Учебное пособие по дисциплине «Ремонт автомобилей»//Составитель: В. П. Шеянов. Омск: Омгкпт, 2006. с. 136
Вид материала | Учебное пособие |
СодержаниеДля очистки погружением Механическая очистка – Комбинированный метод – Старую краску Очистка от консервационных смазок |
- Учебное пособие Омск 2004 удк 681., 1015.29kb.
- Методические указания по выполнению курсового проекта по дисциплине «Ремонт автомобилей», 1848.24kb.
- Учебное пособие Составитель Шершова Л. В. Томск 2006 удк, 674.1kb.
- Учебное-методическое пособие омск 2008 Печатается по решению, 602.49kb.
- Учебное пособие Омск Издательство Омгту 2008, 2846.95kb.
- Учебное пособие Г. П. Синицына Воспитание современного школьника Омск 1999, 1929.66kb.
- Государственное образовательное учреждение среднего профессионального образования, 839.78kb.
- Учебное пособие Ульяновск 2010 удк 004. 8(075. 8) Ббк 32. 813я73, 1559.86kb.
- Учебное пособие для вузов Составитель Т. А. Тернова, 241.22kb.
- Учебное пособие для вузов Составитель Т. А. Тернова, 241.72kb.
Учебные вопросы:
1. Значение моечно-очистных работ.
2. Мойка и обезжиривание объектов ремонта.
3. Очистка деталей от нагара, накипи, коррозии и старой краски.
4.Организация рабочих мест и техника безопасности (отработать самостоятельно, (1), с.49-50).
1. Моечно-очистные работы представляют собой ряд многостадийных операций мойки и очистки объектов ремонта, способствующих повышению качества ремонта, обеспечению необходимых санитарно-гигиенических условий работы разборщиков и повышению производительности их труда.
Особенно велико влияние моечно-очистных работ на качество и ресурсы отремонтированных автомобилей и их агрегатов (ресурс отремонтированных агрегатов увеличивается на 25-30% и на 15-20% повышается производительность труда разборщиков).
* Вычертить на доске и дать под запись Рис. 7.1. «Виды загрязнений объектов ремонта», (1), с. 41.
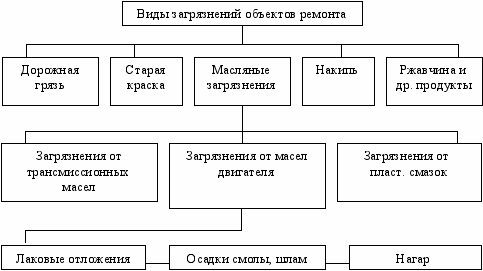
Моечно-очистные работы можно разделить на следующие стадии:
- мойка шасси;
- мойка подразобранных агрегатов;
- мойка и очистка деталей.
* (Струйные моющие машины; мойка погружением) – пояснить по плакату их устройство и принцип действия.
2. Сущность процесса мойки и обезжиривания состоит в удалении загрязнений с поверхностей деталей и переводе их в моющий раствор в виде растворов и дисперсий, для этого на АРП прим. моющие средства и специальное оборудование (смс – лабомид и растворы каустика и кальцинированной соды).
Существует большое количество моющих растворов для обезжиривания деталей:
Компоненты | Содержание компонентов в растворе для мойки деталей, % | ||||
Из чугуна и стали | Из сплавов алюминия | ||||
1 | 2 | 3 | 1 | 2 | |
Кальцинированная сода | 5,50 | - | 10,00 | - | 1,00 |
Компоненты | Из чугуна и стали | Из сплавов алюминия | |||
1 | 2 | 3 | 1 | 2 | |
Каустическая сода | 0,75 | 2,00 | 00,00 | 0,10-0,20 | - |
Тринатрийфосфат | 1,00 | 5,00 | - | - | - |
Нитрат натрия | - | - | - | 0,15-0,25 | - |
Жидкое стекло | - | 3,00 | - | - | - |
Хромчик | - | - | 0,10 | - | 0,55 |
Хозяйственное мыло | 0,15 | - | - | - | - |
Силикат натрия (жидкое стекло).
Состав СМС
Компоненты СМС | Марка и состав МС, в % | ||||
МС-6 | МС-8 | МС-15 | Лабомид 101 | Лабомид 203 | |
Сода кальцинированная | 40 | 38 | 44 | 50 | 50 |
Триполифосфат натрия | 25 | 25 | 24 | 30 | 30 |
Метасиликат натрия | 29 | 29 | 28 | 16,5 | 10 |
Синтанол ДС-10 | 6 | - | - | 3,5 | 8 |
Синтамид - 5 | - | 8 | - | - | - |
Алкилсульфаты | - | - | - | - | 2 |
Оксифос Б | - | - | 8 | - | - |
Растворы моющих средств лабомид–203, МС-8, МС-15 в 3-4 раза эффективнее растворов каустической соды.
Для устранения пенообразования в раствор следует вводить 0,2-0,3% пеногасящих добавок (ДТ, керосин, Уайт-спирит) к объему раствора. Пеногасители вводят по мере образования пены.
Для очистки погружением рекомендуется лабомид – 203, МС-8 и МС-15 с концентрацией 20-30 кг/м³ и tº = 80-100 ºC.
Для удаления асфальтосмолистых отложений с деталей можно использовать растворители и растворяющие эмульсирующие средства (РЭС).
Хлорированные | Ароматические | Предельные |
тетрахлорэтилен, трихлорэтилен, хлористый метилен, дихлорэтан | ксилол | дизельное топливо, керосин, бензин, Уайт-спирит |
3. Очистка деталей от нагара, накипи и продуктов коррозии производится механическим, термохимическим и комбинированным методами.
