Краткая инструкция по технике безопасности и противопожарным мероприятиям При проведении испытаний двигателей серьезное внимание уделяется технике безопасности и противопожарным мероприятиям
Вид материала | Инструкция |
- Инструкция по правилам и мерам безопасности при работе на компьютерной технике Кабинет, 17.19kb.
- Инструкция №4 по охране труда при погрузочно-разгрузочных работах, 27.34kb.
- Инструкция по технике безопасности при проведении уроков на открытых площадках, 171.11kb.
- Инструкция по технике безопасности при проведении погрузочно-разгрузочных работ, 18.86kb.
- Планирование План конспект урока Лист здоровья (в журнале) Инструкции по технике безопасности, 9.83kb.
- Аннотация дисциплины «прогрессивные методы литья», 29.9kb.
- Инструкция № По технике безопасности при работе на компьютере. I. Общие требования, 156.44kb.
- Инструкция по технике безопасности: Внимание!, 629.5kb.
- Справочное пособие авторы: Арнополин А. Г., Мичков В. И. Рецензент: инж. В. П. Михайлов, 2704.1kb.
- Инструкция по технике безопасности при проведении погрузочно-разгрузочных работ Погрузочно-разгрузочные, 8.98kb.
Новосибирский государственный аграрный университет
Инженерный институт
Теория, основы расчета и испытание
автомобильных двигателей
Журнал лабораторно-практических работ для
студентов специальности 150200
“Автомобили и автомобильное хозяйство”
Фамилия студента __________________
Группа _________
Преподаватель _____________________
Новосибирск 2010
Кафедра «Автомобили и тракторы»
Теория, основы расчета и испытание автомобильных двигателей. Журнал лабораторно-практических работ для студентов специальности 150200 / Новосиб. гос. аграр. ун-т. Инженер. ин-т; Сост.: П.И. Федюнин, В.А. Комлев, С.П. Сальников, Е.А. Булаев, И.С. Белоусов. – Новосибирск, 2010.- 40 c.
Рецензент : канд. техн. наук. проф. В.И. Воробьёв
В журнале даны краткая инструкция по технике безопасности, организационно-методические указания, формулы для обработки полученных опытных данных, а также таблицы и поля графиков, которые студенты заполняют и вычерчивают по результатам опытов.
Утверждены и рекомендованы к изданию методической комиссией Инженерного института (протокол № __ от ___________ 2010 г.)
Новосибирский государственный аграрный университет, 2010
Инженерный институт, 2010
Краткая инструкция по технике безопасности и
противопожарным мероприятиям
- При проведении испытаний двигателей серьезное внимание уделяется технике безопасности и противопожарным мероприятиям.
- Все приводные и соединительные устройства вращающихся деталей должны иметь надежные ограждения.
- Запрещается производить какие-либо регулировки и техобслуживание при работе двигателя и электростенда.
- Перед началом испытаний необходимо произвести наружный осмотр тормозных стендов и двигателей. Запрещается работа на стендах при отсутствии защитных кожухов у коллектора двигателя, на реостате, над муфтой, соединяющей редуктор с электродвигателем, и над соединением двигателя со стендом. Особое внимание следует обращать на крепление и шплинтовку деталей соединительной гибкой муфты и карданного вала, а также на крепление двигателя к раме электротормоза. Необходимо проверить заправку двигателя маслом и водой.
- В случае перегревания двигателя нужно осторожно открыть крышку верхнего бака радиатора, пользуясь рукавицами или тряпками, так как возможны ожоги паром и кипящей водой. При перегреве следует плавно уменьшать обороты двигателя и дать ему возможность охладиться при работе без нагрузки.
- Нельзя касаться нагретых стенок выхлопных труб, коллектора двигателя и экрана термопары.
- При появлении ненормального стука в двигателе, тормозном стенде и стенде для регулировки топливных насосов или в других агрегатах студент обязан выключить работающий агрегат.
- Пользование открытым огнем, а также курение в лаборатории испытаний двигателей категорически запрещаются.
- Запрещается всякое хранение топлива и масел в дополнительных емкостях в лаборатории испытаний двигателей.
- Недопустимы подтекания топлива и масла.
- Лаборатория должна иметь хорошую вытяжную вентиляцию и освещение.
- Внутри помещения должны быть необходимые противопожарные средства для тушения горящих нефтепродуктов (огнетушители, ящики с песком, кошма). Заливать водой горящее топливо или масло категорически запрещается.
- На пуск двигателя необходимо получить разрешение руководителя и подать сигнал.
- Во избежание аварии запрещается сообщать валу двигателя стендов типа СТЭУ – 40 более 2200 мин-1.
Подпись студента _________________
Общие положения
Испытания являются завершающим этапом технологического процесса производства двигателей и предназначены для контроля качества их производства и соответствия характеристик техническим условиям на поставку.
Испытание двигателей можно подразделить на опытно-конструкторские и серийные [1].
Опытно-конструкторские испытания делятся на исследовательские и контрольные.
Исследовательские испытания проводятся для изучения определенных свойств конкретного двигателя и в зависимости от целей могут быть доводочными, испытаниями на надежность и граничными.
Доводочные испытания предназначены для оценки конструктивных решений, принятых для достижения мощностных и экономических показателей, установленных в техническом задании.
Граничные испытания проводятся для оценки зависимости мощностных, экономических показателей и работоспособности двигателя от граничных условий, установленных в техническом задании.
Контрольные испытания предназначены для оценки соответствия всех показателей опытного двигателя требованиям технического задания.
Серийные испытания делятся на приемо-сдаточные, периодические и типовые.
Приемо-сдаточные испытания проводятся с целью проверки качества сборки двигателя и отдельных его узлов, приработки трущихся поверхностей, определения соответствия показателей двигателя техническим условиям на поставку.
Периодические испытания предназначены для периодического контроля стабильности технологического процесса в период между этими испытаниями, подтверждения возможности продолжения изготовления двигателей.
Тормозные устройства
Тормозные устройства служат для создания внешнего сопротивления, которое поглощает мощность, развиваемую двигателем. Такие стенды должны иметь топливную, воздухопитательную и газоотводящую системы.
В зависимости от принципа создания тормозного момента различают механические, воздушные, гидравлические и электрические тормозные устройства. Первые три типа тормозных устройств используют только для торможения двигателей, а электрические тормоза – также для пуска и холодной обкатки двигателя.
Тормоз любого типа характеризуется следующими основными параметрами: максимальной NTmax и минимальной NTmin поглощаемыми мощностями; максимальной и минимальной частотами вращения; максимальным и минимальным тормозными моментами.
