Б. А. Сентяков Официальные оппоненты: доктор технических наук, профессор
Вид материала | Автореферат |
- Г. Г. Яновский Официальные оппоненты: доктор технических наук, профессор, 614.77kb.
- Разработка системы управления инновационными проектами в образовании на основе оптимизационных, 229.88kb.
- Лазерная фотодинамическая терапия ожоговых ран (экспериментальное исследование) 14., 295.89kb.
- Ветеринария. – 2011. №1(17). – С. 20-21 Нужен ли нам сегодня новый аграрно-технический, 46.59kb.
- Phodopus, 940.53kb.
- В педагогическом взаимодействии, 811.25kb.
- Ч. Г. Гусейнов Официальные оппоненты доктор философских наук, профессор, 305.07kb.
- Прагматика языка туристической рекламы, 1403.92kb.
- Синтез, свойства и биологическая активность производных 2-хлорникотинонитрилов, 264.36kb.
- Модели регионализма и регионализации восточной азии, 1934.71kb.
На правах рукописи
УДК 621.002.5
Святский Владислав Михайлович
РАЗРАБОТКА ПРОЦЕССА И ОБОРУДОВАНИЯ ДЛЯ ПОЛУЧЕНИЯ ВОЛОКНИСТЫХ МАТЕРИАЛОВ ВЕРТИКАЛЬНЫМ РАЗДУВОМ ИСТЕКАЮЩЕЙ ПОД ГИДРОСТАТИЧЕСКИМ ДАВЛЕНИЕМ СТРУИ ТЕРМОПЛАСТА
Специальность 05.02.13 – Машины, агрегаты и процессы (машиностроение)
АВТОРЕФЕРАТ
диссертации на соискание ученой степени
кандидата технических наук
Ижевск - 2011
Работа выполнена в ГОУ ВПО «Ижевский государственный технический университет»
Научный руководитель: доктор технических наук, профессор
Б. А. Сентяков
Официальные оппоненты: доктор технических наук, профессор
С. Н. Храмов
кандидат технических наук
А. Е. Причинин
Ведущая организация: Институт прикладной механики УрОРАН, г.Ижевск
Защита состоится «5» мая 2011 года в 16-00 часов на заседании диссертационного совета Д 212.065.03 ГОУ ВПО «Ижевский государственный технический университет» по адресу 426069, г. Ижевск, ул. Студенческая, 7.
Отзыв на автореферат в двух экземплярах, заверенных гербовой печатью, просим направить на имя учёного секретаря диссертационного совета.
С диссертацией можно ознакомиться в библиотеке ГОУ ВПО «Ижевский государственный технический университет» по адресу: 426069, г.Ижевск, ул. Студенческая, дом 7, к. 1.
Автореферат разослан « 5 » апреля 2011г.
Ученый секретарь диссертационного совета
доктор технических наук, профессор Ю.В. Турыгин
ОБЩАЯ ХАРАКТЕРИСТИКА РАБОТЫ
Актуальность темы. Технический прогресс в машиностроении определяется качеством машин и агрегатов, реализующих различные технологические процессы. Качество и себестоимость производства изделий машиностроения зависит от материалов, из которых они изготовлены.
В машиностроении используются волокнистые синтетические материалы для тепло- и звукоизоляции различных машин и агрегатов, например, транспортных средств и летательных аппаратов, в конструкциях фильтров для очистки газов и жидкостей от инородных частиц в металлорежущих станках. Они обладают высокой прочностью, стойкостью к агрессивным воздействиям, хорошим фильтрующим свойством, низким влагопоглощением. Исходным сырьем для их производства являются термопластичные пластмассы, например, полиэтилентерефталат.
Наибольший интерес среди известных технологических процессов получения волокнистых материалов из термопластов представляет процесс, суть которого заключается в раздуве истекающей из плавильного агрегата струи расплавленного термопласта потоком сжатого воздуха. Известен вариант исполнения плавильного агрегата в виде экструдера, недостатком которого являются сложность конструкции и большие металло- и энергоемкость. Наиболее простую конструкцию имеют плавильные агрегаты, в которых истечение струи расплавленного материала происходит под действием гидростатического давления. Предварительные исследования процесса получения волокнистых материалов с применением таких плавильных агрегатов подтвердили его положительные качества, в том числе уменьшение материальных и энергетических затрат на производство волокна по сравнению с традиционной технологией. Однако, такой процесс до сих пор не реализован в промышленных условиях.
С этой точки зрения разработка научных и методологических основ проектирования и создания новых процессов и агрегатов, для получения волокнистых материалов вертикальным раздувом струи расплавленного термопласта и создание в результате этого промышленных агрегатов, позволяющих сократить затраты на производство волокнистых синтетических материалов, обеспечивая при этом получение качественного материала с высокой производительностью, в настоящее время является актуальным.
Цель работы — разработка процесса и оборудования для производства волокнистых материалов из термопластов за счет практической реализации результатов теоретического и экспериментального исследования физико-механического процесса вертикального раздува истекающей из плавильного агрегата под действием гидростатического давления струи расплавленного термопласта потоком сжатого воздуха.
Задачи исследований:
1. Разработать метод расчета производительности плавильного агрегата для получения волокнистых материалов вертикальным раздувом истекающей под действием гидростатического давления струи расплавленного термопласта.
2. Исследовать закономерности процесса изменения температуры струи расплавленного полимера, при истечении ее из выходного отверстия плавильного агрегата определяющие качество получаемого материала.
3. Расчетными и экспериментальными методами определить рациональные параметры и режимы работы дутьевой головки с кольцевым сходящимся соплом для получения волокнистого материала вертикальным раздувом струи расплавленного термопласта.
4. Разработать опытно-промышленную установку и технические средства для реализации физико-механического процесса получения волокнистых материалов способом вертикального раздува истекающей из плавильного агрегата под действием гидростатического давления струи расплавленного термопласта.
5. Определить эксплуатационные свойства волокнистого материала, полученного вертикальным раздувом истекающей под действием гидростатического давления струи расплавленного термопласта.