Механическая очистка – металлические щетки, косточковая крошка, металический песок, гидропесконструйная обработка.
Термохимический метод – очистка деталей в щелочном растворе
– tº = 400±20 ºC;
65% - едкого натрия,
30% - азотнокислого натрия,
5% - хлористого натрия.
Для очистки применяются установки ОМ-944 и ОМ-5458.
Установка состоит из 4-х ванн:
1 – щелочной раствор 5-10 мин. => разрушение загрязнений;
2 – проточная вода => перепад температур, бурное парообразование, способствуют рыхлению остатков нагара, накипи;
3 – кислотная обработка (травление) => осветление поверхности деталей и нейтрализация остатков щелочи => фосфорная кислота 85кг/м³ + хромовый ангидрид
tº = 30±5 ºC;
4 – горячая вода в чистой ванне.
Общее время 20-25 минут.
Комбинированный метод – ультразвуковой, виброабразивный и метод с использованием электрогидравлического эффекта.
Для мойки точных деталей (подшипники, плунжерные пары) применяют бензин с последующей промывкой их веретеным маслом.
При очистке деталей электрооборудования используют керосин и бензин, заменителем может служить раствор:
40% сульфонефтяных кислот;
8% минеральных масел;
1% серной кислоты,
остальное вода, прим. только при механизированной мойке, не подогревают, добавляют до 1% хромника для предохранения деталей от коррозии.
Накипь удаляют раствором тринатрийфосфата (3-5 кг/м³ воды) и 8-10% соляной кислоты. Для предохранения деталей от коррозии добавляют 3-4 г/л технического уротропина. tº раствора 50-60 ºС, продолжительность мойки 50-70 мин.
Старую краску удаляют обработкой щелочным раствором каустической соды (80-100 кг/м³) при tº 80-90 ºС. Время обработки 60-90 мин. Затем промывают горячей водой в установках ванного или струйного типа. Завершают пассированием поверхности деталей в ванне с раствором нитрата натрия (5 кг/м³) при tº = 50-60 ºС.
Можно удалять краску смывками и растворителями, скорость 5-30 мин., расход 0,15-0,25 кг/м².
Растворители Р-4, № 646, 647.
Очистка от консервационных смазок – лабомид 101 =>10 кг/м³, tº = 80-90 ºС.
Очистку деталей от технических загрязнений (пыль, стружка, смазочная эмульсия) ведут в машинах струйного типа под давлением 0,4-0,6 МПа, тринитрофосфат или нитрат натрия (3-5 кг/м³), при tº = 75-85 ºС.
Поддерживание моющей способности раствора зависит от контроля за его концентрацией, производится по плотности раствора с помощью индикаторной бумаги или методом титрования.
Качество моечно-очистных работ оценивается степенью удаления всех загрязнений. Контроль осуществляется визуально (осмотром), протиранием бумагой или салфетками, проверкой на смачивание, освещением ультрафиолетовыми лучами, взвешиванием и т.п.
Д/з: (1) Гл. 7, с.41-50, Рис. 7.1.
(2) Гл. 5, с.52-82, Рис. 5.3., Табл. 5.2.
ТЕМА: «Дефектация и сортировка деталей».
Учебные вопросы:
1. Сущность процесса дефектации и сортировки деталей.
2. Характерные дефекты деталей.
3. Технические условия на дефектацию деталей.
4. Методы контроля.
5. Сортировка деталей по маршрутам восстановления.
6. Коэффициенты годности, сменности и восстановления деталей.
1. Под дефектами детали понимают всякие отклонения ее параметров от величины установленных ТУ или рабочим чертежом.
Основными задачами дефектации и сортировки является:
- контроль деталей для определения их технического состояния;
- сортировка деталей на три группы: годные для дальнейшего использования, подлежащие восстановлению и негодные;
- накопление информации о результатах дефектации и сортировки с целью использования ее при совершенствовании технологических процессов и для определения коэффициентов годности, сменности и восстановления деталей;
- сортировка деталей по маршрутам восстановления.
Дефектацию деталей производят путем их внешнего осмотра, а также с помощью специального инструмента, приспособлений, приборов и оборудования. Результаты фиксируют путем маркировки деталей краской:
- зеленой – годные;
- красной – негодные;
- желтой – требующие восстановления.
2. К числу наиболее распространенных дефектов деталей относятся следующие:
- изменение размеров и геометрической формы рабочих поверхностей;
- нарушение точности взаимного расположения рабочих поверхностей на детали;
- механические повреждения;
- коррозийные повреждения;
- изменение физико-механических свойств материала детали.
1) Изменение размеров рабочих поверхностей деталей происходит в результате их изнашивания. При неравномерном изнашивании возникают различные погрешности в геометрической форме рабочих поверхностей деталей в виде овальности, конусности и т.п. (гильзы цилиндров и коленный вал).
2) Нарушение точности взаимного расположения рабочих поверхностей проявляется в виде нарушения расстояния между осями цилиндрических поверхностей, и осей и плоскостей, несоосности цилиндрических поверхностей (несоосность (биение) коренных шеек). Причиной появления этих дефектов является: неравномерный износ рабочих поверхностей; внутренние напряжения, возникающие в деталях при их изготовлении; остаточная деформация от чрезмерных эксплуатационных нагрузок на детали и др.
3) Механические повреждения в деталях возникают при воздействии на них в процессе эксплуатации нагрузок, превышающих допустимые, а также вследствие усталости материала (трещины, пробоины, изломы и деформации – изгиб, скручивание, коробление).
