Основы построения автоматизированных систем проектирования технологических процессов и сопровождения производства изделий в геофизическом приборостроении
Вид материала | Автореферат |
- Методика проектирования автоматизированных систем, 36.85kb.
- План занятий третьего года обучения, по специальности «Программное обеспечение вычислительной, 103.35kb.
- Рабочей программы дисциплины Проектирование автоматизированных систем по направлению, 34.43kb.
- Основы построения автоматизированных систем иерархически-взаимосвязанного управления, 455.86kb.
- Основы построения автоматизированных систем иерархически-взаимосвязанного управления, 455.78kb.
- Аннотация рабочей программы дисциплины «Теория автоматического управления» Направление, 32.95kb.
- 220703 Автоматизация технологических процессов и производств, 46.56kb.
- Задачи и методы синтеза линейных су. Линейные дискретные модели су: основные понятия, 80.42kb.
- Влияние технологических процессов на формирование затрат производства и себестоимости, 29.68kb.
- Программа предназначена для работников машиностроительных предприятий, имеющих среднее, 16.96kb.
ТП являются управляемыми АССП подсистемами, состоящими из различных подсистем – участков, и осуществляют преобразование предметов производства в соответствии с алгоритмами (технологической документацией), задаваемыми командами
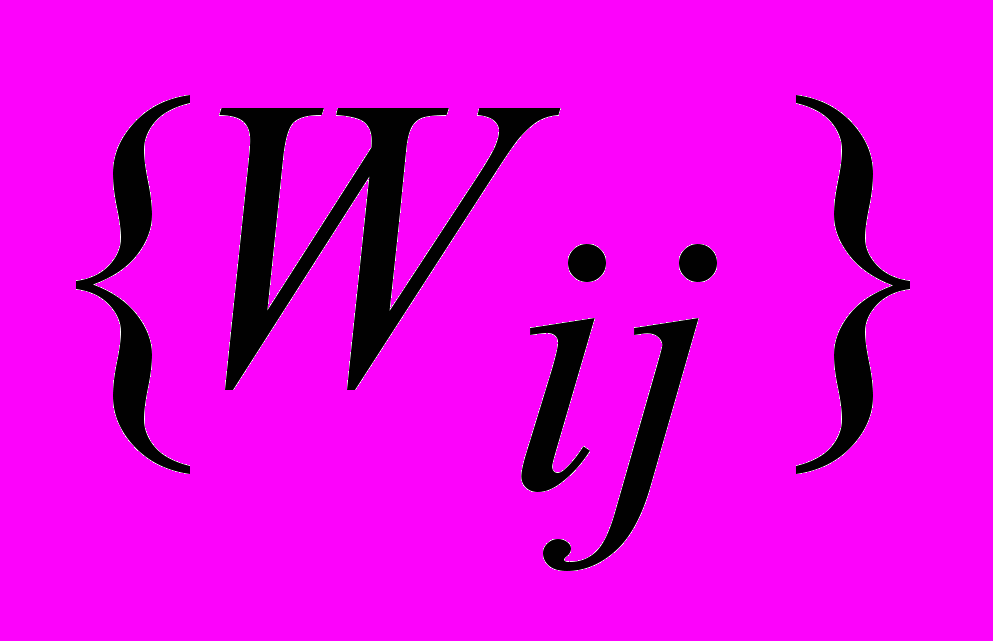
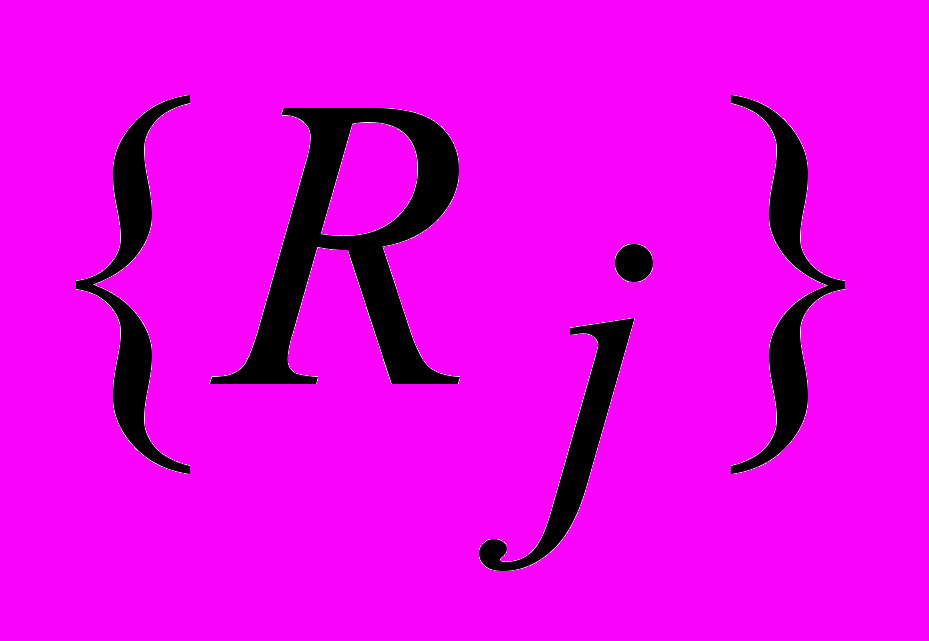
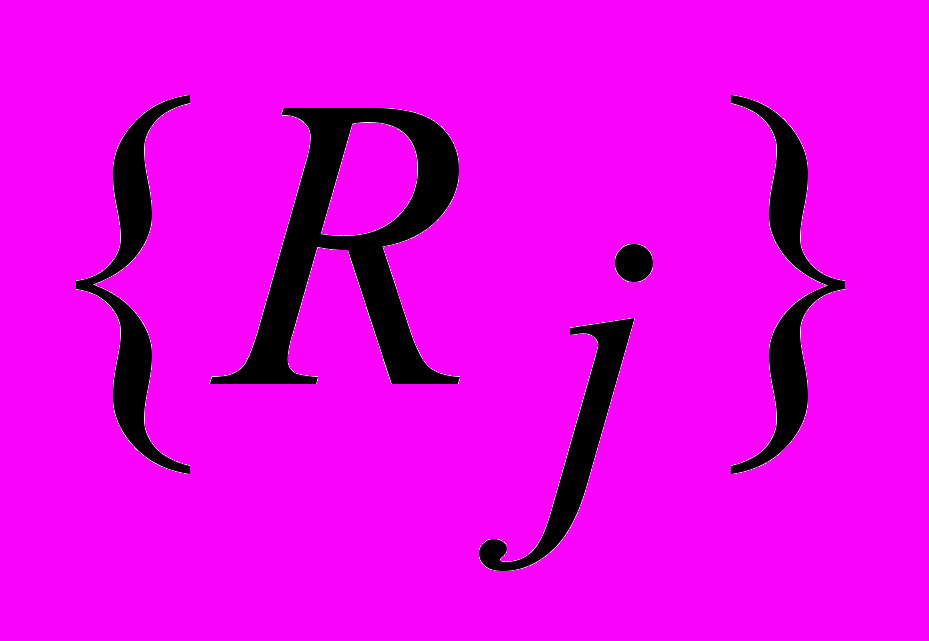




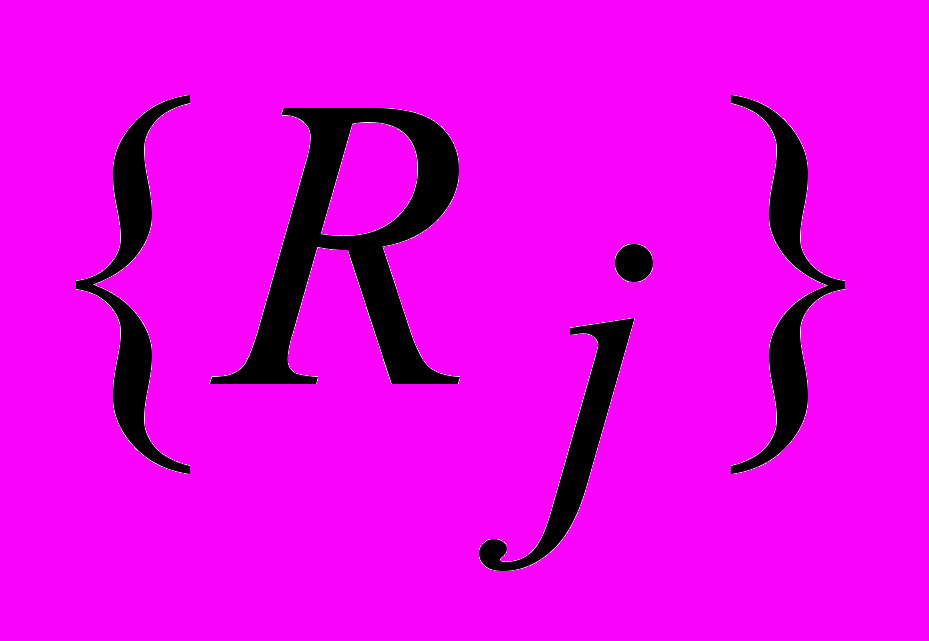




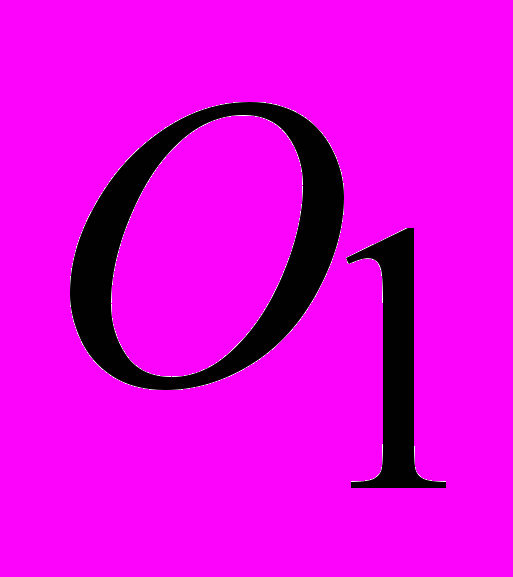










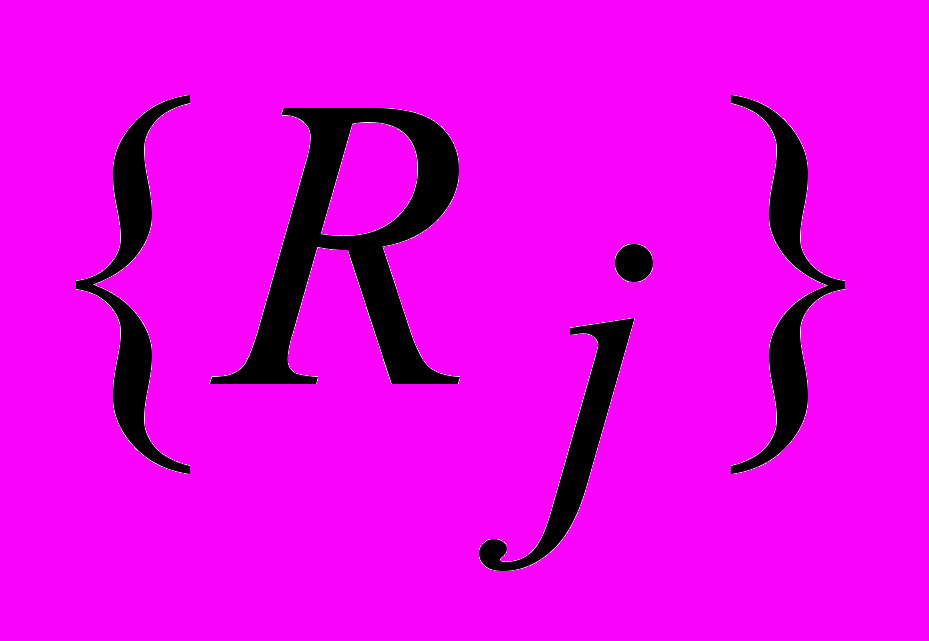

Выявлены принципы формирования систем приоритетов (иерархичность, целевая направленность-соответствие целям функционирования организации и иерархии организации, ситуативность-учет параметров состояния ТП при выборе приоритетных схем, постоянство действия важнейших приоритетов, отражающих смысл функционирования ПС, вариабельность- наложение вариативных приоритетов на постоянные). Обосновано и сформировано 11 систем иерархических приоритетных схем (ПРС), выбираемых продукционными моделями знаний на основе формального распознавания и анализа ситуации в ТП (загрузки оборудования по ходу основного детале-потока, длительности и числа операций в маршрутах запускаемых деталей, времени поступления деталей, наличия свободного оборудования, длительности первой следующей операции и т.д.). Каждая ПРС (рис.5) имеет иерархию приоритетов: глобальный (разряды работ), внутренний (группы работ в пределах разряда), частный (виды работ в пределах группы).
