П. В. Русаков, О. И. Шинский, Н. И. Тарасевич
Вид материала | Документы |
СодержаниеТаблица 1. технические характеристики экспериментального стенда Диапазон изменений Таблица 2. Исходные данные Диапазон изменения значений Таблица 3. Расчетные параметры литья |
- Современные тенденции конструирования опочной оснастки для лгм, 140.67kb.
- И. О. Шинский, к т. н., В. С. Дорошенко, к т. н., О. И. Шинский, д т. н., И. Т. Соловко,, 327.56kb.
- Песчаные смеси на основе пенополистирола для литейных форм и стержней. Способ вторичного, 29.41kb.
- Шинский И. О., к т. н., Дорошенко В. С.,, 42.46kb.
- Современные знания — в жизнь, 3735.25kb.
- Виконав: Павлюк О. В., ст гр. Уп-06-з Перевірив: Тарасевич В. М. проф.,, 518.71kb.
- Блок «Изучение этнических меньшинств» 34 часа, 64.17kb.
- Ахромеева Т. С., Капустин М. А., Кащенко С. А., Куракин П. В., Малинецкий Г. Г., Медведев И., 459.22kb.
- Название доклада «Эмоциональное здоровье школьника и корреция психо-эмоциональной сферы, 31.49kb.
- Программа конференции october 03 07, 2011 Saratov, Russia, 524.92kb.
УДК 621.74.045
П.В.Русаков, О.И.Шинский, Н.И.Тарасевич
Физико-технологический институт металлов и сплавов НАН Украины, Киев
ДИНАМИКА ДВИЖЕНИЯ ПУАНСОНА И СНИЖЕНИЕ ОСТАТОЧНЫХ НАПРЯЖЕНИЙ В ПРОЦЕССАХ ФОРМИРОВАНИЯ СТАЛЬНОЙ ОТЛИВКИ В ПЕСЧАНОЙ ФОРМЕ
Проведены экспериментальные исследования динамики процессов литья и управляемого формирования стальных сосудов в песчаной форме с выжигаемой моделью. Применение математических методов моделирования теплофизических процессов и научно обоснованных методик определения оптимальных значений технологических параметров литья позволило совместить в одном цикле процессы формирования отливки с операцией снижения остаточных напряжений.
Проведено експериментальне дослідження динаміки процесів лиття та керованого формування стальних посудин у піщаній формі з випалювальною моделлю. Застосування математичних методів моделювання теплофізичних процесів та науково обґрунтованих методик визначення оптимальних значень технологічних параметрів лиття дозволило поєднати в одному циклі процеси формування виливки та операцію зниження залишкових напружень.
The dynamics of casting processes and controlled formation of lost-wax steel vessels in sand molds were investigated. The use of mathematical methods of modeling and scientifically proved methods for determination of technological parameters optimal values allow to combine the processes of casting formation and residual stresses decrease in one cycle.
Процесс принудительного формирования отливок в песчаной форме можно охарактеризовать как силовой возмущение пуансоном жидкого расплава, в дальнейшем твердеющего, в интервале полного цикла формирования отливки. Для реализации процесса дозу расплава с необходимым запасом тепловой энергии принудительно выжимают пуансоном в песчаную форму, которую рассматривают как объект температурного и силового воздействия. Качество протекающих при этом процессов зависит от давления в камере выжимания и в полости песчаной формы, скорости движения пуансона и впуска жидкого металла в форму, проходного сечения литника, начальной температуры жидкого расплава, а также режимов газового разрежения, создаваемых в рабочей полости формы. Некоторые из этих параметров не всегда контролируются в процессе работы машины, что приводит к литейному браку и разрушению песчаной формы.
Как показала практика, для реализации процессов литья по газифицируемым моделям способом выжимания металла в форму необходимо специальное оборудование, которое выполняет заданные программы заполнения формы в функции времени или по перемещению положения фронта жидкого металла. Кроме того, необходимы дополнительные специальные возможности для осуществления последующей (после заполнения формы) подпрессовки и гидродинамической импульсно-вибрационной обработки металла в форме специальными силовыми возмущениями, которые обеспечивают качественное протекание процесса формообразования отливки и снижение остаточных напряжений. Качество получаемых отливок зависит от правильного выбора всех технологических режимов заполнения и подпрессовки давлением.