Методы исследования. В работе реализованы теоретические и экспериментальные методы исследования. Теоретическое исследование процесса истечения струи расплавленного термопласта из плавильного агрегата под действием гидростатического давления выполнено на основе законов течения вязкой жидкости, в том числе, формулы Пуазейля и рекомендаций П.Ю.Апеля и С.Н.Дмитриева. Теоретическое исследование процесса охлаждения струи расплавленного термопласта выполнено на основе уравнения теплопроводности Фурье. Экспериментальное исследование дутьевой головки выполнено с применением теории планирования эксперимента, на специальных стендах с применением аттестованных приборов для измерения давления и расхода воздуха. При расчетах и обработке экспериментальных данных использовалась современная компьютерная техника.
На защиту выносятся:
1. Метод расчета производительности плавильного агрегата с истечением струи расплавленного материала под действием гидростатического давления при получении волокнистых материалов вертикальным раздувом такой струи потоком воздуха, основанный на использовании формулы Пуазейля для течения вязких жидкостей.
2. Закономерность изменения температуры струи расплавленного полимера, истекающей из плавильного агрегата под действием гидростатического давления, по ее длине.
3. Результаты расчета и экспериментальных исследований дутьевой головки с кольцевым сходящимся соплом для получения волокнистого материала способом вертикального раздува свободной струи расплавленного термопласта, позволяющие определить рациональные параметры ее проточной части.
4. Опытно-промышленная установка и технические средства для получения волокнистых материалов способом вертикального раздува истекающей под действием гидростатического давления струи расплавленного полиэтилентерефталата потоком воздуха, оснащенная плавильным агрегатом для плавления исходного сырья, автоматическим дозирующим устройством, дутьевой головкой с механизмом качания, вальцовым агрегатом и пневматическим устройство для измерения среднего диаметра элементарных волокон в процессе их производства.
5. Результаты определения эксплуатационных свойств волокнистого материала, полученного вертикальным раздувом истекающей под действием гидростатического давления струи расплавленного термопласта.
Научная новизна работы заключается в том, что:
- разработан новый метод расчета производительности плавильного агрегата для получения волокнистых материалов вертикальным раздувом струи расплавленного термопласта потоком воздуха с истечением струи из выходного отверстия плавильного агрегата под действием гидростатического давления, подтверждающий возможность использования различных модификаций формулы Пуазейля для определения расхода расплава при истечении его из плавильного агрегата;
- решена задача определения закономерности изменения температуры переменной по сечению струи расплавленного полимера, истекающей из плавильного агрегата под действием гидростатического давления;
- получены новые расчетные и экспериментальные данные, характеризующие эффективность работы дутьевой головки с кольцевым сходящимся соплом: рациональная величина кольцевого зазора В=0,5÷0,6 мм при среднем диаметре кольцевой щели 10 мм, центральный угол диффузора – 12 градусов, а рациональное отношение его длины к диаметру кольцевой щели – 1,8÷2,0, рациональное давление в кольцевой полости от 100 до 150 кПа при котором происходит деформирование струи расплавленного материала на элементарные струйки с последующим образованием штапельных волокон;
- разработан вальцовый агрегат, который защищен патентом РФ, дутьевая головка, оснащенная механизмом качания, пневматическое устройство для измерения среднего диаметра элементарных волокон, обеспечивающее погрешность измерения диаметра волокон в диапазоне от 10 до 100 мкм с погрешностью не более 9%;
- выявлены новые свойства волокнистого материала полученного способом вертикального раздува струи из расплавленного полиэтилентерефталата, которые позволяют расширить его область применения.
Достоверность и обоснованность полученных результатов подтверждается использованием при составлении математических моделей отдельных элементов физико-механического процесса получения волокнистых материалов вертикальным раздувом струи расплавленного термопласта известных законов движения вязкой жидкости и классических уравнений тепломассообмена – при рассмотрении струи расплавленного материала, законов движения идеальной несжимаемой жидкости – при рассмотрении процесса работы дутьевой головки, а также удовлетворительной сходимостью результатов расчетов с результатами экспериментов и натурных испытаний действующей установки для производства волокнистых материалов рассмотренным способом. Достоверность результатов подтверждается также успешным внедрением разработки в производство.
Практическая ценность работы. Полученные в ходе выполнения работы рекомендации по расчету и проектированию плавильного агрегата и дутьевой головки с кольцевым сходящимся соплом для получения волокнистых материалов вертикальным раздувом истекающей из плавильного агрегата под действием гидростатического давления струи расплавленного термопласта использованы при проектировании и изготовлении опытно-промышленной установки, внедренной в производство в ООО «Маркет» (г.Воткинск). Конструкция вальцового агрегата для формирования из получаемого на действующей установке волокнистого материала холстов переменной плотности защищена патентом РФ на изобретение. Результаты исследований могут быть использованы при проектировании аналогичного оборудования для получения волокнистых материалов из других типов сырья, например, стекла или базальта.
Личный вклад автора. Основные результаты и положения, выносимые на защиту, получены автором лично. Автор произвел составление математических моделей отдельных элементов физико-механического процесса получения волокнистых материалов вертикальным раздувом струи расплавленного термопласта, а также разработал технические средства необходимые для реализации процесса получения волокнистых материалов предлагаемым способом и режимы их изготовления, анализировал их структуру и определял показатели свойств. По результатам выполненных исследований опубликовано 14 работ, из них 8 статей в ведущих рецензируемых изданиях, рекомендуемых ВАК, получен патент РФ.
