К лекции 2 Структура себестоимости
Вид материала | Лекции |
- Методы учёта затрат и учёта себестоимости Понятие себестоимости. Виды себестоимости, 232.07kb.
- Нормативный метод калькулирования себестоимости как российский вариант «стандарт, 32.79kb.
- Такие разные лекции, 101.86kb.
- И. Г. Лекции по теории интегральных уравнений(7382) Петровский И. Г. Лекции, 55.62kb.
- Тема 7 Анализ себестоимости сельскохозяйственной, 555.39kb.
- «Статистические методы изучения уровня и динамики себестоимости продукции», 457.54kb.
- Планирование себестоимости продукции на предприятии. Ценовая политика на различных, 26.91kb.
- Задачи статистического изучения себестоимости. Основные показатели в анализе себестоимости, 92.6kb.
- Технический Университет «военмех», 1200.54kb.
- Управление персоналом вопросы для подготовки к экзамену, 23.69kb.
1 2
К лекции 2
Структура себестоимости
Химическая технология изучает массовое производство и поэтому она тесно связана с экономикой, т.е. с управлением заводским хозяйством (от греч. оikos – дом, хозяйство; nomos – закон, управление). Знание технико-химических характеристик диктует выбор такого метода производства, который обеспечивает получение максимального количества продукта в единицу времени при минимальных затратах. При расчётах издержек учитывают вид, доступность и стоимость сырья (исходных веществ), количество химических стадий производства целевого продукта, его выход, энергоёмкость и материалоёмкость процесса, возможность комбинирования данного способа производства с другими производствами химического предприятия, т.е. комплексного использования всех получаемых продуктов – не только целевых, но и побочных. Жёсткие требования к выбору метода синтеза целевого вещества включают экологичность производства – отсутствие вредных отходов и отбросов, а также необходимость реализации побочных продуктов, чёткое знание их рынка (потребностей). В целом выбранный процесс должен обладать рентабельностью (Р), которую можно охарактеризовать отношением чистого годового дохода (Д) предприятия к себестоимости (С) целевого продукта:
Р = Д/С = [(ЦС)∙М]/С,
где Ц – цена единицы продукта, М – количество выпускаемых единиц продукта в год.
Таким образом, себестоимость (наряду с удельными капитальными затратами) является одним из главных показателей эффективности массового производства химического продукта. Себестоимостью называют стоимостные издержки предприятия, которые выражают в денежных единицах затраты средств производства и живого труда на получение единицы целевого продукта (обычно в расчёте на одну тонну конечного продукта).
В расчёте себестоимости учитывают следующие элементы затрат.
- Исходное сырьё – основное (превращаемое – например, колчедан, метан, керосин, ацетон) и вспомогательное (катализатор, инертный разбавитель, движущаяся через реактор промежуточная теплопередающая насадка). В химической промышленности это наиболее ёмкий затратный показатель (от 30 до 90% от общей себестоимости).
- Топливо-энергетические затраты (топливо, пар, электроэнергия) состоят из расхода тепловой энергии (на нагревание или охлаждение потоков, на их химическое превращение), электроэнергии и механической энергии (на сжатие газов, перемешивание реакционной смеси, перемещение материальных потоков и т.д.). Известно, что затраты энергии требуются при тепло- и массо-передаче на всех стадиях переработки сырья, выделения и очистки целевого и побочных продуктов. Кроме того, энергетические средства расходуются и на вспомогательные нужды (вентиляция, освещение и прочее). Эта статья затрат обычно колеблется от 8 до 25% от себестоимости.
- Амортизационные отчисления (составляют 5-10% - от себестоимости) представляют собой издержки на восстановление основных фондов предприятия: текущий и капитальный ремонт, замена износившихся (физический износ) или устаревших (моральный износ) аппаратов, ремонт зданий и сооружений. Они являются источником финансирования воспроизводства заводского оборудования и зданий.
- Заработная плата и отчисления на социальное страхование – это затраты, связанные с воспроизводством рабочей силы и охраной труда на предприятии.
- Прочие денежные расходы – накладные. Сюда входят затраты цеховые, общезаводские, административные, транспортные, на хранение продукции, её рекламу, на обучение персонала и другие издержки.
- В случае реализации побочных продуктов, их стоимость вычитается из суммы затрат.