Теоретические основы литья по газифицируемым моделям с регулированием процессов газодинамики (в форме с сыпучем наполнителем) на основе проведенных научных исследований и накопленного производственного опыта обобщены в работах [1-4]. Принципы управления процессами формообразования литых структур в песчаной форме под силовым воздействием пуансона можно найти в публикациях [5-7], а описание конструктивного исполнения литейных машин (рис. 1) приводится в работах [5, 8].
Динамические методы снижения остаточных напряжений в отливках из железоуглеродистых сплавов и описание механизмов воздействия на отливку силовых возмущений можно найти в публикациях [9-12]. Следовательно, исследование динамики движения пуансона можно рассматривать в контексте решения комплексной задачи управляемого формирования стальной отливки в песчаной форме и интервале полностью завершенного технологического цикла.
Рассматривая процессы принудительной регулируемой подачи расплава в песчаную форму с газифицируемой моделью, можно отметить, что вопросы оптимизации технологических режимов при формировании герметичных отливок, получение отливок с армирующим каркасом методами пропитки и композитных литых материалов с применением дисперсных наполнителей до настоящего времени освещены недостаточно. При разработке технологий существуют принципиальные трудности расчета оптимальных давлений пуансона, напрямую связанные с определением соответствующих скоростей потока и градиентов температур, которые вместе предопределяют ход процесса формирования отливки. Совместное рассмотрение этих комплексно связанных параметров обусловлено низкими прочностными характеристиками песчаной формы и сложной формой получаемых отливок. Последнее обстоятельство дополнительно порождает нелинейность функции управления внутриформенным развитием и скоростью потока расплава.
В такой ситуации при расчете технологических параметров литья возникает необходимость в проведении предварительной оценки процесса и установлении функциональных закономерностей динамики движения пуансона как главного исполнительного элемента, определяющего на всех стадиях характер поведения системы пуансон-металл-форма.
Необходимо отметить, что проведение исследований процессов литья с позиций теплофизики, механики многофазных систем, динамики и кинематики
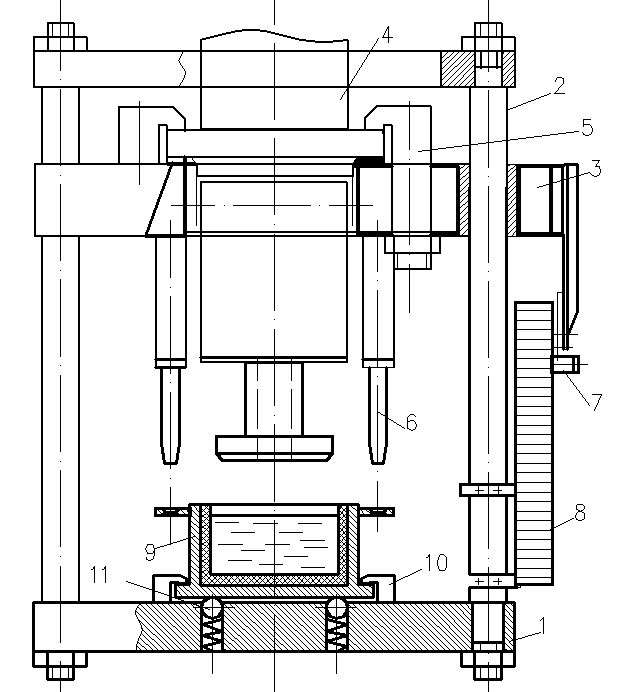






Рис. 1. Конструкция литейной машины для литья отливок по ЛГМ-процессу способом выжимания: 1 – подвижная плита; 2 – подвижные колоны; 3 – опорная плита; 4 – форма; 5 – фиксаторы для закрепления формы; 6 – направляющие штоки; 7 – датчик положения; 8 – оптическая линейка датчика положения; 9 – камера выжимания; 10 – фиксаторы для закрепления камеры выжимания; 11 – центрирующие фиксаторы.
привод специализированных литейных машин позволяет более глубоко подойти к рассмотрению данной проблемы и создать информативную базу по разработке основ теории управления процессом формообразования сложных кристаллизующихся систем в песчаной форме.