Апробация. Основные положения диссертационной работы докладывались:
- на Международной научной конференции «XVIII Туполевские чтения» (г. Казань, КГТУ им. А.Н. Туполева, май 2010г.);
- на Международной научно-технической конференции «Актуальные вопросы современной техники и технологии» (г. Липецк, апрель 2010г);
- на IX выставке-сессии инновационных проектов (г.Ижевск, май 2010г);
- на IX Международной специализированной выставке «Комплексная безопасность - 2010» (г.Ижевск, 21 – 24 сентября 2010г);
- на IX Международной специализированной выставке «Нефть, Газ, Химия - 2010» (г. Ижевск, 19 – 22 октября 2010 г);
- на Научно-методических конференциях Воткинского филиала ИжГТУ (г.Воткинск, Воткинского филиала ИжГТУ, февраль 2009 и 2010 гг);
- на научных семинарах кафедры «Технология машиностроения и приборостроения» (г. Воткинск, Воткинского филиала ИжГТУ в 2008-2010 гг).
Структура и объём диссертации. Диссертационная работа состоит из введения, 4 глав, заключения, библиографического списка, включающего 78 наименований. Работа изложена на 145 листах машинописного текста, содержит 67 иллюстраций, 22 таблиц и приложения.
ОСНОВНОЕ СОДЕРЖАНИЕ РАБОТЫ
Во введение обоснована актуальность темы диссертации, сформулированы цели и задачи исследования, излагается научная новизна и практическая ценность проведенных теоретических и экспериментальных исследований процесса получения волокнистых материалов вертикальным раздувом струи расплавленного термопласта, истекающей из плавильного агрегата под действием гидростатического давления, формулируются основные положения, выносимые на защиту, приводится структура диссертации.
В первой главе диссертации приведен анализ известных процессов, технологий и оборудования для получения волокнистых материалов на основе термопластичных пластмасс.
Проведенный аналитический обзор позволил установить, что классическая технология получения синтетического волокнистого материала путем плавления термопластов, вытягивания бесконечных волокон толщиной в несколько микрометров через фильеры диаметром менее полумиллиметра с последующим образованием жгутов из таких волокон, их резкой на элементы одинаковой длины, перемешиванием, рассыпкой на транспортер и дальнейшим формированием холстов или нетканого материала сложна для реализации, требует применения дорогостоящего оборудования и малопроизводительна. Именно по такой технологии, на импортном оборудовании, производят в настоящее время известный волокнистый материал – синтепон.
Существенно проще является технология получения волокнистых материалов способом вертикального раздува струи расплавленного сырья потоком сжатого воздуха, реализованная на практике при получении волокнистых материалов из минеральных расплавов. Известный вклад в разработку и исследование процессов производства волокнистых материалов из минерального и синтетического сырья различными способами, в том числе и способом вертикального раздува воздухом внесли отечественные и зарубежные ученые: С. П. Папков, В. А. Груздев, И. П. Бакшеев, Г. Ф. Тобольский, А. Б. Пакшвер, Э. М. Айзенштейн, В. Э. Геллер, Х. Людвиг, и др. Опыты получения по такой технологии полиэтилентерефталатного волокна, проведенные в Воткинском филиале ИжГТУ, подтвердили целесообразность ее практической реализации.
Наиболее сложными и недостаточно изученными элементами технологии получения волокнистых материалов способом вертикального раздува струи расплавленного термопласта являются плавильный агрегат и дутьевая головка.
Используемые в качестве агрегатов для плавления пластмасс при решении аналогичных задач устройства экструдерного типа имеют сложную конструкцию и требуют больших затрат энергии, поэтому в настоящей работе поставлена задача подтвердить возможность использовании для получения струи расплавленного термопласта и дать рекомендации по расчету плавильного агрегата с истечением струи под действием гидростатического давления – без применения шнековых устройств. Рассмотрение теоретических основ расчета аналогичных агрегатов показало, что для решения этой задачи следует использовать известные уравнения движения вязкой жидкости и классические уравнения теплопроводности.
После анализа известных конструкций дутьевых головок для получения различных волокнистых материалов способом раздува, принято решение подробнее изучить и дать рекомендации по проектированию головок с кольцевым сходящимся соплом, которые обеспечивают лучшую концентрацию энергии потока воздуха при взаимодействии его со струей расплавленного материала в зоне волокнообразования. При их теоретическом исследовании возможно использование уравнений движения идеальной несжимаемой жидкости.
Анализ известных способов получения из синтетических волокнистых материалов готовых к практическому использованию в машиностроении материалов и изделий показал необходимость изучения процесса получения нетканых материалов путем прокатки бесформенного волокна с его подогревом и последующим образованием материала с переменной по сечению плотностью.
На основе выполненного обзора научной, технической и патентной литературы, изучения действующего оборудования для производства волокнистого материала из термопластических расплавов сформулирована цель работы и определены задачи исследования.
Во второй главе диссертации приводятся теоретические исследования плавильного агрегата и дутьевой головки для реализации процесса получения волокнистых материалов способом вертикального раздува струи расплавленного термопласта воздухом, позволяющие на стадии проектирования агрегатов для его реализации, определить основные геометрические параметры оборудования и выбрать рациональные режимы технологического процесса.
Агрегат для получения волокнистых материалов вертикальным раздувом истекающей из плавильного агрегата под действием гидростатического давления струи расплавленного материала потоком сжатого воздуха содержит устройство для подачи исходного сырья, плавильный агрегат с внешним и внутренним электрическими нагревательными элементами, а также дутьевую головку с кольцевым сходящимся соплом (рис.1). Для определения производительности плавильного агрегата, применена методика расчета характеристик потока вязкой жидкости использованной П.Ю. Апелем и С.Н. Дмитриевым при расчете формы пор трековых мембран. При этом рассмотрено движение расплавленного материала с применением формулы Пуазейля и ее модификаций для вязкой жидкости в каждом из четырех геометрических элементов внутренней полости плавильного агрегата, соответственно: в основной плавильной камере, во втором коническом сужающемся элементе, в малой плавильной камере и в полусферическом элементе вблизи выходного отверстия:
P1 = 8μ1L Q / π (R-r1) 4 , (1)
Р1+P2 =(8μ2 l Q/3πr4)(r/R+(r/R)2+(r/R)3) , (2)
Р1+Р2+ P3 = 8μ3 L1 Q / πr4, (3)
Р1+Р2+ Р3+ P4 = 3 Q μ4 / rф3 . (4)
где μ1 – коэффициент динамической вязкости расплавленного термопласта в основной плавильной камере, Па.с; Q – объемная производительность агрегата, м3/с; Р1 – давление воздуха в основной плавильной камере, Па, μ2 – коэффициент динамической вязкости расплавленного термопласта во втором элементе, Па.с; Р2=ρgL – гидростатическое давление над вторым элементом, Па (ρ=1300 кг/м3 – плотность термопласта (полиэтилентерефталата), g=9,8 м/с2), μ3 – коэффициент динамической вязкости расплавленного термопласта во втором цилиндрическом элементе, Па.с; Р3=ρgl – гидростатическое давление перед малой плавильной камерой, Па, μ4 – коэффициент динамической вязкости расплавленного термопласта на выходе струи в атмосферу, Па.с; Р4= ρgL1 – гидростатическое давление над выходным отверстием, Па.
