применяется принцип дифферен-циации операций, особенно если используются поточные и автоматические линии с использованием специального оборудования.
При разработке технологической операции необходимо стремиться к уменьшению штучного времени. Очень эффективным направлением в этом плане является оптимизация построения схемы станочной операции. Для этого используются:
- одноместные и многоместные схемы (по числу одновременно устанавливаемых для обработки заготовок);
- одноинструментальные и многоинструментальные схемы (по числу участвующих в обработке инструментов);
- схемы последовательного, параллельного и параллельно-последовательного выполнения (по очередности участия в работе режущих инструментов).
Выбор модели станка определяется, прежде всего, возможностью изготов-ления на нем деталей необходимых размеров, конфигурации и шероховатости. Если эти требования можно обеспечить на различных станках, то конкретную модель оборудования выбирают из следующих соображений:
- соответствия размеров рабочей зоны станка габаритам заготовки;
- соответствия точности станка заданной точности детали;
- соответствия его производительности расчетной;
- соответствия мощности оборудования потребной мощности;
- возможности автоматизации и механизации выполняемых на этом станке работ;
- обеспечения минимальных затрат по себестоимости продукции…
При выборе оборудования с использованием ЧПУ, кроме вышесказан-ного необходимо учитывать объем инструментального магазина, количество управляемых координат, постпроцессор и др. Технические характеристики ряда станков можно найти в литературе [4].
Таким образом, на этапе разработки операции определяется тип и модель станка, установочно-зажимное приспособление, режущий, вспомогательный и мерительный инструмент и оснастка, СОЖ, количество одновременно изготавливаемых деталей, технологические базы, схема последовательности обработки поверхностей, последовательность выполнения переходов и т.д.
5.5.5 Определение рациональных режимов резания
Разработка технологического процесса механической обработки завер-шается установлением технически обоснованных норм времени на каждую операцию. Чтобы добиться оптимальных норм времени, необходимо в полной мере использовать режущие свойства инструмента и технические возмож-ности металлорежущего оборудования. Для этого определяются рациональ-ные режимы резания на все операции механической обработки детали. Наилучшие результаты дает аналитический расчет режимов резания с помощью эмпирических зависимостей.
При выборе режимов обработки необходимо придерживаться опреде-ленного порядка, т.е. при назначении и расчете режимов резания учитывают тип и размеры режущего инструмента, материал его режущей части, материал и состояние заготовки, тип и мощность оборудования и т.д. Следует помнить, что элементы режимов резания функционально взаимосвязаны между собой.
Определение режимов резания начинают с описания исходных данных, куда входят: наименование и номер операции, содержание (структура) операции, операционный эскиз, технические требования на изготовление детали, паспортные характеристики оборудования, материал заготовки и его механические свойства, сведения о режущем инструменте (материал режущей части, стойкость). Для каждого перехода определяют глубину резания, подачу, скорость резания, частоту вращения, силу резания, крутящий момент и мощность резания.
Полученные режимы резания корректируются по паспортным данным станка и проверяются по мощности его электродвигателя. Необходимо, чтобы потребная мощность резания не превышала номинальную мощность электродвигателя оборудования.
В связи с тем, что аналитический расчет режимов резания является процессом довольно трудоёмким, в курсовом или дипломном проекте таким методом определяются режимы резания на 2-3 операции по согласованию с руководителем проекта. Для остальных операций технологического процесса режимы резания определяются по нормативам режимов резания с учетом конкретных условий [4].
5.5.6 Нормирование технологических операций
Техническая норма времени на обработку заготовки является одним из основных параметров для расчета стоимости детали, количества метал-лорежущего оборудования, заработной платы рабочих, планирования произ-водства.
Техническую норму времени определяют на основе технических воз-можностей станочного оборудования, технологической оснастки, режущего инструмента, схемы построения операции и переходов, автоматизации процесса обработки детали. В массовом производстве рассчитывается штучное время, в серийном и единичном – штучно-калькуляционное.
