Ия твердых топлив, по отношению к жидким и газообразным, возрастает главным образом за счет более широкого вовлечения в энергобаланс низкосортных углей [21, 78]
Вид материала | Документы |
- Пермском Прикамье обеспечивается, главным образом, за счет открытия залежей в ловушках, 163.4kb.
- Демонстрационная версия рабочей программы по дисциплине: дс., 40.47kb.
- Программа породненных университетов и кафедр юнеско кафедра юнеско, 207.32kb.
- Активизировать работу учащихся на уроке за счёт вовлечения их в игру, 81.17kb.
- Авлении увеличения масштабов производства химической продукции, так и в направлении, 475.78kb.
- Развивалась также новая область химии физическая химия радиоактивных твердых тел. Совместно, 213.01kb.
- О состоянии профилактической работы, 79.63kb.
- Аналитическая записка по обращению с твердыми бытовыми и промышленными отходами, 582.24kb.
- Аналитическая записка по обращению с твердыми бытовыми и промышленными отходами, 603.31kb.
- Программа спортивно игровой секции «Баскетбол» для детей 12-17 лет (4 года), 350.69kb.
Рис. 5. Схема экспериментального плазмотрона
1 – катод; 2 – анод; 3 – кольцо закрутки плазмообразующего воздуха; 4 – корпус.
5. Технология плазменного розжига и подсветки
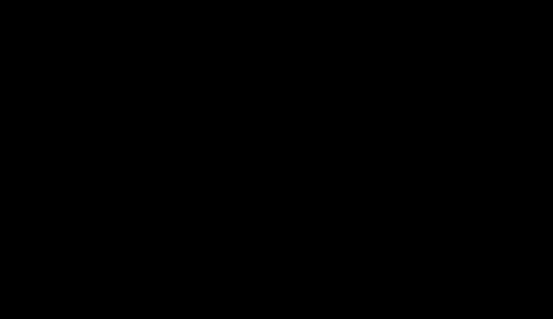
Рис. 6. Принципиальная схема экспериментальной промышленной установки
1 – розжиговая горелка; 2 – основная горелка; 3 – система электропитания плазмотронов; системы подачи: 4 – угольной пыли, 5 – вторичного воздуха, 6 – сжатого воздуха, 7 – охлаждающей воды; приборы измерения: 8 – тока и напряжения на плазмотронах, 9 – давления плазмообразующего воздуха, 10 – охлаждающей воды, 11 – температуры пылеугольного факела.
Выше отмечалось, что сущностью технологии заключается в обработке струей низкотемпературной плазмы (3500…5000 ОС) потока угольной пыли, транспортируемой воздухом. Высокая температура теплового удара приводит к прогреву топлива со скоростью 103…104 К/с при размерах частиц менее 250 мкм, при этом достигается конечная температура чатиц 800…900О С и выше, что интенсифицирует разложение органической части топлива.
Поток плазмы создается в плазмотроне,который может иметь конструкцию аналогичную показанной на рис.5 и может быть вмонтирован в пылеугольную горелку или установлен в специальном муфеле под основной горелкой. Плазмотрон состоит из анода 1, катода 2, кольца закрутки плазмообразующего воздуха 3 и охлаждаемого водой корпуса 4.
На рис.6 показана принципиальная схема промышленной установки, которая была реализована на работающем котле ТП-170 (ст. №4), на одной из нижних горелок (горелка №2), на Новосибирской ТЭЦ-2.
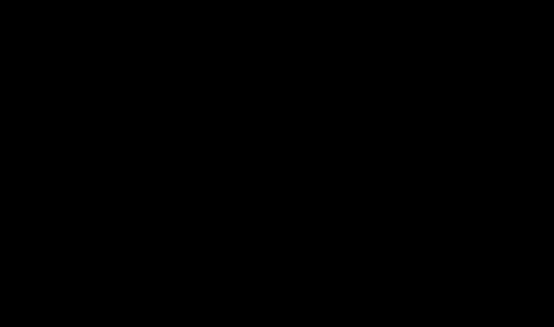
Рис. 7. Розжиговая горелка
1 – канал подачи угольной аэросмеси; 2 – завихритель; 3 – плазмотрон; 4 – камера смешения; 5 – камера воспламенения; 6 – водоохлаждаемый канал термозонда; 7 – термопара зонда; 8 – канал подачи вторичного воздуха для розжига горелки; 9 – завихритель; 10 – основная горелка.
