Инструкция по разборке и сборке катков опорных гидроцилиндр автогрейдера дз-98в
Вид материала | Инструкция |
Содержание2.1. Устройство и принцип работы опорных катков 2.2. Техническое обслуживание 2.4. Инструкция по разборке и сборке катков опорных Механизм рулевой гидравлический |
- Ходовая часть, 561.51kb.
- Настоящая технологическая инструкция определяет требования по подготовке, сборке, сварке,, 139.25kb.
- Методика проведения производственного ультразвукового неразрушающего контроля опорных, 70.15kb.
- Инструкция по сборке и эксплуатации душевых кабин тимо:, 182.75kb.
- Инструкция по охране труда № при сооружении воздушных линий электропередачи, 461.98kb.
- Методические рекомендации по работе со схемами опорных сигналов внимательно ознакомьтесь, 42.68kb.
- Инструкция по сборке введение, 22.48kb.
- Организация учебного процесса на основе использования опорных конспектов, 42.02kb.
- Положение о смотре-конкурсе опорных предметных кабинетов общеобразовательных учреждений, 241.96kb.
- Задачи: Образовательная расширить представление учащихся об опорных системах животных, 65.48kb.
Опорный каток бульдозера Д-355А
2.1. Устройство и принцип работы опорных катков
Литые стальные опорные катки 15 (см. рис. 2.1) с закаленными
ободьями установлены в расточках балансиров с помощью оси 28
катков на конических роликоподшипниках 27. При этом сначала
на ось напрессованы своими внутренними обоймами роликопод-
шипники, а затем — опорные катки. От проворачивания на оси
катки удерживаются призматическими шпонками, а в осевом на-
правлении затягиваются гайками.
Гайки стопорятся с помощью многолепестковых пружинных шайб. Положение шпонки в пазу оси катка определяется упором внутреннего торца шпонки в специальные выступы на боковых поверхностях шпоночного паза оси.
Внешние обоймы конических роликоподшипников поджимаются корпусами 26 уплотнений, закрепленных четырьмя болтами каждый на балансире. Осевые зазоры в подшипниках регулируют с помощью прокладок, устанавливаемых между балансиром и корпусом уплотнения. Применяются прокладки трех толщин: 0,2; 0,4 и 0,6 мм. Нормальный осевой зазор 0,2 ... 0,6 мм. При регулировке подшипников необходимо следить, чтобы толщина набора прокладок с правой и левой сторон отличалась как можно меньше.
Подшипниковый узел опорных катков смазывается маслом, заправляемым через сверления в оси катка. Для этого в осевое продольное сверление вводят наконечник нагнетателя до упора в конец сверления большего диаметра и через этот наконечник подается свежее масло, которое затем проходит по осевому сверлению меньшего диаметра и радиальному сверлению в масляную полость, вымывая продукты износа и абразивные частицы, попавшие в полость. Загрязненное масло через второе радиальное сверление и зазор между наконечником нагнетателя и осевым отверстием большего диаметра выливается наружу.
Между опорным катком и балансиром установлено торцевое уплотнение. Основные его элементы: неподвижное 19 и подвижное 20 уплотнительные кольца, изготовленные из стали или порошкового материала высокой твердости. Обращенные одна к другой рабочие поверхности колец обработаны с высокой степенью точности. На них имеются рабочие плоские пояски шириной 2-.шш 2,5 мм, переходящие в конические поверхности — микроконусы.
Неподвижное уплотнительное кольцо 19 установлено в корпусе 26 уплотнения и зафиксировано от проворачивания лысками. Подвижное в осевом направлении кольцо 20 установлено на ступице опорного катка 15, удерживается от проворачивания на ступице лысками и поджимается к неподвижному уплотнительному кольцу пружиной 23 через шайбу 22 и резиновое кольцо 24, которое усилием пружины прижимается одновременно и к тороидальной поверхности подвижного кольца, и к цилиндрической поверхности колпака 25 уплотнения, приваренного к опорному катку.
Вытекание масла между балансиром и корпусом 26 уплотнения, между катком 15 и колпаком 25 уплотнения, между катком 15 и осью 28 катка предотвращается с помощью резиновых колец.
Стопорное кольцо, установленное в канавку на ступице опорного катка, предотвращает соскакивание со ступицы подвижного и резинового колец, шайбы и пружины при разборке-сборке уплотнения, т. е. является монтажным или вспомогательным.