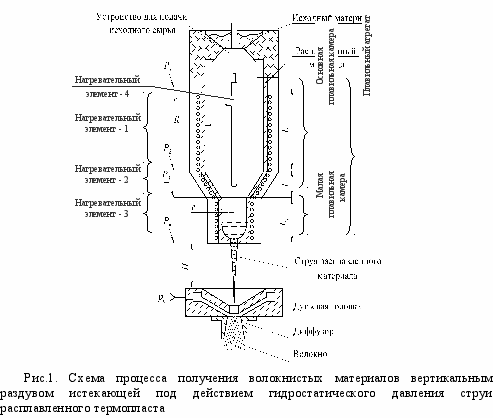
Анализируя выражения (1), (2), (3) и (4), после преобразований получена формула для определения массовой производительности G, плавильного агрегата:
G =ρ (4Р1+3Р2+2Р3+Р4)/(A+B+C+D). (5)
где A=8μ1L / π (R-r1)4 ; B=(8μ2 l / 3 π r4)(r/R + (r/R)2 + (r/R)3); C=8μ3 L1 / πr4; D=3μ4 / rф3.
Результаты анализа формулы (5) представлены на графиках (рис.2 и 3), откуда следует, что наибольшее влияние на производительность плавильного агрегата при рациональной температуре расплава оказывает изменение радиуса выходного отверстия rф и изменение давления сжатого воздуха, действующего на поверхность расплавленного материала Р1. Расхождение результатов расчета производительности по формуле (5) с экспериментальными данными, полученными при испытаниях плавильного агрегата при получении волокнистого материала из полиэтилентерефталата с указанными выше геометрическими параметрами проточной части при изменении радиуса выходного отверстия rф от 1,5 до 2,5 мм и изменении давления Р1 от нуля до 20 кПа не превышает 8%.
П
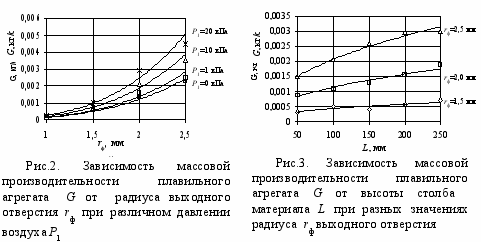
ри проектировании агрегатов рассматриваемого типа для производства волокнистого материала требуемого качества необходимо знать, как изменяется температура струи расплавленного термопласта на участке ее течения от выходного отверстия плавильного агрегата до координаты встречи с дутьевой головкой. Ранее проведенные эксперименты при получении волокнистых материалов из полиэтилентерефталата показали, что при температуре в указанной координате менее 250…270 0С образуется волокно в виде непрерывной нити, а при температуре более 270 0С – штапельное волокно.
При аналитическом решении этой задачи, расчетная схема которой приведена на рис.4а, приняты следующие допущения: струя расплавленного полимера имеет форму бесконечного стержня с убывающим по длине радиусом; движением струи в осевом направлении пренебрегаем вследствие малых скоростей потока; охлаждение струи расплавленного полимера эжектируемым дутьевой головкой потоком воздуха на рассматриваемом участке происходит равномерно по всей длине струи; струя находится в среде с постоянной температурой ta; коэффициент теплопроводности материала струи λ достаточно велик, а площадь сечения струи мала по сравнению с ее длиной.
Уравнение теплового баланса для элемента струи длиной dx:
dQ = Qx-Qx+dx , (6)
где dQ=2πrαθdx – количество теплоты, отдаваемое окружающей его среде; Qx – количество теплоты, входящее в верхнюю грань элемента; Qx+dx – количество теплоты, которое выходит за это же время через нижнюю грань выделенного элемента; где α – коэффициент теплоотдачи, Вт/(м2·К).
Согласно основному закону теплопроводности:
dQ=-λ(dθ/dx)πr2 , Qx+dx=-λπr2 [d(θ+(dθ/dx)dx]dx. (7)
Подставив (7) в (6), получено дифференциальное уравнение, описывающее процесс охлаждения струи расплавленного материала:
d2θ/dx2=q2θ, (8)
где q2=2α/(λr); λ- коэффициент теплопроводности материала.
Зависимость текущего радиуса струи r от осевой координаты x после анализа фотографий струи (рис.4б) определяется эмпирической формулой:
r= (r0-rc)e-cx+rс, (9)
где rс – радиус струи, охлажденной ниже температуры плавления; с- параметр, определяемый в зависимости от скорости V потока воздуха.