В механических тормозах механическая энергия, развиваемая двигателем поглощается работой сил трения. Шкив механического тормоза охватывается гибкой стальной лентой, облицованной фрикционным материалом, благодаря чему между шкивом и лентой возникают силы трения, которые компенсируют энергию, развиваемую двигателем, превращая ее в тепло, которое отводится в охлаждающую воду.
Механические тормоза просты по устройству, но обладают малой энергоемкостью, нестабильной характеристикой и плохой способностью к саморегулированию (момент торможения у них почти не зависит от частоты вращения).
В воздушных тормозах развиваемая двигателем мощность затрачивается на перемещение и частично на нагрев воздуха.
Гидравлические тормоза весьма энергоемки, просты по конструкции и в свое время получили широкое распространение в практике стендовых испытаний двигателей. Поглощаемая гидравлическим тормозом энергия расходуется на совершение гидродинамической работы и работы трения (вращающегося ротора о жидкость).
По конструкции в основном различают штифтовые, дисковые и лопастные гидравлические тормоза.
Электрические тормоза, обладающие рядом преимуществ по сравнению с механическими и гидравлическими, нашли широкое применение в испытательской практике.
Электрические тормоза переменного тока на базе асинхронных двигателей с фазным ротором просты по устройству, имеют сравнительно небольшие габариты, но не обеспечивают достаточно широкого диапазона регулирования частоты вращения.
Электрические тормозные стенды ГОСНИТИ с асинхронными электрическими машинами применяют для обкатки и испытаний тракторных, комбайновых и автомобильных двигателей.
На рис. 1 показано устройство стенда ГОСНИТИ с асинхронной машиной типа АК. Балансирная электрическая машина 1 цапфами боковых щитов опирается на шариковую самоустанавливающиеся подшипники стоек 2. К плите 3 прикреплены стойки 2 и стойка маятникового весового механизма 4.
Карданный вал 6 соединяет между собой валы ротора машины и испытуемого двигателя. Частота вращения вала машины измеряется электрическим тахометром, датчик 5 которого приводится во вращение от вала машины через зубчатую передачу.
Жидкостной регулировочный реостат предназначен для изменения тока в обмотке ротора и тем самым частоты вращения вала асинхронной машины, как в режиме двигателя (холодная обкатка), так и в режиме генератора (горячая обкатка и испытания двигателя). Реостат представляет собой за-
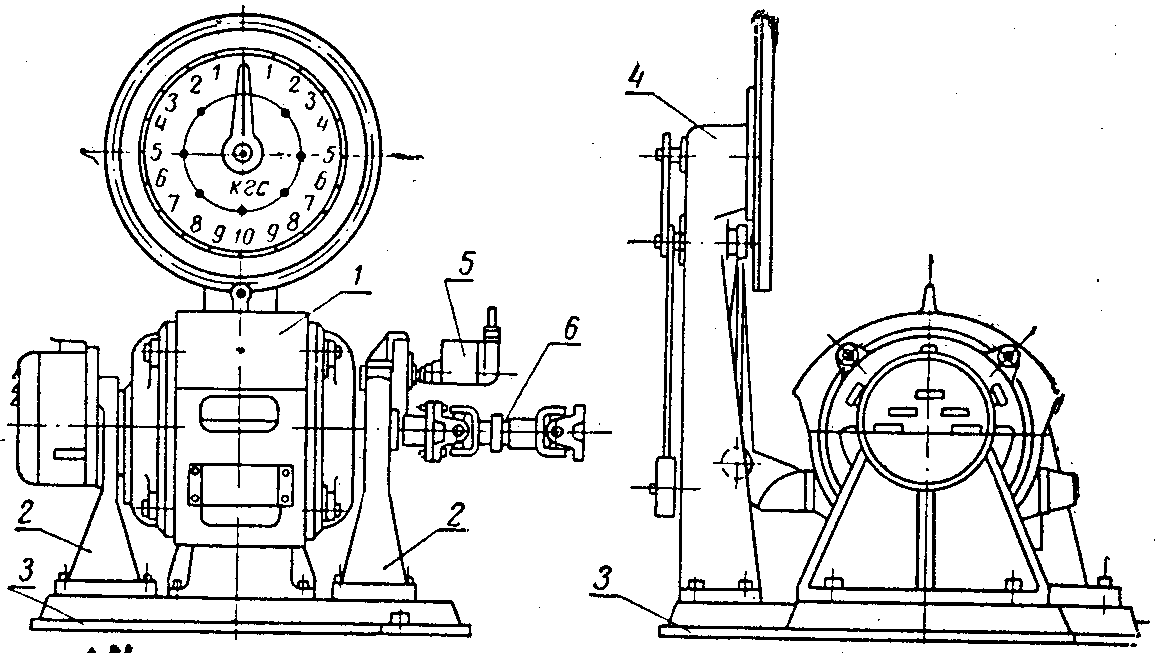
Рис. 1. Электрический стенд ГОСНИТИ с асинхронной машиной типа АК: 1 – асинхронная машина; 2 – стойка; 3 – плита; 4 – весовой механизм; 5 – датчик электрического тахометра; 6 – карданный вал.
крытый сетчатым кожухом бак емкостью 300 л, наполненный 1–3 % - ным раствором кальцинированной соды. Внутри бака на валу при помощи изолятора укреплены три электрода, каждый из которых состоит из трех стальных пластин, средний из которых основная, а две боковых – дополнительные. Каждый электрод соединен проводом с фазовой обмоткой ротора. Изменяя степень погружения электродов в жидкость, регулируют активное сопротивление в обмотках ротора и тем самым частоту его вращения (в режиме двигателя) или нагрузку (в режиме генератора).
Температура жидкости в баке (около 50С) поддерживается при помощи электропомпы, перемешивающей раствор, и охлаждающей воды, циркулирующей в рубашке бака.
Если раньше на стендах с машиной типа АК реостат приводился в движение рукояткой червячной передачи, то теперь на стендах с машиной типа АКБ благодаря применению электрического исполнительного механизма работой реостата можно управлять дистанционно, при помощи кнопок управления, расположенных на отдельном пульте.
На основном пульте управления стендом, кроме циферблата весового механизма, установлены манометр для измерения давления масла в системе смазки двигателя, два указателя дистанционных термометров для измерения температуры воды на входе и выходе из рубашки двигателя, измеритель электрического тахометра.
Асинхронные балансирные тормозные машины типа АКБ по сравнению с машинами типа АК обладают рядом особенностей: щеточный механизм введен в корпус машины, на боковых щитах предусмотрены цапфы для балансирной подвески машины на стойках, увеличено сечение обмотки ротора, бандажи ротора из стальной проволоки заменены лентой из стеклоткани, вал ротора выведен в оба конца машины. Все эти усовершенствования позволили тормозной машине работать с частотой вращения до 3000 мин-1.
