К лекции 2 Структура себестоимости
Вид материала | Лекции |
- Методы учёта затрат и учёта себестоимости Понятие себестоимости. Виды себестоимости, 232.07kb.
- Нормативный метод калькулирования себестоимости как российский вариант «стандарт, 32.79kb.
- Такие разные лекции, 101.86kb.
- И. Г. Лекции по теории интегральных уравнений(7382) Петровский И. Г. Лекции, 55.62kb.
- Тема 7 Анализ себестоимости сельскохозяйственной, 555.39kb.
- «Статистические методы изучения уровня и динамики себестоимости продукции», 457.54kb.
- Планирование себестоимости продукции на предприятии. Ценовая политика на различных, 26.91kb.
- Задачи статистического изучения себестоимости. Основные показатели в анализе себестоимости, 92.6kb.
- Технический Университет «военмех», 1200.54kb.
- Управление персоналом вопросы для подготовки к экзамену, 23.69kb.
1 2
1.2. Расчётная часть
Задание. Определить поверхность теплопередачи кожухотрубчатого подогревателя (рис.1) для нагрева потока (2,6 кг/c) толуола от 20С до 100С с помощью конденсирующегося пара, имеющего температуру 115С.
При расчетах теплообменных аппаратов для установившегося процесса теплопередачи используют общее уравнение следующего вида:
Q = K Ftср ,
где Q – количество передаваемого тепла от горячего теплоносителя к холодному в единицу времени, вт или дж/c;
К – коэффициент теплопередачи вт/( с м2град) или дж/(с м2град). Его физический смысл – это количество тепла передаваемого через единицу поверхности теплообменника в единицу времени при температурном напоре (разности температур), равном одному градусу;
F – поверхность теплообменника, м2;
tср – средняя разность температур между паром и толуолом (усредненный температурный напор вдоль теплопередающей поверхности – длине теплообменника, или движущая сила процесса теплопередачи), град.
Последовательный расчет (Q), tср и затем (K) позволяет полчеить конечный результат, т. е. определить поверхность теплообменника (F).
1.2.1. Определение количества передаваемого тепла (Q) и tср
Количество тепла (Q), получаемого толуолом при его нагревании от начальной температуры tн.тол. до конечной tк.тол. можно рассчитать по уравнению:
Q = Gт. ст. (tн.тол. -tн.тол.),
где Gт. – массовый расход толуола; кг/c
ст. – средняя удельная теплоемкость толуола при средней температуре толуола tср.тол., дж./(кг град); для заданных условий tср.тол.= tпара-tср. 72С;
ст. = 1800 дж/кгград (по номограмме х1 в [7], стр.562).
Среднюю (среднелогарифмическую) разность температур определяют по формуле:
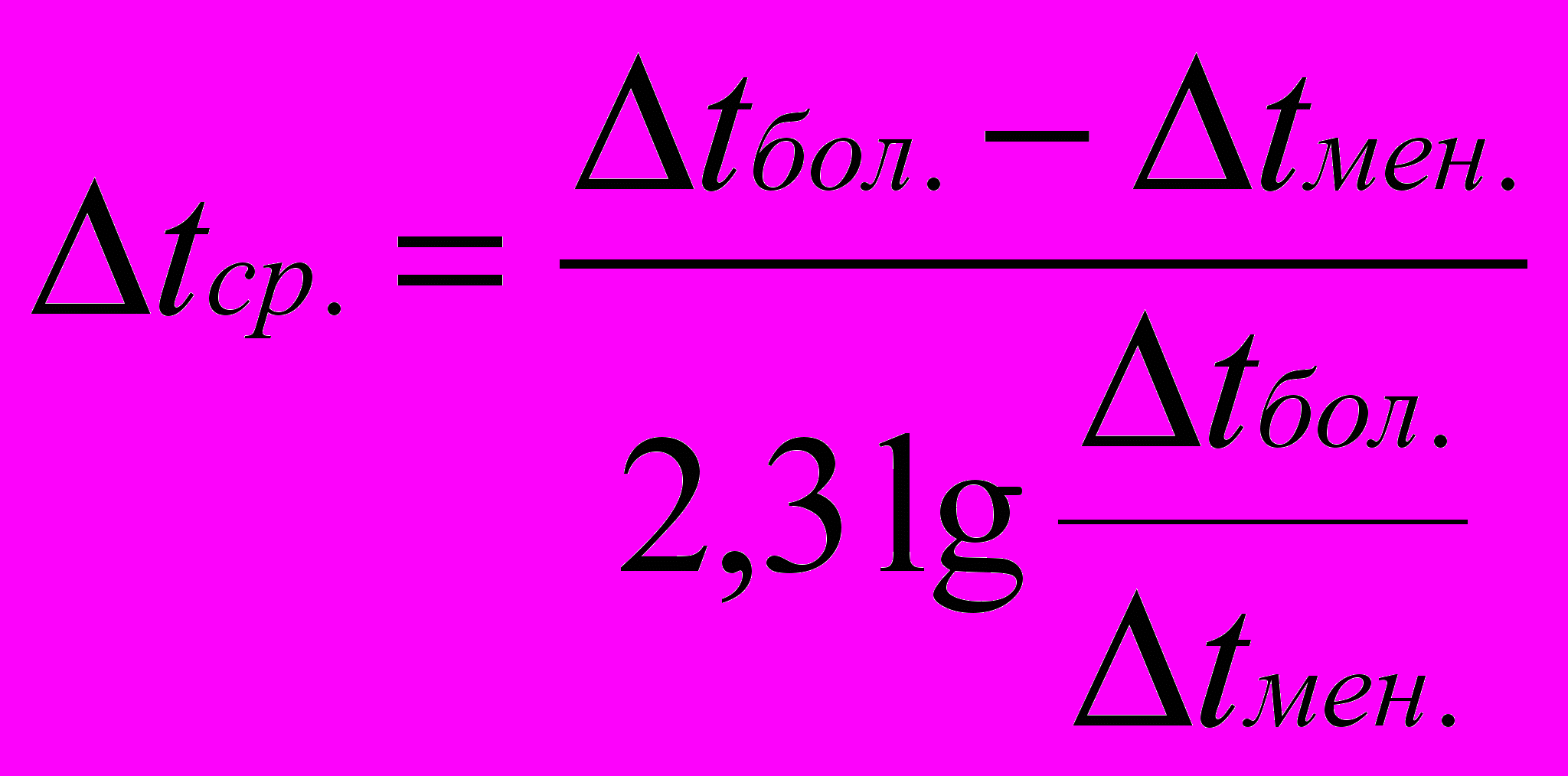
где tбол. и tмен. – большая и, соответственно, меньшая разность температур на концах теплообменника, определяемая для случая противотока теплоносителей по графику:
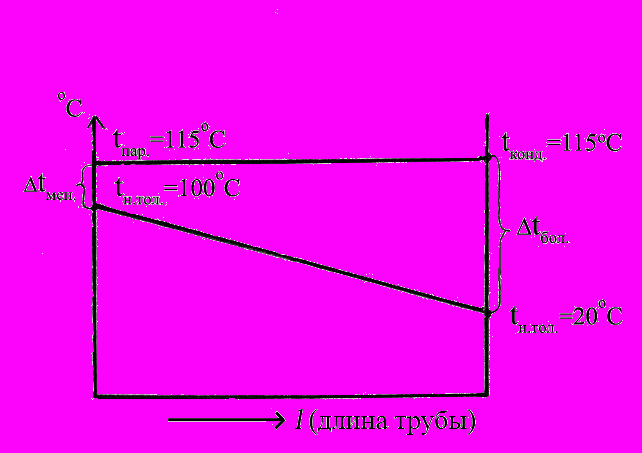
Рис. 2. График изменения температуры вдоль длины трубы
Расчет tср можно упростить при условии
0,5 tбол./ tмен. 2
В этом случае применима среднеарифметическая разность температур:
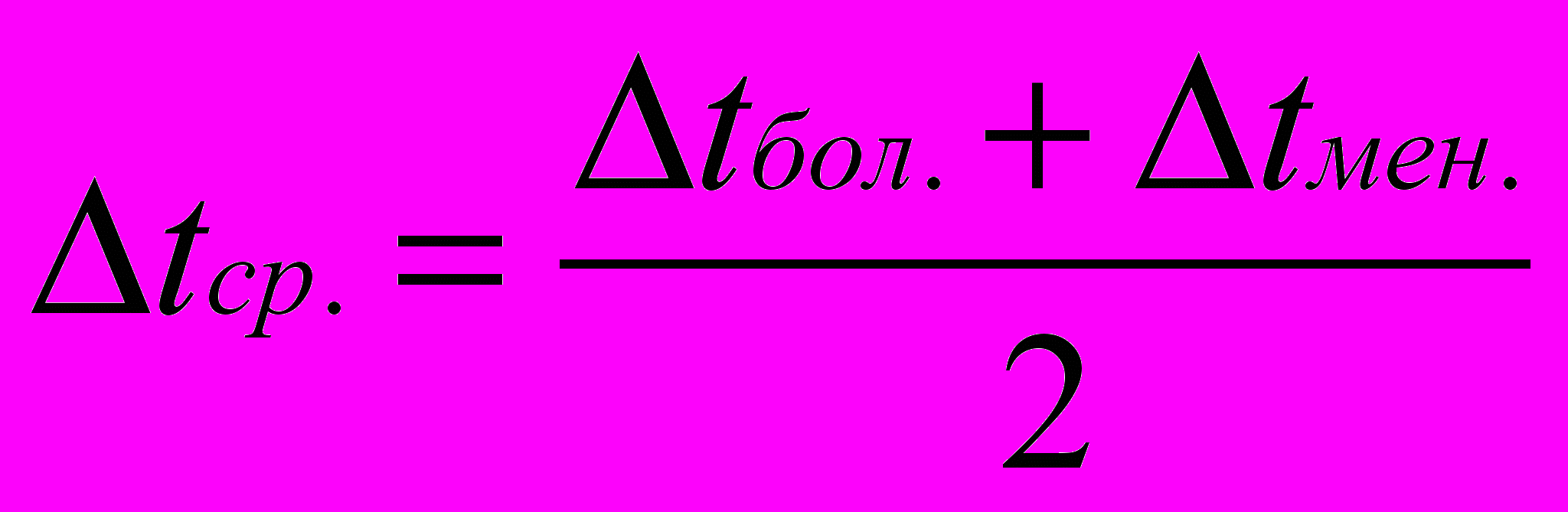
После расчета tср определяем количество передаваемого тепла:
Q = 2,61800 tср
и анализируем размерность:
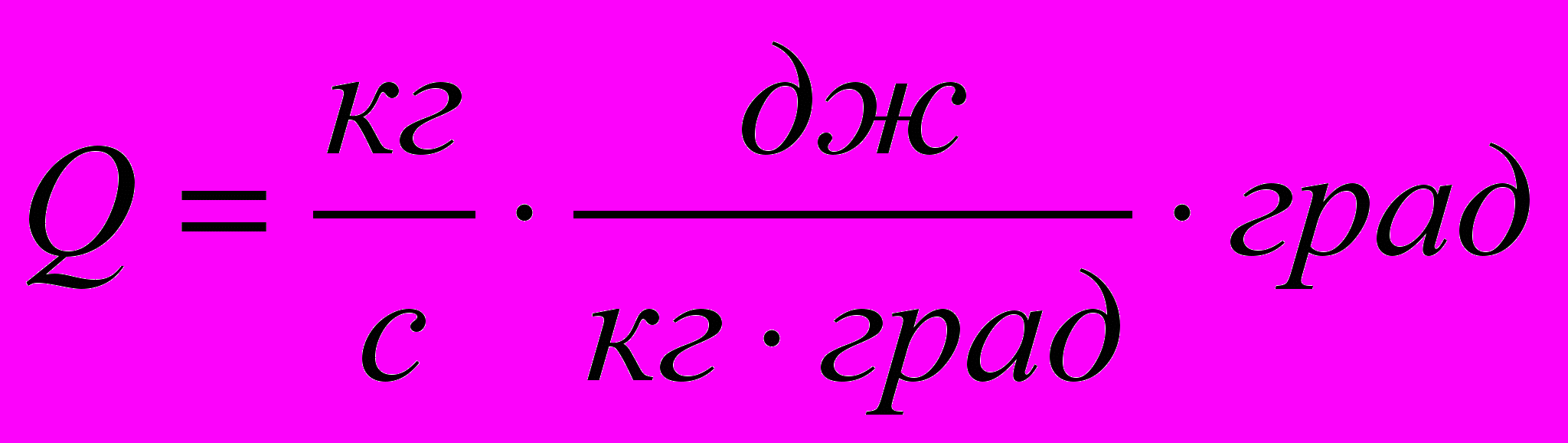
После сокращений получаем Q [дж/c] или [вт].
1.2.2. Определение расхода теплоносителя
Полученная величина расхода тепла на нагревание известного массового потока толуола позволяет теперь определить требуемое для этой цели количество водяного пара Gг.п. по формуле:
Gг.п. = Q/rв,
где rв – удельная теплота конденсации водяного пара, равная при 115С 2222000 дж/кг (см.[7], стр.549, табл.57).