4) Коррозийные повреждения образуются на деталях результате химического или электрохимического взаимодействия металла с коррозийной средой и появляются в виде сплошных окисных пленок или в виде местных повреждений (пятен, раковин, точек).
5) Изменение физико-механических свойств материала деталей в процессе эксплуатации автомобилей выражается наиболее часто в снижении твердости и упругих свойств.
3. При дефектации (Д) и сортировке (С) деталей руководствуются ТУ, которые содержатся в руководстве по КР. ТУ на дефектацию деталей составляются в виде карт, которые по каждой детали в отдельности содержат следующие сведения:
- общие сведения о детали;
- перечень возможных ее дефектов;
- способы выявления дефектов;
- допустимые без ремонта размеры детали;
- рекомендуемые способы устранения дефектов.
Общие сведения о детали включают в себя:
- эскиз детали с указанием мест расположения дефектов;
- основные размеры;
- материал;
- твердость основных поверхностей.
Все эти сведения могут быть получены из рабочего чертежа.
Наибольшую сложность при разработке ТУ на дефектацию деталей представляет определение величины допустимого размера детали, он определяется из условия известной величины допустимого износа,
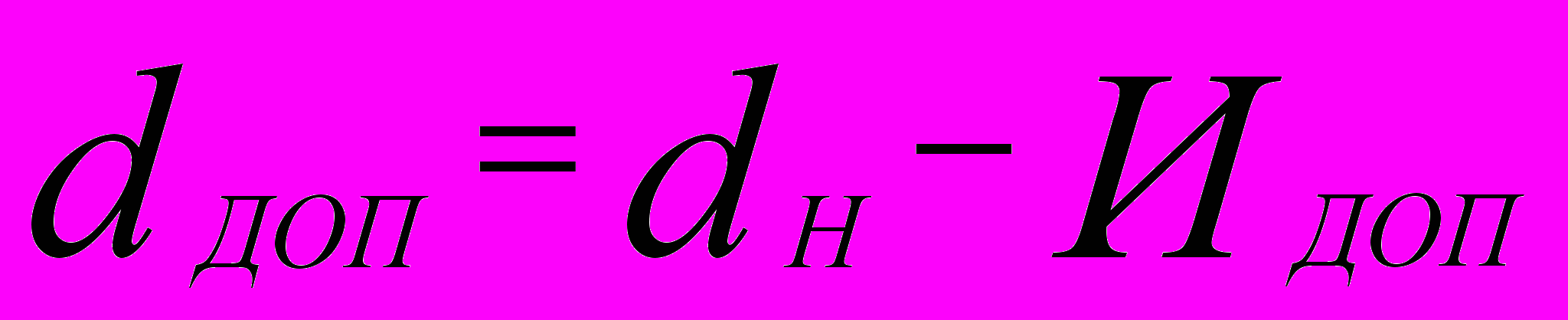
где:
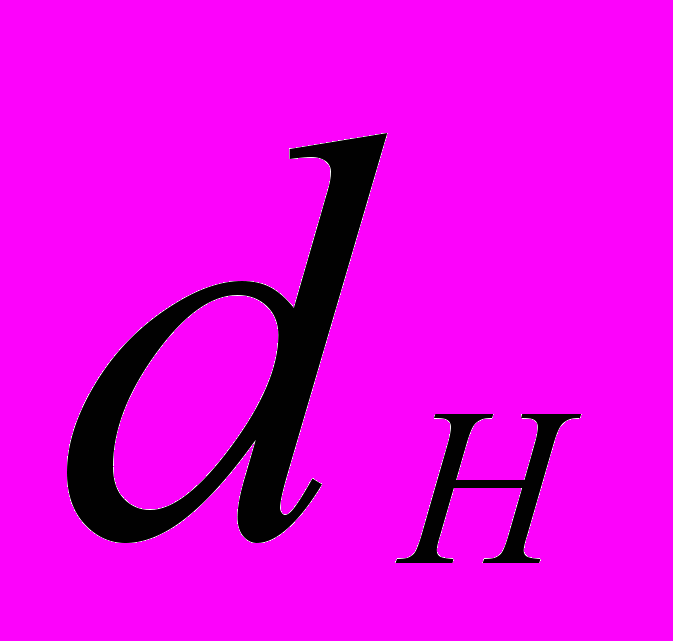
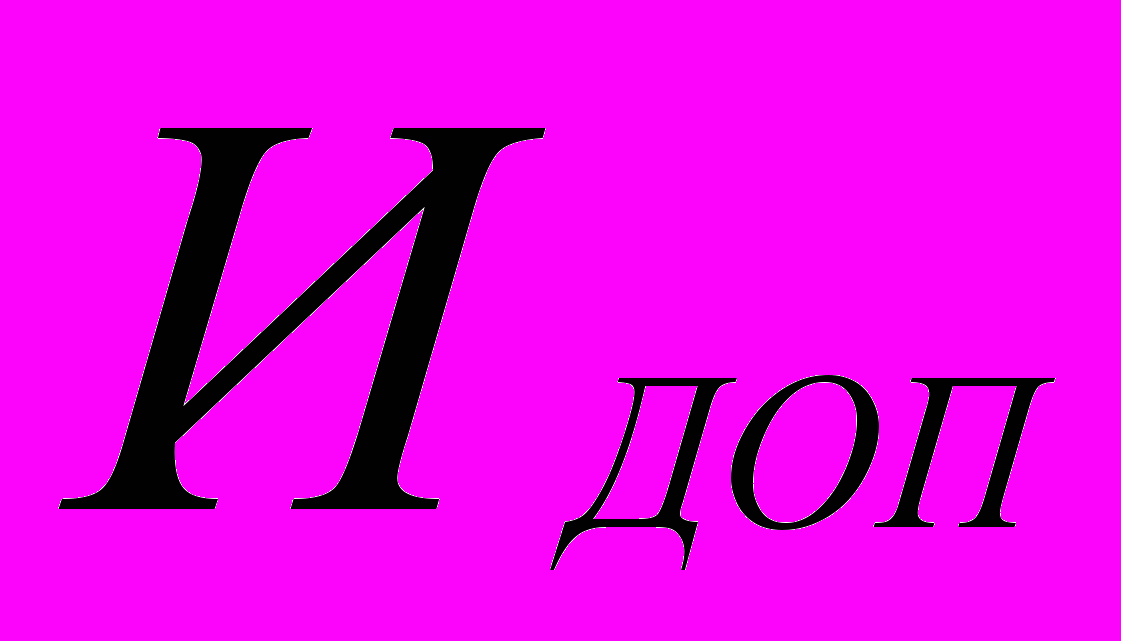
Допустимым износом детали называют такой ее износ, при котором деталь будучи установленной на автомобиль при КР, и ее износ не превысит предельного.