При движении трактора неподвижное уплотнительное кольцо вместе с корпусом уплотнения и балансиром не вращается. Подвижное уплотнительное кольцо вращается вместе с катком, а герметизация подшипникового узла достигается благодаря поджатию одна к другой точно обработанных рабочих поверхностей уплотнительных колец, масло между которыми не подтекает. Узкий рабочий поясок кольца быстро прирабатывается. В процессе эксплуатации рабочие поверхности уплотнительных колец изнашиваются абразивными частицами почвы и плоский рабочий поясок при этом постепенно перемещается от периферии к внутреннему диаметру.
От возможных повреждений уплотнение подшипникового узла опорного катка предохраняется лабиринтом, образованным расточкой в корпусе уплотнения и входящим в нее колпаком.
Заливное отверстие в оси катка закрывается конической резьбовой пробкой. Все конические резьбовые пробки, используемые в каретках подвески, а также направляющих колесах и поддерживающих роликах, одинаковы.
Каретки подвески собирают и устанавливают на трактор так, чтобы оси катков заливными отверстиями были обращены наружу.
На бульдозерах KOMATSU D355A установлены катки опорный однобортный и опорный двубортный.
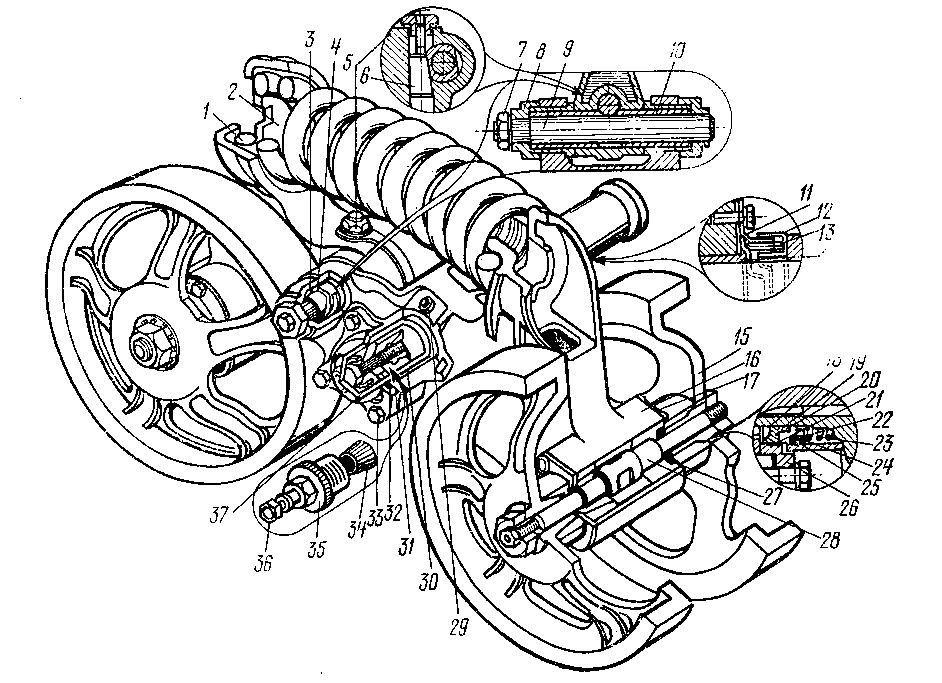
Рис. 2.1. Каретка подвески:
1 — пружина-рессора; 2 — внутренний балансир; 3 — малая втулка; 4 — большая ось качания; 5 — гайка клина; 6 — клин; 7 — гайка; 8 — крышка; 9 — малая ось качания; 10 и 14 — втулки; 11 — внешняя обойма; 12 — ведущая обойма; 13 — чехол уплотнения цапфы; 15 — опорный каток; 16 — внешний балансир; 17 — регулировочная прокладка; 18 — стопорное кольцо; 19 — уплотнительное неподвижное кольцо; 20 — уплотнительное подвижное кольцо; 21 и 24 — уплотнительное резиновое кольцо; 22 шайба; 23 — нажимная пружина; 25 — колпак уплотнения; 26 — корпус уплотнения; 27 — роликовый подшипник; 28 — ось опорного катка; 29 — заливная пробка; 30 — втулка цапфы; 31 — прокладка крышки; 32 — упорная шайба; 33 — контрольная пробка; 34 — конусная втулка; 35 — цанговая гайка; 36 распорный болт; 37 — крышка каретки подвески.