![]() |
Рис.5. Иерархия приоритетов |
Разработаны правила переназначения приоритетов при переходе в следующие интервалы оперативного планирования (ИОП). Обоснован критерий разработки КПГ- минимальный совокупный цикл изготовления запускаемых в обработку партий деталей. Для использования приоритетных схем уточнена постановка конвейерной задачи (М.Х. Прилуцкий, Стайглиц К. и др.) составления КПГ применительно к ТП ГФП путем введения 4-го (первые 3- ненарушаемость маршрута, непрерывность операции, число рабочих мест) ограничения: из находящихся в очереди на обработку на операции







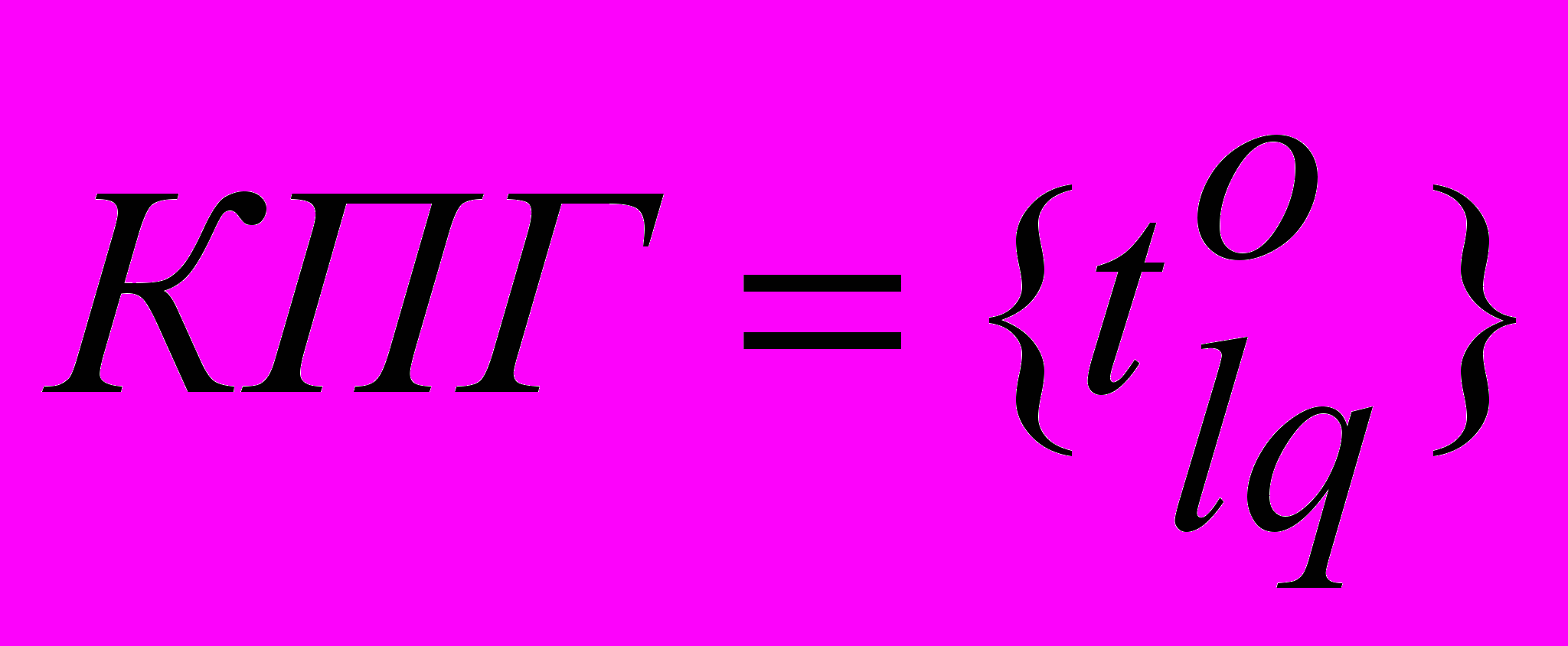
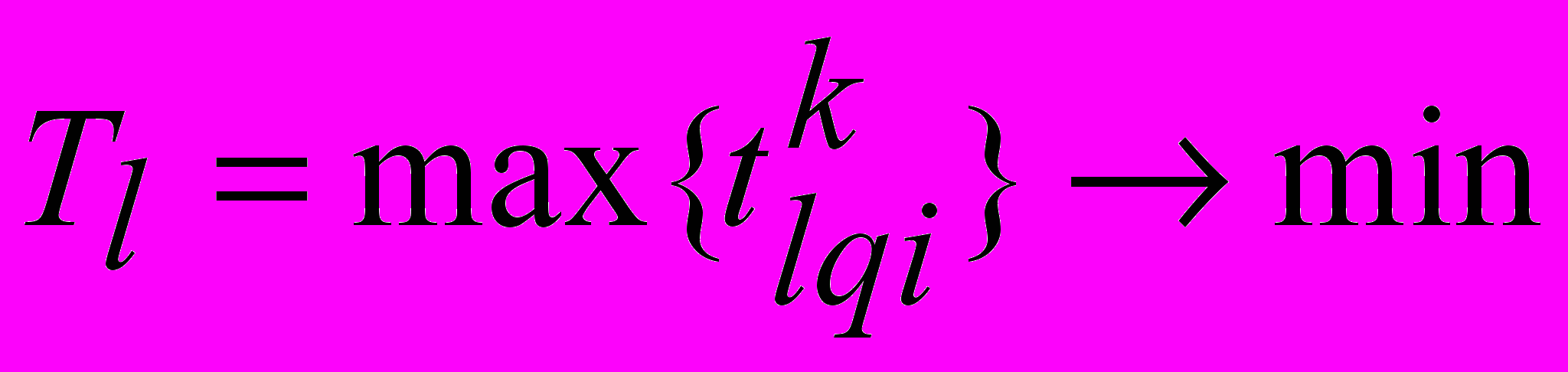





Диспетчирование строится на отслеживании фактических времен начала операций и сравнении их с расчетными (КПГ) по каждой обрабатываемой партии деталей. Анализом состояния при запуске деталей
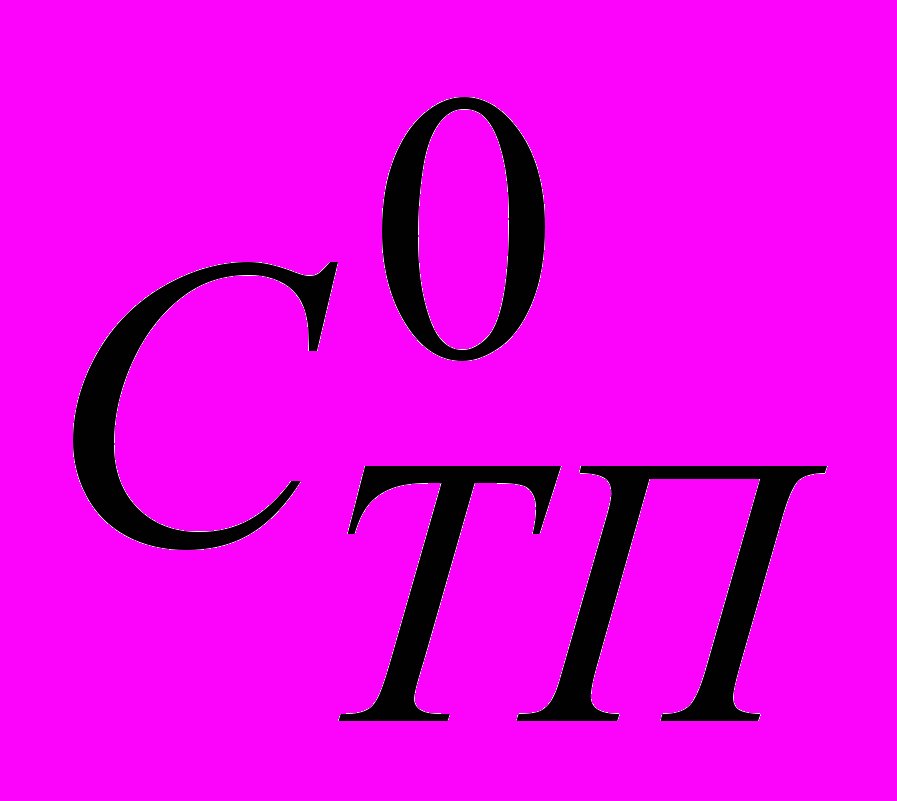
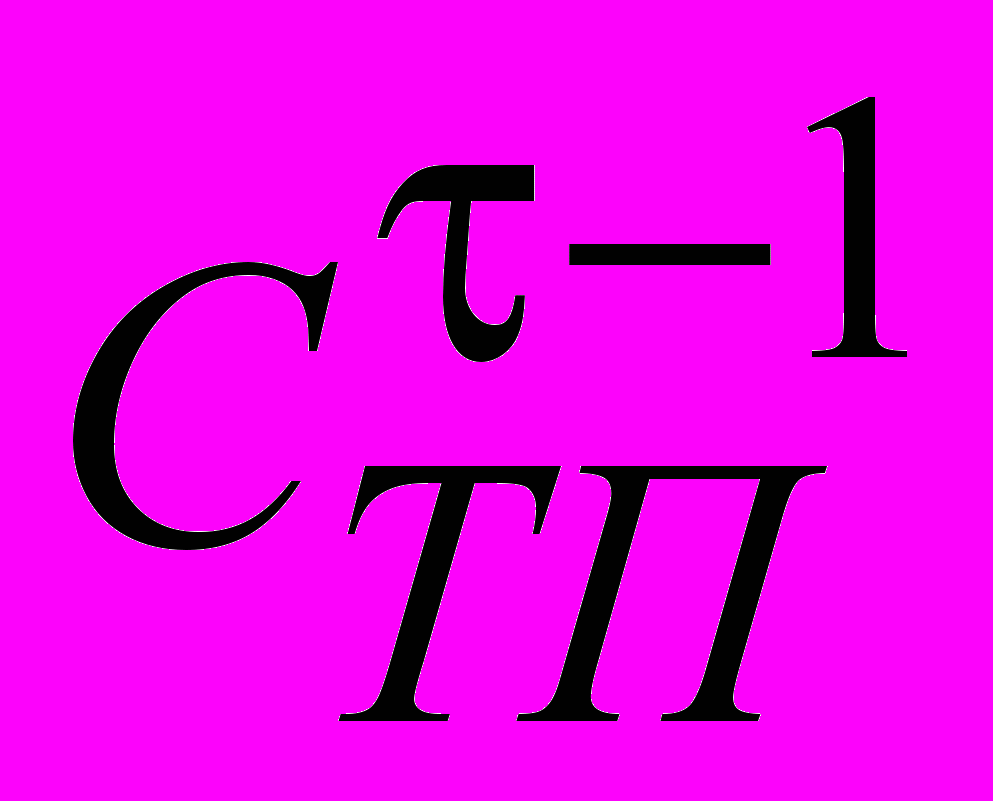
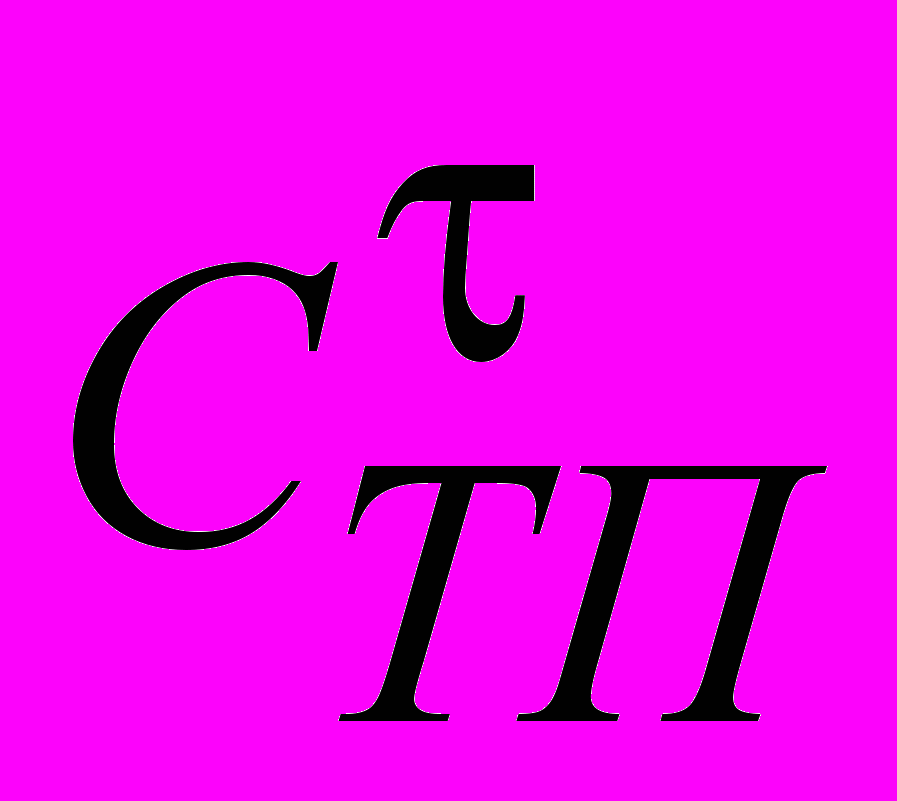
