Xiv переработка каменноугольной смолы
Вид материала | Лекция |
- Vii переработка химических продуктов термической переработки твердых горючих ископаемых, 256.07kb.
- Чупахина Олега Николаевича, 811.58kb.
- I межрегиональная выставка-ярмарка, 43.59kb.
- Закон україни, 1242.64kb.
- Разработка реагентных режимов флотации каменноугольной мелочи на основе использования, 325.1kb.
- Xiv международная выставка пир, 176.11kb.
- Тема урока: Кризис европейского средневекового общества в XIV-XV вв. Столетняя война:, 74.68kb.
- Двор Людовика XIV, 62.17kb.
- Xiv-xvi вв.: площадь Вогезов такая, какой она была еще до избрания на русский престол, 87.15kb.
- Далай-Лама XIV этика для нового тысячелетия, 8032.98kb.
ЛЕКЦИЯ 10
XIV. ПЕРЕРАБОТКА КАМЕННОУГОЛЬНОЙ СМОЛЫ
14.5. Получение высокотемпературного пека
Каменноугольным пеком называется остаток, получаемый при фракционировании каменноугольной смолы. Это продукт черного цвета, однородный по внешнему виду. Пек застывает в определенном температурном интервале в твердую хрупкую массу, имеет раковистый излом. Определенной температуры плавления и застывания он не имеет: плавится в температурном интервале. Плавление и затвердевание пека не сопровождается тепловым эффектом – он не имеет скрытой теплоты плавления. По своей химической природе каменноугольный пек представляет многокомпонентную смесь многоядерных углеводородов и гетероциклов, образующихся не только в процессе получения каменноугольной смолы при коксовании углей, но и при ее переработке в результате термической поликонденсации.
Соединения, входящие в состав пека могут быть разбиты на три группы:
1) мальтены, или -вещества, растворимые в нейтральном эфире (смешанный раствор кристаллизующихся веществ, образующих вязкую маслообразную фазу);
2) асфальтены, или -вещества, растворимые в толуоле, но нерастворимые в петралейном эфире (плавкое вещество черного цвета), эта часть может вытягиваться в нити;
3) нерастворимый остаток, или -вещества, нерастворимые в толуоле (неплавкий и непластичный порошок черного цвета).
При температуре размягчения пека 63–70°С выход -составляющей части около 25%; -составляющей 41% и -составляющей 34%.
По физической природе каменноугольный пек представляет собой переохлажденную систему истинных и коллоидных растворов, в результате чего по своим свойствам он резко отличается от обычных твердых кристаллических веществ. Для пека характерен температурный интервал пластичности. Он определяется разностью двух условных температурных точек: температуры размягчения и температуры появления хрупкости. Этот интервал является важным техническим показателем, характеризующим пригодность пека для тех или иных процессов.
В зависимости от температуры размягчения пеки разделяются на мягкие, средние и твердые. Мягкие пеки имеют температуру размягчения 40–55°С (плотность 1286 кг/м3), средние 65–90°С (плотность 1290 кг/м3) и твердые 135–150°С (плотность 1320 кг/м3). Отечественная коксохимическая промышленность выпускает пеки двух видов: среднетемпературные марки А и Б и высокотемпературный пек.
Пек является самым многотоннажным продуктом смолы. Пек, выходящий из нижней части испарителя второй ступени или отпарной колонны, имеет температуру выше 300°С. Выдача такого пека в открытую емкость недопустима, так как выделяющиеся при этом токсичные пары отравляют окружающую атмосферу и легко воспламеняются. Поэтому пек предварительно выдерживается несколько часов в закрытых емкостях-пекотушителях, где он охлаждается до 145–160°С. Охлажденный пек поступает на гранулирование.
Широкое распространение получил способ охлаждения расплавленного пека и его последующая грануляция под слоем воды на пластинчатом транспортере. Разливка пека осуществляется с помощью струйного питателя, представляющего собой емкость прямоугольного сечения с плоским днищем, в котором просверлено от 175 до 176 отверстий диаметром 8–10 мм.
Разливка, охлаждение, хранение и погрузка пека в железнодорожные вагоны осуществляется в пековом парке смолоперегонного цеха. Установка для охлаждения и грануляции среднетемпературного пека состоит из железобетонного бассейна с проточной водой, металлического пластинчатого транспортера, погруженного в воду, и питателя, через который горячий пек (с температурой 145–160°С) поступает на грануляцию при температуре не выше 31–32°С. Время пребывания пека в проточной воде около 4 мин. Охлажденный гранулированный среднетемпературный пек должен иметь влажность не более 2–3%.
Для совершенствования технологии разливки и охлаждения пека может применяться усовершенствованный струйный питатель, позволяющий регулировать расход разливаемого пека в зависимости от температуры его нагрева, в результате чего достигается тщательное охлаждение струй пека и получаемые гранулы полностью затвердевают. Длительная эксплуатация такого питателя на Донецком коксохимическом заводе показала достаточную эффективность охлаждения пека, значительное улучшение условий труда обслуживающего персонала. Большой интерес представляет использование грануляторов пленочного типа и специальных грануляционных аппаратов.
Для охлаждения пека могут использоваться холодильники испарительного охлаждения, напорные баки и горизонтальные цилиндрические пекотушители.