2.2. Техническое обслуживание
При разборке подшипниковых узлов опорных катков, направляющих колес и поддерживающих роликов для регулировок и устранения неисправностей необходимо оберегать подвижное и неподвижное металлические уплотнительные кольца торцевых уплотнений от ударов, падений. Особенно необходимо следить за точно обработанными рабочими поверхностями колец, не допуская на них забоин, царапин и рисок. Не следует также менять одно из уплотнительных колец в приработавшейся паре. Не рекомендуется также без надобности выпрессовывать неподвижное уплотнительное кольцо из корпуса.
При длительных стоянках трактора узлы ходовой системы следует очищать. В холодное время года прежде чем начать движение необходимо убедиться в том, что поддерживающие ролики вращаются.
Для этого нужно ломиком приподнять верхнюю ветвь гусеничной цепи и проконтролировать, свободно ли вращаются поддерживающие ролики. При необходимости надо добиться их вращения, очистив от намерзшей грязи и прокрутив их. Движение трактора с невращающимися поддерживающими роликами приводит к быстрому изнашиванию резиновых бандажей.

Рис.2.2. Каток опорный однобортный 195-30-00444
2.3. Ремонт
К основным дефектам опорных катков и колес относятся износ обода катка, трещины в спицах, износ или повреждение защитного колпака, подшипников и уплотнений. Обод катка восстанавливают наплавкой под слоем флюса до номинальных размеров и устанавливают на тракторе без дополнительной обработки. Трещины в спицах разделываются по схеме, аналогичной описанной при ремонте направляющего колеса. При износе или повреждении защитный колпак заменяется новым, крепится он в зависимости от конструкции катка сваркой или пружинным кольцом. После разборки катка осматривается ось и устанавливается износ подшипников. Характерные места износа на оси находятся под подшипниками и опорным катком в месте установки уплотнений. Для восстановления посадочных мест на оси применяют плазменную наплавку. Отбраковывается ось при выявлении трещин или изломов. При нарушении шпоночных канавок их восстановление возможно без реставрации фрезерованием под больший размер шпонки или наплавкой и восстановлением канавки прежних размеров. Аналогичным, образом устраняются повреждения резьбы.
2.4. Инструкция по разборке и сборке катков опорных
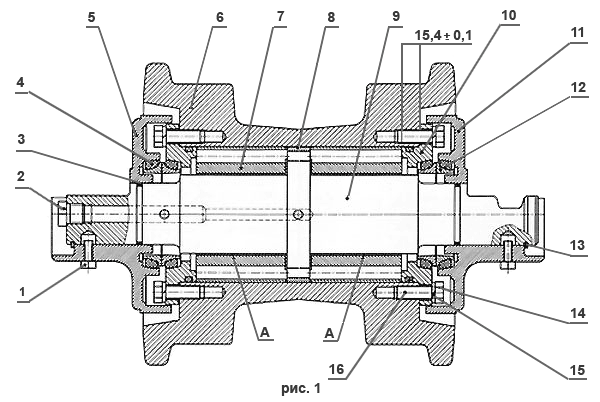
1.Разборка
1.1. Вывернуть болты 1 (рис.1). На катке, снятом с трактора, болты должны отсутствовать.
1.2. Выбить опорные кольца 13 из канавок оси 9.
1.3. Демонтировать крышки 5 и 11 с уплотнительными кольцами. Слить остатки масла из катка.
1.4. Аккуратно, чтобы не повредить резиновые кольца 4, вынуть металлические кольца 12 из крышек 5 и 11 и упорных шайб 10.
1.5. Снять резиновые кольца 4 с металлических колец 12.
1.6. Металлические кольца 12, работавшие совместно, попарно связать проволокой, чтобы использовать при последующей сборке.
1.7. Вынуть резиновые кольца 3 из канавок оси 9.
1.8. Отвернуть и снять болты 16 с пружинными шайбами 15.
1.9. Демонтировать шайбы упорные 10 и вынуть из канавок резиновые кольца 14.
1.10. Вывернуть пробку 2.
1.11. Выпрессовать поочередно биметаллические втулки 7, надавив прессом на торец оси, противоположный выпрессовываемой втулке.
