Лекции по курсу: «Техническая диагностика сэу»
Вид материала | Лекции |
- Оглавление к лекции, 174.31kb.
- 9-я Международная выставка и конференция «неразрушающий контроль и техническая диагностика, 112.56kb.
- Лекции по курсу «Теория ценных бумаг», 347.23kb.
- Аннотация дисциплины, 33.44kb.
- Лекции тема №6, 17.29kb.
- Пути кластеризации экономики с целью повышения конкурентоспособности Запорожской области, 1906.4kb.
- Конспект лекций по курсу: «Техническая эксплуатация силовых агрегатов и трансмиссий», 860.12kb.
- Научно-техническая конференция в рамках 8 Международной специализированной выставки, 45.35kb.
- Тесты По теме лекции, 269.39kb.
- А. Е. Александрович московский инженерно-физический институт (государственный университет), 24kb.
ЛЕКЦИИ по курсу:
«Техническая диагностика СЭУ», для специальности
180403 «Эксплуатация судовых дизельных энергетических установок»
РАЗДЕЛ 1. ПОНЯТИЕ О ТЕХНИЧЕСКОЙ ДИАГНОСТИКЕ СЭУ
Тема 1.1. Предпосылки применения технической диагностики
С научно-техническим прогрессом неразрывно связаны как рост сложности и разнообразия технических объектов, так и повышение требований к эффективности их функционирования. Эти требования удовлетворяются в той или иной мере на всех этапах существования объекта диагностирования (ОД) (проектирование, производство, использование по назначению). Одним из определяющих показателей эффективности работы ОД считается его надежность. Это свойство обеспечивается на этапах проектирования и производства и поддерживается в период его эксплуатации. Наряду с усовершенствованием структурных схем отдельных устройств и систем в целом, применением высоконадежных элементов и структурного резервирования, снижением нагрузки и стабилизацией условий эксплуатации ОД мощным средством поддержания необходимого уровня надежности является научная организация процесса эксплуатации ОД. В ней особая роль принадлежит диагностированию, по результатам которого определяется действительное техническое состояние ОД и характер его изменения с течением времени.
В самом общем случае процесс технического диагностирования технического объекта предусматривает решение задач:
1) определения его действительного технического состояния;
2) поиска дефектов;
3) прогнозирования изменения технического состояния.
В частных случаях в процессе диагностирования могут решаться отдельные из этих задач или их сочетания, поскольку каждая из них относительно самостоятельна.
На рис. 1 приведен один из возможных вариантов схемы, иллюстрирующей место задачи поиска дефектов в теории технического диагностирования и место последней в решении общей проблемы обеспечения надежности технических объектов.
Несмотря на наличие большого числа теоретических работ, эффективность методов технического диагностирования в повышении качества эксплуатации изделий еще остается крайне низкой, особенно при поиске дефектов. Известно, что ежегодные затраты на ремонт машин и оборудования в России и странах СНГ достигают очень больших значений, до 30% всех эксплуатируемых машин находится в неработоспособном состоянии в связи с их ремонтом, а число рабочих; занятых ремонтными работами, в 3—10 раз превышает число рабочих, занятых производством новых изделий.
Эффективность восстановления технического состояния тем выше, чем меньше время восстановления при удовлетворении заданным показателям его качества. Опыт эксплуатации сложных технических систем показывает, что при отсутствии специальных средств диагностирования основную долю времени восстановления составляет время, затрачиваемое на поиск дефекта(ов). Эта доля часто составляет 70—80% от общего времени восстановления.