Анализ структуры себестоимости химических продуктов синтеза показывает, что наибольший вклад в расходы на их получение вносят затраты на сырьё. В связи с этим главное внимание в химической технологии уделяется изысканию новых способов производства нужного продукта на других видах сырья, более дешёвого и доступного, на увеличение степени превращения сырья и селективности процесса за счёт подбора новых, более эффективных катализаторов. Эти поиски наряду с другими путями совершенствования химического производства (уменьшение потерь тепла, материалов и т.п.) могут привести к значительному снижению себестоимости целевого продукта, т.е. к его удешевлению и повышению его конкурентоспособности.
3.2. Характеристика методов получения ацетилена
Ацетилен, мировое производство которого достигает нескольких миллионов тонн, служит сырьем для синтеза многих важных продуктов в химической промышленности. Из ацетилена получают ацетальдегид и н-бутанол, уксусную кислоту и её ангидрид, винилацетат и винилхлорид, акрилонитрил, бутадиен и хлоропрен и др. Поэтому поиск новых и совершенствование существующих методов получения ацетилена занимает важное место среди основных направлений развития промышленности основного органического синтеза.
Раньше ацетилен получали, главным образом, карбидным методом. В настоящее время промышленность освоила производства, основанные на пиролизе углеводородного сырья – природного газа и жидких нефтепродуктов. К ним относятся термический и термоокислительный пиролиз, а также электродуговой метод. Комплексное использование продуктов переработки углеводородов обеспечивает получение кроме ацетилена ряда ценных химических продуктов – водорода, низших олефинов, сажи. Таким образом, могут быть снижены капитальные, эксплуатационные, энергетические и трудовые затраты.
3.2.1. Карбидный метод. Этот способ производства ацетилена включает три технологические стадии – обжиг известняка, получение карбида кальция и его разложение до ацетилена:
CaCO3 → CaO + CO2 − 41,8 ккал
CaO + 3C → CaC2 + CO − 108,0 ккал
CaC2 + 2H2O → Ca(OH)2 + C2H2 + 26,5 ккал
Концентрация ацетилена достигает 99,5%. Однако процесс энергоёмок (11-12 квт.ч на один куб. метр ацетилена), многостадиен и характеризуется большим расходом кокса (2,5 кг кокса и 0,25 кг электродов на 1 куб. метр ацетилена) и наличием большого количества труднореализуемых отходов.
3.2.2. Термоокислительный и термический пиролиз. Сырьём для термоокислительного пиролиза являются газообразные углеводороды. За счет их частичного сжигания достигается высокая температура (~1500оС), необходимая для синтеза ацетилена. В случае использования метана суммарная реакция следующая:
1.0 CH4 + 0.63 O2
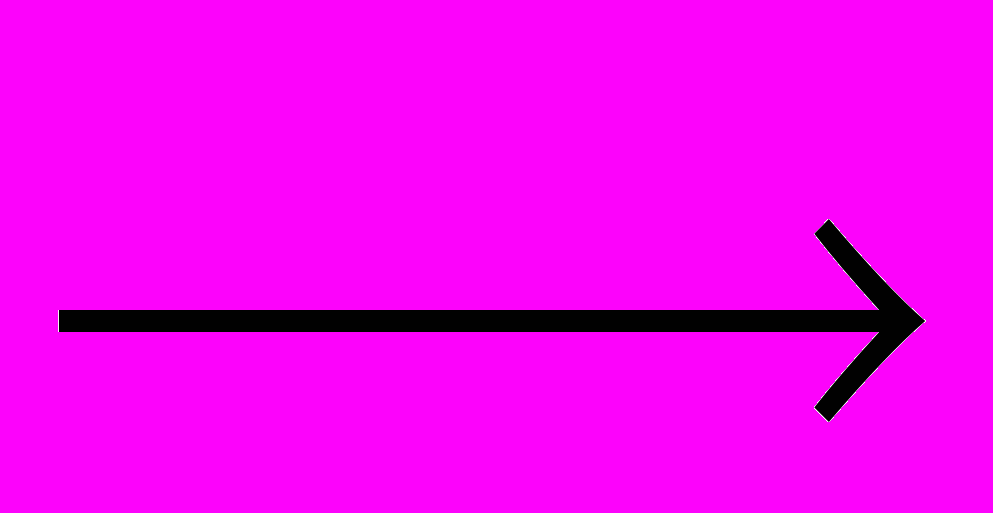
Время пребывания сырья в зоне пиролиза 0,01 – 0,001 сек. В газе пиролиза концентрация ацетилена составляет ~8–12 об. %, этилена 1–2%, гомологов ацетилена ~0,3%, водорода ~55–60%, СО – до 25%. К достоинствам этого способа можно отнести возможность переработки различных видов сырья, высокую производительность реакторов и наличие используемых побочных продуктов. К недостаткам – малую концентрацию ацетилена, высокую температуру в реакторе, большой расход кислорода.