2. Сборка
2.1. Внимание! К сборке допускаются детали и комплектующие, соответствующие чертежно-технической документации и следующим требованиям:
2.1.1. Ролик однобортный и двубортный:
диаметр беговых дорожек 230±1,5 мм; минимально допустимый диаметр 224 мм; толщина наружных реборд 20±1,5 мм, внутренних реборд 18±2,0 мм; минимально допустимая толщина наружных реборд 16,7 мм; внутренних - 13,6 мм;
2.1.2. Кольца торцевого уплотнения должны быть скомплектованы попарно. У колец, работавших ранее, обязательно наличие конусной поверхности под рабочим пояском не менее 3 мм.
2.1.3. Ось:
- радиальное биение поверхностей А друг относительно друга не более 0,03 мм.
2.1.4. Каток в сборе
- натяг в соединении ролик - биметаллическая втулка должен быть 0,046...0,116 мм;
- радиальный зазор в соединении ось - биметаллическая втулка должен быть 0,35...0,44 мм;
- осевой зазор, обеспечиваемый разностью длин дистанционной втулки и бурта оси, должен быть 0,1...0,4 мм.
2.1.5. Резиновые кольца не должны иметь деформаций, порывов, надрезов, трещин.
2.2. Все трущиеся поверхности перед сборкой смазать маслом трансмиссионным ТСп-10 ГОСТ 23652-79
2.3. Торцы биметаллических втулок 7 со слоем бронзы должны быть направлены внутрь ролика к бурту оси 9.
2.4. Запрессовать одну биметаллическую втулку 7 на глубину 15,4±0,1 мм относительно торца ролика, вставить ось 9, дистанционную втулку 8 и запрессовать вторую биметаллическую втулку до упора в дистанционную втулку, при этом глубина запрессовки относительно торца ролика должна быть не более 15,5 мм.
2.5. Установить резиновые кольца 14 в канавки упорных шайб 10, смазать их маслом ТСп-10, после чего закрепить упорные шайбы 10 в ролике болтами 16 с пружинными шайбами 15. Момент затяжки болтов 50...80 Н·м(5..8 кг·м).
2.6. Перед установкой резиновых колец 4, поверхности деталей 5, 10, 11 и 12, с которыми они соприкасаются, обезжирить смесью спирта этилового ТУ 38.402-62-117-90 или спирта этилового ректификованного ГОСТ 18300-72 и воды в соотношении 1:1, после чего высушить на воздухе. Допускается использовать для обезжиривания ацетон ГОСТ 2603-79.
2.7. Резиновые кольца, использовавшиеся ранее, также тщательно обезжирить вышеуказанной смесью.
Наличие следов смазки на резиновых кольцах 4 не допускается!
2.8. Установить резиновые кольца 4 на металлические кольца 12.
Перекручивание колец не допускается!
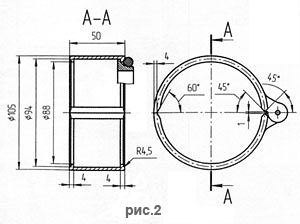
2.9. С помощью специального приспособления (рис.2) резиновые кольца 4 с металлическими кольцами 12 установить в упорные шайбы 10 и крышки 5 и 11. Плоскости притертых рабочих поясков колец 10 должны быть параллельны торцам смежных плоскостей деталей, в которые они установлены, допускается непараллельность не более 0,5 мм.
2.10. Притертые рабочие пояски колец 12 обезжирить смесью (см. п. 2.6) и салфеткой, не оставляющей ворсинок, смазать маслом трансмиссионным ТСп-10, после чего касание к пояскам не допускается. Попадание масла на резиновые кольца не допускается.
2.11. Установить резиновые кольца 3 в канавки оси, смаазать их маслом ТСп-10.
2.12. Аккуратно, не повредив резиновые кольца 3, установить на ось крышки 5 и 11, поджать их и поставить стопорные кольца 13.
Выступание стопорных колец за привалочные плоскости оси не допускается!
2.13. Завернуть болты 1 в крышки 5 и 11. После установки катка на трактор болты 1 снять!
2.14. Внутреннюю полость катка испытать на герметичность воздухом под давлением 0,05...0,07 МПа (0,5...0,7 кг/кв. см.) в течение 10 сек, не менее.
Падение давления не допускается!