Для упрощения решения уравнения (8) струя представлена в виде последовательности уменьшающихся в радиусе цилиндрических элементов (рис.4в). Избыточная температура θi в нижней части таких элементов определяется по формуле:
θi =θi-1 е-qi Δx , (10)
где i=1…n; n=10…20 – количество условных цилиндрических элементов; Δx=(0,1…0,05)xmax; xmax – максимальное расстояние по длине струи, при увеличении которого существенного изменения температуры, влияющей на физические свойства струи, не происходит. Параметр qi в этом случае вычисляется по формуле:
qi=[2α/(λ ( (r0-rc)e-ciΔx+rс))]0,5 . (11)
Результаты расчета температуры струи по формуле (11), полученные при рассмотрении струи расплавленного полиэтилентерефталата с коэффициентом теплопроводности λ=0,14 Вт/(м·К), истекающей из сопла плавильного агрегата радиусом r0 = 0,0015 м, при rс=0,0002 м, при неработающей дутьевой головке, когда V=0, при коэффициенте теплоотдачи αс = 0,000512 Вт/(м2·К), при параметре с =108 м-1, представлены на рис.5. При этом принято, что i=1…10, xmax=0,04 м, Δx=0,004м. Графики получены при температуре струи на срезе сопла плавильного
агрегата t0=3300С, t0=3100С и t0=2900С. Температура среды ta=200С.
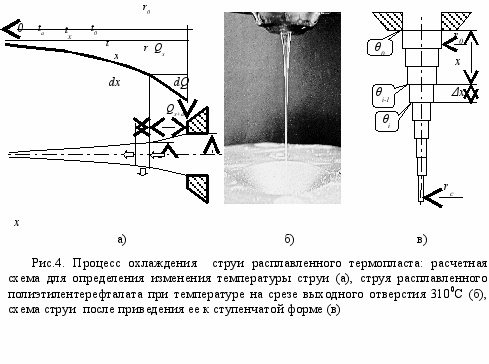
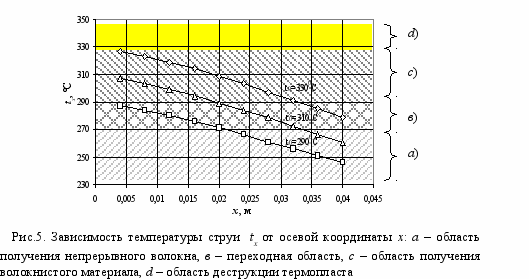
Температура струи, соответствующая осевой координате x определяется как tx= θi + ta. Эти результаты могут быть использованы для назначения рационального расстояния между плавильным агрегатом и дутьевой головкой при получении волокна требуемого качества и рациональной температуры струи.
Производительность и качество получаемого рассматриваемым способом волокна определяется также конструкцией и расходными характеристиками дутьевой головки. В ходе экспериментальной отработки процесса получения полиэтилентерефталатного волокна рациональной признана дутьевая головка с кольцевым сходящимся соплом, расчетная схема которой приведена на рис.6.
Управляемыми параметрами при проектировании дутьевой головки, для получения нужной скорости воздушного потока, являются давление в кольцевой полости рк и геометрические размеры проточной части В и К.
Р
Рис. 6. Схема дутьевой головки
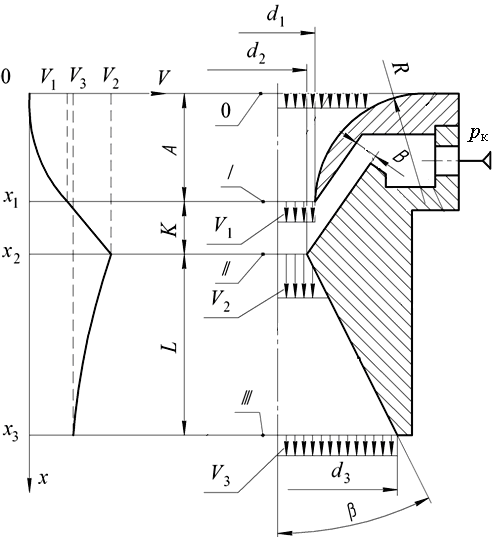
асход эжектируемого воздуха Qв и средняя скорость потока через центральное отверстие в сечении I определены по формулам:
Qв = 0,25μв π d12 (2pв/ρ)0,5, V1 = μв(2pв/ρ)0,5 , (12)
где μв – коэффициент расхода профилированной части верхнего элемента 1; d1 – диаметр центрального отверстия, м; рв – разрежение в центральном отверстии, Па; ρв – плотность воздуха, кг/м3.
Если принять, что профиль рассматриваемого отверстия в плоскости, проходящей через ось устройства, имеет окружность радиусом R, то закон изменения скорости на рассматриваемом участке, при 0≤x
Vx1= V1 d12/(4t2), (13)
где t = R+ d1/2 – [R2 – (R – x)2]0,5.
Расход воздуха через кольцевое сходящееся сопло Qк шириной В и скорость потока в сечении II V2 :
Qк= μкπB d1(2pк/ρ)0,5 , V2=4(Qв+ Qк)/π d2 2 , (14)
где μк – коэффициент расхода кольцевого сопла; pк – давление воздуха в кольцевой полости, Па; d2 – внутренний диаметр нижнего элемента.
На участке осевой координаты х от х1 до х2 (где х1 = А; х2 = А+К), или А<х< А+K, скорость изменяется по следующему закону:
Vx2= V1 – А(V2 – V1)/K + x(V2 – V1)/K. (15)
В крайнем нижнем сечении III на выходе струи из диффузора скорость воздушного потока V3 уменьшается вследствие увеличения площади сечения и определяется следующим образом:
V3= V2 d2 2/ d3 2. (16)
На участке между сечениями II и III при А+К <x< L+А+К скорость воздушного потока вычисляем по формуле:
Vx3= V2 d2 2/ [d2 + 2(x – А–K)tgβ]2. (17)
В результате анализа полученных зависимостей (рис.7) установлено, что наибольшая скорость воздушного потока создается на нижнем срезе кольцевого сопла – именно на этом участке происходит деформирование струи расплавленного материала на элементарные струйки с последующей вытяжкой элементарных волокон.
