Керамические материалы и изделия
Вид материала | Документы |
СодержаниеГлина для связки Охрана окружающей среды в ТСМ Пылеосадительные камеры – Пластическое формование. |
- Группа 69 керамические изделия примечания, 104.42kb.
- Лекции по курсу «композиция в технике», 590.8kb.
- 1. классификация и общие свойства керамических строительных материалов и изделии, 267.69kb.
- Керамические строительные материалы боспора в эпоху эллинизма (типология и хронология, 459.36kb.
- Безобжиговые строительные материалы и изделия на основе бесклинкерных и малоклинкерных, 607.91kb.
- Вопросы к итоговому контролю и для самостоятельной работы, 25.17kb.
- Xxxii российскую конференцию по проблемам науки и технологий, 44.39kb.
- Отпускные цены на основные строительные материалы, изделия и конструкции, производимые, 2880.69kb.
- Показателей качества продукции. Строительство, 69.52kb.
- Теплоизоляционные строительные материалы на основе низинных торфов Томской области, 275.61kb.
Требования предъявляемые к огнеупорам
- Огнеупорность – способность материала противостоять, не разрушаясь действию высоких температур.
Показатель огнеупорности: t0, под влиянием которого образец спец. формы (трехгранная усеченная пирамида h=30 мм со сторонами нижнего основания 8 мм и верхнего – 2 мм, т. е. конус Зегера. Деформируется так, что его вершина касается основания. Огнеупорность определяют в сравнении со стандартными конусами – пироскопов. Огнеупорность материала считается равной огнеупорности того пироскопа, который при испытаниях коснулся основания одновременно с испытуемым образцом. Пироскопы изготавливают с t до 2000 0С с интервалом 20-40 0С. Численное значение t0 падения пироскопа соответствует его номеру, увеличенному в 10 раз (177·10=1770 0С).
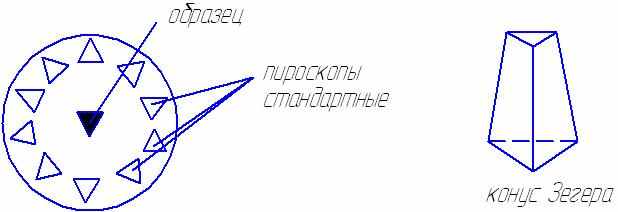
- Ползучесть при сжатии (крип) – определяется изменением линейных размеров образца d = 36 мм и h = 50 мм, подвергнутого действию постоянной сжимающей нагрузки и постоянной температуры в течении заданного времени.
- Испаряемость (кг/м2·с) – заметное испарение начинается с 1700 0С. Наиболее сильно испаряется магнезиальные огнеупорные материалы.
- Газопроницаемость – зависит от количества сквозных пор, их размера и формы. С повышением температуры газопроницаемость уменьшается.
- Шлакоустойчивость – способность огнеупоров противостоять действию расплавляющихся шлаков, стекла и других материалов, соприкасающихся с огнеупором в процессе службы;
- Термическая стойкость – способность материалов выдерживать без разрушения резкие колебания температур. Определяется количеством теплосмен, которые может выдержать изделие до потери 20% своей первоначальной массы. При нагревании торцевой его части до 1300 0С, с последующим охлаждением раскаленной части изделия в проточной воде.
Изделия изготавливаются полусухим прессованием более термостойкие, чем изделие сформованные пластическим способом.
- Теплопроводность – зависит от химико-минералогического состава материала и его структуры.
- Теплоемкость;
- Температуропроводность;
- Электрическое сопротивление;
- Правильность формы и точность размеров.
Алюмосиликатные огнеупоры.
Система Al2O3-SiO2.