Среднетемпературный пек характеризуется содержанием веществ, нерастворимых в толуоле (16–20%) и выходом летучих веществ (68–71%). Среднетемпературный пек находит широкое применение в цветной металлургии в качестве связующего в производстве электродных изделий и для производства пекового кокса (до 73% от общего его производства), для производства мягкой кровли, угольных брикетов, в черной металлургии, в производстве дорожного дегтя и в дорожном строительстве, в производстве лаков и т.д.
Среднетемпературный пек используется для производства высокотемпературного пека, производство которого осуществляется в пекоксовом цехе коксохимического завода. Этот цех состоит из отделения пекоподготовки, пекококсовых печей и отделения конденсации.
На заводах, располагающих установками для коксования высокотемпературного пека отсутствует грануляция среднетемпературного пека, так как горячий Среднетемпературный пек из отделения ректификации смолы непосредственно передается в пекококсовый цех.
Для получения пека с температурой размягчения 140–150°С в коксохимической промышленности получил применение метод обработки среднетемпературного пека воздухом. Сущность метода заключается в накоплении продуктов уплотнения и в повышении температуры размягчения пека в результате дегидрирования и последующих процессов конденсации – полимеризации многокольчатых ароматических соединений, находящихся в пеке. На долю процессов конденсации – полимеризации приходится около 80%.
Частично количество продуктов уплотнения увеличивается, так как они концентрируются в высокоплавком пеке в результате дистилляции (удаление пековых дистиллятов). Воздух выполняет роль химического агента и служит средством для перемешивания.
Процесс окисления среднетемпературного пека протекает с выделением тепла, однако скорость его очень мала в начале окисления, особенно когда температура исходного пека ниже 300°С. Оптимальная температура, при которой начинают интенсивно протекать процессы конденсации и полимеризации пека, 340°С. Основными факторами процесса являются расход воздуха (на 1 кг пека), температура и продолжительность процесса.
Высокотемпературный пек получают по непрерывной схеме окисления сырья в специальных аппаратах реакторах, объединенных в технологическую цепь (последовательно соединенных по два или три).
Исходным сырьем для получения высокотемпературного пека служат среднетемпературный пек и коксовая смола, образующаяся при коксовании высокотемпературного пека (и пековые дистилляты).
Выход высокотемпературного пека достигает 87–89%. Качество продукта характеризуется следующими данными: температура размягчения 140–150°С, выход веществ, нерастворимых в толуоле 45–50%; выход летучих веществ 49–52%. Выход пековых дистиллятов 10–13%. Высокотемпературный пек является исходным сырьем для получения пекового кокса.
Для получения высокотемпературного пека воздушным способом применяются кубы-реакторы диаметром 3000 мм и рабочей емкостью 27 м3. Обогрев куба ведется доменным или коксовым газом. Для улавливания капель фракций пека, уносимых из куба-реактора отработанным воздухом, используется отбойник диаметром 800 мм, изготовленный из стали и теплоизолированный.
14.6. Технология пекококсового производства
Для получения пекового кокса применяются пекококсовые печи конструкции Гипрококса, приспособленные для обогрева коксовым и доменным газом. Отопительный простенок состоит из 27 вертикалов, соединенных между собой горизонтальным каналом. Горение в отопительных каналах происходит на одной половине простенка, продукты горения отводятся через горизонтальный сборный канал на другую половину простенка. Камера коксования имеет полезный объем 12 м3, разовая загрузка камеры 18–18,5 т пека с температурой 320–340°С.
Коксовая батарея компонуется из печей, которые группируются на блоки по 5–7 камер. Выдача печей осуществляется по серийности 2–1, которая обеспечивает оптимальные условия эксплуатации. На некоторых заводах для создания оптимальных условий труда для рабочих, обслуживающих выдачу печей, обеспечения равномерной разовой загрузки газосборников принята серийность 5–2 и 7–2. Контроль теплотехнического режима пекококсовых печей аналогичен контролю, применяемому на обычных коксовых печах.
Готовность пекового кокса определяется температурой по оси коксового пирога, которая к концу периода коксования достигает 950–1050°С.
Для загрузки камер пеком служат дозаторы. Каждый блок печей (5–7 камер) обслуживает один сдвоенный дозатор, имеющий два независимых устройства для переключения расхода пека. Оно выполнено в виде семиходового (или пятиходового) крана, позволяющего переключить загрузку с одной печи на другую, в соответствии с серийностью выдачи печей 7–2 или 5–2. Одновременно от одного дозатора грузятся две печи. Процесс загрузки камер автоматизирован.
Охлаждение летучих продуктов коксования пека осуществляется в стояках и газосборниках надсмольной аммиачной водой (до 80–90°С), расход которой составляет 10–12 м3 на 1 т коксуемого пека.
Дальнейшее охлаждение и конденсация из газа химических продуктов производится либо совместно с летучими коксового цеха в цехе улавливания, либо самостоятельно в отделении конденсации пекококсового цеха.
Выдаваемый из печей пековый кокс тушится мокрым или сухим способом и разделяется по крупности на два класса: >10 мм – электродный кокс и <10 мм – коксовая мелочь.
Качество пекового кокса оценивается его зольностью, выходом летучих веществ и содержанием серы. Кокс пековый электродный первого сорта (КПЭ-1) должен содержать: золы менее 0,3%, летучих веществ менее 0,8 и серы менее 0,3%. Он используется в цветной металлургии для изготовления пековых электродов.