1.2.3. Определение коэффициента теплопередачи (К)
Коэффициент теплопередачи расчитывают по уравнению:
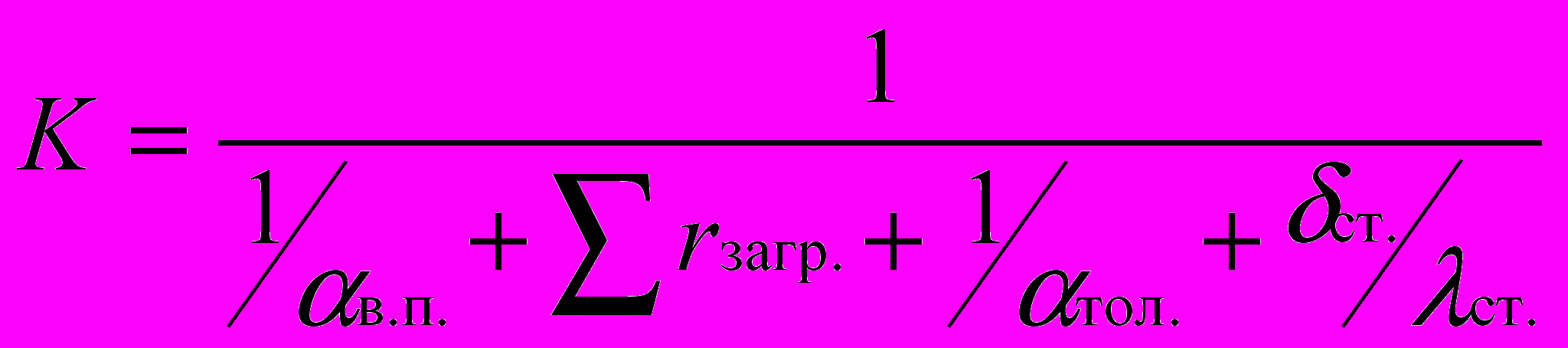
где в.п. и тол. – частные коэффициенты теплоотдачи со стороны водяного пара и толуола, соответственно; ст. – толщина стенки трубы; ст. – коэффициент теплопроводности материала, из которого изготовлена труба.
1.2.3.1. Определение термического сопротивления стенки трубы
Для данного теплообменника выбираем стальные трубы размером 25 2 мм, где 25 – это внешний диаметр трубы в мм, а 2 – толщина ее стенки () в мм. Для стали выписываем коэффициент ст.= 46,5 вт/мград (см.[7],табл. 28 на с. 523).
Тогда
ст./ст.= 0,002 м / 46,5 вт/мград = 4,30 × 10-5 [(м2град)/вт].
В случае загрязненных теплоносителей на стенках труб образуется слой отложений, увеличивающий их термическое сопротивление при теплопередаче (rзагр)
rзагр. =1/rв.п. + 1/rтол. =1/5800 + 1/5800 = 3,45 × 10-4 [вт/(м2град)],
где rв.п. и rтол. – сопротивление загрязнений со стороны конденсирующего пара и толуола (см.[7],табл. 31 на с. 531).
Перед тем, как определить коэффициенты (), проводят предварительное определение числа труб (n) в теплообменнике. Для этого запишем уравнение для секундного объёма (Vтол. , м3/с) потока толуола внутри труб.
Vтол. = Gт./т. = (d2Wn)/4 = 0,785 d2Wn ,
где т. – плотность толуола для tср.тол.; d – внутренний диаметр труб, м ; W- линейная скорость потока толуола , м/с ;
Анализ размерности: Gт. ./т = [кг/c / кг/м3] = [м3/c] ; d2Wn = [м2 м/с] = [м3/c].
Откуда n = Gт./ ( 0,785 d2W).
Заменяя W на ее выражение (Rе)/(d), получаемое из формулы
Rе = (Wd)/,
имеем
n = Gт./ ( 0,785 d Rет) ,
где т – динамический коэффициент вязкости толуола, равный 0,3710-3 Па/с [или кг/(мс)] (см.[7], с. 556, рис V).
Задаваясь численным безразмерным значением критерия Рейнольдса (т.е., выбирая ламинарный, переходный или турбулентный режим движения толуола), рассчитываем (n), например, для развитого турбулентного режима Re= 15000:
n = 2,6./ ( 0,7850,02115000,00037);
Анализ размерности: [кг/c /м кг/мc] = [ штук ].
В случае подбора стандартного теплообменника по определенному выше числу труб, можно уточнить значение величины критерия Рейнольдса.
1.2.3.2. Определение коэффициента теплоотдачи со стороны жидкого теплоносителя (тол)
Коэффициент теплоотдачи для толуола расчитываем из формулы:

где коэффициент теплопроводности тол. = 0,125 вт/мград (см. рис.10, стр.561).
Откуда
тол= ( Nuтол)/d = ( Nu0,125)/0,021.
Поскольку толуол проходит внутри труб, не меняя агрегатного состояния, для расчета критерия Нуссельта (Nu) пользуются критериальными уравнениями:
Nu = 0,021 Re0,8Pr0,43(Pr/Prcт.)0,25l (при Re104) или
Nu = 0,008 Re0,9Pr0,43 (при 104 Re 2300)
В случае Rе 2300 принимаем Nu = 4 ([7], с. 188).
Принимаем l = 1,0 ([7], с. 157) и (Pr/Pr cт.)0.25 = 1,0 (для нагревающихся жидкостей).
Критерий Прандтля (Рr =4,5) находим по [7] (рис. XIII, стр.564).
1.2.3.3. Определение коэффициента теплоотдачи со стороны конденсирующего пара (в.п.)
Расчет проводят для пучка горизонтальных труб, пользуясь формулой ([7], глава 4):
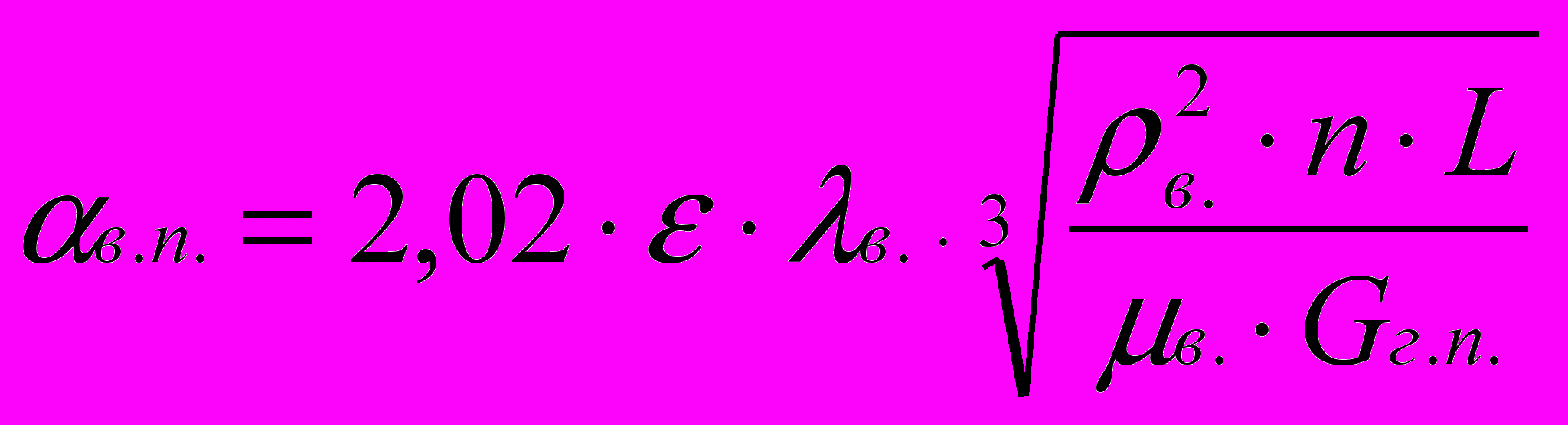
= 0,6 – коэффициент, зависящий от расположения и числа труб в вертикальном ряду;
в = 0,685 вт/мград – коэффициент теплопроводности конденсата (рис.10, стр.561);
в. = 947 кг/м3 – плотность конденсата ([7], табл.39, стр.537);
L – длина трубы (задаемся длиной 1,0; 1,5; 2,0; 3,0; 4,0; 6,0 м);
в = 0,24410-3 кг/мс или Пас – динамический коэффициент вязкости конденсата ([7], табл.39,стр.537).
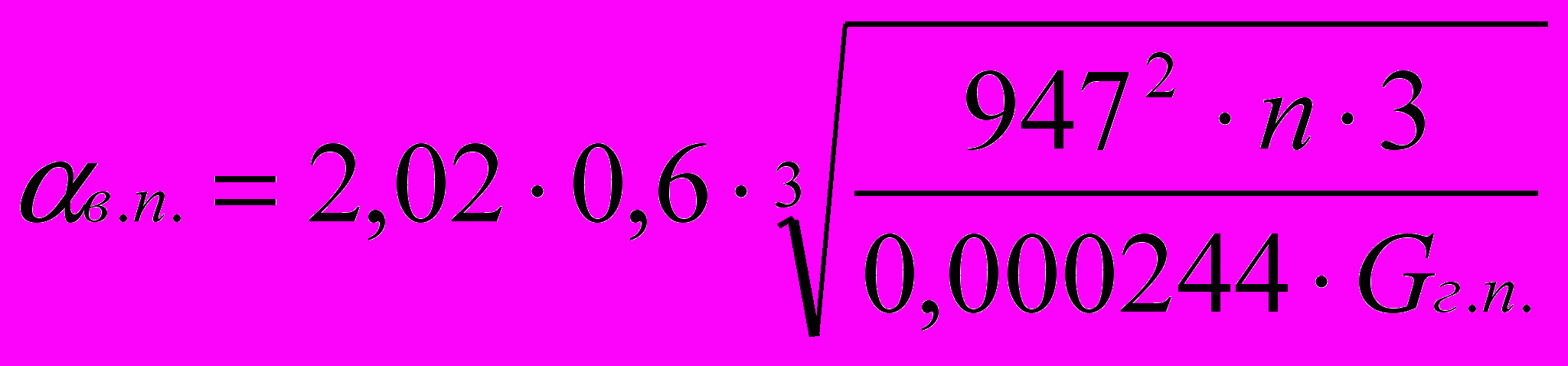
1.2.4. Нахождение требуемой площади поверхности подогревателя (F)
В заключении расчета теплообменника в первом приближении определяем площадь поверхности аппарата по формуле
F = Q/Ktср.
По найденной поверхности (F) можно подобрать стандартный теплообменник по каталогам и провести расчет во втором приближении по уточненным значениям числа труб, их длины и диаметру.
В работе [5] приведены методические указания по составлению компьютерной программы для расчета теплообменников на ЭВМ.
К лекции 8
Разделение жидкой гомогенной смеси веществ методом перегонки (дистилляции) основано на различии температур их кипения (летучести). В случае простой перегонки бинарной смеси происходит однократное испарение низкокипящего компонента (НК) с его последующей однократной конденсацией при охлаждении паров в вынесенном теплообменнике-конденсаторе. Высококипящий компонент (ВК), как правило, почти полностью остаётся в перегонном кубе при условии, что разница между температурами кипения НК и ВК велика. Однако при не очень больших различиях в их температурах кипения прибегают к более сложному случаю перегонки – ректификации, при которой наблюдается многократное частичное испарение и частичная конденсация разделяемых компонентов (НК и ВК). В этих случаях над перегонным кубом расположена колонна с насадкой или с тарелками ситчатого или колпачкового типа. Горячие пары смеси ВК и НК, образующиеся в кубе, поднимаются вверх по колонне и контактируют с относительно холодной жидкой смесью НК и ВК, опускающейся вниз. При этом между паровой и жидкой фазами, движущимися противотоком, происходят теплообменные процессы – пары охлаждаются, а жидкость нагревается, что в свою очередь вызывает массообменные процессы. По закону Коновалова при охлаждении паров конденсируется, прежде всего, ВК, а из нагреваемой жидкой фазы испаряется главным образом НК. Таким образом, поднимающийся вверх по колонне пар постепенно обогащается НК, а опускающаяся вниз жидкость обогащается ВК. В верхней части колонны отбирают сконцентрированный НК, который в виде флегмы частично возвращают в верхнюю часть колонны. Из кубовой части колонки отбирают ВК.
На рис.3 представлена схема установки ректификации непрерывного действия для разделения бинарной смеси с обозначениями массового (G) и мольного (Gm) потока исходной смеси, мольных потоков дистиллята (D), кубовой жидкости (Wo), паров в колонне (Gp), массовых (a) и мольных (х) концентраций этих потоков (для бинарной смеси приводят лишь долю НК, т.к. хн.к.+хв.к.=1, или 100%).