Предельным износом называют такой износ детали, при котором ее дальнейшее использование невозможно. Деталь, достигшую предельного износа, восстанавливают или заменяют новой.

где:
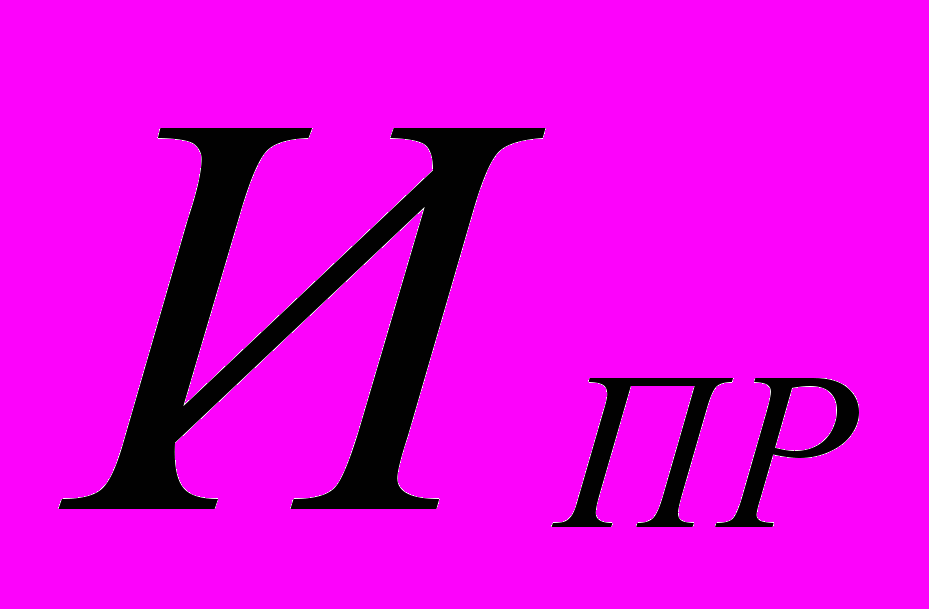
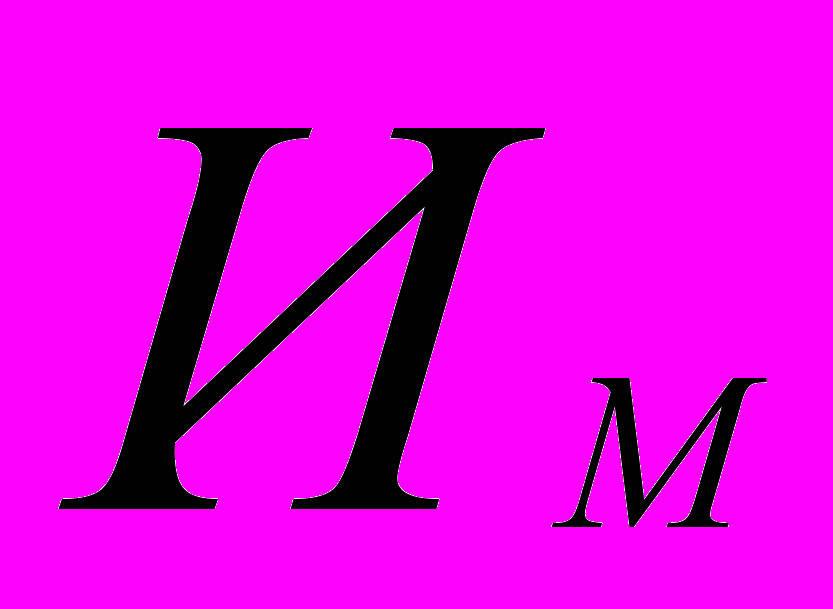
Величину износа детали за межремонтный пробег (
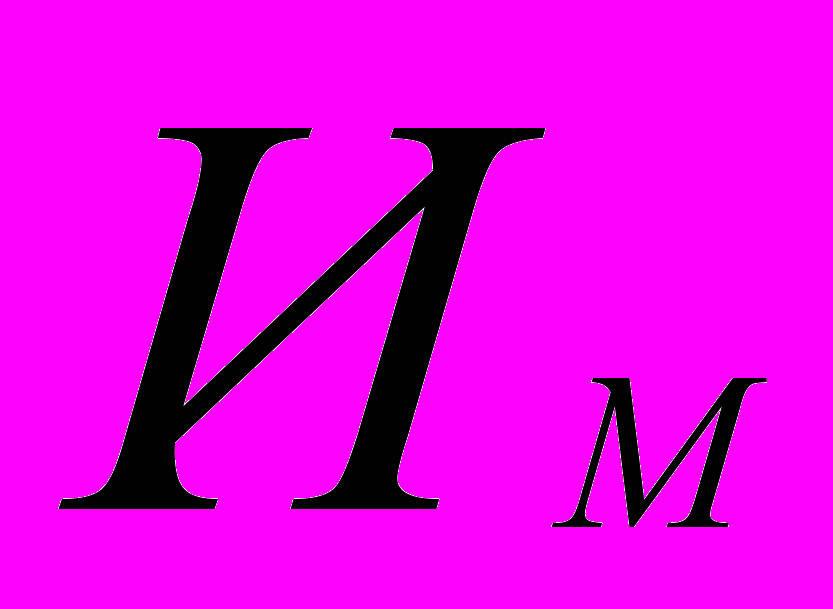
4. Порядок дефектации:
- внешний осмотр деталей с целью обнаружения повреждений, видимых невооруженным глазом (трещины, пробоины, излом);
- проверка на специальных приспособлениях для обнаружения дефектов, связанных с нарушением взаимного расположения рабочих поверхностей и физико-механических свойств материала;
- контроль на отсутствие скрытых дефектов (невидимых трещин, внутренних пороков);
- контроль размеров и геометрической формы рабочих поверхностей детали.