Технической нормой времени называется время, необходимое на выполнение операции в конкретных производственных условиях. Расчет заработанной платы, входящей в себестоимость продукции, и сравнение трудоемкости различных операций производятся на основании штучно- калькуляционного времени, которое определяется по формуле:
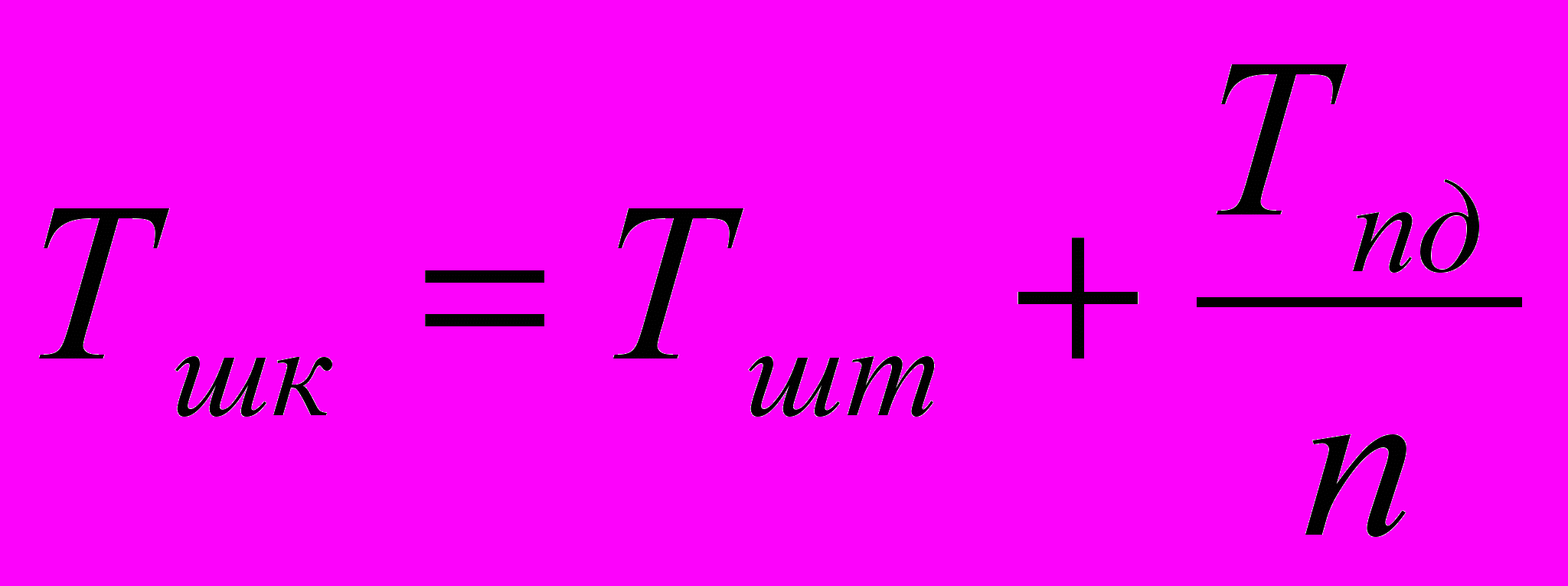
где
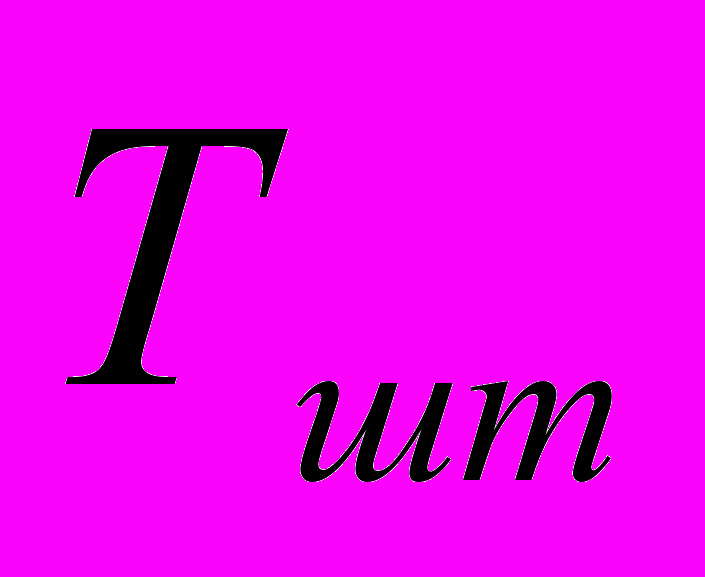
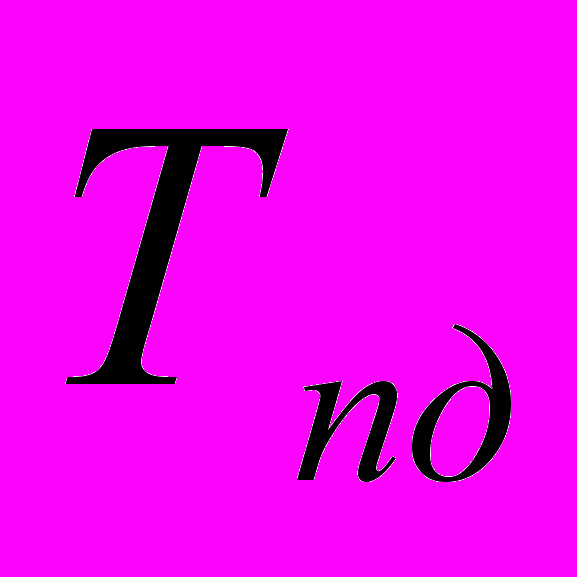
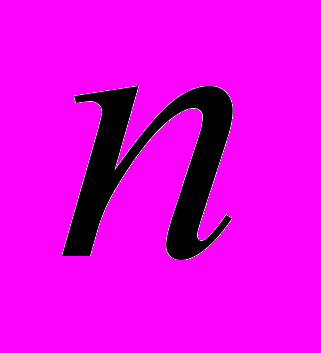
Подготовительно-заключительное
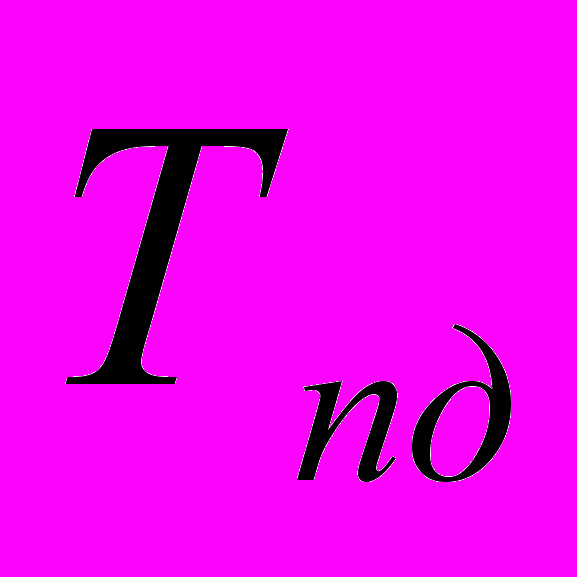
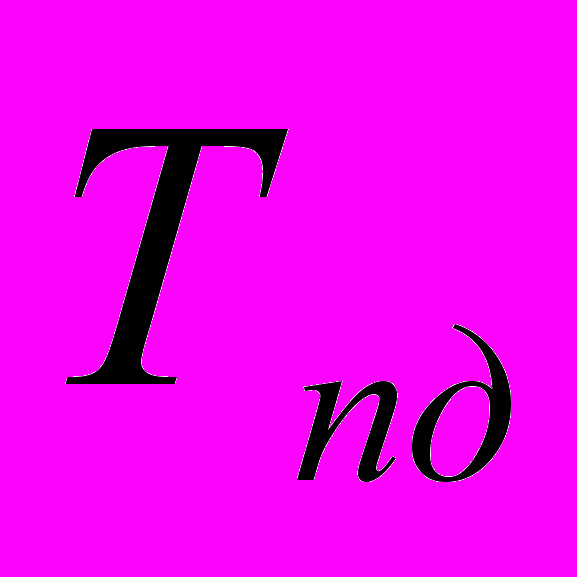
Количество деталей в партии можно определить исходя из годовой программы выпуска данных деталей N , запаса деталей в днях (в сутках)