Получение шамота
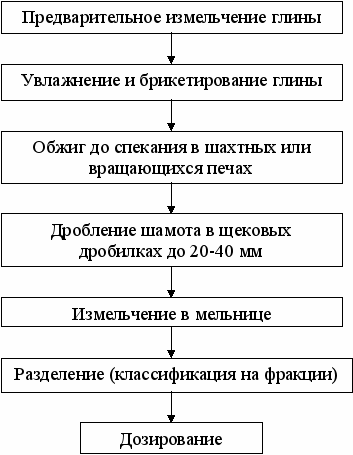
Глина для связки
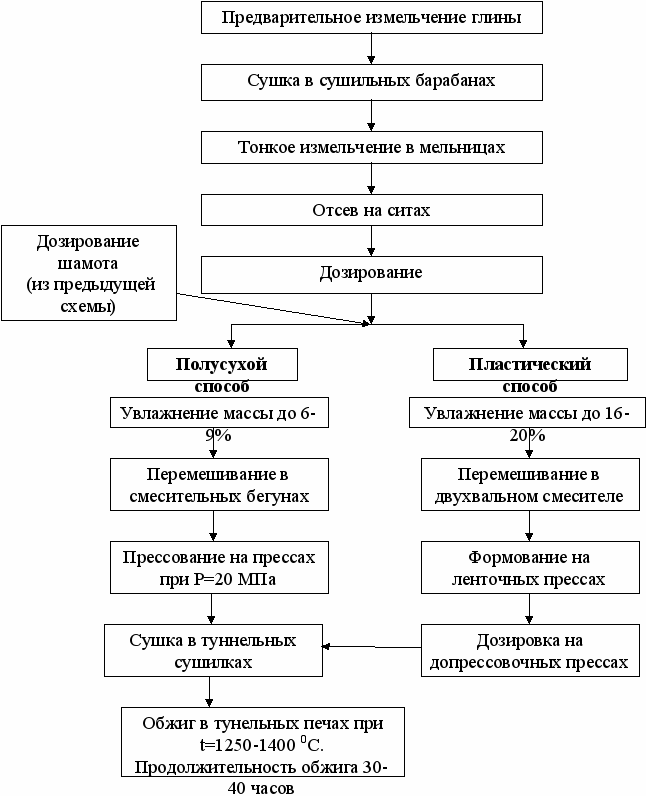
Различают следующие виды алюмосиликатных огнеупоров:
а) низкоглиноземистые (полукислые) с содержанием Al2O3 < 28%;
б) среднеглиноземистые (шамотные) – Al2O3 = 28-45%;
в) высокоглиноземистые – Al2O3 > 45%.
Охрана окружающей среды в ТСМ
Силикатная промышленность перерабатывает огромные объемы различных видов твердого сырья, использует тысячи и тысячи кубометров воды. Часть перерабатываемого сырья и воды в процессе производства попадает в виде различных отходов в помещения цехов и в окружающую среду, негативно действуя на условия труда работающих, повышая экологическую напряженность в районе размещения предприятий. Предприятия силикатной промышленности, особенно цементные и известковые, требуют повышенного внимания экологов. Радикальный путь, обеспечивающий охрану природы, создание малоотходных и безотходных технологий. Эта задача решается по нескольким направлениям:
- создание принципиально новых процессов получения традиционных видов продукции без образования отходов;
- создание бессточных технологических производств на основе рекуперационных методов очистки сточных вод;
- создание производств, использующих отходы как вторичные материальные ресурсы;
• создание территориально-промышленных комплексов с замкнутой
структурой материальных потоков сырья и отходов внутри комплексов с
минимумом выбросов в окружающую среду.
Образование побочных продуктов производства – процесс неизбежный. Задача состоит в том, чтобы по возможности снизить их объемы и не допустить попадания в окружающую среду. Все побочные продукты в зависимости от их агрегатного состояния могут быть сведены в три группы: твердые, жидкие (производственные сточные воды) и пылегазовые выбросы. В зависимости от их агрегатного состояния по-разному решаются и вопросы по защите окружающей среды от их влияния.