1) Контроль взаимного расположения рабочих поверхностей:
- контроль несоосности шеек валов;
- контроль неперпендикулярность фланца к оси вала;
- контроль несоосности отверстий;
- контроль межцентрового расстояния и непараллельности осей отверстий;
- контроль неперпендикулярности осей отверстий к плоскости.
2) Контроль нарушения физико-механических свойств материала деталей, может проявляться в виде изменения твердости или жесткости детали (рессоры, пружины) – выполняется универсальными приборами для определения твердости.
3) Контроль скрытых дефектов, определяется следующими методами: опрессовка, красок, люминесцентный, намагничивания, ультразвуковой.
Метод опрессовки применяется для обнаружения скрытых дефектов в полых деталях, производят водой (гидравлический) и воздухом (пневматический).
Метод красок основан на свойстве жидких красок к взаимной диффузии.
Люминесцентный метод основан на свойстве некоторых веществ светиться при облучении их ультрафиолетовыми лучами.
Метод магнитной дефектоскопии применяется в деталях изготовленных из ферромагнитных материалов (сталь, чугун). Деталь в начале намагничивают.
Ультразвуковой метод основан на свойстве ультразвука проходить через металлические изделия и отражаться от границы двух сред, в том числе и от дефекта.
4) Контроль размеров и формы рабочих поверхностей деталей – выполняется универсальным инструментом, измерительным: микрометры, штангенциркули, индикаторные нутромеры и др.
5. Сортировка по маршрутам восстановления – является одной из задач дефектации.
Маршруты восстановления деталей разрабатываются заблаговременно.
Чем сложнее деталь, тем количество возможных дефектов на ней будет больше.
При определении маршрутов восстановления деталей необходимо руководствоваться следующими основными принципами:
1 принцип – сочетание дефектов в каждом маршруте должно быть действительным (реально существующем). Действительное сочетание дефектов устанавливают путем проведения специальных исследований, при которых определяеться сочетание дефектов на большом количестве деталей одного наименования, выявляют повторяющиеся сочетания и частоту их наблюдения;
2 принцип – количество маршрутов восстановления каждой детали должно быть минимальным 2-3, а для сложных деталей не > 5;
3 принцип – необходимо учитывать применяемый способ восстановления;
4 принцип – восстановление детали по данному маршруту должно быть экономически целесообразным. Если затраты на восстановление детали, отнесенные к единице ее наработки, будут меньше соответствующих затрат на изготовление детали, то восстановление детали по данному маршруту считается целесообразным.
При дефектации деталей контролер определяет действительное сочетание дефектов по каждой из деталей и сортирует их по маршрутам восстановления. Результаты сортировки деталей по маршрутам восстановления отмечают краской на самих деталях (указывается номер маршрута).