Предложенная экспериментальная установка, состоит из розжиговой горелки 1, встроенной в основную горелку 2, системы электропитания плазмотронов 3, регулирующих систем подачи в розжиговую горелку пылеугольной аэросмеси 4, вторичного воздуха 5, сжатого воздуха 6, охлаждающей воды 7; приборов: контроля тока и напряжения 8, давления и расходов плазмообразующего сжатого воздуха и воды на охлаждение плазмотронов и термозонда в розжиговой горелке для измерения температуры факела от места ввода плазмы в поток угольной аэросмеси до выхода в топку 9, 10, 11 соответственно, рис.6.
Конструкция розжиговой горелки показана на рис.7.
Розжиговая горелка, встроенная в основную горелку, состоит из центрального канала для подачи пылеугольной аэросмеси 1, съемного завихрителя 2, двух подвижных плазмотронов 3, расположенных у среза канала и параллельно его оси, камеры смешения плазмообразующего газа с потоком пылеугольной аэросмеси 4, камеры воспламенения в виде канала, стенки которого ошипованы и покрыты корундовой обмазкой 5, термозонда, состоящего из водоохлаждаемого канала 6 и встроенной в него термопары 7, канала подачи вторичного воздуха 8 и завихрителя 9.
Выполненные экспериментальные работы и исследования в промышленных условиях на опытно-промышленном стенде позволили получить необходимую информацию и сделать следующие выводы для совершенствования элементной базы технологии:
- При розжиге прямоточные струи воспламеняются при меньших мощностях плазменных струй по сравнению с закрученными. Это можно объяснить тем, что в нижней зоне камеры смешения (см. рис. 7) наблюдается повышенная локальная концентрация угольной пыли под влиянием силы тяжести.
- В режиме стабилизации горения для закрученной и прямоточной струй требуется примерно одинаковая мощность плазменной струи, а в режиме розжига требуется на 20% меньше первичного воздуха для закрученной струи по сравнению с прямоточной. Закрученный горящий факел способствует наиболее полному заполнению горелки на выходе в топку, тогда как прямоточный входит в топку отдельными языками- не заполняя всего сечения горелки.
- Проведенные эксперименты показали, что в режиме розжига отношение мощности плазменной струи к мощности воспламеняемой пылеугольной аэросмеси составляет в среднем 0,35%, а в режиме стабилизации 0,25% как для вихревой, так и для прямоточной горелок.
- Наименьшие затраты (около 12 – 13 кВтч/т у.т.) получены при концентрациях угольной пыли в пределах = 1,3 – 1,6 кг/кг и выходе летучих веществ VГ = 18…24%. При уменьшении концентрации угольной пыли до 0,4 кг/кг затраты электроэнергии на подсветку пылеугольного факела резко возрастают от 12 – 13 до 30 кВтч/т у.т.
- С увеличением выхода летучих и концентрации угольной пыли энергозатраты на подсветку пылеугольной аэросмеси уменьшаются и при концентрации угольной пыли = 1,2 кг/кг становятся минимальными и меньше зависят от вы хода летучих сжигаемого угля.
Кроме технических решений была получена информация системно-технологического характера:
- Применение плазменной технологии увеличивает возрастание электроэнергии на собственные нужды станции, но отпуск электроэнергии с шин не уменьшится вследствие сжигания дополнительного угля для выработки соответствующей электроэнергии на питание плазмотронов.
- С учетом соотношения цен на мазут и уголь переход к схеме плазменного розжига и подсветки приводит к удешевлению затрат на растопочное топливо в 1,3 раза.
- Важной задачей, требующей всестороннего рассмотрения, является дальнейшая разработка простых и надежных плазмотронов, пригодных для длительной безостановочной эксплуатации на ТЭС. С этой точки зрения необходимо еще продолжить исследовательские и конструкторские поиски для выявления оптимального варианта плазменно-дугового устройства для розжига и стабилизации горения пылеугольной аэросмеси. Это могут быть плазменно-дуговые устройства на постоянном или переменном токе с закрытой или открытой дугой. В системном плане низкий ресурс плазмотронов и недостаточная надежность электроснабжения технологии плазменного розжига и подсветки требуют структурного резервирования для сохранения уровня надежности функционирования котла. Структурное резервирование обуславливает увеличение капиталовложений в технологию в два раза. С учетом затрат на плазменную технологию капиталовложения в электрическую часть ТЭЦ увеличиваются в 1,1 раза.
- Актуальной проблемой также является разработка надежной экономичной системы автоматического управления плазменно-электродуговыми устройствами, работающими по параллельной схеме от одного источника электропитания, так как число пылеугольных горелок на современных котлах составляет от 4 – 6 до нескольких десятков.
- В связи с увеличением теплонапряженности горелок котла учтено также снижение на 3% коэффициента готовности.