Наиболее распространенными видами твердых отходов являются стекольный бой и бой керамических изделий. В ряде случаев их направляют в отвалы, что нежелательно. Важнейшим способом снижения экологической напряженности является возврат твердых отходов в процесс производства. Стекольный бой обычно вводят в шихту в количестве до 20%. Это позволяет не только уменьшить объем отходов и снизить расход природных ресурсов, но и сократить расход энергии на производство стекла. Подготовка стеклобоя сводится к его сортировке и дроблению. Другим направлением использования стеклянного боя является получение новых материалов, например, путем наполнения смол или цемента измельченным стеклом. Из такого материала изготовляют панели, фланцы для груб, покрытия для пола.
Воду в технологии ТНСМ применяют для охлаждения оборудования (технологического, энергетического, вентиляционного), для подготовки материалов и приготовления шихты, для бытовых целей. В зависимости от дальнейшего использования воды меняются требования к ее качеству. Так, вода для охлаждения оборудования должна иметь температуру не выше 40 °С, карбонатную жесткость 1 -3 мг.экв./л и концентрацию взвешенных веществ не более 30 мг/л. Вода, используемая для промывки песка, не должна содержать химических примесей, вредно действующих на стекломассу. Жесткость и содержание железа должно быть как в питьевой воде.
Сточные воды керамического и стекольного производств загрязнены как взвешенными частицами, так и растворенными веществами. Например, в сточных водах составных цехов стекольных заводов содержится песок, сода, мыло, глинистые вещества; в сточных водах производства листового стекла – стеклянная крошка, абразивные материалы; в сточных водах производства стекловолокна – следы органических смол. В сточных водах производств сортовой посуды содержится фтор, при химической полировке хрусталя туда попадают фтор и свинец.
Защита водных источников от загрязнений обеспечивается сокращением потребления воды, уменьшением сброса сточных вод в водоемы, созданием замкнутых систем водоснабжения, предполагающих многократное применение воды с извлечением и переработкой всех примесей. В замкнутых оборотных системах предусматривается охлаждение воды и ее очистка. Сброс сточных вод в водоем не предусматривается. Потери покрываются свежей водой из водоема.
Для удаления грубодисперсных загрязнений (кусков шихты, камней и т.д.) сточную воду процеживают через решетки и сита. Песок и другие минеральные частицы выделяют осаждением в песколовках, представляющих собой горизонтальные отстойники, в которых сточная вода движется со скоростью 0,15-0,3 м/с. При таких скоростях 65-70% частиц песка в сточных водах осаждается под действием силы тяжести.
Для удаления тонкодисперсных взвешенных частиц чаще всего к сточным водам добавляют химические реагенты, которые вступают в реакцию с загрязнениями и способствуют коагуляции и выпадению нерастворимых коллоидных веществ. Для коагуляции сточных вод, загрязненных глиной, в качестве коагулянта применяют сернокислый алюминий с подщелачиванием известью. Чем выше рН среды, тем меньше доза коагулянта. Для интенсификации процесса образования хлопьев гидроксидов алюминия добавляют флокулянты. Они ускоряют слипание агрегативно-неустойчивых частиц и повышают прочность хлопьев. В качестве флокулянта наиболее широко используют полиакриламид. Коагулированные хлопья отделяются в гидроциклонах или на фильтрах (сетчатых или с зернистым слоем). Для удаления мелких твердых частиц используют также процесс флотации, основанный на способности частиц прилипать к пузырькам воздуха в водной среде и переходить с ними в пенный слои.