6. Результаты сортировки деталей на группы после статистической обработки большого количества дефектных ведомостей позволяют определить очень важные для организации ремонта автомобилей показатели:
к
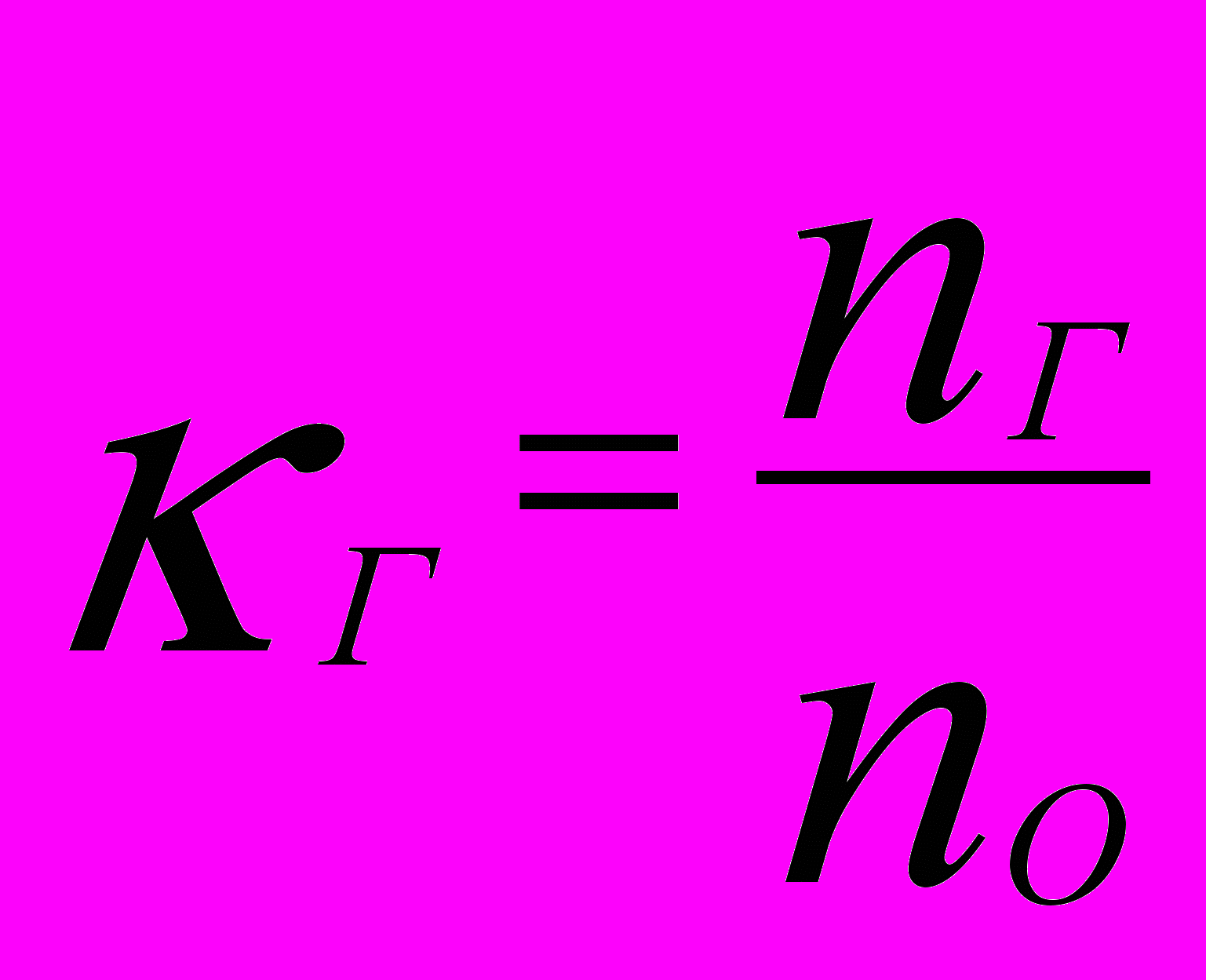
к
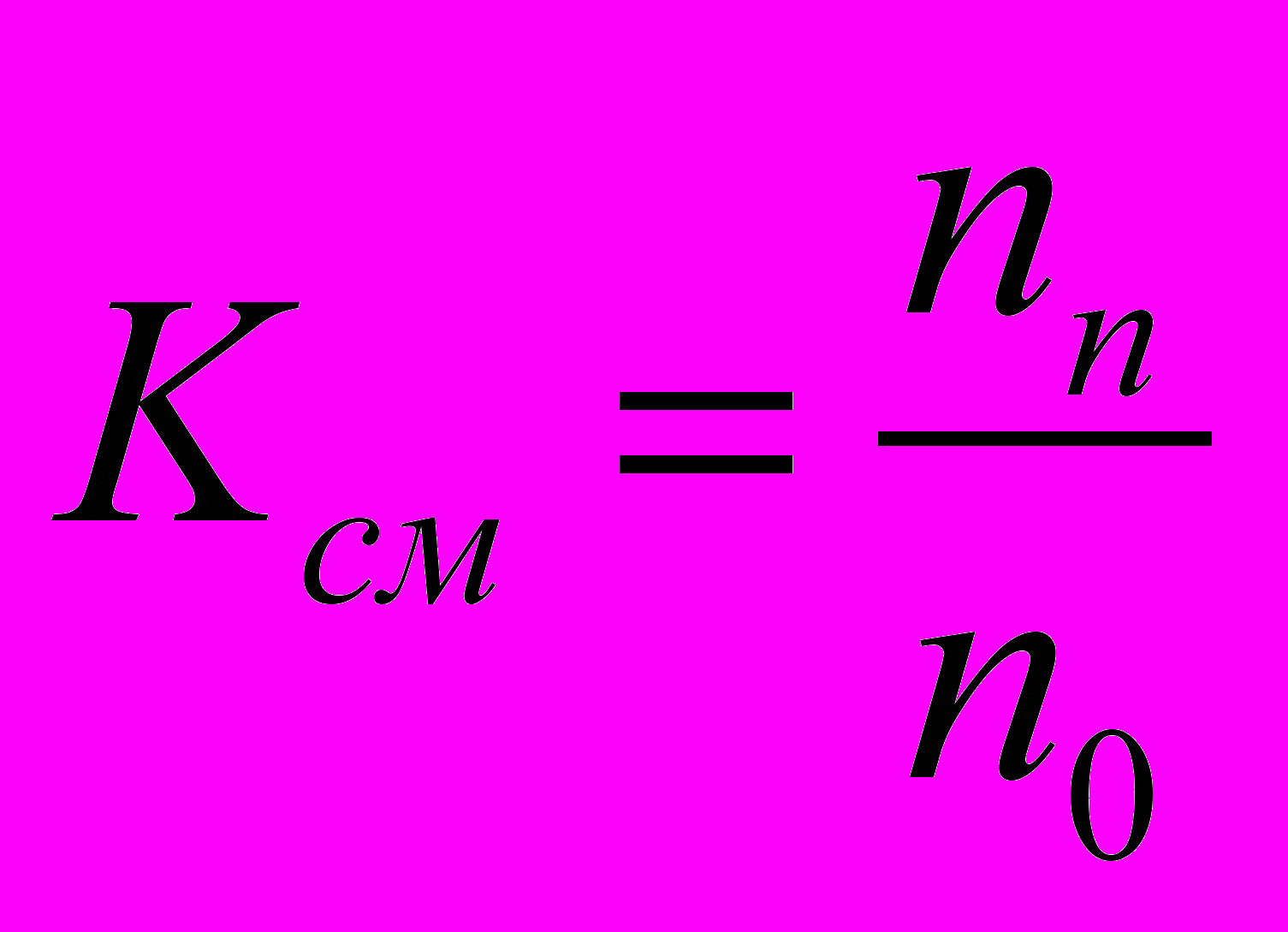
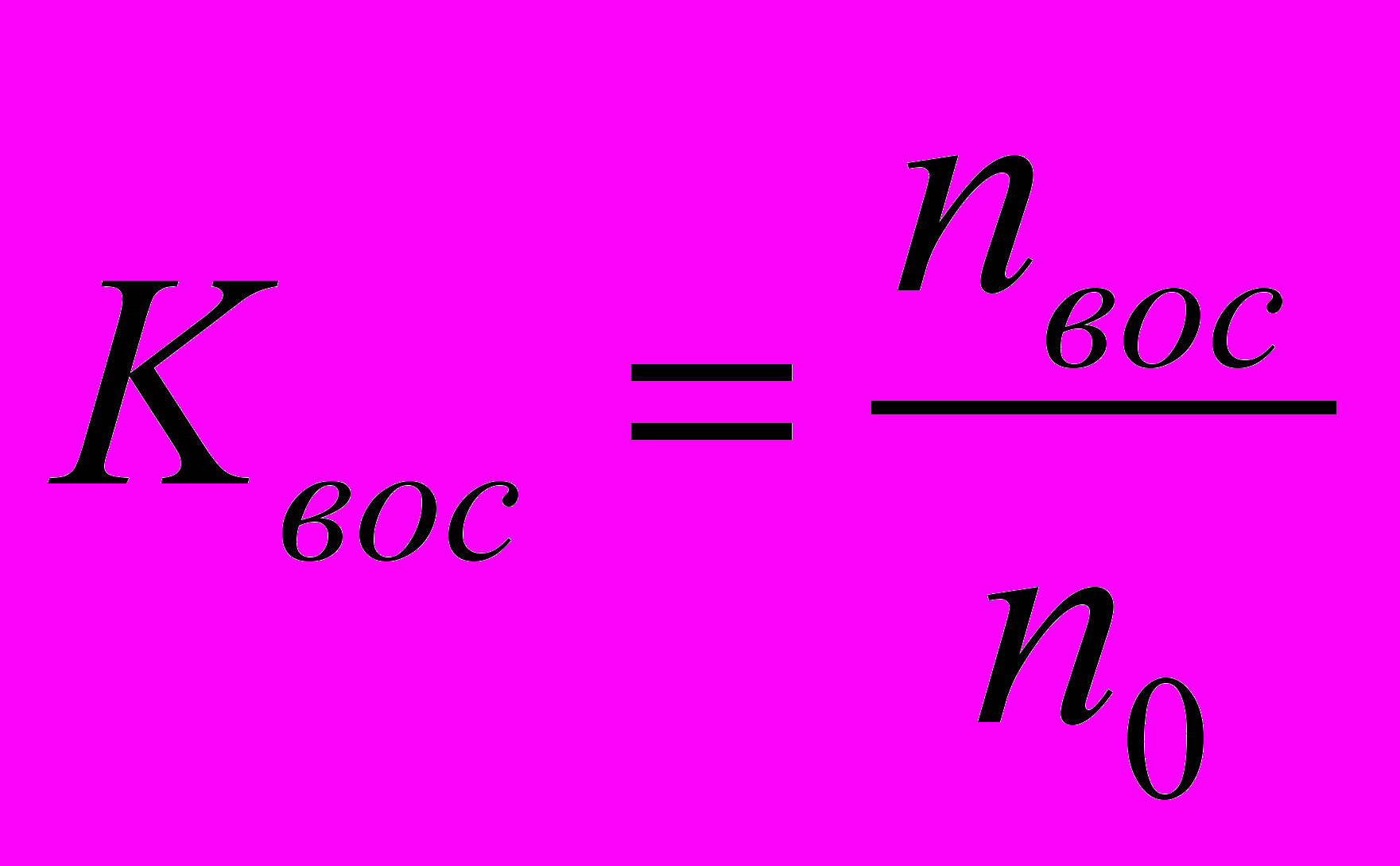
коэффициент восстановления показывает какая часть деталей данного наименования требует восстановления.
Значение этих коэффициентов позволяет более точно планировать потребность АРП в запасных частях и определяет объем работ участков восстановления деталей.
Обработка информации о сортировке деталей по маршрутам восстановления позволяет также уточнить маршрутные коэффициенты восстановления деталей, т.к.