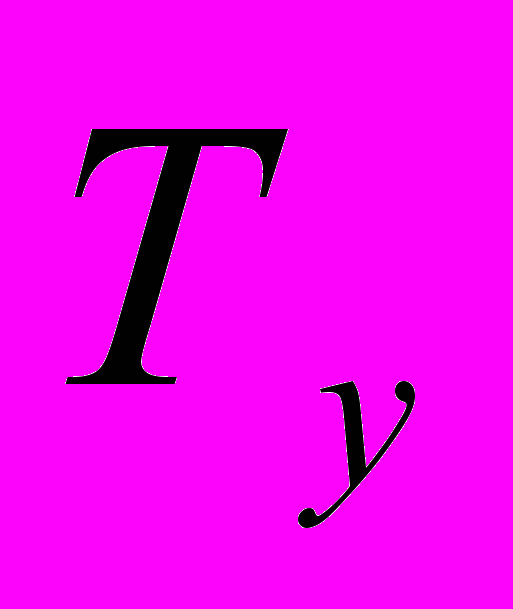
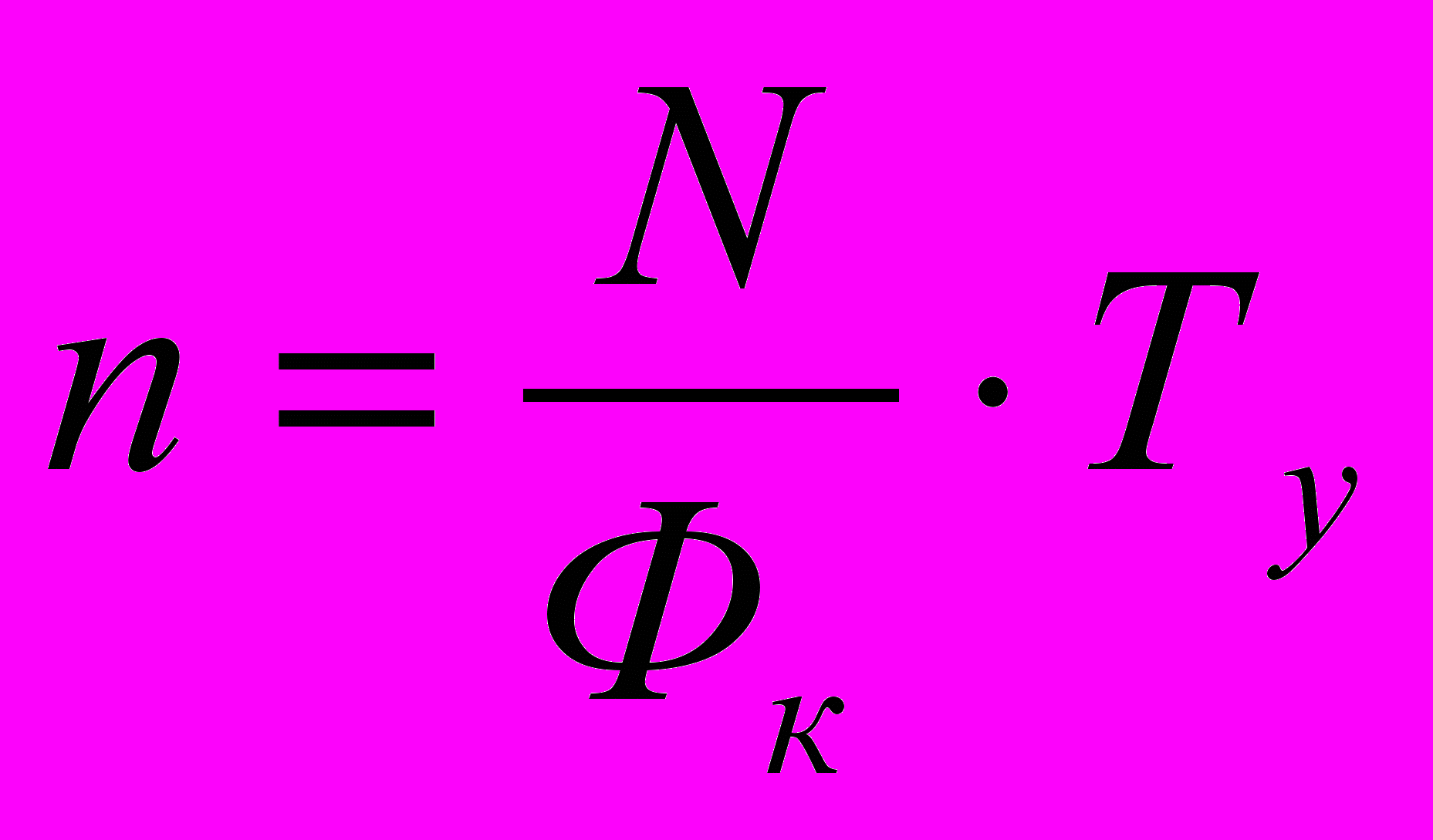
Время
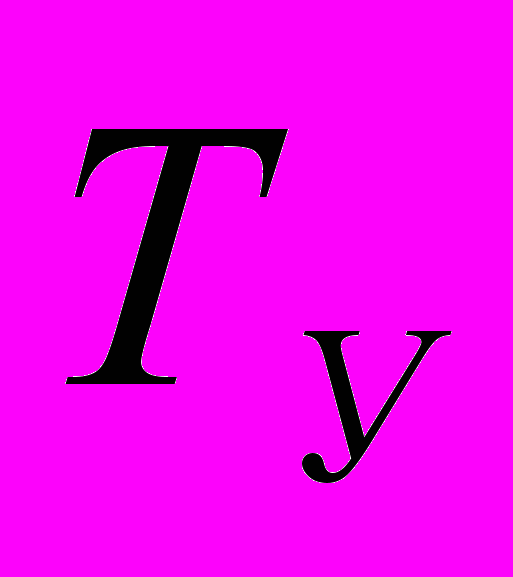
Штучное время в общем виде может быть представлено в виде суммы следующих слагаемых:
Тшт =То + Тв + Торг +ТTах + Тотд .
Основное время То – время, в течение которого происходит изменение формы, размеров или состояния поверхности обрабатываемой детали.
Для процессов механической обработки основное время определяется по формуле:
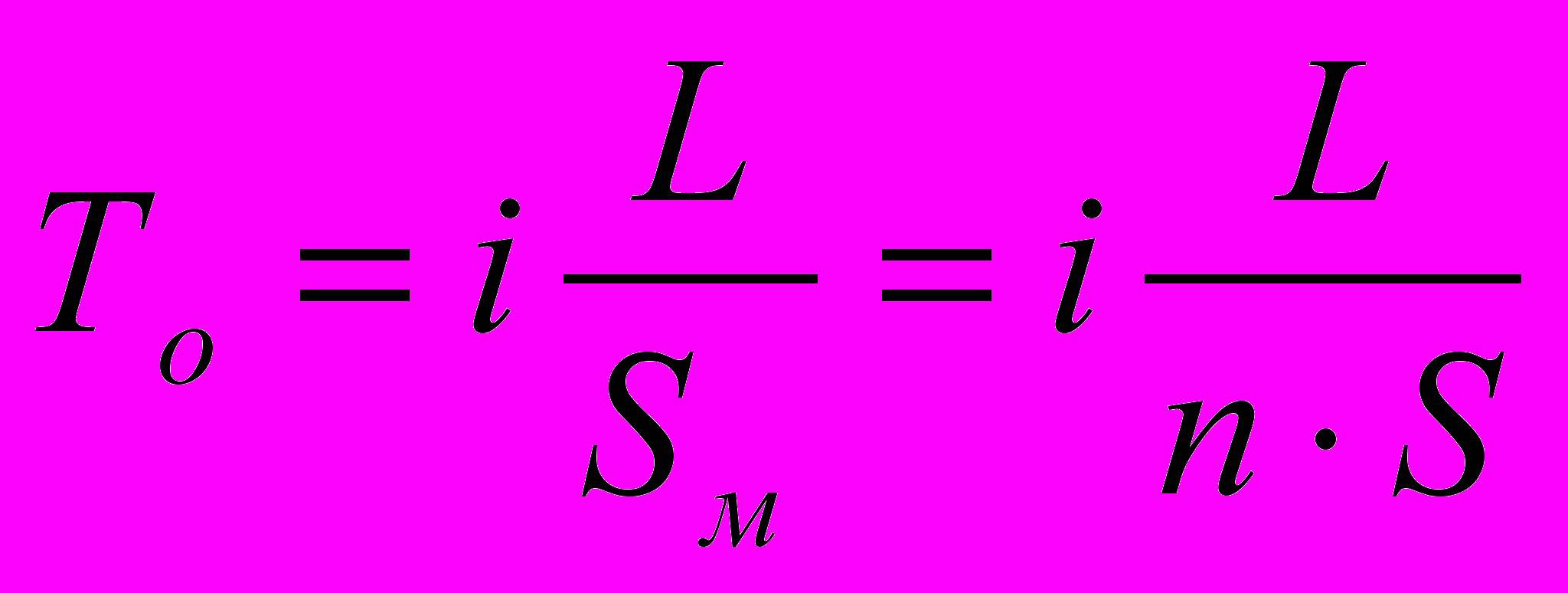
где i – число проходов для снятия припуска; L – длина рабочего хода в направлении подачи; мм; Sм – подача, мм/мин; n – частота вращения изделия или инструмента (об/мин) или число двойных ходов в мин;
S – подача на один оборот или двойной ход (изделия или инструмента), мм.