2.15. Опорный каток заправить самотеком маслом трансмиссионным ТСп-10 ГОСТ 23652-79 в количестве 0,23...0,28 кг (250...300 куб. см), ввернуть пробку 2 и затянуть ее моментом 50...80 Н·м (5...8 кг·м).
2.16. Ролик должен плавно, без заеданий проворачиваться на оси.
Гидроцилиндр автогрейдера ДЗ-98В
Рулевое управление - гидростатического типа, работает как независимый контур гидросистемы автогрейдера, имея с ней общий гидробак (рис.3.1) и заборную трубу 8.
Шестеренным насосом НШ-50 (поз.7) рабочая жидкость подается в гидроруль 9. Гидроруль обеспечивает, в зависимости от направления поворота установленного на нем рулевого колеса подачу жидкости в одну из полостей гидроцилиндра 1 поворота колес и слив жидкости другой полости. При этом шток гидроцилиндра поворачивает правый поворотный кронштейн переднего моста, одновременно с которым при помощи поперечной тяги 2 поворачивается и левый поворотный кронштейн. Вместе с поворотными кронштейнами происходит поворот передних колес автогрейдера.
Поперечная тяга 2 соединяет поворотные кронштейны 11 переднего моста при помощи шаровых шарниров. Устранение люфтов в шарнире осуществляется с помощью гайки, которую затягивают до упора, а затем отпускают настолько, чтобы можно было ее зашплинтовать.
Поперечная тяга 2 выполнена регулируемой для установления требуемого размера схождения колес. Схождение колес проверяется на ровной площадке, при этом колеса устанавливаются в положение для прямолинейного движения.
Схождение колес определяется как разность размеров между внутренними торцами ободов сзади и спереди на высоте оси колес. Размер по бортам ободов спереди должен быть на 1,5-2,5 мм меньше размера сзади.
Гидроруль 9 служит для уменьшения усилия на рулевом колесе при повороте передних колес автогрейдера.
Применяется гидроруль одной из следующих моделей:
1) механизм рулевой гидравлический У 245006-00-01;
2) насос-дозатор моноблочный НДМ200-У600.
Механизм рулевой гидравлический У245006-00-01 (рис.3.2) состоит из трех элементов: распределительного блока, планетарного редуктора и гидромотора обратной святи. Распределительный блок состоит из корпуса 14, золотника 15, вала 12, закрепленного на подшипнике 13. В центральном отверстии золотника 15 находится втулка 16. Втулка имеет возможность проворачиваться без осевого перемещения относительно золотника.
В нижней части втулки имеются эвольвентные шлицы, в верхней - два направляющих паза, в которые входит палец 11, соединяющий вал с втулкой. Между валом и втулкой установлена пружина 10 установки золотника в исходное положение.
Планетарный редуктор состоит из коронной шестерни 18, сателлита 8, закрепленного на эксцентриковом валу 5 гидромотора.
Распределительный блок соединен с планетарным редуктором карданом 9, зубчатые венцы которого одной стороной входят в зацепление с втулкой 16, а другой - с сателлитом 8.
Гидромотор обратной связи состоит из корпуса 21, цетральной шестерни 22, трех периферийных шестерен 23, установленных на валиках 19.
Центральная шестерня конусным штифтом 20 связана с экцентриковым валом 5 гидромотора.
В верхней 6 и нижней 2 крышках гидромотора размещены подшипники 7 и игольчатые подшипники 1 и 24.
Бандаж 4 обеспечивает герметичность гидромотора. Три штифта 3 обеспечивают сборку и центрирование гидромотора.
Все три элемента стягиваются шестью болтами 25.
Подключение гидроруля к гидросистеме рулевого управления осуществляется посредством четырех резьбовых отверстий на корпусе распределительного блока гидроруля: Н - напор, СЛ - слив, Л и П - соответственно левая и правая рабочие полости исполнительного гидроцилиндра.
Работа. В среднем положении золотника рабочая жидкость, подаваемая насосом питания в подвод Н гидроруля, поступает по каналам распределительного блока на слив в бак. Все остальные каналы заперты.
При повороте вала 12 гидроруля в одну из сторон, золотник 15 под воздействием пальца 11 на направляющие пазы втулки 16 смещается в осевом направлении, плавно перекрывая своими кромками канал распределительного блока, соединяющий отверстия Н и СЛ. При этом рабочая жидкость направляется через гидромотор обратной связи в одну из полостей исполнительного гидроцилиндра. Вытесняемая из противоположной полости жидкость сливается в гидробак.