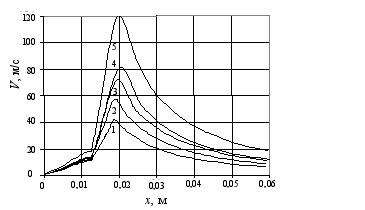
Рис. 7. Средняя скорость воздушного потока в характерных сечениях дутьевой головки: 1 – рк = 50кПа, В = 0,3 мм, K = 0,62м; 2 – рк = 100 кПа, В = 0,3 мм, K = 0,62 мм;3 – рк = 70 кПа, В = 0,46 мм, K = 0,67 мм; 4 – рк = 50 кПа, В = 0,6 мм, K = 0,69 мм; 5 – рк = 125 кПа, В = 0,6 мм, K = 0,69 мм
В третьей главе приведены результаты экспериментального исследования процесса получения волокнистых материалов вертикальным раздувом истекающей из плавильного агрегата под действием гидростатического давления струи расплавленного термопласта и дутьевой головки для его реализации.
Э
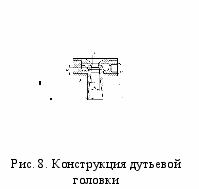
При получении волокна рассматриваемым способом возможно использование вторичного полиэтилентерефталатного сырья, например, дробленых пластиковых бутылок. При этом наблюдается наличие в готовом продукте неволокнистых включений в виде каплеобразных элементов.
Экспериментально доказано, что производительность процесса и качество получаемого волокна зависят от величины разрежения в центральном канале и расхода эжектируемого дутьевой головкой (рис.8) воздуха в направлении движения струи расплавленного материала, которые определяются величиной давления воздуха подводимого для питания дутьевой головки и ее геометрическими параметрами – шириной кольцевого зазора и формой проточной части диффузора. Характеризующие это влияние графики представлены на рис.9, 10, 11 и 12. С использованием теории планирования эксперимента получена математическая зависимость безразмерного разрежения q=pв/pо в центральном канале дутьевой головки без закрутки питающего потока от величины давления питания p0 , ширины кольцевого зазора В и длины диффузора L:
q = 0,1 +0,048Z1+0,029 Z2+0,053 Z3+0,016 Z4+0,027 Z5+0,008 Z6-0,0044 Z7 (18)
где нормализованные факторы имеет вид: Z1=2(р0-125)/150; Z2=2(h-0,45)/0,3; Z3=2(L-20)/40; Z4= Z1 Z2; Z5= Z1 Z3; Z6= Z1 Z3; Z7= Z1 Z2 Z3.
Рациональной является величина зазора В=0,5-0,6 мм при среднем диаметре кольцевой щели 10 мм. Рациональный центральный угол диффузора – 12 градусов, а рациональное отношение его длины к диаметру кольцевой щели -1,8…2,0. В зависимости от диаметра выходного отверстия плавильного агрегата и температуры расплавленного материала существует рациональная величина разрежения. При малом разрежении возможно налипание струи материала на внутреннюю поверхность головки и прекращение процесса волокнообразования, а при большом разрежении – слишком интенсивное охлаждение струи и, как следствие этого – невозможность расщепления струи на элементарные волокна. Например, при диаметре выходного отверстия 3 мм и температуре струи на его срезе 290 0С рациональное разрежение должно быть в пределах от 10 до 20 кПа.
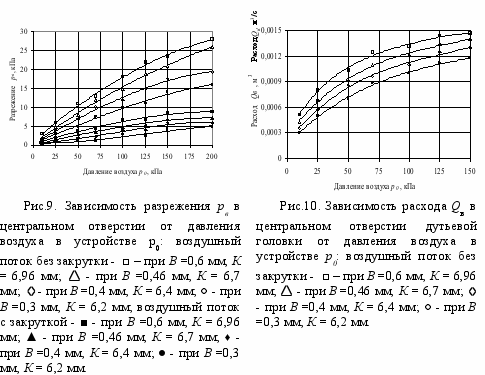
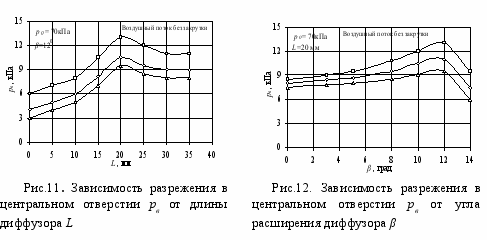
Процесс волокнообразования существенно зависит от сил, действующих со стороны потока воздуха на струю расплавленного материала. В настоящей диссертационной работе выполнено экспериментальное моделирования силового действия потока воздуха, истекающего из дутьевой головки указанной выше конструкции на размещенную в ее центральной части условно бесконечную мононить, имитирующую струю расплавленного материала. При этом получены экспериментальные зависимости силы поверхностного трения Fт, действующей со стороны потока воздуха на мононить разного диаметра dн от величины давления p0 питания дутьевой головки сжатым воздухом (рис. 13). Сила поверхностного трения увеличивается при увеличении давления питания, ширины кольцевого зазора В в дутьевой головке и при увеличении диаметра dн мононити. Закрутка питающего потока в дутьевой головке путем тангенциального подвода воздуха уменьшает силу поверхностного трения ввиду уменьшения осевой проекции скорости потока, которая определяет силу трения.
Анализ результатов такого моделирования процесса позволяет предположить, что полученной в опытах силы не достаточно для расщепления струи расплавленного термопласта на множество штапельных волокон, в этом случае образуется только непрерывная нить. Вероятно, что процесс образования волокна обусловлен еще и поперечными пульсациями струи в момент образования волокна, что существенно увеличивает силу вытягивания. При получении непрерывного волокна закрутка не нужна, а при получении штапельного – закрутка потока усиливает турбулентные пульсации струи расплавленного материала и стимулирует процесс расщепления ее на множество элементарных волокон.
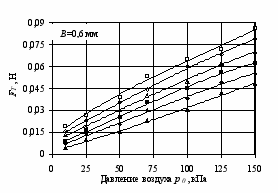
Рис.13. Зависимость силы трения FТ от давления питания дутьевой головки р0: воздушный поток без закрутки - □ – при dн=3 мм; ♦ – при dн=1 мм; ▲ – при dн=0,15 мм; воздушный поток с закруткой - ■ - при dн=3 мм; ♦ – при dн=1 мм; ▲ – при dн=0,15 мм.