Проводятся исследования по разработке технологии получения сверхтвердого пека (с температурой размягчения выше 250°С) как спекающего компонента для электроэразионного графита, методом растворения и обработкой воздухом.
В последние годы в связи с развитием конвертерного производства стали, возникла необходимость в изготовлении на основе пека и масел связующего для безобжиговых смолодоломитовых и смоломагнезитовых огнеупоров.
14.7. Переработка антраценовой фракции
Методом кристаллизации перерабатывают первую антраценовую фракцию, состоящую главным образом из ароматических соединений с числом бензольных колец от трех до пяти и незначительного количества соединений с меньшим (два) и большим (свыше пяти) числом колец. Основными компонентами фракции являются трехъядерные ароматические соединения – антрацен, фенантрен, карбазол, пирен и их метилированные производные.
Первая антраценовая фракция заводов Юга характеризуется такими данными:
-
Плотность, кг/см3
1125–1140
Отгон до 300°С, %
15–38
Температура,°С:
95% отгона
360–336
появление кристаллов
92–86
Содержание, %:
антрацена
9,1–7,9
фенантрена
37,4–28,4
карбазола
12,5–10,3
Переработка антраценовой фракции осуществляется в две стадии: кристаллизация и разделение полученной в результате кристаллизации гетерогенной системы. Для охлаждения и кристаллизации фракции применяют кристаллизаторы периодического действия с внутренней мешалкой (механические).
Цель кристаллизации антраценовой фракции – выделение основных компонентов в кристаллическом виде с получением сырого антрацена.
Кристаллизация антраценовой фракции протекает при высокой вязкости среды и низком содержании кристаллизующихся компонентов, в частности антрацена и карбазола. Это обусловливает структуру твердой фазы, которая выделяется в виде мелких кристаллов. Наличие во фракции нерастворимых веществ, находящихся во взвешенном состоянии, ухудшает ее фильтруемость. Эффективность кристаллизации антраценовой фракции повышается в присутствии растворителей.
Переработка антраценовой фракции осуществляется в основном по двум схемам: механический кристаллизатор–вакуум-фильтр-центрифуга или механический кристаллизатор–центрифуга. Вторая схема является более совершенной и применяется на современных заводах.
В схеме кристаллизатор–центрифуга (рис. 27) применена высокопроизводительная автоматическая центрифуга типа АГ-120-4ц.
Антраценовая фракция перерабатывается в смеси с 20% поглотительного масла, полученного после регенерации сетки центрифуги. Это ускоряет процесс кристаллизации фракции, улучшает качество сырого антрацена и в первую очередь его гранулометрический состав.
Откристаллизованная фракция с температурой 30–35°С поступает в центрифугу АГ, в которой наполнение барабана, фильтрование, выгрузка и регенерация сит автоматизированы.
В результате переработки I антраценовой фракции получают два продукта: антраценовое масло и сырой антрацен.
Показатели процесса характеризуются следующими данными: температура загружаемой фракции 35–40°С, поглотительного масла, поступающего на регенерацию, 95–98°С; расход масла на регенерацию 15–20% от исходной фракции; температура воды, поступающей на охлаждение, 25–30°С. При кристаллизации фракции в сырой антрацен переходит до 80% антрацена, 50% карбазола и 30% фенандрена от их ресурсов во фракциях.
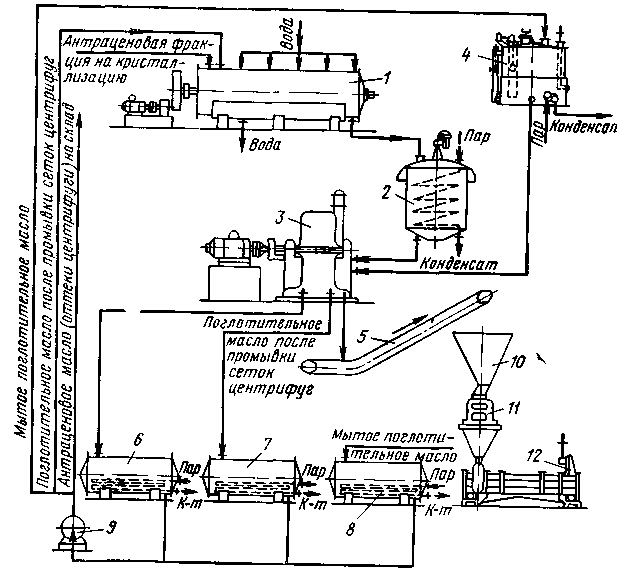
Рис. 27. Технологическая схема переработки I антраценовой фракции:
1 – барабанный кристаллизатор; 2 – мешалка; 3 – автоматическая горизонтальная центрифуга; 4 – напорный бак мытого поглотительного масла; 5 – транспортер; 6–8 – сборники мытого поглотительного масла; 9 – насос; 10 – бункер; 11 – весы; 12 – зашивочная машина
Сырой антрацен под названием «Антрацен технический каменноугольный» является товарным продуктом. Он применяется в производстве синтетических дубителей, красителей, сажи (вместе с антраценовой фракцией) и для энергетических целей.
Выход сырого антрацена от каменноугольной смолы составляет 2–2,2%.