Процессы литья и динамику движения пуансона исследовали на примере формирования полой стальной отливки по схеме, приведенной на рис. 2, где песчаная форма является главным объектом, на который передается силовое воздействие через жидкий расплав. Для заливки форму-контейнер помещали на специальный литейный стенд (рис. 3), который был оборудован следящим гидроприводом с системой импульсного возмущения пуансона и микропроцессорной системой управления [5, 13]. Технические характеристики стенда приведены в табл. 1.
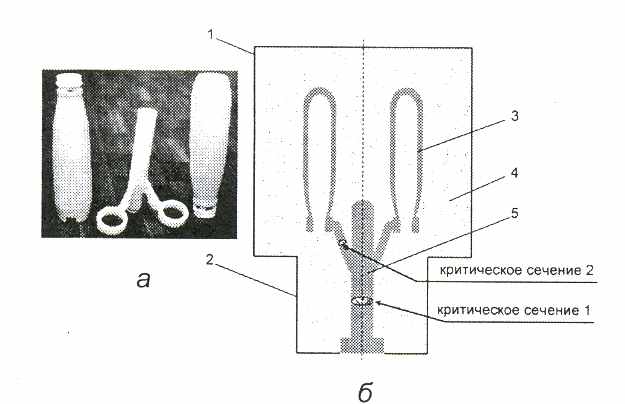
Рис. 2. Литейная форма с выжигаемой моделью: а – пенополистироловая модель сосуда высокого давления; б – герметизированный податливый контейнер с модельным блоком: 1 – податливый контейнер; 2 – пуансон контейнера; 3 – модельный блок; 4 – сыпучий наполнитель; 5 – литниковая система
Таблица 1. технические характеристики экспериментального стенда
Параметры | Величина | Диапазон изменений |
Максимальный объем выдавливаемого жидкого расплава в камере выжимания, л | 89 | - |
Секундный расход при выжимании расплава, л/с | 8,9 | 0,3-17,8 |
Максимальный диаметр поршня камеры выжимания, мм | 450 | - |
Площадь поршня камеры выжимания, см2 | 2131 | 400-2500 |
Рабочий ход поршня, мм | 420 | - |
Диаметр поршня гидроцилиндра, мм (см) | 190, (19) | 150-200 |
Площадь поршня гидроцилиндра, см2 | 284 | - |
Максимальное усилие, развиваемое гидроцилиндром, кН | 300 | - |
Максимальное рабочее давление в гидроцилиндре, МПа | 17 | - |
Рабочий объем гидроцилиндра, л | 12,5 | |
Максимальный расход рабочей жидкости, л/с (л/мин) | 2,5 (150) | - |
Процесс ЛГМ стальных отливок предварительно предусматривал проведение математического моделирования процессов затвердевания в критических узлах сечений стальной отливки. Данные, приведенные на рис. 4, позволили установить оптимальные температурно-временные интервалы технологической обработки жидко-твердеющего расплава. Продолжительность затвердевания отливки в массивных сечениях значительно больше времени затвердевания в сечении литника. Оптимальное время заполнение формы расплавом рассчитывали с учетом движения металла по наиболее критическим сечениям литниковой системы (см. рис. 2).
Динамику движения расплава математически можно выразить на основе уравнения Лагранжа второго рода с учетом переходных процессов и влияния вектора суммарных сил от действия вакуума и газового давления при сгорании модели.