Эксцентриковый вал 5 гидромотора потоком жидкости, поступающей в гидромотор и далее в исполнительный гидроцилиндр, приводится во вращение и через планетарный редуктор (понижение частоты вращения в 15,5 раза) карданом 9 поворачивает втулку 16 в сторону вращения вала 12 гидроруля, стремясь сместить ее, а следовательно, и золотник, в осевом направлении в исходное положение по направляющим пазам втулки.
При остановке вращения вала гидроруля и его удержании происходит осевое смещение золотника в сторону исходного положения до момента снижения давления в системе до величины,
меньшей внешней нагрузки, и прекращение поворота машины.
При отпускании рулевого колеса под действием пружины 10 золотник возвращается в исходное положение и направляет рабочую жидкость от насоса на слив.
Насос-дозатор моноблочный НДМ 200-У600 (рис.3.3) представляет собой сблокированный с насосом-мотором следящий гидрораспределитель, входным сигналом для которого является вращение рулевого колеса. Объем рабочей жидкости, подаваемой от насоса-дозатора к гидроцилиндру поворота колес, пропорционален углу поворота рулевого колеса.
Для подсоединения к гидросистеме насос-дозатор имеет на корпусе четыре резьбовые отверстия: Р, Т, А и В.
При работающем питающем насосе за счет встроенного усилителя потока насос-дозатор обеспечивает увеличенную подачу рабочей жидкости по сравнению со своим номинальным рабочим объемом.
В аварийном режиме, при отсутствии потока рабочей жидкости от питающего насоса, насос-дозатор работает как ручной насос, приводимый вращением рулевого колеса, и обеспечивает уменьшенную подачу, равную своему номинальному рабочему объему. Таким образом сохраняется возможность управления автогрейдером в аварийном режиме.
Насос-дозатор выполнен:
- ″открытым центром" - при отсутствии управляющего воздействия на рулевое колесо свободно пропускает рабочую жидкость от питающего насоса на слив;
- "без реакции" - воздействие дороги на колеса не передается на руль.
Насос-дозатор снабжен встроенными клапанами, которые выполняют следующие функции: предохранительный - защиту питающего насоса от перегрузки по давлению;
обратный - предотвращение вытекания рабочей жидкости при
обрыве трубопровода питания;
противоударные - защиту гидросистемы от скачков давления в результате ударных воздействий дороги на колеса;
противовакуумные - подпитку противоположной полости гидроцилиндра при срабатывании противоударного клапана и предотвращение кавитации.
Давление настройки предохранительного клапана 16 ±0,5 МПа (160 ± 5 кгс/см2), противоударных клапанов - 21 МПа (210 кгс/см2). ВНИМАНИЕ! РЕГУЛИРОВАНИЕ ПРЕДОХРАНИТЕЛЬНОГО И ПРОТИВОУДАРНЫХ КЛАПАНОВ ПРОВОДИТСЯ ПРИ НЕОБХОДИМОСТИ ТОЛЬКО ПО ОКОНЧАНИИ ГАРАНТИЙНОГО ПЕРИОДА АВТОГРЕЙДЕРА. Вращением винта 1 (рис.3.3) регулируется предохранительный клапан. Вращением винта 2 регулируются одновременно оба противоударных клапана.