Для кристаллизации антраценовой фракции применяются механические кристаллизаторы периодического действия диаметром 1,6 м с полезной длиной 6,56 м, общей емкостью 12 м3, поверхностью орошения 25 м2. Для разделения фаз применяют центрифуги АГ-1200-4ц завода им. Фрунзе; вакуум-фильтры непрерывного действия завода «Уралхиммаш» с поверхностью фильтрования 5 м2, производительностью по твердому остатку 144 кг/(м2 ч).
14.8. Переработка нафталиновой фракции
Нафталин – один из важнейших продуктов переработки каменноугольной смолы. Он является ценным сырьем для химической промышленности. Потребность народного хозяйства в нем обеспечивается только за счет коксохимического нафталина. Поэтому максимальное извлечение нафталина из каменноугольной смолы и рациональное его использование являются исключительно актуальной задачей.
Основным исходным сырьем для получения нафталина является нафталиновая фракция, полученная при фракционировании смолы и содержащая до 80–85% нафталина, т.е. 92–93% его ресурсов в смоле.
В процессе ректификации смолы в нафталиновую фракцию переходят вещества, выкипающие в пределах 210–230°С, т.е. при температуре кипения нафталиновой фракции. Поэтому нафталиновая фракция представляет собой сложную смесь соединений ароматического ряда, кислого, основного и нейтрального характера. Наиболее ценным компонентом является нафталин (С10Н8). Нафталин кристаллизуется в виде белых тонких лепестков (звездочек), хорошо сублимируется, сгорает светящимся пламенем с образованием большого количества копоти. Нафталин растворяется во многих растворителях и сам является хорошим растворителем.
В нафталиновой фракции содержатся, %: метилнафталинов до 6, тионафтена до 3,8, фенолов до 2,3, оснований около 1,9, непредельных соединений до 0,4, индола 0,3 и др. Основными примесями, затрудняющими получение технического и чистого нафталина, являются: из серусодержащих примесей тионафтен, из непредельных соединений кумарон, инден и др., фенолы, основания и насыщенные соединения.
Способы выделения нафталина из фракции определяются требованиями потребителей к качеству продукта и экономичности процесса.
На коксохимических заводах применяют два способа переработки нафталиновой фракции: кристаллизации фракции с последующим механическим разделением твердой и жидкой фаз прессованием с получением технического прессованного нафталина и получение дистиллированного нафталина с использованием химической очистки нафталиновой фракции и последующей ее ректификации.
Содержание примесей в техническом или дистиллированном нафталине обусловливается свойствами и поведением примесей в процессе кристаллизации фракции, химической очистке и ректификации очищенной фракции при получении дистиллированного нафталина.
При переработке нафталиновой фракции кристаллизацией и прессованием такие примеси как тионафтен, инден, индол, хинолин, изохинолин и др. образуют с нафталином смешанные кристаллы, т.е. вместе с нафталином переходят в твердую фазу и при прессовании не отделяются и загрязняют окончательный продукт (прессованный нафталин).
Другие примеси образуют с нафталином эвтектические смеси при температуре 25–60°С и в виде пленки удерживаются на поверхности кристаллов нафталина. Эти примеси выделяются из нафталина прессованием.
В производстве дистиллированного нафталина используются два процесса: химическая очистка нафталиновой фракции концентрированной серной кислотой с последующей промывкой щелочью и ректификация очищенной фракции. При сернокислотной очистке нафталиновой фракции протекают реакции сульфирования тионафтена и других примесей, реакции поликонденсации, в результате которых хорошо удаляется большинство примесей, в том числе фенолы, основания, непредельные соединения и др. за исключением тионафтена, метилнафталинов и индола.
При этом содержание тионафтена в конечном продукте уменьшается на 30–40%, но глубокая очистка дистиллированного нафталина от этой примеси не обеспечивается.
При ректификации очищенной нафталиновой фракции оставшиеся примеси также ведут себя по-разному. Тионафтен, образующий с нафталином азеотропную смесь, практически не выделяется. Температура кипения нафталина 217,96°С, а тионафтена 219,9°С, т.е. t = 1,9°. Поэтому при ректификации снова единственно трудноудаляемой примесью остается тионафтен.
При переработке нафталиновой фракции методом кристаллизации и горячего прессования откристаллизованной массы – первым и основным процессом является кристаллизация.
Нафталиновая фракция представляет собой насыщенный раствор нафталина в каменноугольных маслах с незначительной примесью других веществ. При охлаждении фракции растворимость нафталина и других кристаллизующихся веществ в масле уменьшается, что вызывает переход раствора в неустойчивое состояние – пересыщенное с последующим выделением кристаллов.
При переработке нафталиновой фракции с содержанием нафталина до 70% механическое удаление масел (жидкой фазы) после кристаллизации осуществляется последовательно центрифугированием и прессованием. При концентрации нафталина выше 80% откристаллизовавшаяся масса сразу может поступать на прессование.
На отечественных заводах широкое применение получили две схемы переработки нафталиновой фракции:
1) кристаллизатор – пресс для нафталиновой фракции с концентрацией нафталина 80–85%. Выход товарного нафталина – 84% от ресурсов во фракции. Оттеки горячего прессования возвращаются в смолу, что увеличивает выход нафталина до 95,0%;
2) кристаллизатор – пресс с обогащением прессовых оттеков по схеме механический кристаллизатор–центрифуга–пресс.