На рис.3 изображена схема непрерывно действующей ректификационной установки с тарельчатой колонной ректификации:
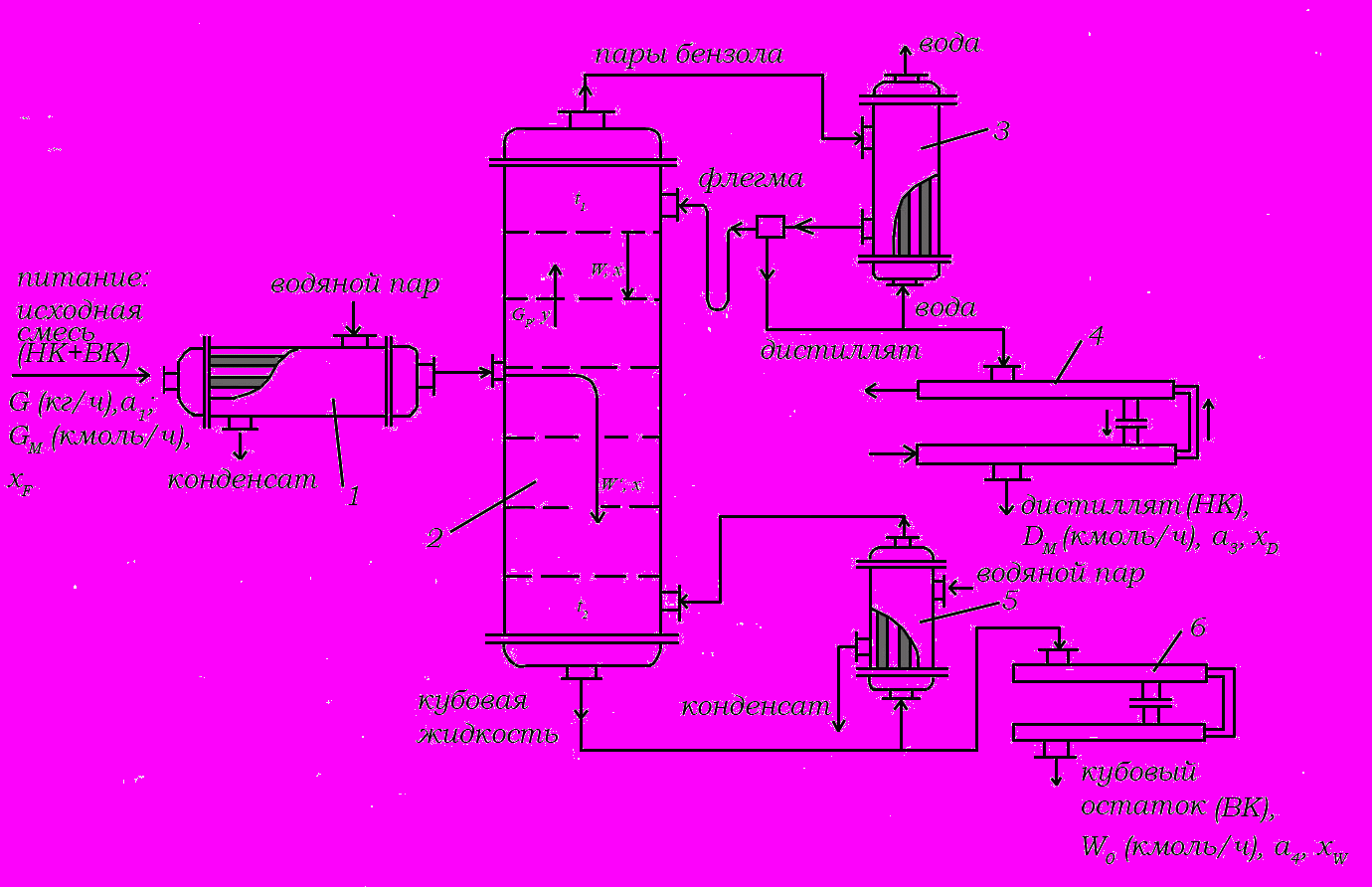
Рис.3. Схема ректификационной установки:
1 – подогреватель; 2 – колонна ректификационная; 3 – дефлегматор; 4 , 6 – холодильники «труба в трубе»; 5 – (кипятильник вынесенный).
2.2. Расчётная часть
2.2.1. Пример-задание
Определить графическим путём число тарелок ректификационной колонны непрерывного действия, её высоту и диаметр для разделения под атмосферным давлением 10000 кг/ч (G) жидкой смеси, состоящей из бензола (a1 = 40% масс.) и толуола. Содержание бензола в дистилляте (a3 = 96% масс.), содержание толуола в кубовом остатке 98% масс. (a4 = 2% масс.). Исходная смесь подаётся в колонну при температуре кипения.
2.2.2. Пересчет массовых долей в мольные
Процесс ректификации удобнее рассчитывать в мольных потоках и концентрациях, т.к. отношения мольных теплот парообразования разделяемых компонентов к их температурам кипения не очень сильно отличаются друг от друга (правило Трутона). Это допущение приводит к тому, что для испарения 1 кмоля НК расходуется теплота, выделяемая при конденсации 1 кмоля ВК. Поскольку мольные теплоёмкости обоих компонентов близки (при допущении, что они мало изменяются с температурой по высоте колонны), то мольные потоки пара и жидкости допустимо мало изменяются по высоте колонны.
В связи с этим производят пересчёт массовых концентраций (ai) в молярные (хi).
По определению молярная доля – это отношение числа кмолей данного компонента (ni) в смеси (ni = ai/Mi) к общему числу кмолей всех компонентов (n):
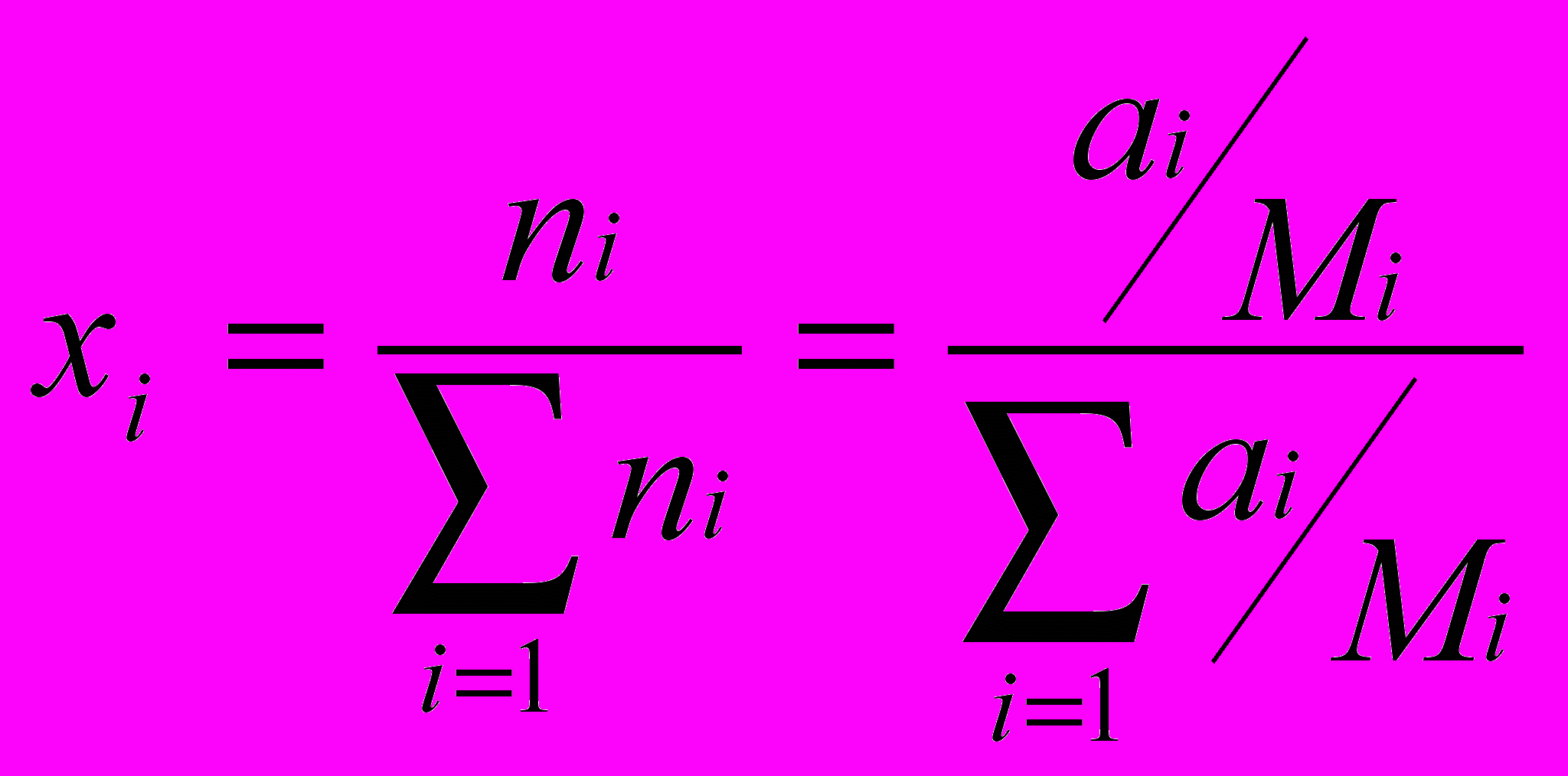
Для бинарных смесей (i=2) формула имеет вид
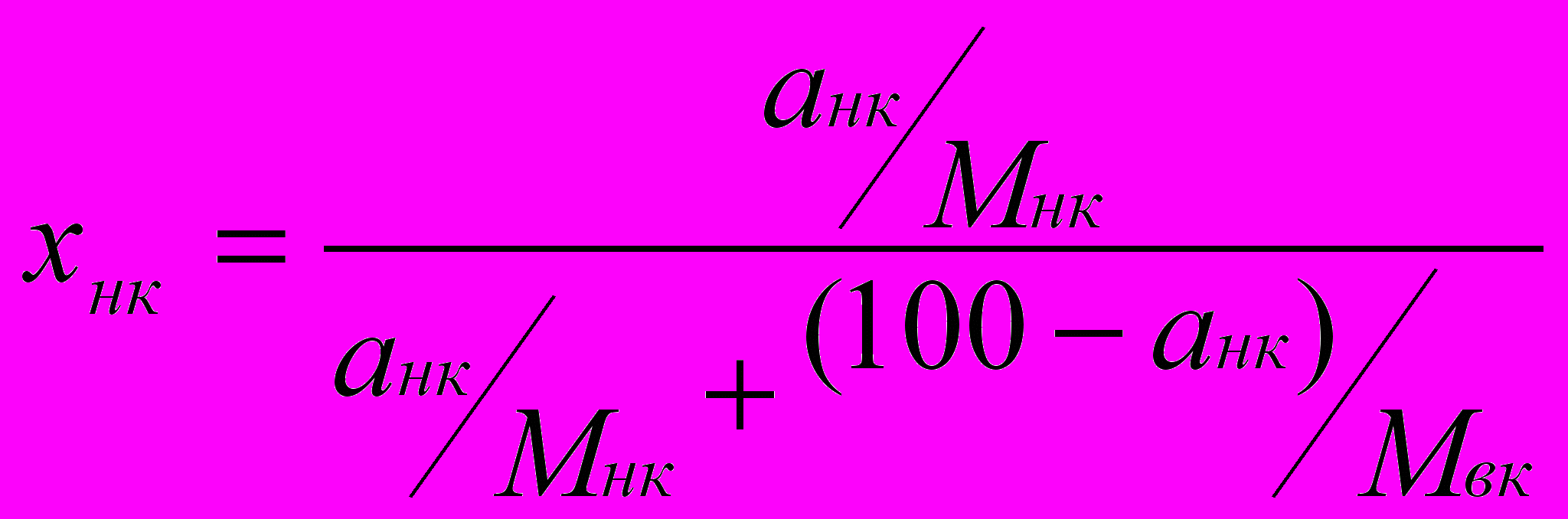
Выражение концентраций питания, дистиллята и кубового остатка в мольных долях. В выбранном примере имеем:
а) для питания:
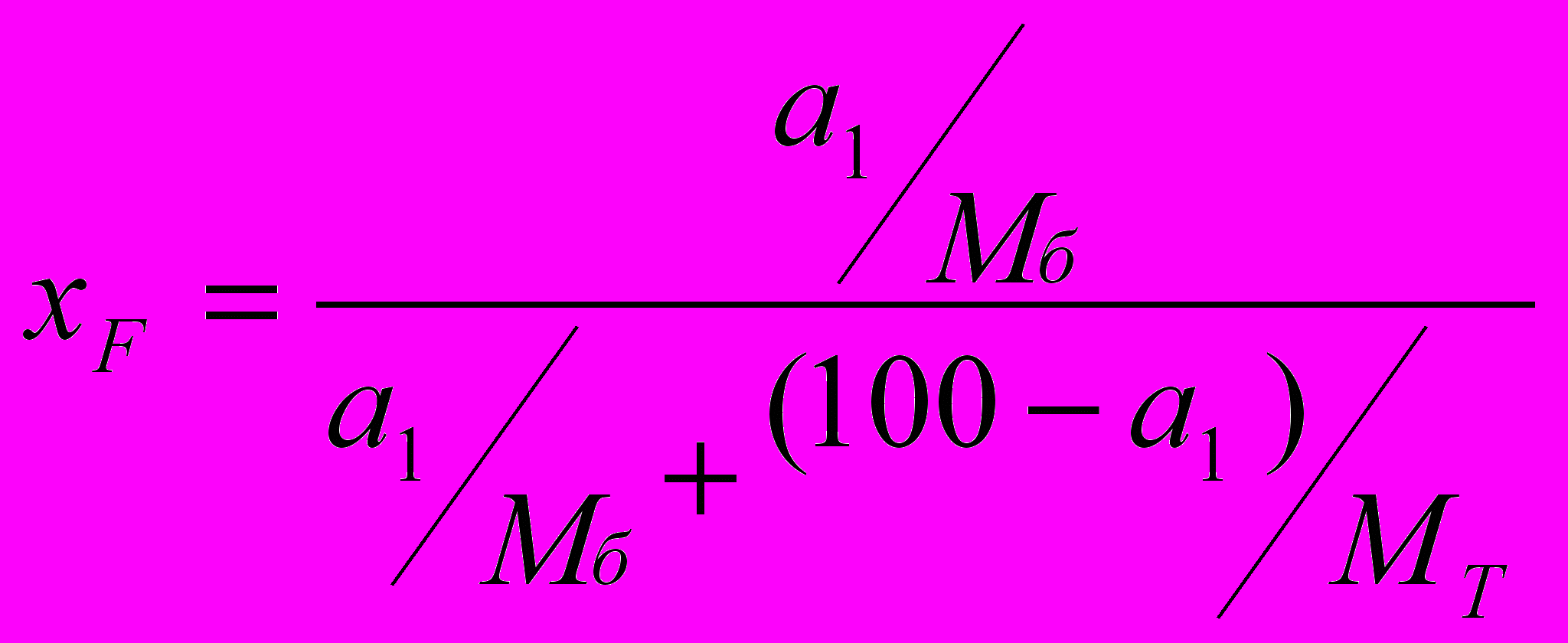
где хF – мольная доля бензола в питании;
а1 – исходная весовая концентрация бензола (%);
Мб – молекулярная масса бензола;
Мт – молекулярная масса толуола;
б) Для дистиллята:
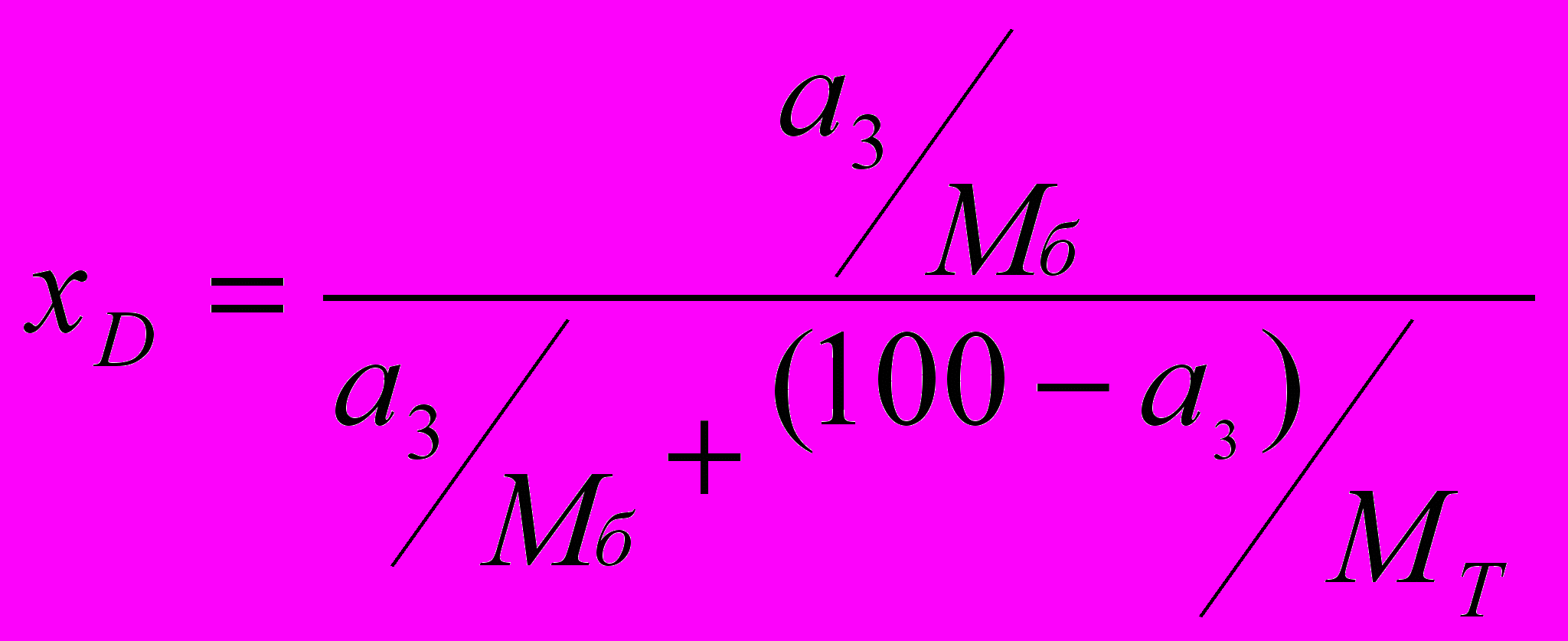
в) для кубового остатка:
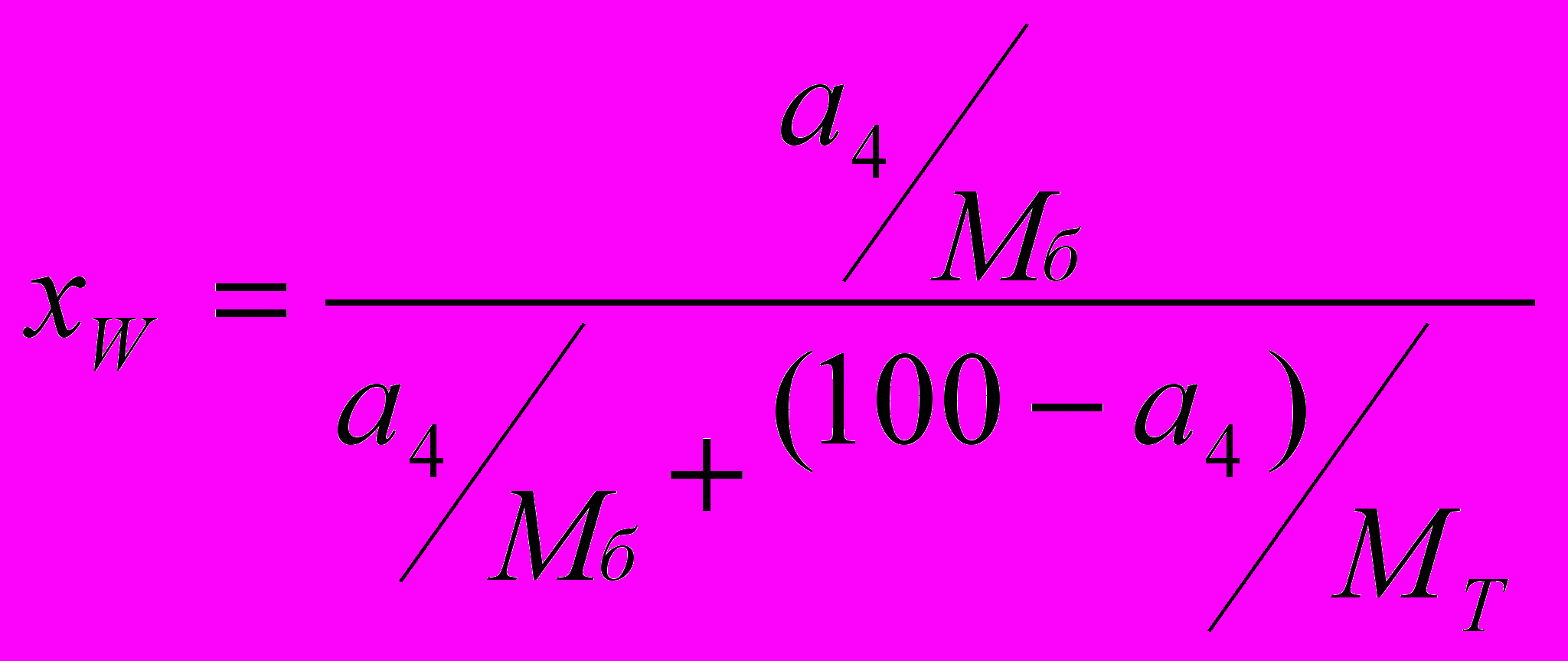
Рассчитанные значения хF, хD,, хW лежат в пределах от 0 до 1,0.
2.2.3. Определение равновесных концентраций системы бензол-толуол для жидкой (х) и паровой (y) фаз в зависимости от температуры
По закону Рауля парциальное давление (рi) паров компонента над жидкой смесью пропорционально его содержанию (х) в смеси и температуре (в приближении к идеальным смесям). Для бинарной смеси можно записать:
рнк = Рнк∙хнк и рнк = Рвк∙(1-хнк),