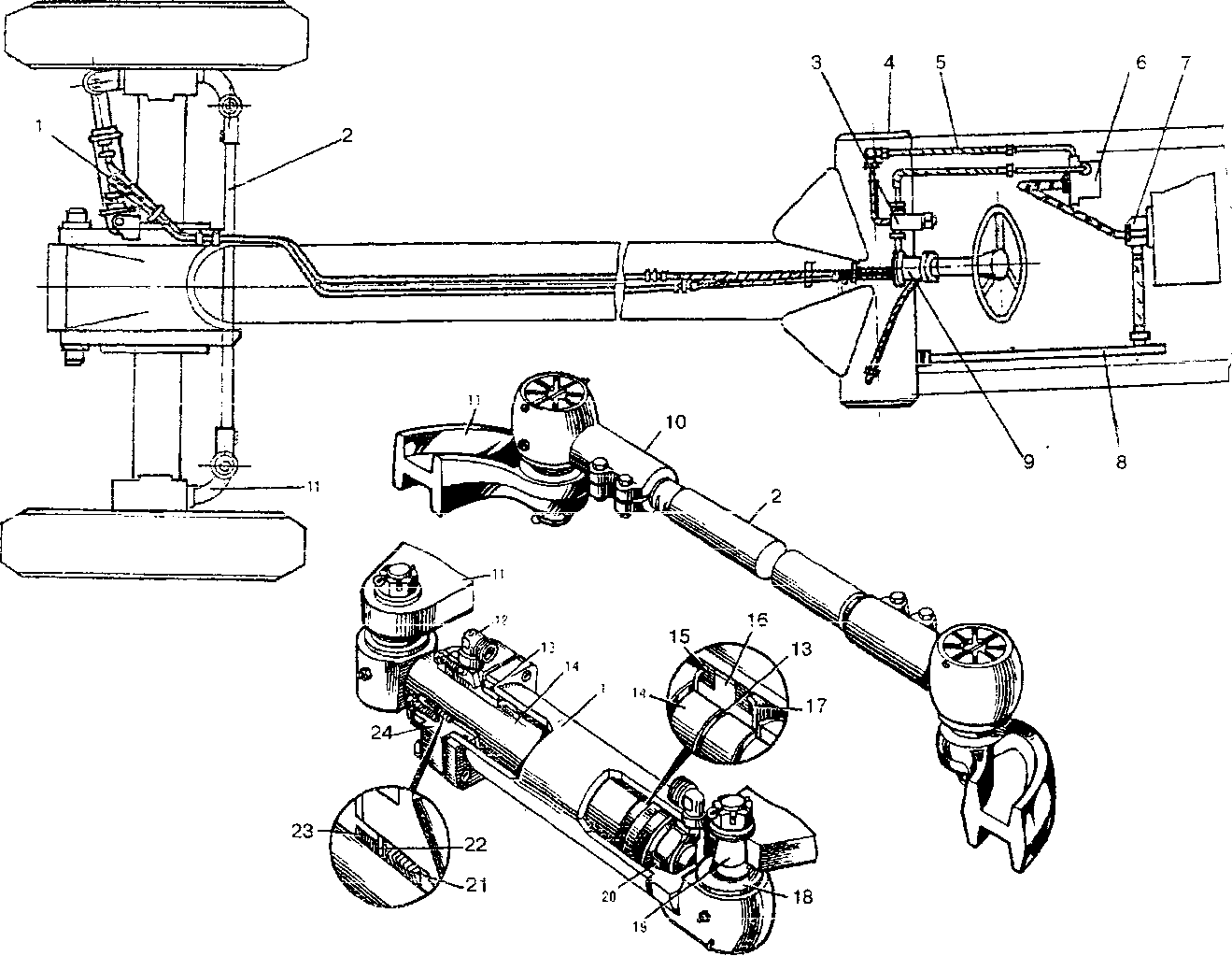
Рис.3.1. Рулевое управление
1- гидроцилиндр; 2- поперечная тяга; 3- предохранительный клапан; 4- гидробак; 5- нагнетательный трубопровод; 6- сервомеханизм; 7- насос НШ-50: 8- заборная труба; 9- гидроруль; 10- наконечник; 11- поворотный кронштейн переднего моста; 12- штуцер; 13- уплотнительное кольцо; 14-шток; 15- манжета; 16- поршень; 17- упор; 18- корпус уплотнителя; 19- шаровой палец; 20-стопорная шайба; 21- шевронная манжета; 22- упорная шайба; 23- чистик; 24- крышка цилиндра
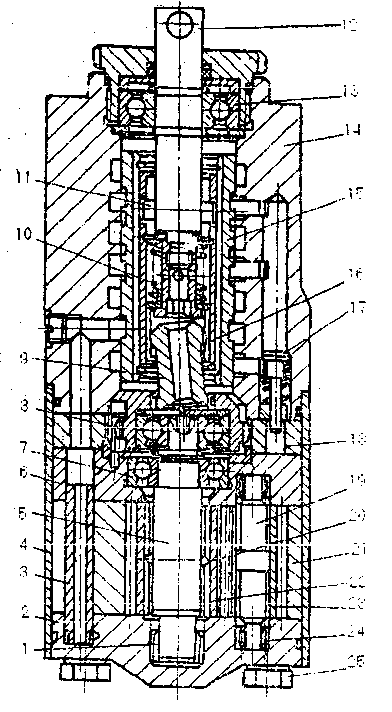