Вторая схема за последние годы получила широкое применение. Одним из первых на такую схему переработки нафталиновой фракции перешел Днепродзержинский коксохимический завод, применив для кристаллизации нафталина высокоэффективный барабанный кристаллизатор собственной конструкции и автоматический с увеличенной производительностью пресс ДО-140А, разработанный Новосибирским заводом «Тяжстанкогидропресс». Это позволило значительно увеличить коэффициент извлечения нафталина и улучшить его качество.
Для более полного извлечения нафталина от ресурсов его в нафталиновой фракции прессовые оттеки подвергают обогащению по схеме механический кристаллизатор–центрифуга–пресс. Полученный при этом фугованный продукт, содержащий 85–90% нафталина, затем перерабатывают в прессованный нафталин совместно с нафталиновой фракцией, а оттеки фугования используют в производстве товарных масел. Таким образом, переработка нафталиновых оттеков является составной частью в технологии производства прессованного нафталина.
Технологическая схема процесса приведена на рис. 28. Нафталиновая фракция при температуре 85–95°С из сборников отделения дистилляции перекачивается насосом в напорные баки 1, а при избытке часть ее передается в хранилище, откуда по мере необходимости также перекачивается в эти напорные баки.
Из напорных баков после частичного охлаждения до 70–75°С фракция поступает в ванны барабанных охладителей 2, где происходит интенсивная кристаллизация нафталина в виде корки по наружной поверхности вращающегося барабана, охлаждаемого водой, так как при кристаллизации происходит выделение тепла. Необходимая температура фракции в ванне поддерживается подачей горячей воды.
С поверхности барабанов корка нафталина снимается специальными ножами и подается на скребковый конвейер 3, питающий мешалки 5.
Для нагрева шихты до нужной температуры (54–55°С) в мешалки прессов подается горячая нафталиновая фракция из напорных баков 1. Затем эта масса перемешивается и подается на горячее прессование в пресс 4.
Прессование нафталина осуществляется под давлением 40– 60 МПа (400–600 ат) с помощью автоматических гидропрессов типа ДО-140 и ДО-140А.
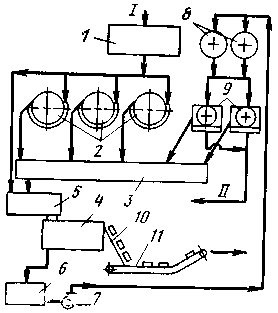
Рис. 28. Технологическая схема переработки нафталиновой фракции:
I – нафталиновая фракция; II – масло; a – прессованный или технический нафталин;
б – конденсат; в – пар
1 – напорный бак; 2 – ванны барабанных охладителей; 3 – скребковый конвейер; 4 – пресс; 5 – мешалки; 6 – сборник оттеков; 7 – насос; 8 – механический кристаллизатор; 9 – центрифуги; 10 – течка; 11 – конвейер
Спрессованные брикеты нафталина выталкиваются в течку 10 и конвейером 11 подаются в плавильник, откуда плавленый нафталин загружается в специальные железнодорожные цистерны и направляются к потребителю.
Оттеки прессования из фильтрпрессов, содержащие 50–60% нафталина, поступают в сборник оттеков 6, откуда насосом 7 перекачиваются в механические кристаллизаторы периодического действия 8. Откристаллизовавшаяся масса из кристаллизаторов направляется в центрифуги 9 периодического действия.
После центрифуг кристаллическая масса через элеватор поступает на скребковый конвейер, где шихтуется с нафталином после барабанных кристаллизаторов, а затем подается в мешалки прессов 5. Оттеки после фугования также могут возвращаться в цикл до определенного накопления нафталина в нафталиновой фракции, после чего эти оттеки на некоторое время выводятся из цикла переработки. В этом случае они поступают в сборник, а затем на химическую очистку от фенолов и пиридиновых оснований.
Так как вторичные оттеки после фугования выводятся из цикла переработки, это дает возможность получать прессованный (технический) нафталин, вполне пригодный для производства фталевого ангидрида.
Основным продуктом процесса является технический плавленый нафталин с температурой кристаллизации 78,85°С, содержанием чистого нафталина 97,5%, тионафтена до 2,0%, золы не более 0,15% и влаги не выше 2,0%. Выход нафталина от фракции составляет 90–92%.
Переработка нафталиновой фракции, полученной из смол восточных коксохимических заводов с низким содержанием серы в ней, может перерабатываться лишь по схеме кристаллизатор– пресс с постоянным возвратом прессовых оттеков в смолу. При этом вполне обеспечивается получение технического нафталина всех сортов (температура кристаллизации 78,5–79,3°С).
Так как основным потребителем нафталина является производство фталевого ангидрида, для которого не требуется нафталин с высокой температурой кристаллизации, то переработка нафталиновой фракции на большинстве заводов осуществляется по схеме кристаллизатор–пресс.
Технический плавленный нафталин выпускается двух марок А и Б, дистиллированный марки В, качество которых нормируется ГОСТ.
Основными направлениями усовершенствования технологии получения технического нафталина из нафталиновой фракции являются: применение барабанных кристаллизаторов с ребристой поверхностью конструкции УкрНИИхиммаша; освоение и дальнейшее совершенствование получения дистиллированного нафталина с целью снижения потерь нафталина с кислыми отходами; освоение способа, сочетающего окислительную очистку сырья озонированным воздухом с последующей дистилляцией; освоение технологии кристаллизации – плавления для переработки нафталиновых оттеков в технический нафталин.