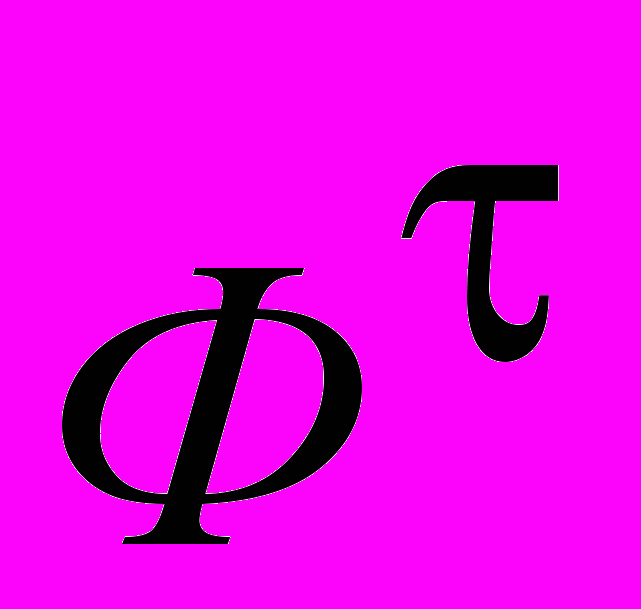
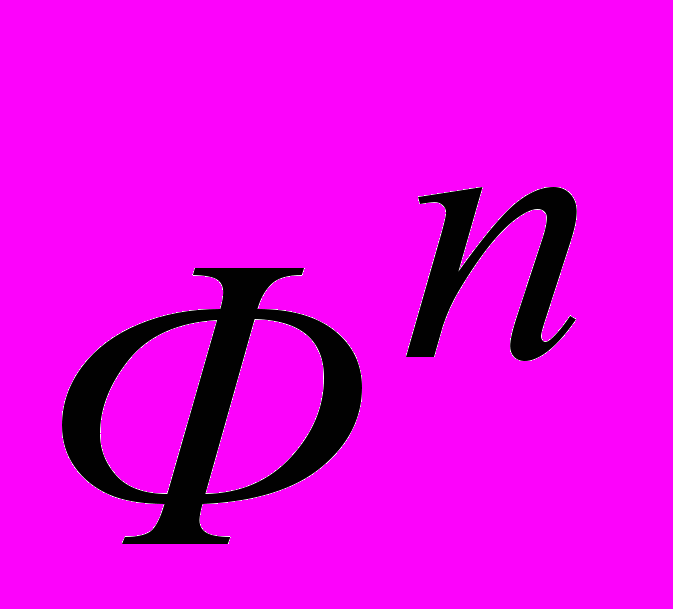
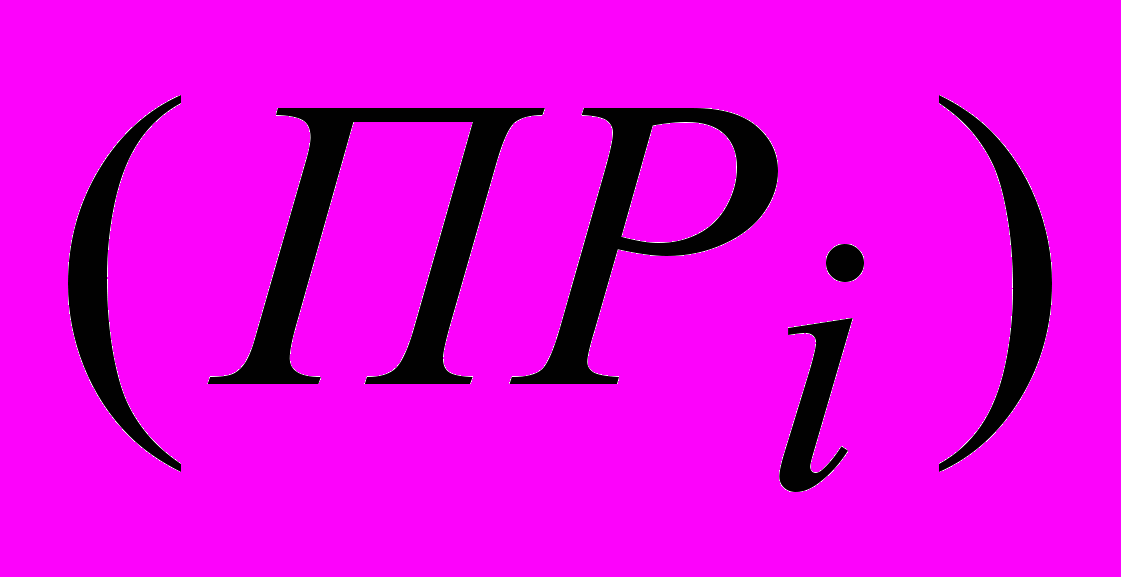
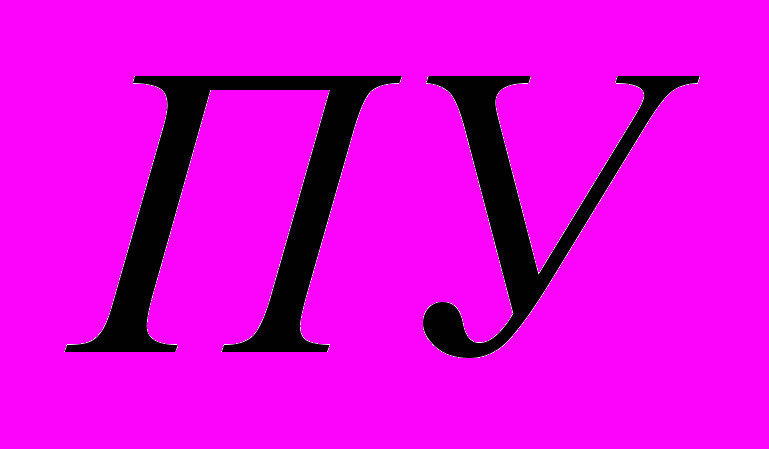

В противоречивых ситуациях предусмотрено вмешательство оператора. Схема работы АССП приведена на рис.6.
Если определение и учет большого числа параметров затруднен, при числе рабочих мест в ТП менее 25-30 (возможна оценка отставаний и выявление причин рассогласования КПГ мастерами), предложено применение диспетчирования на основе аппарата нечетких множеств. Объект управления - КПГ. Управление ведется по входам: 1) относительное объемное отставание (опережение) плана по типу и (или) группе станков с начала диспетчирования; 2) относительное среднее объемное отставание (опережение) плана по типу и (или) группе станков за 1-н ИОП с начала диспетчирования; 3) увеличение (уменьшение) отставания (опережения) объемного плана за последний ИОП по сравнению со средним по типу и (или) группе станков.
![]() |
Рис.6. Схема работы АССП |