Особую сложность представляет очистка сточных вод, содержащих токсичные соединения. Так, при производстве хрусталя в сточные воды попадают свинец, плавиковая, кремнефтористая, серная кислоты и их соли. Для очистки сточных вод от этих соединений используют реагентные, сорбционные и ионообменные методы. Для сорбции фтора применяют активированный уголь и свежевыделенные осадки гидроксида магния и фосфата кальция. Для ионного обмена пригодны сильноосновные аниониты, гидроксилапатит и др. Однако в большинстве случаев фторсодержащие соли нейтрализуют суспензией мела или гидроксидом кальция. В результате соединения фтора переходят в трудно растворимый фторид кальция. После осаждения осадок обезвоживают на вакуум-фильтре и направляют в большинстве случаев, осадки сточных вод утилизировать в производстве не удается, и они подлежат захоронению. Однако при очистке загрязненных вод керамических заводов образуется осадок в виде частичек глины, который можно утилизировать. Осадок глины уплотняется медленно и через сутки имеет влажность порядка 85% и рыхлую структуру. Наиболее совершенным способом удаления осадка за пределы очистных сооружений является перекачка по напорным трубам. Перед очисткой отстойника нужно слить осветленную воду. Осадок перекачивают на обезвоживание и в виде кека подают на склад.
Источником загрязнения воздушной среды прежде всего является сжигаемое топливо. При неполном сжигании выделяется угарный газ, а при использовании мазута – дополнительно сернистый и серный ангидриды. Загрязненность воздуха угарным газом и двуокисью серы в сушильном отделении кирпичного завода составляет соответственно 1,3 и 2 ПДК, а в цехе обжига кирпичей – 2 и 3 ПДК.
Наиболее опасные газовыделения связаны со стекольным производством. Применение фторидов для ускорения варки и глушения стекла способствует выделению фтористых соединений в атмосферу. В отходящие газы поступает 33-50% введенного в шихту фтора. Фтористые соединения выделяются также при химической полировке хрусталя. Для устранения выбросов фтора в окружающую среду заменяют фтористое сырье бесфтористым, а газовое и жидкое топливо электроэнергией, а также применяют сухую или мокрую очистку отходящих газов. Мокрые методы более эффективны. Фтористые соединения улавливаются водой или щелочными растворами.
Степень очистки в скрубберах, орошаемых водой, 60%, в пенных адсорберах – 96-98%. Образующаяся в процессе кислая вода нейтрализуется.
По сухому методу фтористые газы улавливаются порошком гидроксида кальция. В результате реакции образуются фториды кальция. Степень улавливания достигает 99%. Образующиеся частицы фторидов выносятся отходящими газами из камеры улавливания в рукавный фильтр, где отделяются от газового потока. После этого они снова используются в производстве.
Однако основной загрязняющий фактор при воздействии силикатной промышленности на окружающую среду – это пыль, возникающая при приготовлении сырьевых смесей, дозировании, перемешивании, тонком измельчении и особенно сушке и обжиге сыпучих материалов. Пыль силикатных производств имеет высокую дисперсность (количество частиц размером менее 5 мкм доходит до 60%) и содержит значительное количество свободного оксида кремния. Степень допустимой запыленности воздуха регламентирована санитарными нормами. Она составляет для пыли, содержащей более 70% свободного оксида кремния, не более 1 мг/м3 для пыли, содержащей 10-70% SiO2 не выше 2 мг/м3 для пыли цемента, глиняных минералов, не содержащих свободной SiO2 6 мг/м3.