Известны промышленные способы совместного получения ацетилена и этилена термическим пиролизом углеводородов, который осуществляется:
а) в регенеративных печах;
б) в трубчатых печах;
в) в токе газообразного теплоносителя (дымовых газов, перегретого пара или, в последнее время, инертного газа, нагретого в плазме).
Температура в зависимости от способа и сырья колеблется от 1000° до 1300о, время пребывания сырья в реакционной зоне – ~0,03 – 0,005 сек, содержание ацетилена 6 – 14 об.% , этилена 0,3 – 15,0 %, Несмотря на низкую концентрацию ацетилена и относительно высокую стоимость эти способы перспективны.
3.2.3. Электрокрекинг. Получение ацетилена в электрических разрядах относится к области технической химии, использующей методы прямого воздействия электроэнергии на вещество. Электрическая дуга позволяет нагреть органическую среду до нескольких тысяч градусов. При этом происходит преобразование электроэнергии в энергию возбуждения, диссоциации и ионизации молекул углеводородного сырья с образованием возбужденных частиц, атомов и ионов. Активные частицы далее реагируют с окружающей средой, что приводит к протеканию реакции термического характера. Из сказанного понятно, что установить механизм превращений в зоне разряда сложно. Предложено много возможных механизмов распада углеводородов. В случае октана распад может быть следующим:
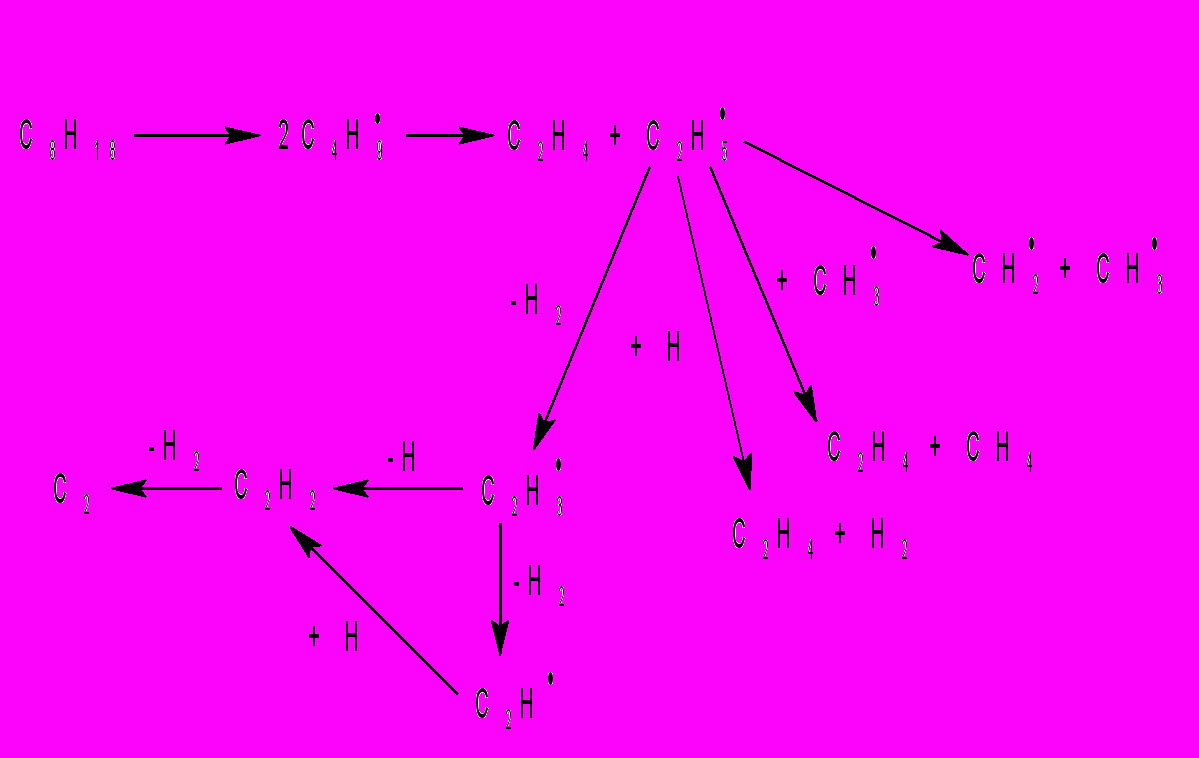
На заводах электрокрекинг метана проводят при напряжении на электродах 300 – 3000 вольт, времени реакции ~ 0,001 сек. Невысокая концентрация ацетилена (~13 %) и большой расход электроэнергии (~13 квт.ч/м3 С2Н2) являются недостатками этого процесса.