XV. ПРОИЗВОДСТВО ЧИСТОГО НАФТАЛИНА
15.1. Производство кристаллического нафталина
Чистый нафталин является продуктом дальнейшей переработки технического прессованного нафталина или концентрированной нафталиновой фракции. На отечественных коксохимических заводах получение очищенного нафталина осуществляется методом ректификации и сублимации.
Наличие в техническом нафталине и нафталиновой фракции различных примесей: сернистых и непредельных соединений, фенолов, оснований, насыщенных углеводородов и др., способных образовывать с нафталином смешанные кристаллы, азеотропные смеси, комплексные соединения не позволяют получить глубокоочищенный нафталин только путем ректификации.
Поэтому технология очистки нафталина от примесей сочетает химические процессы и ректификацию. Цель такой очистки заключается в получении продукта, содержащего не менее 99% основного вещества нафталина.
В качестве реагентов для химической очистки нафталина применяют серную кислоту, формалин, хлористый алюминий, металлический натрий, хлор, водород и др.
Так как наиболее трудноудаляемой примесью является тионафтен, поэтому для его выделения выбирается реагент, отличающийся достаточной избирательностью к последнему.
В промышленности наибольшее применение получили сернокислотный и формальдегидный методы.
Очистка технического нафталина (или нафталиновой фракции) сернокислотным методом основана на различии в скорости сульфирования нафталина и тионафтена с помощью 93–94%-ной серной кислоты с образованием тионафтен- и нафталинсульфокислот. При очистке протекают следующие процессы: а) основной – сульфирование тионафтена; б) побочные – сульфирование нафталина, конденсация непредельных и других соединений с образованием сложных веществ; окисление органических соединений при восстановлении серной кислоты до SO2; растворение продуктов реакции в углеводородном или в кислотном слое.
Из продуктов реакций в углеводородном слое (нафталине) растворяются сульфокислоты. Продукты конденсации растворяются в серной кислоте.
Процесс сернокислотной очистки технического нафталина (или фракции) включает такие операции: обработка нафталина концентрированной кислотой; промывка продукта водой и обработка 13–14%-ным раствором щелочи. В процессе сернокислотной очистки из нафталина выделяются пиридиновые основания и фенолы.
Промывка мытого нафталина раствором щелочи (13–14%-ным) необходима для нейтрализации и удаления примесей, кипящих выше 245°С. При промывке нафталина водой и щелочным раствором растворяются сульфокислоты, оставшиеся в мытом нафталине. Содержание их в промытой воде может составлять 10–15%.
Очистка нафталинсодержащего сырья может осуществляться в установках периодического и непрерывного действия. В установках непрерывного действия обеспечивается достаточный массообмен, что снижает потери продуктов и улучшает его качество.
Очистка нафталина концентрированной серной кислотой представляет сложный процесс, протекание которого зависит от многих факторов и в первую очередь от количества и концентрации кислоты и времени контакта. Основными показателями процесса являются: глубина очистки, расход серной кислоты и потери нафталина. На новых заводах при сернокислотной очистке прессованного нафталина расход серной кислоты составляет 12–15% (по массе). Отходы производства – кислая смолка – подвергаются утилизации. Потери нафталина на стадии очистки достигают 7–10% (от ресурсов). Показателем степени очистки служит температура кристаллизации нафталина.
После сернокислотной очистки нафталин подвергают ректификации, при которой получают сорта чистого нафталина (первый, второй и третий) и кубовые остатки. Последние используют для получения сублимированного нафталина или возвращают в нафталиновую фракцию перед ее кристаллизацией и прессованием.
Более эффективным реагентом для очистки нафталина является формальдегид (СН2О). Формальдегидный метод очистки нафталина в кислой среде был разработан сотрудниками УХИНа и фенольного завода и с некоторыми видоизменениями успешно применяется в производстве.
Применение формальдегида основано на различии в скоростях реакции конденсации формалина с нафталином и тионафтеном.
Процесс формальдегидной очистки ведется в присутствии 90–94%-ной серной кислоты, которая необходима для конденсации непредельных соединений, содержащихся в техническом нафталине. Образующиеся смолы хорошо растворяются в серной кислоте и поэтому легко разделяются с отработанной серной кислотой. В процессе очистки происходит частичное сульфирование нафталина и тионафтена. Но в связи с тем, что расход кислоты небольшой, эта реакция существенно не влияет на выход нафталина.
Серная кислота каталитически воздействует на реакцию конденсации тионафтена.
Продукты реакции конденсации тионафтена растворяются в нафталине и выделяются при ректификации в виде кубовых остатков. Этим формальдегидный способ отличается от сернокислотного, при котором тионафтен выводится в виде сульфокислот с промывными водами. Такое действие реагентов обусловливает раздельный порядок ввода серной кислоты и формальдегида в расплавленный нафталин.
Как и при использовании сернокислотного метода очистки, очищенный нафталин подвергают ректификации для получения чистого нафталина (первого, второго или третьего сорта) и кубовых остатков.
Достоинства способа: более глубокая степень очистки нафталина; большой выход кристаллического нафталина; возможность применения технических сортов нафталина с низкой температурой кристаллизации, что повышает степень извлечения нафталина из смолы; возможность использования технического нафталина с повышенным содержанием серы (0,6–0,8%); снижаются потери нафталина.