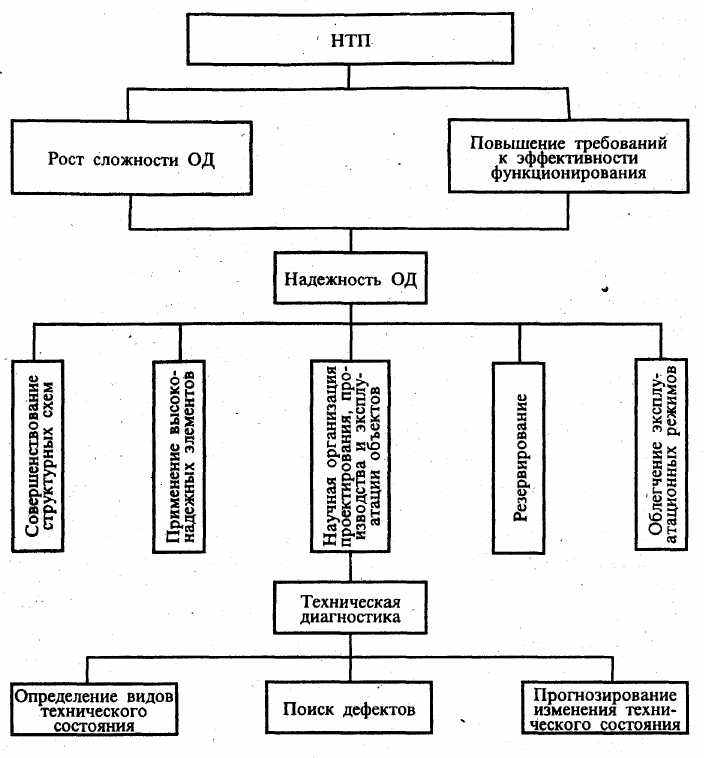
Рисунок 1 – Схема, обуславливающая появление ТД и ее задачи
Задача поиска дефектов или некоторые вопросы, связанные с ней, возникают на всех этапах жизненного цикла ОД, а именно:
- разработка и изготовление ОД с элементами приспособленности к решению задачи поиска дефектов;
- сборка и обкатка (испытания) ОД в целях оценки их качества и
в том числе надежности;
- приемочные испытания ОД;
- техническое обслуживание, определение объема планируемых
профилактических операций по фактическому техническому состоянию;
- предремонтное диагностирование с целью поиска дефектов;
- приемочные испытания и контроль отремонтированных объектов;
- своевременное переключение на резерв, т.е. оперативное управление техническим состоянием.
Эволюционность информационных технологий их новый этап развития, начавшийся в конце XX века, позволяет осуществить разработку и исследование целого ряда автоматизированных методов поиска дефектов из заданного их множества в объектах диагностирования непрерывного типа с разработкой алгоритмического и программного обеспечения на основе динамических моделей ОД.
Диагностика состояния того или иного объекта служит целям контроля, управления, включая регулировочные и наладочные процедуры. В широком плане эти вопросы позволяет решать прогнозирование, которое в данном контексте выступает составной частью диагностики.
Тема 1.2. Применение средств технической диагностики для судовых дизелей
Использование средств технической диагностики (СТД) дизелей направлено на увеличение ресурсных характеристик дизелей и продление межремонтного периода их эксплуатации, вплоть до перехода от системы плановых обслуживаний и ремонта к системе обслуживания по фактическому техническому состоянию.
Технико-экономическая эффективность СТД дизелей обуславливается:
- снижением затрат на техническое обслуживание благодаря уменьшению числа разборок и вскрытий дизелей при переходе от планово-технических норм обслуживания и ремонта к обслуживанию и ремонту их по фактическому состоянию;
- снижением затрат на ремонт за счет выявления потенциальных отказов на ранней стадии их возникновения;
- сокращением расхода топлива путем своевременного обнаружения разрегулировки топливной аппаратуры;
- и т.д.
Анализ эксплуатационных качеств элементов судовых энергетических установок судов показывает, что наибольшие эксплуатационные потери связаны с отказами дизель-редукторных агрегатов и дизелей. При этом 70-90 % всех отказов приходится на главные дизели и 3-18% - на вспомогательные дизели. Отказы главных редукторов и разобщительных муфт составляют до 5 % полного числа отказов элементов СЭУ.
Наиболее частые отказы дизелей связаны с:
- системой топливоподачи (форсунки и ТНВД);
- клапанами газораспределения;
- рамовыми и мотылевыми подшипниками;
- нарушением уплотнений цилиндровой втулки с блоком и крышкой цилиндра;
- кавитационно-коррозионными разрушениями и трещинами опорных буртов втулок.
Тема 1.3. Основные определения технической диагностики
(по ГОСТ 20911-89 Техническая диагностика Термины и определения)
Объект технического диагностирования (контроля технического состояния или ОД) – изделие и (или) его составные части, подлежащие (подвергаемые) диагностированию (контролю).
В качестве ОД понимаются судовые технические средства и конструкции, состояние которых подлежит определению. В понятие судовые технические средства включаются главные и вспомогательные двигатели, вспомогательные механизмы, части главных и вспомогательных систем, общесудовых системы и устройства, их части и т.д.
Техническое состояние объекта – состояние, которое характеризуется в определенный момент времени, при определенных условиях внешней среды, значениями параметров, установленных технической документацией на объект.
Техническая диагностика – Область знаний, охватывающая теорию, методы и средства определения технического состояния объектов.
Контроль функционирования – контроль выполнения объектом части-всех свойственных ему функций.
Контроль технического состояния – проверка соответствия значений параметра объекта требованиям технической документации и определение на этой основе одного из заданных видов технического состояния в данный момент времени.