При разложении жидких нефтепродуктов в электрических разрядах содержание ацетилена в газе пиролиза достигает 30-33 об%. Высокий выход ацетилена связан с тем, что температура в центральной зоне разряда может достигать 2-4 тысячи градусов (область синтеза ацетилена), в то время как жидкая органическая среда имеет температуру 50-60о (область "закалки"). Образующийся газ пиролиза мгновенно подвергается "закалке", т.е. охлаждению за счет барботажа через холодную жидкость. Это способствует достижению почти равновесных концентраций ацетилена. В случае погружения дуги в жидкую фазу конструкции реакторов упрощаются, однако расход энергии всё-таки остаётся высоким. В качестве сырья можно использовать любые жидкие нефтепродукты от низкооктановых бензинов и керосина до тяжелых масел и сырой нефти. Технико-экономические расчёты показывают, что если принять себестоимость производства одной тонны ацетилена по карбидному методу за 100%, то в случае термоокислительного пиролиза метана она составляет 40%, при термическом пиролизе пропана и для электрокрекинга метана она снижается до одной трети от расходов при карбидном способе.
3.3. Кадькуляция себестоимости ацетилена, получаемого электропиролизом керосина
Себестоимость в части материальных и топливно-энергетических затрат (СМТЭ) расчитывают как сумму произведений расходных коэффициентов (Кi) на цену единицы затраченных средств (Цi):
СМТЭ = Кi∙Цi.
Расходный коэффициент по сырью (например, прямоточная фракция нефти с пределами выкипания 150-240оС) определяется полнотой проведения реакции, эффективностью разделения реакционной смеси продуктов и степенью очистки конечного химического продукта. Расходные коэффициенты по вспомогательным материалам (электроды) устанавливают экспериментально по мере их эрозии за определённый промежуток работы реактора электрокрекинга.
Контрольные измерения расходов электроэнергии (силовой, технологической), а также водяного пара, технологической жидкой воды и инертных газов позволяет установить их расходы на производство одной тонны ацетилена.
Примерные единичные затраты на амортизацию оборудования, частичная компенсация единовременных капитальных затрат, зарплата с социальными отчислениями взяты ориентировочно по аналогии с существующими производствами (число и стоимость аппаратуры, затраты на строительство зданий цеха и монтаж оборудования, штаты работников и фонд зарплаты). Количество реализуемых отходов (газ обратный после выделения ацетилена (Н2 – 87 об%, СН4 – 5%, С2Н4 - 5%, С2Н6 – 3%, сухая сажа)) определяют из материального баланса процесса.
Основные расходные коэффициенты и цены за единицу расхода материалов (цены приняты в условных единицах).
А. По сырью. Из данных по материальному балансу электрокрекинга на производство 1 т ацетилена расходуется 2,53 тонны керосина. Цену 1 т керосина принимаем равной 200 у.е.
Б. По вспомогательным материалам. Принимаем расходный коэффициент электродов – 10,1 кг/т, ценой 12 у.е. за 1 кг угольных электродов. Расход бензола для промывки сажи – 2кг/1т, ценой 2 у.е. за 1кг.
В. По энергии. Электроэнергия технологическая (на электропиролиз) расходуется в количестве 10000 квт.ч/т ценой 0,07 у.е./квт.ч. 250 квт.ч/т по цене 0,16 у.е./квт.ч. Расходный коэффициент (Ri) по водяному пару (на обогревание) принимаем равным 0,3 т (по цене 2 у.е. за тонну), по охлаждающей воде – 30 м3 (по 0,01 у.е./м3).