В четвертой главе представлены результаты разработки и испытаний технических средств для реализации процесса получения волокнистых материалов способом вертикального раздува струи расплавленного термопласта.
В ходе внедрения результатов работы в производство разработана и изготовлена опытно-промышленная установка для получения полиэтилентерефталатного волокна, схема и общий вид которой приведены на рис.14. Установка содержит плавильный агрегат, обеспечивающий истечение струи расплавленного термопласта под действием гидростатического давления с элементами автоматического поддержания температуры, автоматическое загрузочное устройство шлюзового типа, обеспечивающее возможность истечения струи расплавленного термопласта под избыточным давлением воздуха или инертного газа, и дутьевую головку с механизмом качания, который обеспечивает равномерное распределение образующегося волокна на поверхности приемного транспортера.
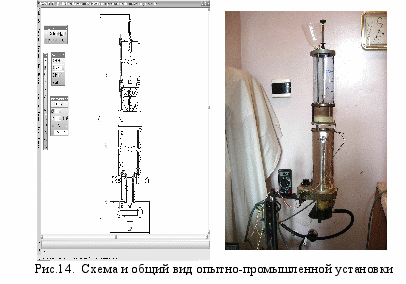
Для оперативного измерения среднего диаметра элементарных волокон разработано и исследовано пневматическое устройство манометрического типа (рис.15). Получена его тарировочная характеристика в виде математической зависимости среднего диаметра d (мкм) элементарных волокон от давления Р (Па) в измерительной камере устройства:
d = 78772 Р-1,05 . (26)
Давление сжатого воздуха на входе в измерительную камеру – 100 кПа. Устройство позволяет измерять средний диаметр элементарных волокон с относительной погрешностью не более 9% в диапазоне диаметров волокон – от 10 до 100 мкм.
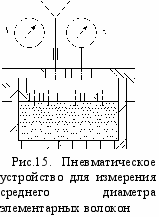
Рекомендуется использовать получаемый рассматриваемым способом волокнистый материал для сорбции нефти с поверхности земли и воды при ее разливах в чрезвычайных ситуациях. Он обладает способностью впитывать нефть, разлитую на поверхности воды и имеет положительную плавучесть. Один грамм волокна впитывает в среднем 20 граммов нефти. Многократная регенерация волокнистого материала возможна центробежным способом или методом отжима. По сравнению с известным порошкообразным сорбентом, волокнистый материал на основе полиэтилентерефталата может быть использован и в ветреную погоду, и для сбора нефти с водных поверхностей при наличии растительности.
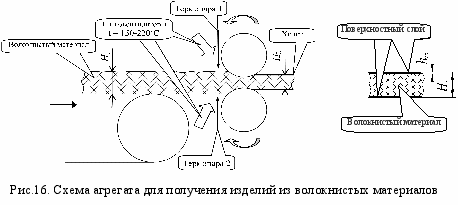
Для производства удобных в практическом применении изделий из полиэтилентерефталатного волокна, полученного рассматриваемым способом, предлагается использовать вальцовый агрегат, схема которого приведена на рис.16. Предварительно подогретый с помощью тепловентилятов волокнистый материал проходит через вращающиеся вальцы и на его поверхности образуется уплотненный поверхностный слой, обеспечивающий достаточную для практики прочность изделия. Плотность поверхностного слоя зависит от температуры воздушного потока действующего на волокно перед вальцами и от среднего диаметра элементарных волокон (рис.17).
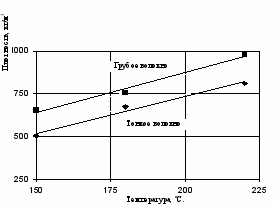
Рис. 17. Зависимость плотности поверхностного слоя от температуры
ОСНОВНЫЕ РЕЗУЛЬТАТЫ И ВЫВОДЫ
1. Разработан метод расчета производительности плавильного агрегата для получения волокнистых материалов вертикальным раздувом струи расплавленного термопласта потоком воздуха с истечением струи из выходного отверстия плавильного агрегата под действием гидростатического давления, основанный на использовании различных модификаций формулы Пуазейля для течения вязких жидкостей. Расхождение результатов расчета по этому методу с экспериментальными данными не превышает 8 %.
2. Предложен метод определения закономерности изменения температуры струи расплавленного полимера, с переменным сечением истекающий из плавильного агрегата под действием гидростатического давления, по ее длине. Метод позволяет определить рациональное расстояние между плавильным агрегатов и дутьевой головкой для получения штапельного или непрерывного волокна.
3. Получены расчетные и экспериментальные данные, характеризующие эффективность работы дутьевой головки с кольцевым сходящимся соплом: рациональная величина кольцевого зазора В=0,5÷0,6 мм при среднем диаметре кольцевой щели 10 мм, центральный угол диффузора – 12 градусов, а рациональное отношение его длины к диаметру кольцевой щели – 1,8÷2,0, при этом рациональное разрежение в дутьевой головке должно быть в пределах от 10 до 20 кПа. Увеличение разрежения в центральном отверстии дутьевой головки может приводить к прекращению процесса образования волокнистого материала вследствие интенсивного охлаждения струи расплавленного термопласта.
4. Процесс образования волокна при взаимодействии струи расплавленного термопласта с потоком воздуха, истекающего из дутьевой головки обусловлен не только силой поверхностного трения, но и поперечными пульсациями струи в момент образования волокна, что существенно увеличивает силу вытягивания. При получении непрерывного волокна закрутка потока воздуха в дутьевой головке не нужна, а при получении штапельного – закрутка потока усиливает турбулентные пульсации струи и стимулирует процесс расщепления ее на множество штапельных элементарных волокон.