Шестая глава посвящена планированию, проведению и анализу результатов апробации, определению степени достоверности предложенных моделей и методов. Учитывая необходимость комплексного подхода к созданию САПР ТП и АССП, выполнены работы по совершенствованию структуры ТП и унификации изготовляемых деталей. В соответствии с классификацией работ, сделанной на основе анализа рабочих и перспективных ТПр изготовления деталей и приборов, предложен состав ТП производственной системы и ее механообрабатывающих подразделений. Предлагаемое оборудование имеет частично общие области по реализации ТПр, что даёт возможность варьировать загрузкой оборудования, и отвечает принципам концентрации, автоматизации и гибкости. Для соблюдения принципа пропорциональности, определение количественного состава оборудования выполнялось анализом станкоемкостей работ, выполняемых по каждому типу и группе станков. Для постепенного уменьшения объема очередей по основному детале-потоку, было обеспечено снижение коэффициента загрузки оборудования по его ходу в пределах 4-6 %. С целью минимизации времени прерывания ТПр, загрузка оборудования на выносных операциях принята меньшей на 20-27%. Пространственная структура ТП формировалась исходя из принципа прямоточности анализом ТПр наиболее трудоёмких в обработке деталей (головки, корпуса и т.д.). Это позволило обосновать и реализовать предложенную функциональную структуру и компоновку (пространственную структуру) ТП на базовом предприятии. Конструкторско-технологическая унификация (КТУ) преследовала 2 цели: сократить время, затрачиваемое на проектирование изделий и создать предпосылки унификации решений в САПР ТП. Проведение КТУ на базовом предприятии позволило достаточно эффективно подойти к проектированию в САПР ТП по методам типизации, и способствовало уменьшению сложности формальных алгоритмов проектирования. Качество проектных решений повысилось за счёт оптимизации элементов технологии для типовых деталей и их поверхностей.