Техническое диагностирование – определение технического состояния объекта.
Задачами технического диагностирования являются:
- контроль технического состояния;
- поиск места и определение причин отказа (неисправности);
- прогнозирование технического состояния.
Термин «Техническое диагностирование» применяют в наименованиях и определениях понятий, когда решаемые основной задачей является поиск места и определение причин отказа (неисправности).
Термин « Контроль технического состояния» применяется, когда основной задачей технического диагностирования является определение вида технического состояния.
Техническое диагностирование ОД представляет собой процесс определения его технического состояния, включающего в себя совокупность свойств ОД, подверженных изменению при производстве или эксплуатации и характеризуемых в определенный момент времени признаками (параметрами), установленными технической документацией на ОД.
Результатом диагностирования является заключение о техническом состоянии объекта с указанием при необходимости места, вида и причин дефекта. Характерными примерами результатов диагностирования являются исправность или неисправность, работоспособность или неработоспособность, правильное или неправильное функционирование отдельных элементов, каскадов или всего ОД в целом.
Тема 1.4. Виды результатов диагностирования
Исправность – состояние объекта, при котором он соответствует всем требованиям, установленным нормативно-технической документацией. Если хотя бы одно из требований нормативно-технической документации на объект не выполняется — объект неисправен. Диагностирование при контроле исправности объекта — есть проверка исправности объекта.
Работоспособность — состояние объекта, при котором он способен выполнять заданные функции, сохраняя значения основных параметров в пределах установленных нормативно-технической документации. Понятие «работоспособность» уже, чем понятие «исправность». Работоспособный объект может быть неисправным, однако его повреждения при этом не настолько существенны, чтобы препятствовать нормальному его функционированию. Например, резервированный объект может быть работоспособным, несмотря на наличие неисправности в резервных компонентах или связях. Диагностирование при контроле работоспособности объекта — есть проверка работоспособности.
К основным заданным функциям, характеризующим работоспособность, дизелей, относятся: мощность, ресурс и расход топлива.
Судовое техническое средство может быть неисправным, но работоспособным. Например, дизель может развивать мощность и обеспечивать ресурс при плохой приемистости или повышенном уровне шума и дымности. С другой стороны, отдельные параметры, характеризующие работоспособность, могут иметь отклонения в пределах, определяющих, что судовое техническое средство неисправно, но частично работоспособно (например, дизель развивает только частичную мощность).
Правильное функционирование — состояние объекта, при котором он способен выполнять в текущий момент времени предписанные ему алгоритмы функционирования со значениями параметров, соответствующими установленным требованиям. В правильно функционирующем объекте могут быть неисправности, которые не позволят ему правильно работать в других режимах. Так, неисправность в регуляторе частоты вращения дизеля не изменит правильность функционирования дизеля на номинальном режиме, но вызовет его неисправность на частичном режиме. Диагностирование при контроле правильного функционирования объекта — есть проверка функционирования.
Примеры неправильного функционирования дизелей – необеспечение заданных динамических характеристик: приемистости, пусковых и реверсивных качеств.
Неисправность, неработоспособность и неправильное функционирование вызваны появлением каких-либо дефектов в техническом объекте. Диагностирование, целью которого является определение места и при необходимости причины и вида дефекта объекта — есть поиск дефекта.
Поиск дефекта осуществляется при помощи тех или иных средств технического диагностирования путем различного рода экспериментов над объектом диагностирования.
Некоторый минимальный (не подлежащий расчленению в данных конкретных условиях) эксперимент над объектом диагностирования, характеризующийся определенным рабочим (пассивный эксперимент) или тестовым (активный эксперимент) воздействием, поступающим или подаваемым на объект, а также составом признаков (параметров), образующих ответ объекта на соответствующее воздействие, представляет собой элементарную проверку. Конкретные значения признаков (параметров), получаемые при диагностировании, являются результатами элементарных проверок или значениями ответов объекта.
Совокупность элементарных проверок, последовательность
(или последовательности) их реализации и правила анализа полученных результатов реализуемых элементарных проверок представляют собой алгоритм диагностирования.