В то же время, например, при производстве кирпича наибольшее пылевыделение наблюдается на складах, в смесеприготовительном отделении (12-15 ПДК), а в отделении помола шамота достигает 30-32 ПДК. Даже на участках погрузки и разгрузки кирпича запыленность в 2-3 раза превышает допустимые концентрации. Причины повышенного загрязнения воздуха – отсутствие надежной герметизации технологического оборудования, местных отсосов, вакуумной пылеуборки, эффективной обменной вентиляции. Поэтому транспортирующие средства для пылящих кусковых и порошкообразных материалов и пылящее оборудование должны устанавливаться в герметически закрытых кожухах. На всех участках пыления должен предусматриваться отсос воздуха и его очистка перед выбросом в атмосферу. В каждом производстве существуют и свои специфические способы уменьшения пылевыделения. Например, в стекольном производстве увлажняют шихту водой, содержащей ПАВ, или гранулируют шихту, переходят на варку стекла в электропечах и т.д. Однако во многих технологических процессах пылевыделение и пылевынос –явления неизбежные. Аспирационный воздух в сырьевых или цементных мельницах увлекает за собой тонкомолотые частицы. Горячие газы, просасываемые через сушильный барабан, также уносят образующуюся пыль. Особенно мощный источник пылевыделения – цементные вращающиеся печи. Пылевынос в печах сухого способа – 25-30%, мокрого способа – 10-20%. Пылевынос не означает пылеунос, так как пылевыделяющее оборудование в обязательном порядке оборудуется системами пылеочистки, позволяющими снизить безвозвратный пылеунос для печей – до 1%, для мельниц – до 0,5%. Применяют разнообразные типы пылеуловителей, принцип действия которых основан на использовании гравитационных, инерционных и электростатических сил. Выбор пылеулавливающих аппаратов определяется в первую очередь их эффективностью. Как правило, в одном аппарате невозможно добиться полной очистки воздуха или горячих газов от пыли. Очистку технологических пылегазовых смесей производят в несколько стадий. Чаще всего применяют пылеосадительные камеры (грубая очистка), сухие и мокрые циклонные аппараты (первая ступень очистки), тканевые рукавные фильтры и электрофильтры (окончательная очистка).
Пылеосадительные камеры – простейшие устройства для улавливания пыли. Чтобы снизить скорость движения газов до 0,1-0,2 м/с, камеры должны иметь достаточно большие размеры. Запыленный воздух просасывается через камеру, и вследствие уменьшения скорости воздушного потока пыль оседает под действием силы тяжести. Ее удаляют периодически или непрерывно при помощи разгружателей. Пылеосадительные камеры используют главным образом для очистки отходящих газов вращающихся печей. У мельниц роль пылеосадительной камеры выполняет аспирационная шахта. Такие устройства улавливают только наиболее грубодисперсную пыль. Коэффициент очистки газа от тонкой пыли не превышает 10-15%. Циклоны используют для очистки газов от пыли с частицами размером более 6 мкм. Поступающий в циклон запыленный газ, проходя по спирали, приобретает вихревое движение. Частицы пыли, проходя по спирали отбрасываются к стенкам, ссыпаются в коническую часть и удаляются через патрубок. Очищенный газ выходит из циклона через верхний патрубок. Степень очистки газа в циклоне достигает 90-97%.
Электрофильтры улавливают частицы размером от 0,1 до 100 мкм. Принцип очистки газа в электрофильтре основан на заряжении взвешенных газов под действием электрического поля высокого напряжения (до 105 В). Заряженные частицы перемещаются в воздушном потоке к электроду противоположного знака, оседают на нем, периодически стряхиваются и удаляются. В оптимальных условиях степень очистки газов в электрофильтрах превышает 99%. Электрофильтры имеют большую производительность, небольшое гидравлическое сопротивление и способны очищать газы при высоких температурах. К недостаткам электрофильтров следует отнести высокие капитальные затраты, потребность в значительных производственных площадях, высокую чувствительность к изменениям параметров процесса, ограничения в применении по удельному электрическому сопротивлению частиц и влажности газов.
Действие рукавных тканевых фильтров основано на том, что газ пропускается через тонкие ячейки ткани, а частицы пыли задерживаются на ее поверхности. Тканевые фильтры обладают высокой эффективностью, которая практически не зависит от вида пыли, ее химического и гранулометрического состава. Они способны улавливать частицы размером до 0,01 мкм. В фильтрах применяют различные тканевые материалы. Новым направлением является использование электростатически заряженных волокон. При этом газ сначала проходит через коронирующие отрицательно заряженные электроды, где частицы пыли заряжаются, а затем осаждаются на волокнах полотна. Степень очистки в таких фильтрах 99,9%.
В каждом производстве должен решаться вопрос о возможности утилизации уловленной пыли, возврате ее в технологический процесс, как правило, в состав сырьевой шихты.