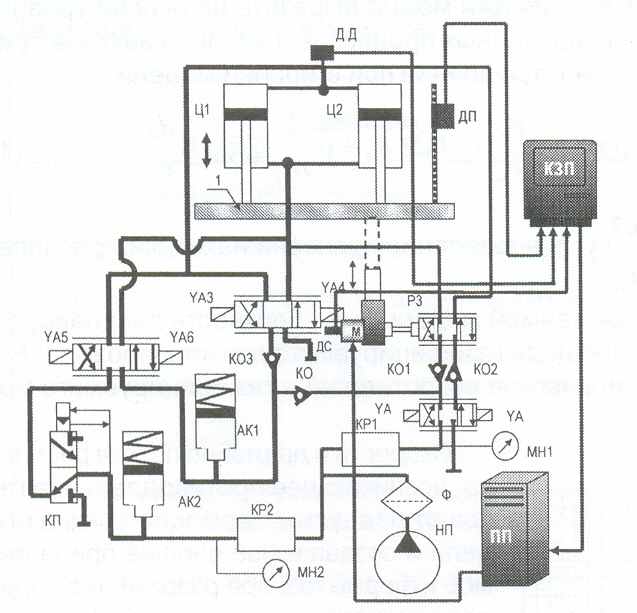
Рис. 3. Схема электрогидропривода стенда для литья отливок по способу выжимания металла в газифицируемую форму: 1 – подвижная траверса; Ц1, Ц2 – цилиндры выжимания; ДП – датчик положения; РЗ – золотник следящий; YA1-YA6 – гидрораспределители золотниковые с электрическим управлением; КО1-КО4 – клапаны обратные; КР1, КР2 – клапаны редукционные; КП – клапан-пульсатор; АК1, АК2 – гидроаккумуляторы; Ф – фильтр; МН1, МН2 – манометры; НП – гидронасос; КЗП – контроллер задания параметров; ПП – полупроводниковый преобразователь; ДП – датчик положения подвижной траверсы; ДС – датчик скорости движения траверсы; ДД – датчик давления; М – исполнительный двигатель следящего золотника
где
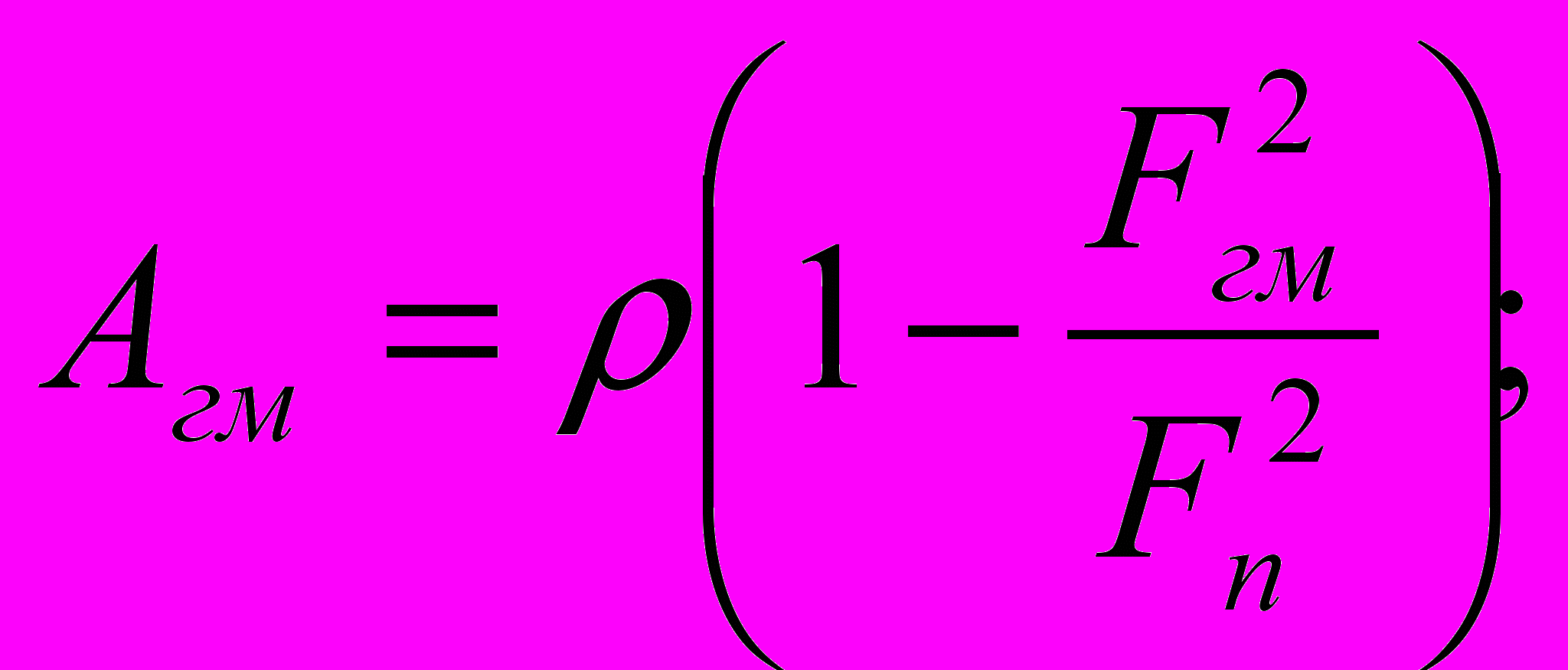

Скорость и давление потока расплава, возникающее противодавление газов от продуктов термодеструкции модели и создаваемое внешне прилагаемое к форме газовое разрежение определяют гидродинамический режим формирования отливки, которым необходимо управлять, регулируя подачу металла в форму во времени и по координате положения фронта жидкости.