где Рнк и Рвк – давление паров, соответственно , НК и ВК над чистыми жидкими НК и ВК при данной температуре.
Полное давление пара смеси НК и ВК (Робщ.) над их жидкой смесью составит
Робщ = рнк + рвк = Рнк∙хнк + Рвк∙(1-хнк),
откуда Хнк=(Робщ-Рвк)/(Рнк-Рвк). Эта формула показывает зависимость изменения молярной концентрации НК (и ВК) в жидкой фазе от температуры по всей высоте колонны ректификации.
Изменение молярной концентрации унк по определению представляет собой отношение парциального давления компонента (рнк) к общему давлению пара над жидкостью (Робщ).
yнк = рнк/Робщ = Рнк ∙хнк/Робщ
В таблице 1 приведены величины давления паров (Рi) разделяемых компонентов над чистым (индивидуальным) жидким компонентом.
Таблица № 1
Давление паров над чистыми жидкостями, Рi = f(t)
Вещество | Давление пара (мм рт. ст.) при Т, 0С | |||||||
60 | 70 | 80 | 90 | 100 | 110 | 120 | 130 | |
Ацетон | 861 | 1190 | 1611 | 2142 | 2797 | 3594 | 4547 | 5670 |
Бензол (Рб) | 389 | 547 | 754 | 1016 | 1344 | 1748 | 2238 | 2825 |
Бутанол | 59 | 112 | 165 | 255 | 386 | 572 | 433 | 1150 |
Вода | 149 | 234 | 355 | 526 | 760 | 1075 | 1489 | 2026 |
Дихлорэтан | 538 | 480 | 664 | 906 | 1220 | 1600 | 2040 | 2580 |
Изопропанол | 289 | 455 | 692 | 1021 | 1480 | 2020 | 2790 | 3800 |
Метанол | 625 | 927 | 1341 | 1897 | 2621 | 3651 | 4751 | 6242 |
Толуол (Рт) | 147 | 204 | 299 | 408 | 571 | 751 | 973 | 1350 |
По результатам расчёта (х) и (у) составляется таблица 2 и строится диаграмма (t – x,y), рис. 4 и диаграмма равновесия (х – у), рис. 5.
Таблица № 2
Результаты расчёта (х и у)
T,0C | Pб | Рт | Робщ. | ![]() | ![]() |
80 | 760 | 300 | 760 | 1 | 1 |
84 | 852 | 333 | 760 | | |
88 | 957 | 379,5 | 760 | | |
92 | 1078 | 432 | 760 | | |
96 | 1204 | 492,5 | 760 | | |
100 | 1344 | 559 | 760 | | |
104 | 1495 | 625 | 760 | | |
108 | 1695 | 704,5 | 760 | | |
110 | 1748 | 760 | 760 | 0 | 0 |
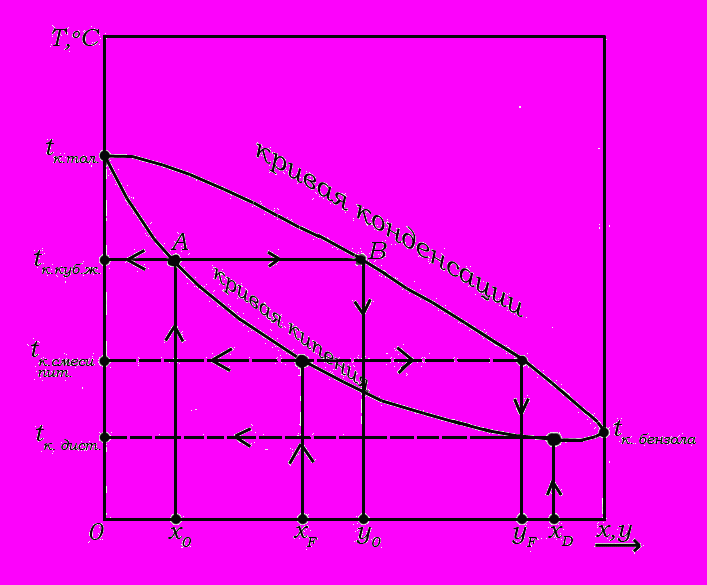
Рис.4. Диаграмма (t – x,y)
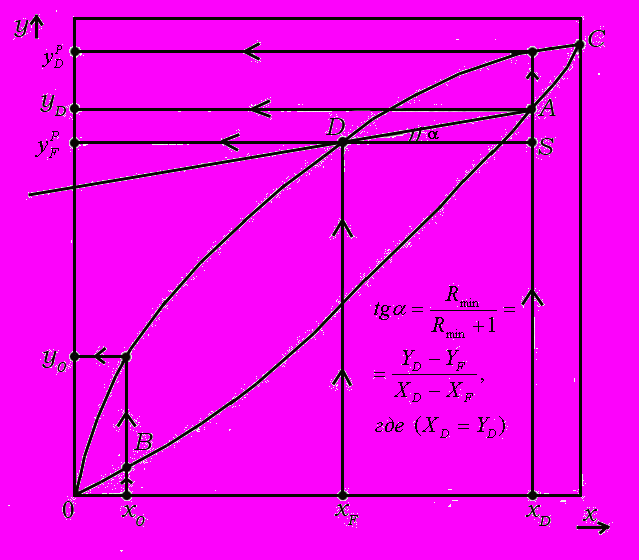
Рис.5. Диаграмма равновесия (х, у) и определение равновесных концентраций для расчёта Rmin
По диаграмме (t – x,y) можно определить температуры кипения бинарных жидких смесей любого состава, а также составы получающихся при этом паров, например: хоАВуо. По диаграмме (х, у), на которой линией равновесия является кривая ОДС (прямая линия ОВАС – вспомогательная диагональная линия), определяют равновесные концентрации (например, хF
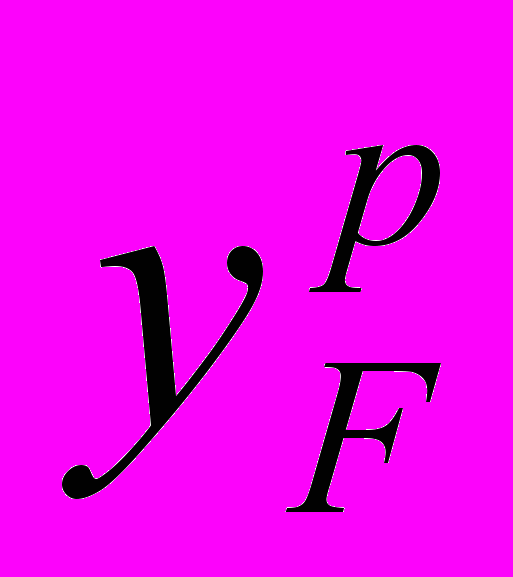
2.2.4. Определение числа теоретических ступеней графическим построением
а) Сначала проводят расчёт рабочего флегмового числа (R).