Пластическое формование.
Пластическое формование базируется на свойстве глин образовывать с водой тестообразные массы, способные к пластичному течению, т. е. к изменению формы под воздействием внешних усилий без разрыва сплошности. Пластичные формовочные массы – высококонцентрированные суспензии дисперсионных минеральных частиц (влажность 18-24%).
Массы имеют коэвалюционную структуру. Они отличаются тиксотропностью т. е. способностью после снятия внешнего воздействия, приведшего к разрушению структуры, самопроизвольно ее восстанавливать. Способы пластического формования, применяемые в ТК можно разделить на 3 группы:
- выдавливание или экструзия массы. Выдавливаемая из пресса масса через формующий мундштук приобретает заданные очертания (керамический кирпич, трубы);
- допресовка или штампование – обжатие заготовки, помещенной в форму при поступательном движении прессующего штемпеля (черепица, кислотоупорный кирпич);
- раскатка в тела вращения – основана на постепенной деформации вращающейся заготовки, при нажатии на нее формующего шаблона (чашки, посуда, электроизолятор).
Выдавливание осуществляющееся на шнековых или поршневых прессах. Наиболее распространено ленточное формование на горизонтальных шнековых прессах, в которых материал не только транспортируется и уплотняется, но также интенсивно переминается и гомогенизируется.
Структура формуемых в прессе масс представляет собой напластование вложенных друг в друга рядов полых конусов; внутренние слои выталкивающие бруса перемещаются быстрее, чем наружные, испытывают большее трение.
Штампование.
Штамповку изделий производят на револьверных и других прессах из заготовок, сформованных предварительно на ленточных вакуум-прессах. Главная цель штампования получить полуфабрикат необходимой формы с точными размерами, качественной поверхностью и четкими углами. Давление при допресовке в формах мало, так как оно должно лишь обеспечить равномерность заполнения формы массой, а не уплотнить ее, поскольку пластичная масса сама по себе очень трудно сжимаема.
Раскатка.
Формование раскаткой ведут в гипсовых или пластмассовых формах с помощью формующих шаблонов, врезающихся штемпелей или роликов. Если шаблон формует внутреннюю поверхность изделия, то такой способ называется «формованием в форму», а если внешнюю – то «на форму». Порция керамической массы под нажимом шаблона, имеющего профиль, и являющийся зеркальным отображением требуемой формы, равномерно распределяется на поверхности гипсовой формы. Избыток массы вытесняется, образуя «бахрому» над верхней кромкой, которая в конце формования срезаемая специальным резцом. Избыток влаги из массы отсасывается в ходе формования в пористой гипсовой форме, при этом срез несколько уплотняется и приобретает механическую прочность, достаточную для транспортировки и дальнейшей обработки.
П
- Гипсовая форма;
- Масса;
- Роликовый шаблон.
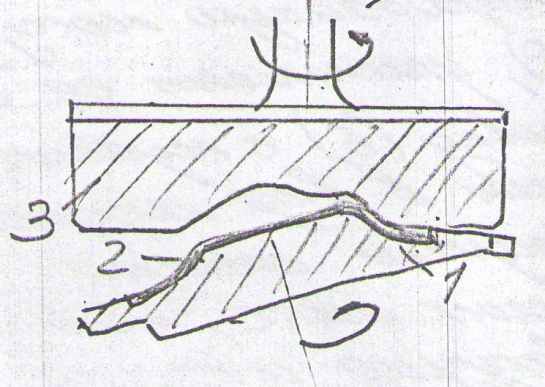
В результате в формуемых изделиях возможно появление различных дефектов. Однородность структуры повышается с ростом влажности массы, при введении крупного наполнителя (песка, или шамота) при пароувлажнении. Одним из недостатков ленточного пресса является значительный захват воздуха массы (до 10% по объему). Этот воздух снижает плотность массы, ее пластичность, вызывает неравномерность уплотнения при формовании, что в конечном итоге приводит к образованию микротрещин. Поэтому желательно удаление вовлеченного воздуха из керамических масс, например вакуумирование в вакуум прессах.