Таблица 1 – Характеристика ТС
Категория (класс) ТС | Вид повре- ждения | Характери-зующий параметр | Вид ТС | |||||
Номер класса | по РД 31.20.50-87 | по Регистру | по ИСО 2372 | по исправ-ности | по работоспо-собности | по функци-онирова-нию | ||
I | Хорошее | Годное | Хорошее | --- | Номина-льное | Исправное | Работоспо-собное | правильное |
II | Удовлетво-рительное | Годное | Приемлемое | Несу- щест-венное | От ном. до предельно-допусти-мого | Исправное | Работоспо-собное | правильное |
III | Неудовле- творитель-ное | Ограни-ченно годное | Допусти-мое (ограни-ченно) | Суще- ствен-ное | От предельно-допусти-мого до предельно-возможного | Неисправ-ное | Частичная утрата работоспо-собности | Ограни-ченное функции-онирова-ние |
IV | Аварийное | Негодное | Недопус-тимое | Отказ | От предельно-возможного до аварийного | Неисправ-ное | Неработо-способное | Неправи-льное |
Тема 1.5. Основные определения, связанные со средствами и системами технической диагностики (по ГОСТ 20911-89)
Контролепригодность (диагностируемость) – приспособленность объекта диагностирования к измерению диагностических признаков (параметров) средствами диагностирования.
Технический диагноз (результат контроля) – Результат диагностирования.
В зависимости от типа воздействий на ОД различают:
Рабочее техническое диагностирование – Диагностирование, при котором на объект подаются рабочие воздействия (в процессе обычного функционирования).
Тестовое техническое диагностирование – диагностирование, при котором на объект подаются тестовые (специальные) воздействия.
Экспресс-диагностирование – диагностирование по ограниченному числу параметров за заранее установленное время.
Приспособленность объекта к диагностированию (контролепригодность) – свойство ОД, характеризующее его пригодность к проведению диагностирования (контроля) заданными средствами диагностирования (контроля).
Алгоритм технического диагностирования (контроля технического состояния) – совокупность предписаний, определяющих последовательность действий при проведении диагностирования (контроля).
Диагностическое обеспечение – комплекс взаимоувязанных правил, методов, алгоритмов и средств, необходимых для осуществления диагностирования на всех этапах жизненного цикла объекта.
Диагностическая модель – формализованное описание ОД, необходимое для решения задач диагностирования.
Диагностический (контролируемый) параметр – параметр ОД, используемый при его диагностировании (контроле).
Тема 1.6. Системы и средства технического диагностирования
(контроля технического состояния, по ГОСТ 20911-89)
Средство технического диагностирования (контроля технического состояния) – аппаратура и программы, с помощью которых осуществляется диагностирование (контроль).
Система технического диагностирования (контроля технического состояния) – совокупность средств, объекта и исполнителей, необходимая для проведения диагностирования (контроля) по правилам, установленным в технической документации.
Автоматизированная система технического диагностирования (контроля технического состояния) – система диагностирования (контроля), обеспечивающая проведение диагностирования (контроля) с применением средств автоматизации и участием человека.
Автоматическая система технического диагностирования (контроля технического состояния) – система диагностирования (контроля), обеспечивающая проведение диагностирования (контроля) без участия человека.
Встроенное средство технического диагностирования (контроля технического состояния) – средство диагностирования (контроля), являющееся составной частью ОД.
Внешнее средство технического диагностирования (контроля технического состояния) – средство диагностирования (контроля), выполненное конструктивно отдельно от ОД.
Специализированное средство технического диагностирования (контроля технического состояния) – средство, предназначенное для диагностирования (контроля) одного ОД или группы однотипных ОД.
Универсальное средство технического диагностирования (контроля технического состояния) – средство, предназначенное для диагностирования (контроля) ОД различных типов.
Тема 1.7. Показатели и характеристики технического диагностирования (контроля технического состояния, по ГОСТ 20911-89)
Продолжительность технического диагностирования (контроля технического состояния) – интервал времени, необходимый для проведения диагностирования (контроля) ОД.
Достоверность технического диагностирования (контроля технического состояния) – степень объективного соответствия результатов диагностирования (контроля) действительному техническому достоянию объекта.
Полнота технического диагностирования (контроля технического состояния) – характеристика, определяющая возможность выявления отказов (неисправностей) в ОД при выбранном методе его диагностирования (контроля).
Глубина поиска места отказа (неисправности) – характеристика, задаваемая указанием составной части ОД с точностью, до которой определяется место отказа (неисправности).
Условная вероятность необнаруженного отказа (неисправности) при диагностировании (контроле) – вероятность того, что неисправный (неработоспособный) ОД в результате диагностирования (контроля) признается исправным (работоспособным).
Условная вероятность ложного отказа (неисправности) при диагностировании (контроле) – вероятность того, что исправный (работоспособный) ОД в результате диагностирования (контроля) признается неисправным (неработоспособным).
Условная вероятность необнаруженного отказа (неисправности) в данном элементе (группе) – вероятность того, что при наличии отказа (неисправности) в результате диагностирования принимается решение об отсутствии отказа (неисправности) в данном элементе (группе).