Для этого определяют минимальное флегмовое число Rmin), проводя из точки хF диаграммы равновесия (х – у) проводят перпендикуляр до пересечения с линией равновесия в точке D (рис.4). Далее из точки D проводим прямую, параллельную оси абсцисс, до пересечения с осью “у”. Точка пересечения
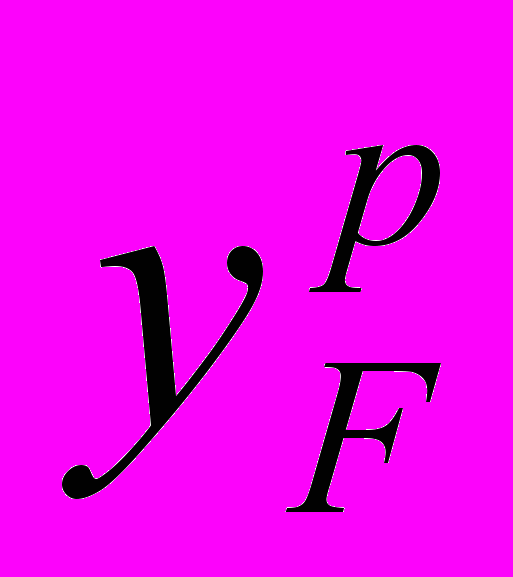
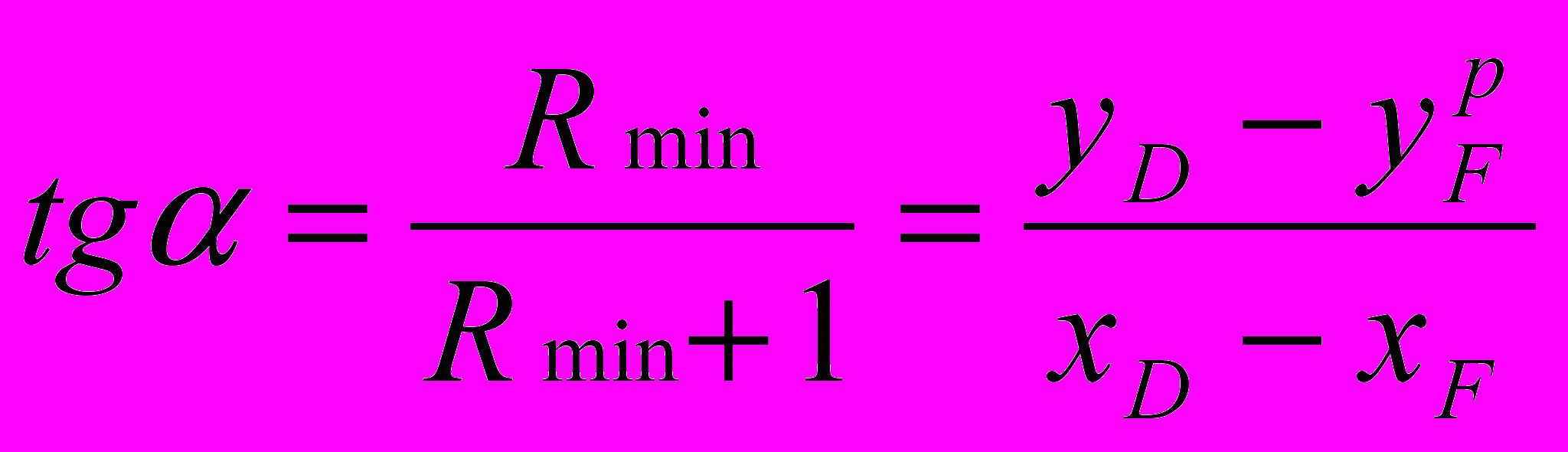
По найденным величинам рассчитываем Rmin [7]:
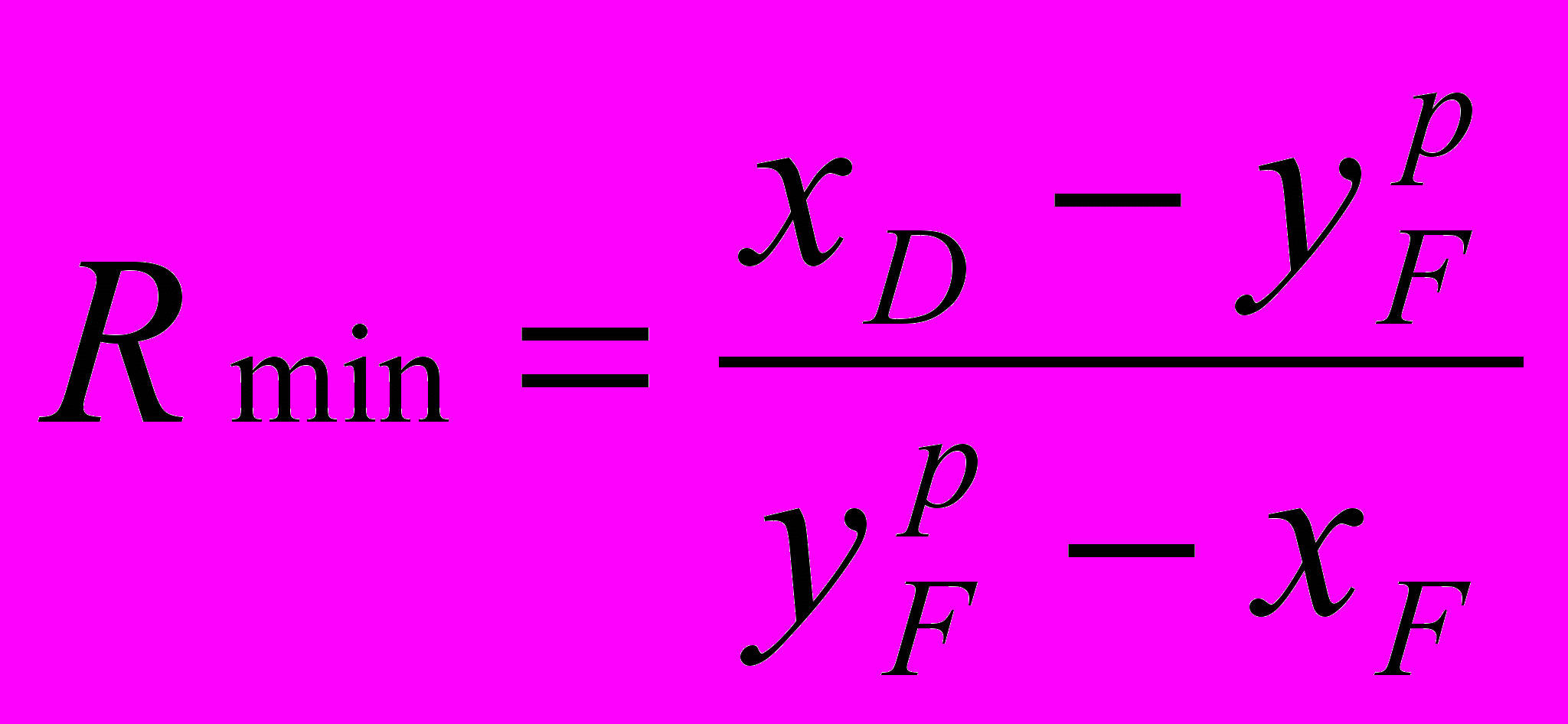
Задаваясь коэффициентом () избытка флегмы (например, =2,5) рассчитываем рабочее флегмовое число ( R ) по уравнению:
R = Rmin∙.
Флегмовое число показывает количество кмоль возвращаемого в колонну дистиллята (W) на каждый кмоль отбираемого дистиллята (DM – готовый продукт), т.е.
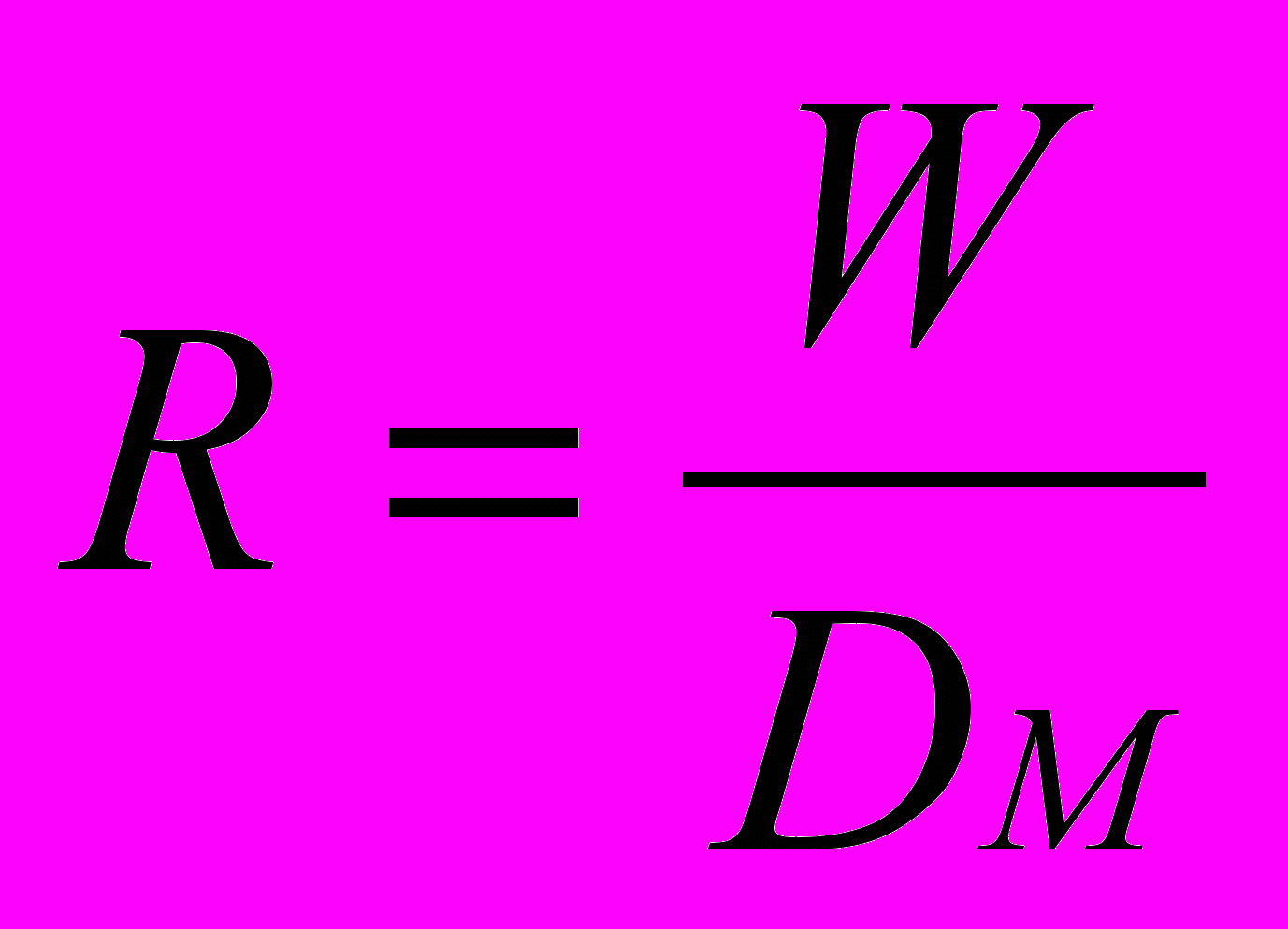
б) Затем выписываем уравнения рабочих линий.