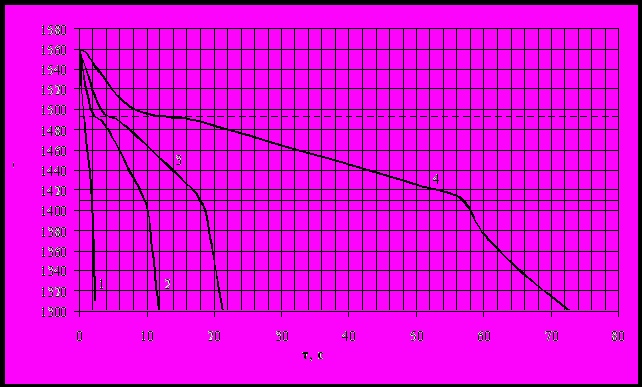
Рис. 4. Изменение температуры стальной обечайкой переменного сечения в песчаной форме с сухим песком: 1 – Δ1 = 0,4 см; 2 – Δ2 = 1,0 см; 3 – Δ3 = 1,4 см; 4 – Δ4 = 2,5 см;
Совокупность перечисленных выше параметров и дополнительно прилагаемые на поверхность формы внешние нагрузки определяют режим поддержания квазистатического равновесия поверхности раздела модель-форма, которыми также необходимо управлять, регулируя расход металла, параметры противодавления в форме и меняя во времени силовое воздействие пуансона.
Температура заливаемого металла, тепловой режим камеры выжимания и формы, продолжительность заполнения, продолжительность действия подпрессовки, а также цикл формирования отливки определяют тепловой режим процесса ЛГМ*, оптимальные параметры которого устанавливаются перед заливкой расплава и по которому в процессе формообразования отливки необходимо корректировать внешние энергосиловые возмущения.
Режим формирования НДС** отливки является четвертым режимом управления оптимальными параметрами, который необходимо реализовать после завершения процесса кристаллизации, учитывая необходимость снижения остаточных напряжений в отливке и стабилизацию ее размерной точности.
При расчете технологических параметров литья сосудов высокого давления проведем начальный анализ исходных данных (табл. 2) и сформулируем основные законы регулирования, касающиеся заполнения формы жидким металлом.
Таблица 2. Исходные данные
Параметры | Величина | Диапазон изменения значений |
Масса заливаемого блока отливок, кг | 94 | 400-650 |
Масса жидкого расплава в камере выжимания, кг | 108 | 600-700 |
Критическое сечение (2,3 х 1,5) металлопровода 4-х питателей, м2 | 13,8·10-4 | (10-15)·10-4 |
Критическое сечение (Ø 5,5 см) металлопровода, м2 | 23,75·10-4 | (25-30)·10-4 |
Материал отливки | сталь 60Л | |
Технологическое время обработки в жидком состоянии расплава по меньшему критическому сечению, с | 55 | 3-60 |
Полное технологическое время цикла обработки расплава, с | 60 | 60-120 |
Остальные необходимые параметры вычислим расчетными методами и сведем в табл. 3.
Таблица 3. Расчетные параметры литья
Параметры | Величина |
Объем выдавливаемого жидкого расплава в камере выжимания для заполнения формы, л | 12 |
Полный объем жидкого расплава в камере выжимания, с учетом пресс-остатка, л | 13,79 |
Минимально допустимый секундный расход при выжимании расплава по критическому сечению стояка, л/с (кг/с) | 0,218, (1,70) |
Минимально допустимая скорость перемещения потока расплава в критическом сечении питателей, м/с | 0,09 |
Минимально допустимая скорость перемещения потока расплава в критическом сечении металлопровода, м/с | 0,158 |
Максимальная критическая скорость по критерию Re, м/с | 0,4 |
Максимально допустимый (по критерию Re) секундный расход при выжимании расплава, л/с (кг/с) | 0,552, (4,32) |
Площадь поршня камеры выжимания, см2 | 452 |
Необходимый рабочий ход поршня, мм | 266 |
Данные, приведенные выше (см. табл. 1, 2), являются базовыми для расчета оптимального управления технологическими параметрами литья сосудов методом выжимания металлического расплава в газифицируемую форму.