Длина рабочего хода в направлении подачи состоит из трех величин:
L = l+l1 +l2 ,
где l – длина обрабатываемой поверхности в направлении подачи; l1 и l2 – врезание и перебег инструмента.
Вспомогательное время Тв – время, затрачиваемое на создание условий для выполнения основной работы.
Во вспомогательное время входит время на установку и снятие детали, на изменение режима работы оборудования, подвод и отвод инструмента, замену инструмента в процессе выполнения операции, измерение детали в процессе ее обработки и т. д. Определяется по нормативам [13-16].
Основное и вспомогательное время составляет вместе оперативное время: Топ = То +Тв .
Время технического обслуживания рабочего места Ттех – время, затрачи-ваемое на смену притупившегося инструмента, регулирование инструмента, подналадку оборудования в процессе работы, сметание стружки и т. д.
Время организационного обслуживания рабочего места Торг – время, затрачиваемое на раскладку и уборку инструмента перед началом и в конце работы, получение инструмента, смазку стакана и т. д.
В некоторых случаях, когда сложно или нецелесообразно определять в отдельности время Ттех и время Торг, определяют время обслуживания рабочего места:
Тобс = Ттех +Торг .
Время на отдых и личные надобности рабочего Тотд определяется по нормативам.
Общая формула для расчета штучного времени в условиях серийного производства включает в себя основное и вспомогательное время, а также доли времени технического и организационного обслуживания и времени на отдых и личные надобности:

где α - отношение времени на техническое обслуживание рабочего места к оперативному времени, %; β - отношение времени организационного обслуживания рабочего времени к оперативному времени, %; γ – отношение времени на отдых и личные надобности к оперативному времени, %.
Величины этих коэффициентов составляют α = (2…10)% , β = (1…8)% , γ = (1…10)% .
В курсовом или дипломном проекте для тех операций, режимы резания которых определялись расчетно-аналитическим путем, нормы времени опре-деляются также расчетно-аналитическим методом [4]. Для остальных операций нормы времени выбираются по табличным данным [15]. Рассчитанные режимы резания и нормы времени вносятся в операционные и маршрутные карты.