Разработанные методики автоматизированного проектирования и сопровождения ТПр реализованы в виде программно-технического комплекса, связывающего конструкторские подразделения (CAD), технологические службы (САПР ТП), цеховой управленческий персонал (АССП), управленческий персонал (мастеров) ТП и систему управления (СУО) организацией (рис.7.) САПР ТП и АССП могут использоваться автономно, предусмотрена возможность интеграции комплекса с ERP-системами.
На этапе опытной проверки САПР ТП выполнялось моделирование процедур проектирования ТПр для 20 деталей. В качестве примера рассмотрим ТПр обработки детали СТО 8.649.009 (Головка верхняя-2, материал-сталь 40Х13, HRC 28..32) в условиях ООО «Нефтегазгеофизика». Базой сравнения был действующий ТПр (



![]() |
Рис.7. Структура программного комплекса |


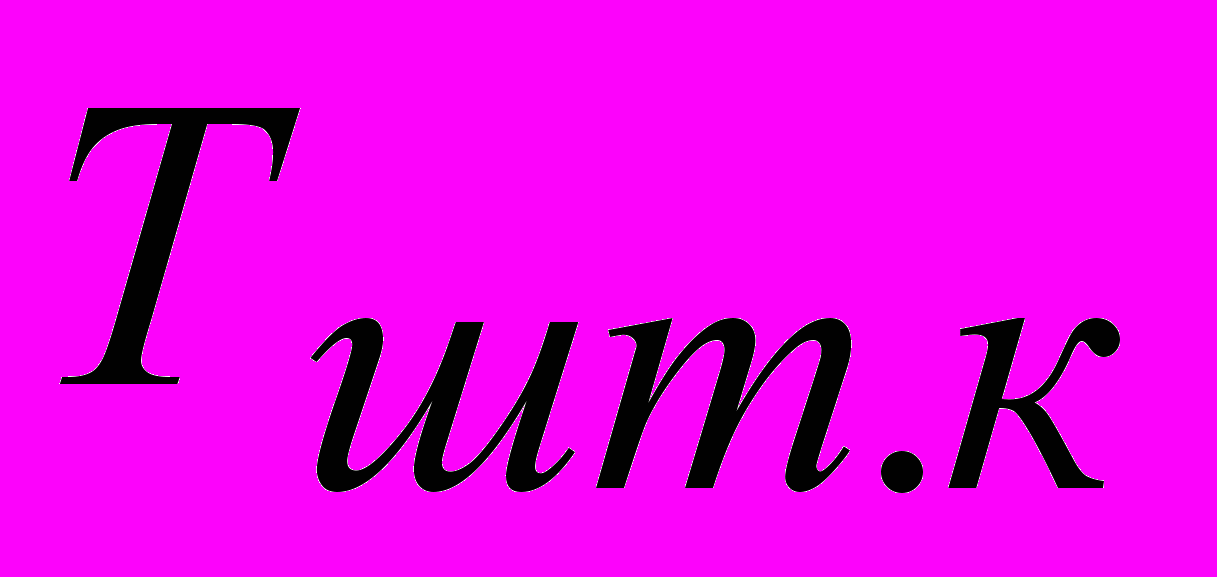





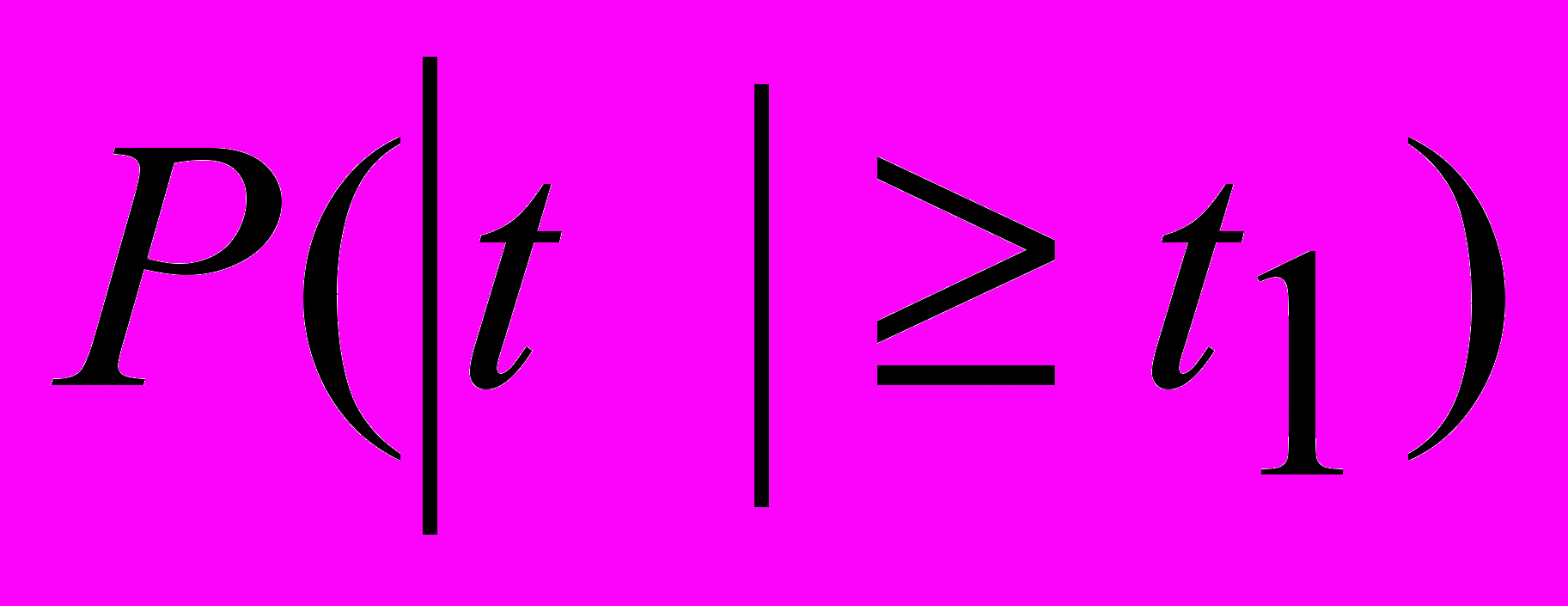
Исследование моделей диспетчирования АССП показало, что они позволяют вводить ТП в плановый режим в 1,5-2 раза быстрее, нежели при применении «ручного управления».