При получении стальных отливок, имеющих тонкую протяженную стенку, характер процессов формирования структуры и динамики возмущения пуансона будет иметь изменение не только в скорости, но и давлении, налагаемом на жидкий расплав, при котором наблюдаются 7 отличающихся стадий изменения состояния динамики возмущения как по гидродинамическим, так и тепловым характеристикам (рис. 5).
На стадии-этапе 1 предусматриваются дозированное перемещение пуансона и мягкая его стыковка с зеркалом жидкого расплава в камере выжимания. Диаграмма скорости (кривая 6) состоит из участка в интервале Т1, ускорения рабочего органа до скорости 1,53 м/с, движения с заданной скоростью и мягкой плавной остановкой в конце временного интервала. Началу процесса выжимания расплава соответствует период Т2, за который происходит выжигание пенополистирола и заполнение расплавом стояка. Т3 – период заполнения расплавом четырех параллельных питателей. Низкая прочность
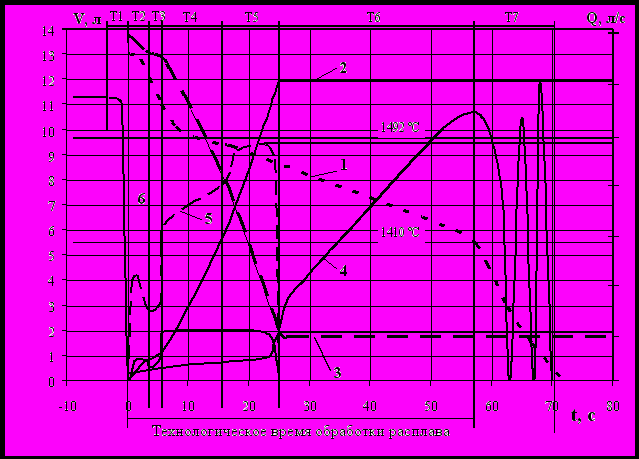
Рис. 5. Изменение технологических параметров литья и формообразования сосудов высокого давления в процессе технологических операций выжимания расплава в газифицируемую форму, подпрессовки и формирования напряженно-деформированного состояния отливки; Т1 – период быстрого подвода пуансона к зеркалу металла; Т2 – период заполнения расплавом стояка; Т3 – период заполнения расплавом четырех параллельных питателей; Т4 – первая ступень заполнения моделей расплавом; Т5 – последний период заполнения формы расплавом; Т6 – период подпрессовки; Т7 – период виброимпульсной обработки горячей отливки для снятия остаточных напряжений. 1 – температурная кривая в наименьшем критическом сечении; 2 – кривая заполнения формы расплавом; 3 – объемное уменьшение расплава в камере выжимания; 4 – временная диаграмма изменения давления жидкого расплава; 5 – диаграмма изменения во времени расхода жидкого металла при заполнении формы; 6 – диаграмма изменения скорости движения пуансона
песчаной формы требует тщательного подхода к регулированию скорости потока и давления (кривая 4), чтобы избежать разрушение формы и выдавливания расплава в сыпучий наполнитель. Т4 – первая ступень газификации моделей и заполнения их расплавом. Т5 – завершающий период заполнения формы. За время Т6 происходит управляемая кристаллизация расплава в форме и образование твердеющей корки по наружному контуру формирующейся отливки. Давление пуансона в этот период постепенно повышают по мере увеличения прочностных свойств твердеющей оболочки. Конец периода Т6 наступает при понижении температуры расплава и перемерзании литников 1410 °С, (рис. 5, кривая 1).
Особый интерес для исследователей представляет исследование возможности применения ударной обработки для воздействия на отливку в нагретом состоянии. Однако на этом пути возникает немало трудностей, которые связаны с подводом виброколебаний отливки и измерением ее виброчастотных характеристик. Специально для этих целей в гидросистему стенда включили гидроаккумуляторы АК1, АК2 (см. рис. 3).