На рисунке 2 в качестве примера приведена электрическая схема стенда СТЭУ-40. Перед пуском электродвигателя включают рубильник Р сети. Загораются сигнальные лампы Л, показывающие, что все фазовые обмотки балансирной машины БМ находятся под напряжением.
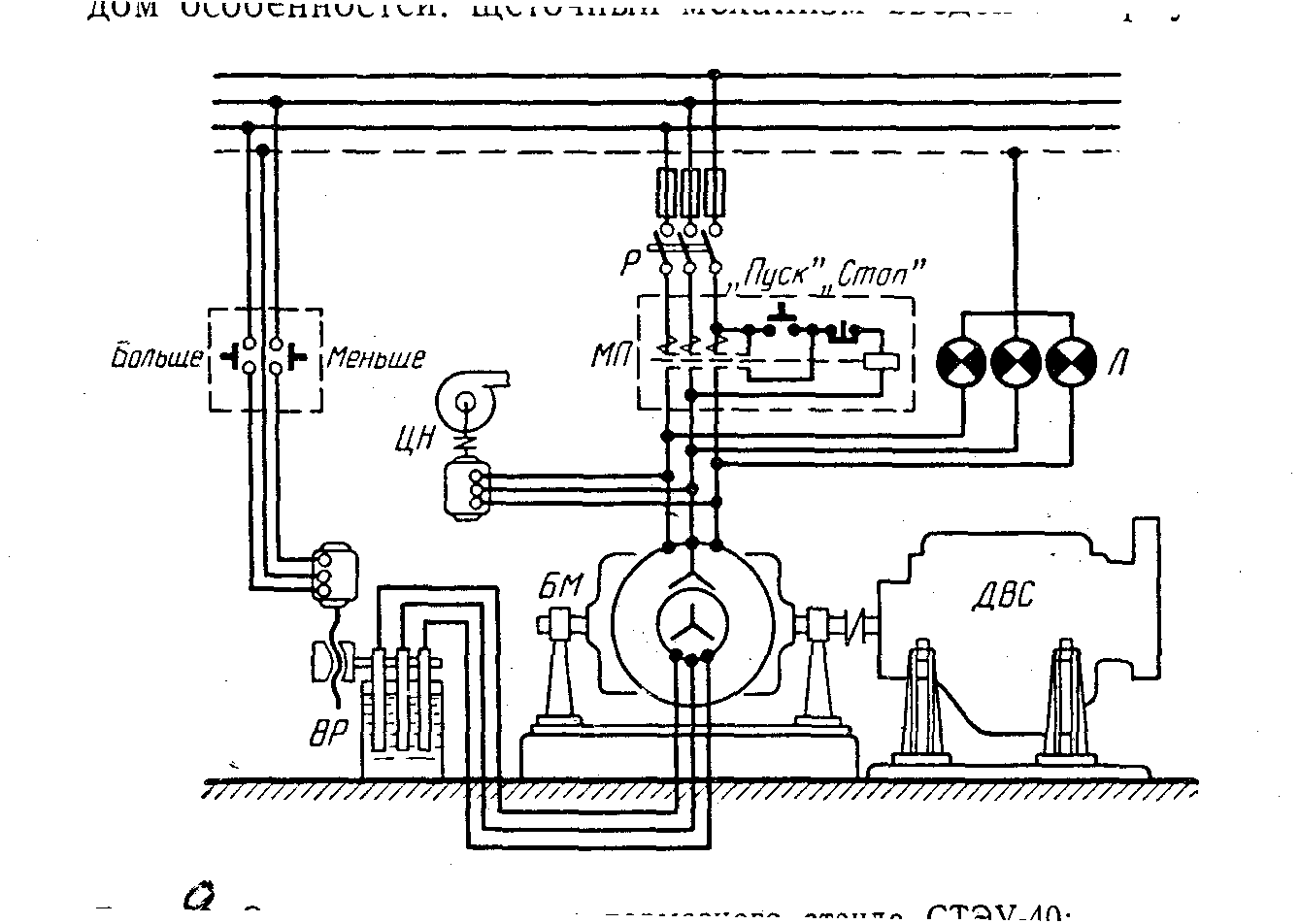
Рис. 2. Электрическая схема тормозного стенда СТЭУ-40: Р – рубильник; МП – магнитный пускатель; Л – сигнальные лампы; БМ – балансирная машина – асинхронный электродвигатель с фазным ротором; ДВС – испытуемый двигатель внутреннего сгорания; ВР – водяной реостат в цепи ротора; ЦН – циркулярный насос системы охлаждения водяного реостата.
Нажав кнопку «Пуск» магнитного пускателя и постепенно заглубляя электроды жидкостного реостата, приводят во вращение ротор электрической машины БМ и вал двигателя ДВС. С увеличением заглубления электродов частота вращения ротора повышается.
После включения зажигания (подачи топлива), пуска испытуемого ДВС и повышения частоты вращения более чем 1000 об/мин электрическая машина БМ перейдет в режим работы генератора и, тормозя испытуемый двигатель, будет отдавать электроэнергию в сеть. По данным испытаний стендов ГОСНИТИ, коэффициент отдачи электроэнергии в сеть (в интервале тормозной мощности) составляет 0,7.
Следует заметить, что стенды ГОСНИТИ оснащены автоматическими устройствами, обеспечивающими переключение заданных режимов обкатки и испытания двигателя и контроль за его работой. Так, применены дистанционное управление реостатом; автоблокировка, предотвращающая запуск стенда, если электроды реостата не находятся в исходном положении; световая сигнализация; дистанционные указатели давления и температуры масла в системе смазки и температуры воды в системе охлаждения; дистанционный указатель частоты вращения вала тормоза и др.
Недостатком рассмотренных балансирных машин трехфазного тока является ограниченный предел минимальной частоты вращения (1000 мин-1) при работе машины в тормозном режиме.
Организационно-методические указания
при испытаниях ДВС
- До начала испытаний необходимо проверить наружные крепления стенда и двигателя, заправку водой и маслом, отсутствие подтекания топлива. При необходимости производят тарировку стенда по определению достоверности показаний.
- В процессе подготовки к испытаниям нужно ознакомиться с устройством и оборудованием стенда, приборами, техникой проведения замеров, формой сводной документации.
- Перед испытанием двигатель должен быть прогрет до номинального теплового состояния.
- Студенты-исполнители в течение одного лабораторного занятия работают на определенных рабочих местах, на следующих лабораторных занятиях состав исполнителей может меняться. Рекомендуем следующие рабочие места:
а) Двигатель (1-2 студента). Запуск двигателя. Изменения положения дросселя карбюратора или рычага управления топливного насоса. Изменение угла опережения зажигания. Замер перепада давления по дифференциальному манометру и угла опережения зажигания.