Для верхней части колонны:
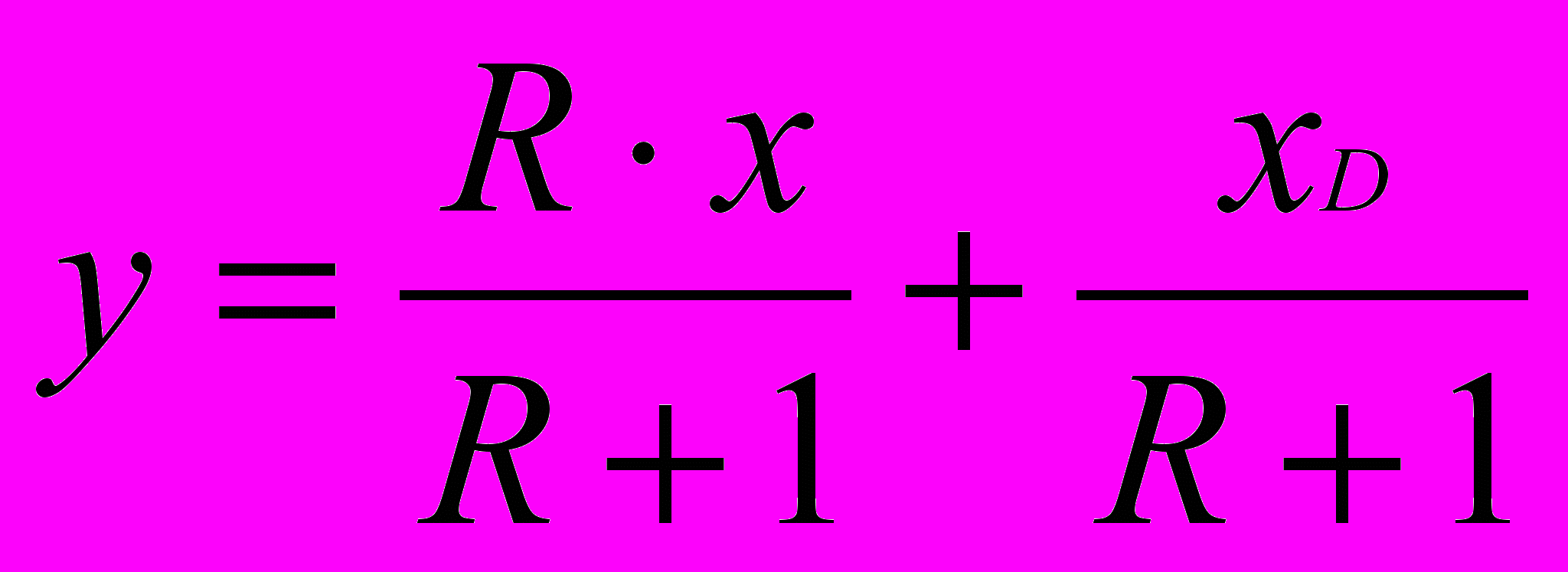
Для нижней части колонны:
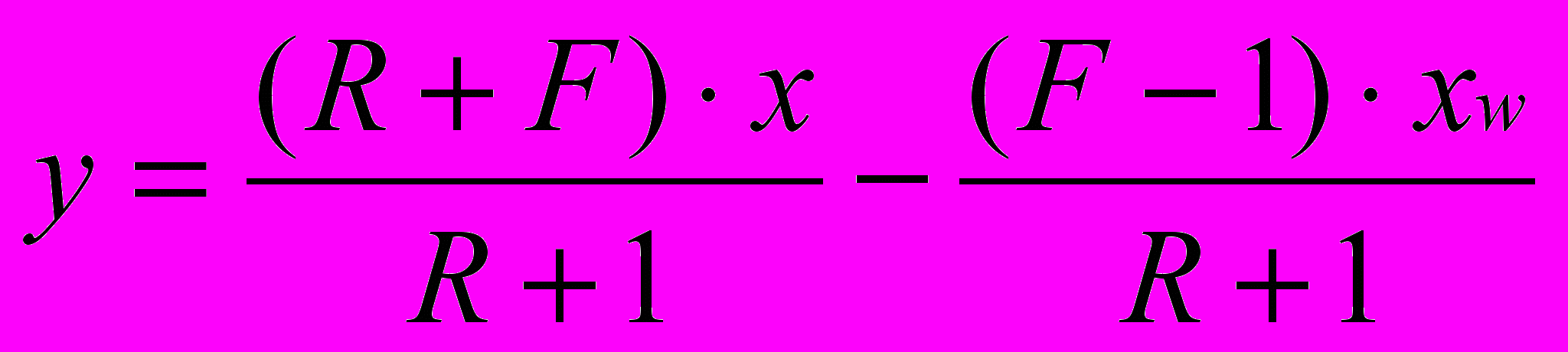
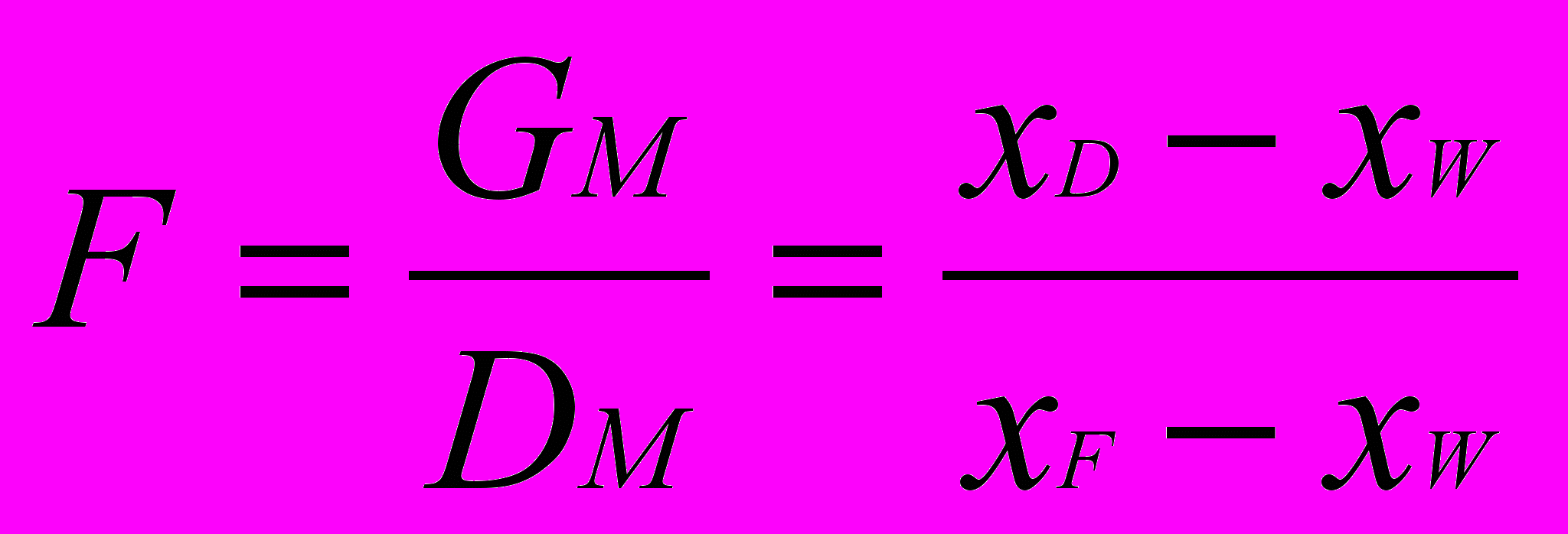
F – количество исходной смеси (питания) в кмолях, приходящейся на кмоль отбираемого дистиллята;
GM – мольный расход питания в кмолях в час;
GM = G/MF,
где MF – средняя молекулярная масса исходного потока,
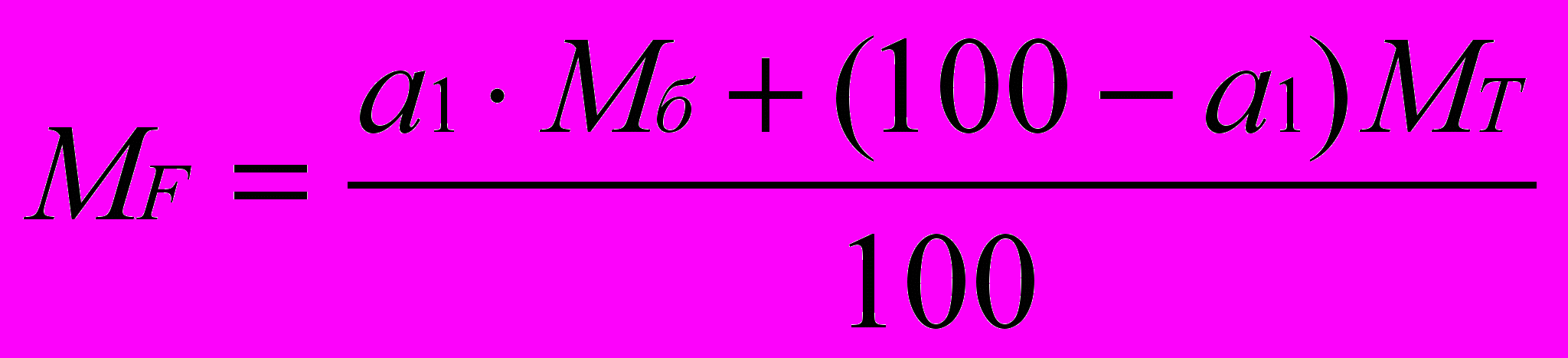
DM – мольный расход дистиллята в кмолях в час,
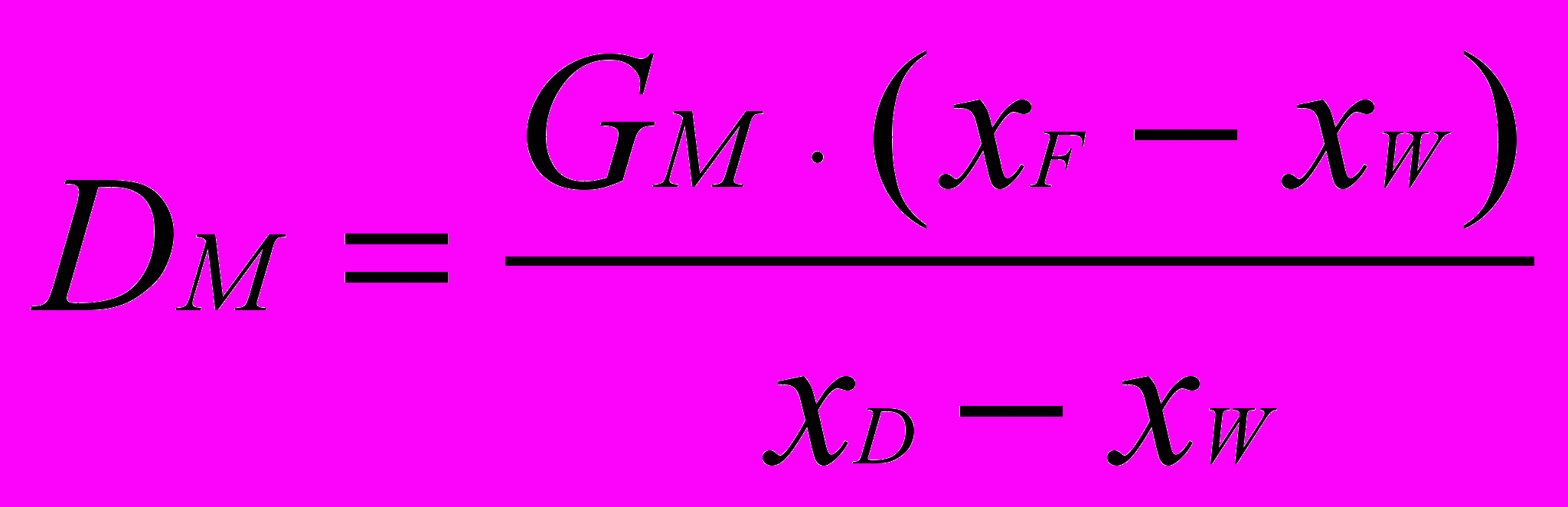
в) Отложив на оси ординат свободный член уравнения для верхней части колонны (точку Е, получаем при х = 0,
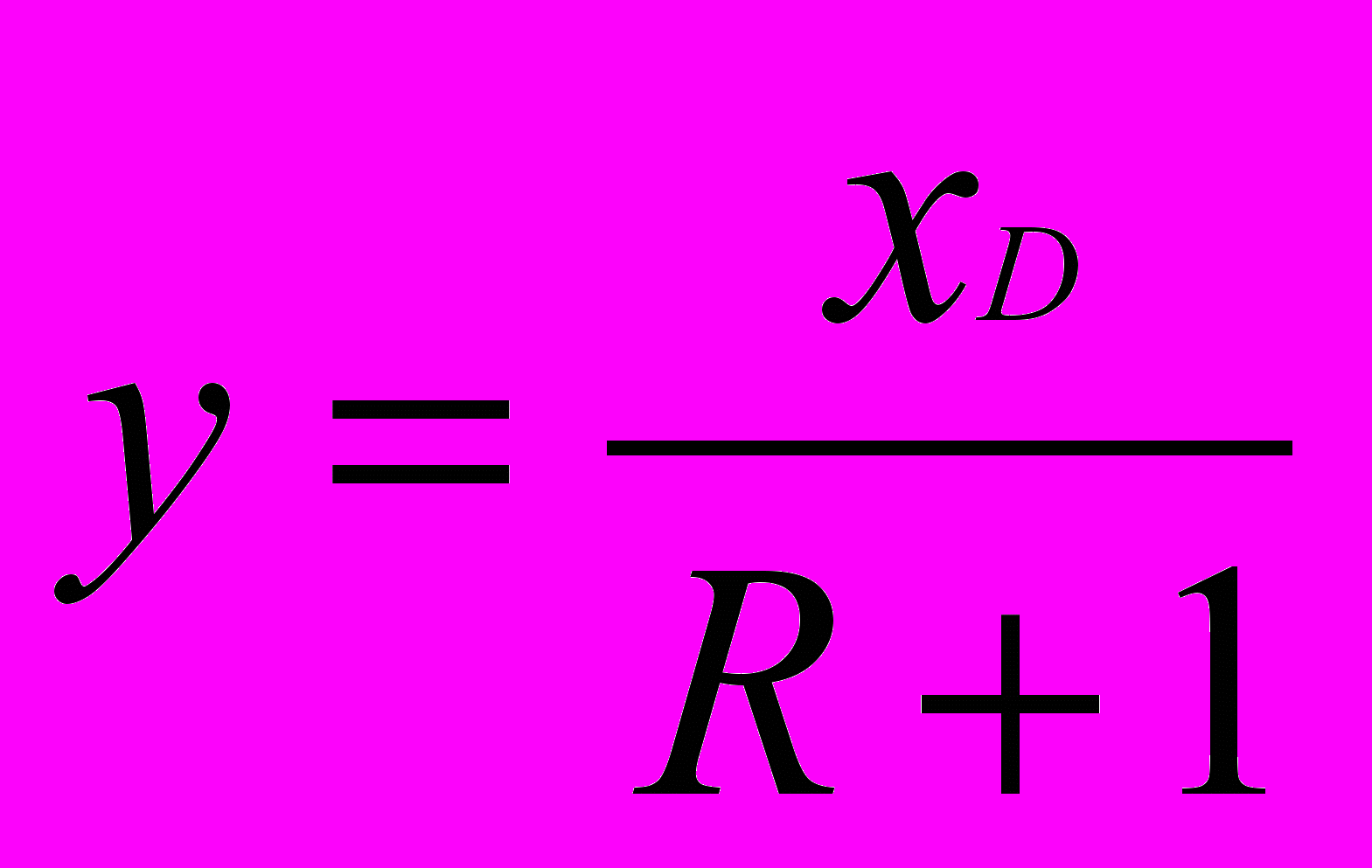
г) Затем выполняем на диаграмме (х-у) построение ломаной линии («лесенки»), начиная от точки А. Для этого из точки А, принадлежащей рабочей линии, проводят линию, параллельную оси абсцисс, до пересечения с кривой равновесия. Затем из этой точки пересечения опускают перпендикуляр до пересечения с рабочей линией. Таким образом, получают первую ступень в виде прямоугольного треугольника. Далее аналогичные построения продолжают вплоть до точки В. Подсчитывают число прямоугольных треугольников, заключённых между равновесной и рабочими линиями. Полученное число треугольников соответствует теоретическому (при условии достижения равновесия) числу ступеней изменения концентраций (числу испарений и конденсаций), необходимых для достижения заданной степени разделения. Для верхней части колонны оно составляет 5, а для нижней 7 (округляем в большую сторону). Всего теоретических тарелок (по рис. 6) nтт равно 12.