Ранее экспериментально было установлено [12], что наибольшая степень интенсификации процессов снижения остаточных напряжений и очистки поверхности достигается при ударно-импульсной обработке стальных структур, находящихся в горячем остывающем состоянии в интервале температур 1400-150 °С. При этом отпадает необходимость в проведении отдельной термической операции по снижению остаточных напряжений в отливке. Приложение ударных импульсов с регулируемой энергией удара Е осуществляется после окончания процесса формирования стальной отливки в период Т7.
Ударные импульсы налагаются путем разряда энергии гидроаккумулятора через пуансон и твердую структуру металлопровода непосредственно на горячую отливку. При этом сыпучий песчаный наполнитель, находящийся в контейнере, исполняет роль гасителя колебаний и, кроме того, как абразивный наполнитель очищает поверхность отливки от пригара.
Таким образом, определили, что динамика движения пуансона в замкнутом законченном цикле формирования стальной отливки носит сложную управляемую функцию с изменяющимися параметрами давления и скорости, которую необходимо предварительно задавать с учетом реальных теплофизических процессов затвердевания отливки. Технологическая оптимизация динамики движения расплава и последующего его формирования в литую структуру способствует поиску эффективных управляющих воздействий на жидкий и кристаллизующийся металл и создает предпосылки по созданию завершенных циклов формирования (с разгрузкой по остаточным напряжениям) литой детали.
Оценка результатов качества литья путем определения действительной плотности отливки методом гидростатического взвешивания и сравнения полученной интегральной плотности структуры отливки с эталоном подтвердили целесообразность и эффективность применения указанного способа для производства плотных стальных отливок.
Список литературы
- Шинский О.И. Газогидродинамика и технология литья железоуглеродистых и цветных сплавов по газифицируемым моделям: Дис. … д-ра техн. наук. – Киев, 1997. – 481 с.
- Шуляк В.С., Рыбаков С.А., Григорян К.А. Производство отливок по газифицируемым моделям. – М.: МГИУ, 2001. – 330 с.
- Шинский О.И. Новое в теории и практике литья по газифицируемым моделям // Литейн. пр-во. – 1998. - № 7. – С. 31-33.
- Шинский О.И. Механизм формирования качества отливок, получаемых по газифицируемым моделям // Там же. – 1991. - № 1. – С. 4-7.
- Исследование и выбор методов автоматического управления процессом литья в газифицируемые формы с наложением избыточных давлений, разработка микроконтроллерной системы управления параметрами формообразования отливок. Отчет по научно-исследовательской работе. Тема № 1.6.5.508, № Государственной регистрации 0103U003054. – Киев: ФТИМС НАН Украины, 2004.
- Русаков П.В. Шинский О.И. Яковишин О.А. и др. Синтез системы управления процессом выжимания потока расплава в форму с газифицируемой моделью // Процессы литья. – 2004. - № 2. – С. 51-56.
- Русаков П.В. Шинский О.И. Следящие системы управления подачей потока расплава в газифицируемые формы // Процессы литья. – 2005. - № 3. – С. 80-85.
- Пат. № 832 Україна. МКИ В22С 9/04. Устаткування для виготовлення виливків по моделях, що газифікуються, з кристалізацією під тиском / О.Й.Шинський, А.І.Валігура, В.І.Лозенко та ін. – Опубл. 15.12.93, Бюл. № 2.
- Шинский О.И., Русаков П.В. Опыт применения центробежных вибрационных машин при решении технологических задач литейного производства // Процессы литья. – 2000. - № 1. – С. 73-78.
- Русаков П.В. Выбор информативных параметров при виброобработке отливок //Интенсификация литейных технологий. – Киев: Ин-т пробл. литья АН УССР, 1989. – С. 70-72.
- Русаков П.В., Шинский О.И. Остаточные напряжения в отливках головок блока цилиндров и способ их уменьшения динамическим нагружением // Процессы литья. – 2000.- № 3. – С. 92-94.
- Русаков П.В. Удосконалення способів застосування динамічного навантаження для інтенсифікації процесів старіння виливків: Автореф дис. … канд. техн. наук. – Київ, 2001. – 18 с.
- Пат. № 5451 Україна. МКИ В22С 9/04. Спосіб формоутворення / П.В.Русаков, О.И.Шинський, І.О.Шинський, О.А.Яковішин. – Опубл. 15.03.2005, Бюл. № 3.
Поступила 20.04 2005
* ЛГМ – литье в форму с газифицированной моделью
** НДС – напряженно-деформированное состояние отливки