Условная вероятность ложного отказа (неисправности) в данном элементе (группе) – вероятность того, что при отсутствии отказа (неисправности) в результате диагностирование принимается решение о наличии отказа (неисправности) в данном, элементе (группе).
Тема 1.8. Основные задачи диагностирования ТС ОД
Диагностирование ОД как процесс определения его ТС включает решение трех задач:
- изучение ОД и его рабочего процесса (либо его узлов, элементов, подпроцессов и т.д.);
- построение алгоритмов диагностирования;
- разработка средств диагностирования.
Задача изучения, например, судового дизеля как ОД связана с исследованием функционирования исправного состояния дизеля, выделением основных его элементов и связей между ними, анализом возможных их ТС, определением параметров, характеризующих ТС дизеля и (или) его элементов, пределов, характера изменения и технической возможности их контроля, оценкой степени детализации возможных мест, видов, причин и частоты появления дефектов (глубины диагностирования), сбором данных о затратах, связанных с осуществлением элементарных проверок.
Для решения перечисленных задач обязательно требуются экспериментальные исследования и анализ процедур диагностирования конкретных судовых дизелей на практике. Указанный фактор является наиболее уязвимым в области диагностирования. Несмотря на то, что ответ на часть вопросов можно найти в специальной технической литературе, все равно для проверки алгоритма диагностирования требуется проведение натурного эксперимента (активного и (или) пассивного).
Стремление к теоретическому обобщению процесса диагностирования дизеля при ограниченной информации о его ТС предопределяет широкое использование формального описания, т.е. математического моделирования.
Модель физического или технического объекта, процесса или системы – это упрощенное их представление в форме отличной от формы их реального существования, сохраняющее с некоторой точностью те их свойства, характеристики и параметры, которые интересуют исследователя.
Математическая модель – модель ОД, использующая для моделирования математический аппарат, в том числе и логический.
Наиболее распространенные способы математического описания, используемые при разработке и исследовании дизелей (дифференциальные и разностные уравнения, структурные схемы), оказываются недостаточными для диагностирования, поскольку в явной форме не отражают процесс появления дефектов и их влияния на ТС дизелей. Необходимы такие математические модели, которые наилучшим образом учитывали бы все стороны явлений, характерных для рабочего процесса дизеля. При этом в первую очередь требуются модели диагностирования отдельных элементов дизеля,
без которых глубина диагностирования будет явно недостаточной – процесса впуска воздушного заряда, процесса его сжатия, процесса впрыска топлива и его горения, процессов выпуска отработавших газов и продувки, рабочего процесса плунжерной пары, движения топлива по трубопроводу высокого давления, форсунки, динамики движения вращающихся и поступательно движущихся масс дизеля (коленвал, шатун, поршень, палец), рабочего процесса агрегатов наддува
и т.д.
Такую задачу обеспечивают в достаточно полном объеме имитационные модели, которые не только обеспечивают точность повторения реакции ОД на входные воздействия, но и практически полностью (с учетом заданной точности) повторяют его внутреннюю структуру.
Представление математической модели дизеля и его отдельных элементов диагностирования в сочетании с его экспериментальными исследованиями является наиболее ответственным этапом в процессе диагностирования дизеля.
Задача построения алгоритмов диагностирования ОД связана с разработкой методов определения и оптимизации алгоритмов поиска в них дефектов с учетом показателей надежности его элементов, временных, материальных и других затрат на реализацию алгоритмов.
Проблемы, возникающие при математическом описании ОД и разработке на его основе алгоритмов диагностирования, тесно взаимосвязаны, поскольку модель должна обеспечивать достаточно простое получение необходимой информации о эталонном (идеальном) рабочем процессе дизеля и его элементов.
Многообразие функций, которые должны выполнять устройства диагностирования (измерение контрольных сигналов, анализ их допустимых уровней, вынесение решений о техническом состоянии объекта, выдача информации о результатах диагностирования и т.п.), в совокупности с широким классом совместно работающих ОД технической системы создают большие трудности при разработке и технической реализации средств диагностирования. Указанная проблема усугубляется и тем, что конструктивные решения, принятые для систем управления техническими системами, как правило, мало учитывают потребности их диагностирования, часто затрудняя доступ к наиболее информативным сигналам управления.
В этих условиях остро стоит вопрос о степени унификации, аппаратном или программном способе реализации средств диагностирования, а также путях их сочленения с ОД.
РАЗДЕЛ 2. КЛАССИФИКАЦИЯ СИСТЕМ ТЕХНИЧЕСКОГО ДИАГНОСТИРОВАНИЯ И СРЕДСТВ ТЕХНИЧЕСКОГО ДИАГНОСТИРОВАНИЯ