5. Разработана и внедрена в производство опытно-промышленная установка для получения волокнистых материалов способом вертикального раздува истекающей под действием гидростатического давления струи расплавленного полиэтилентерефталата потоком воздуха. Установка оснащена автоматическим дозирующим устройством, средствами автоматического поддержания температуры в плавильном агрегате и устройством качания дутьевой головки. Разработано и используется в производстве пневматическое устройство для измерения среднего диаметра элементарных волокон, обеспечивающее погрешность измерения диаметра волокон в диапазоне от 10 до 100 мкм с погрешностью не более 9%.
6. Разработан и защищен патентом на изобретение вальцовый агрегат для изготовления из полученного рассматриваемым способом волокна изделий с переменной по толщине плотностью.
7. По сравнению с базальтовым супертонким волокном водопоглощение полученного волокнистого материала способом вертикального раздува струи из расплавленного полиэтилентерефталата в три раза меньше, упругость в два раза больше, прочность на растяжение в пять раз больше, а коэффициенты теплопроводности практически не отличаются.
8. Экспериментально подтверждена возможность получения волокнистых материалов рассматриваемым способом из вторичного полиэтилентерефталата с незначительным снижением качества готового продукта. Доказана возможность использования такого волокна для сорбции нефтепродуктов с поверхности воды: один грамм волокна впитывает в среднем 20 граммов нефти.
Опираясь на выше изложенные научно обоснованные технологические разработки, имеющие существенное значение в машиностроении, позволяют использовать полученные в ходе выполнения работы рекомендации по расчету и проектированию плавильного агрегата и дутьевой головки с кольцевым сходящимся соплом необходимые для получения волокнистых материалов внедрить на предприятии ООО «Маркет» (г.Воткинск, Удмуртская Республика), с 2011 года. Ожидаемый экономический эффект внедрения результатов работы составляет около одного миллиона рублей в год с одной установки по производству волокнистых материалов. Результаты работы используются в учебном процессе подготовки специалистов в Воткинском филиале ГОУ ВПО «Ижевский государственный технический университет».
Основное содержание диссертации отражено в следующих публикациях:
В изданиях, рекомендованных ВАК для публикации основных научных результатов:
1. Сентяков Б.А., Широбоков К.П., Святский В.М. Методика расчета средней скорости воздушного потока в рабочей зоне устройства волокнообразования [Текст] // Машиностроение и инженерное образование. - №3. Москва: ГОУ МГИУ, 2010. – с. 20-24.
2. Сентяков Б.А., Широбоков К.П., Святский В.М. Влияние конструктивных параметров устройства на процесс волокнообразования [Текст] // Вестник машиностроения. - №3 – Москва: 2010. с.32-34.
3. Сентяков Б.А., Широбоков К.П., Святский В.М. Исследование дутьевой головки для получения полиэтилентерефталатного волокна способом вертикального раздува [Текст] // Автоматизация и современные технологии. - №12. Москва: 2010. с. 6 - 10.
4. Сентяков Б.А., Широбоков К.П., Святский В.М. Определение производительности плавильного агрегата при производстве волокнистых материалов из расплава термопластов [Текст]// Современные технологии. Системный анализ. Моделирование. ИрГУПС. Научный журнал №2. – Иркутск: 2010. с. 36-40.
5. Широбоков К.П., Святский В.М. Охлаждение свободной струи расплавленного полимера при производстве волокнистых материалов способом вертикального раздува воздухом [Текст] // Современные технологии. Системный анализ. Моделирование. ИрГУПС. Научный журнал №3. – Иркутск: 2010. с. 126-129.
6. Широбоков К.П., Святский В.М. Исследование влияние конструктивных параметров диффузора на характеристику устройства волокнообразования [Текст] // Вестник ИжГТУ. - №3.- Ижевск: 2010. с. 42-44.
7. Святский В.М. Расчет производительности вальцового агрегата [Текст] // Вестник ИжГТУ. - №4.- Ижевск: 2009. с. 43-45.
8. Сентяков Б.А., Широбоков К.П., Святский В.М. Пневматическое устройство для измерения среднего диаметра элементарных волокон [Текст] // Датчики и системы. - №7. Москва: 2010. с.45-47.
В том числе патент:
9. Вальцовый агрегат [Текст]: патент №2403109 РФ. // Святский В.М., Святский М.А., Сентяков Б.А.; заявитель и патентообладатель Святский В.М; Опубл. 10.11.2010, Бюл.№31.
Другие публикации:
10. Святский В.М. Перспективы производства теплоизоляционных материалов на основе полиэтилентерефталата [Текст] // Актуальные вопросы современной техники и технологии: Сборник докладов Международной научной конференции. Т.1/ Под ред. А.В. Горбенко, С.В. Довженко. – Липецк: Издательский центр «Де-факто», 2010. –с.148-150.
11. Святский В.М. Технология производства полиэтилентерефталатного волокна способом вертикального раздува [Текст] // «XVIII Туполевские чтения»: материалы международной конференции. (2010.Казань). В 5 частях. Часть1. 2010. с.50-51.
12. Святский В.М., Сентяков Б.А. Влияние исходного сырья на качество полиэтилентерефталатного волокна при реализации технологии вертикального раздува [Текст] // Материалы межрегиональной науч.-практич. конф.– Ижевск: Изд-во «Удмуртский университет», 2010.- с.195-199.
13. Сентяков Б.А., Широбоков К.П., Святский В.М. Волокнистый сорбент для сбора нефти на основе полиэтилентерефталата [Текст] // Предотвращение аварий зданий и сооружений: Сборник научных трудов, выпуск 9. – Москва, 2010. – с. 631-634.
14. Святский В.М. Технические и экономические параметры установки для производства нетканых материалов на основе полиэтилентерефталатного волокна [Текст] // «Прогрессивные технологии в современном машиностроении»: сборник статей VI Международной научно-технической конференции. – Пенза: Приволжский Дом знаний, 2010. – 244-246 с.
Подписано к печати Формат 60×84/16. Бумага писчая.
Усл. печ. л. 1,0. Тираж 100 экз.
Отпечатано в Воткинском филиале ИжГТУ.
427430, г.Воткинск ул. им.П.И. Шувалова 1