Г. По зарплате. Принимаем, что в цехе работают 30 человек с средней заработной платой 300 у.е./месяц (т.е. 108 тысяч у.е. в год). Следует рассчитать расход на зарплату, приходящийся на 1 т ацетилена, при его годовом производстве равном 25000 тонн. Отчисления на страхование примем в количестве 10% от зарплаты.
Д. По амортизации. Для оборудования и аппаратов амортизационные отчисления составляют 10% от его стоимости (примем их стоимость равной 500 тыс. у.е.). Для зданий – 2,5% от их стоимости (200 тыс. у.е.). Сумму полученных амортизационных отчислений следует отнести к одной тонне получаемого ацетилена (т.е. разделить на годовую производительность – 25000 тонн).
Е. По реализуемым отходам. Отходами являются сажа и газ, полученный после выделения ацетилена или после его селективного химического использования. Этот газ называют обратным (он содержит главным образом водород). По данным материального баланса на 1 т С2Н2 приходится 2550 м3 обратного газа (ценой 86 у.е. за 1 тыс. м3) и 300 кг сухой сажи (ценой 300 у.е. за 1 тонну). Стоимость полученных реализуемых отходов следует вычесть из общей себестоимости 1 т ацетилена.
Ж. По накладным цеховым расходам. Расходы по технике безопасности (10% от зарплаты), по содержанию и текущему ремонту оборудования и зданий (2% от их стоимости), на внутрицеховой транспорт и хранение реагентов (10% от стоимости сырья и вспомогательных материалов) расчитываем, суммируем и относим к одной тонне производимого ацетилена (делим на 25000 т).
З. По общезаводским затратам. Эти расходы составляют от 2 до 5% от цеховой себестоимости. Они отражают издержки по оплате работы заводской администрации, коммерческо-экономического отдела, центральной лаборатории, общезаводского и внезаводского транспорта и складов. Принимаем к расчёту 3%.
Сумма всех перечисленных затрат за вычетом реализуемых отходов производства составляет общезаводскую себестоимость (С).
На основе себестоимости определяется отпускная цена одной тонны ацетилена (Ц), планируемая годовая прибыль (чистый годовой доход (Д)) от продажи продукта и оценивается планируемая рентабельность (Р):
Р = Д/С = [(Ц-С)∙М]/С,
где М = 25 000 т ацетилена в год;
Ц – принимаем на 20% выше величины себестоимости.
Результаты расчёта вводят в таблицу планируемой калькуляции себестоимости ацетилена.
Таблица № 4
Перспективная калькуляция себестоимости 1 т С2Н2,
получаемого электрокрекингом жидкого нефтяного сырья
№ п/п | Статьи расходов | Ед. измер. | Кол-во (Кi) | Цена (у.е.) | Сумма (у.е.) | % от с/б | |
1. | Сырье и вспомогательные материалы | | | | | | |
| 1.1. | нефтепродукты Нк=150о Нк=240о | т | | | | |
| 1.2. | электроды | кг | | | | |
| 1.3. | бензол (для промывки сажи) | кг | | | | |
Итого стоимость сырья и вспомогательных материалов: | у.е. | | | | | ||
2. | Энергозатраты | | | | | | |
| 2.1. | силовые (на перемещение мат. потоков) | кВтч | | | | |
| 2.2. | технологические (на реакцию) | кВтч | | | | |
| 2.3. | пар | Т | | | | |
| 2.4. | вода | м3 | | | | |
| 2.5. | азот | м3 | | | | |
Итого энергетических расходов: | у.е. | | | | | ||
3. | Другие основные расходы | | | | | | |
| 3.1. | Заработная плата | у.е. | | | | |
| 3.2. | Начисления на страхование (10 % от зарплаты) | у.е. | | | | |
| 3.3. | Амортизационные отчисления | у.е. | | | | |
| 3.4. | Накладные цеховые расходы | у.е. | | | | |
| Продолжение таблицы № 4 | ||||||
| 3.5. | Транспорт | у.е. | | | | |
Итого основных расходов: | у.е. | | | | | ||
4. | Накладные цеховые расходы (обучение персонала, транспортные затраты, уборка) | у.е. | | | | | |
Итого цеховая себестоимость | у.е. | | | | | ||
5. | Отходы реализуемые | | | | | | |
| 5.1. | газ обратный | тыс. м3 | | | | |
| 5.2. | сажа сухая | т | | | | |
Итого стоимость реализуемых отходов: | у.е. | | | | | ||
6. | Накладные заводские расходы | у.е. | | | | | |
Итого цеховая себестоимость за вычетом отходов: | у.е. | | | | | ||
7. | Общезаводские расходы | у.е. | | | | | |
Итого общезаводская себестоимость: | у.е. | | | | |
К лекции 6
Теплообмен является одним из основных элементов химической технологии.