Применение формальдегида для очистки нафталина не исключило стадию сульфирования, хотя расход серной кислоты снижен до 5–6%; температура кристаллизации очищенного нафталина 80,2°С.
Таким образом, этим методам присущи общие недостатки: сложность аппаратурного оформления, трудоемкость, наличие токсичных отходов, загрязняющих окружающую среду, большие потери нафталина (до 7–11%), процесс трудно поддается автоматизации.
Перспективным методом, позволяющим получить глубокоочищенный нафталин, является каталитическая гидроочистка.
Сырьем для процесса является непосредственно нафталиновая фракция, прошедшая предварительное обесфеноливание и обеспиридинивание. Технологический процесс протекает в две стадии: гидрокрекинг и ректификация, минуя производство технического нафталина. Гидроочистка обеспечивает переработку сырья с повышенным содержанием тионафтена и получение высоких выходов нафталина от ресурсов, исключает образование неутилизированных отходов, уменьшает количество вредных выбросов в окружающую среду и создает основы для централизации производства. Глубокоочищенный нафталин можно получить методом противоточной жидкостной экстракции нафталиновой фракции, который позволяет получить нафталин, температура кристаллизации которого 80,2°С, с содержанием тионафтена (бензотиофена) до 0,3% из высокосернистого сырья с выходом продукта до 97,7% от ресурсов. Вторым продуктом процесса является концентрат бензотиофена с содержанием его 11%.
Для очистки технического нафталина с высоким содержанием сернистых соединений целесообразно использовать безводный А1С13. Небольшие количества этого реагента позволят эффективно очистить технический нафталин от индола, хинолина и регулировать остаточное содержание в нем тионафтена до норм, предъявляемых при использовании нафталина в производстве фталевого ангидрида и для синтеза.
XVI. ПРОИЗВОДСТВО ВЫСОКОПРОЦЕНТНОГО АНТРАЦЕНА
16.1. Характеристика сырья
Сырьем для получения антрацена, карбазола и фенантрена служит сырой антрацен, полученный при кристаллизации I антраценовой фракции. Он представляет собой смесь антрацена, карбазола, фенатрена, их гомологов и других высококипящих ароматических соединений. Такая смесь не может быть использована как сырье для органического синтеза. Главные компоненты сырого антрацена имеют вполне определенную ценность для промышленности органического синтеза.
Сырой антрацен – это твердый маслянистый продукт, содержащий, % (по массе): антрацена 18–26, карбазола до 30, фенантрена около 30, каменноугольных масел и высококипящих продуктов 25–50.
Содержащиеся в сыром антрацене примеси – многоядерные соединения (выкипающие выше 360°С) – затрудняют процессы получения антрацена и других компонентов особо глубокой степени очистки.
Антрацен представляет собой моноклинические бесцветные листочки. Он хорошо растворяется при температуре 50–100°С в сольвенте, тяжелом бензоле, в легких и тяжелых пиридиновых основаниях. Очищенный антрацен используется в основном для производства антрахинона, который применяют для синтеза особо прочных протравных, кислотных и кубовых красителей для крашения синтетических волокон. Алкилированием антрацена получают масла специального назначения.
Карбазол (дибензопиррол) представляет собой бесцветные листочки, хорошо растворимые в тяжелых пиридиновых основаниях при температуре 80–100°С, в ацетоне и других растворителях.
Карбазол в отличие от антрацена и фенантрена проявляет кислые и основные свойства и при определенных условиях вступает в реакцию с кислотами и щелочами, склонен к реакциям сополимеризации с ненасыщенными соединениями и реагирует с альдегидами.
На этих свойствах карбозола основываются те методы разделения сырого антрацена, по которым либо сначала удаляют фенантрен (растворителями), а затем разделяют антрацен и корбазол, либо сначала удаляют корбазол (химическим способом), а затем разделяют антрацен и фенантрен.
Карбазол используется для производства красителей, некоторых инсектицидов (пирозан) и пластасс, карбазол-формальдегид-ных смол и сополимерных карбазол-инден-кумароновых смол. Фенантрен представляет собой бесцветные моноклинические лепесточки. Он значительно лучше антрацена и карбазола растворим в бензоле, толуоле, сольвентах I и II, в тяжелом бензоле, легких и тяжелых пиридиновых основаниях. Фенантрен является исходным сырьем для получения дифеновой кислоты, фенантрен-формальдегидных смол, фенантрахинона и других веществ.
Выделение из сырого антрацена индивидуальных компонентов основано на их различии в растворимости или отношении к реагентам и к процессу ректификации.
Известен ряд методов разделения сырого антрацена, которые предусматривают либо комплексное использование компонентов (антрацена, карбазола, фенантрена), либо выделение только антрацена и использование остатка в производстве сажи, дорожных дегтей и т.д.
Последние методы можно разделить на группы: 1) обработка антрацена селективными растворителями; 2) разделение антрацена химическим путем; 3) выделение компонентов из сырого антрацена с помощью ректификации при нормальном и пониженном давлении.
Практическое применение получили методы, основанные на выделении компонентов путем кристаллизации из растворителей и калиплавление.
Из других методов получения технического антрацена известны очистка жидкой сернистой кислотой, жидким аммиаком, оксидами азота, каталитическим окислением.