6. Обобщение перспектив развития природоохранных технологий
Проведенный таким образом анализ современных и перспективных систем очистки от выбросов вредных веществ показал, что в условиях, когда одним из основных источников производства электроэнергии и тепла продолжают оставаться теплоэлектроцентрали, и в условиях прогнозируемого роста потребления твердых горючих ископаемых при высоком фоновом загрязнении окружающей среды, сложившемся в крупных промышленных регионах (в частности, в районе КАТЭКа) наряду с использованием традиционных технологий по обеспечению экологической чистоты ТЭС, необходимо создание новых технологий. При этом химические методы очистки дымовых газов не могут считаться безусловно перспективными из-за большого количества недостатков.
Из систем, обеспечивающих совершенствование топочных процессов с целью снижения вредных выбросов, перспективны малозатратные технологии к которым в первую очередь можно отнести тармоподготовку топлива и плазменный розжиг и подсветку основного пылеугольного факела ввиду их технологичности, простоты, дешевизны и возможности использования даже на действующих энергетических установках.
В то же время, необходимо отметить, что современные энергетические объекты являются крупными комплексами, которые имеют разностороннее влияние на многие сферы жизни и деятельности общества. При этом такие объекты тесно взаимоувязаны с потребителями производимой продукции, с поставщиками сырья и между собой, и образуют энергетические системы с большим количеством экологических, социальных и технологических связей. Последние во многом определяют структуру и технологический профиль самого энергетического объекта как с точки зрения целесообразности его размещения в той или иной энергосистеме, так и с точки зрения оптимизации его внутрицикловых параметров. Это означает, что при проектировании и разработке новых и перспективных технологий по производству энергопродукции следует учитывать технологические, экологические, экономические и социальные факторы, которые выражают разную сущность, а потому могут иметь разную, не всегда согласующуюся между собой размерность.
Поэтому следует помнить, что кроме технических аспектов проблемы существует и ряд методических проблем к которым можно отнести следующие:
- Разработку методик технико-экономических расчетов и оптимизации экологически перспективных энергоблоков как с новыми технологиями, так и с технологиями денитрации и десульфаризации дымовых газов. При этом следует исходить из комплексного учета обеспечения графиков нагрузки, заданной надежности энергоснабжения, возможных режимов работы в энергосистеме и современных требований к инфраструктуре (экологической, социальной, производственной).
- Обобщение результатов исследований экспериментальных и опытно-промышленных установок с перспективными технологиями и установок с химической очисткой дымовых газов по выходу, составу, свойствам и характеристикам получаемых продуктов.
- Комплексная оптимизация экологически перспективных ТЭС с целью получения рекомендаций по выбору параметров процессов и характеристик оборудования.
- Определение технико-экономической эффективности оптимального профиля и рационального направления развития ТЭЦ в новых и перспективных экономических условиях.
В то же время, разрабатываемые на период до 10…12 лет мероприятия должны соответствовать современным технически осуществимым и экономичестки целесообразным методам снижения токсичных выбросов, условиям энергоснабжения района и не должны приводить к снижению надежности оборудования.
При выборе способов уменьшения загрязнения атмосферы выбросами действующих ТЭС и котельных должен быть рассмотрен широкий круг мероприятий различного характера, в том числе:
- изменение качества топлива – ограничение содержания серы, применение при особо неблагоприятных условиях малосернистого мазута или природного безсернистого газа;
- переход на технологии не требующие использования мазута;
- изменение режима работы и состава основного оборудования – перевод ТЭЦ в режим котельных, демонтаж устаревших котлов, работа городских ТЭЦ по тепловому графику, замена малоэффективных золоуловителей более совершенными установками, автоматизация процесса горения и т.п.;
- реконструкция оборудования, например организация рециркуляции дымовых газов, двухступенчатого сжигания, впрыска воды в горелки для уменьшения оксидов азота;
- обоснование изменения параметров дымовых труб с целью улучшения рассеивания дымовых газов;
- строительство установок по очистке дымовых газов от окислов серы и азота;
- внедрение автоматизированных систем контроля за выбросами и за состоянием атмосферного воздуха в районе максимального воздействия дымового факела ТЭС;
- оснащение котлов системой подавления оксидов азота с использованием контактных теплообменников в “хвосте” котла;
- использование химически активных веществ (например, мочевины) для разложения оксидов азота на азот и кислород;
- разработка и использование катализаторов для очистки дымовых газов от оксидов азота;
- разработка новых способов сжигания топлива с утилизацией углекислоты, снижением окислов серы и азота;
- внедрение физико-химических технологий очистки дымовых газов, в том числе с помощью пучка электронов (радиолиз);
- др.
Разва А.С.