б) Регулировочный реостат (1 студент). Изменение нагрузки двигателя регулировочным реостатом для установления требуемого скоростного и нагрузочного режимов.
в) Пульт управления (2 студента). Запись в журнал наблюдений показаний приборов.
г) Замер расхода топлива (1-2 студента). Измеряется расход топлива и продолжительность опыта.
д) Построение дежурной кривой (1 студент). Строится кривая непосредственно по результатам опыта.
е) Регистрация барометрического давления и температуры окружающего воздуха (1 студент). Непосредственное руководство проведением опытов (1 студент-бригадир) – подача сигнала начала опыта (один звонок) и окончания опыта (два звонка).
5. Результаты тормозных испытаний ДВС заносятся в таблицы.
Обработка опытных данных
Эффективная мощность двигателя Ne (л.с.) при испытаниях может быть рассчитана по формуле
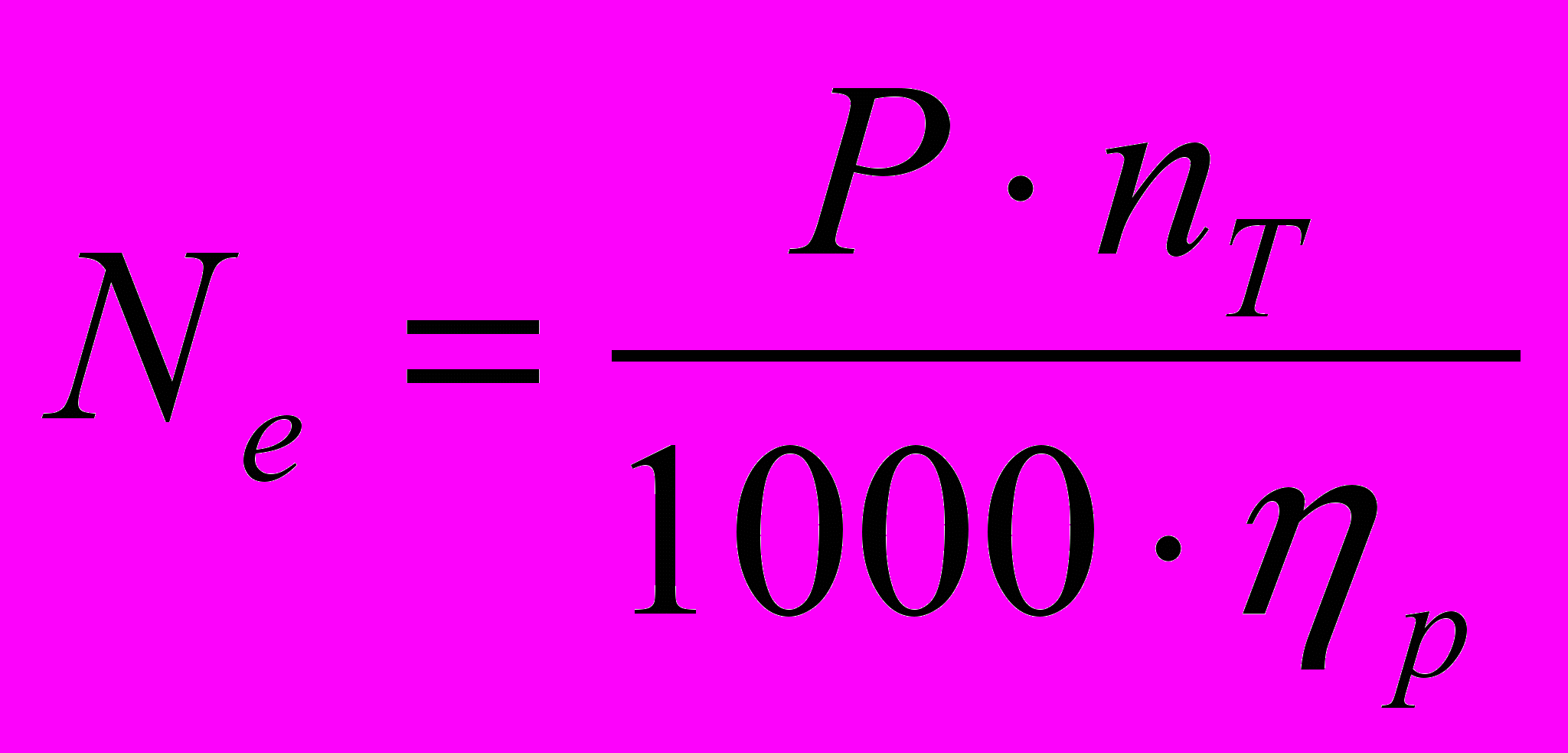
1 л.с. = 0,736 кВт (2)
где P – тормозное усилие, определяемое по шкале весов тормозного стенда, кгс;
nT – частота вращения вала тормоза, мин-1;
р – механический КПД редуктора, р = 0,96-0,98.
При отсутствии редуктора
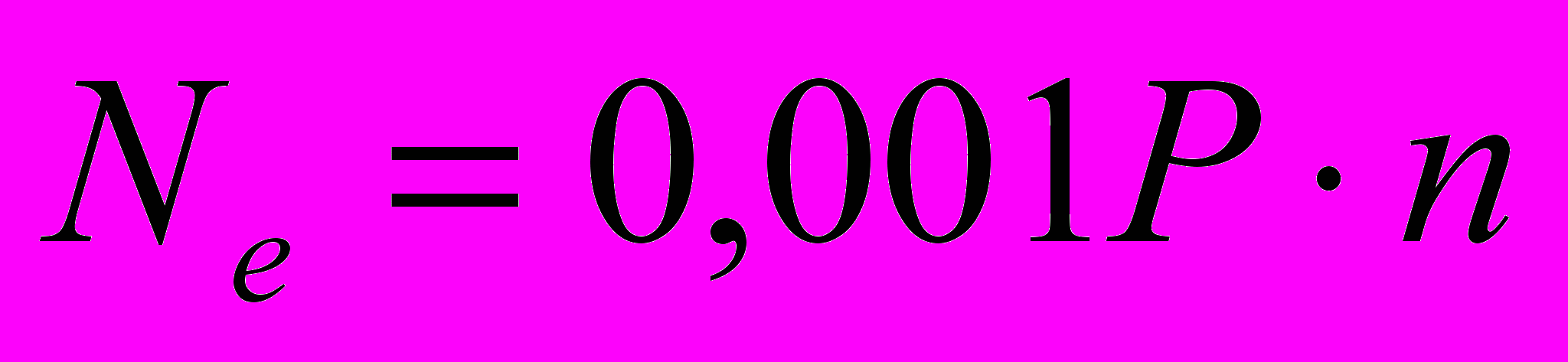
где n – частота вращения коленчатого вала двигателя.