- ЗАЩИТА КУРСОВОГО ПРОЕКТА
Текущий контроль за выполнением курсового проекта осуществляется преподавателем. При каждом посещении студента он делает отметку в процентовочном графике о ходе работы и оценивает в процентах готовность графической части и пояснительной записки. По мере готовности работы каждый студент проходит консультацию у своего преподавателя по проделанной работе. Защищенный курсовой проект сдаётся преподавателю с простановкой оценки в ведомость и зачетную книжку. Плановые сроки защиты курсовой работы – 12-13-я неделя семестра.
7. ЗАДАНИЯ К КУРСОВОМУ ПРОЕКТУ
Задание на курсовой проект включает в себя чертёж детали, на которую разрабатывается технологический процесс и оформляется преподавателем на бланке установленного образца. В нем указываются наименование детали, процесс изготовления которой должен разрабатываться, годовая программа выпуска деталей. Чертеж детали и заводскую технологию студент подбирает на производственной практике.
8. РЕКОМЕНДУЕМАЯ ЛИТЕРАТУРА
- Технология машиностроения: проектирование технологии изготовления изделий / В.А. Лебедев, М.А. Тамаркин, Д.П. Гепта. – Ростов н / Д: Феникс, 2008. – 361 с.: ил. – (Высшее образование).
- Клепиков В.В. Технология машиностроения: учебник. – М.: ФОРУМ: ИНФРА-М. 2004. – 860 с.: ил. – (Серия «Профессиональное образование»).
- Технология машиностроения: в 2 кн. / Э.Л. Жуков, И.И. Козарь, С.Л.Мурашкин и др.; Под ред. С.Л. Мурашкина. – 2-е изд., доп. – М.: Высш. шк., 2005. Кн. 1. Основы технологии машиностроения – 278 с.: ил.
- Справочник технолога-машиностроителя: в 2-х т./под ред. А.Г. Косилова и Р.К. Мещерякова. - 5-е изд. перераб. и доп.- М.: Машиностроение, 2003.
- Маталин А.А. Технология машиностроения. – 2-е издание - Лань.: Машиностроение, 2008. - 512 с.
- Горбацевич А. Ф., Шкред В. А. Курсовое проектирование по технологии машиностроения: учебное пособие для вузов. — 5-е издание, стереотипное. Перепечатка с четвертого издания 1983 г. - М.: ООО ИД «Альянс», 2007. - 256 с.
- ГОСТ 3.1130-93. Межгосударственный стандарт. Единая система технологической документации. Общие правила записи технологической информации в технологических документах на технологические процессы и операции. Взамен ГОСТ 3.1104-81 в части раздела 1, 2, 3. - М.: Изд-во стандартов, 1995.
- ГОСТ 3.1129-93. Межгосударственный стандарт. Единая система технологической документации. Общие правила записи технологической информации в технологических документах на технологические процессы и операции. Взамен ГОСТ 3.1104-81 в части раздела 3. - М.: Изд-во стандартов, 1995.
- ГОСТ 3.1404-86. Единая система технологической документации. Формы и правила оформления документов на технологические процессы и операции обработки резанием / Комитет стандартизации и метрологии СССР. - М.: Изд-во стандартов, 1992.
- ГОСТ 3.1105 – 84. Единая система технологической документации. Формы и правила оформления документов общего назначения. - М.: Изд-во стандартов, 1992.
- ГОСТ 3.1502 – 85. Единая система технологической документации. Формы и правила оформления документов на технический контроль. - М.: Изд-во стандартов, 1987.
- ГОСТ 3.1118 – 82. Единая система технологической документации. Формы и правила оформления маршрутных карт. - М.: Изд-во стандартов, 1987.
- ГОСТ 3.1702-79. Единая система технологической документации. Правила записи операций и переходов. Обработка резанием. - М.: Изд-во стандартов, 1980.
- ГОСТ 3.1703-79. Единая система технологической документации. Правила записи операций и переходов. Слесарные, слесарно-сборочные работы. - М.: Изд - во стандартов, 1980.
- ГОСТ 14.004 – 83. (СТ СЭВ 2521 – 80). Единая система технологической подготовки производства. Термины и определения основных понятий / Государственный комитет СССР по стандартам. - М.: Изд-во стандартов, 1984.