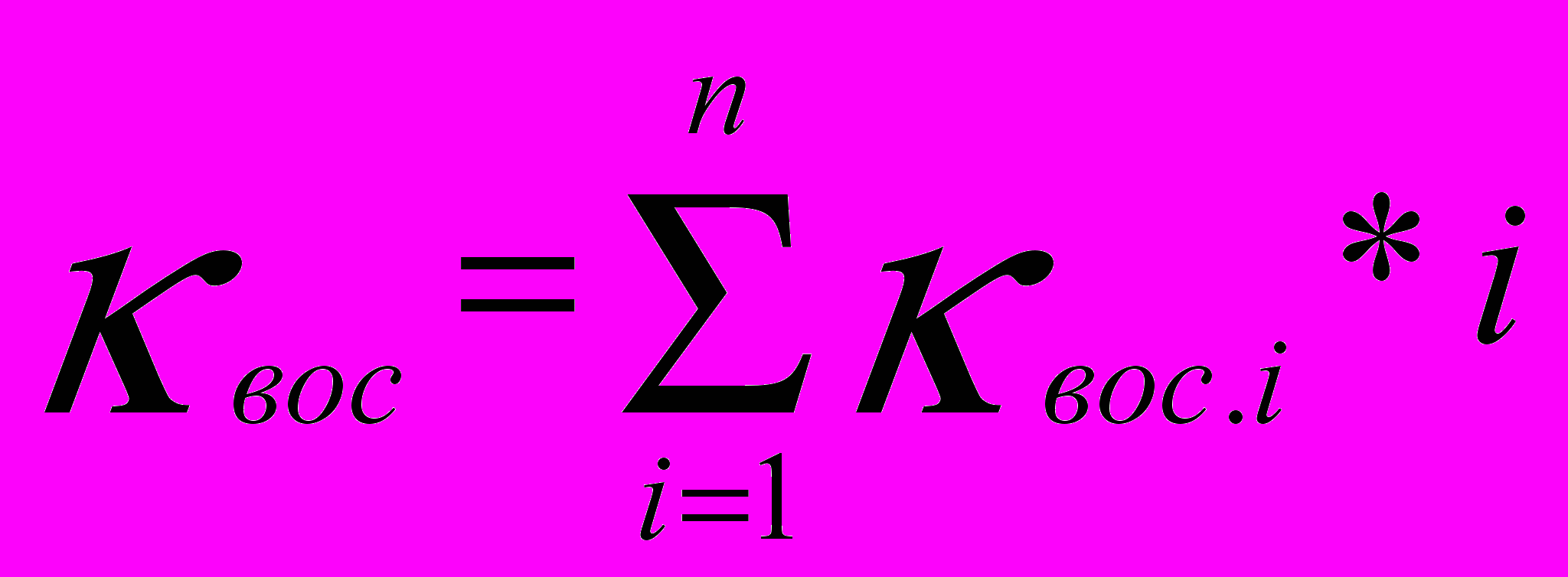
где:
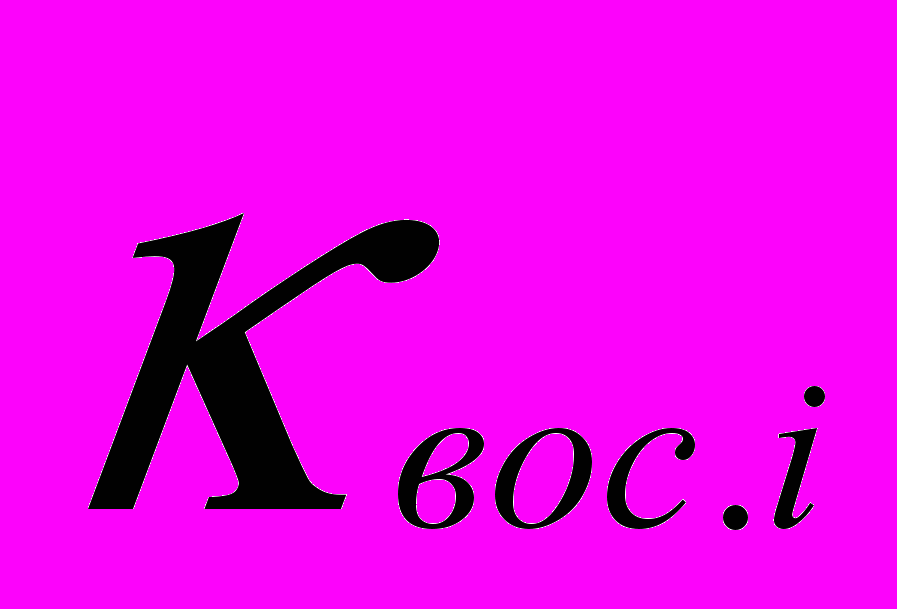
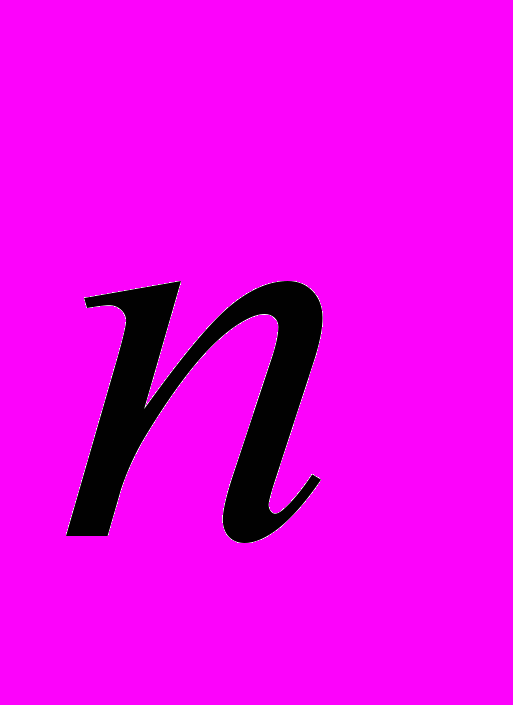
Значение маршрутных коэффициентов позволяет определить объем работ по каждому маршруту и, следовательно, планировать загрузку оборудования на участках восстановления деталей.
Д/з, (1) Гл. 8, с.50-62, Рис. 8.2, 8.3, 8.4, - 8.8, 8.13.
(2) Гл. 6, с.82-111, Табл. 6.1.