Массовый (часовой) расход топлива GТ (кг/ч) вычисляется по формуле
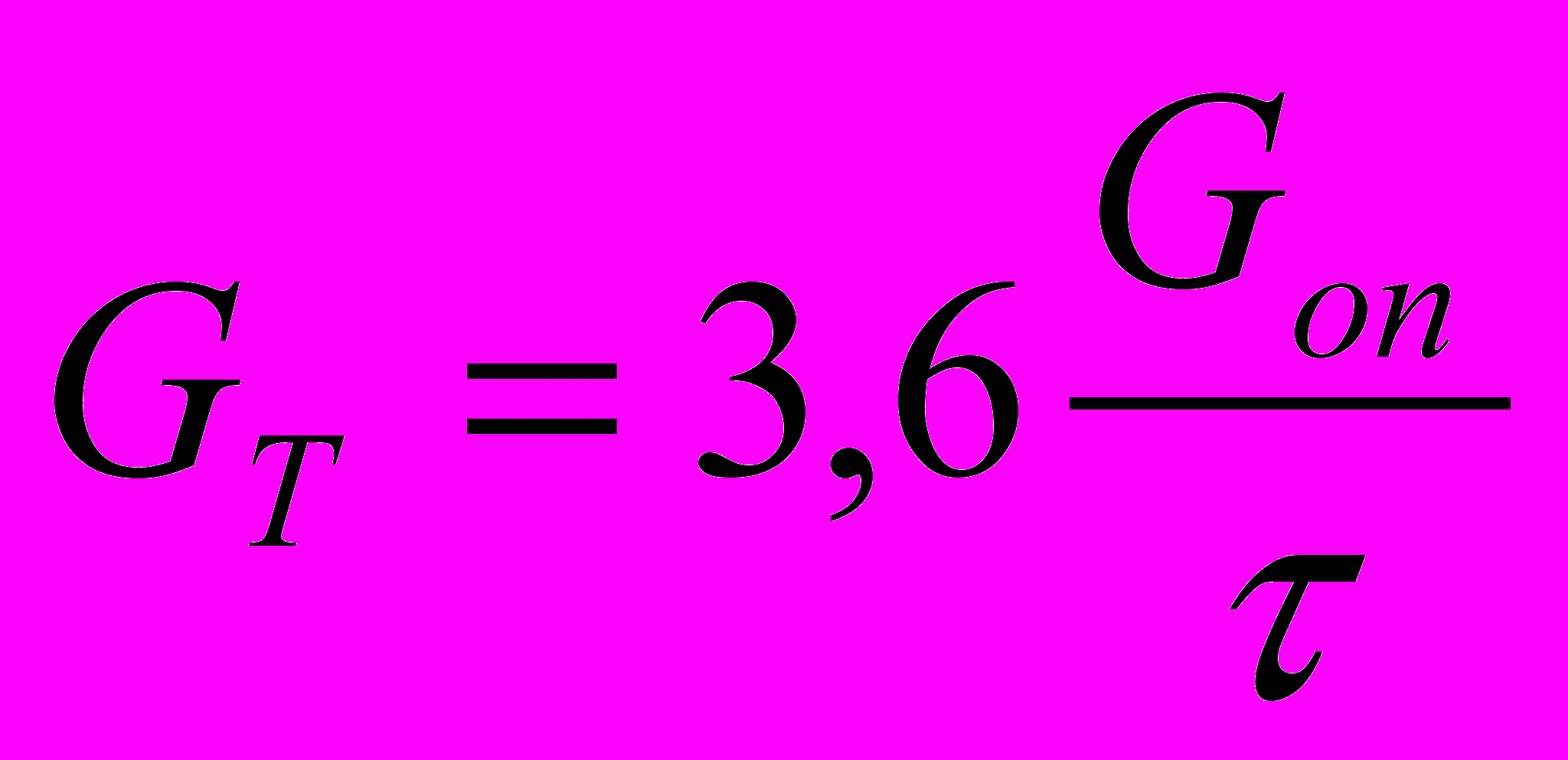
или при измерении GТ в других единицах г/с:
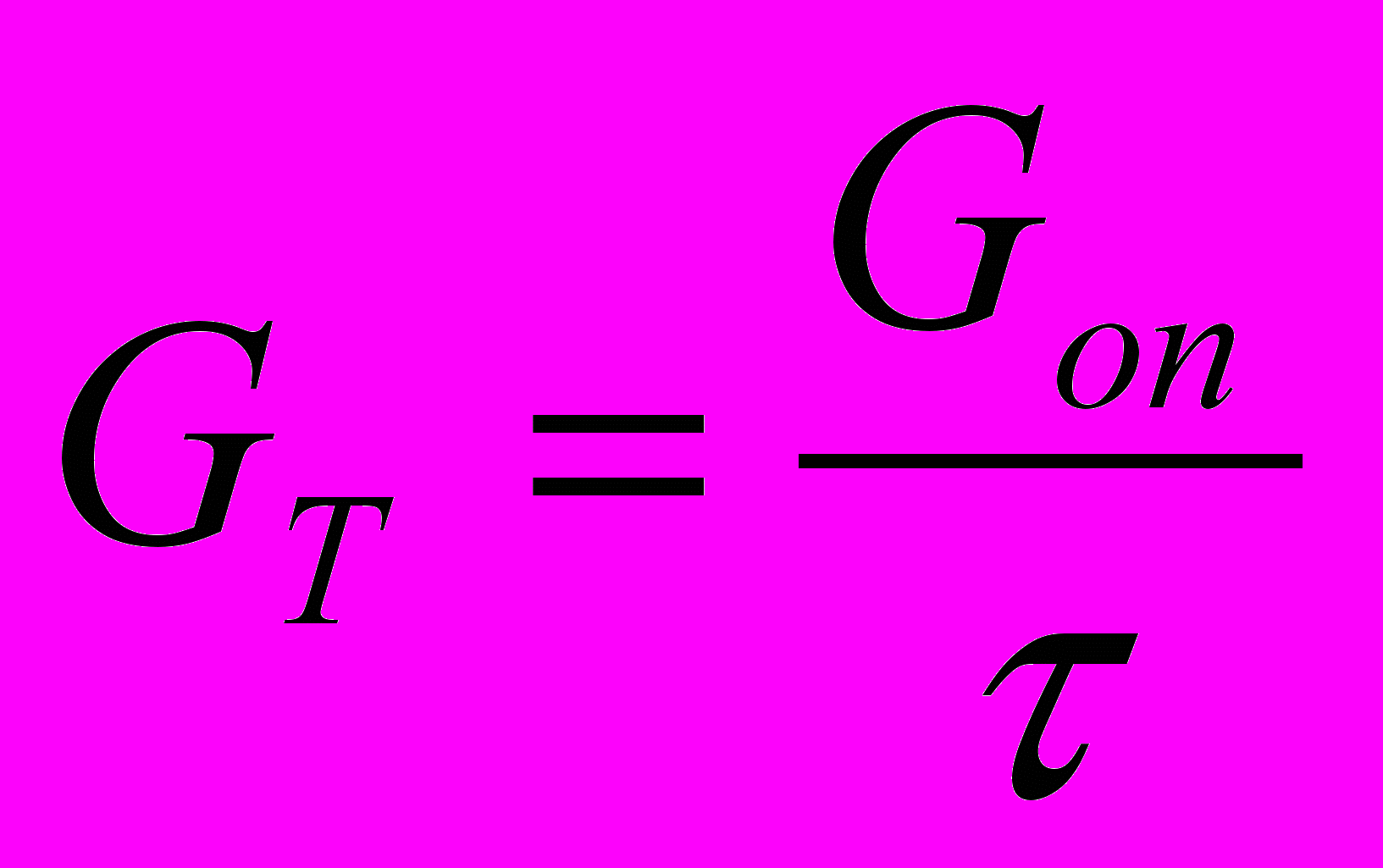
где Gоп – расход топлива двигателем за опыт, г;
- продолжительность опыта, с.