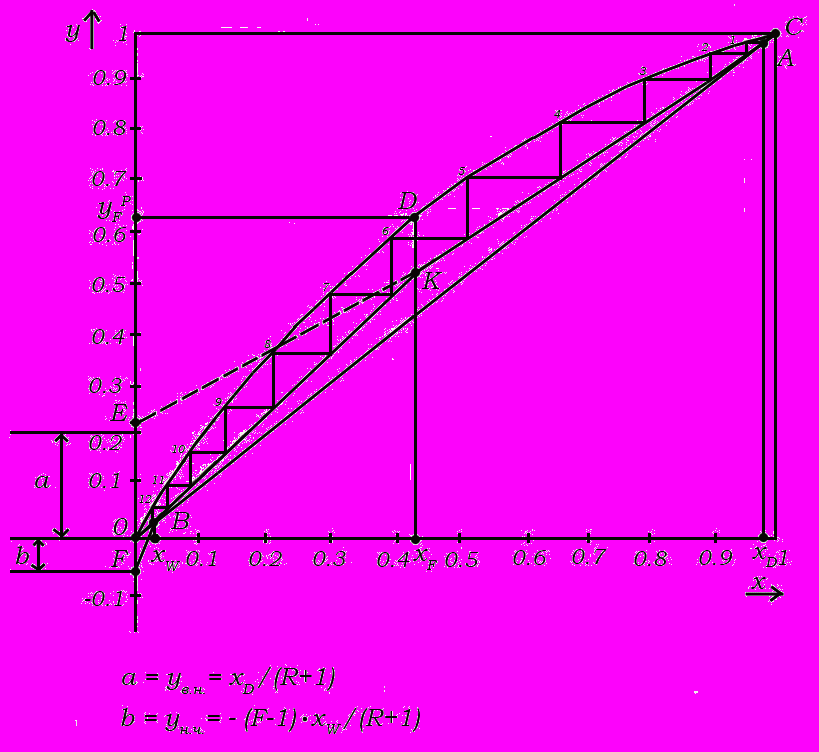
Рис. 6. Графическое построение для приближенного определения числа теоретических тарелок (nтт).
2.2.5. Определение высоты колонны
Для определения действительного числа тарелок можно воспользоваться приближёнными значениями КПД тарелки . Его вводят, чтобы учесть реальные условия, при которых не достигается равновесия в массообмене. Значения КПД определяют экспериментально. Они находятся в пределах 0,3-0,8.
Принимая к расчёту КПД равный 0,7, получаем действительное число тарелок:
nд.т. = nт.т/
Суммарная высота нижней и верхней рабочих частей колонны (Нр) составляет (принимая расстояние между тарелками h = 0,4 м):
Нр = (nд.т.-1)∙h.
Для получения общей высоты колонны (Ноб.) необходимо к рабочей высоте (Нр) приплюсовать высоту (Нс.п.) сепарационного пространства (для предотвращения уноса капель жидкости паром) и высоту (Нк.) кубовой части колонны, в которой расположен встроенный кипятильник.
Ноб. = Нр + Нс.п. + Нк.
2.2.6. Материальный баланс
а) мольный поток питания (GM):
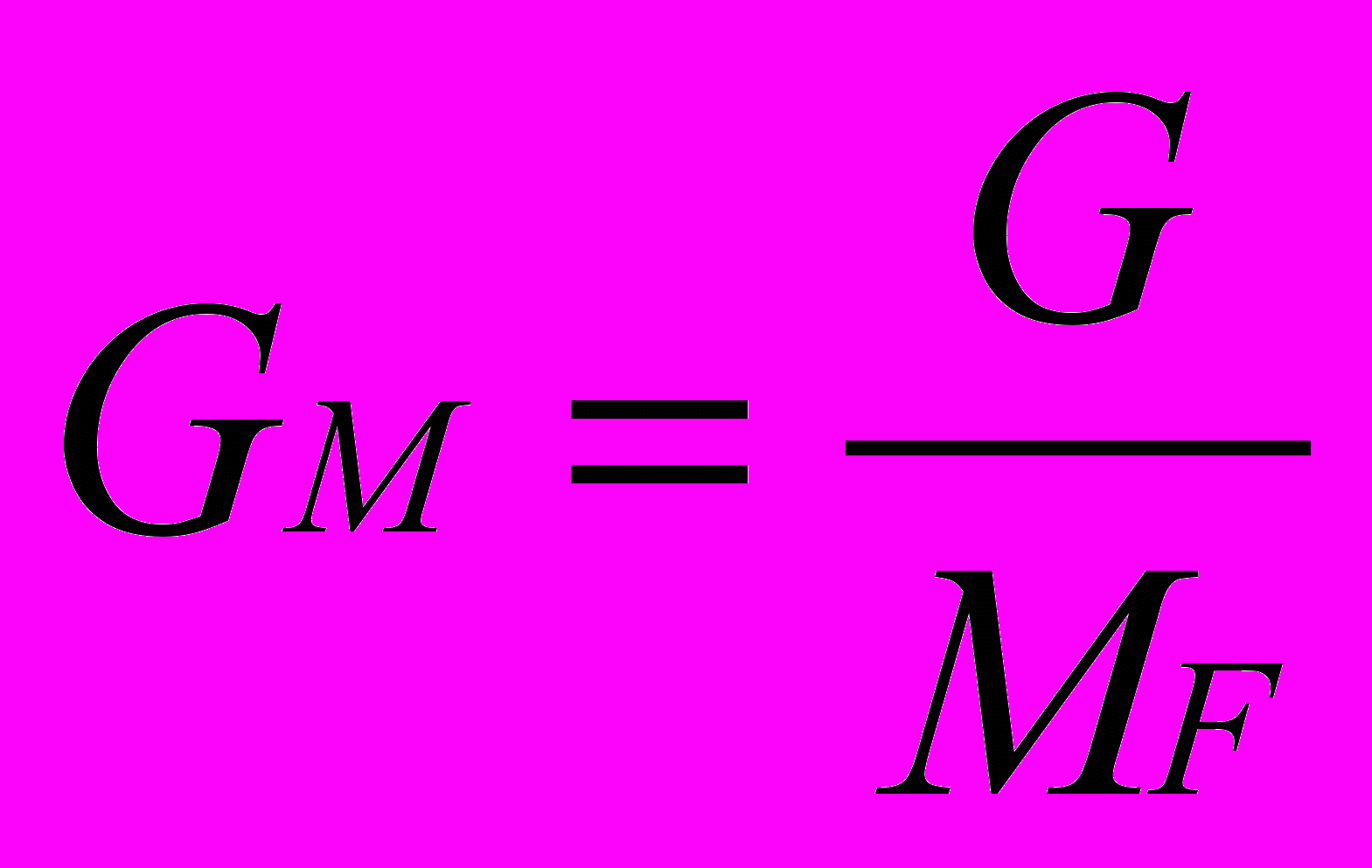
где G – заданный массовый расход питания в кг/час;
MF – молекулярная масса исходного потока, кмоль;
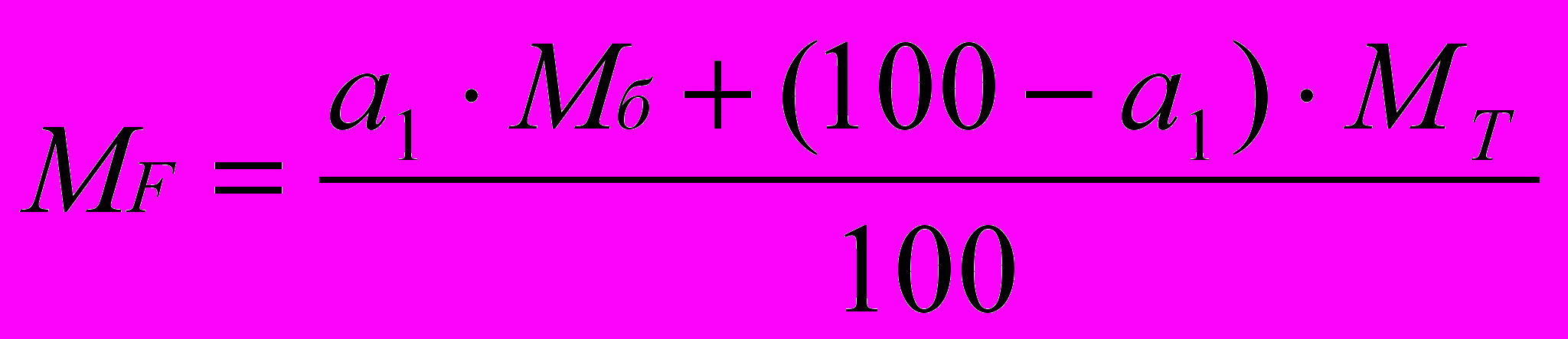
Мольные потоки отбираемого дистиллята (DM), кубовой жидкости (WO), проходящего по всей высоте колонны пара (GP) определяют из уравнений материального баланса по всей колонне по всем потокам смесей:
GM = DM+WO
и по НК в этих потоках:
GM∙хF = DM∙хD+WO∙хW.