![]() |
Рис.8. Трудоемкость проектирования ТПр деталей средней сложности |
Опытная эксплуатация программно-технического комплекса в 2009-10 гг. показала, что сокращение времени проектирования ТПр обеспечивалось до 3-4 раз (рис.8, 1-й столбец-база; 2-й-перепроектирование по методу типизации; 3-й -проектирование единичных ТПр) по сравнению с базой (программные средства T-Flex) при высоком качестве технологий (брак при изготовлении уменьшен в 1.9 раза). Проанализирована ожидаемая точность и откорректированы 68 ТПр, спроектированным ранее. У 13 из них (порядка 20%), точность размеров обеспечивалась с вероятностью от 74 до 88%. Предложено изменить размеры заготовок для основных деталей, что обеспечило сокращение их материалоемкости до 8%.
![]() |
Рис.9. Результаты работы ТП |
В заключение приведена общая характеристика, основные результаты работы.
ОСНОВНЫЕ РЕЗУЛЬТАТЫ
В ходе выполнения исследования получены результаты, обеспечивающие решение крупной научно-технической проблемы, имеющей важное значение для отечественной промышленности и хозяйства: создание теоретических основ для построения систем и применения методов автоматизированного проектирования технологических процессов и сопровождения производства изделий, позволяющих осуществить автоматизацию и интеллектуализацию решения задач, а именно: для предложенного в работе интегрированного организационно-технологического проектирования в производственных системах геофизического приборостроения разработаны:
1. Теоретико-множественные модели производственной системы, САПР ТП и АССП, построенных на основе системных отношений и категорий «часть-целое», «система-подсистема», «целостность-разобщенность», «внешняя среда», «подчиненность целей», «преемственность структур», позволяющие информационно описать процессы технологической подготовки и выпуска изделий, получить новые системные свойства при проектировании ТПр и сопровождении производства изделий, и определить функции, структуры и параметры решений в САПР ТП и АССП.
2. Модель процесса проектирования в САПР ТП, отвечающая выявленным системным принципам преемственности структур, целостности и разобщенности, взаимосвязи и взаимообусловленности, связи с внешней средой, включающая: модели и структуры проектируемого объекта на различных уровнях декомпозиции с соответствующими системными характеристиками, определяющими пространства поиска решений; модели и структуры процесса осуществления проектных процедур: иерархическую 4-х уровневую структуру (способ декомпозиции), модели представления знаний для синтеза решений соответствующего уровня декомпозиции, модели поиска решений (последовательность преобразования одного пространства поиска решений в другое), способы оценки решений, обобщения и накопления опыта проектирования, модель технологичнских подразделений, логико-функциональную структуру (функции и последовательность выполнения проектных процеду), информационную структуру (модели обмена информацией).
3. Принципы построения САПР ТП и АССП, определяющие их информационную интеграцию, связи с ТП и СУО, наличие элементов ИИ, иерархичность и способ оценки решений, интеграцию в единое информационное пространство, и детализируемые: 1) для САПР ТП - а) принципами декомпозиции процесса проектирования, б) принципами разработки системы критериальных оценок, в) методикой структуризации и формализации знаний на основе иерархических системно-технологических положений, отражающих технологические, организационно-экономические и системные закономерности проектирования ТПр, и определяющих базу знаний продукционных моделей, логических, оптимизационных и интуитивных функций, обеспечивающих синтез решений и накопление опыта проектирования в САПР ТП; 2) для АССП - а) принципами разработки приоритетных схем, б) принципами планирования и управления.
4. На основе выявленных принципов построения САПР ТП методика автоматизированного организационно-технологического проектирования для единичных технологических процессов и по методу типизации, состоящая в формальном представлении: проектных процедур на уровнях синтеза укрупненных схем, маршрутной и операционной технологии, разработке управляющих программ для станков с ЧПУ; процедур оценки решений на уровнях системами критериев, зависящими от целевой функции производственной системы, состояния ТП и параметров технологии рассматриваемого уровня декомпозиции; способов модификации решений при изменении загрузки оборудования и целевой функции.
5. Система моделей для информационного обеспечения АССП, включающая: функциональное описание уровней сопровождения, логическую схему взаимосвязи проектных процедур, иерархические системы приоритетов для разработки календарных планов-графиков прохождения деталей по операциям на основе иерархических приоритетных схем, способы осуществления проектных процедур, способы распознавания ситуации в ТП, нечеткое управление.
6. Методика автоматизированного сопровождения процессов изготовления приборов, соответствующая системе планов организации и основанная на: систематизации и формализации процедур расчета на уровнях объемного, календарного, оперативного планирования и диспетчирования; интервальной критериальной оценке, обеспечивающей реализацию обратных межуровневых связей, автоматический переходе от одного уровня сопровождения к другому и в режим диалога; оперативном планировании и диспетчировании на основе интервального метода и распознавания ситуации в технологических подразделениях.
7. Предложены методики и элементы программных средств по проектированию ТПр (зарегистрирована программа для ЭВМ) и сопровождению процессов изготовления приборов, отражающие выявленные принципы создания САПР ТП и АССП и предложенную методологию автоматизированного проектирования и обеспечивающие формализацию и интеллектуализацию процедур синтеза решений. При модификации, методики могут быть использованы в других областях единичного и мелкосерийного машиностроения.
ОСНОВНЫЕ РЕЗУЛЬТАТЫ ОПУБЛИКОВАНЫ: