Лекции по курсу: «Техническая диагностика сэу»
Вид материала | Лекции |
- Оглавление к лекции, 174.31kb.
- 9-я Международная выставка и конференция «неразрушающий контроль и техническая диагностика, 112.56kb.
- Лекции по курсу «Теория ценных бумаг», 347.23kb.
- Аннотация дисциплины, 33.44kb.
- Лекции тема №6, 17.29kb.
- Пути кластеризации экономики с целью повышения конкурентоспособности Запорожской области, 1906.4kb.
- Конспект лекций по курсу: «Техническая эксплуатация силовых агрегатов и трансмиссий», 860.12kb.
- Научно-техническая конференция в рамках 8 Международной специализированной выставки, 45.35kb.
- Тесты По теме лекции, 269.39kb.
- А. Е. Александрович московский инженерно-физический институт (государственный университет), 24kb.
Системы технического диагностирования (СиТД) могут быть различны по своему составу, назначению, структуре, конструкции, схемотехническим решениям, месту установки. Они, как правило, классифицируются по ряду признаков, определяющих их назначение, задачи, структуру, состав технических средств: по степени охвата ОД; по принципу взаимодействия между ОД и СТД; по используемым средствам технического диагностирования и контроля; по степени автоматизации ОД.
По степени охвата СиТД разделяются на локальные и общие. Под локальными понимают СиТД, решающие одну или несколько задач диагностирования – определения ТС, дефекта или прогнозирования. Общими называют СиТД, решающие все задачи диагностирования.
По принципу взаимодействия ОД и СТД СиТД подразделяют на системы с функциональным диагнозом и системы с тестовым диагнозом. В первых решение задач диагностики осуществляется в процессе функционирования ОД, во вторых решение задач диагностики осуществляется в специальном режиме работы ОД путем подачи на него тестовых сигналов.
По используемым СТД СиТД можно разделить: на системы с универсальными СТД (например универсальные информационно-измерительные комплексы в комбинации со специальным ПО); системы со специализированными средствами (стенды, имитаторы, специализированные СТД); системы с внешними средствами, в которых СТД и ОД конструктивно отделены друг от друга; системы со встроенными средствами, в которых ОД и СТД конструктивно представляют одно изделие.
По степени автоматизации СТД делятся на: автоматические, в которых процесс получения информации о техническом состоянии ОД осуществляется без участия человека; автоматизированные, в которых получение и обработка информации осуществляется с частичным участием человека; неавтоматизированные (ручные), в которых получение и обработка информации осуществляется человеком-оператором.
Аналогичным образом могут классифицироваться также СТД: автоматические, автоматизированные, ручные.
СиТД применительно к ОД прежде должны: предупреждать постепенные отказы; выявлять неявные отказы; осуществлять поиск неисправных узлов, блоков, сборочных единиц и локализовать место отказа.
В системе управления качеством диагностико-прогнозирующие процессы подразделяют на три основные временные составляющие:
- прогноз – процесс определения ТС ОД в будущем на конечном временном интервале с заданной достоверностью;
- диагноз – процесс определения технического состояния объекта в данный момент;
- генезис – процесс определения ТС ОД с определенной точностью на заданном в прошлом временном интервале;
Согласно приведенной выше классификации, техническая диагностика может быть соответственно представлена: как непосредственно техническая диагностика; техническая прогностика; техническая генетика (прогнозирование назад или ретропрогноз).
Такое деление имеет место тогда, когда процесс прогнозирования осуществляется как бы раздельно. Но на практике все три процесса представляют собой неразрывное единство, ибо они выражаются в динамике изменения состояния функционирующей системы или объекта.
Тема 2.2. Последовательность этапов развития систем технического диагностирования
Практическая потребность в решении задач ТД возникла одновременно с появлением объектов, дефекты в которых нужно было находить и устранять. Эти функции стихийно были возложены на оператора (О). Промышленные изделия на заре развития техники отличались несложной конструкцией и выполняли относительно простые функции. Поэтому О мог без особых усилий решать задачу поиска и устранения дефектов. Взаимодействие О и ОД можно рассмотреть с позиции системного подхода и считать их элементами системы диагностирования (СД).
Первую ступень исторического развития СД можно иллюстрировать информационной схемой, приведенной на рис.2, а.
Согласно этой схеме, процесс поиска и устранения дефектов является кибернетическим процессом (кибернетика – наука, определяющая связь живого и искусственного (машины) при осуществлении процесса управления). При этом, имеется некоторая неопределенность относительно текущего технического состояния ОД. В этой ситуации О должен принять решение о состоянии ОД, для чего ему необходимо организовать процесс получения диагностической информации. Приняв решение, О организует воздействие на ОД по устранению дефекта. Таким образом, имеют место все остальные части процесса управления: цель – найти и устранить дефект: получение и обработка информации; принятие решения; управляющие воздействия; устранение дефекта, если принято решение о его наличии.
Согласно рассмотренной схеме, объектом управления является ОД, а все управляющие функции сосредоточены у О. Оператор реализует принятие решения о ТС ОД в виде диагноза (Д).
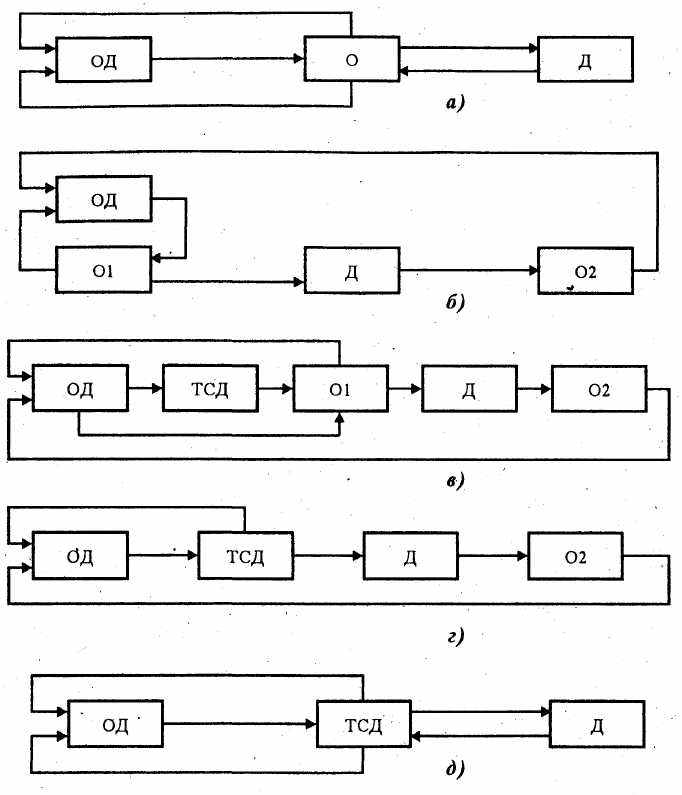
Рисунок 2 – Этапы развития систем диагностирования
Вторая ступень в развитии СД связана с разделением функций О по принятию решения о техническом состоянии (ТС) (О1) и по реализации управляющего воздействия (О2). Схема такой СД приведена на рис.2, б, при этом один узкий специалист – О1 выявлял диагнозы, а другой узкий специалист устранял выявленные дефекты – О2.
Третья ступень появилась с усложнением ОД, при котором органолептические методы поиска дефектов (с использованием человеческих органов чувств) стали плохо работать. Ограниченность возможностей органов чувств О считается одним из существенных факторов, обусловивших появление и развитие специфической отрасли приборостроения, занимающейся разработкой СТД. На начальном этапе развития на СТД возлагалась одна функция — усиление и расширение возможностей органов чувств О1. Один из возможных вариантов СД с третьим ее элементом приведен на рис.2, в. Часть информации получают и обрабатывают СТД, а другую часть – О1.
В дальнейшем развитии СД ( Четвертая ступень) происходит постепенное перераспределение нагрузки по получении обработке информации в сторону СТД. Этот факт и дальнейшее усложнение ОД привели к усложнению задачи о получении диагноза (принятии решения). О1 не стал обеспечивать требуемого уровня эффективности. В результате решения этой проблемы были разработаны СТД нового поколения, которым были переданы функции по принятию решения, т.е. функции О1, рис.2, г.
Дальнейший процесс в развитии некоторых отраслей техники ( Пятая ступень – настоящее время) поставил задачу оперативного (непосредственного) управления техническими средствами сложных ОД путем своевременного переключения на резерв, или перехода на новые рабочие режимы. Эта задача возлагается на автоматические СТД, структура которых не включает О2 (рис.2 ,д).
Автоматизированные и автоматические СТД предполагают широкое использование вычислительной техники, которая входит в них составным элементом. Это, в свою очередь, выдвигает проблему формализации процессов получения и обработки информации, принятия решения, реализации управляющего воздействия. Такая комплексная проблема известна как проблема разработки диагностического обеспечения. Наиболее трудной задачей этой проблемы считается задача построения диагностической модели (ДМ), которая предназначена для формального отражения процесса изменения ТС ОД. В неявной форме такая ДМ присутствует на всех вышеперечисленных этапах развития СД (рис.2). Особенностью первых трех этапов является то, что ДМ неявно присутствует в сознании О1 и ее качество определяется квалификацией О1. Следующие два этапа требуют разработки явных формальных ДМ.
Тема 2.3. Структура типовой СиТД
На рис.3 представлена развернутая структура типовой СиТД.
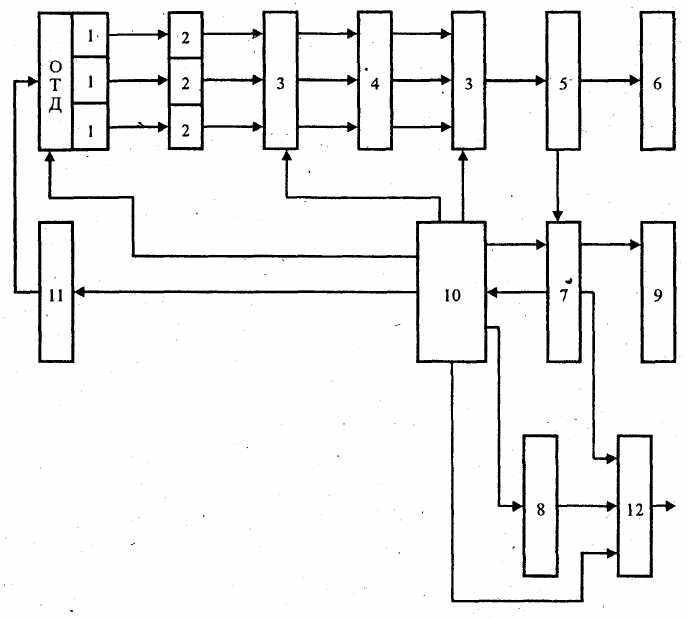
Рисунок 3 – Структура типовой СиТД:
1 – датчики сигналов; 2 – линии связи с усилительными устройствами; 3 – коммутаторы; 4 – преобразователи; 5 – измерительный прибор; 6 – индикатор; 7 – дискриминатор; (устройство сравнения), 8 – поле допусков, вычисленные коэффициенты модели ОД;
9 – индикатор вида ТС (документирующее или запоминающее устройство);
10 – управляющее устройство, 11 – стимулирующее (воздействующее на ОД) устройство; 12 – прогнозирующее устройство.
Первичной подсистемой СТД является измерительное устройство, обеспечивающее заданную точность диагностирования. Так как измерительное устройство, как правило, не может прямо измерять все виды параметров сигналов технической системы или ОД, составными элементами СТД являются такие устройства как коммутаторы и преобразователи.
На выходе измерительного устройства формируется информация позволяющая определить техническое состояние объекта. Эта информация путем различных способов отображения может быть представлена оператору или может быть автоматически обработана для дальнейшего использования.
Важным элементом такой обработки является сравнение представленной информации с полем допусков для вынесения решения о виде ТС ОД.
После принятия решения о ТС ОД осуществляются еще две операции: операция управления качеством изделия и операция стимулирования – изменения структуры ОД.
Прогнозирующее устройство способно определять состояние объекта в будущем посредством обработки информации о текущем и прошлом состояниях системы.
В результате работы функциональных подсистем СиТД, за каждой из которых стоит конкретная схемотехническая реализация, и воздействия на тракт помех и шумов, решения о виде ТС всегда выносятся с определенной ошибкой. Из опыта известно, что ошибки диагностирования могут быть допущены в основном из-за неисправности средства диагностирования и больших погрешностях измерений в процессе диагностирования. Этого можно попытаться избежать применением средств контроля и самодиагностики самих СТД.
Исходя из этого, правильное диагностирование ТС ОД будет определяться совокупным состоянием ОД и СТД, характеристиками измерительных устройств и устройства сравнения, а также правильности применяемых методов диагностирования.
Поэтому количественные характеристики показателей диагностирования должны быть представлены вероятностями состояний ОД и СТД, и вероятностями принятия решений о их ТС.
На количественное значение этих вероятностей в той или иной степени оказывают влияние все элементы структурной схемы технического диагностирования. На погрешность точности измерения параметров сигналов в большей степени влияют:
- выбор допусков на диапазон изменения диагностируемых параметров;
- погрешности преобразования и измерительных приборов;
- аддитивные (ступенчатые одиночные) и мультипликативные (повторяющиеся – шум) помехи, возникающие в самом ОД;
- шумы в каналах связи и в цепях коммутации;
- погрешности сравнения;
- ошибки при принятии решения о ТС;
- быстродействие системы;
- ошибки, возникающие в наборе управляющих и стимулирующих сигналов.
Тема 2.4. Классификация технических средств диагностирования
Техническое диагностирование, как правило, осуществляется путем измерения и контроля количественных значений параметров энергосистемы и, возможно, качественных значений диагностических признаков, анализа и обработки результатов их измерения и контроля, а также путем управления объектами в соответствии с алгоритмом диагностирования.
Диагностический признак – параметр ОД, используемый в установленном порядке (алгоритмом диагностирования) для определения технического состояния ОД.
Большое разнообразие ОД и задач ТД привело к тому, что в настоящее время используются СТД самых различных принципов построения и назначения. Все эти средства отличаются способами технической реализации, конструктивным исполнением и расположением относительно объекта диагностирования, степенью автоматизации и универсальности, принципами воздействия на объект диагностирования, формой обработки и представления информации о состоянии объекта, режимами работы и рядом других признаков. Основные из них указаны на рисунке 4.
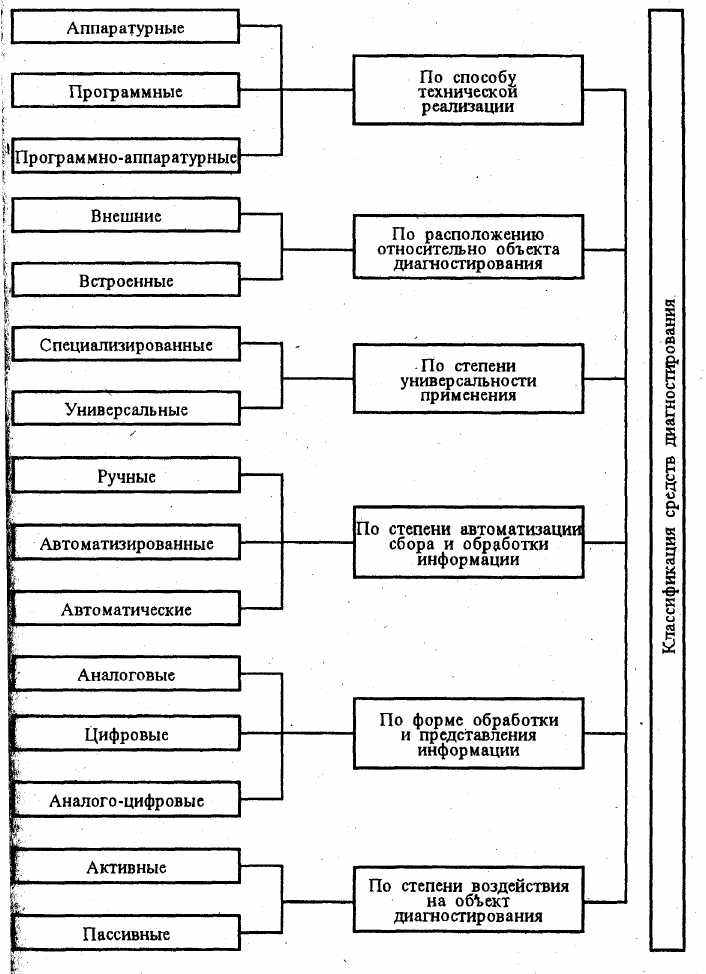
Рисунок 4 – Классификация СТД
К аппаратурным СТД относят различные устройства: приборы, пульты, стенды, специальные вычислительные машины.
Аппаратурные средства, составляющие с объектом диагностирования конструктивно и, возможно, функционально единое целое, являются встроенными аппаратурными средствами диагностирования.
Примерами подобных средств могут быть измерительные приборы (частоты вращения, давления, температуры и т.п.), устройства индикации технического состояния элементов (реле, светоизлучающие диоды, неоновые лампы и т.п.), устройства контроля изоляции и другие, выстроенные в схемы управления дизелями, судовыми электрораспределительными щитами и т.д., часто с целью воздействия результатов диагностирования на работу схем управления.
Если в схемах управления дизелями не предусмотрены встроенные средства диагностирования либо их оказывается недостаточно для диагностирования с требуемой глубиной, то применяют внешние аппаратурные средства диагностирования, выполненные отдельно от конструкции объекта и подключаемые к нему лишь в процессе диагностирования.
Простейшими примерами внешних аппаратурных средств могут быть приборы, присоединяемые к индикаторному крану, моментоскопы, приборы для измерения компрессии и т.п.
Аппаратурные средства диагностирования могут быть специализированными, если они предназначены только для однотипных объектов, или универсальными, если предназначены для объектов различного конструктивного выполнения и функционального назначения.
Программные СТД представляют собой программы, записанные на носителе и применяемые в составе специальных измерительных комплексов, выполненных, как правило, на базе переносных персональных компьютеров.
По степени автоматизации СТД могут быть ручными, автоматизированными и автоматическими.
Применение ручных средств, например, тестеров аналоговых или логических сигналов, требует участия человека-оператора как в подключении СТД к ОД, так и в принятии решений о его ТС. Использование ручных средств дает низкую производительность и недостаточную объективность диагностирования. Как правило, ручные средства выполняются специализированными.
Автоматизированные средства, требуют частичного участия оператора для их подключения к ОД и выбора режимов диагностирования. Основная же процедура диагностирования, включая выдачу информации о ТС ОД, осуществляется автоматически.
Автоматические средства (микропроцессорные комплекты, микро- и мини-ЭВМ) решают задачи диагностирования без вмешательства человека.
Автоматизированные и автоматические средства могут быть как специализированными, так и универсальными Они обладают высоким быстродействием и достоверностью диагностирования.
В зависимости от форм обработки и представления информации СТД могут быть разделены на аналоговые, цифровые, цифро-аналоговые.
По степени воздействия на ОД СТД могут быть активными и пассивными. Активные воздействуют на ОД, посылая в него сигнал, вызывающий реакцию, которая затем и анализируется. Возмущающие сигналы могут быть импульсными, ступенчатыми, гармоническими и др. Пассивные средства выполняют лишь измерения, обработку и оценку сигналов, характеризующих ТС ОД в процессе его эксплуатации, чаще всего на номинальном режиме.
Из всего многообразия средств диагностирования в промышленных ОД наибольшее применение в настоящее время находят аппаратурные средства для определения работоспособности и неисправности отдельных элементов или локальных систем управления ОД. Программные и программно-аппаратурные средства диагностирования получают широкое внедрение по мере распространения микропроцессорных систем управления.
РАЗДЕЛ 3. СПЕЦИФИЧЕСКИЕ ОСОБЕННОСТИ
ДИАГНОСТИРОВАНИЯ ОБОРУДОВАНИЯ СЭУ
Тема 3.1. Распределение отказов на судне
При построении судовых систем диагностирования необходимо учитывать следующее:
- Большое разнообразие судового оборудования по используемым физическим принципам (механические, электромеханические, гидравлические, электронные, радиотехнические и др.) затрудняет получение универсальных решений (методов и ТСД).
- Большое разнообразие конструкций судового оборудования требует построения программы диагностирования с учетом конструкций приборов и устройств. Это усложняет получение универсальных решений и усложняет алгоритмы диагностирования.
- Наличие на судах как дискретных, так и непрерывных объектов определяет различные подходы при решении задач диагностирования. В оборудовании, построенном по дискретному принципу, информация обрабатывается в соответствии с правилами арифметики или формальной логики, что требует использования подобных же принципов при построении алгоритмов диагностирования. Оборудование непрерывного принципа действия преобразует физические величины в соответствии с заложенными отношениями (непрерывными), поэтому диагностирование подобного оборудования должно предусматривать имитацию в той или иной степени этих отношений.
- Различия в структуре судового оборудования. Так на судах имеются как одноканальные, так и многоканальные объекты. К многоканальным относят объекты с функциональным резервированием, избыточного выполнения функций или несколькими независимыми трактами. Возникновение дефектов в многоканальных объектах приводит только к снижению надежности функционирования таких объектов (кроме дефектов в последнем работоспособном резервном контуре).
- Различный уровень надежности судового оборудования затрудняет организацию процесса диагностирования. Трудность сбора статистических данных о надежности судового оборудования, объясняемая ограниченным числом объектов и высокой стоимостью испытаний на надежность, также усложняет принятие решений при определении состояния оборудования на судах.
- Различные режимы использования оборудования на судах. Судовое оборудование можно использовать в длительном режиме: элементы энергетической и электроэнергетической систем, движительная система, насосы постоянной производительности и др.) и кратковременном режиме: агрегаты выдвижения рулей успокоителей качки, управление ВРШ и др. Диагностирование оборудования с длительным режимом использования связано со сложностями исключения влияния на параметры его функционирования режимных факторов. Диагностировать кратковременно используемое оборудование можно в то время, когда оно простаивает (не выполняет свои рабочие функции) или непосредственно перед использованием. Диагностирование оборудования повторно-кратковременного использования необходимо согласовать с режимом его использования.
- Высокая степень автоматизации производственных процессов на судах: А1, А2, А3. Необходимо одновременное автоматизированное диагностирование судовых объектов и диагностирование средств автоматики.
- Ограниченные возможности восстановления судового оборудования из-за недостаточного количества и, зачастую, невысокой квалификации обслуживающего персонала и ограниченного объема запасных деталей. Поэтому при плавании судна в программу диагностирования включают только задачу определения работоспособности. Задачу поиска возникшего дефекта включают в программу диагностирования при нахождении судна на базе (при ремонте). В ряде случаев перед выходом судна в море целесообразно решить задачу прогнозирования, что позволит принять обоснованное решение об использовании оборудования при плавании судна.
- Большое разнообразие условий диагностирования оборудования во многом определяет место расположения средств технического диагностирования (не всегда идеальное).
Можно выделить следующие группы оборудования: энергетическое (дизеля, ГТЗА, АЭУ, гребная электрическая установка, котлы); электрооборудование (генераторы, электродвигатели, распределительные щиты, преобразователи, аккумуляторы); навигационное (гирокомпас, эхолот, авторулевой, автопрокладчик, курсограф, измеритель ветра, качки, эхоледомер, пеленгаторы); радиооборудование (радиолокационные средства, телевидение, радиосредства связи и др.); средства автоматизации, палубные механизмы (швартовные и буксировочные лебедки, якорные и швартовные шпили, грузовые лебедки, стрелы, краны), внутритрюмные механизмы (грузовые устройства, элеваторы); рефрижераторное (холодильные системы, кондиционеры) и др.
Расходы на контроль и ремонт энергетической установки и электрооборудования судна составляют около 80 % общих затрат на контроль и ремонт судна. О распределении отказов в судовых машинах и механизмах свидетельствуют результаты многочисленных анализов, которые, однако, весьма противоречивы. Имеющиеся данные указывают, что на ГД приходится 30-50 % всех дефектов. Из них - 84,9% от всех отказов, составляют отказы главного двигателя. Для более точной оценки важности (а не частоты) отказов энергетической установки можно рассмотреть такой показатель, как время простоя в результате появления отказа (табл. 2).
Таблица 2 - Распределение отказов подсистем главных двигателей KZ70/120,
установленных на судах разных типов
Наименование | Средняя продолжительность простоя, мин | Время простоя, % |
Блок цилиндров, поршневая группа | 211 | 33,5 |
Насос подачи топлива | 65,1 | 14,7 |
Форсунка | 33,6 | 23,5 |
Турбокомпрессор | 97,2 | 13,2 |
Отчетливо проявляется максимальная концентрация отказов в подсистемах ЦПГ – топливо – наддув. Причины отказов судовых ДВС (крейцкопфных): износ − 44,7%, поломка − 11%, загрязнение − 8,5 %, эрозия, кавитация, коррозия − 6,6 %, негерметичность − 5,7 %, старение материала − 3,7 %, заклинивание − 3,7 %.
Износ, поломка и загрязнение вызывают > 60 % всех отказов.