Передача тепла от холодного теплоносителя к горячему происходит в результате: а) теплопроводности (передачи тепловой энергии в результате соударений частиц при их колебательном движении); б) конвекции (перемещения частиц и масс за счет разности плотностей или при вынужденном их движении); в) лучеиспускания (передачи энергии электромагнитными волнами).
Технически передачу тепла осуществляют тремя способами:
- непосредственным контактом (смешением) горячего и холодного теплоносителя;
- через разделяющую оба теплоносителя поверхность (стенку);
- через промежуточный твердый контакт, который попеременно нагревают (подачей горячего теплоносителя), а затем охлаждают (подачей холодного теплоносителя).
Для нагревания и испарения в технике используют парообразные, жидкие и газообразные горячие теплоносители, а также электрический ток и сверхвысокочастотное облучение. Самым распространенным парообразным горячим теплоносителем является водяной пар (до 170С). Иногда в процессах дегидрирования и пиролиза применяют нагретый до 450-800С водяной пар. В маломасштабных производствах часто применяют пары высококипящих веществ, например дифенильную смесь, состоящую из 73,5% дифенилоксида и 26,5% дифенила. Эта смесь переходит в пар при 258С, поэтому она применима для нагревания от 260С до 360С (выше 400С она разлагается).
В качестве горячих жидких теплоносителей используют воду (до 150С), глицерин, кремнийорганические масла, минеральные масла (до 300С), дифенильную смесь (при 1 атм до 250С, а при 10 атм – до 400С), расплавленные неорганические соли (NaNO2, NaNO3 , KNO3 – от 190С до 500С и металлы и их сплавы (до 1000С).
Горячие газообразные теплоносители – это топочные газы (от 400 до 1000С) и инертные газы плазменных процессов. Основной недостаток использования газов заключается в их малой удельной теплоемкости и низких величинах коэффициентов теплоотдачи.
Для охлаждения и конденсации в технике применяют воздух, жидкую воду, жидкий аммиак, рассолы (растворы хлоридов кальция и натрия), галогензамещенные углеводороды (галоны, фреоны).
Теплообменные аппараты классифицируют по следующим типам: трубчатые, пластинчатые, спиральные, рубашечные и оребренные. Самые распространенные из них – трубчатые, которые подразделяют на кожухотрубчатые, оросительные, погружные и теплообменники типа “труба в трубе”.
Кожухотрубные аппараты (см. рис.1) имеют пучок труб, плотно развальцованных в трубные решетки. Этот пучок труб находится в цилиндрическом корпусе (кожухе), закрытом с обеих сторон крышками, которые образуют распределительное и коллекторное пространство. В крышках и корпусе имеются патрубки для подвода и отвода теплоносителей. Один теплоноситель проходит через трубы, а другой – через межтрубные пространства, осуществляя передача тепла через стенки труб.