б) мольный поток дистиллята (DM), кмоль/ч:
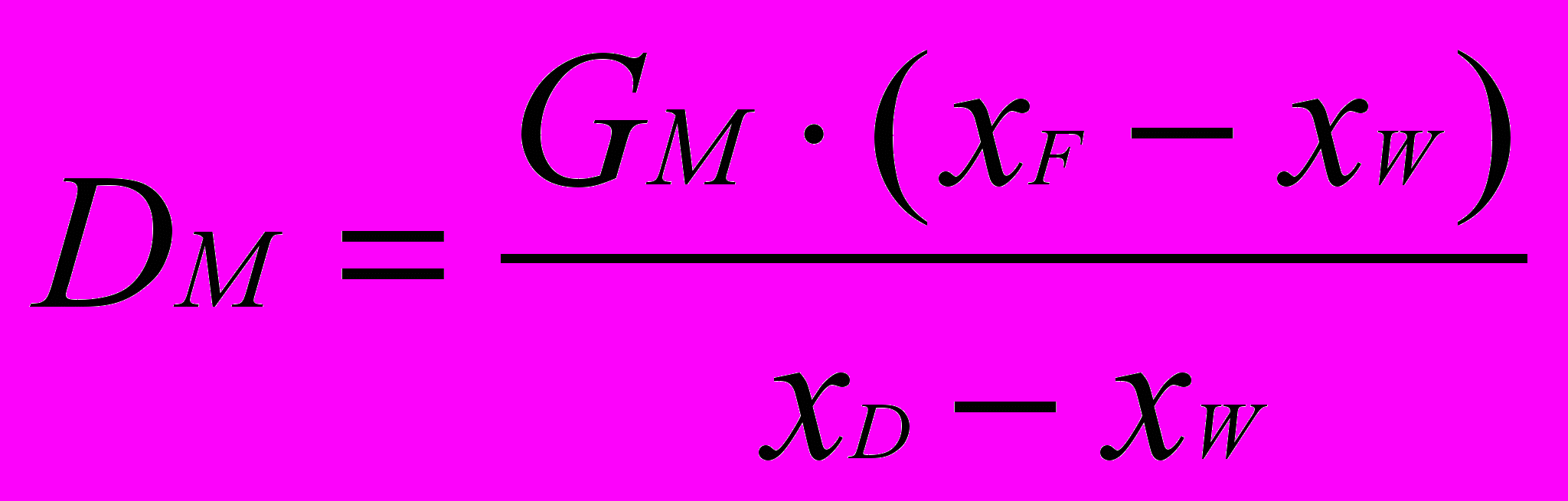
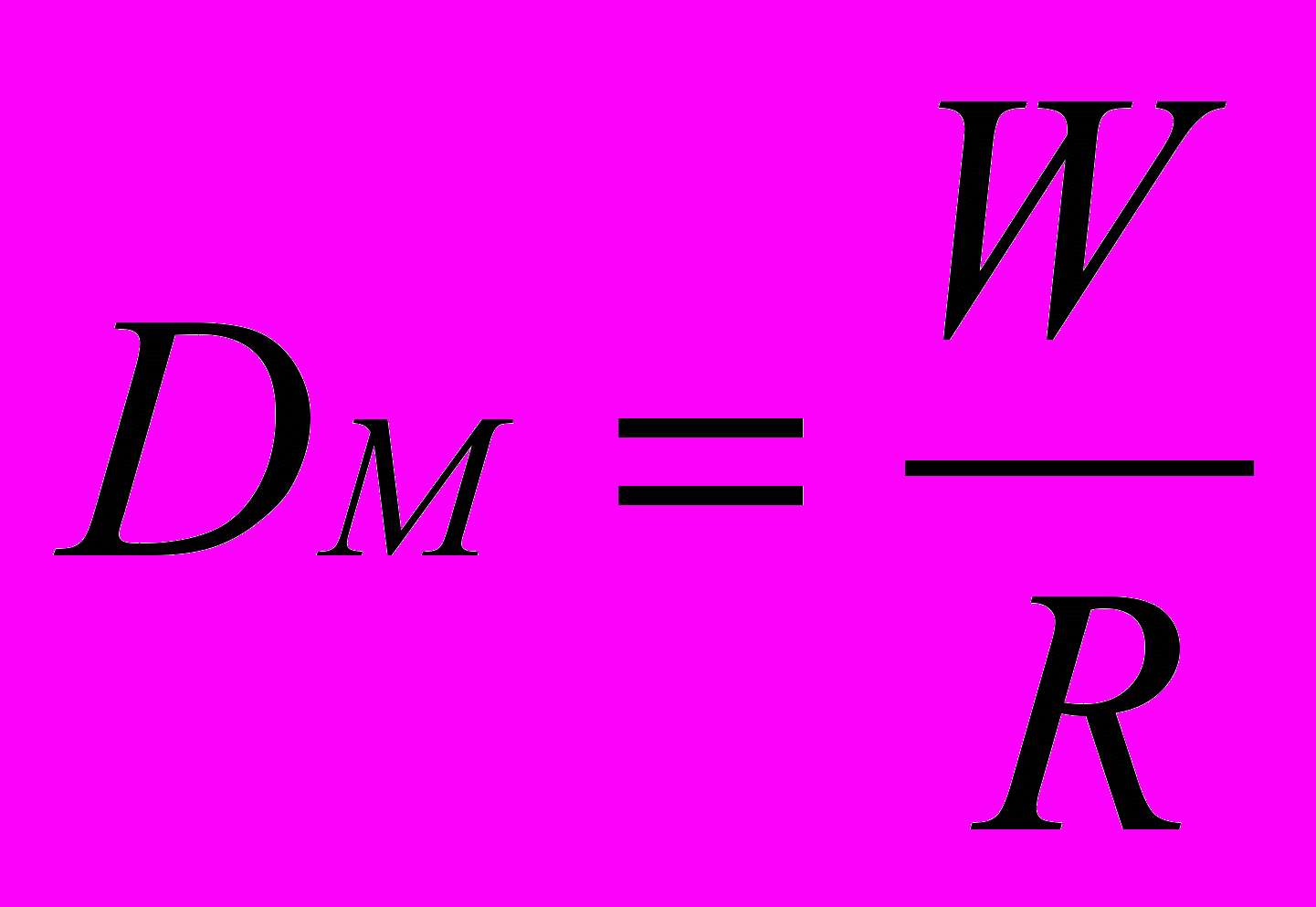
в) расчёт мольного потока паров в колонне (GP), кмоль/ч:
GP = GM∙R+DM .
г) Расчёт мольного потока кубовой жидкости, кмоль/ч:
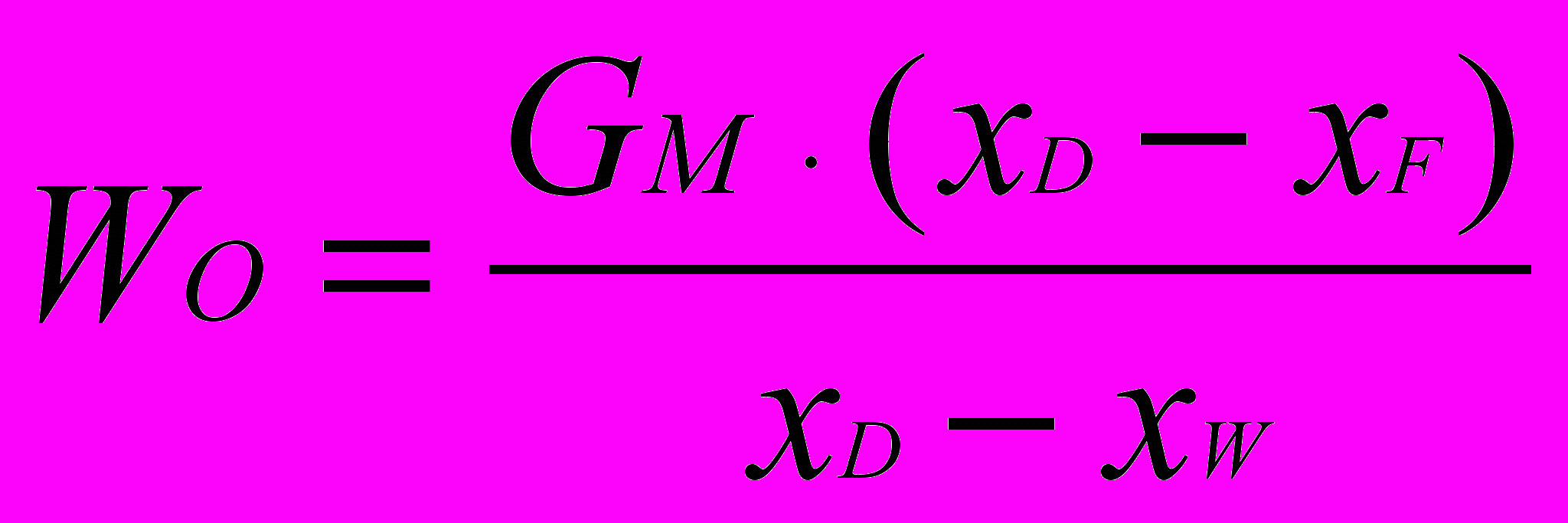
д) Количество флегмы, возвращаемой в колонну, кмоль/ч:
W=DM∙R.
При необходимости проводят пересчёт мольных потоков в час в массовые секундные:
DMM = DM∙MD, GPM = GP∙MP и WOM = WO∙MO, где MD, MP и MO – средние молекулярные массы дистиллята, паров в колонне и кубовой жидкости, которые рассчитывают следующим образом:
MD = хб∙Mб+(1−хб) ∙Mт и т.д.
2.2.7. Расчёт диаметра верхней (d1) и нижней (d2) частей колонны
Из общего выражения

d – диаметр колонны,
W – линейная скорость паров, м/с,
t – температура в колонне, и принимая, что Рраб. Мало отличается от атмосферного, имеем для верхней части колонны
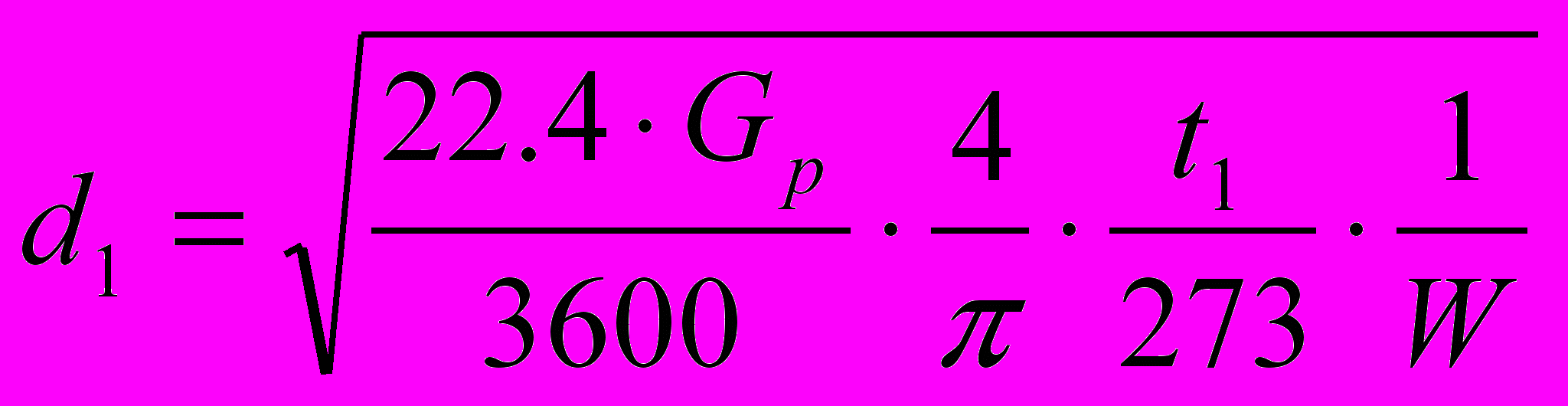
и для нижней части колонны
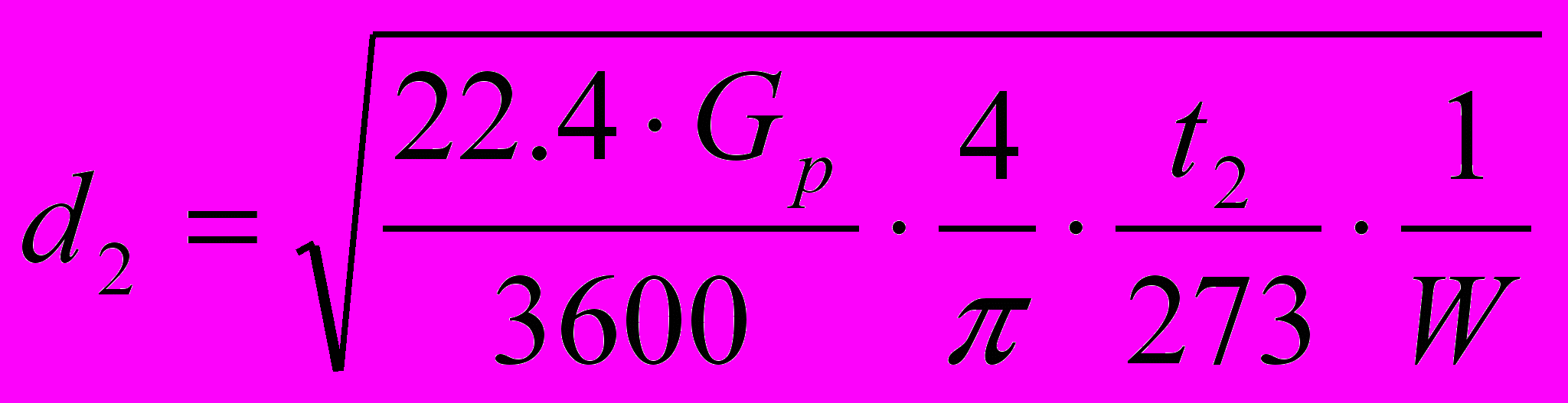
К расчёту принимаем скорость паров 0,5 м/с (рекомендуется выбор в пределах 0,3-0,8 м/с), а t1 и t2 – температуры кипения дистиллята и кубового остатка, которые определяют по диаграмме (t – x,y) для состава хD и хW.
В работе [6] приведены методические рекомендации и компьютерные программы по расчёту ректификационных колонн.