П
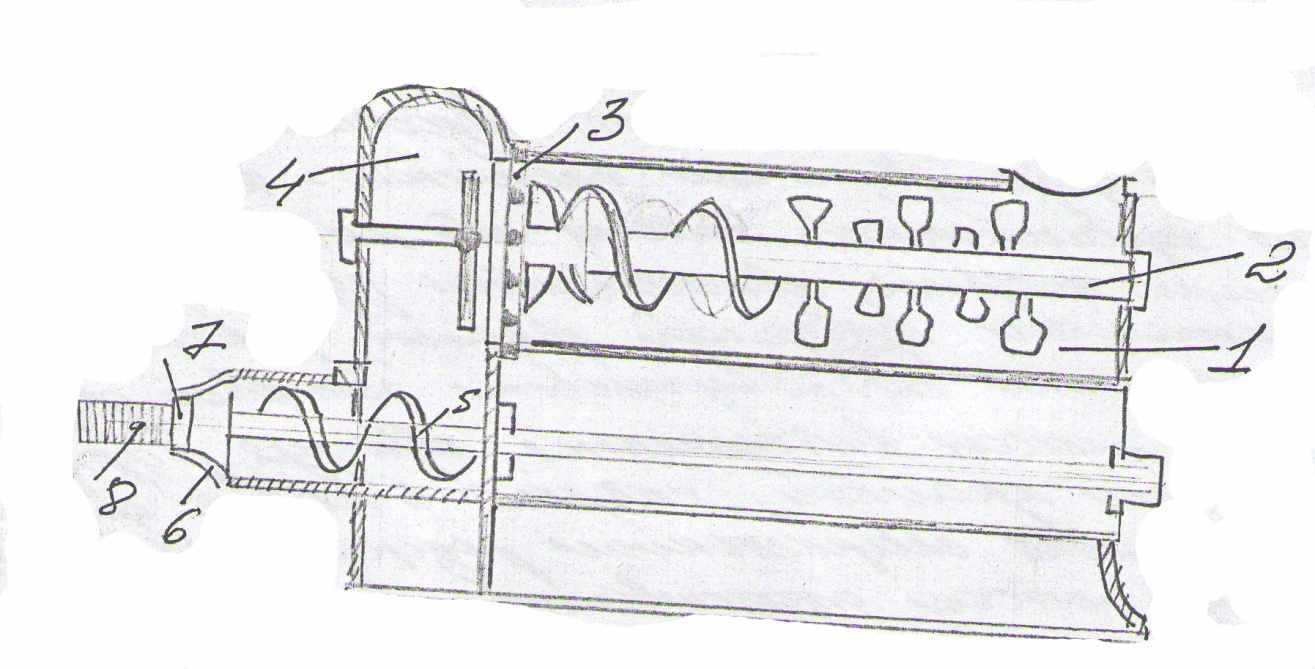
ринципиальная схема ленточного вакуум-пресса
Тестообразная масса разминается в смесительной камере пресса 1 лопастным винтом 2 и продавливается через перфорированную перегородку 3 в вакуум-камеру 4, где под действием разряжения из нее удаляется воздух. Вакуумированную массу подхватывает шнековый вал 5, уплотняет ее и перемещает в прессующую головку 6 с мундштуком 7, откуда масса выходит виде непрерывного бруса 8, заданного мундштуком сечения.
Чем выше пластичность глиняных масс, тем выше должна быть величина вакуума и дольше пребывание массы в вакуумной камере. Прочность высушенного сырца из вакуумированной массы в 1,6 раза выше, чем из невакуумированной. Плотность обожженных изделий увеличивается на 3-5%, водопоглощение снижается на 10-15%, а прочность повышается в 1,5-2 раза.