- ГОСТ 2.105-95. Единая система конструкторской документации. Основные требования к текстовым документам / Межгосударственный совет по стандартизации, метрологии и сертификации. - М.: Изд-во стандартов, 1995.
- ГОСТ 2.106–96. Единая система конструкторской документации. Текстовые документы. - Мн.: ИПК Изд-во стандартов. 1998.
- ГОСТ 2.109-73. Единая система конструкторской документации. Основные требования к чертежам. - М.: Изд-во стандартов, 1995.
- ГОСТ 2.305-68. Единая система конструкторской документации. Изображения-виды, разрезы, сечения. - М.: Изд-во стандартов, 1995.
- ГОСТ 2.307-68. Единая система конструкторской документации. Нанесение размеров и предельных отклонений. - М.: Изд-во стандартов, 1995.
- ГОСТ 2.309-73. Единая система конструкторской документации. Обозначение шероховатости поверхности. - М.: Изд-во стандартов, 1995.
- ГОСТ 2.314-68. Единая система конструкторской документации. Указания на чертежах о маркировании и клеймении изделий. - М.: Изд-во стандартов, 1995.
- ГОСТ 3.1107-81. Единая система технологической документации. Опоры, зажимы и установочные устройства. Графические обозначения. - М.: Изд-во стандартов, 1995.
- ГОСТ 3.1407-86. Единая система технологической документации. Формы и требования к заполнению и оформлению документов на технологические процессы (операции), специализированные по методам сборки. - М.: Изд-во стандартов, 1987.
- ГОСТ 2.403-75. Единая система конструкторской документации. Правила выполнения чертежей цилиндрических зубчатых колес. - М.: Изд-во стандартов, 1982.
- ГОСТ 3.1108-74. Единая система технологической документации. Комплектность документов в зависимости от типа и характера производства. - М.: Изд-во стандартов, 1975.
9. СОДЕРЖАНИЕ
1. ВВЕДЕНИЕ 2
2. Основные положения 2
3. Оформление расчётно-пояснительной записки 3
4. Оформление графической части проекта 6
5. Последовательность работы над проектом 6
5.1. Определение типа производства 6
5.2. Анализ исходных данных 7
5.2.1Служебное назначение детали и условия её работы
в сборочной единице 7
5.2.2 Конструкторский контроль чертежа детали 8
5.2.3 Анализ технических требований на изготовление детали 9
5.2.4 Анализ технологичности конструкции детали 9
5.3 Технико-экономическое обоснование выбора метода получении заготовки и её проектирование 13
5.4. Анализ базового технологического процесса изготовления детали 14
5.5. Разработка и обоснование проектируемого технологического процесса
изготовления детали 15
5.5.1 Выбор баз 17
5.5.2 Разработка маршрутного технологического процесса
обработки детали 17
5.5.3 Расчёт припусков и промежуточных размеров 19
5.5.4 Построение операций и выбор оборудования 21
5.5.5 Определение рациональных режимов резания 23
5.5.6 Нормирование технологических операций 24
6. Защита курсового проекта 27
7. Задания к курсовому проекту 27
8. РЕКОМЕНДУЕМАЯ ЛИТЕРАТУРА 28
ПРОЕКТИРОВАНИЕ ТЕХНОЛОГИЧЕСКИХ ПРОЦЕССОВ
МЕХАНИЧЕСКОЙ ОБРАБОТКИ ДЕТАЛЕЙ
Методические указания
к выполнению курсового проекта по дисциплине
«Технология машиностроения»
для студентов специальностей 120100, 060801
всех форм обучения
Составила КУДАШЕВА Ирина Олеговна
Рецензент В.Н. Евсюков
Редактор Л.В. Максимова
Корректор Е.В. Рубан
Подписано в печать Формат 60x84 1/16
Бум. тип. Усл. печ. л. 2,0 Уч. изд. л. 2,0
Тираж 100 экз. Заказ Бесплатно
Саратовский государственный технический университет
410054, г. Саратов, ул. Политехническая, 77
К