16.2. Технология получения 93%-ного антрацена
Технология выделения антрацена из сырого антрацена, разработанная УХИНом и запроектированная Гипрококсом, основана на различии растворимости основных компонентов сырого антрацена в ацетоне.
Ацетон как растворитель имеет ряд преимуществ: обладает достаточно высокой селективностью, имеет низкую температуру кипения и малую теплоту испарения, легко доступен, дешев и относительно малотоксичен, легче подвергается регенерации.
Сырьем для процесса служит сырой антрацен, содержащий антрацена 21–26%. Процесс получения концентрированного антрацена проводят в три стадии: первое и второе обогащение антрацена осуществляется из маточного раствора, третье – ацетоном. На каждой стадии процесса обогащения антрацена осуществляются растворение антрацена при 30 и 50°С; кристаллизация при охлаждении до 30°С с декантацией части раствора; интенсивное перемешивание кристаллизованной массы и фугование.
На рис. 29 приведена принципиальная технологическая схема производства 93%-ного антрацена.
Сырой антрацен, содержащий не менее 26% антрацена, со склада (после взвешивания) поступает в нижние аппараты для растворения сырого антрацена 1. В этих аппаратах сырой антрацен растворяется вторым маточным раствором, который подается из сборников 14 насосом 23. В аппаратах поддерживается температура 30°С. Из нижних аппаратов 1 образовавшаяся суспензия насосами 23 подается в верхние аппараты для растворения сырого антрацена 2, где поддерживается температура 50°С. Из аппаратов 2 суспензия поступает в кристаллизаторы первой ступени обогащения 3, где охлаждается до 30°С с последующей декантацией части раствора. Декантированный раствор из кристаллизаторов перетекает в сборники третьего маточного раствора 6, а сгущенная суспензия поступает в мешалки центрифуг 4, а затем в центрифуги первой стадии обогащения 5. Маточный раствор В из центрифуг перетекает в сборники 6. Отфугованный первично обогащенный антрацен из центрифуг смывается первым маточным раствором по желобу в нижние аппараты 9 для растворения второй стадии обогащения.
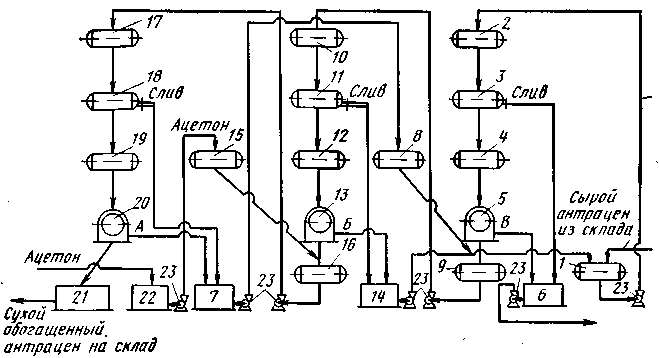
Рис. 29. Принципиальная технологическая схема производства 93%-ного антрацена
1, 2– нижний и верхний аппараты для растворения сырого антрацена; 3 – кристаллизатор; 4, 5, 13, 20 – центрифуги; 6 – сборник маточного раствора; 7, 14 – сборники; 9, 16 – нижние аппараты; 10, 17 – верхние аппараты; 11, 12, 18 – кристаллизаторы; 12, 19 – мешалки; 15 – напорный бак; 22 – сборник; 23 – насосы
Отфугованный антрацен второй стадии обогащения поступает в нижние аппараты для растворения третьей ступени обогащения 16. Схема третьей стадии обогащения аналогична первой и второй, т.е. суспензия второго обогащения после ее растворения ацетоном, который поступает из напорных баков 15, насосами 23 подается в верхние аппараты для растворения третьей стадии обогащения 17. Ацетон в напорные баки 15 подается насосами 23 из сборников 22.
Суспензия антрацена третьей стадии обогащения из верхних аппаратов 17 поступает в кристаллизаторы 18, мешалки 19 и центрифуги 20. Слив из кристаллизаторов 18 и первый маточный раствор А после центрифуг 20 самотеком перетекают в сборники 7.
Отфугованный чистый антрацен третьей стадии обогащения направляется на сушилку, откуда конвейером передается в бункер для расфасовки, где установлены весы ДСА-50. Погрузку мешков в вагоны и складирование их производят автопогрузчиком.
Из аппаратов 9 насосами 23 антрацен первой стадии обогащения подается в верхние аппараты 10 для растворения второй стадии обогащения при температуре 50°С. Затем, как и в первой стадии обогащения суспензия поступает в кристаллизаторы 11, мешалки 12 и центрифуги 13. Раствор из кристаллизаторов 12 и второй маточный раствор Б из центрифуг 13 перетекают в сборники 14.
Все оборудование цеха находится под «азотным дыханием», в систему которого азот подают через работающие центрифуги, что обеспечивает безопасность их эксплуатации. Для возврата ацетона в систему и уменьшения его потерь предусмотрена на кристаллизаторах и других аппаратах с ацетоном установка обратных холодильников, охлаждаемых рассолом. Регенерация сеток центрифуг осуществляется поглотительным маслом. Маточный раствор после первого обогащения для регенерации ацетона подвергается дистилляции в колонне.
Продуктом процесса является 93–94%-ный антрацен. Степень извлечения составляет 52–54% от ресурсов.10>