Удельный расход топлива gе (г/л.с.ч) определяется соотношением
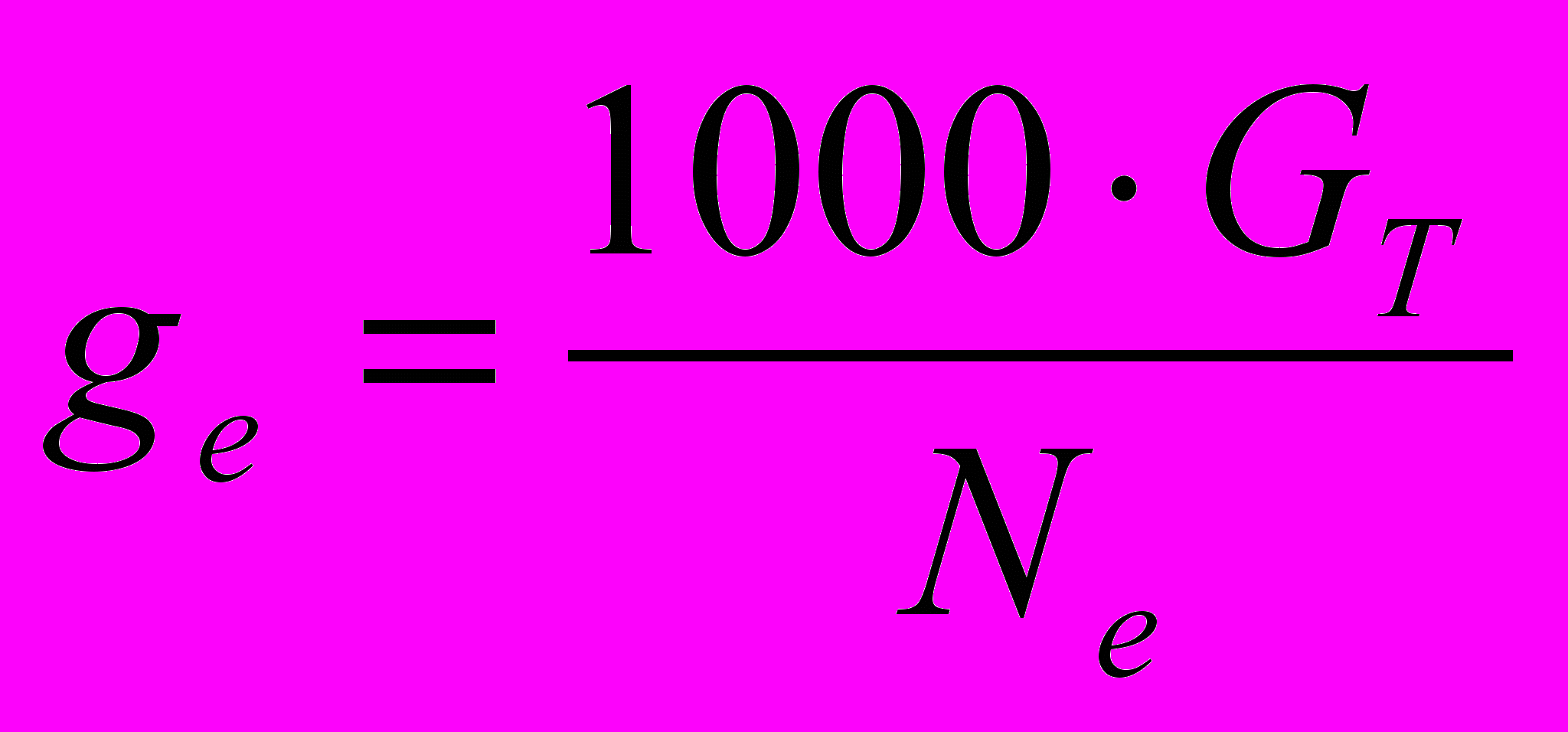
Крутящий момент двигателя Me (Нм, кгсм) рассчитываем по формуле
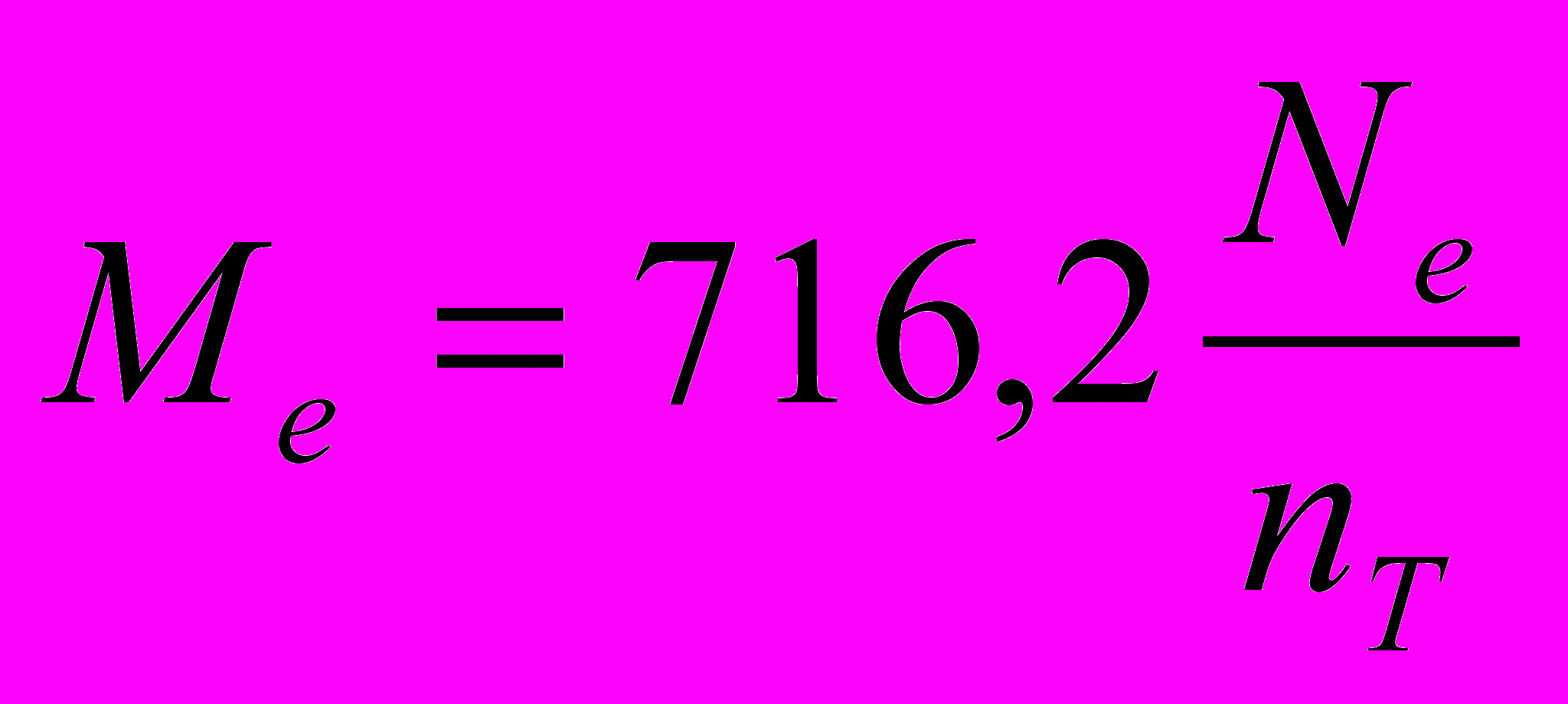
В частности, при условии отсутствия редуктора
nT = n, р = 1,
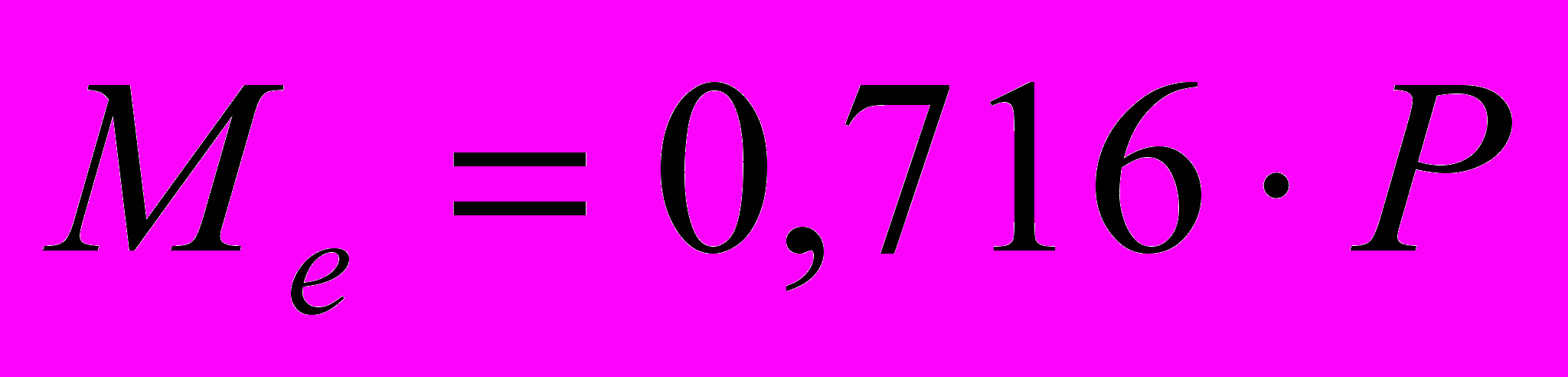
Приведение результатов испытания двигателя
к нормальным условиям
Изменение атмосферных условий относительно стандартных и температуры топлива вызывает соответствующее изменение мощностно-экономических показателей. Согласно ГОСТам 18509 – 88 и 14846 – 69 за стандартные условия приняты: барометрическое давление B0 = 1013 гПа (760 мм рт. ст.), температура воздуха tокр =20С, относительная влажность воздуха окр = 50%, температура топлива tт = 20С.
Для дизельных двигателей без турбонаддува повышение tокр на 1С и понижение В0 на 1 гПа вызывает соответствующее уменьшение эффективной мощности на 0,15% и 0,045% (0,06% на 1 мм рт. ст.). На аналогичные величины повышается удельный расход топлива.
Применительно к карбюраторным двигателям уменьшение и увеличение удельного расхода топлива составляет 0,18% при повышении tокр на каждый градус и на 0,1% при понижении атмосферного давления В0 на каждый гектопаскаль (0,135% на 1 мм рт. ст.).
Построение графиков. Масштабы
Результаты обработки данных испытаний изображают в виде графиков-характеристик, которые служат основной технической документацией испытаний двигателя. Для изображения графиков зависимостей данной характеристики необходимо заранее заготовить форматки на миллиметровой бумаге. Стандартные размеры форматок приведены в ГОСТ 18509 – 73.
Данные опытов, полученные в результате измерений (Ne, GT, t), на графиках обычно изображают в виде маленьких окружностей диаметром 1–2 мм. Полученные точки соединяют кривой так, чтобы на ней уложилось наибольшее количество кружков. Не следует соединять их прямыми отрезками, так как в этом случае получается ломаная линия, искажающая характер протекания действительного процесса работы двигателя.
Величины Mкр, Pе, gе и др., полученные в результате расчетов, откладывают на графике в виде точек, а не окружностей, и кривые изменения этих величин строят в виде сплошных линий.
При соединении плавной кривой опытных точек следует уделять внимание выпавшим точкам и устанавливать причины, которые могли это вызвать.
Прежде чем строить характеристики, весьма важно выбрать правильные масштабы. Основное правило здесь – наглядность, простота понимания графика и полное использование площади форматки. При выборе масштаба необходимо руководствоваться ГОСТ 18509 – 73.
Рационально выбранный масштаб графика в значительной мере облегчает выявление закономерностей протекания процесса и уменьшает разброс точек при построении характеристик.
Лабораторная работа №1
Обкатка двигателей
Назначение обкатки. Обкатка — часть технологического процесса ремонта. Во время обкатки происходит приработка рабочих поверхностей деталей, осадка прокладок, выявляются и устраняются отдельные дефекты сборки.
Рабочие поверхности прирабатываются с постепенным уменьшением интенсивности изнашивания. Однако завершается приработка только через несколько десятков, а иногда и сотен часов работы дизеля. В этой связи обкатку разделили на стендовую и эксплуатационную.
Стендовая обкатка выполняется на ремонтных предприятиях. Ее режимы определены для каждой конкретной модели дизеля в нормативно-технической документации.
Эксплуатационная обкатка проводится на предприятиях (в хозяйствах) при последовательном увеличении нагрузки по режимам обкатки той машины, на которой установлен дизель. Оптимальная продолжительность этого вида обкатки находится в пределах 30...60 ч работы дизеля.
Износостойкость новой детали, полученной механической обработкой, условно может быть рассмотрена как суммарная величина, обусловленная износостойкостью основного материала и свойствами рабочего поверхностного слоя, т. е. геометрическими и физико-механическими свойствами, сообщаемыми поверхности в процессе механической обработки. Первая составляющая — физико-механические свойства основного материала — играет значительную роль как в начальный период работы детали, так и в период эксплуатации. Вторая условная составляющая — физико-механические свойства поверхностного слоя материала — имеет технологическую природу, связана с особенностями процесса механической обработки, когда создается микрорельеф и происходит некоторое изменение пластичности и напряженности поверхностного слоя.
Эта составляющая определяется качеством поверхностей трущихся деталей и проявляется только в период их приработки, характеризующий начальную износостойкость. Качество рабочих поверхностей деталей слагается из ряда параметров: шероховатости, микротвердости, микронеровности размера остаточных напряжений и др.
Продолжительность и качество приработки зависят в значительной степени также от качества сборки (соблюдение установленных в технической документации зазоров, параллельности осей и контактирующих поверхностей). Нарушение технологической дисциплины при сборке приводит к необходимости увеличения продолжительности процесса приработки. При прочих равных условиях качество приработки зависит от нагрузки на трущиеся поверхности, их относительной скорости перемещения, температуры контактирующих поверхностей, качества и эффективности фильтрации картерной смазки (удаления продуктов износа).
С учетом этого в задачу обкатки дизелей входит: получение высокого качества рабочих поверхностей деталей при минимальном их износе в процессе обкатки; завершение приработки при минимальной продолжительности обкатки.
Сокращение продолжительности приработки не должно приводить к сокращению послеремонтного ресурса работы дизелей.
Идеально было бы иметь для каждого дизеля свою программу обкатки, которая учитывала бы конкретные его особенности, такие как качество рабочих поверхностей деталей, качество сборки, литраж, мощность и частоту вращения коленчатого вала. Однако пока нет достаточно надежных, пригодных для применения в условиях ремонтного производства средств и критериев, позволяющих определить момент завершения приработки.
В этой связи нормативно-технической документацией на капитальный ремонт установлены единые режимы обкатки для дизелей каждой модели, гарантирующие достижение такой степени приработки, при которой он подготовлен для проведения приемо-сдаточных испытаний (приемочного контроля).
Основное соединение, определяющее качество приработки дизелей, — гильза цилиндра — поршневые кольца. После завершения приработки трущихся поверхностей этих деталей принято считать обкатку двигателя законченной. В условиях ремонтного производства прямое измерение качества приработки в процессе обкатки не представляется возможным, поэтому для оценки качества приработки дизелей обычно используют технико-экономические параметры (эффективную мощность, удельный расход топлива, расход масла на угар). Значение этих показателей дается в нормативно-технической документации на капитальный ремонт дизелей.
Обкатка дизелей. Стендовой обкатке подвергают каждый дизель, выходящий из капитального ремонта.
Стендовая обкатка включает в себя холодную обкатку, обкатку на холостом ходу и горячую обкатку (обкатку под нагрузкой).
Обкатку проводят на летнем дизельном топливе (ГОСТ 305—82) и на моторном масле М-10В или М-10Г2. Физико-технические параметры топлива и масла должны быть удостоверены документом.
На обкатку и испытания дизели поставляют без вентилятора, гидронасоса, водяного и масляного радиаторов, выпускной трубы и искрогасителя. Допускается обкатка без генератора с применением натяжного ролика. Технологический воздухоочиститель должен иметь устройство для прекращения (в случае аварийной ситуации) поступления воздуха в цилиндры дизеля.
Холодная обкатка. Холодную обкатку дизелей выполняют на режимах, указанных в таблице 1.
Таблица 1.
Режимы холодной обкатки дизеля Д-240
Дизель | Показатели на ступенях обкатки | ||||||
первая | вторая | третья | продолжительность этапа, мин | ||||
частота вращения, мин-1 | продолжительность, мин | частота вращения, мин-1 | продолжительность, мин | частота вращения, мин-1 | продолжительность, мин | ||
Д-240 | 500 – 600 | 10 | 700 –800 | 10 | 900 – 950 | 10 | 30 |
В процессе обкатки поддерживают следующие условия: давление масла в магистрали не менее 0,15 МПа; температура воды на выходе из дизеля 60...75 °С.
Подтекание и каплеобразование топлива, масла и воды в местах соединения трубопроводов и плоскостей стыков соединяемых деталей не допускается. В случае появления посторонних стуков и шумов в дизелях обкатку прекращают и устраняют неисправность.
После завершения холодной обкатки проверяют правильность установки угла начала подачи топлива до в. м. т., зазоров между бойками коромысел и торцами стержней клапанов.
Горячая обкатка на холостом ходу. Этап обкатки проводят по трем или более ступеням (в зависимости от модели дизеля), продолжительность каждой 5...10 мин. Первая ступень обкатки начинается при частоте вращения коленчатого вала, равной 65...70% номинальной, и затем через определенные интервалы последовательным переводом на следующие ступени доводят частоту вращения до номинальной (табл. 2). После окончания обкатки проверяют затяжку гаек шпилек крепления; головки цилиндров дизеля.
Таблица 2.
Режимы обкатки дизеля Д-240 на холостом ходу.
Дизель | Показатели на ступенях обкатки | ||||||
первая | вторая | третья | продолжительность этапа, мин | ||||
частота вращения, мин-1 | продолжительность, мин | частота вращения, мин-1 | продолжительность, мин | частота вращения, мин-1 | продолжительность, мин | ||
Д-240 | 1000 | 5 | 1400 –1800 | 10 | 1900 | 5 | 20 |