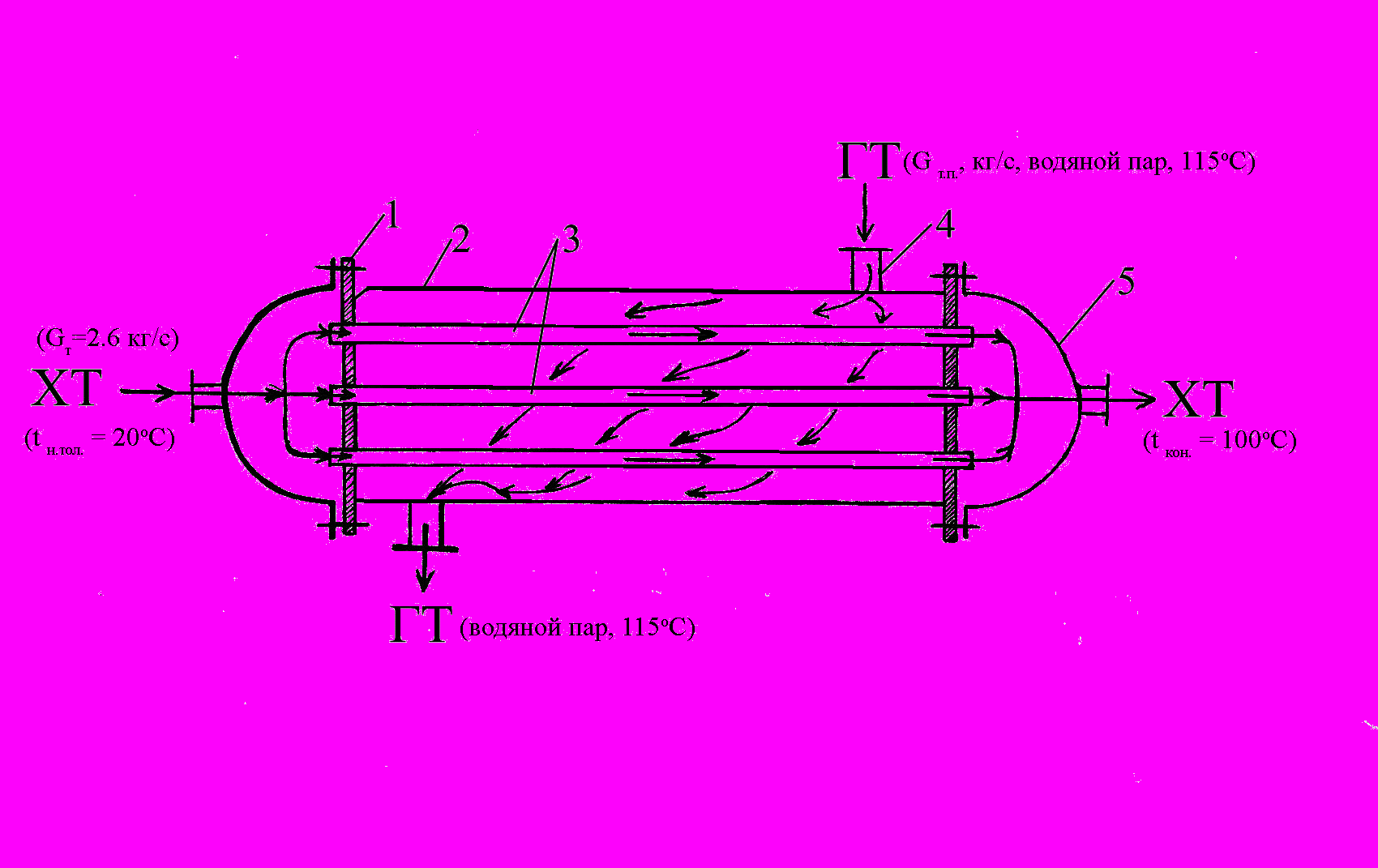
Рис.1. Кожухотрубчатый горизонтальный теплообменник.
1 – трубная решетка; 2 – кожух; 3 – пучок труб; 4 – патрубок;
5 – крышка; ХТ и ГТ – холодный и горячий теплоносители.
Кожухотрубные аппараты компактны, экономичны и трубы легко очищать. Однако чистка межтрубного пространства затруднена, а линейные скорости прохождения теплоносителей ограничены.
Обычно порядок расчета теплообменника включает:
- Составление теплового баланса т.е. определяемого количества передаваемого тепла (Q) при теплообмене между заданным и выбранным теплоносителями, а также количество выбранного теплоносителя (G);
- Опредение средней разности температур между теплоносителями (tср);
- Расчет или выбор скорости движения (W), коэффициентов теплоотдачи (), теплопроводности () и теплопередачи (К);
- Определение теплообменной поверхности теплообменника (F);
- Расчет и выбор конструктивных размеров аппарата (диаметра, толщины, длины и числа труб);
- Выбор стандартного (заводского) теплообменника по каталогам;
- Вторичный расчет (Q, G, tср, W, , K) с целью уточнений принятых и расчетных параметров по характеристикам выбранного стандартного аппарата.
В работе [5] приведены примеры расчета кожухотрубчатых теплообменников (холодильника, нагревателя, испарителя и конденсатора) с применением компьютерных программ, составленных на языке Fortran.